11 minute read
CLEANING
Next Article
CATTLE COMPATIBLE: As cleaning products evolve, animal nutritionists suggest ethanol plants maintain contact with their feed markets, updating them on any content changes.
CIP:
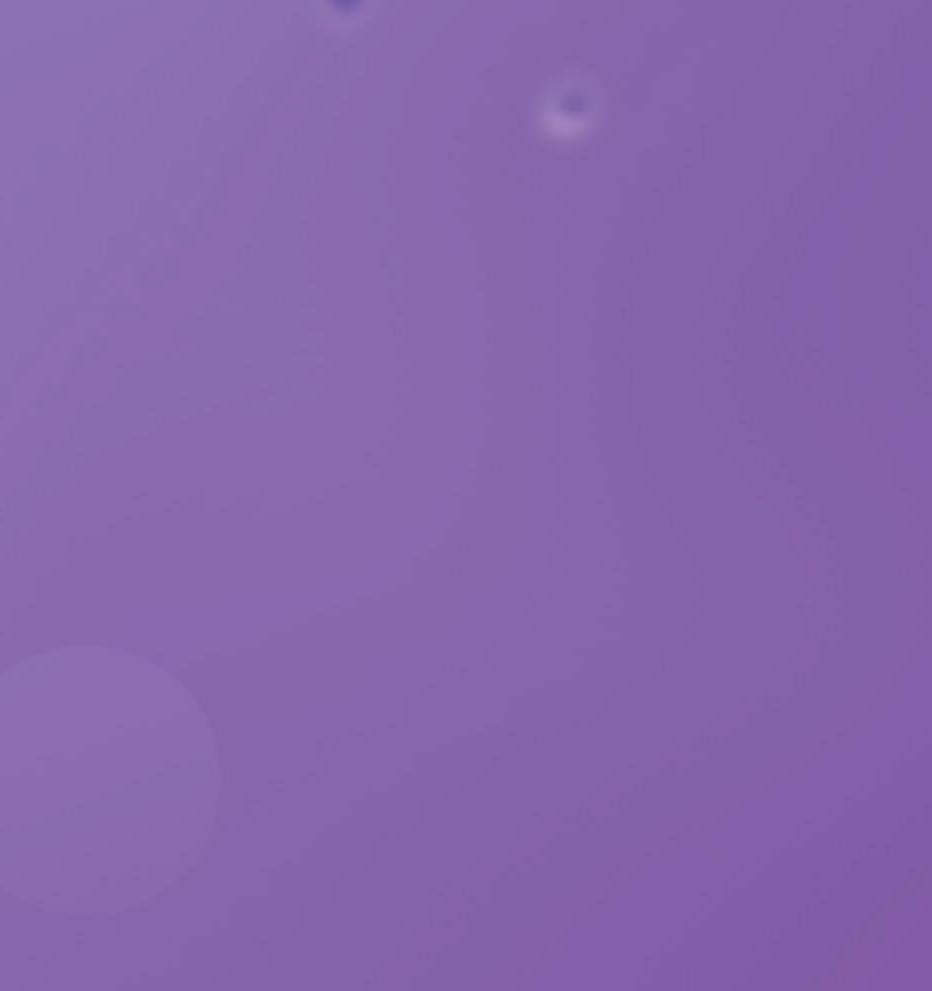
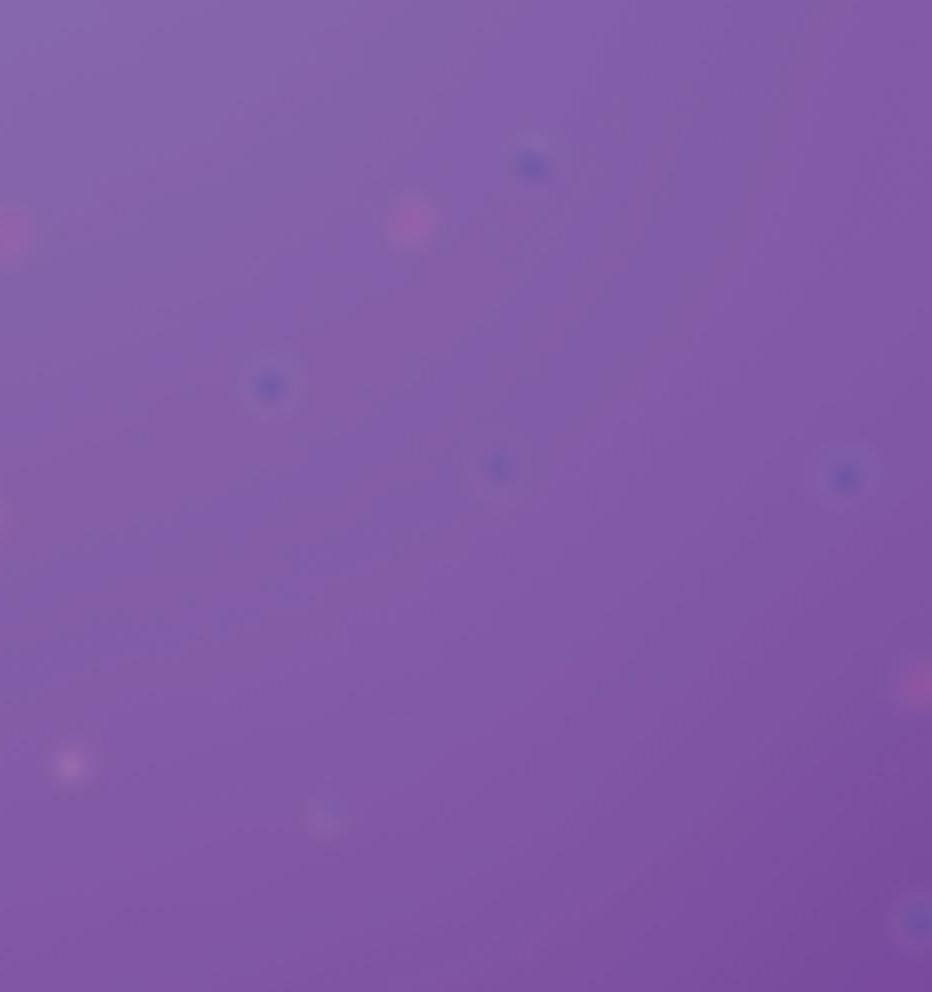
COPRODUCTS AND COMPATIBILITY
New product rollouts in clean-inplace processes ease burdens on plants, but proper care to analyze impacts downstream is crucial.
By Matt Thompson
As more ethanol producers seek to remove caustic soda from their CIP processes, they’re forced to consider all aspects of their plants, from the composition of piping to potential impacts on DDGs and other coproducts.
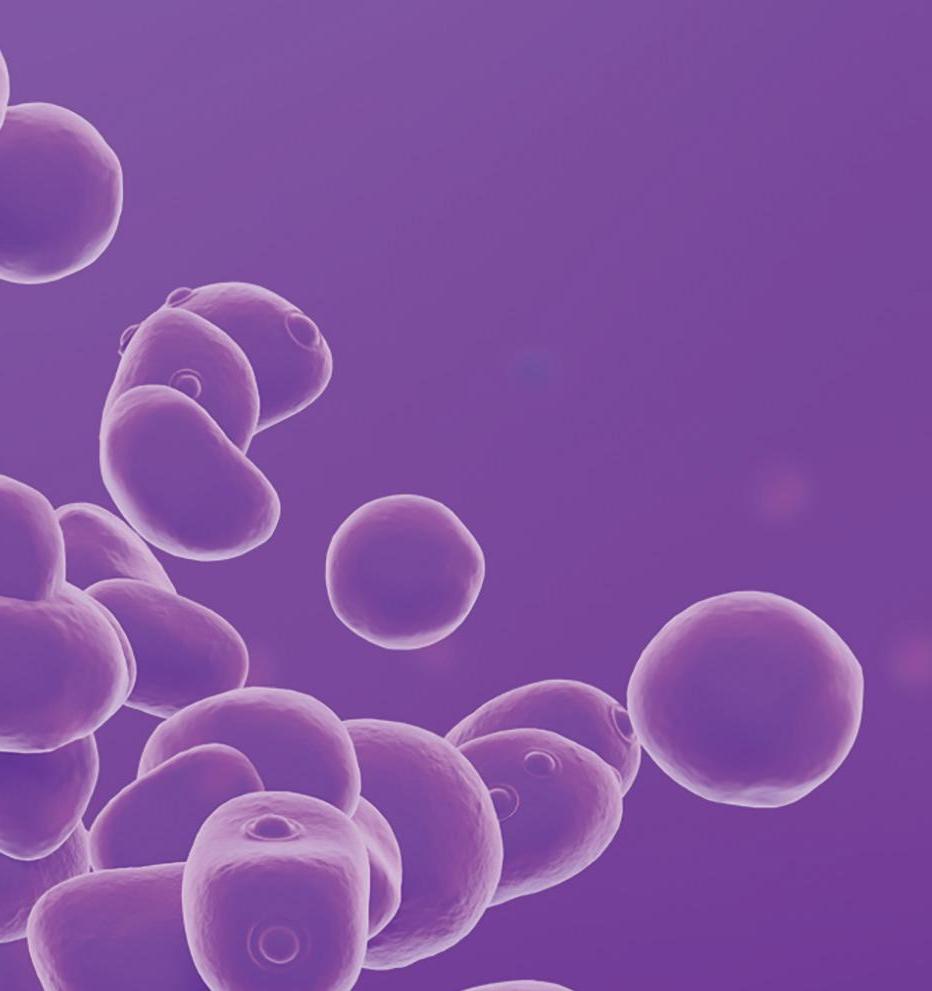
Brian McCluskey, biofuels sales manager at Hydrite Chemical Co., says his company’s introduction to the ethanol industry of Hydri-Maize CRC-152— an acid cleaner that can replace caustic soda in CIP processes—was born out of a desire to help ethanol plants with their cleaning processes. “Really, it came down to just wanting to do a better job, and change up the [CIP] program,” he says.
Hydrite took a cleaning cue from the food processing side of the business, McCluskey explains. “Cleaning with an acid-based product is commonplace in the food industry. It can do a better job keeping things clean and so we just took that ideology and created a formula that can be used in ethanol and it grew from there.”
