28 minute read
News
Next Article
Thai energy ministry sets March target to resolve Chevron dispute
Thailand’s energy ministry said it had set a March target to resolve a $2 billion dispute with U.S. oil and gas major Chevron Corp and would make the “utmost effort” to reach a deal after the company halted arbitration. The dispute resulted from a retroactive Thai law in 2016 requiring gas field operators to pay the costs of decommissioning assets they have installed even if they no longer operate them. “This negotiation will require our utmost effort because it concerns national interests,” permanent-secretary Kulit Sombatsiri said. “We have up to 180 days to work it out,” Kulit said, adding that the time frame was stipulated by law.
Exxon to make $500 mln initial investment in Mozambique LNG project
Exxon Mobil plans to invest more than $500 million in the initial construction phase of its liquefied natural gas (LNG) project in Mozambique. The U.S. oil company’s $30 billion Rovuma LNG project, jointly operated with Italy’s Eni, has a capacity of more than 15 million tonnes a year (mtpa) and is set pump much-needed cash into the southern African nation’s ailing economy. “The Area 4 partners will advance midstream and upstream area project activities of more than $500 million as initial investments,” Exxon head of power and gas marketing Peter Clarke said. Construction of onshore facilities has been awarded to a consortium led by Japan’s JGC, U.K firm TechnipFMC and U.S. company Fluor Corp. “These EPC (engineering, procurement and construction) contracts cover the construction of two natural gas production trains with a total capacity of 15.2 million tons per annum, as well as associated onshore facilities,” Clarke said. Final investment decisions, a term used by the oil industry to mean the commercial and regulatory aspects of a project are finalized, would be made in 2020, Clarke said.
Petrobras removes 133 tonnes of oil from Brazil,s beaches, CEO says
State-run oil company Petroleo Brasileiro has collected 133 tonnes of oil along Brazil’s northeastern shoreline, Chief Executive Roberto Castello Branco said, in an unexplained mystery he said was worrying. Speaking with lawmakers, he said the company had not identified any of its own oil in its analyses. He also said that, in order to maintain stable production, Petrobras, as the company is known, needed new reserves of 1 billion barrels per year, at a cost of $3 billion.
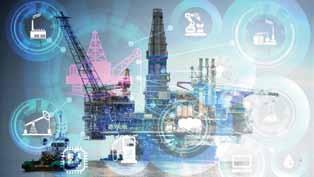
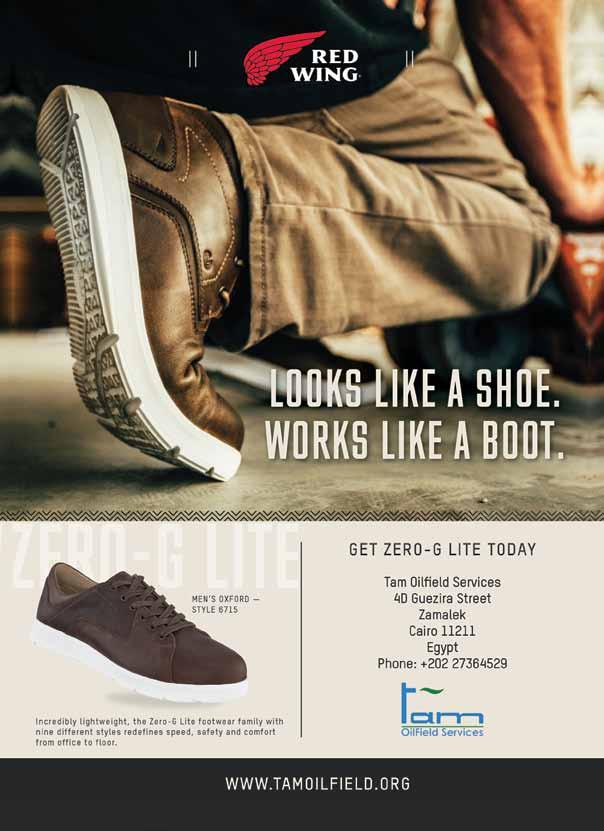
Corporate News
Rockwell Automation and Schlumberger Announce Closing of Sensia Joint Venture
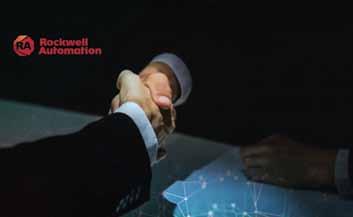
Sensia, the oil and gas industry’s first digitally enabled, integrated automation solutions provider, will drive efficiency, optimize performance and reduce risk Rockwell Automation (NYSE: ROK) and Schlumberger (NYSE: SLB) announced the closing of their previouslyannounced joint venture, Sensia, the oil and gas industry’s first digitally enabled, integrated automation solutions provider. The joint venture leverages Schlumberger’s deep oil and gas domain knowledge and Rockwell Automation’s rich automation and information expertise to address this fastgrowing market. “Sensia will make industrial-scale digitalization and seamless automation available to every oil and gas company so their assets can operate more productively and profitably,” said Allan Rentcome, Chief Executive Officer of Sensia. “It will make oil and gas production, transportation and processing simpler, safer, and more secure.”
Eni Announces New Production from the Western Desert
Successful MSD-19 Well at West Gharib Concession in Egypt
Eni announces that production from South West Meleiha Development Lease, located in the Egyptian Western Desert, some 130 Km North of the oasis of Siwa, has started. The current production, delivered through two oil producer wells, is around 5.000 barrel of oil per day (BOPD) and is expected to reach 7.000 BOPD within September 2019. The oil is transported and treated at the Meleiha Plant facilities operated by AGIBA, a company equally held by IEOC and the Egyptian General Petroleum Corporation (EGPC). South West Meleiha oil discoveries have been made in 2018, while other exploration wells are now planned to be drilled on the nearby prospects within the exploration area. Eni, through its subsidiary IEOC, holds a 50% interest in South West Meleiha while EGPC holds the remaining 50%. AGIBA is the operator.
