4 minute read
Metaal uit een draadje: FFF 3D metaalprinten
Als er over 3D metaalprinten wordt gesproken, gaat het meestal over laserpoederbed en binder jetting systemen. Dat je met een FFF printer ook metalen onderdelen kunt printen, is veel minder bekend. Hoewel de techniek zeker beperkingen kent, is het voor bepaalde toepassingen absoluut bruikbaar. De instapdrempel ligt laag.
METAAL FFF BIEDT KANS VOOR WIE SNEL OVER 3D GEPRINTE METALEN ONDERDELEN WIL BESCHIKKEN
Het Franse Nanoe levert traditioneel keramische materialen voor onder andere spuitgieten van keramische componenten (Ceramic Injection Molding). Een indirect proces, want de poeders zijn verpakt in een polymeer die verwijderd moet worden en daarna moeten de onderdelen gesinterd worden. Nanoe zoekt inmiddels ook toepassingen in de AM-industrie, met zowel filamenten die gevuld zijn met keramiek als met metaal. Dat gebeurt onder de merknaam Zetamix.
Nichetoepassing
In een webinar eerder dit jaar gaf Guillaume de Calan, founder en CEO van Nanoe, aan hiermee niet te willen concurreren met binder jetting, lasersmelten of een andere AMtechnologie voor metaal. “Elke technologie heeft zijn nichetoepassing.” Voor hem ligt de toepassing van het metaalgevuld filament in applicaties waarvoor bedrijven een laagdrempelige metaalprinttechnologie zoeken. Laagdrempelig in de zin van sneller te leren dan poederbedgebaseerde technieken én in de betekenis van aanzienlijk lagere investeringskosten. Het voordeel is de korte doorlooptijd, het feit dat je alle stappen intern in de onderneming kunt doen en dat het een relatief veilige technologie is, die geen bijkomende investeringen vraagt in speciale opslag en beschermingsmiddelen. Daar staat tegenover dat - zoals bij elk indirect proces - er onvermijdelijk krimp optreedt. Nanoe weet deze te beheersen, waardoor je met een nauwkeurigheid van 0,1 mm kunt printen. “Je kunt elke bewerkingstechniek gebruiken die je normaal voor metalen onderdelen gebruikt, inclusief fijnslijpen en stralen.”
Volume- of massaprocent?
Het eerste waar je volgens De Calan op moet letten, is het percentage metaaldeeltjes in het filament. En dan gaat het specifiek om het volumeprocent metaal, wat iets anders is dan het percentage uitgerekend in verhouding tot het gewicht, massaprocent. In het Zetamix metaalfilament zit 50 volumeprocent metaal, wat hoog is aldus De Calan. Een filament met bijvoorbeeld 80% van het gewicht metaaldeeltjes, levert in volumeprocent een waarde van ongeveer 33% op omdat het gewicht van de metaaldelen 8 keer hoger is dan van het bindmiddel. 33 volumeprocent is te laag om nog een goede dichtheid te realiseren. Met 50 volumeprocent vulling haalt Nanoe na het sinteren een dichtheid van meer dan 90% en een nauwkeurigheid van 0,1 mm over een stuk van 8 tot 10 cm groot.
Thermische debinding
Ook qua proces kiezen de Fransen voor een andere weg dan andere aanbieders. Nanoe kiest namelijk voor thermische debinding. Anderen kiezen voor chemisch debinding (Markforged) of katalytisch (BASF Ultrafuse). Dat laatste proces is snel, maar heeft als nadeel volgens De Calan de hoge kosten qua investering. Chemische debinding is eveneens snel, waardoor er minder risico is op vervorming. Maar je werkt met oplosmiddelen. Het nadeel van thermische debinding, zoals Nanoe bij Zetamix doet, is dat het risico op vervorming toeneemt en er kan oxidatie optreden. Thermische debinding is wel veel sneller dan chemische. Daarnaast zijn er geen zuren en oplosmiddelen nodig. En met de juiste parameters kun je de nadelen van thermische debinding beperken. Nanoe put hierbij uit de ervaringen met de poeders voor MIM en CIM.
