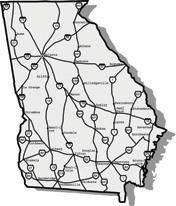
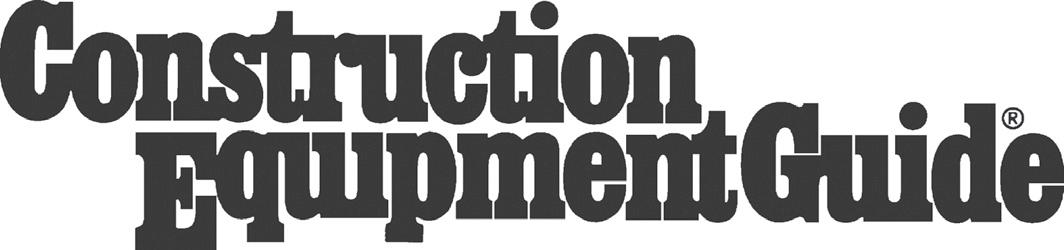
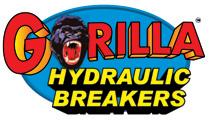
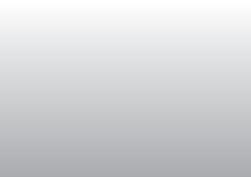
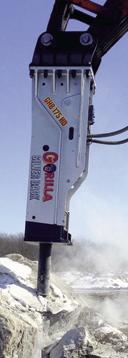
Fortune-Johnson General Contractors began construction of the $53 million RENDER Covington apartment complex in 2022 in the city of Covington for Crescent Communities, which converted a 20-acre green field into a community consisting of seven three-story garden-style apartment buildings with 315 units in total.
The project, located on the east side of metro Atlanta and designed by Dwell Design Studio, was delivered on March 1. The complex also includes a 7,000-sq.-ft. standalone clubhouse/amenity building in the center, with 10 free standing garage buildings. The surface parking lot (502 spots) is asphalt over soil cement base.
Despite some challenges, the construction process pushed forward and made solid progress.
“We faced the typical issues the whole industry experienced in 2022 and 2023 related to the supply and cost uncertainty,” said Jeffrey J. Carroll, Fortune-Johnson’s vice president of construction. “Additionally, the city was still figuring out its processes governing building permits in relation to site work completion. These procedures caused a bit of confusion right before the project started but worked out well for all parties in the end. The project was on or ahead of schedule.”
Rock in the soil was an issue.
see COVINGTON page 6
The second new nuclear unit at Plant Vogtle has entered commercial service, Georgia Power announced April 29, marking the end of the 15-year expansion of the nuclear power facility near Augusta, a project beset by years of delays and cost overruns.
The Vogtle units are the first new commercial reactors built from scratch in the United States in more than three decades, the Atlanta Journal-Constitution noted. With the second unit now online, known as Unit 4, the two reactors combined will produce enough electricity to power 1 million homes, without adding heattrapping carbon pollution to the atmosphere.
The first one, Unit 3, has been in service since last July, joining the original two Vogtle reactors, which
have been producing electricity since the late 1980s.
The addition of the two new units makes Plant Vogtle the country’s largest generator of carbon-free electricity, according to Georgia Power.
The latest Vogtle units were dogged by various problems, and ultimately reached completion roughly seven years later than initially forecast. Their total price tag also blew past the original cost estimate of $14 billion to around $35 billion. Most of Georgia Power’s portion of those costs will continue to come out of the pockets of its customers.
In a statement, Georgia Power president and CEO Kim Greene praised the new unit’s co-owners and reg-
see VOGTLE page 4
A busy stretch of Georgia Highway 42/North Druid Hills Road in DeKalb County has shut down for the next three months, the state’s Department of Transportation (GDOT) announced during the last full week of April.
The state agency began work April 26 to replace an old bridge on the highway between Interstate 85 and Ga. 13/Buford Highway, sending drivers on a 5-mi. detour.
