2022July/Aug|60Issue MED-TECH innovation www.med-technews.com MED-TECH INNOVATION | NEWS PLUS The winner of Pitch@Med-Tech Innovation Expo How motors facilitate innovation in Ireland How UKCA requirement has changed medical device manufacturing Delivering innovative and safe products, fast:products, ARENA EXPLAINS HOW PRODUCT-CENTRIC QMS AIDS COMPLIANCE AND COMMERCIALISATION SUCCESS IN VOLATILE MARKETS MEDICAL DEVICE SUPPLY CHAIN INTELLIGENCE
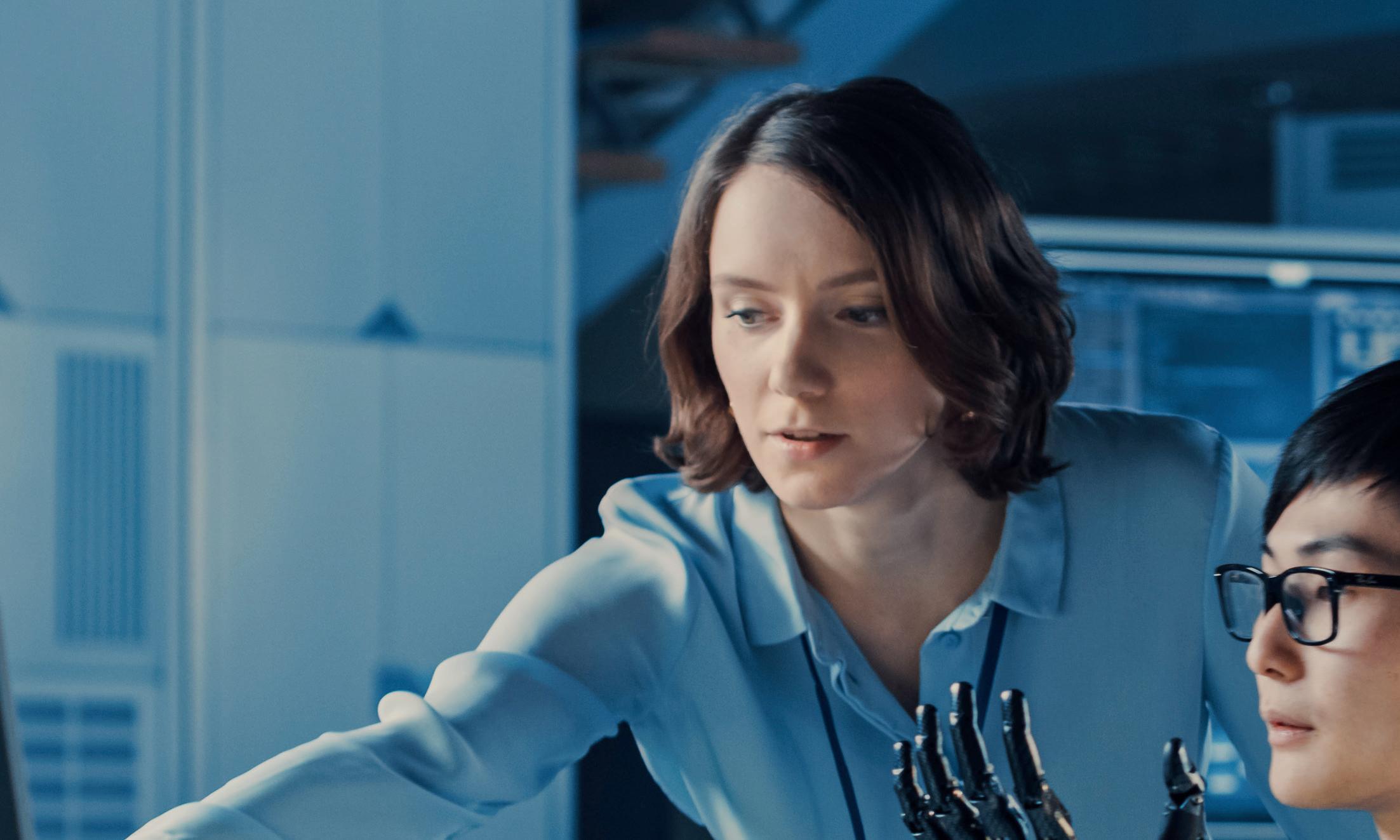
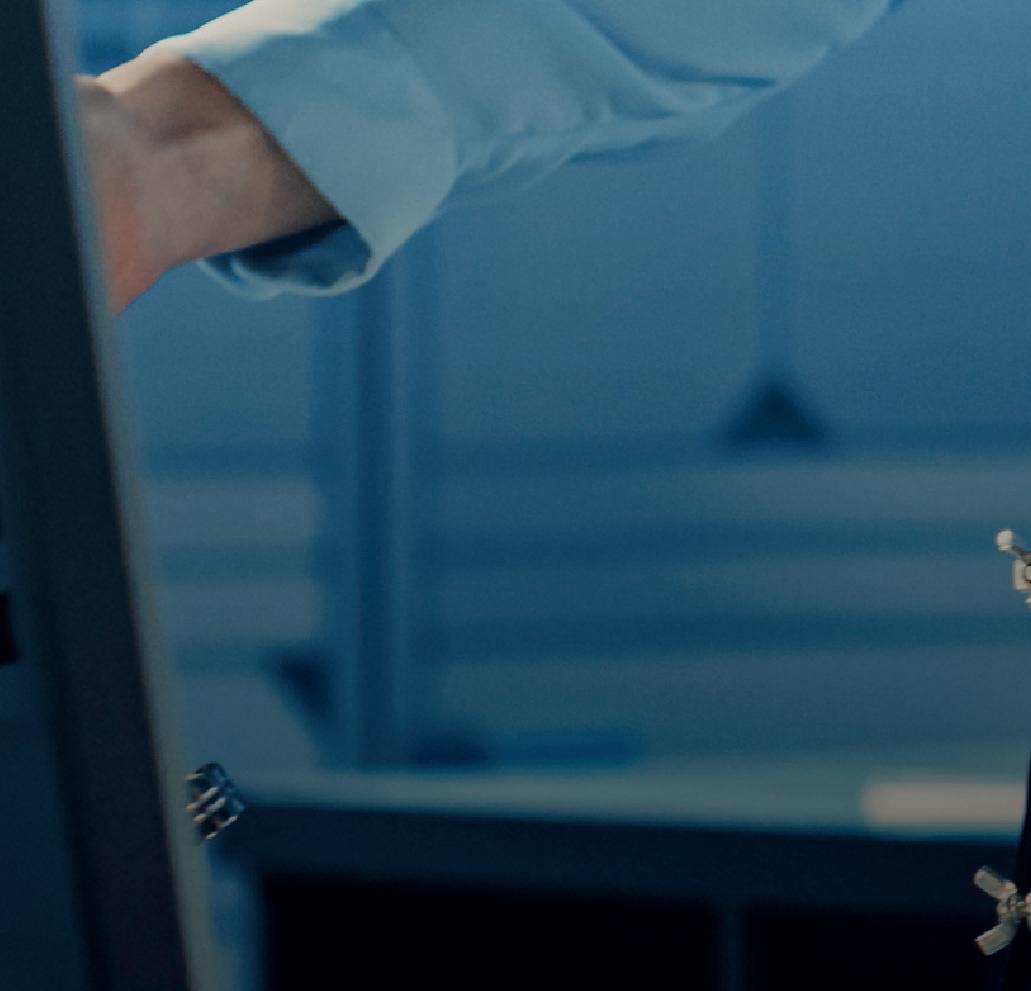
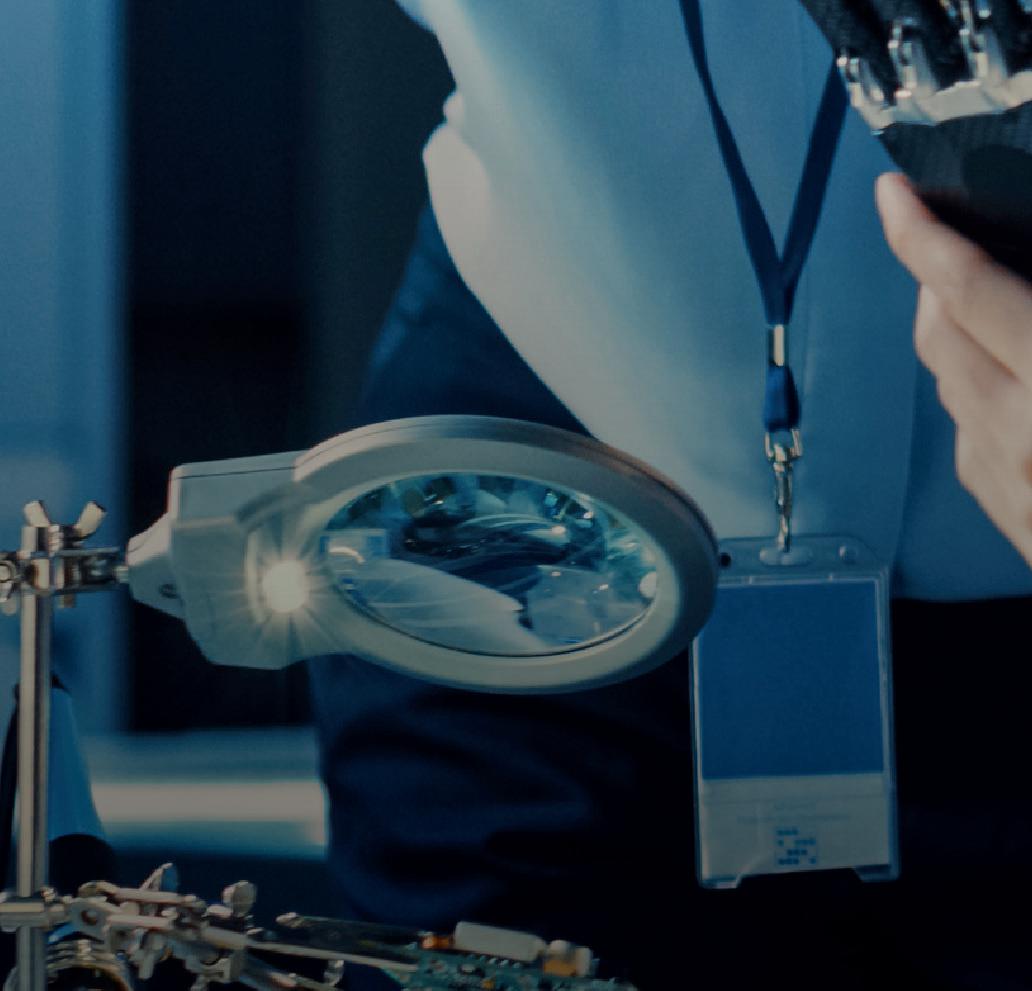
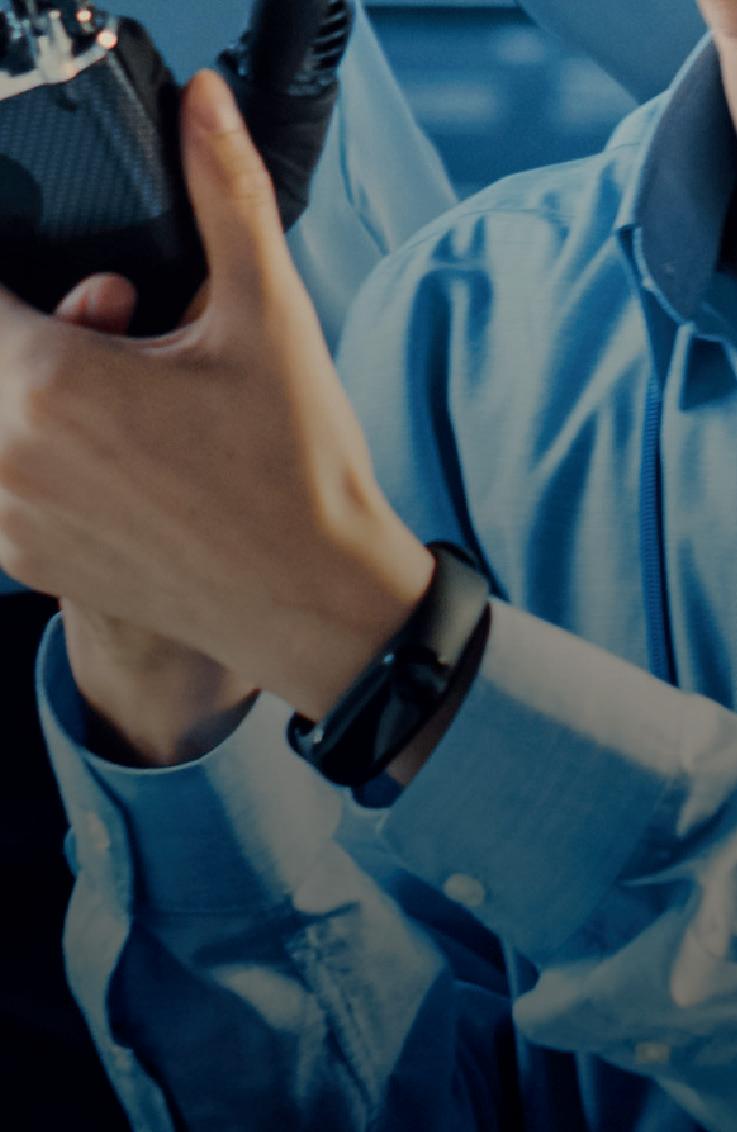
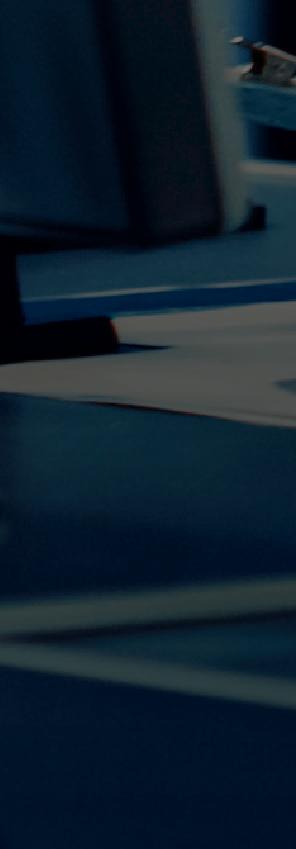
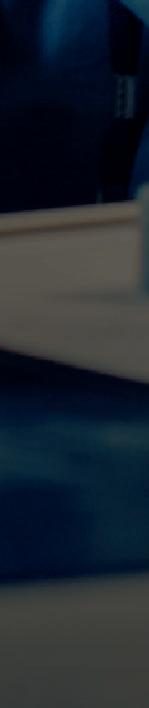
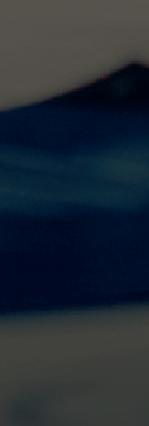

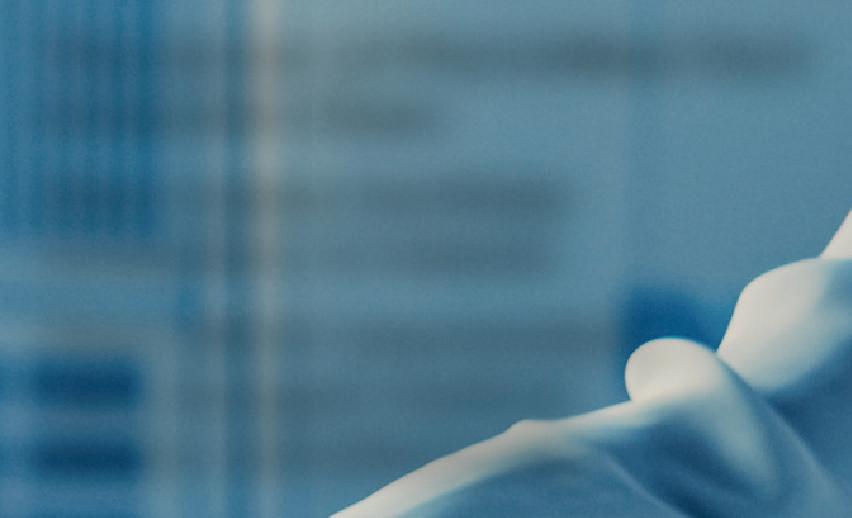

The topics covered were highly relevant and useful, so I can take many lessons back to my day-to-day role and share them with colleagues — 2020 TOPRA Symposium Regulatoryattendee Science –leading the way to the future Register now www.topra.org/MTI-symp The first-choice key event in the European regulatory affairs calendar When 17–19 October 2022 Where Vienna, Austria VIENNA TOPRA Annual Symposium 2022 • Digital Health Opportunities and Advancements in Healthcare • How to approach Artificial Intelligence and Cybersecurity now and in the future • IVDR – where are we? An update on the IVDR implementation AndMDmore...Medical Devices/IVDs Symposium
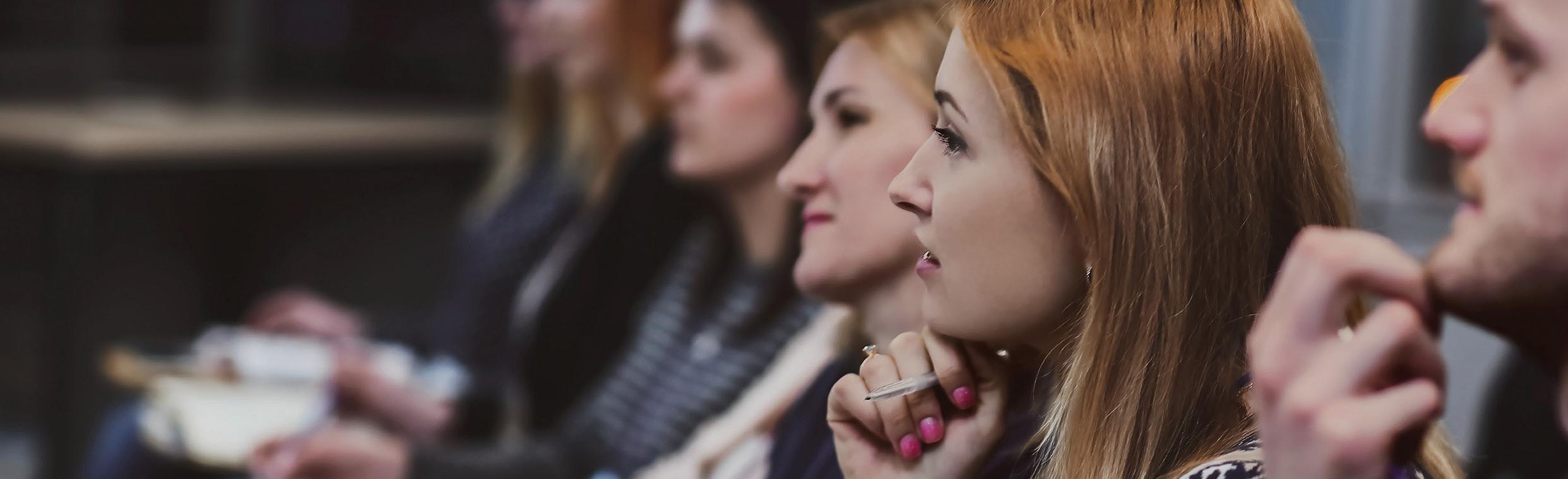
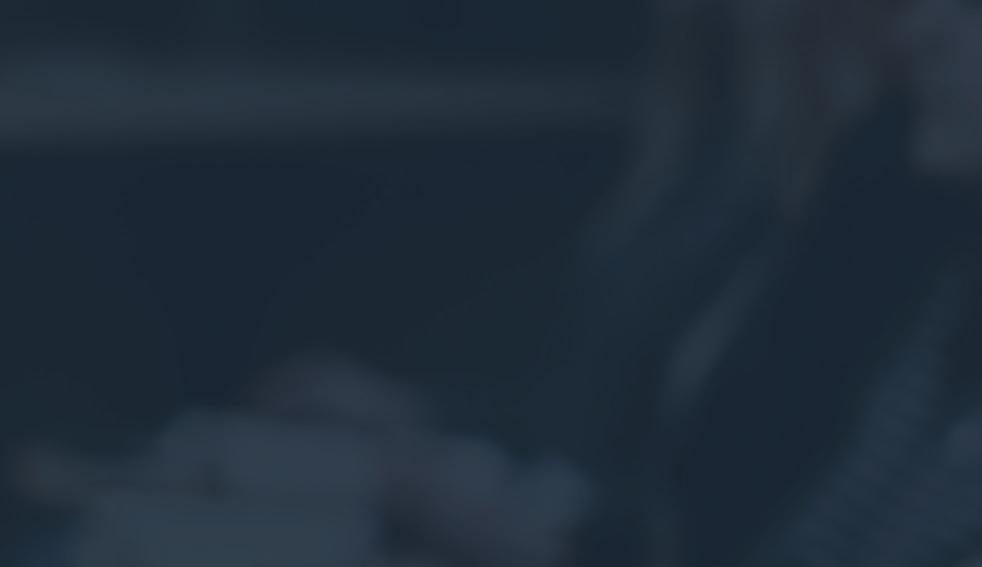
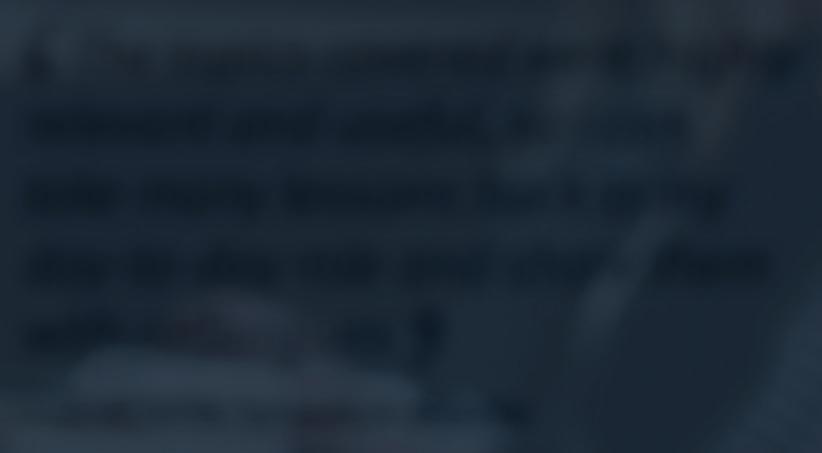


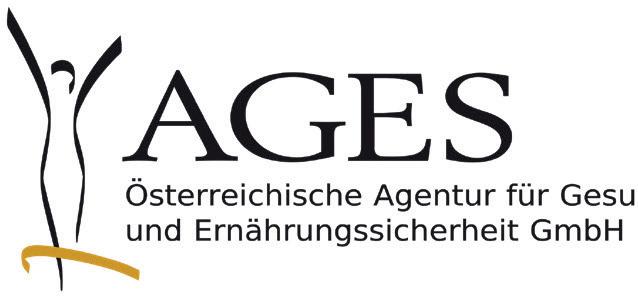
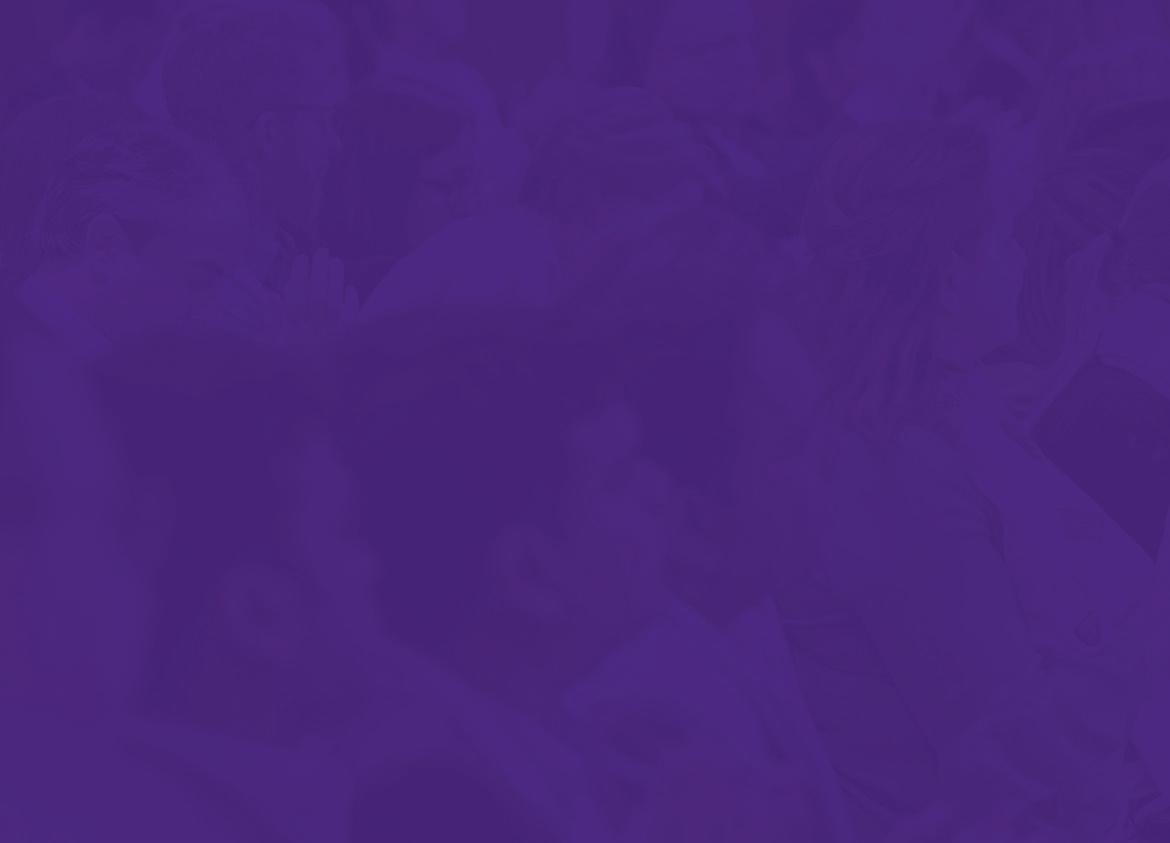
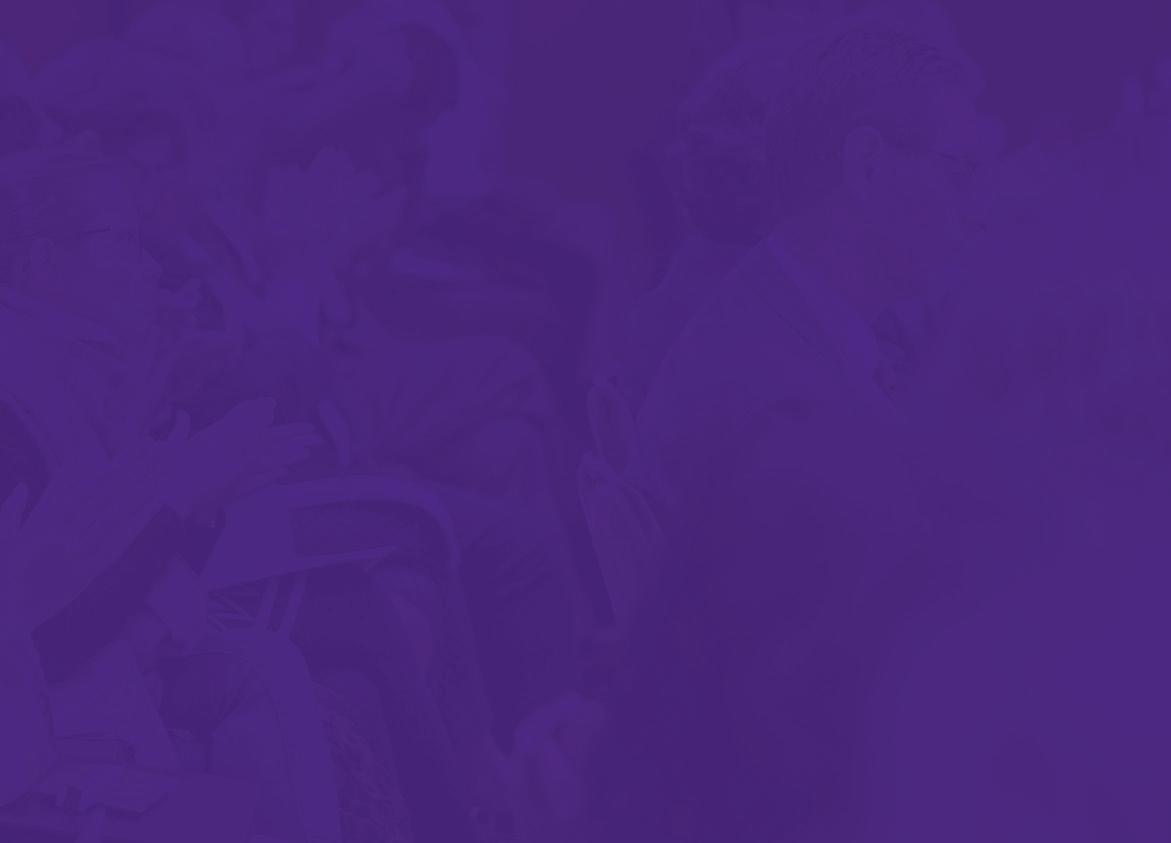

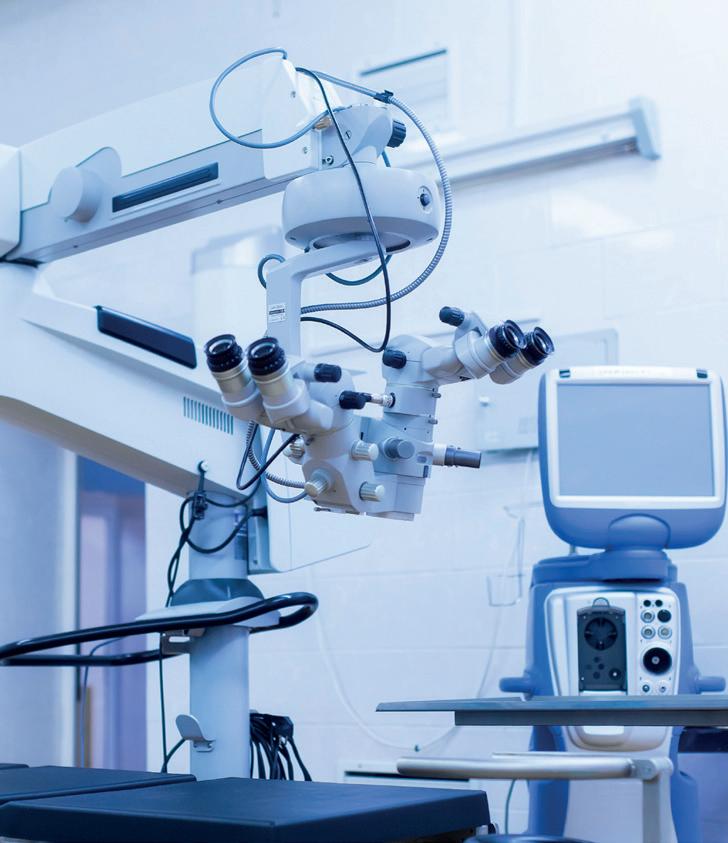
THE TEAM
ISSN
| ian caroline.jackson@rapidnews.com+44carolineportfoliovictoria.dunsmore@rapidnews.com+44victoriaportfoliochristine.joinson@rapidnews.com+44christineportfolioian.bolland@rapidnews.combollandsalesmanager|joinson(0)1244952385salesmanager|dunsmore(0)1244952247salesmanager|jackson(0)1244952358 8. Medilink Top tips for exhibitors to make the most of their presence at international events 9. Ireland EMS explains how cutting-edge advances in Ireland have been made with the support of micromotors 14. Regulation The di erences between CE and UKCA marking are outlined by Kolabtree 16. Tubing TekniPlex looks at ways to manage your supply chain at di cult times 19. Coatings Microban looks at how built-in facilitiesmedicaltechnologiesantimicrobialhelpskeepequipmentandcleanerforlonger 24. Packaging Essentra analyses the rise of at-home diagnostics and the role of packaging 13 MED INNOVATION-TECH|NEWS 3 10 1626
vp
CONTENTS regularsfeatures 5. Comment Ian Bolland invites readers to become part of the Med-Tech Innovation roadshow 6. Making Medtech A round-up of the latest industry news 7. Expo News A round-up of the latest news surroundingInnovationMed-TechExpo 10. Cover story Arena, a PTC company, outlines how a successful QMS helps achieve commercialisation success in a volatile market 18. InnovationMed-TechExpo A selection of highlights from the 2022 running of the show in Birmingham in June 26. RealMedtechWorld SiMed explains its approach to working with start-ups and bringing their innovationstomarket Rapid Medtech Communications Ltd.Carlton House, Sandpiper Way, Chester Business Park, Chester, CH4 9QE MTI PRINT SUBSCRIPTION –subscriptions@rapidnews.comSubscriptionFREEROWEuropeUKQUALIFYINGCRITERIA&Ireland–Free–£249–£249oniOSandAndroiddevicesenquiriesto
©Rapid Medtech Communications Ltd. No part may be reproduced or transmitted in any form without the prior permission of the Publisher. 2046-5424 sales & sales talent | julie publisherdesignersamheadjulie.balmforth@rapidnews.combalmforthofstudio&production|hamlyn|robertwood|duncanwoodeditor
The Publisher endeavours to collect and include complete and current information in Med-Tech Innovation, but does not warrant that any or all such information is complete, correct or current. The Publisher does not assume and hereby disclaims any liability to any person or entity for any loss or damage caused by errors or omissions of any kind, whether resulting from negligence accident or any other cause.
Med-Tech Innovation does not verify any claims or other information appearing in the advertisements contained in the publication and cannot take any responsibility for any losses or other damages incurred by readers in reliance on such content. All submissions are handled with care. Every precaution is taken to ensure accuracy, but the Publisher cannot accept responsibility for the accuracy of the information here.
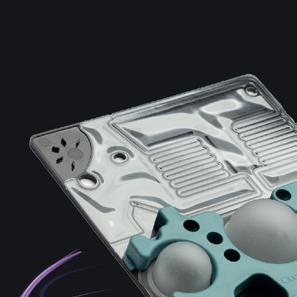
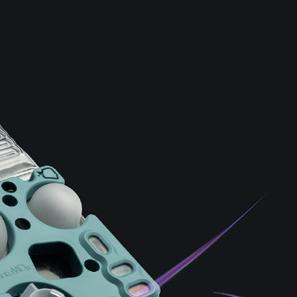
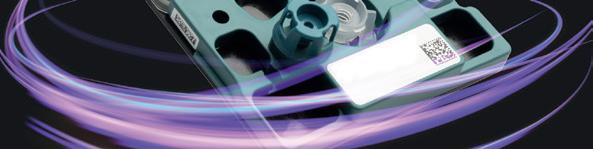
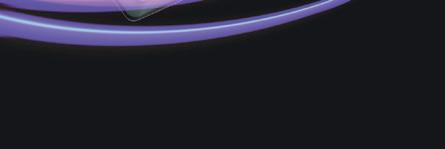
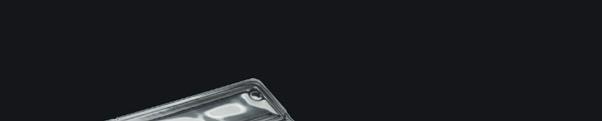
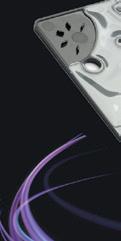
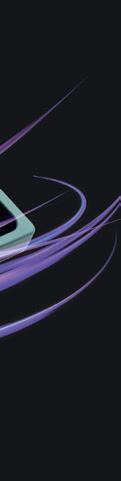
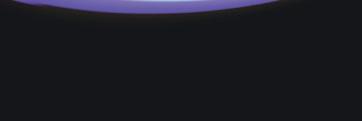
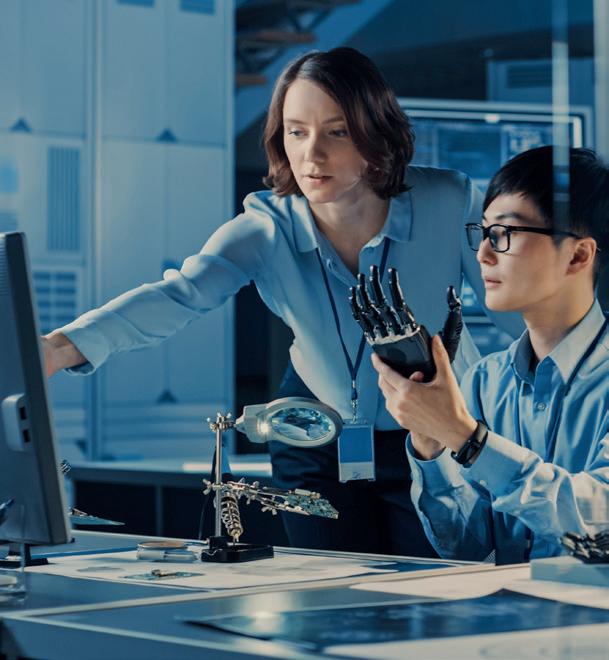
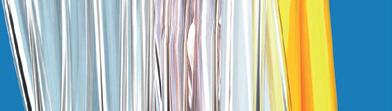
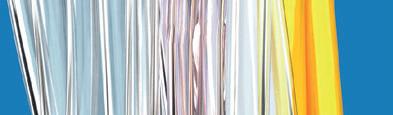


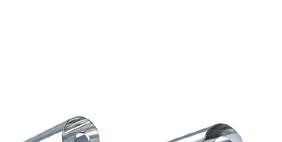
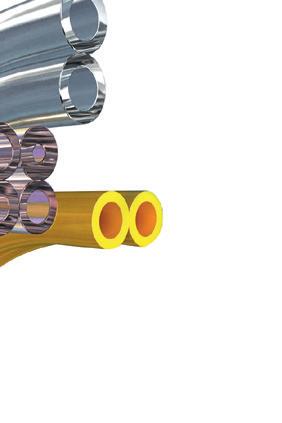



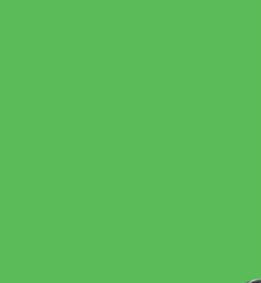

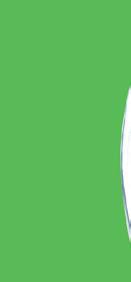
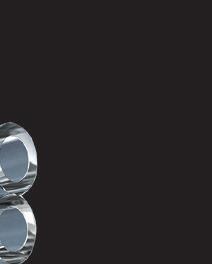
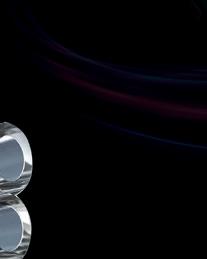
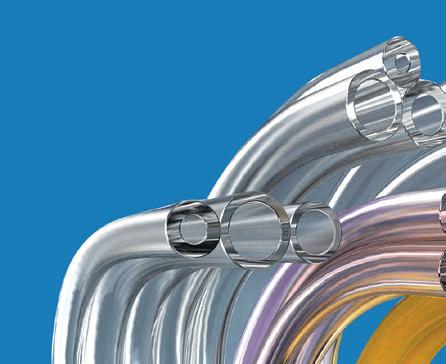
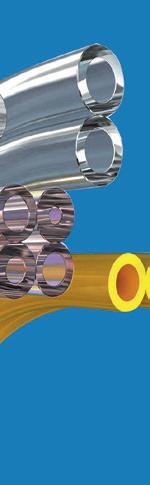
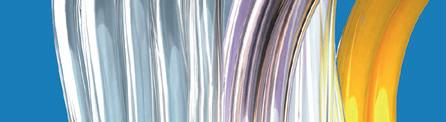
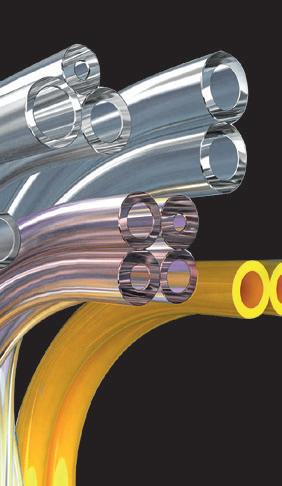
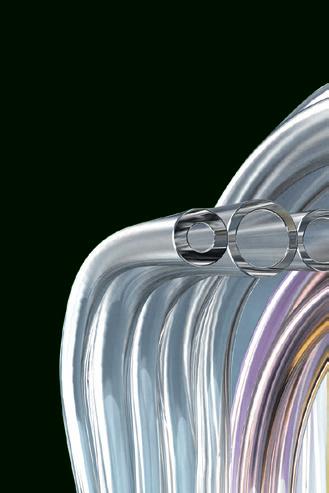
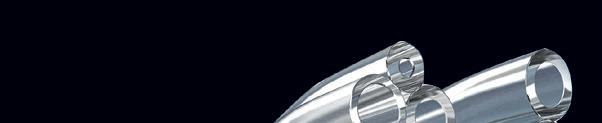
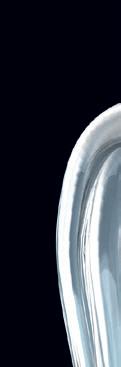
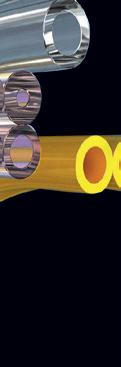





