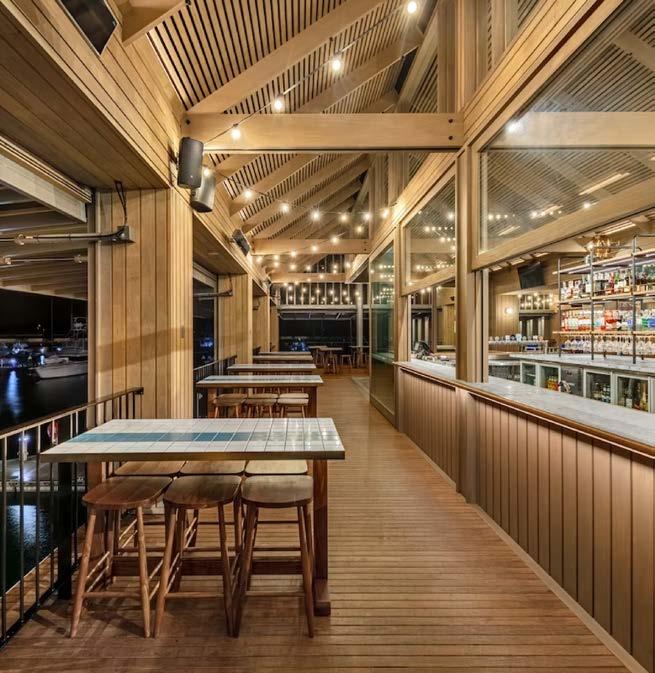
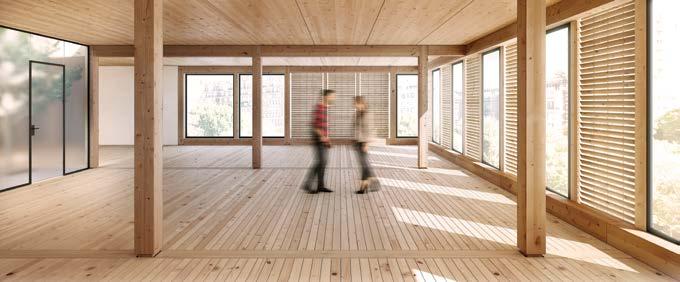
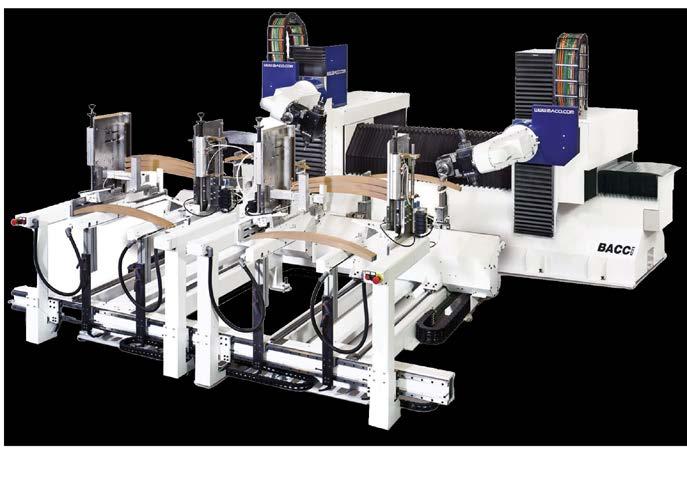
RESIDENTIAL CLASS 1 – NEW BUILDINGS
Sponsor: Pentarch Forestry
THE HÜTT 01 PASSIVE HOUSE
MELBOURNE DESIGN STUDIOS
Structural Engineer: GCE Consulting Engineers Builder: G–Lux Builders
Timber Supplier and Fabricator: Hutt Sustainable Building Supplies Location: Melbourne, Victoria.
RESIDENTIAL CLASS 1 – ALTERATION OR ADDITION –
Sponsor: TimberNSW
BARWON HEADS HOUSE
ADAM KANE ARCHITECTS
Builder: Technique Construction Group Location: Barwon Heads, Victoria
INTERIOR FITOUT – RESIDENTIAL
Sponsor: Pentarch Forestry THE PAD
SUZANNE HUNT ARCHITECT
Structural Engineer: Cenit Structural Engineers Builder: Valento Residences Location: Perth, Western Australia
MULTI–RESIDENTIAL
Sponsor: XLam Australia
IRON CREEK BAY FARM STAY
MISHO + ASSOCIATES
Structural Engineer: XLam Australia Builder: EG Building
Timber Supplier and Fabricator: XLam Australia, Hyne Timber Location: Sorell, Tasmania
COMMERCIAL BUILDINGS
Sponsor: XLam Australia
WATERFRONT TAVERN H & E ARCHITECTS
Structural Engineer: Cantilever Consulting Engineers
Builder: New England Constructions Location: Shell Cove, New South Wales
PUBLIC BUILDING
Sponsor: Rubner/Theca Australia
POINT LONSDALE SURF LIFE SAVING CLUB JACKSON CLEMENTS BURROWS
Structural Engineer: Vistek – Structural and Civil Engineers Builder: Lyons Construction Project Manager: PDS Group Location: Point Lonsdale, Victoria
INTERIOR FITOUT – COMMERCIAL OR PUBLIC
Sponsor: Binderholz Group WALSH BAY ARTS PRECINCT TONKIN ZULAIKHA GREER
THE winner of this year’s Timber Design Award is the Waterfront Tavern at Shell Cove south of Wollongong in New South Wales.
The tavern was designed by leading Sydney firm H&E Architects led by co-directors Chris Grinham and Glenn Cunnington.
The awards were presented on December 8 at the Crown in Sydney at an event hosted by The Ultimate Renewable brand ambassador Adam Doville.
The form of the building consists of four pavilions of differing lengths resulting in a building that partially cantilevers over the public boardwalk and water below.
The central premise is conceptualised around the appeal of timber boathouses.
Acetylated radiata pine was chosen externally – trialled and stained until a correct ‘aged’ patina was discovered, assuring conformity of natural wear.
The exterior consists of acetylated
pine, used as weatherboards, exposed framing, batten external soffit and window and door joinery.
The interior consists of American red Oak linings, clear pine batten ceiling, and T&G oak flooring.
The quality of the build is evident and impressive and captured the attention of the judging panel. From the pavilion roofs, the operable exterior walls, and the bistro’s boardwalk – fine artistry is layered throughout the whole build, exceptional in a commercial context.
Ultimately, there’s an immediate warmth such timber use brings – important given the Waterfront Tavern must also work as a community anchor to the new development. Such warmth carries to the interior –where planning was forged on the maximisation of the views.
From the material selection, architectural form, creative and operable features, and fine craftsmanship, this project is an exceptional celebration of what is possible with timber design. This project is sure to be cher-
ished by its local community. It will undoubtedly inspire others to push the creative limits of designing our buildings with timber as the winner of the Australian Timber Design Awards 2022.
Structural Engineer: Taylor Thomson Whitting Builder: Richard Crookes Construction Timber Supplier and Fabricator: Ultraflex Location: Sydney, New South Wales
STAND–ALONE STRUCTURES AND OUTDOOR APPLICATIONS
Sponsor: Design Pine
GRAMPIANS PEAKS TRAIL STAGE 2
NOXON GIFFEN ARCHITECTS
Structural Engineer: OPS Engineers Builder: Linct Group Location: Grampian Ranges, Victoria
AUSTRALIAN CERTIFIED TIMBER
Sponsor: Responsible Wood
ANNANDALE CLT HOUSE
STILL SPACE ARCHITECTURE
Structural Engineer: Sellick Consultants Builder: Arc Projects
Timber Supplier and Fabricator: XLam Australia Location: Sydney, New South Wales
RECYCLED TIMBER
Sponsor: Kennedy’s Timber BONES HOUSE
LACHLAN SHEPHERD ARCHITECTS
Structural Engineer: PM Design Group Builder: Torquay Homes
Location: Bells Beach, Victoria
Issue 8 – Volume 32
Incorporating Australian and New Zealand Timberman. Established 1977.
