25 minute read
Impact of Formation Damage on Well Productivity throughout Experimental Work and Field case study
Next Article
By
Dr. Ahmed Nooh Egyptian Petroleum Research Institute, Cairo, Egypt.
Abstract the efficiency with which we produce Well productivity de- oil and gas. cline have been widely Laboratory core flood tests had been observed in Western used to determine the causes, degree, Desert, Egypt for oil and extent of damage. Scanning elecand gas wells producing the reservoir tron microscopy (SEM) was used to fines. The phenomenon has been ex- analyze the rock samples used for the plained by the lifting, migration and core flood test before and after the subsequent plugging of the pores by test. Core flood test had been done to the fine particles, finally resulting in evaluate the effect of acid on damaged permeability decrease. It has been ob- cores. Matrix acid stimulation on a served in numerous core flood tests case study from the studied field was and field cases. evaluated. This extensive paper dealt with the subject of formation damage by drilling fluids. It discusses the impact of damage on well productivity, the major mechanisms of formation damage by drilling fluids, assessment and testing of damage, outline considerations for mud selection and optimisation, and removal of mud damage. We define formation damage for the purposes of this report as any process that impairs the permeability of reservoir formations such that hydrocarbon production (in production wells) or injectivity (in injector wells) is reduced. While formation damage can occur at all stages of well construction, during remedial treatments and during production, this paper is concerned only with damage caused by drilling fluids. Work in progress in oil companies, service companies and academic institutions will continue to improve our knowledge, which in turn will increase
1. Introduction
A traditional philosophy has been to worry less about formation damage by drilling fluids because stimulation treatments could generally be employed to recover lost productivity. There is now a growing awareness that prevention of damage is better than cure. If muds are designed and used properly, the need for stimulation can be reduced and often removed. An increasing number of wells are completed without casing and perforation, using instead gravel packs, pre-packed screens and slotted liners. In these completions, near-wellbore damage by drilling fluids is not bypassed by perforation tunnels. Hence avoidance of shallow mud-induced damage becomes a major issue in nonperforated wells. These considerations explain the increased importance given to the understanding and control of formation damage. Of the preventable forms of damage, that caused by drilling fluids is generally seen as a major issue. This report will discuss the impact of mud damage on well productivity, the mechanisms by which drilling muds can cause damage, methods of formulating low damage muds, and ways of preventing and removing damage.
1.1 Impact of Formation Damage On Well Productivity
Pressure draw-down measurements made during well tests give information on the actual performance of a well and allows comparisons to be made with a model well where productivity is estimated from reservoir data, including rock permeability and porosity, permeability variations, reservoir size and shape, structural characteristics and the properties of the formation fluids. If the well produces at a rate lower than its full potential, the well is said to be damaged. This damage is depicted as a permeability reduction, or skin, which surrounds the wellbore (Figure 1). There are many causes of skin, including damage by drilling mud, cement, perforating, well geometry, stimulation and production, and the total skin measured in a well is the combination of these effects. The component of the skin caused by drilling mud damage is frequently highlighted as a major
cause of reduced inflow. Furthermore, cause of reduced inflow. Furthermore, it is a cause that can often be signifi it is a cause that can often be signifi- cantly reduced by proper mud design cantly reduced by proper mud design and engineering practices. and engineering practices.
1.2 Formation Damage Mech 1.2 Formation Damage Mech- anisms of Drilling Fluids anisms of Drilling Fluids
From the time the drill bit contacts the From the time the drill bit contacts the top of the reservoir until the well is top of the reservoir until the well is brought into production, the formation brought into production, the formation is exposed to several fluids and opera-is exposed to several fluids and operations which have the potential to reduce tions which have the potential to reduce permeability and hence impact pro-permeability and hence impact productivity. The possibility of formation ductivity. The possibility of formation damage does not, of course, stop when damage does not, of course, stop when the well is brought on stream, but may the well is brought on stream, but may occur during the entire life of the well occur during the entire life of the well when changes in the reservoir stress, when changes in the reservoir stress, pressure, temperature, fluid chemistry pressure, temperature, fluid chemistry etc. can give rise to permeability im-etc. can give rise to permeability impairment known as production dam-pairment known as production damage. Discussions of the full range of age. Discussions of the full range of damage types can be found elsewhere. damage types can be found elsewhere. In this paper we limit ourselves to con-In this paper we limit ourselves to considerations of permeability impairment siderations of permeability impairment caused by drilling fluids. caused by drilling fluids. A wide range of mud types and com-A wide range of mud types and compositions are used as drilling fluids positions are used as drilling fluids for reservoir sections. These fluids are for reservoir sections. These fluids are often called drilling-in or drill-in flu-often called drilling-in or drill-in fluids to signify that special fluids and/or ids to signify that special fluids and/or engineering practices are adopted when engineering practices are adopted when drilling the reservoir. The possible dam-drilling the reservoir. The possible damage caused by these mud components age caused by these mud components can be classified in several ways (1). can be classified in several ways (1).
