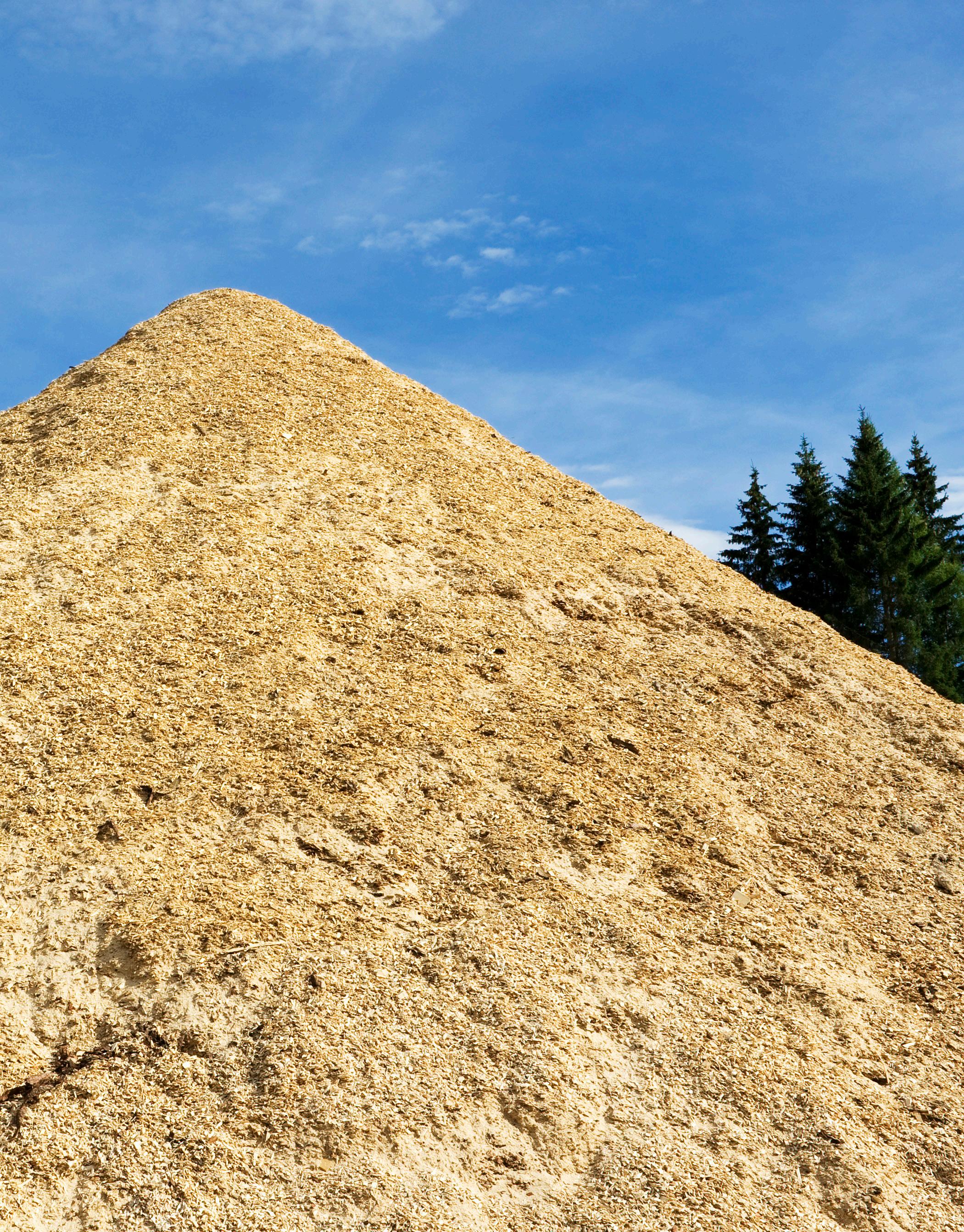
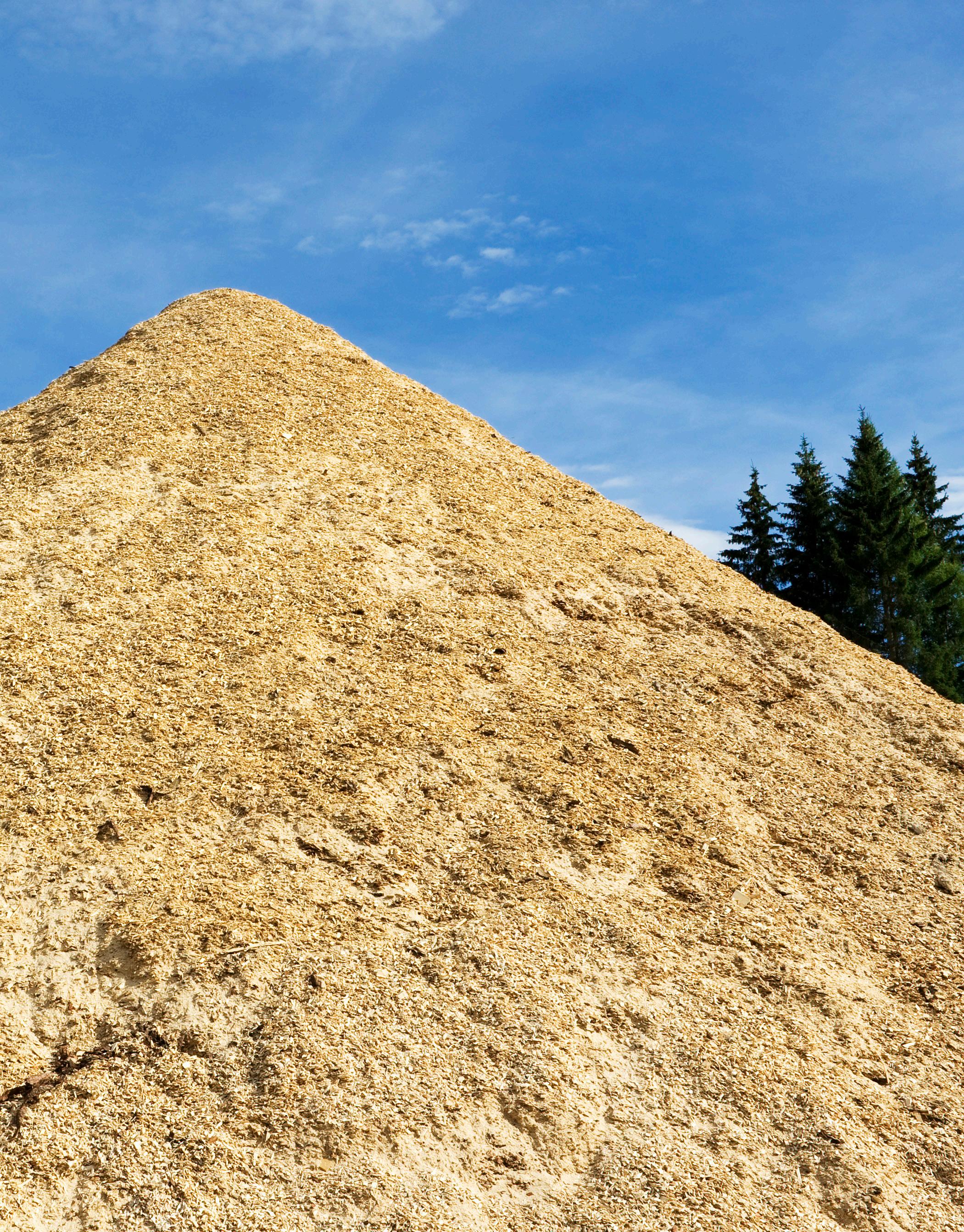
Leading Carbon Capture Business


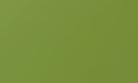










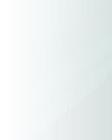




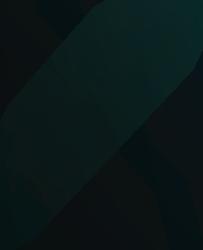



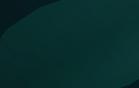
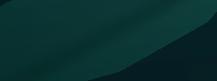

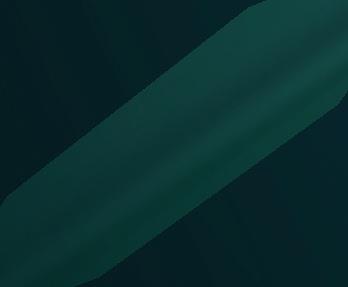




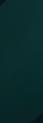
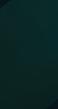

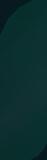


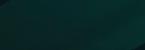




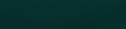


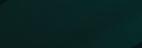
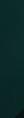




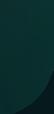






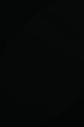

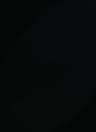

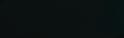



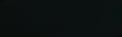









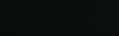

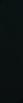




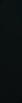


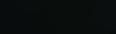
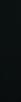


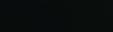
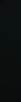

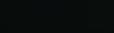

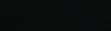



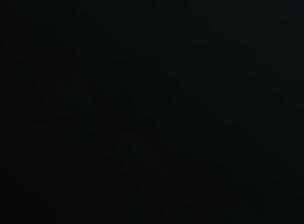
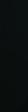

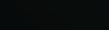


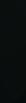

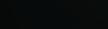




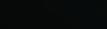




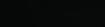


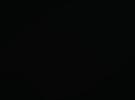
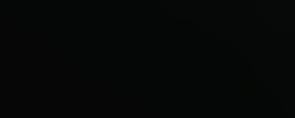


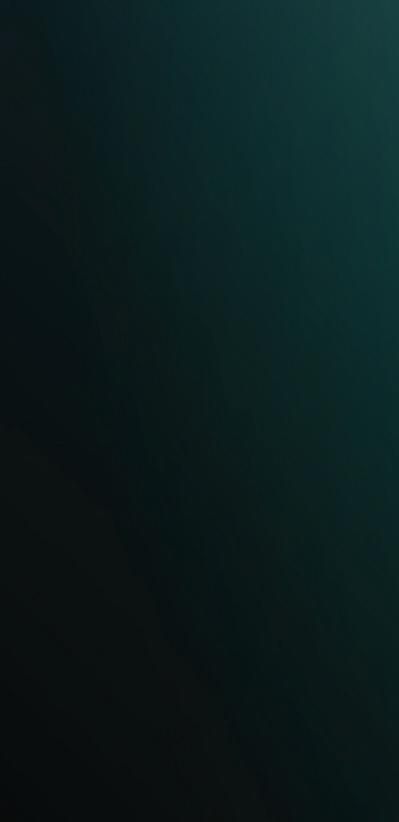
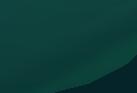

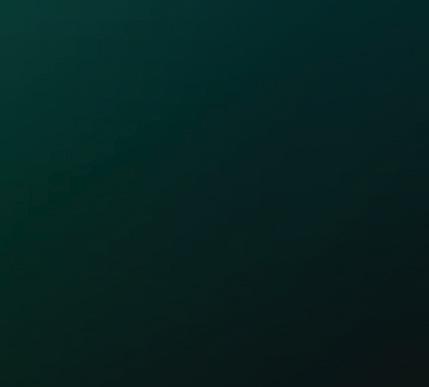



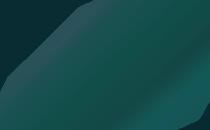


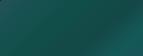








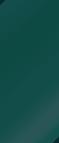
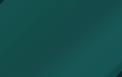





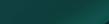
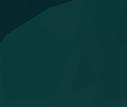


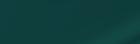




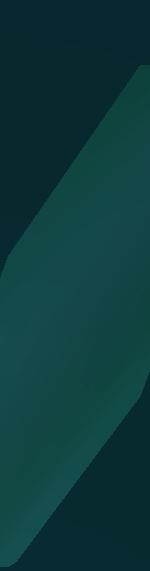
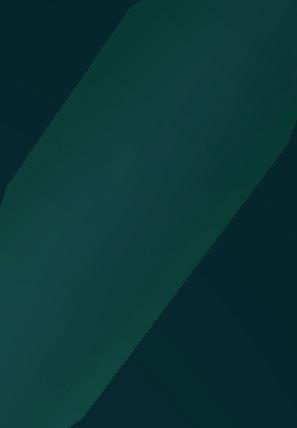
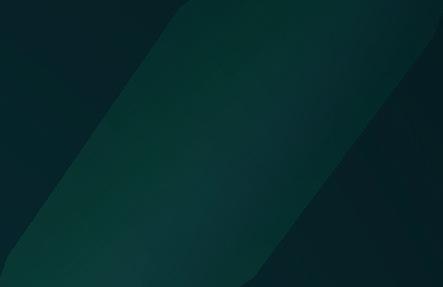
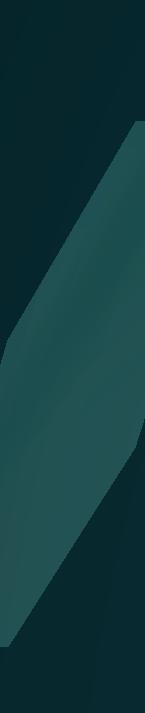
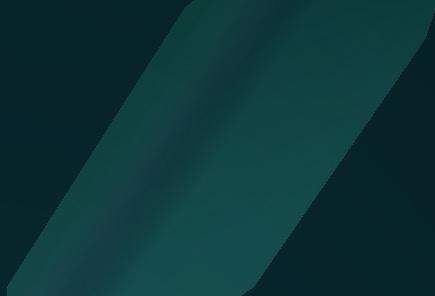
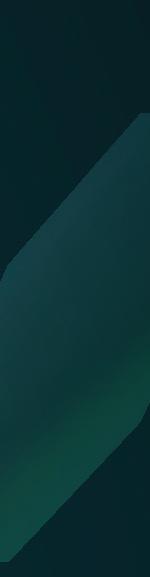
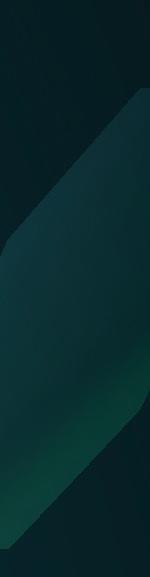

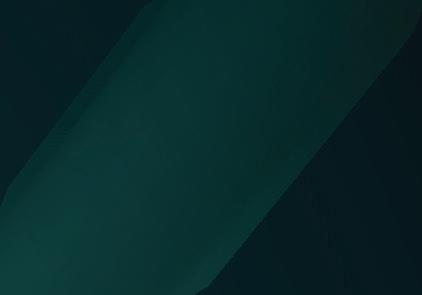
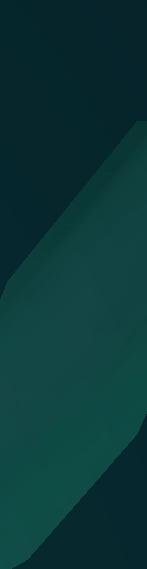

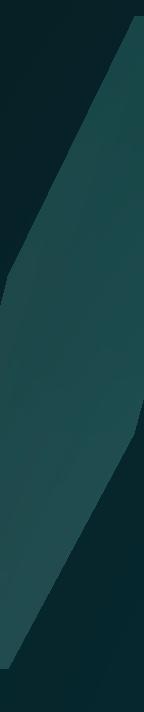
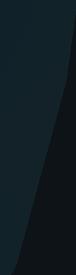
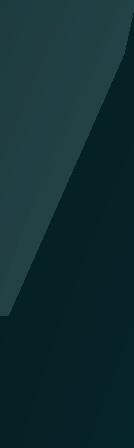



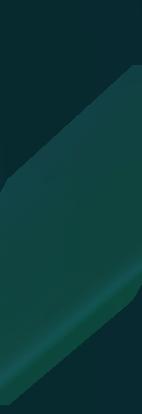
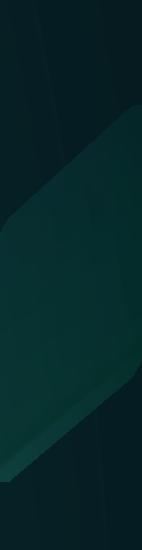
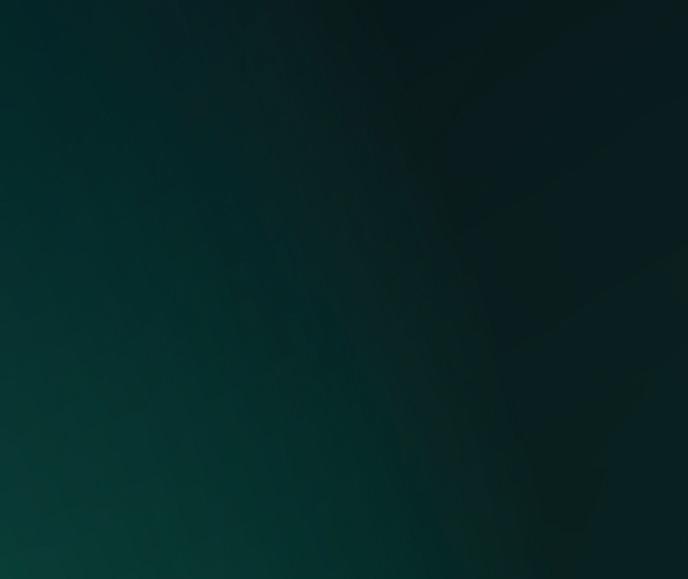
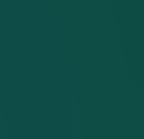
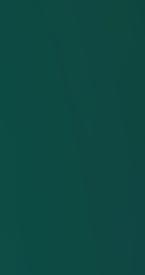
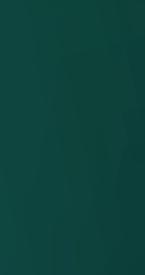
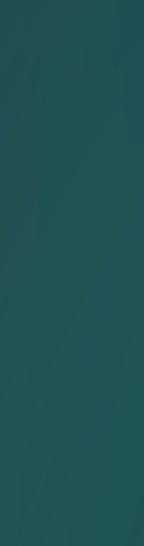
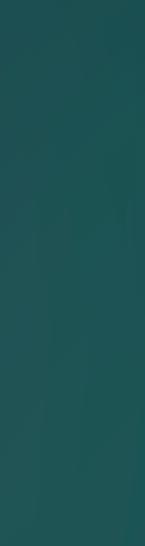
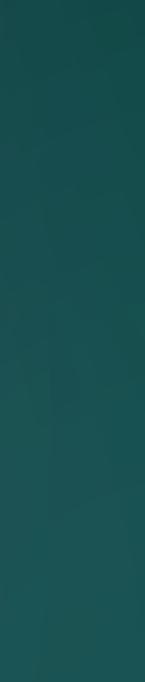
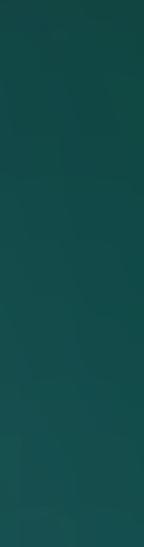
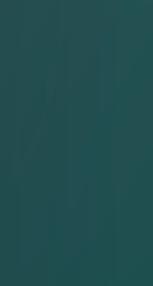
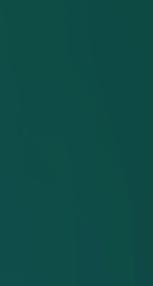

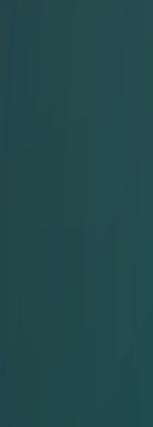

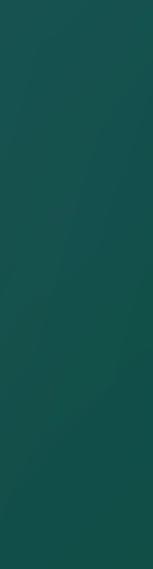
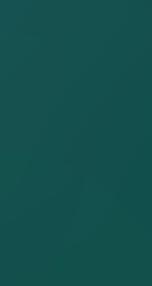
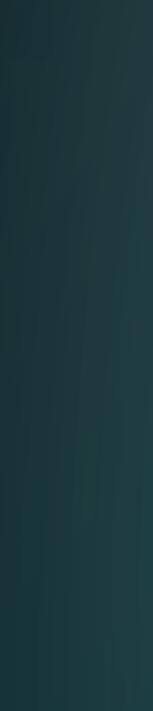


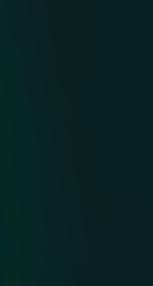

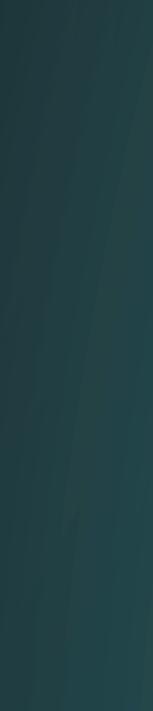
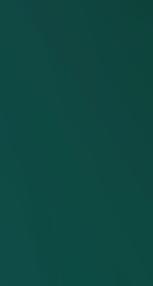
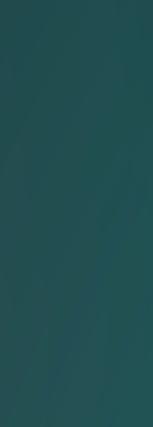
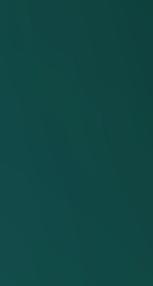

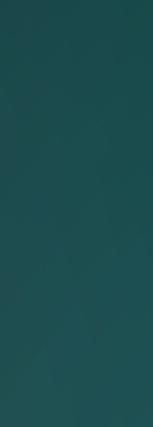

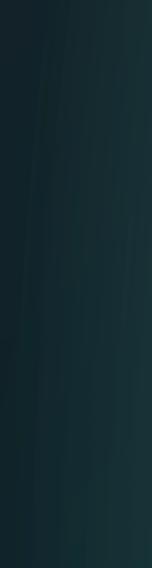

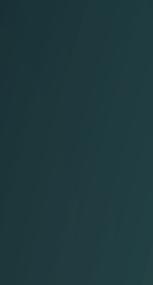
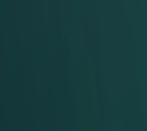
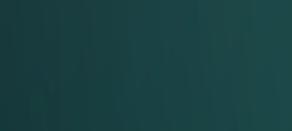

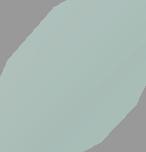
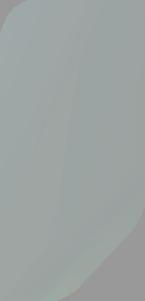
How Can You Be a Part of the Action?
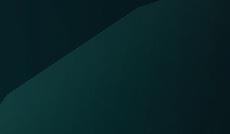

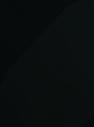



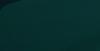
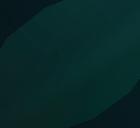

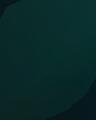



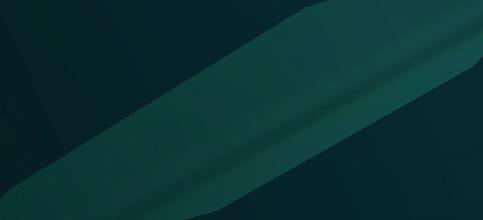




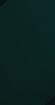
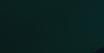



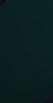
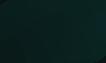





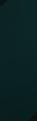



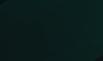
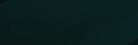

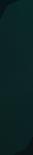







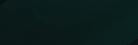
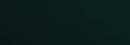







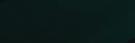






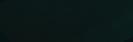










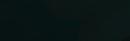





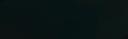













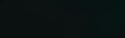














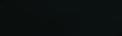
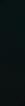




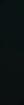





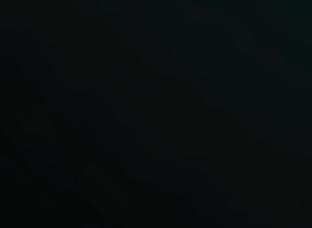
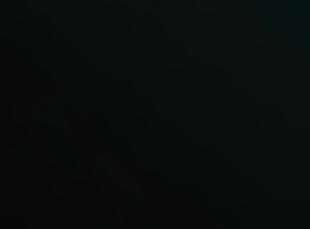
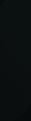
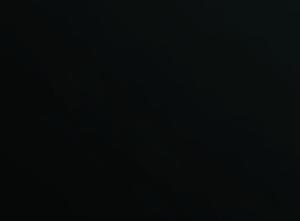
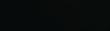
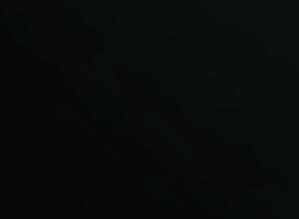
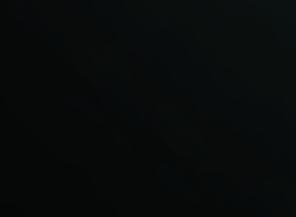



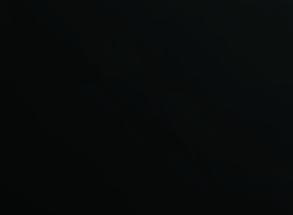
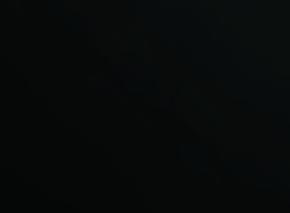

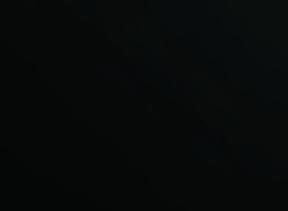

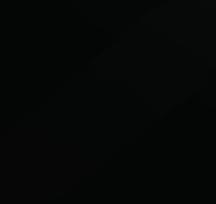
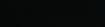
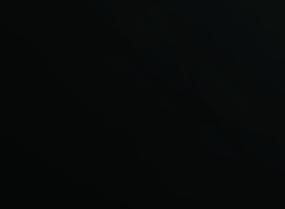
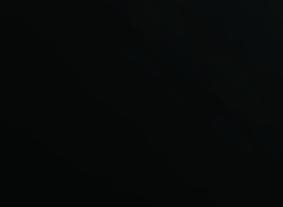



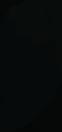


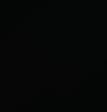

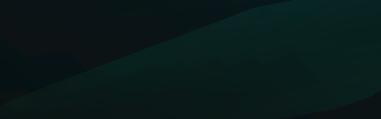
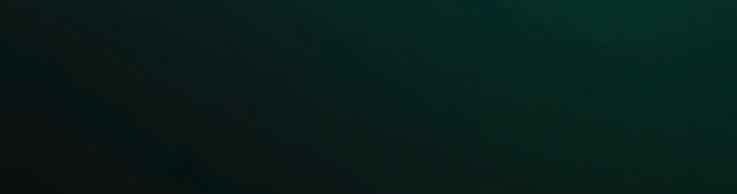
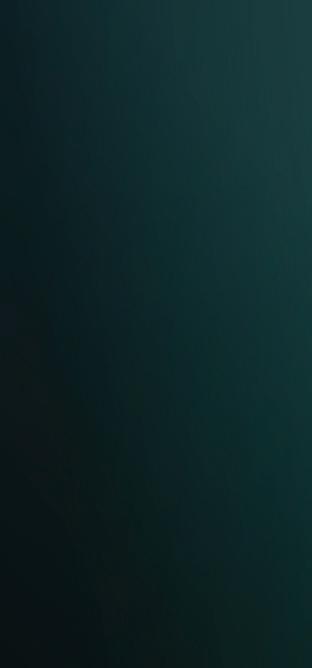
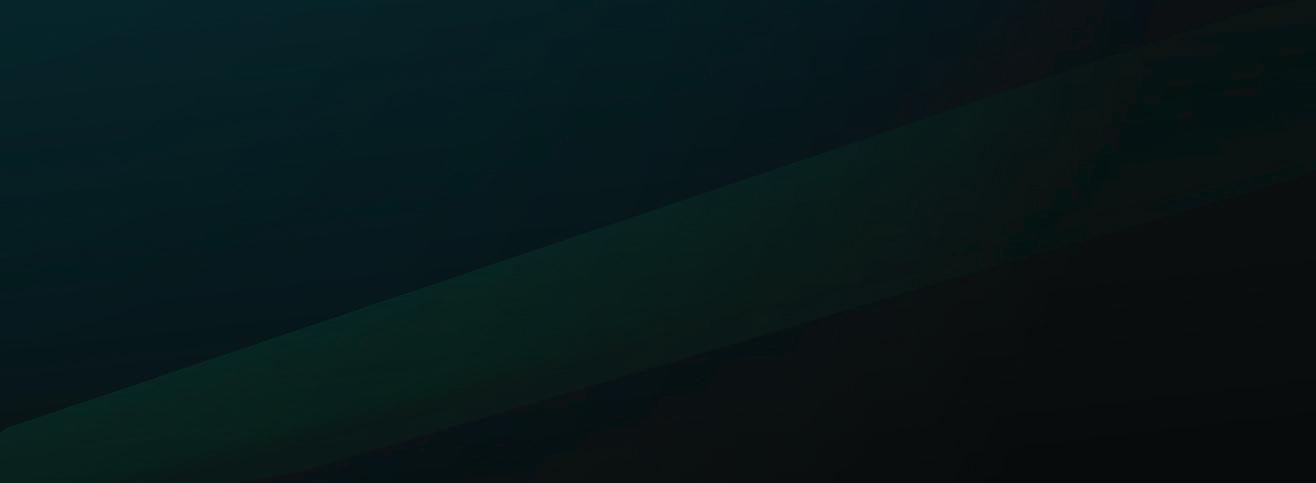
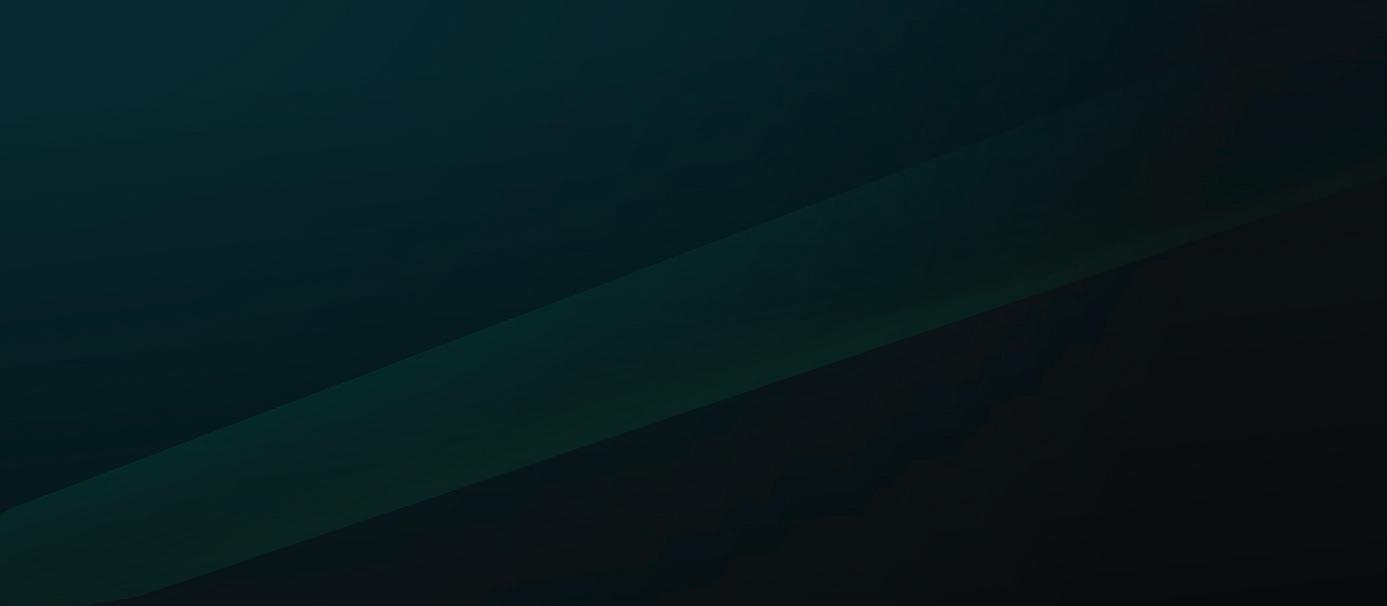
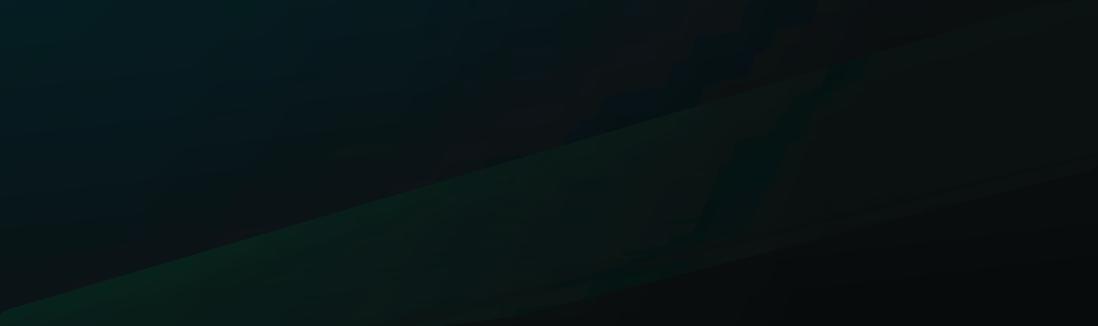

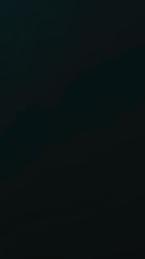
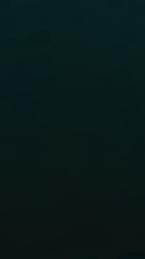

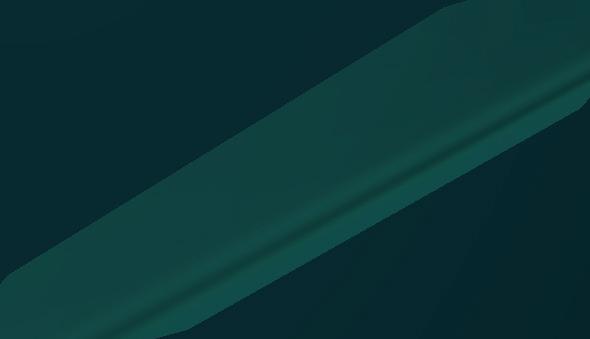
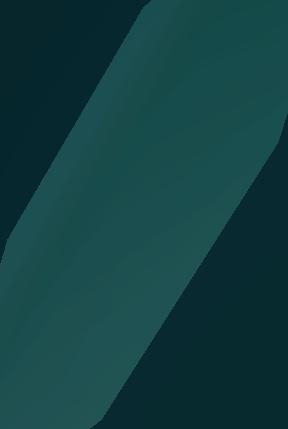

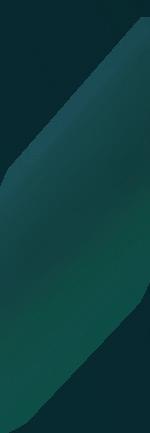
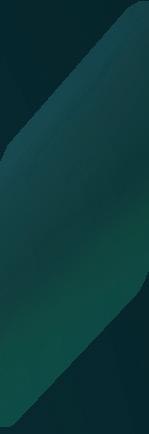
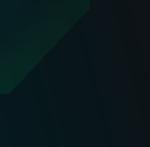

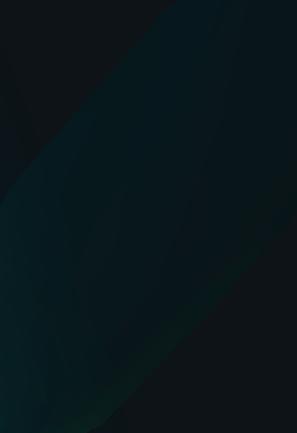
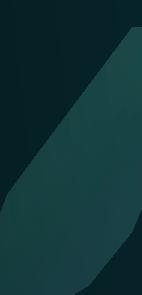

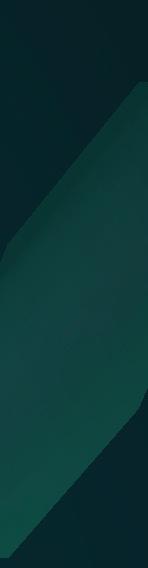
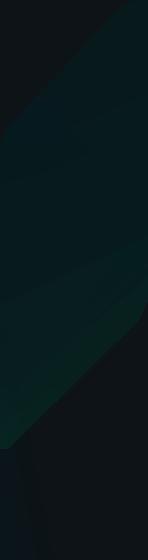




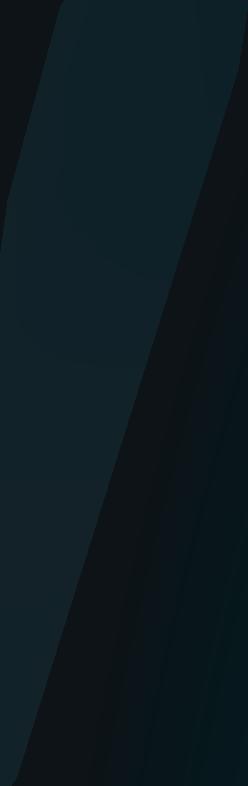



Capturing and storing carbon dioxide in underground wells has the potential to become the most consequential technological deployment in the histor y of the broader biofuels industry.
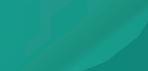
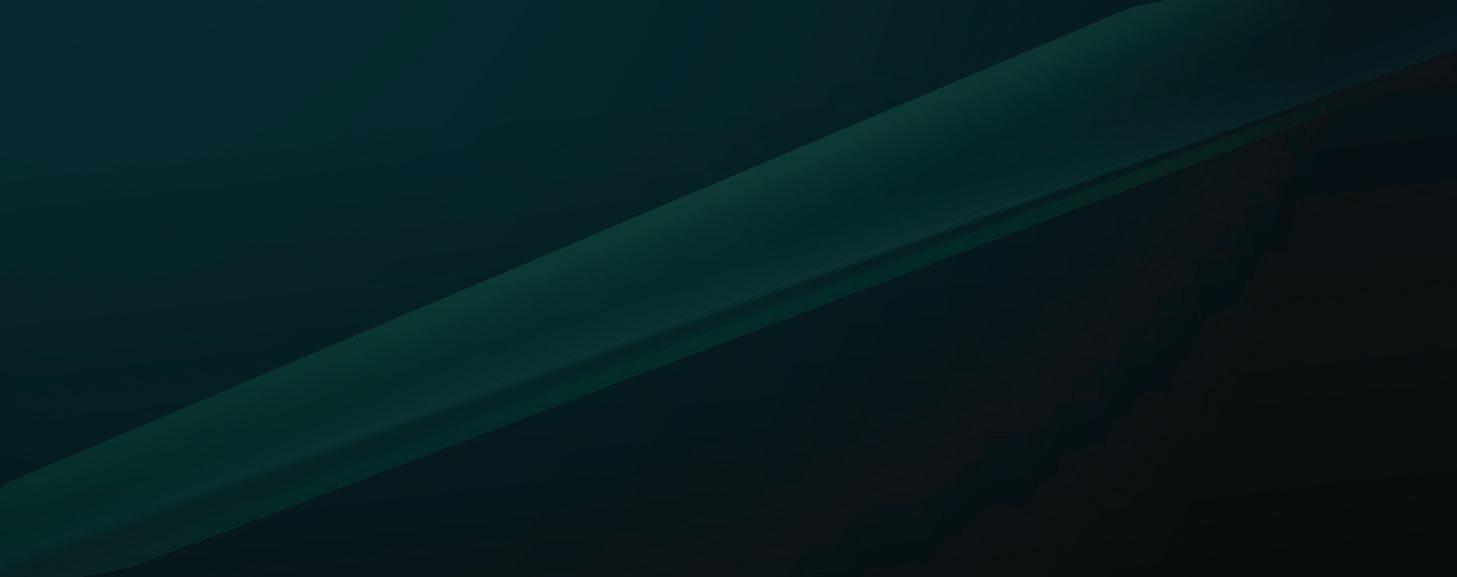



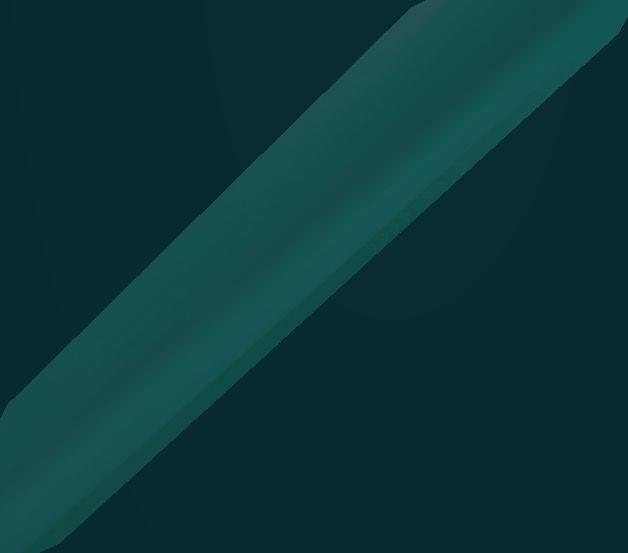
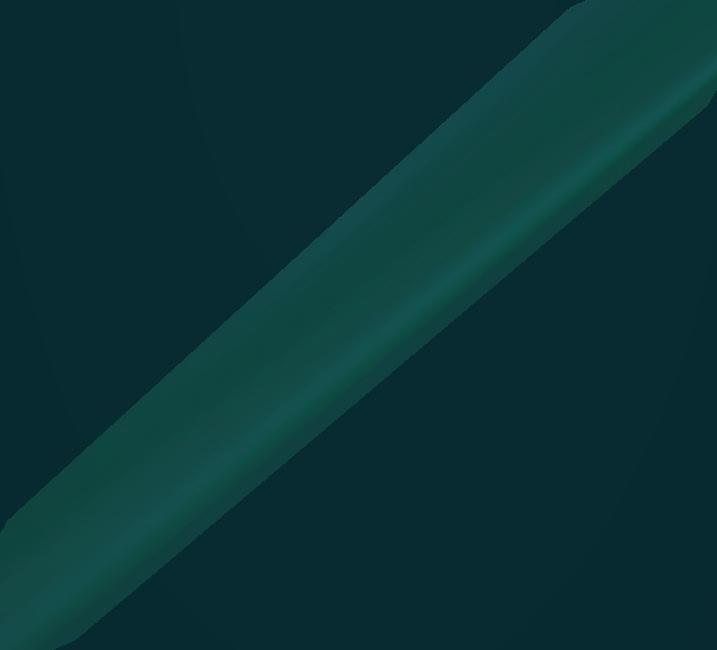
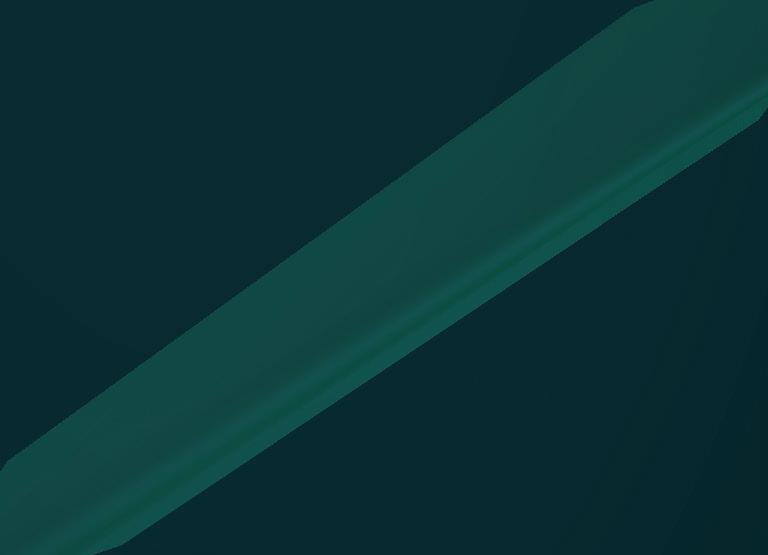
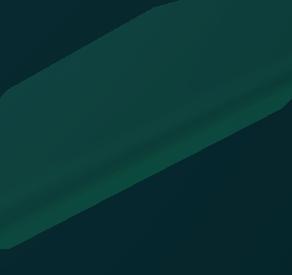
The National Carbon Capture Conference & Expo will offer attendees a comprehensive look at the economics of carbon capture and storage, the infrastructure required to make it possible and the nancial and marketplace impacts to participating producers.
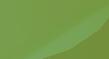
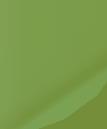

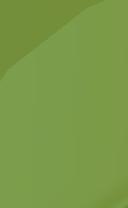
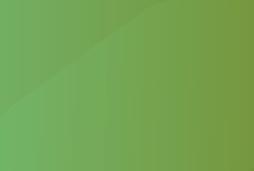
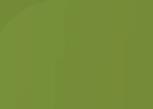
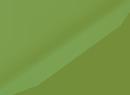
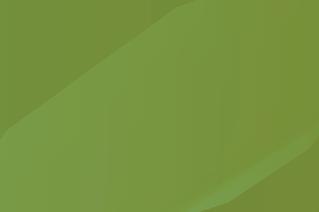

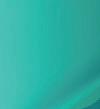
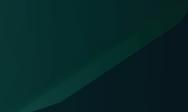
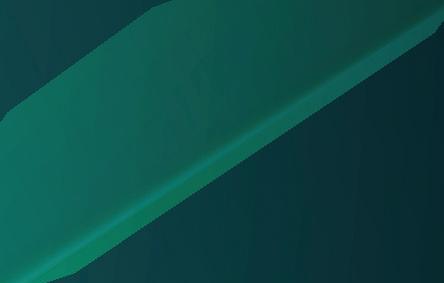
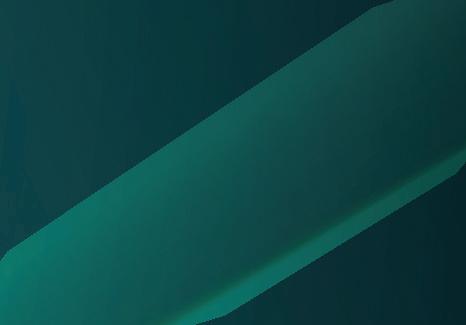




