17 minute read
A Business Case for Environmental Solutions
Next Article
importance of managing environmental performance throughout the entire drilling and completions process. Reducing the presence and/or environmental impact of drill cuttings may be essential for obtaining market access, complying with regulations, and avoiding possible remediation costs. Complying with environmental laws and regulations is business critical as non-compliance may result in either the inability to drill or substantial fines. Regulatory controls minimize the impact of permitted discharge of cuttings based primarily on toxicity. Laws and regulations vary by location. On US land, for example, waste requirements typically originate at the state level for oil and gas exploration and production while the Environmental Protection Agency is the primary regulatory agency for environmental concerns (API 2011). In addition, many of the local watersheds and ground water protection agencies are either at a multi-state level or a river basin level (EPA 2012). Offshore, national government agencies regulate the permitted discharge of cuttings to prevent unreasonable degradation of the marine environment. Depending on the drilling location, the target level of non-aqueous fluids on cuttings typically ranges from 0% to 8%. In recent years, regulations governing the treatment and disposal of drill cuttings have become more stringent with multiple areas moving towards complete zero discharge (Figure 1).
Maintaining Social License to Drill
The rising power of local community stakeholders— particularly in US land, where individual landowners maintain subsoil ownership rights—may have greater impact on our industry today than ever before. Now, the ability to conduct oil and gas drilling is subject to opinions of outside parties in addition to environmental laws and regulation. In today’s technology-driven world, everyone has access to information. Traditional news outlets are no longer the sole opinion leaders. Everyone has the ability to create and disseminate information, fact-based or not. In some cases, this can contribute to more entrenched environmental opposition, especially in ecologically and socially sensitive areas like those described above. How environmental risks are perceived and regulated has impacted access to oil and gas reserves worldwide. Today, public opinion helps determine the ability to obtain and maintain drilling permits. A company that is not conscientious of its environmental impact and/or working to mitigate may be subject to losing its social license to drill (Kitasei 2011).
Technologies Delivering Operational and Cost Benefits Along with Improved Environmental Performance
A central challenge surrounding the implementation of select environmental technologies is ensuring efforts to reduce the environmental impact intrinsic in oil and gas development do not negatively impact operational and cost performance. For waste management, technologies that reduce the amount of drill cuttings and/or treatment required before disposal achieve this balance. The technologies discussed below demonstrate how business and environmental goals can be achieved in parallel, proving that technology decisions made on the basis of performance and bottom-line dollars can also deliver legitimate environmental gains.
Drilling Tools for Wellbore Stabilization Reduce Amount of Cuttings Generated While Drilling
When a drill bit deviates from the desired well path, drillers must reduce the pressure applied to the drill bit and make frequent adjustments to the bottom hole assembly (BHA) to steer the bit back to the desired course. These corrective actions consume valuable drilling time and result in crooked oversized wellbores for drilling efficiency losses estimated as high as 200%. Through the use of rotary steerable systems and similar low-cost alternatives, drillers can maintain verticality in the wellbore and recover the lost time and cost. They can also reduce the amount of environmental waste by an estimated 30% through decreased cuttings and fuel consumption. Therefore, along with well-accepted efficiency gains, drilling straighter wells delivers positive environmental impact by reducing drilling waste from the source.
Centrifuges and Dryers Reduce Presence of Non-Aqueous Fluids on Cuttings
Drilling fluid type and local discharge requirements (in terms of the permitted level of non-aqueous fluids on cuttings) help determine the method for cuttings disposal offshore. For cuttings with non-aqueous fluids, the main options include: Ó Cuttings re-injection into existing or new wells Ó Shipping cuttings onshore for treatment and disposal Ó Offshore discharge following treatment (Tullow Oil 2009). While cuttings re-injection and shipment are the preferred methods for zero discharge environments, in environments where offshore discharge is allowed centrifuges and dryers offer operational and cost efficiencies along with environmental performance. Centrifuges separate fine drilled solids from the drilling fluid. Doing so prevents drilled solids volume from exceeding a threshold level in the drilling fluid that could inhibit the drilling process and/ or damage additional rig equipment. When drilled solids increase above the acceptable threshold level, the only way to reduce the solids to fluid ratio to acceptable levels involves dumping and diluting the fluid.