SDX Energy plc (SDX) is pleased to announce that the MSD-19 development well in the West Gharib Concession in Egypt (SDX 50% Working Interest & Joint Operator) has encountered a commercial oil accumulation. The well was drilled to a total depth of 4,665 feet and encountered approximately 135 feet of net heavy oil pay across the Asl Formation, with an average porosity of 24%. The well was completed as a producer, connected to the central processing facilities at Meseda and brought online at an average stabilised rate over five days of approximately 315 bbl/d (gross).
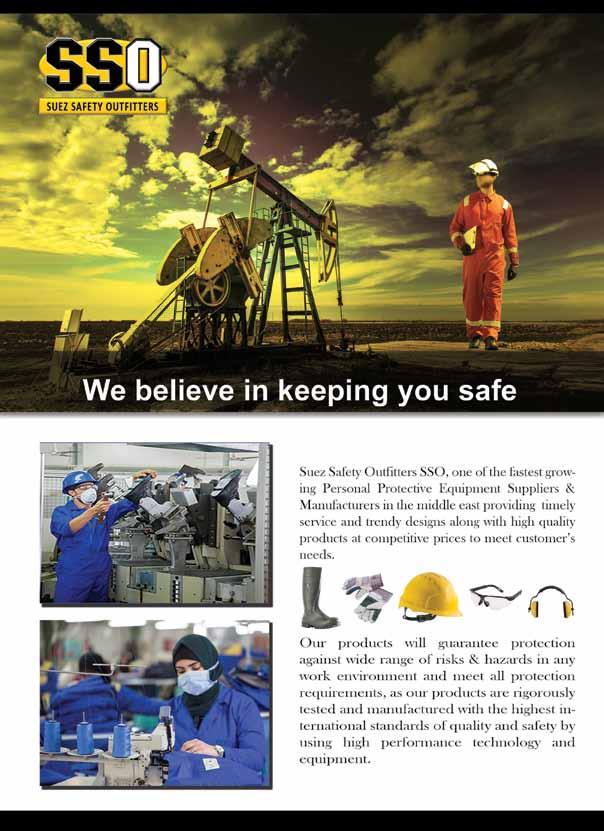
Wintershall Dea Committed to Egypt
In early 2018, Wintershall Dea announced the start of an extensive work program in all own-operated Egyptian assets. The company is currently investing more than 500 Million US-Dollars over three years (20182020-), aiming to significantly boost its gas and oil production in the country. “We look back on very active 18 months in Egypt”, says Mario Mehren, CEO of Wintershall Dea. «We have already realized a good part of the upside potential in our ownoperated assets Disouq and in the Gulf of Suez. Furthermore, the West Nile Delta project is progressing towards completing the development of the five fields by end of this year. These achievements are indicative of our lasting and sustainable commitment to Egypt», he adds. «We look forward to making further contributions to the development of the Egyptian energy sector, supporting the country on its way to become an energy hub for the region.»
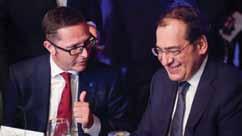
BP announces industry-first, continuous methane measurement programme
Drones equipped with space-age sensors are part of a wave of advanced technology zooming into operation at BP’s new major oil and gas processing projects as part of a programme to continuously measure methane emissions. The high-tech kit is part of an industry-leading BP programme to continuously detect, measure and enable the reduction of methane emissions at new and existing BP-operated Upstream assets. This crackdown on emissions has been made possible by a raft of new and complementary technologies.
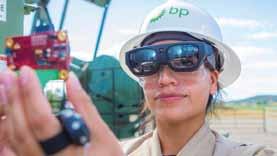
Hady Meiser Egypt
Mr. Eslam Abdel-Hady
CEO Hady Meiser Egypt for producing steel gratings is specialized in fabricating steel gratings (blackgalvanized) as well as steel stair steps which is also made with gratings by press welding according to DIN 24537 & 24531 and ISO 1461 & ASTM A 123 . All specification is according to the shown onto our catalogue and dimensions are according to client›s inquiries.
Address :ElShrouk Industrial Zone – Khanka – Kaiobia Contacts : 01001726068 -01144877633 - 0127 679 8800 – 01001726135 Fax : +2 02 44698047 – 44698212- 44604123 E-mail :trabia.meiser@gmail.com trabia_meiser@hadymeiser.com
Mr. Taha Abo Rabia
General Manager
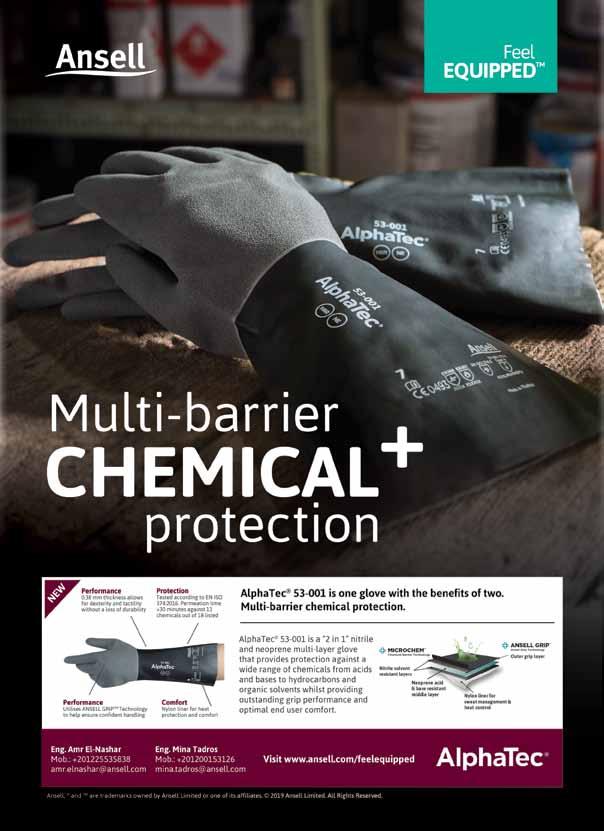
Talent & Technology
Electro-mechanical downhole cutting technology
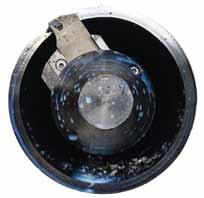
[ Fig-1 Halliburton Electro-mechanical downhole cutting tools ] Halliburton Company has announced an asset acquisition of a new portfolio of electro-mechanical downhole cutting tools and tubing punches from Westerton (UK) Ltd. These services provide operators with a safe and reliable alternative to traditional pipe recovery and intervention across the well lifecycle from exploration to abandonment. The electro-mechanical downhole cutting portfolio includes single and rotating blade configurations that perform precision cuts on oilfield tubulars. Operators can achieve single blade cuts in less than two minutes with real time downhole data that reduces uncertainty. This new technology eliminates the need for traditional explosive charges and chemicals, resulting in improved safety and easier transportation. Each cutting operation requires minimal surface equipment to enable faster deployment from any wireline unit. “The ability to deploy cutting services rapidly and efficiently is important for pipe recovery,” said Trey Clark, vice president of Wireline and Perforating. “This new technology complements Halliburton’s extensive well intervention portfolio, helping operators reduce the cost to construct new wells and extend the life of old wells.” On a recent campaign in the North Sea, an operator utilised the electro-mechanical downhole cutting service for a well abandonment program. The technology successfully saved one and half days of rig time per well – a substantial reduction from the initial plan.