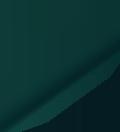
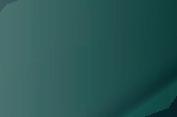
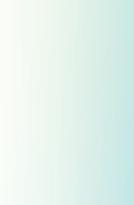



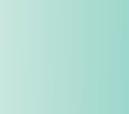
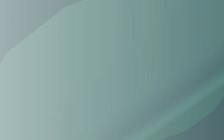
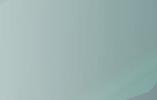
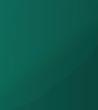



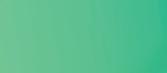

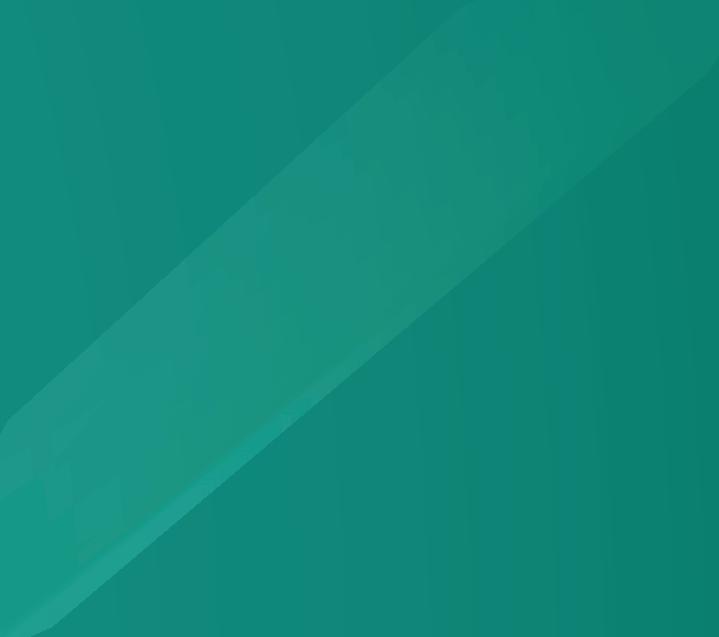


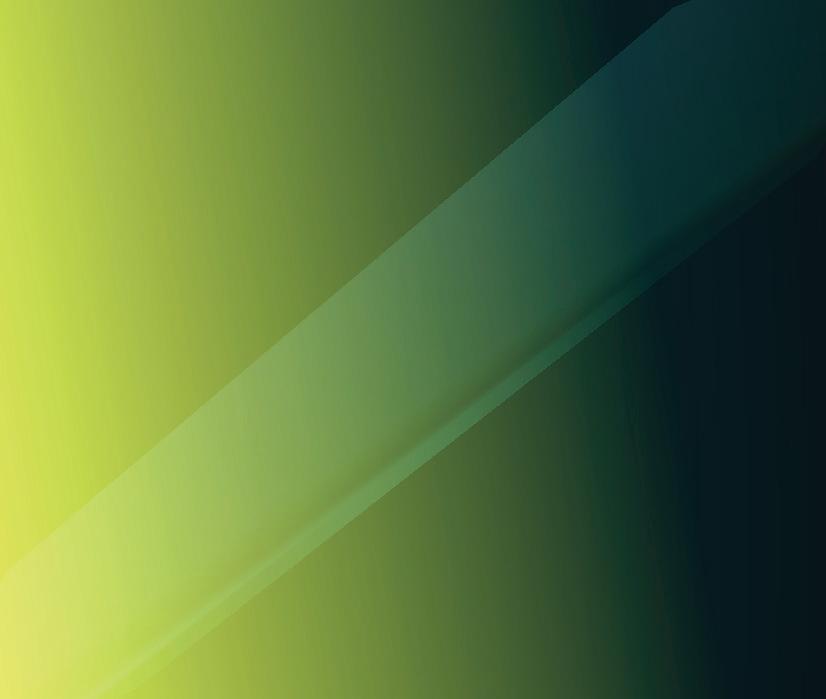
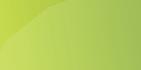



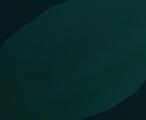
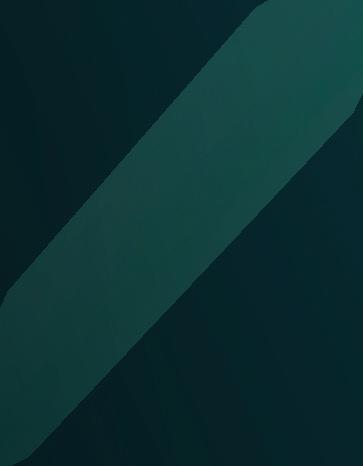

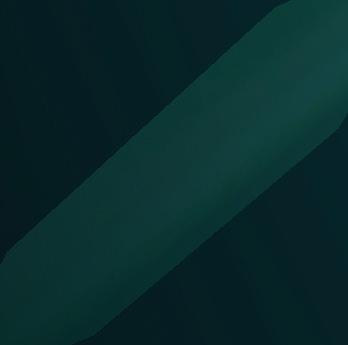
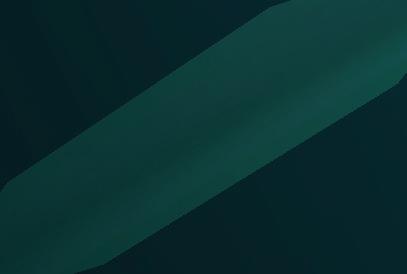


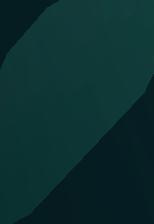


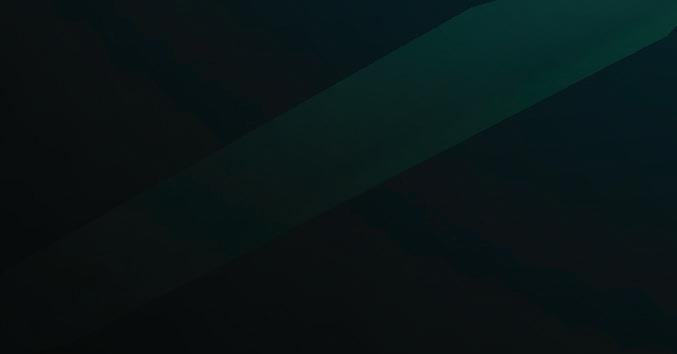
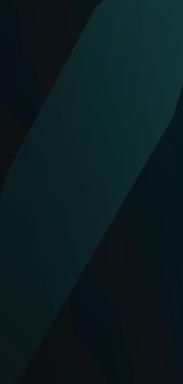
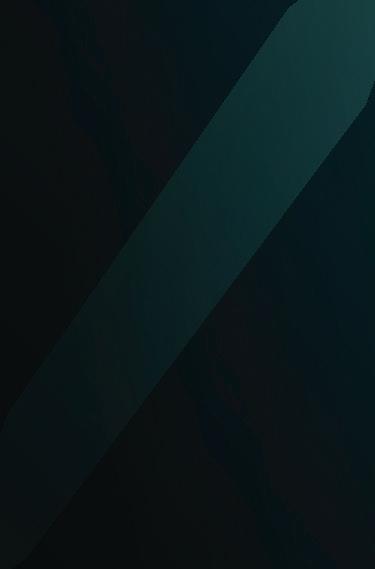
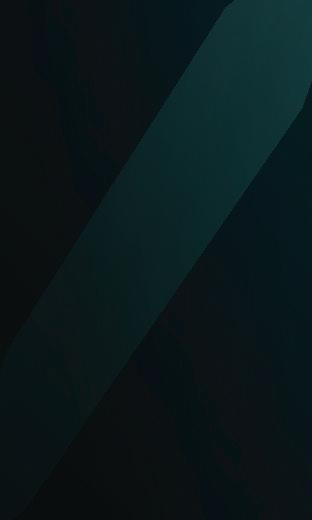
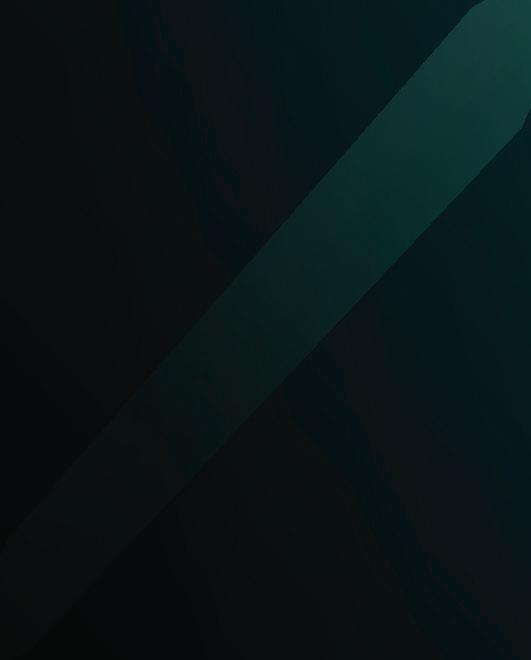
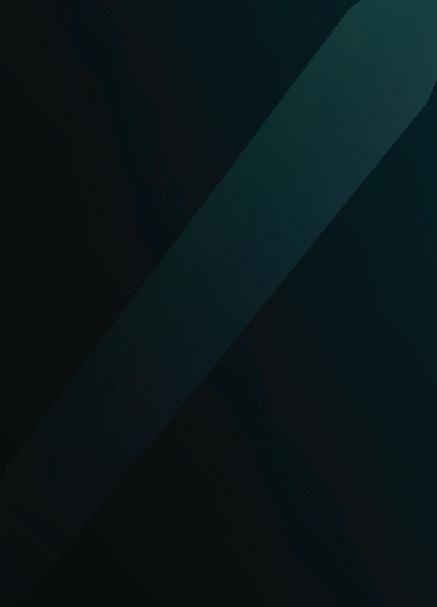
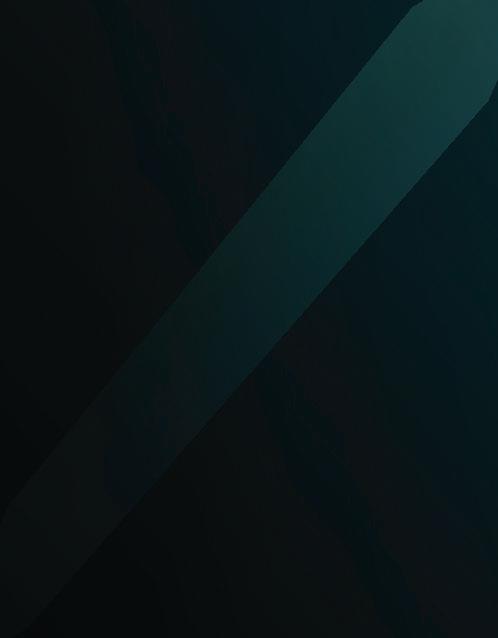
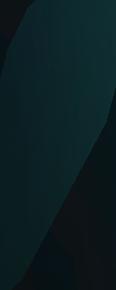
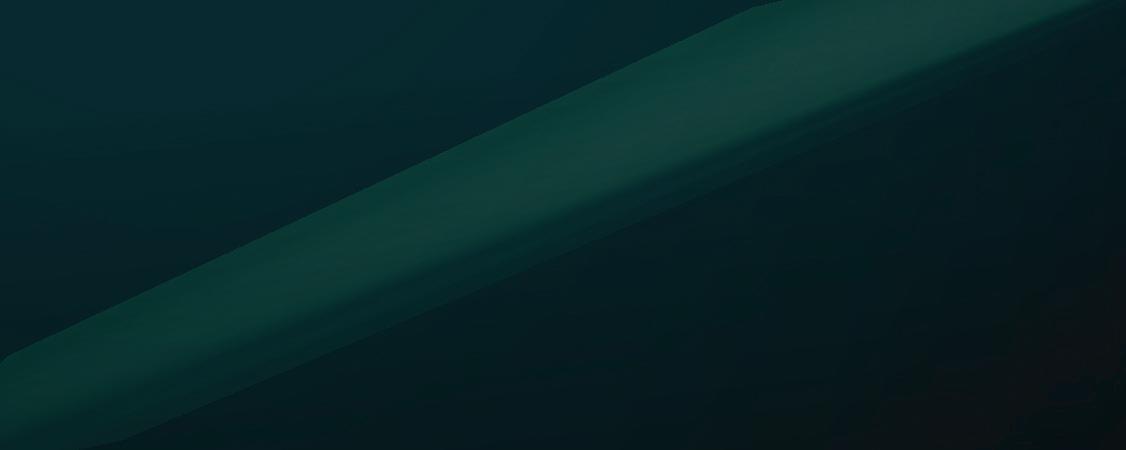
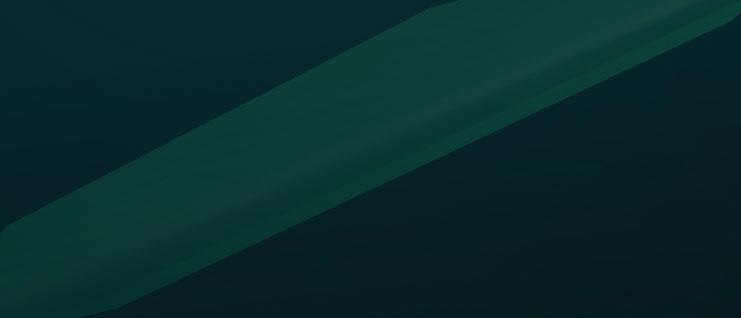
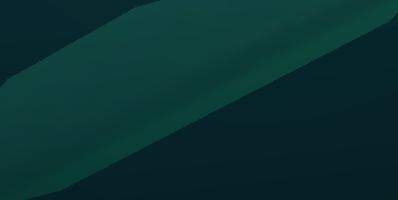

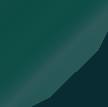
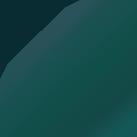




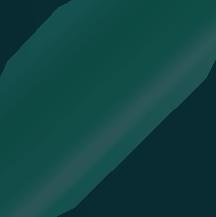
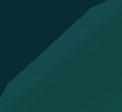
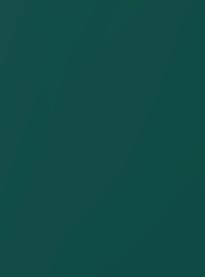
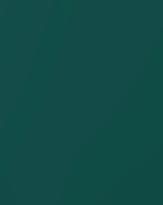

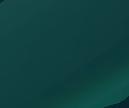
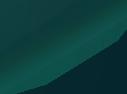

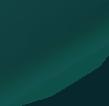


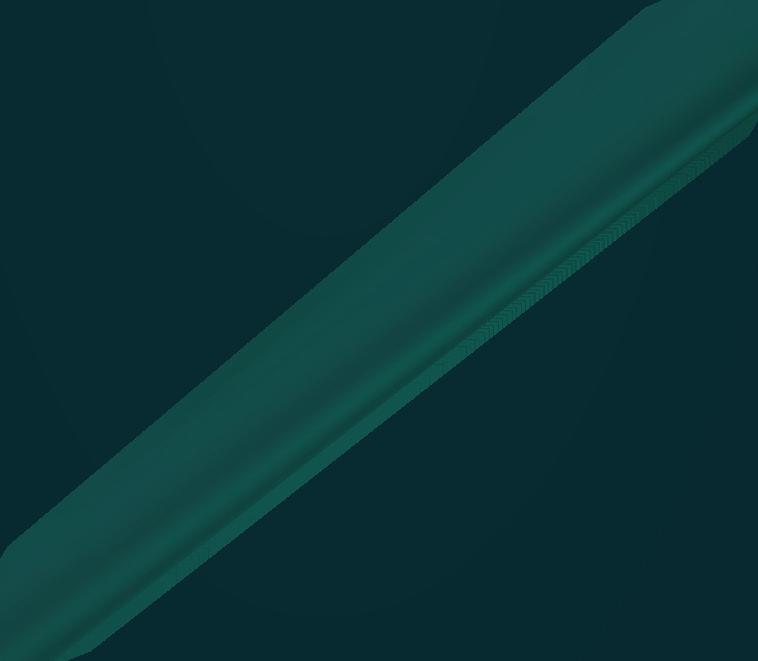

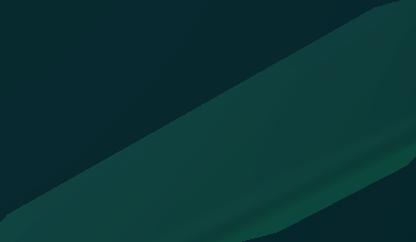
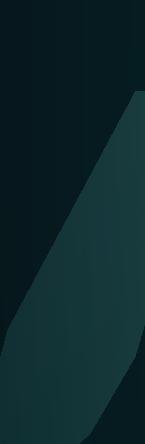

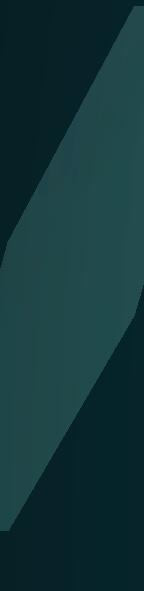
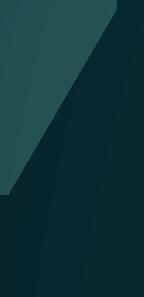
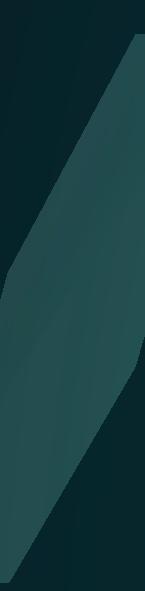
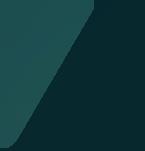
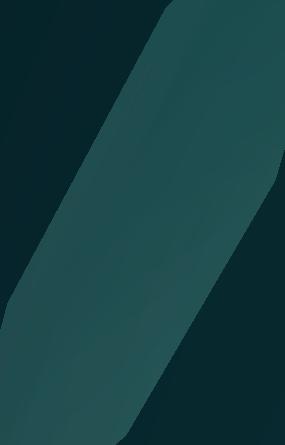
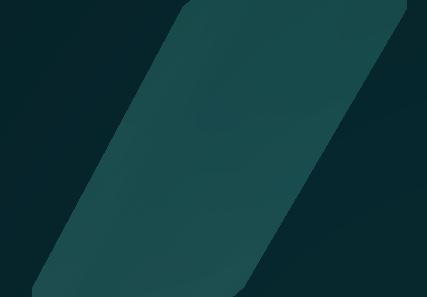
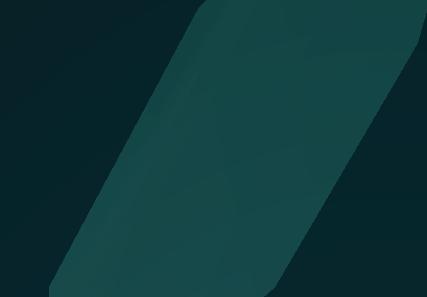

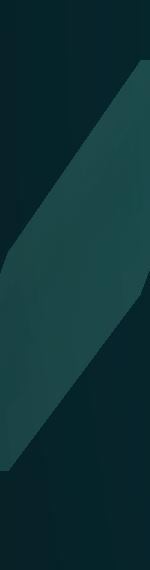
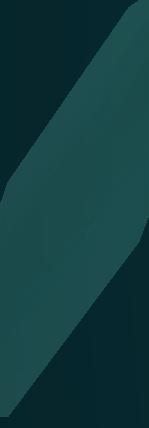

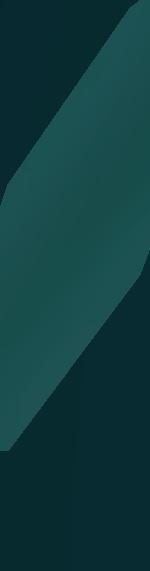

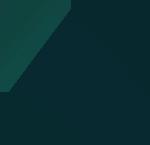
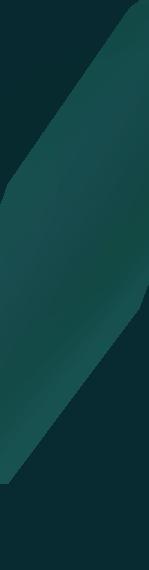
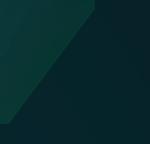
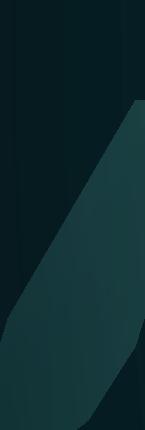

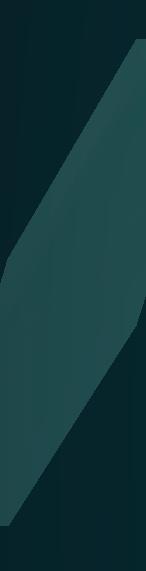
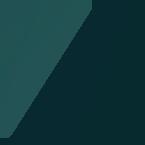
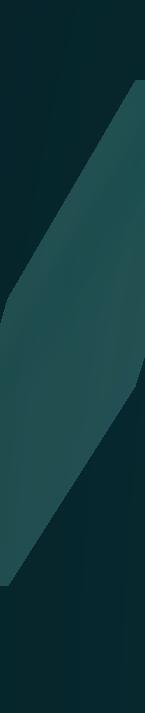
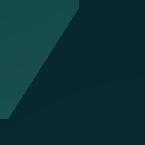
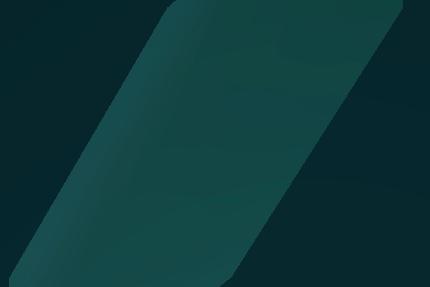
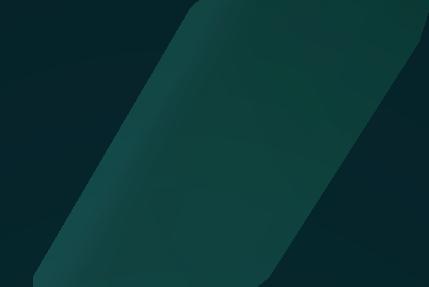
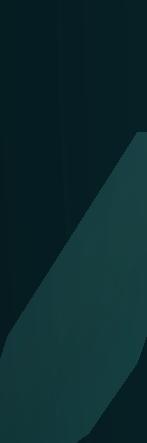
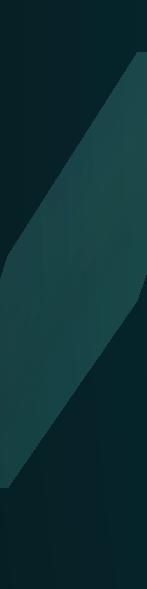
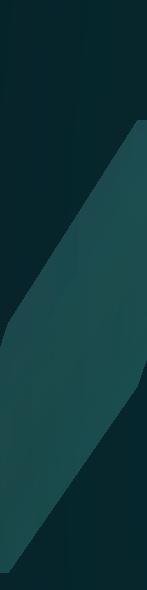
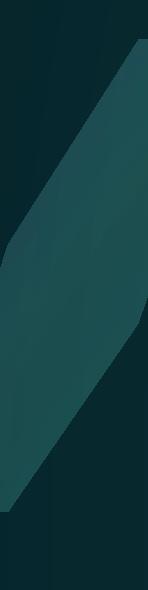

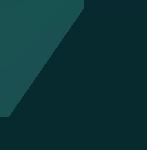
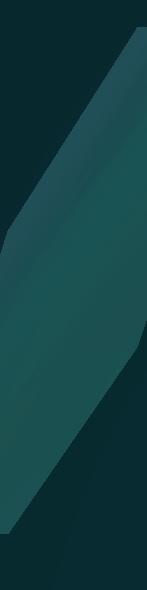


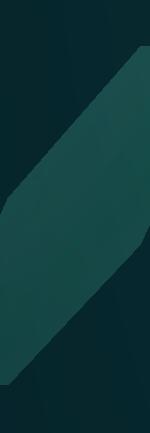
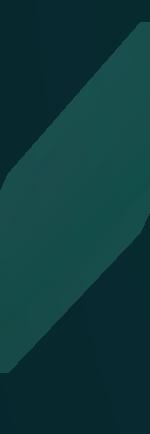
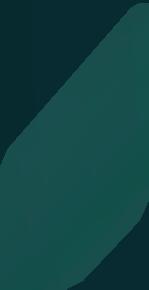

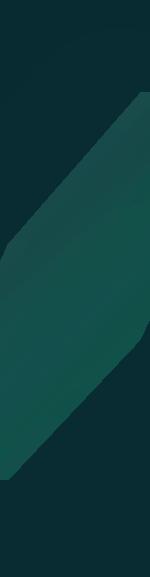

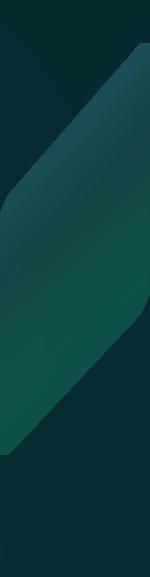
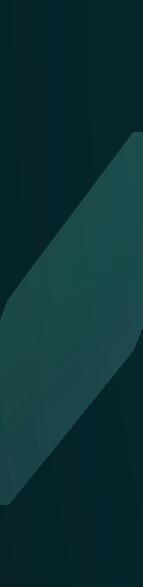
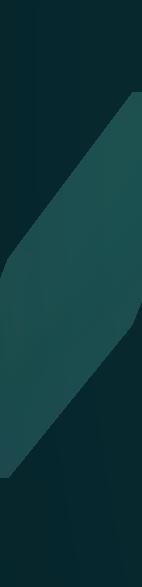


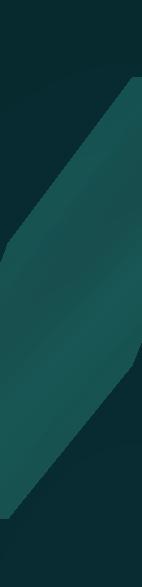
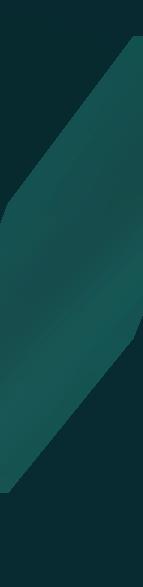
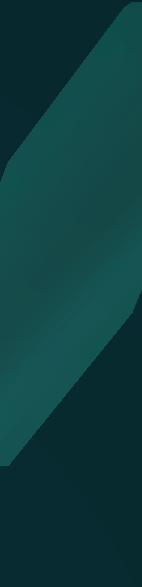

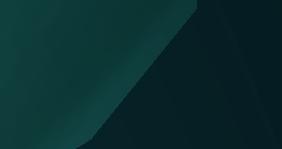
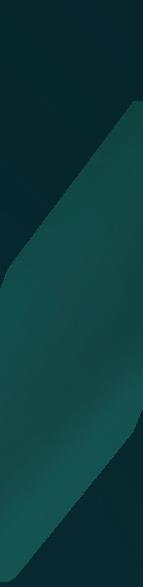
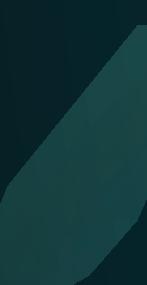
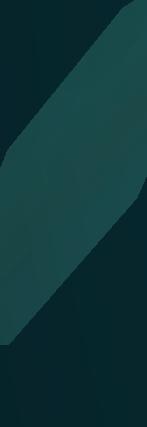
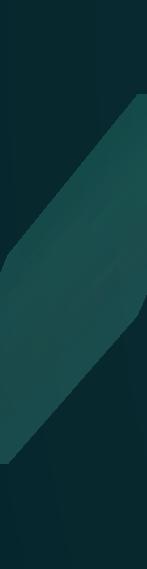
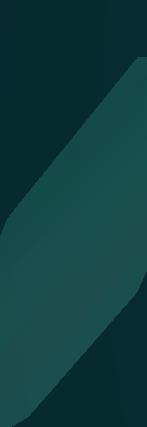
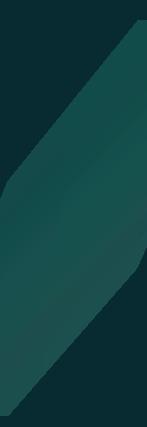
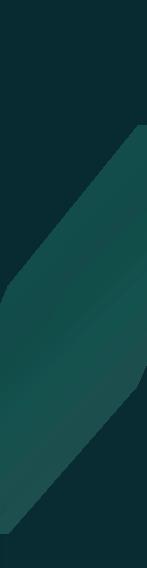
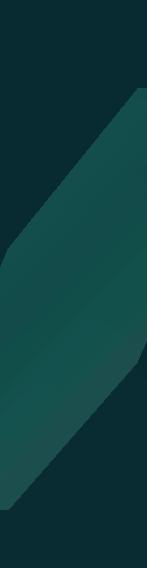

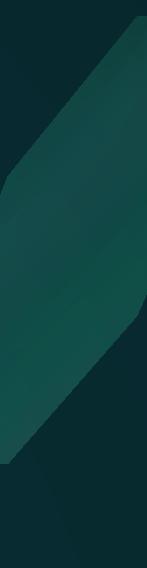
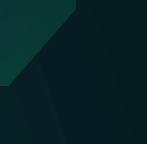
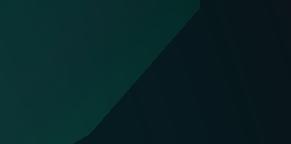
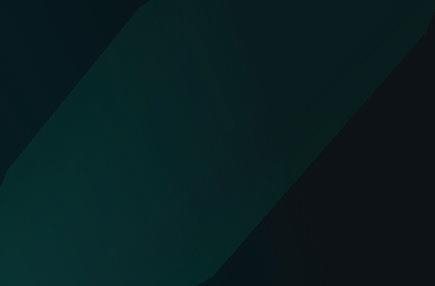
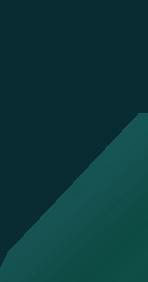

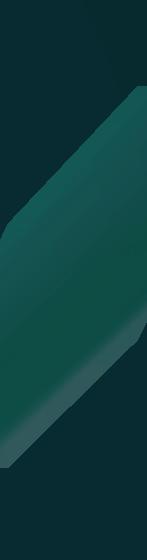
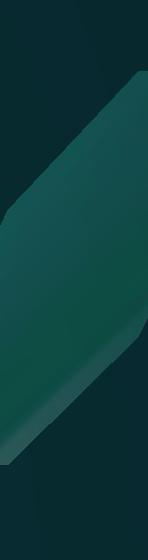
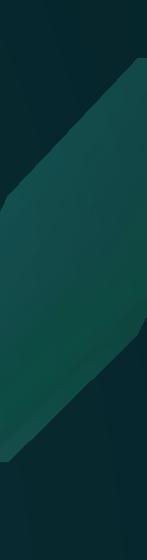

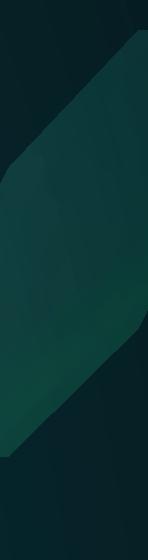
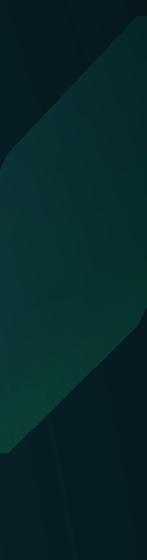
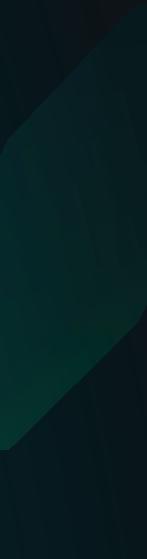



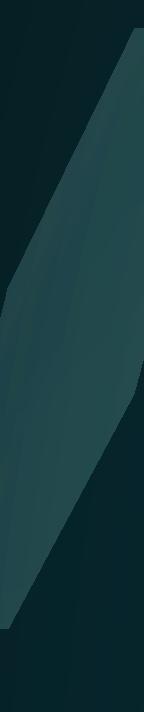
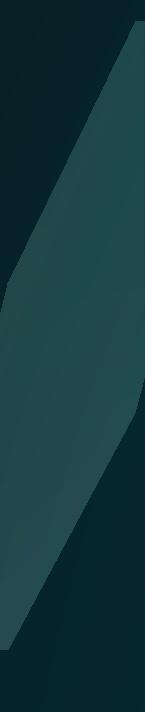
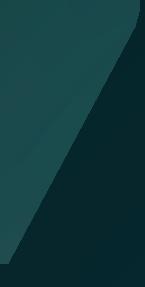
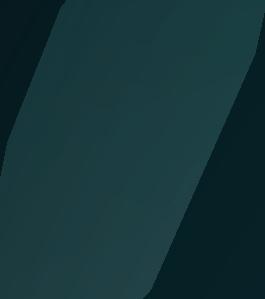


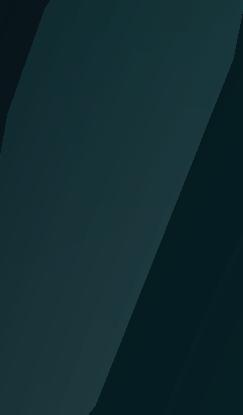
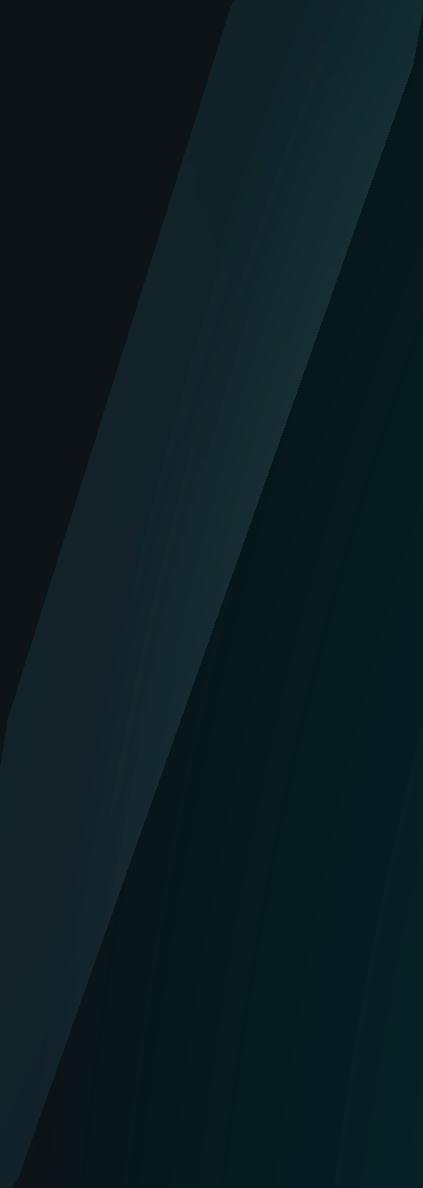
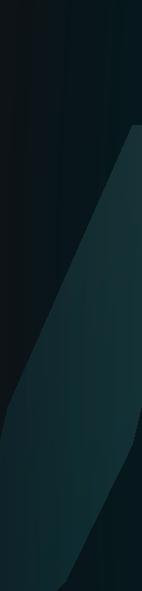



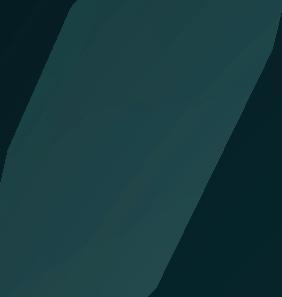
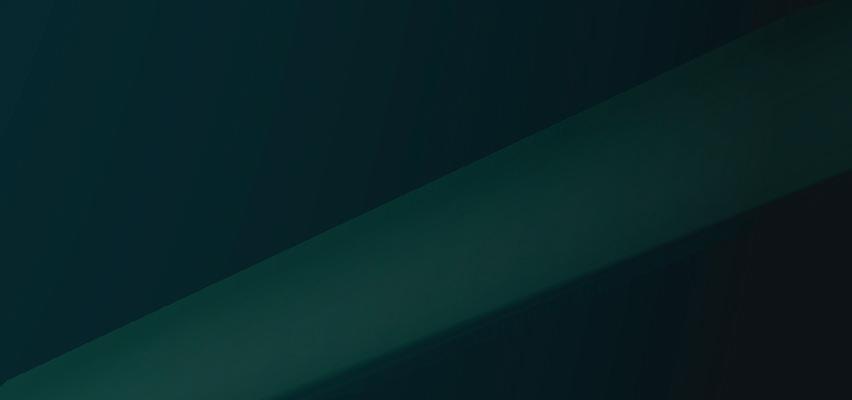
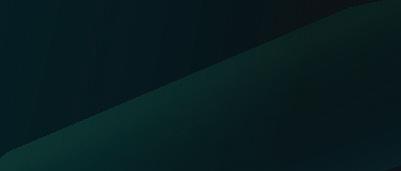
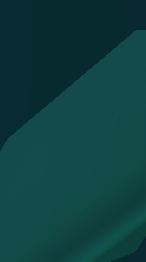

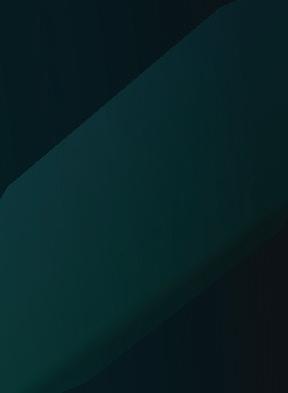
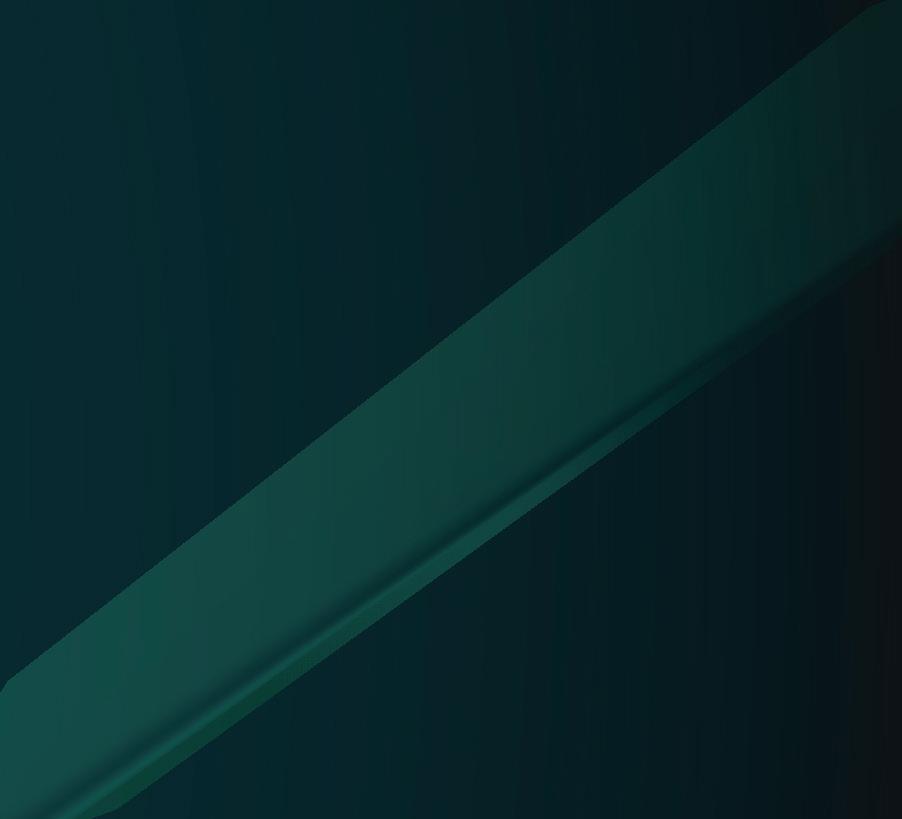
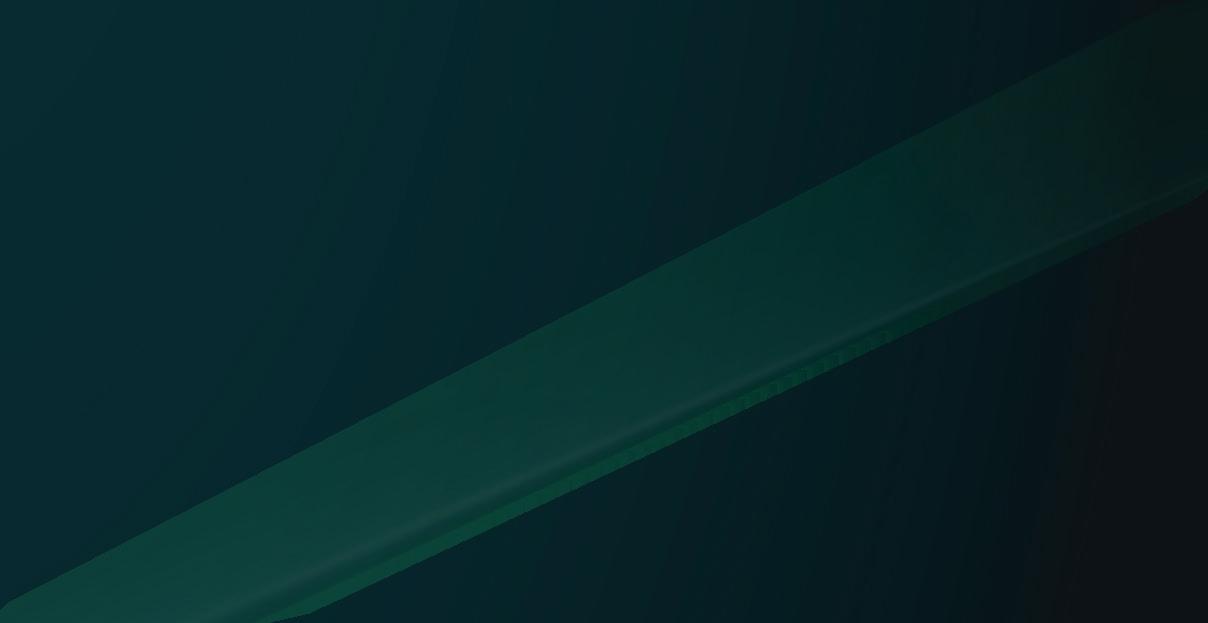
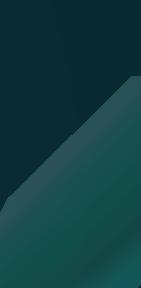
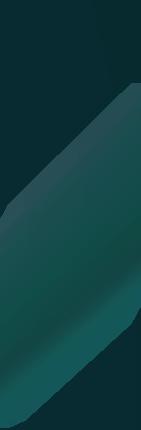

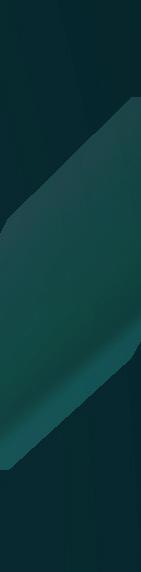
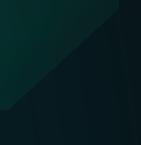
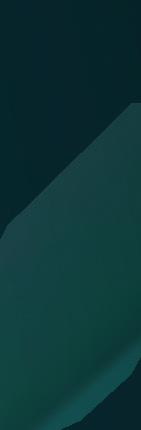
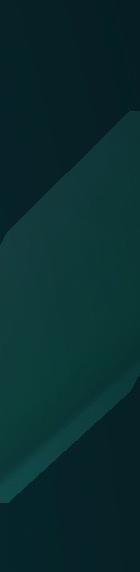
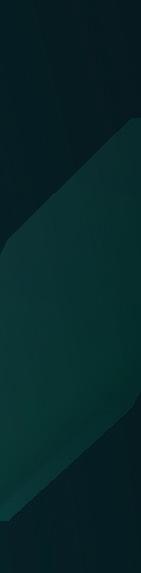
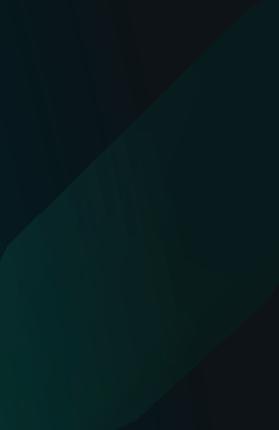
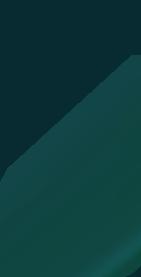