L e e P r o d u c t s L i m i t e d , 3 H i g h S t r e e t , C h a l f o n t S t P e t e r, G e r r a r d s C r o s s , B u c k s S L 9 9 Q E Te l : 0 1 7 5 3 8 8 6 6 6 4 F a x : 0 1 7 5 3 8 8 9 5 8 8 e m a i l : s a l e s @ l e e p ro d u c t s . c o . u k I n n o v a t i o n i n M i n i a t u r e operated fixed volume dispense pumps The pumps feature a revolutionary port head design that allows tubing connections and manifold mounting This enables the designer to test the fluidic system using connections to soft tubing, and then once the system design has been finalized, the same pump can be manifold mounted using standard O rings The electrical interface of the pumps feature a contoured end cap that provides secondary connector retention and is compatible with standard AMP connectors ● 12 or 24vdc ● 10, 25, 50, 100 or 175μL dispense per Shot ● Inert wetted materials ● Low power consumption For more information visit www.leeproducts.co.uk Iner t Solenoid Pumps Inert Solenoid Pumps Ad_THE LEEDERS AD 07/06/2016 15:57 Page 1
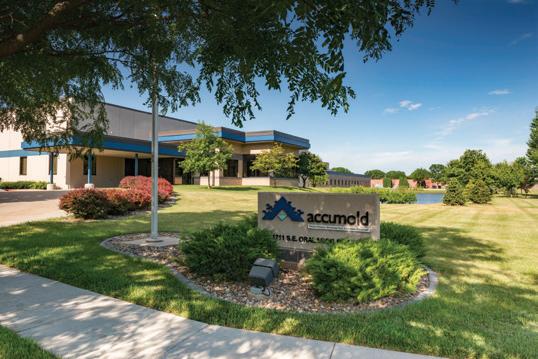
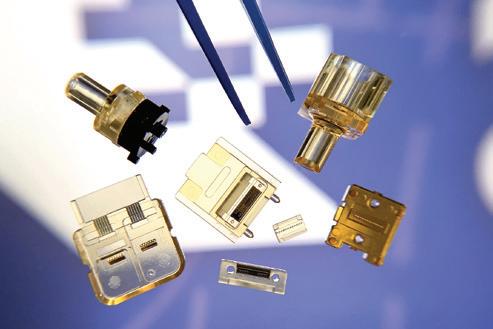
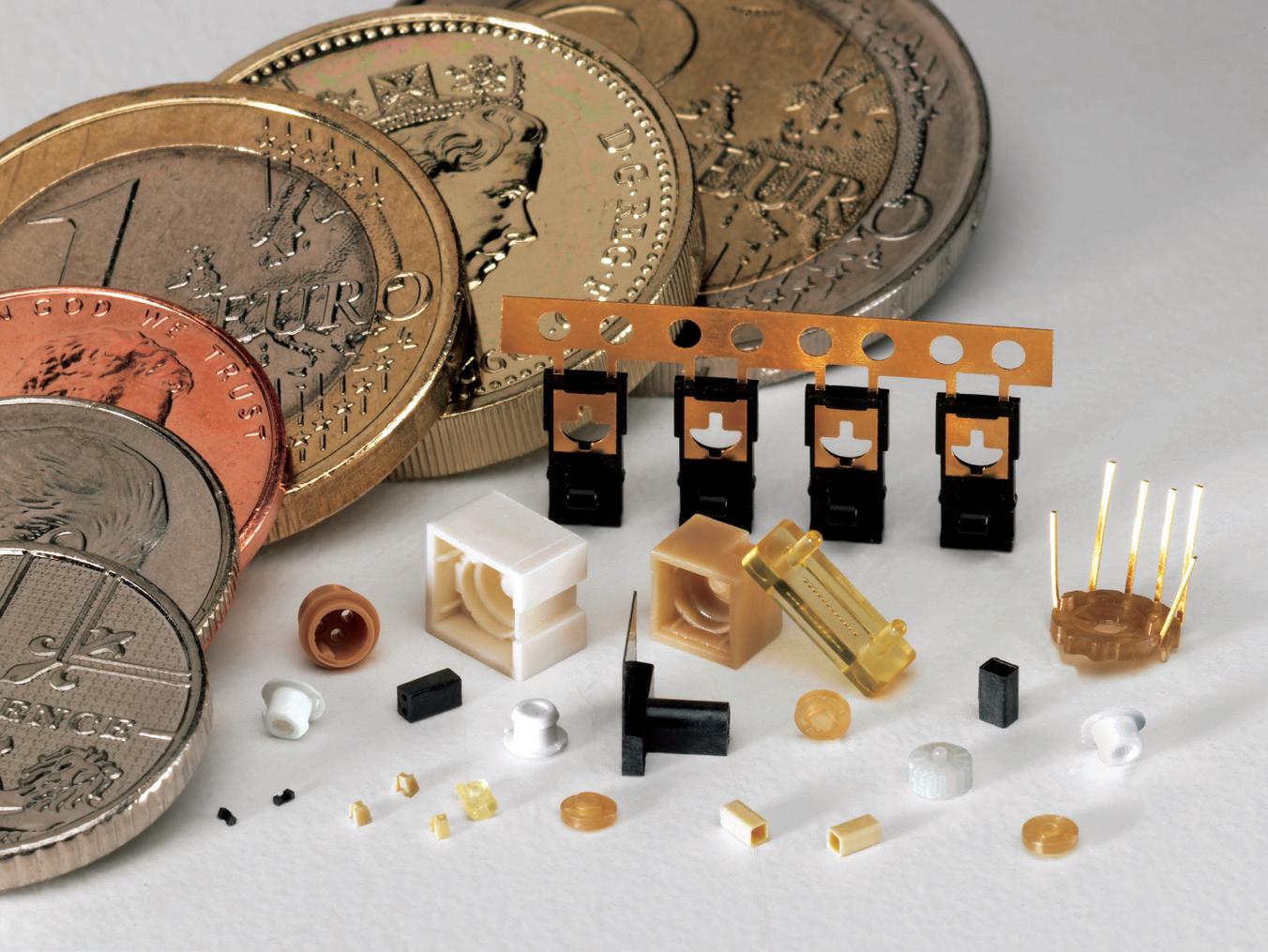
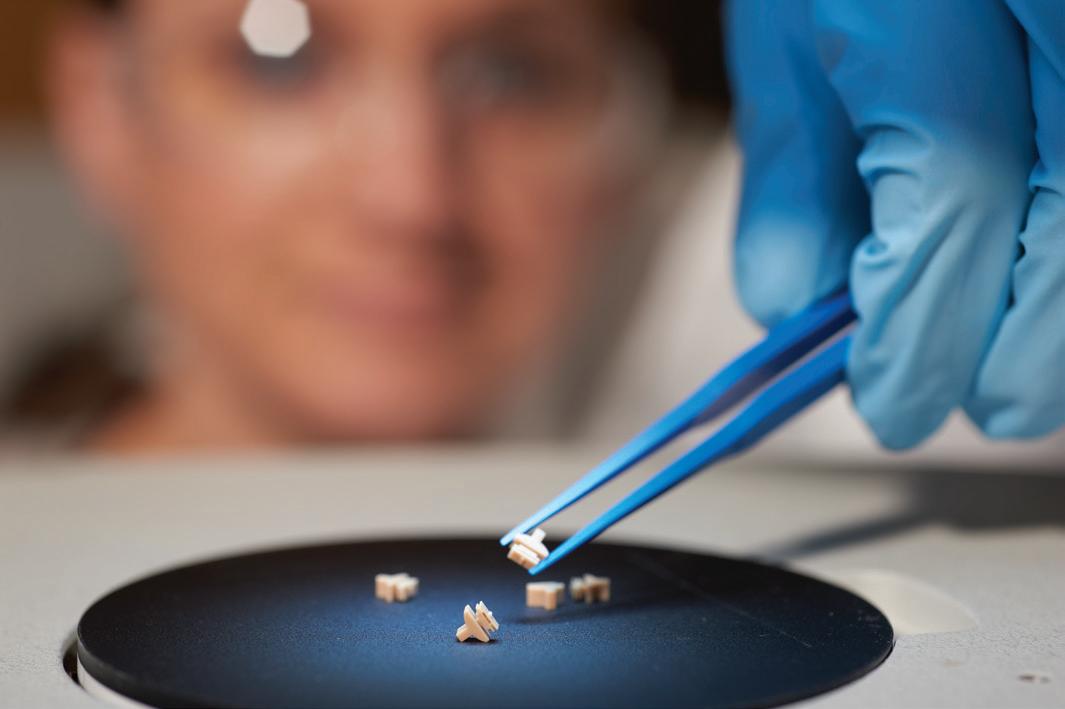
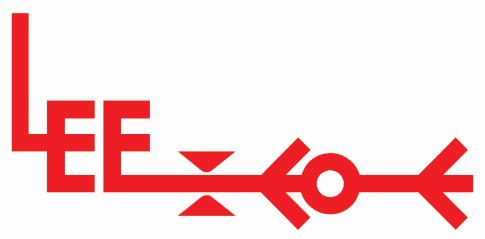

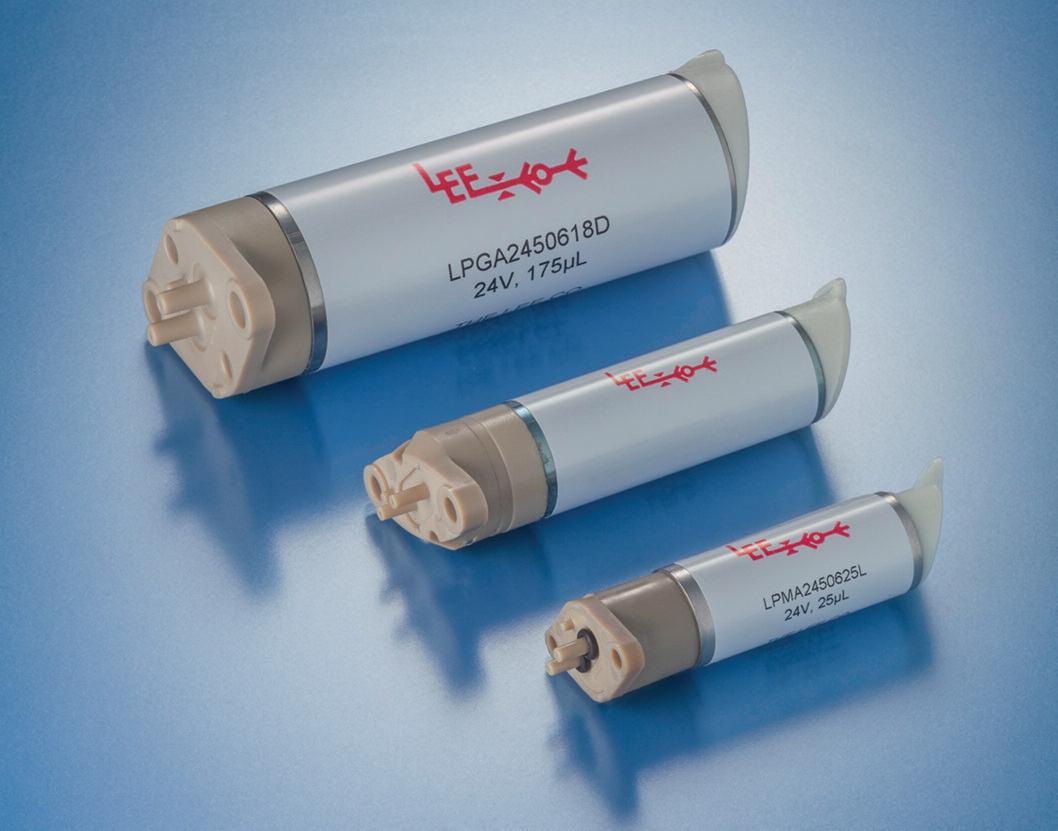
irst of all, I would like to start this issue by saying how nice it was to see everyone at this year’s running of Med-Tech Innovation Expo. You can read a couple of my highlights later on in this issue, but it was really nice to see the show floor buzzing, stages busy, and as well as everyone generating those all-important leads and connections, it was great to see a lot of people just having a nice time and enjoying themselves. And a particular thank you to those who came to the live episode of the MedTalk Podcast focused on regulation – it was my first time (ever) hosting a panel session and it was great to see it was standing room only
recovery.abybepandemic,andtheoutlookworriesWhilethroughout!thereareseveralabouttheeconomicformanyindustriesatmomentashighinflationenergycostsfollowsthemedtechseemstoanindustrytakingthebullthehornsandbecomingfocalpointforeconomic
It’s also a reminder that in a world where we have adopted to video calls and the like – and they most certainly have their place – there is nothing quite like face-to-face interaction and getting to hold and play with new products and demonstrations. In the same vein, I’m keen to get back on the road and not just meet you at exhibitions but see a lot more of what you’ve got to offer. My colleagues and I are eager to fill our diaries and make a visit to where you are based and if you have something that you would like to show us, then by all means get in touch.
F [ On the road again from The editor 5
The Med-Tech Innovation Roadshow has already begun. It was a pleasure to head to Derby and visit Shawpak who hosted a Shawmed exhibition. As well as meeting representatives from Sterimed, Amaco and SP Automation & Robotics, it was great to see behind the scenes at Shawpak at Riverside Medical. You will be able to see a write-up on the Med-Tech Innovation News website very soon. I’ve also recently had the pleasure of visiting Circular1Health –a massive success story from the pandemic whose ideas certainly got me thinking as they went beyond the bread and butter of innovation. This is a bid to find out more about what makes companies tick, what exciting products and innovations they have in the pipeline, and really demonstrate just how the pandemic might have changed the way you operate. A lot can happen in a few years, even more can happen when there have been massive changes that have caused a public health crisis – where we saw medtech at the front and centre of the response to support the front-line. Essentially, we want to hear from you, and we want to see a lot more from you. We’re open to any invitation to come and see what you have got to offer – and, of course, how we can help you get the most out of what you’re offering.
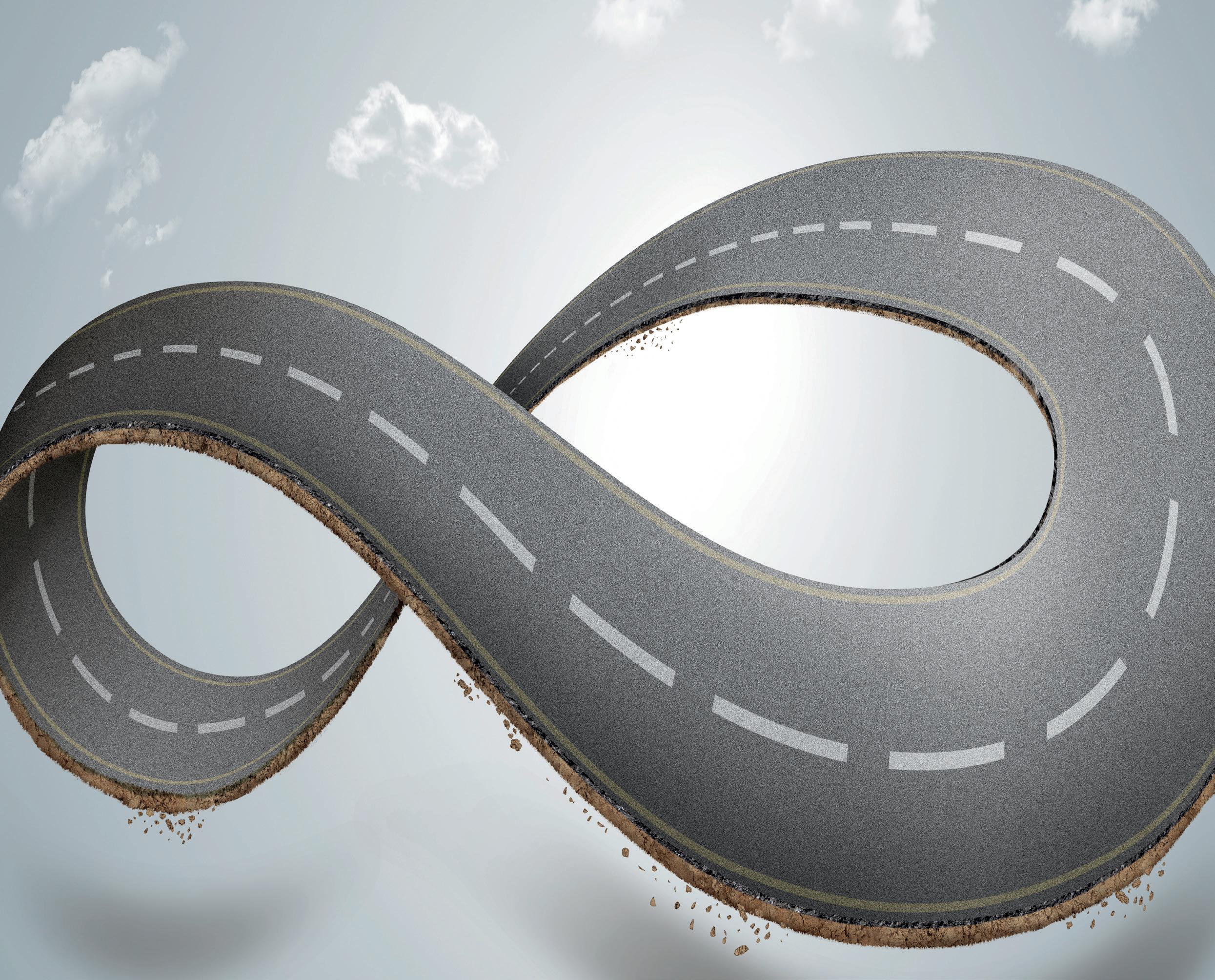
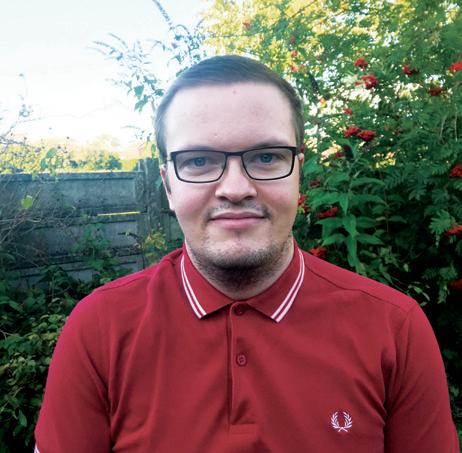
Making medtech 6
G anymed Robotics, a developer of computer vision software and robotics technologies for orthopaedic surgeons, has raised €21 million in its Series B funding. The funding will be used to:
• Accelerate regulatory and marketing developments across geographies;
• Finalise the arthroplastyroboticdevelopmentindustrialofitssurgicalassistantforknee(TKA);
C anon Medical Systems UK has announced a health and wellbeing collaboration with Sheffield City Council, Sheffield Olympic Legacy Park, BBraun Sheffield Sharks basketball franchise, PCA Ltd and The LivingCare Group. The new ‘Park Community Arena’ is anticipated to open in 2023 as the UK’s first affordable carbon net-zero built sports, healthcare and community arena featuring an integrated Medical Diagnostic Centre. Based at the heart of the Sheffield Olympic Legacy Park, the sustainably built arena will offer a flexible sporting facility, featuring three fullsize basketball courts, and is designed to hold 2,500 spectators. It will be the new home for the Sheffield Sharks and the Sheffield Hatters (women) professional basketball teams, and the arena will be available to wider sporting, education, and community organisations. To the north end of the arena, Canon Medical will open a Medical Diagnostic Centre to boost access to health screening and disease prevention. This is in synergy with national health strategies to create ‘one-stop-shops’ for healthcare checks, scans and tests outside the traditional hospital environment to overcome COVID-19 pandemic backlogs, improve earlier diagnosis and contribute to NHS carbon net-zero ambitions by reducing patient journeys. The Medical Diagnostic Centre will feature Canon Medical imaging systems including AI-assisted CT and MRI, diagnostic ultrasound, digital X-ray and include consulting rooms, a minor surgery operating theatre and an Endoscopy suite. Bringing all these modalities together will be Canon Medical’s healthcare information technology augmented with machine learning and AI to improve productivity and accuracy of Thediagnosis.Medical Diagnostic Centre will provide the region’s first specialist Sports Diagnostic Imaging Centre that will translate elite-level health, injury, and rehabilitation learnings to routine clinical practice. This will enable early detection, prevention and faster rehabilitation for sports injury and illness, as well as provide pre-season medicals and sports injury services to professional, elite, semi-professional and committed athletes.
Software and robotics firm raises $21m in Series B round
• Diversify the innovation product pipeline. Since inception in 2018, Ganymed Robotics has experienced a rapid growth. In collaboration with clinicians, it has validated its algorithms and collected in vivo data via a 100-patient observational study, successfully completed functional prototype tests, initiated industrialisation of its first device dedicated to TKA through strategic partnerships manufacturerswithand secured a robust patent portfolio.
Sophie Cahen, co-founder and CEO of Ganymed Robotics, said: “The support of this high-profile group of investors, specialised in innovation and healthcare is a strong endorsement of the work accomplished and of our vision for the future of orthopaedic surgery. We are eager to enter this new phase of growth. With our unique robotwith-eyes platform, we are committed to providing all surgeons and care centres, large and small, with an easyto-use and cost-effective solution that will radically improve patient outcome, surgeon experience and overall efficiency of joint replacement interventions.”
Tánaiste and IDA Ireland mark 40 years of Medtronic in Ireland
Our sites in Ireland have played a significant role in Medtronic’s evolution from medical device manufacturer to a global leader in healthcare technology. “These roles will support the development of products and services in the coronary artery, heart valve and peripheral vascular disease, heart arrhythmia and pacing, hypertension and spinal injury areas. There will also be roles in the Chemical Analysis and Biocompatibility fields supporting a new Global Laboratory Services team.”
• Support andexpansionGanymed’sinFranceintheUnitedStates;
teams up with She eld authorities for Park Community Area
I DA Ireland, together with Tánaiste and minister for enterprise, trade and employment, Leo Varadkar attended a 40-year celebration at Medtronic’s Parkmore facility in Galway where 200 Research & Development roles were announced.Thenewly announced jobs include growth in new product development and a new Global Laboratory Services team in Galway. In what is part of a $30 million capital investment by Medtronic, recruitment is underway with just over half of the roles filled to date. The projects are supported by the Government through IDATheIreland.Tánaiste said: “Medtronic came to Ireland in 1982 with plans to manufacture a small number of cardiovascular devices. Forty years later, the company now employs more than 4,000 people across five sites in Galway, Athlone and Dublin and with a further 200 new jobs announced for Galway, just over 50% of which are already filled. That is remarkable growth. Medtronic Ireland has been a leading light in Ireland’s vibrant medtech sector and this latest growth underlines the company’s dedication to our country. I’d like to thank the Medtronic’s team for their continued commitment to Ireland and wish them all the best for the next fortySinceyears.”1982 Medtronic has expanded its manufacturing presence to also include new product development, sustaining and process engineering, customer innovation, global shared services, and locates its corporate headquarters in Dublin.Gerard Kilcommins, country director, Campus Ireland at Medtronic said: “The 40-year anniversary is an important milestone to celebrate in Medtronic’s Irish story.
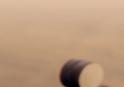
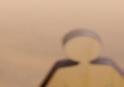
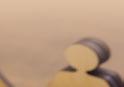
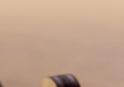
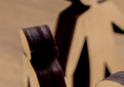
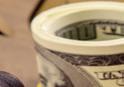
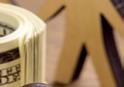
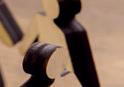
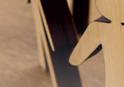
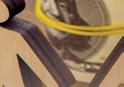
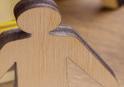
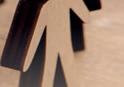
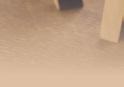
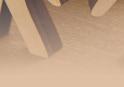
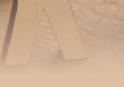
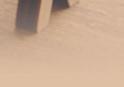
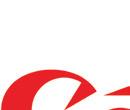

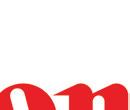
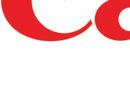
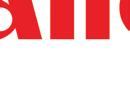
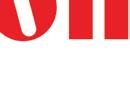

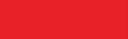
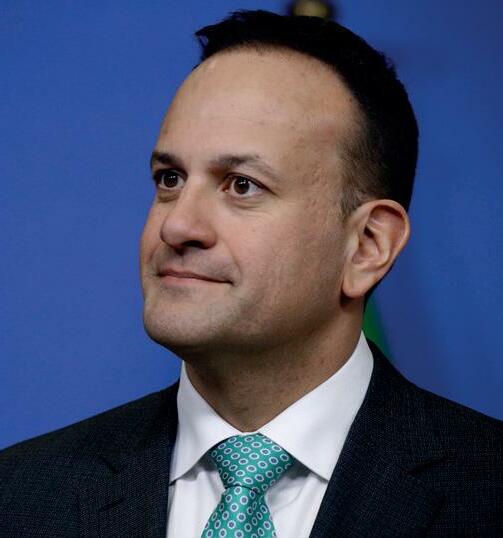
Matthew Rich, general manager of PolarSeal, said there were “fl oods of leads” during the fi rst morning of the show and explained the critical role that Med-Tech Innovation Expo has for the industry, as well as for the company. Med-Tech Innovation Expo is really critical for the industry as it brings so many people together in a networking way, and there’s so many diff erent companies that can be bought together, so we’ve had people coming to us asking for a particular thing, and we can pull in other companies that are here at the MedTech show to make that complete device. For us, it’s critical that we’re here to be in front of our customers and potential customers, people get to see the name.”
Expo News
Our first day at the show was the best we’ve had in terms of number of enquiries. At any show. And we’re looking forward to coming back next year.
Andy Tibbs, CEO of Boddingtons Plastics was especially impressed saying: “Our first day at the show was the best we’ve had in terms of number of enquiries. At any show. And we’re looking forward to coming back next year.”
Leads from start to finish
The continued partnership between Med-Tech Innovation Expo and Medilink UK delivered two highlights to the show: the conference and the awards ceremony on the evening of day one. The awards saw the celebration of outstanding business internationalachievements,successes and innovative breakthroughs made across the life sciences and healthcare technology sectors in the past year.
The international medical design and manufacturing community gathered on the 8-9th June at the NEC, Birmingham, for two full days of innovation, learning and theirorganisationsOvercommerce.100cutting-edgeshowcasedlatestdevelopments at the event. This included more than 40 international exhibitors from countries including China, France, Germany, Italy, Monaco, Mauritius, Netherlands, Pakistan, South Korea, Sweden, Switzerland, Thailand, and the United States, giving the event a real international feel.
Exhibitors to the 2022 Med-Tech Innovation Expo hailed it a success after those in the medical device manufacturing supply chain came together to do business in Birmingham.
After a successful 2022, a rush of bookings has already begun for next year’s edition of Med-Tech Innovation Expo. OxDevice Ltd, Guardtech Group, ChorleyBioInteractions,Consultingand Xi Engineering are all among those who’ve secured their place for 7-8th June 2023.
The Med-Tech Innovation Conference, in association with Medilink UK, presented a world-class, CPD-accredited programme offering thought leadership from the sector’s biggest names from Microsoft, Roche Diagnostics, Department for International Trade, Deloitte, NIHR and more.
Roaring international success at Med-Tech Innovation Expo 2022
The two-day event saw thousands of enthusiastic and engaged visitors congregate at the NEC to witness the latest industry developments, network with colleagues, and build longterm business partnerships. Highlights included a CPD accredited programmeconferencewithmore than 30 inspiring presentations covering the use of technologies, machines, material, and case studies showcasing technology in action. The Introducing HealthTech Stage saw industry experts share tips on how to bring a device to market while maintaining regulatory compliance and overcoming challenges. This stage, sponsored by Hessen Trade and Invest, covered every aspect of the medical device supply chain, and provided something for everyone.
7
Rush begins for 2023
Arjun Luthra, commercial director at BioInteractions said: “We like to exhibit at as many medical shows as possible but really the most impactful ones. There are numerous ones to choose from and we want to choose the most impactful not only for offering, but actually as a brand. After a successful show in 2021, Shawpak returned in 2022 with an expanded space, and have also secured their spot for next Lucieyear.Markgraf, sales administrator, said: “Shawpak exhibited again at Med-Tech Innovation but this time with a bigger stand. We opted for the bigger space so we could showcase two of our medical packaging machinery. We had a busy three days and captured a lot of new contacts. The quality leads and successful networking has given us confidence to rebook in 2023, with an even bigger stand!”
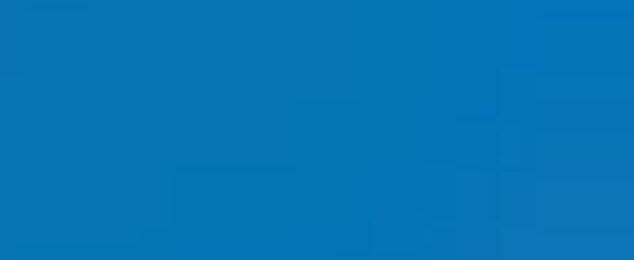
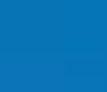

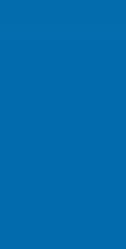
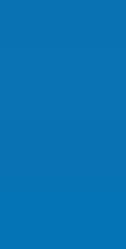
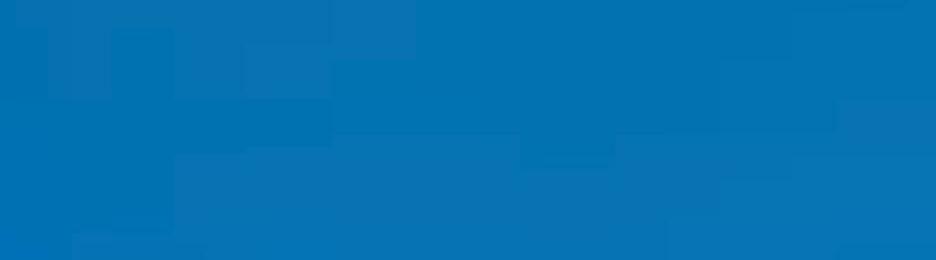
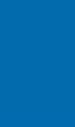
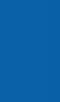
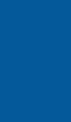
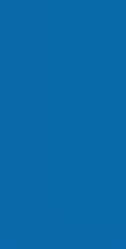

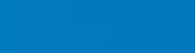
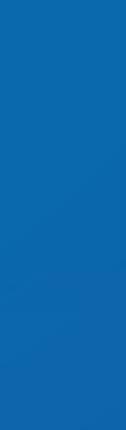
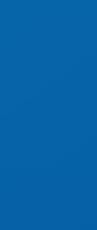
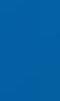

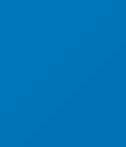
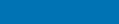












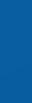


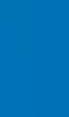

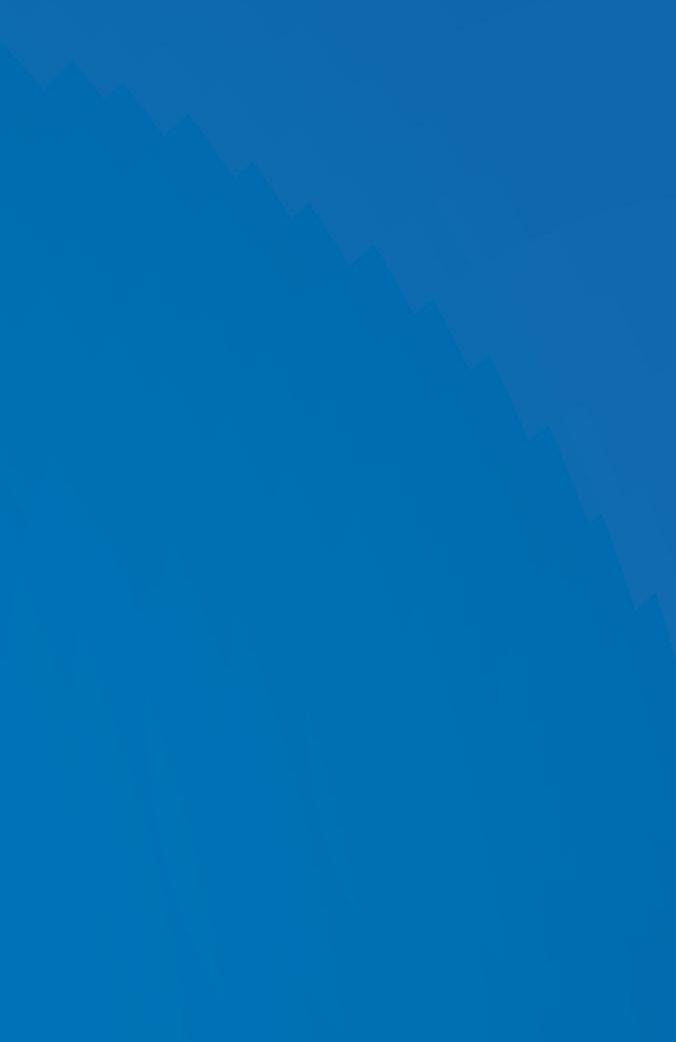
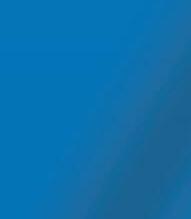

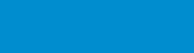

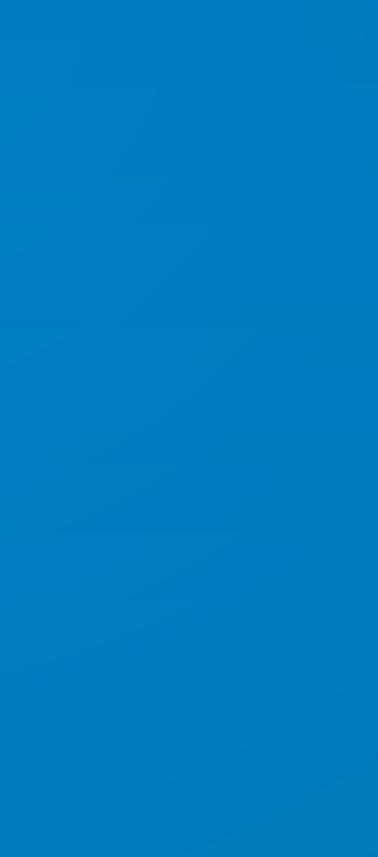
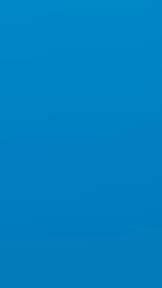
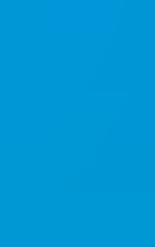



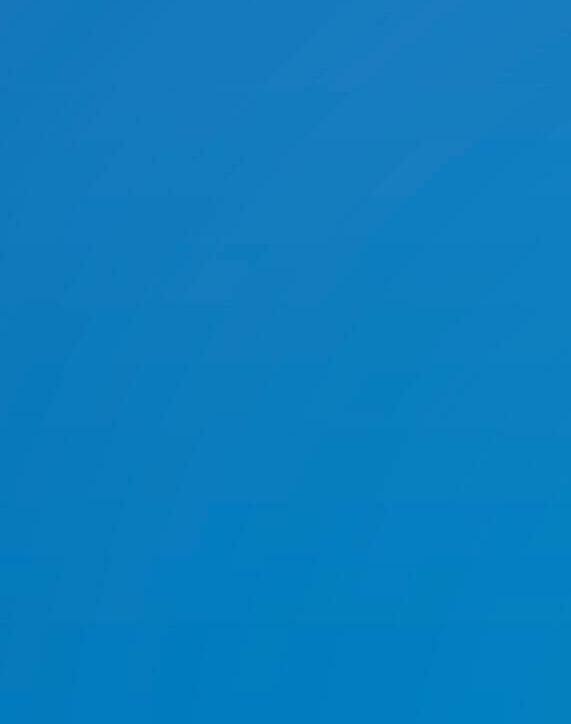
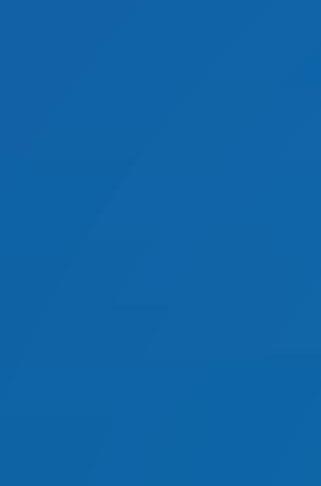
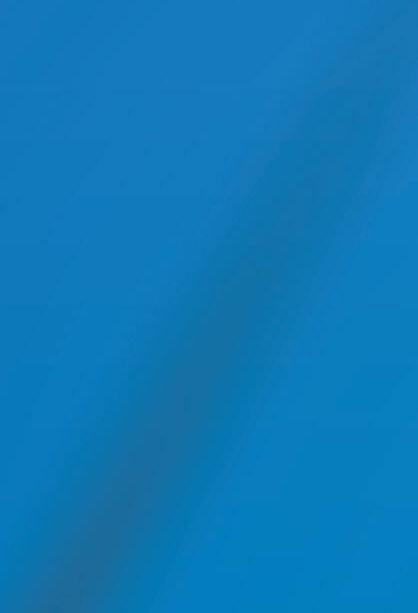
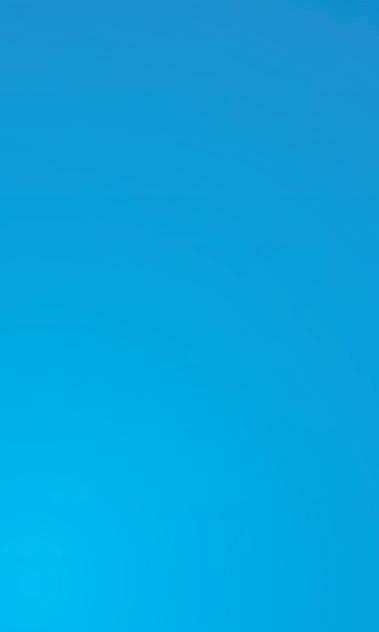
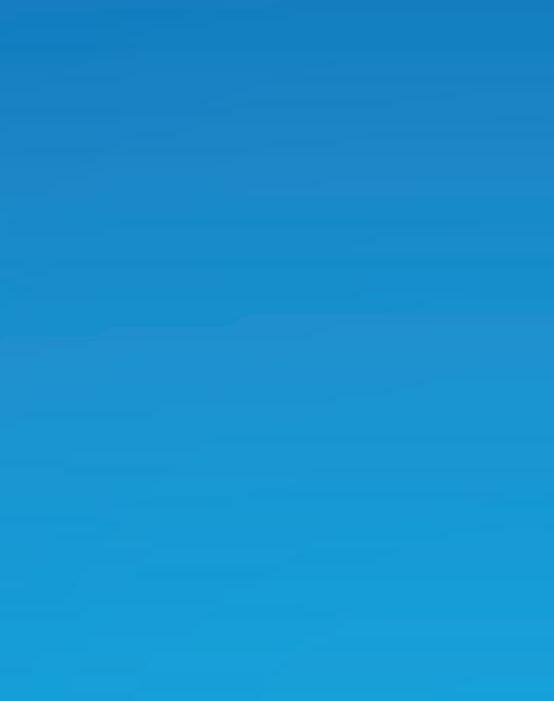
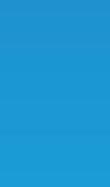
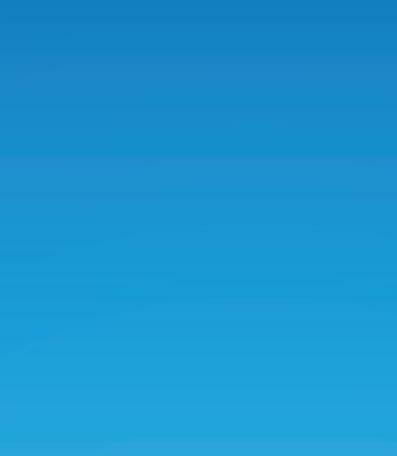
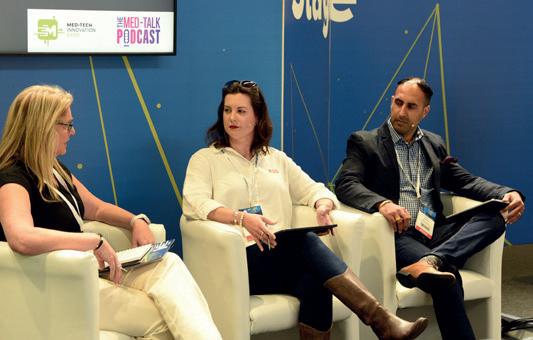
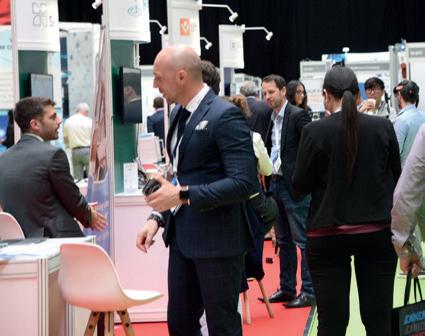
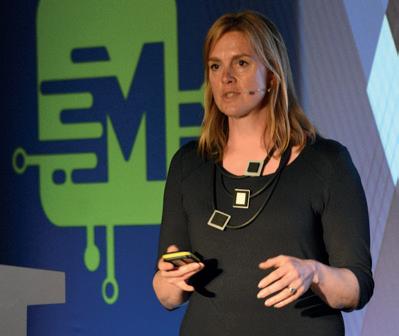