Monitoring Pressure in Applications with Vibration and Pulsation
Liquid-filled gauges have several drawbacks that can introduce unnecessary elements of risk into a work environment. The issues associated with liquid-filled gauges can now be overcome with a new product solution that can be applied in all applications with vibration and pulsation, without the restrictions associated with liquid filling. One of the initial challenges that arose in monitoring pressure with dry gauges was caused by applications with vibration and pulsation. It was difficult to measure pressure in these types of applications as the pressure gauge pointer would shake making it impossible to get an accurate reading. Liquid-filling pressure gauges became the common method for steadying the pointer of a gauge in vibrating and pulsating applications. By filling the gauge case with a liquid, the movement of the gauge was dampened preventing the pointer from shaking. Liquid-filling has been the primary way of dealing with vibration up until today. While adding liquid to a gauge allows operators to accurately monitor the pressure of a process, it has limitations on where it can be installed compared to a dry gauge. In addition, liquid-filed gauges have several drawbacks that can introduce unnecessary elements of risk to a work environment. The challenges associated with liquid-filled gauges can now be overcome with a new product solution that can be applied in applications with vibration and pulsation without the limitations. Winters’ StabiliZR™ pressure gauges are dry gauges that can be installed in applications where liquidfilled gauges have traditionally been installed. The reason for StabiliZR’s effectiveness where other dry gauges fail is the StabiliZR™ movement which provides pointer dampening without requiring the entire case to be filled with liquid.
Connector Subsea Solutions acquires Hydratight’s MORGRIP business
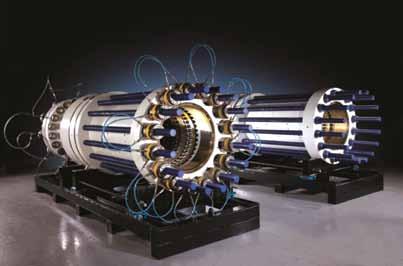
[ Fig- 5 MORGRIP subsea pipeline repair connector ]
Pipeline repair connectors are critical components in the repair of oil and gas pipelines. The operator’s requirements for this type of equipment are extremely high as the consequences of failure are dramatic with regards to potential environmental and commercial impacts and even to a region’s overall energy supply. MORGRIP Connectors boast a 100% leak free in-service track record of over 30 years. Hydratight’s MORGRIP business has a reference list second to none with more than 3,000 connectors delivered to the global oil and gas industry. MORGRIP’s offer a unique, robust, field proven, durable design that meets all of the industry’s strictest qualifications. This makes MORGRIP the primary choice of connector for the repair of critical pipelines and is in use by most of the major operators. The MORGRIP connector has also proven to be the connector of choice for emergency pipeline repair systems (EPRS) worldwide and through the acquisition; CSS takes a lead position providing emergency pipeline repair for more than 300 high value pipelines. The acquisition of the MORGRIP business completes CSS’ products and service offering enabling CSS to take a lead role in providing complete subsea and deepwater pipeline repair solutions, delivering it’s services on a sale or rental basis worldwide. “This has been a strategic move to build a foothold in a market that we believe will grow significantly the next few years. With the MORGRIP Connector and the MORGRIP team onboard we have taken a position to meet client’s requirements for the effective execution of demanding deepwater pipeline repair projects,” said Pål Magne Hisdal, chairman of CSS.
Chevron Technology Ventures pitches in on Well Conveyor development
The Conveyor has been optimized for running on batteries, with an efficient electro-mechanical design, allowing for extended tractoring distances of more than 15,000 feet. Not being dependent on power and communication from the surface allows operators greater flexibility and lower priced conveyance alternatives. The Conveyor has been designed for simplified operations and reduced maintenance, enabling the service to be provided by the regular wireline / conveyance providers. This translates into less interfacing and manpower being needed for operations. Well Conveyor was founded in 2015 by Kenneth Fuglestad to pursue the development of a novel downhole tractor that would be more cost-effective, slimmer, simpler to operate and more power efficient than existing offerings, allowing for the utilization of downhole battery power. Early support came from angel investors, the Research Council of Norway and Innovation Norway, which took the company through the concept, feasibility and early development phases for the Conveyor. ProVenture and Investinor invested in the company early 2018, and Chevron Technology Ventures (CTV) invited Well Conveyor to participate in its Catalyst Program. CTV’s Catalyst Program was created to support early-stage companies advancing cutting-edge technologies that can directly benefit the oil and gas industry. These relationships provided the means to advance the development and qualification phases and to expand the organization. Well Conveyor has carried out extensive in-house qualification testing of the technology and is now preparing for first field trials in the US. The patented Slim Batterypowered Conveyor will serve as a platform for additional innovative and cost-effective conveyance solutions to be developed by the company.
