4 minute read
GROUP AMANA DELIVERS THE WORLD’S LARGEST VERTICAL FARM IN DUBAI SOUTH
by tpg media
Next Article
REGIONAL LEADER IN DESIGN-BUILD CONSTRUCTION, GROUP AMANA HAS MARKED A MAJOR MILESTONE AS IT HAS DELIVERED ITS FIRST-EVER VERTICAL FARM IN THE REGION, WHICH WILL BOOST LONG-TERM FOOD SECURITY AND SELF-SUFFICIENCY IN THE UAE.
The high-tech hydroponic facility in Dubai South was constructed by AMANA Contracting in collaboration with Crop One Holdings and Emirates Flight Catering (EKFC). The $40 million Bustanica hydroponic farm, which spans 330,000ft2 and is located in Dubai World Central, will produce more than a million kilos of high-quality leafy greens with 95% less water than conventional farming and will boost the UAE’s food security. The produce will be available on certain Emirates flights and for consumers to purchase across stores in the UAE under the Bustanica brand.
Joe Labaky, General Manager of UAE and Emerging Markets, AMANA Contracting, said: “AMANA continues to push the boundaries of innovation using the latest building techniques. Being a part of a revolutionary project in the UAE’s agriculture industry to ensure long-term food security and strengthen national resilience is a great privilege for the AMANA team.”
To construct the world’s largest vertical farm, AMANA brought in the best and latest innovations in building and construction. The construction leader executed and installed specialized systems to ensure maximum sustainability and environmental conservation. The project was completed on time, by leveraging advanced to maximize output on-site.
The $40 million Bustanica hydroponic farm, located near Dubai World Central, will produce more than a million kilos of highquality leafy greens with 95% less water than conventional farming