1.3. Damage by Physical Reduc 1.3. Damage by Physical Reduc- tion in Pore Sizetion in Pore Size
1.3.1. Invasion by mud solids1.3.1. Invasion by mud solids Drilling fluids can contain various Drilling fluids can contain various types of solids that are used to give types of solids that are used to give density (barite, calcium carbonate, density (barite, calcium carbonate, hematite), fluid loss control (e.g. hematite), fluid loss control (e.g. sized calcium carbonate) and, some-sized calcium carbonate) and, sometimes, viscosity (bentonite). Drilled times, viscosity (bentonite). Drilled solids, which build up in the mud as solids, which build up in the mud as drilling proceeds, are also generally drilling proceeds, are also generally present in significant concentrations. present in significant concentrations. Undissolved polymers (fisheyes) and Undissolved polymers (fisheyes) and insoluble polymer residues may also insoluble polymer residues may also be present. These solids can invade be present. These solids can invade the rock during the early (spurt) stage the rock during the early (spurt) stage of the filtration process (Figure 2). of the filtration process (Figure 2). Most muds will quickly form a fil-Most muds will quickly form a filtercake on the majority of permeable tercake on the majority of permeable rocks (exceptions being some very rocks (exceptions being some very permeable, vuggy or fractured forma-permeable, vuggy or fractured formations) and, once this has taken place, tions) and, once this has taken place, further invasion of mud solids is gen-further invasion of mud solids is generally prevented. This filtercake can erally prevented. This filtercake can be located on the surface of the rock be located on the surface of the rock (an external cake), within the rock (an (an external cake), within the rock (an internal cake) or be a combination of internal cake) or be a combination of the two.the two. The damage potential of mud solids The damage potential of mud solids will depend on the size of the particles will depend on the size of the particles relative to the size of the pore throats relative to the size of the pore throats in the rock formation being drilled. in the rock formation being drilled. The shape, flexibility and degree of The shape, flexibility and degree of dispersion of particles will also be im-dispersion of particles will also be important. Table.1 (4), shows typical size portant. Table.1 (4), shows typical size ranges of solids commonly found in ranges of solids commonly found in muds. The relative proportion of each muds. The relative proportion of each size range of drilled solids will depend size range of drilled solids will depend on the type of solids control system in on the type of solids control system in use. There are some accepted rules of use. There are some accepted rules of thumb concerning bridging and plug-thumb concerning bridging and plugging of pores by particles: ging of pores by particles: If the solid particles have a diameter If the solid particles have a diameter greater than about 1/2 of that of a greater than about 1/2 of that of a pore throat they tend to bridge pores pore throat they tend to bridge pores very effectively and will therefore not very effectively and will therefore not invade far into the rock. Possible ex-invade far into the rock. Possible exceptions to this statement are highly ceptions to this statement are highly flexible particles such as bentonitic flexible particles such as bentonitic clays which can deform sufficiently clays which can deform sufficiently to penetrate pores smaller than the di-to penetrate pores smaller than the diameter of the clay sheets. If particles ameter of the clay sheets. If particles are between 1/6 and 1/3 of the diame-are between 1/6 and 1/3 of the diameter of a pore throat, it has been shown ter of a pore throat, it has been shown (5) that they can invade a significant (5) that they can invade a significant distance into the rock before bridging distance into the rock before bridging pore throats. Particles less than 1/6 pore throats. Particles less than 1/6 of the pore throat diameter generally of the pore throat diameter generally do not bridge (but can migrate freely do not bridge (but can migrate freely through the rock) and so, might be through the rock) and so, might be considered non-damaging. The op-considered non-damaging. The optimum particle size distribution for timum particle size distribution for mud solids is normally selected after mud solids is normally selected after obtaining pore size measurements on obtaining pore size measurements on reservoir cores, for example by mer-reservoir cores, for example by mercury porosimetry or Scanning Elec-cury porosimetry or Scanning Electron Microscopy (SEM). tron Microscopy (SEM). Techniques such as SEM can also be Techniques such as SEM can also be used to examine rock cores for invad used to examine rock cores for invad- ed solids. Because of the high atomic ed solids. Because of the high atomic number of barium, barite is easily im number of barium, barite is easily im- aged in filtercakes and cores, as shown aged in filtercakes and cores, as shown in Figure 3.in Figure 3. Several studies of formation damage Several studies of formation damage due to mud solids invasion have been due to mud solids invasion have been carried out (6), (7),(8).