3 minute read
Chain Reaction Unlocking Warehouse Potential: Exploring AMRs in Automated Material Handling
dynamic environments using advanced mapping and localization technologies. AMRs across vendors cater to diverse warehouse environments, ensuring that the right solution is available for specific operational needs.
In the realm of warehouse automation, Autonomous Mobile Robots (AMRs) have emerged as a revolutionary solution for streamlining material handling operations. AMRs offer a myriad of benefits, but it is essential to understand their pros, cons, and alternative technologies to make informed decisions. This article delves into the world of AMRs, their advantages and limitations, and explores alternative technologies worth considering.
AMRs offer numerous advantages that contribute to improved warehouse efficiency. Providers like Fetch Robotics have developed advanced AMRs equipped with cutting-edge perception and navigation capabilities. These robots can autonomously navigate complex warehouse environments, collaborate with human workers, and perform tasks such as picking, sorting, and item transportation. Locus Robotics, another prominent player, specializes in AMRs tailored for e-commerce fulfillment operations. Their robots work collaboratively with human pickers, increasing productivity and reducing order fulfillment time. MiR (Mobile Industrial Robots) offers a diverse lineup of flexible and collaborative AMRs for material transportation and logistics within warehouses. MiR's robots autonomously transport pallets, carts, and bins, adapting to
Operating tirelessly, 24/7, AMRs ensure optimal performance and accelerate operational throughput. The versatility of AMRs allows them to adapt to changing warehouse layouts and operational requirements, making them highly flexible and scalable. Integrated with warehouse management systems, AMRs enable real-time monitoring and optimization, contributing to continuous improvement and streamlined operations.
Safety is a paramount consideration in warehouse environments, and AMRs excel in this aspect. Equipped with advanced sensors and intelligent navigation systems, AMRs from providers like Fetch Robotics, Locus Robotics, and MiR can detect obstacles, avoid collisions, and ensure safe movement within the warehouse. This eliminates the risk of accidents caused by human error, enhancing overall workplace safety.
While AMRs offer substantial benefits, they are not without limitations. Initial investment costs, including the procurement of AMRs, necessary infrastructure modifications, and system integration, can be significant. However, the longterm gains in efficiency and productivity often outweigh these costs. Warehouse layouts with high complexity or dynamic elements may pose challenges for AMR navigation and operational efficiency. In such cases, alternative technologies or hybrid solutions that combine AMRs with other automation systems may be more suitable. Furthermore, regular maintenance and repair requirements should be considered to minimize downtime and ensure smooth operations.
Determining the ideal scenarios for AMR implementation requires careful assessment. AMRs are particularly well-suited for repetitive material handling tasks, stable environments with clearly defined paths, and high-volume operations that demand efficient and agile movement.
AMRs offered by notable providers like Fetch Robotics, Locus Robotics, MiR and others provide significant advantages for warehouse automation, including enhanced efficiency, safety, and scalability. However, a thorough evaluation of specific warehouse requirements is crucial to determine their suitability. By considering factors such as complexity, flexibility, and budget constraints, warehouse operators can make informed decisions regarding AMRs or alternative technologies. Embracing the right mix of automation solutions, including those offered by leading providers, ensures optimized operations, and unlocks the true potential of your warehouse. Remember, the journey to warehouse excellence encompasses a diverse range of technologies, and AMRs are just one exciting piece of the puzzle.
Bill Denbigh serves as the vice president of product marketing at Tecsys. Bill started working in supply chain software some 30 years ago; his entire career has been laser-focused on designing and building pragmatic supply chain solutions that address the real problems that customers are facing in their supply chain operations. Bill has worked on virtually every aspect of the software in the supply chain, gaining insight into the inner workings of some of the industry’s most complex challenges; Bill, however, tackles those challenges with a no-nonsense levelheadedness that has earned him great repute both internally and among customers.
Blocks the Spread of FireActivates the Sprinkler System
Today’s warehouse fire protection systems include more than just pipes and sprinklers. When the products being stored include highly flammable items such as plastics, aerosols, liquors or oils, fire barriers may be required inside the racking structure.
Solid steel rack decking and flat sheet accessories from DACS make effective fire or heat barriers in warehouse environments.
They can be used on storage racks horizontally or vertically to block the spread of fire, or to capture heat for in-rack sprinkler activation.
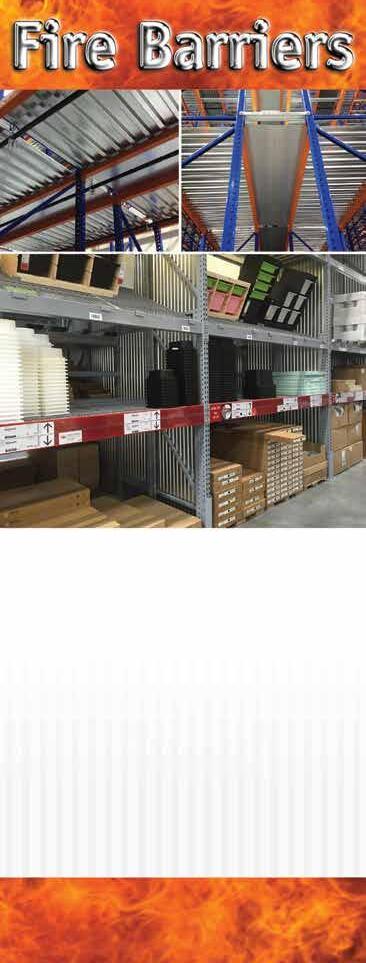