6 minute read
TCO per part beslissend bij opschalen additive manufacturing
Automatisering die integraal onderdeel is van de 3D metaalprinter draagt substantieel bij aan een lagere Total Cost of Ownership per geprint onderdeel. Dat toont een benchmark van Ampower aan. Het Duitse consultancybureau heeft de MetalFAB1 van Additive Industries vergeleken met 15 laser powderbed fusion (LPBF) systemen. De uitkomsten verrasten zelfs de consultants zelf.
Additive Industries heeft zelf het initiatief voor de benchmark genomen. De Nederlandse fabrikant wil objectief cijfermateriaal in handen hebben om klanten te overtuigen van iets dat ze zelf in Eindhoven al lang weten. “Als relatief jong bedrijf moeten wij meer data overleggen om mensen te overtuigen. Deze benchmark helpt ons om de claim van productiviteitsleiderschap te onderbouwen”, zegt Daan Kersten, CEO van Additive Industries. Dat het Eindhovense AM-systeem zo goed uit de bus zou komen, had hij echter niet verwacht. Ook Matthias Schmidt-Lehr, een van de drie oprichters van Ampower, is verrast door dat de resultaten van de benchmark. “Eerlijk gezegd ben ik altijd sceptisch geweest over volautomatische systemen. Je betaalt veel voor een investering die je maar beperkt gebruikt, dacht ik.” De benchmark toont echter aan dat automatisering wel degelijk zin heeft en de Total Cost of Ownership (TCO) per geprint onderdeel verlaagt; bij de ene toepassing meer dan de andere maar bij een bezetting met één ploeg, levert het een lagere kostprijs per onderdeel op. Daan Kersten is overtuigd dat de TCO een beslissende factor wordt als het om de investering in een AM-systeem voor metaal gaat. “Als de industrie naar full production met Additive Manufacturing gaat, dan heb je andere systemen nodig dan voor prototyping.” En als de voorspellingen die het World Economic Forum onlangs heeft gedaan uitkomen, zul je volgens hem snel deze verschuiving zien. Bij Additive Industries merkt men dat al aan de vragen waarmee potentiële klanten binnenkomen. “Hun kennisniveau is veel hoger, hun vragen gaan veel meer de diepte in.”
De aanpak van de benchmark
Ampower doet vaker benchmarks voor fabrikanten van 3D metaalprinters. Daarbij rekent men altijd met cijfers die de fabrikanten zelf publiceren. Matthias Schmidt-Lehr verdedigt deze aanpak door erop te wijzen dat er qua laserbronnen, scanners en snelheid weinig verschillen meer bestaan tussen de verschillende AM-systemen. Door voor deze aanpak te kiezen, wordt de invloed van het kennisniveau van de operator geëlimineerd. “Dit maakt de benchmark objectiever.” Vier typische AM-onderdelen zijn helemaal doorgerekend wat betreft kosten per geprint onderdeel, de investering in het systeem, de investering per cm2 laservermogen en leadtime. De vier AM-werkstukken uit de aerospace-, olie- en gas-, medische en automobielindustrie zijn virtueel geprint in titanium. Er zitten zowel grotere als kleinere stukken bij. Vervolgens zijn er twee berekeningen gemaakt: eentje als je de machine in 1 shift per dag inzet, de andere met 2 ploegen. De andere systemen waren eveneens laser poederbed systemen maar zonder automatisering, omdat geen andere fabrikant dit als standaardoplossing aanbiedt.
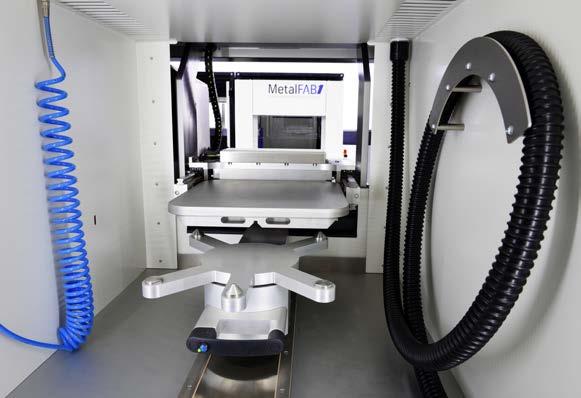
TCO op MetalFAB1 het laagste
Het blijkt dat de MetalFAB1 van Additive Industries voor op één na alle onderzochte onderdelen de laagste TCO oplevert. De enige uitzondering is een onderdeel waarvan één stuk op een bouwplatform van 250 bij 250 past en dat in een bezetting met twee - of meer - ploegen wordt geprint. “Dan heeft de MetalFAB1 een nadeel”, zegt Matthias Schmidt-Lehr. “Als je kleinere delen print en je voert de packing density op, dan wordt het voordeel van de MetalFAB1 groter.” De Nederlandse machine verslaat de andere systemen qua productiviteit en TCO echter bij alle vier de stukken als er in één shift wordt gewerkt. Dan is de standaard aanwezige automatisering duidelijk een voordeel. “Als je de hoge arbeidskosten wilt verminderen, dan wordt automatisering