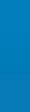

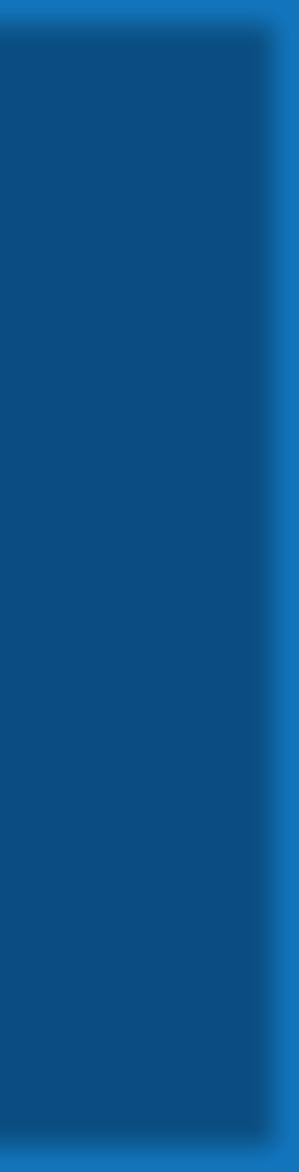




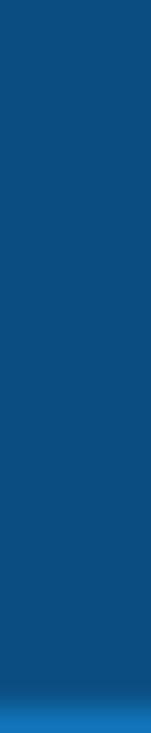
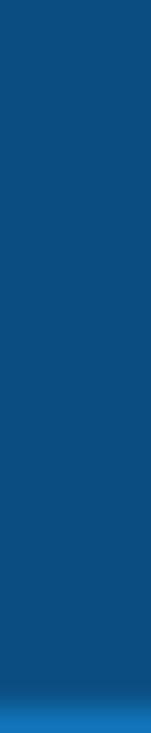
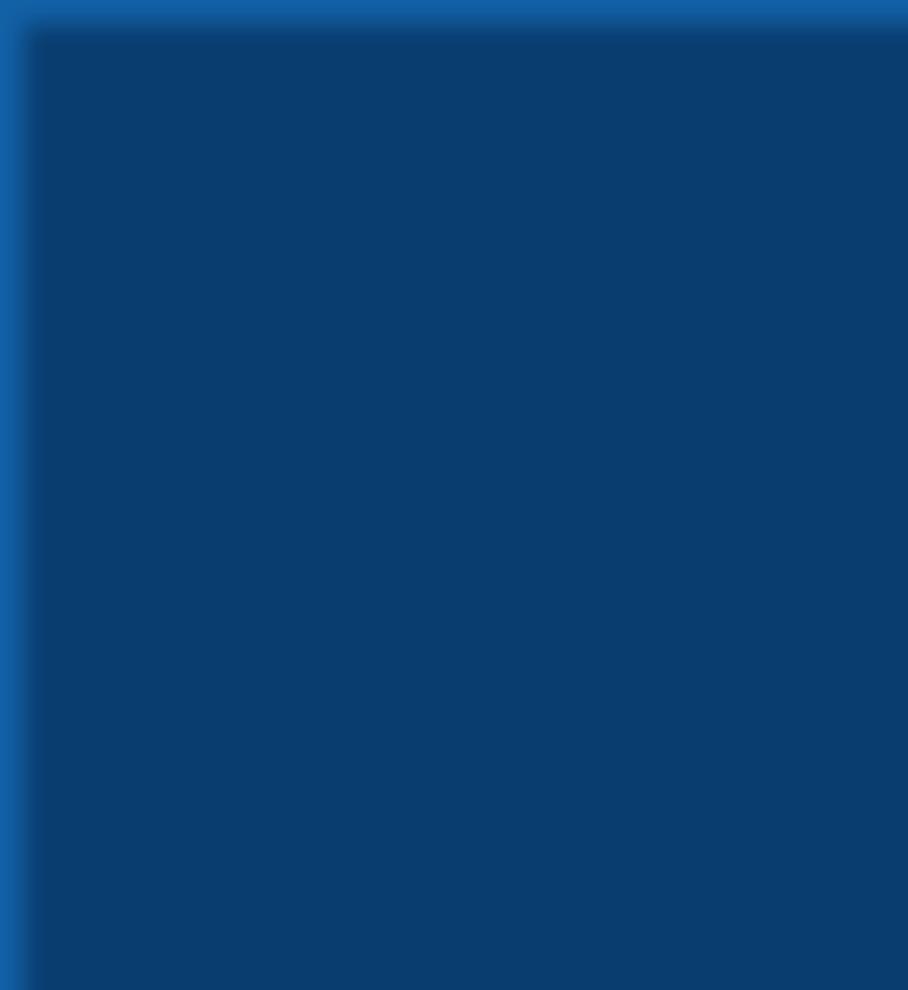
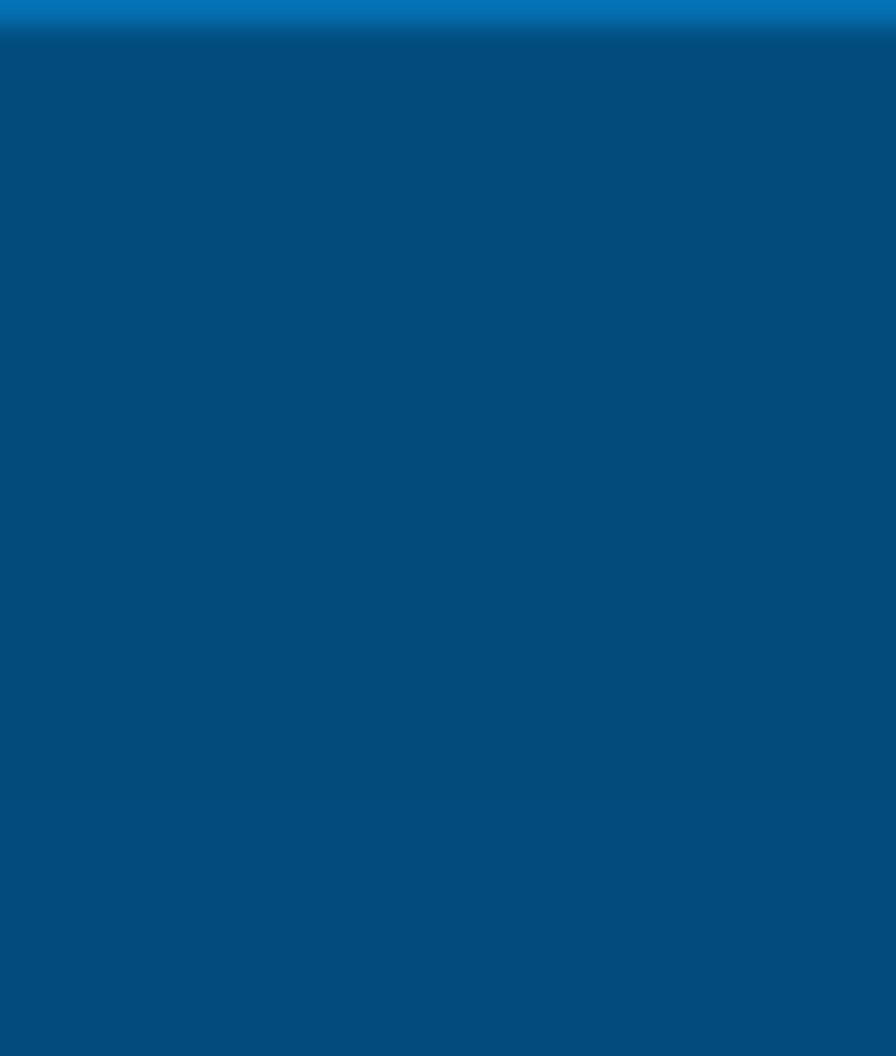
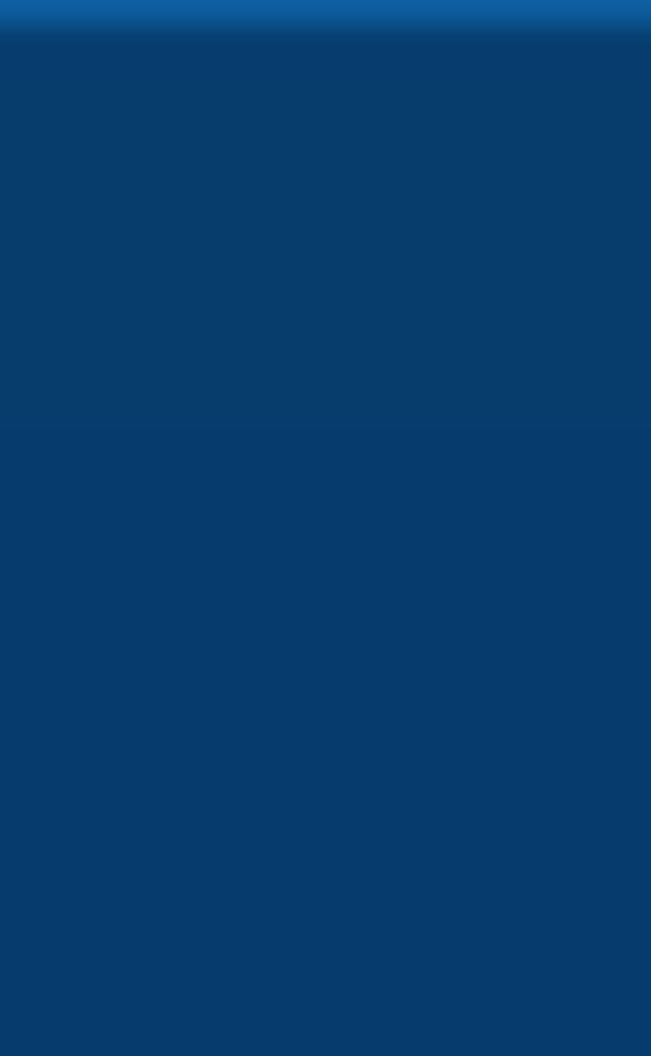
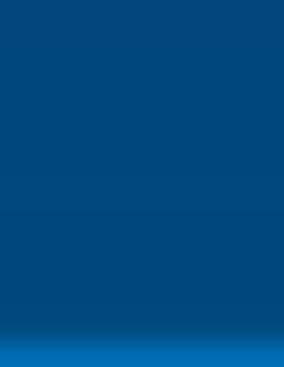
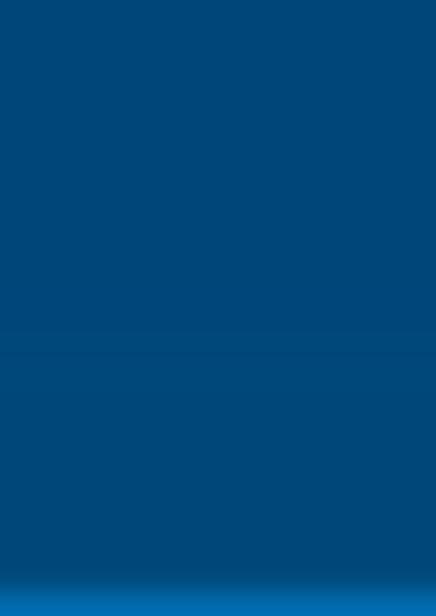
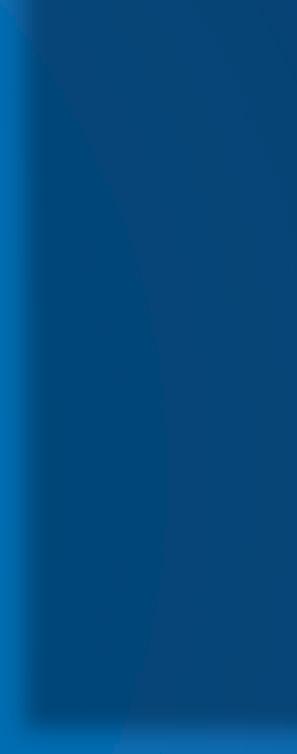
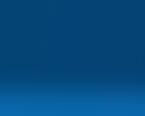
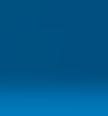

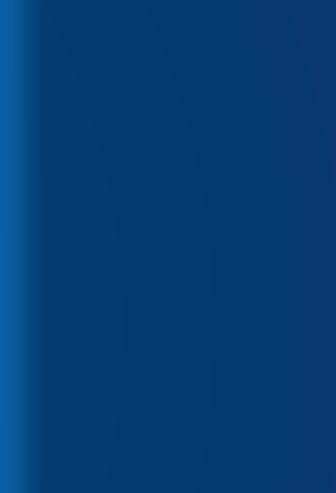

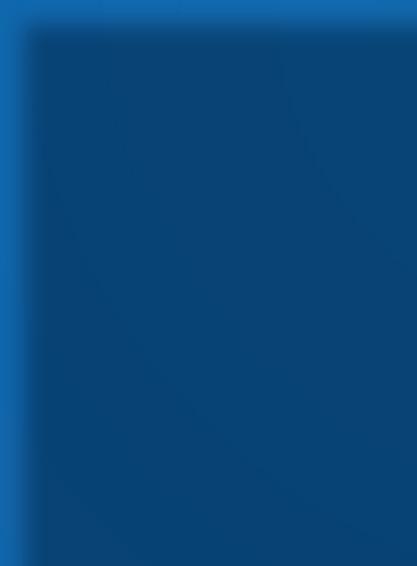
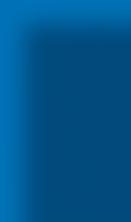
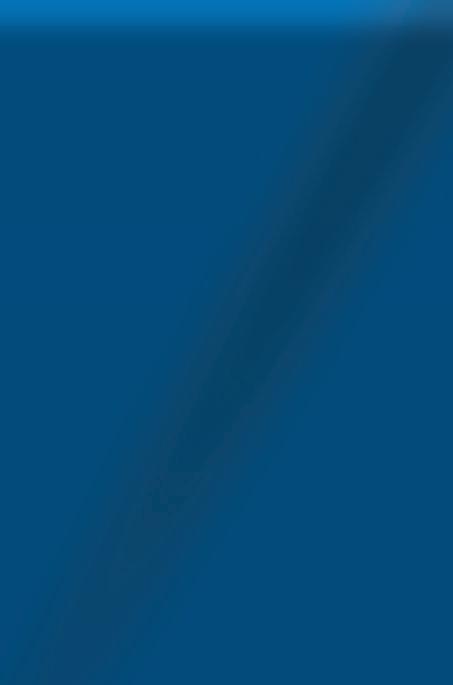
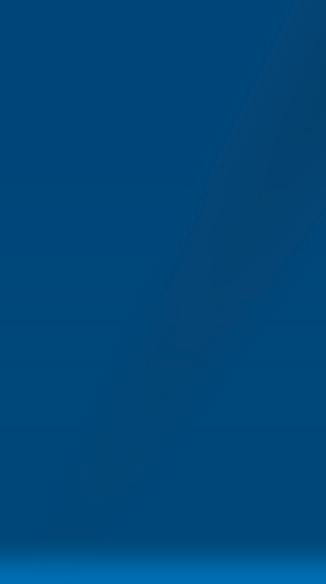

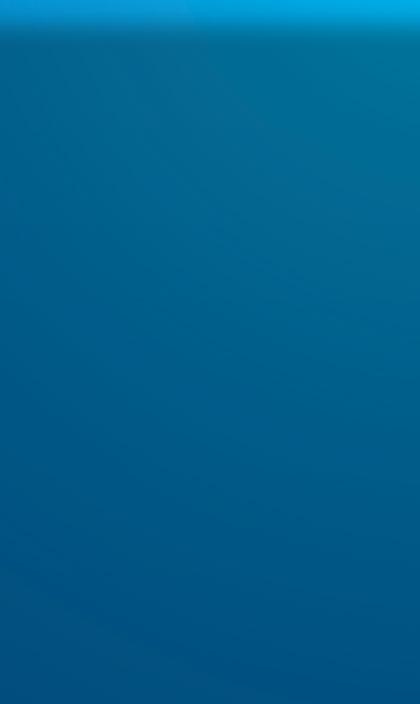
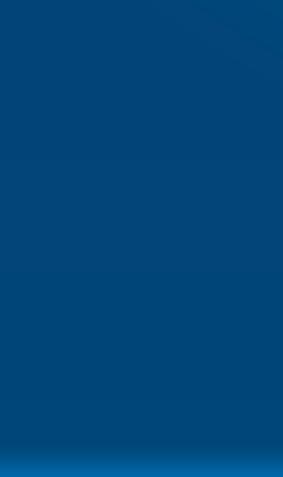
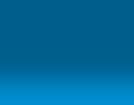

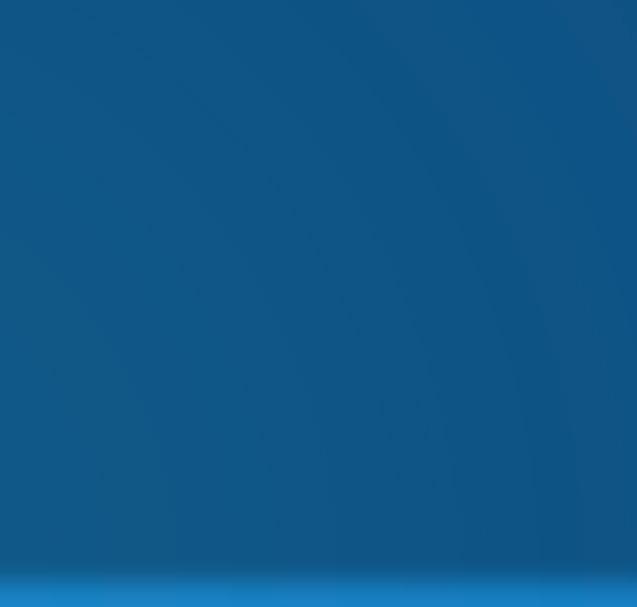
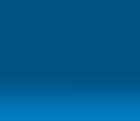



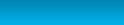





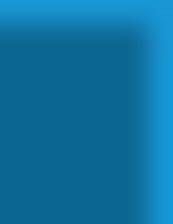
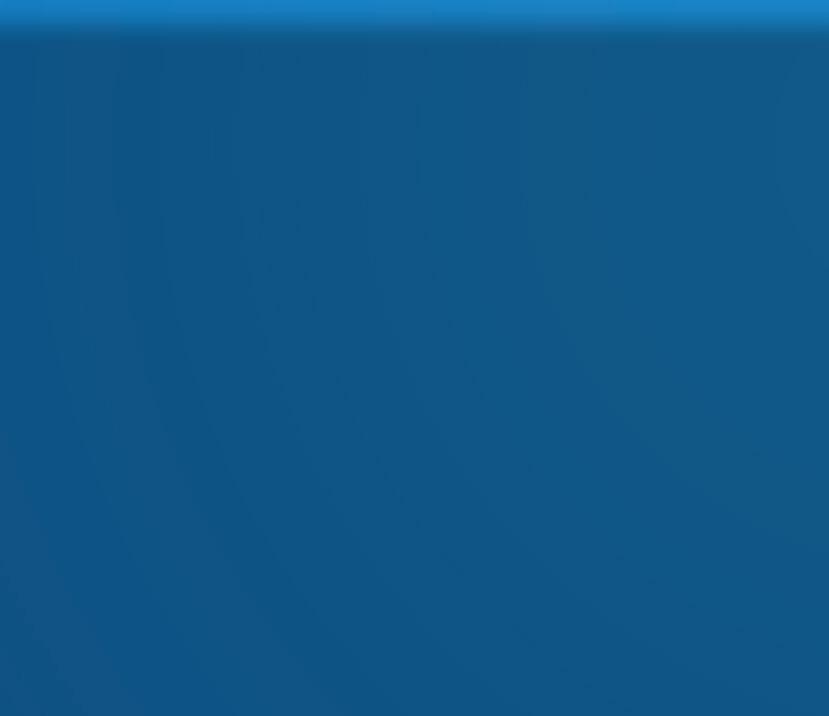








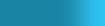
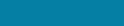






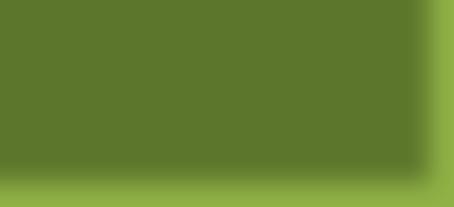
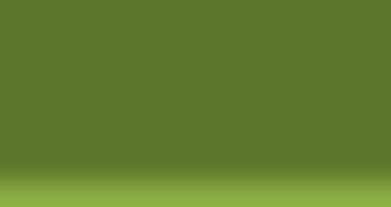

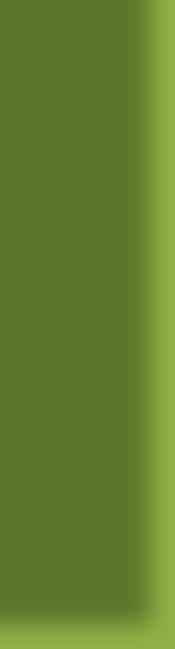
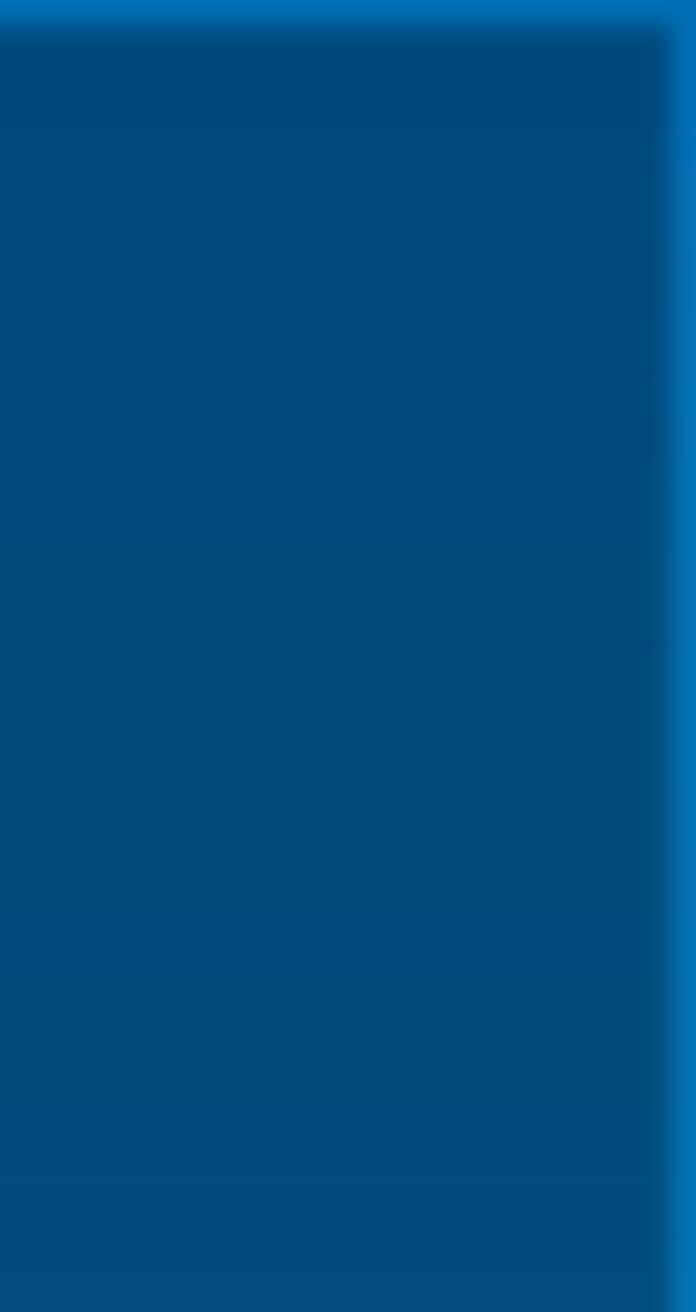


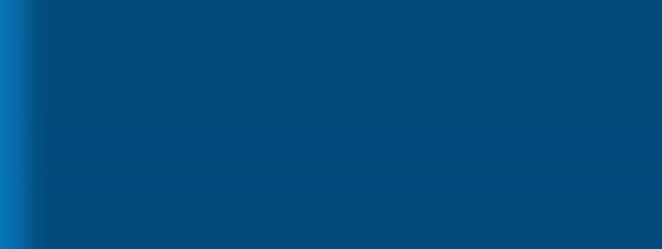
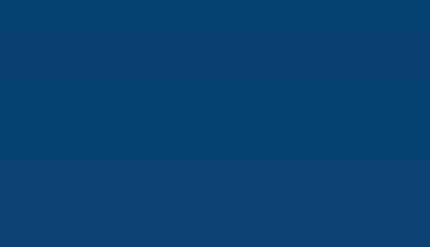
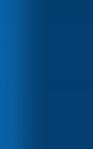
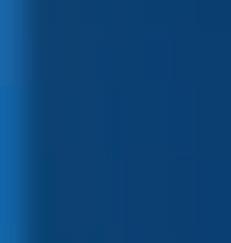
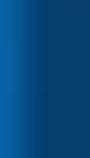
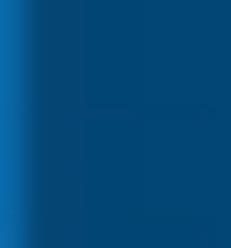
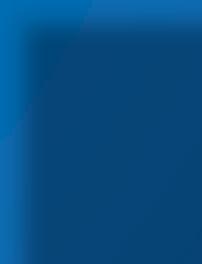
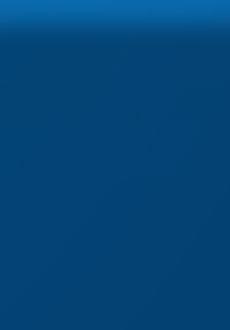
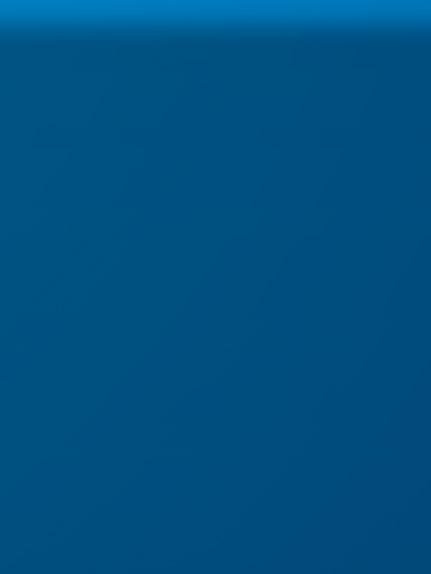
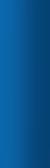
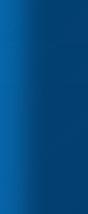
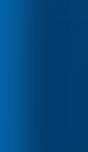
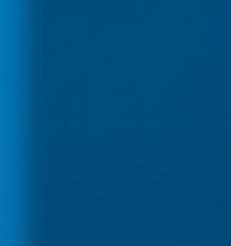









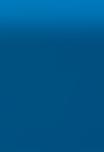
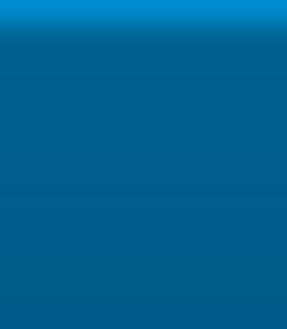

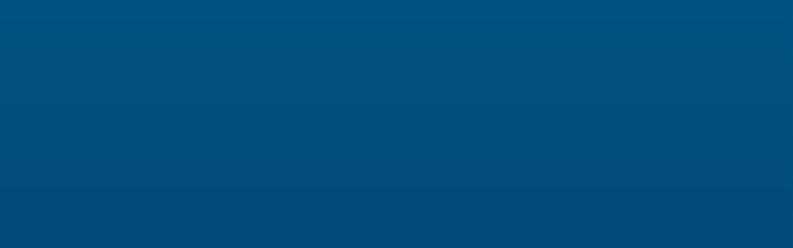
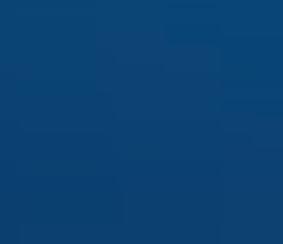
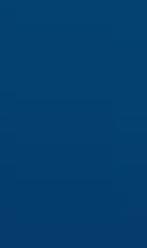
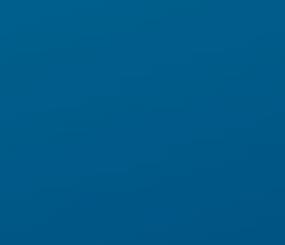
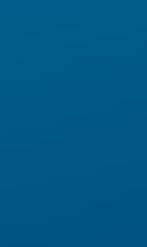

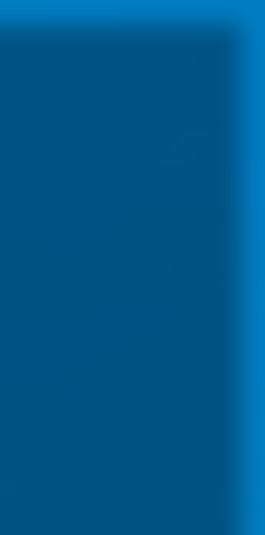
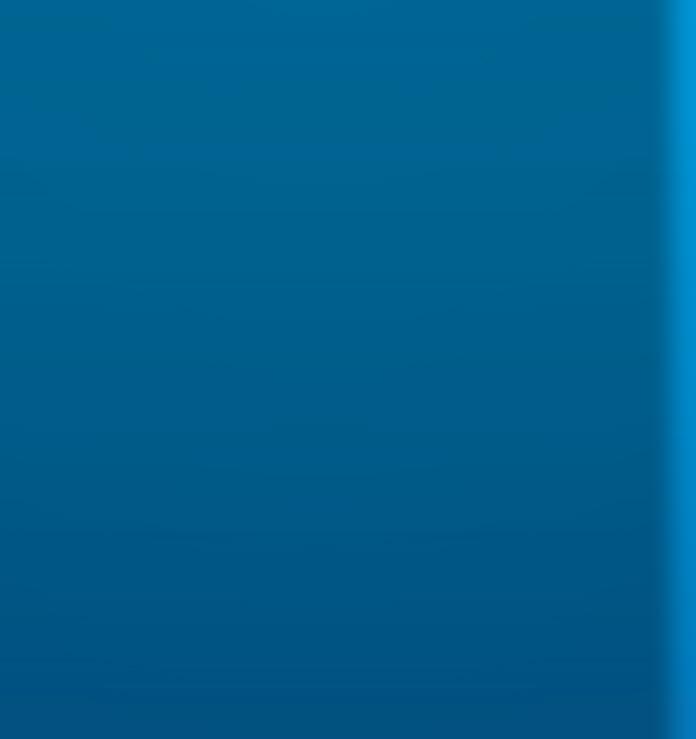
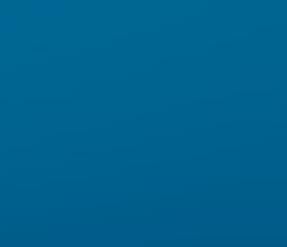
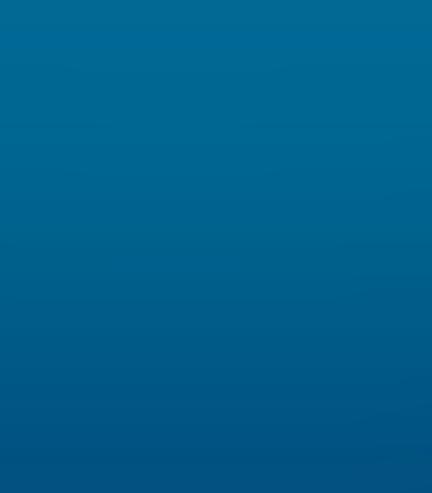
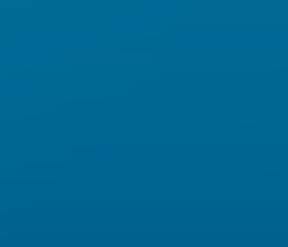
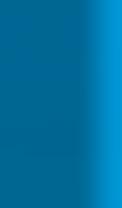






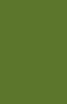
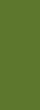


























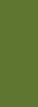



















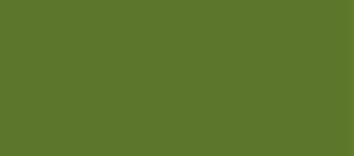
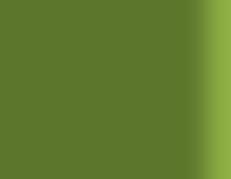

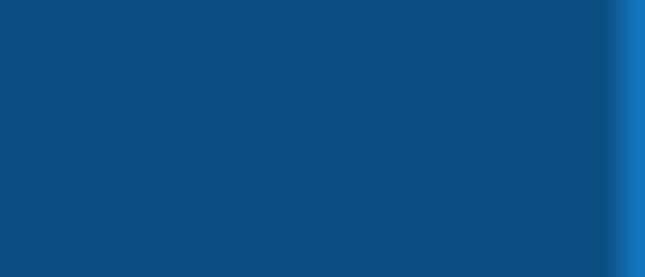
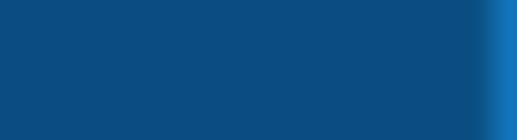
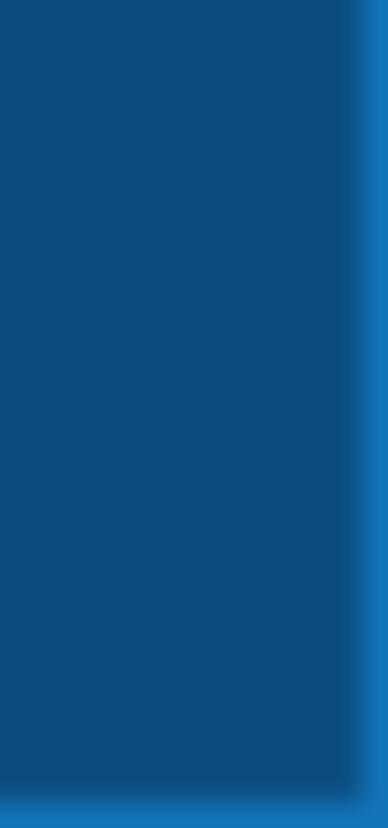
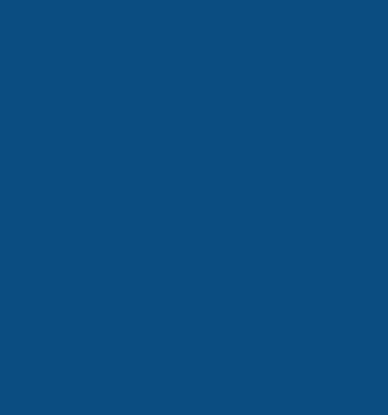

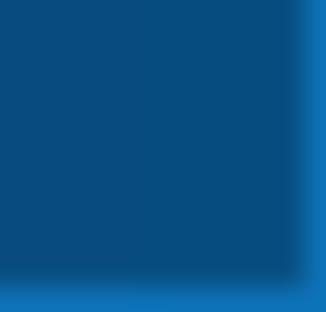



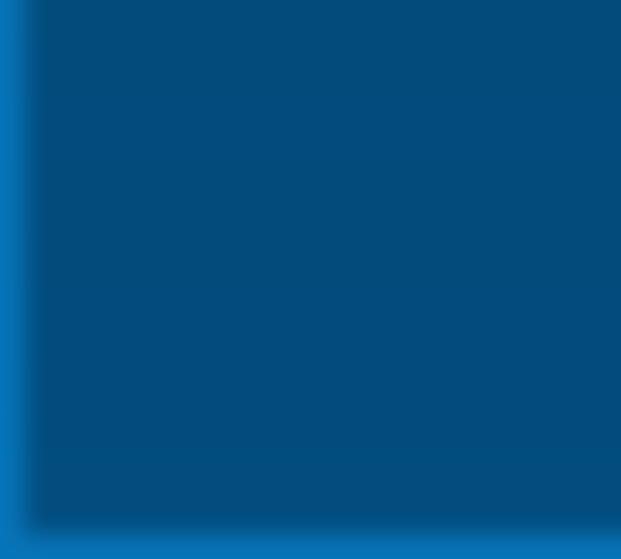
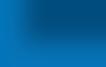
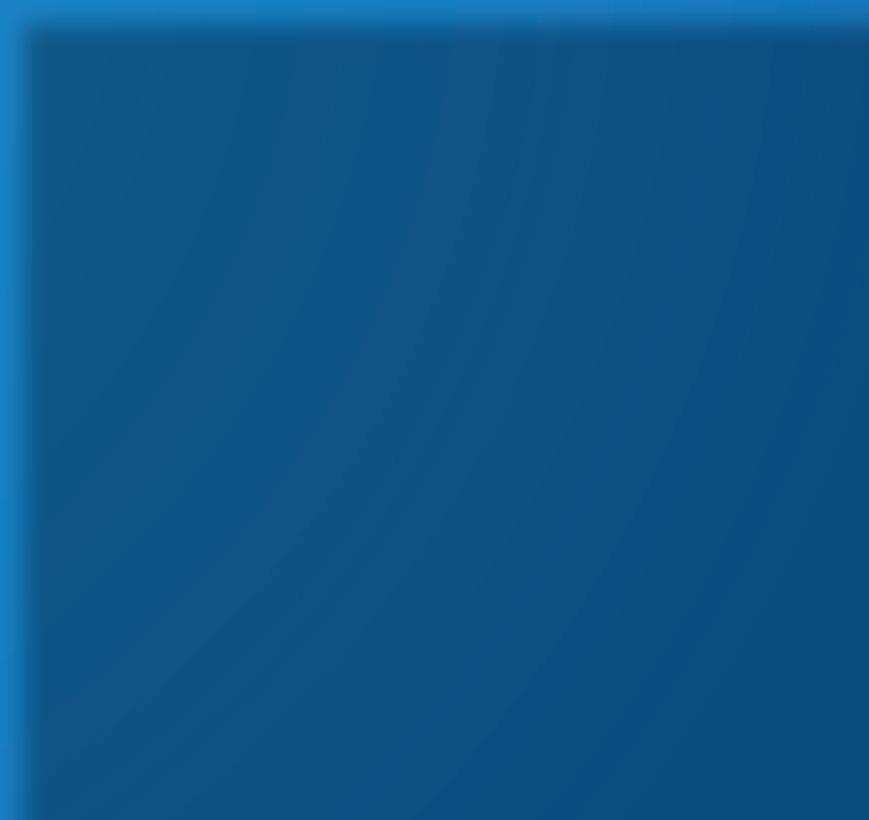
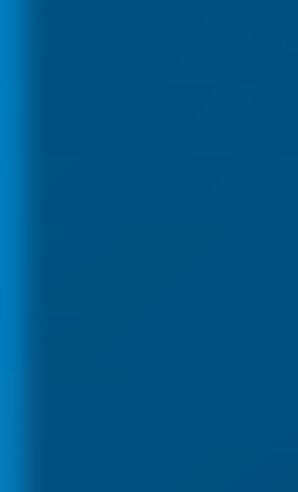











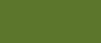


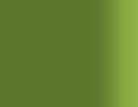


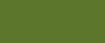
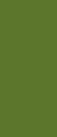






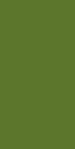

















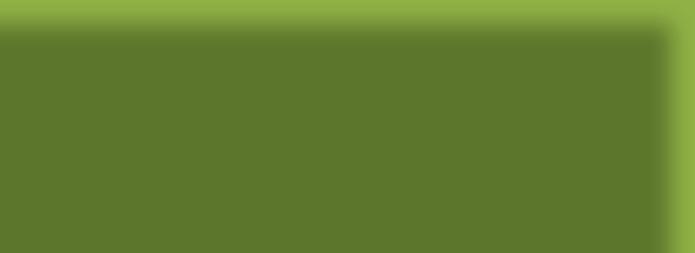
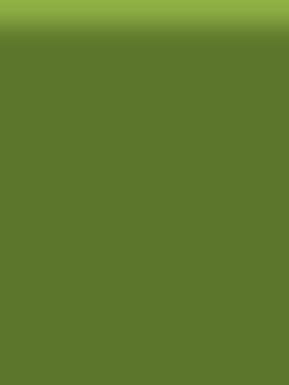
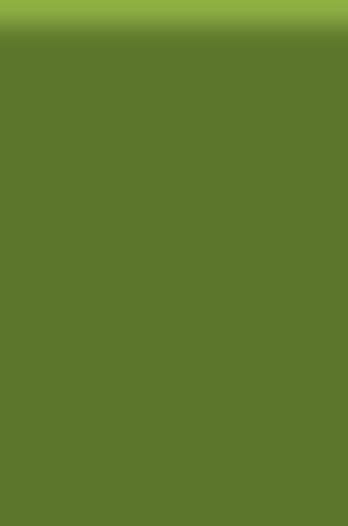
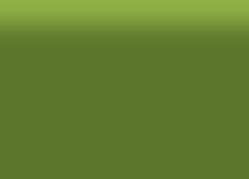
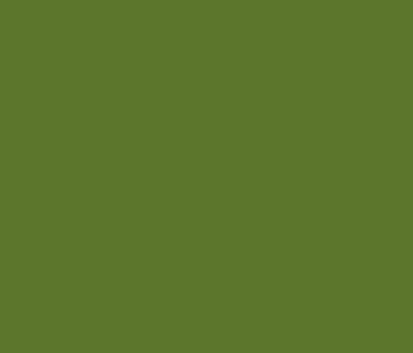

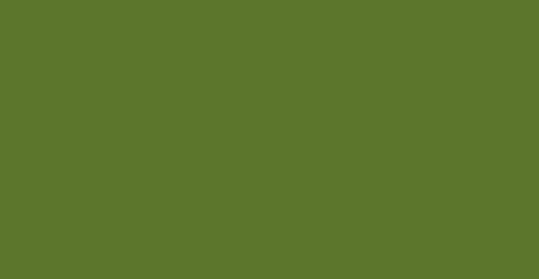
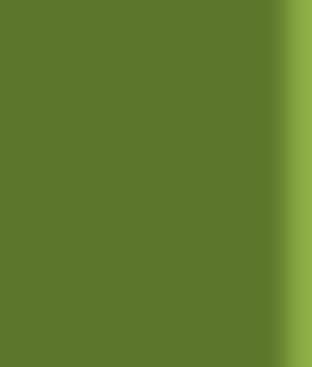



































































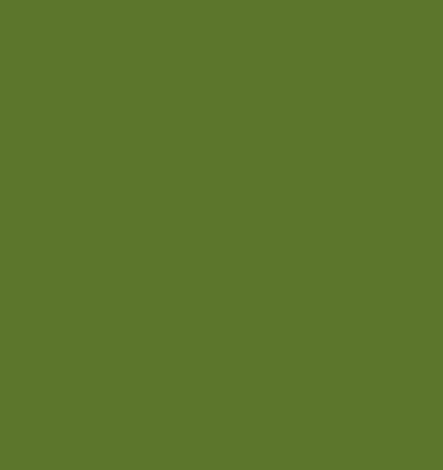
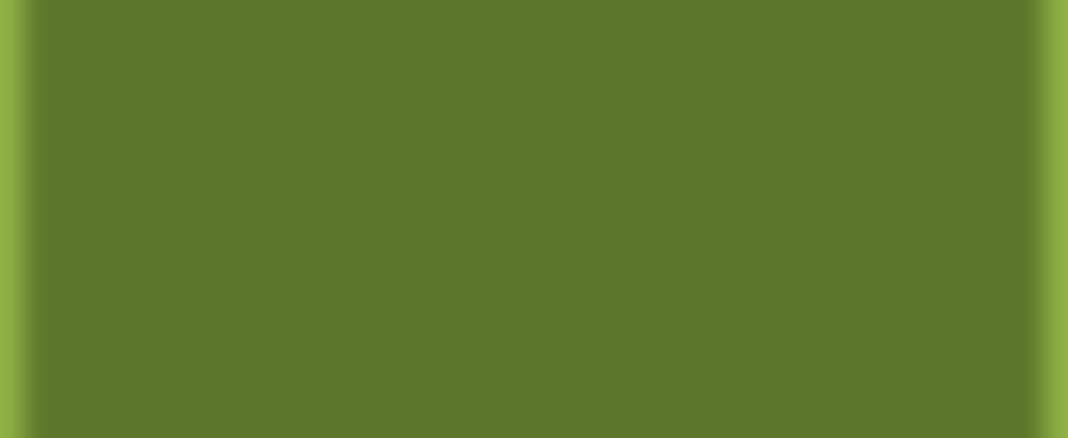
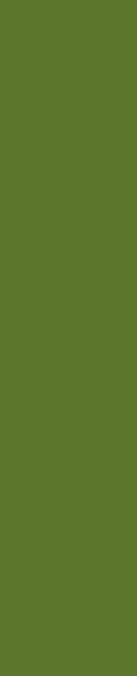
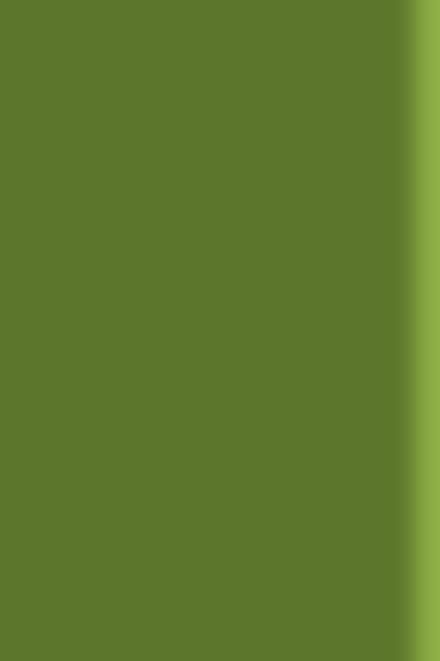


