7 minute read
Designing to Scale
Next Article
HELLMAN-CHANG FURNITURE LOOKS TO FUTURE GROWTH WITH A RELOCATION AND UPDATED PRACTICES
BY BILL ESLER
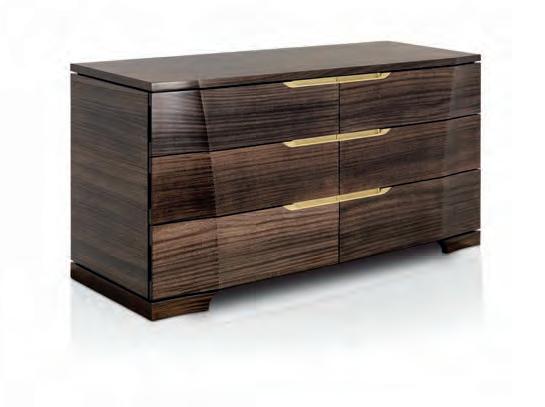
Beautiful furniture and interior appointments are inherently marketable. Pieces with a story behind them…even more so. Furniture designers Hellman-Chang has both, with arresting designs created and produced by a business rooted in a storybook tale of woodcraft that commands extraordinary prices. Dan Hellman and Eric Chang met when they were 10 and shared a love of woodworking that they indulged in during high school in a basement workshop in Brooklyn.
Years later and after pursuing different career paths, they met up once again in Brooklyn, where they helped establish and embody the “Brooklyn Renaissance” with their sleek, timeless designs. Neither formally studied furniture design—Chang having studied finance and marketing in college and
Hellman studying classical guitar performance. “I worked at an artists’ agency representing other artists,” says Hellman. Chang helped start a successful
New York marketing agency. “But we both moved into furniture pretty quickly.” While they are self-taught in furniture design, the duo are well-schooled on the technical side of woodworking. And perhaps because they lacked that conventional training, their work is idiosyncratic and unique.
“We have a passion for making furniture and trusting our own eye for what are good propositions and what is aesthetically pleasing,” says Hellman. “The market then responds to that. Most pieces get a good response and some are not very popular—we don’t bat a thousand.
But as a large body of work, we definitely have a look, and a design and an appeal—design vocabulary, so to speak—that we feel our customers come back to us for.” This combination of design and woodcraft allows for extraordinarily innovative designs, yet springs from techniques in casework and joinery that push their pieces into a category all their own. When Hellman-
Chang launched in 2011 their reputation took off quickly with the introduction of their Z table, and soon their
Brooklyn showroom was buzzing with activity as wellheeled patrons ponied up for their unique bespoke designs—some selling for more than $20,000.
DESIGNS AND FINISHES The furnishings produced by Hellman-Chang are almost sculptural, with curving surfaces embedded with brass, carved solid woods and flat-paneled wood veneers. Each piece is unified by rich, artisanal hand finishes that reveal the wood grain either explicitly or subtly—cerused, bleached, dyed, stained—but always there. Some designers must return to the drawing board to adapt their vision to the practicalities of production, but for Hellman-Chang, joinery and casework are inherent to their designs, which are almost immediately executable.
This makes each piece—bureaus, tables, sideboards—a design expressive of the vernacular of traditional woodwork, as integrated as a classic craftsman piece. The energy flowing through the individual pieces is carried out to the finishes, which largely reveal the underlying woodgrains.
“Most everything that we do is wood that is stained and colored, bleached in some instances, sealed, maybe glazed or cerused, and then top coated,” says Hellman. “All for that open-pore, close-to-the-wood look.” Wood species for lumber and veneers gravitate to oak and walnut.
“We use a combination of solids and veneers as our main building materials, we accent with brass for pulls, inlays and things like that,” explains Hellman. “On the wood side, if it is shapely, it is solid wood carved. If it’s flat, it is veneer. So dining tabletops, flat doors, will be an MDF core with veneers on both sides.”
While Chang leads a design team in Brooklyn as creative director, Hellman is the company’s operations manager and technical designer, translating everything into drawings—done on SolidWorks—to guide the production of each workpiece. “I’m very much a numbers guy,” says Hellman, who had a double major in statistics. “I actually do all the engineering of the furniture.”
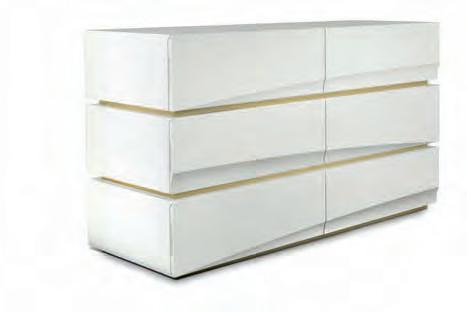
MOMENTUM AND EXPANSION With everything done by hand, including the multi-step finishes cured solely by air drying, the 5,500-square-foot Brooklyn shop soon maxed out its capacity, and the duo began planning to move to larger quarters. Finding this was simply impractical in metropolitan New York City, so Chang and Hellman looked elsewhere. They found a welcome setting in Dawsonville, Georgia, and have expanded their production facilities in a 32,000-square-foot facility there.
The momentum of the business soon overwhelmed the seven Brooklyn craftsmen, each carving and joining by hand, with signature hand-finishes applied by a master craftsman. As back orders rose, Hellman and Chang were intent on planning a way forward that would resolve these challenges.
Recognizing that hand-carving surfaces and joints was a production
CONTINUED ON PAGE 46 ›
FACING PAGE: HELLMAN-CHANG CLEO DINING TABLE IN BRANDY WALNUT AND HAYDEN DRESSER IN CINDER SAPELE WITH BRASS HANDLES. LEFT: XIE EXECUTIVE DESK IN BRANDY WALNUT. BELOW: WAVERLY DRESSER IN POWDER WHITE WITH BRASS ACCENTS, MARCUS COCKTAIL TABLE IN BURNISHED WALNUT AND CREAM SUEDE WITH BRASS ACCENTS, AND WAVERLY DRESSER IN CINDER SAPELE.