Generally, the desired ratio between drilling fluids and drilled solids is 95:5. Therefore, for every barrel of drilled solids a centrifuge removes, it eliminates the need for ~19 supplemental barrels of drilling fluid. Using a centrifuge eliminates the costs associated with adding extra base fluid (estimated at USD 2500 for 19 barrels) as well as treating the increased volume of produced waste. The use of dryers further eliminates cost by returning base fluid back into the mud system for re-use. Centrifuges can be considered an environmental tool, as demonstrated by the above example. Proper waste management begins with shale shakers. Improved and automated shakers increase the efficiency with which solids are removed from the drilling fluid, leading to better reuse and fewer requirements for additions for time and cost savings (El Dorry 2012). However, one operator explained that, on average, centrifugal dryers offered a 65% reduction in the amount of barrels of cuttings discharged over shale shakers alone (Figure 2).
Enhanced Water-Based Mud Delivers More than Environmental Benefits
Drilling with water-based mud eliminates the more environmentally damaging side effects of oil-based mud: no hydrocarbons and no chlorides that require treatment prior to proper disposal. Oil-based mud remains popular for land applications because of its consistent performance. New drilling fluid technologies offering improved environmental performance as a primary benefit must also deliver bottomline operational and cost gains. An oil and gas equipment manufacturer developed an enhanced water-based mud that does just that: matching oil-based mud’s performance in days versus measured depth and cost. Proven on land and inland waters, the enhanced water-based mud has proven to be as fast as oil-based mud. For a sample of wells with a total vertical depth of 12,500 feet to 14,000 feet, drilling with oil-based mud took an average of 15.9 days to complete while enhanced water-based mud took 15.8 days. It has also matched performance in ways other than days versus measured depth. One operator in the Eagle Ford Shale in south Texas, US has used the enhanced waterbased mud on 43 wells. Each was drilled with no stuck pipe and casing reached bottom. Enhanced water-based mud also offers an improved lubricity coefficient over traditional water-based mud. Whereas water-based mud has a lubricity coefficient of 0.28, the enhanced water-based mud has 0.14 which results in improved penetration rates, consistent reduction of lost circulation and delivery of stable wellbore. Enhanced water-based mud matches oil-based mud performance without the increased disposal cost typically associated with non-aqueous fluids. Upfront costs for enhanced water based mud is higher, with an operator in the Eagle Ford reporting a cost of USD 150,000 compared to an USD 85,000 cost for oil-based mud. However, associated costs for oil-based mud add up quickly, notably the cost for the required base oil (Figure 3). Operators may spend nearly as much on diesel as they are on oil-based mud, ranging from USD 50,000 to USD 70,000 according to one operator. Additional savings associated with disposal costs include additional equipment rental, rig cleaning, oil-based mud and base oil trucking, and cement slurry to surface for oil-based mud recovery. In the Eagle Ford, an operator saved USD 300,000 per well using enhanced water-based mud. The operator reported a total savings of USD 12.9 million over 43 wells. In areas where leasing requirements forbid landforming cuttings and/or require cuttings to be disposed offsite the savings are less substantial. Nonetheless, the cost of enhanced waterbased mud is comparable to the combined cost of oil-based mud and necessary diesel.
Market Acceptance of Environmental Technology Related to Operation’s Economics
The market acceptance of technologies that improve environmental performance is directly tied to the operational and/or cost efficiency gains they also deliver. Consideration of environmental impact, while important for market access in terms of compliance with laws and regulatory and maintaining social license to drill, will only become commonplace should the technologies offered meet the operational and/or cost demands of standard drilling operations. One of the challenges oilfield service and supply companies face is addressing the environmental gains offered by some of their more traditional products. The root cause of this challenge is the lack of common metrics for evaluating environmental performance. Nonetheless, across the industry operators, drilling contractors, and service and supply companies have identified the main focus areas for improvement: energy efficiency and emissions, water use and recycling, leak prevention and spill containment, and drilling waste management. Considering these areas, oilfield service and supply companies can begin preliminary evaluations of their existing product portfolio and market added benefits. Taking the next step of creating and incorporating a standard method for assessing environmental performance of technologies requires industry-wide support. The challenge of demonstrating the positive economic impact of the implementation of select environmental technologies cannot be resolved by one company alone; it will require the collective commitment and collaboration of all industry players.
