7 minute read
News in brief
NEWSIN BRIEF
Alumina handling operator set to benefit from Siwertell ship unloading technology
itself, but evidently, wanting to order its own unloader, after experiencing what our equipment could offer, speaks volumes in terms of Trímet France’s trust in the equipment and in us as a company,” continues Ojeda.
“Siwertell unloaders have unbeatable environmental performance with zero spillage and virtually no dust creation. They also offer minimal material degradation, which delivers a particular advantage to the alumina industry,” he adds.
“Our systems handle materials carefully, which minimizes the production of powdery fines,” Ojeda explains. “Aluminum smelting is energy intensive, and is very sensitive to the amount of fines in the alumina; the lower the percentage of fines, the lower the temperature required in the process, which therefore reduces energy consumption. This is ultimately good news for the planet and for profitability.”
Trimet France’s new Siwertell 10,000 S next-generation road-mobile unloader is commencing operations in Marseille. It offers extremely efficient, dust-free alumina handling with minimal material degradation and very low energy consumption. It also features advanced digital technology for remote monitoring and service support.
Trímet France placed the contract in 2021 following a 20-month lease of an older Siwertell 10,000 S unloader from another Bruks Siwertell customer. “Over this time, we supported Trímet France with any servicing needs, and had the rare opportunity to form a relationship with the customer before its purchase,” explains Jörgen Ojeda, Sales Director Mobile Unloaders, Bruks Siwertell.
“Trímet France wants to strengthen its present alumina unloading operation. Its original decision to lease our hardware was an endorsement of Siwertell systems in Many port operators already benefit from the flexibility and efficiency of Siwertell road-mobile unloaders. “Although we have unloaded 1.25 million metric tons of alumina with a previous road-mobile installation in Croatia, which operated between 1997 and 2006 and ran up over 10,500 hours of service, the application of Siwertell unloader technology for handling alumina is still relatively new. So, this order strengthens our strategic aim for more operators to benefit from our market-leading alumina handling capabilities,” he says.
The new road-mobile unloader offers a rated capacity of 130t/h, discharging vessels up to 10,000 dwt, and can be folded down and relocated in under an hour. It also features the Internet of things (IoT) device, Compulab, which enables extensive monitoring, follow-up, support and trouble-shooting through safe, remote access.
Ozinga takes delivery of new road-mobile cement unloader
American organization, Ozinga, has taken delivery of its Siwertell road-mobile ship unloader, which is now securing environmentally friendly cement handling for the company in the US Midwest.
“The Ozinga team invested time in researching various types of unloading equipment and concluded that the Siwertell roadmobile unloader was the best solution for its application,” says Ken Upchurch, VP Sales and Marketing, Bruks Siwertell.
Ozinga specializes in concrete, dry bulk materials, and natural gas energy solutions. Its 5000 S road-mobile unloader delivers a continuous rated unloading capacity of 300t/h for vessels up to 5,000 dwt and also features advanced digital technology for diagnostics and trouble-shooting.
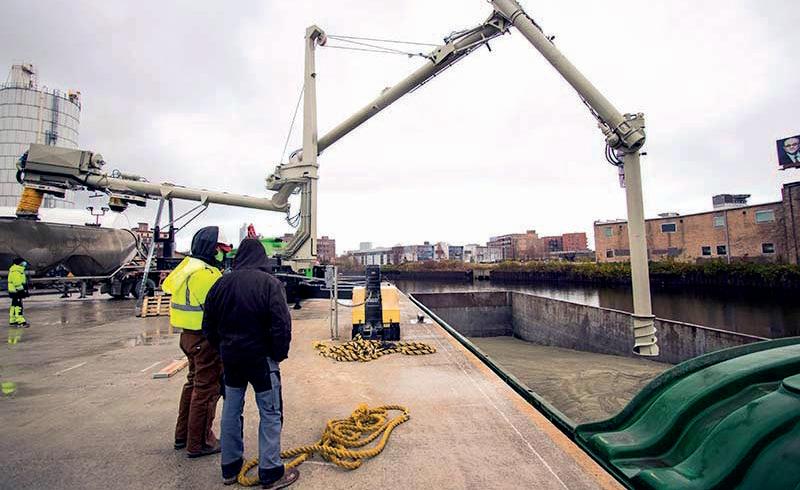
High-capacity cement handling opens up opportunities
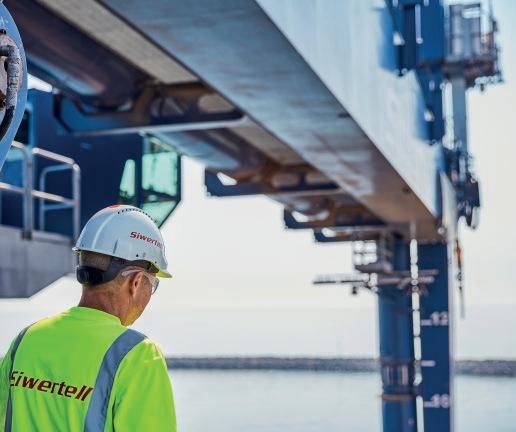
A new Siwertell ST 640-M screw-type ship unloader in Houston, Texas, USA is now helping an undisclosed owner switch from bagged to bulk deliveries of cement.