Hydri-Maize CRC-152 isn’t an untested solution for ethanol plants. Several are using it in place of caustic. And through those various trials and case studies, Hydrite discovered that CRC152 does its job almost too well. “Given the nature of the product, it does aggressively go after scale deposits,” Mc-
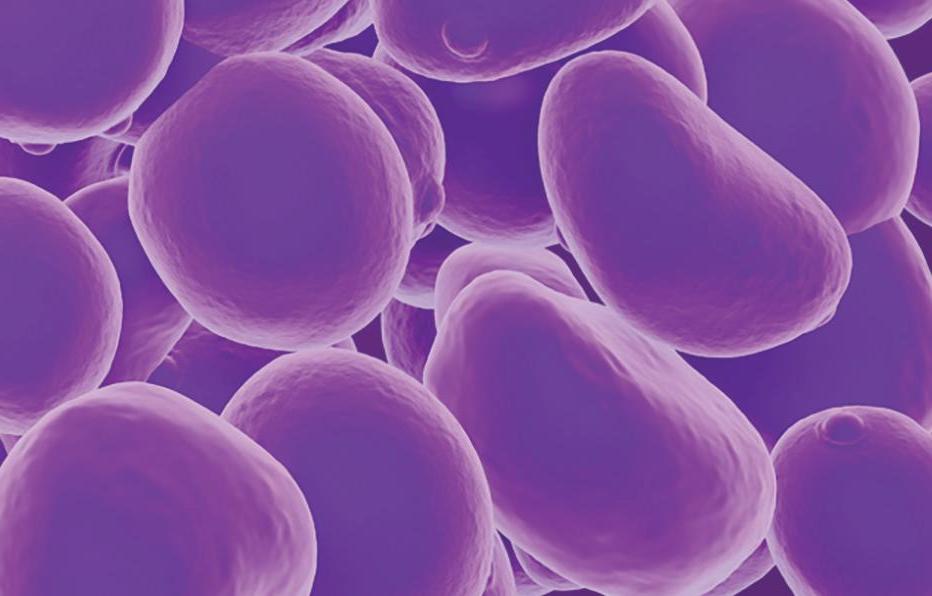
Introducing ®the SYNERXIA Gem Collection
The next advancement in high-performance yeasts to make your plant shine.
www.xcelis.com
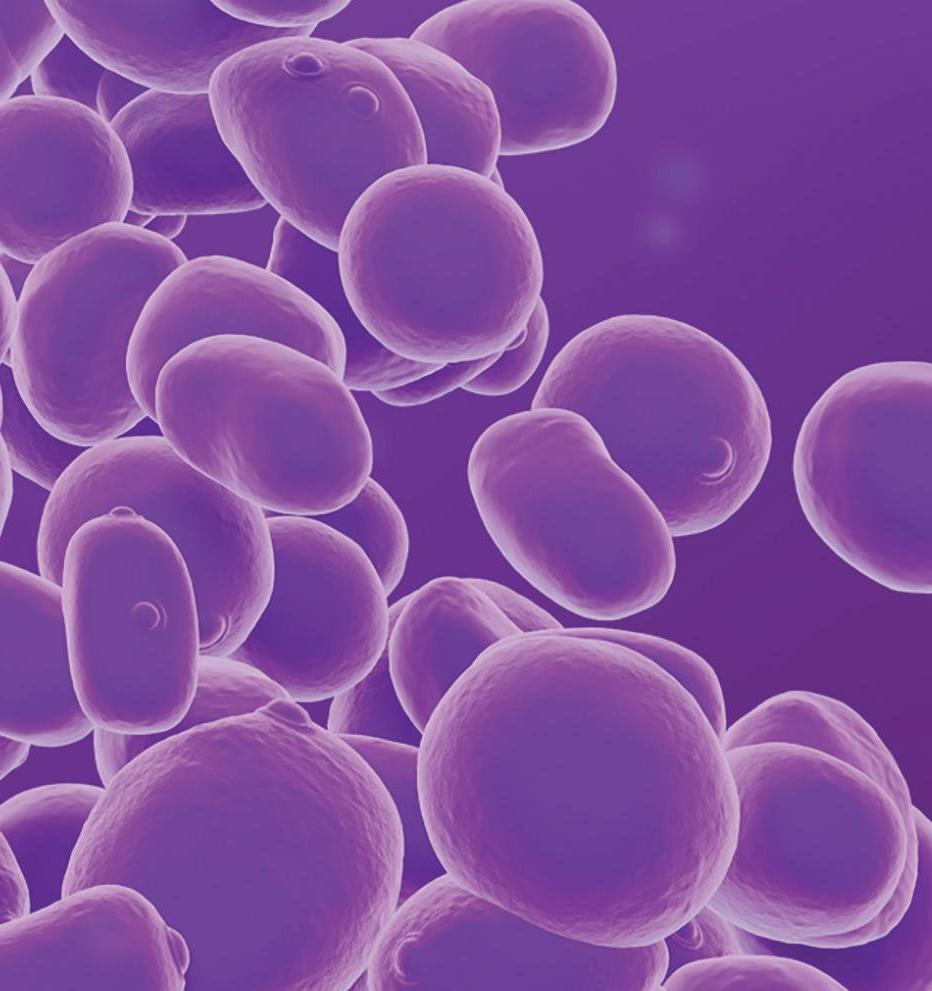
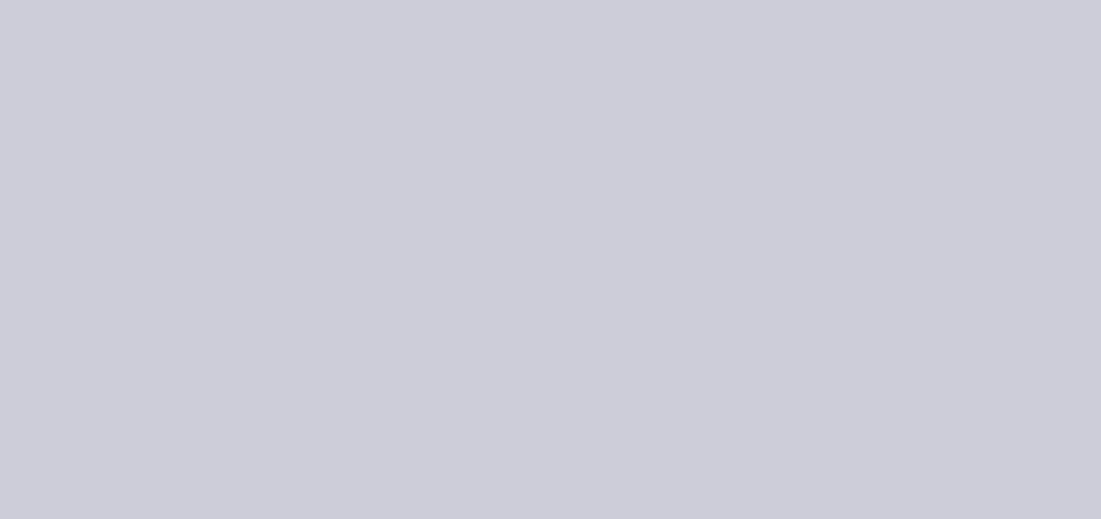
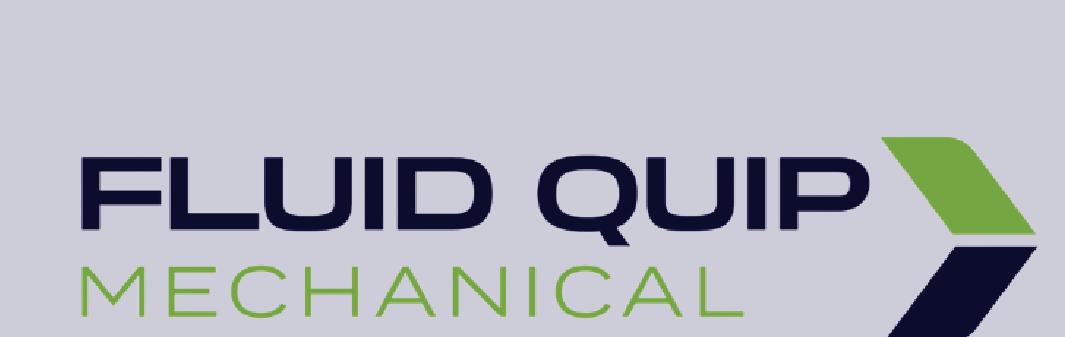




PLANT UPTIME IS IMPORTANT TO YOU, SO IT IS IMPORTANT TO US. Our full service team of experts have 20 years of ethanol plant maintenance reliability and uptime history. 24/7 support and ready access to a full inventory and all Fluid Quip equipment parts, ensures that you maintain your plant’s uptime status.