Acknowledgements
The authors would like to thank David Reid, Tom Yost, Federico Mezzatesta, Khaled El Dorry, Garry McCraw, Mike Usher, Scott Jackson, Carl Tolbert, and Joe Blanc of National Oilwell Varco for their contribution of expertise and support.
REFERENCES
API. 2011. Environmental Regulation of the Exploration and Production
Industry. Associated Press. 2012. Vt. Becomes first state to ban hydraulic fracturing. Bolstad, Erika. 2010. McClatchy Newspapers. Arctic drilling still a no-go, despite judge’s moratorium ruling. El Dorry, Khaled and Bill Dufilho. 2012. Automation Improves Shaker
Performance. SPE 151180-MS. Environmental Protection Agency. 2012. Ocean Discharge Criteria
Evaluation. ExxonMobil.2012. Environmental Drilling Initiatives. Harvard Business Review. 2006. Strategy and Society: The Link Between
Competitive Advantage and Corporate Social Responsibility. Jacobs, Justin. 2012. Petroleum Economist. Bulgaria joins France in fracking ban. Kitasei, Saya. 2011. World Watch Institute: Vision for a Sustainable World.
License to Drill? Revised Study from New York Department of Environmental Conservation Outlines Conditions for
Permitting Shale Drilling- but Not in Unfiltered City Watersheds. Neff, Jerry. 2010. Neff & Associates. Fate and Effects of Water Based
Drilling Muds and Cuttings in Cold Water Environments. Oil & Gas UK. Knowledge Centre: Drill Cuttings. Railroad Commission of Texas. Surface Waste Management Manual. Reddoch, Jeff. 2008. World Oil. Why cuttings reinjection doesn’t work everywhere—Or does it? Tullow Oil. 2009. Summary of Development Drilling Impacts and
Assessment of Drill Cuttings Disposal Options.
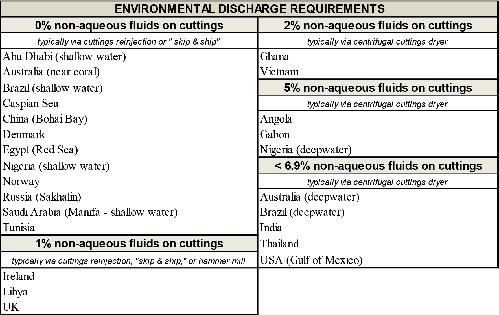
Fig. 1—Environmental discharge requirements
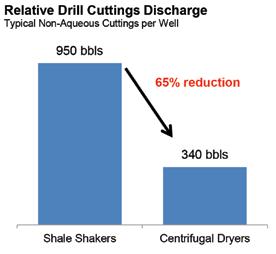
Fig. 2—Relative drill cuttings discharge by equipment type
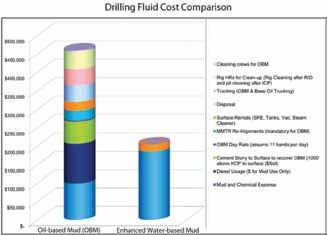
Fig. 3—Cost savings offered by enhanced water-based mud
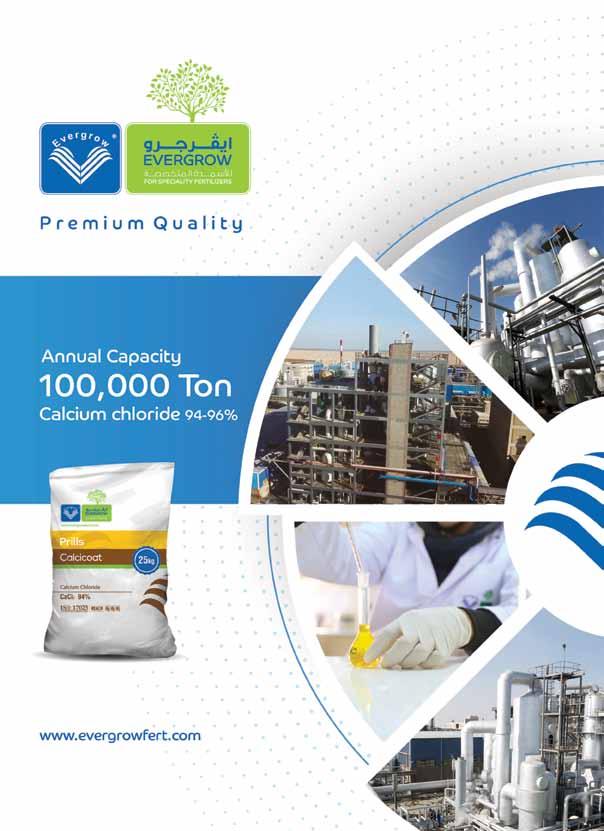
H350 a multipurpose masterpiece for all business needs in Egyptian market
WHATEVER YOU WANT. EQUIPPED WITH WHATEVER YOU NEED
Egyptian international motors (EIM) the sole agent for Hyundai commercial vehicles in Egypt. Introduces newest member of Korean giant family Hyundai H 350 in Egyptian market, a multipurpose vehicle that suits all business and commercial needs.
H350