AMANA Contracting delivered the project while adhering to the highest quality and safety norms, using off-site construction techniques. The company executed and installed specialized systems throughout the project, such as LED lights in the grow room and germination room, grow fans, grow room controls, pack house equipment, grow kit, racking, nutrient dosing systems, and germination room equipment, among other facilities.
AMANA leveraged BIM technology to develop all the workshop drawings and executed MEP using offsite construction. Given that modular techniques are more efficient, leaner, and result in less waste production, AMANA ensured that the project was executed in the most sustainable way possible. AMANA also achieved a milestone of 1+ million work hours without any LTI at the project.
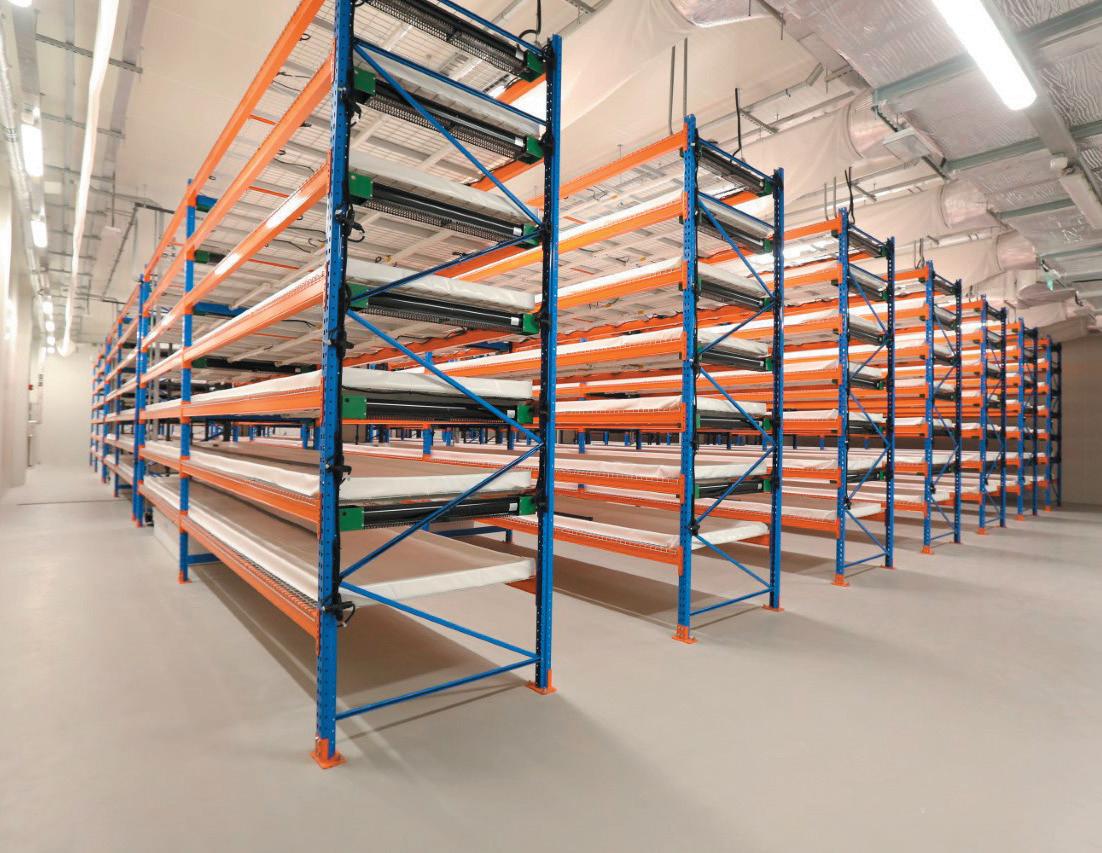
Offsite construction is becoming increasingly popular because the industry has recognized that it is a time-saving, no wastage, super safe and clean process that benefits all stakeholders – clients, contractors, the workforce, and the environment. The turnaround time on the projects is shorter and cost overruns are significantly reduced. It also improves workplace safety and reduces environmental impact when compared to traditional on-site construction. This made it the most ideal building solution to develop the world’s largest vertical farm here in the UAE. Last month, Group AMANA revealed its revitalized brand identity. Now organized into three verticals: Construct, Manufacture and Enhance, the transformation reflects the Group’s offerings for an evolving business landscape and the drive to build cleaner, greener, and smarter. AMANA has built a formidable reputation over three decades of operations in the region, with its commitment to sustainability, innovation, and digitalization.
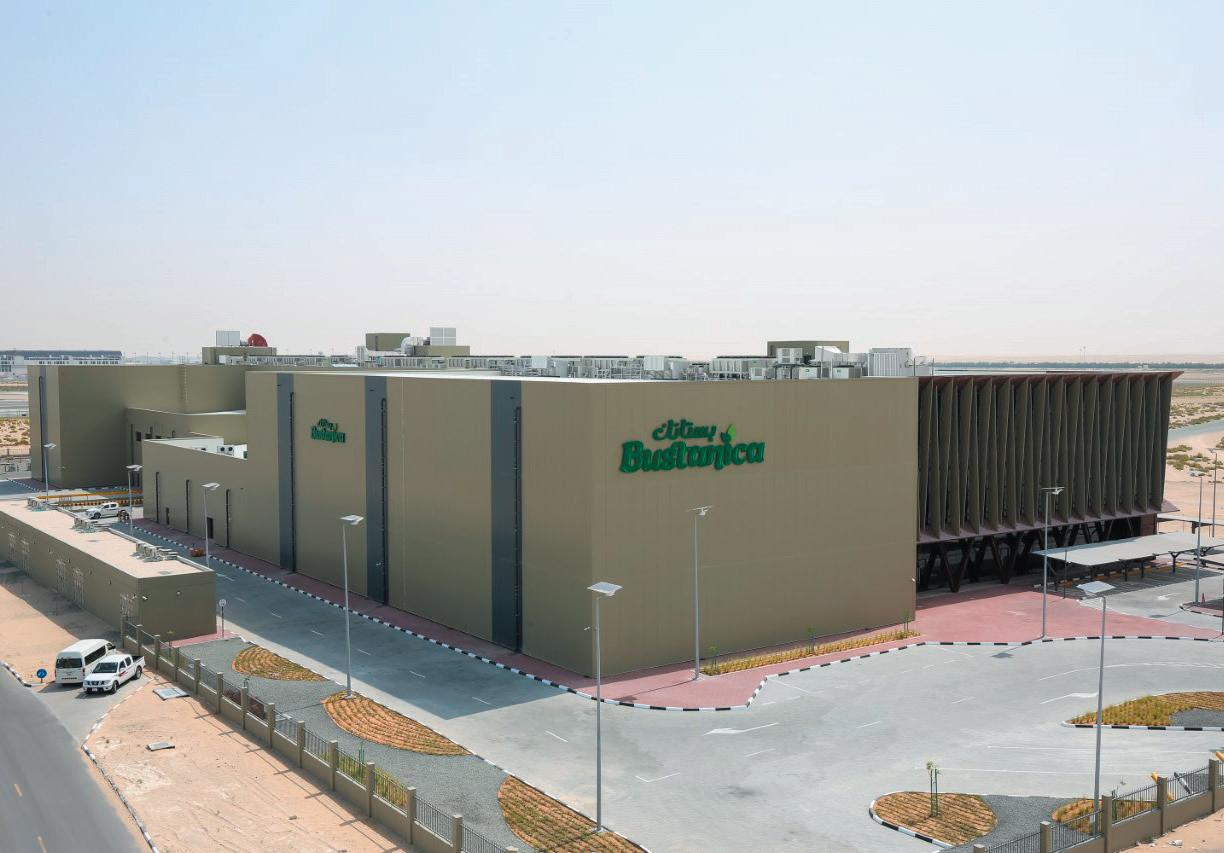
As a fast-growing multinational organization with employees spread across multiple geographies, it is important for us to drive seamless interconnectivity, offer remote accessibility, and implement a data-driven modern performance management and rewarding tool. With Oracle Cloud Applications, we can provide a consistent employee experience across devices, realize significant efficiencies across departments, and enable one source of truth for HR data to improve decision-making on one integrated platform spanning the entire employee life cycle, from hire to retire.