belangrijker”, zegt Matthias Schmidt-Lehr. “De grootste USP van de MetalFAB1 is automatisering, deze zorgt voor het grote kostenvoordeel als je in 1 shift werkt.” Die kant gaat het op, merkt Daan Kersten aan de gesprekken die hij met (potentiële) klanten heeft. “De algemene trend is dat men een kortere bouwtijd wil, door met meer lasers de snelheid op te voeren om de doorlooptijd te verkorten. Dan kom je met meer stukken in de bandbreedte waar automatisering zin heeft.” Het is dan ook de architectuur van het systeem dat volgens hem de Nederlandse machine boven die van de concurrentie uittilt. Automatisering is de kern van het concept van de MetalFAB1. Deze zorgt ervoor dat handelingen zoals het uitnemen van de bouwplaat en het verwijderen van poeder, automatisch gebeuren, zodat de lasers onbemand met de volgende printjob kunnen beginnen. Bij de ene toepassing is dat voordeel groter dan bij de andere, maar de MetalFAB1 is ten opzichte van alle andere geteste systemen de metaalprinter met de hoogste productiviteit en de laagste kostprijs per onderdeel dat van het systeem komt. Daan Kersten: “Als je de productie wilt opschalen, is de total cost per parts de kritische factor. Zodra wij met een test hebben aangetoond dat we de kwaliteit die de klant vraagt halen, komt de vraag naar TCO per part en onze roadmap om deze kosten verder te verlagen. Deze benchmark draagt bij aan onze geloofwaardigheid.” Hij denkt dat de productiviteit van de MetalFAB1 in de praktijk hoger zal zijn dan de benchmark weergeeft. “Wij weten uit ervaring dat onze systemen in het veld een hogere operationele beschikbaarheid hebben dan waarmee Ampower heeft gerekend.” Daar is echter geen rekening mee gehouden, zegt Matthias Schmidt-Lehr. Om objectief te blijven, is gerekend met data die fabrikanten publiek bekend maken.
“In een markt met te veel aanbieders moet je je onderscheiden. Additive Industries doet dat heel slim door met hun volautomatisch AM-systeem te focussen op productiviteit en kostprijs per part”
Zin van automatisering
Additive Industries scoort dus hoog dankzij de architectuur van de MetalFAB1. Dat concept is geen rocket science, zegt Daan Kersten die acht jaar geleden Additive Industries startte samen met Jonas Wintermans. Toch heeft het concept van geïntegreerde automatisering tot nog toe geen navolging gekregen. De andere fabrikanten kiezen voor oplossingen met AGV’s, robots en losse modules. “Een dure oplossing voor dezelfde uitdaging”, zegt Daan Kersten daarover. “En als je nu nog onze oplossing wilt integreren, ben je te laat. Wij hebben vier jaar praktijkervaring met een installed base.” Additive Industries heeft vanaf de eerste dag voor een concept gekozen waarbij de configuratie zowel met als zonder automatisering mogelijk is en deze zelfs naderhand geïntegreerd kan worden. En dat is een goede strategie van Additive Industries, vindt Matthias Schmidt-Lehr. Nu de markt minder snel groeit dan verwacht, zijn er te veel aanbieders in de markt, zeker in het laser poederbed segment. “Dan moet je je onderscheiden. Sommigen focussen op een toepassing of een materiaal, Additive Industrie kiest heel slim voor productiviteit en kosten.”
Gaan bedrijven nu veranderen?
Ofschoon productiviteit en TCO belangrijker worden, verwacht noch Daan Kersten noch Matthias Schmidt-Lehr dat bedrijven die de afgelopen jaren hun AM-productie hebben gevalideerd, nog gaan veranderen van systeem. “Als je de businesscase rond hebt, is de drempel om nog te veranderen in de gevalideerde processen erg hoog”, aldus Matthias. Hij schat in dat maar weinig van deze bedrijven bereid zijn in de ramp up van de productie de certificering opnieuw te doen. “Als ze de businesscase rond hebben, is productiviteit geen driver meer. Dat komt pas later als ze gaan produceren.” Wel bij nieuwe toepassingen kan de uitkomst van de benchmark een rol gaan spelen. Dat kan volgens hem een omslagpunt in de markt betekenen waarop de automatisering belangrijker wordt.
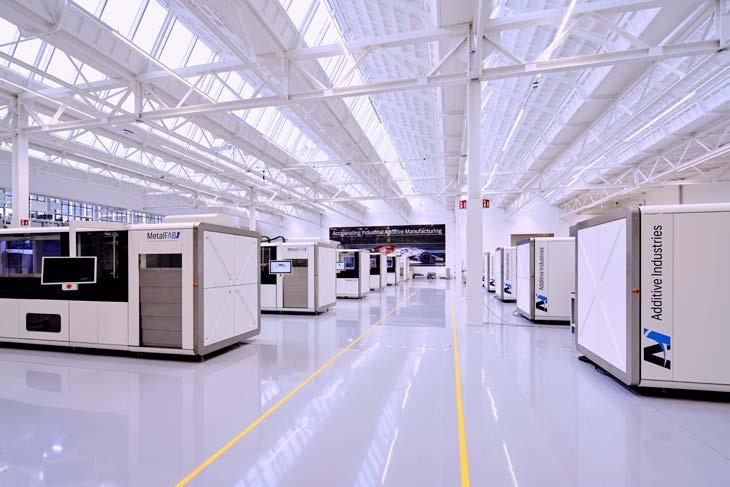