The H350 is a reliable and efficient partner that gives your business a real advantage. It’s impressively well equipped with features that are designed to save you time and money. Active ECO drive mode, for example, improves fuel efficiency and is now standard across the entire range. Clever interior layout and packaging creates a ‘Mobile office’, designed to ease the driver’s daily task. For maximum practicality, there are up to 25 storage compartments around the cab. H350 is classified into two applications: Bus and van. Moreover, it can be customized such as overall lengths, overall heights, and door locations. H350’s infinite transformation still continues.
H350 Bus application
EIM & Hyundai offer a business class comfort on the road, with various seating layout starting from 14+1 seats up to 29+1 seats in addition to luxurious limousine application. The refined interior design reflects the latest design trends achieving elegant and classy interior space for passengers. LED overhead lighting is precise without being harsh, a sliding door or the front passenger door with inbuilt step makes entry easy and the hand rails are in the right place. There is even a sophisticated 8 speaker sound system that brings clear sound to every seat. Flush fitted side windows and specially developed air conditioning help ensure the perfect interior climate.
H350 Van application
Whatever you need to move, wherever you need to take it, H350 delivers. The design philosophy for H350 van application makes it durable and operational efficient as the loading or unloading of H350 is easy work thanks to the short distance from the ground to the cargo deck. Load space between the rear wheel arches has not compromised thus maximizing cargo hauling capacity and convenience. H 350 can be in different applications as, -Ambulance -Cargo van -Maintenance vehicle -Refrigerated -Mobile office -Double cab -Prisoner transportation
H350 Ambulance application
In cooperation with one of the biggest companies in petroleum sector, EIM succeeded in 2019 to supply Gulf of Suez petroleum Co. (GUPCO) with two H350 ambulance application vehicles equipped with all needed equipment that serves the hard and dangerous business locations the company operates in.
EIM Group
EIM group was established in 1979 as one of ALKAN holding companies. Its remarkable growth over years has positioned it as a market leader in various business fields. EIM became sole agent for Hyundai commercial vehicles since 2010. EIM exclusively has been distributing and serving more than 28 world reowned brands in more than 9 business sectors in the region operated through 2000 EIM business experts .Group activities include; multinational enterprise representation, after sales activities and free zone storage and clearance.