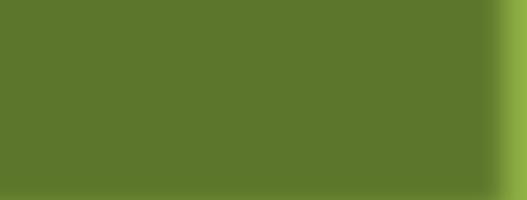

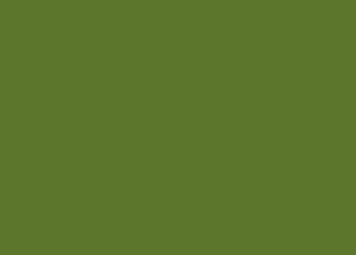
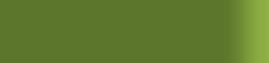
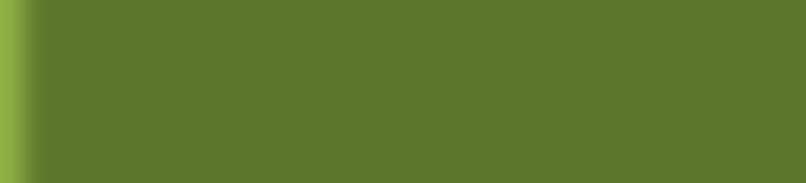
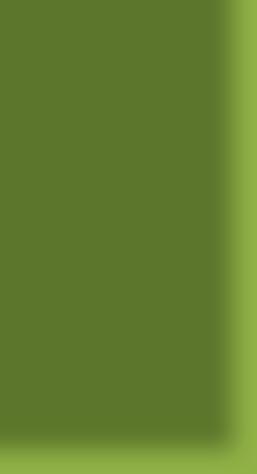

8 MEDILINK
Think about any promotional materials that you may need, such as leafl ets or brochures, and whether it may be worth translating these to the local language.
PLAN YOUR SPACE Your stand is your selling point –make sure it is easily accessible and clearly includes your brand assets and key messages that you want to convey.
Top tips for exhibiting at international exhibitions
Think about what specific information you would need about your leads and what’s the best way to gather it.
Over the years, the International team at Medilink UK have supported a huge range of healthcare and life sciences companies at some of the largest exhibitions and trade shows in the world. You can find out more at international@medilink.co.uk.support-and-exhibitions,www.medilink.co.uk/international-https://orvia
Melissa Erwin, senior international officer at Medilink UK, shares what exhibitors should do to make sure they get the most out of their presence at international events.
1 2 3 4 5 6 7 8
Different countries have different cultures and customs – it is important that you do your research and familiarise yourself with these prior to the show. Some of the best leads may come at the end, so never leave early – stay until the end of the event and make the most out of it – you have spent a lot of time, effort, and resources to be there!
GET ORGANISED Set measurable and realistic goals –what do you want to achieve through exhibiting? Estimating and calculating this may be quite difficult, so take your time. Once you tick if off, the next step is to book your place including for travel and accommodation. Medilink UK offer a range of services to help make your experience stress-free and costeffective, such as through working with a specialist travel and freight provider. When planning your exhibition, don’t forget to reach for professional support and advice from trade associations and advisors, such as from the Department for International Trade.
Think of the sizing of your products, promotional materials, and furniture to estimate what stand size you will need. You can seek advice from your pavilion organiser (such as Medilink UK) who will offer options based on your budget and goals from the outset.
ENGAGE Don’t assume that exhibiting simply means staying in front of your stand and handing out marketing brochures. It is your chance to network with a range of healthcare professionals from around the globe and showcase the best of your company, so be engaged and approachable. If there are multiple staff members, make sure you have a plan on how you will interact with visitors and who will be visiting other halls, so that you can maximise your team’s productivity.
I nternational exhibitions are a great way to showcase your medical products and services to a global audience and find out about the latest trends in the sector. However, there are some important aspects to consider before, during and after your participation, to ensure you get the highest return on your investment.
Check if there are any scanning devices or other convenient options offered by the organisers to streamline the process and make it as easy as possible.
CAPTURE AND FOLLOW UP ON YOUR LEADS
PROMOTE YOUR PRESENCE AT THE SHOW Spread the word about your participation, either via your social media channels, email signatures, website, or all of them. This way, people will have already recognised you, which will facilitate further Manynetworking.exhibitions now offer digital platforms to complement a physical show and encourage networking after the event, so consider utilising this online side to maximise your reach and brand awareness.
BOOK THE CORRECT STAND SIZE
Consider how you will follow up with your leads, including who will be responsible for this – it is important that you set goals and timelines in advance.
PICK THE RIGHT EVENT
With a huge variety of sector-specific healthcare events across the world, you need to decide which one is the most relevant to your business – and your audience. Are you planning to target buyers and distributors in the Middle East? Or maybe you’re keen to network with healthcare professionals and government representatives from South Africa? Make sure that the exhibition you choose is also the most reputable or biggest in the region, as these tend to attract the largest numbers of visitors.
REFLECT Planning your presence for exhibitions requires time and effort – after the event, make sure to evaluate this process. Did you meet your goals? Was there something that could have been improved? You will learn from this experience and be able to make your next participation even more costeffective and worthwhile.
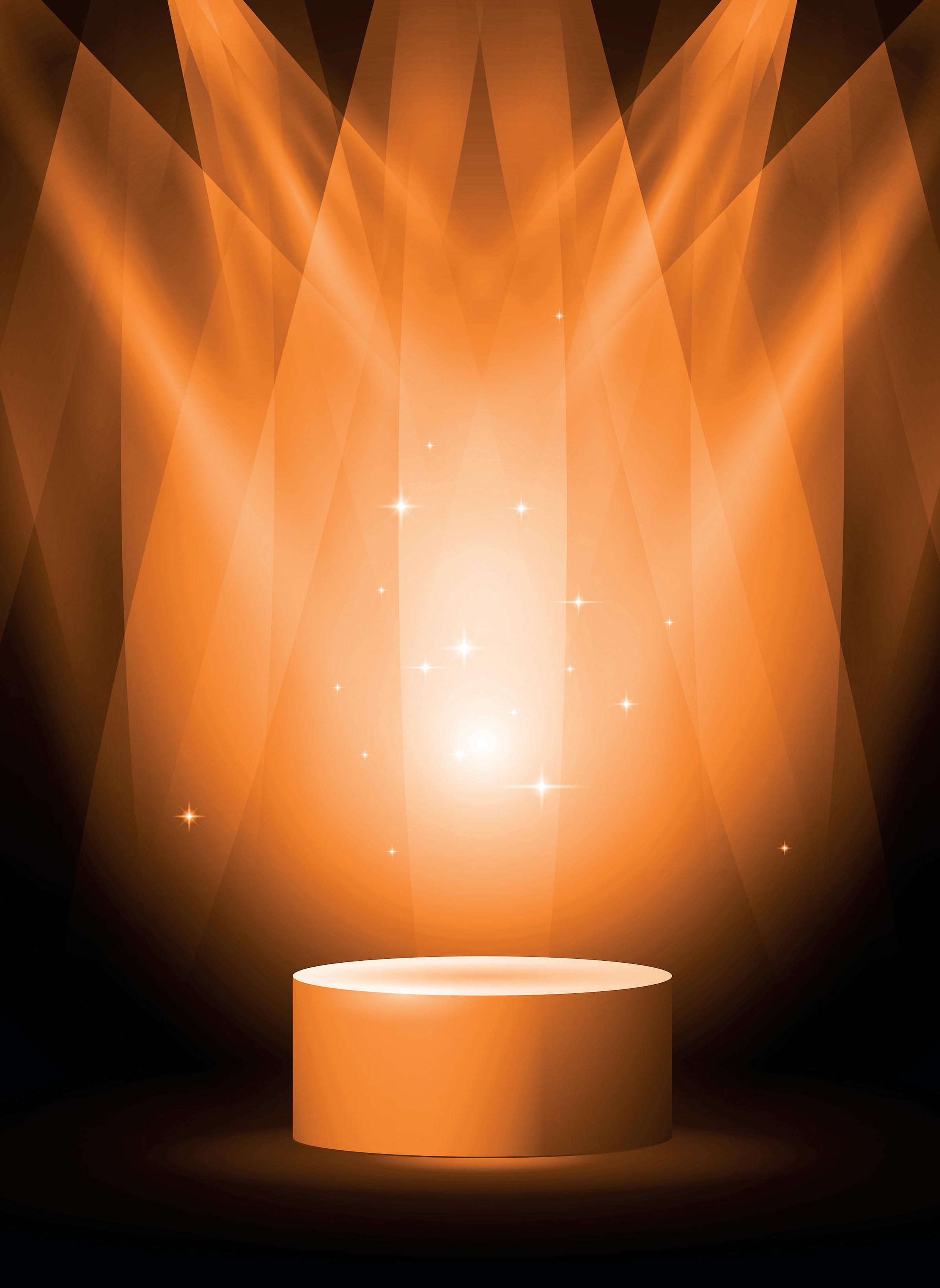


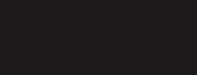

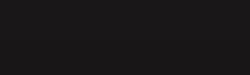

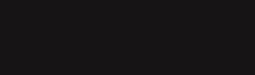

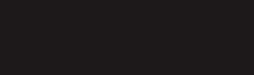

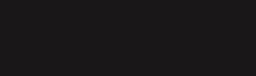

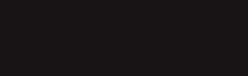

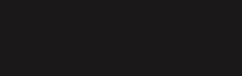


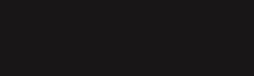
The success of Irish medtech wouldn’t be possible without local talent feeding into the industry. NUI Galway’s BioInnovate Fellowship programme equips aspiring innovators with the necessary skills to identify unmet clinical needs, innovate a novel solution to address them and implement those solutions into patient care. Point of care analysis To make diagnostic testing cheaper, faster, and smarter, many healthcare professionals are turning to point of care (PoC) testing. This is testing that is performed outside of a laboratory setting, such as in the doctor’s office or the emergency department. In minutes, a medical practitioner can gain an accurate picture of the patient’s health. The medical practitioner can make clinical management decisions much faster, resulting in improved patient care. With PoC testing, patients no longer have to wait for results, offering instant peace of mind and allowing treatment to begin PoCimmediately.analysis devices use miniature drive systems for the disposition of samples, and to mix with reagents using rotating and shaking motions, allowing the testing to be nearly fully automated. Therefore, minimal training is required for personnel using PoC testing, making it widely accessible. Laboratory diagnostics However, PoC cannot be used in all circumstances, and more complex cases will require laboratory diagnostics. Thanks to innovations in automating laboratory diagnostics, this is no longer the fastestIrelandtherevolution,atIrisheffsystemwouldaaworksofaloweringthediagnostics,repetitiveequipmentAutomatedoncelabour-intensivetime-consuming,processitwas.laboratorycanperformallthestepsinvolvedinsuchasmovingtesttubeintopositionandtheneedletotakesample,withhighlevelsprecision.Thesystemwithoutinterruptionatconstantspeed,enablinghigherthroughputthanbepossiblewithaPoCandincreasingcost-ectivenessinthelaboratory.medtechcompaniesaretheforefrontofadiagnosticsbothinandoutsidelaboratory.MediconisoneofIreland’sgrowingcompanies within the health sector. It specialises in laboratory diagnostic equipment, as well as providing a range of PoC systems including blood glucose meters. Supporting motors Whether diagnostics is being undertaken by PoC testing or in the laboratory, the equipment must be powered by a reliable drive system to ensure results are fast and accurate. EMS is the UK and Ireland supplier of FAULHABER motors, which are made in a finely controlled manufacturing process that ensures they perform with high repeatability and reliability. For PoC systems, the motors must be as compact and as fast as possible. FAULHABER DC micromotors available with graphite or precious metal commutation or stepper motors are compact, efficient and offer a high power to weight FAULHABER’sratio. DC micromotors can be used in automated laboratory diagnostics, as their ironless, self-supporting copper coil with skew-wound design makes them lightweight and compact. They can be integrated into the moving component without adding unnecessary bulk. Alongside government support and excellent local talent, it is the constant drive for innovation that has cemented Ireland’s position as a world leader in medtech. High performance, reliable motors have been fundamental in revolutionising diagnostics. We can only imagine how Irish medtech will develop the technology in the coming years, improving patient quality of life even further.
E xports of medtech products represent 8% of Ireland’s total merchandise exports, making Ireland the second largest exporter of medical technology in Europe, according to IDA Ireland. Investment in research and development (R&D) and innovation has positioned Ireland as a world leader in medtech innovation. In the 1980s, manufacturingIreland’sindustry suffered a downturn. To safeguard the sector, the Irish government and its manufacturers turned to medtech. From just a small group of 50 companies in the early 1990s, the medtech landscape in Ireland has rapidly expanded to become a leading global hub that’s home to 350 companies employing over 38,000 people. For example, Pfizer was one of the first pharmaceutical companies to move to Ireland in 1969 and now has five sites in the country employing over 4,000 people.
Drivers for success A key factor in the success of Ireland’s medtech industry is the support shown by the Irish government, which continues today. IDA Ireland, a government body designed to encourage investment into Ireland, provides valuable consultancy and support services to help medtech organisations establish and expand. In addition, the Irish government has provided financial support for medtech companies in the form of various government grants and the 25% R&D tax credit, which encourages foreign medtech companies to establish a base in Ireland.
IRELAND 9
Dave Walsha, sales manager at small DC motor supplier EMS, explores how Ireland’s medtech industry has made cutting-edge advances, with the support of micromotors.

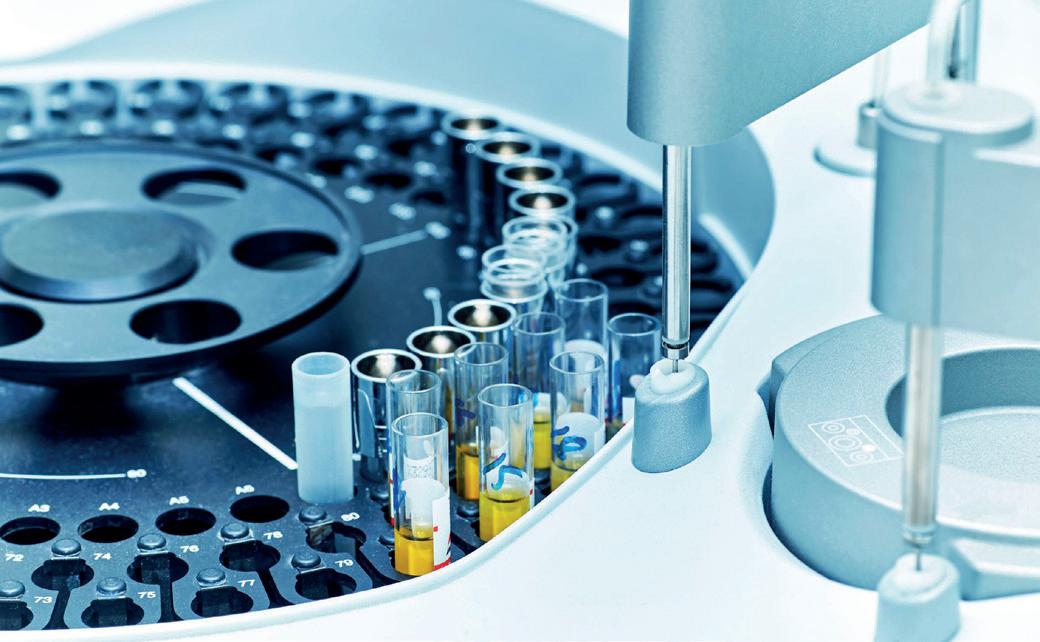
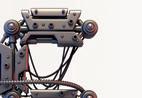
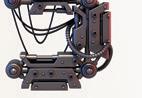
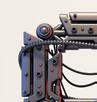
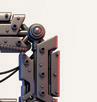
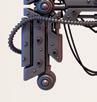
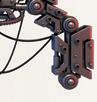
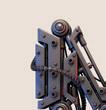
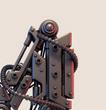
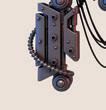
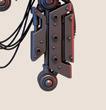
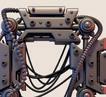
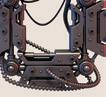


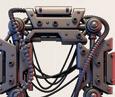
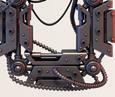
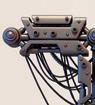
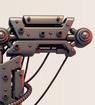
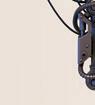
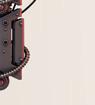
With product teams and supply chain partners more dispersed than ever, it’s imperative that everyone involved in the design, validation, production, and certification process has complete visibility into the latest product information so they can stay on track with compliance requirements and other key deliverables. Yet, many companies manage product and quality processes using manual, paperbased systems and lack a single source of product truth to ensure quality and streamline compliance.
Training management An employee training program is essential to demonstrating adherence to FDA, commercialisationAchievinginavolatilemarket
QUALITY PRODUCT
Design controls Companies must establish effective design controls to verify that devices perform according to their intended use. To ensure accurate controls, the design history file (DHF) and device master record (DMR) must be managed in context of each other and the entire product record. Because traditional paper-based systems and document-centric QMS platforms leave quality records, design files, bills of materials (BOMs), and other key components of the product record disconnected, teams lack full visibility and traceability, which leads to errors and inconsistent information. These design control issues often result in audit citations and derailed product launches.
10 on the cover 10 Arena, a PTC company, outlines the role of a successful cloud QMS in helping medical device manufacturers achieve commercialisation success in a volatile market. D elivering safe and effective medical devices ahead of the competition is difficult for today’s manufacturers as they navigate evolving customer demands, increasing product complexity, supply chain disruptions, and more stringent industry regulations.
PRODUCT RegulatoryDEVICECHALLENGESDEVELOPMENTFORMEDICALMANUFACTURERScompliance
As FDA, ISO, EU MDR, and other regulations across the globe become more stringent, manufacturers are having to gather extensive technical data to ensure patient safety and demonstrate compliance. And although the different regulations share the same basic principles, manufacturers still need to monitor them closely to keep up with the ongoing changes and intricacies that impact their business.
In this article, we explore some of the product development hurdles that medical device manufacturers typically face in getting products to market. We also reveal how an enterprise quality management system (eQMS) solution can help companies meet their compliance goals and achieve commercialisation success.
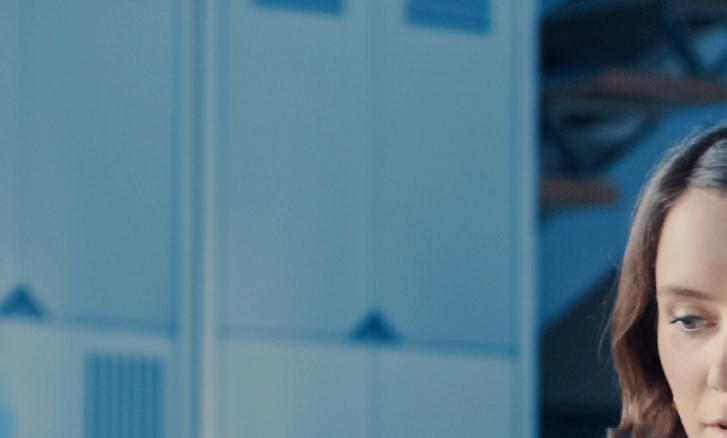
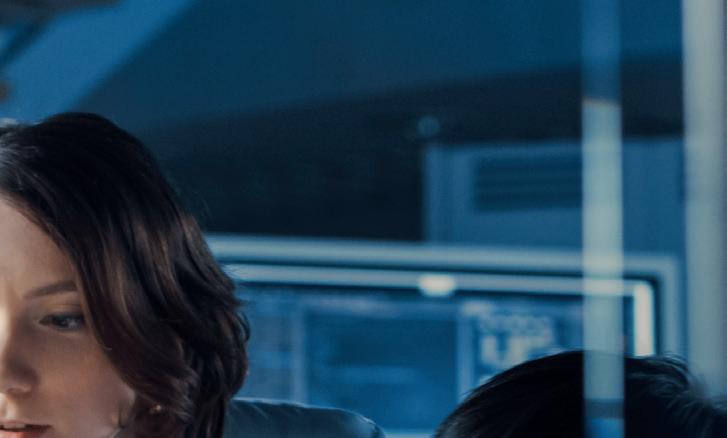
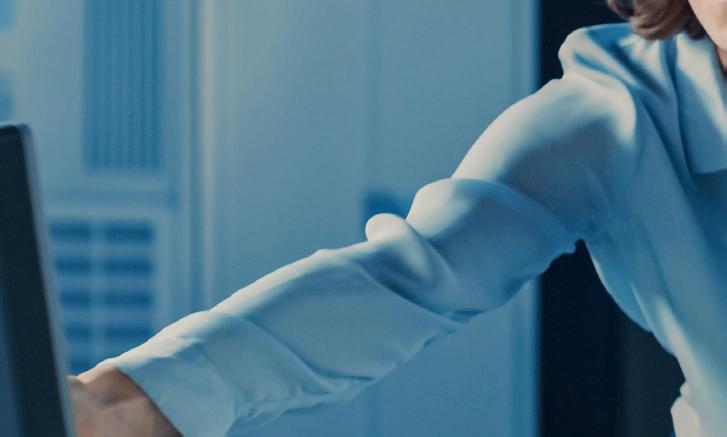
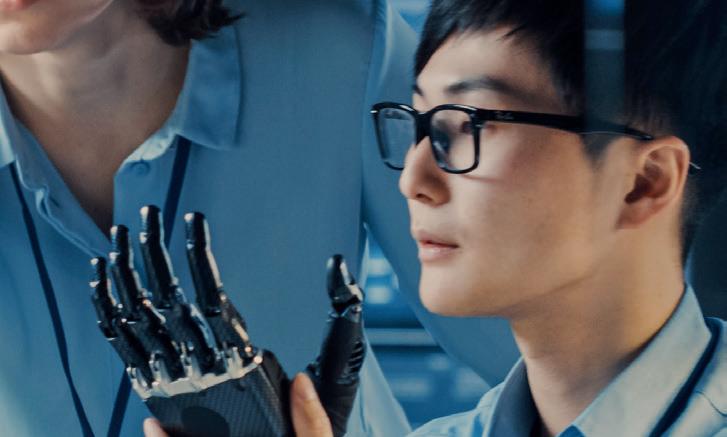
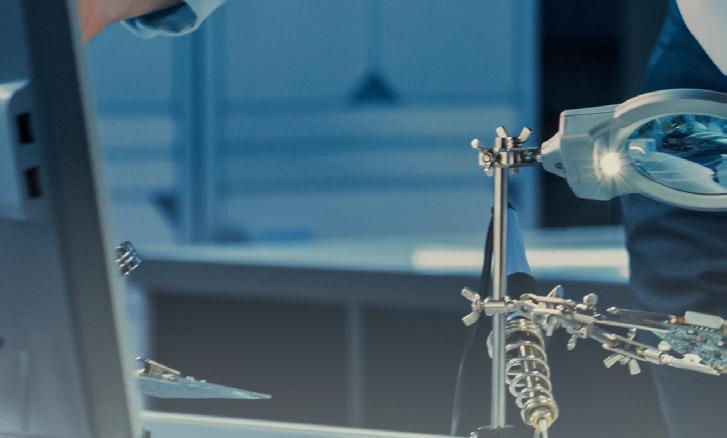
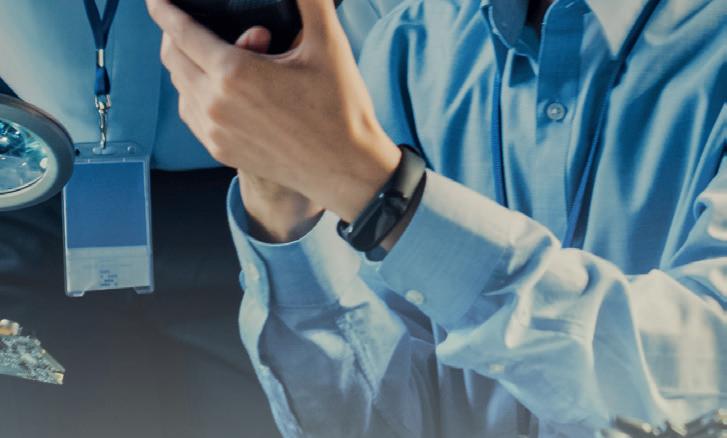
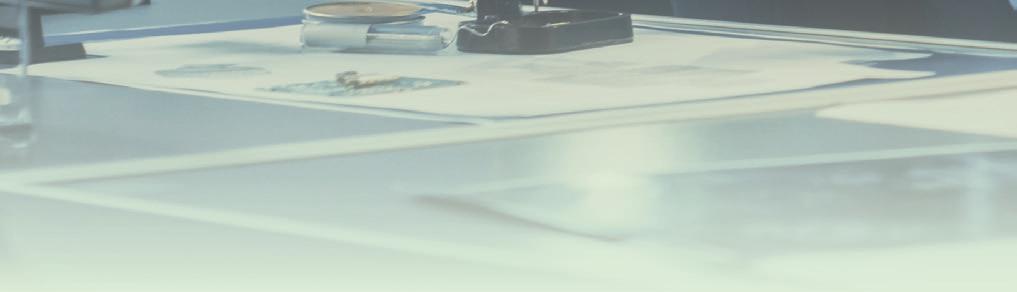
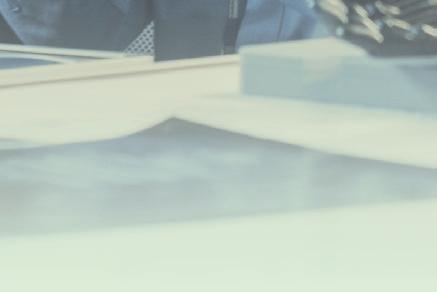
Today, more and more companies are moving away from traditional paper-based systems and leveraging digital technologies to better manage and track their new product development and introduction (NPDI) processes. By embracing cloud-based eQMS solutions, companies can eliminate data silos and communication barriers to quickly resolve quality issues and drive continuous improvement.
Document management Centralised storage, tracking, and management of all product and quality documentation is necessary to meet the demands of today’s highly regulated environment. Medical device companies must maintain vast amounts of documentation including standard operating procedures (SOPs), specifications, engineering drawings, and policies as part of their QMS. However, these documents are often stored in different systems and multiple locations, making it difficult for dispersed teams and supply chain partners to identify the latest version and conduct reviews and approvals in a timely manner. During audits, it is also difficult to quickly compile requested information and demonstrate proper revision and document control.
Verification Validation User Needs Design Input Design Process Design Output Medical Device ISO, safety, and other standards. Regulatory agencies focus on a training management system to determine the company’s ability to follow its documented business policies and procedures. For instance, as part of an inspection, the FDA will first review a medical device company’s training records to assess whether employees are following current good manufacturing practices (cGMPs). Documenting, testing, and tracking that employees are properly trained is a heavy burden for those responsible for executing the program, especially when using manual, paper-based systems, or a siloed solution. Without training record management automation in place, companies are prone to compliance risks and unnecessary administrative costs. Requirements management Requirements management is the process of documenting, analysing, tracing, prioritising, and agreeing on product requirements and then controlling and communicating changes to relevant stakeholders. This process occurs throughout new product development (NPD) and leading up to new product introduction Requirements(NPI).are typically: ● Design constraints ● Testable ● Interface-centric (what the product is perceived to be) ● Mostly about what the product should Accordingdoto LNS Research, 91% of organisations still use spreadsheets and electronic documents to track requirements. Since these ad hoc solutions are not tied to the product record, cross-functional teams lack full visibility into quality issues, customer needs, design defects, and other dependencies that impact NPI. Reliance on multiple disconnected systems also results in more work and increased risks to launch schedules and Asprofitability.thedemand for more sophisticated products continues to rise, manufacturers need a more unified system to track requirements that span mechanical, electrical, and software disciplines and keep everyone on the same page.
DRIVING COMMERCIALISATION AND COMPLIANCE SUCCESS WITH CLOUD QMS
Review ON THE COVER 11
To learn more about how a product-centric QMS helps medical device companies streamline NPDI and achieve compliance goals, read Arena’s customer success stories.
With product teams and supply chain partners more dispersed than ever, it’s imperative that everyone involved in the design, validation, production, and certification process has complete visibility
pdfSuccess-Story_Potrero-Medical.wp-content/uploads/Customer-https://www.arenasolutions.com/
Advanced solutions like Arena’s product centric QMS connect product and quality records in a single electronic system. This enables organisations to establish strong design controls and gain greater visibility and traceability over corrective and preventive actions (CAPAs), DHFs, DMRs, SOPs, requirements, and other quality processes that are critical to meeting regulatory requirements. Teams can leverage quality templates to easily develop post-market surveillance (PMS), clinical evaluation, and corrective action reports as well as other documentation necessary for a technical file submission. The platform also provides an automated system to create employee training plans, assign training records, and generate progress reports to help reduce compliance risks and eliminate reliance on a separate disconnected training system.
Because automated change processes and revision controls are applied to all product and quality information, companies have greater success in passing audits and meeting their commercialisation milestones.
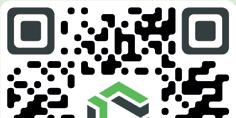
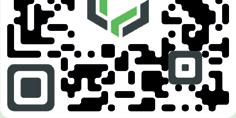
12 Remove bottlenecks and simplify your processes Intertronics Process Improvement Qtr Page 124x86 ad 01865 842842 intertronics.co.uk/productivityinfo@intertronics.co.uk Make your adhesive and dispensing processes more productive with process-optimising materials & systems • Improve speed and accuracy of dispensing with dedicated dispensing robots • Reduce work in progress with fast UV light curing materials • Improve process simplicity with process-convenient materials packaging • Get fast, homogenous mixtures of liquids, powders and pastes with mixing and degassing machines • Achieve more consistent bonding results with plasma surface treatment Could you reach your productivity potential by improving some of these areas? Read more at intertronics.co.uk/productivity. BEYONDTOOLINGMOULDINGDEVELOPMENTDESIGNTHEMOULD Pentagon, pro-actively supporting you from the early stages of design assistance right through to mould tool manufacture and repeat production of your injection moulding project. Your new or existing plastic injection moulding project will benefit from years of technical moulding experience! UK Manufacturing services delivering ease of communication and a smooth supply chain www.pentagonplastics.co.uk | websales@pentagonplastics.co.uk Tel: +44 (0) 1403 264 397 |
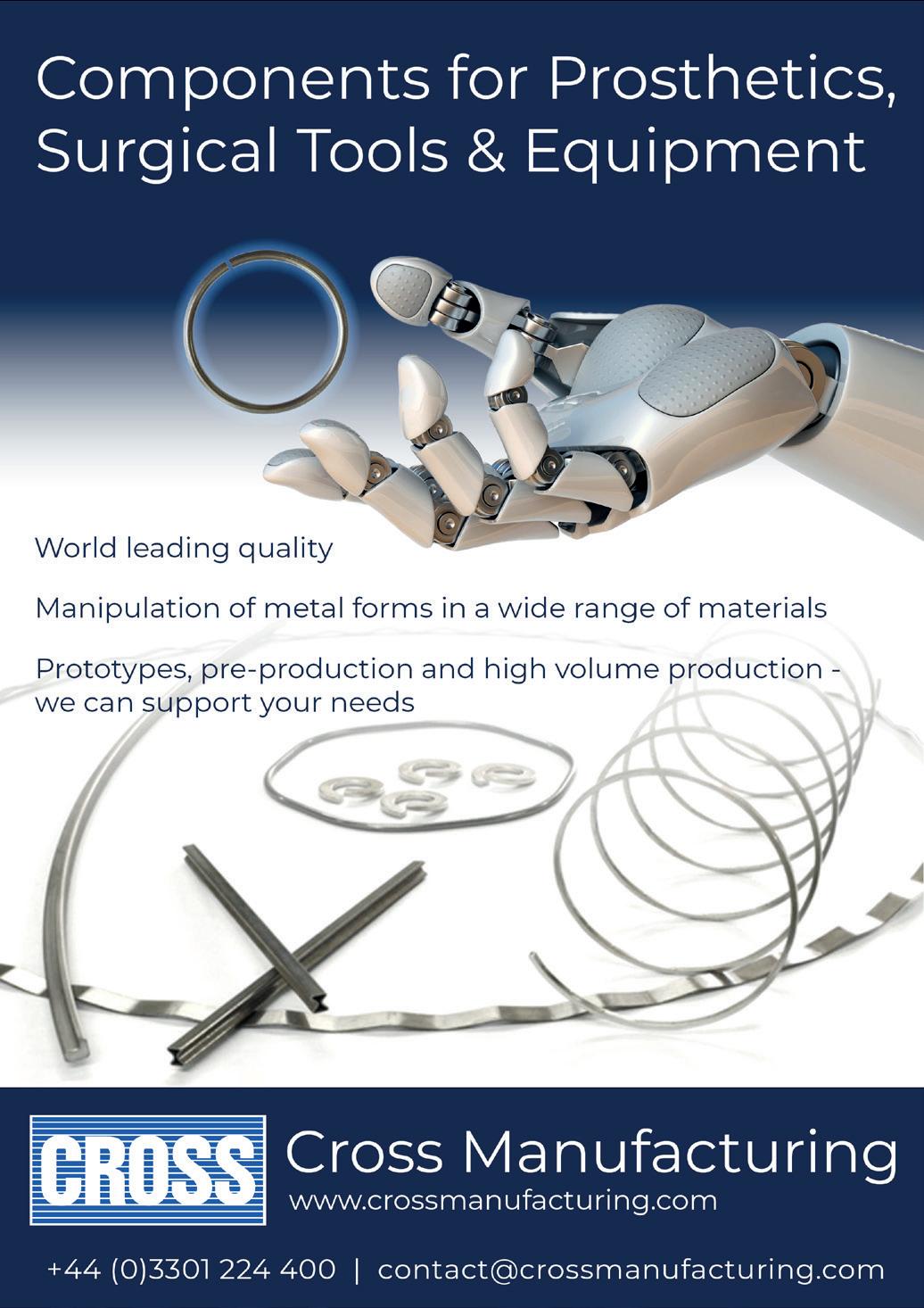