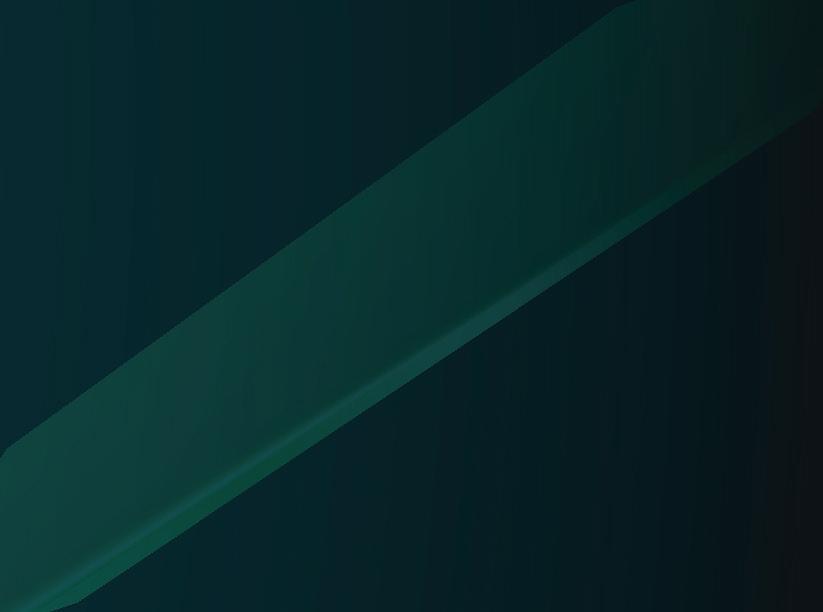

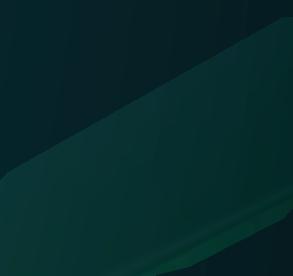
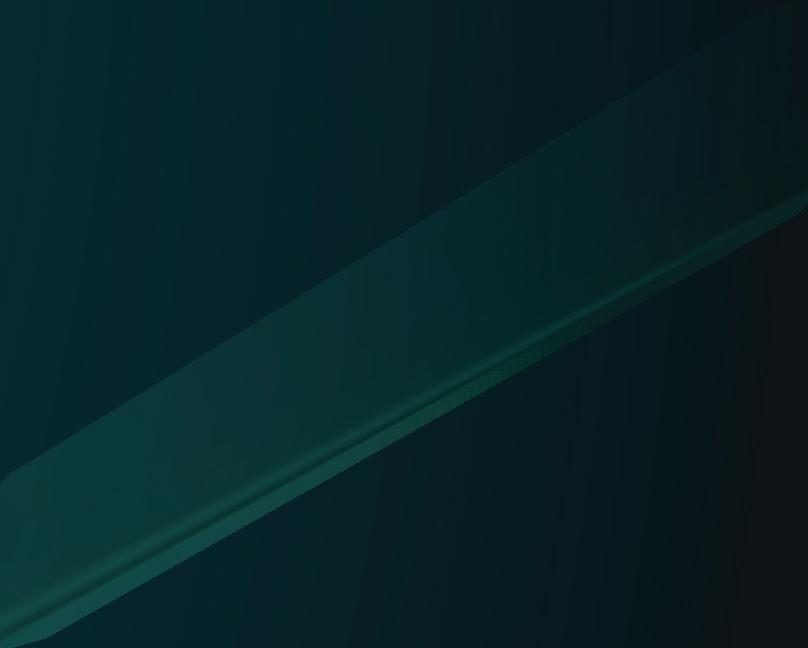

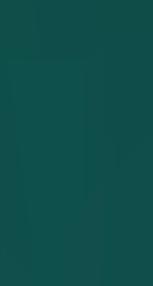
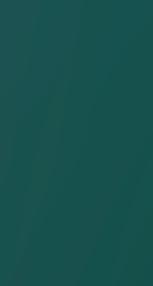
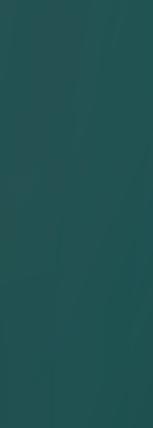
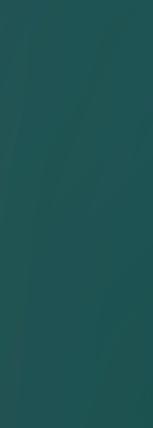

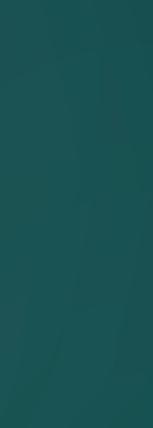
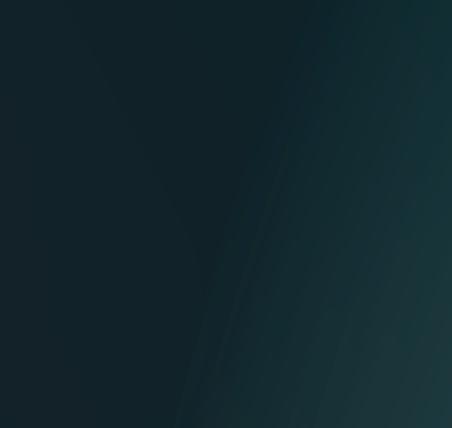

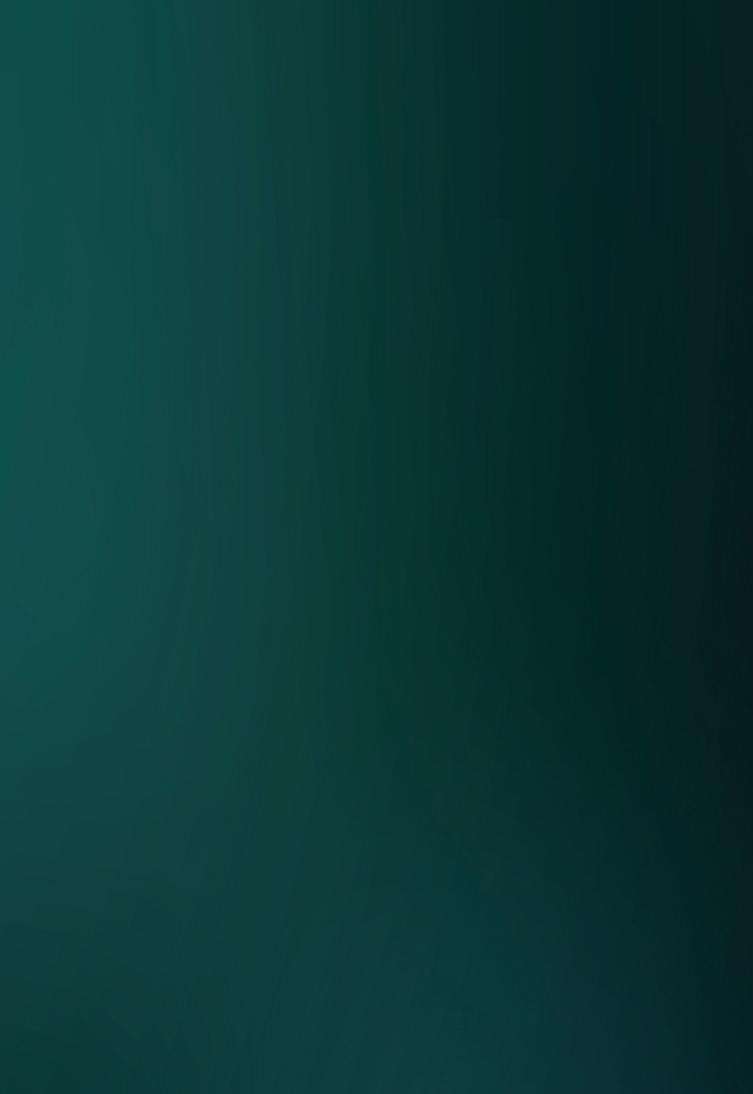
DEPARTMENTS
FEATURES
12 PROJECT DEVELOPMENT
A Mountain of Ambition
Driven by a stream of waste with nowhere to go, Aspen Wood Products is producing fuel pellets and other products for local markets through its spin-off business, Mesa Verde Pellets.
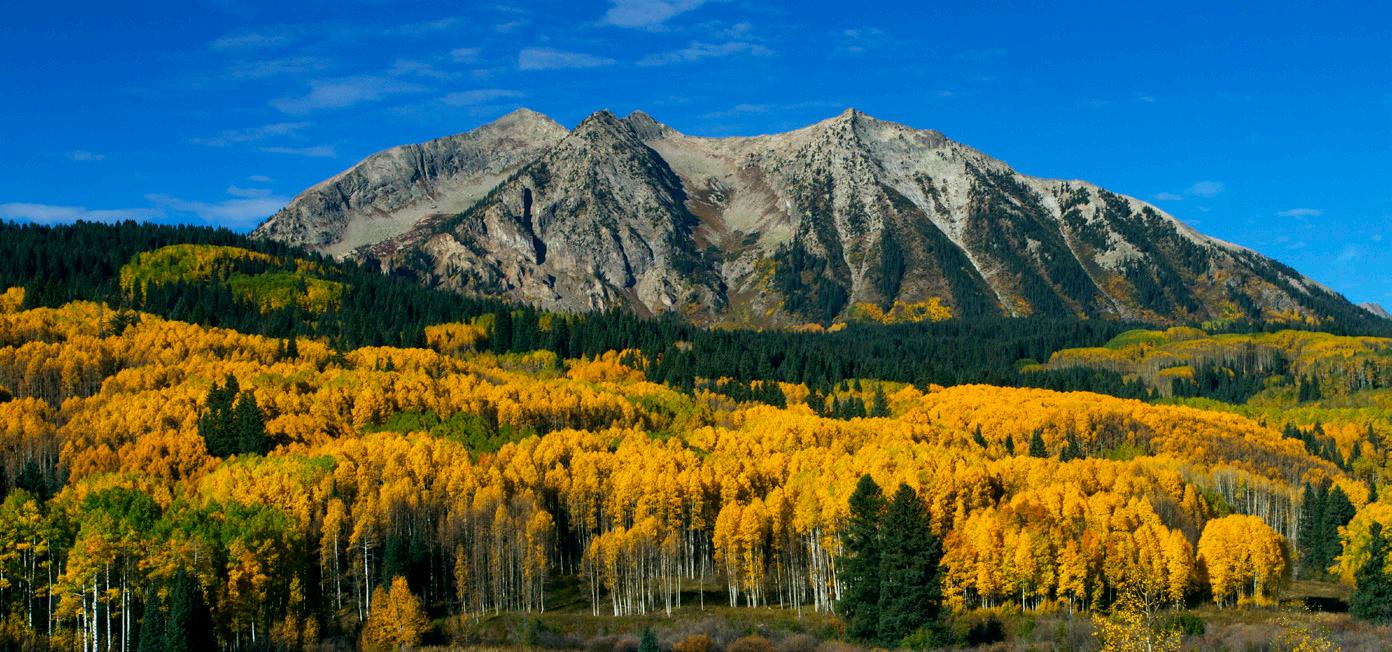
19 FIRE & EXPLOSION

Innovations in Fire & Explosion Protection
Pellet Mill Magazine conducts a Q&A with five industry experts about the latest trends in fire and explosion prevention and mitigation, innovative products and what they believe should be future priorities.
By Keith Loria24 PROFILE
From the History Books
Bruce Lisle, former owner of one of the longest-running fuel pellet plants in North America, talks about the early industry, the plant’s history and how he came to buy it.
By Anna SimetCONTRIBUTION
28 TECHNOLOGY
Fiber Optic Linear Heat Detection: Enhanced Fire, Hotspot Sensing
Fiber optic linear heat detection is highly sensitive and can detect heat changes before they become a fire hazard.
By Jaedyn MatsallaBack on the ENplus Track
This week, we received notice from the United Kingdom Pellet Council that the government’s temporary suspension of ENplus wood pellet standards would expire Nov. 22. Come then, U.K. traders and customers will be required to move back to using all ENplus certified pellets. Most of you reading this likely know the reason for implementing the suspension, and we have covered this story as it has evolved. In short, the requirement was waived due to Russia’s invasion of the Ukraine, via a complete ban of all wood products coming from Russia. This meant 3.5 million metric tons of pellets flowing into the European supply chain was no longer allowed, prompting end users to look elsewhere due to this shortfall—and not all sellers with tonnage to spare were ENplus certified, for a variety of reasons. The UKPC stated in the memo that the suspension served its purpose, as “The U.K.’s wood pellet and biomass for heating sectors have witnessed minimal disruption to consumer supply, especially over the winter months when customer demand is usually greater.” While there have been assertions that some Russian wood pellets were rerouted, repacked and ultimately sent where banned, producers across the globe were able to temporarily participate in that market—including in the U.S.—at least for a while. Mark Lebus, chair of the UKPC, explained, “Given the scale of this reduction and the speed in which sanctions were applied, having no interruption to supply for U.K. biomass boiler owners was a major achievement and something which couldn’t be done by fossil fuel suppliers who continue to import Russian gas, oil and coal.”
Moving onto content in this issue of Pellet Mill Magazine, our themed stories include a Q&A with five fire and explosion technology experts on the evolution of the sector and their favorite products, as well as aspects they believe the industry should improve. Check out “Innovations in Fire & Explosion Protection” by freelance writer Keith Loria on page 19. As well, you’ll find a contribution article focused on fiber optic linear heat detection and its benefits to the wood pellet industry on page 28, written by AP Sensing.
Additional features in this story include a profile story on Mesa Verde Pellets, a Mancos, Colorado-based wood pellet operation implemented by Aspen Wood Products. They're just commencing startup at the plant, an endeavor the company decided to pursue when the offtaker of its sawdust went away. Staff writer Katie Schroeder chatted with President and CEO David Sitton about the driving force behind the project, as well as challenges and future plans.
Finally, I got a brief industry history lesson when I chatted with Bruce Lisle of Lignetics (who sold Energex to the company a few years ago) for our page-24 feature, “From the History Books.” During our conversation, he told me about how he got into the industry, the history of Energex’s Lac-Mégantic, Quebec, pellet plant, and a little about the domestic heating industry’s roots and early pioneers. While this is quite a boiled down version of industry beginnings, I hope you learn something new.
On a different and closing note, we’re looking for new guests for our podcast. If you’re interested, drop me a line—would love to hear from you.
EDITORIAL EDITOR
Anna Simet | asimet@bbiinternational.com
ONLINE NEWS EDITOR
Erin Voegele | evoegele@bbiinternational.com
STAFF WRITER
Katie Schroeder | katie.schroeder@bbiinternational.com
DESIGN
VICE PRESIDENT, PRODUCTION & DESIGN
Jaci Satterlund | jsatterlund@bbiinternational.com
GRAPHIC DESIGNER
Raquel Boushee | rboushee@bbiinternational.com
PUBLISHING & SALES
CEO
Joe Bryan | jbryan@bbiinternational.com
PRESIDENT
Tom Bryan | tbryan@bbiinternational.com
VICE PRESIDENT, OPERATIONS/MARKETING & SALES
John Nelson | jnelson@bbiinternational.com
SENIOR ACCOUNT MANAGER/BIOENERGY TEAM LEADER
Chip Shereck | cshereck@bbiinternational.com
ACCOUNT MANAGER
Bob Brown | bbrown@bbiinternational.com
CIRCULATION MANAGER
Jessica Tiller | jtiller@bbiinternational.com
MARKETING & ADVERTISING MANAGER
Marla DeFoe | mdefoe@bbiinternational.com
2023 Int’l Fuel Ethanol Workshop & Expo
JUNE 12-14, 2023
CHI Health Center, Omaha, Nebraska
From its inception, the mission of this event has remained constant: The FEW delivers timely presentations with a strong focus on commercial-scale ethanol production—from quality control and yield maximization to regulatory compliance and fiscal management. The FEW is the ethanol industry’s premier forum for unveiling new technologies and research findings. The program is primarily focused on optimizing grain ethanol operations while also covering cellulosic and advanced ethanol technologies.
(866) 746-8385 | FuelEthanolWorkshop.com
2023 Biodiesel Summit: Sustainable Aviation Fuel & Renewable Diesel
June 12-14, 2023
CHI Health Center, Omaha, Nebraska
The Biodiesel Summit: Sustainable Aviation Fuel & Renewable Diesel is a forum designed for biodiesel and renewable diesel producers to learn about cutting-edge process technologies, new techniques and equipment to optimize existing production, and efficiencies to save money while increasing throughput and fuel quality. Produced by Biodiesel Magazine, this world-class event features premium content from technology providers, equipment vendors, consultants, engineers and producers to advance discussion and foster an environment of collaboration and networking through engaging presentations, fruitful discussion and compelling exhibitions with one purpose, to further the biomass-based diesel sector beyond its current limitations.
(866) 746-8385 | BiodieselSummit.com
2023 Carbon Capture & Storage Summit
June 12-14, 2023
CHI Health Center, Omaha, Nebraska
Capturing and storing carbon dioxide in underground resivoirs has the potential to become the most consequential technological deployment in the history of the broader biofuels industry. Deploying effective carbon capture and storage at biofuels plants will cement ethanol and biodiesel as the lowest carbon liquid fuels commercially available in the marketplace. The Carbon Capture & Storage Summit will offer attendees a comprehensive look at the economics of carbon capture and storage, the infrastructure required to make it possible and the financial and marketplace impacts to participating producers.
(866) 746-8385 | FuelEthanolWorkshop.com
2024 Int’l Biomass Conference & Expo
March 4-6, 2024
Greater Richmond Convention Center Richmond, VA
Now in its 17th year, the International Biomass Conference & Expo is expected to bring together more than 900 attendees, 160 exhibitors and 65 speakers from more than 25 countries. It is the largest gathering of biomass professionals and academics in the world. The conference provides relevant content and unparalleled networking opportunities in a dynamic business-to-business environment. In addition to abundant networking opportunities, the largest biomass conference in the world is renowned for its outstanding programming—powered by Biomass Magazine–that maintains a strong focus on commercial-scale biomass production, new technology, and near-term research and development. Join us at the International Biomass Conference & Expo as we enter this new and exciting era in biomass energy.
(866) 746-8385 | BiomassConference.com
Codifying Wood Pellet Heating’s Renewable Bona Fides
BY TIM PORTZIn the past year and a half, the Pellet Fuels Institute has found itself in the vexing position of testifying before two different committees within the International Code Council, defending the renewable nature of wood pellets for home heating. On its homepage, the ICC says it is a “leading global source of model codes and standards and building safety solutions that include product evaluation, accreditation, technology, training and certification.” ICC’s model codes serve as a reference point for municipal, state and federal regulators in the development of their own building codes. The council makes recommendations on the items you would expect to fall within the purview of commercial and residential building codes, such as guidance on the R-value requirements of insulation to the moisture barrier requirements in home foundations. Increasingly, however, the ICC is pushing beyond these traditional areas of focus and ratcheting up its energy efficiency and sustainability efforts with an eye on driving carbon out of the world’s residential and commercial building stock. While those ambitions are honorable and the work is important, the opportunity to get some things wrong, particularly the treatment of wood heating within the International Energy Conservation Code, is very real. Specifically, the question before both the commercial and residential committees within the International Energy Conversation Code is what kinds of biomass-derived energy would be considered renewable for new residential construction. Increasingly, devisers of building codes are looking for guidance on how to include renewable requirements in their code structure for new construction. It isn’t difficult to imagine communities requiring a certain minimum level of renewable energy production and consumption to be built into the home. To support that, there must be a list of technologies that do and do not qualify. The code currently identifies “Energy derived from solar radiation, wind, waves, tides, landfill gas, biogas, biomass or extracted from hot fluid or steam heated within the earth” as technologies that can be considered. Believing that “biomass” was far too broad, the New Buildings Institute, a committee member, introduced new language to further clarify biomass and exclude wood and wood-derived fuels. Specifically, NBI suggested revised language changed “biomass” to “biomass waste” adding a definition of biomass waste that stated, “but excludes wood and wood-derived fuels (including black liquor) biofuels, feedstock, biodiesel
and fuel ethanol.” With the adoption of this language, anyone using the ICC’s International Energy Efficiency Code as a reference for their own renewable energy requirements in building codes would similarly exclude wood and wood pellet heating. The Pellet Fuels Institute cannot let language like this be forwarded for consideration without objection.
The motivations for the introduction of this amended language stems from a misunderstanding of the domestic wood pellet industry mixed with with a heaping teaspoon of the anti-biomass rhetoric the industry has been fighting for years. During a committee hearing, proponents of the language stated that “we need to stop burning things for energy” and that the wood pellet sector was resulting in “deforestation in the Southeast [U.S.].” The deforestation assertion has been and will continue to be disproven by growth versus drain data. Moreover, wood pellets for home heating are not manufactured using softwood fiber from the Southeast, but rather, from hardwood residues from sawmills and secondary wood product manufacturing sites all across this country.
The Pellet Fuels Institute made this point and numerous others in public comment forums and will continue to do so on behalf of its manufacturers. Most bothersome of all is that this proposed language and definition welcomes biomass energy sources that aren’t even relevant for a home—like sludge waste and agricultural crop byproducts—but slams the door on a proven (and yes, renewable) technology that millions of American households are using successfully today.
The good news is this proposed language was rejected, and before it was it galvanized, the impressive ad-hoc group of wood heat defenders who won this battle recognized that the effort to defend wood heating as a renewable and sustainable technology will be a much longer campaign, indeed.
Author: Tim Portz Executive Director, Pellet Fuels Institute tim@pelletheat.org www.pelletheat.org

Pellet News Roundup
The U.S. EIA released its January Monthly Densified Biomass Fuel Report on April 3, with data collection including 79 operating manufacturers of densified biomass fuel. These manufacturers had a total production capacity of 13.05 million tons per year and collectively had an equivalent of 2,544 full-time employees.
In January 2023, the monthly respondents purchased 960,000 tons of raw biomass feedstock, compared to 1.55 million tons in January 2022. Production was at 910,000 tons of densified biomass fuel, up approximately 120,00 tons from the same month of last year. Sales were at 650,000 tons of densified biomass fuel, down from 740,000 tons in January 2022. Domestic sales in January 2023 totaled 150,000 tons and averaged $210.94 per ton, compared to 110,000 tons at $195.19 per ton last year. Exports in January 2023 were approximately 500,000 tons averaging $191.31 per ton, down from 630,000 tons but up in price from $168.38 per ton from the same reporting period last year.
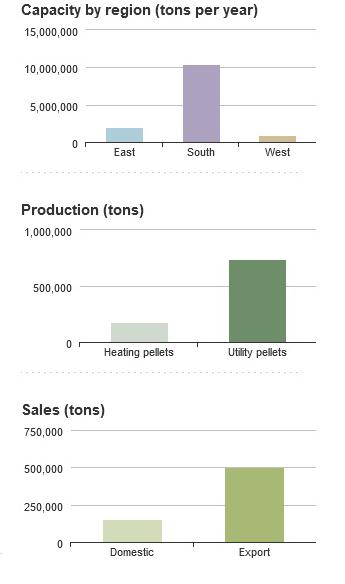
The EIA noted that some totals in the report may be relatively smaller for January, as the agency withheld some values to avoid disclosing individual company data.
The European Commission on March 30 reached a provisional agreement on the Renewable Energy Directive III (RED III) that aims to increase targets for renewable energy. It also includes provisions to strengthen bioenergy sustainability criteria. The provisional agreement raises the European Union’s binding renewable target for 2030 to a minimum of 42.5%, up from the current target of 32%. Negotiators also agreed that the EU would aim to reach 45% renewables by 2030. For bioenergy, the agreement strengthens bioenergy sustainability criteria in line with the increased climate and biodiversity ambition of the European Green Deal. In the future, the criteria will apply to smaller installations of 7.5 MW or above, rather than the 20 MW threshold in place as part of the current directive. The agreement includes provisions to ensure that forest biomass is not sourced from certain areas with a particular importance from a biodiversity and carbon stock perspective. In addition, wood biomass will have to be used according to its highest economic and environmental added value. Financial support will be banned for energy produced through the use of saw logs, veneer logs, industrial grade roundwood, and stumps and roots. The U.S. Industrial Pellet Association is welcoming the agreement, calling it “positive for the climate, forests and the continued contributions of sustainable biomass toward supporting both.”
Enviva Inc. issued a statement on March 16 thanking the Mississippi Department of Environmental Quality ’s permit board for the unanimous approval of the construction permit of Enviva’s Bond, Mississippi, facility. According to Enviva, the permit was issued after an extensive review process that included a public comment period, a well-attended public hearing and numerous public comments. The proposed facility will be designed to produce approximately 1.2 million oven dried tons per year of wood pellets and will be equipped with maximum achievable control technologies to curb emissions to the greatest extent possible.
In a subsequent announcement, Enviva said that John Keppler, who temporarily stepped down as chairman and CEO to address a health condition, has returned to the company as executive chairman. Thomas Meth will continue to lead the company as president and CEO, and the company’s interim chairman, Ralph Alexander, will transition to the role of lead independent director of the board.
The U.S. exported 632,043 metric tons (MT) of wood pellets in February, down from 637,518 MT the previous month, but up nearly 3,400 tons from February 2022, according to data released by the USDA Foreign Agricultural Service on April 5. The U.S. exported wood pellets to approximately 12 countries in February. The U.K. was the top destination for U.S. wood pellet exports at 405,390 MT, followed by the Netherlands at 144,394 MT and Japan at 76,895 MT. The value of U.S. wood pellet exports reached $117.99 million in February, up from both $114.66 million in January and $82.71 million in February of last year. Total U.S. wood pellet exports for the first two months of this year reached 1.27 million MT at a value of $232.65 million, compared to 1.28 million MT exported during the same period of last year at $185.36 million.
As part of its goal of investing in rural America, the BidenHarris Administration announced on April 6 that $33.7 million from President Biden’s Bipartisan Infrastructure Law will fund projects to strengthen the wood products economy and promote sustainable forest management. The program is focused on forest restoration byproducts such as small-diameter timber and woody biomass with little market value, and provides $29 million to establish, reopen or improve businesses that purchase and process these byproducts from projects on federally managed lands or tribal lands at risk of wildfire, insects and disease. More than twothirds of the funded businesses will use byproducts from forest
restoration and hazardous fuels reduction on landscapes identified in the Forest Service’s Wildfire Crisis Strategy.
The USDA on March 31 announced more than $1 billion in grants available under the Rural Energy for American Program to help agricultural producers and rural small businesses invest in renewable energy systems and make energy efficiency improvements. The funding was allocated by the Inflation Reduction Act, which provides more than $2 billion in funds for the REAP program through 2031. The USDA is offering $1.055 billion through six quarterly competitions that will be held throughout the remainder of 2023 and 2024.
The REAP program was first created by the 2008 Farm Bill to award grants and loan guarantees to agricultural producers and rural small businesses to purchase and install renewable energy systems and make energy efficiency improvements to their operations. Eligible renewable energy systems include renewable biomass, including anaerobic digesters and biogas, wind, solar, small hydro-electric, ocean, geothermal or hydrogen derived from any of those sources. According to the USDA, numerous changes are being implemented to the program with inclusion of funds from the IRA. Changes include increasing the maximum grant size from $250,000 to $500,000 for energy efficiency products, and from $500,000 to $1 million for renewable energy systems. The agency is also raising the federal share to 50% for all energy efficiency projects, all zero-emission renewable energy projects, and all projects in designated energy communities and projects submitted by eligible tribal entities. All other projects are eligible to apply for grants of up to 25% of the total project costs.
The USDA is also taking action to ensure that small projects have a fair opportunity to compete for funding by setting aside at least 20% of the available funds until June 30 of each year for grant requests of $20,000 or less, including the grant portion of a combined grant and loan guarantee request.
The United Kingdom Pellet Council recently released a notice indicating that the government's decision last year to temporarily suspend the need for large U.K. users to only use ENplus A1 standard wood pellets will come to an end on Nov. 22. The suspension was part of a complete ban of all wood products (including pellets) coming from Russia since April 2022, which removed up to 3.5 million metric tons of pellets from the European supply chain.
PODCAST PREVIEW PLAY WITH BRANDI COLANDER, ENVIVA
Season 2, Episode 6, of the Biomass Magazine podcast featured Brandi Colander, senior vice president and chief sustainability officer (CSO) at Enviva. Colander assumed the role in January, and is charged with maintaining and enhancing Enviva’s leadership in sustainability and environmental stewardship. Colander is armed with extensive policy, sustainability and external affairs experience, most recently leading the enterprise sustainability portfolio at WestRock as chief sustainability officer. Colander holds a bachelor’s degree in urban and environmental planning from the University of Virginia, a Juris Doctor from Vermont Law School, and a master’s degree in environmental management from Yale University. Colander joined the podcast to discuss the current landscape of the biomass energy industry, misconceptions, trends and more.

PMM: In our industry, there are a lot of misconceptions. What do you wish people understood about biomass?
Colander: I would start with tree and forest management practices. I encourage people to look outside of Enviva to understand those, and look at academic institutions, organizations like the U.S. Endowment … Preferred by Nature … there are many organizations, like the Society of American Foresters—so many that don’t have a business model around advocacy; their business
model is around conversation. If you really want to understand the sustainability of technologies that require natural resources, you have to get to know the conservation organizations that do this work every day. And I say this having actually spent time in advocacy organizations and have tremendous respect for them. I am also fully appreciative of the work conservation organizations do with businesses to support scaled opportunities to provide resources to customers in a thoughtful way ... I would go back to early education around forest management practices. If you look around the country with what’s happening with wildfire season, it’s devastating. A lot of that is because we have unmanaged forests. There is brush that’s easy to catch flame, and now it’s completely uncontrolled. One of the things that’s exciting about a company like Enviva is that we have effectively created a market for these resources in the forest that includes brush, slash, trees that are small in a diameter and would have absolutely no utility at a sawmill ... those are now resources that, instead of getting burned in open fields, now actually have another life and currency. It's helpful for forest management practices, and it’s also incredibly helpful at a time when the geopolitical landscape has, in a really devastating way, changed the energy needs abroad.
PMM: For those interested in this space that you’re in, or for current CSOs, do you have any thoughts or advice to offer them?
Colander: I think we’re still searching for community. [In order to] stay current, there is a support system that’s necessary for CSOs, because frankly, people are passionate about the issues and believe it gives them a license to think they know what you should be doing all the time—perhaps not realizing that you’ve been thoughtful about your role, that you have a remit, and that there is accountability around that remit. And I think there is some creep around mission with sustainability practitioners that can be really challenging. Sometimes, you’re fitting the mold of a processor, sometimes you’re shaping comms and narratives ... I think most CSOs would be well served to figure out what their support system looks like to develop their community. I would also encourage them to find and very actively seek opportunities to stay engaged in the messaging and the conversations about the work they’re shepherding forward. These things change a lot, but the core tenants don’t. I think staying engaged and relevant however you see fit is one thing that’s important to do because you want to show that your company is considerate of change—a lot of this does deal with change—but is not willing to change so much that you can’t count on commitments that are made, relationships that are established, etcetera ... At the end of the day, what you’re really trying to do is
better align those negative externalities, make sure they’re adequately accounted for, build credibility, and the last thing I think is really important is developing data management systems that create good guiderails for your company to continue to operate accordingly.
Listen to the rest of the podcast: www.biomassmagazine.com/pages/podcasts
Don't Miss an Episode:
S2
Southwest Colorado is home to a new pellet facility. In the small mountain town of Mancos, which is dubbed the “Gateway to Mesa Verde” due to its proximity to the national park, construction of the plant was ultimately prompted by COVID-19. The result of research, innovation and creativity, the facility turns a waste product with no immediate end market into a valuable coproduct.
Mesa Verda Pellets is now one of three associated businesses including Aspen Wall Wood, a lumber mill that specializes in aspen paneling, and Aspen Wood Products, which makes a wood fiber product called excelsior, or wood wool. CEO and President David Sitton purchased Aspen Wood Products in 2018—formerly Western Excelsior Plant—after it experienced a catastrophic fire the year prior, and rebuilt it. The new pellet mill, colocated with the wood fiber facility in Mancos, is a beneficial solution for wood waste generated at both Aspen Wood Products and Aspen Wall Wood. Sitton explains that this project has been in the works for at least two years. “We anticipate after we get up and running that we will be pretty much a zero-waste operation overall, utilizing all parts of the tree,” he says.
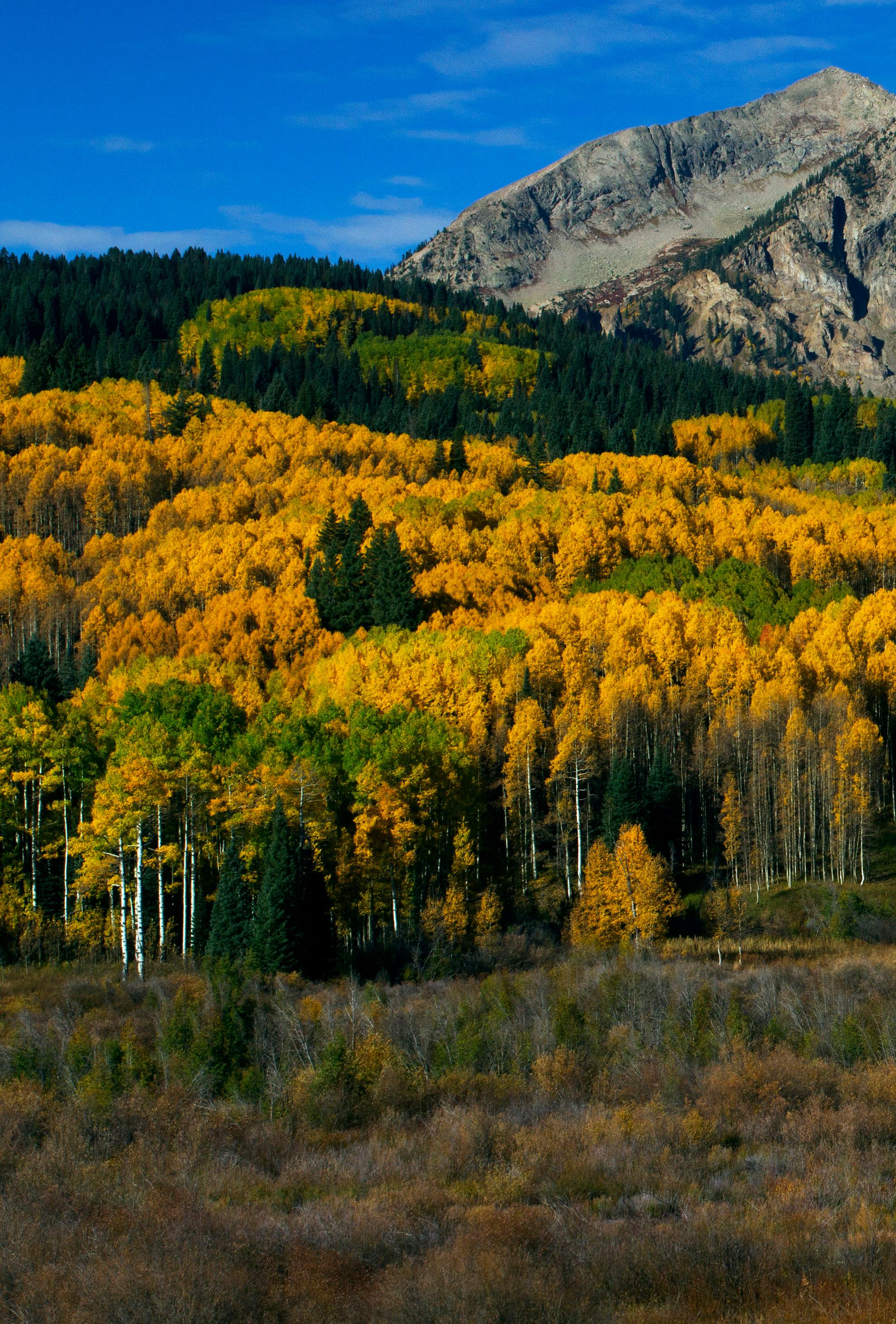
Prior to the COVID-19 pandemic, the company's sawdust found a market as horse bedding at local racetracks, Sitton explains. Unfortunately, the racetracks shut down during the pandemic and failed to recover, leaving the sawdust and wood waste without a place to go—and it began to build up.
When Sitton and his team began considering possible solutions, pellets were not their first resort, but after a fire broke out at the lumber mill—burning 20,000 cords of waste wood—they decided to change course. This led to the acquisition of a mill from a local pellet plant that had also shut down during the pandemic, and company
leadership decided to pursue wood pellet production. Through conversations with Colorado Mill Equipment, however, it was discovered that it was actually a grain pellet mill. The company continued conversations with CME to determine what was needed to make wood pellets. “We then made the decision to go [to] a much bigger scale than what we had initially looked at, and we felt like there was opportunity in the market regionally for us with pellets,” Sitton
says. “And so … it kind of morphed over a little bit of time.”
The feedstock used for the pellets will include sawdust from Aspen Wood Products and Aspen Wall Wood, and products other than logs (POL) including spruce, fir and ponderosa pine that are not suitable for wood fiber or lumber products. “Because we have to harvest that timber, we have log decks that [make us] wonder, ‘What are we going to do with this?’” Sitton says. “We will
Mountain of Ambition
BY KATIE SCHROEDERbegin utilizing all of that timber—chipping and drying—and also turning it into pellets. Our pellet operation is a way to utlize our waste and logs that we kind of were struggling [to know what to do with].”
Aspen Wood Products and Aspen Wall Wood primarily source their feedstocks from public lands, including the San Juan National Forest, Colorado state lands, Utah state lands, northern New Mexico andU.S. State Forest Service lands, along
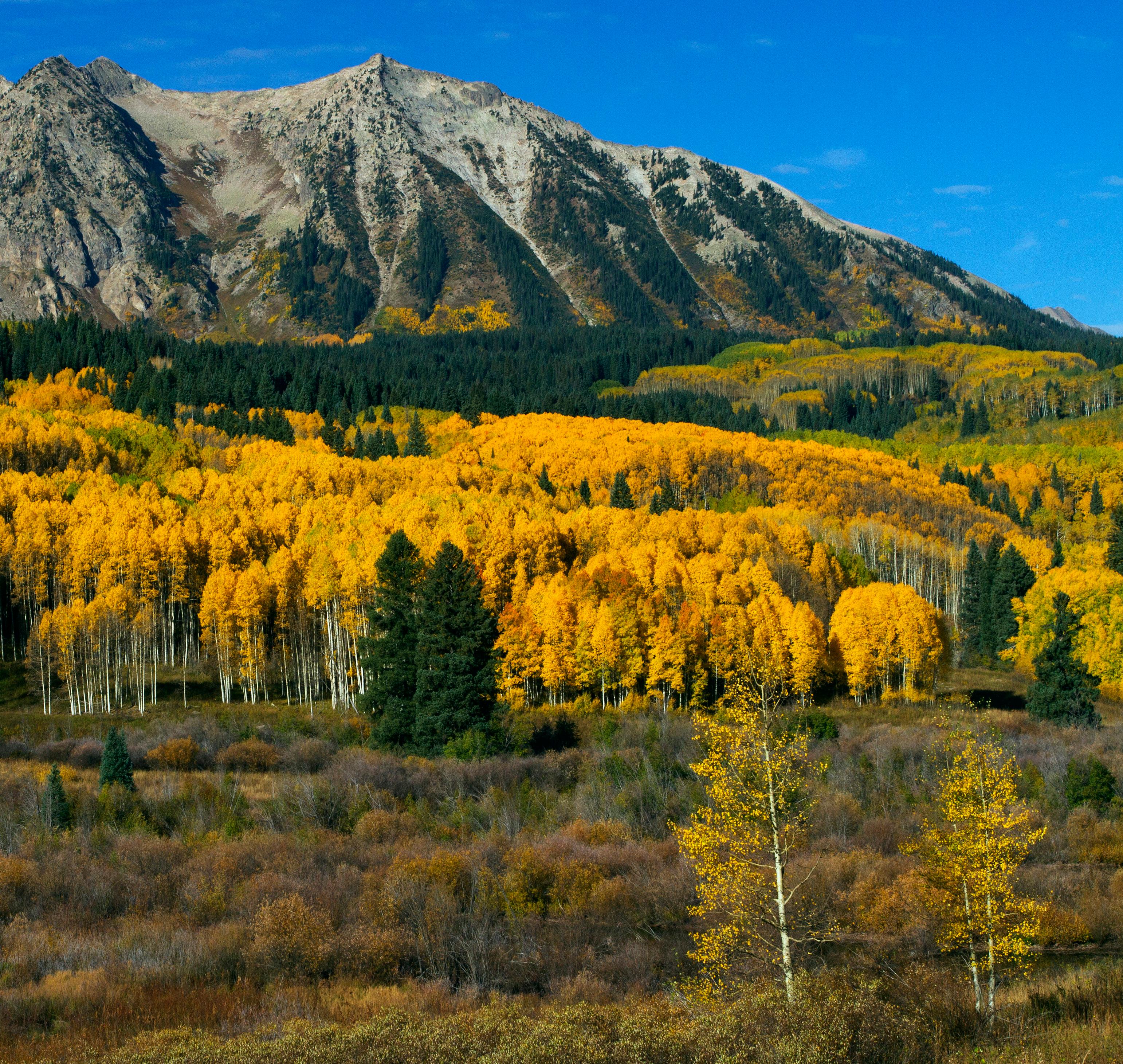
with some sourcing from private ranches. All of the pellet feedstock will be waste wood from Aspen Wood Products process, Sitton explains. MVP will not purchase any sawdust or chips from other sources. Initially, the pellets will only be produced with aspen wood. In the longterm, however, Sitton and his team intend to use POL as well, to create a pellet that blends a variety of wood types. The plant will annually produce 18,000 tons of pel-
lets on a single shift, pushing 30,000 tons on a double shift once markets develop, Sitton explains.
Plant Specs
Building the facility itself required innovation and a blend of new and reused components. MVP uses three pellet mills from Colorado Mill Equipment. Rated at two tons an hour each, the mills are capable of producing six tons per hour “to
start with at least,” Sitton explains. The cooling tower, grinder and cooling system were also purchased new from CME.
Dust collection and fire suppression systems did not need to be bought new due to the fact that Aspen Wood Products already had those installed. “Because of the other products we make in our plant, we already had dust collection and fire suppression in place, both in the building and then for collection of dust off of the other systems that we have in place,” he says. “So, we just extended that and right-sized it for wood pellets.”

The material moving systems and conveying systems in the pellet facility were built in-house and made out of repurposed materials, due to difficulties in attaining
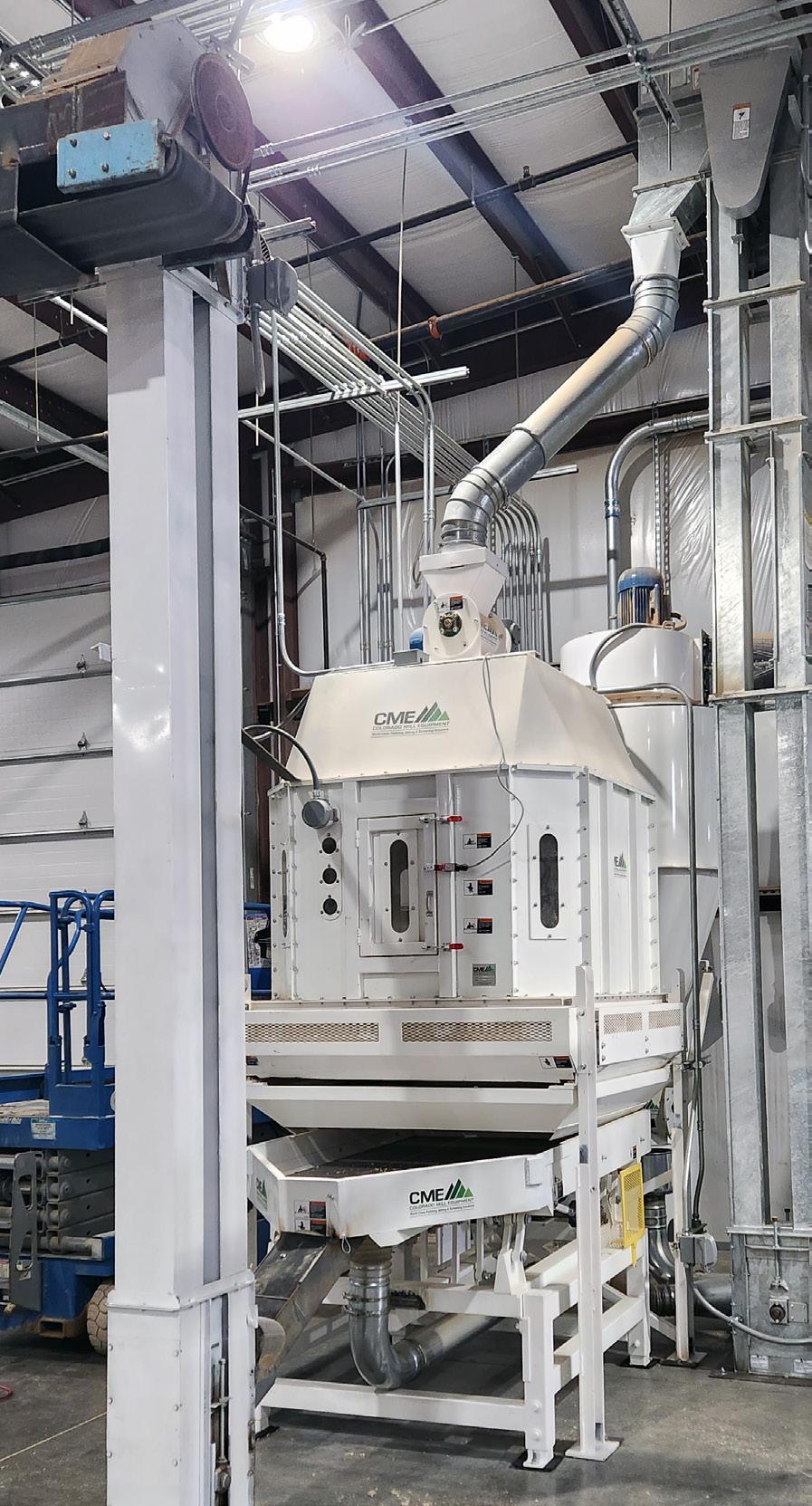

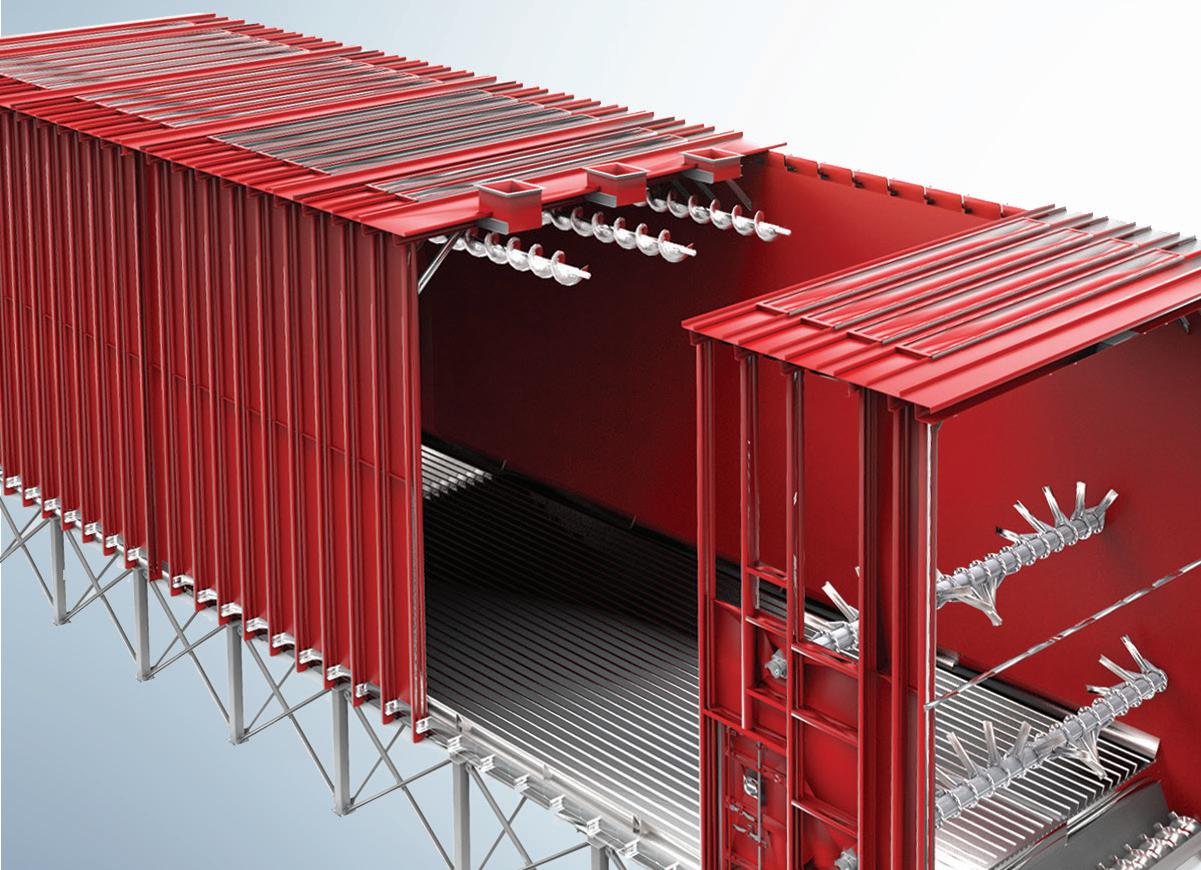
new parts because of supply chain delays. “We’re a pretty typical sawmill in that we reuse equipment, and we have to fabricate and manufacture lots of equipment that we normally use on a daily basis anyway—it’s kind of in our DNA,” Sitton says. He and his team took elements such as motors, motor controls and gear boxes used in their milling system and repurposed them for the pellet line.
MVP is a member of the Pellet Fuels Institute and is in the process of getting their pellets certified with PFI’s Quality Mark, which, according to PFI, indicates pellet producers who receive regular thirdparty plant inspections and lab testing.