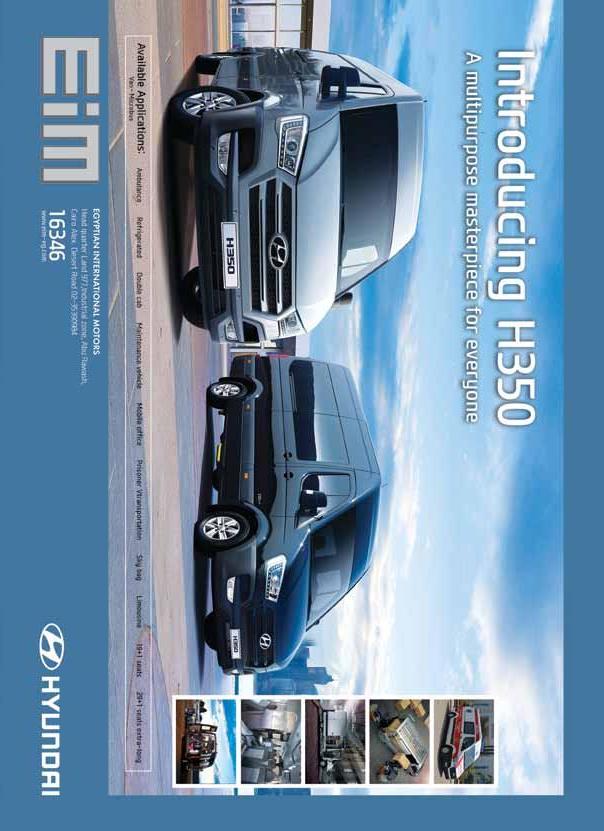
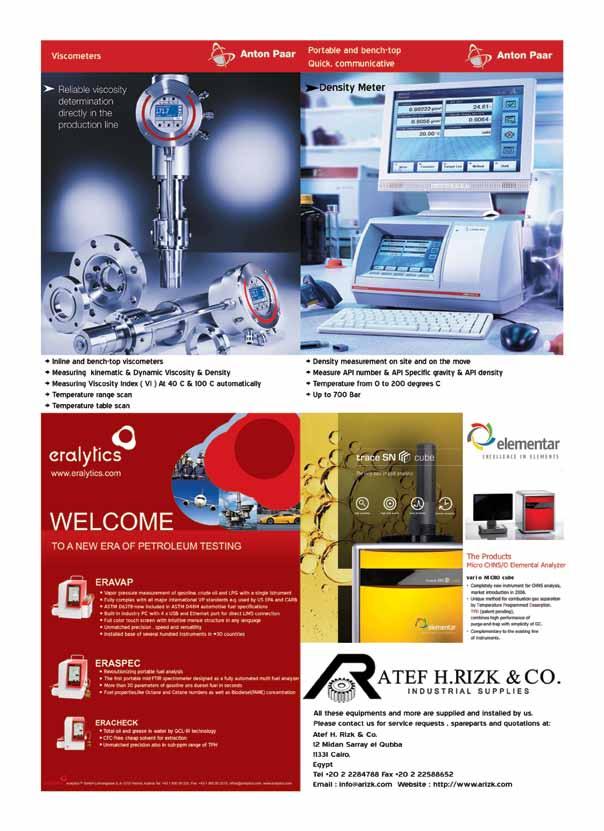
Technology Applications
Well control Safety and Regulations on Deep Water and Onshore wells
By: Prof. Dr. Ahmed. Nooh - Eng. Mohamed Safan
Well control has always been a very important issue in the oil and gas industry because it involves enormous amount of money, people’s safety, and environmental issues. Well- control fundamentals have been understood and taught for almost half a century, but still well control problems and blowouts occur in the industry. Substantially, all blowouts are related to human failure and error relative to well operations. Early acknowledgment of a kick and fast close in are the keys to successful well control. Well control consider as a very sensitive and a systematic process. It is a team work and it requires a complete dedication to the job from each member of the team. A large portion of the blowouts are caused by either human error or equipment failure. Human mistakes are generally a result of the lack of regard, ignorance and miscommunication between the workers. Equipment failure can likewise be a piece of human ignorance. On the off chance that the objective is a protected and effective drilling procedure then each and every detail ought to be considered and ought to be sufficiently given consideration from the administration. An entire coordination between the workers is obligatory and a far reaching and dependable communication system is a fundamental piece of drilling process.