News 3-8
Tooling 10 Decking 11 Associations 16-19
FRONT Cover: The interior of this year's Timber Design Award, the Waterfront Tavern at Shell Cove south of Wollongong in New South Wales. Picture: Murray Fredericks Photography
PUBLISHER and Chief Executive: Hartley Higgins
General Manager: Robyn Haworth
Editor: Bruce Mitchell b.mitchell@ryanmediapl.com.au Adelaide Office (08) 8369 9512
Advertising: Gavin de Almeida g.dealmeida@ryanmediapl.com.au Adelaide Office (08) 8369 9517
Creative Services: Tim Coleman
Publication Design: Tim Coleman Timber classifieds: g.dealmeida@ryanmediapl.com.au Adelaide Office (08) 8369 9517
Subscriptions: subs@forestsandtimber.com.au Adelaide Office (08) 8369 9522
Subcription rates
One-year (8 editions) $55 Two-years (16 editions) $95
Accounts: Adelaide Office (08) 8369 9514
Postal Address: 630 Regency Road, Broadview South Australia 5083 Phone: (08) 8369 9555 Fax: (08) 8369 9501
Melbourne Office: Suite 2262, 442 Auburn Rd, Hawthorn VIC 3122 Phone: (03) 9810 3262
Find us on Facebook
@AustralasianTimber Website www.timberbiz.com.au
Printed by Lane Print, Adelaide, SA
The opinions expressed in Australasian Timber Magazine are not necessarily the opinions of or endorsed by the editor or publisher unless otherwise stated.
All articles submitted for publication become the property of the publisher. All material in Australasian Timber Magazine copyright 2022 © Ryan Media. All rights reserved. No part may be reproduced or copied in any form or by any means (graphic, electronic, or mechanical including information and retrieval systems) without written permission of the publisher. While every effort has been made to ensure the accuracy of information, the publisher will not accept responsibility for errors or omissions, or for any consequences arising from reliance on information published.
AUSTRALIA’S first mass engineered timber fire and emergency services complex has officially opened in Maryborough, Queensland.
The design and construction of the Queensland Fire and Emergency Services North Coast Region Headquarters and Maryborough Fire and Rescue Station is a story of innovation, collaboration, restoration, and carbon sequestration.
Hyne Timber’s Strategic Relations Manager Katie Fowden said the whole project started as an idea at an innovation forum held in Maryborough.
“From a light-bulb moment inspired by innovative discussion, through to the opening of the completed building, this has been an extraordinary journey, bringing together many people who knew this would deliver a great outcome for our frontline responders,” Ms Fowden said.
Entering the Queensland Government’s Market Led Proposal process, Hyne Timber brought together partners including XLam, Hutchinson Builders, Baber Studio, the University of Queensland’s Centre for Future Timber Structures and Bligh Tanner.
“Together, we progressed through stages until we were officially working with the client, Queensland Fire and Emergency Services to ensure we were designing and
delivering a contemporary, state-of-the-art and fit for purpose, mass timber hybrid solution. Attending the official opening was a proud moment for us all and I can’t thank all the partners enough for sharing this journey with us.”
The design included the restoration of the original brick façade which is considered of heritage value to the Fraser Coast community while specifying materials to ensure the right use of the best material, prioritising XLam’s Cross Laminated Timber and Hyne Timber’s locally sourced and manufactured Glue Laminated Timber beams for the new structure.
XLam’s Business Development Manager, Robert Mansell said the new building delivered many benefits.
“The mass engineered structure of this new building delivers excellent fire performance qualities, carbon sequestration, aesthetic appeal and prefabrication for faster construction. In addition to these benefits there will be long term biophilic benefits for the people that will use this fantastic new complex,” he said.
“All the materials from walls, floors, ceilings, stairs and even the tower were delivered on trucks in the correct order that it comes off for immediate construction, minimising the need for set down space, and as the community witnessed, very fast construction.”
The new facility constructed mainly with timber is a first for Queensland and Australia and hopefully inspires Government and design professionals to consider future mass timber projects.
“XLam Engineers supported by the broader team, developed XLam’s first ‘Band Beam’ solution which improved overall head height in the lower level allowing easy installation for mechanical services while improving the overall performance of the floor system above. This is possible the first of its kind in the world,” Mr Mansell said
Principal architect Kim Baber said the specification of locally grown and manufactured engineered timber was a key part of the design from the onset.
“We know when building a mass engineered timber building that the benefits come from early contractor involvement. It is imperative to be designing for manufacture and assembly by partnering with the timber suppliers early for support, especially XLam and their inhouse design solution specialists,” Mr Baber said.
AS 2022 draws to an end it is a chance, given the past two years, to draw breath.
Life, as we know it, seems to be getting back to some sort of normal with Covid restrictions almost a thing of the past.
Almost - the use of facemasks is still being quietly recommended by some State Governments given the appearance of new cases as we approach Christmas.
Still, it was heartening to see the Timber Design
Awards return to an actual event instead of a virtual gathering.
The awards, now in their 23rd year, celebrate the excellent work being done with timber by architects, designers and builders across the country. Each year the quality and ingenuity, as well as the beauty, seems to surpass the year before, as does the
desire by decision makers to see more and more timber used in major construction projects.
And so often the timber being sought is engineered wood, the use of which is now the subject of new research by Stora Enso into how to prevent fungal and structural decay. Given the rainfall the eastern seaboard has experienced in recent months that research is now most timely.
I would like to thank the many contributors and industry organisations who are
integral to this publication, plus the advertisers who have supported us to bring it to our readers. Our sales, editorial production and support team remain passionate about the industry and we look forward to serving our customers and readers in 2023.
After all, we print your industry details on a product that you produce.
Best wishes to all for a Merry and Safe Christmas followed by a Prosperous New Year.
Bruce Mitchell EditorISAAC Griffin began his Certificate IV in Timber Truss & Frame design with his employer Dahlsens.
In 2021 he transitioned to Certificate IV in Timber Systems designs due to a training package update and is on track to complete in October 2023.
And this year he won the Student of the Year award at the 2022 TABMA NSW Awards for his outstanding commitment to his traineeship.
Isaac has always been a dedicated and hard-working young man. Isaac’s work history is a testament to his strong work ethic.
“I have worked at my grandparents fishing tackle shop, then went to a butcher shop washing dishes and scrubbing the floors of an
afternoon after school, then worked at Woolworths for seven years where I became a supervisor, then worked at a place that specialised in 2 Pac kitchen painting and then started here at Dahlsens.”
Isaac explains how the most enjoyable part of the course is extending his knowledge and applying it to his everyday work.
Colin Taranto, Isaac’s trainer states that “Isaac has a real willingness to learn and has produced quality assessments. Isaac enrolled into the old Cert IV which required 6 pre-requisite design units to
be completed before commencing the current Cert IV, all of which were completed. I have seen Isaac’s knowledge and experience grow since commencing, feedback from his employer is very positive commenting on his great attitude to taking on more responsibility. Isaac will be a great asset to whoever he works for and will no doubt make a career in design and detailing”.
“I would recommend TABMA because everyone is very helpful whenever I need guidance in regard to my assessments. Colin Taranto has been super helpful, nothing is ever an issue and the course is put together so well that it makes it easy to follow”, says Isaac.
TABMA Australia is proud of what Isaac has achieved and are excited to be a part of his journey.
Is your business in need of an apprentice or trainee or looking to upskill your current workforce? TABMA Australia can assist you through our Group Training Organisation (GTO) and our Registered Training Organisation (RTO).