Probe releases new calliper for geothermal well operations
Probe has launched its UHT Dimension XY Caliper, the first XY Caliper Tool specifically designed to operate in ultra-high temperature environments. This new development expands upon the renowned Kuster® geothermal logging tool portfolio, used extensively in the global geothermal industry for its performance and reliability. Developed to operate in hostile environments up to 325°C (617°F), the UHT Dimension tool provides two continuous independent perpendicular measurements (X and Y) of the internal diameter of the casing. The tool also produces a highresolution temperature profile of the well via an external fastresponse resistance temperature detector (RTD). There is no other caliper tool that offers this versatility for ultra-high temperature and geothermal well operations. “The introduction of ultra-high temperature XY Caliper technology for the geothermal industry is a major breakthrough. A critical factor is that mineral deposition regularly affects geothermal well conditions. Until now, gauging the internal diameter of these wells was ineffective. The ability to generate a continuous log and accurately calculate flowrates is huge differentiating advantage,” said Steve Beattie, Sales Manager for Well Monitoring for Probe. “By gathering accurate, reliable on-depth casing dimensions, geothermal companies can quantify scale build-up and any other restrictions due to [ Fig-3 UHT first XY Caliper Tool ] the reduction in casing diameter. The tool also identifies downhole components and other anomalies. By detecting such issues early on, the operator engaging in such proactive maintenance can maintain a critical flowrate by removing the restriction; which will aid in reducing the operational downtime and treatment cost.” The UHT Dimension tool is very versatile. It can be run stand-alone or combined with other Kuster geothermal PT and PTS tools. Its robust mechanical design features single roller arms that conform easily to most wellbore conditions. However, if there is a need to run over slotted sleeves or sandscreens, an optional triple roller arm is available for increased run efficiency.
About the Course:
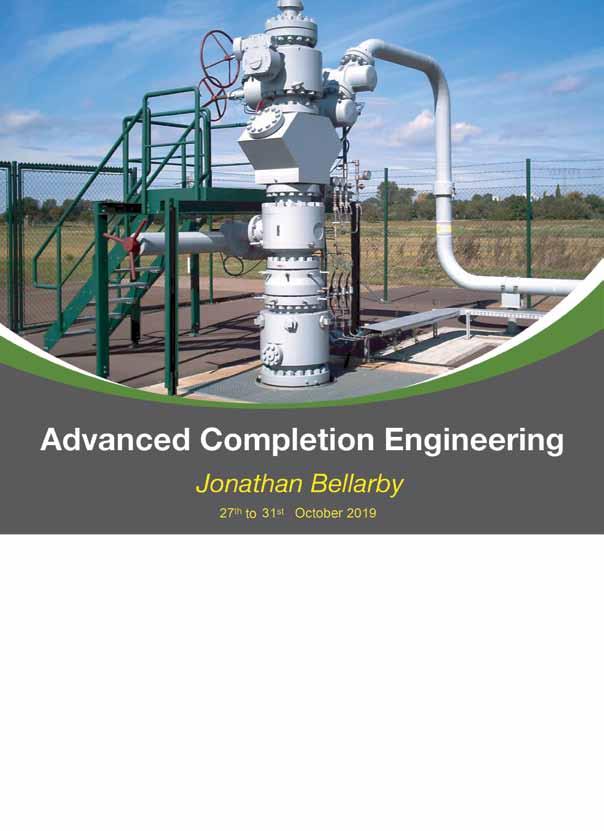
This course is of interest to Engineers - both Operating and Service Companies personnel – who are familiar with basic completion processes and willing to extend their understanding to cover more advanced aspects. The course also suits Production personnel, Engineers from disciplines other than Production Technology
About the Material:
Each participant will be given a copy of the original textbook WELL COMPLETION DESIGN March 2009, 700+ pages Elsevier Publication.
Book your Place:
Mobile: +2 (010) 05618777 Line : +20 (2) 25194800 Fax : +20 (2) 25194900 Email : asalah@sapesco.com
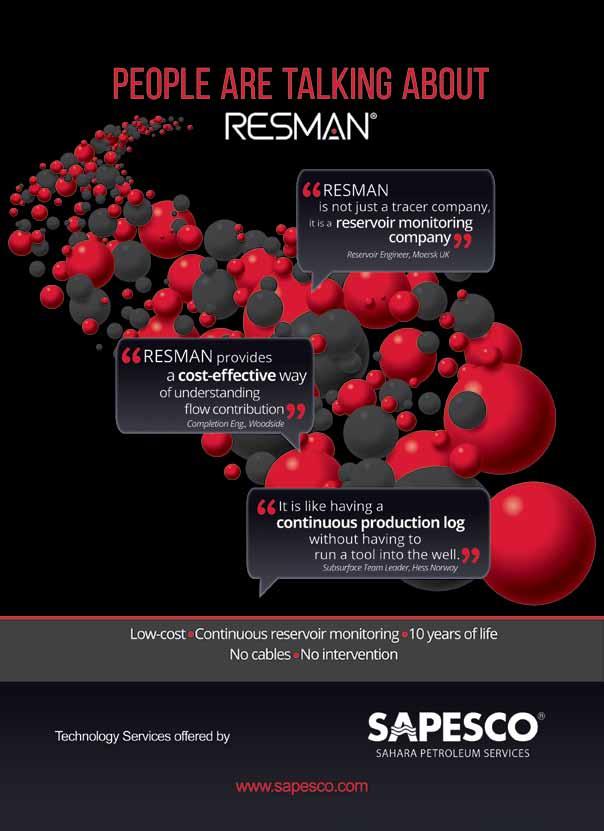
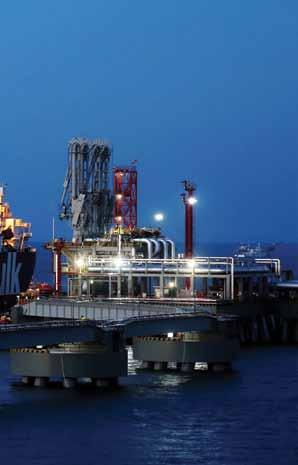
A number of North American LNG export projects are progressing to supply this growing market demand in Europe and Asia. Unprecedented gas discoveries in deep-water offshore Eastern Mediterranean and East Africa are also likely to compete for LNG market share in growing Asian and European gas markets. The regional statistics reveal the complexity of commercial, political and technical drivers at play, particularly in the case of Europe, and how these drivers are collaborating to boost future demand for LNG.