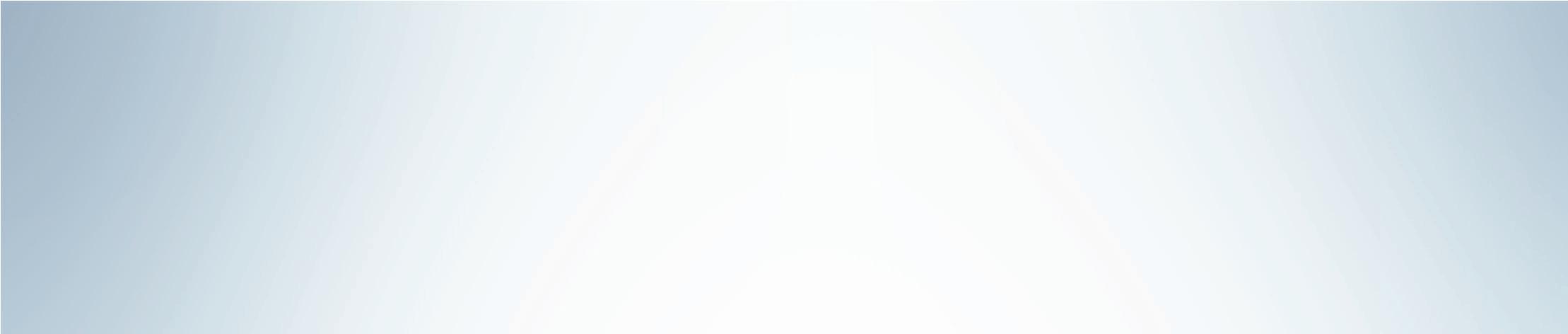
Once

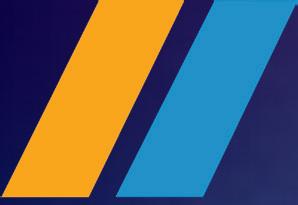
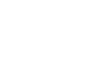
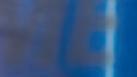
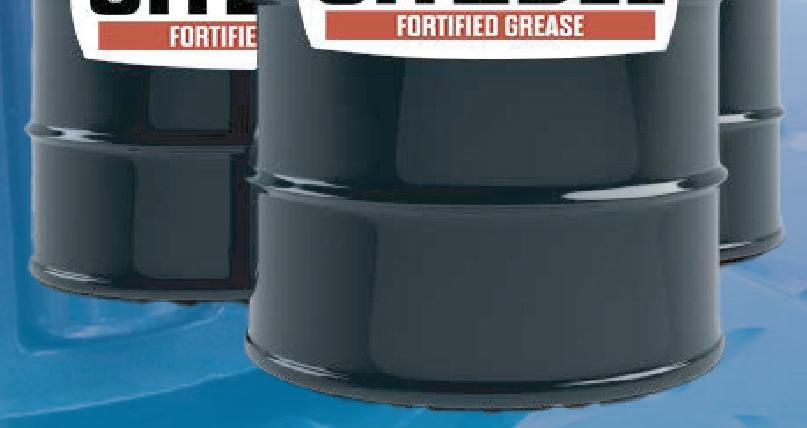
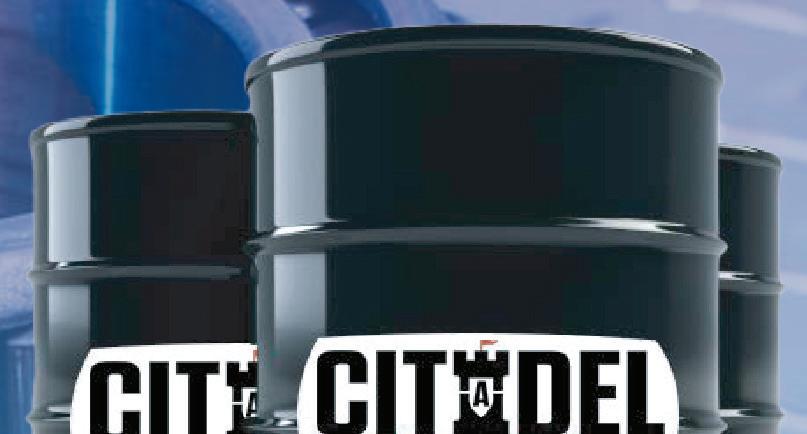
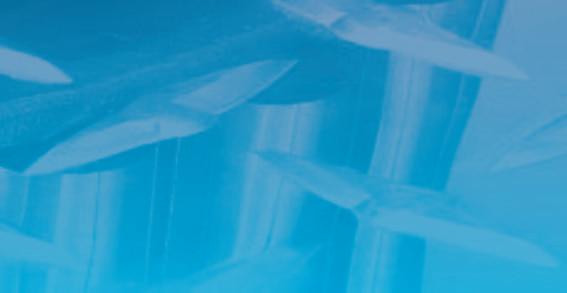
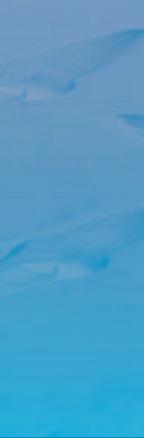


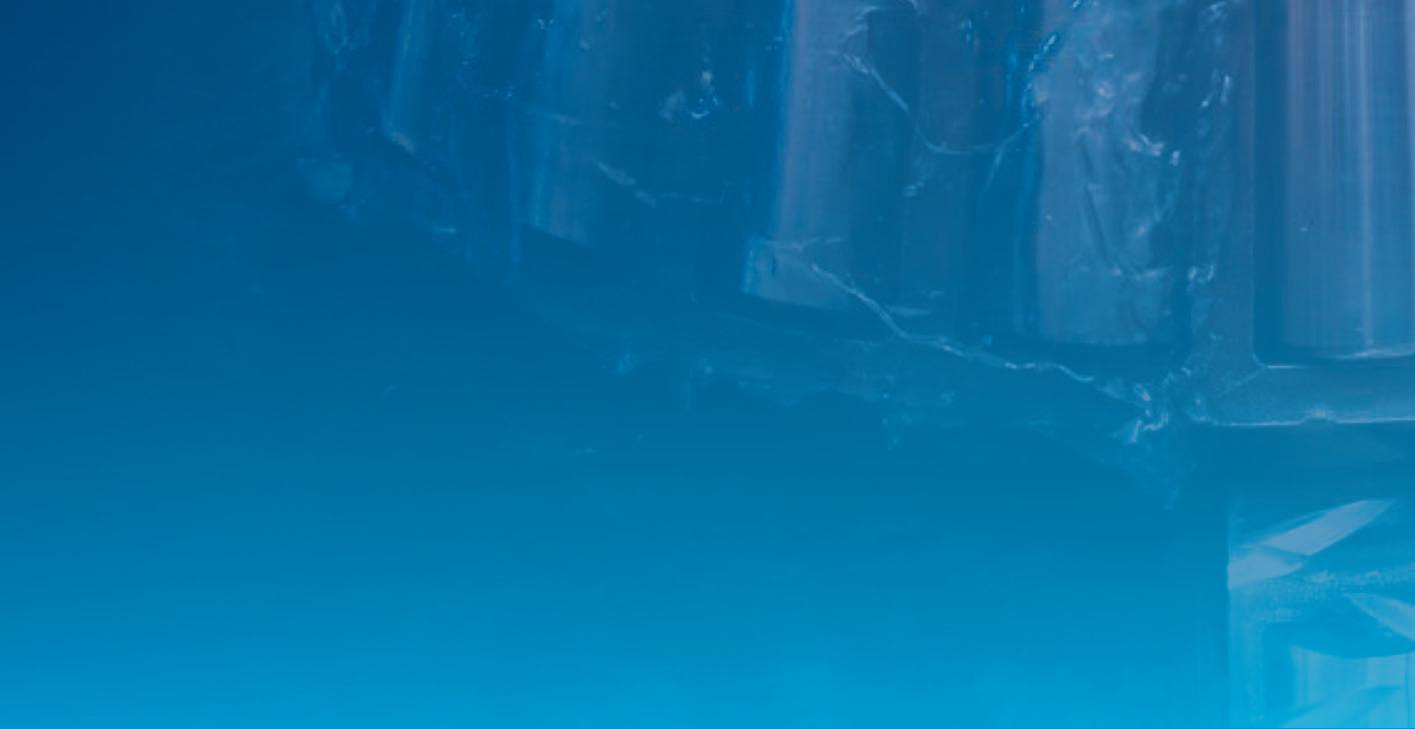
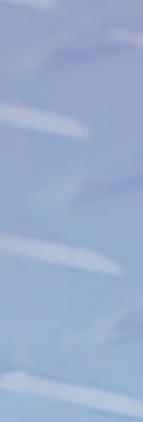
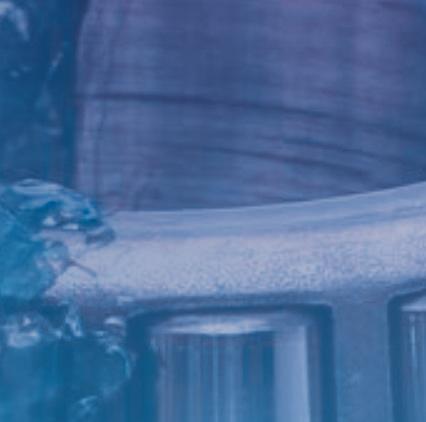
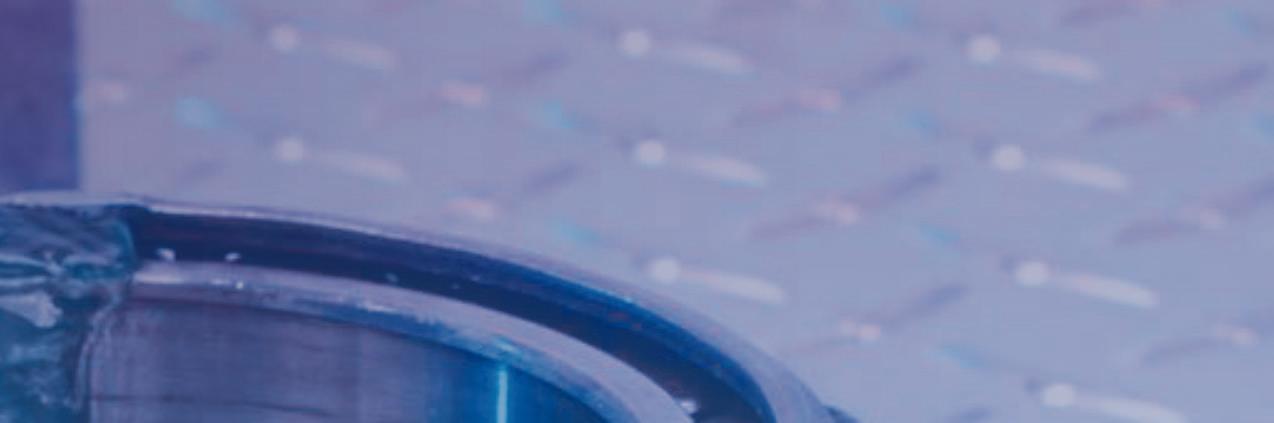

Startup Challenges
As of late March, MVP was still in the process of startup. Sitton explains that there has been some problem-solving to get the plant running properly. Some of the challenges they have been facing with startup include supply chain difficulties, material handling and feedstock moisture. “When we started, we anticipated that making pellets was more of a science than an art, but we’re finding that it may be more art than science,” Sitton says.
The primary feedstock MVP currently uses is aspen waste wood, and one of aspen’s unique qualities is its highly absorptive nature. This quality is great for some of the products Aspen Wood Products makes, including aspen A/C pads that absorb water for air cooling and erosion control prod-
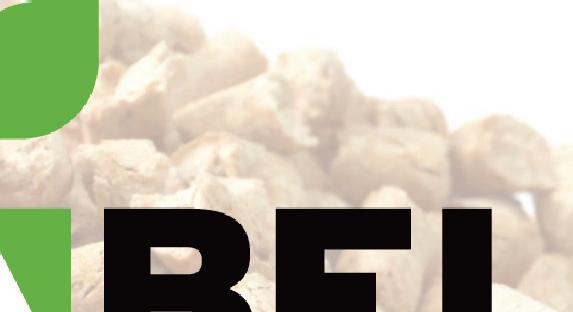
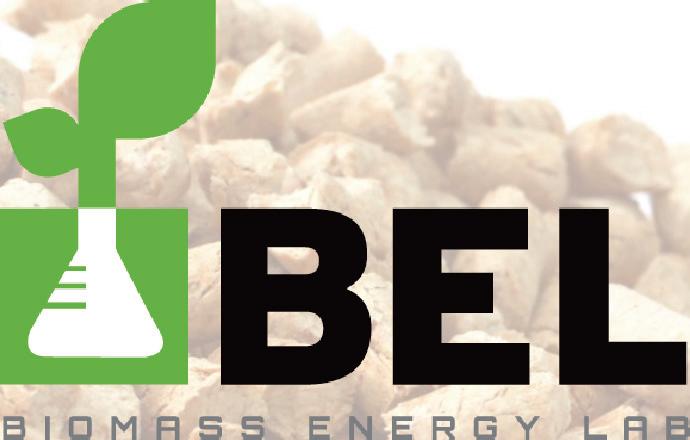
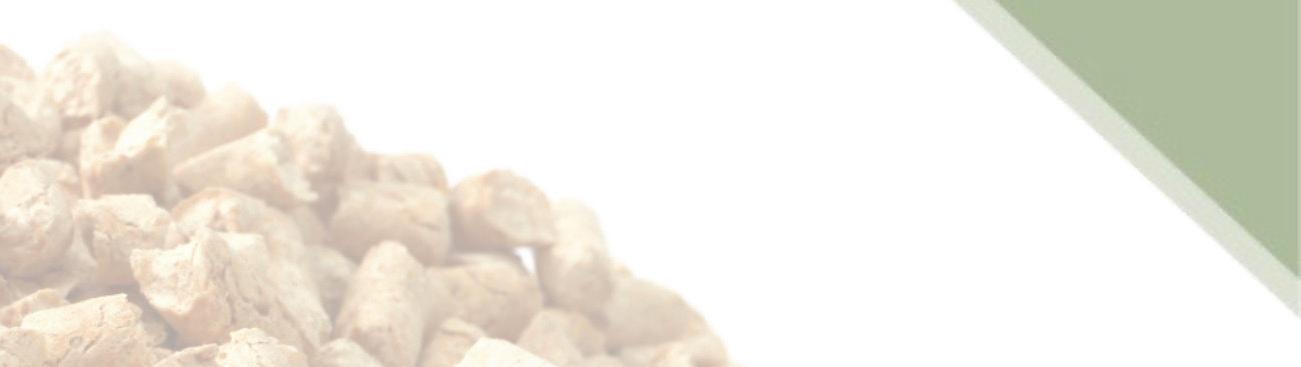

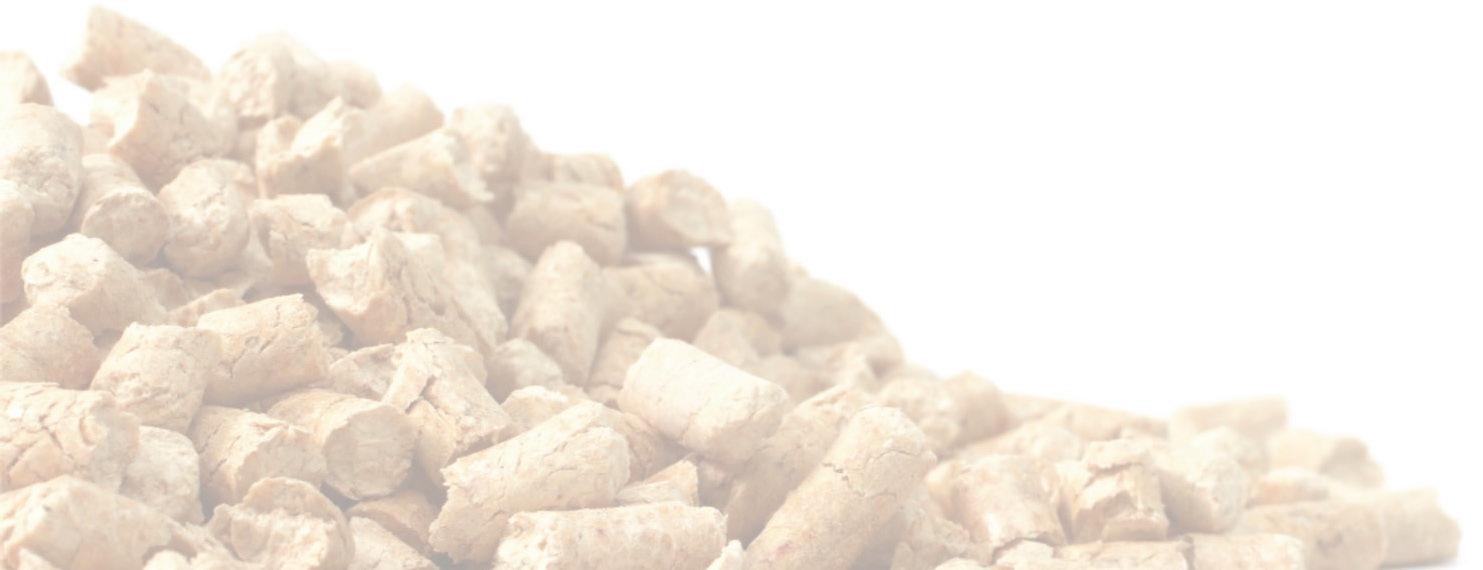
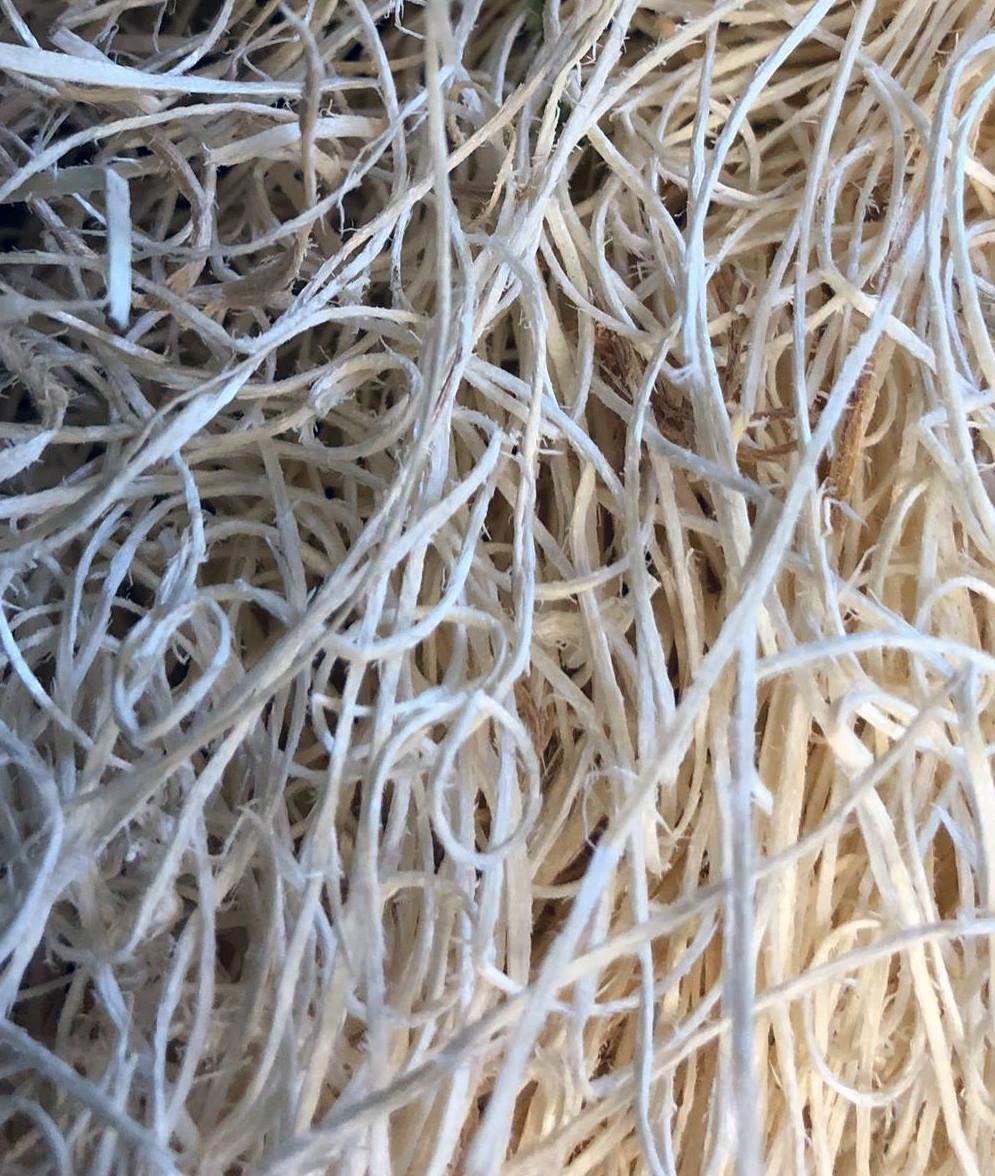
ucts. “By nature, it absorbs and releases moisture, so part of our challenge is that we’re having to remove moisture to be able to make a pellet that’s quality,” Sitton says, explaining that moisture degrades the material’s size after it’s ground, negatively impacting the quality of the final product. He and his team are working to resolve the issue by installing a drying system to keep the aspen at a consistent entry moisture level.
MVP was originally planning on commissioning in summer 2022, but supply chain issues delayed startup until early April 2023. These bottlenecks made it difficult to acquire a variety of components, particularly electrical and plastics.
The material moving system has been the most challenging element of the facility, Sitton explains. The first day the plant was
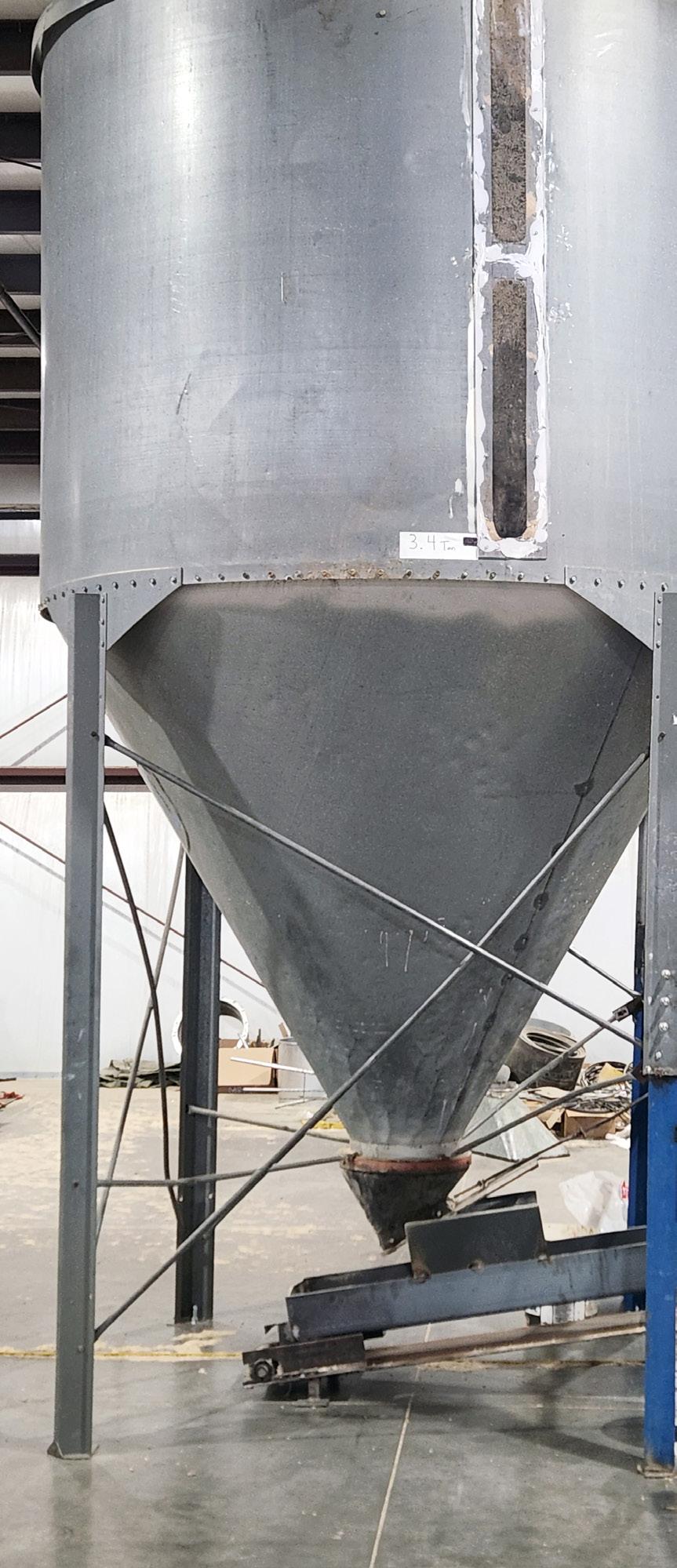
started up, he and his team discovered the material moving system was not working properly. “We had to modify our vents to handle the material better, so that took us a couple of weeks by the time we got parts, motors and bearings, and all the stuff that it required,” he says. The material handling needed for a pellet mill is different than what Aspen Wood Products and Aspen Wall Wood normally use. “We’ve never really ground sawdust,” Sitton says. “We’ve never really moved fine material like that. So, material handling, material moving, specifically for pellets, is [a] different pro cess than we’re accustomed to.”
Phase two of the project will be intro ducing a grinding system that can handle POL into their system. “We peel our logs today to make our products, so we’ve got peeled log decks waiting to make pellets,” Sitton explains. These other wood types would be added to the aspen already in the process and be used to make blended or non-aspen pellets.
Markets and Benefits
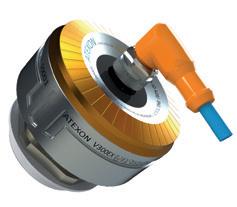

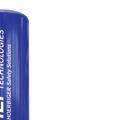
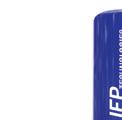
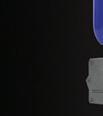
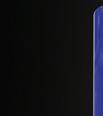

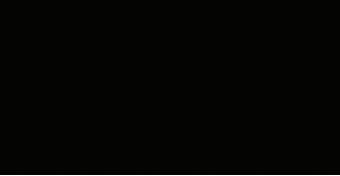
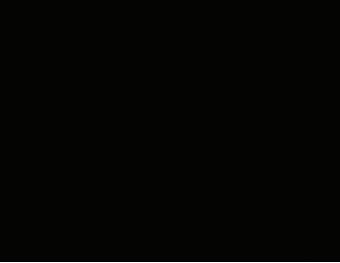

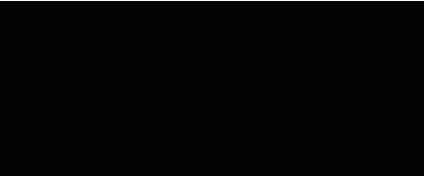
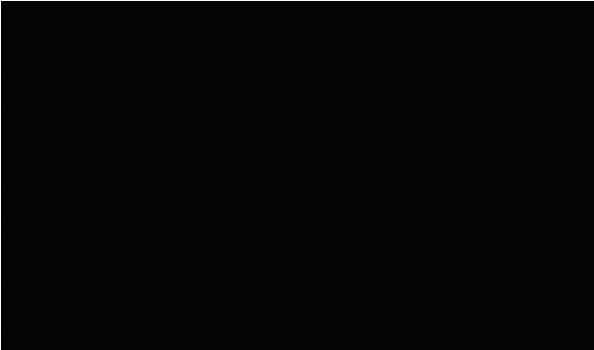
MVP has found a market for both the heating pellets and animal bedding pellets locally, and plans to eventually produce both products. Aspen Wood Products cur rently sells bagged shavings for livestock and pet stores, Sitton explains. “Being a part of those markets already, we intend and expect to begin making a bedding

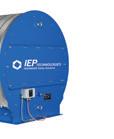
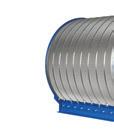
pellet maybe as much of a focus for us as heating pellets are,” he says. “Only yet to be seen is what the markets do as far as getting into business. We are working on labeling, bagging and all of that … specifically for animal bedding—those pellets will be purely aspen pellets.” Down the road, Sitton hopes to also start making cat litter.
As production commences, Sitton finds it rewarding to see all of the sawdust going directly into the pellet line and being turned into a product rather than waste

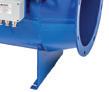

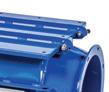
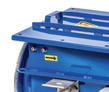
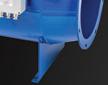
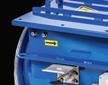

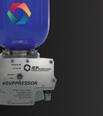
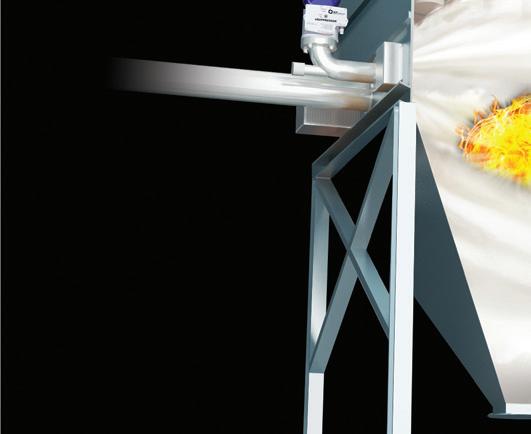
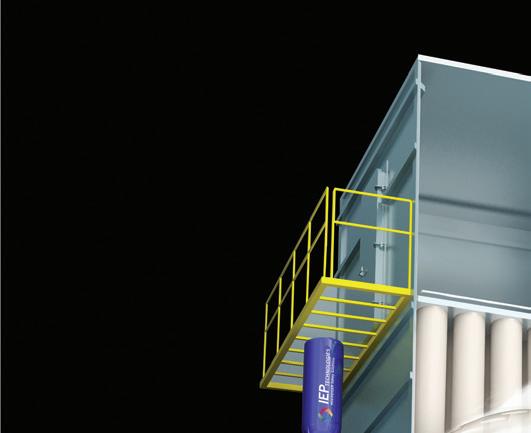
wood. “We’re real tickled about the ability to make our operation a lot more efficient, by having the pellet mills in place,” he says. “And it’s cool to see the pellets actually coming out of the machines turning sawdust— which has always been a challenge for any sawmill—into a product like this. It’s a thing that we really appreciate.”
Author: Katie Schroeder Katie.schroeder@bbiinternational.com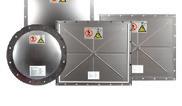
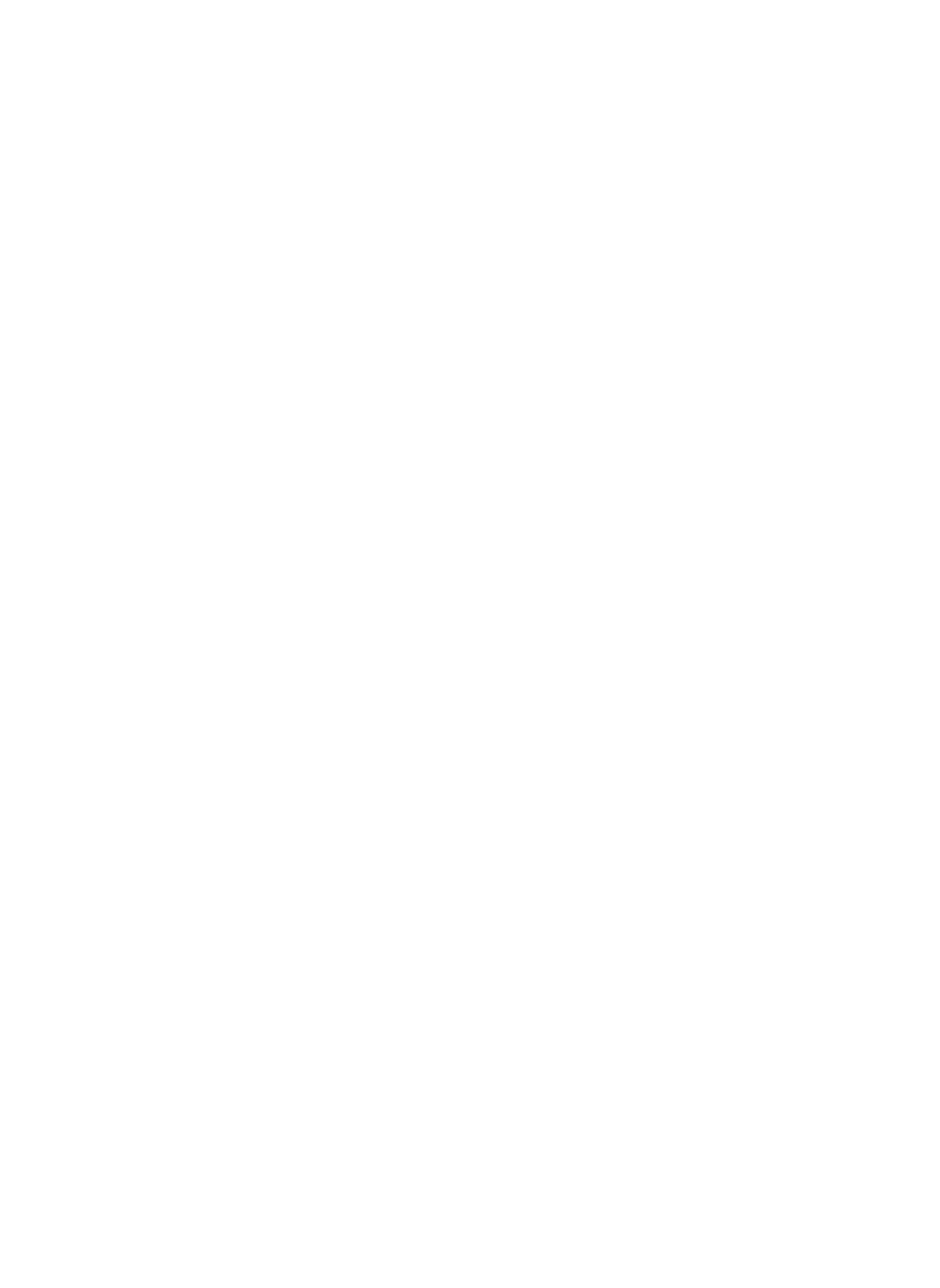
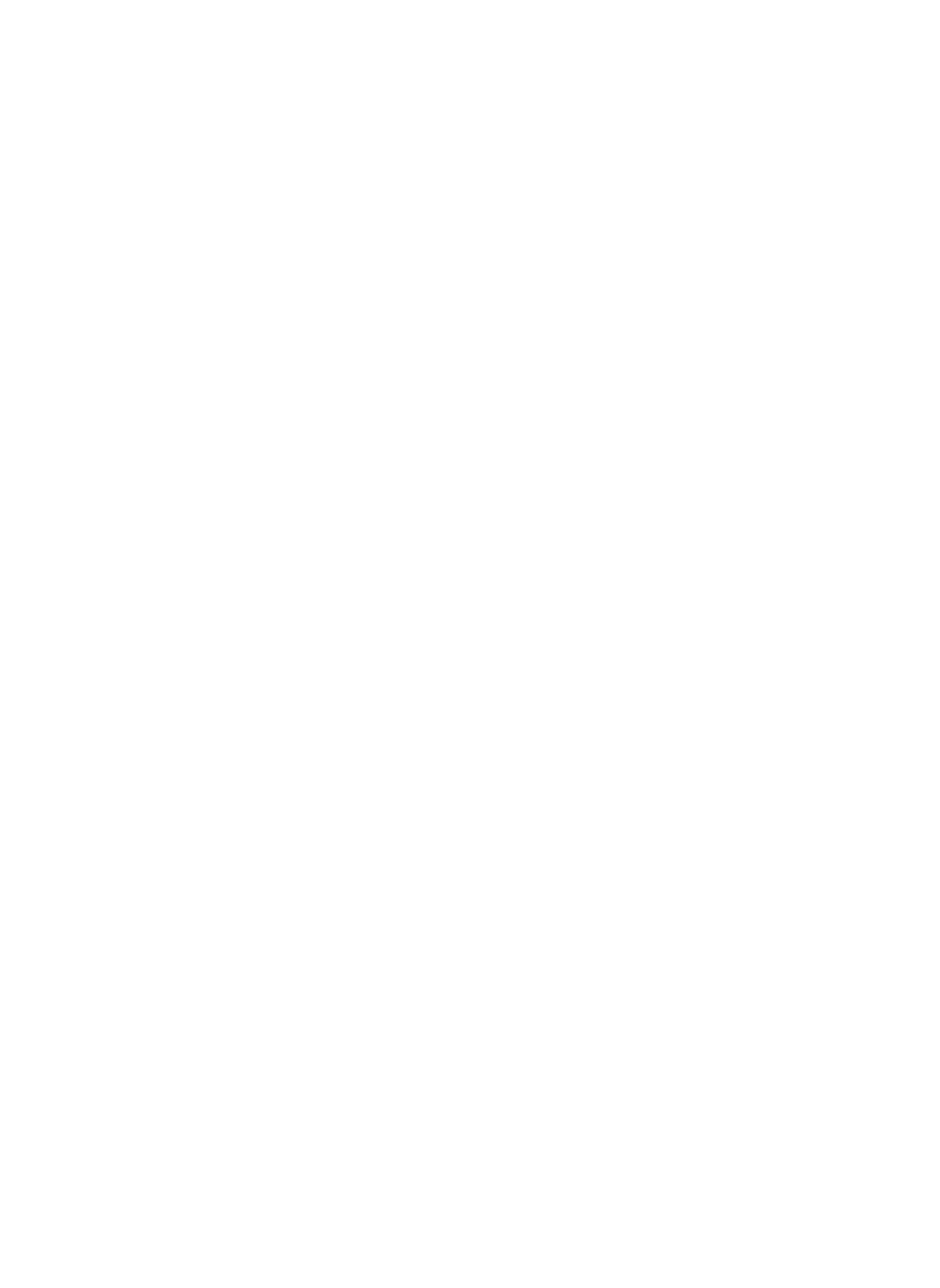

‘We’re a pretty typical sawmill in that we reuse equipment, and we have to fabricate and manufacture lots of equipment that we normally use on a daily basis anyway— it’s kind of in our DNA
— David Sitton, CEO, Aspen Wood Products/Mesa Verde Pellets
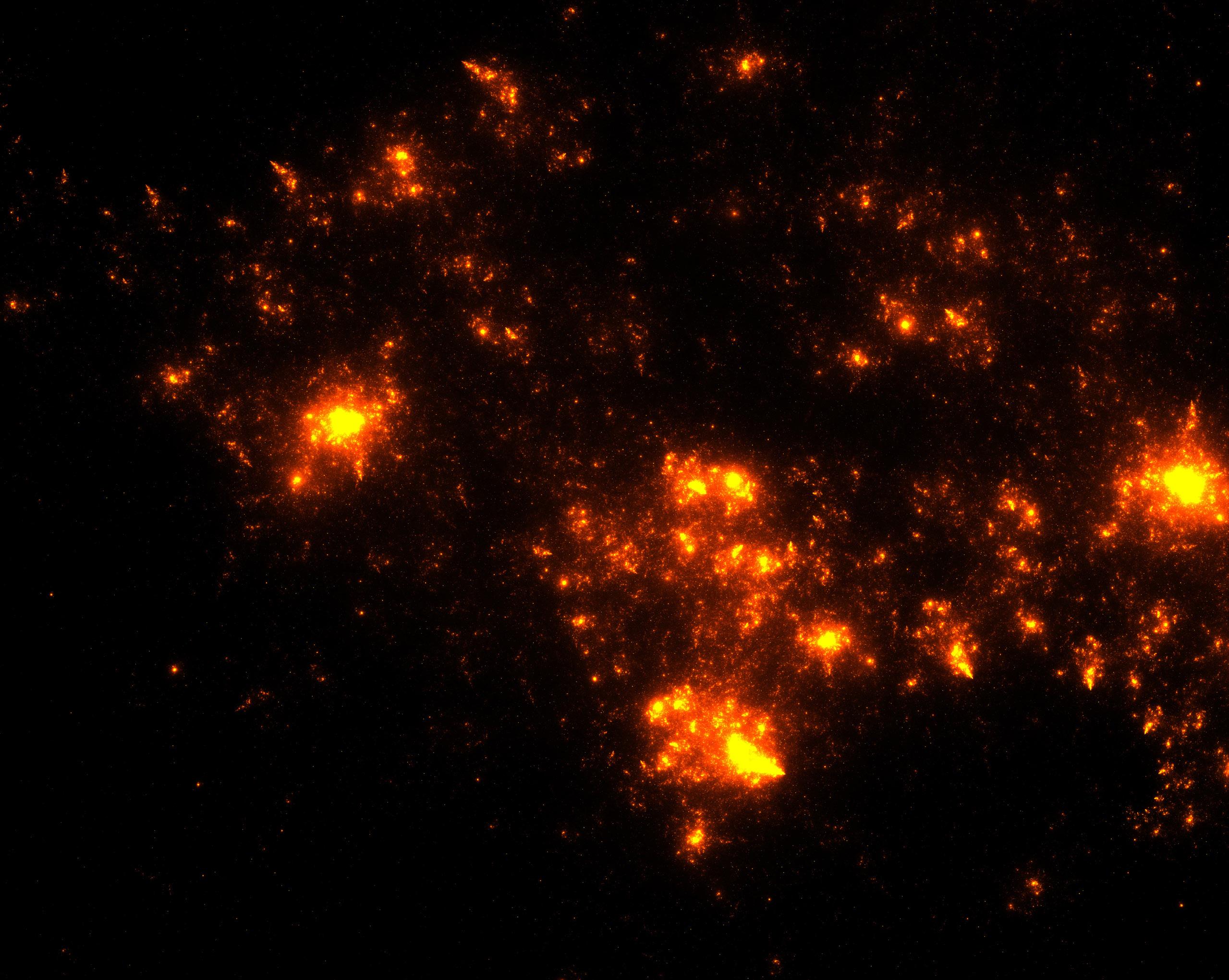
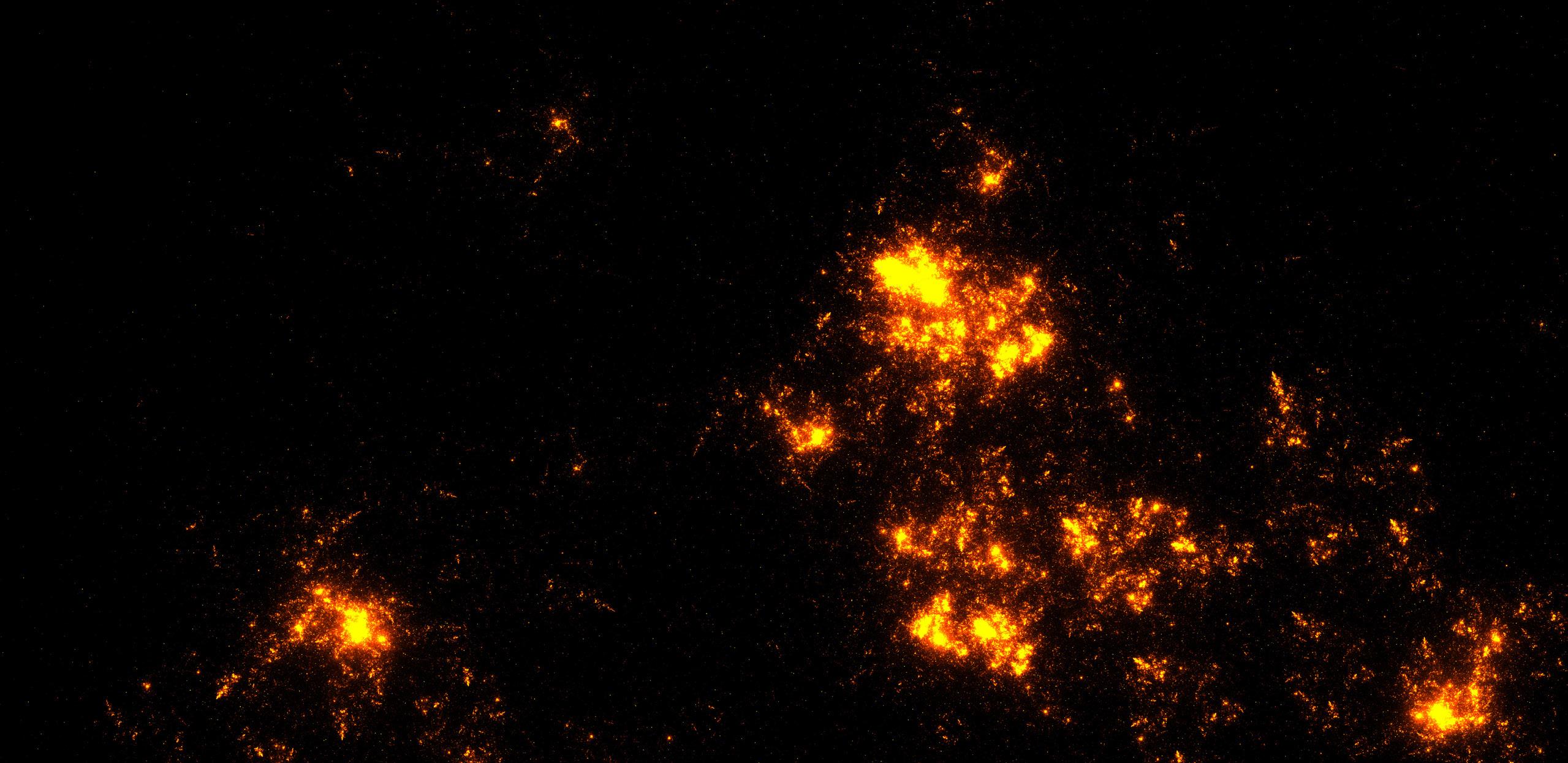
Innovations in Fire & Explosion Protection
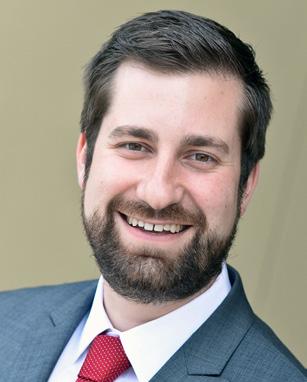