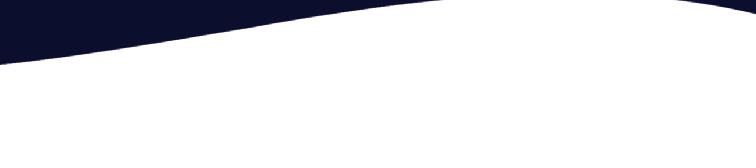
• OEM Parts Warehouse • $1 million+ on-hand inventory • Fully stocked trucks • Overnight/hot shot shipping
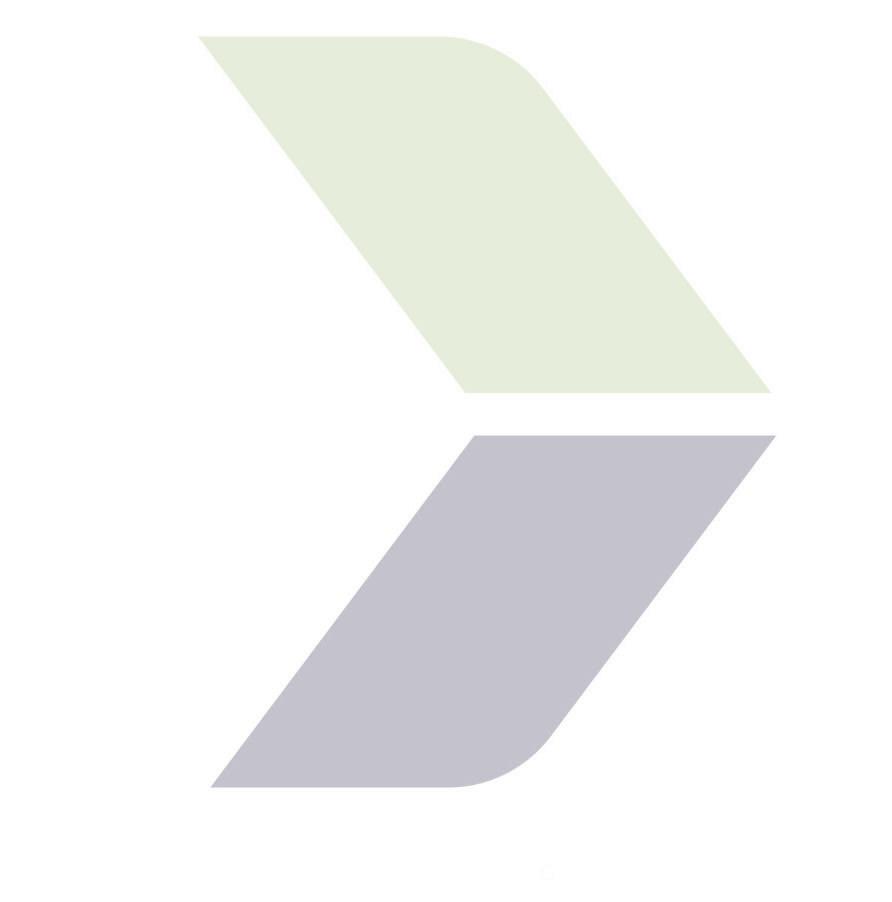
PARTS
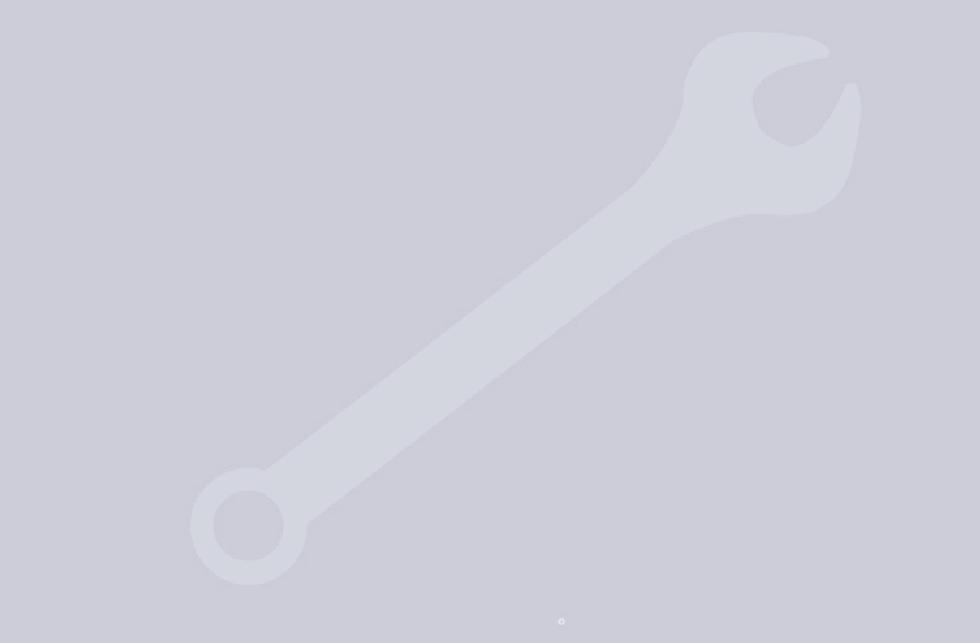
EQUIPMENT SERVICE
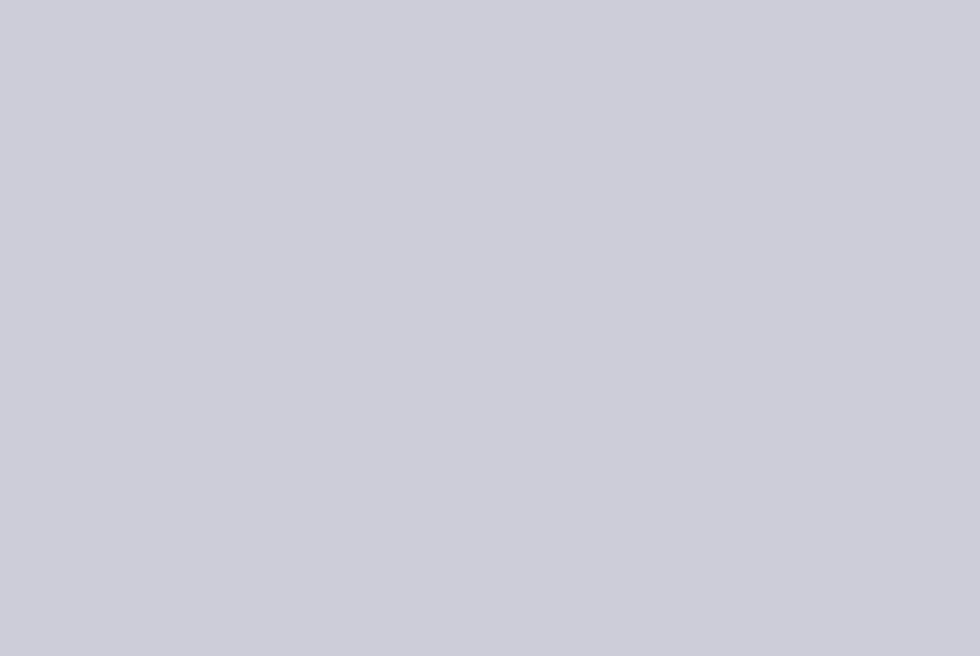
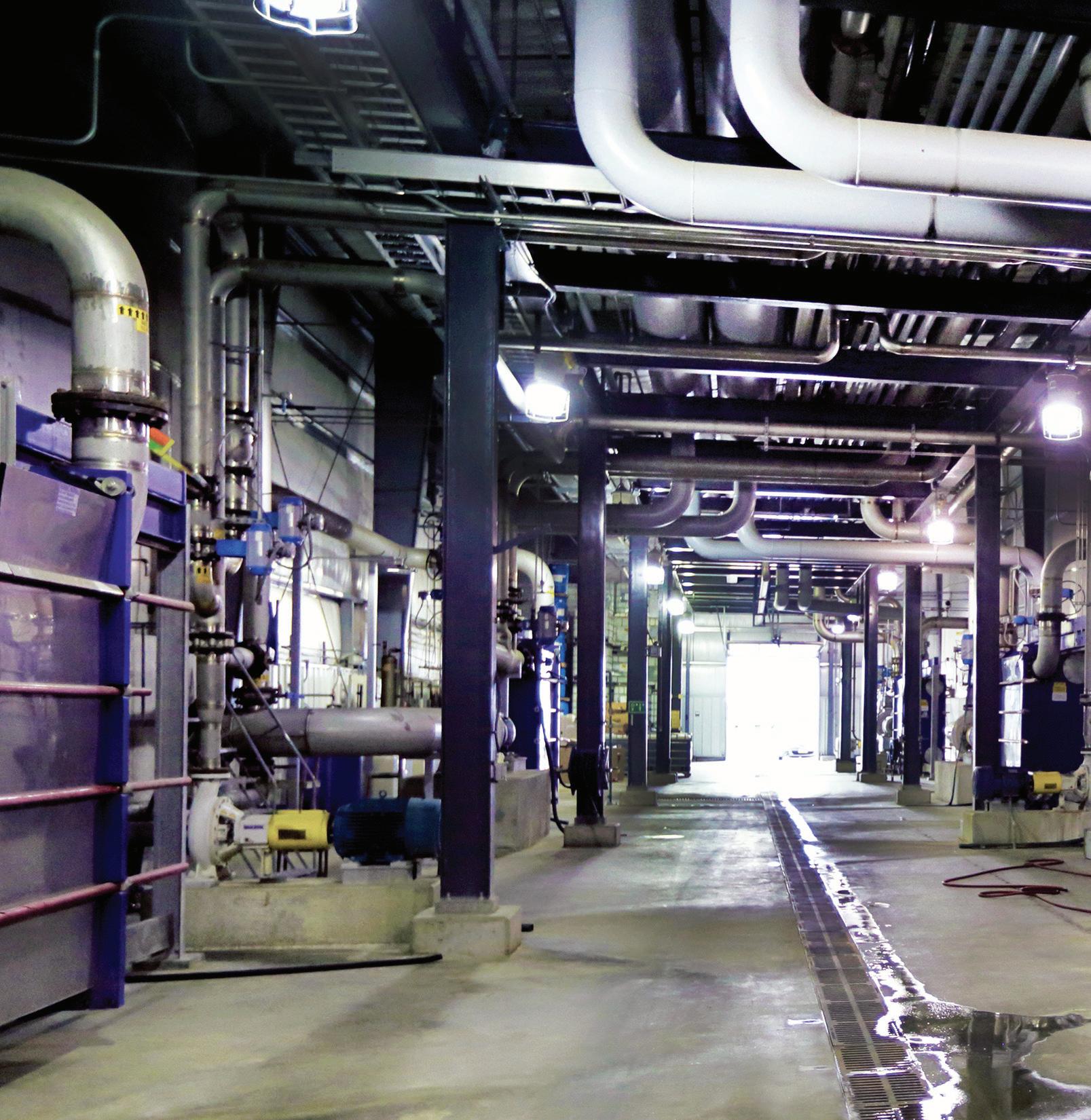
FERM FOULING: Hydrite Chemical Co. says its new CIP product initially led to some extra fouling in fermentation, but product polishing has alleviated that issue.
PHOTO: STOCK PHOTO
• Factory Trained & Certified • MSC™ Systems • SGT™ Grind Systems • FBP™ Fiber By-Pass Systems • MZSA™ Screens • Paddle Screens • Grind Mills • • Centrifuges Centrifuges
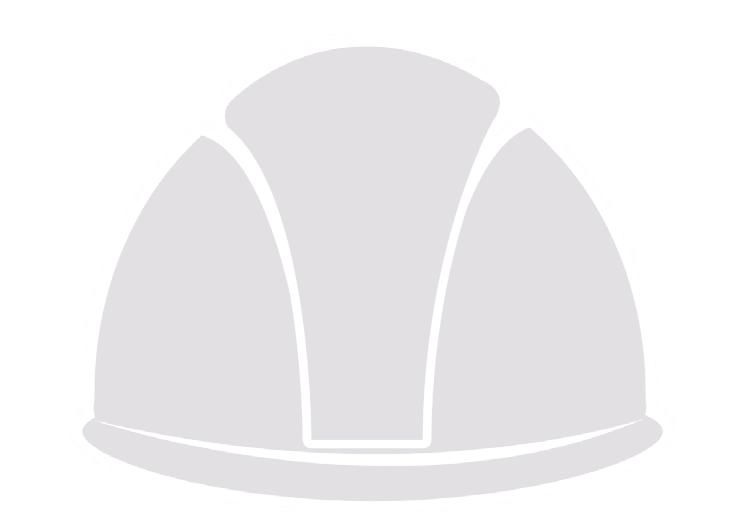
FluidQuipMechanical.com | 920-350-5823 | follow us on on Fluid Quip Mechanical is a division of Fluid Quip Technologies i .
Hydrite says lactic and acidic were reduced by at least 40%, the need for both bulk caustic and sulfuric acid were eliminated and antibiotic use was reduced by about 44%.
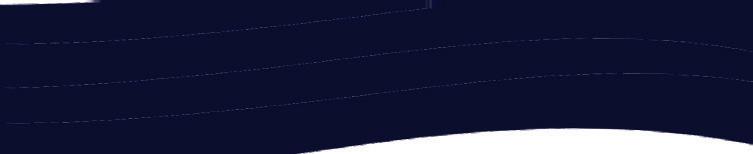
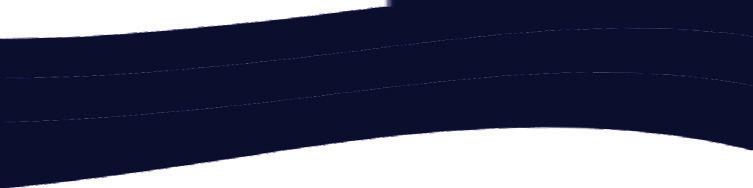
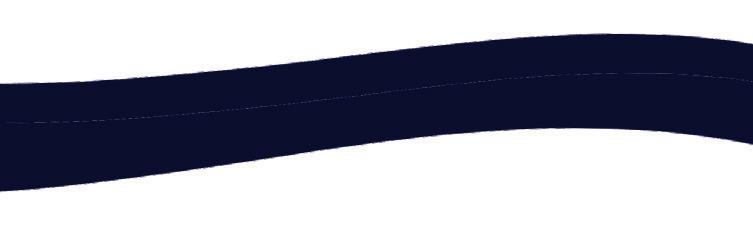
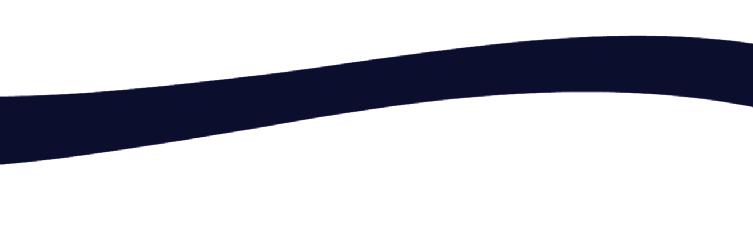

Cluskey says. “Those scale deposits, when they break free, they end up right in the fermenter, and they harbor a lot of bacteria.”