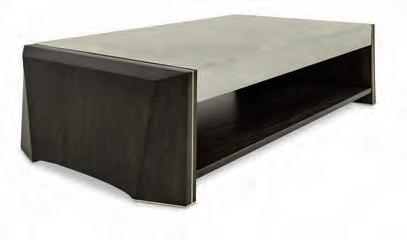
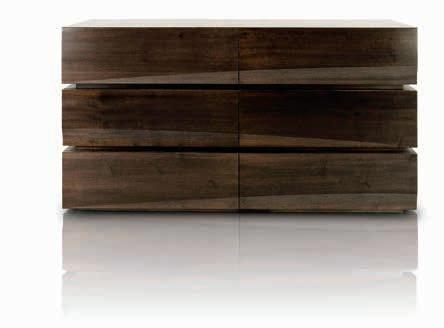
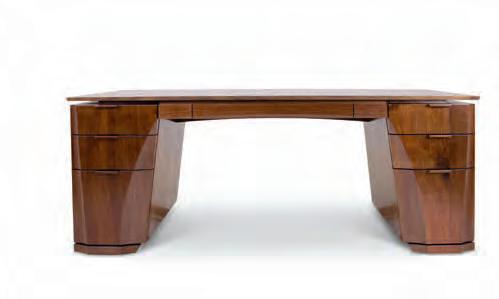
“We have a passion for making furniture and trusting our own eye for what are good propositions and what is aesthetically pleasing.”
DAN HELLMAN
‹ CONTINUED FROM PAGE 45
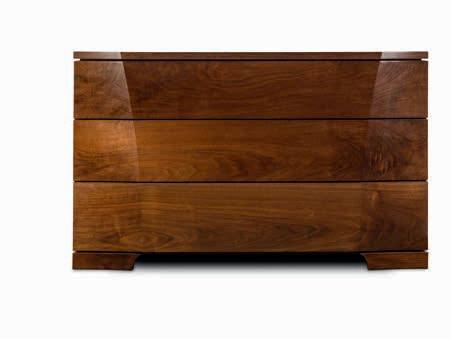
bottleneck, the duo commissioned a customized Thermwood CNC, so the workpiece creation could be automated. “We worked with them to adapt one of their base models,” Hellman explains. “They beefed it up a bit. They raised the Z-axis a bit to accommodate an aggregate cutter that was also controlled by the C-axis, so we could do some complex joinery on things.”
“Basically it is a lot of milling…we rough out a shape, and we mill the final,” he says. “And we use the aggregate to cut critical joints.” In addition to cutting and refining joints, the CNC is now used instead of hand carving to shape the contoured, solid-wood surfaces that are a signature of many Hellman-Chang designs.
With the recent relocation, the CNC was simply unplugged in Brooklyn, shipped, and quickly resumed its work in Georgia.
With the CNC taking on workpiece creation, the next challenge was finishing. Hellman-Chang relied on a master craftsman who, like many traditional specialists, used memory and feel in producing the finishes. But relying on a single individual’s skill and knowledge would not be scalable as business grew.
The company’s longtime master finishing craftsman also relocated to Georgia to help maintain the quality of the finishes, but indicated he would be leaving the company down the road. To prepare for this change, the company brought on a professional with a background in architectural millwork finishing nearly two years ago. That person is now set to continue the high-quality work that has come to be expected of the brand.
These specific finishing techniques are now mapped out in recipes and a local finishing supplies source was found, eliminating another production bottleneck. This required a transition to coatings from Renner, which went relatively smoothly.
“Our new finishing manager helped us create very accurate step boards documenting how we create each of our standard finishes, so that we could grow the team around that,” says Hellman. “Because we now are using a local vendor, we needed to change everything we were using, down to the bleach, the different dyes we were using. We were still using the vendor in New York and having it shipped, but we needed to develop a more sustainable way to do it now that we had relocated.”
“The choice of Renner was driven by our local supplier who we know and trust, and that’s who they represent,” says Hellman. “We saw we would get the service at many levels.” Subtle differences in the coatings are largely undetectable to customers, he adds.
“You can over-catalyze it to get a floor quality finish, but we don’t even need to do that,” says Hellman. “It’s hard enough for even our dining table so it seems to have the best of all worlds, It’s got a nice hand to it. Our customers who are really high end…they like it.”

ABOVE: HAYDEN DRESSER IN BRANDY WALNUT. BELOW: HELLMAN-CHANG XIE EXECUTIVE DESK IN CARBON OAK WITH PENCIL DRAWER.
In the process of designing workflow for the new production facility, Hellman-Chang retained Industrial Wood Process Solutions, Inc., with principal Joe Baggett guiding equipment purchases (new planer, angle saw, and their first clamp carrier) and the arrangement of work centers as the company moved from bench-made to factory workflow. Baggett’s expertise in finishing was also tapped, and a forced curing system was added for the first time at Hellman-Chang, in the form of a batch oven from Prime Heat. The oven speeds the curing process by using a combination of warm and hot air and infrared energy.
SCALING FOR A GROWING BUSINESS With these changes, Hellman-Chang has laid initial groundwork for a business that can grow its output volume. But getting to fully scalable processes will take more time.
“Arguably our largest challenge is how to scale it,” says Hellman. “Because now we gravitate toward bench-made furniture, but benchmade is difficult to scale. We desperately want to have the stations that are fully set up by process, but because we don’t just build cabinets, we have so many different processes that require different set ups…we haven’t really cracked that nut yet.” s p