SP: How is BIM helping AMANA with projects? What are your most recent projects completed on BIM?
RA: AMANA has made significant investments in digitalization, migrating to the Revit BIM platform to enable integrated project delivery, shortening production cycles, and fostering collaboration amongst various departments. Recently, we leveraged modular construction to deliver the world’s largest vertical farm – Bustanica – in Dubai South, spanning 330,000ft2. It was built using innovative off-site construction methodologies such as BIM, saving time, and reducing waste and work hours. We’ve used intelligent solutions across several key projects for clients such as Red Sea Global, NEOM, Nupco, and Veolia in Saudi Arabia.
SP: What technology is at the center of AMANA strategy?
RA: I would say BIM has been a key enabler for AMANA’s digital transformation initiatives, helping us to fulfil our goal to build more efficiently.
This technology has enabled us to design and integrate our key projects in Saudi Arabia for Red Sea Global, NEOM, Nupco, and Veolia. Our project delivery team worked with engineers in different offices and countries to design and build in real-time as both design and construction progressed, enabling us to deliver the project in record time.
SP: What do you think are the major challenges in digital transformation?
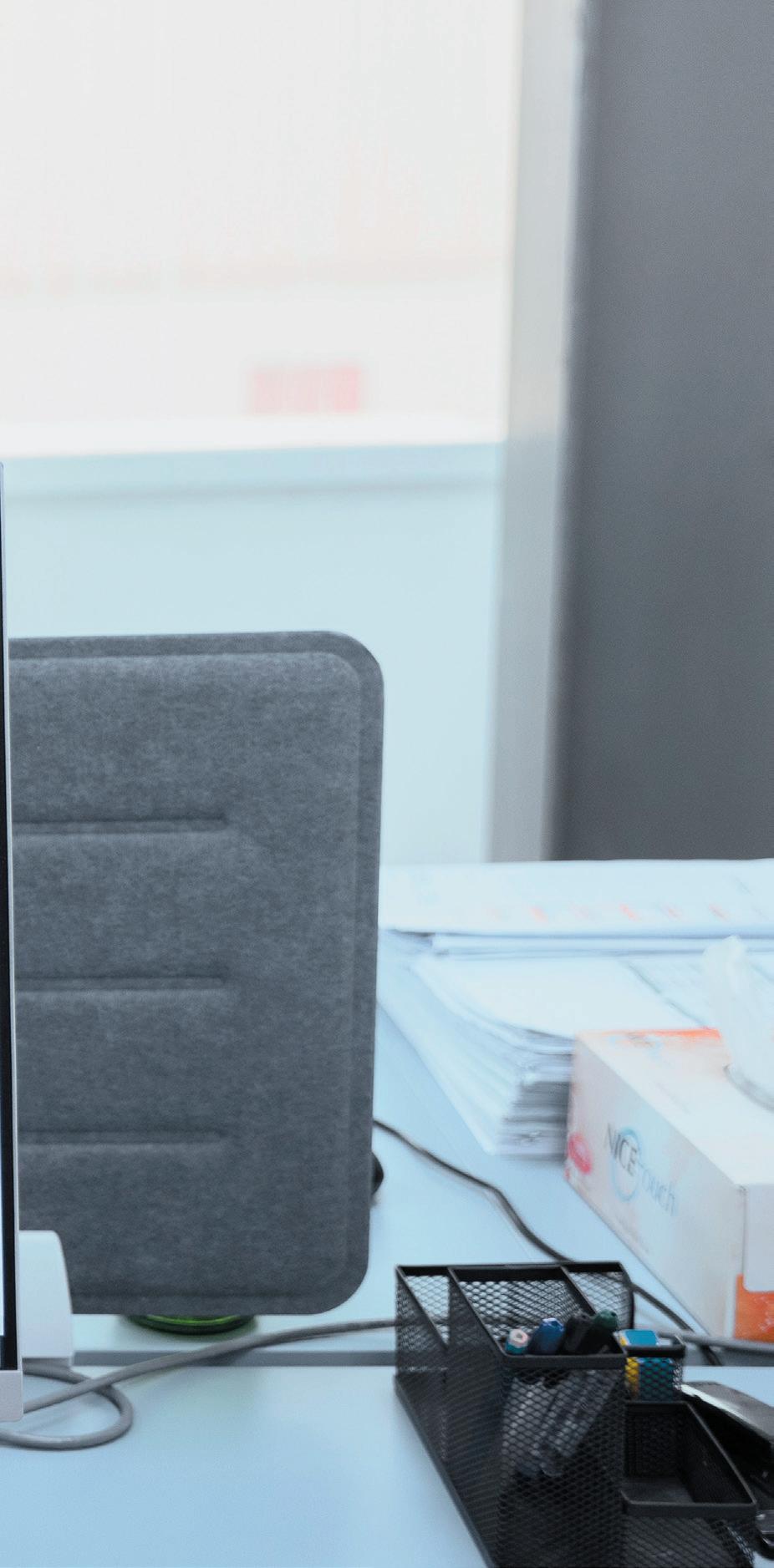
RA: Overhauling legacy systems is a challenge. In some instances, financial constraints and lack of proper training also affect digital adoption. But project managers must leverage software to make their construction business more interconnected and agile, both internally and externally. The industry will also need to look beyond the obvious cost and efficiency benefits of digital transformation and see how it is driving many environmental benefits.