After about two weeks of trials with CRC-152, plants saw infections in their fermenters. But, McCluskey says, there is a solution. “One of the things that we’ve implemented moving forward is bringing in one of our GRAS-approved paracetic acid blends, Hydri-Maize 2759, an antimicrobial for further protection. Because now we know that we do expect that to happen in the future, so at least we can be prepared for it.”
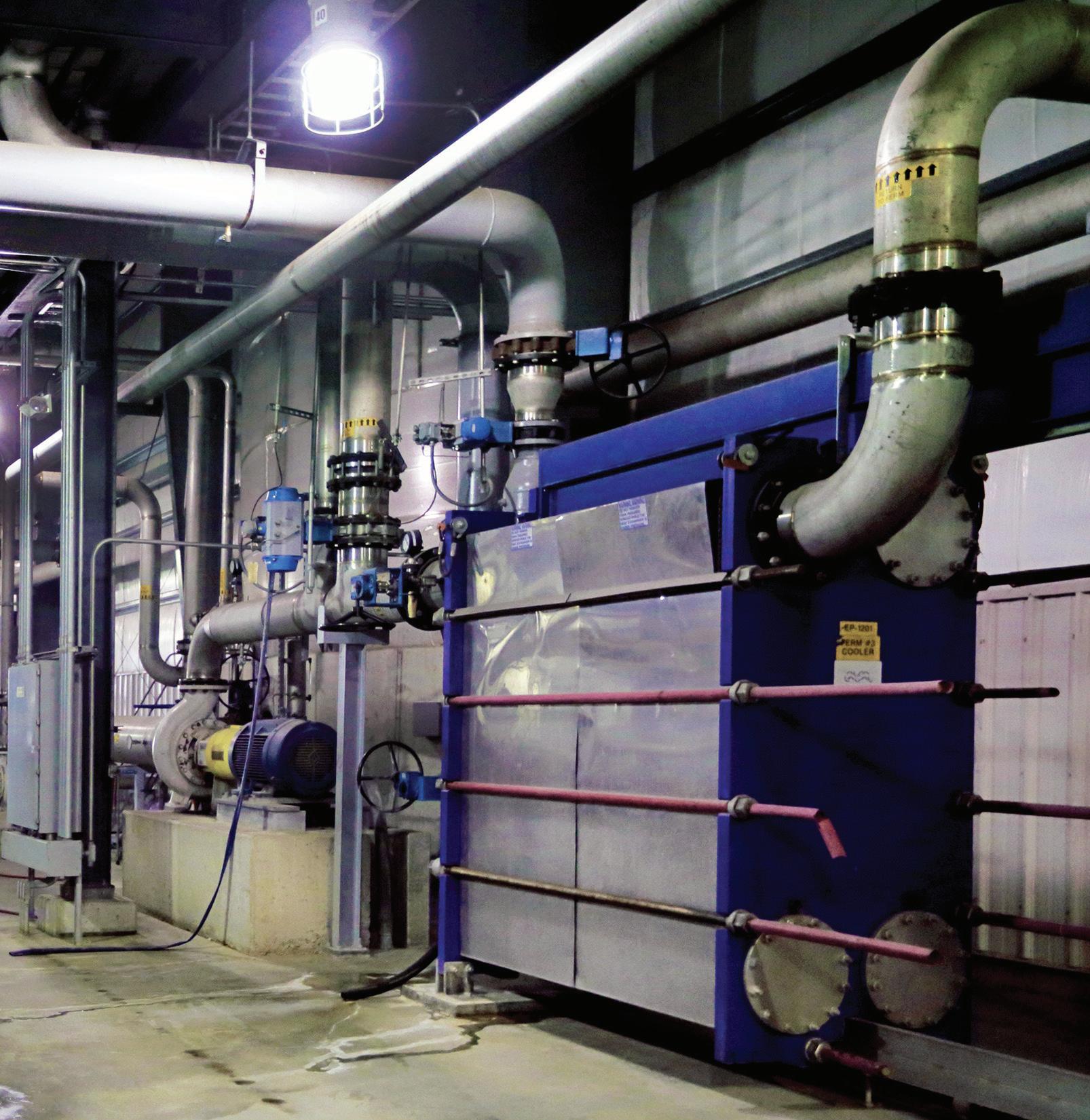
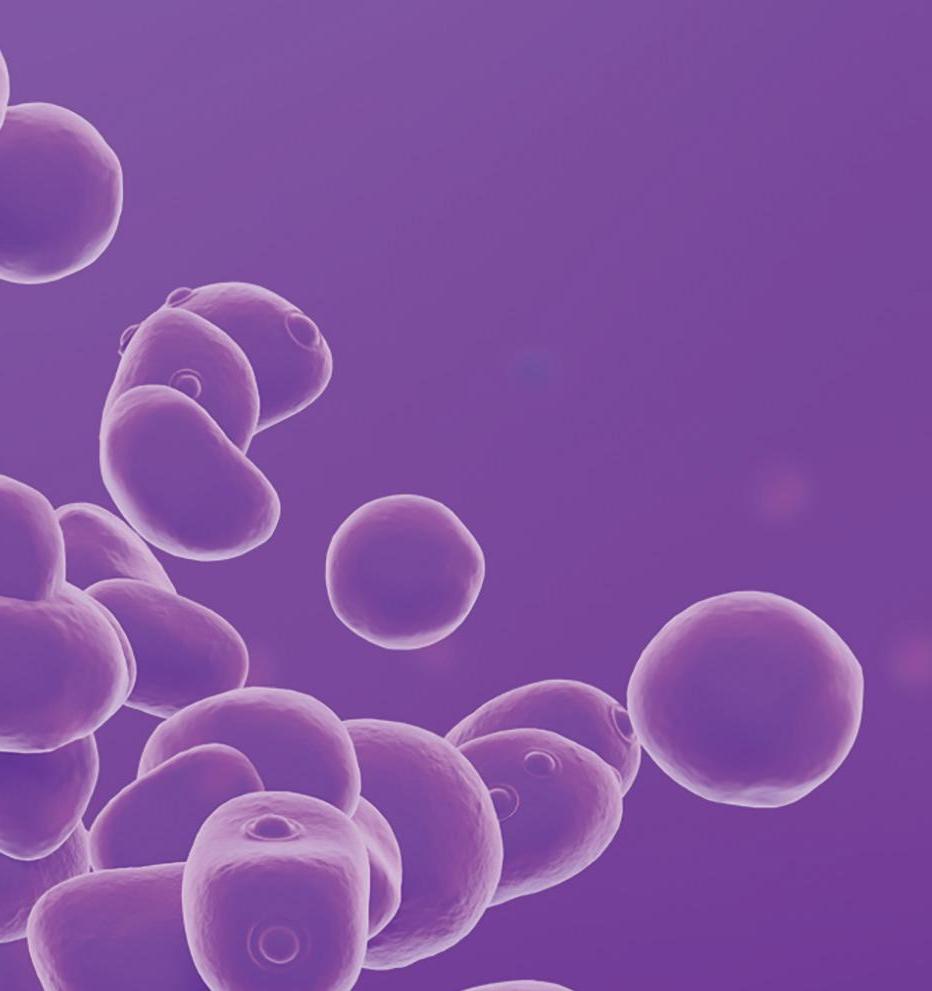
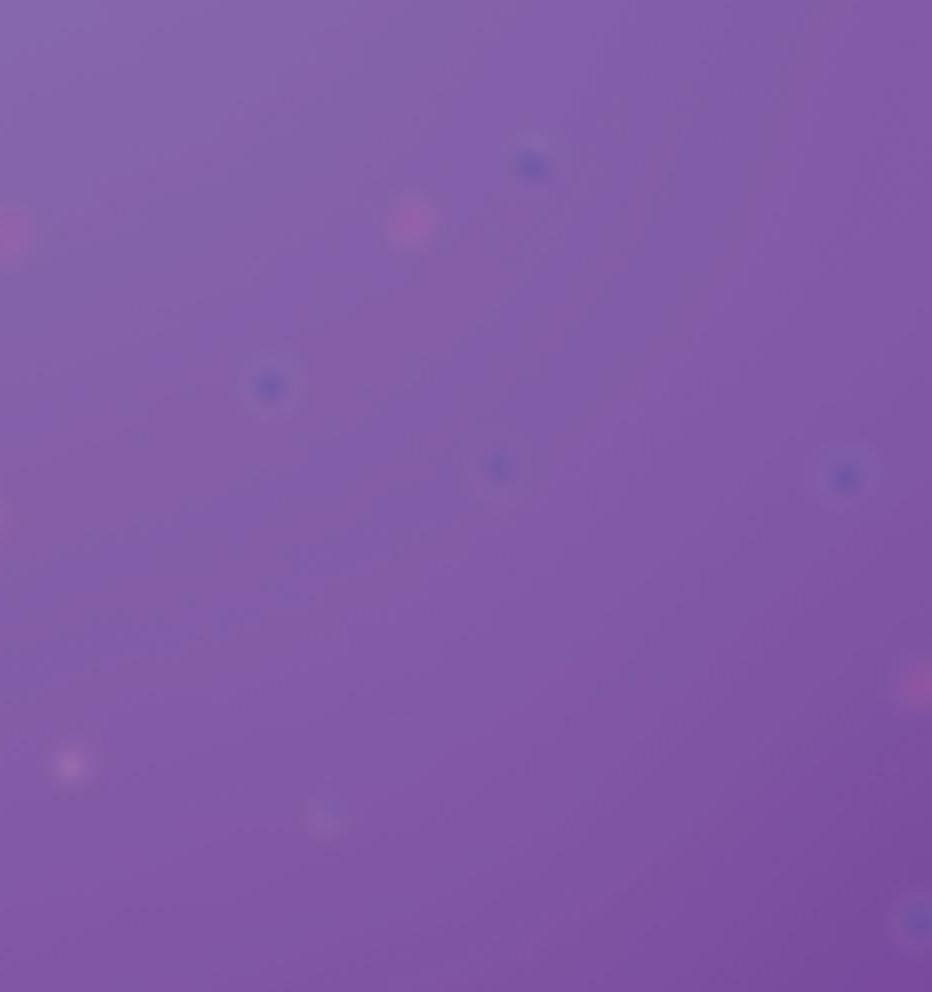
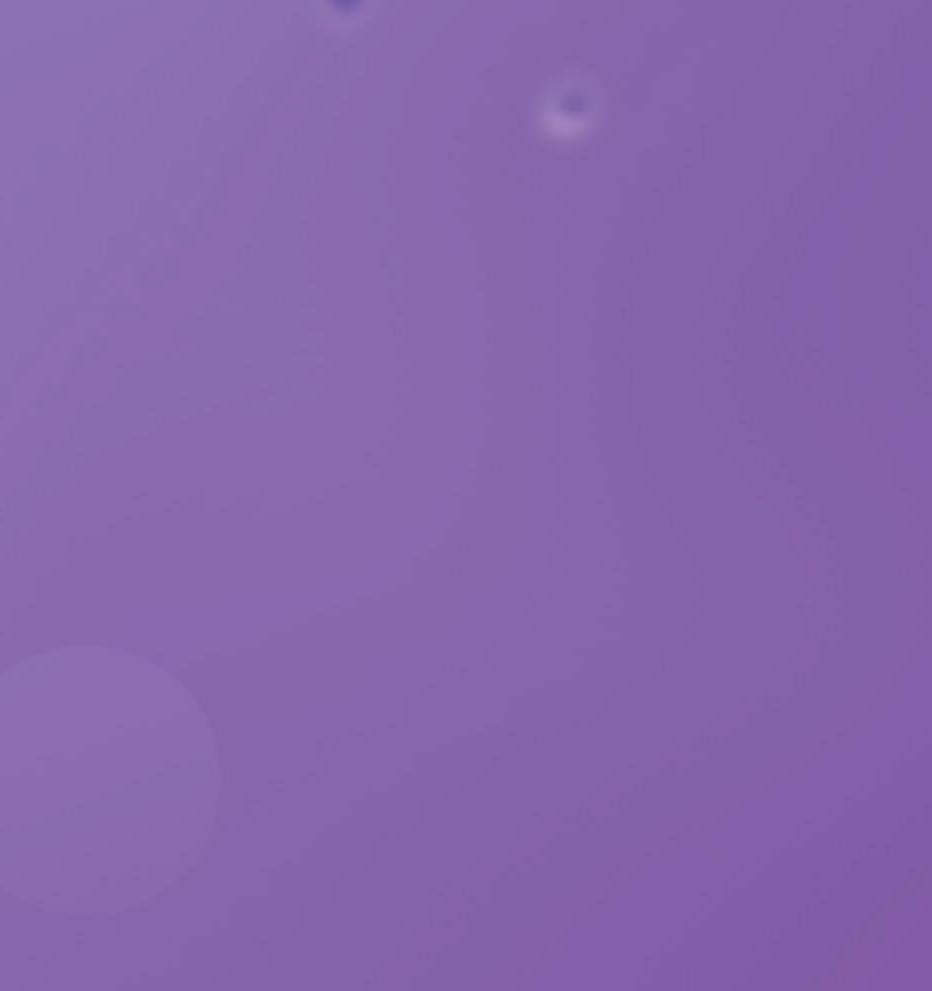
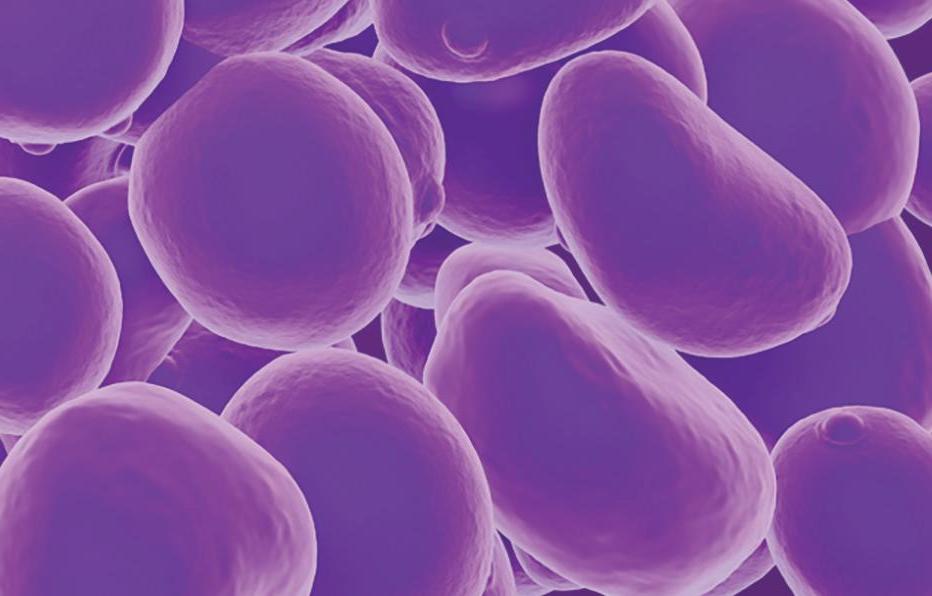
Real Results
A Nebraska ethanol plant, whose managers have asked to remain unnamed, has been using Hydri-Maize CRC-152 for about a year and a half, and confirms initial issues with fermentation. “Our lactics did jump up a little bit and that’s just because it was breaking off some of the minerals that were stuck inside our associated piping and fermenters,” says one plant official. “So we did see lactic elevate initially, and then they worked back down to a more reasonable, if not lower, baseline.”
