6 minute read
Timber structures: sustainability Affordable low-carbon timber homes: a balancing act
Affordable low-carbon timber homes: a balancing act
Jae Cotterell outlines the challenges of construction budgets versus sustainability.
Many think that a sustainable, climate-ready future requires new housing to be built using timber, wherever feasible. This reflects a significant shift from the belief that energy efficiency alone would be required, and we are beginning to appreciate that embodied carbon is also critical to reduce carbon emissions sufficiently.
The UK building culture has been rooted in masonry construction and in recent decades there have been modest increases, across all sections of construction, in the amount of insulation used, generally using high embodied carbon insulation. The necessary shift of emphasis towards timber structures reflects its low-carbon and renewable credentials. Building in timber frame also enables use of modern methods of construction (MMC), which assist with erection speed, quality control systems and waste management.
With the need for highly insulated and airtight homes, timber can offer carefully targeted solutions, instead of simply tweaking traditional construction methods. The potential benefits to the environment are significant. However, there are caveats and pitfalls to be avoided, or at least carefully considered. Here are three examples where specifying timber and claiming eco-credentials must be carefully balanced against environmental impacts and the potential for elevated costs.
Protecting limited resources
First, there is the over-use of timber itself – it is after all a limited resource, and we suffer from a lack of biodiverse forests both worldwide and in the UK. Planting for use as a ‘product’ is not the same as enlarging existing established woodland, and we need to keep this in mind. Allocating large areas of land for single growth ‘tree farms’ reduces land available for biodiversity and other activities such as supporting generation of renewable energy and increased local food production – land is under great pressure in the context of building a decarbonised economy.
When specifying timber, we must consider resource efficiency and newer timber products; using laminated veneers such as I-joists can be a good fit for smallscale developments as they enable minimisation of structure and maximisation of insulation.
Claims of carbon offsetting through sequestration in the timber elements can be misleading and could simply reflect extravagant use of the timber itself. Certainly, if we are looking at affordable housing and switching to timber frame construction, appropriate >>
Figure 2: Laminated veneer lumber. Photo: Passivhaus Homes Ltd
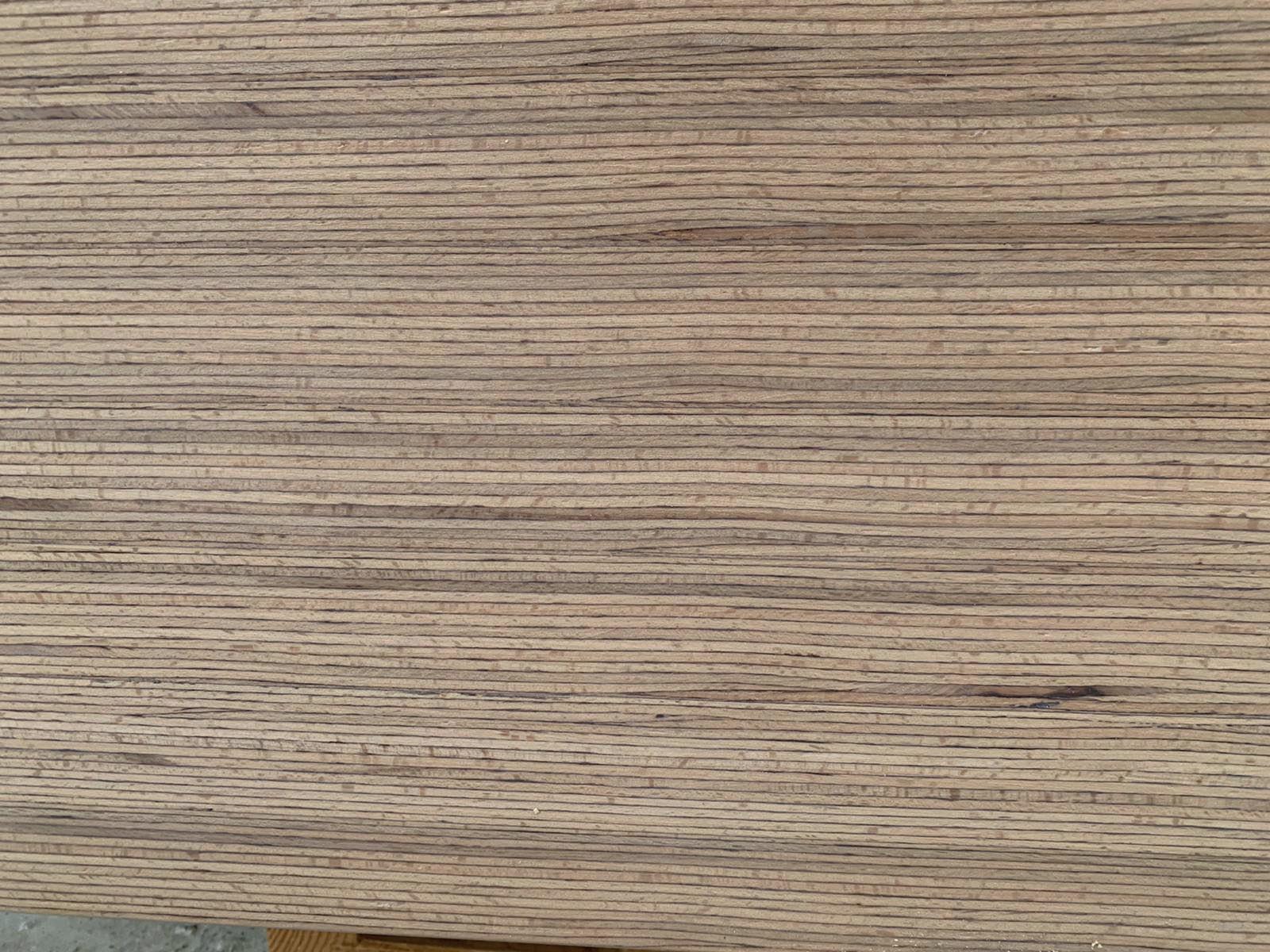