“The operator was looking to expand its US operations,” explains Per Wahlström, Contract Manager, Bruks Siwertell. “For some time, it has imported bagged deliveries of cement, but bulk imports hold the potential for greater market impact.
“The Siwertell unloader was an ideal choice for this terminal,” adds Wahlström. “It was light enough to minimize jetty reinforcement costs, but still deliver the throughship capacity that it required. Performance tests have gone to plan, and the operator is happy.”
The new rail-mounted Siwertell unloader offers continuous dust-free cement handling at a rated capacity of 1,500t/h, with a peak capacity of 1,650t/h, discharging vessels up to 80,000 dwt. Furthermore, as it is totally enclosed, no dry bulk material is lost through spillage. Bruks Siwertell also supplied 1.6m-wide jetty conveyors, with a belt length of 192m.
Good service keeps Mailiao ship unloader in peak condition
In a new service contract, Bruks Siwertell will deliver original equipment manufacturer (OEM) parts and expertise to a long-serving ship unloader at the 4,200 MW Mailiao power plant; the third largest operating in Taiwan.
Six large Siwertell unloaders, owned and operated by Formosa Petrochemical Corporation (FPC) and Mai-Liao Power Corporation (MPC), supply fuel to the plant. Three of these were delivered in 2001, two in 2006 and one in 2018. Four Siwertell ST 790-type unloaders handle coal, and one ST 790 and one ST 940-DOB unloader are combined coal and salt unloaders.
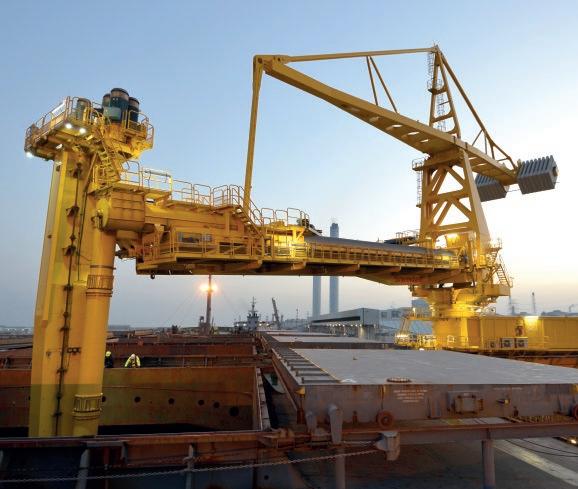
A new electrical system will be installed on a long-serving Siwertell ship unloader at the Mailiao power plant in Taiwan
Bruks Siwertell will deliver a new electrical system including a motor control center and transformer housing for one of the 2006-delivered ST 790 ship unloaders, which currently handles salt and coal at a rated capacity of 2,000t/h, discharging vessels up to 180,000 dwt.
“Over the years, these hard-working machines have been kept in excellent condition, and after clocking-up over 30,000 operational hours have undergone major electrical and mechanical upgrades and overhauls, including replacement slewing bearings and an upper turret exchange,” says Tony Aronsson, Area Manager APAC, Bruks Siwertell. “We did discuss several options, including overhauling the existing system and components within the motor control center and transformer housing,” Aronsson explains. “However, this would have been extremely time-consuming and incur considerable downtime for the ship unloader; not a realistic option for the power plant as the unloaders are in near-constant operation. Our solution was to exchange the parts entirely, delivering a fully equipped and tested system in a fraction of the time.”
The replacement system will be installed in 2022. It will take about six weeks to complete, minimizing any downtime.