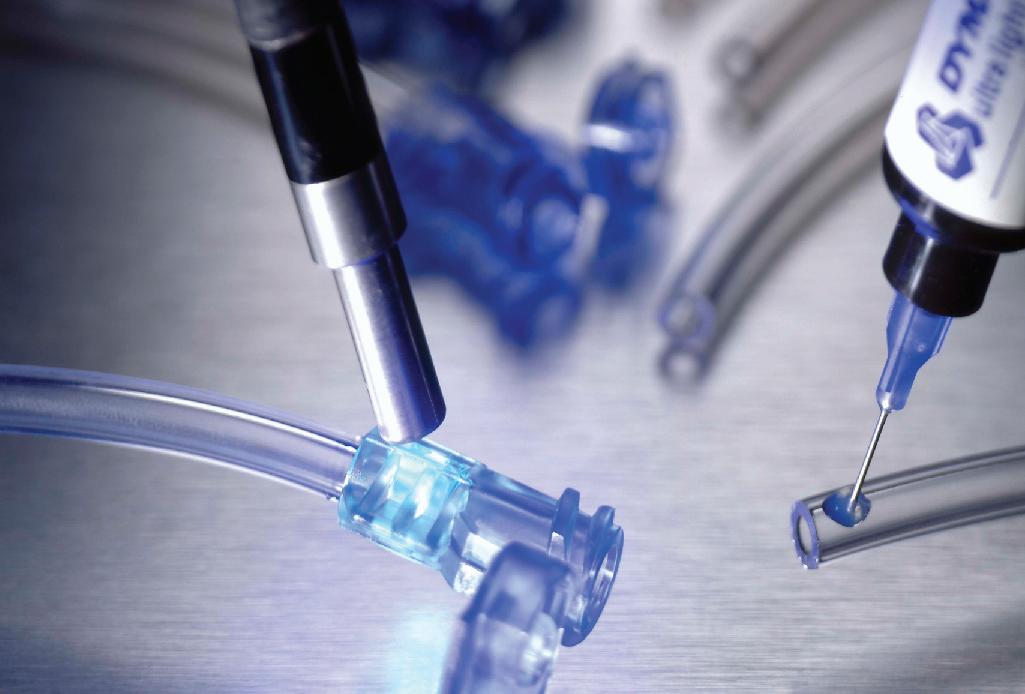
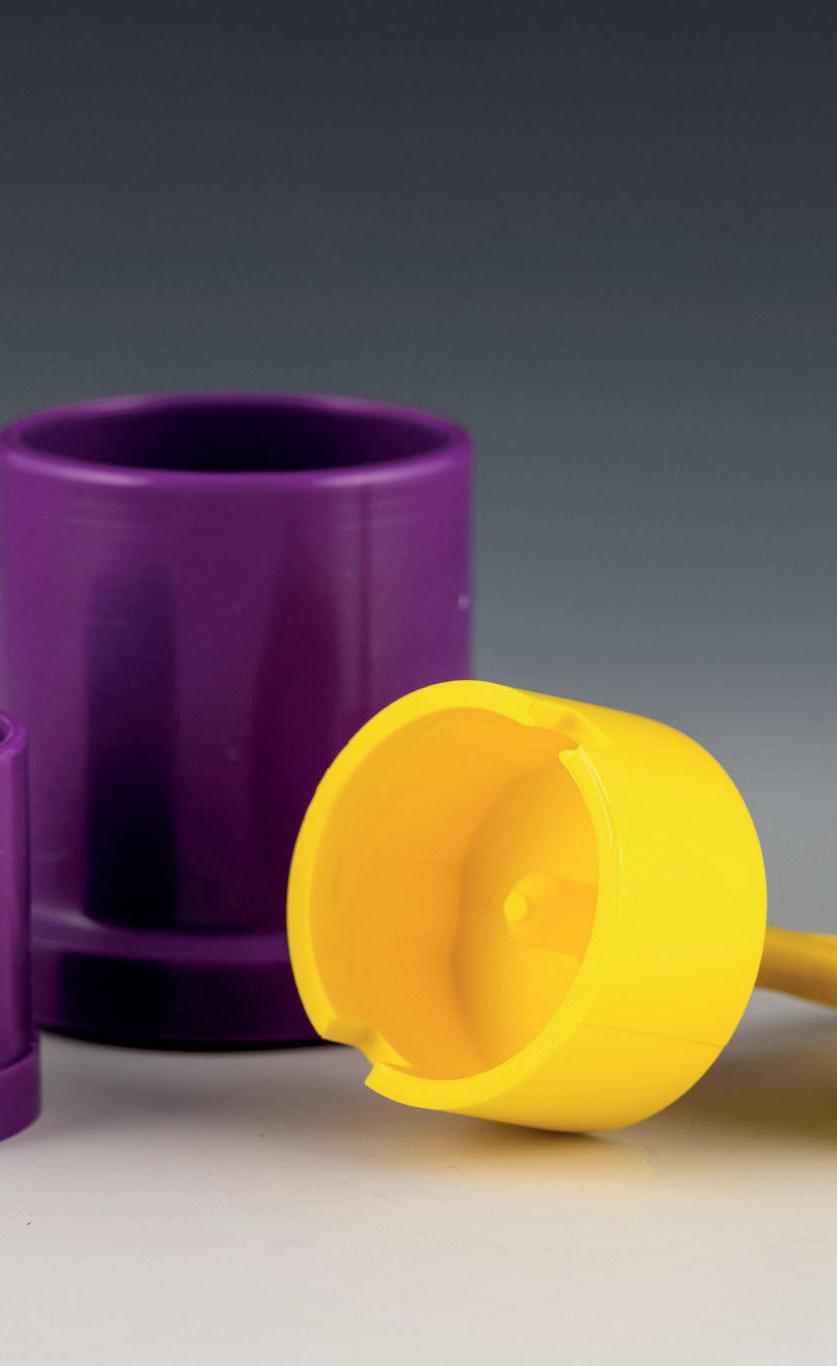
As a result, it can save the patient time and reduce primary care costs.
“We’d be reducing the cost of drugs because we can treat the patient with the right drug at the right time, first time. The convenience of it all means that that people don't have to worry about having a disease for prolonged time, which will also cost more.”
whatThisprobes.”andprimerswerealteredtoneededthing–offocusedmorewassameis“Theminutes.”engineeringexactlytheasitfortheCOVID-featurestheproducttheonlythatbetheispartofO’Halloran describes as forgedpartnershipsatproductwell-developedapipelinethecompanywithbeingandlikelytobe announced in the very near future. Though Q-POC is currently focused on respiratory conditions for now, O’Halloran sees the product becoming a jack of all trades –with the Point of Need element a crucial aspect, to provide an instant diagnosis and could be a key tool in combatting drug resistance.
Hot on the heels of winning Med-Tech Innovation’s special recognition award for its response to the COVID-19 pandemic by developing Q-POC, QuantuMDx has been developing a new assay to help combat a spike in seasonal respiratory diseases.
Heading things off
The diagnostics company has developed an assay that can detect up to four different respiratory diseases, flu A, flu B, all know sequences of COVID-19 and RSV. After periods of lockdowns and other lesser restrictions in the UK, there’s the worry of hospitals not just being overwhelmed by COVID admissions, but of flu too.
Diagnostics 13
Jonathan O’Halloran explains the difficulty distinguishing different respiratory diseases from one another and hopes that the new development can help clinicians on the front-line. He said: “Q-POC, our rapid PCR testing system, is going to have a long menu of different assays coming through, some exciting ones as well in a space that we call syndromic testing. “You're not necessarily always going to have a doctor there to do the imperial diagnosis to decide what you want to test for. “You need to test for everything that causes a certain symptom, hence a syndromic panel. So, if someone rocks up to a pharmacy or a doctor's office with something like diarrhoea, then a test can be run for everything that causes diarrhoea. Or a fever test for everything that causes fever, respiratory test for everything that causes respiratory distress and so on. These syndromic panels are the true future of Point of Need testing. “The Q-POC and its assays are so easy to use. You just do a swab, put it in the buffer, trip up and down five times, and then put it in the device.”
Ian Bolland spoke to Jonathan O’Halloran, CEO of QuantuMDx about the latest assay developed by the company as it aims to help battle flu season in the UK.
Ease of use is key to this Point of Need diagnostic - to help establish the condition and to isolate any patients if required. “You want to use something that's simple because people in A&E, they're busy as hell and, they've only got time to just collect a sample, press it (the device), go and forget about it. And then when Q-POC starts flashing or stopped (in approximately 30 minutes), then they know it's ready, they have their results and then they can figure out how best to treat that patient. “Q-POC is game changing from that perspective.”
The potential isn’t just for the diagnosis and aiding treatment of respiratory diseases as O’Halloran says - this form of testing can be replicated with other conditions, such as sexually transmitted infections. Having such a device on a university campus that can rapidly diagnose a sensitive condition when someone might shy away from a consultation is something that O’Halloran feels is a useful asset. “If they've got a certain symptom, people don't necessarily want to talk about it, but they want to know what it is, because the treatment is going to be different and often needed quickly. So, a healthcare professional can swab, put it in the Q-POC, run the test and get the result in approximately 30
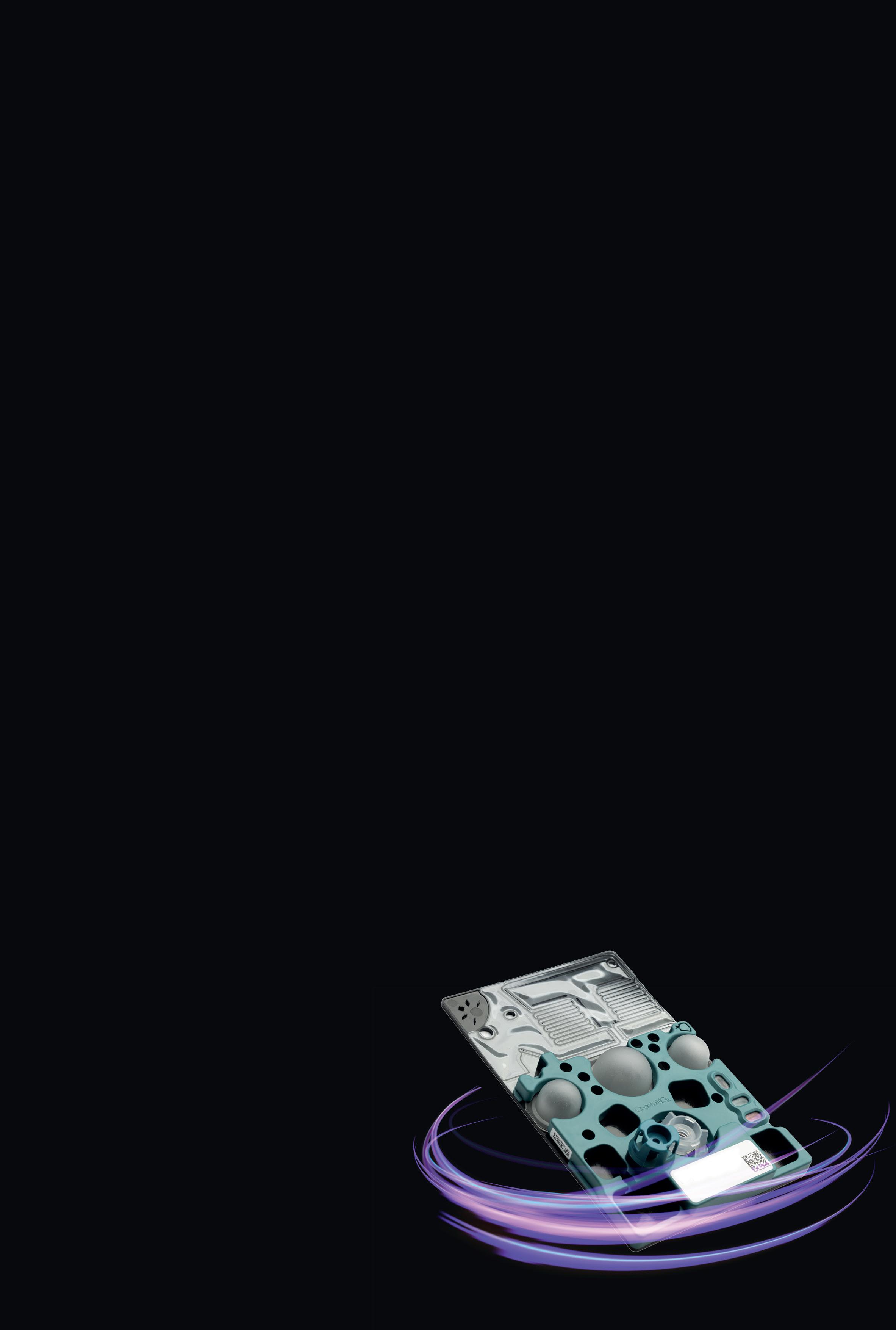
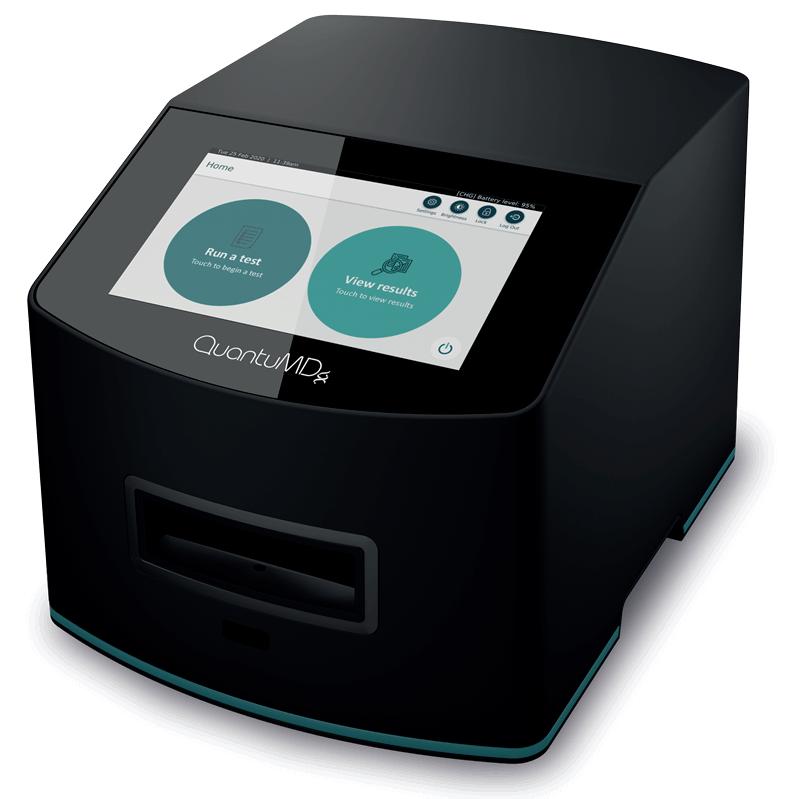
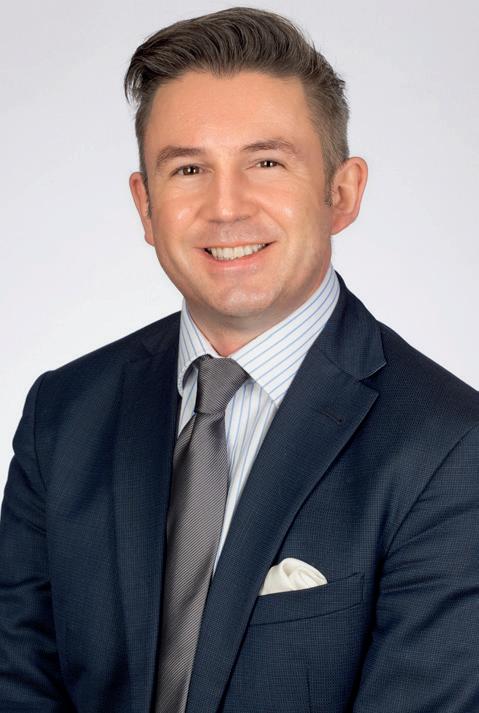
NS: “The UKCA is not the only new regulation to come into effect in recent years. New and updated medical device regulations from jurisdictions like the US, EU, and Australia are refocusing compliance requirements for the medical technology industry. The changes are intended to enhance product quality and safety. For example, the UKCA requires human trials to be approved by the Medicines and Healthcare products Regulatory Agency. They are also meant to give companies better insight into the entire product lifecycle via improved quality metrics and a more processinspectionefficientby
T
UKCA vs CE marking: How the new requirement has changed medical device manufacturing
Currently, Great Britain is allowing a transitional period until 2023 for businesses to switch to UKCA.
marking is the new legally required product marking for goods being placed on the market in Great Britain from January 2021, covering most products that previously required a CE mark. While similar to the EU’s CE marking requirements, the UKCA means many must relearn the necessary requirements for medical device manufacturing. CE marking is a self-declaration where a company demonstrates conformity with EU health, safety, and environmental regulations and affirms that a product meets essential standards. Similarly, UKCA marking demonstrates conformity with UK regulations. For medical devices intended for Great Britain’s market, a UKCA is needed.
he UK Conformity Assessed (UKCA)
AD: Can you explain the process of getting a UKCA mark?
Ashmita Das, CEO of scientific talent platform Kolabtree, sits down with freelancers Nare Simonyan and Nida Ali to discuss how the UKCA marking has impacted medical device manufacturing in the UK.
NA: “The first step is creating a Declaration of Conformity to prove your medical device meets all the quality and technical requirements needed to perform its tasks. Manufacturers need an ISO to declare all requirements are met, including a statement from the manufacturer. Then a technical document is needed explaining the design, material, manufacturing, and records of how the device meets the relevant quality checks. For medical devices with 25% similarity to those already on the market, a clinical performance document is required. This can be compiled of relevant literature discussing the device compared to others on the market.”
AD: How has the regulatory change impacted NA:technologies/devicesmedicalspecifically?
14 REGULATION 14
NS: “It’s also important to note that the UKCA mark itself is not evidence of compliance – the technical documentation/technical file is. A Declaration of Conformity is a legal claim that products comply with applicable directives and standards but is not evidence of compliance.”
“UKCA is a regulatory process for products to be placed in Great Britain. It originated because of Brexit and is similar to the EU CE marking process. CE marking is a self-declaration where a manufacturer proves compliance with EU health, safety and environmental protection legislation and confirms a product's compliance with relevant requirements. In the same way, UKCA marking proves compliance with UK legislation. The UKCA marking has incorporated its requirements from the EU’s MDR and applies to all aspects of medical devices. The UKCA is mostly mapped on the CE format but there is a slight variation. Products that show compliance with MDR will meet the UKCA as well. Most of the differences between the two systems are administrative in nature and reflect the fact that the UKCA mark only applies in Great Britain. By adhering to the MDR, the UKCA addresses safety issues and helps mitigate safety and quality risks to ensure devices are clinically safe for use. The UKCA also requires goods undergo third-party evaluation.”
REGULATION 15 simplifying the process and focusing on key aspects inspired by the CE marking. These changes could require strategic organisational and process transformation to ensure compliance and avoid loss of revenue and market share.”
NS: “While this is true, for both parties (the UK seeking CE certification in the EU and the EU seeking UKCA conformity in the UK) time is of the essence. Yet for many manufacturers, the lack of time afforded to fulfil their regulatory obligations remains a critical issue of contention.
NS: “Using the Guidance for UKCA marking freelancers can offer insight into the main requirements for the company services. Keeping on top of your product conformity requirements will now become more complex and time-consuming than ever, with many businesses juggling a mixture of UKCA and CE marking obligations. Quality management software can be applied in multiple ways to simplify, streamline, and support your product conformity processes and ease your organisation’s compliance burden.”
The new product safety marking rules will affect businesses supplying most products on the market in Great Britain. The decision to delay the switchover is likely to have a huge impact on supply chains and consumers and it is hoped will prevent product shortages.”
AD: How can freelancers make the process easier? What specific services can they offer? NA: “Freelancers can only assist in structuring the technical document or clinical evaluation. All documentation and record keeping from the time raw materials arrive at the facility to when goods are ready to be shipped must be documented by the in-house team. However, the clinical evaluation is typically given to freelancers as this needs to be outsourced for third party verification. Freelancers can identify any risks and raise questions before its approval. It’s crucial for the document to include all issues, post-market follow up, and all regulations the device will fall under. Freelancers can also create an analysis gap of the current document to identify areas left to fill in by the in-house team.”
NA: “The UKCA in many ways is actually simpler to the CE mark. This is because CE marking requires a lot more documentation, making it more expensive with extra inspections and time consuming. The CE guidance document can also be difficult to understand as there is lots of material, over 100 pages, making it easier to make mistakes. However, as the UKCA is only applicable for medical devices on the British market, the additional marking means that manufacturers bringing medical devices to both the EU and British markets need to spend more time obtaining both markings instead of just one.”
AD: What are the issues/bottleneckscommonwiththe new requirements manufacturers face when getting a UKCA mark?
The UKCA marking has incorporated requirements from the EU's MDR and applies to all aspects of medical devices. The UKCA is mostly mapped on the CE format but there is a slight variation. Products that show compliance with MDR will meet the UKCA as well. Most of the differences between the two systems are administrative in nature
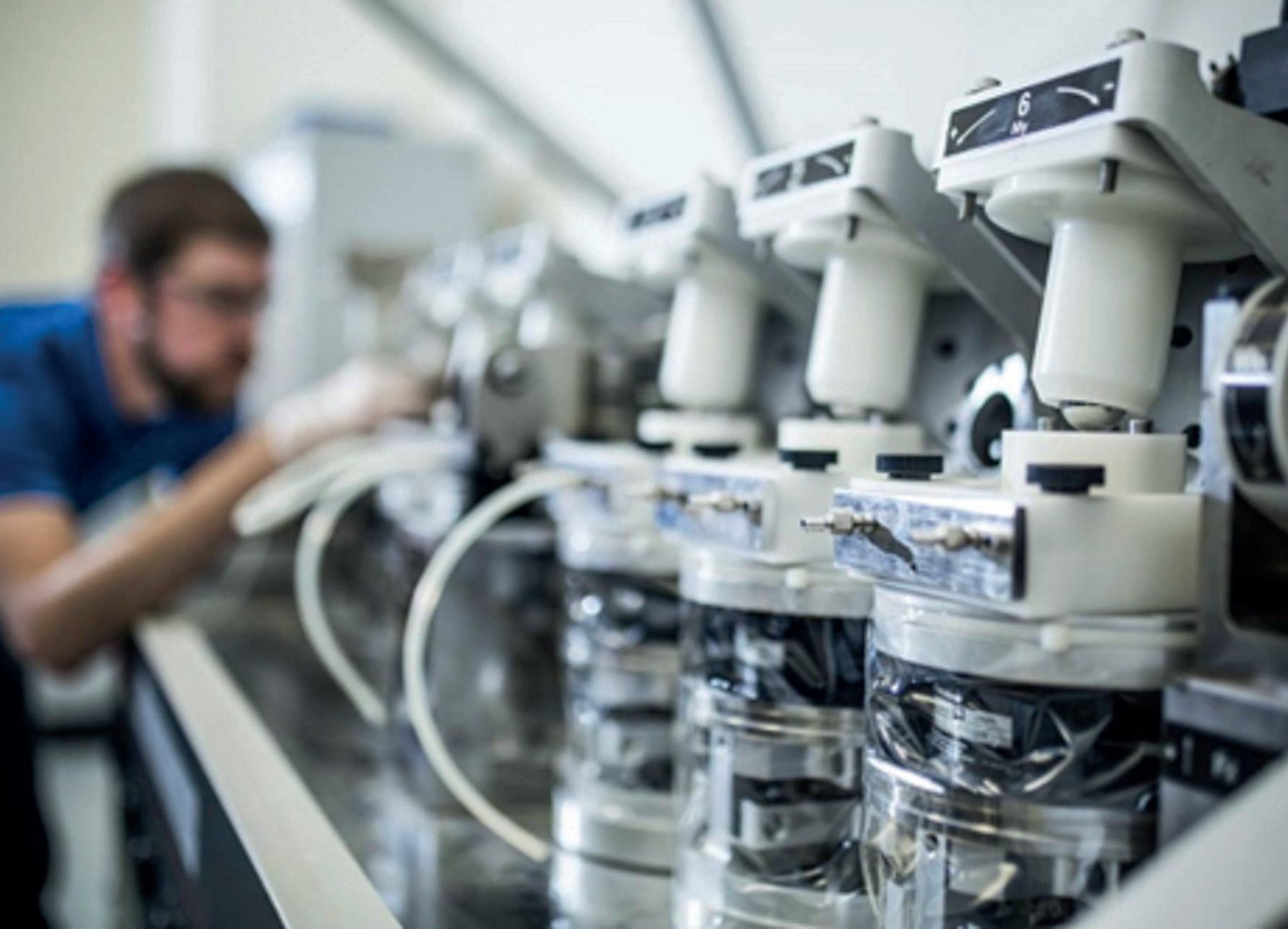
the healthcare industry’s top priority, so when disruption affects the supply chain, a cascading set of issues ensue, as even modest reactive changes to materials or manufacturing processes require re-qualifications and regulatory approvals. Given one
1616 TUBING T here are many aspects to running a business, and most require sound acumen in problem solving and handling unexpected challenges. Over the last two-plus years, we have all experienced several unprecedented, intense examples of both, from the frequency and severity of natural disasters and the supply chain-stifling COVID-19 pandemic, to escalating inflationary pressures and the geopolitical upheaval of armed conflict in Eastern Europe. In my 32-year career, never have we been faced with this many challenges in such a condensed timeframe. Our interconnected global economy has been disrupted and remains vulnerable. We’ve been faced with production interruptions, uncertain supply chain deliveries and rising costs. As a result, we are challenged with managing through a scarcity of valuable materials and product availability, much of which is also subject to unanticipated price Patientincreases.safetyremains
1. LONG TUBES, SHORT TIMEFRAME The first example highlights the
Chris Qualters, CEO, TekniPlex Healthcare, explains how unpredictability favours partners with a robust reach, foresight, and creative solutions. need to keep healthcare facility solution implemented fast was,
MANAGING CRITICAL SUPPLY CHAINS IN TURBULENT TIMES
pre-qualifipartnershipsThemitigatingsupplierthebusinesshowcompaniesconstant—change—healthcaretruemustcarefullyconsidersupplychainriskscanaffectcontinuityandrecognisevalueorganisationalheftinpartnershipsbringstochallenges.advantagesofrobustincludemulti-factorycations;outsourcing
secondary and tertiary production to focus on core competencies; and the benefits of engaging entities offering vertical integration when time constraints or cost of ownership make internal production untenable. BUMPS IN THE ROAD So many factors are impacting production in factories around the world. One troublesome trend that has worsened in recent years is climate change. More extreme weather has meant more—and more severe—supply chain disruptions. And then… COVID-19. The ensuing worldwide lockdowns, labour shortages, and supply-demand imbalances created by the pandemic showcased how a health crisis quickly becomes a supply chain one. As the COVID crisis wanes, another is born: Russia’s invasion of Ukraine has ushered in a period of geopolitical instability and contributed to inflation fuelled by spiralling energy prices. Here, healthcare companies are undoubtedly being impacted, as nearly all medical-grade plastics typically require petroleum. A looming scarcity of some commodities and disrupted EastWest shipping routes continue to exacerbate these
developerglobally-integratedourchaintowell-roundedcompaniesHealthcareissues.productsneedastrategyminimisesupplypitfalls.Whilecompanyisaandsupplier of inofasolutionspolymermedical-gradeadvancedforwidevarietyapplications,recentyears we’ve also become supply chain mavens of sorts—an innovation born of our customers’ necessities. Let’s explore examples of increasingly common supply chain challenges and potential tactics toward alleviating them.
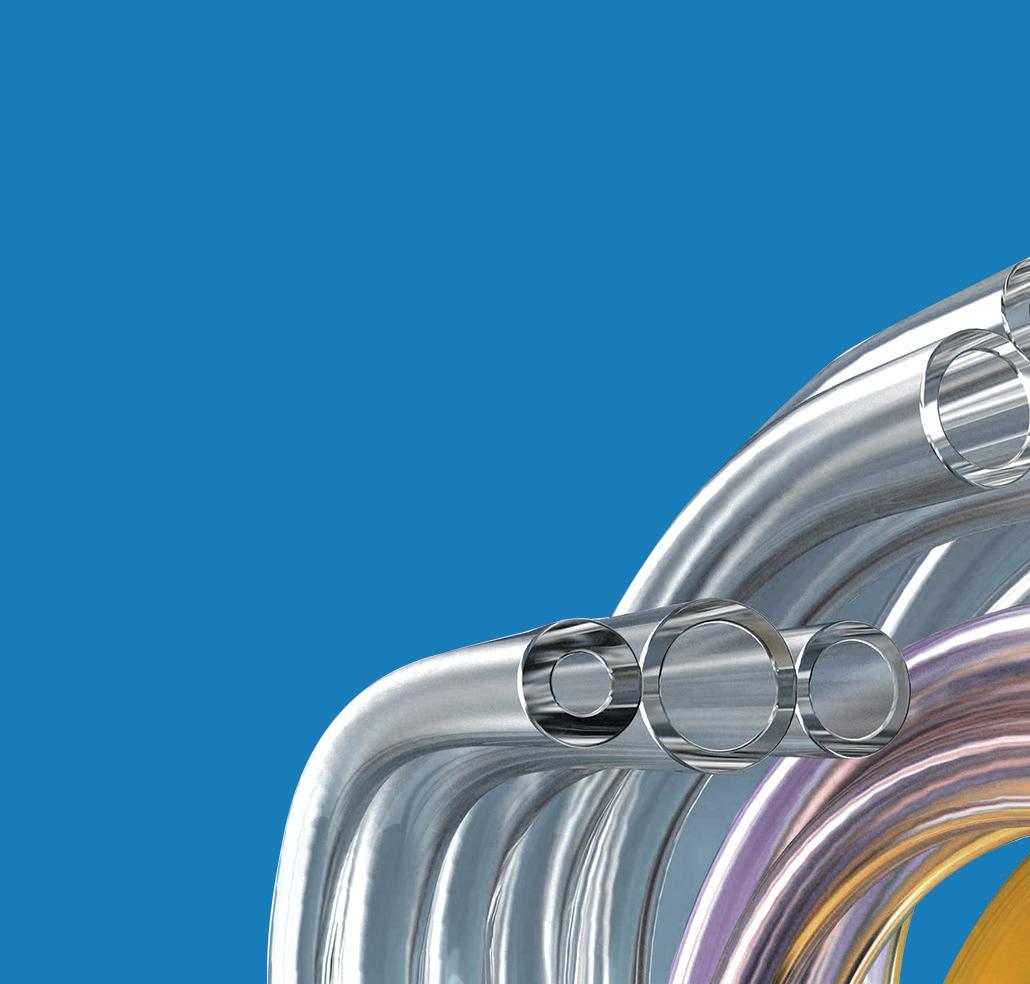

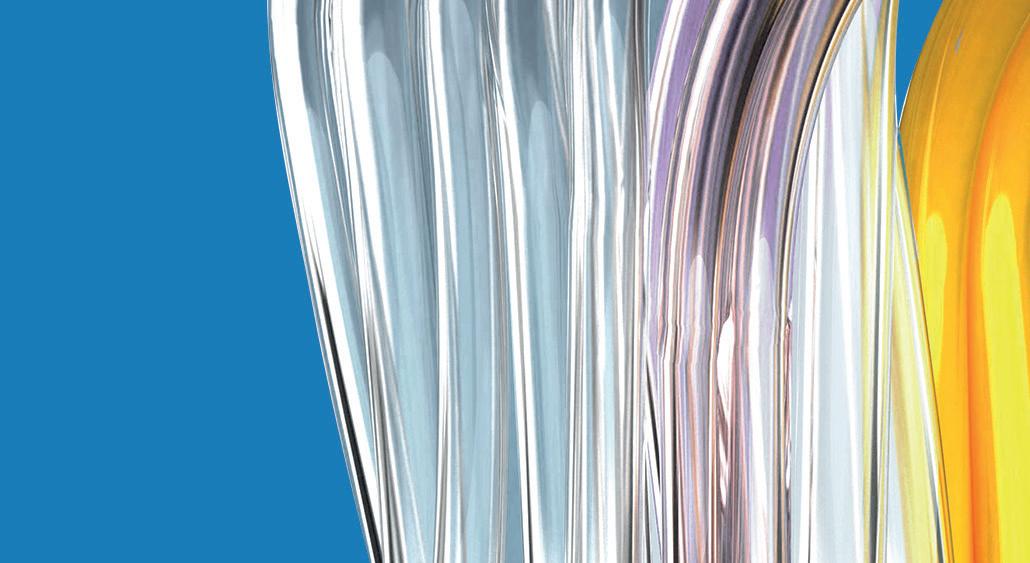







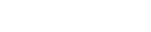

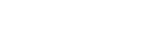
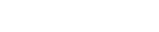
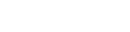
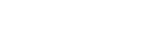



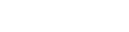

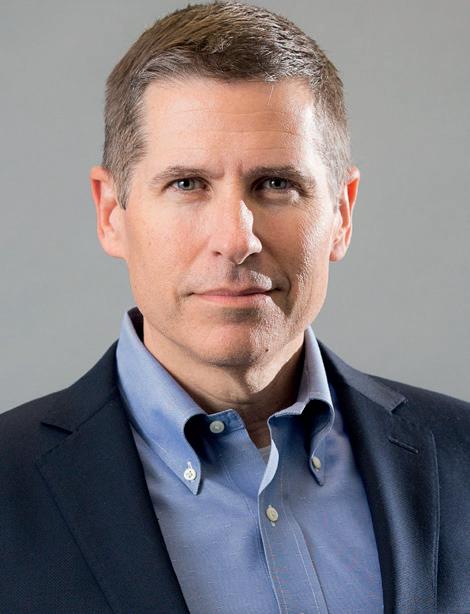
WHAT WE’VE LEARNED, AND FUTURE CONSIDERATIONS
While our company is a globally-integrated developer and supplier of advanced medical-grade polymer solutions for a wide variety of applications, in recent years we’ve also become supply chain mavens of sorts shifts.
2. MORE THAN ONE AND DONE A natural disaster impacted multiple suppliers along a supply chain, causing a domino effect for numerous medical device companies. This triggered a race to secure volumes of materials, resins, compounds, and finished parts. Device purchasers started gobbling up product wherever it was, depleting stockpiles and, via supply and demand, driving up prices. To remedy this and increase supply, we produced qualification samples on three continents to supply manufacturers in North America, Europe, and Asia—including, not coincidentally, several new customers. As demand continued to rise, we installed and qualified higher-volume machinery and ran multiple Crucially,shifts.thisdid not require tradeoffs, such as delayed lead times for current customers. A key factor was strategically located sister sites providing widescale redundancy and expedited regional delivery. The takeaway: standalone facilities face elevated risk of production disruption and delay.
the company needed to outsource quickly to a competent partner to free up space for its core competencies. This required a partner who could quickly qualify the production process, all product SKU’s and build buffer inventory to bridge transitional gaps.
3. WHEN GROWTH BECOMES A COST OF OWNERSHIP A customer needed to increase production quickly to meet growing demand. Its production facility was at capacity, and building an extension wasn’t an option because of time and real estate constraints. Skilled labour also was scarce. A significant portion of its footprint and personnel were being utilised in the extrusion department, which produced a high-volume but low mix of tubes for interventional catheter lines. While most extrusions were already outsourced, these lines remained on-site due to an earlier “make or buy” evaluation. Ultimately, they determined cost of ownership had become too high compared to outsourcing. A key factor was vertical integration. With just one of its devices’ several components requiring too much floorspace and peoplepower, the solution involved engaging a partner for whom tubing wasn’t part of the product, but rather the entire Inproduct.thisscenario,
TUBING 17 institutions opted to move certain machinery outside patient rooms. This included IV pumps and tubing, which required frequent changing. The solution was that tubes connecting pump to patient needed to be longer—as in three to four times the length. In addition to unprecedented demand, this swift sea change in procedure meant the design of certain IV pump tubing needed to be reconfigured. This would necessitate qualifications across various geographic locations, ASAP. Our medical device partner contacted us, and together we quickly formed a multifunctional, multi-national team. Mission accomplished – in just ten working days. Our ability to produce both the compound and extrude the tubing was critical to meeting the customer’s needs.
Finally, choose partners with a comprehensive solutions platform to solve both product and supply chain challenges globally. Seek companies that have extensive technical, supply chain and project management acumen; embedded materials science expertise; and precision manufacturing processes aligned in a worldwide network.
While there may be a bit more initial cost and qualification efforts, we’ve learned this approach protects patients and, ultimately, is also the most economically efficient.
First and foremost, failing to address turbulent environments can impact patient care. It also can cost extraordinary amounts of money, time, and reputation damage. Fortunately, a growing number of forward-thinking companies are evolving to advanced scenario planning that bakes robust risk and uncertainty analyses into materials and supply chain strategies. Moving forward, the best approach is to ensure new projects robustly address supply chain risk mitigation.
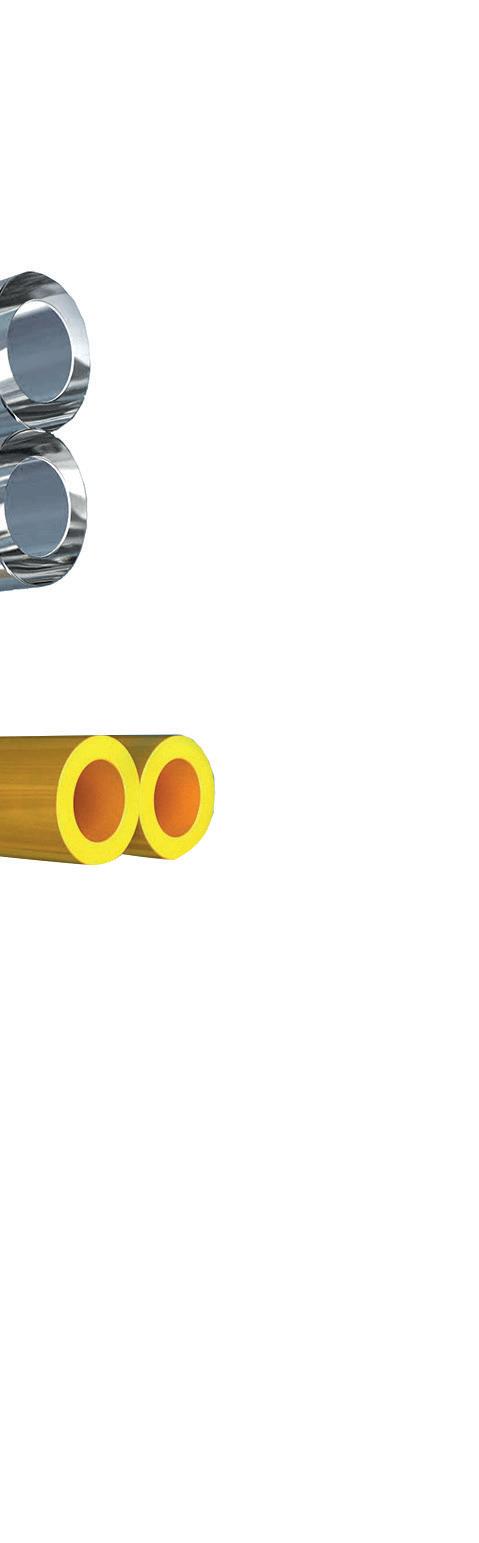




























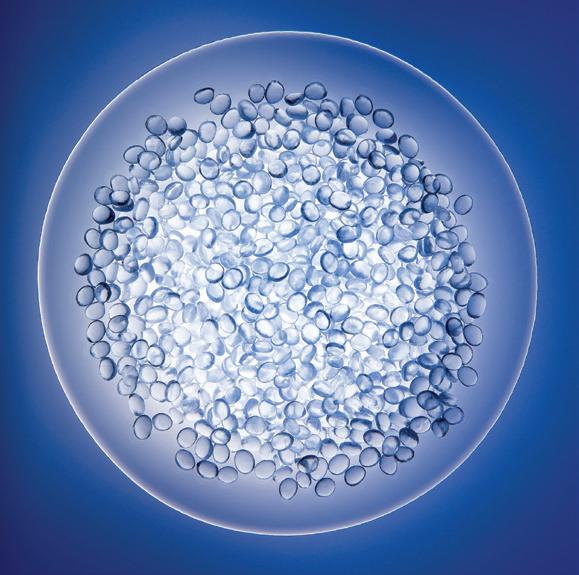
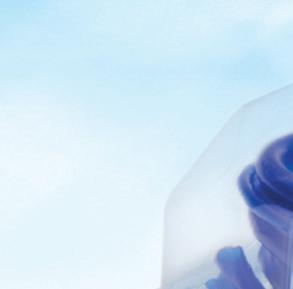
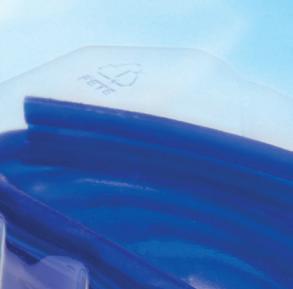
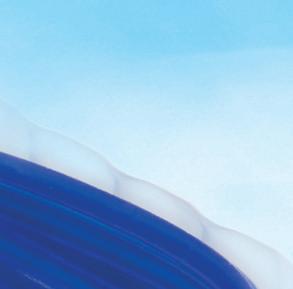
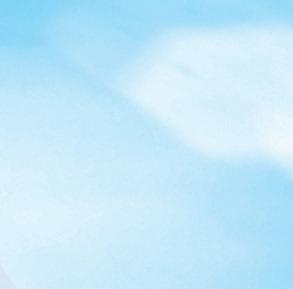
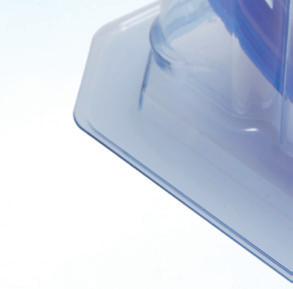
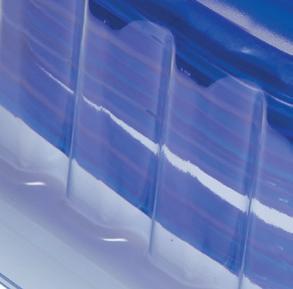
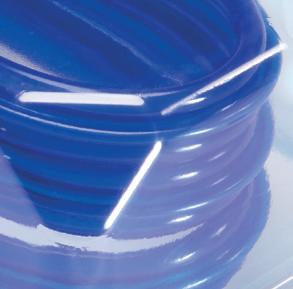
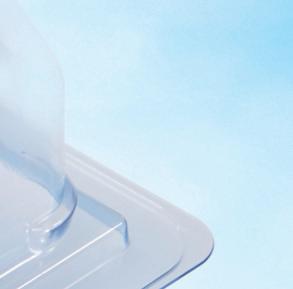
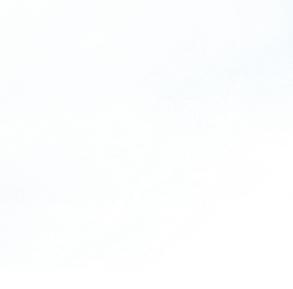
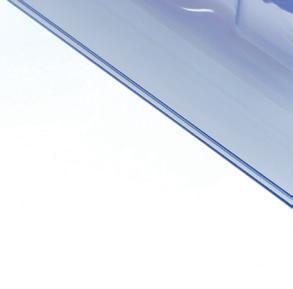
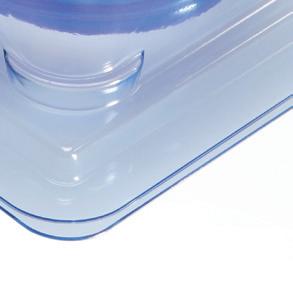
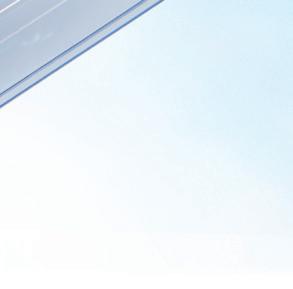
Innovation Expo returns on 7-8th June 2023 and companies have already taken the opportunity to secure their place for the show after a successful 2022 andforwardNECalongsideInnovation2023.whoarePolarSealConsulting,Group,Boddingtons,Shawpak,showing.BioInteractions,GuardtechNelipak,ChorleyITL,OxDevice,andWickhamMicrojustafewofthenamesarebackformoreinOnceagain,Med-TechExpowillbeheldTCT3SixtyattheinBirmingham.Welooktoseeingyouall,others,againin2023!
FEELING THE BUZZ
Expo review 18
Med-Tech Innovation Expo returned with a bang as over 100 exhibitors made their mark at the NEC in Birmingham in early June. Ian Bolland gives you a brief overview of what happened across the two days.
There was an international feel to this year’s edition of the show. With the Italian Trade Agency and the Economic Development Board of Mauritius accompanied by a cluster of medtech companies their countries had to offer, while the show floor also saw representation from Germany, China, Switzerland, the USA and Ireland among others. With seven ambitious innovators on the start-up zone, sponsored by NIHR, Innovate UK and SBRI, it was good to see the buzz about these young companies as they showcased their innovations and ideas, culminating in the Pitch@Med-Tech Innovation competition on the afternoon of the second day.
The Introducing HealthTech Stage also drew a lot of interest for its talks for breaking down the barriers for healthtech innovation, and advice on how to get a product into the NHS – while afternoon sessions also covered new approaches to treat mental health conditions, how to launch a new medical device during a pandemic and the pitfalls medtech innovators should avoid. The Med-Tech Innovation Conference Stage in association with Medilink had two days of discussion on pertinent issues that medtech is at the heart of. Speakers offered advice for start-ups, the opportunities for companies to grow beyond the UK, providing some insights of the opportunities that digital technologies can provide, while keynote speakers from Microsoft and Deloitte spoke about the need for a technological ecosystem surrounding social and research into innovation in diagnostics respectively. One highlight was a discussion hosted by Roche Diagnostics on how innovation can help rebalance health inequalities for women. COVID-19 has shone a light on all three of these particular issues and having expert insight like this certainly added to my knowledge, while audience members seemed particularly Forengaged.those who were unable to attend, you will be able to get a flavour of what was on offer on our Med-Tech Innovation Conference Stage on medtechnews.com in the near Med-Techfuture.
The Pitch was the last session of Day 2, and the second running of this saw a packedout Introducing Health-Tech Stage as Neuronostics fought off close competition of 10 other start-ups in this session of quick-fire presentations. The companies had two minutes to set out their innovation and pack as much important information, including whether their innovation was a gamechanger for the field it was operating in and could attract investors, meaning that it had to be a good business proposition too. Earlier on in the day we heard from many of the exhibitors on the show Thesefloor.talks ranged from the use of digital twins, some practical examples to improve medical device manufacturing, infection prevention measures that can be put into place to prevent HAIs and a personal look at the effects of the recently implemented EU Medical Device Regulation. The ever-changing nature of regulation was a hot topic on Day One as a live episode of The MedTalk Podcast addressed navigating the regulatory landscape. Not only was MDR touched upon, but also the effects of Brexit, IVDR, the effects of COVID-19, and what the medical device sector could learn from pharma as I was joined by Laurie Rowe from Red Medtech, Fiona Maini from Medidata and Ricky Lakhani from Pharmaseal and a big thank you to everyone who attended, we hope you got something out of it (and we could be back for more next year, watch this space).
MED TECH INNOVATION | expo
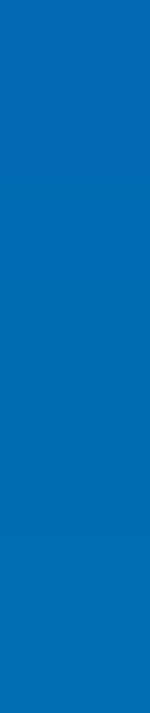
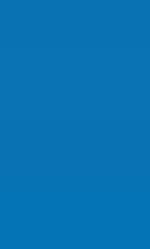
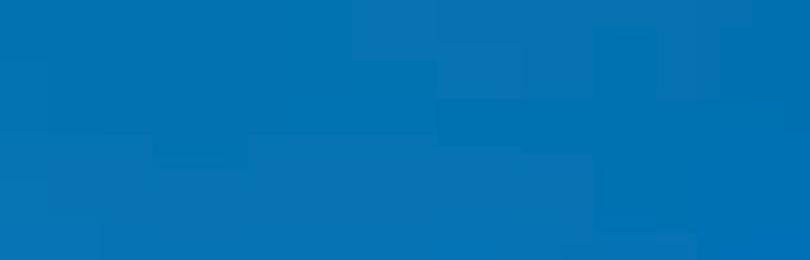


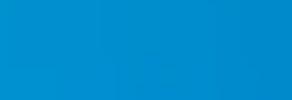
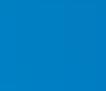
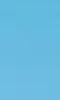
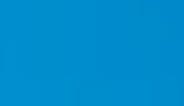
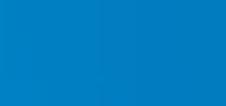
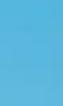
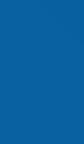
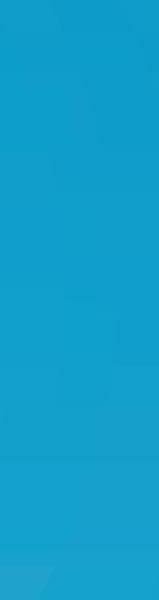