(9). The results carried out (6), (7),(8).(9). The results show that, with the correct choice of show that, with the correct choice of mud system, significant invasion of mud system, significant invasion of solids (and hence damage) can be re-solids (and hence damage) can be restricted to the first 2 or 3 centimetres stricted to the first 2 or 3 centimetres of formation, and often to the first of formation, and often to the first few millimetres in rocks with perme-few millimetres in rocks with permeabilities below about 1 Darcy. This is abilities below about 1 Darcy. This is achieved by ensuring the mud is able to achieved by ensuring the mud is able to form a good quality external filtercake form a good quality external filtercake rapidly (i.e. the spurt volume in the rapidly (i.e. the spurt volume in the pre-cake formation stage is kept as low pre-cake formation stage is kept as low as possible) and that amounts dispersed as possible) and that amounts dispersed and deflocculated colloidal mud solids and deflocculated colloidal mud solids are kept to a minimum. However, even are kept to a minimum. However, even though the depth of invasion is gener-though the depth of invasion is generally small, the degree of damage in the ally small, the degree of damage in the invaded zone can often be extremely invaded zone can often be extremely high, in some cases reducing the origi-high, in some cases reducing the original permeability by over 90%. In rocks nal permeability by over 90%. In rocks with permeabilities greater than about with permeabilities greater than about 1 Darcy, and in situations where high 1 Darcy, and in situations where high differential pressures exist, invasion is differential pressures exist, invasion is often found to be deeper than 2 - 3 cen-often found to be deeper than 2 - 3 centimetres. Krueger (8) quotes data from timetres. Krueger (8) quotes data from an Alaskan field where wells drilled an Alaskan field where wells drilled with mud overbalances less than 1500 with mud overbalances less than 1500 psi typically produced about 2000 bar-psi typically produced about 2000 barrels per day more oil than those drilled rels per day more oil than those drilled at differential pressures higher than at differential pressures higher than 1500 psi. 1500 psi. The impact of damage by colloidal The impact of damage by colloidal fines has been investigated (10) using fines has been investigated (10) using some muds which contain chemically some muds which contain chemically deflocculated bentonite and others deflocculated bentonite and others where the clay has been flocculated where the clay has been flocculated with sodium chloride. In the defloc with sodium chloride. In the defloc- culated mud, the dispersed particles of culated mud, the dispersed particles of bentonite were able to invade deep into bentonite were able to invade deep into rocks with a wide range of permeabili rocks with a wide range of permeabili- ties. Experiments identified bentonite ties. Experiments identified bentonite particles in the effluent obtained dur-particles in the effluent obtained during dynamic and static filtration on 5 ing dynamic and static filtration on 5 cm long cores of Clashach Sandstone cm long cores of Clashach Sandstone (permeability about 400 mDarcies), (permeability about 400 mDarcies),
showing that dispersed clay can penetrate deeper than 5 cm. Permeability measurements indicated some damage along the full length of the core. Provided invasion and damage by mud solids is confined to the first few centimetres of rock adjacent to the wellbore, then the productivity of perforated wells should not be affected, since perforating guns will easily bypass the damage. Mud solids invasion does, however, become important in fractured or vugular formations where the primary production comes via these high permeability channels. In these cases, coarse particulates (lost circulation materials) added to the mud system are sometimes effective at minimising solids invasion (11). Techniques such as underbalanced drilling may also offer ways of drilling these (and non-fractured) formations whilst avoiding invasion and damage (underbalanced drilling is not discussed in this report).