David Proudford, Manager of the Dahlsens Ulladulla truss and frame manufacturing plant has witnessed Isaac’s growth firsthand.
“Since Isaac joined us as a trainee, we’ve watched him become more confident as he has improved his skills in detailing, estimating and customer liaison. This growth has come from his-on-the-job
skills development and learnings, supplemented by learnings from the other students, the trainers, and his study. We’re thrilled to have Isaac on the team,” said David.
Rob Mavin, Dahlsens’ Regional Manager Trade NSW, says that as a long-term member of Tabma Dahlsens hugely values the young people that Tabma continues to introduce to our business.
“Today, we employ trainees at most sites across our network – these are very much relied upon team members, some who have progressed into leadership roles. Thanks to Tabma, we are recruiting go-getters who might not have considered jobs in our industry. It’s a great partnership,” Rob said.
STORA Enso and Voodin Blade Technology
GmbH have signed a partnership agreement to develop sustainable wind turbine blades from wood.
Under the agreement, the two companies are committed to developing sustainable alternatives for wind turbine blades and creating a competitive and reliable supply chain. They are currently producing and installing a 20 m blade for a 0.5 MW turbine and have plans for an 80m blade.
Voodin Blades is a Germanbased start-up company developing sustainable rotor blades for wind turbines and the partnership supports Stora Enso’s strategic offering of innovative solutions to replace less environmental-friendly materials with renewable ones made from wood.
Wind power blades are typically produced with fibreglass and carbon fibre, energy-intensive non-renewable plastics made from petrochemicals that cannot be easily recycled. Tens of thousands of ageing blades today end up in landfill. By developing blades with sustainable wood, Stora Enso and Voodin Blades can make the blades lighter and reduce the overall dependency on fossil fuel extraction.
Stora Enso is providing 100% sustainable wood for the new blades. The first 20 m blade will be developed using Stora Enso’s LVL, a mass timber product that has a high load-bearing capacity that easily supports largescale rotary blades. Unlike steel and concrete, LVL is relatively lightweight to transport on-site without heavy-duty equipment. Furthermore, LVL is a renewable material with a minimal carbon footprint. The 20 m blade will be installed on a 0.5-megawatt turbine near Warburg, Germany by the end of 2022.
In addition to its collaboration with Voodin Blades, Stora Enso recently announced a partnership with wood technology company Modvion to establish wood as the material of choice for wind turbine towers.
COMPANIES looking for ways to reduce carbon emissions are turning to mass timber as a climate and building solution.
With efforts to find new ways to lock up carbon, developers, architects and net zero committed companies are asking, “is wood the new concrete?” New technology in what’s called mass timber production offers a carboncutting alternative to concrete and steel in the building sector.
In addition to the aesthetic benefits of wood as a building material, advocates say that using timber can substantially reduce the building sector’s greenhouse gas emissions. Its use can also slash waste, pollution, costs and time compared with the materials more commonly used now.
“Mass timber isn’t the right material forever, but it’s the right material for now,” says architect Michael Green, a
timber building proponent based in Vancouver. “If we had other carbon-neutral ways of building, we wouldn’t need mass timber.”
New techniques to trim, dry and glue planks of wood together — including waste wood — to create large “slabs,” mass timber is now being used for everything from floors, walls and ceilings to entire buildings and skyscrapers … even cities.
Tech giant Microsoft is currently updating its campus in Silicon Valley, using timber with its carbon and other eco benefits in mind. At 644,000 square feet, the campus will be the largest mass timber project in North America.
“The use of mass timber is part of Microsoft’s commitment to becoming carbon negative by 2030, including reducing our Scope 3 Emissions by 55%,” said Darren Lombardi, senior real estate manager at Microsoft SVC. Scope 3 Emissions are those from customers or assets
not owned or controlled by a company but that indirectly impact its value chain and emissions. Microsoft uses data from an Embodied Carbon Calculator for Construction (EC3) tool, which analyzes construction materials, for data to drive building decisions including the most effective ways to reduce carbon.
Currently, the world’s tallest mass timber building is in Norway at 18 stories and 280 feet. City planners in Helsinki, Finland, are creating what’s called Wood City, an entire city made using timber as the key building material.
“Mass timber encompasses a suite of building elements that transform relatively lowvalue timber feedstock into structural elements that have superior weight-to-strength performance than steel or concrete,” says Keith Crews, a professor at Australia’s University of Queensland. Supporting energy-efficient buildings throughout their
life cycle can be an effective way to reduce long-term carbon emissions and push toward net zero, he said.
Typically, mass timber is made using fast-growing softwood trees like fir, pine and spruce. A variety of methods are used to make it into a durable and adaptable building material, including dowellaminated (DLT), glue-laminated (Glulam or GLT) beams, laminated veneer lumber (LVL) and nail-laminated timber (NLT). The type that shows the most promise for large construction projects is cross-laminated timber (CLT).
“It’s a bit like what IKEA has done with furniture,” Crews says. “Everything is prefabricated to very high tolerances, arrives in a flat pack, and is assembled into the final product.”
Emissions from the building sector accounted for nearly 38% of total green-
house gas emissions globally and hit an all-time high in 2019, according to a new U.N. Environment Program report. Using timber in place of steel and concrete can significantly reduce construction’s carbon footprint by preventing carbon from entering the atmosphere and sequestering it for the lifetime of the building. Because wood captures and stores carbon via photosynthesis, proponents say mass timber functions as a form of carbon removal.
Construction is a $9 trillion industry, and mass timber production is a growing enterprise that is newly part of the climate change solution. It’s estimated that the global CLT market, just one of a variety of mass timber products, will reach $3.5 billion by 2027.
Michel Green says there needs to be a continued push on investment and innovation to find ways to build better, and mass timber is just a
stepping stone for what we can ultimately do.
Some of the global leaders using mass timber include Stora Enso in Finland, Mayr Melnhof Holz Holding AG in Austria and Xlam Ltd. in Australia & New Zealand. Global developer Lendlease has built several multi-story timber buildings in its home base of Australia. Walmart is even getting into the mass timber game and contracting with Structurlam, North America’s leading provider of mass timber, to build their new campus offices.
Mass timber can play a role in creating a circular economy and provides jobs in forestry, design, construction and installation, according to a report from the Forest Economic Advisors. In an ideal world, Bodie said, we’d use less wood for pulp and paper –– through increased recycling and other means –– so that it can be used for mass timber instead.
“Shifting our wood use from shortlived products to long-lived products like [buildings] would have huge climate benefits,” Bodie said.
A2022 survey of New Zealand design, construction and building professionals into the perceptions and barriers to mass timber use in construction highlights a growing awareness and adoption of mass timber however also that more can be done.
The survey was distributed to manufacturers, builders, architects, designers, engineers, building officials and quantity surveyors. It was commissioned by the Mid-Rise Wood Construction Programme and carried out by BRANZ, using the same format as a 2019 survey for comparing results.
The analysis report of the survey noted that recent years have seen a significant global increase in the use of timber products within the built environment.
A major portion of this increase being attributable to engineered wood products (EWPs), from large-scale structural elements through to nonstructural and decorative components used on the interior and exterior of buildings. This includes materials such as LVL, CLT, plywood, particleboard, and other composite products utilising wood as a base material.
The report concluded that there was a general impression that barriers do exist to increasing the uptake of EWPs in the New Zealand construction in-
dustry. These barriers, as well as perceived advantages of using EWPs, manifested themselves in different ways and could be summarised into four categories: cost, availability, regulation and standards, and Information/Education.