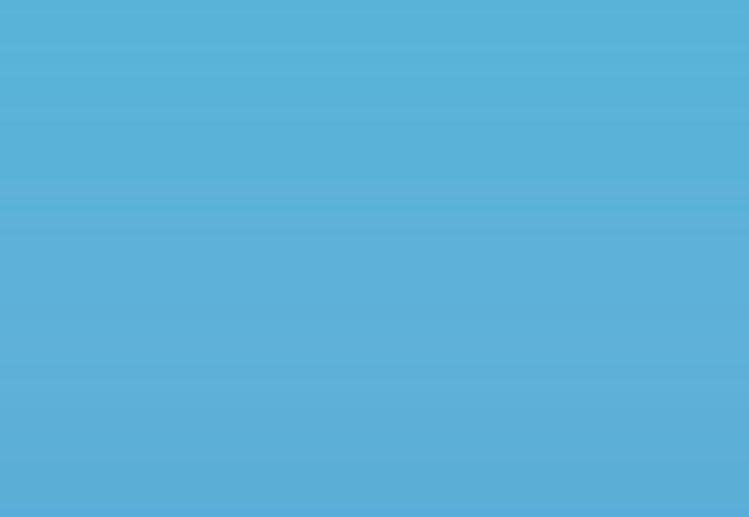
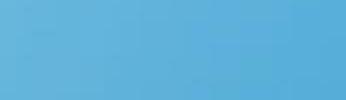
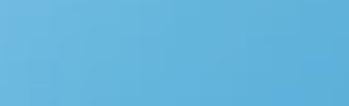
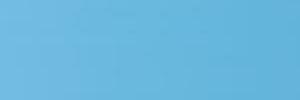
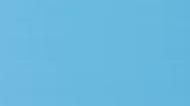
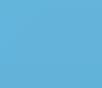
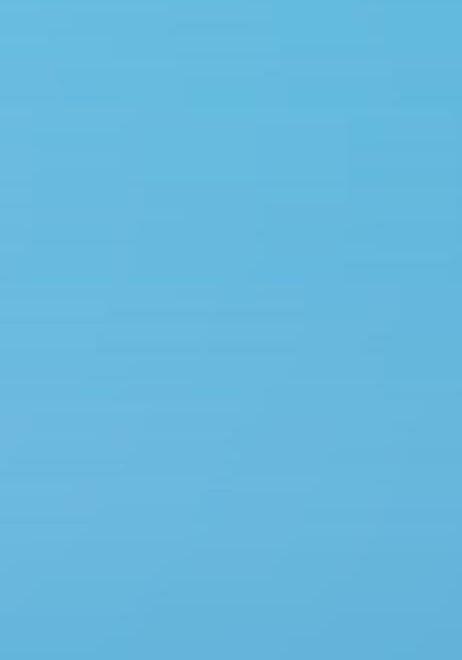
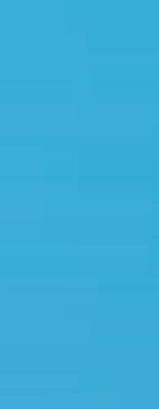
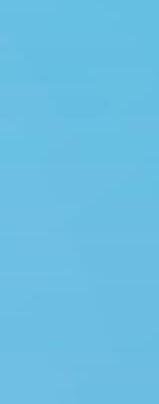
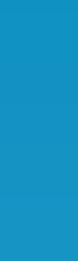
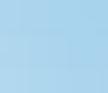
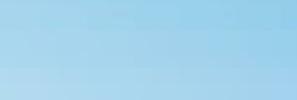
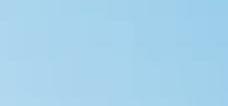
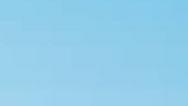
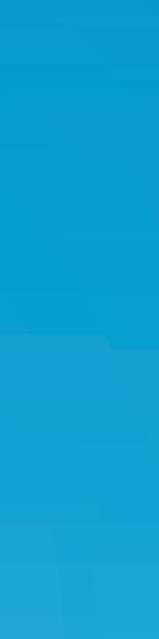

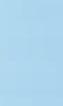
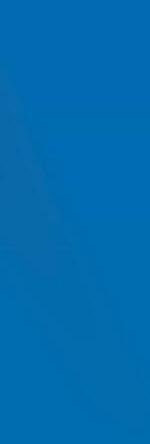
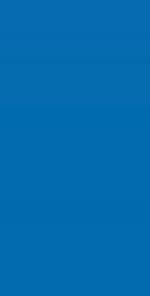
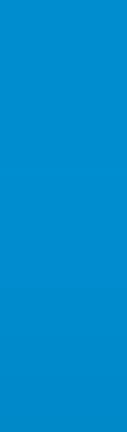
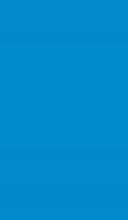
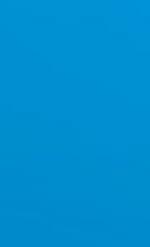

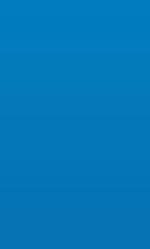
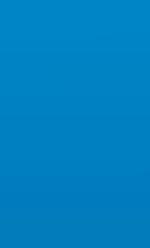
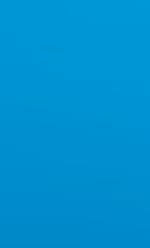
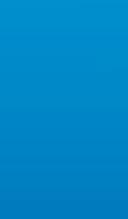
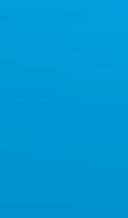



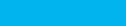
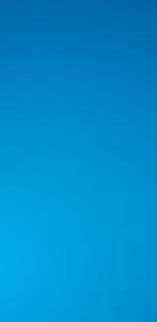
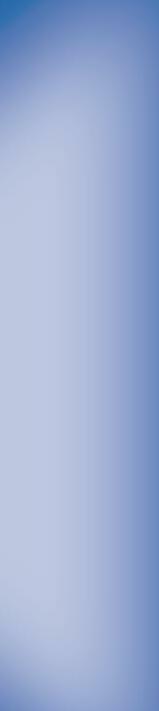
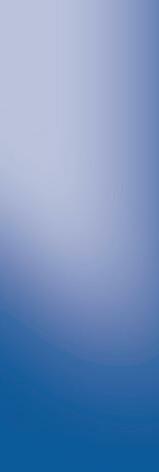
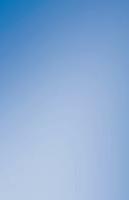
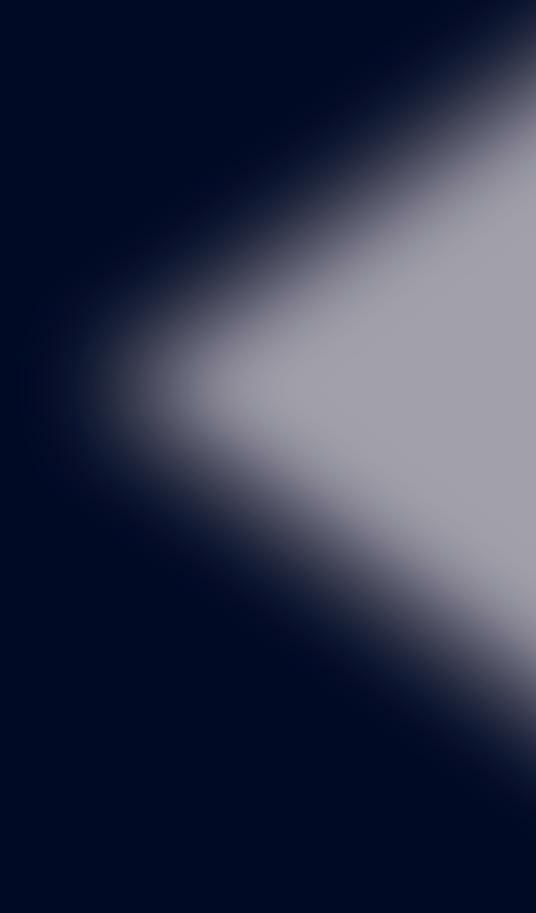
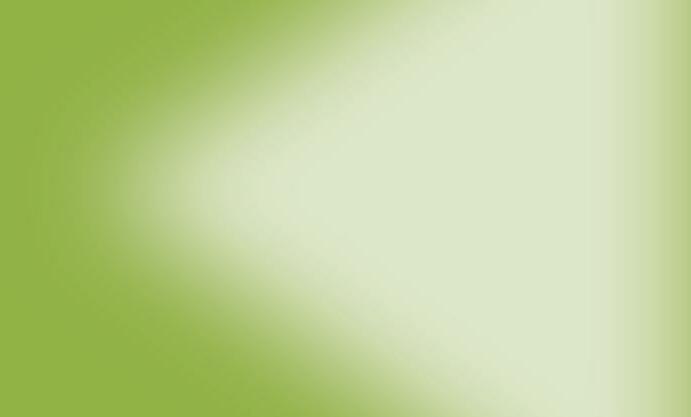
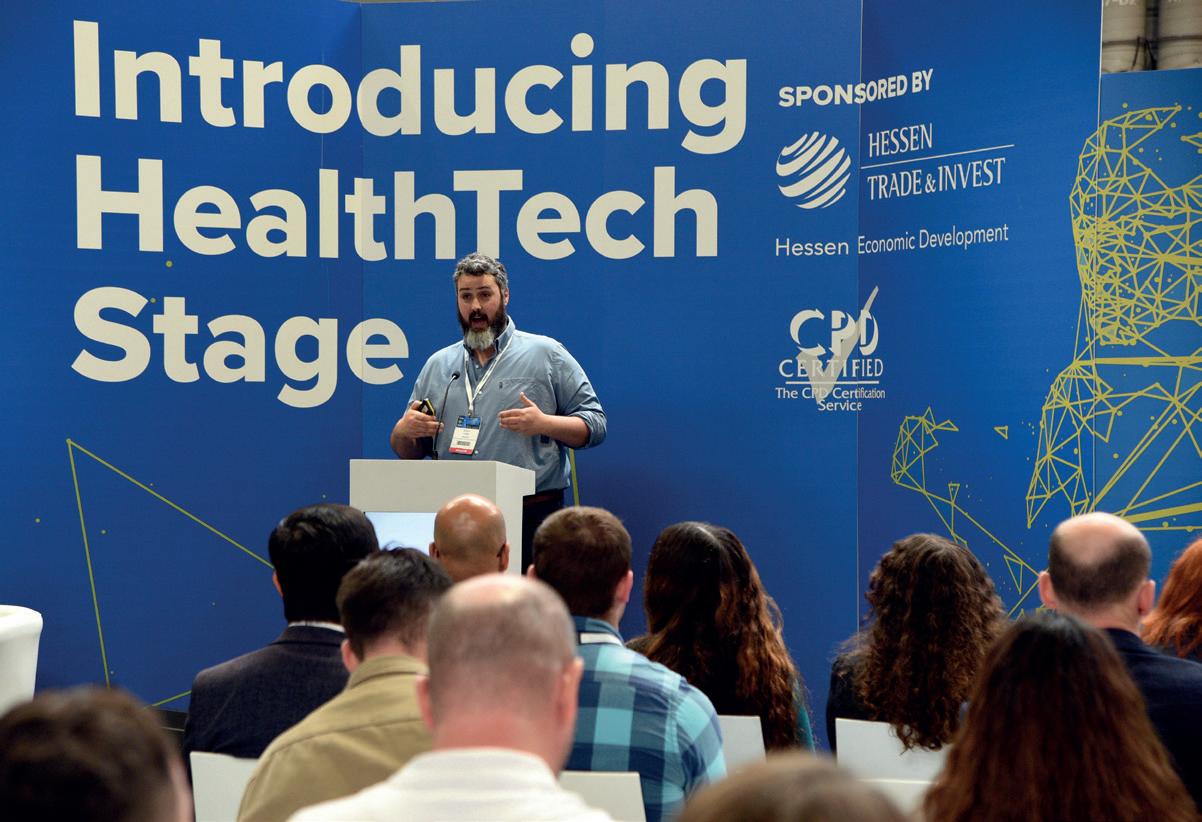
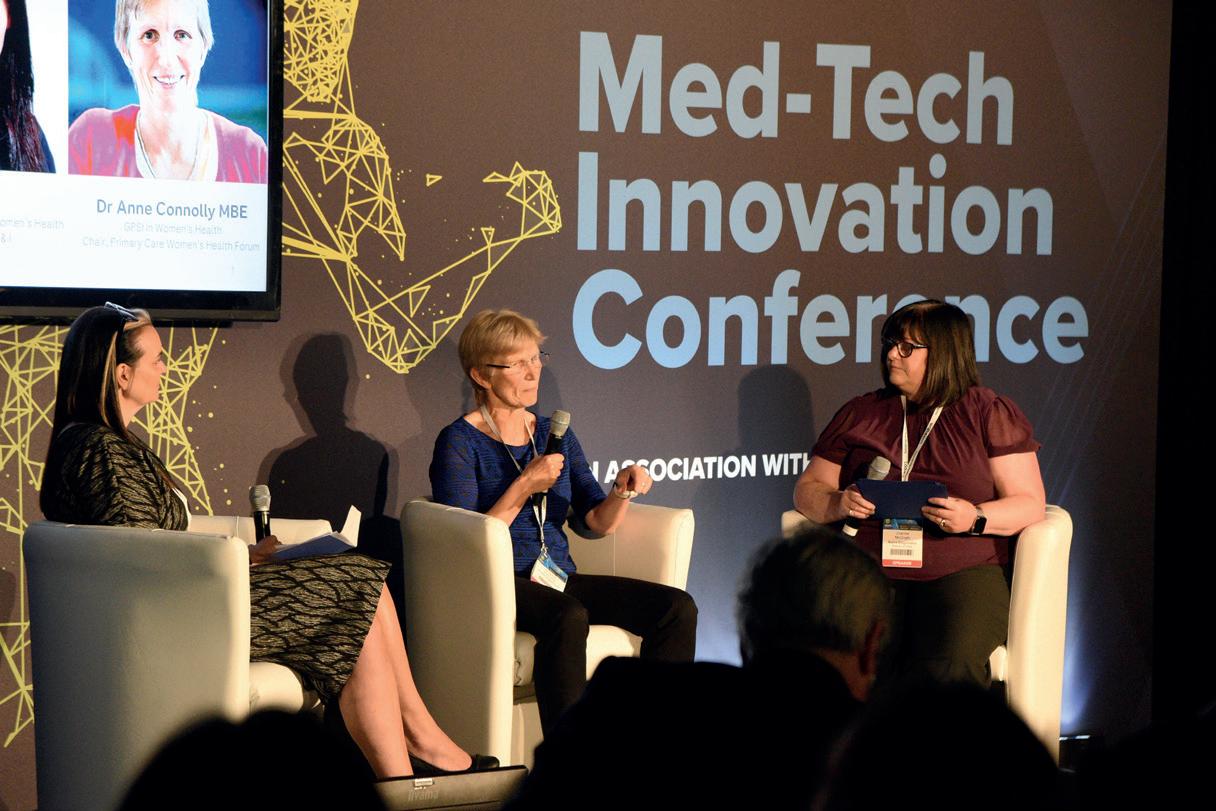
Coatings
The existence of healthcareassociated infections (HCAIs) presents a continual challenge in hygiene-critical medical environments such as hospitals. Healthcare providers face a constant battle to improve patient health and, at the same time, maintain an aseptic environment to limit the growth of HCAIsmicroorganisms.poseaserious threat to healthcare institutions, putting staff and patients at risk and incurring significant costs. In the period of 2016/17, 653,000 HCAIs were reported among 13.8 million adult in-patients in the NHS, of which 22,800 patients died as a direct consequence. Also, anxieties around the possibility of catching such a disease can also deter patients from seeking necessary treatment, as seen in the COVID-19 pandemic. Hospitals do everything in their remit to help combat this issue and combining enhanced cleaning practices with the implementation of preventative methods and technologies can be the best way to maintain a clean environment that is protected from microbial growth. Despite healthcare providers’ best efforts, the high volume of foot traffic through almost every hospital setting – including patients, staff, and visitors –can make it difficult to maintain a clean environment, particularly where it matters most on hightouch surfaces and medical devices. The incorporation of antimicrobial additives into healthcare furnishings and medical equipment at the point of manufacture is increasingly being seen as a key part of a systematic approach to keeping hospitals cleaner, with the healthcare segment accounting for almost 25% of the overall antimicrobial additives market by the end of 2018. This has resulted in a growing demand for medical products with antimicrobial features, as manufacturers worldwide seek biocompatible, biostable, and non-toxic antimicrobial coatings that are proven to be effective against a broad spectrum of microbes. These formulations can be added to a range of medical products and surfaces – from flooring and beds to trolleys and wall cladding – to help minimise the spread of microorganisms by inhibiting their growth on surfaces.
19
A prime example of this is the incorporation of antimicrobial technologies into the privacy curtains that separate each medical bay, a surface that is often susceptible to microbial growth. This technology can be built into the curtain to actively impart ongoing antimicrobial properties, effectively helping to reduce the growth of microorganisms on the surface. This type of technology can also be applied to medical devices, such as nebulisers, complementing good hygiene practices to help keep this hightouch device cleaner for longer. Whatever the application, this ‘always on’ technology works 24/7 to maintain a consistently lower bio-burden than would be expected on a product without antimicrobial protection.
PROTECTING MEDICAL DEVICES
Coatings for medical devices are also an excellent example of how antimicrobial protection can be used to improve cleanliness in healthcare facilities. HCAIs are often attributed to medical devices and associated cleaning lapses which can lead to microbial crosscontamination between surfaces. This presents a challenge to healthcare providers, which need to deliver appropriate treatment while simultaneously reducing the spread of microbes. The use of carefully engineered, long-lasting, built-in antimicrobial agents for supplementary product protection can make a significant contribution to the overall strategy, keeping these surfaces cleaner by reducing microbial colonisation. It isn’t just medical devices that can benefit from this type of antimicrobial product protection, as patients, visitors and medical professionals also come into contact with many other high-touch surfaces, including door handles, elevator buttons and toilet facilities. These coatings can also be applied to other hospital equipment, including mobile workstations, medication delivery carts and automated dispensing cabinets, contributing to a systematic approach to creating cleaner healthcare environments.
REDEFINING CLEAN IN HEALTHCARE SPACES Maintaining a clean, hygienic environment is critical to help limit the growth of microorganisms in healthcare settings. The use of antimicrobial technologies in various surfaces and products –from medical device coatings to soft furnishings – can supplement regular cleaning protocols to provide a longer-lasting effect and keep the environment cleaner between cleans. Building antimicrobial technologies into the coatings used for medical devices will provide long-term product protection that works around the clock to prevent the unwanted growth of microbes, without washing off or leaching out. Used as part of a comprehensive cleaning strategy to prevent contamination by microorganisms, this will give patients and medical professionals additional peace of mind in the battle against microbes.
Keeping healthcare environments cleaner for longer
Kimberley Cherrington, international marketing manager at Microban International looks at how built-in antimicrobial technologies can help to keep medical equipment and facilities cleaner for longer, by reducing the growth of microbes on surfaces.
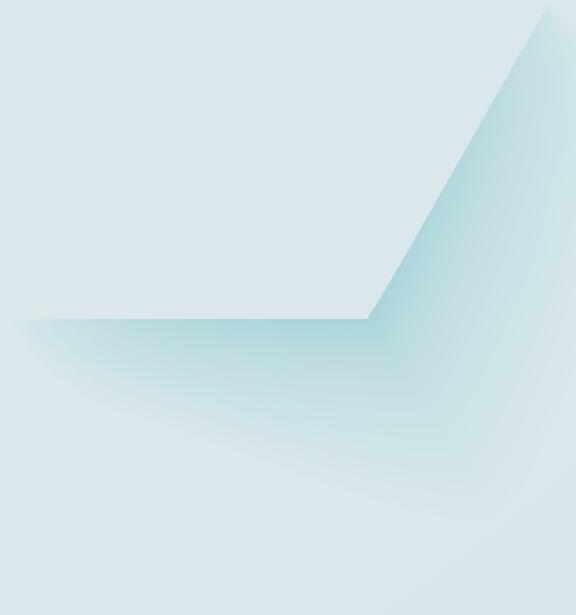

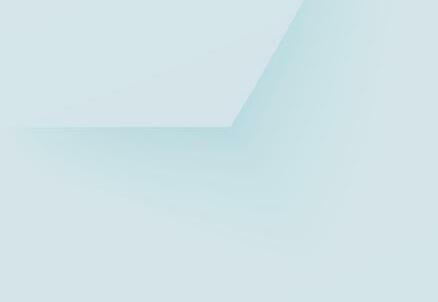
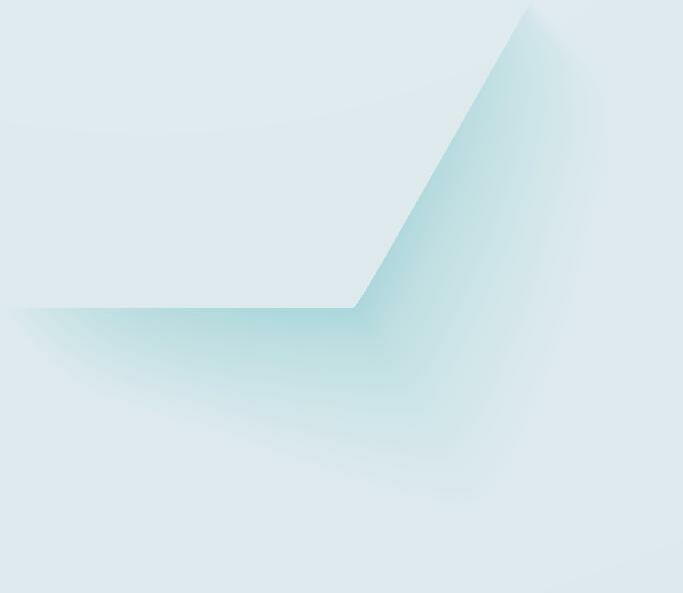




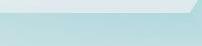
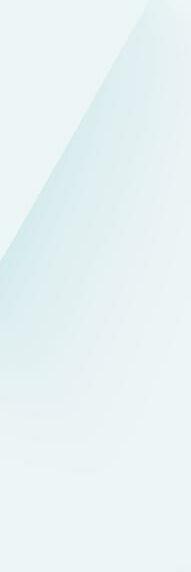
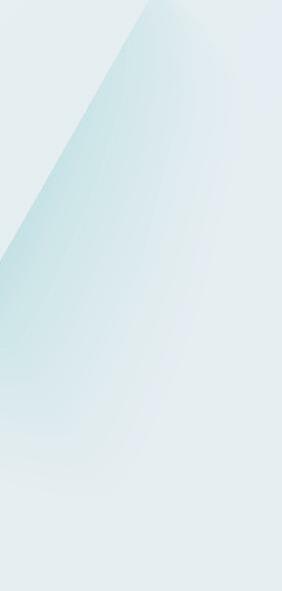



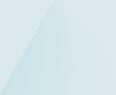
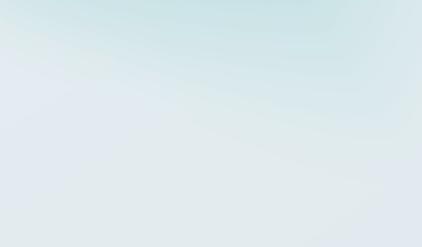
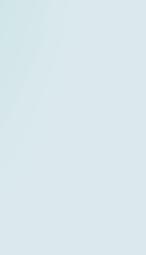

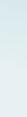
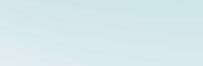

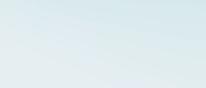

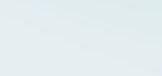


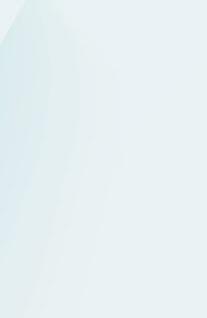



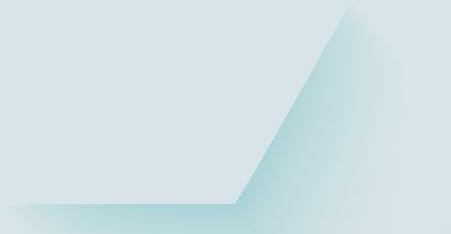




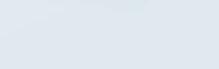
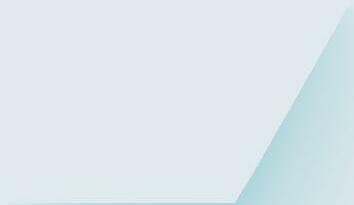



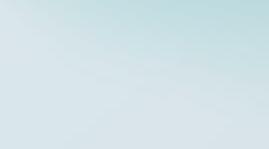



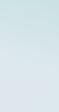


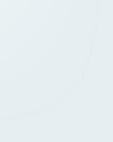
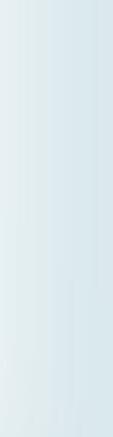
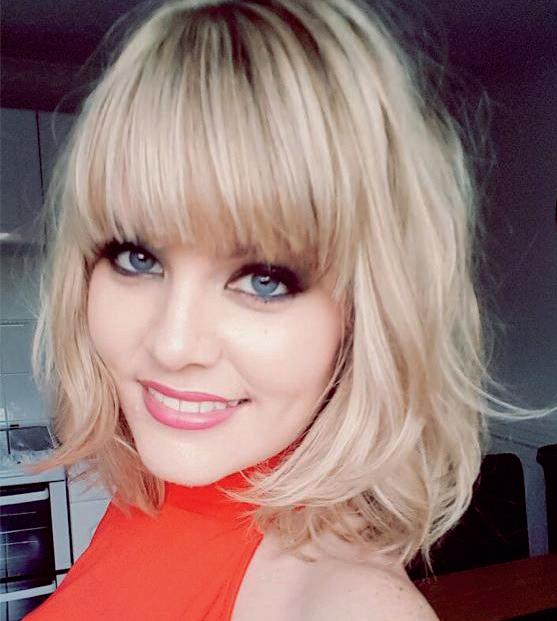
WHAT NEXT FOR ZIO? As the AI Award draws to a close later this year, these sites are using up their remaining Zio devices. The effectiveness of Zio in detecting cardiac arrythmias more accurately and at the first time of asking has been proven by the positive patient outcomes experienced across sites. So that sites have sufficient resource to prioritise all aspects of their day-to-day work, iRhythm is supporting them with their conversations with local commissioners, as they look to submit business cases for Variouscommissioning.longer-termtrusts,suchas North Bristol NHS Trust, outlined during the recent roundtable discussion their concerns about what a delay to longterm commissioning could mean for their workflows. Hatfield said: “The waiting list was horrendous before we were able to send so many Zio devices out to patients, and I’m worried that 24-hour monitor numbers will go back up if the Trust runs out of Zio devices to send to patients.”
Hatfield has shown her concern associated with returning to the previous way the Trust operated. According to 2020 research from Public Health England, approximately 2.4% of residents that live in the NHS Bristol, North Somerset and South Gloucestershire CCG are estimated to have atrial Northfibrillation.Bristol is one of numerous trial sites concerned with what the future will look like for their cardiology departments. Decisions will need to be made – at local commissioning perspective and at the national level – about how patients with suspected cardiac arrythmias can be best supported moving forward.
n September 2020, iRhythm Technologies was named as a winner of the NHSX (now the NHS ofwhilstbeenHoltertransitionwithEachredesigningespeciallywithouthealthtechnologiesImplementinglongerthoselandscape,forThistesting,accuracy,alsolowaperiodelectrodes.todueburdensome,canheartsuspectedtheHolterBeforeselectedatcompanyenablingDirectorate)TransformationAIAward,thedigitalhealthcaretotrialitsZioservicescaleacrossarangeoftrustsinEngland.Zio’simplementation,monitorswere‘norm’formonitoringarrythmiasandconditions.Thesebeviewedasoutdated,andnoticeabletotheirsizeandtheneedhavewiresconnectedtoTheshorttestingtypicallyseenwithHolter(24-48hours),andpatientcompliancehadledtoconcernsaboutleadingtorepeatorevenmisdiagnosis.demonstratedaneedchangewithinthehealthespeciallyforpatientsrequiringmonitoringperiods.innovativewithinthesectordoesn’tcomeitschallenges,whenitalsomeanspatientpathways.siteworkedcloselyiRhythmtoensurethefromtraditionalmonitorstoZiohasasseamlessaspossible,consideringtheneedscliniciansandpatientsalike.
20 DIGITAL HEALTH sponsored
Improving health outcomes: Where now for cardiology? I
CLINICIAN WORKFLOWS
ACCURACY Zio is worn by patients for up to 14 days and analyses the vast amount of data collected over that period using an AI-powered algorithm. Longer monitoring provides a more comprehensive picture of a patients’ heart rhythm, which was particularly seen by Barts Health NHS Trust. The Trust’s consultant stroke physician, Ollie Spooner, mentioned that “96% of its two weeks recording was analysable,” which was the same in the more functionally impaired group, and that “repeat testing for inconclusive results overall, was only 1%.”
During iRhythm’s recent roundtable with the sites it currently operates in, a common theme amongst clinicians was the timesavings that Zio has allowed. Releasing resource and capacity has enabled clinical teams to focus on all aspects of their day-to-day work.
20
East Kent has been working through its waiting list of patients with comeslackensuringcardiovascularsuspectedconditions,thereisadistinctofambiguitywhenittoactionsrequired to understand their condition.
Followingby a roundtable discussion held in 2021 with Liverpool Heart and Chest Hospital, iRhythm heard from NHS sites in East Kent, Barts and North Bristol about Zio’s impact, and what the future looks like for their trusts beyond the conclusion of the AI in Health and Care Award.
Speaking about the data that her hospital has collected to date, Mellissa Baker, lead physiologist at East Kent Hospitals University NHS Foundation Trust, mentioned they have “definitely seen reductions in waiting times for monitoring, fitting, and analysis, and its stroke service has seen an overall RTT pathway reduction.” In turn, this has created “quite a lot of time saved”, “when looking at the 3,000 patients they’ve seen so far.”
CHALLENGES Getting to grips with new technology isn’t always a straight-forward process, and this has been experienced at times by the sites’ staff. Suzanne Hatfield, physiology manager at North Bristol NHS Trust, agreed that behind the scenes, although the implementation of Zio did improve workflow efficiencies and reduce the burden on clinicians’ time, it did create more administrative work for Hatfieldthemselves.explained that, in some instances, the Trust had some enquiries from patients about what they could or couldn’t do while wearing the device. However, Mel Baker from East Kent acknowledged that, as Zio becomes more commonplace these administrative processes will become smoother.
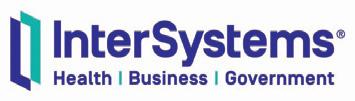
GETTING CONNECTED Surely, the biggest data and analytics trend right now and one that will surely continue for years to come is the Internet of Things (IoT). And for good reason. The IoT enables organisations to collect and integrate data from various internet connected devices, or “things” with sensors, and automatically apply analytics to them. Because IoT platforms can pinpoint exactly what information is useful and what can safely be ignored, it negates the need for human intervention. This can reduce time to action and improving understanding of what interventions will help citizens. The IoT can be used to detect patterns, recommendations,makeand detect possible problems before they occur. The move towards an inter-connected IoT is staggering. IoT Analytics expects the global number of connected IoT devices to grow 18%, to 14.5 billion active endpoints this year. The Internet of Medical Things (IoMT), in particular, is set to skyrocket. The global spend on IoT in healthcare is forecast to grow to $260.75 billion by 2027, at a CAGR of 19.8%. The market growth is driven by increasing focus on active patient engagement and patient-centric care, growth of high-speed network technologies for IoT connectivity, and the surging need for the adoption of cost-control measures in the healthcare sector. A PARADIGM SHIFT With the IoT, data comes to the fore. practitionersMedicalcanuse this real-time data to render immediate services and track resources such as staff, assets, patients, and more. Through more significant use of personal devices such as smartwatches, medical practitioners can collect data on sleep patterns, blood pressure, ECG patterns, and more to enable realtime assessment of patients. It is a paradigm shift in care. Especially for elderly patients, as they can now continue their care in the comfort of their own home. The fact that IoT allows a constant tracking of their health conditions without any major disturbance to their daily life is a big plus for Throughpatients.the IoT, digital leaders have more information available than ever before. Think of adult social care. By using data, and working as part of an integrated care system, healthcare professionals can understand what the demand is going to be by each patient. They can better know who ‘Molly’ is, when she’s likely to hit the system and what support she’ll need. They can also ascertain who is best placed to support her, and what in-home technology solutions can be used to assist in her care.
improveservicetechniquestechnologiessomecapabilitiespotentialorganisationsyears,OverTheseforofimprovementssignificantinthematurityorganisationalcapabilitiesdigitalanddata.areexcitingtimes.thecomingmonthsandweexpecthealthcaretoharnesstheoftheseenhancedandworkwithofthemostadvancedandanalyticaltotransformprovisionandthelivesofpatients.
THE INTERNET OF THINGS: A WIN, WIN FOR HEALTHCARE
sponsored by DIGITAL HEALTH 21
We are transformativebehindleavingaradicallytime for healthcare. Not that long ago, pen and paper remained the primary means of recording patient information. However, since the onset of the pandemic, many healthcare organisations have accelerated their digital transformation programmes and achieved
Dora Mitter, data strategy and insights consultant at Agilisys, summaries the shift to internet of things and its effects.
OUTCOMESBENEFITTING Apart from monitoring patients’ health, there are many other areas where IoT devices are very useful in hospitals. IoT sensors can be used to track real time location of medical equipment like wheelchairs, defibrillators, nebulizers, oxygen pumps and other monitoring equipment. They can also help in asset management like pharmacy inventory control, and environmental monitoring, for instance, to check refrigerator temperature and humidity control. IoT sensors can help with human assets too. Through analysing where staff are located, staff can be deployed across different locations to ease pinch Throughpoints.the power of the IoT, the use of data in providing optimum care is coming to the fore. Realtime monitoring systems and connected devices are being leveraged to gather extensive data recording and analysis. Underpinned by AI (Artificial Intelligence), the IoT is revolutionising patient care and minimising errors. It has improved functional efficiency, enabled better patient care, improved disease management, and benefitted treatment outcomes. Overall, the use of IoT in healthcare is making care more cost-effective, thanks to early detection and intervention. It’s a win, win.
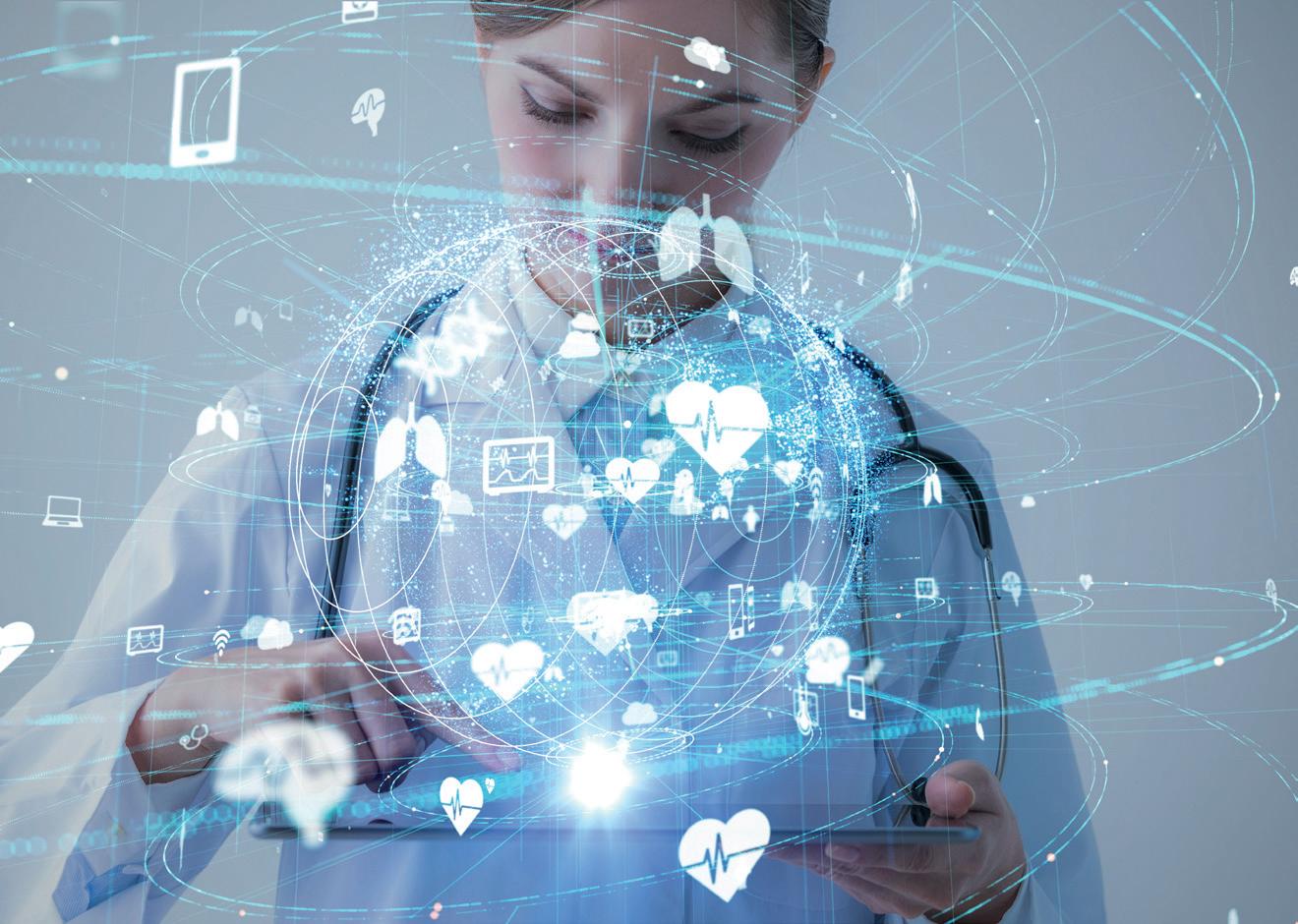
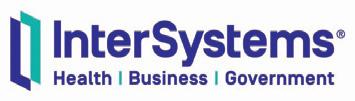
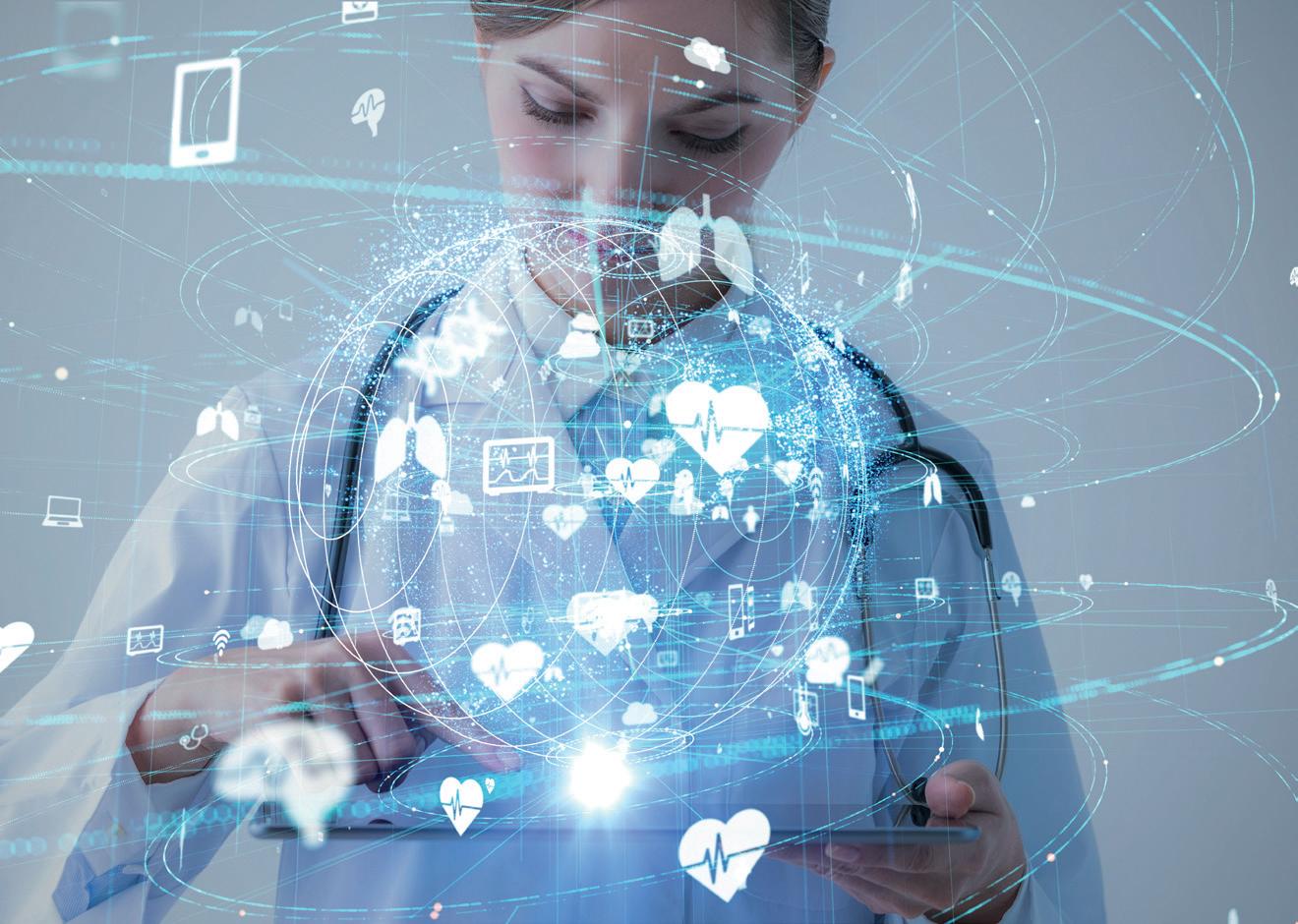
irst, congratulations on winning the Pitch competition. How did you feel when you were declared the winner? Wow, it was a pretty amazing feeling. With 10 other start-ups, all working on great ideas and tech, the field was tough. When the panel chair was giving feedback on what constituted a good pitch, I was mentally ticking off the aspects we’d covered. So come the end I was thinking we were in with half a shout, but it was still amazing for Neuronostics to be announced as the winner. And whilst I’m the front of house, so to speak, it’s really a team effort and a great reflection of the hard work everyone is putting in! For those who weren't in attendance, tell us about Neuronostics? We’re on a mission to revolutionise diagnosis and prognosis of neurological conditions. Spun out of the University of Exeter in 2018, we’re currently developing a cloud-based platform to support clinical decision making in epilepsy. Right now, we’re a team of 10 with scientific, technical, commercial, and clinical expertise based in the heart of Bristol at the Engine Shed. We’re part of the SETsquared accelerator, which is a fantastic community that supports emerging companies with a focus on tech. What does your innovation do that others don't in the area of epilepsy? At present, if you want to confirm a case of epilepsy you really need to see a seizure, or a signature of a seizure, in a clinical test called an EEG. This test measures the large-scale electrical activity of the brain, which can become disrupted and result in a seizure. However, most people with epilepsy most of the time don’t have seizures and so their electrical activity appears apparently normal. This makes diagnosis very challenging. In contrast, we have developed an approach that enables us to create a personalised computer model of the brain that is informed by these apparently normal EEG recordings. We use this model to understand how easy it is for seizures to emerge, and this ease informs a risk score that we call BioEP (short for Biomarker of Epilepsy). We provide a report to the treating neurologist, who can use the risk score alongside other information they have collected to determine the most appropriate next steps for the person with suspected Byepilepsy.analogy, imagine going to the mechanic suspecting there is something wrong with your car and the mechanic asks you to A
HEAD –NEURONOSTICS INNOVATIONPITCH@MED-TECHTAKESCROWN START P: MEET THE
F
John Terry, co-founder and managing director of Neurnostics, speaks to Med-Tech Innovation News after the company took the 2022 Pitch@Med-Tech Innovation prize.
2222 TUBING
WINNER BY
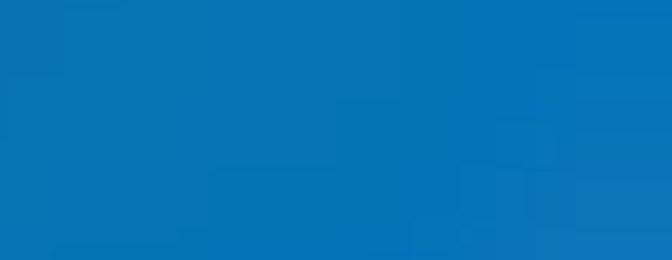
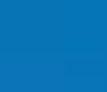