Since then, the plant has been pleased with CRC-152’s performance and the benefits realized, the main one being the cost reduction from eliminating caustic. “CRC-152 is a reduced cost to what we would normally spend,” the plant official says. “That’s definitely the main benefit.”
A second benefit is that CRC-152 reduces the amount of flushes the plant performs. “Before, you had to do a water flush, then an acid flush, then a water flush, then a caustic flush,” he says. “This is a much simpler process.” He adds that it prevents sanitation water from going to the beer well and diluting the beer.
McCluskey says the benefits that the Nebraska plant has seen are com-
XCELIS® Yeasts SYNERXIA® SAPPHIRE
The most powerful combination of yield, robustness and enzyme expression in a yeast.
www.xcelis.com
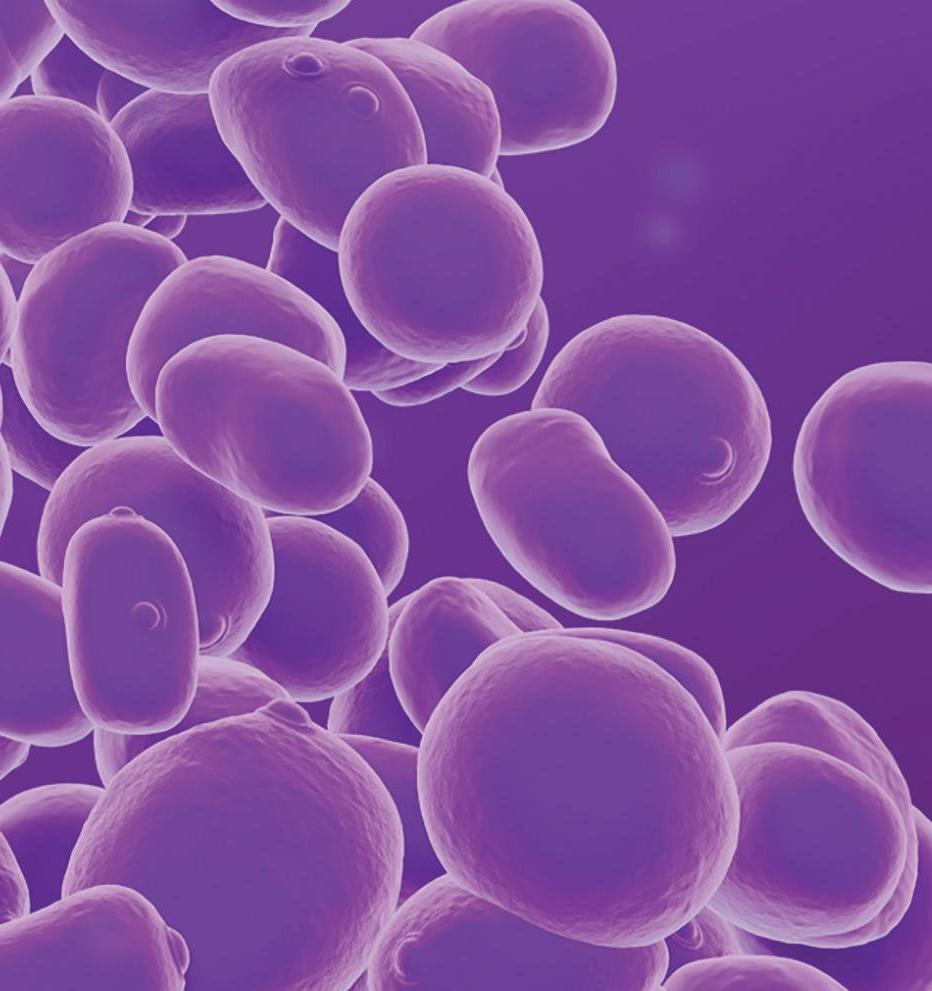
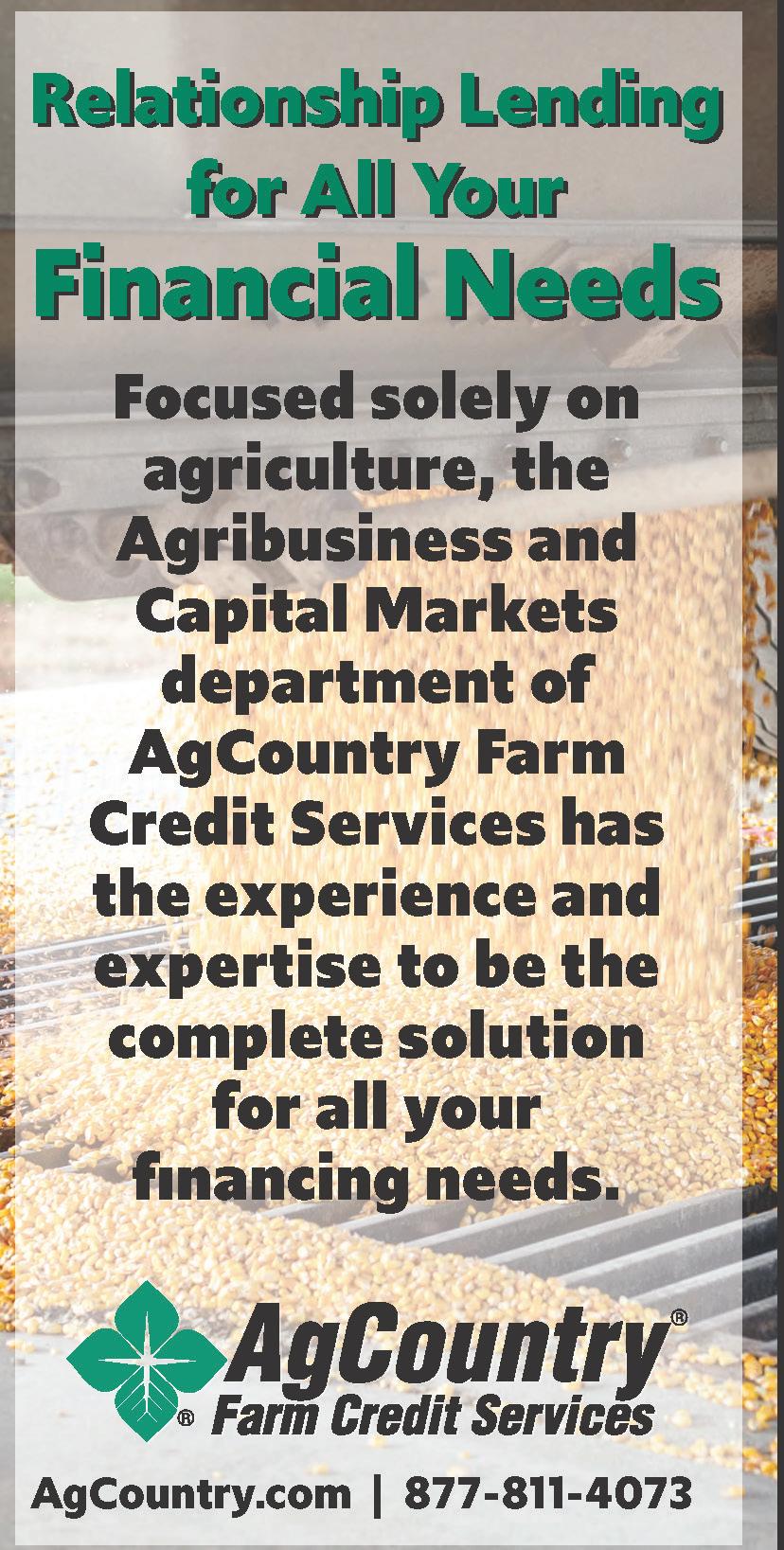
mon to the other plants using CRC152, as well. “They’re seeing cleaner ferms; they’re seeing lower organic acids; they’re saving money. The variable cost [of caustic] has virtually disappeared,” he says.