State of the LNG Industry and Global Trade
For the fifth successive year, global LNG trade set a record, reaching 316.5 million tonnes (MT). This marks an increase of 28.2 MT from 2017, equating to 9.8% yearon-year (YOY) growth. The continued growth in trade was supported by increases in LNG output from liquefaction plants ramping-up and coming online, more than offsetting lower production from several legacy projects. Australia led all exporters in gradual growth (+12.2 MT), supported by the Wheatstone LNG and Ichthys LNG projects. The United States was again the second-biggest driver of LNG supply growth, adding 8.2 MT as trains at Sabine Pass LNG operated for the full year and Cove Point LNG came online. Asia continued to be the driver of international LNG demand growth, as China broke its own record for gradual LNG by importing an additional 15.8 MT in 2018. This was driven by the powerful enforcement of environmental policies prepared for promoting coal-to-gas switching as well as continuing economic growth. Other key markets that lead global LNG growth included India, South Korea, and Pakistan, which took in a combined 12.8 MT of incremental imports. The Pacific Basin continues being the key driver of trade growth, with intra-Pacific trade flows reaching a record 134.2 MT, confirmed by Australian production and Chinese demand.
East Med Gas Potentials
Massive gas reserves are considered the game changers in the East Med. The three big finds of that period – Egypt’s offshore Zohr field, with reserves of 21.5trn cu feet of gas; the Israeli offshore Tamar and Leviathan fields, with 11trn cu feet and 22trn cu feet of reserves, respectively; and the 8trn-cu-feet Aphrodite find off the coast of Cyprus – have the prospect to transform the .region’s energy landscape In Egypt, the Zohr Progress by ENI, among others, has led to a revival in gas production: output grew from a low of 3.9bn cu feet per day in 2016 to 6.65bn in February 2019. For Israel and Cyprus, the gas discoveries assure greater energy security and new export revenues. A group of other fields have also been and are starting .to be developed, notably in Cyprus more recently
Mediterranean Gas Infrastructure and Liquefaction Plants
On 16thApril 2019, on the occasion of the Mediterranean Gas Infrastructure Operator (MedGio), organized by the Egyptian Natural Gas Company, Eng. Tarek El Molla, Minister of Petroleum and Mineral Resources,
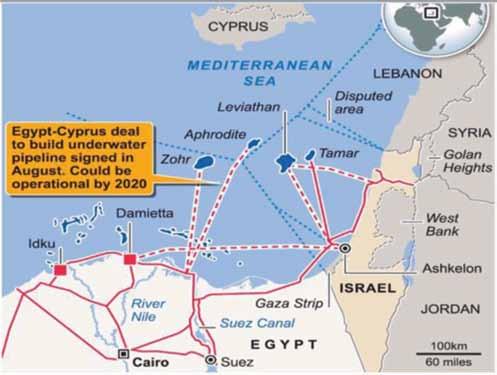
delivered a speech, in which he assured that the Mediterranean region holds a significant importance in the world order politically, economically and geographically. It is gaining major significance over the coming years, in the light of the existence of abundant gas resources, due to the big discoveries especially in the Eastern Mediterranean Region. El Molla assured that cooperation among the Mediterranean countries, members of MedGio, will consolidate the available infrastructure, in the light of the growing strategic importance, for the security of energy supply, in which the gas represents a fundamental role towards cleaner energy system. Compared to other countries on the Mediterranean, Egypt’s gas infrastructure is more developed. It has a relatively large natural gas export infrastructure, but is underutilized. With a total length of 7,485 km of transmission grid and 38,000 km of distribution grid, Egypt has the biggest infrastructure in the East Mediterranean area. Connecting the Mediterranean discoveries to Egyptian infrastructure necessitate ultimately lower investment than the construction of Greenfield LNG facilities in Cyprus or Israel. The Egyptian option is beneficial to all parties involved and enhances the role of Egypt in the region and its ability to secure revenue from being a transit route and re-operating the two LNG plants. Global liquefaction capacity still in the widespread phase of build-out that began in 2016, driven largely by capacity additions in Australia, the United States, and Russia. Between January 2018 and February 2019, 36.2 million tonnes per annum (MTPA) of liquefaction capacity was added. In September 2018, Egypt signed an agreement with Cyprus to connect Aphrodite gas field to its liquefaction plants in Idku and Damietta, whereby Cypriot gas would reach Egypt via a marine pipeline to be liquefied and re-exported. Also, $15 billion worth of gas from Israel’s Tamar and Leviathan fields will be processed in Egypt as part of a 10-year deal between the Israeli Delek Drilling Company and the Egyptian Dolphinus holding company. Existing LNG terminals on the two branches
of Nile Delta provide Egypt with an edge as a transit point for gas coming from Cyprus and Israel. The two plants are capable of exporting 1.8 BCFD, providing a platform to handle the combined production of both Leviathan and Aphrodite gas fields. Egypt’s strategic location and an infrastructure including refineries, liquefaction plants and petrochemical factories, poises it to become an important trading and distribution center for natural gas. This is a boost to Egypt’s international standing to grow reliance on natural gas, especially from Europe. EU gas demand is rated to range at around 400 billion cubic meters per year. Currently, Russia and Norway are considered the leading suppliers to the EU.
Regional Integration between East Med Countries
A series of major natural gas discoveries made in recent years and the prospect of substantial hydrocarbons resources waiting to be tapped beneath the Eastern Mediterranean waters have sparked major international interest. If developed in a successful way, they may significantly alter the energy picture in the Mediterranean region. They may also be a force that enhances energy security, economic evolution and regional cooperation. If not, they might become a major component of the geopolitical struggle, fuel existing disputes and add to the various anxieties in the region and beyond.