An increased and thorough understanding of the environmental impacts of EWPs is also seen as necessary in order to determine the effects of including these products for building projects, particularly in light of the recently introduced climate change objectives from the Ministry for Building, Innovation & Employment. This combination of information and education would need to include the carbon benefits of using more timber, but also the potential detriments of manufacturing processes, treatments and adhesives used and end-of-life impacts.
The recommendations of the report for supporting greater uptake of EWPs were to develop more data on the economic and environmental impact of using EWPs including Life Cycle Analysis, to continue to provide detailed case studies of buildings using EWPs, to provide more education on EWP’s to building sector players, the public and at tertiary level and to provide more design and product information on specific EWP’s.
The Combilift range of warehouse forklifts and pedestrian reach trucks will allow you to maximize the storage, efficiency and safety of your warehouse & storage facility.
Contact us today to find out how Combilift can help you unlock every inch of your space
combilift.com
TASMANIA has appointed its first Wood Encouragement Officer.
Gary Fleming has been jointly appointed by the Tasmanian Timber Promotion Board (TTPB) and the University of Tasmania.
Mr Fleming will collaborate with industry stakeholders including project design teams, government agencies, and suppliers to identify and facilitate project opportunities that increase the use of timber and wood products.
This appointment is supported by $150,000 from the Tasmanian Government and delivers on a 2021 election commitment.
With a background in architecture and having worked on multiple projects involving the use of timber, Mr Fleming has a passion for seeing Tasmanian timber used in the built environment.
He will be based at the University’s Centre for Sustainable Architecture with Wood, an industry-funded research facility of the School of Architecture and Design.
Mr Fleming will also help the TTPB leverage further benefits from its marketing campaign, which is being supported by an additional $1 million in Tasmanian Government funding.
TTPB deputy Chair Shawn Britton said part of Mr Fleming’s role would also be to encourage the public and the private sector to consider the use of Tasmanian wood, timber products and bioenergy, particularly in construction, fit out, and building and construction projects.
“The timing of this new role is perfect as the need for timber and wood is increasing, as we know wood has multiple benefits from environmental, health and wellbeing, and creating a circular building sector in the State,” Mr Britton said.
While the forestry sector is worth about $1.2 billion to the economy annually, growth through the Wood Encouragement Policy will provide more benefits to the economy and local communities and support more regional jobs.
TIMBER-FRAMED construction is robust and resilient even when exposed to moisture and other extreme conditions.
When adverse conditions, extreme weather or other unexpected circumstances occur there is no one size fits all approach to assessing the impact. Each instance must be evaluated on a case-bycase basis to determine the extent of any degradation and the rectification or repair that is required.
How to assess moisture affected timber
Many factors must be considered when assessing timber-framed construction that has been affected by moisture including:
• macro and micro climatic conditions
• length of exposure
• number and intensity of rain days
• sun exposure
• drying conditions and prevailing winds
• temperature
• degree of protection from weather
• for flood or tidal surge, length of time inundated
• if the water is contaminated with chemicals or sewage, etc...
When unfinished homes and exposed timber are subject to weather, the level of degradation depends on a combination of these factors.
Some structures will require extensive repair, while others will have little to no longterm damage if addressed and dried as quickly and safely as possible. Ask a professional builder to perform a detailed evaluation and the subsequent repairs and replacements.
Waterlogged timber is often thrown away when it doesn’t need to be. The good news is that waterlogged timber can be saved and reused, and information is available for free on the WoodSolutions website. This includes resources for builders that can help assess if a home’s timber frame is salvageable and what people affected by flood can do to help save or protect items during clean-up.
WoodSolutions Technical Design Guide 12 – Impact and Assessment of MoistureAffected Timber Construction has been written by experts and is backed by extensive research. The Guide has been prepared to assist the building industry and owners understand the key issues and factors that need to be considered when assessing
moisture-affected timber construction and to provide some guidance on how to address these considerations. What to do if your timber home has been flooded Here are some simple tips that everyone can use to help preserve all or part of a home’s timber frame that has suffered from water damage for the long-term.
Mould grows incredibly fast – sometimes as quickly as 24 to 48 hours after exposure to moisture. While mould does not damage the structural capacity of timber, it does create a health hazard, especially if timber is allowed to decay.
Once it is safe to do so, the sooner you can act to minimise damage the better.
The most important thing to do is to open walls and other closed cavities to allow for airflow. It is usually best to remove deluged plasterboard and insulation as in most cases they are beyond salvage. They should be removed at least up to the point where wetting occurred.
Timber saturates far more quickly than it dries, but you can speed up the drying process by exposing the timber and increasing airflow with fans, if possible.
A simple moisture meter, available from most building centres and hardware stores, can help you determine when the wood has dried.
Timber that reaches below 20% moisture content and is free of mould can generally be reused. The areas of a flood-damaged frame most likely to have the highest moisture content are bottom plates under slabs or sheet floors as well as the parts of studs that are lowest to the ground.
How quickly the timber dries after being exposed to air is dependent on different factors such as how long the timber was submerged, how soon after it being submerged it was exposed to air and local weather conditions.
It can be difficult to determine what is salvageable because there are so many variables involved. Once the timber has dried, put it aside to be checked out by a professional before confirming that the timber can be reused.
Get more information
More detailed information can be found at www. woodsolutions.com.au and by downloading Technical Design Guide 12 – Impact and Assessment of Moistureaffected Timber-framed Construction.
OMNIA House, by Elizabeth Wheeler of Future Focus Buildings and Tamar Boyd of Blue Lotus Energy Rating, have taken out the National Award for the Design Matters National True Zero Carbon Challenge 2022.
In addition to the National Award, Omnia House also came away with the Victorian State Award.
The DMN True Zero Carbon Challenge is an annual competition where a building designer and home energy assessor team up to design a home that not only produces more power than it uses over a year but calculates embodied carbon in material selection. Through energy-efficient design, careful appliance selection and enough photovoltaic panels to pay back the home’s entire carbon debt by 2050 this inaugural competition attracted entries from across Australia.
This Challenge not only furnishes entrants with the necessary skills to thrive in the coming decades but paves the way to true Net Zero housing. The competition is pivotal to show what is possible and to let the industry know that DMN members are ready, willing, and able to meet the challenges of the low carbon future.
“DMN Members Elizabeth Wheeler and Tamar Boyd were the deserving recipients of the highest accolade in the 2022 True Zero Carbon Challenge Awards which saw entries from Victoria, New South Wales, Western Australia, South Australia, Tasmania, and Queensland, this year,” DMN CEO Peta Anderson said.
“We congratulate Elizabeth Wheeler and Tamar Boyd on winning the Victorian and National Awards in this year’s inaugural DMN True Zero Carbon Challenge. Their project is a real stand-out, sustainable, and ready to build. Omnia House makes a strong sustainable statement and is an exceptional conceptual design,” Ms Anderson said.
WITH nine out of ten CNC machines sold in Australia being nesting machines, one of the most-used cutting tools in Australia is the small diameter router cutter. Manufacturers utilising panel products, solid wood and advanced materials for production of goods where manufactured boards are the main raw material (kitchens, office furniture etc), are always looking to increase production while reducing unit costs.
A small diameter cutter is required to reduce the amount of waste in a nested board, but this can reduce production speed. The tool also needs to eliminate any breakout on both surfaces of the material, resulting in the call for a very unique and complex tool.
Enter the compression cutter that has completely revolutionised the small scale, high turnover nested manufacturing cabinet industry in Australia, the United States and the United Kingdom – the Carbide Compression Router Cutter. It’s fair to say that the small diameter router bit is one of the hardest working tools used by the industry.
Compression cutters for nesting historically have been imported from the United States, Europe and now SE Asia, but a few years ago, Leitz Australia considered the possibility of manufacturing them here.
“We said at the time we’d love to be able to make these cutters ourselves,” Andrew Bismire, Product Manager of Leitz Australia, said.