use of timber is key to minimising both the environmental impact as well as cost. The amount of timber structure required to meet an efficient wall or roof build can vary significantly, easily doubling the amount of timber required (e.g. a 360mm I-joist frame versus a 90mm cross-laminated timber panel). Even within a frame type (e.g. structural insulated panels, I-joists or solid timber studs) the timber frame fraction¹ (TTF) can vary significantly. If you want to maximise thermal efficiency (and therefore cost), you must also keep these timber fractions low, certainly aiming for <15%. A useful analysis of the TFF and its impact is referenced under ‘Further reading’. If you design or specify a frame with a high structural ratio and/or high timber fraction, then thermal and resource efficiency, as well as cost, are likely to be impacted negatively.
Reducing operational carbon
Second, to achieve low carbon, consider the use of timber beyond the structural frame. Low carbon involves reducing operational carbon too, and to achieve low heat demands we must specify lots of insulation along with designing to remove or minimise thermal bridging. With a structurally efficient timber frame, 85% of a wall or roof construction might be insulation (certainly at Passivhaus or net zero carbon performance levels). The carbon intensity of the insulation is therefore even more important than your structural elements – that is if your whole construction solution is to reduce carbon sufficiently to meet net zero energy targets.
Using high performance insulations within a frame will significantly increase the embodied carbon impact. To provide comparative figures:
• a loose wood fibre insulation might be as low as 12kgCO2e/m3 • a wood fibre board around 40kgCO2e/m3 • a high performance PIR insulation commonly above 130kgCO2e/m3 .
Of course, you only require about half the depth of a higher performance insulation, to achieve similar U-values, but it is clear to see how the embodied carbon figures will still be significantly impacted by insulation choice. Certainly, a low-carbon house involves more than specification of timber structure. The further advantage of using lower embodied carbon insulations (wood fibre would be a good low-carbon choice) is that generally these insulations are also vapour permeable and enable the natural breathable properties of timber to be maintained across the entire element (roof or wall). This allows for potential drying to external air and follows timber best practice.
External finishes
Third, the carbon intensity of the finished house will also be significantly impacted by choice of the external finish. A frame might be finished in several ways, from timber cladding all the way to full brick outer skins.