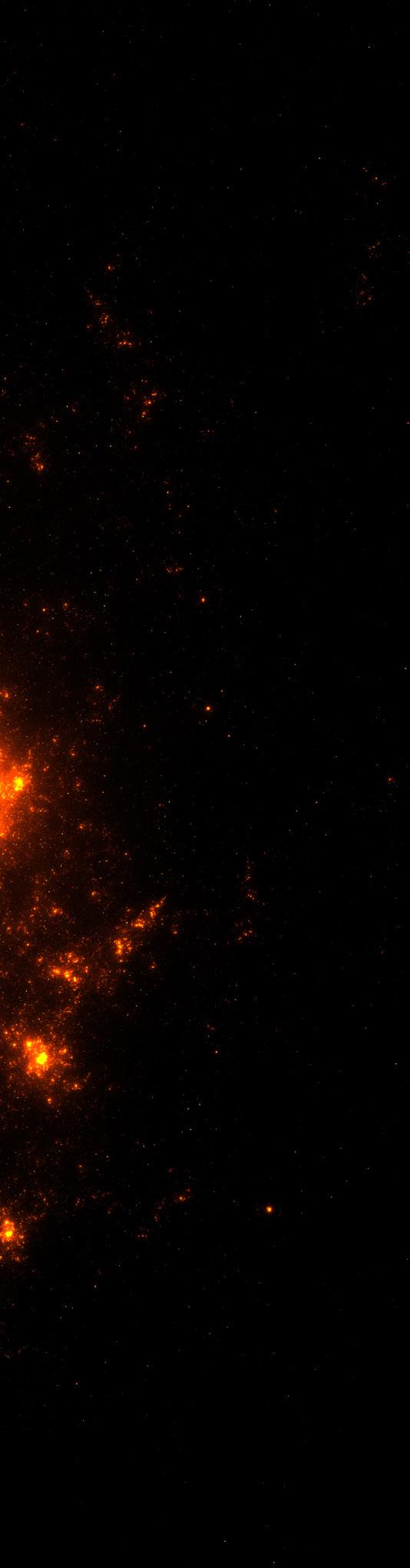
Improvements and innovations in fire and explosion protection have come at a steady pace in recent years, as more companies are investing in products to make things safer and easier while complying with regulations. Pellet Mill Magazine spoke with five industry experts about the latest trends, innovative products and what they believe should be future priorities. Interviewees include: Jeramy Slaunwhite, chief technical officer, explosion safety for Rembe Inc.; David Grandaw, vice president of sales for IEP Technologies; Allen Wagoner, president of FLAMEX Inc.; Jason Krbec, sales engineering manager for CV Technology Inc.; and Eric Peterson, CEO of Fagus GreCon Inc.
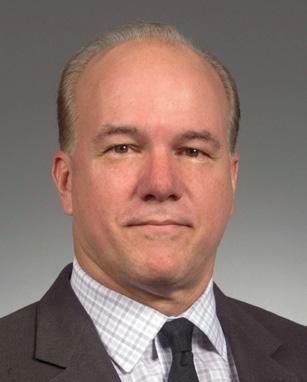
PMM: What do you think has been the most significant innovation in fire and explosion protection in recent years?
Slaunwhite: Holistically, the higher awareness and regard for dust explosion hazards and mitigation strategies in industrial processing facilities have greatly improved. Considering combustible dust fires and explosions have been occurring for as long as dusts and powders have been handled, the development and refinement of flame-arresting technology over the past few decades has provided feasible explosion
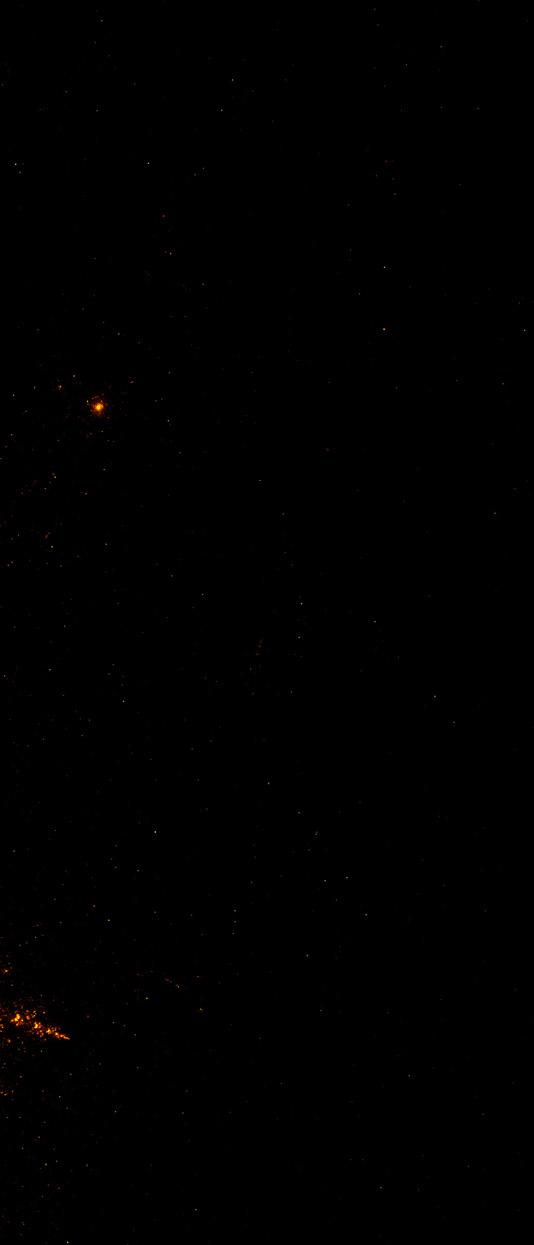
protection solutions for many facilities and industries. Flameless venting allows for reliable explosion protection without harmful fireballs and pressures inside buildings and occupied areas.
Krbec: The most significant innovation is the more costeffective and advanced design isolation systems, specifically explosion isolation systems for the inlet lines to dust collectors and also the clean air exhaust return lines from dust collectors. We’ve seen more reliable solutions developed, as well as some really improved testing standards for those type of products. It’s been a point of emphasis, because it’s where we see one of the largest gaps in the process industry.
Grandaw: The electromechanical suppressor used for active explosion suppression and isolation systems. For many decades, all styles of high-rate discharge extinguishers used for explosion suppression or isolation systems used some version of pyrotechnical device to activate, such as electro-explosive actuators or gas cartridge actuators. Besides the safe handling considerations necessary for these types of
devices, there were often challenges with shipping, as some of these devices required special licensing. In addition, most of the pyrotechnical actuating devices required periodic changeout to ensure proper operation of the extinguisher.
Peterson: As everything gets a little more technically advanced, having things become more intelligent and smarter on their own—as we struggle with labor and a lot of different parts and pieces—is important. The interconnectedness and equipment that delivers things just a little bit easier is very helpful. It’s still new in the fire and explosion side of things.
Wagoner: It’s a broad area, and encompasses a lot. A number of processes


employed in the manufacturing of wood pellets present a fire and explosion hazard that must be addressed to ensure workplace safety, protection of assets and avoidance of downtime. Drying and hammer milling of wood material are particularly conducive to the generation of sparks and fire within the pneumatic transport system. Other processes such as pelletizing, pellet cooling, screening and product load out are also subject to possible ignition from sparks, overheated pellets and mechanical friction sources. To combat the all too common problem of dust collector fires and explosions in woodworking industry, we pioneered the use of a new technology in North America by introducing the FLAMEX Spark Detection and Extinguishing System in 1977. Since that time, thousands
of have been installed in a variety of industrial facilities across North America, including many medium and large industrial wood pellet operations.
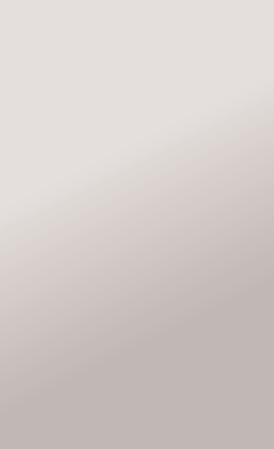

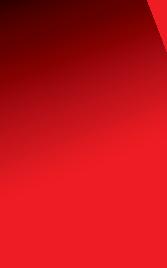
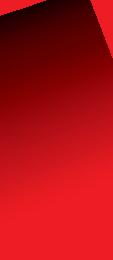





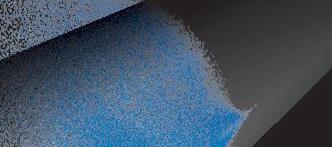
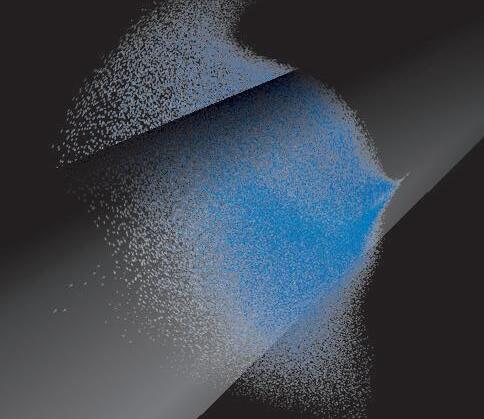
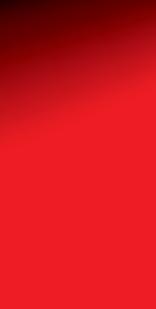

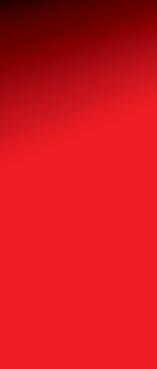
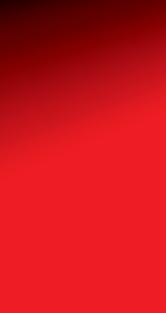
PMM: What product or service designed for this space is your company the proudest of?
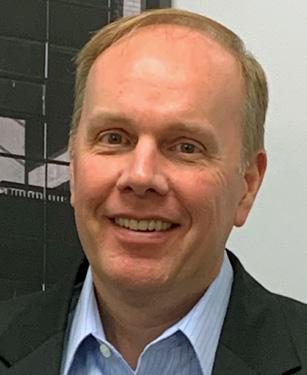
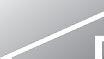







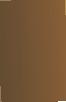




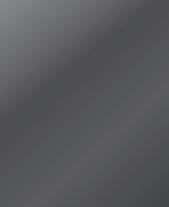

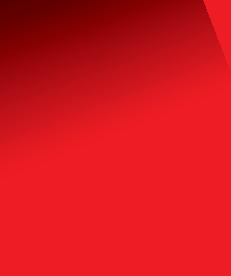




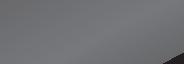
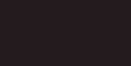



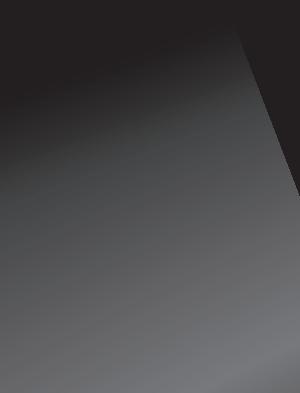
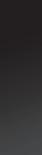
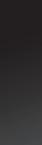



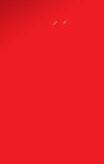
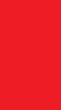










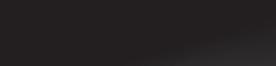



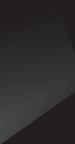
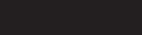
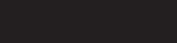

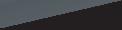
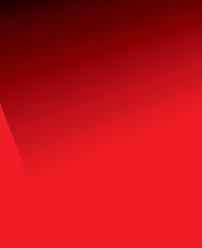
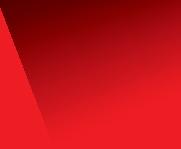




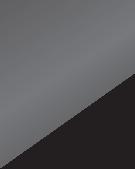

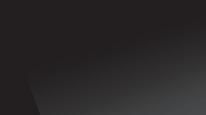





Krbec: We developed a completely passive isolation device for clean air exhaust for dust collectors, and one that uses the same technology as our flameless vents—to have an isolation point that doesn’t require any moving components. We call it the Interceptor–QV and developed it a few years back, and we have had a lot of success with it in various industries—not just biomass. It’s won a couple of design awards for safety products.
Grandaw: From a product standpoint, it would be our SmartDS detection system. Most explosion suppression or isolation
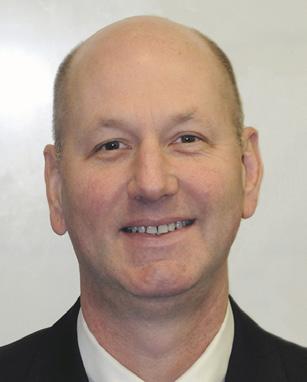


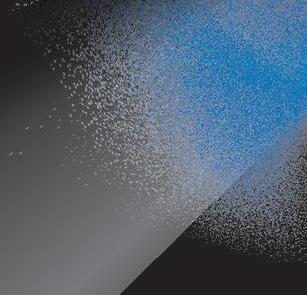
systems use pressure-activated explosion detectors to initiate explosion control. This is a detection method well proven for many decades. With the SmartDS system, we use a rate-of-pressure rise detection technology that is programmed to respond to explosive rates of pressure rise, thus minimizing false actuations due to process pressure issues. The system has a history buffer that provides graphical evidence of the pressure increases just prior to and during any event leading to a system discharge. This is a great investigation tool for determining that an incipient explosion has been suppressed, resulting in the post-event investigation focusing on corrective action to address the ignition source.
Slaunwhite: At REMBE, one of our major shining achievements is the development of flameless venting technology for dust explosion venting, several decades ago with the Q-Rohr. This has led to our Q-Box flame arrestor and particulate retention device, a flameless explosion vent.
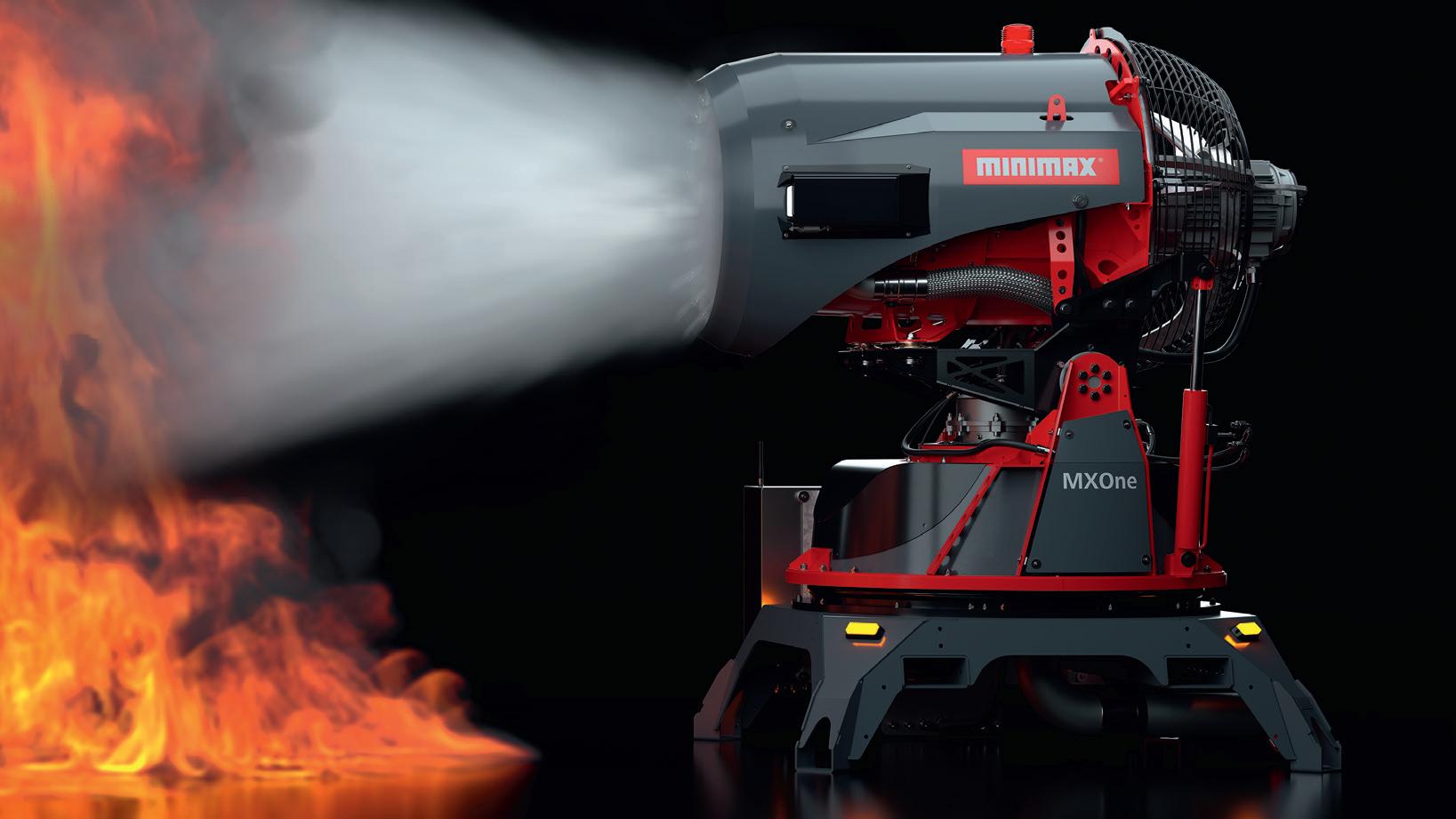

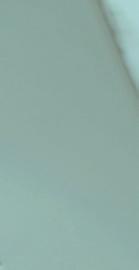
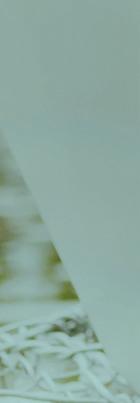

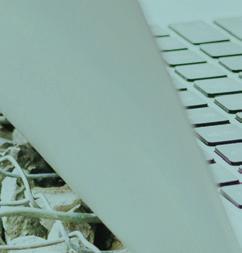
The Q-Box is a versatile, economical and third-party tested and certified solution for safe indoor explosion protection in many industries, including food and wood processing.
Peterson: One is a spark detector that has been on the market for about a year and a half. It can basically adapt whether there’s light or not, and actually gets smart
and adjusts to the light over time. So, if there’s a hole in the duct work or a flap that opens up, historically, the sensor would just fire off. This one will get smart and realize there’s a certain amount of light, and adjust to it. That type of detection obviously has a lot of benefits for anyone who has extraneous light. The other is GreCon IEM, an intelligent extinguishment system that we just came out with this year. It will
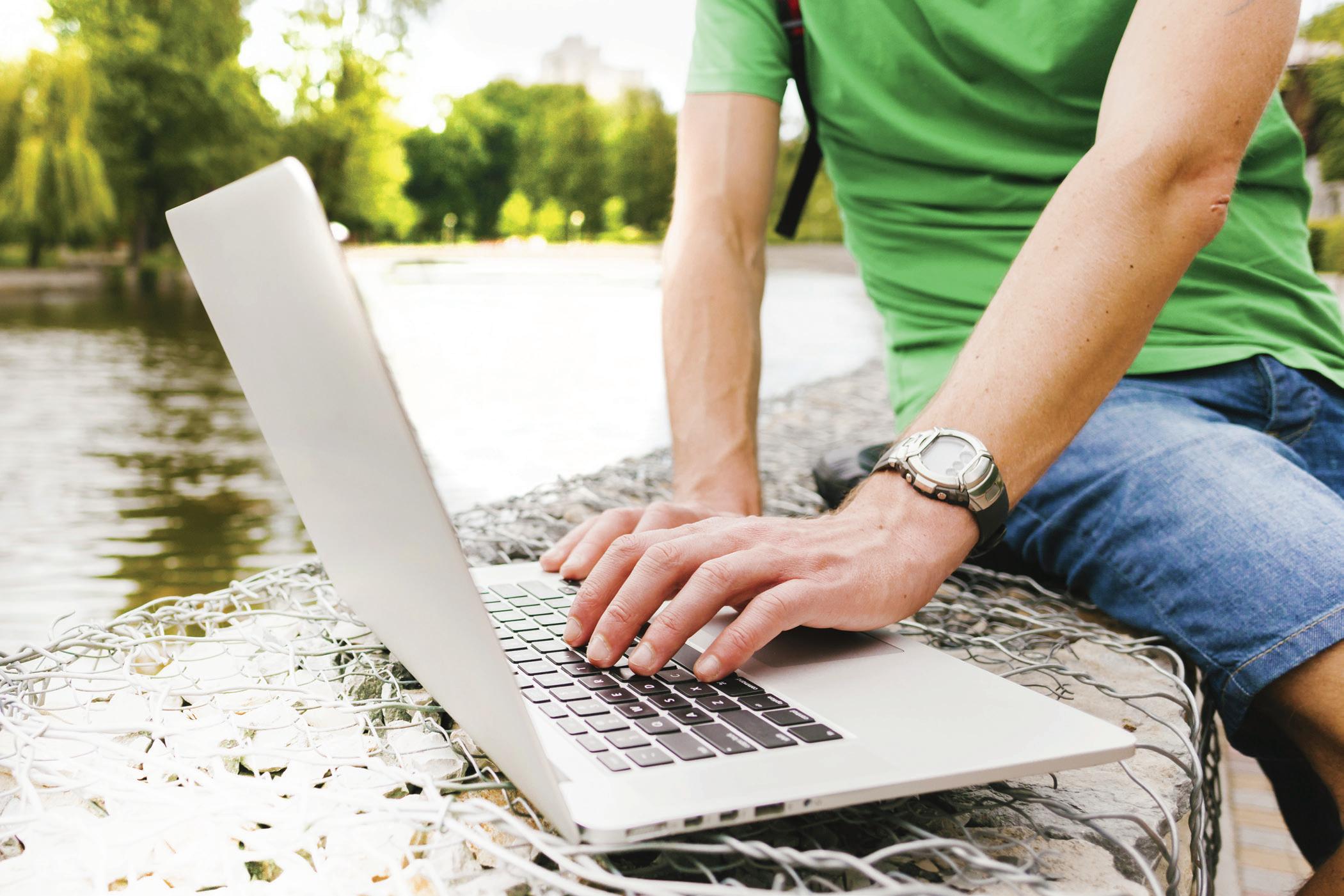
monitor the wear of the nozzle and it will also monitor the flow. It helps with proactive maintenance.
Wagoner: Our extinguishing turbine, the MXOne Firefighting Turbine, represents a new generation of stationary firefighting. The system has a 360-degree operating range and allows the application of water mist from a long, safe distance and with high accuracy. When extinguishing a fire with water mist, the water is atomized under high pressure, producing a dramatic increase of water surface which allows
a greater efficiency in the absorption of heat. When water evaporates, its volume is increased many times over, which causes a cooling and suffocating effect on the fire. The volume of water consumed during the firefighting effort, as well as the consequential damage caused by the water, are extremely low. The control and direction of the extinguishing turbine can be done fully automatically upon detection by IR Flame Detectors, remotely by mobile devices or manually. Various stationary and mobile control variants can be implemented according to the operator's requirements.
PMM: What aspect of fire and explosion protection could use improvement?
Slaunwhite: In my opinion and observations, the most widespread shortfall regarding combustible dust explosion safety is the do-it-yourself approach to protection equipment with a “good enough” mentality. There are recognized standards for design, performance testing, application and reliability of explosion safety equipment that ensure the equipment will do its job if called upon. The nature of dust explosions is highly chaotic. As such, these standards use testing and calculations based on actual explosion testing to ensure reliable protection. In a high quantity of site inspections, especially in the wood industry, I have observed uncertified and
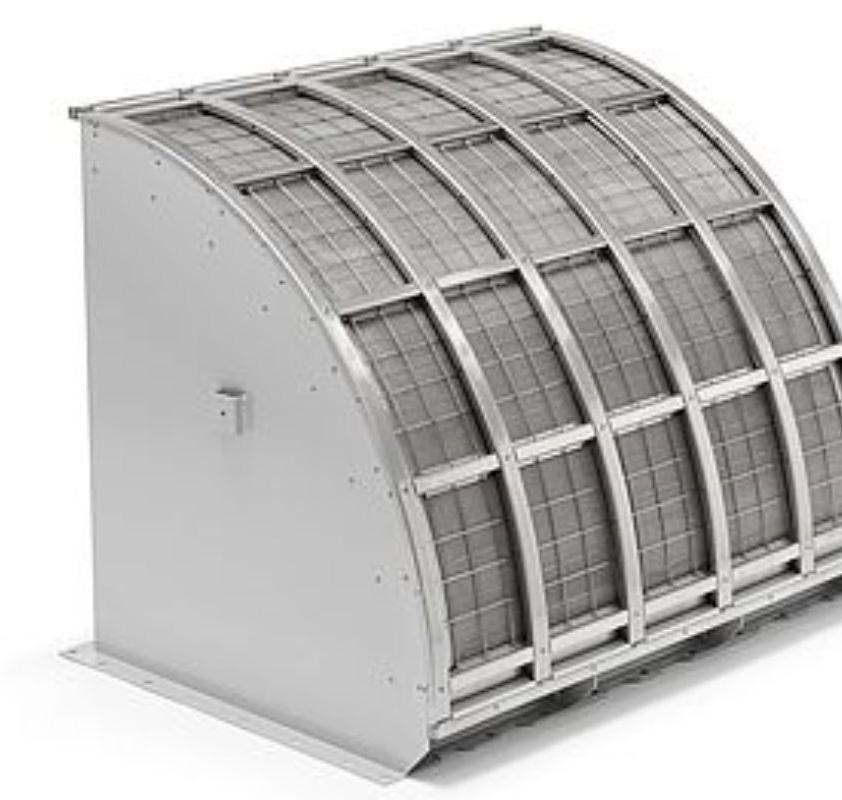
undocumented explosion relief vents and isolation devices, often with visible deterioration. Unlike other fire safety system such as sprinklers, which must be designed and certified by an engineer with listed and approved components without question, dust explosion protection is too often under-designed with no accountability, using questionable equipment. The awareness and standards have certainly been evolving over the past few decades, as has much of industrial technology.
Grandaw: Regular periodic inspections of fire and explosion protection systems. While it is true that these systems are designed for use in the challenging conditions found in industrial plants, if these
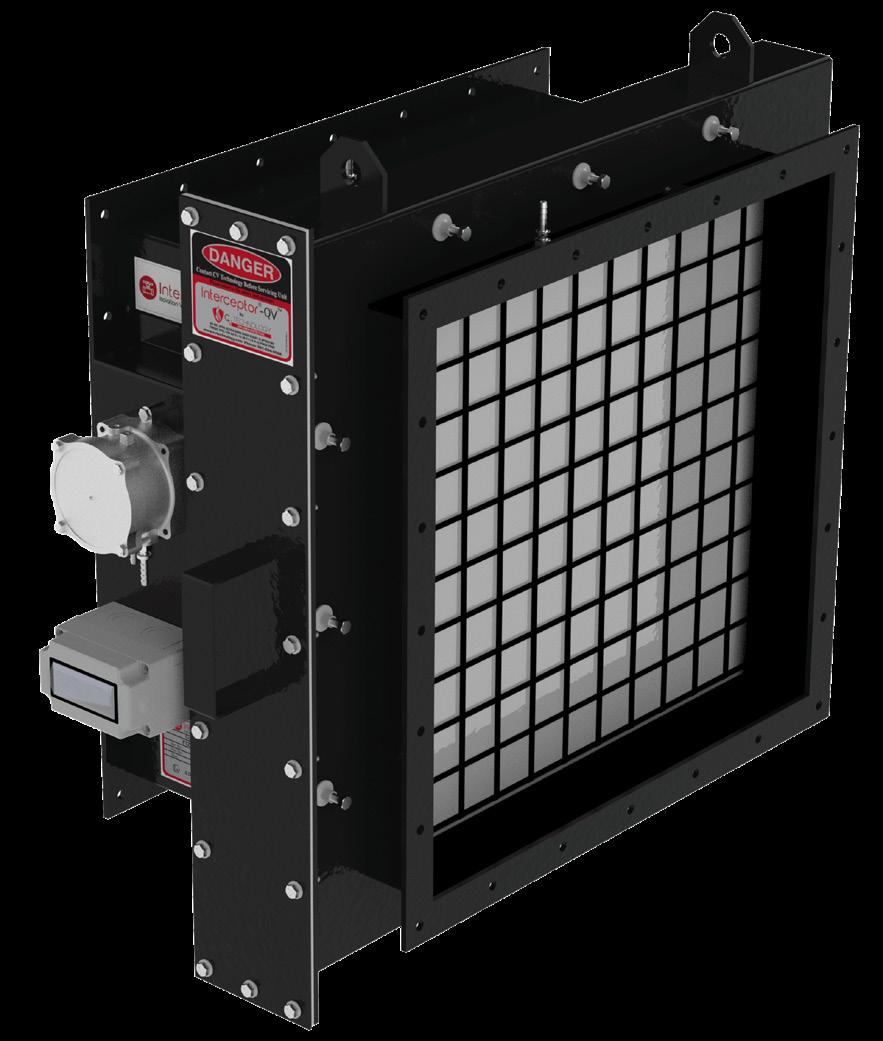
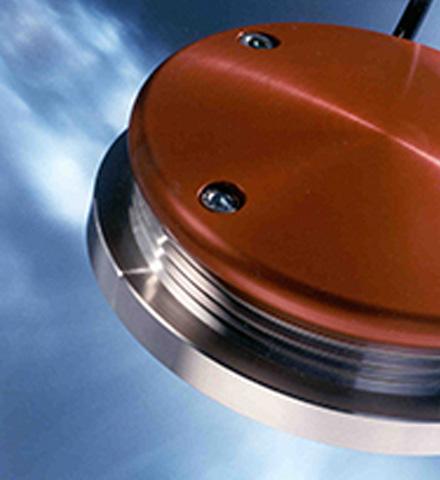
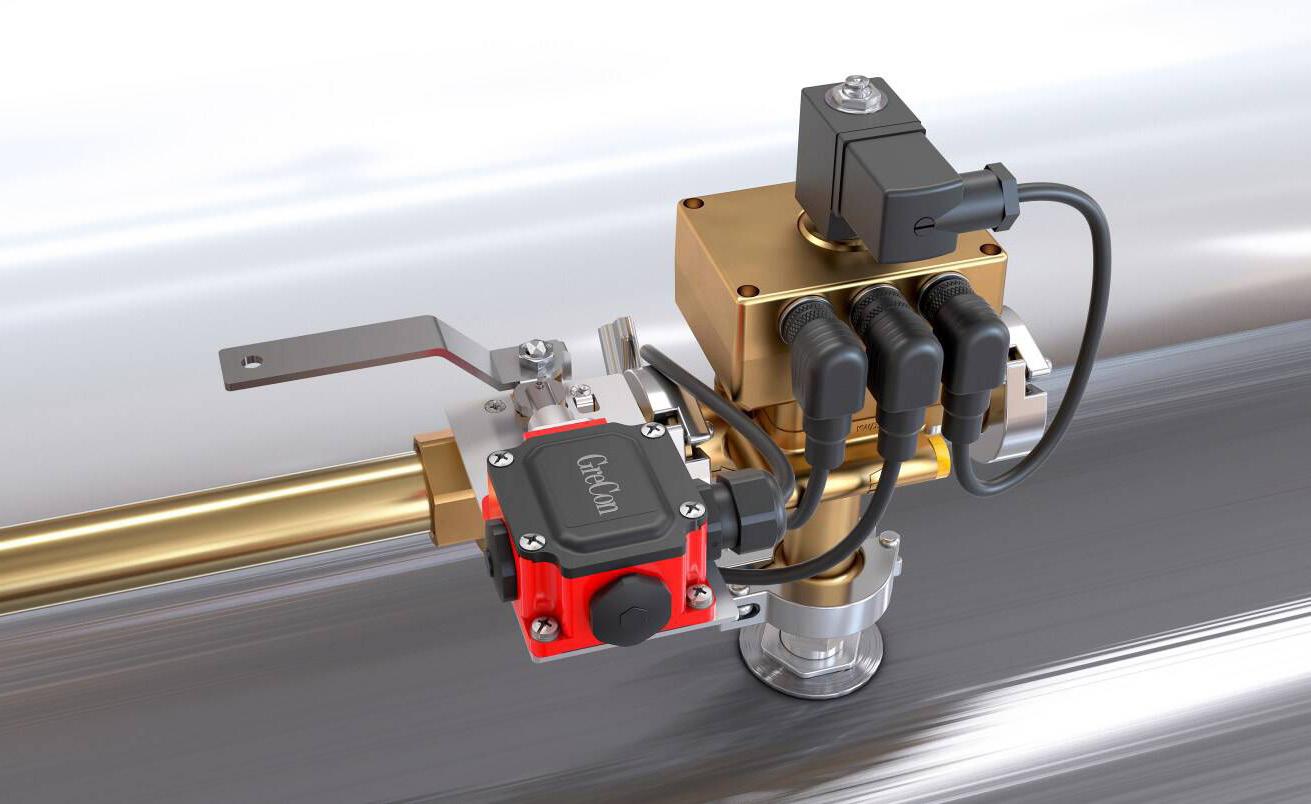
protection systems are compromised due to lack of proper maintenance, process equipment damage, injury to personnel or worse can happen. Fire and explosion protection systems are like other processrelated equipment, needing periodic inspections, and sometimes component replacement when compromised.
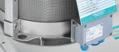

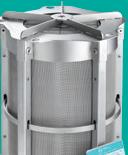

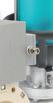


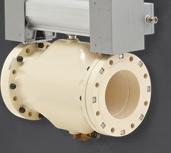
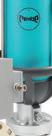
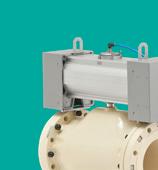
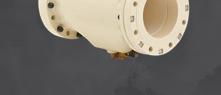
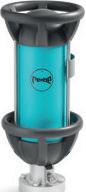

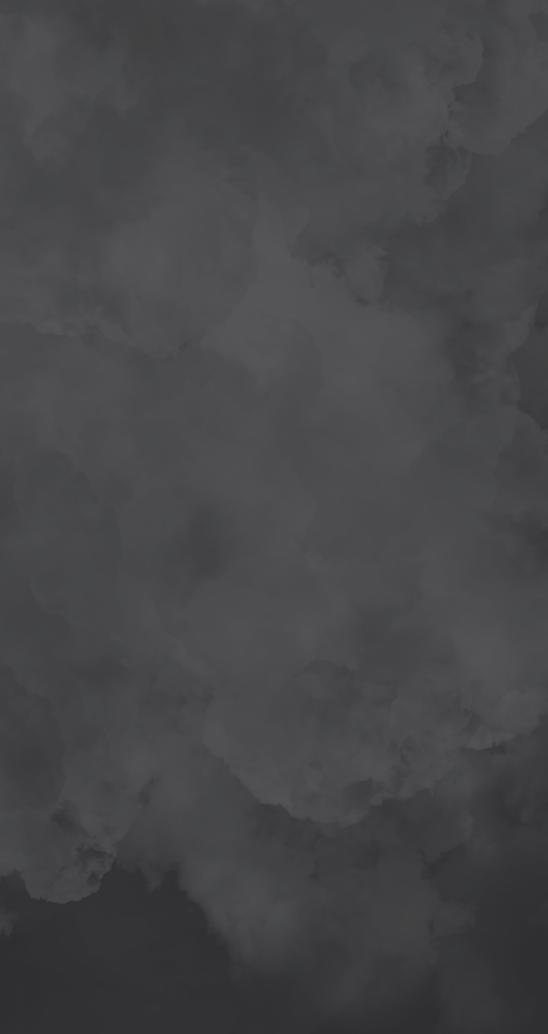
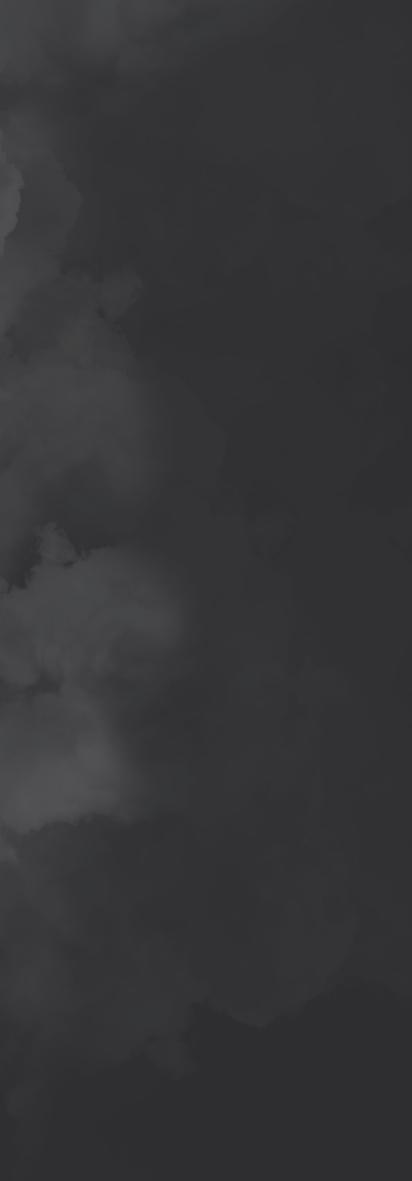


Krbec: One of the major things that need to be improved is some of the training and awareness of protection systems themselves. A lot of that goes to the plant operations side. Much of the explosion and fire protection systems are not completely hands-off; they do require some understanding of how to operate and use them properly if you’re doing certain types of process activity. That communication and training is still one of the big gaps we see.
Peterson: One of the big challenges is that most everything in today’s systems and facilities is all wired. There isn't a lot of wireless. Being able to move into some sort of cloud environment where we can go into a lot of different places and not have everything connected back to a system would certainly be extremely beneficial from a time, cost and maintenance perspective. Anything we can do to start connecting these pieces would be big plus.
Wagoner: Owners or operators of a facility where materials determined to be combustible or explosible are present in an enclosure are responsible for obtaining a dust hazard analysis (DHA) in accordance with NFPA 652, Chapter 7. A DHA is a written document that is prepared by a qualified individual to identify specific hazards in the facility, and to provide prescriptive measures to be taken to address those identified hazards. The DHA is to be re-
Fire & Explosion »


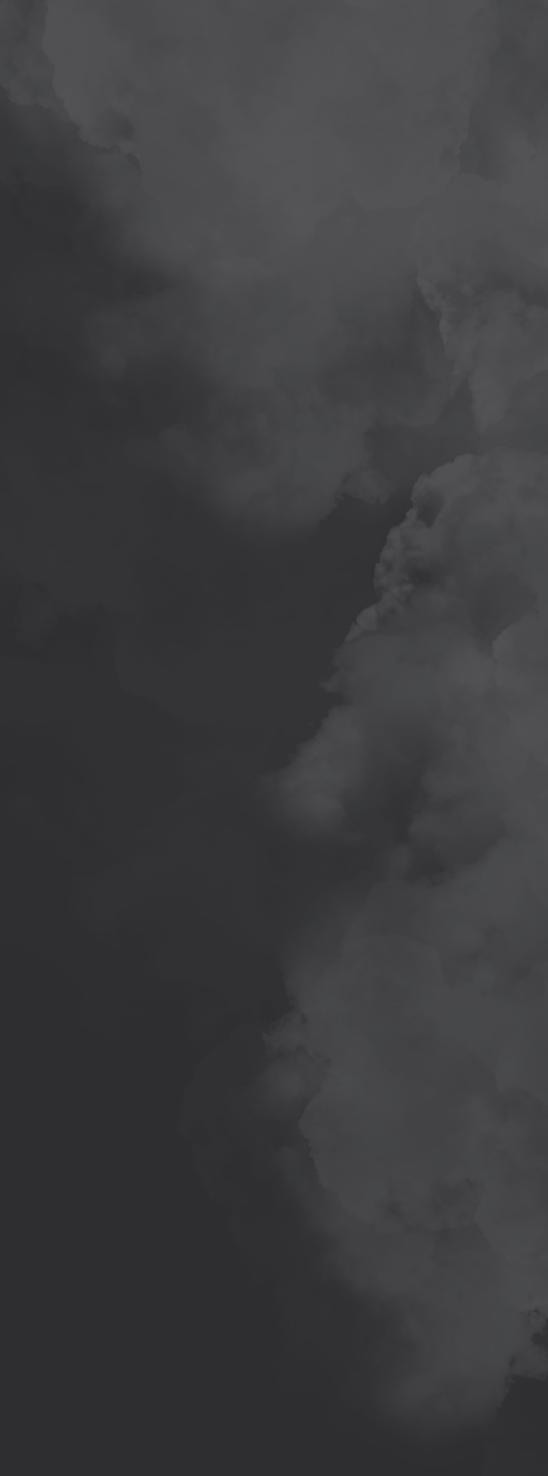
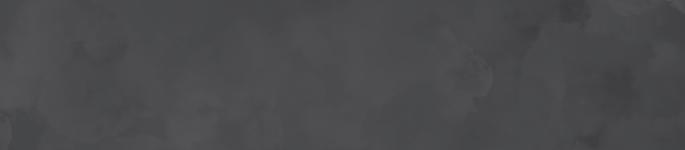
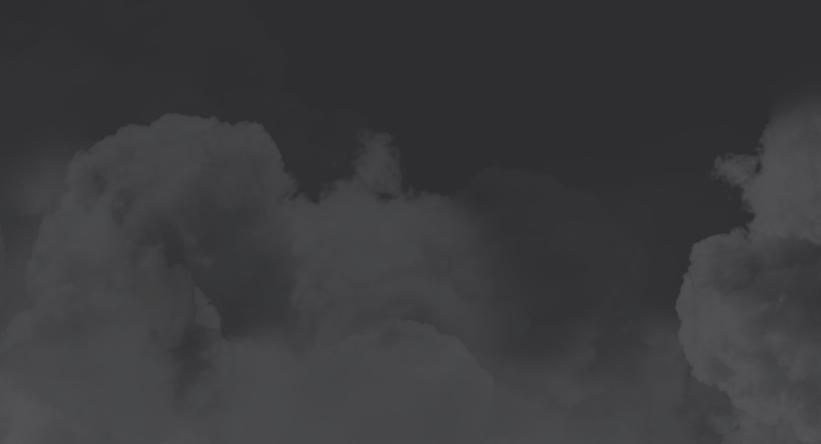
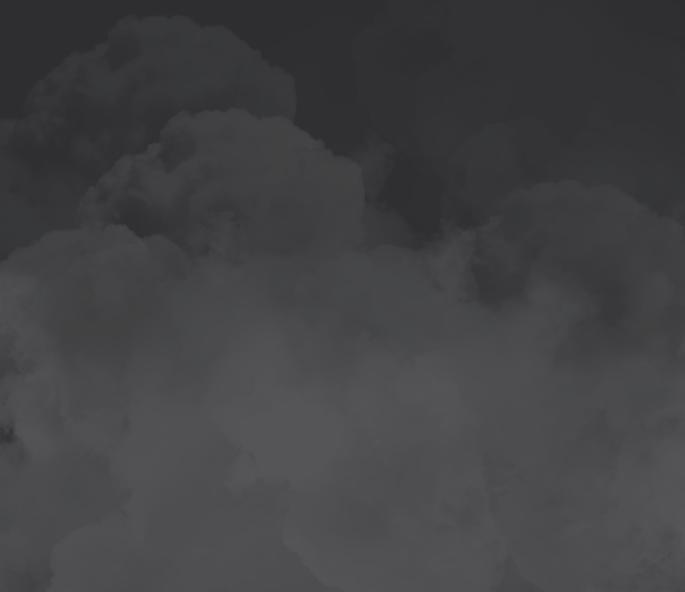
viewed and updated every five years. Many facility owners are unaware of this requirement or have failed to take steps to have one conducted. It is widely believed that this is the first step in addressing the dangers of potential fires and explosions that are largely inherent in facilities that handle combustible dusts.