“It’s something we can do that’s purely Australian and would add unique benefits to both Leitz and our local manufacturers.”
Following the belief that a CNC Machine is only as good as the tools being used, the Compression Router Cutter range developed by Leitz Australia is produced to exact high precision standards required by their German parent company. With more than 145 years experience producing cutting tools for the woodworking industry, Leitz is one of the top producers of quality, premium tools in the world. This rich Leitz history has ensured that
Leitz Australia has the technical knowledge and skill to manufacture these highly engineered and complex tools. There were some compelling economic reasons to manufacture in Australia; largely being the ability to provide speed of supply to the local market. Leitz also believes there are significant benefits to local manufacturers. An example of this is the partnership that resulted with ANCA – a market leader in quality CNC grinding machines, and an Australian local success story.
Leitz already had several pieces of high-end grinding equipment for automatic sharpening of cutting tools, but only one machine for producing router bits. To meet the expected product demand, a higher output machine was required, as well
as one that could produce at a standard that would satisfy Leitz’ exacting tolerances.
Leitz installed one Australian made ANCA FX7 Linear 5-axis tool grinder equipped with a robot inside the cabinet for changing router cutters and grinding wheels. This was soon followed by a second ANCA FX7 machine. These machines can run unattended, with a capacity of several hundred router bits at a time and are equipped with a refrigerated coolant system to ensure that heat does not affect the fine tolerances the machine works to.
The ANCA FX7s are fully programmable– ensuring consistent high-quality standards of every router bit produced. The ANCA machine puts Leitz at the forefront of router manufacturing in Australia.
Striving for the utmost quality in everything they do, Leitz Australia only uses the best quality carbide rod for their router bits. Carbide can be made from soft to hard, so the right grade is required to get the most life from the tools, while not being too brittle and breaking under load. Both characteristics are important in a quality tool and the reputation of Leitz and their customer’s production depends on it.
Leitz Australia takes pride in that due to this this local production, these compression bits can be customised to suit individual manufacturer’s needs and a large range of machines.
“We chase microns to get the desired result for our customers,” Mr Bismire said.
“Provided the customer has a machine where the collet is in good condition and holds the bit over its entire clamping length, we can achieve up to 40% more tool life from the cutters we make here in Australia.”
This has been verified by a manufacturer capable of recording actual lineal metres, in trials conducted in conjunction with Leitz Australia.
Leitz Australia’s achievement of producing these tools themselves has increased local production levels and reduced delivery times for customers while maintaining the highest quality. It also increases tool production skills within Australia, an opportunity for apprenticeship programs and a long-term benefit to the industry. The compression router bits carry the Australian Made logo and have proven to be hugely popular with manufacturers keen on supporting local productions.
WITH access to nature on our doorsteps, it’s no surprise that Australian’s love spending time outside.
An increasing demand to enjoy outdoor living at home has turned the humble backyard into an al fresco lifestyle dream. Homeowners investing in this multi-functional space are finding it offers a variety of benefits that provide a long-term contribution to their property investment and, more importantly, their lifestyle.
Installing a timber deck will allow the area to be used in most weather conditions.
Considering the deck’s purpose will help decide its size. How many people will it need to accommodate, for example.
“Look for timbers that are designed for exterior use, remembering, the better quality the materials, the greater the longevity of your deck. There are two choices when
selecting the best timber for a deck: softwood or hardwood. The decision is dependent on budget, required lifespan and quality of finish,” says John Lorente, General Manager, Big River Group.
“Spotted Gum and Merbau are the most common hardwood decking options in Australia and, with regular maintenance, should last 20 plus years. Treated pine is the preferred softwood option and is a good value option.”
When deciding on the timber, colour, texture and the environment can play an important role. Durable hardwoods are easy to stain or oil to complement an outdoor colour scheme or can be left raw to create a natural, weathered look. Merbau timber requires much less main-
tenance than some other hardwoods and is known for its beautiful rich reddish colour and wavy grain design, as well as its high usability, resistance to termites and resilience. Australian native Spotted Gum gradually turns a golden light brown through to chocolate brown as it matures, depending upon the type of Spotted Gum chosen. Spotted Gum also has an attractive grain structure with knots and growth lines, as well as minimal shrinkage which all add to its popularity.
If the home is in a bushfireprone area, consider Merbau and Spotted Gum timber which are both bushfire resistant and suitable for use in many bushfire prone areas up to BAL 29, as set out under Australian Standard AS3959.
Treated pine is a sustainable and prolific outdoor decking option that can be painted or stained to match any colour scheme, unlike
other woods that only showcase certain colours well.
Additional considerations when choosing your timber type include the location of the deck at your home. Darker coloured decks will absorb heat from the sun, so if your deck is on the south side of your house, a dark coloured
floor can make it very difficult to use the deck during the afternoon and early evening in summer, so it may be wise to opt for a lighter deck colour instead of a darker one. A covered deck is a way to create some shade and prevent your deck’s surface from overheating during the summer.
Margules Groome are independent consultants to the forestry, wood products, bio solutions, pulp & paper, and agriculture sectors.
Our unique combination of forest management and consulting skills, deep industry knowledge and technical know-how, enables us to provide a wide range of expert services. These include forest valuation and transaction due
diligence, sales advisory services, analysis and advice for forest owners, resource planning and business strategy, markets and market forecasts, operations and tech solutions.
At its core, Margules Groome stands for objectivity, impartiality and ethical business practice. Professionalism and integrity underpin everything we do.
Australian Sustainable Hardwoods has assured its customers that the Victorian Government’s ban on the harvesting of native timber by 2030 will not affect supply in the immediate future.
And the company says it will be working hard to ensure that sustainably certified, regrowth sawlogs are made available after 2030.
In a statement to customers the company’s managing director Vince Hurley said it would be business as usual for the next six years as ASH did not process of growth.
2016
Composite flooring systems consisting of cross laminated timber with reinforced concrete have significant potential for use in multi-storey buildings such as offices, hospitals and schools throughout Australia, according to a leader within the engineered timber sector in Australia.
Following tests in the US in which a flooring system involving a cross layered timber deck topped with a thin layer of reinforced concrete was shown to support loads of around eight times what is required by code in that country, XLam technical manager Nick Hewson says there are opportunities to use similar types of systems in Australia.
2011
Wood has long been seen as an attractive option for buildings and renovations, and now a new consumer awareness campaign from environmental education organisation Planet Ark is encouraging consumers, architects and builders to see wood for its environmental benefits too.
Planet Ark’s Make It Wood – Do Your World Some Good campaign promotes the increased use of certified, responsibly sourced wood as a building material.
A recent survey conducted by campaign partner Forest and Wood Products Australia (FWPA) showed that although 93% of people understood that trees absorb carbon, only 39% of them realised that when the tree is responsibly harvested and used to make wood products, the carbon remains locked in the wood for the life of the product.
THE Stirling Group, providers of complete solid timber solutions, is excited to announce that their woodworking machinery division, Stirling Machinery, has recently partnered with Italian manufacturer Bacci, in a deal that grants them exclusive distribution rights for Australia and New Zealand. Known worldwide as ‘the innovators of the modern-day CNC’, Bacci draws on over a century of industrial production.
Stirling’s Craig Honeyman says the Bacci lineup features a huge range of CNC options, with 5-axis machines through to double heads and mobile uprights, through to cutting machines and copying lathes.
The machines empower businesses to undertake greater volumes of work and of a more complex nature, with a higher value. They free up highly skilled staff, boast higher output volume and are infinitely capable of repeating very detailed, complex tasks. The Bacci line focuses on component production and is designed with output volume to investment in mind.
In 1998, Bacci became the world’s first company to manufacture 5-axis CNC machining centres with double heads, capable of machining the same piece with two heads working simultaneously.