SP: What do you think the construction industry will look like five years down the road if digital transformation has the impact that is envisaged?
RA: The benefits of true digital transformation are enormous for the construction sector. Innovation, the adoption of new technologies like AI and robotics, and a shift towards sustainable practices will put the construction industry on the fast track to growth. It’s time for the industry to recognize that the repetitive, simplified, and standardized factory operating process promotes safer, healthier, and cleaner working conditions, with far lower wastage rates than an open construction site. Encouragingly, the regional construction industry is also improving its performance on sustainability, diversity, and inclusion by increasing investments in connected construction, leveraging technology, and innovative methodologies. The future over the next five years looks quite promising for the regional construction industry if more technology is adopted to boost efficiencies.
SP: What other emerging technologies do you currently have your eyes on in the construction sector?
RA: Robotics, AI, and ML are shaping the future of construction. The use of technology in the construction sector is expanding quickly with the goal of improving productivity and sustainability on the job site. Construction robotics and connected construction site are examples of developing technologies. At AMANA, our focus will be on start-ups and scaleups that foster innovation and boost intelligence in these fields, but it's also crucial to maintain a shared data environment where data from building initiatives is preserved and easily accessible to everyone.
As the GCC is accelerating towards a decarbonized future, the construction industry, responsible for one-third of global carbon emissions, will play a key role in fulfilling green agendas for a circular economy.