2 minute read
IMPACTING SECTOR TRANSFORMATION: FROM THE ACADEMIC MIND TO THE MINE SITE
Demonstrating the potential of the REFLUX™ Flotation Cell in collaboration with FLSmidth
(Centre industry partner) FLSmidth is one of the leading technology and service suppliers to the global mining and cement industries. With a history stretching back to 1882, the company has a long tradition of industry-shaping innovation. Its focus in recent years has been the development of solutions to support the shift to sustainable mining.
Under its MissionZero program, the company has set a target to make zero-emission and zero-water waste mining a reality by 2030.
Central to MissionZero is the need to do more with less: to improve mineral recovery while at the same time reducing energy, water, and other inputs. It is a mission that aligns perfectly with the research goals of COEMinerals.
Improving mineral flotation
With such similar philosophies, it is perhaps no surprise that FLSmidth – with its strong presence in the Australian mining industry – has partnered with COEMinerals to commercialise the REFLUX™ Flotation Cell (RFC) technology.
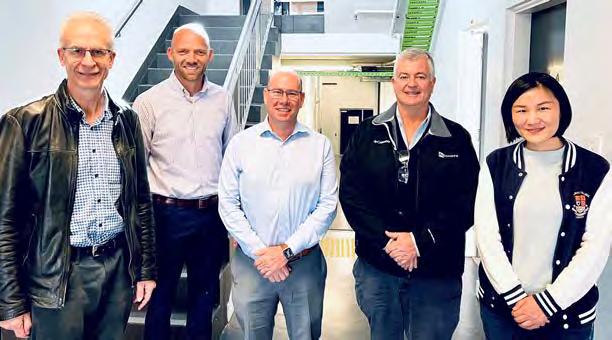
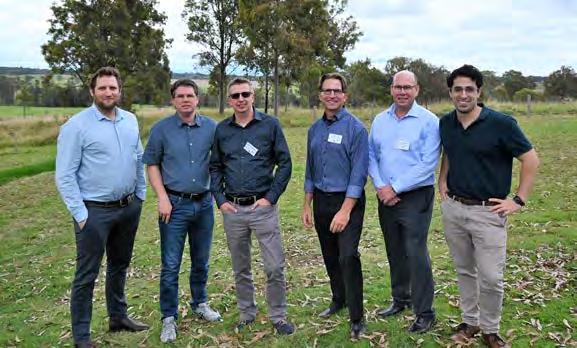
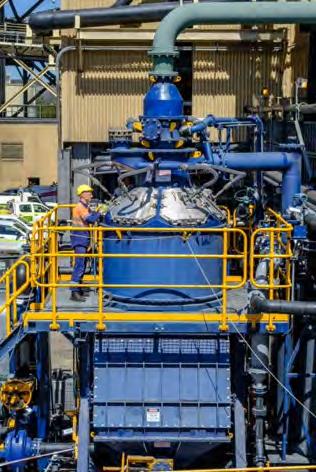
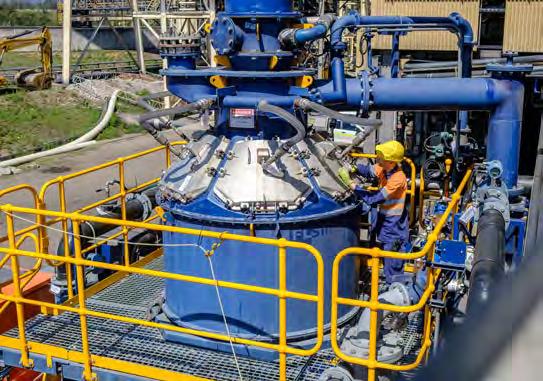
The RFC concept was developed by academics at the UON to deliver a step-change in flotation cell productivity. It is a frothless system able to operate at levels of gas, feed, and fluidisation water flux far above conventional flotation cells. It can thus deliver fast and effective flotation performance that pushes the boundaries of concentration grade, recovery, and throughput.
The result is a seven to tenfold reduction in required flotation volumes. Ultimately, this offers flotation with significantly lower air and water consumption when compared to conventional systems; no direct power input, reducing flotation energy demand; and reduced plant footprint and capital costs.

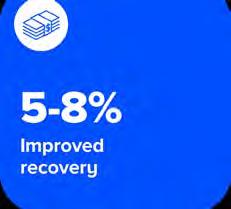
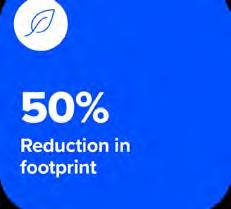
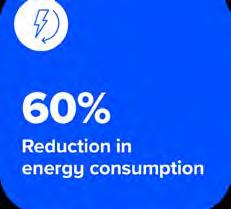
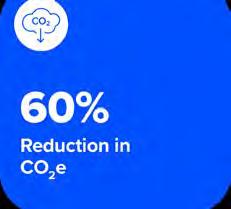
Passing the test
However, it is not until a technology faces realworld testing that its true worth is known.
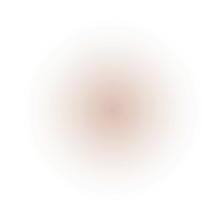
Fortunately, (FLSmidth) pilot trials through 2021 and 2022 have shown that the RFC lives up to its potential. Testing took place at Australian copper and North American molybdenum applications. During these trials, the RFC pilot plants demonstrated the ability to reduce energy consumption by 60%, CO2 emissions by 60%, and plant footprint by 50% compared to traditional flotation cells. It also delivered significant process benefits that resulted in a 5-8% improvement in recovery and 10% increase in throughput.
Spreading the word in Australia and beyond
FLSmidth is actively promoting the RFC within the global mining industry with a wide range of activities across various platforms. It has also been integrated into the company’s ‘mine of the future’ flow sheet, the MissionZero Mine.
The FLSmidth team were also present at the RFC Upscaling Symposium, hosted at UON and bringing together consortium partners from COEMinerals, EIT RawMaterials, and industry. The five-day event included presentations and lab visits that ranged from basic theory to practical process assessment.
Next steps
Work on RFC upscaling is continuing. The next stage involves feasibility testing at larger-scale copper and iron ore mine sites in Poland and Sweden, along with interest from a nickel site in
Australia. Experimental and modelling work to further scale-up the design will also continue, on top of life cycle assessment, as the consortium works toward commercialisation of the technology at a global level. “FLSmidth is committed to enabling a sustainable mining future, but we also know we cannot do this alone,” said Lance Christodoulou, Global Product Line Manager, REFLUX Technologies at FLSmidth.
He added: “Collaboration with partners such as COEMinerals are vital to fasttrack technology development and see it adopted into industry. With its potential to revolutionise mineral flotation, RFC is an exciting case in point, and we look forward to continuing our strong relationship with COEMinerals to implement the technology at a commercial scale.”