1.3.2. Plugging by mobilised formation fines It is not uncommon to encounter reservoir rocks which contain fine minerals in the matrix. Often, as shown in Figure 4, a high proportion of these fines are located at the surfaces of the rock pores and can become mobilised when exposed to certain fluids or flow conditions. These fines can comprise a range of minerals including clays (illite, kaolinite, chlorite, montmorillonite), carbonates, quartz and feldspars. The occurrence and composition of potentially-damaging formation fines can be identified by a combination of SEM and X-ray diffraction studies on reservoir cores, although in some cases it is easy to confuse formation fines with invaded mud solids. Migrating fines can cause extensive damage (12), (13),(14) by blocking pore throats (Figure. 4). In most formations mobile particles in the size range from 1 to 100 microns are believed to be most damaging, since particles finer than 1 micron are normally strongly held to the surfaces of larger mineral grains by Van der Waals forces and are difficult to dislodge, while particles above 100 microns are larger than most pore throat diameters and so cannot migrate any great distance. It is usually difficult to carry out successful remedial treatments to remove damage caused by formation fines and sometimes these treatments can, themselves, cause fines to become mobilised (e.g. by dissolving intergranular cements) or can leave reaction products which are themselves damaging. If possible, it is better to avoid inducing fines mobilisation by correct choice of drilling fluids than to plan for remedial treatments.
1.3.3. Swelling of smectite clays Rocks that contain swelling clays (montmorillonite, or other smectite minerals) in the pore system can suffer significant permeability reduction if the clays are allowed to swell and block, or partially block, pores (Figure.5). As the minerals swell (15) they also become more fragile, and may be broken up and mobilised by the flowing filtrate. Hence damage can occur through fines migration as well as through swelling. Smectites swell most in low salinity aqueous environments and therefore will become a problem when pore fluid is replaced by a low salt water-based mud filtrate. Sodium exchanged Smectites swell more than calcium or magnesium varieties. Swelling can be controlled by maintaining a high salinity filtrate, preferably containing some potassium or calcium ions which adsorb on the clay and greatly limit water uptake. The clays will not swell in oil, making oil-based muds an option for Smectite-rich reservoirs. Water-based mud additives which use cationic polymers or aluminium chemistry to stabilise swelling clays have been described in the literature (16),(17).
2. Damage by Relative Permeability Reduction
In their natural state, hydrocarbon reservoirs can be water-wet (i.e. a layer of water is in immediate contact with the surfaces of rock grains), oil-wet (oil in contact with the rock grains) or in an intermediate, or neutral, state. Oil production is more efficient when formations are water-wet because then oil does not cling to the mineral grains but moves smoothly in a piston-like displacement through the pore system, sliding on an oil/water interface. By contrast, oil draining from an oil-wet reservoir does so by a less efficient film drainage mechanism. Most sandstone oil reservoirs are in a water-wet state, while many carbonates are intermediate or oil-wet. Invaded drilling mud filtrate can cause damage by introducing an additional fluid phase into the formation, or by increasing the saturation of the nonhydrocarbon phase. These processes can result in a reduction in the relative permeability of the formation to the hydrocarbon phase, and consequently a decrease in well productivity. Damage due to relative permeability changes may only be temporary in the case of emulsion and fluid blocking; however, the higher the viscosity of the damaging phase, the longer it will take for the formation to recover its initial permeability. In long producing intervals, such as in horizontal wells, low drawdown pressures may make it impossible to restore the original permeability along the full length of the producing interval.