Egypt’s Steps towards Regional Integration
Egypt is in a strategic location and proximate to the gas resources-rich countries, which helps it to take steps towards regional integration. Egypt Initiated a strategic dialogue with the EU on energy and Signed a Memorandum of Understanding on an Egypt-EU Strategic Energy Partnership (April 2018). It signed an agreement with Cyprus to establish a natural gas subsea pipeline between the two countries, in order to facilitate natural gas delivery from Cyprus to Egypt’s liquefaction plants in Idku and Damietta. (September 2018). With Jordan, both countries signed MoUs between natural gas companies to regulate the sale and purchase of natural gas (January 2019). Also, it signed an MoU with Iraq and Jordan to transport Iraqi natural gas and crude oil to Egypt via Jordan. The discovery of hydrocarbon resources presents an exceptional window of opportunity for regional cooperation, and long term energy security. Exploitation and transportation of these resources in a timely and effective way could pave the way for minimizing the time-tomarket and boost the access to more valuable markets. Influential cooperation between the different countries and the energy companies active in the area could result in “optimal” investment decisions, such as the development of joint export infrastructure for fields located in various countries. As mentioned by Amos J Hochstein, US former Special Envoy for International Energy Affairs, countries will save billions if they share in-
frastructure and market access. If they don’t share those resources, most of the gas will have to stay in the ground.
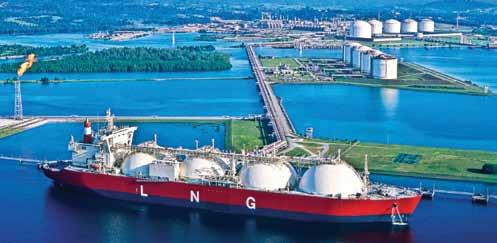
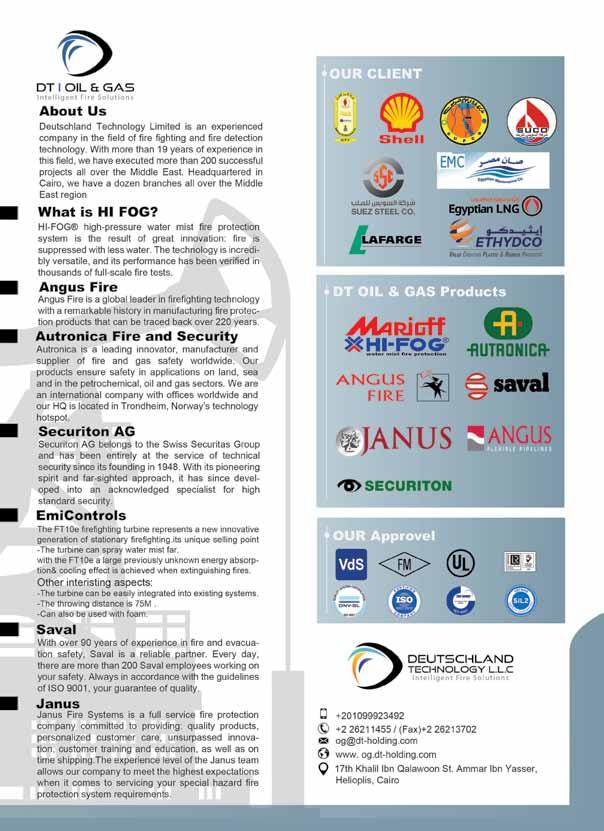
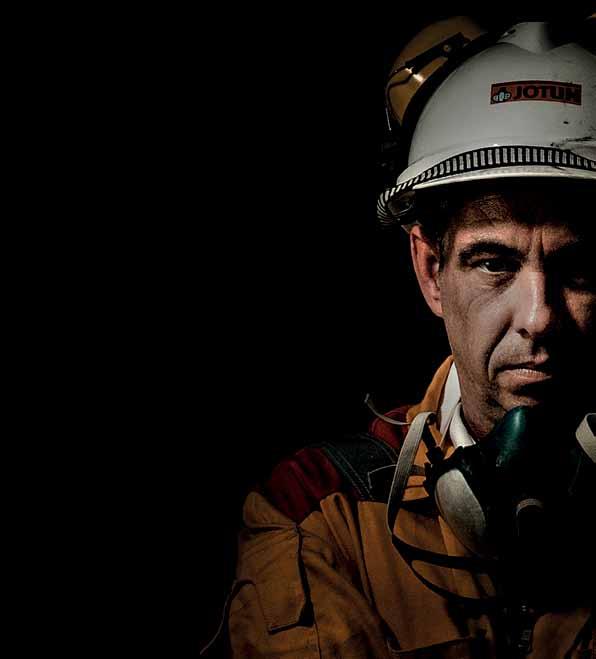
Jotun A/S
P.O. Box 2021 N-3202 Sandefjord, Norway Tel:+47 33 45 70 00
jotun.com
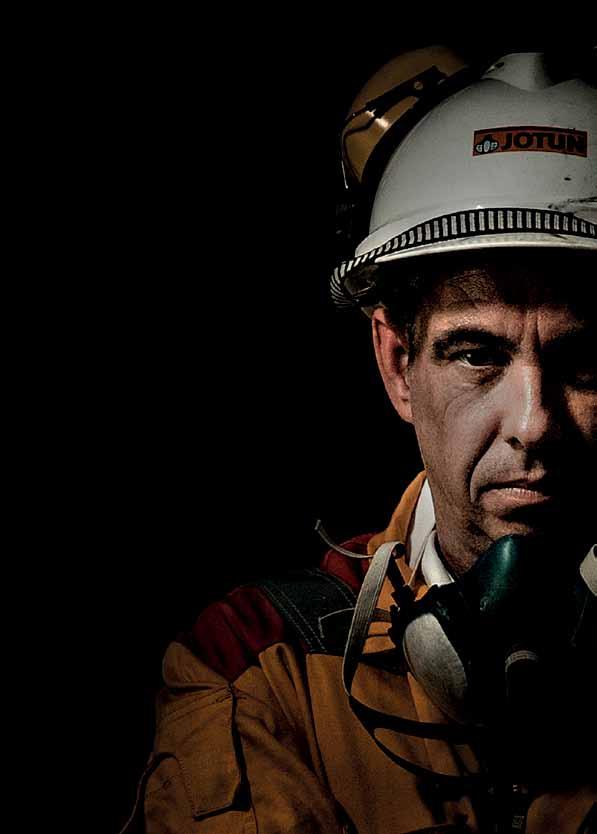
THE MOST SIGNIFICANT HAZARDS FOR FACILITIES IN THE OIL, GAS & PETROCHEMICAL INDUSTRIES ARE EXPLOSION AND HYDROCARBON FIRES. WITHOUT PASSIVE FIRE PROTECTION
(PFP) MEASURES, INCIDENTS CAN ESCALATE RAPIDLY, LEADING TO CATASTROPHIC LOSS OF LIFE, ASSETS AND INVENTORY.