Extra hoge sintertemperatuur
Na het 3D printen van het werkstuk gaat het naar een oven en vindt in de eerste fase (tot 600 graden C) debinding plaats. Het thermisch bindmiddel wordt verwijderd. In de tweede fase (800 tot 1200 graden C) worden de metalen poederdeeltjes met elkaar verbonden. Nanoe past daarna nog een derde fase toe, waarmee je volgens Guillaume de Calan voorkomt dat je een poreus metalen werkstuk overhoudt. In deze laatste fase (1200 tot 1400 graden C) gaan de metaaldeeltjes over in een andere fase, zonder te smelten. Dan vindt het echte sinteren plaats en ontstaat de dichtheid. Zet je deze stap onder beschermgas (bijvoorbeeld argon, stikstof of maximaal 3% waterstof, afhankelijk van het metaal) dan voorkom je oxidatie van het werkstuk. Met deze aanpak kun je volgens het Franse concern een dichtheid bereiken van 90 tot 95%. Voor tal van toepassingen is dat voldoende. Je moet echter blijven oppassen voor het ontstaan van microscheuren en vervorming, alhoewel het risico met een goed temperatuursprofiel tijdens debinding en sinteren beheersbaar blijft.
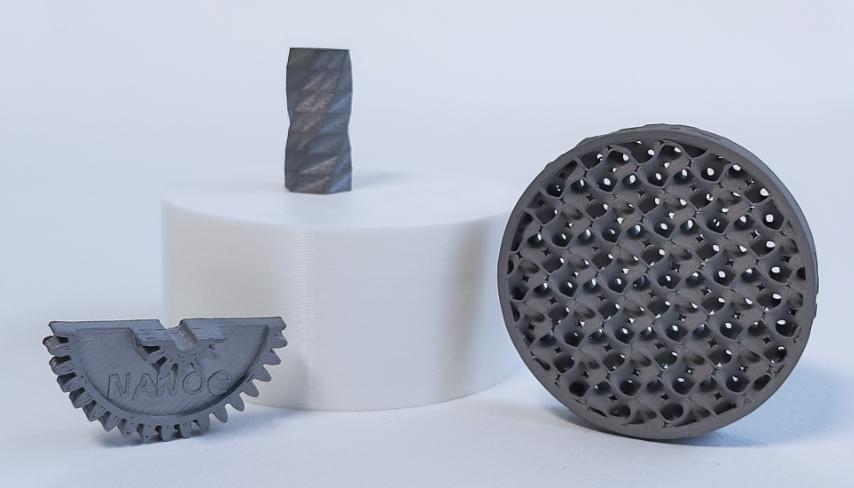
Moeilijker dan PLA
Guillaume de Calan waarschuwde tijdens het webinar dat FFF metaalprinten méér kennis en ervaring vereist dan 3D printen met PLA. Desalniettemin liggen er kansen voor bedrijven die het hele proces in huis willen doen om snel over 3D geprinte metalen onderdelen te beschikken, zonder dat ze direct fors moeten investeren.
COMPLETE OPLOSSING
De ontbrekende schakel in het FFF metaalprinten is een compleet systeem, zo heeft Nanoe tot nog toe ervaren. Hoewel je het metaalfilament op veel industriële FFF printers kunt verwerken en de standaard industriële sinterovens geschikt zijn, merkt hij dat de drempel nog steeds hoog is om in te stappen. Nanoe biedt daarom een complete oplossing aan: FFF printer met debindingunit en sinteroven die tot een temperatuur van 1550 graden C en een effectieve ruimte van 10 bij 20 cm. Daarmee wil het materiaalbedrijf zich beslist niet op het terrein van de printerfabrikanten begeven. “Maar hoe meer mensen deze techniek gaan gebruiken, des te groter kan de markt worden. Dat maakt op termijn FFF metaalprinten mainstream. En dat is ons doel.”