2.1. Wettability change due to adsorption of mud surfactants Surfactants (or certain types of polymer) in mud filtrate can change the wettability of the rock and thus affect hydrocarbon production. In particular, oil-based and synthetic-based muds
(both invert and all-oil fluids) contain highly surface active emulsifiers and oil-wetting agents which can change grain surfaces from their natural water-wet to an oil-wet state (Figure.6). Indeed, oil-wetting agents are specifically designed to make weighting agent and drilled solids particles hydrophobic so that they remain in the continuous oil phase of the mud; it is therefore inevitable that, if free surfactant enters the rock in the mud filtrate, the rock is also likely to become oil-wet. Permeability damage caused by wettability change is generally assumed to be permanent, and is most common with oil-based muds. However, due to the low fluid loss rates of oil muds, the depth of damage will often be small. Wettability change generally has a greater impact on production in tight rocks which contain pores of small diameter(18). It has been demonstrated that damage due to wettability change in oil-based muds can be reduced if muds are formulated with low concentrations of free surfactant. However, these muds need careful monitoring to ensure sufficient surfactant is always present to maintain stable fluid properties.
2.2. Emulsion formation If two immiscible fluids - such as crude oil and water-based mud filtrate or formation water and oil-based mud filtrate - are mixed with sufficient energy, an emulsion (water in oil or oil in water respectively for the two above cases) will form which will have a higher viscosity than either of the component fluids. If the emulsions form inside pores, or are transported into pores, an emulsion block can form (Figure.7) and productivity will be decreased. Fine mud solids or formation fines can stabilise these emulsions as can mud surfactants or any natural surfactants in the crude oil. The energy needed to form stable emulsions is greatly reduced in the presence of surfactants. Some workers think it is unlikely that sufficient shear will be present inside rock pores to form an emulsion, but they will form in the wellbore and may then invade (consider the emulsion droplets as flexible solid particles with a range of diameters similar to mud solids). Like drilled solids, the invasion of emulsion droplets is unlikely to extend beyond a few centimetres unless fractures are present or the rocks have a very high permeability. Other authors (18),(19) suggest sufficient shear does exist to form emulsions inside rock because, even though the bulk flow rate of mud filtrate is low, the localised rate of shear at pore throats and other constrictions is sufficient to produce emulsions, particularly when mud surfactants are present in the filtrate.
2.3. Fluid saturation change and blocking A fluid saturation change can occur when, for example, an aqueous mud filtrate invades an oil-bearing zone. The water saturation is increased in the near-wellbore region, which reduces the relative permeability to oil. (Figure. 8). The effect of increasing water saturation on relative permeability has been demonstrated by several workers. Figure. 9 shows data by Keelan and Koepf (19). In this figure, the residual water saturation is defined as the minimum water saturation of the rock when only oil is flowing at a specified pressure drop (i.e. water trapped near grain surfaces or in small pores is not flowing). The residual oil saturation is the corresponding value for oil retained in rock when water is flowing. As water-based mud filtrate invades an oil reservoir, the rock is driven towards residual oil saturation. When the well is turned on to production the oil will push the aqueous filtrate out of the rock, moving the formation back towards residual water saturation and to improved relative permeability to oil. Temporary damage by saturation change and blocking is common in many wells, however this normally clears up during production provided sufficient drawdown can be placed on the producing formation (20) maintaining a low fluid loss in the mud will minimise the problem.
3. Conclusions and Summary
In this paper, the author have studied the impact of formation damage caused by drilling fluids on well productivity and hence on the commercial viability of some oil and gas developments. While damage can be caused by drilling fluids, cements, the perforation or other completion processes, remedial (stimulation) treatments and by the act of producing from a reservoir, we focused only on damage by drilling muds. This can occur by a number of mechanisms:
Ó Blocking of rock pores or pore throats by - invasion by mud solids - plugging by mobilised formation fines - swelling of smectite formation clays - adsorption/precipitation of polymers - inorganic scale formation Ó Relative permeability effects - wettability change by surfactants - emulsion formation - fluid saturation change and fluid blocks The susceptibility of a formation to damage is strongly dependant on the nature of the rock (mineralogy, pore size distribution etc.), the composition of the pore fluids, the temperature and the pressure. The degree of damage caused by a drilling fluid will then depend on variables such as the chemical composition of the mud, the nature and size of the solids in the mud, the spurt and fluid loss rate, and the stability of the fluid components. The prevention of formation damage
by drilling muds has become a major consideration for the oil and gas industry, since damage can have a significant adverse impact on the profitability, and sometimes the economic viability, of many fields. The industry still does not have a complete understanding of: Ó the mechanisms of formation damage. Ó how mud and filtercake damage to certain types of open hole comple-
tions impacts well performance Ó how, in quantitative terms, formation damage impacts well productivity Ó how to formulate stable, environmentally-acceptable, minimallydamaging drilling muds Ó how to measure accurately the damage caused by drilling muds in real wells. Laboratory experiments and scanning electron microscope studies have shown that, these particle-particle interactions are responsible for the formation of gel bridges across pore throats and that these bridges prevent invasion of mud solids into the formation. Thus, the filtercake formed with Visplex is located external to the formation and is easily removed at low drawdown pressures when the well is brought on production.