Bacci machines are multiaxis CNCs which are suited but not limited to solid timber processing. “They range from what we call a standard type of solid timber pod and rail CNC to multi-spindle CNC lathes,” Craig says.
“Their products are designed to help solve component manufacturing bottlenecks in production,” Craig explains. “These may be caused by staff skills shortages, complex designs, hardto-work-with materials or high-volume output.”
Craig also says that one of Bacci’s greatest strengths is its customisation capabilities. Every Bacci machine that leaves the factory is made-to-order and fully tailored to suit the customer’s business requirements. Rather than having to adapt an ‘off-the-rack’ machine,
taking delivery of one that is customised specifically for the volume and type of timber, and the type of tasks it has to perform eliminates operational barriers. Ready to go from the moment it’s installed, and infinitely capable of intricate processing, a Bacci machine offers a truly unparalleled experience.
“Stirling works closely with you and your business to understand your challenges and requirements,” he explains. “Once we have a true understanding of you and your situation, we take this knowledge and collaborate with Bacci to create a machine with custom configuration to suit exactly what you need. From clamping options through to the number of axes required, we’ll tailor your machines in the most efficient way to suit the needs of your business.”
Bacci is the latest machinery brand to partner with The Stirling Group, whose own star continues to rise on the strength of the organisations with whom it aligns.
“At Stirling,” Craig says, “we pride ourselves on pro-
viding the highest quality complete solutions for the solid timber industry. To do that, we’re absolutely committed to connecting our customers with the best possible machinery brands and products available in the market today.”
Stirling enjoys a reputation for outstanding customer service founded on deep expertise, decades of experience and its own long history of business success.
“Our success has not come by accident,” Craig says. “Our culture is one of genuinely focusing on the customer, their needs, their challenges and their operations. We’re out there every day talking to our customers and finding ways to reduce costs and increase revenue for them, while finding solutions for the challenges they face. By partnering with Bacci, we now have another set of solutions in our toolbox, and we look forward to making a meaningful difference to our customers’ businesses. To further support this partnership, Panel Tools is coming onboard as our official tooling supplier.”
Founded in 1918, Bacci was originally a manufacturer of traditional woodwork-
ing machines. Fast forward to the 1950s, the company diverted its focus to producing machinery for the solid wood industry. Over the decades since, Bacci have gained international recognition for the performance, reliability, and longevity of their machines. They hold more than forty international patents and as such, are recognised as global leaders in innovative technologies.
In 1986, Bacci became the first Italian company to receive the USA’s ‘Challengers Award’, a prestigious prize bestowed by the International Woodworking Fair (IWF) in Atlanta. Nine years later, in 1995, Bacci introduced its first 5-axis CNC machine, which now forms the company’s core business. In 1998, the company became the first in the world to manufacture 5-axis CNC machining centres with double heads, capable of machining the same piece with two heads working simultaneously.
It is precisely this level of innovation and expertise that positions Bacci as the world leaders they are, and why Stirling is so proud to partner with them and bring their high-end products to customers here in Australia.
WHILE on the surface plywood and MDF may seem quite similar, there are some really important differences that set them apart.
Understanding the strength and weaknesses of both products in terms of performance, durability, flexibility and aesthetics, is the key to choosing the right material for the substrate on a project.
The makeup and manufacturing processes behind plywood and MDF are both unique, which leads to two very different products. Plywood is created using thin layers of carefully selected soft or hard wood, which has been conditioned, cut and peeled to form veneers. The sheets are then dried, trimmed and cut to size, before the layers are bonded together using adhesives. To create a strong and durable bond, the panels are placed in a hot press, before being quality tested and graded.
Medium Density Fibreboard, or MDF as it is commonly known, is made using wood fibres rather than solid timber. The process involves breaking wood down into fi-
bre, which means the type of wood and its aesthetic and form are unimportant, allowing the manufacturer to use cheaper timber. This aspect is reflected in the purchase price of products, with MDF panels generally costing less to buy than plywood. During the manufacturing process, the fibres are pressed together with adhesive under heat, to create panels that come in a range of sizes, thickness and grades.
The visual and internal characteristics of both products are varied, and knowing these allows you to choose the right substrate for the job at hand. Plywood offers a quality finish that retains the look of real wood, making it highly suited for staining or as a substrate for veneer where a finish with exposed edges is required. When sourced from responsibly managed plantation forests, plywood is also a sustainable product.
When it comes to MDF, it has a smooth, consistent surface that is ideal for painting, laminating or as a substrate for veneer. It is the preferred product for cabinetry doors. The lack of durability means
it does split more easily and it is also less resistant to impact. Another consideration is that when it comes into contact with water, MDF acts like a sponge, readily soaking up liquid which leads to damage. MDF can be made from any timber products, which means it can be a good choice for the eco conscious, however many MDF products also use unhealthy chemicals to bind the fibres which can counteract the environmental benefits.
While both plywood and MDF can be highly suitable for use as substrates, the opposing characteristics mean they are each best suited to different purposes. For example, MDF is the choice for cabinet doors and is also used as a wall and ceiling substrate.
Plywood products on the other hand is the preferred choice for most Architects for joinery units, showing off the ply edge grain and as a sustainable, natural option for walls and ceilings.
Both MDF and Ply are a great choice with the application determining the specification.
OVER the past two decades, cross-laminated timber has slowly but surely increased in popularity as a construction material.
It’s easy to see why, as CLT can be deployed in a range of applications, including complex timber structures for residential, educational and commercial builds. Moreover, it offers exciting opportunities for low, or even negative, carbon construction.
Executed well, timberbased buildings can remain in service indefinitely – indeed, lightweight timber frame buildings have been used for nearly 100 years. What’s more, a large proportion of the UK housing stock features pitched timber roofs, many of which are centuries old.
However, given the ‘newness’ of this CLT, there has been a learning curve with understanding its strengths and weaknesses. Crucially, as with all varieties of timber, moisture can have a significant impact on durability and longevity.
One of the biggest risks facing timber buildings is fungal decay, which can occur if the moisture content within the building product exceeds 20% for an extended period of time. In a well-designed timber frame building or pitched roof, moisture content in service will be between 10% and 14% –well below the fungal decay threshold.
CLT follows the same durability principles as lightweight timber structures, but because of its thickness and the mass of timber used, it can present additional considerations when exposed to moisture. For example, timber studs, joists and rafters have a relatively large surface-area-to-volume ratio and so typically dry rapidly when conditions allow. CLT however, has a much smaller surface-areato-volume ratio, meaning drying rates can be substantially slower and ultimately affect the endurance.
Insulation and limited drying
Another prominent factor that can affect CLT drying time is insulation. CLT external walls and roofs should always be designed as ‘warm’ construction. This means all thermal insulation is placed on the outside face of the wall or roof panel. By putting the CLT panels within the thermal envelope of the building, it should facilitate a warm and dry environment – enabling timber to survive and last.
In the UK, the most common insulation material to be placed on the outside of CLT has been rigid foil-faced insulation boards (e.g., PIR/ PUR/phenolic), which are installed to walls, flat roofs and pitched roofs. While these insulation materials have excellent thermal resistance and provide the necessary Uvalues for a given thickness, the foil facings limit the ability for the CLT panels behind to dry effectively.
Historically it was assumed that any wetting to the CLT panels (either through trapped construction moisture or cladding leaks/water ingress in service) would be able to dry through the panel to the inside of the building. However, this was just a widely held assumption.
Moisture dynamics – new data and research
To improve decision making and construction, BM TRADA and Stora Enso conducted research to better understand the moisture dy-
namics in CLT. The two-part project looked at both wetting risk during construction and drying rates, serving as information which can be used to determine moisture distribution behaviour.