The choice of cladding materials has expanded over recent years and it is worth considering newer options on the market that are lower in carbon, are robust over the lifetime of the building and offer practical disposal options at end of life. Architects currently frequently specify timber frame while >>
Learn more by visiting: www.posi-joist.co.uk
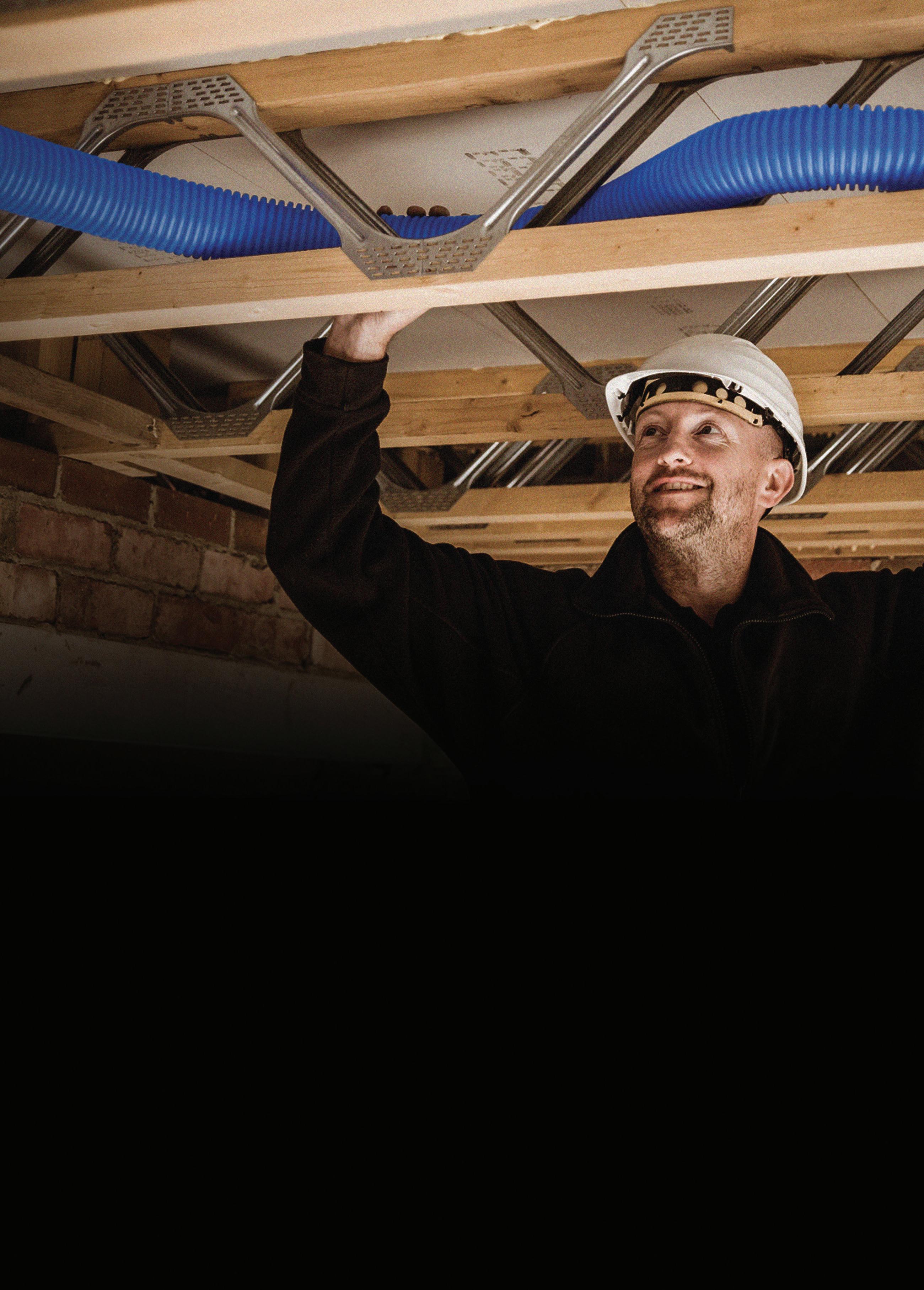
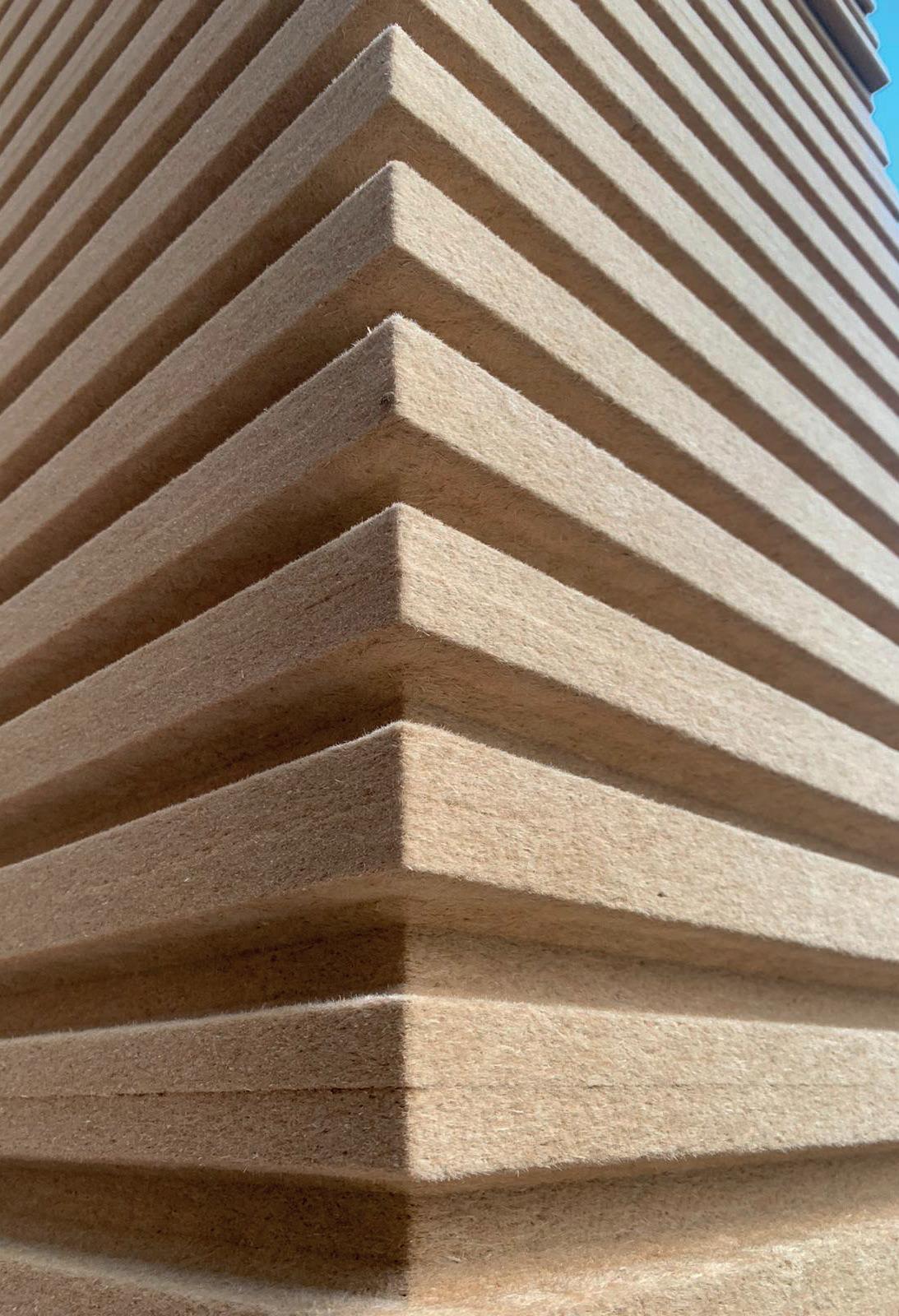
Figure 3: Wood fibre insulation. Photo: Passivhaus Homes Ltd Having reduced the embodied carbon with a timber shell, consideration of the final finishes should form part of a properly integrated specification. There is much potential for use of a wider variety of durable and recyclable finishing materials, ones that could add cost value. We don’t need to revert to brick facades. A limited use of more carbon-intense options in critical areas and in locations where they might be optimally appreciated (e.g. around entrances) could be another useful strategy.
Summary
Delivering affordable low-carbon timber houses sits at the top of the built environment agenda and taking time to consider how to approach this thoughtfully would be time well spent. Achieving environmentally appropriate solutions requires broad considerations and an understanding that simply specifying timber frame will not be good enough. n
About the author
Jae Cotterell Passivhaus Homes Ltd Co-creator of the PH15 System – winner of the Ashden Award 2020 for scaleable climate change solutions
Further information
For more information, visit www.phhomes.co.uk
To find out more about timber and sustainability, visit www.trada.co.uk/sustainability
also designing with brick outer finishes – this will be a highcost and high embodied carbon option. However, brick does offer a durable and robust finish that can maintain an excellent aesthetic appeal over time.
Timber cladding is typically cheaper and much lower in carbon cost, but appearance can significantly degrade with age if it is not designed, specified, built and maintained well. Choosing to use timber cladding needs that extra level of care to ensure durability and aesthetic quality over time. There are an increasing number of modified timbers now available, along with other material cladding options – considering these materials can introduce variety in the design, be cost effective, lower the carbon intensity, and offer good maintenance and appearance characteristics.
Further reading
• Innovative timber construction, ISBN 978-1-9005-875,
BM TRADA, 2012 • Low energy timber frame buildings: designing for high performance, 2nd edition, ISBN 978-1-900510-80-6,
BM TRADA, 2011 • Zaccaro, F., Littlewood, J. R. and Hayles, C., ‘An Analysis of Repeating Thermal Bridges from Timber Frame
Fraction in Closed Panel Timber Frame Walls: a Case
Study from Wales, UK’. Email fzaccaro@cardiffmet.ac.uk for more information.