REFERENCES
1. Bennion. D.B, Thomas, F.B, and Bennion. D.W: “Effective laboratory coreflood tests to evaluate and minimise formation damage in horizontal wells”: Third International Conference on Horizontal Well
Technology, November 12 - 14, 1991, Houston, Texas 2. Ghalabor. A, Hayatdavoudi. A and Shahidi-Asl. M: “A study of formation damage of selective mineralogy due to bacterial plugging”: 3rd Latin American/Caribbean Pet. Eng. Conference, Argentina, April 1994, 818 - 829 3. Lappan. R.E and Fogler. H.S: ”The effects of bacterial polysaccharide production on formation damage”: SPE 19418, 1990, 165 - 172 4. Amoco Production Training Centre: “ Reservoir engineering rock properties”: Volume II (Private communication) 5. Sparlin. D.D and Hagen. R.W: “ Formation damage prevention”: SPE
Short Course, Feb. 1994, Lafayette, LA. 6. Abrams. A: “ Mud design to minimise rock impairment due to particle invasion”: Journal of Petroleum Technology, May 1977, 586 - 592 7. Glenn. E.E and Slusser. M.L: “ Factors affecting well productivity
II - drilling fluid particle invasion into porous media”: Trans Soc. Pet.
Eng. 1954, Vol. 210, 126 - 131 8. Krueger. R.F: “An overview of formation damage and well productivity in oilfield operations”: Journal of Petroleum Technology,
Feb. 1986, 131 - 152. 9. Francis. P.A, Eigner. M.R.P, Patey. I.T.M and Spark. I.S.C: “
Visualisation of drilling-induced formation damage mechanisms using reservoir conditions core flood testing”: SPE 30088, European
Formation Damage Conference, The Hague, May 1995, 101 - 115 10. Fordham. E.J, Sezginer. A and Hall. L.D: “ Imaging multiexponential relaxation in the (y, log, t) plane, with application to clay filtration in rock cores”: Jour. of Magnetic Resonance, 1995, Series A 113, 139 - 150 11. Jiao. D and Sharma. M.M: “ Mud induced formation damage in fractured reservoirs”: SPE 30107, European Formation Damage
Conference, The Hague, may 1995, 299 - 310 12. Schechter. R.S: “ Oil well stimulation”: Prentice Hall, New Jersey, 1992. 13. Porter. K.E: “ An overview of formation damage”: Journal of
Petroleum Technology, Aug. 1989, 780 - 786
NAME: AHMED ZAKARIA NOAH
EDUCATION: Associate.Prof at TheAmerican University in cairo PhD. in Petrophysics.Waseda and Menofia University, 2003. ACADEMIC EXPERIENCE: Faculty of Science and Engineering, The AmericanUniversity in Cairo (12010/9/ – Now, full time Ass.Prof of drilling, completion and workover). -Faculty of Petroleum Engineering, The BritishUniversity in Egypt (212010/9/1 – 2008/12/, full time lecturer and Ass. prof), Undergraduate Level: Oil well drilling, Advanced drilling Engineering, Horizontal drilling, Drilling fluids, Principles of Petroleum Geology, Well logging, core analysis, Development Geology, Completion and workover, Reservoir Rock properties, Reservoir Engineering. -Petroleum Research Institute, Cairo (Full time Researcher : (12008/12/21 - 2005/12/) Faculty of Science, Menofia University, Egypt : (2003 - 2008), Graduate Level:Method of Prospecting. And Well Logging
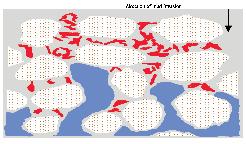
Figure 1: Schematic representation of skin surrounding a wellbore Figure 2: Mud solids invasion. Water-based mud (light background) invading a rock containing oil (dark background). Rock grains are shown in white.