A fundamental part of the research was observing the drying rates of five-layer, 100mm-thick CLT panels. Various configurations were tested, including covering the wet outer face of panels with foil to replicate panels covered with rigid foil-faced insulation boards and/or vapour control layers. This test set-up was intended to imitate typical UK construction build-ups for warm walls as well as flat and pitched roofs.
In testing of the covered panels, water in the wet outside face lamination was seen to be slowly passing through the thickness of the panels to the dry uncovered side, confirming the previously held assertion that panels could dry to the inside. That said, with a starting moisture content of 35% in the wet outer lamination, it took almost 16 months for the moisture content to fall to 20%. For higher moisture contents and/or thicker panels, this means it could take years for the timber to
dry. On the flip side, uncovered panels that were able to dry directly from the wet face took approximately six weeks for a similar moisture content reduction.
Achieving long-term durability of timber structures depends on a primary consideration – breathability. To provide this, there must be a good combination of drainage and ventilation. If timber gets wet, it is not usually problematic, provided that water can drain away swiftly, and the timber is then allowed to dry. However, issues can start to occur if timber drying times are slowed down or restricted by the use of high resistance insulation products and/ or vapour control layers on the inner or outer faces of the panels. These can cause drying to decelerate to an extent that the development of fungal decay may become a risk, especially if panels are subjected to adverse conditions during construction or in service.
Looking over to European construction methods, CLT building systems are often paired with mineral wool or wood-fibre insulation products. Typically, these are more beneficial to timber construction as such breath-
able insulation materials allow for faster drying of the CLT panels if they are exposed to wetting.
In summary, the use of breathable insulation products and systems, paired with good overall design and an effective moisture management plan will have a considerable positive impact on the long-term durability and robustness of CLT structures.
CLT will certainly have a role to play in the move to create greener, low carbon buildings. However, to ensure that CLT buildings are successful, it is crucial to know how to protect the material against moisture ingress. When moisture content does pose an issue, it is important to take action straight away. These considerations should be made at the start of any timber construction project, and it is notably important to plan in time for timber to sufficiently dry to prevent the onset of fungal and structural decay.
For more about BM TRADA and its range of timber services, please visit www. bmtrada.com/timber-services
Phil O’Leary is Technical Manager at BM TRADA.
KOSKISEN’S rapidly advancing sawmill investment will bring changes to the day-to-day work of the sawmill’s employees and the sawmill’s internal logistics.
But changes are also in store for the sales department, as the future sawing line will offer customers options that were previously not available.
The new sawing line is being built around HewSaw’s large-log SL250 model, which includes three machines: a chipper canter, cantsaw and ripsaw. The sawing line is 85.6 metres long in total, and so far no other setup quite like it exists anywhere.
The new line will feature all functions to boost productivity, such as Prologic’s sorting and optimization scanners, log spacing control, a log rotator, curve sawing, optimized edging, high-speed feed, scan and set technology and fast setting changes. To ensure durability, the frames of the chipper canter were made of special steel, whereas previously the steel used in aircraft landing gear was used.
The new sawmill’s production target of 400,000 m3 was calculated based on two shifts a day for a five-day period.
Tommi Sneck, Director of Koskisen’s Sawn Timber Industry, says there is room for growth
in volumes before the line’s full capacity is reached.
“The sawing line comes with the DX option, which makes it possible to ramp up the line’s speed and use thinner kerf saws. Thinner kerf saws result in either a higher yield or a longer interval between blade changes. In Koskisen’s case, this would mean a production increase of as much as 200,000 cubic metres. More efficiency can also be achieved by adding circular saw blades to both the cantsaw and the ripsaw,” Sneck said.
The line’s maximum speed is 180 metres per minute, but with DX sawing, the speed could even reach 230 metres
per minute. Faster speeds are not the goal at least for the time being, since Koskisen’s line is meant for sawing larger logs.
“At least until the end of 2023, only large-diameter logs will be sawn,” says Sneck.
The line’s scan and set technology combined with optimized production planning will open up entirely new possibilities from a sales standpoint. Log optimization will mean more products can be directed to processing and, for example, the constant headache sawmills face with regard to side boards will be eased.
“Previously, side boards could not be fully optimized
and 3-metre logs could not be sawn. These limitations have now been eliminated, and particularly in our main market of Japan, where 3-metrelong products are in demand, customers will have more options,” says Sneck.
For customers, the new sawmill will mean not only new products, but also better quality.
“The products’ dimensional accuracy and technical quality will improve. For example, straightness will improve, as we will switch to using 11 drying sticks in the drying loads. As production volumes grow and errors decrease, deliveries will become more reliable,” he said.
Two head saw configuration
Digital controllers allow accurate saw wheel positioning
Automatic blade tension is controlled by hydraulic cylinders
Variable feed speed by hydraulic motor drive
Large horsepower Seimens or equivalent saw wheel motors drive the blades allowing for heavy-duty cutting
The conveyor belt is driven by a high performance hydraulic motor
Adjustable feed speed allows flexibility to saw hard and soft wood
Full wheel and blade lubrication
Low maintenance Safety cage.
Large
The conveyor belt is driven by a high performance gearbox and electric motor setup. Adjustable feed speed allows flexibility to saw hard or soft wood.
THERE is no doubt the past few years during the pandemic, FTMA has been busy supporting members. Not one member had to wonder what the COVID rules meant for their business, as FTMA ensured timely and easily read materials were in members inboxes shortly after any announcements.
With the impact of COVID on the workplace reducing, FTMA has wanted to focus on what’s next for our industry. We changed our by-line to reflect our aim of supporting fabricators by investing in new projects which will help grow our market share and ensure our sector is best placed to meet the needs of zero nett carbon housing for our future.
FTMA Australia has worked extremely hard over the past decade to lift the standards within our industry by making our members, and fabricators in general, better businesses.
By making fabricators better businesses we are making them better customers for suppliers, and also better suppliers to the construction industry, which in turn will help grow our markets.
“We
chain.
KERSTEN GENTLE Executive Officer FTMA AustraliaThe FTMA Board came together on with a facilitator to review our strategic plan. It was reassuring to look back at our past plan and see that, with the exception of training, we had delivered everything we had planned to do.
Throughout the planning session, the board worked with Andrew Gosbell, from the Associations Forum and created our new vision, mission, values and pillars.
Our Vision
An industry where timber manufacturers thrive and contribute to Australia’s sustainable built environment.
Our Mission
FTMA is recognised as the trusted representative body and unified voice for all timber frame and truss manufacturers of Australia, whilst strengthening the connection with the broader supply
FTMA supports timber manufacturers while investing in our industry to grow and strengthen the professionalism of the timber fabrication market and viability of our members.
FTMA’s approach to achieving its mission is to:
Support: Providing support to our members to help them become better businesses.
Invest: Investing to create more opportunities for our members.
Grow: Driving industry growth and strengthening the professionalism of our sector.
The final Strategic Plan is being formatted and will be distributed in the next few weeks.
Following the Strategic Planning session, our valued partners joined us for dinner and some great networking before coming together on Tuesday to address the key issues in the industry and go through the programs FTMA is wanting to introduce over the next few years.
One thing FTMA has always prided ourselves on is our
ability to listen and understand the needs of fabricators, however, they are so busy manufacturing products and working in their businesses, that they do not have the time to invest in growing the sector or markets.
FTMA plans to tackle the issues which Fabricators have expressed concerns with, such as:
• Training including the inability to attract new people into our sector.
• Keeping on top of their legal obligations as employers and the need for further HR support.
• Dealing with increased costs relating to timber waste and ways of disposing of waste.
• Exploring new markets and/or products to grow the sector
• Lack of data for our sector
• Promotion of the environmental benefits of timber through Carbon Warrior and renewable timber framing.