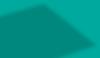
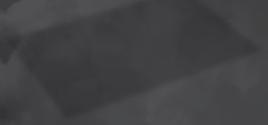
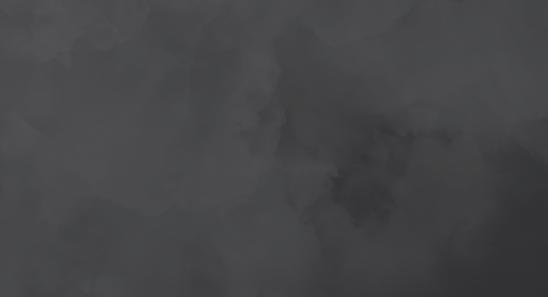
In an article dated May 11, 1982, United Press Canada reported that BioShell Inc.—a wholly owned subsidiary of Shell Canada Ltd.—was planning to build a “wood densification plant” in Lac-Mégantic, Quebec, to produce fuel pellets from wood waste. The plant was to be the first of its kind in the province, but similar to others the company had in Hearst and Iroquois Falls, Ontario, including BioShell’s initial densification operation—a sawmill residue-to-brick plant that was built in 1980. The Lac-Mégantic plant would come at a price tag of about $5.7 million and have an annual capacity of 105,000 metric tons of finished product. Construction was to begin “immediately, with the plant scheduled for a start-up in December 1982.”
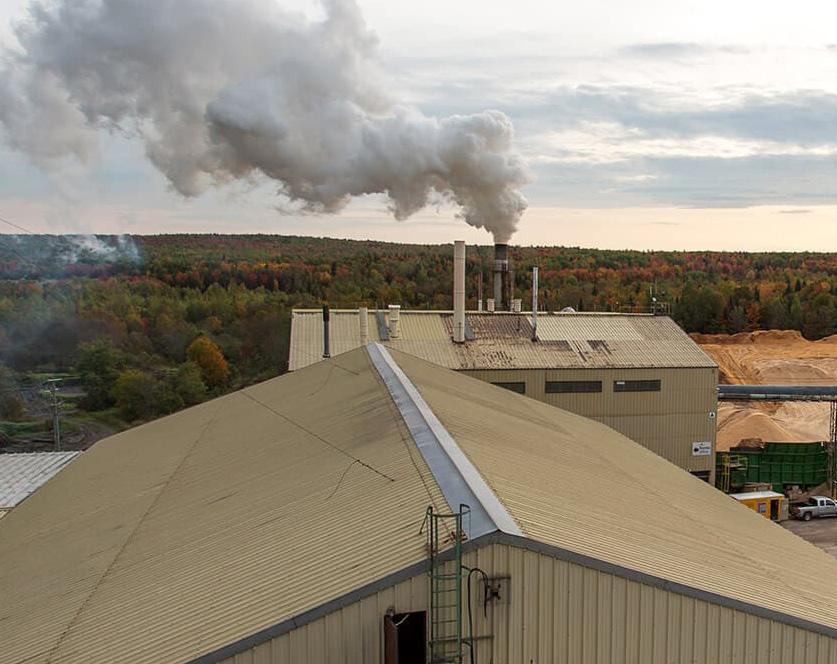
Fast-forward 42 years, and that plant is still operating, a relic and one of the oldest mem-
bers of the North American wood pellet plant family. And, as demonstrated in local newspaper archives, the first shipper of transatlantic wood pellets (see sidebar). The plant has not changed hands much over the years; BioShell owned it for just over a decade. For Bruce Lisle, buying the plant from BioShell at an opportune time when Plan A didn’t come to fruition has resulted in a 30-plus-year career in the industry.
Working Up Plans
“I was actually looking at coal briquetting in the mid-80s, and I formed a relationship
with a guy who had developed a binder to briquette coal fines—it was so clean you could put a briquette in your pocket and not turn it black,” Lisle tells Pellet Mill Magazine. “My deal with him was to build a plant in Canada, in Nova Scotia, which had coal mines at the time.”
Lisle met his wife during his work travels and subsequently moved to Cape Breton Island, Nova Scotia, where he began working with the Nova Scotia Research Foundation to conduct a residential market study for those coal briquettes. “It was a great product, but nobody would buy it because there just weren’t many coal clients,” he says. “In the meantime, I read an article on wood pellets in what was then called Wooden Energy—which ultimately turned into Hearth & Home Magazine—and they said it was a bullseye. Long story short, I

From the History Books
Energex Inc. is one of the longest-running fuel pellet plants in North America. Former owner Bruce Lisle chats with Pellet Mill Magazine about the early industry, the plant’s history and how he came to buy it.
BY ANNA SIMETthen spent several years trying to build a plant (pellet production and cogeneration facility) in Cape Breton. I had an office, an engineer, a wood procurement guy … we were very close to building it and had raised $16 million, but ran into an unfriendly government.”
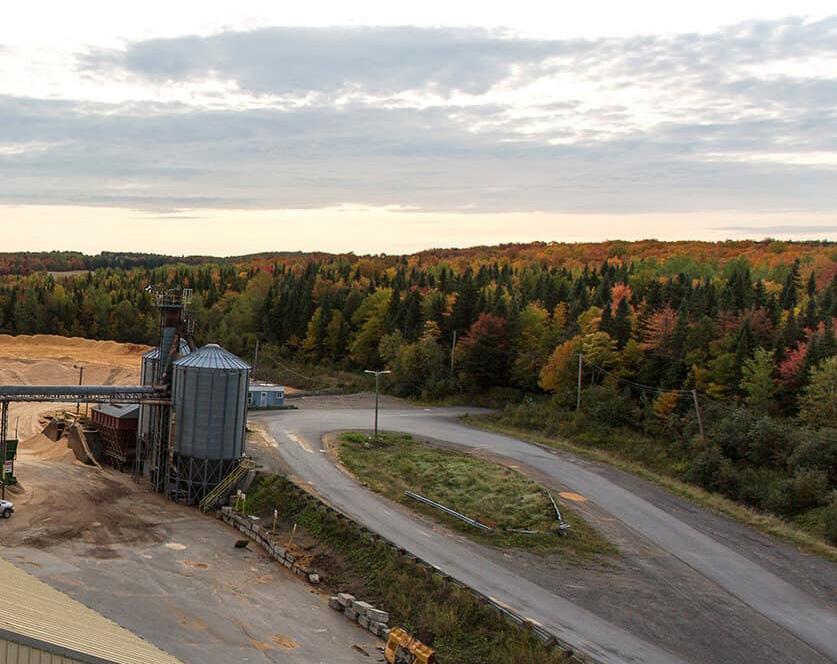
Ultimately, Lisle came across the opportunity to purchase the plant in Lac-Mégantic from BioShell. “On March 5, 1992, I called the president of BioShell—a subsidiary of Shell Petroleum, in their nontraditional business unit—to see if there was interest in developing a plant through a joint venture. He told me that out of the three plants they had, one was basically already dismantled, another was shut down because its long-term contract was canceled, and the plant in Quebec was running at 50% capacity, selling bark pellets to a paper plant in Maine—and it was for sale.”
When Shell invested in these plants in the late 1970s and early ‘80s, Lisle says, the company planned to build many more. “In Quebec, they really expected to push this forward, but Quebec Hydro—with its very cheap power—began subsidizing the installation of electric boilers in the province, which basically blew Shell’s plan to expand wood pellet fuel operations. So, they decided to consolidate back to their core oil and gas business and get rid of all their nontraditional business units.”
Fast forward one year to the date of when Lisle called the president of Shell, and he signed the purchase agreement to buy the Lac Mégantic plant, taking over in early June 1993. “That’s how I got my start,” he says.
Only running bark pellets at the time, Lisle added a packaging facility and began bringing in clean sawdust to make a residential
product. “Energex was built from there,” he says. In 2000, another plant would be added to the company's portfolio—Energex merged a West Virginia pellet plant with another in Mifflintown, Pennsylvania, and created Energex American Inc.
Industry Pioneers
Backing up again to the purchase of the Lac-Mégantic plant, the very next day, Lisle found himself in Nashville, Tennessee, setting up a trade show booth at the Hearth & Home Expo. There, he met Averill Cook of Catamount Pellet, who produced the Stove Chow brand, and Barb Shine of Dry Creek Products. “The three of us were the first to establish mills for the Northeast residential bag market,” he says. “We were the 'three amigos' who really pioneered wood pellet fuel on
Under BioShell’s ownership, the first documented shipment of transatlantic wood pellets was sent overseas from the company’s Lac-Mégantic plant. “At the time, [BioShell] decided there was a worldwide market for pellet fuel, which was starting to take hold in Europe,” Lisle says. In 1991, a 5,000-ton shipment of bark pellets was loaded at the Port of Quebec and sent to Helsingborg, Sweden. “But the Europeans didn’t realize they were getting bark pellets, which are a completely different animal than premium grade fuel,” Lisle says. “They average over 3% ash, and when you burn high-ash products in boilers, depending on how it’s burned, can cause issues like slagging—this was before there were any fuel standards.”
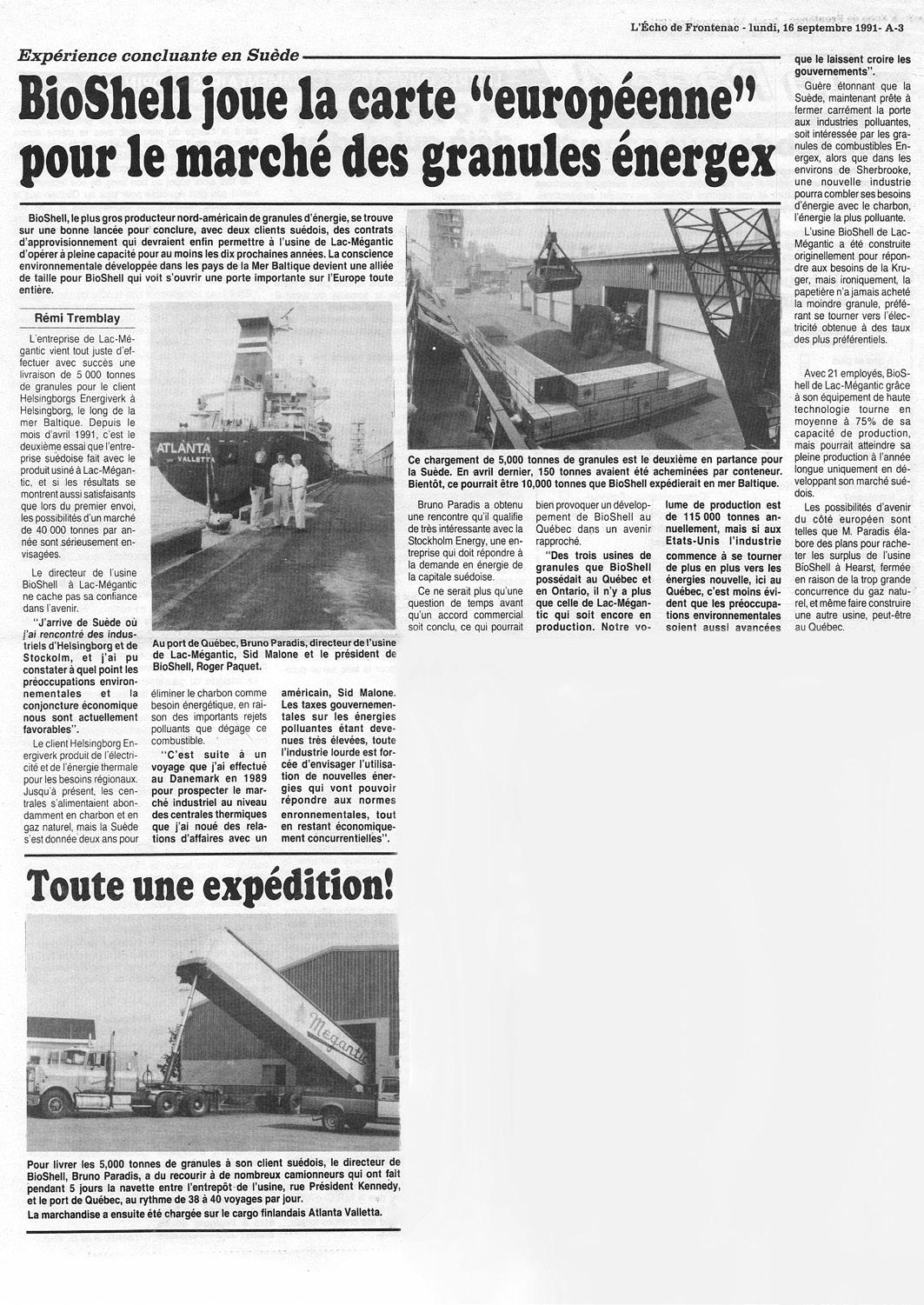
Lisle notes that bark pellets can work great in the right burn climate. “You can do it all day long without a problem,” he says. “We were shipping 50,000 tons to a paper plant in Maine and they loved it, as they knew how to handle that kind of high-ash fuel. Through my Lac-Mégantic plant, I used to take excess capacity and probably shipped 15 to 20 loads myself—this was in the 2000s. The last time I sent a ship was a few months before Lignetics bought the plant in 2020.”
DON’T LET THIS HAPPEN TO YOUR FACILITY
Combustible dust can cause personnel injuries, equipment & plant damage. Spark & embers from dryers, hammer mills, pelletizers & coolers can cause cascading dust fires & explosions
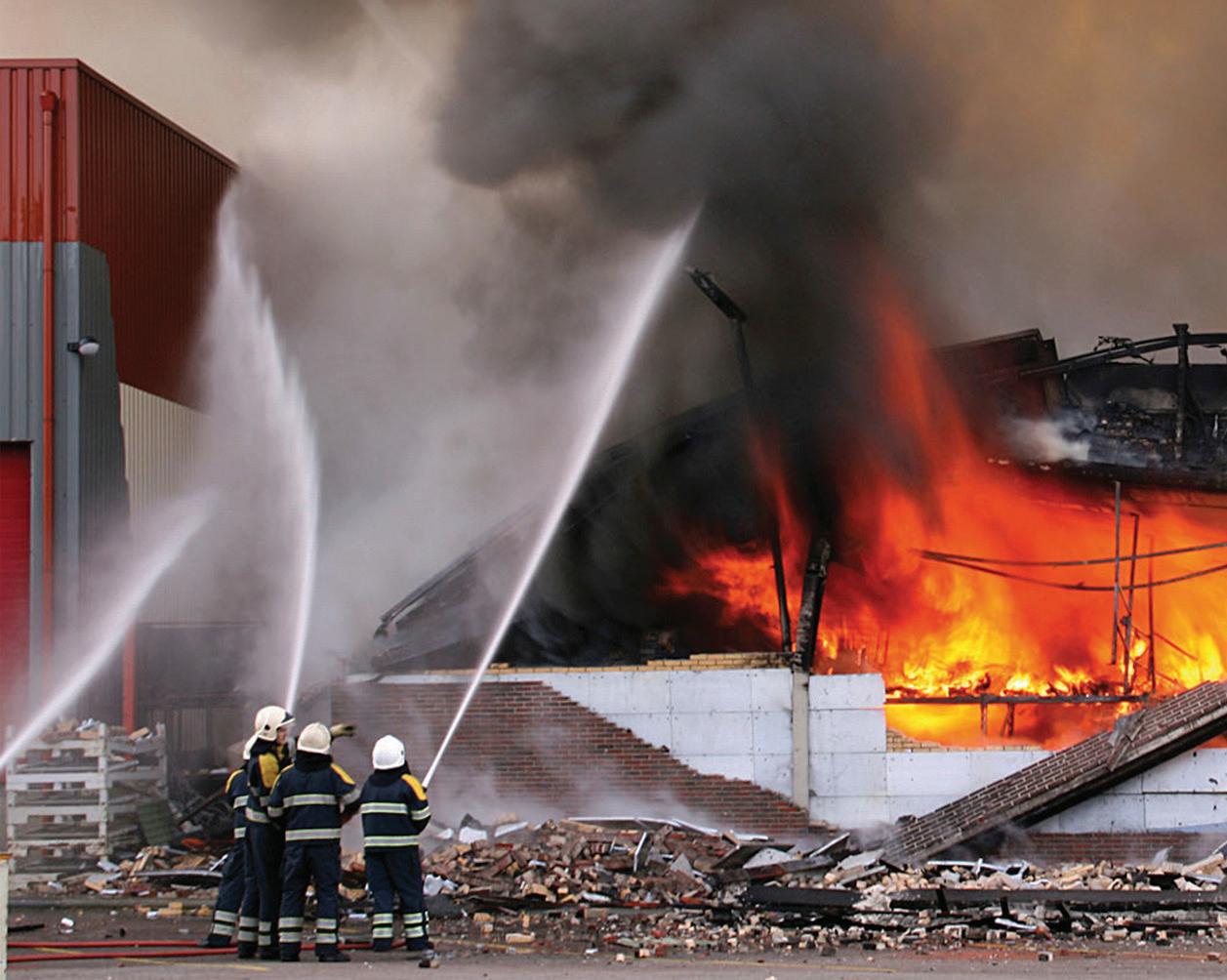
GreCon Spark Detection & Extinguishing Systems





are a preventative measure against fire or dust explosions by detecting and extinguishing sparks & embers in processing and conveying equipment without production interruption.

the East Coast—everybody else came later.”
Each of them would eventually become presidents of the Pellet Fuels Institute, which was established in 1994—and the industry continued its buildout over the years, the result of determination, collaboration and resilience. And, of course, a strong passion for wood heat.
Lisle reflects on a remarkable coincidence that would eventually emerge: Energex ultimately bought out Catamount and its




Stove Chow Brand, and in 2020, Lisle sold Energex sold to Lignetics. In a final intertwining of fate, in 2021, Energex bought BioMaxx, which at the time owned the Dry Creek brand. “The three amigos were all under one roof,” Lisle chuckles.

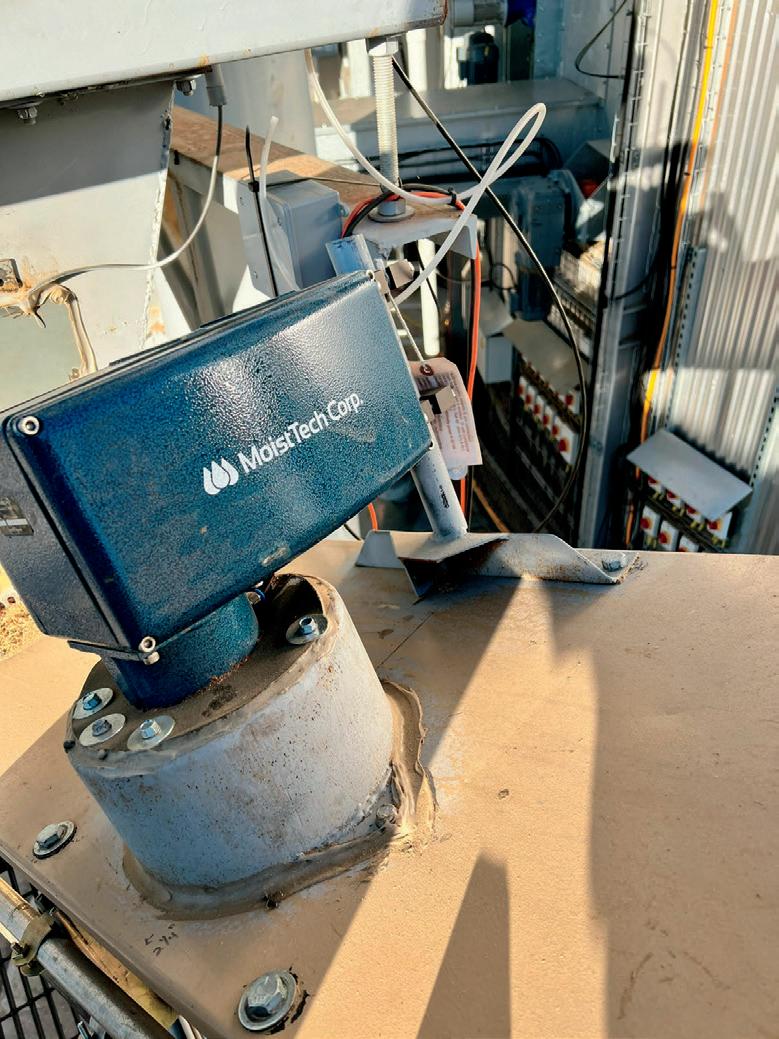

Still Pushing Forward
Lisle notes that one facet of the domestic wood heating pellet industry that he is proud of is that it was developed on free market
economics without subsidies, and stakeholders have based their investment and expansion decisions on supply and demand. He adds that there have been shortage years in recent decades and that when new capacity is built in response, it does take time for the market to absorb that additional capacity.
Today, Lisle continues to work for Lignetics on strategic initiatives. A love for the industry has been passed down in the family, as his son, Kenny Lisle, also works for Lignetics as director of national accounts. Among his industry endeavors, Lisle sits on U.S. Department of Commerce’s Renewable Energy and Energy Efficiency Advisory Committee. “I call myself the token biomass guy,” he says. “I have put together recommendations on biomass, and one of them last year was that we need to develop manufacturing plants for pellets on the West Coast to service the Asian markets,” he adds. “It takes the canals and some logistics out of it, and importantly, it’s fire mitigation.”
Author: Anna Simet asimet@bbiinternational.com
Fiber Optic Linear Heat Detection: Enhanced Fire, Hotspot Sensing
BY JAEDYN MATSALLAAs the demand for alternative and renewable energy sources has grown, the wood pellet industry has emerged as a significant player in the global energy market. In recent years, fiber optic linear heat detection (FO LHD) technology has become a gamechanger by providing an advanced and reliable solution for detecting and preventing hotspots and fires. Protection against fire may not be the primary concern with wood pellets themselves. Nevertheless, operators and users of biomass plants and wood pellet-burning points must ensure the operational safety of their plants, also in terms of fire protection and early fire detection. The production and storage of wood pellets are associated with risks, including the potential for fires. The use of FO LHD technology can mitigate these risks, providing an effective way to monitor temperature changes and detect fires before they become a hazard.
Fiber Optic Linear Heat Detection
FO LHD is a type of fire detection system that utilizes fiber optic sensor cables to detect temperatures along the entire asset that the sensor cable is monitoring. These sensor cables are made up of thousands of measuring points that can detect changes in temperature along their length, making them ideal for use in monitoring large areas such as warehouses, factories, conveyors and storage facilities. Sensor cables can have a length of up to 16 kilometers (16,000 meters) on each of the one, two or four channels.
Wood Pellet Monitoring
In the wood pellet industry, FO LHDs are used as a suitable and tested special fire detector for a wide variety of areas including storage silos, conveyor belts and other areas where the risk of fire is high. These can be used in expolosive gas and dust environments up to zones 2 or 20 on pipelines, con-
veyor belts and in hot ambient conditions of biomass and wood pellet plants. Often, these systems are also coupled in conjunction with larger rooftop or greenfield solar systems. The energy generated is transported to the point of use via medium-voltage energy cables; here, too, fiber optic linear heat detectors utilize sensor cables 4 millimeters in diameter to pinpoint temperature measurements (maximum temperature and rateof-rise, plus hotspot detection) and provide early alarming even before the development of an open fire.
Advantages
The advantages of using FO LHD systems in the wood pellet industry are numerous. For example, the system is highly sensitive and can detect heat changes before they become a fire hazard, allowing for early intervention and prevention. This is especially important in the wood pellet industry,
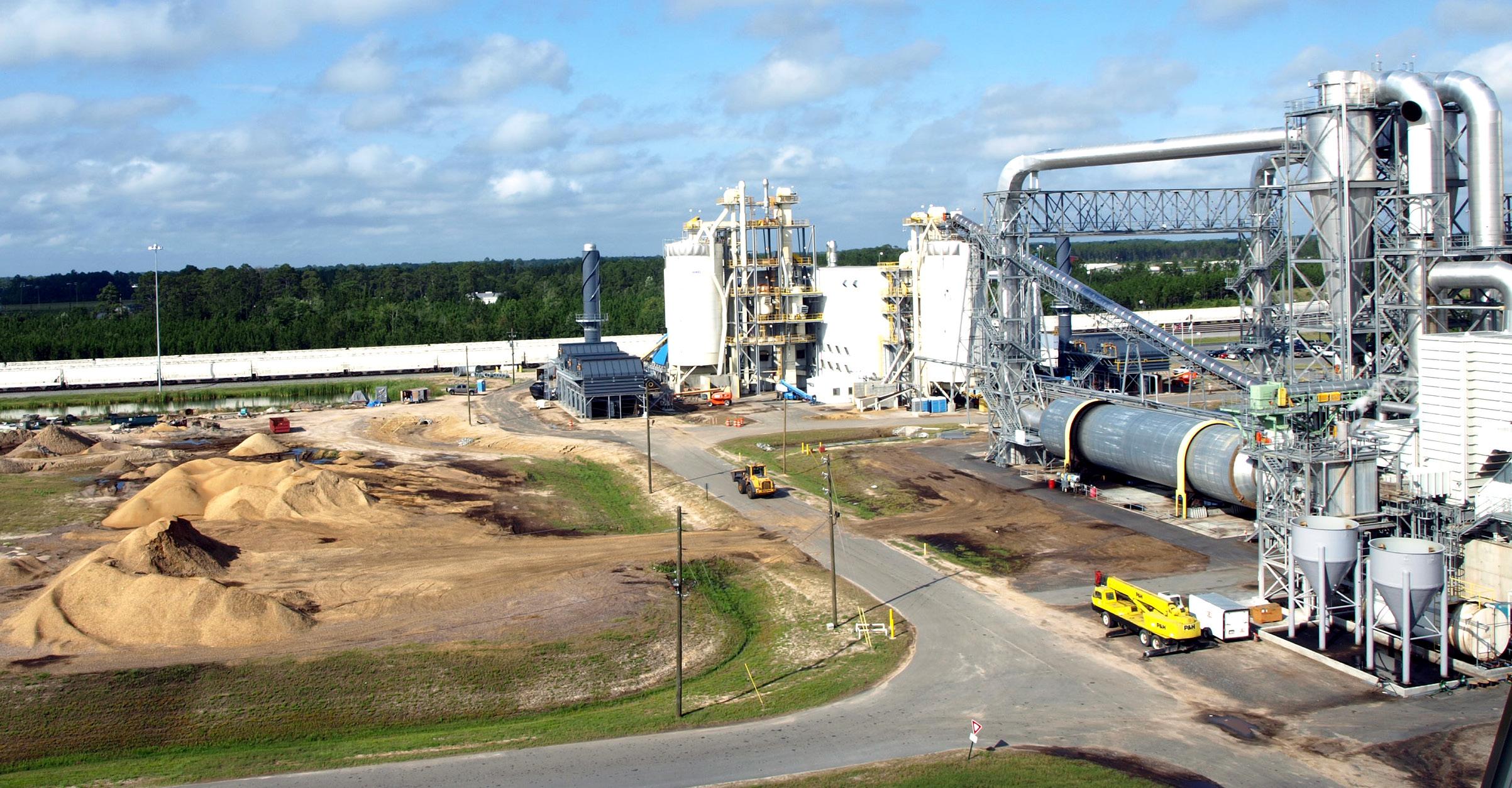
where fires can spread quickly due to the combustible nature of pellets. FO LHD systems can detect temperature changes in real-time, allowing for immediate action to be taken.
Another advantage is that these systems are highly accurate and can pinpoint the exact location of a temperature increase, allowing for targeted interventions and reducing system downtime and disruptions to the production process.
Unlike other fire detection systems, FO LHD systems are immune to industrial conditions including electromagnetic interference (EMI), dirt, dust and corrosion, extreme temperature changes, and explosive environments due to gas or dust, making them ideal for use in harsh industrial environments. The system is almost maintenance-free, as the optical fibers do not require any calibration or replacement, reducing the overall cost of ownership and ensuring that maintenance can be conducted without entering the protected area. Lastly, FO LHD systems are cost-effective and provide complete fire detection that is suitable for insurance purposes.
AP Sensing’s FO LHD solution has the most thorough set of type tests and certifications on the market with incredibly fast detection and a low false alarm rate. This solution utilizes a single passive fiber to cover the longest range on the market and offers extremely accurate localization of temperature changes and absolute val ues.
Success Story: Biomass Power Plant in Japan
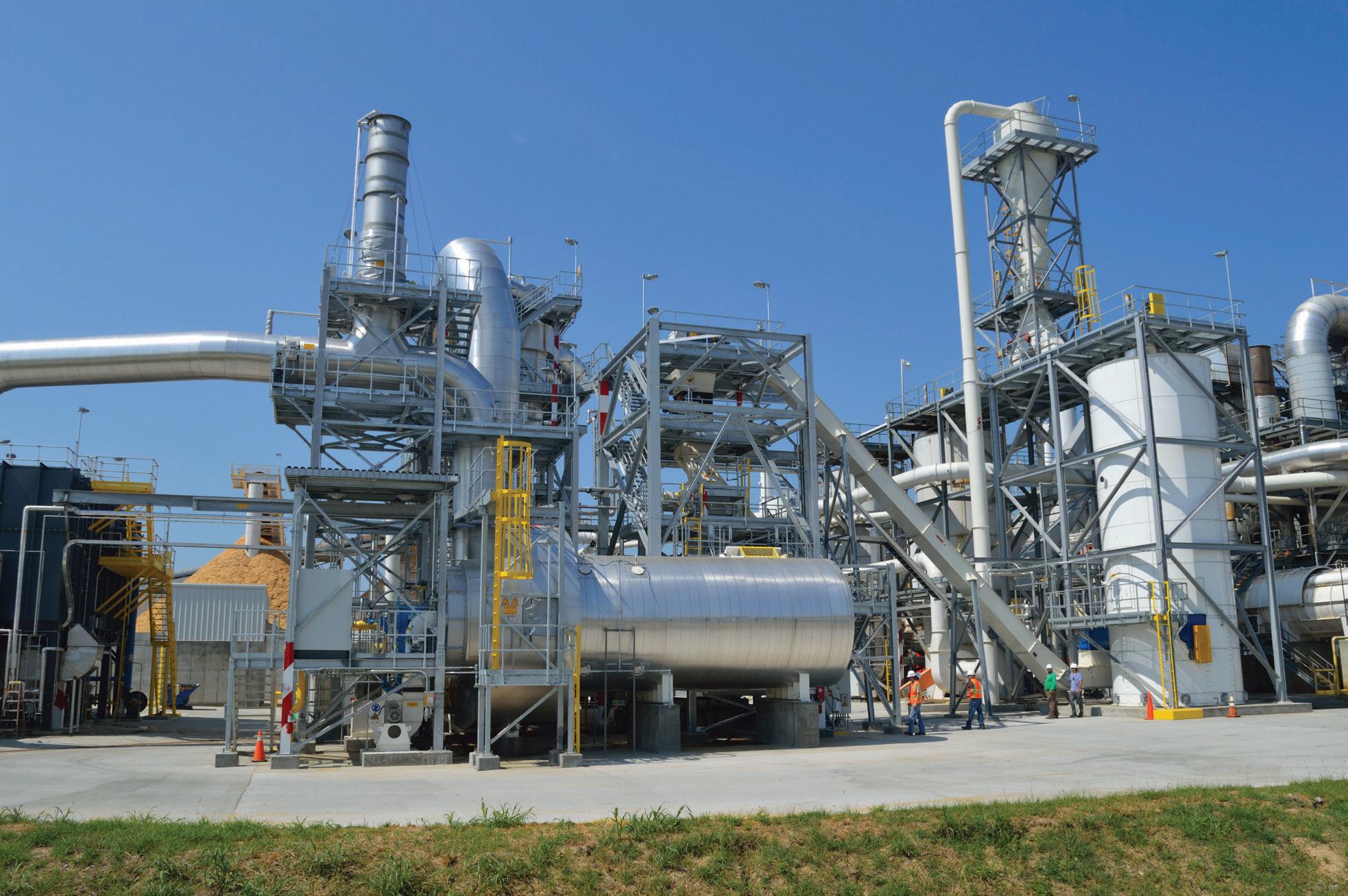
Biomass power generation uses bio logical materials as fuel to generate elec tricity. Wood chips, wood pellets and palm kernel shells are used as biomass fuel. Us ing biomass fuels as an alternative to fossil fuels enables the reduction of CO2 emis sions during power generation. By nature, woody fuels are flammable. For example, when wood chips stick to moving parts of conveyors, they may cause fire. To prevent this, continuous monitoring along the en tire conveyor of biomass fuels is necessary. Therefore, a renewable energy company
selected an AP Sensing FO LHD system for monitoring a newly constructed biomass power plant in Japan. AP Sensing’s system provided many benefits to the customer, including:
• One continuous sensor, monitoring the 4-kilometer conveyor 24/7, 365 days a year
• Pinpointing of temperature measurements for rotors as well as conveyor-side atmosphere
• Graphic display shows real-time temperature
• Historical temperature trace data
• Maximum reliability under harsh, explosive, and EMI environments
• Integrates easily into existing fire detection systems or fire control panel
Conclusion
The use of FO LHD technology provides a wide range of benefits to the wood
pellet industry, including continuous, complete fire and hotspot coverage and detection, a reduction of costly downtime and damages, as well as loss of reputation.
FO LHD technology is a cost-effective tool for the wood pellet industry, offering a highly sensitive, accurate and reliable solution for detecting temperature changes and preventing fires. As the demand for renewable energy sources continues to grow, the wood pellet industry is set to expand, and FO LHD systems play a critical role in ensuring the safety and reliability of wood pellet production and storage.
Largest Biomass Event in North America
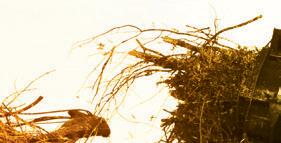


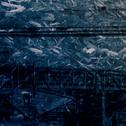
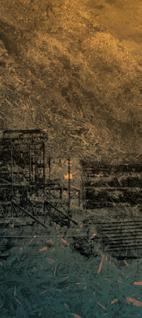


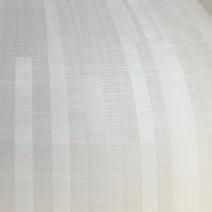
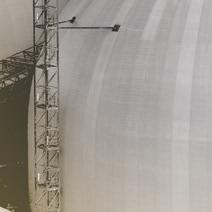
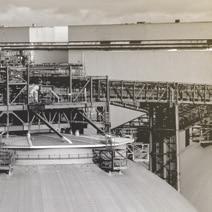
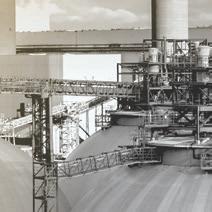
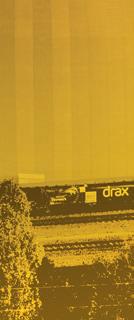
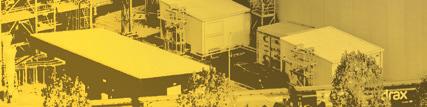
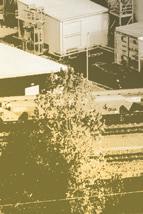
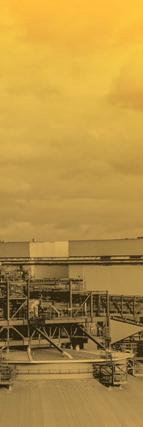
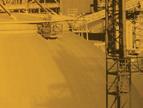
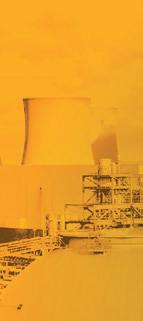
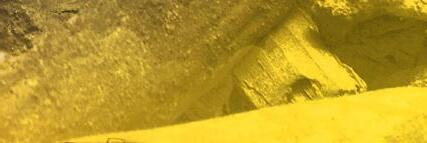
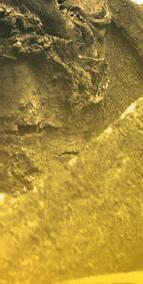
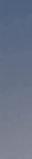

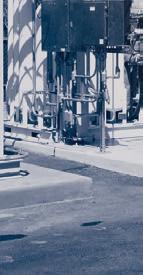
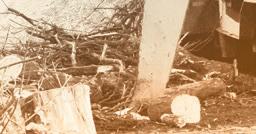
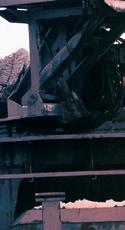
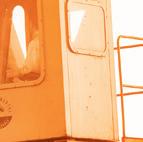
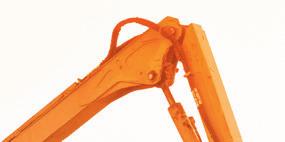
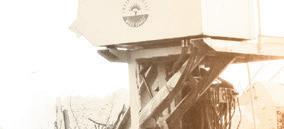
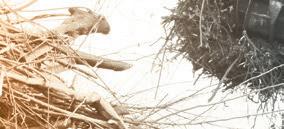
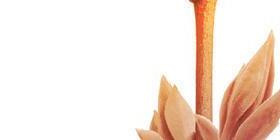
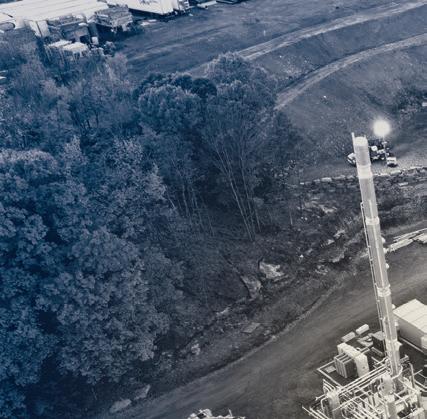
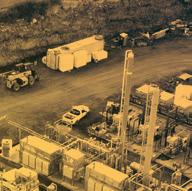
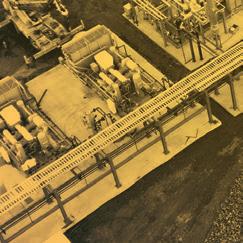
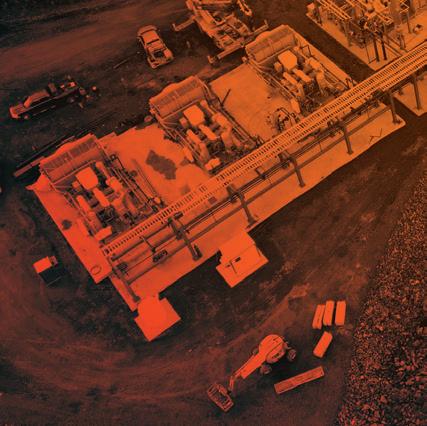

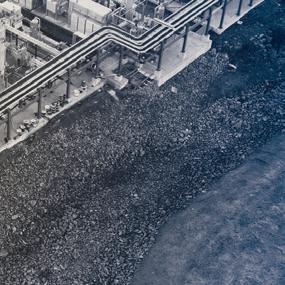
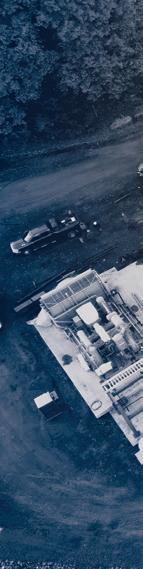

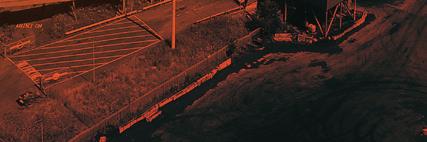

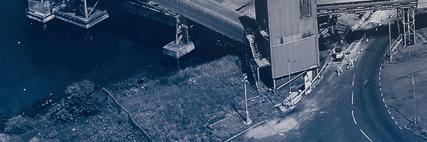
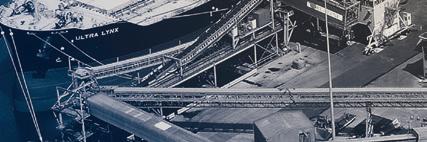
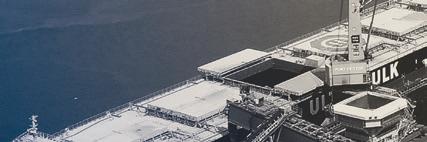
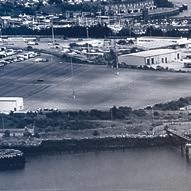

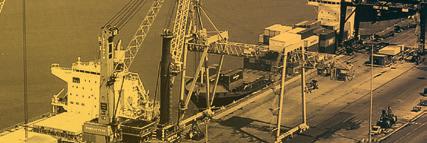
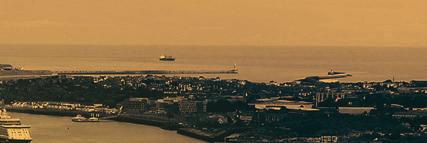
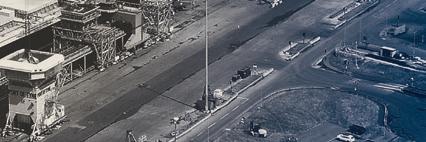
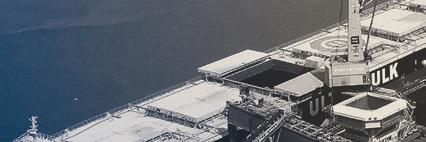
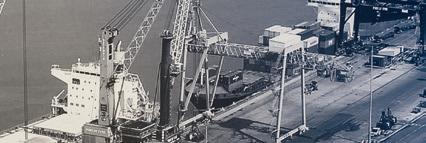
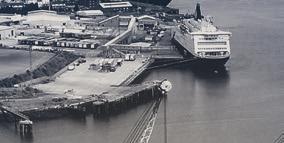

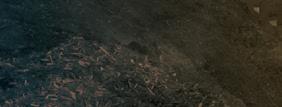



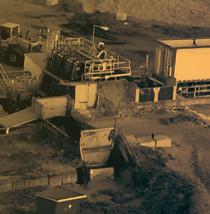

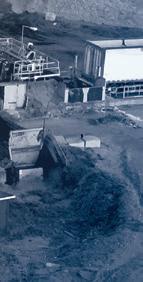

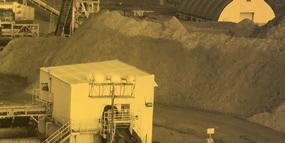
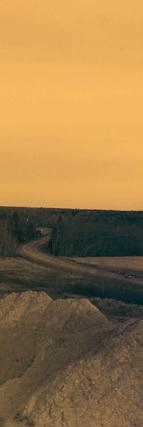
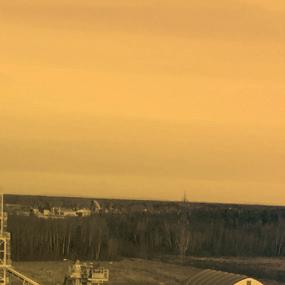
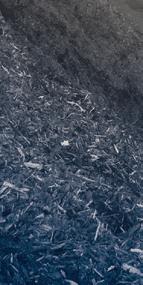
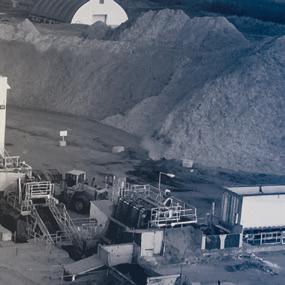
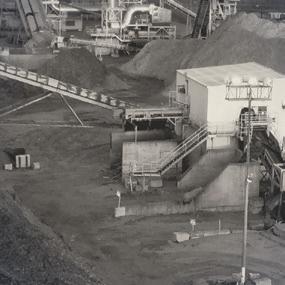
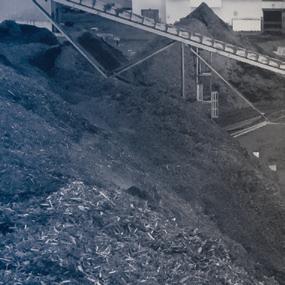
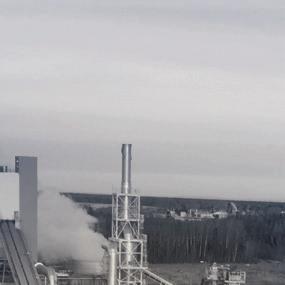
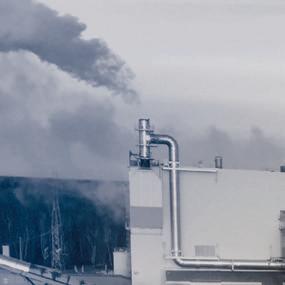
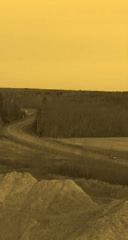
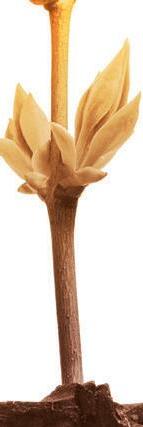
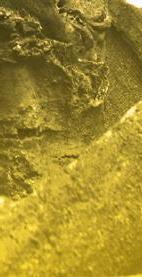
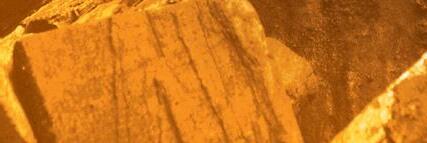
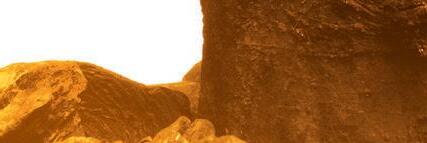
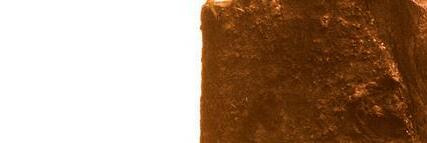

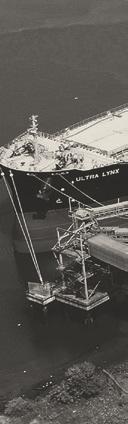
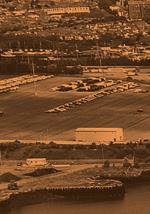