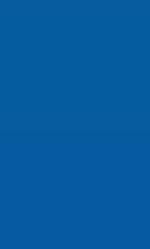
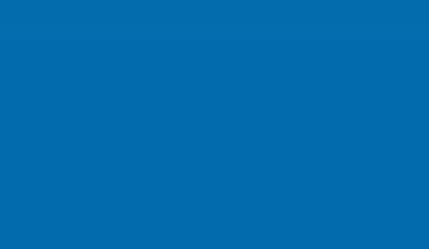
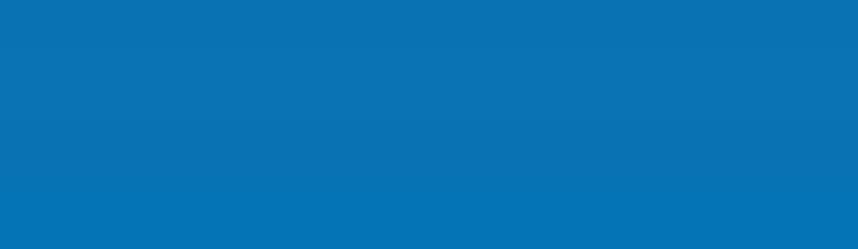
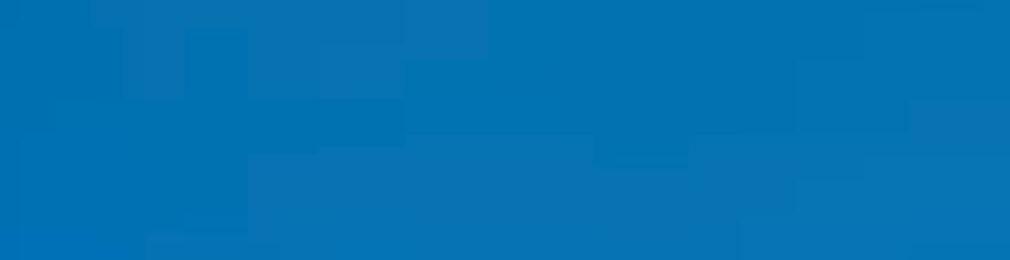
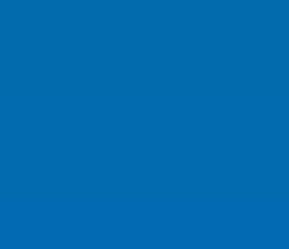
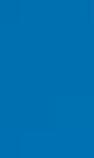
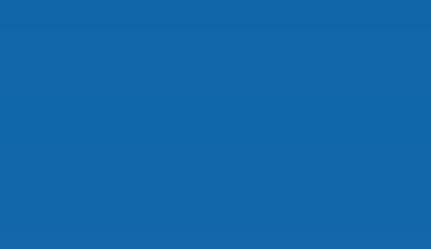
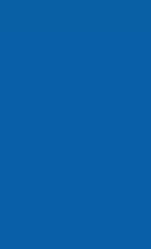
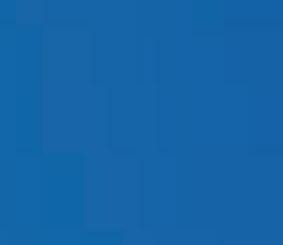
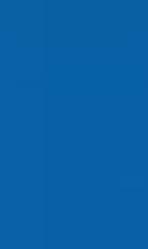
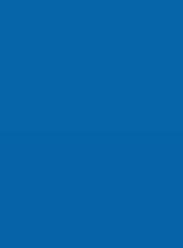
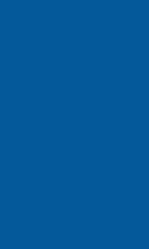
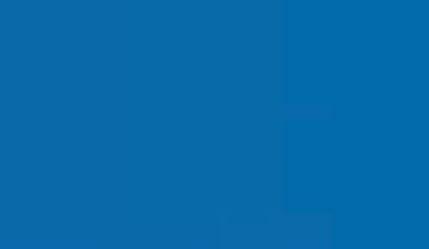
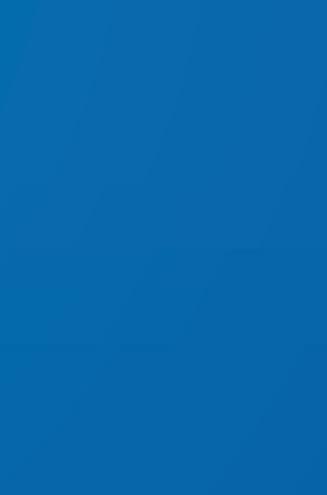
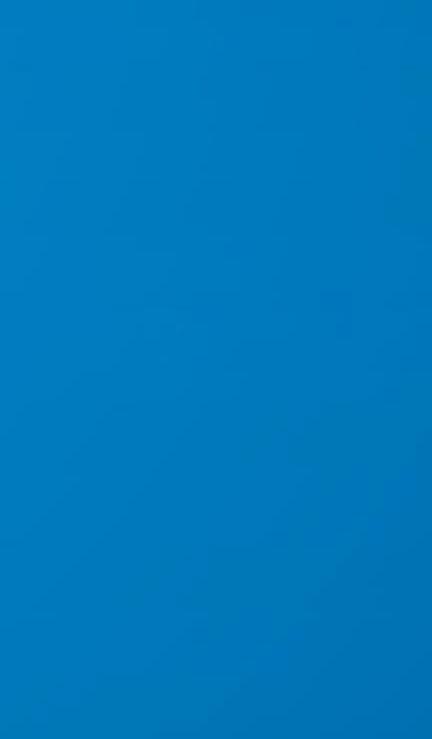
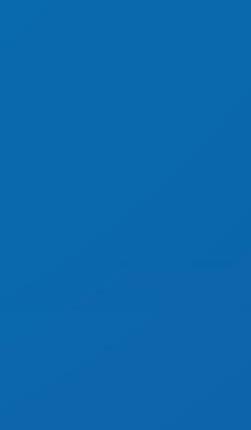
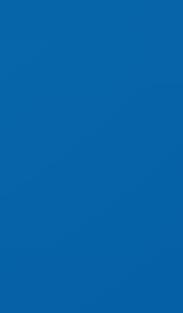

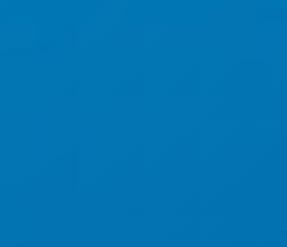
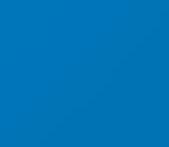

















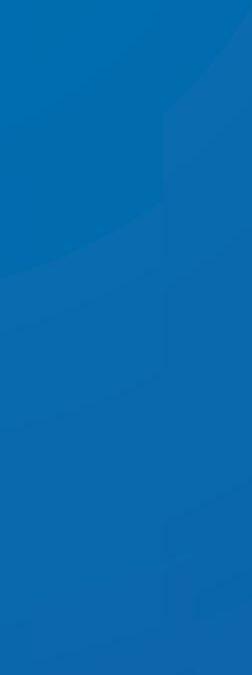
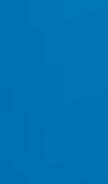
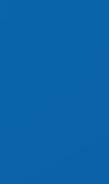
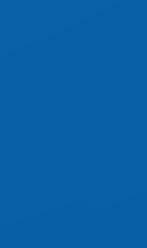
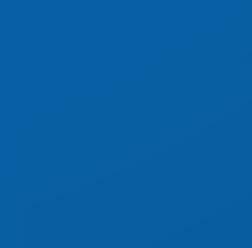

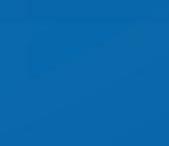


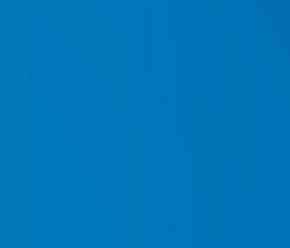

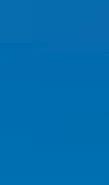
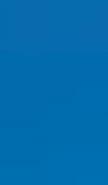
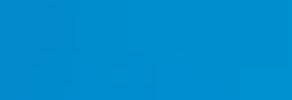
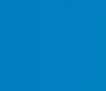
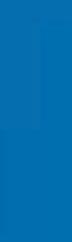
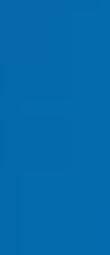
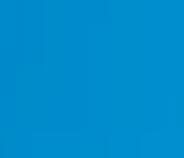
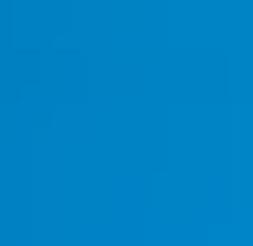
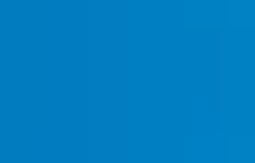
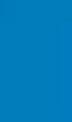

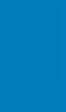
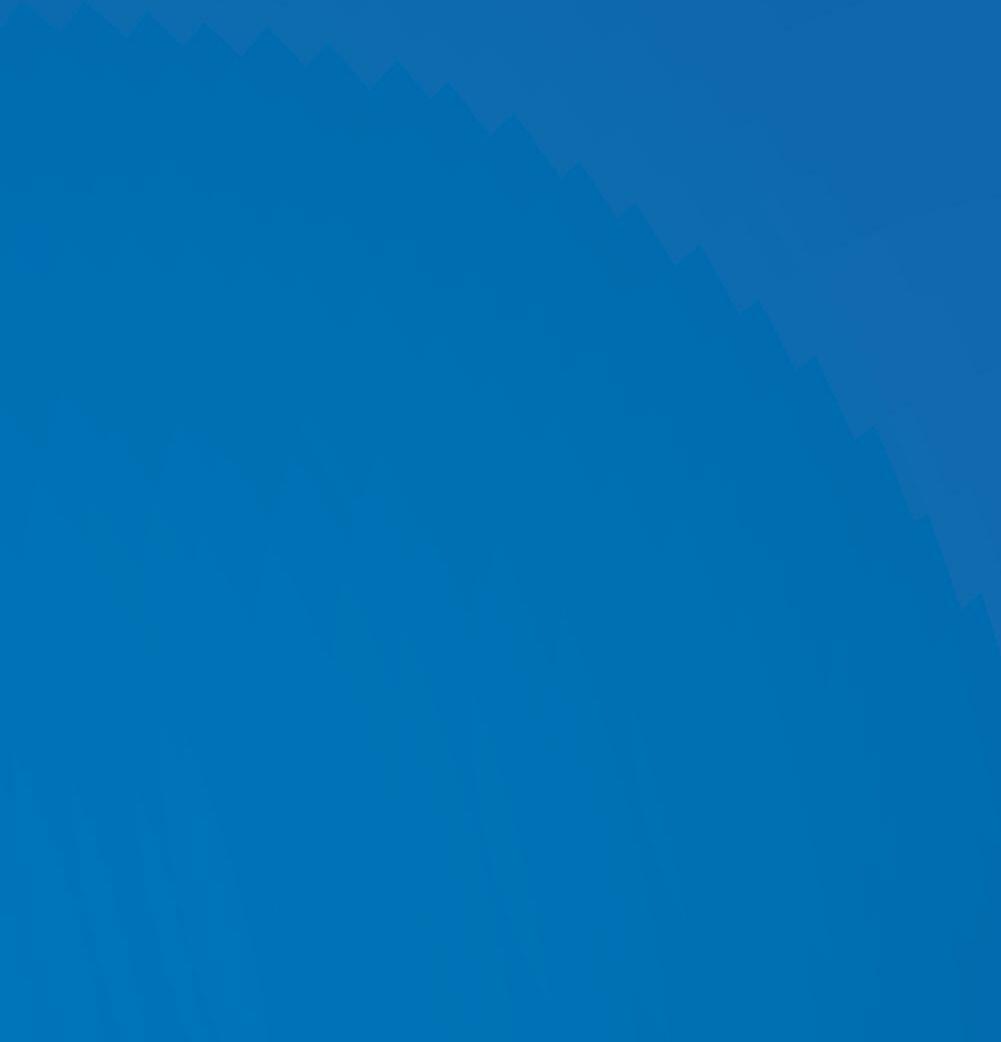
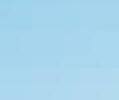
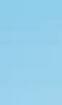
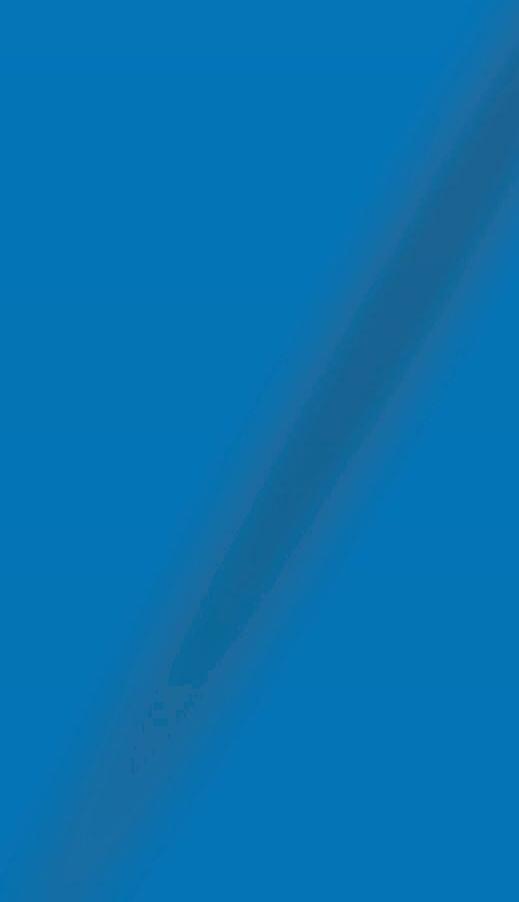
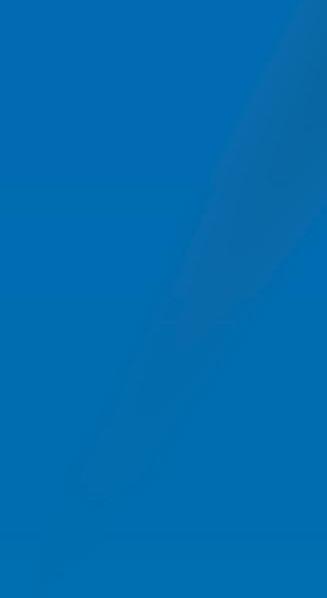
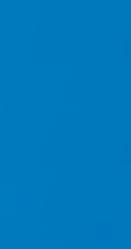
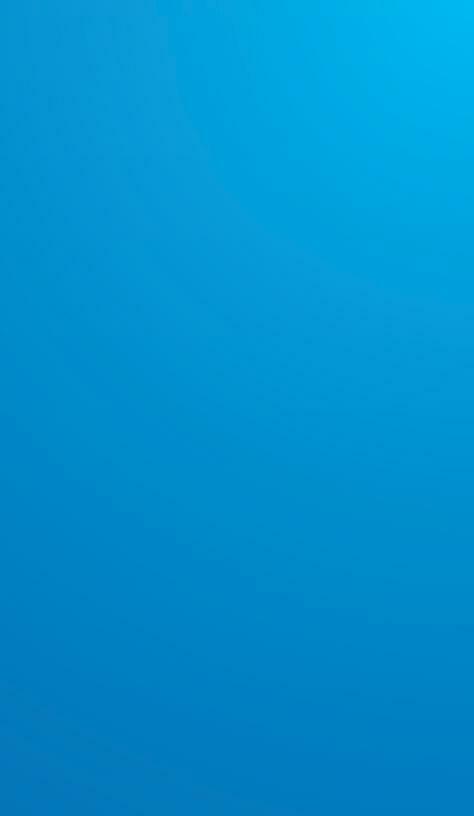

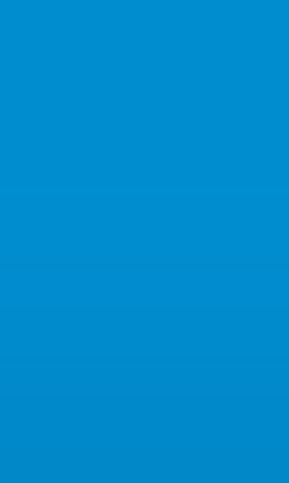
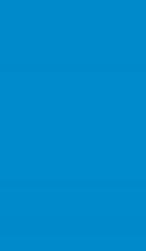
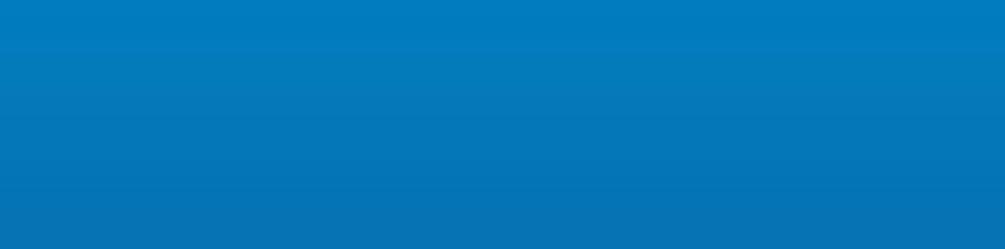
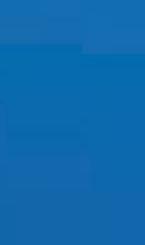
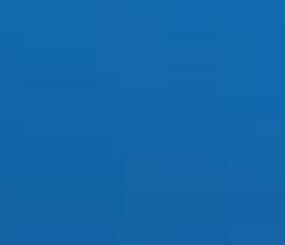
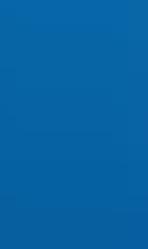
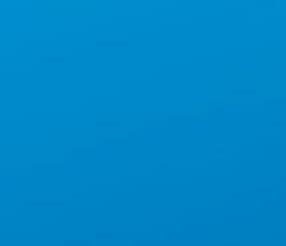
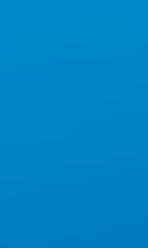


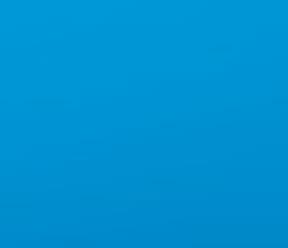
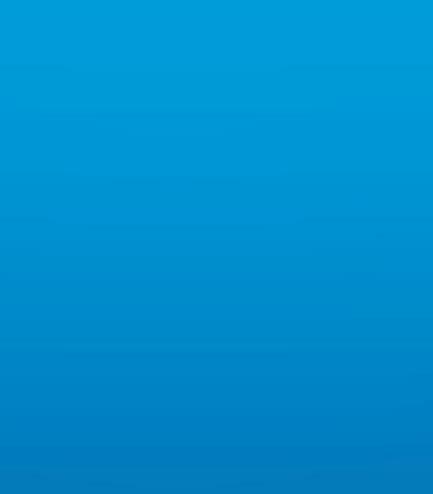
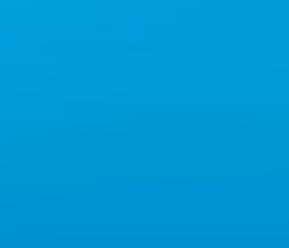
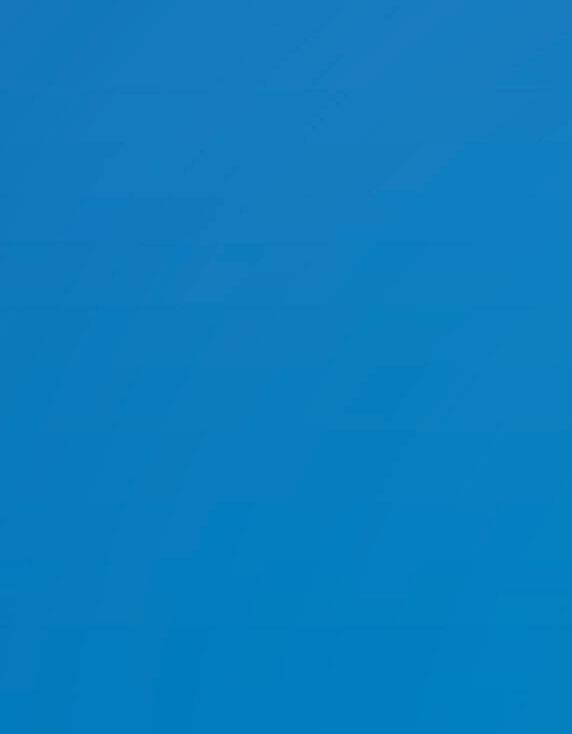
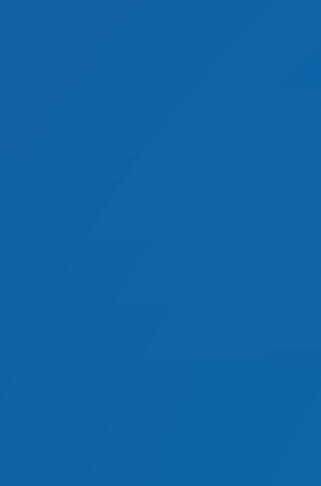
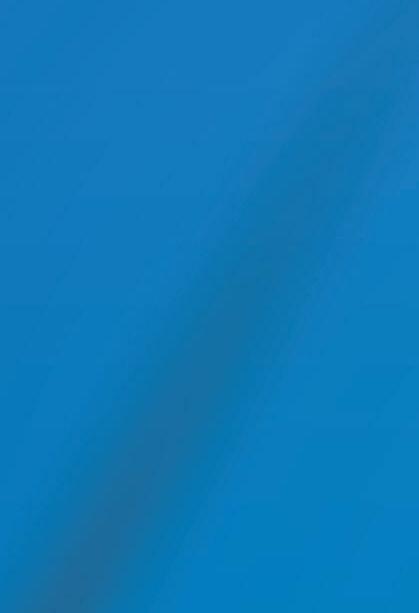
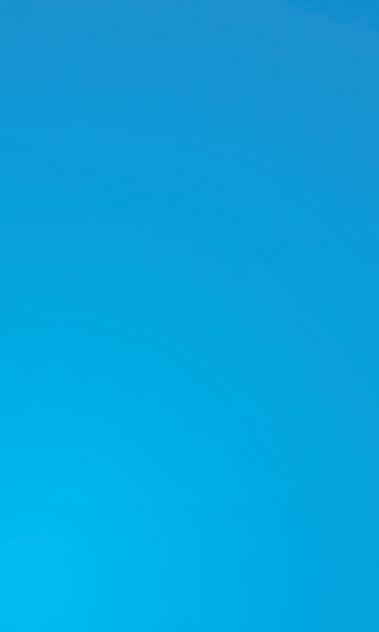

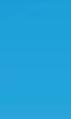
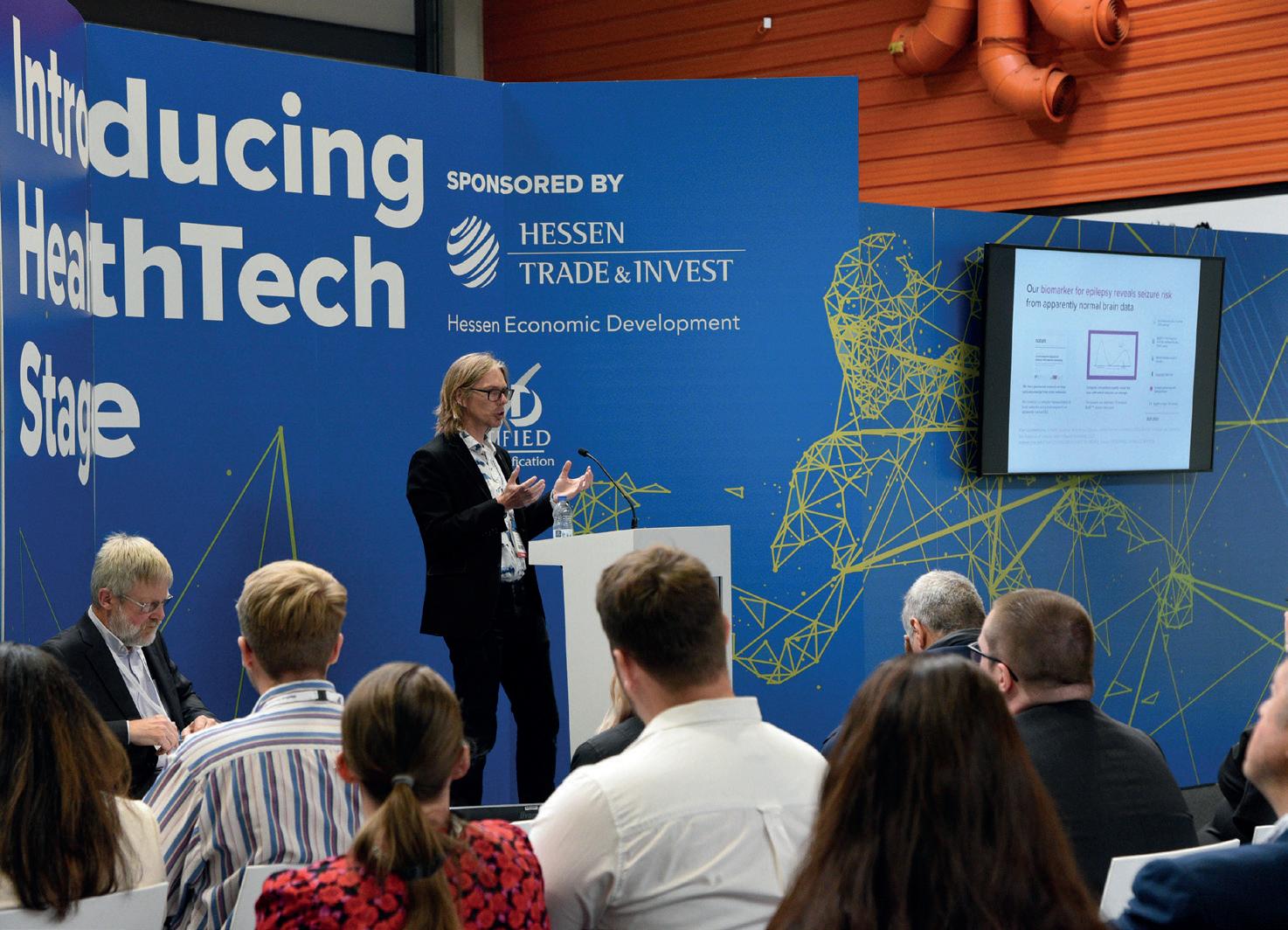
What kind of support have you received in recent years? We’ve been really fortunate to have received significant financial and business development support. We’ve received over £1.5 million in grant funding from Innovate UK and NIHR, as well as smaller grants from the West of England Business Innovation Fund and the Epilepsy Foundation. Last year we also closed an oversubscribed pre-seed round, raising £300,000 from a group of nine angel investors. However, beyond the financial support we’ve also really benefited from belonging to communities like SETsquared, as well as being a part of the Creative Destruction Laboratory. We’ve just graduated from the scheme, and this provided us with access to a range of mentors with global expertise in the medtech space.
TUBING 23 drive down the road so they can observe what happens. If you fail to brake effectively and crash, only then does the mechanic realise there’s a problem with your tyres. This is effectively how epilepsy diagnosis works at present. For cars we have markers of tyre or brake wear that tells us when we need to replace them to reduce the risk of accidents. Until now, we haven’t had robust markers of future seizure risk. Our innovation – BioEP – provides this. Can you tell us what kind of work has gone into the development of this biomarker? For the first few years, we were focused on fundamental research. By this I mean creating mathematical models that could describe the transition between apparently healthy brain states and pathological brain states (such as seizures). At first these models described the brain activity within a single region of the brain, but over time we extended them to describe an interacting network of brain regions. In this description the emergence of seizures can be due to alterations in the brain network or the brain dynamics within a region or regions, or even a combination of both. From these early theoretical studies, we then sought evidence that these mechanisms could exist in the human brain. To do this, we have worked really closely with clinicians and people with epilepsy to develop a carefully controlled database of human EEG recordings. From these recordings we found evidence that the mechanisms we proposed theoretically were present in many people with epilepsy. This exciting finding ultimately led to the development of BioEP. At the heart of your development appears to be a seizure risk score, how did you develop something that can quantify the risk of such events? Building from our research, we developed a suite of patented algorithms that could extract information about brain networks from clinical EEG recordings that are collected routinely as part of the diagnostic journey for someone with suspected epilepsy. We use these recordings to create a patient-specific representation of the brain. Simulating the model under a variety of different conditions gives you an indication of how easily the specific brain network can enable transitions into seizure like brain states. This likelihood informs the risk score.
Building from our research, we developed a suite of patented algorithms that could extract information about brain networks from clinical EEG recordings that are collected routinely as part of the diagnostic journey for someone with suspected epilepsy
What next for Neuronostics? We’ve just launched our next funding round, which will enable us to complete prospective studies of the BioEP technology, as well as to develop new markers for other clinical indications such as autism, dementia, and traumatic brain injury. These are all conditions that commonly co-exist with epilepsy. Anything else that you'd like to tell us? We’d love to hear from people who can contribute to our mission to revolutionise diagnosis and prognosis of neurological conditions. Whether you are a person with a neurological condition, a clinician interested in using our technology or demonstrating its efficacy, an industry partner with whom we can collaborate or an investor looking to support us on our journey feel free to reach out on info@ neuronostics.com.
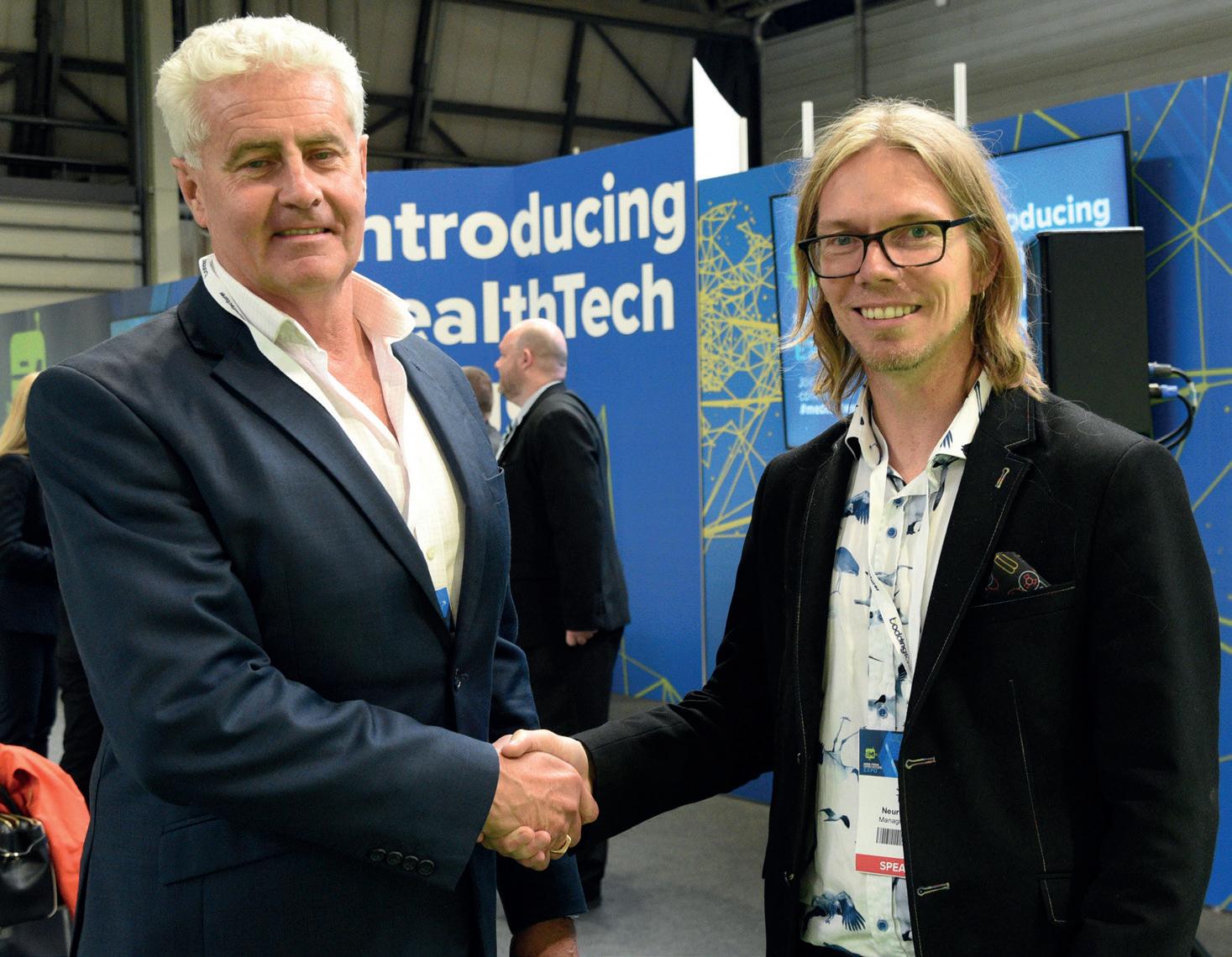
























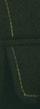



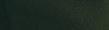



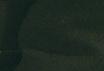















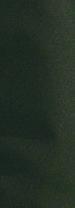


























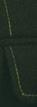














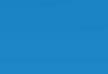
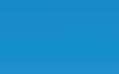