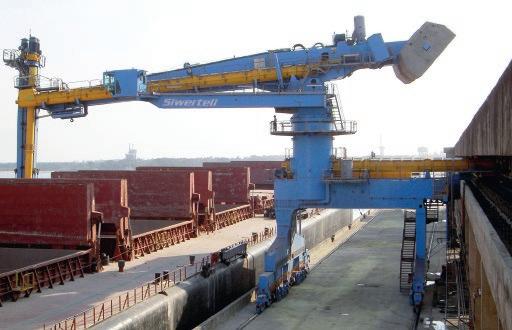
A second Siwertell ship unloader has been ordered by PPL for the Indian port of Paradeep
Repeat unloader order secures safe sulfur handling in Paradeep
A second Siwertell screw-type ship unloader will be delivered to leading Indian fertilizer company, Paradeep Phosphates Ltd (PPL), operating at the port of Paradeep, in Odisha, India. The new Siwertell 640 D-type ship unloader joins a similar unit, which has been serving the company since 2006.
Similar to its predecessor, the new rail-mounted ST 640-D unit has the capacity to discharge sulfur from vessels up to 60,000 dwt, at a rated capacity of 1,500t/h. It will alternate handling this cargo with rock phosphate at a rate of 1,200t/h and muriate of potash (MOP) at 1,050t/h. The unloader will work on the same jetty as Bruks Siwertell’s previous delivery for PPL, and double the operator’s material handling capacity. Both units, like all Siwertell ship unloaders that handle sulfur, are fitted with the Siwertell Sulfur Safety System (4S), which minimizes the risk of explosions when handling this extremely volatile and corrosive dry bulk material.
The new unloader will be delivered to the port in component parts and assembled on site. It is scheduled to enter operations at the end of 2022.
Siwertell screw-type loader ensures dust-free dry bulk handling in the Caribbean
A Siwertell screw-type ship loader, ordered for totally enclosed, dust-free cement and clinker handling, will enter operations at a new cement plant being built in the Caribbean. It provides a unique solution for a complex set of dry bulk material handling requirements.
“We are delighted to be working on this project and our expertise has been called upon from the start,” says Axel Dahl, Sales Manager, Bruks Siwertell. “It really has been a case of engineering experts coming together to solve a particularly complex set of operational and dry bulk material handling needs. us was to consider robust screw-conveyor technology. The final design offers benefits to both the environment and the operator; a screw-type loader that delivers totally enclosed material conveying, preventing dust emissions and spillage, combined with the ability to withstand the abrasive effects of tougher dry bulks, like clinker, prolonging component wear and service life,” adds Dahl.
The type-1B ship loader will deliver cement and clinker handling at a continuous rated capacity of 600t/h, with a peak loading rate of 750t/h, for vessels up to 20,000 dwt.
“This is our first Siwertell loader installation in this particular region, which is currently undergoing some of its most advanced improvements in decades. The equipment has to protect the environment and work in one of the most earthquake-prone zones of the world,” Dahl continues. “Some of the technical challenges that we had to consider for the contract included a new optimized conveying system for handling clinker.
“It is a very abrasive material and wears down standarddesigned components relatively quickly. The obvious choice for
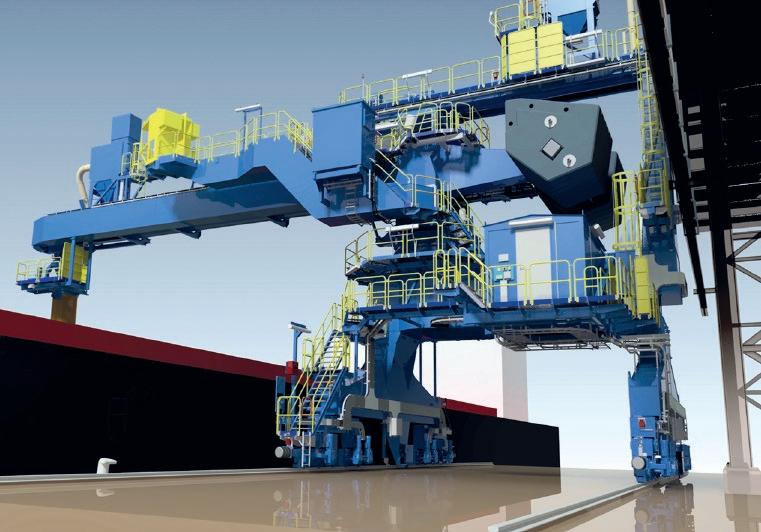
The new loader solves a particularly complex set of operational and material handling needs