We have many important points which can be very improved to make sure a safe drilling process. Human mistakes and equipment failures are the primary driver of the blowouts in an oil and gas well drilling process, as exhibited in the BP, 2010 and a well in Western Desert, Egypt. This contemplate infers that drilling mud is the essential obstruction to prevent hydrocarbons from going into the wellbore thus a cautious checking of the well is critical. It is the first obligation of the apparatus group to ensure that the thickness of the drilling fluid is more than the thickness of the reservoir fluid. Ó This study about accentuate that the rig crew should ensure that there are sufficient barriers in the wellbore to control oil from going into the wellbore. For instance separated from the drilling mud there ought to be blowout avoidance equipment introduced at the wellhead to seal the well if kick happens.
Ó Blowout prevention (BOP) equipment at the wellhead go about as an optional obstruction amid kick circumstances via fixing admirably from the wellhead. A watchful checking and testing of the Bow out preventer equipment previously and amid drilling process is vital. As showed in the BP contextual analysis that Macondo BOP system was not tried and checked for extensive stretch of time.
Ó If possible companies ought to introduce two blind shear rams (BSR) in BOP system on the off chance that on the off chance that one neglects to seal the well amid crisis circulation there is another accessible as a backup. The accident of the April 20, 2010 involved a well integrity failure, followed by a loss of hydrostatic control of the well. This was followed by a failure to control the flow from the well with the BOP equipment. The following are few main key findings relating to the casual chain of events, a better performance in the respective areas could have saved this catastrophic incident from happening. 1. The negative pressure test results were accepted although the well integrity was not established. 2. The annulus cement failed to isolate the hydrocarbon zone and allowed hydrocarbons to flow from the formation into the wellbore.
3. Hydrocarbons entered the wellbore undetected; the rig crew ignored the abrupt pressure changing readings from the Macondo Well monitoring system. 4. The shoe track cement could not provide a strong barrier to the hydrocarbons and allowed them to enter into the production casing. 5. Float valves were not converted, which allowed hydrocarbons to rise up in the production casing. 6. BOP system completely failed to seal the wellbore.
7. Delay in the recognition of the hydrocarbons influx. The crew could not realize the influx until it entered into the riser.
8. Well control actions after explosions failed to regain the control on the well.
9. Diversion of the flow towards MGS resulted in gas venting to the surface of the rig. 10. Lack of real leadership and unprofessionalism was another big contributor to this incident.
Onshore well was taken as an example for Egyptian blow out well was at The Western Desert.
Ó During lost circulation, drilling process ought to be ceased and lost circulation sites ought to be stopped before
continuing the drilling. The choices how to stop the lost circulations destinations ought not be deferred as occurred in the Egyptian well blowout, it enabled hydrocarbons to movement a significant separation up to the wellbore. Ó Driller,s and Engineering method are generally utilized as a part of the business to circle out the influx of hydrocarbons from the wellbore after a fruitful well closed
«shut in» in case of kick circumstances.
Ó The comparison between these two wells shows that:
Engineering method is more efficient than Driller method as its kill the well in less time but its need more drilling training for the rig: crew. Ó By Studying the Macondo well case study , it was found that:
Ó Cementing of a well ought to be done carefully and companies ought to never move to the following stage unless the well respectability is set up. Once establishing is done companies should run well integrity tests to ensure a successful cement activity. As BP sent Schlumberger group home without performing cement integrity tests which turned out to be a wrong choice. Ó Cement slurry design ought to accord to the wellbore conditions and its strength and uprightness ought to be tried before sending it into the wellbore. As BP did not have any desire to sit tight for the bond slurry integrity results about rather they raced to cement the Macondo
Well. Therefore they wound up with an extremely poor cement job. Ó After completion of a cement job the positive and negative pressure tests to set up the well integrity ought to be done and perused deliberately. Confusion of their outcomes can prompt a blowout as occurred at the BP Macondo well. Ó There ought to never be an absence of real leadership at the rig because drilling a well is a consider team work and a team cannot succeed without a great leader.
Comparing between the two cases (Macondo of Gulf of Mixico and the well of Egypt) it was found that:
1.The pressure of Macondo was higher as its deep water horizon and the depth of the waster was extra weight and