WSB-TV got a look at the bridge in the Atlanta suburb of Brookhaven as crews worked on the final preparations. Over the next 90 days, they will tear down and replace the bridge over North Peachtree Fork Creek with a wider one. The current structure has been in place for 62 years.
The businesses next to the work site — a gas station and an LUV car wash — will continue to be accessible from North Druid Hills Road, according to the TV station.
New Bridge Designed to Handle Increasing Traffic
The North Druid Hills Road bridge over the North Fork of Peachtree Creek will be replaced with a structure designed to be better equipped for moving increasing traffic levels in the area. The new structure also will be beneficial for pedestrians with wider sidewalks and ADA-compliant ramps at crosswalks.
Officials with GDOT also believe that when the road/bridge project is completed, there will be a reduction in traffic congestion and crash frequency at the interchange of I-85 and North Druid Hills Road.
To that end, GDOT’s plans for the work area include adding a displaced left turn for the westbound to southbound movement of traffic, constructing an additional bridge over I-85, adding a braided ramp from the I-85 northbound off-
ramp to an I-85 northbound access road along, with replacing the North Druid Hills Road bridge.
A displaced left-turn intersection, or DLT — formerly known as a continuous-flow intersection — is an alternative intersection that allows left turning vehicles and thru-traffic to travel simultaneously through a main roadway junction, GDOT described. Their design directs cars and trucks to first cross opposing thru-lanes at a signal-controlled intersection several hundred feet from the main intersection. Left-turning vehicles then travel on a new roadway parallel to the opposing lanes and execute the left-turn simultaneously with the thru-traffic at the primary intersection.
On April 26, the transportation department’s contractors closed the North Druid Hills Road bridge to safely expedite
the bridge reconstruction work. During the effort, a signed 5-mi. detour route is in place, and motorists will still have direct access from the I-85 interchange, via Exit 89, and properties adjacent to the bridge work zone during the project’s timeline.
The bridge replacement is part of the larger I-85 at Ga. 42/North Druid Hills Road interchange upgrades now under way.
Despite the expected benefits from the GDOT road project, many area drivers expressed their unhappiness about the project to WSB-TV
“I know how much traffic comes through that corridor, [but closing it] for three months? That’s terrible for commuters,” said Josiah Oakley. “It’s terrible for people trying to get into the city and get into Buckhead from here.”
But a GDOT spokesperson explained that shutting the road down for three months is the most efficient way to get the job done.
“Ninety days of a full closure allows us to do it quickly,” said the state agency’s Natalie Dale. “That allows us to get it complete [and] get out of the road so that traffic can get moving in that area again.”
The construction will not allow Aisha Johnson to drive straight through on her way to work, she told WSB-TV. Instead, she will have to follow the detour along Ga. 13/Buford Highway, which she worries will become clogged with traffic.
“I guess we’ll make it some kind of way,” Johnson remarked. “I’m just glad I know the back roads. And other people need to learn the back roads too.”
ulators at the Georgia Public Service Commission (PSC), who greenlit the project and repeatedly voted to continue construction, despite skyrocketing costs.
Georgia Power owns the largest share in the Vogtle expansion with 45.7 percent, followed by Oglethorpe Power, the Municipal Electric Authority of Georgia and Dalton Utilities.
“The new Vogtle units are a key piece of our strategy to meet the energy needs of our customers not only tomorrow, but 20 years from now,” Greene said.
In a statement, Mike Smith, Oglethorpe Power’s president and CEO, called the project’s completion the “culmination of a remarkable journey.” The utility company and its partners serve 38 not-for-profit electric membership corporations that provide electricity to more than 4.4 million people in the Peach State.
“We celebrate not only the completion of this important emission-free resource, but also the historic achievement it represents as the first advanced commercial nuclear project in the nation in more than three decades,” Smith added.
Even before the first new unit produced any electricity, the average Georgia Power residential customer had already paid about $1,000 over the last decade-plus in monthly bill fees to cover the project’s financing, the Atlanta newspaper reported.