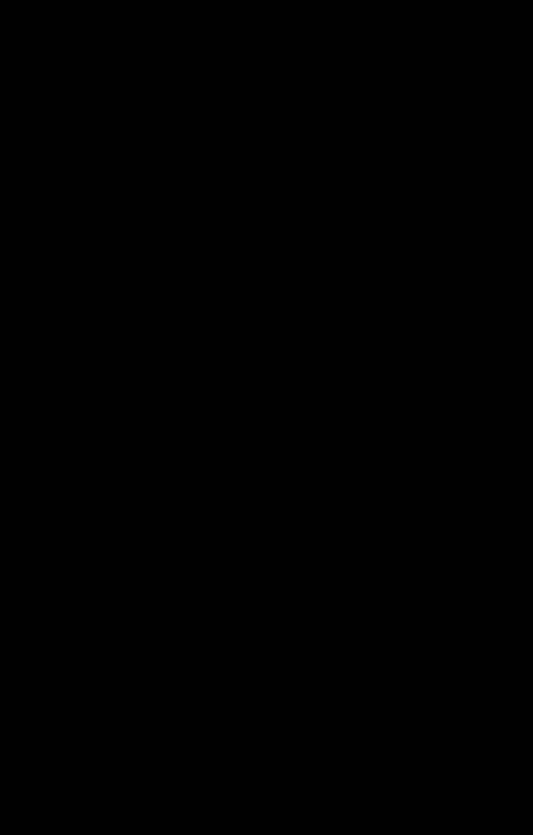
As steel temperature increases during exposure to fire, strength dramatically reduces. PFP measures prevent or delay collapse of steel structures by significantly reducing the rate of temperature increase. Until now, the industry has depended upon epoxy PFP coating systems that require additional mesh reinforcement to deliver the required performance. Mesh can be difficult and complex to install correctly. Incorrectly installed mesh can lead to uncertified installation and system failure when exposed to fire.
With Jotachar, there is no requirement for any additional mesh, meaning significantly reduced risks associated with incorrectly installed PFP. Jotachar incorporates an advanced fibre matrix, eliminating the need for complex mesh reinforcement.
The first mesh-free epoxy fire protection solution for all hydrocarbon and jet fires.
No additional mesh reinforcement. Just significantly reduced installation time and substantial material and labour savings. When exposed to fire, Jotachar JF750 produces a robust and temperature stable insulating char whilst risks associated with incorrect mesh installation are completely eradicated.
Jotachar 1709 combines passive fire protection and corrosion protection with low
lifecycle costs to asset owners. Jotachar 1709 is a highly durable solution with extended life to first maintenance, tested to rigorous industry fire & durability standards. No additional mesh reinforcement. Just significantly reduced installation time and substantial material and labour savings.
Jotachar benefits:
• Mesh-free time-saving solution • Up to 50% increase in installation efficiency • No compromise in fire and corrosion protection • Zero cost for mesh reinforcement materials.
No pins, no additional metal or fabric mesh. • Substantial time savings on installation • Lower lifetime maintenance costs compared with all other systems
Find out more at www.jotun.com/jotachar
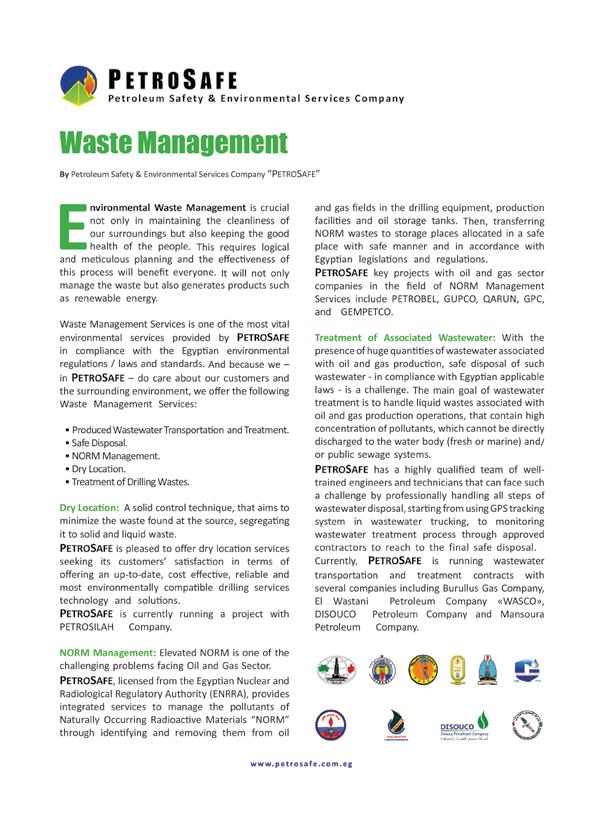
Technology Applications
Performance and Cost Benefits of Environmental Drilling Technologies: A Business Case for Environmental Solutions
By: Lydia Brantley, Jennifer Kent, Natalie Wagner, SPE, National Oilwell Varco
Abstract
Environmental impact has become business critical as we have been unable to crack certain issues to the degree expected for our industry. It is the central challenge for the continued development of shale markets, as it has been offshore. In a customer survey completed in the first quarter of 2012, a diverse group of operators, drilling contractors, and service companies identified their top three challenges for shale development: pricing, inexperienced personnel, and—of paramount importance—environmental impact. The industry recognizes the need for reduced environmental impact, but what do we need to achieve it? In the aforementioned survey, many operators and drilling contractors expressed looking to oilfield service and supply companies for continued innovation with the expectation that they continue to be to be forward-thinking and present ideas that provide value. The industry has two primary means for reducing environmental impact of its operations: processes (operator and contractor-driven) and equipment (service and supply-driven). This paper proposes that the two must work hand-in-hand. It explores the opportunity to take this further: identifying critical steps such as process design for reduced environmental impact with lower-impact technology and industrial engineering. The dual approach is needed to affect large-scale change. This paper will examine the positive impact of the implementation of select environmental technology can have on oilfield economics from the perspective of an oilfield equipment, technology, and services provider. It aims to: Ó Demonstrate a case for environmental solutions Ó Establish the importance of improved environmental
performance for market access Ó Identify areas in which operators evaluate environmental impact Ó Discuss the technology opportunities available to operators Ó Recognize and quantify the performance and cost benefits of aforementioned technologies.