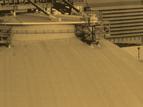
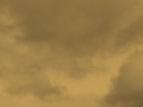
SAVE THE DATE
RICHMOND, VA
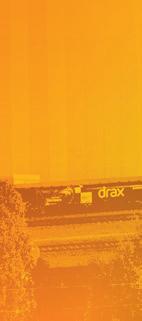
The Int’l Biomass Conference & Expo is where future and existing producers of biobased power, fuels and thermal energy products go to network with waste generators and other industr y suppliers and technology providers.
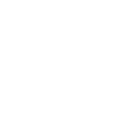
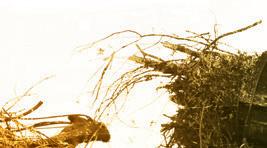
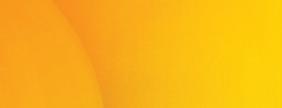
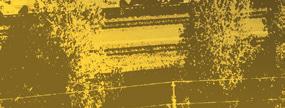

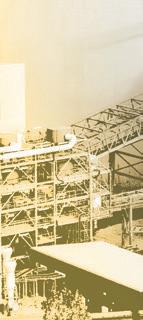

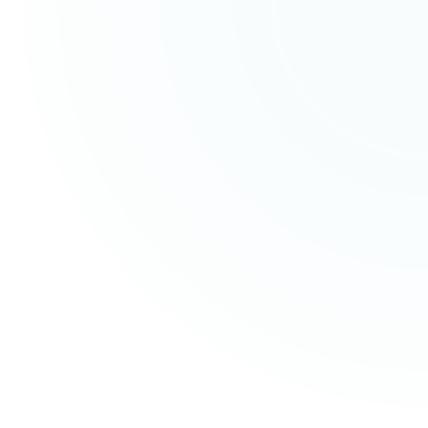

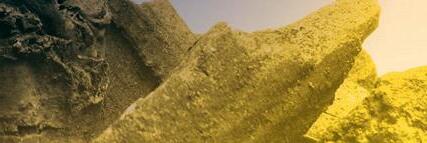

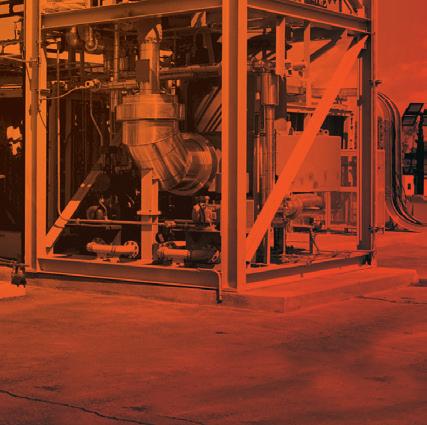

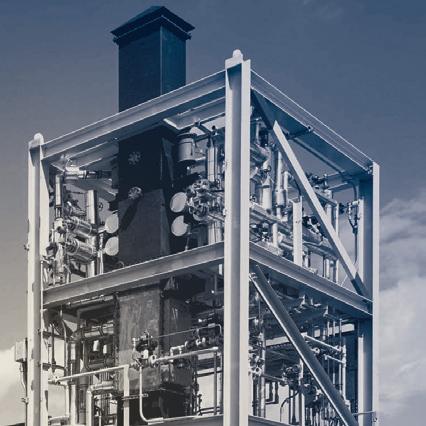
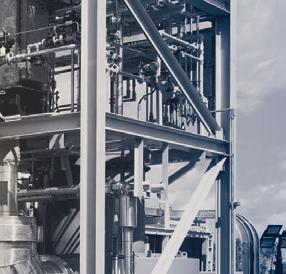
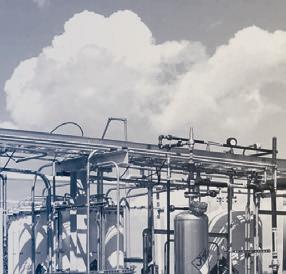


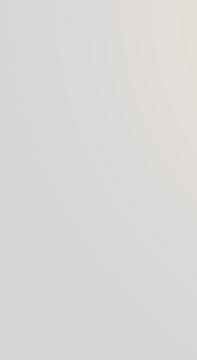
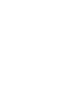




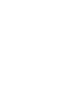
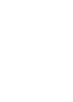


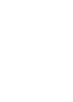

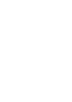
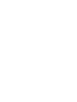
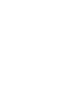
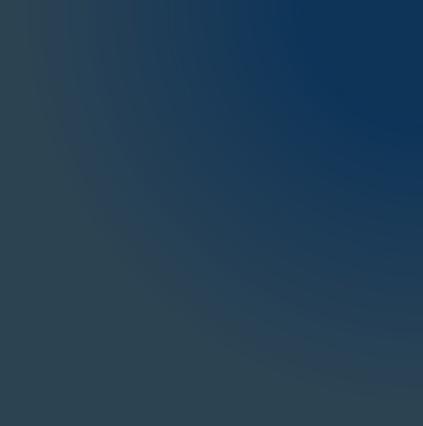

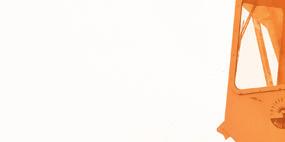
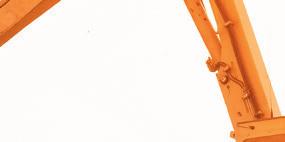
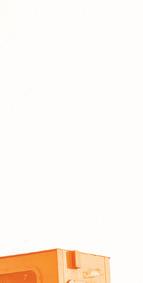
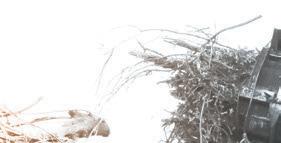


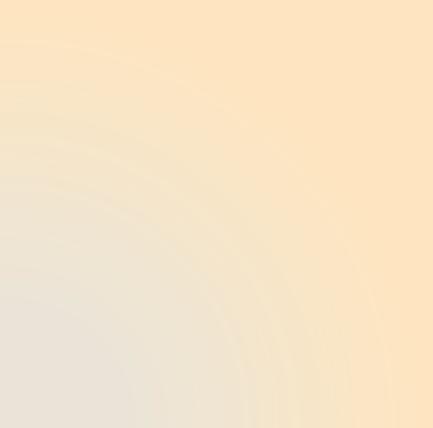
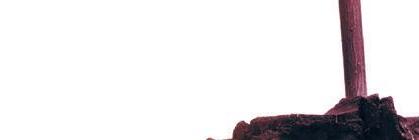
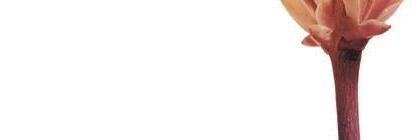
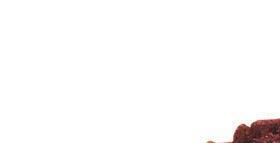

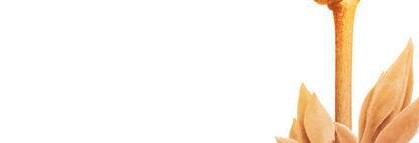
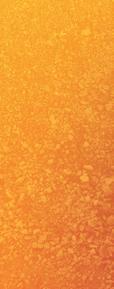
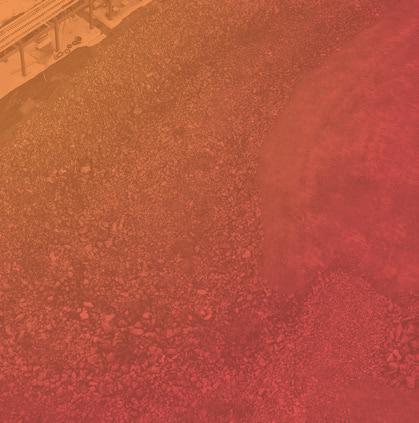
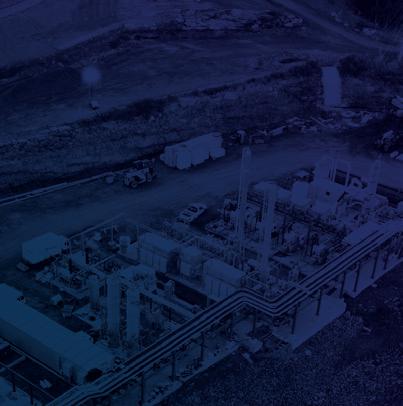
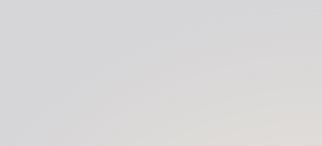

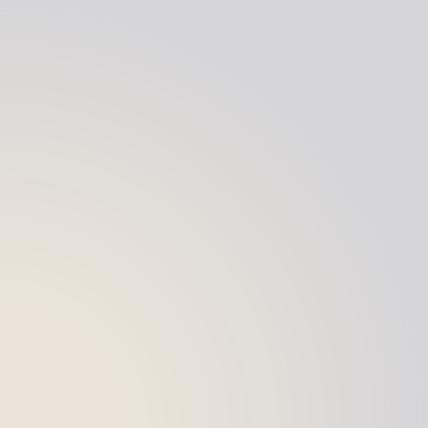
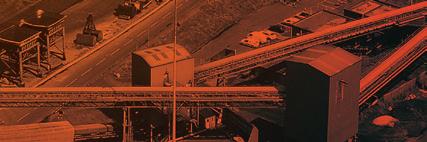
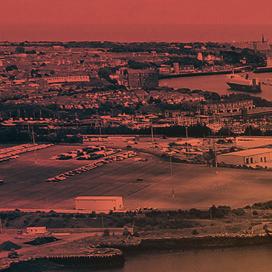
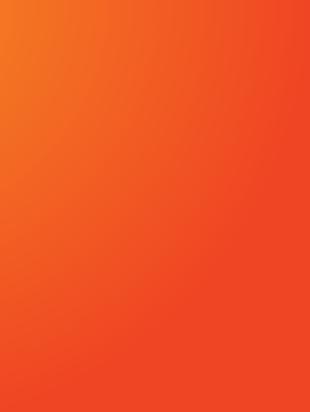
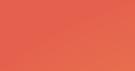
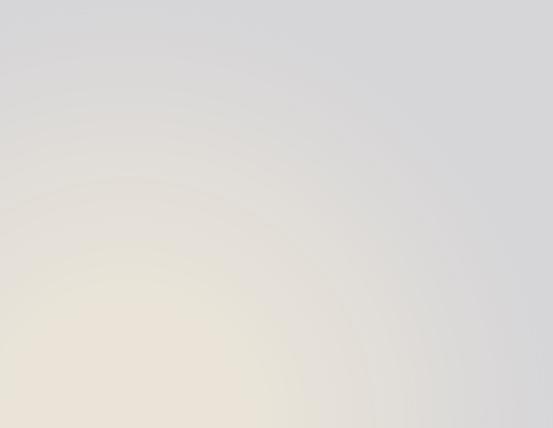
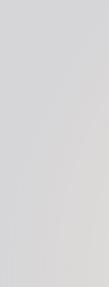

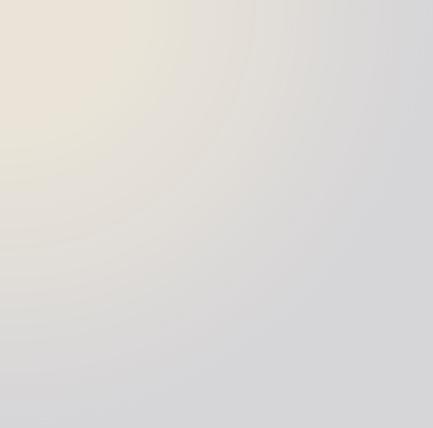
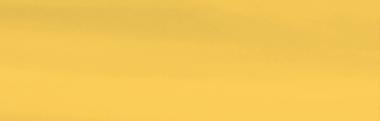

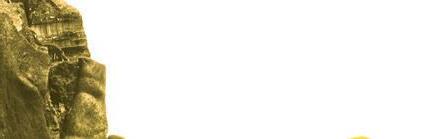

The Int’l Biomass Conference & Expo is the largest, fastest-growing event of its kind, the Int’l Biomass Conference & Expo is expected to draw nearly 800 attendees in 2024. In 2022, the event drew more than 700+ attendees, double the attendance of the inaugural show. This growth is fueled by a world-class expo and an acclaimed program.
#IBCE24
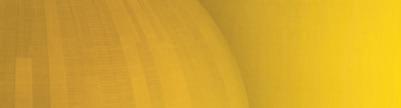
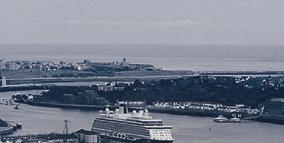
twitter.com/biomassmagazine
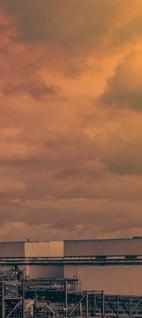
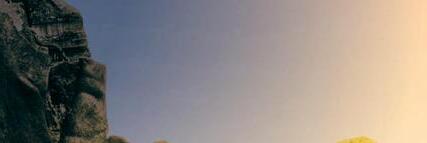


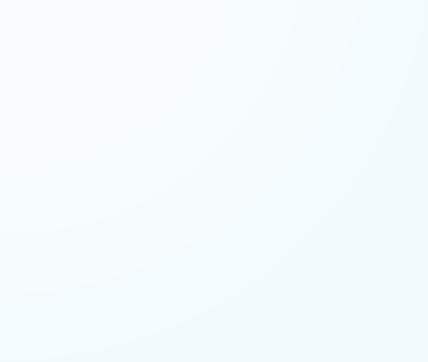
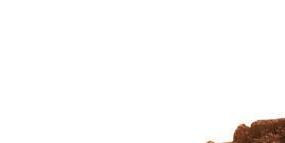
866-746-8385
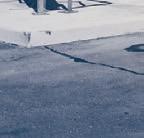
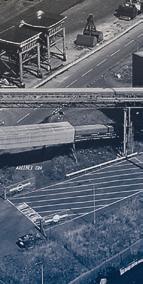
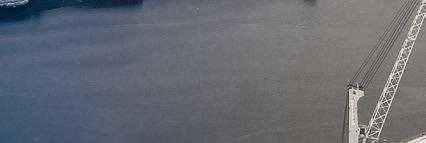



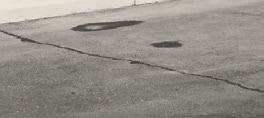

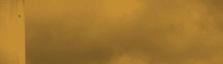
service@bbiinternational.com
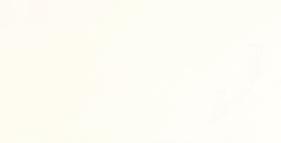
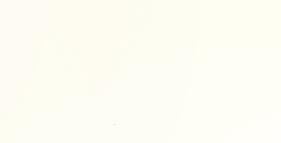

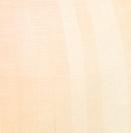

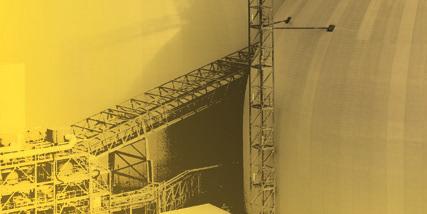

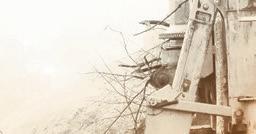

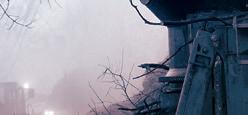
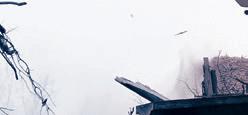
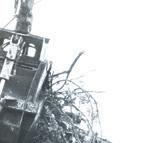

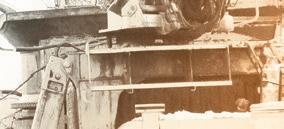
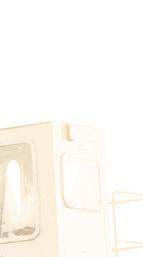
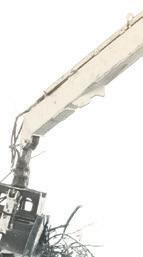
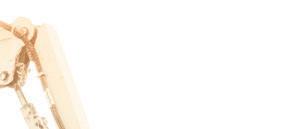
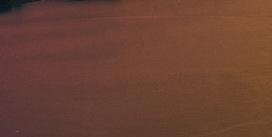
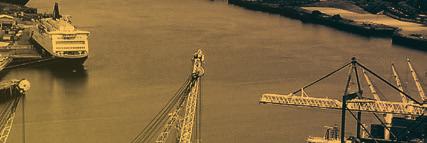
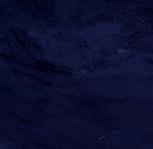

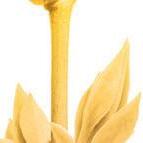


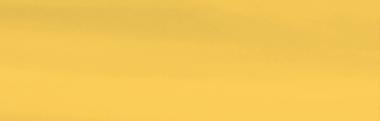
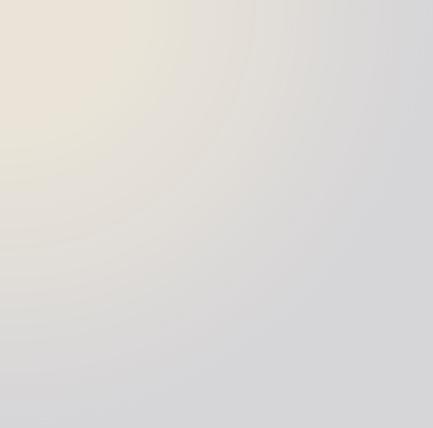
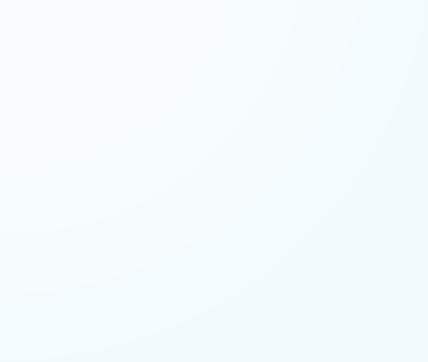

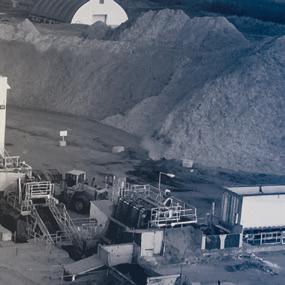
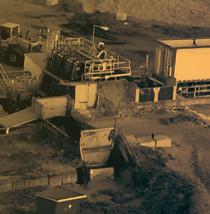
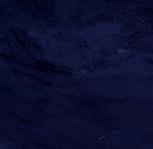
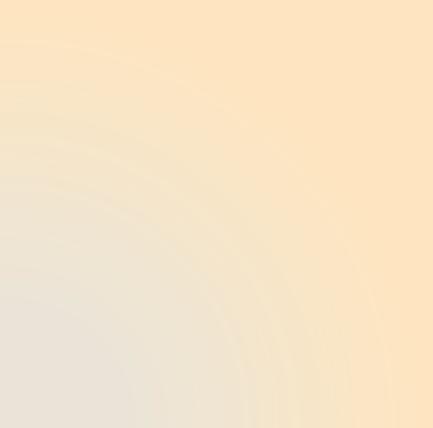
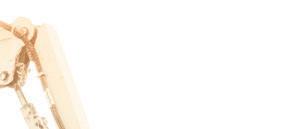
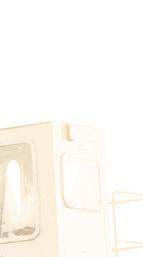
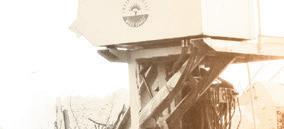
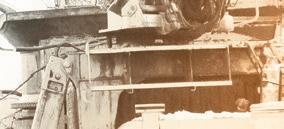
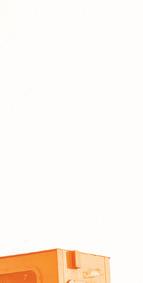
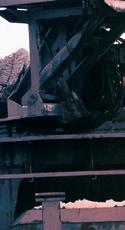


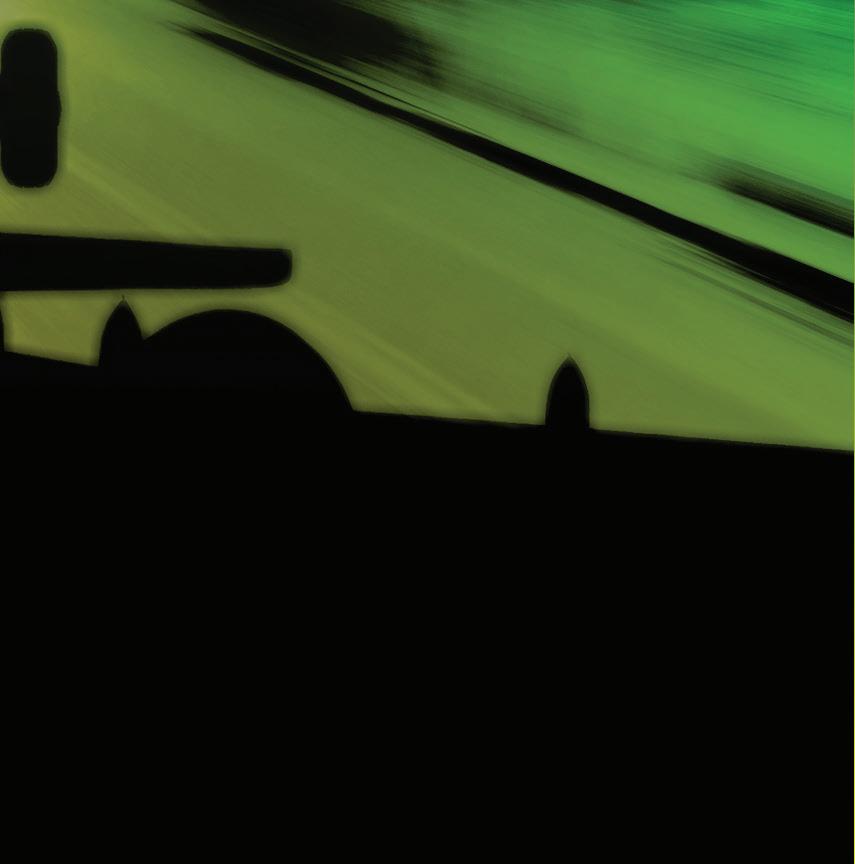
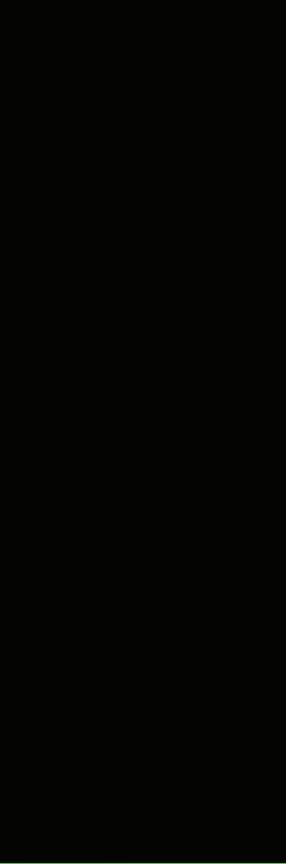
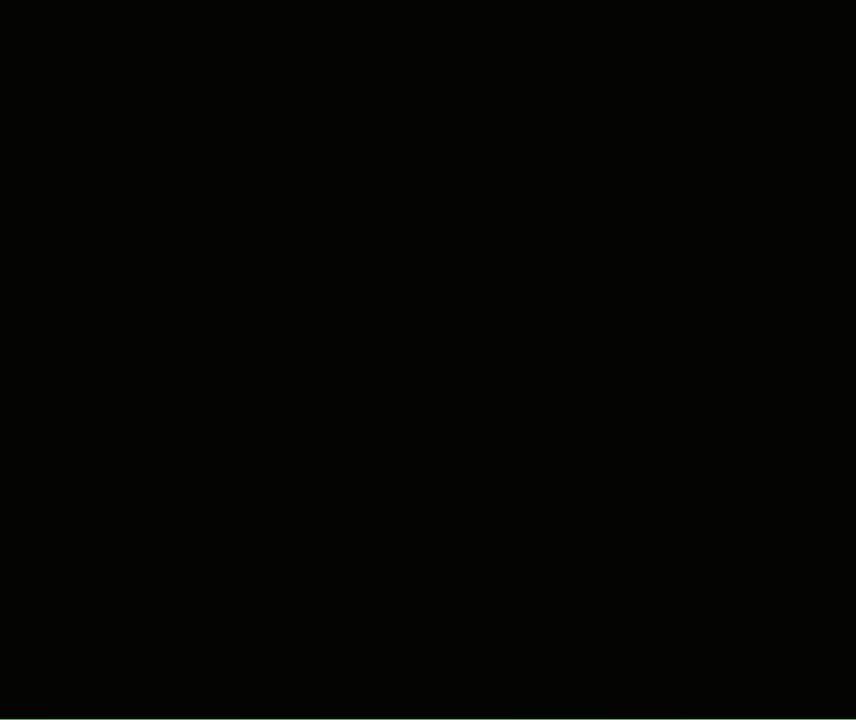
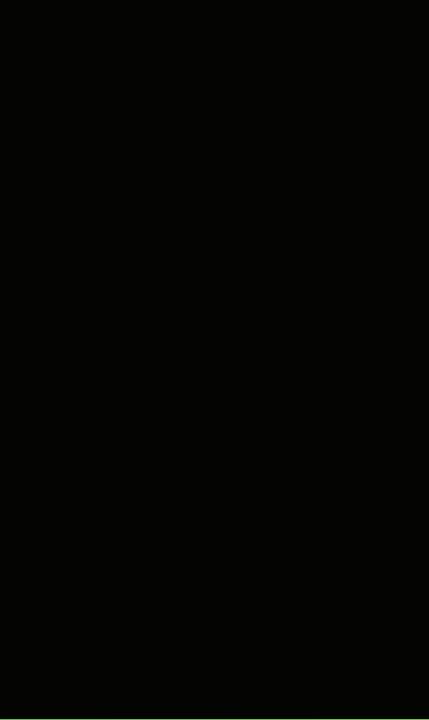
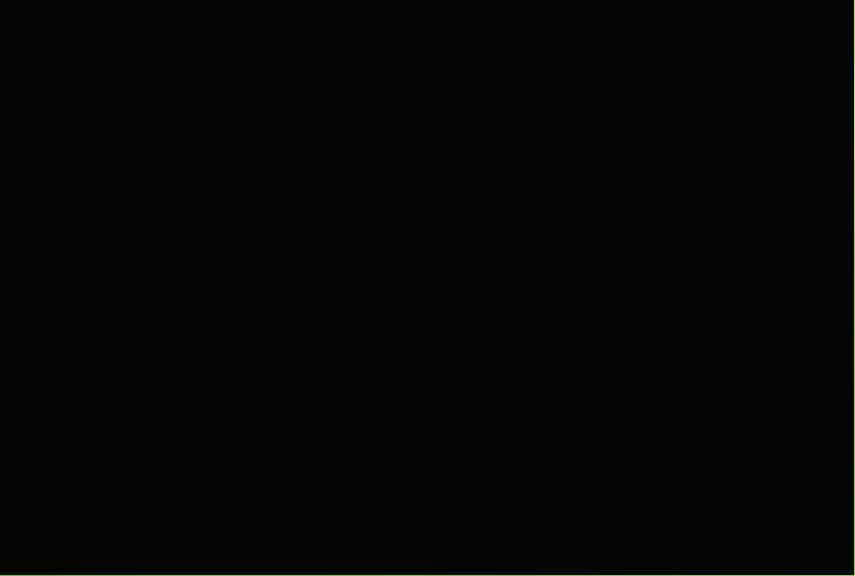

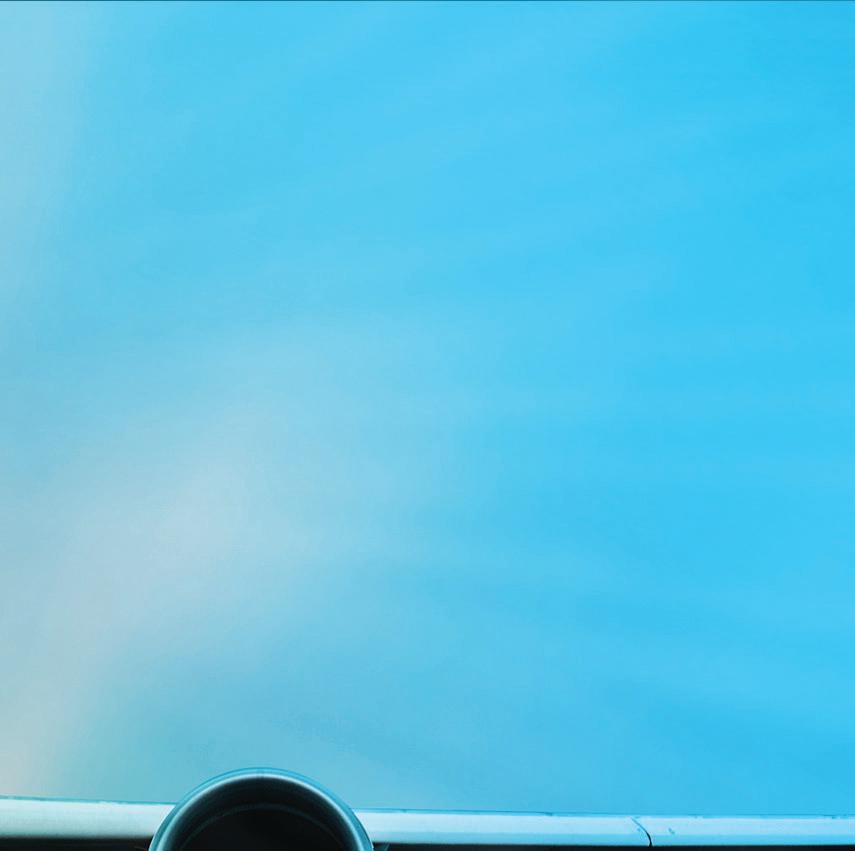
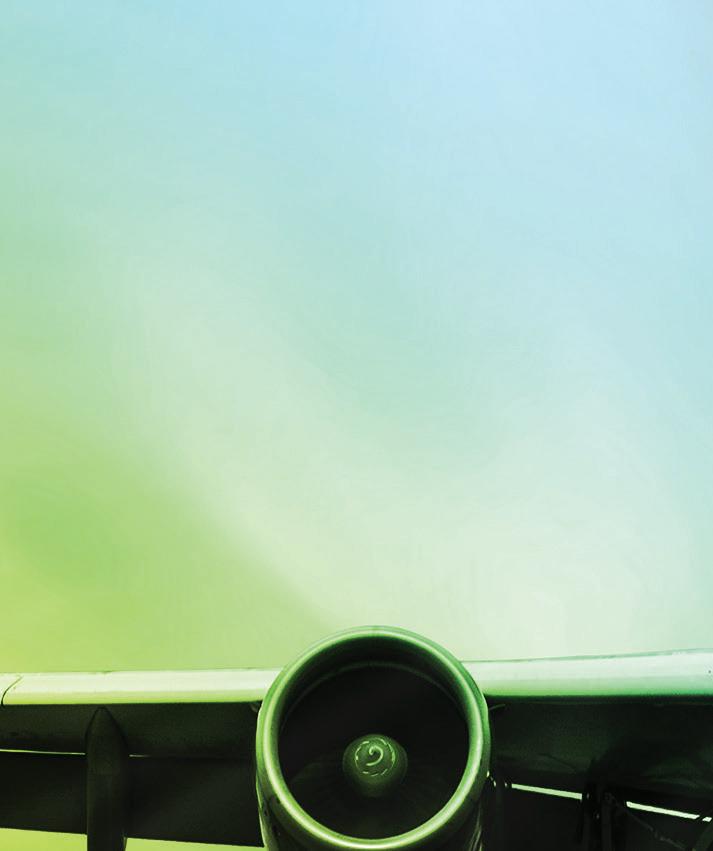
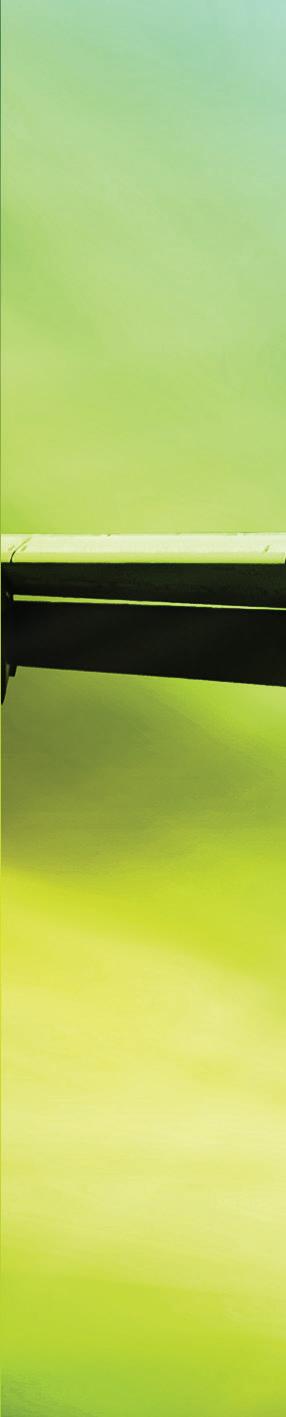
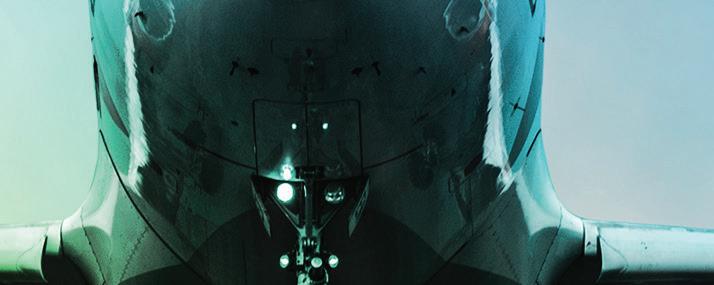
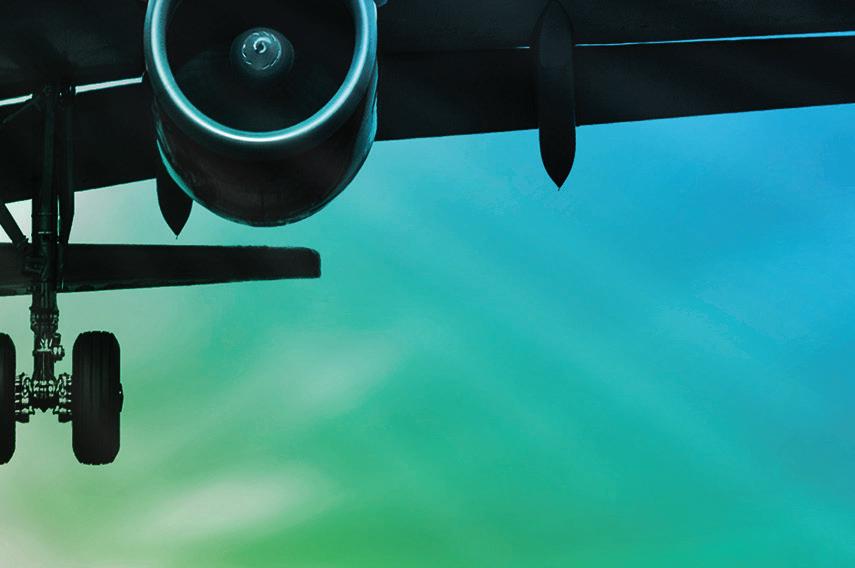
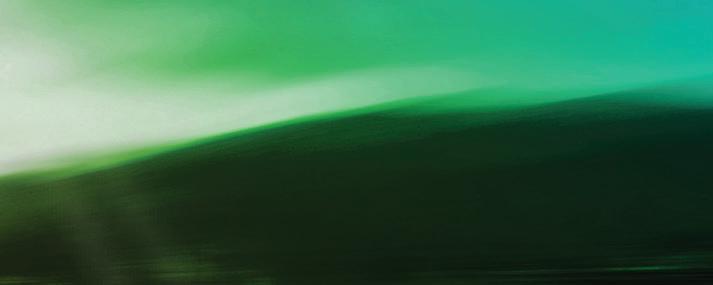
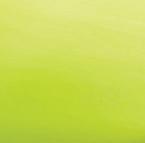

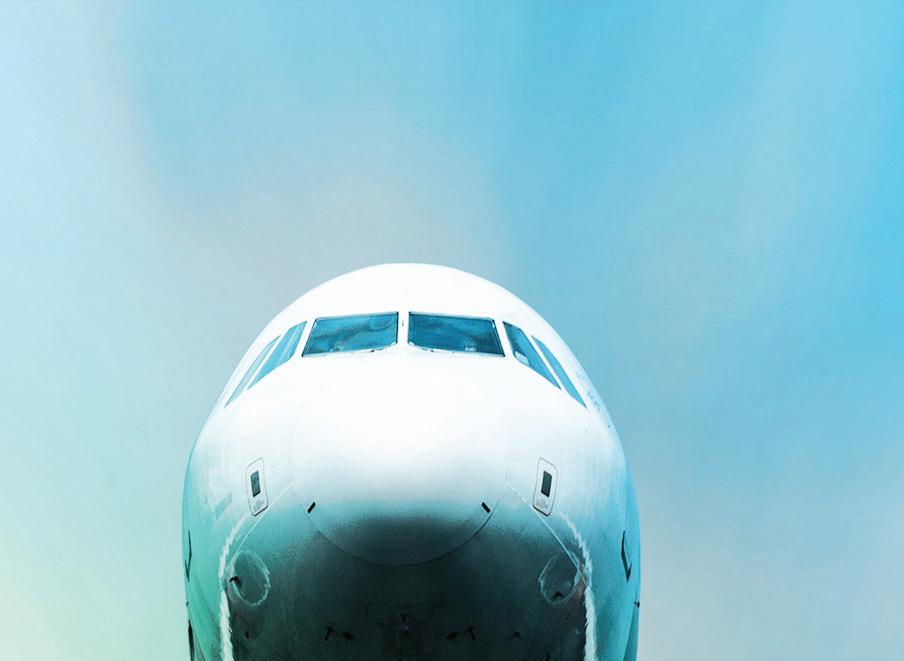
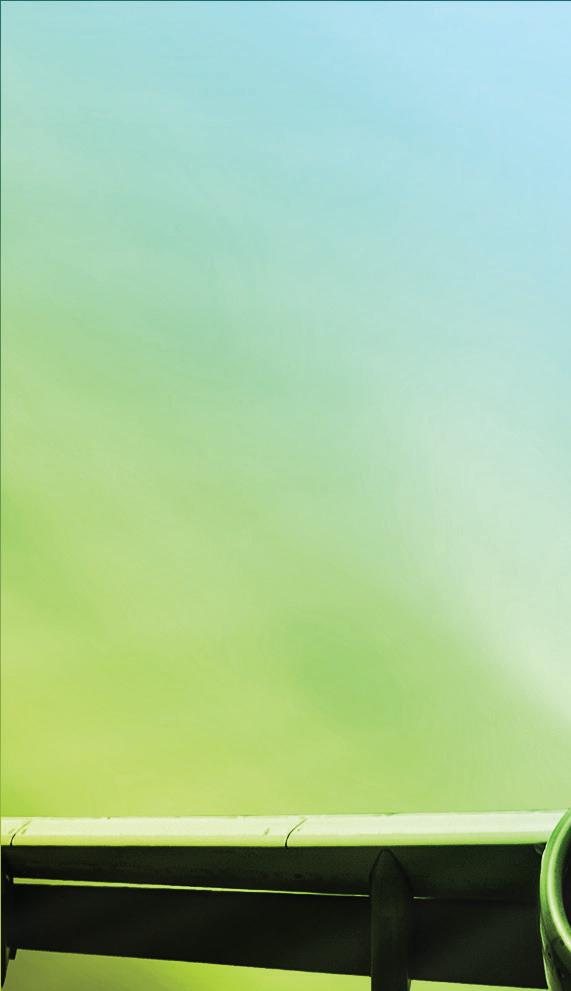
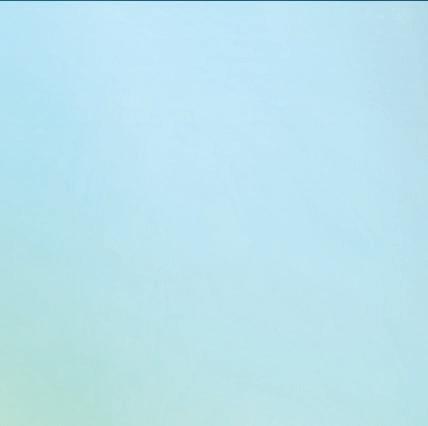

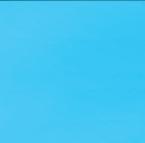
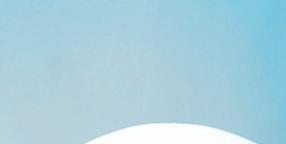
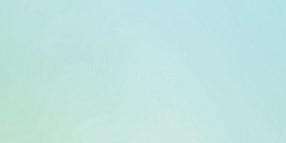
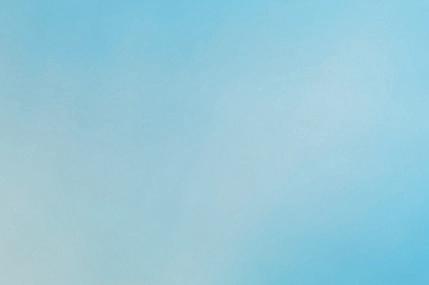

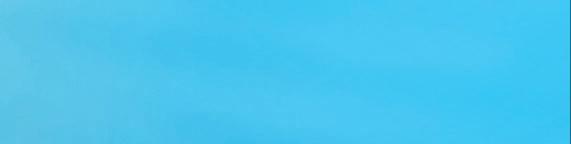
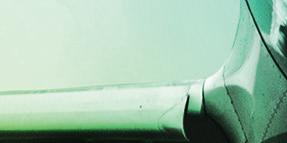
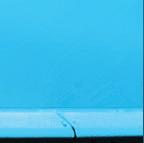

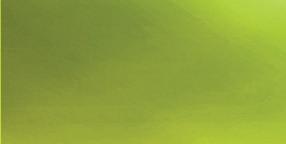

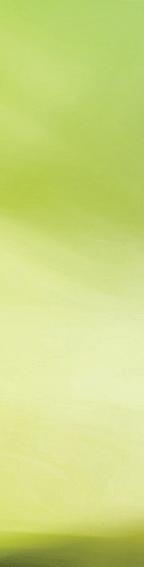
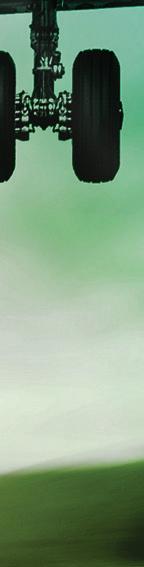
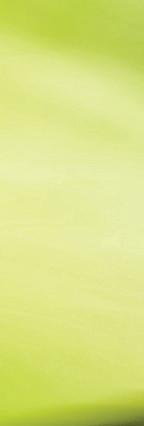
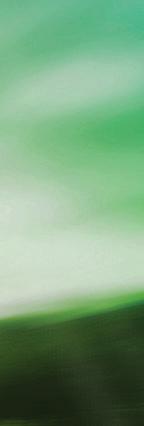
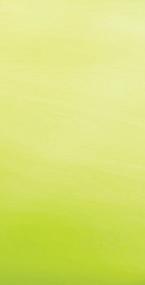
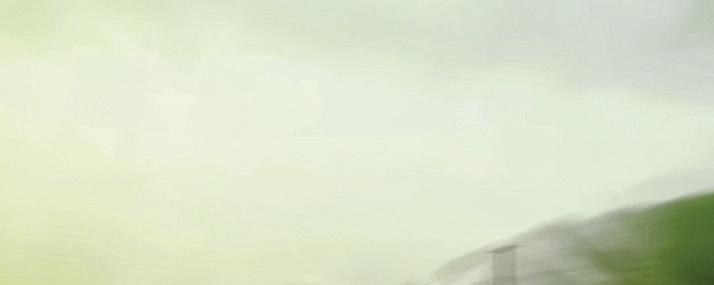

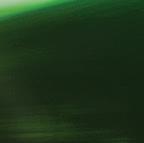
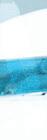
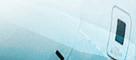
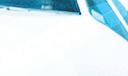










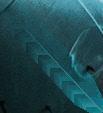
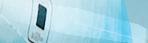



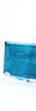

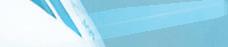


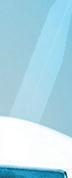
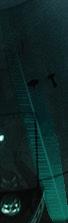



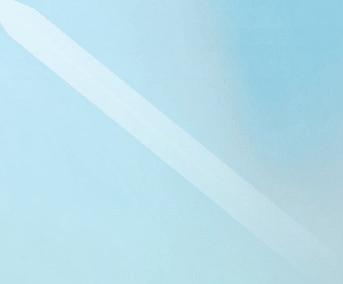
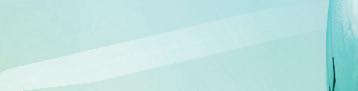
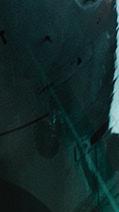
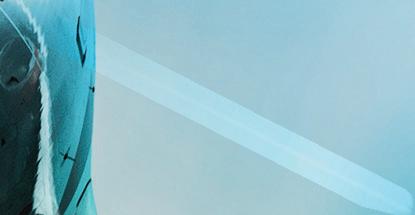
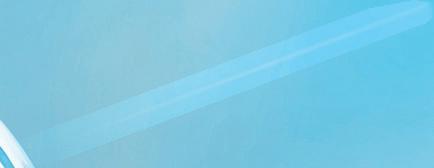
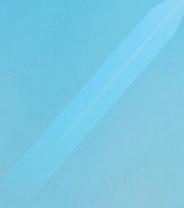
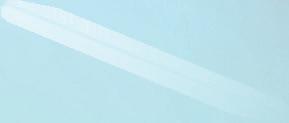
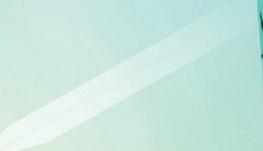
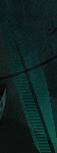