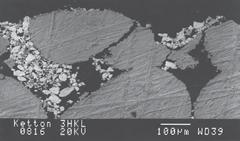
Figure 3: Scanning electron micrograph of barite particles (light grey) in pores of Ketton limestone
Figure. 5 Swelling of Smectite formation clays. Water-based mud (light background ) invading a rock containing oil (dark background).
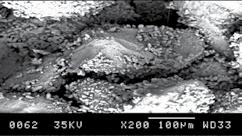
Figure 4: Scanning electron micrograph of sandstone reservoir rock showing secondary quartz fines lining pores.
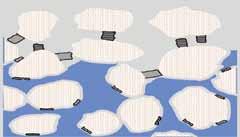
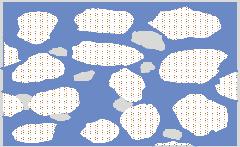
Figure. 6: Wettability change caused by oil-based mud filtrate (dark background) invading a water-wet formation. Figure .7: Emulsion formation . Water droplets (light background ) emulsified in oil (dark background).
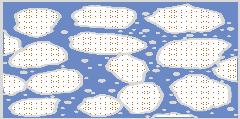
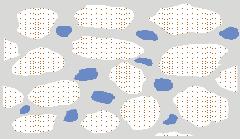
Figure 8: Fluid blocking. Water-based mud (light background ) invading a rock containing oil (dark background).
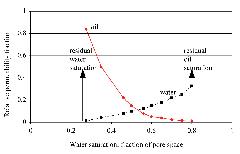
Figure 9: Effect of degree of water saturation on relative permeability to oil(23)
Table 1: Classification of drilling mud solids by particle size
Type of Solid Barite Typical Size Range (microns) 1 – 100
Bentonite 0.1 – 2 Calcium carbonate 1 - 3000 (different size ranges available) Drilled solids (coarse) > 2000 Drilled solids (intermediate) 250 – 2000 Drilled solids (medium) 74 – 250 Drilled solids (fine) 44 – 74
Drilled solids (ultrafine) 2 – 44 Drilled solids (colloidal) < 2
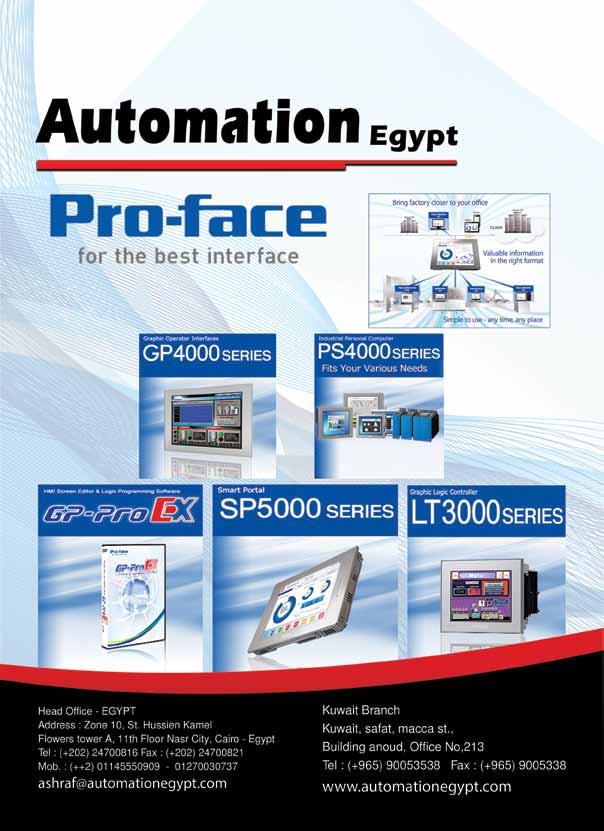