Late last year, state regulators voted to approve a deal to pass $7.56 billion of Vogtle’s construction costs on to the company’s ratepayers. Georgia Power and shareholders of its parent, Southern Company, will absorb the remaining $2.63 billion of the project’s construction costs.
As a result, the average residential customer using 1,000 kilowatt-hours of electricity a month will see a cumulative increase of $14.38 in their monthly bills. Part of that increase — about $5.42 — kicked in last year after Unit 3 entered service.
Now that Unit 4 is online, the rest — about $9 — will show up on customer bills in May.
With the new units completed, the expanded Vogtle plant will support 800 permanent jobs. At its peak, the reactors’ construction brought 9,000 workers to rural Waynesboro, 30 mi. south of Augusta.
Georgia Power, the federal government, and the nuclear industry had hoped that the completion of the Vogtle reactors and their newly trained workforce would provide momentum for nuclear power in other parts
of the United States.
So far, though, that has not happened.
Currently, there are no other commercial nuclear plants under construction in the United States, or any signed orders to build new ones.
Still, as energy-hungry data centers proliferate and electricity demands grow, many experts consider nuclear expansion a vital tool for fighting climate change and building American energy independence.
In an interview with the JournalConstitution April 29, Greene left the door open to the possibility that Georgia Power could seek to add even more nuclear power to its own system in the future. The company will submit its next long-range energy plan to the PSC early next year, and she said the utility is still weighing its options.
“We are going to consider all the options and look at the best long-term needs for our state and our customers,” Greene added.
Your choice of a sealed or pressurized cab is equipped with system, adjustable wrist rests and a suspension seat to help comfortably all day long. Controls are easy to use, and the i monitor provides customizable machine operator preferenc information.
Maneuvering on the jobsite is even easier with the Cat Stick traditional travel controls with levers and pedal to joystick c button.
an improved air conditioning p keep you working ntuitive Next Generation es and easy to read machine
Increased lifting, swinging and travel and multi-functional pe k Steer option. Switch from controls with a push of a erformance help you get the
are just a few of the safety feature
Maintenance is quick and easy on access at ground level with group
with a variable displacement pum es built into the
the Cat 306 CR. Routine check poi ped service points and robust servic &
mp, the Cat 306 CR was designed to ints are easy to ce panels. reduce operating
blade, angle blade or Extra Tool C
Contact our dealership today t excavator in the market. arrier (XTC). to learn more about the newest 6-t
excavation/removal took approximately 3.5 months.”
“There were some slope design issues related to the site interacting with GDOT, but they were worked through per the normal process of contracting,” said Carroll, who noted that the work was based on day shifts.
Fortune-Johnson, a construction management firm, does not self-perform any of the work. The subcontractors and vendors ensured that their heavy equipment was transported to the site where it was rapidly put to work.
Civil Site Services (CSSI), the grading subcontractor, hired a firm to cut down the trees on the site, which were primarily pine trees. The work was completed seven months prior to the construction of the buildings.
“The trunks were taken out with a root rake before topsoil was removed,” said Carroll. “The wood was immediately removed from the site.”
With trees removed, the earthwork and site prep could begin. CSSI, a grading and utility pipeline company, participates in many projects across Georgia.
“The equipment we use focuses on moving, excavating, hauling and installing storm, water and sewer pipelines,” said Philip Pond, CSSI’s vice president/COO. “At any given time on the project, we had 20 to 25 pieces of equipment onsite during our phase of the operation. We are always the first subcontractor on the site, due to the need to clear the land of trees, etc, and grade the site to obtain the proper elevations for the various building pads.”
On this project, the firm used Cat 336 and Volvo 460 excavators, Volvo articulated dump trucks, Cat D4 dozers, Cat 815 compactors and Cat IT28 wheel loaders.
“All of our machinery is equipped with GPS systems,” said Pond. “It is imperative for meeting the required finish grade elevations for building pads and roadways, and parking lots. It saves time, eliminates human error, and confirms the actual results.”