During one trial at an ethanol plant, the results of which were released during the summer of last year, Hydrite says lactic and acidic were reduced by at least 40%, the need for both bulk caustic and sulfuric acid were eliminated and antibiotic use was reduced by about 44%.
In addition, there are no negative effects to distillers grains, McCluskey says. “There’s been absolutely zero impacts, even as plants are doing coproduct generation with high-protein coproducts, there has been absolutely no issue.” The Nebraska plant also reports no changes in its DDGs.
Like other solutions that seek to rid ethanol plants of their caustic soda, Hydri-Maize CRC-152 has some limitations. Mainly, some plants aren’t able to use it. “The challenge that we’re running into with an acid-based product is a lot of the plants out there still contain a fair amount of carbon steel,” McCluskey says. “They’re interested in the technology, but they just can’t use it because of the carbon. That’s been the biggest drawback.”
But that might soon change. McCluskey says Hydrite is working on a solution for plants that haven’t yet switched to stainless steel. “A CIP program that is going to be more friendly to those customers that still have carbon steel infrastructure will be rolling out in 2021,” he says.
Downstream Impacts
Jerry Shurson, a professor in animal science at the University of Minnesota, has been researching and providing education on distillers grains for over 20 years. He says he hasn’t
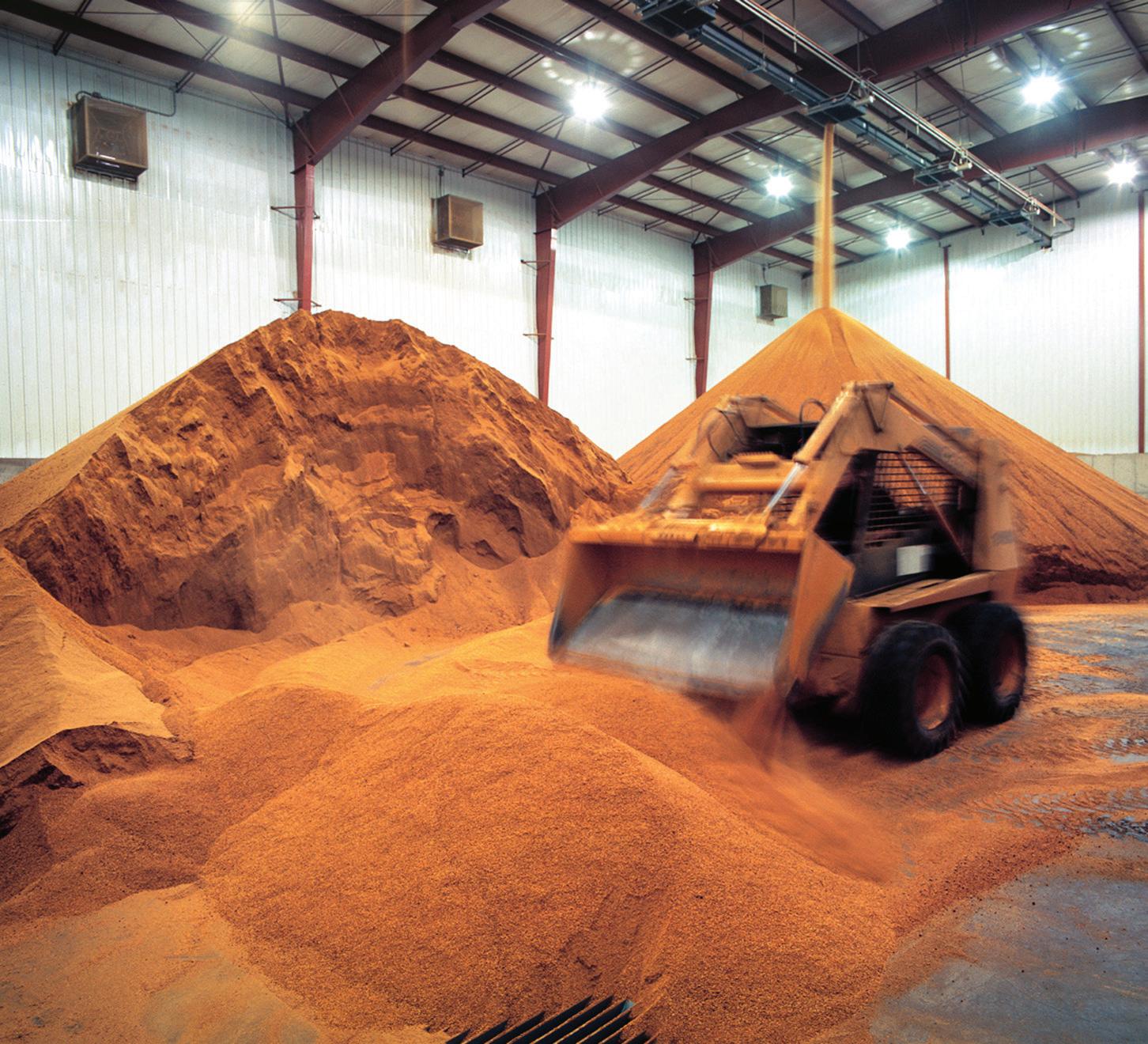
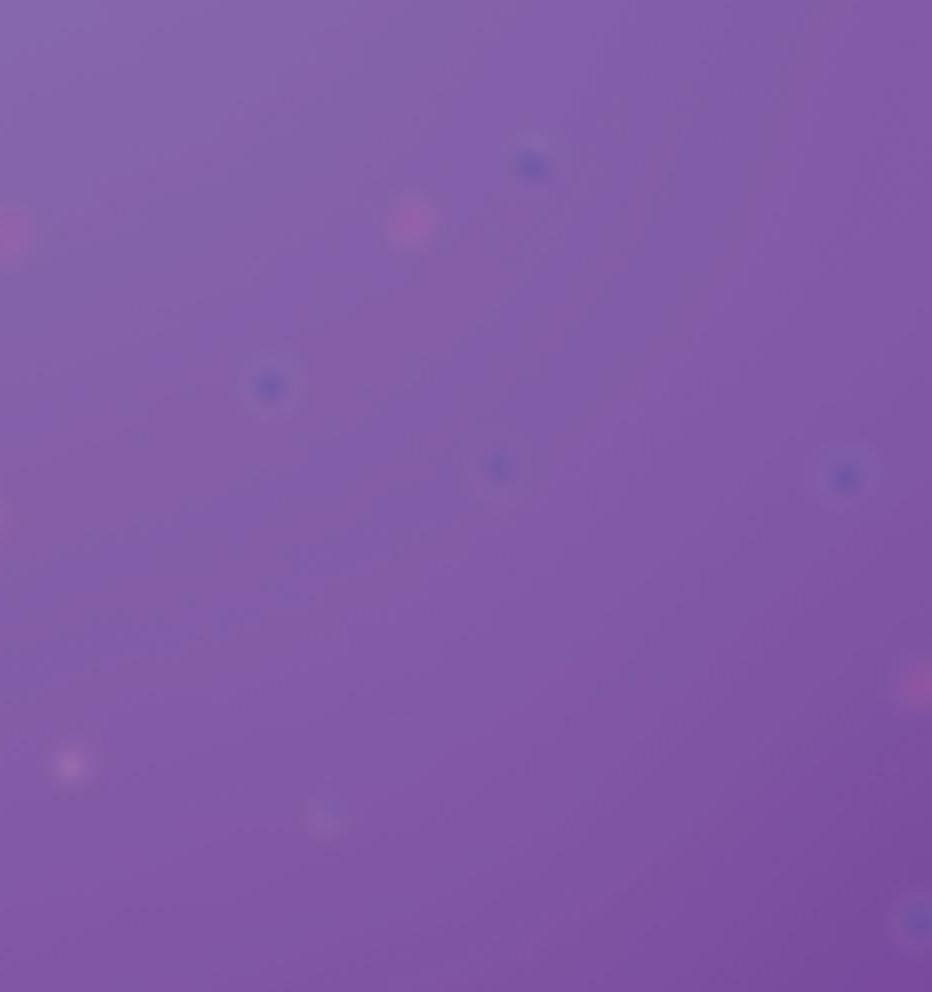
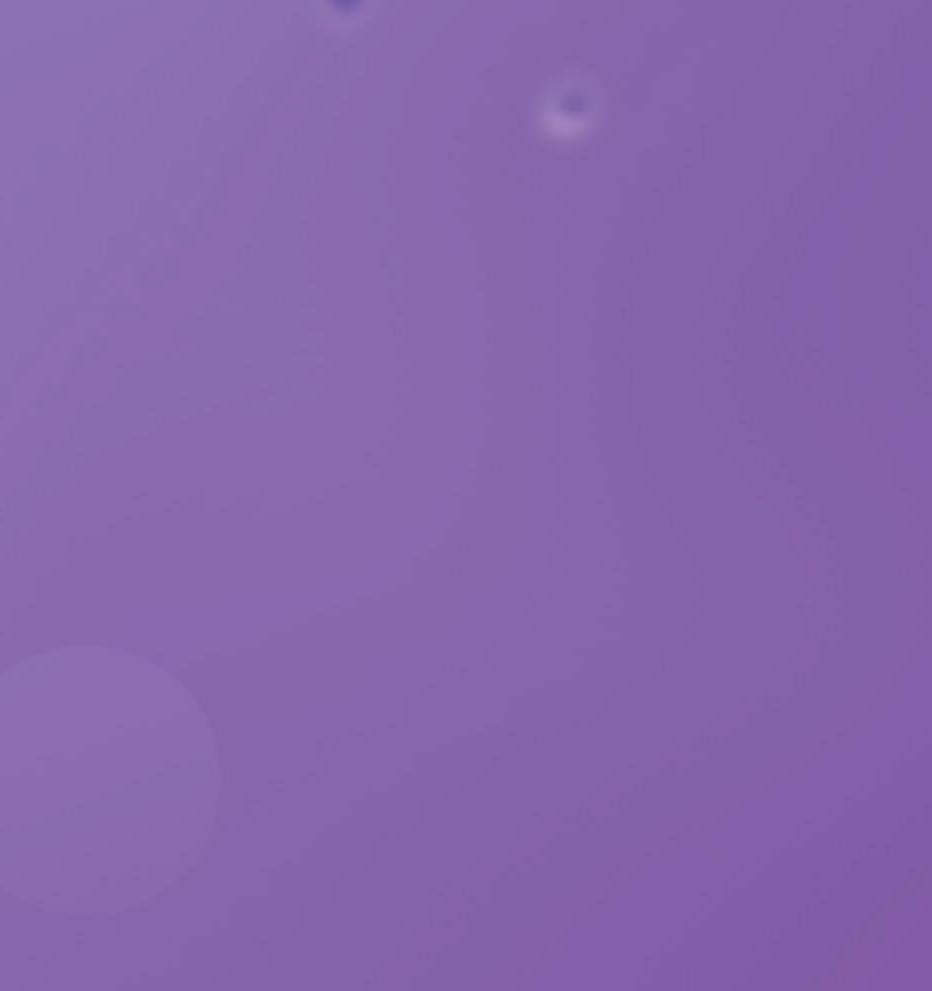
PROTEIN PILE: As ethanol plants transition to new and better cleaning aids, it’s important to evaluate changes to animal feed. Hydrite says its new acid cleaner does not adversely impact feed nutrition.
