2 minute read
von SOFC-Elektroden
Next Article
Massive Simultaneous Cloud Computing (MSCC) für datengetriebene Optimierung von SOFC-Elektroden
Digital Materials Design (DMD) ermöglicht eine systematische modellbasierte Entwicklung und Optimierung von Materialsystemen und Mikrostrukturen. Die Anwendung von DMD für die Entwicklung von Solid Oxide Fuel Cell (SOFC)-Elektroden führt zu einem sehr grossen Parameterraum, der mit konventionellen Rechenressourcen sehr zeitaufwändig ist. Das Konzept des Massive Simultaneous Cloud Computing (MSCC) ermöglicht den Zugriff auf nahezu unbegrenzte Rechenressourcen auf Abruf. Diese drastische Reduktion der Rechenzeiten ermöglicht die volle Nutzung des DMD-Ansatzes für die Entwicklung der nächsten Generation von SOFC-Elektroden.
Mitwirkende: L. Holzer, P. Marmet, T. Hocker, G. Boiger, J. M. Brader, J. G. Grolig, H. Bausinger, A. Mai, M. Fingerle Partner: Hexis AG, Math2Market GmbH, Kaleidosim Technologies AG Finanzierung: BFE Dauer: 2019–2022
Digital Materials Design (DMD) ist ein moderner Ansatz zur modellbasierten Materialoptimierung. In unserem DMD-Ansatz zur Optimierung von SOFCElektroden kombinieren wir stochastische Mikrostrukturmodellierung (d. h. Simulation der Auswirkung von Fertigungsparametern auf 3D-Morphologien), virtuelle Tests von 3D-Mikrostrukturen und ein Multiphysik-Elektrodenmodell. Damit kann ein grosser Parameterraum als Basis für die datengetriebene Mikrostrukturoptimierung untersucht werden.
a) b)
Abb. 1: a) Virtuelle LST/CGO-Struktur einer SOFC-Anode mit simuliertem Potentialabfall, b) Vergleich der Rechenzeit mit klassischem und MSCC-Ansatz.
Allerdings begrenzen lange Rechenzeiten oft den Einsatz von grossen Parameterstudien. In einer Zusammenarbeit von ZHAW, Kaleidosim AG und Math2Market wurden kürzlich neue Konzepte für Massive Simultaneous Cloud Computing (MSCC) entwickelt, die den Zugang zu nahezu unbegrenzten Rechenressourcen ermöglichen. Tausende von Mikrostrukturen können parallel berechnet werden. Für eine Parameterstudie mit z. B. 103 -104 3D-Szenarien, wie in Abb. 1 b) visualisiert, beträgt die Rechenzeit für stochastische Simulationen und zugehörige virtuelle Tests mit einem klassischen Ansatz auf einem lokalen Server typischerweise mehr als 1 Jahr. Im Gegensatz dazu ist die Rechenzeit mit MSCC nahezu unabhängig von der Anzahl der Parameterkombinationen und reduziert sich daher auf nur 1–2 Tage. Ein Beispiel für eine relativ kleine Parameterstudie ist in Abb. 2 dargestellt, wobei die Zusammensetzung und Porosität einer LST/CGO-Anode variiert werden.
→ Porosity
Composition →
Abb. 2: Beispiel einer kleinen Parameterstudie für verschiedene Porositäten und Zusammensetzungen einer LST/CGO-Anode.
Die virtuellen Mikrostrukturen werden mit einer Kombination von 3D-Analysen und numerischen Simulationen charakterisiert. Anschliessend werden die Mikrostruktureigenschaften als Input für ein Elektrodenmodell verwendet, welches die Leistungsfähigkeit der Elektroden berechnet (Abb. 3). Die Analyse dieser Ergebnisse führt schliesslich zu neuen Designrichtlinien für optimierte SOFC-Elektroden.
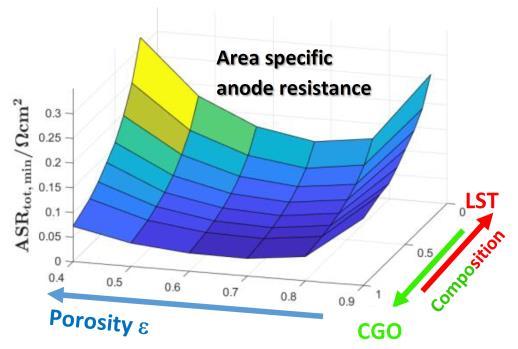
Abb 3: Flächenspezifischer Anodenwiderstand als Funktion der Porosität und Zusammensetzung einer LST/CGO-Anode.