The removal of rock was far from easy.
“Once the rock was identified,” said Pond, “confirmed depths that needed to be removed by blasting, then excavated and removed by dump trucks, multiple loads were an everyday process, Some days as many as 50 loads per-day. Between the unsuitable soils and rock removal, there were approximately 3,124 loads removed from the site. We stripped approximately 9,250 cubic yards of topsoil and moved approximately 84,500 cubic yards of dirt within the site in order to provide a balanced site to meet the required elevations. The majority of the dirt moving process and rock
“A significant amount of blast rock was known and included as an allowance with the owner," said Carroll. “This job was a net export site and CSSI found a nearby site to accept the material.”
CSSI installed approximately 3,724 ft. of storm piping, 2,902 ft. of sanitary sewer piping and 6,320 ft. of domestic and fire line water. Most of the installation was completed by using the Cat 336 excavator.
“No underground plumbing or slab work could be started prior to all utilities, curbs and base/binder [or in this case, soil cement] being completed,” said Carroll, who pointed out that shallow turn-down footings were critical for the foundations of the structures.
Once the earthwork and site prep was completed, crews poured the foundations for the buildings. The concrete (3000 psi) was poured via cranes linked to pumps. The SOG buildings had shallow foundations.
“Slab prep by plumber and electricians took about five days and prep and pouring the slabs took about another week for each building,” said Carroll. “This was repeated for all buildings. Each building was divided into two pours. The club house and garages were single pours.”
The apartment buildings and other structures are wood framed.
“It took about five weeks per-building to frame on average,” said Carroll.
Once framed, electrical, plumbing, HVAC and other systems were installed.
“We were never framing more than two buildings at a time,” said Carroll. “Everything progressed in one-week pods, so that all trades just chased each other week after week through the buildings.”
The roads and surface parking areas are based on asphalt paving: soil cement, 2-in. binder and 1-in. topping. The roads and surface parking were installed prior to the construction of the buildings. The roads could be driven on one day after they were paved.
Fortune-Johnson’s management team had an excellent team dynamic.
“The efforts of the crews exceeded expectations in almost all cases,” said Carroll. Project
provide residents with convenient access to area amenities and employment with more approachable rents compared to those in high-density urban markets.
“Our expansion into new suburban markets with RENDER was fueled by the continued growing demand for quality multifamily housing in areas outside of the urban core,” said Jay Curran, president of Multifamily at Crescent Communities. “We knew we could bring our resident-oriented approach and design expertise into these markets and offer renters thoughtfully crafted communities rich in character, but at a more approachable price point. The RENDER product will allow us to scale the offering and bring more homes to the market faster, while keeping the renters’ desire for beautiful homes with amenities they desire at the forefront.”
The Covington project, 40 mi. east of downtown Atlanta, is Crescent’s first RENDER community. It provides access to the popular Eastside Trail, a 2.5-mi. multi-use greenway trail that runs from Chimney Park to Eastside High School. The main street within RENDER Covington, Delk Drive, honors Cheryl Delk, one of the largest proponents and driving forces behind the Eastside Trail and a beloved resident of Covington.
Crescent Communities has plans to expand its footprint in the greater Atlanta area. In addition to the construction of NOVEL Midtown and NOVEL West Midtown, RENDER Covington will be Crescent’s eighth multifamily family investment in the Atlanta market.
“More broadly, Crescent Communities continues to experience significant growth with $6 billion of multifamily and commercial investments and developments currently under construction, operations and planning including 13,000 units of multifamily, 260,000 square feet of complementary retail and 8.0 million square feet of office, industrial and life-sciences,” stated a company press release. “With a focus on sustainable development practices, the organization pursues USGBC LEED certification or commercial spaces and NGBS certification for multifamily residences. Crescent Communities has also recently launched its single-family build-to-rent product with plans to seek opportunities to serve suburban markets in the Atlanta metropolitan area.” CEG
(All photos courtesy of Fortune-Johnson General Contractors.)