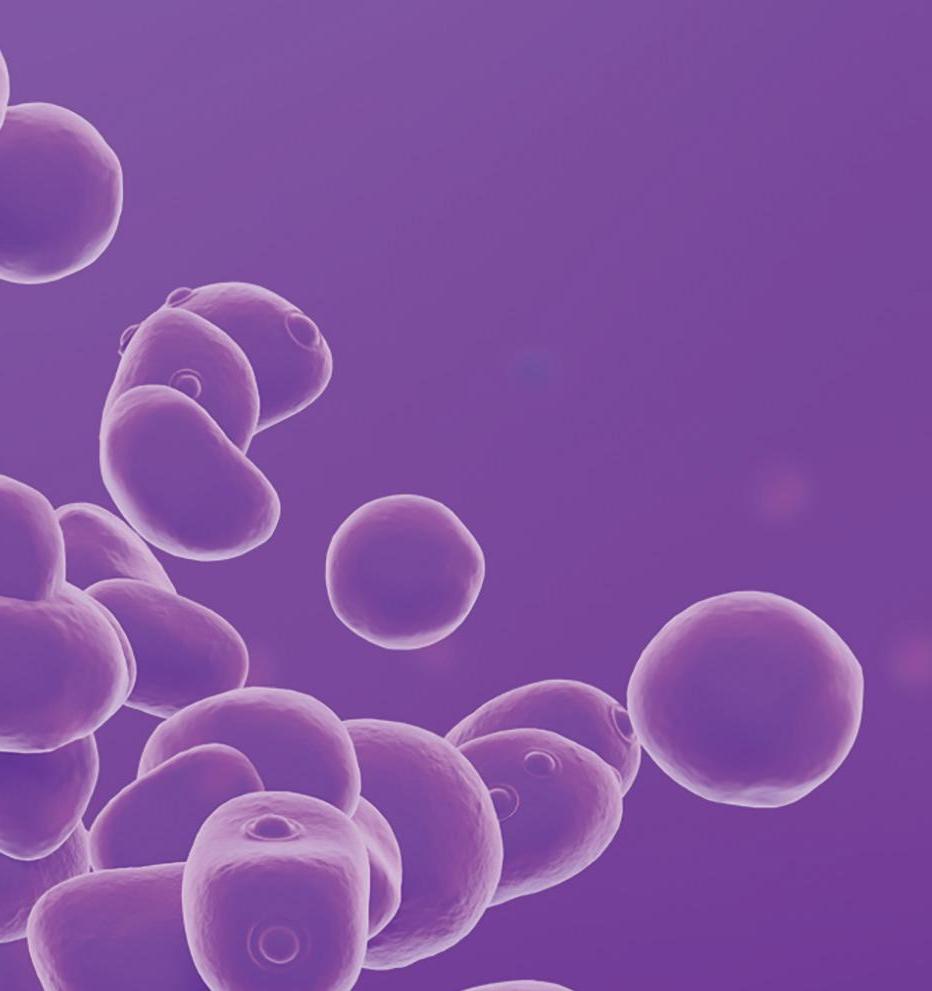
PHOTO: STOCK PHOTO
studied the effects of these caustic-alternative CIP methods, but offers some advice for ethanol plants.
One is to keep animal scientists and nutritionists apprised of process changes. “I continue to struggle with this disconnect between what goes on in processes in ethanol plants and the impacts they have on the final coproducts that our ethanol plants are becoming very reliant upon from a revenue point of view,” he says. “That kind of communication is not happening with the animal feed world to help us understand, are those changes positive, are they negative, and do we need to make adjustments in our formulations?” he says, giving an example of sulfur levels in coproducts.
“Sulfur’s always been a scary topic for ethanol producers because of some historic cattle kills, as I call them, from unfortunate feed of wet distillers grains that was really high in sulfur content causing (Polioencephalomalacia) PEM in cattle,” he says, adding that many nutritionists who aren’t familiar with ethanol production don’t understand where the sulfur in DDGs comes from. McCluskey says CRC-152 contains no sulfur.
He also says that caustic replacements need to have the proper approvals. “Whatever is used to replace [caustic soda], it’s got to be GRAS (Generally Recognized as Safe) listed,” he says. “It’s got to be approved for its intended use from a food or feed safety point of view to be considered compliant with FSMA (Food Safety Modernization Act) regulations.”
There are also considerations in
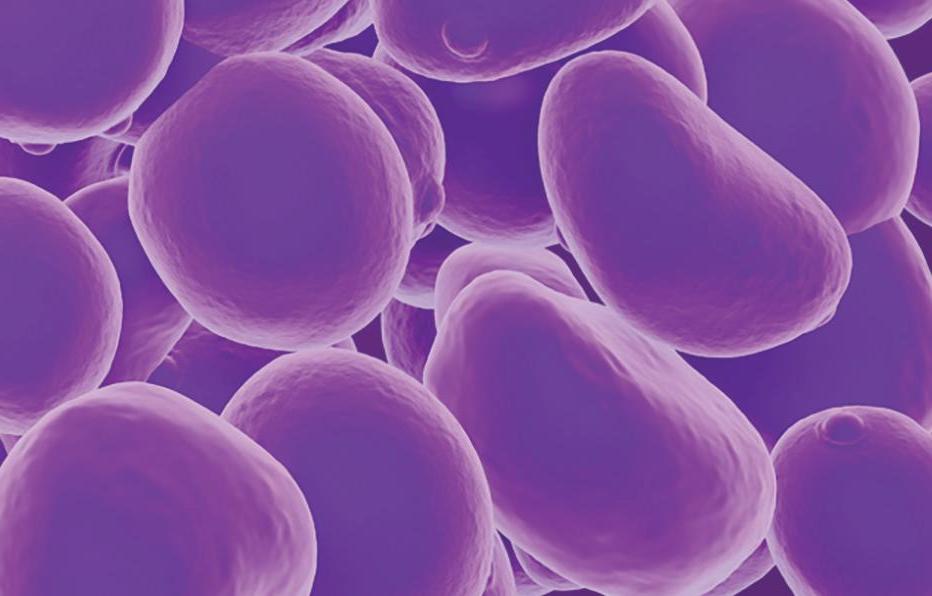
XCELIS® Yeasts SYNERXIA® RUBY
The new standard in high yield yeast driving plants to the peak of performance.
www.xcelis.com
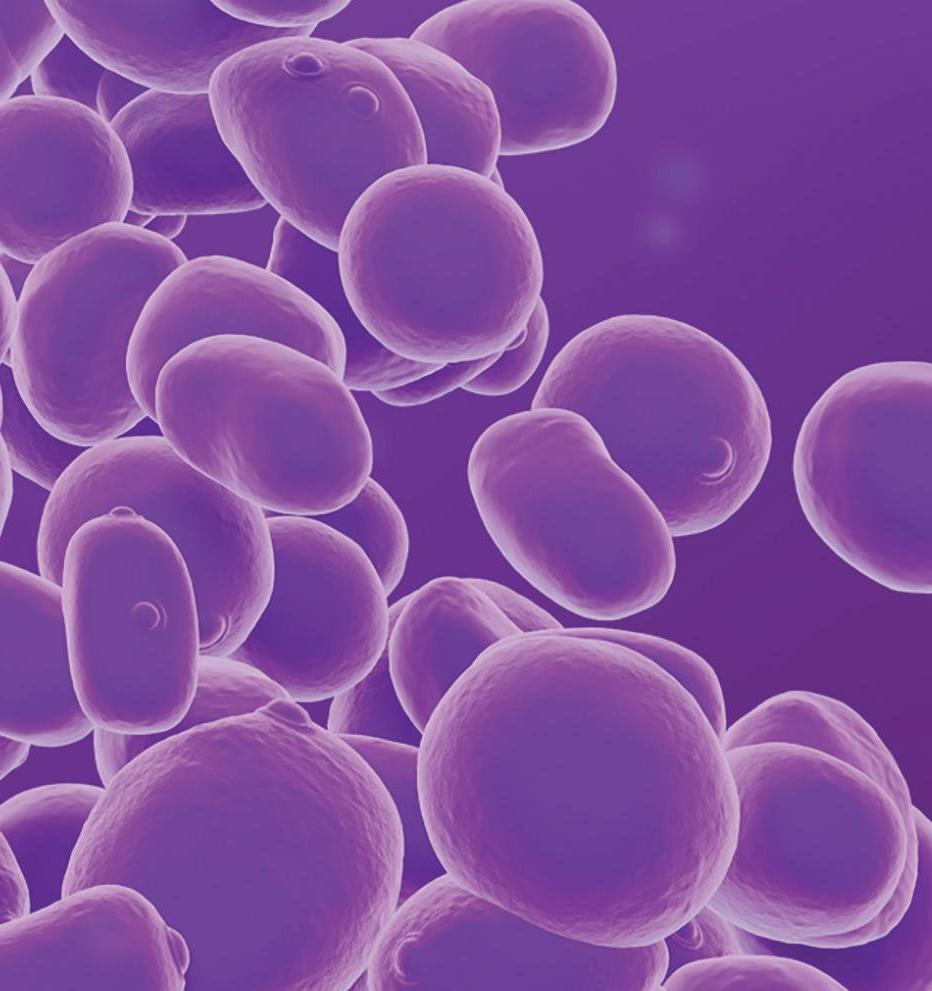
'[DDGs] is not as consistent as many nutritionists would like, but it’s gotten better and more predictable and we’ve developed enough prediction equations and prediction tools, as I call them, to help end users capture as much value as they can for different species.'