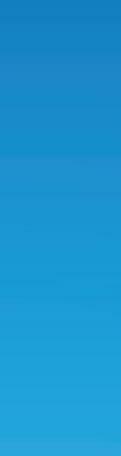
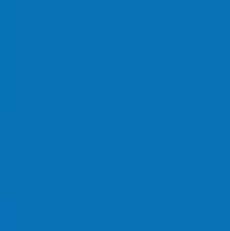
24 Packaging
Quality assurance hampers the use of POC and home testing kits in some LMICs, so providing greater clarity in this area is of immense benefit to brands, manufacturers, and end users alike. Smart packaging solutions, such as track and trace, RFID and QR code technologies, contribute towards improved stock control and quality management systems. Incorporating lighter, alternative materials into the design of diagnostic device packaging can contribute to reductions in size and weight, making it easier to transport and store products. Carton packs are particularly useful because they are light and can be formed to incorporate in-built crumple zones and tamper-evident security features, without the need for plastics keeping sustainability and recyclability front of mind too.
THE RISE OF PROACTIVEDIAGNOSTICSHOMEANDSELF-CARE
It estimates approximately 1.1 million premature deaths could be avoided annually by prioritising the use of diagnostics in Low to Middle Income Countries (LMICs).6
Whilst progress has been made for some viruses, such as HIV and Zika, several complex issues remain for manufacturers of point-of-care (‘POC’) and athome testing devices in certain regions. With little appetite for investment in LMIC diagnostics, financial barriers are concerning for vulnerable populations, and this is compounded by supply chain, logistical and geographical challenges. The likelihood is that diagnostic technology will be required to further evolve to meet the demands of specific locations.
Marga Romo of Essentra Packaging investigates the rise in demand for at-home diagnostics and the role of packaging.
Arapidly increasing number of global consumers are taking greater interest in and control of their personal health and wellbeing. A recent Global Health & Wellness Study of 17 Markets carried out by NielsenIQ reported 48% of global consumers regularly make proactive health and wellness choices1 and these healthconscious consumers are driving the phenomenal growth of the over-the-counter home diagnostics market. The home care and testing market is enabling consumers to gain greater control over their everyday wellbeing. Test kits conveniently and affordably purchased overthe-counter or online provide rapid results without the need for traditional referrals and, in many cases, laboratories. The process is discreet, personalised, and fast. At-home testing kits can be used to detect a vast range of conditions, including infectious diseases, health issues, allergies, deficiencies, pregnancies, and substance abuse. The testing kits vary from cassettes and midstream applications to strips, test panels and dip cards, but they are all designed with simplicity of use and affordability in mind. The Home Diagnostics Market Insiders 2021-20312 report compiled by Transparency Market Research revealed the most widely used at-home diagnostic device is the glucose monitoring kit. The soaring number of adults living with diabetes no doubt contributes to the continued growth of this market segment. According to the International Diabetes Federation, 537 million adults are living with diabetes worldwide, a figure that is expected to increase to 783 million by Whilst2045.3glucose testing kits dominate the market, there has been a noticeable shift in the use of wider home diagnostics following the COVID-19 pandemic. Not only did the pandemic led to a huge surge in demand for COVID-19 home testing kits, but global lockdown restrictions resulted in fewer people accessing traditional healthcare services and more acquiring a greater interest in managing their personal health and wellness. These factors combined to accelerate the market’s growth. FutureWise Market Research & Consulting now forecasts growth of over 5% by 2028, with a projected market value of $7.6 billion.4 Despite its substantial growth, the market faces several challenges. Calls for equitable access to diagnostics are increasing. According to the ESOMAR-certified market research company, Fact. MR, the US accounts for 40% of the industry’s market revenue and the European market is buoyant in the UK, France and Germany.5 However, the industry has yet to successfully penetrate lowand middle-income countries. Limited access to diagnostic equipment leaves the most vulnerable exposed to the risks associated with the pandemic and other infectious diseases. The Lancet’s commission on diagnostics, Transforming Access to Diagnostics, reveals “47% of the global population has little or no access to diagnostics.”
6. 5/fulltextlancet/article/PIIS0140-6736(21)00673-https://www.thelancet.com/journals/
References: 1. wellness-revolution/#chapter-12021-global-consumer-health-and-report/2021/an-inside-look-into-the-https://nielseniq.com/global/en/insights/
4. Diagnostics/181healthcare-market-research/At-Home-https://www.futurewiseresearch.com/
The challenges are not limited to low- and middle-income countries, of course. The global diagnostic market is subject to the pharmaceutical industry’s complex regulatory framework. Regulations differ from country to country, which is why product compliance, quality assurance and product efficacy must be clearly stated. Product packaging innovations, such as folded leaflets and mini booklets provide the necessary space to communicate regulatory information, such as the new European UDI system and product serialisation details. Flexible printing technologies can accommodate these requirements with ease and digital printing also enables brands to customise and personalise the messages displayed on packaging, which enhances their engagement with patients and consumers. In its wellness study, NielsonIQ found that consumers associate environmental responsibility with personal wellbeing. Deloitte’s Sustainable Consumer research revealed that 85% of UK consumers consider sustainability within their lifestyle choices.7 Single-use plastics and product lifecycles continue to concern consumers.
In addressing this, manufacturers of diagnostic devices must balance the protection of public health and infection control with responsible environmental and sustainable practices. These can conflict, which is why the industry has adopted a highly proactive approach to reducing its environmental impact across its wider activities. Manufacturers continually seek to reduce their emissions, optimise resource usage, and improve the management of internal waste. The packaging of diagnostic devices is also changing to meet environmental concerns. Plastic fitments, for example, are being replaced with fibre alternatives, making it viable for consumers to control waste at home. Brands must demonstrate these green credentials to engage with the rising number of eco-centric Accordingconsumers.to the global management consultancy firm McKinsey, the global wellness market is valued at approximately $1.5 trillion8. Enabling consumers to manage and understand their own wellbeing requirements through the use of at-home diagnostics will inevitably contribute towards the evolution of global healthcare. The consumer can receive faster diagnoses, make informed choices, and effectively manage their overall physical and mental health. Clinicians and healthcare providers can screen patients with greater ease, identify potential issues earlier and optimise treatment plans. The growing trend in proactive self-care not only benefits the pharma and healthcare industries financially, but through the wider use of POC and at-home diagnostics has the power to transform and save lives. Product packaging innovations, such as folded leaflets and mini booklets provide the necessary space to communicate regulatory information, such as the new European UDI system and product serialisation detials
8. https://www.mckinsey.com/industries/ consumer-packaged-goods/our-insights/ feeling-good-the-future-of-the-1-5trillion-wellness-market
5. home-diagnostics-markethttps://www.factmr.com/report/1892/
7. https://www2.deloitte.com/uk/en/pages/ consumer-business/articles/sustainableconsumer.html
2. home-diagnostics-market.htmltransparencymarketresearch.com/https://www.
3. is-diabetes/facts-fihttps://www.idf.org/aboutdiabetes/what-gures.html
Packaging 25
At one with nurture
“I think what people want is they want to be going on a journey, you want to be on that journey with people next to you, and who are passionate.”
Maurer feels this is where SiMed’s offering differs from others, and at Med-Tech Innovation Expo, SiMed was showcasing the Virion device from Kidod Science and Technology which is a rapid COVID-19 test which provided results in approximately 50 seconds. That’s not the end of the company's projects as he referred “Every time one of those start-ups fail, there’s a potential solution to a problem. There’s an ethical issue here. “By integrating people into a quality management and regulatory strategy, we can get market two-to-three years earlier. There's less suffering in the world and that's the ethos driving behind it.”
26
Below: Simon Mauer from SiMed at Med-Tech Innovation Expo 2022
26
At Med-Tech Innovation Expo, Ian Bolland sat down with Simon Maurer and Patrick Druggan from SiMed to discuss the company’s approach to start-ups and how it feels it differs from others. to tests for women’s health and innovations to combat gum disease. He revealed that prior to the company’s appearance at Med-Tech Innovation Expo that SiMed has embarked on partnerships with four other companies. “We want to go on a journey with early-stage start-ups. We've got a track record and, like I said, there's a lot more of that journey for us to go on Drtogether.”Patrick Druggan, director of regulatory affairs and quality management at SiMed, referred to findings from MIT a decade ago outlining a high rate of start-up failure – saying it wasn’t down to technical capability or money, but a failure to understand regulation, and a lack of understanding marketing when it came to distribution sales. He said: “What we're doing is trying to take from where you get one in 10 succeeding today to get to one in five.
S iMed’s offering is that of one which can incubate and nurture start-ups and help in areas they are struggling. Maurer says SiMed’s approach to start-ups is different in the way that instead of running away from certain challenges and companies, SiMed is prepared to embrace them and take them on. As well as being able to work with companies to develop their products and bring them to market, SiMed offers itself as an investment partner as it seeks out and identifies opportunities within the medical technology space before the companies mature. Overall, the focus is on identifying and nurturing start-ups, and delivering worthwhile investments. “There are many brilliant ideas out there and there’s a huge amount of life changing, potential devices and potential things that early diagnostics, which COVID has very much brought back to the forefront, can pick up.
This includes nurturing the people behind the technologies and developing their skills rather than operating in a style that sees people simply move onto the next contract, SiMed wants to see investment in the people behind the technology and ideas Druggantoo.summed this up saying: “We need to be invested in nurturing people. Rather it be vulture capitalism, let’s have nurture capitalism.”
“A lot of people seem to struggle. They've got an idea but how do you take the idea and then actually put it into the market? Obviously, there's stages in order to do that. So, you need a strategy. You need to get to a regulatory approval, which is a minefield in itself. “We always look for the next great start-up or the next great idea and get involved with them at the very early stages.
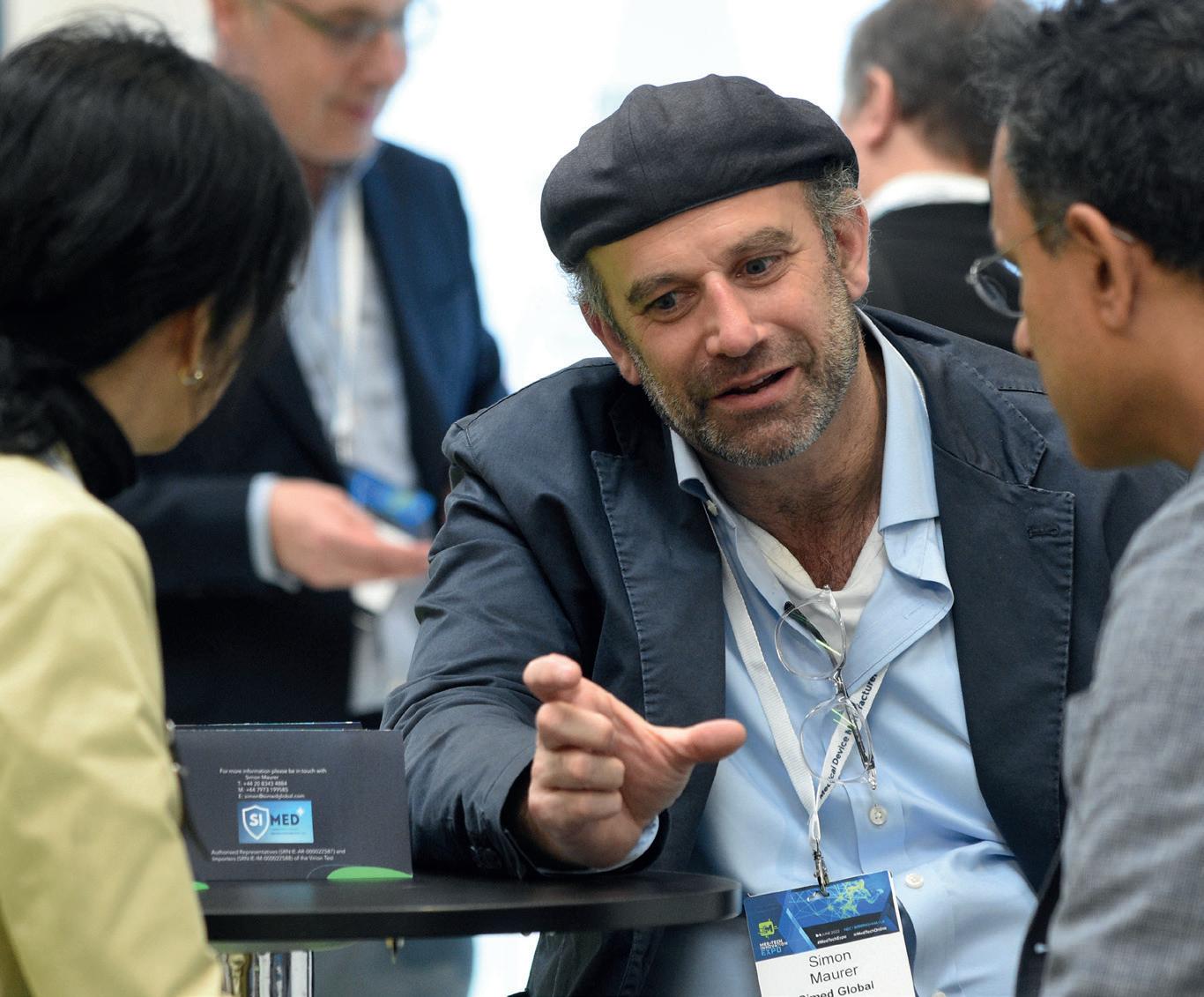
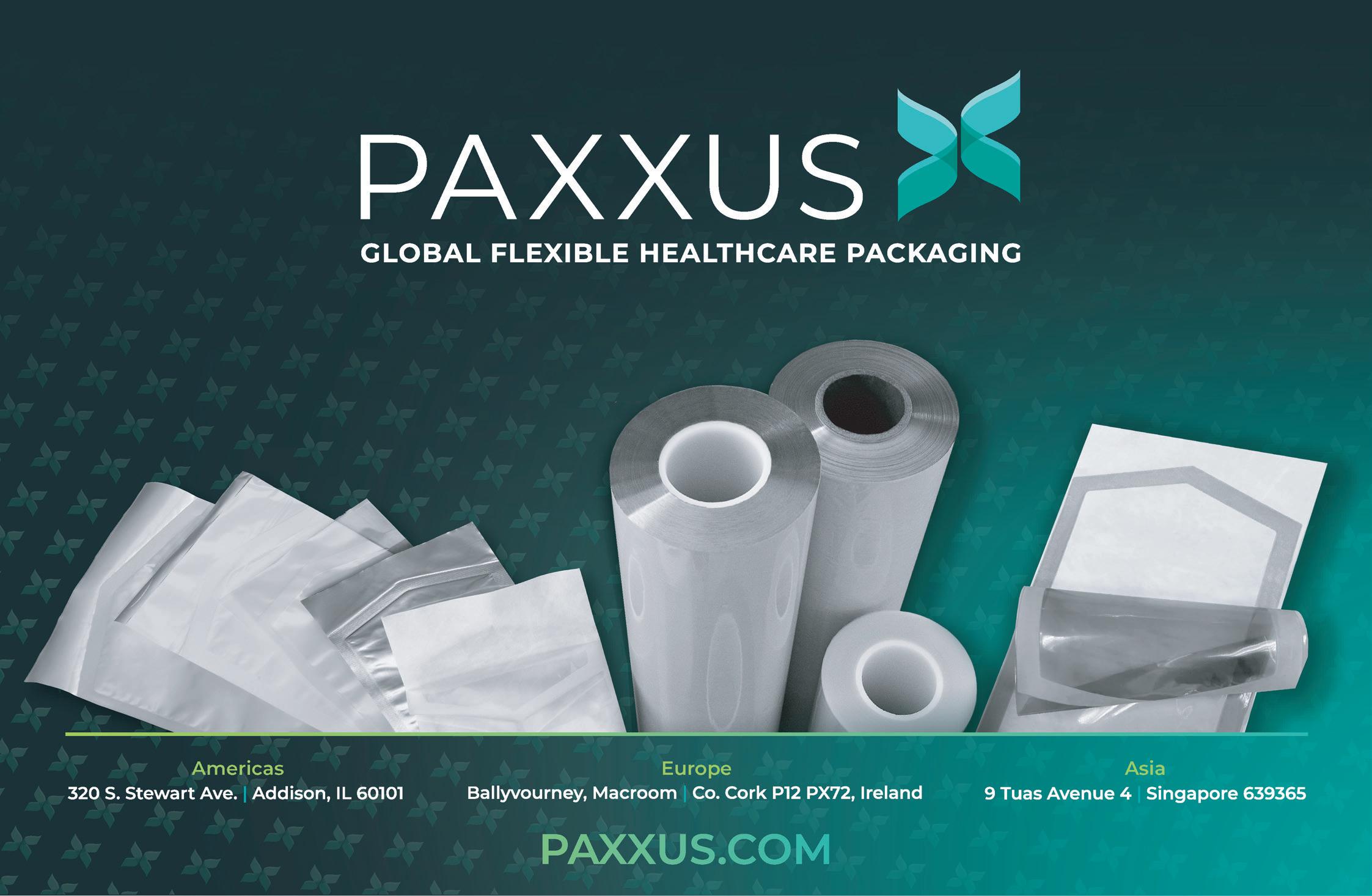
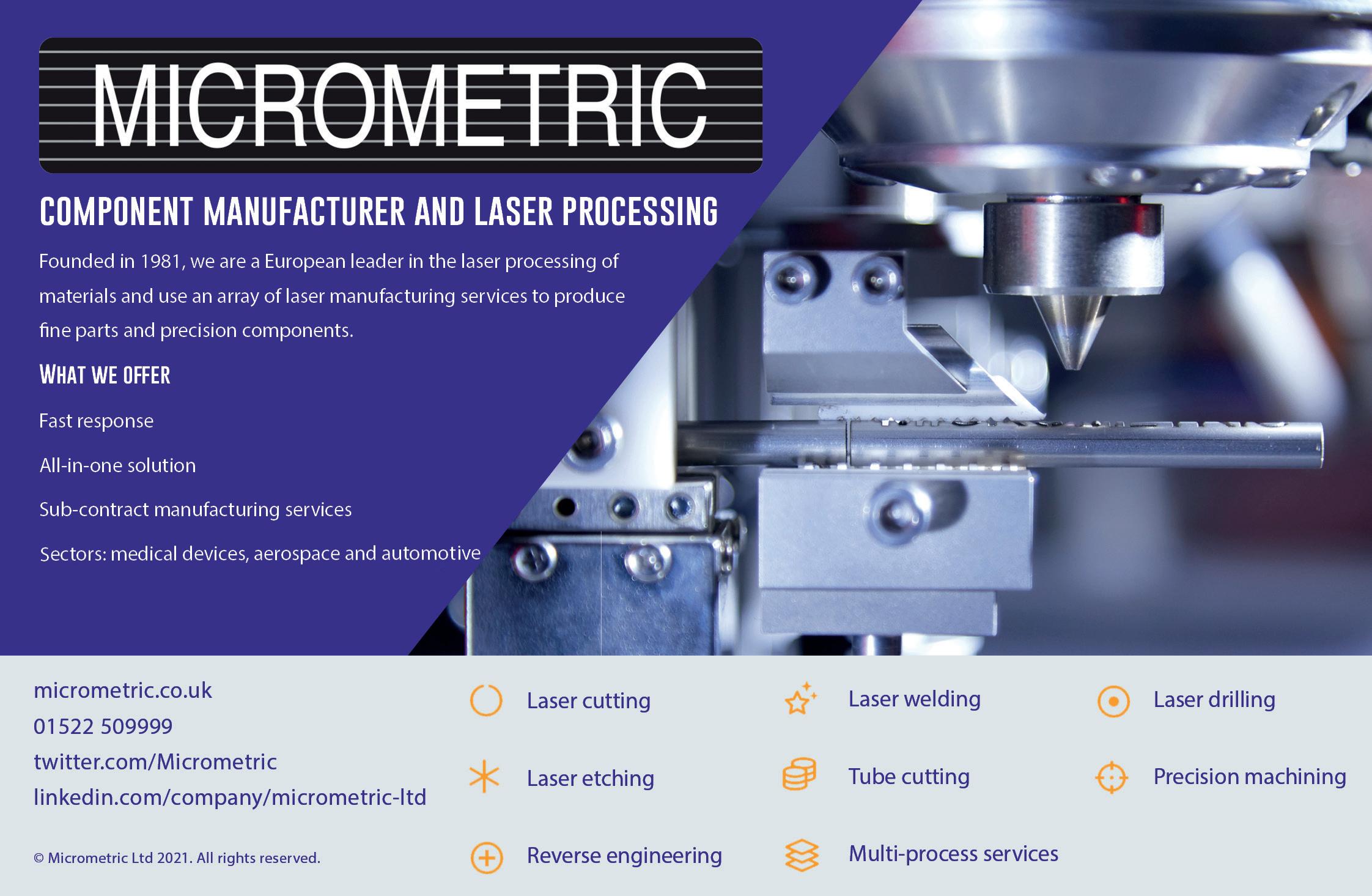
28 MED-TECH INNOVATION 7-8 JUNE 2023 NEC | BIRMINGHAM | UK Medical Device Supply Chain Intelligence Exhibit with us in 2023 Medtech | Digital HealthTech | Medical Plastics | Manufacturing | Software | Inspection and Metrology Regulation | Design | Early-Stage | Innovation | Pharmaceutical | Manufacturing
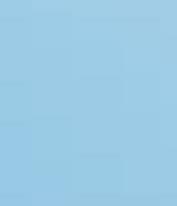
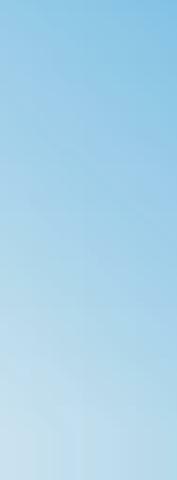

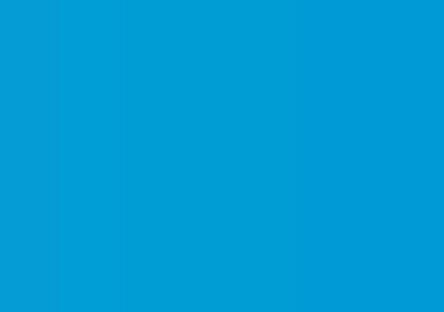
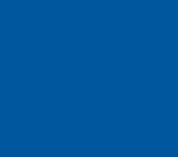
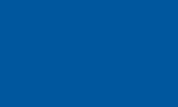
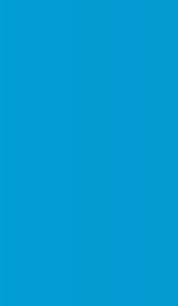
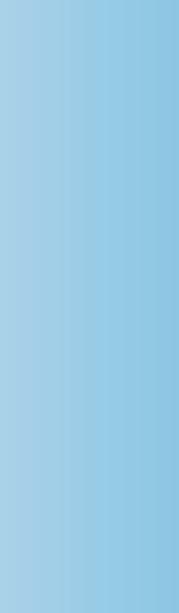
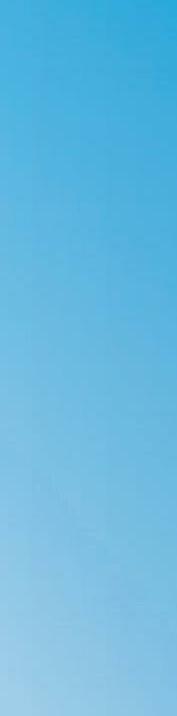
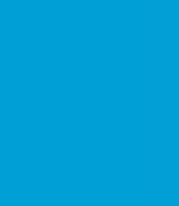
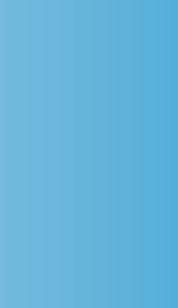
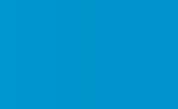

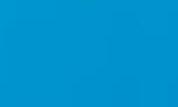
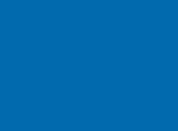
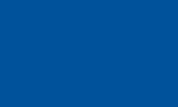

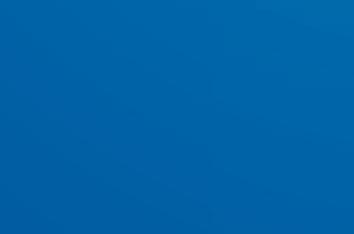
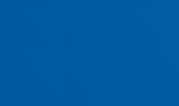
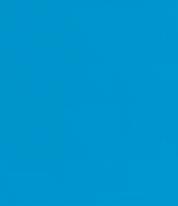
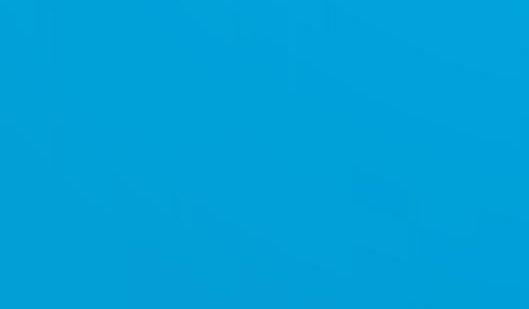
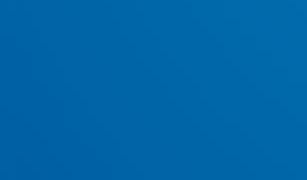
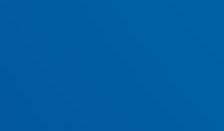
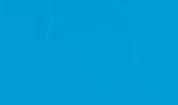
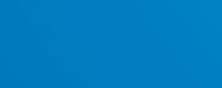
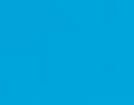
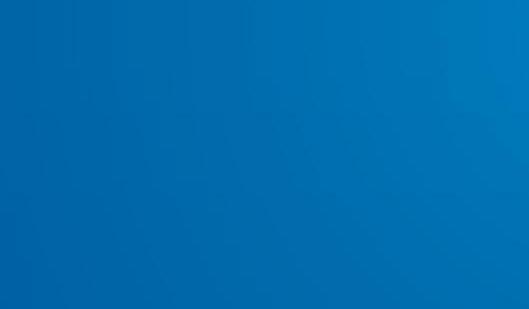
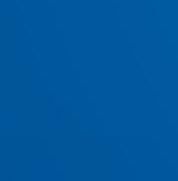

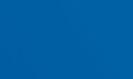

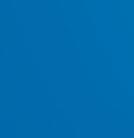
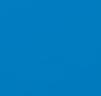

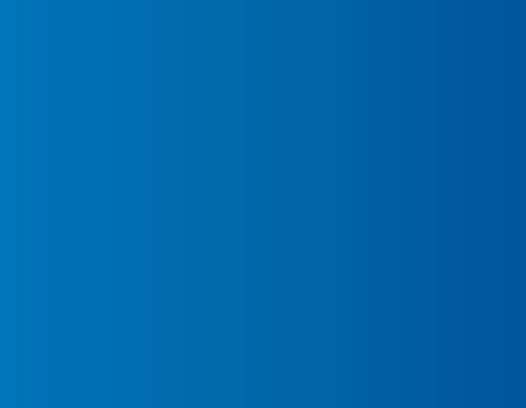
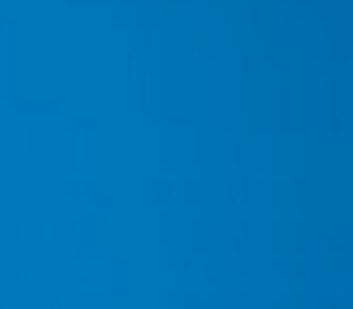

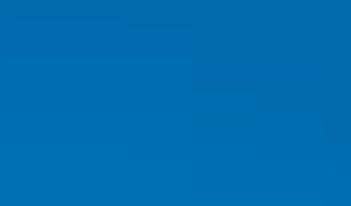
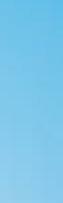

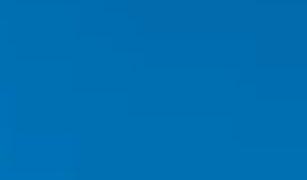
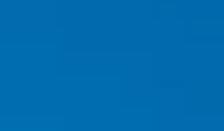
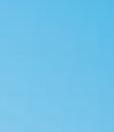
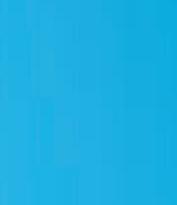
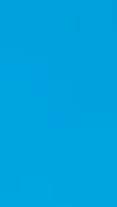




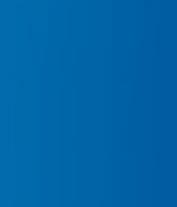

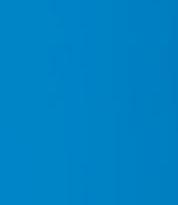
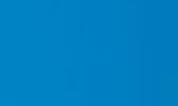
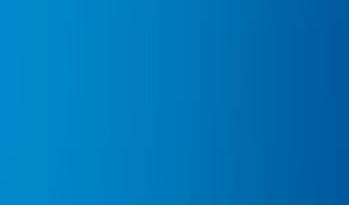

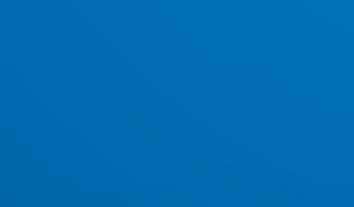
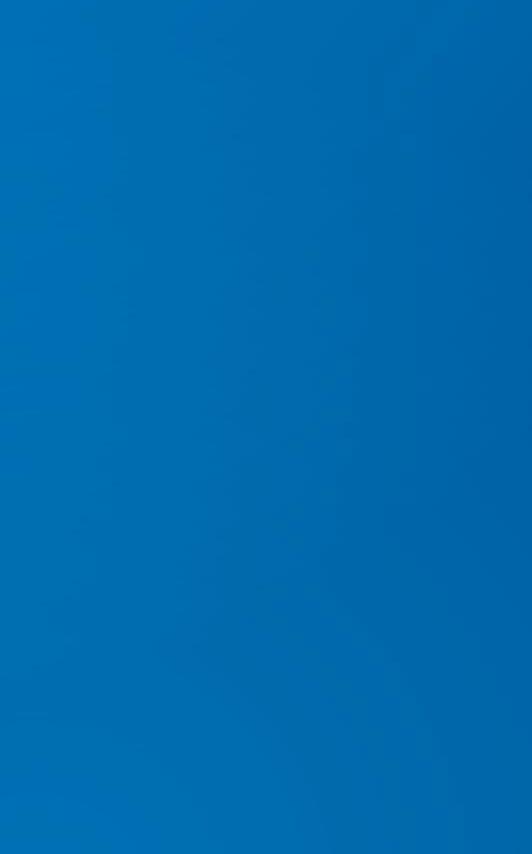
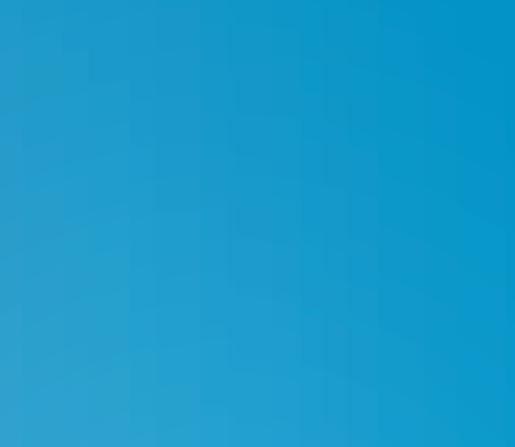
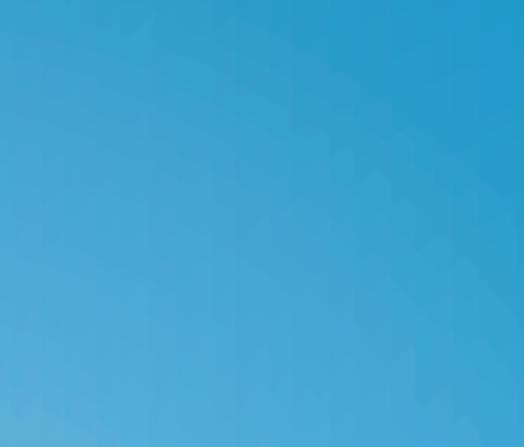
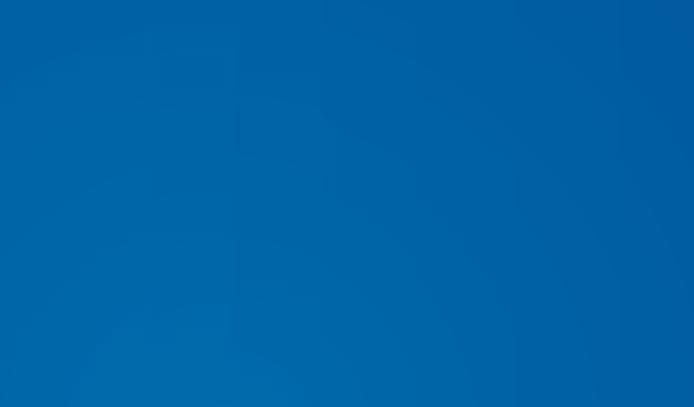
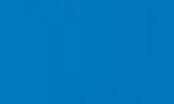
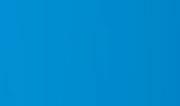
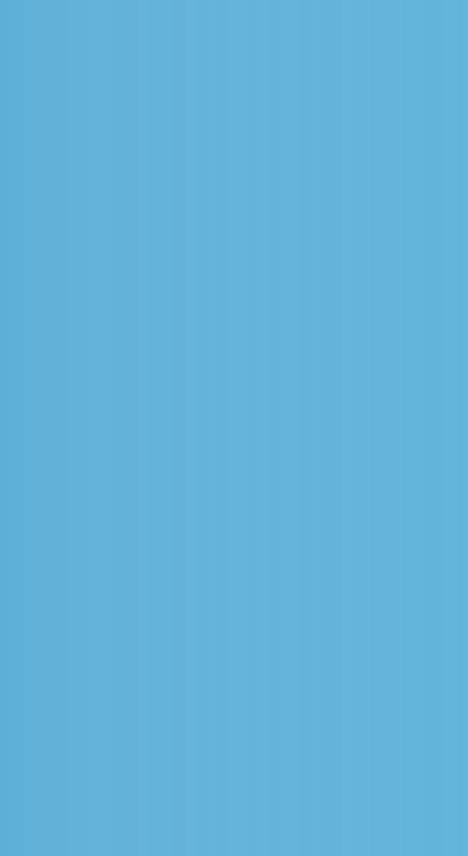
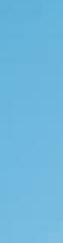
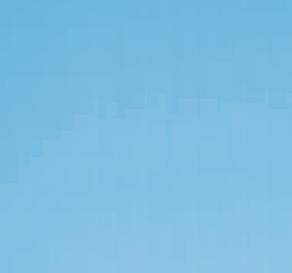
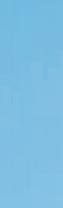
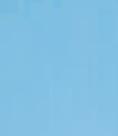

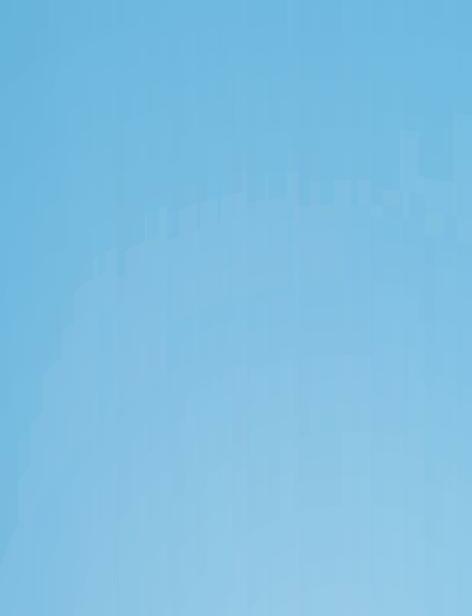
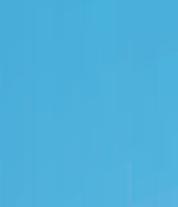
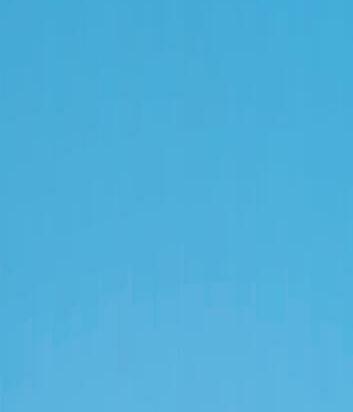
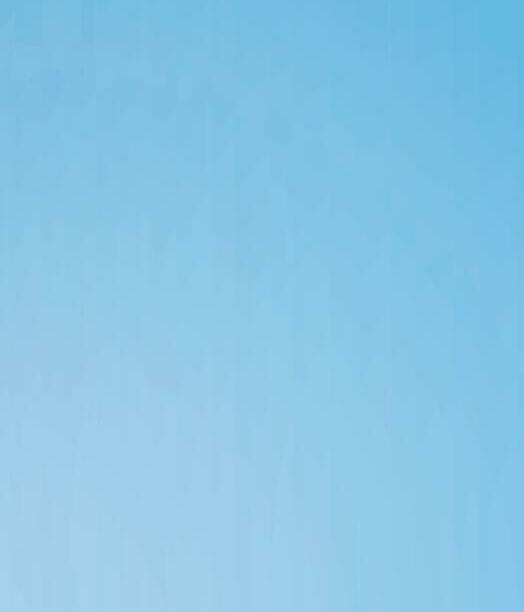
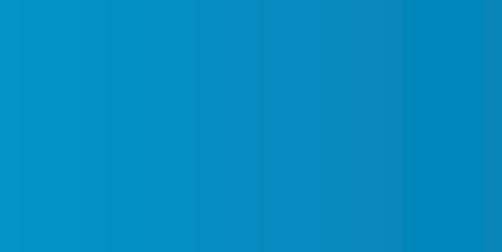
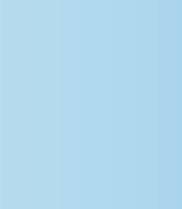
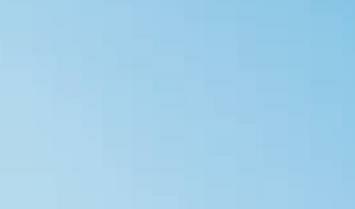

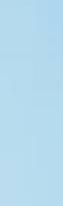
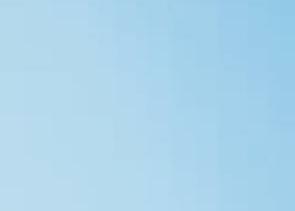
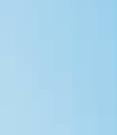
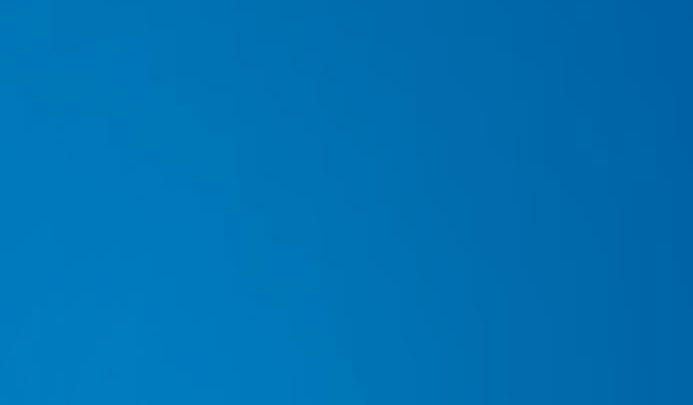
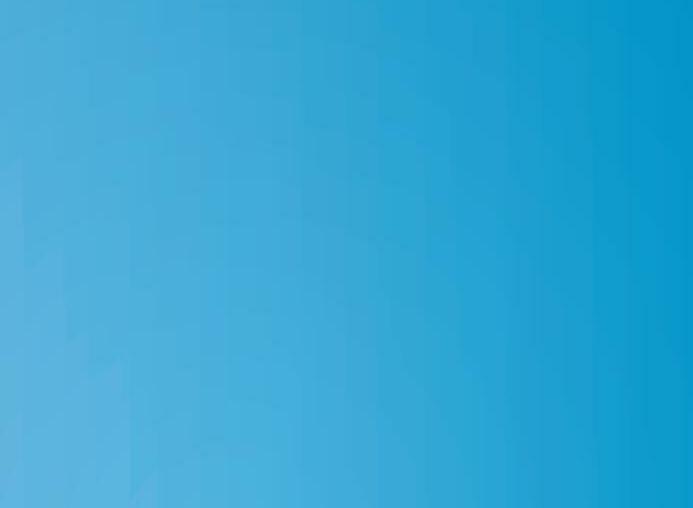
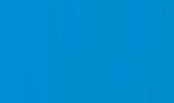
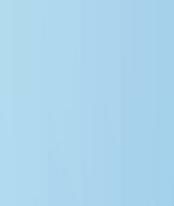
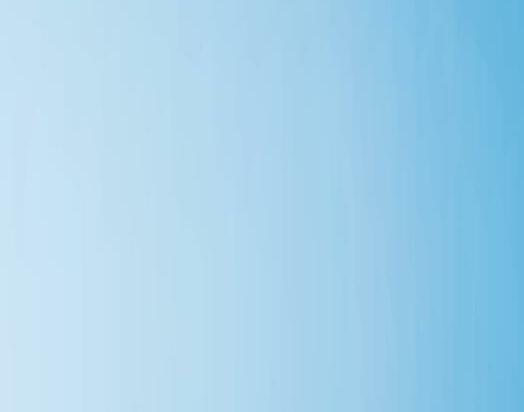
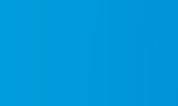
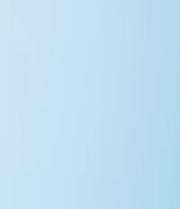
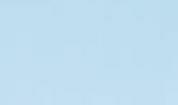

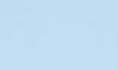
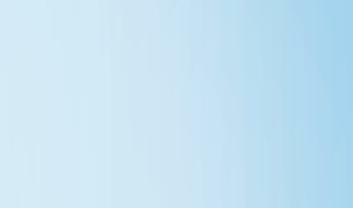
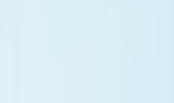
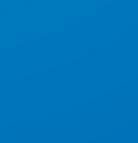
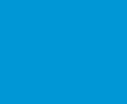

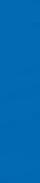
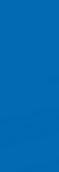
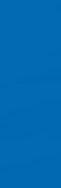




















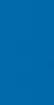









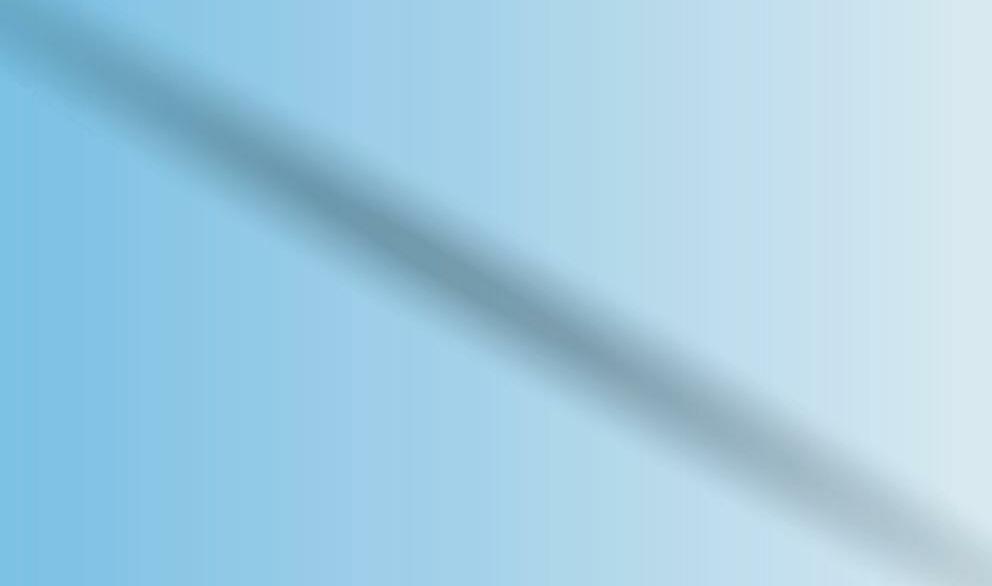
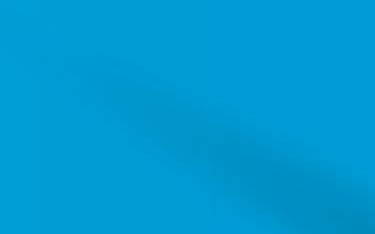
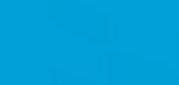

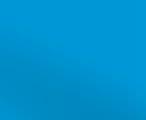


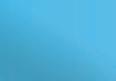

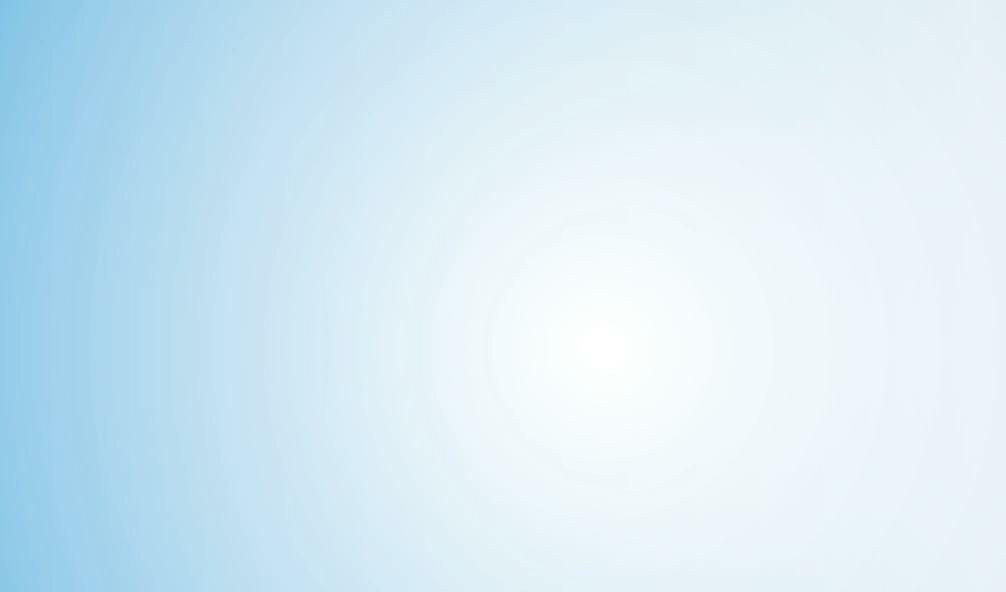

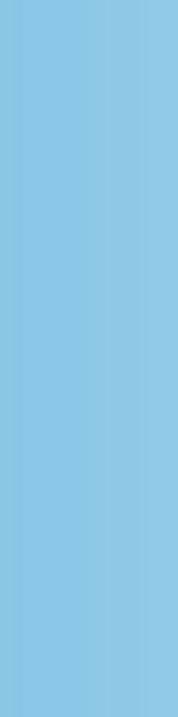
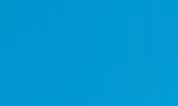
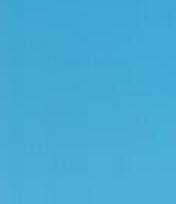
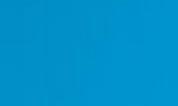
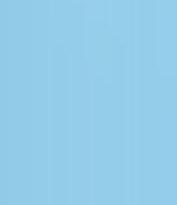
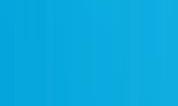
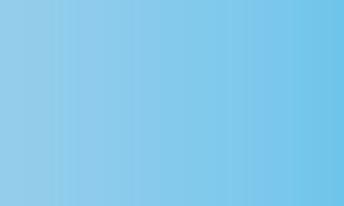
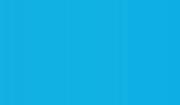
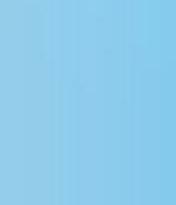
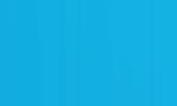
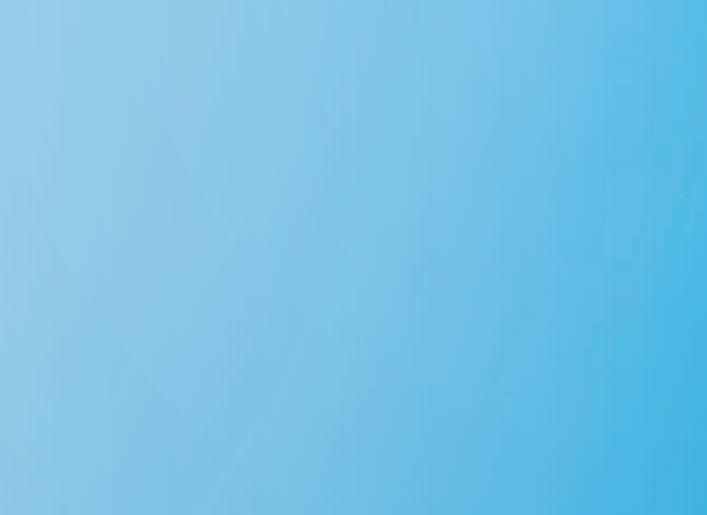
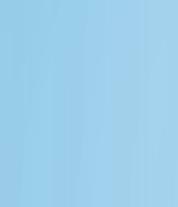
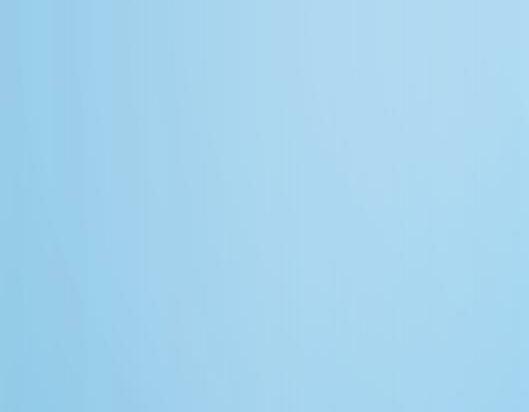
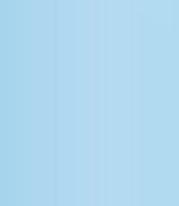
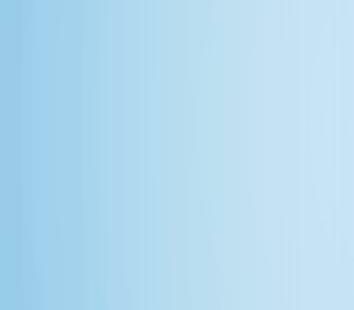
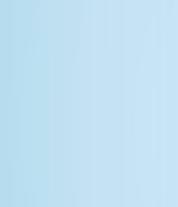
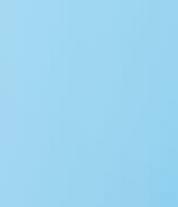