• Steels growth within the market and how to combat this through better understanding of the environmental benefits of timber
Other issues were raised such as fibre utilisation, operational efficiency, WHS, increased marketing and protecting the value of our products.
We thank our partners (formerly sponsors) for attending the day and contributing to our plan which we look forward to implementing and sharing with our members in the new year.
FTMA has just completed the 2022 FTMA National Fabricator Census which has provided a great insight into our sector. The final copy of the Census will be provided to all
FTMA Members and fabricator non-members.
The Executive Summary stated:
The report provides a detailed analysis of the 2022 FTMA census. Overall, it had a fantastic completion rate with over 160 plants(60% of entire industry) across each state in Australia taking part with the bulk of the plants surveyed operating in the Eastern states. Due to data privacy, when reporting at a state level, this report has combined ACT and NSW as well as QLD and NT.
At a high level, workforce size has not changed dramatically since the last census, with each plant having an average of 28 employees up from 27. In addition to this, approximately three quarters of the workforce is currently permanent, with around two thirds of all employees working in the factory department.
Aboriginal and Torres Strait Islanders make up 2.9% of the total workforce, which is up from 2.7% in the previous census. The percentage of employees with disabilities and employees aged over 45, however, are down from 1.7% to 1.6% and 33% to 29% respectively.
Around 70% off the work currently being done is new detached dwellings however approximately 63% of plants operate in at least three mar-
ket types including townhouses and renovations. Cassette floors are only offered in 9% of plants but around 20% of additional plants are looking to move into this product in the future. Similarly, off-site prefabrication looks to be another large growth area. Around three quarters of plants do not appear to have interest in introducing lightweight steel framing to their offering.
Around half of all plants surveyed do not have succession plans for their business. Interestingly, the percentage of businesses that are planning to sell and the percentage that are planning to buy are very similar to each other, both sitting around 15%. There is a large amount of fear around builders defaulting with over 75% of plants expressing their concern. Of these concerned plants, only one third of them have already been impacted by defaulting.
FTMA believes this aggregated data is important for planning our future and it also helps paint a picture of our industry when lobbying different levels of Government.
If you require further information on the 2022 FTMA National Fabricator Census, please contact me at kersten@ ftma.com.au, otherwise we would like to sincerely thank the 160 fabricators for providing this aggregated data.
FTMA Australia is an independent, national organisation representing fabricators of and suppliers to the timber prefabricated truss and wall frame industry in all Australian states & territories providing a unified voice, to protect and advance our multi-billion dollar industry.
FTMA Australia thanks our dedicated supporters and encourages you to support those who support your industry
MGA TMA is pleased to announce the appointment of David Inall as our new Chief Executive Officer. David commenced with us on 10 October 2022.
David has 30 years’ senior experience providing strategic and operational direction within the not-for-profit sector. With extensive global experience in political advocacy and policy development for primary industry, David comes into the role after five years as CEO of the Australian Dairy Farmers.
David is taking over the reins from Jos de Bruin. Jos has lead the MGA TMA team as CEO for 16 years and has made the decision to retire.
David is a dedicated supporter and advocate for family and private businesses and will naturally be very keen and enthusiastic to meet as many MGA TMA members and industry stakeholders as possible, and as such, David and Jos will together be attending meetings, forums and industry engagements around Australia during this transition period.
MGA TMA is well regarded in the industry for the advice and support provided by our in-house employment lawyers. Our team have been incredibly busy – especially over the past few years with so many different COVID-19 restrictions across the states, changes to wages, adjustments to the Fair Work Act and other general enquiries.
MARIE-CLAIRE MCKIERNAN NATIONAL MEMBERSHIP MANAGERWe are therefore excited to have Martin Stirling join our Employment Law team as Head of Legal. Martin commenced his employment with MGA TMA on 17 October 2022.
Martin has a diverse background and has experience across both private firm and in-house legal environments.
He is looking forward to getting to know our members and provide strategic employment law support.
MGA TMA wishes all our members and industry friends a very happy and safe Christmas and a prosperous New Year.
We will continue to be available to assist members over the Christmas & New Year period (with the exception of Christmas, Boxing and New Year’s days and their relevant public holidays) with your enquires.
We look forward to exciting times with our members in 2023.
ON 26 October 2022, the Minister for Industrial Relations introduced a Bill into Parliament to amend the Fair Work Act 2009 (‘the Act’) and related legislation which, when passed, will have many significant changes for employers in Australia.
The Fair Work Legislation Amendment (Secure Jobs, Better Pay) Bill 2022 (‘the Bill’) is the first of at least two tranches of amendments to the Fair Work Act (the Act), dealing with some previously published parts of the Government’s election platform earlier this year, but also many changes where details were not publicised as part of the platform. Minister Tony
Burke has stated that the second tranche will be next year.
The Bill and its supporting Explanatory Memorandum (EM) are very detailed, each over 200 pages in length and
require careful examination. Despite the complexity of the amendments and their implications for employers, it appears that the Government intended to enact the changes before Parliament rose on 1 December. Although the Bill has been referred to a Senate Committee, submissions to the Senate Inquiry closed on Friday, 11 November.
The Bill, if passed, will involve changes for the following:
• Enterprise bargaining;
• the Objects of the Fair Work Act;
• Equal remuneration;
• Prohibiting ‘pay secrecy;’
• Sexual harassment;
• Anti-discrimination;
• Fixed term contracts of employment;
• Requests for flexible working arrangements;
• Small claims; and
• Pay advertisements.
In relation to enterprise bargaining, it is already apparent that the proposed changes would be very significant, perhaps the most significant changes since bargaining at the enterprise level was introduced in 1993. The new bargaining streams in the Bill appear to be intended to operate in favour of industry, quasi-industry, or pattern bargaining, at the expense of enterprise bargaining. The amendments would permit, under certain circumstances, compulsory bargaining initi-
ated by unions, compulsory arbitration, and scope for employers to be ‘roped-in’ by unions, with or without their consent, into other employer agreements.
TTIA will be going through any changes in depth in its first post-COVID Member seminars during the first half of 2023. If you need further details phone (02) 9264 0011 or email ttia@ttia.asn.au
On behalf of myself and the staff at the TTIA, best wishes for a safe and happy holiday from us all to Members and readers of this industry publication. We look forward to being of service to you in 2023.
THE Annual General Meeting of the Timber Veneer Association of Australia (TVAA) was held at the Rendezvous Hotel in Melbourne on Wednesday, 2 November 2022.
The AGM was the occasion for the election of members of the Association’s Committee, to serve during 2023.
The AGM was also an opportunity to re-state the objectives of the Association which are:
1. To be recognised as the leading authority on decorative wood veneer and deco-
PETER LLEWELLYN Technical representative, Timber Veneer Association of Australiarative wood veneered panel products in Australia and New Zealand; and
2. To be actively involved in the promotion and expansion of the market of decorative wood veneered panel products manufactured in Australia and New Zealand; developing industry standards; providing education for the industry and the wider public; and a forum for networking for its members.
During 2022 the Association continued to raise its profile in pursuit of these objectives by the use of social media, press releases in industry journals, and its website.
In the coming year TVAA plans to shift focus a little by engaging more with educational institutions. Members will be encouraged to conduct tours of their facilities, and talk to student groups on a more regular and structured basis.
TVAA’s marketing campaign and website will be steered towards educating students and specifiers, as well as manufacturers such as cabinet makers and shop fitters, in how to accurately select, order and manufacture with timber veneer.
The intent is to give our customer base confidence in working with timber veneer whilst also gaining an appreciation for the processes involved in producing timber veneer from forest to factory floor, and understanding its environmental benefits
Coming out of a difficult time during Covid, which imposed some supply chain issues, TVAA is in a secure financial position and looks forward to a prosperous 2023 for its members, and for the veneer industry in general.