The Positive Impact of Environmental Technologies on Oilfield Economics
Easy oil is gone. The aging of the conventional reservoir base, evident in the dearth of conventional green fields, acceleration of production decline rates, and limitations on spare capacity, combined with increasingly restricted reserve access following the wide reassertion of state control over national petroleum resources worldwide has driven operators to pursue higher-risk/higher-cost projects in order to replace reserves and maintain attractive assets. Along with the technical and economic challenges of these projects, operators now have to manage new challenges associated with drilling in areas that are more socially sensitive areas (e.g. northeast US, continental Europe, and Australia) and environmentally sensitive (e.g. the Arctic). Mitigating environmental impact has become business critical—both on land and offshore—as we have yet to effectively address certain issues to the degree expected for our industry. It would be naïve to think that regulations will drive improvement in our industry. Economics drive technology, and technology drives change. The oil and gas industry constantly seeks new ways to drill better, faster, and safer. Like any industry, oil and gas strives to do so while
increasing performance and reducing direct and associated costs; yet unlike many others, oil and gas faces the additional challenge of managing and mitigating the environmental impact of its operations. Our actions are magnified in part due to the areas in which we operate, and our missteps can have a significant impact on local communities and the environment. Engineering and industrial controls should be used together to achieve parallel goals of increased performance and reduced environmental impact. By aligning the right people, processes, equipment, and technology, we can do more. Increasing operational performance and reducing environmental impact do not have to be mutually exclusive (Harvard Business Review 2006). Admittedly, there are reasons why this perception exists. In some instances, environmental regulations have contributed to lower rates of return for oilfield players. For example, emission control regulations for new non-road diesel engines (i.e. the US and Europe’s respective Tier 4 Interim/Stage IIIB and Tier 4 Final/Stage IV) have forced oilfield equipment manufacturers and technology providers to pursue costintensive technology development and engineering. While some companies have taken advantage of the opportunity to establish a competitive advantage in these fields, the transition has been demanding in terms of resources, both financial and otherwise. This paper examines the positive impact that the implementation of select environmental technology can have on the economics of the oilfield. Across the industry, the main focus areas for improved environmental performance involve: energy efficiency and emissions, water use and recycling, leak prevention and spill containment, and drilling waste management. Acknowledging that the implementation of processes and technologies needed to mitigate the environmental impact of oil and gas drilling will be a longterm process achieved through incremental goals, this paper will concentrate primarily on the possibilities for improved environmental performance matched with operational and efficiency gains in one area: drilling waste management.
Drill Cuttings: An Introductory Definition
The largest source of drilling waste, drill cuttings present a significant challenge both on land and offshore as their presence, treatment, and disposal can inhibit the operational and economic efficiency of a drilling program. Drill cuttings refer to the materials (mainly solids plus some residual fluids) removed from the wellbore during drilling operations. Drilling fluid circulated through the wellbore and annular space during drilling carries the cuttings out of the wellbore and out to the surface. There the cuttings are separated and disposed: either discharged, re-injected, or (in the case of offshore wells) shipped to land-based treatment facilities (Oil & Gas UK 2012). While cost plays a role in determining the disposal option, environmental laws and regulation limit options based on the drilling location as well as the type of drilling fluid used. Cuttings generated from wells drilled with oil-based mud, for example, must be treated extensively prior to disposal (as compared to those generated from wells drilled with water-based mud). Treatment vis-à-vis technologies like centrifugal dryers and thermal desorption units can limit the environmental risks associated with disposal both on land and offshore. Processes and technologies that reduce the amount of drill cuttings and/or treatment required before disposal can deliver operational and economic benefits while mitigating environmental impact, proving: what’s good for business can also be good for the environment.
Waste Management Helps Enable Market Access
With the increase of drilling in more technically challenging operating environments, environmental performance has become business critical as we have been unable to resolve certain issues to the degree expected for our industry. Improved waste management enables market access, particularly in environmentally and socially sensitive areas. Compliance with environmental laws and preservation of positive public opinion play a role in market access. While the conversation below focuses on waste management, the same general ideas are transferrable to the other major focus areas for improving environmental performance in the oil and gas industry.
Compliance with Environmental Laws and Regulations
The way in which environmental risks are perceived and regulated can impact the support for and development of drilling in certain areas. Regulations have barred drilling in areas rich in resource potential at various times due to political and public concerns of environmental impact. For example, various countries controlling Arctic access declared a temporary moratorium on drilling following 2010s Gulf of Mexico oil spill due to concerns that current infrastructure for spill cleanup was inadequate (Bolstad 2010). Similarly, multiple countries with technically recoverable shale gas resources (e.g. France and Bulgaria) have placed a temporary moratorium on the hydraulic fracturing necessary for shale gas development pending further environmental investigation (Jacobs 2012). Certain areas of the US are banning the practice following recently passed ballot amendments (Associated Press 2012). The aforementioned may be extreme examples, but they demonstrate the business