Jerry Shurson University of Minnesota terms of how the nutritional properties of DDGs are going to be impacted. “Are the products, or is the product that’s going to become the substitute, does it bring with it high concentrations of some chemical compounds, whether its minerals, whether it’s something else, that is going to adulterate or negatively impact the nutritional value of the coproduct in some way? I mean, is the concentration going to be high enough to even matter?” Shurson says.
While caustic substitutes may not change the nutritional value of the coproduct, some chemical compounds could affect the measurement of certain compounds in DDGs. Shurson uses crude proteins as an example. Those proteins, he says, aren’t measured directly, but are
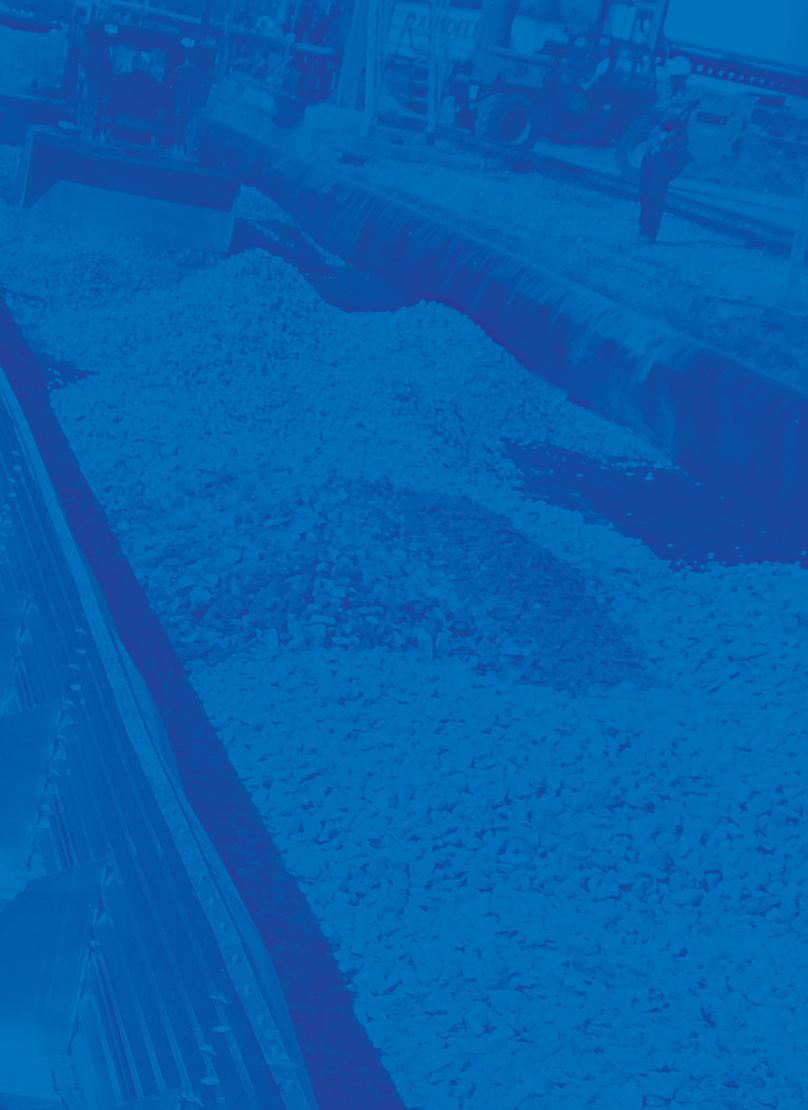
When what’s inside gets out.
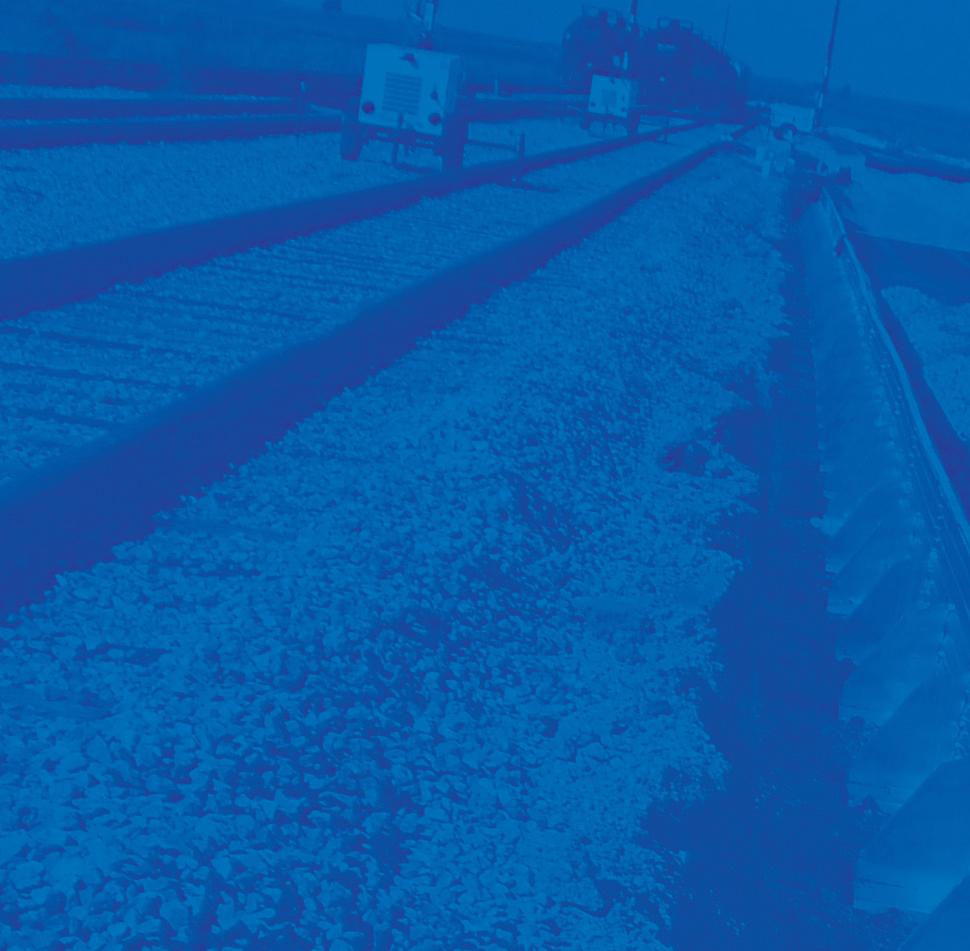
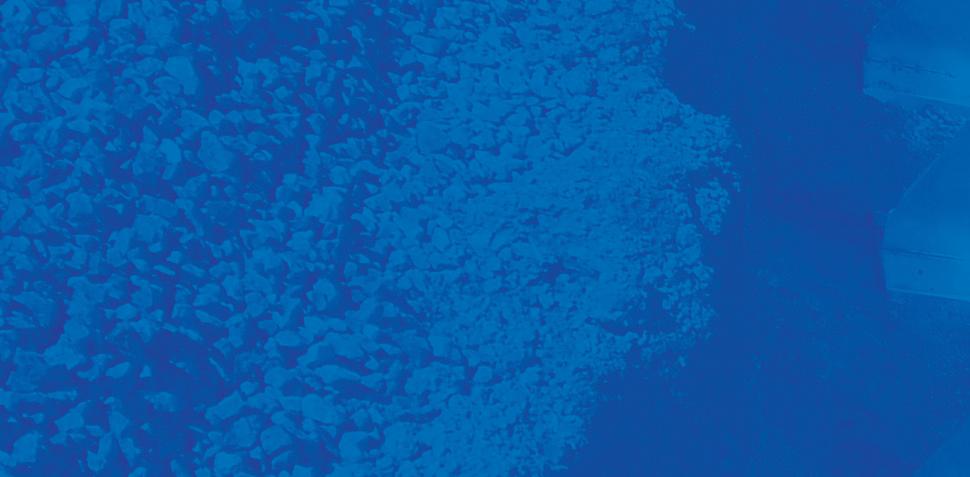
Ramsdell’s got you covered. Our secondary containment systems have been protecting valuable tank contents—and the environment—since 1988. From storage tanks to railcars, when what’s inside gets out, you have one chance to capture it.

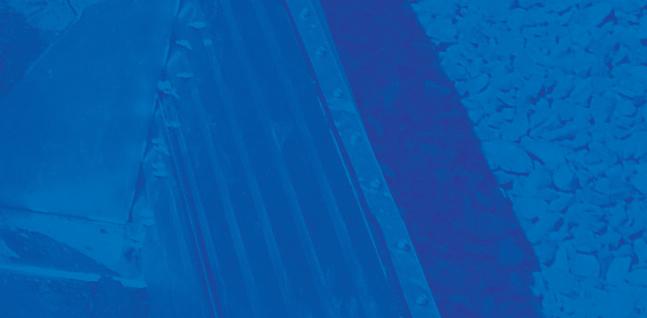
estimated by measuring nitrogen levels. “Let’s say some substitute compound added some significant amounts of nitrogen,” he says. “You could inflate your protein content of your coproducts and say ‘Oh, look at this, this is great. I can get a greater market value for it.’ While that may be acceptable for cattle, monogastric animals may be negatively affected. I think it depends on the context and what the components are of whatever products are going to be used.”
The Importance of DDGs
Hydrite reiterates the importance of its products not impacting DDGs, as plants become more reliant on distillers grains as a revenue source.
“As you read reports and so on, particularly over the last several years, ethanol profit margins have been flat or negative, and it’s really put a lot of pressure on ethanol plants to rethink other coproduct streams,” Shurson says.
And ethanol plants are more consistently able to produce high-quality DDGs, he says. “I think as the industry has matured in recent years, its consistency has improved,” Shurson says. “It’s not as consistent as many nutritionists would like, but it’s gotten better and more predictable and we’ve developed enough prediction equations and prediction tools, as I call them, to help end users capture as much value as they can for different species.”
And that’s a trend Shurson expects to continue. “[Ethanol plants] are becoming much more reliant on revenue streams from coproducts than they have been on ethanol in the past,” he says. “And I think going forward, that’s going to continue to be the case.”
Author: Matt Thompson Freelance Writer m.thompson2005@gmail.com