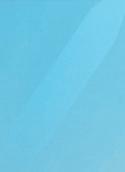
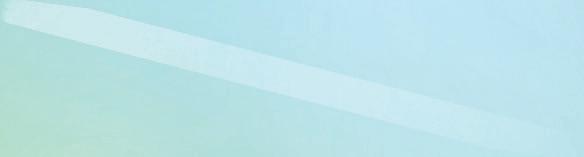
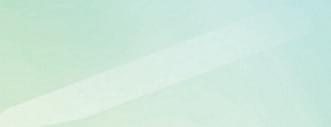
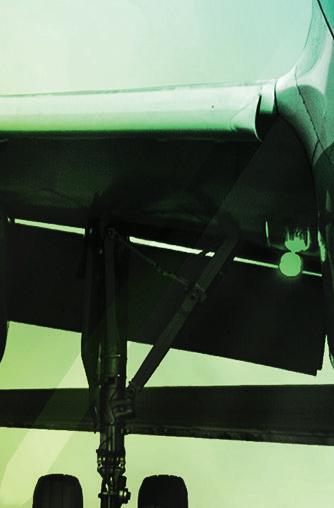
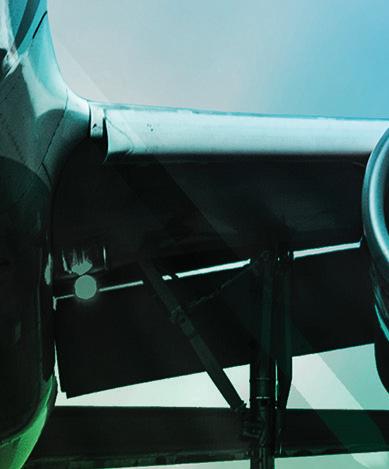
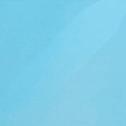
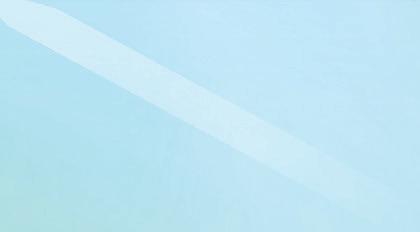

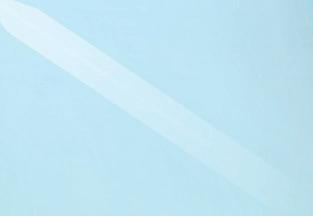


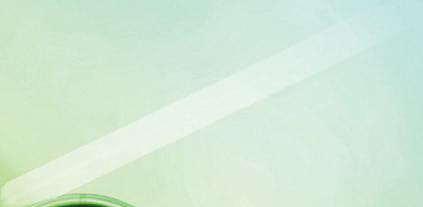

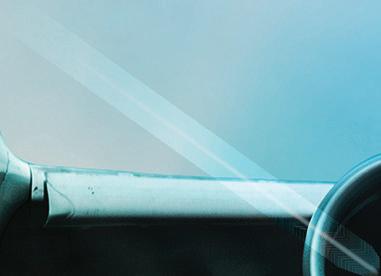


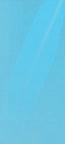
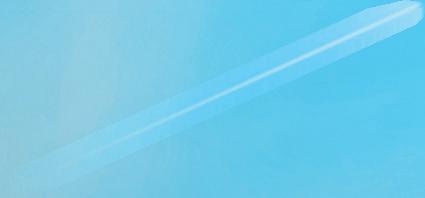
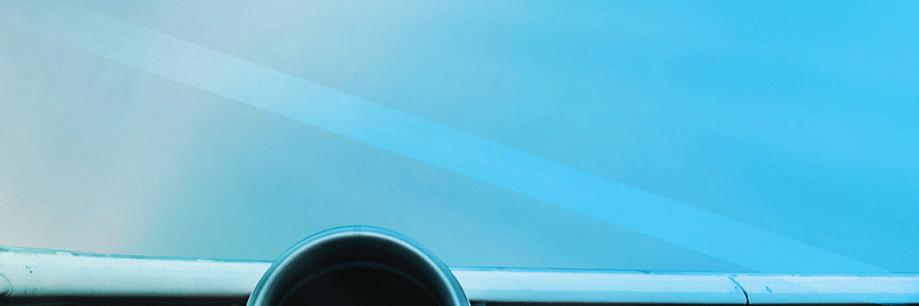
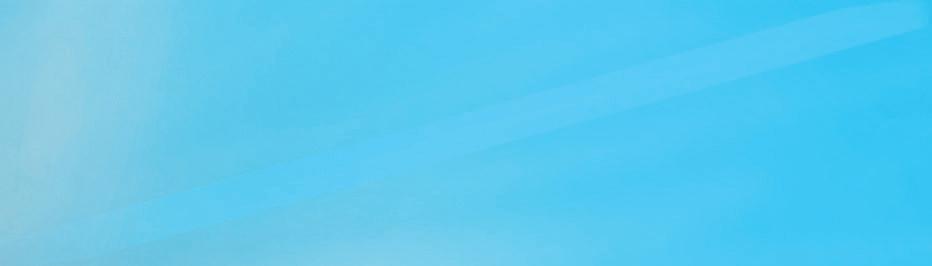
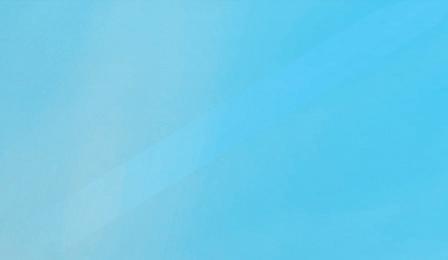

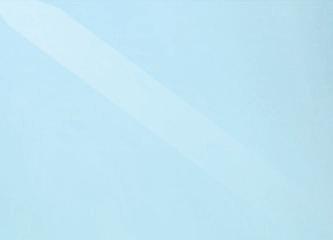



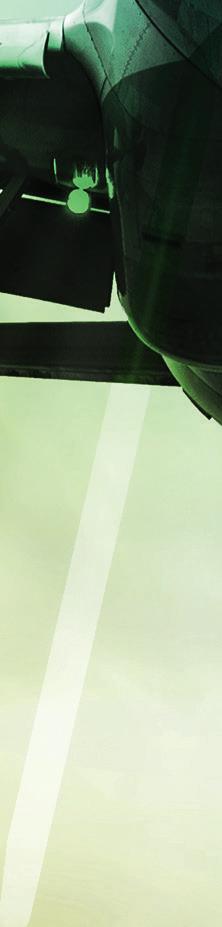
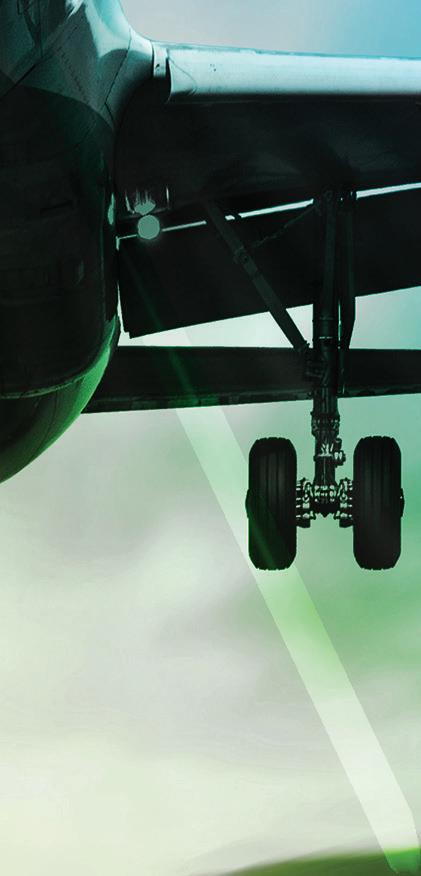
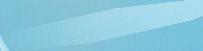
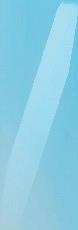


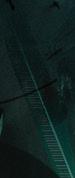
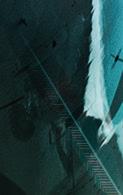
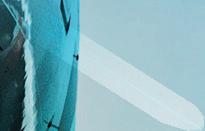
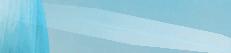
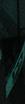
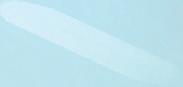
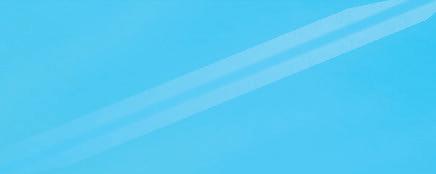

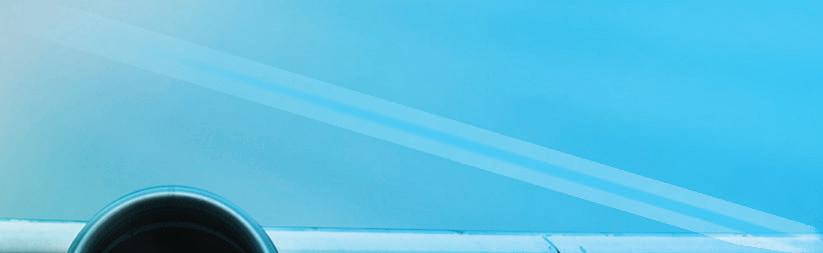
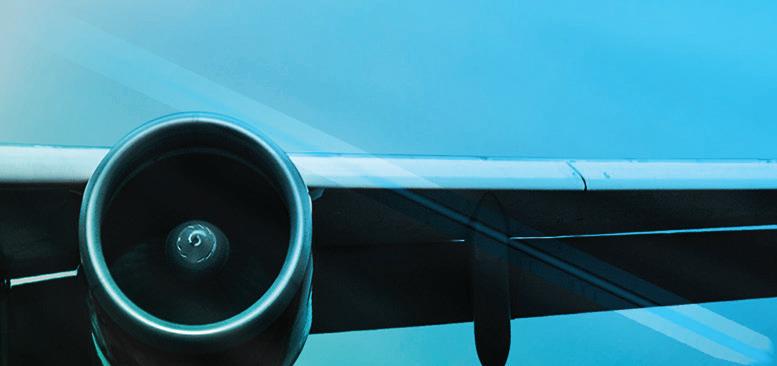
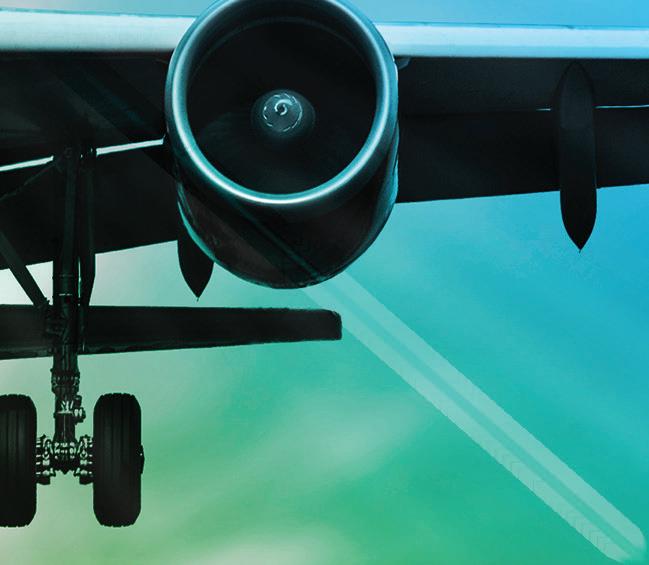
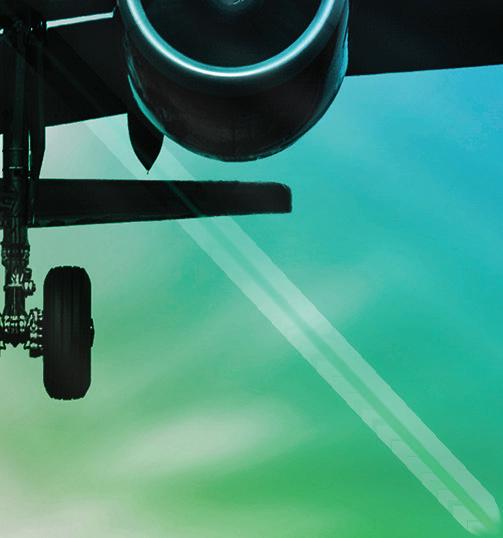
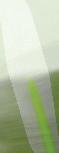

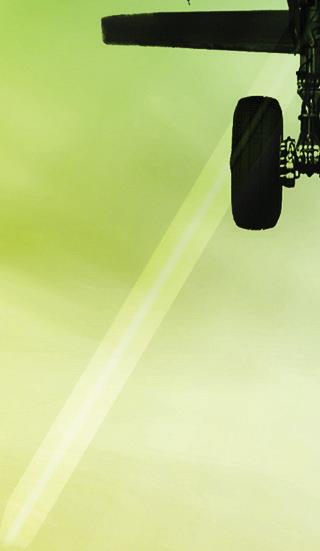
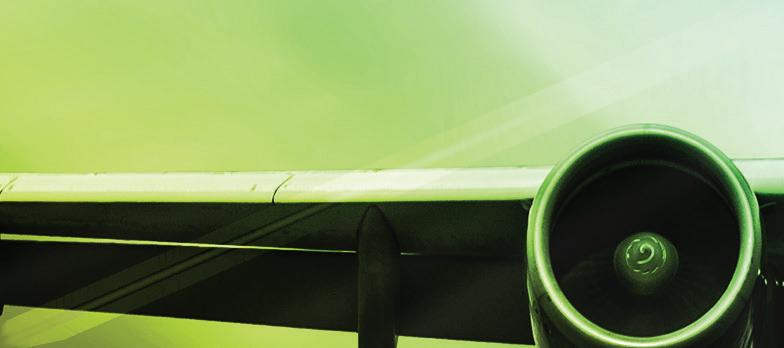
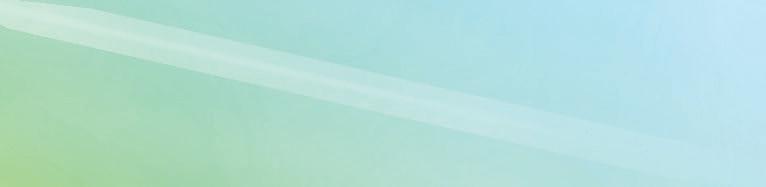
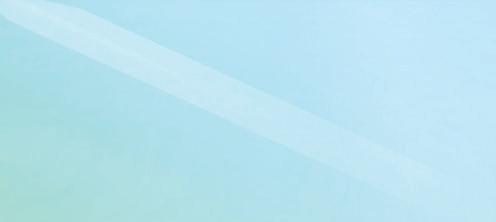
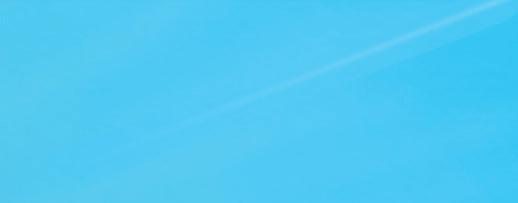


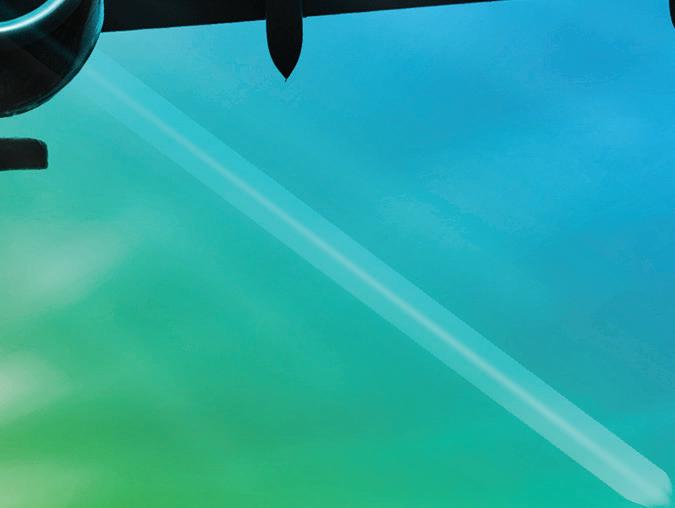
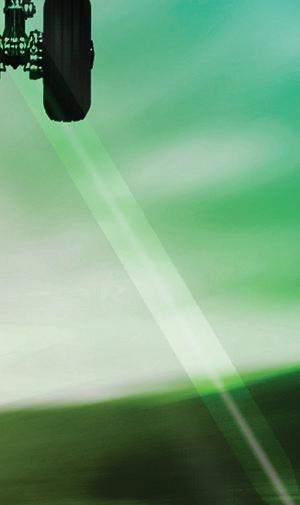

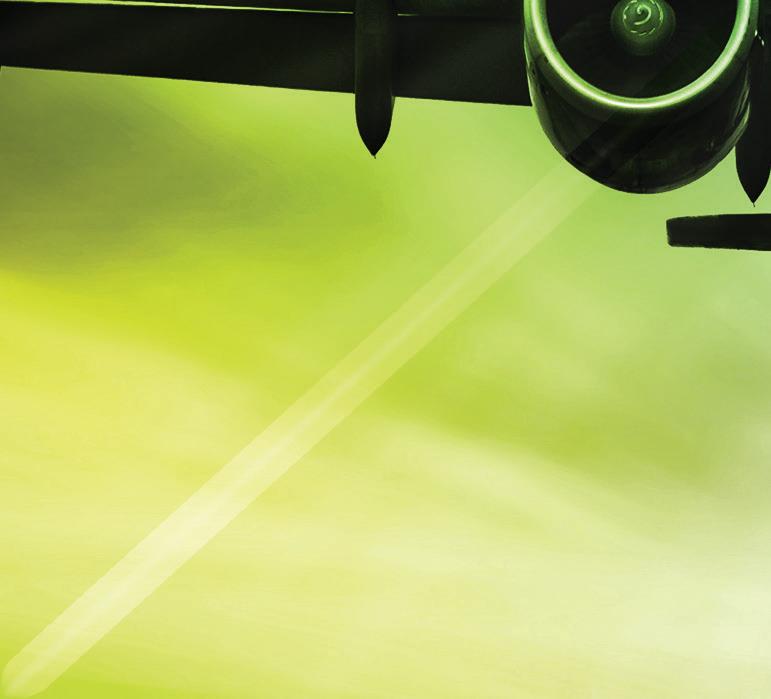
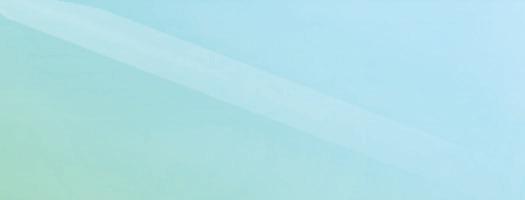
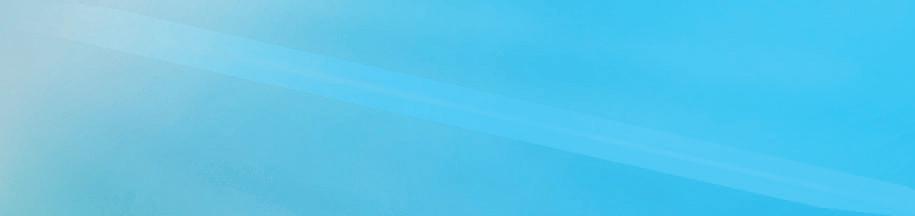
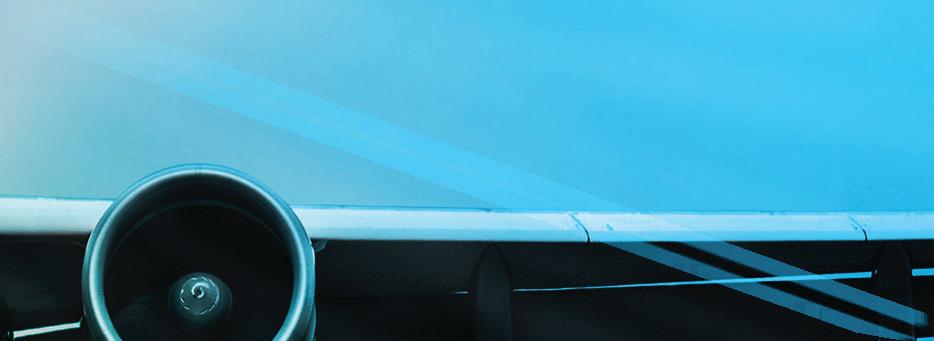
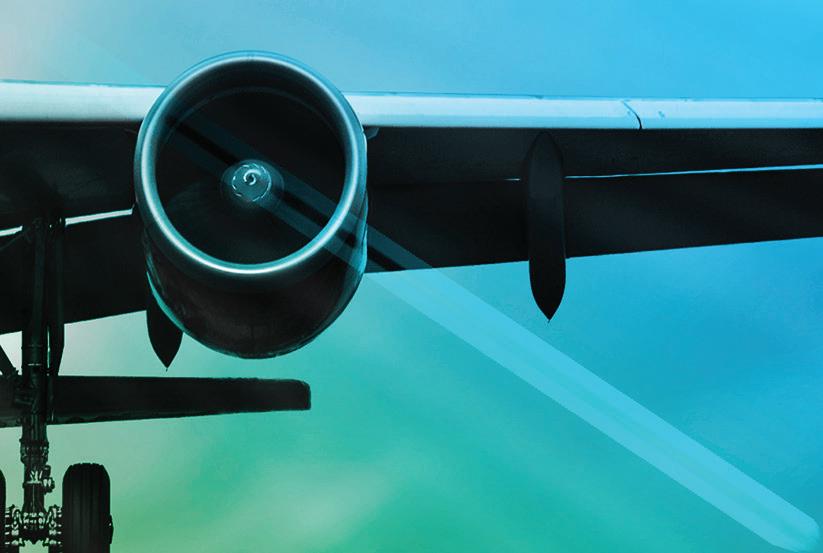
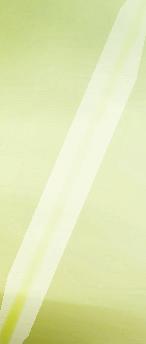

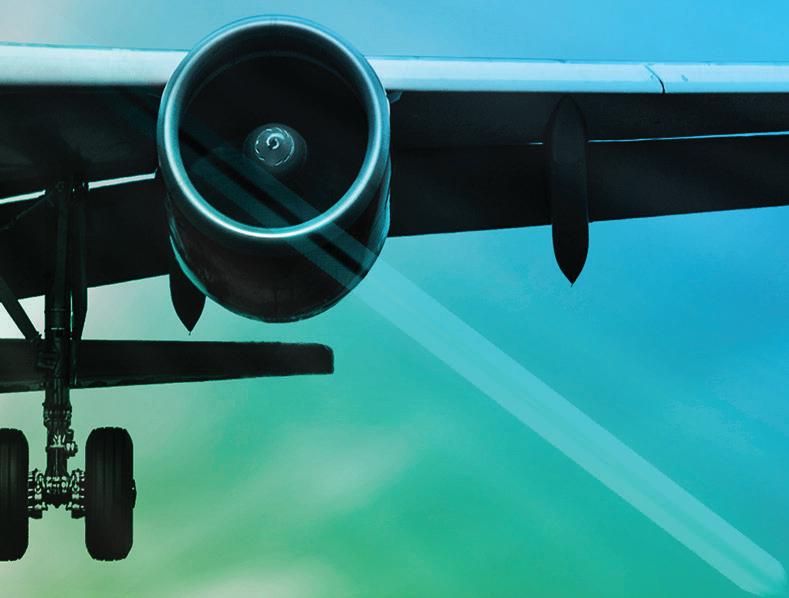
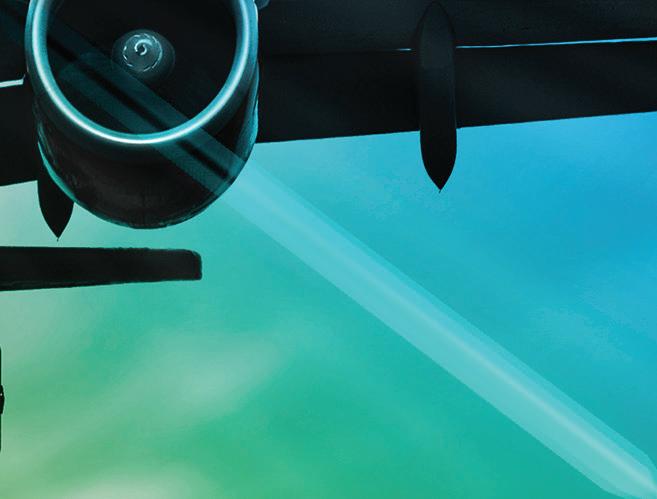
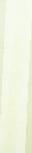

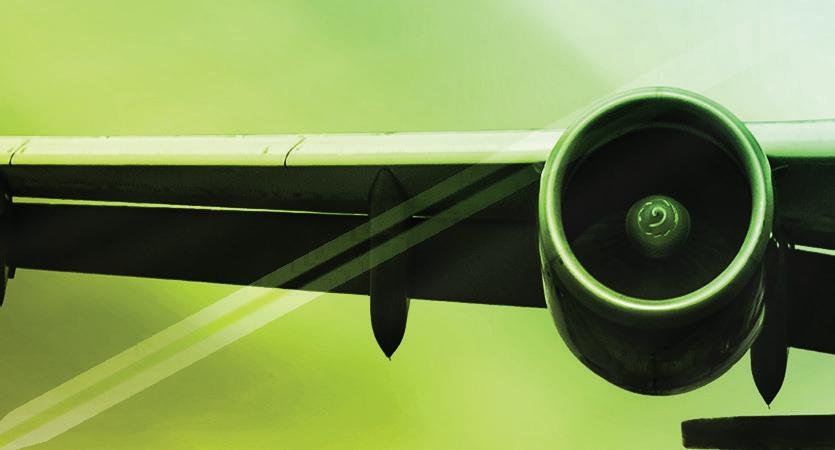
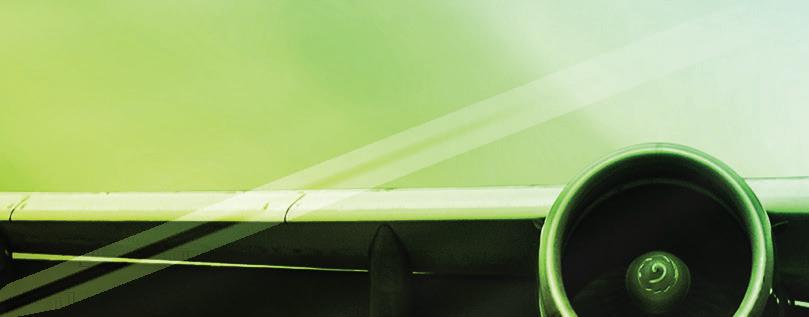


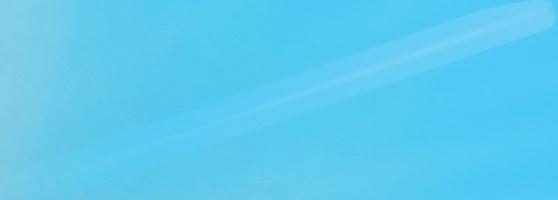
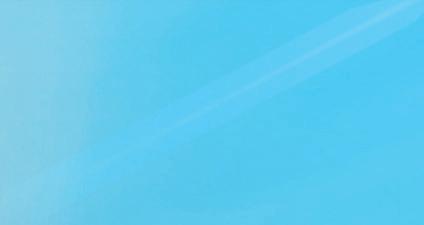
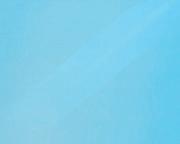
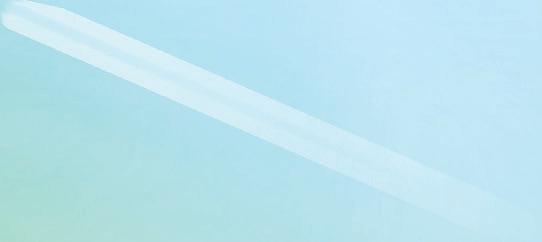

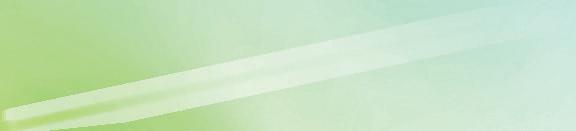

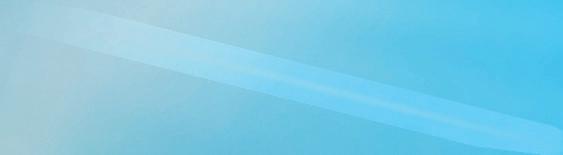



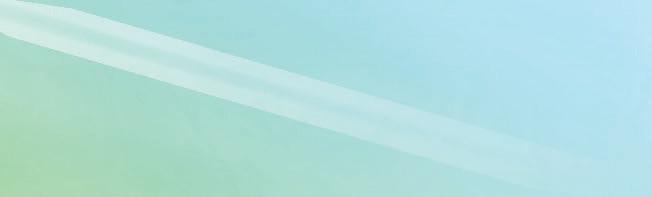

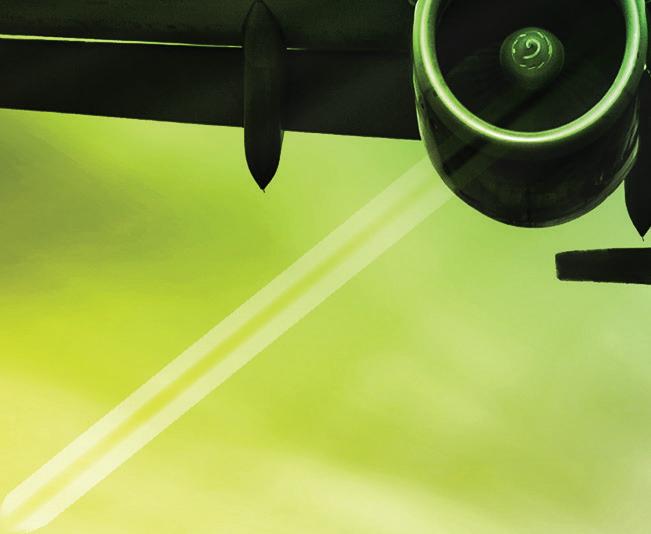
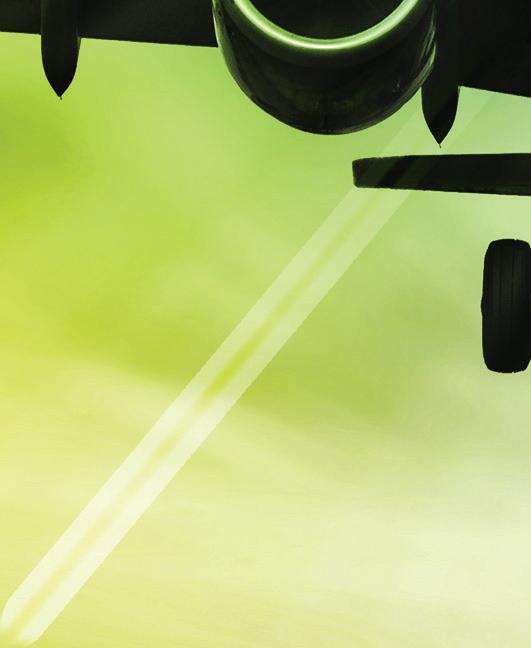
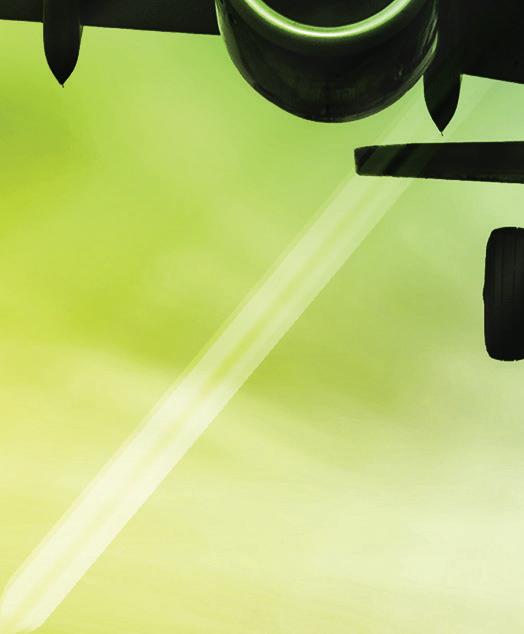
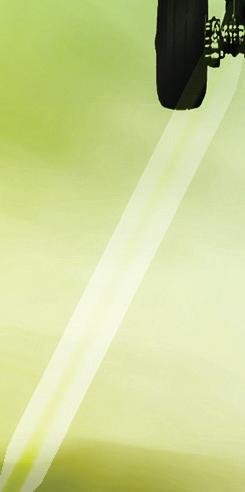
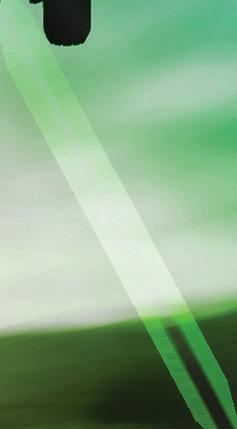
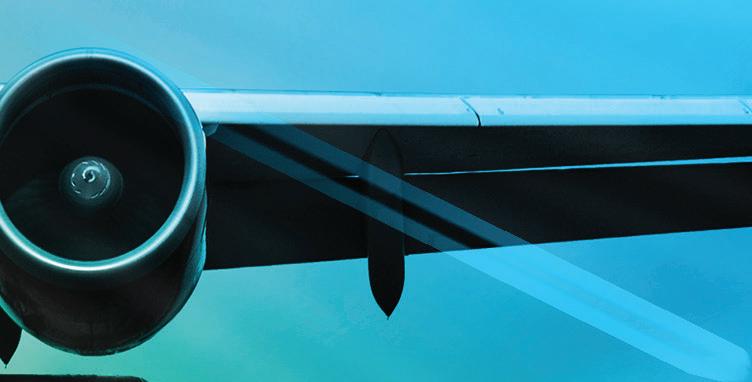

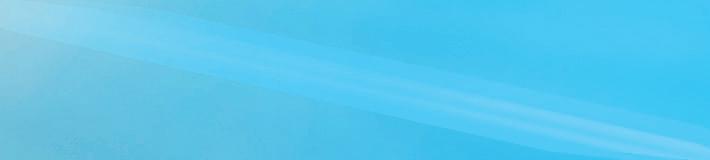

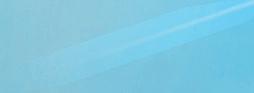
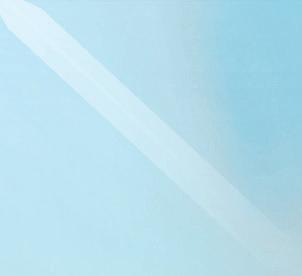
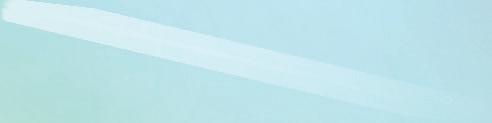



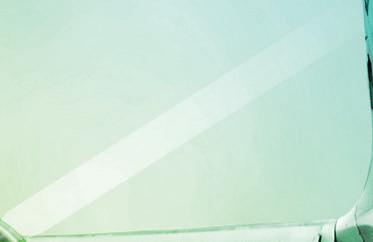





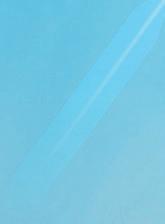
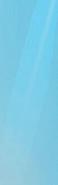
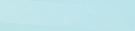
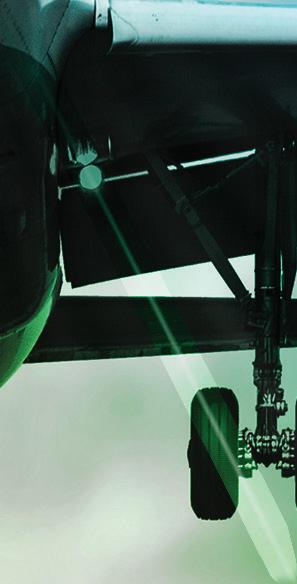

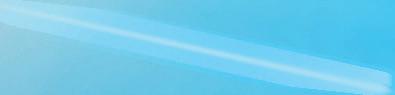
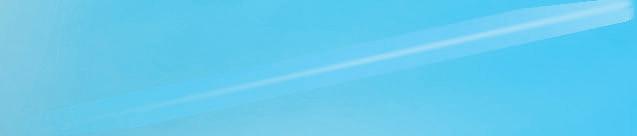
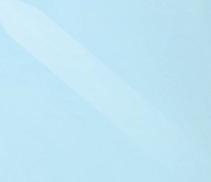
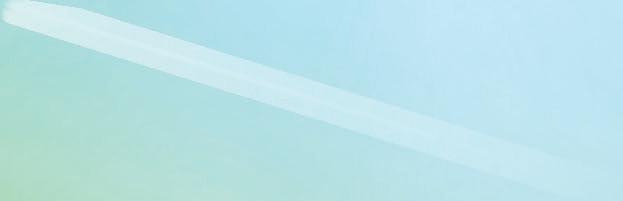

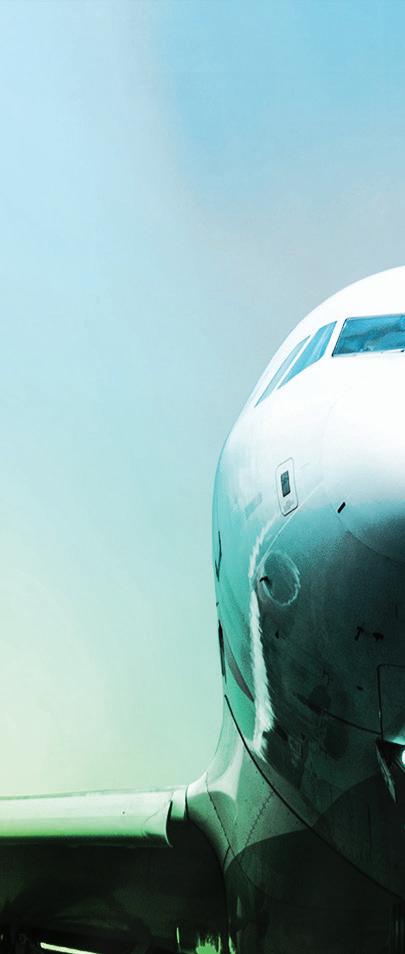


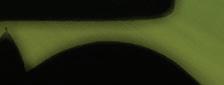
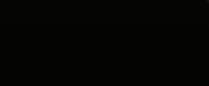

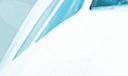


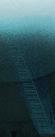

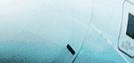





















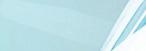
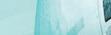

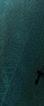
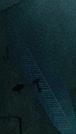


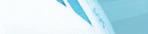

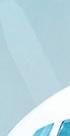





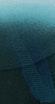

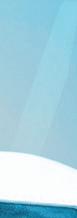
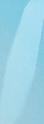


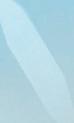



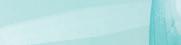
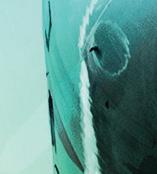
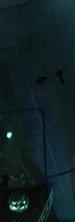
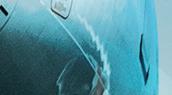
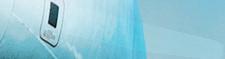

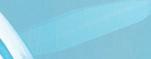

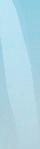
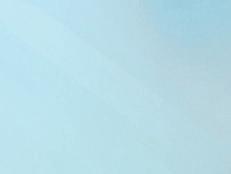


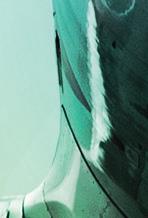

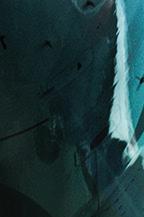

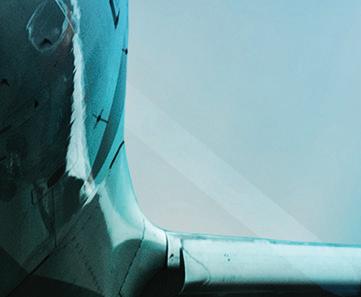
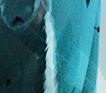

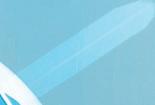
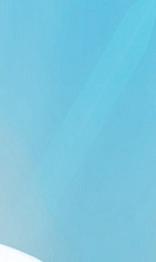


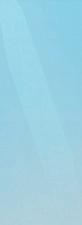

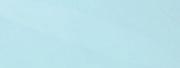



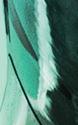
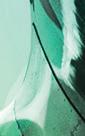
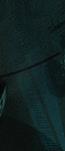


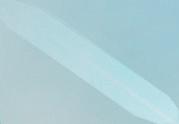
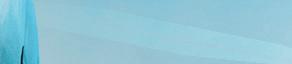
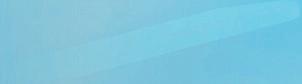
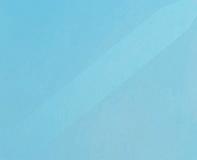
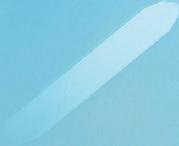


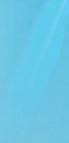
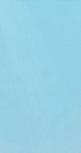
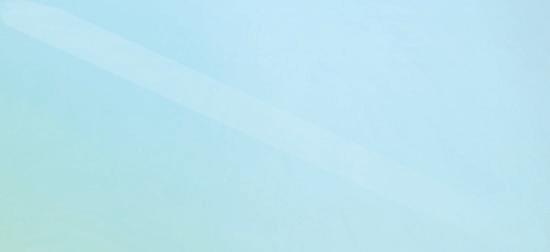
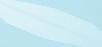
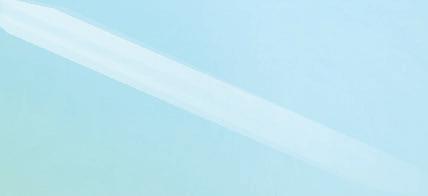
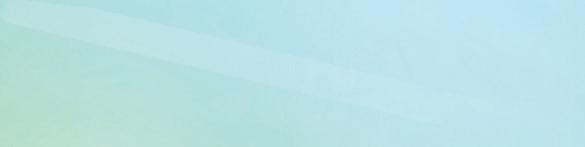
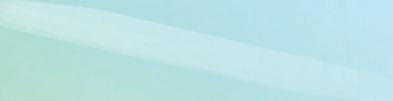
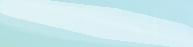

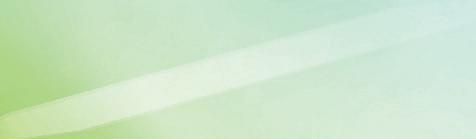
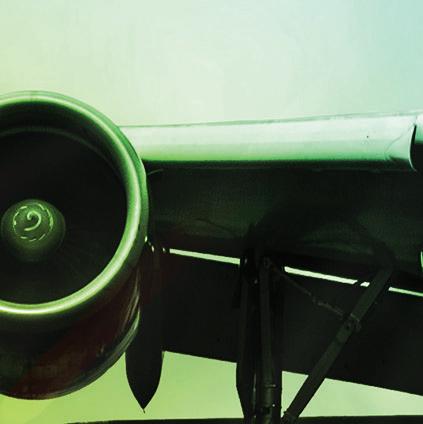
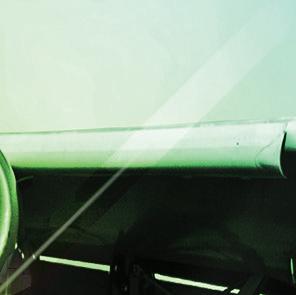
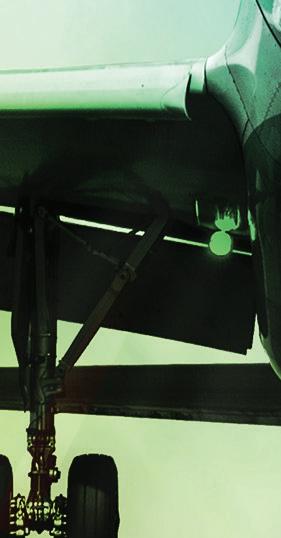

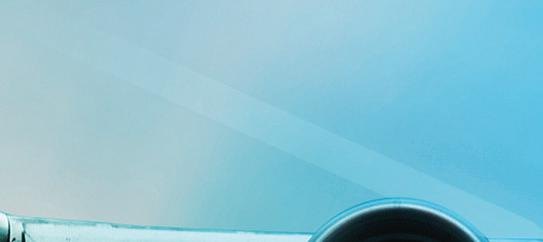









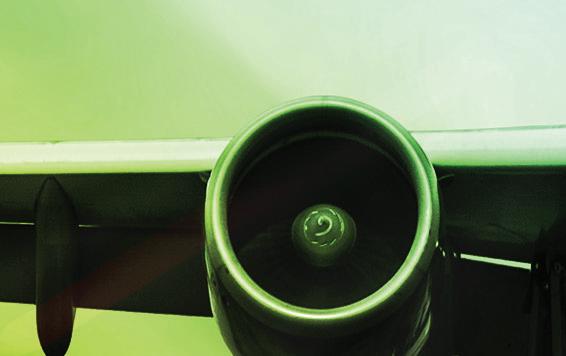
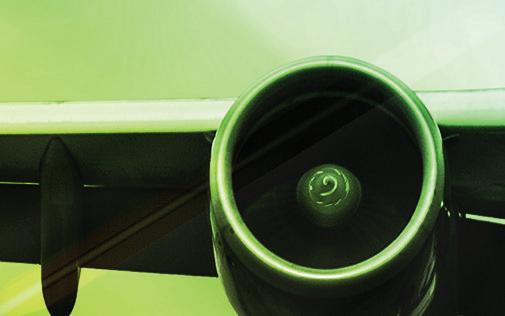
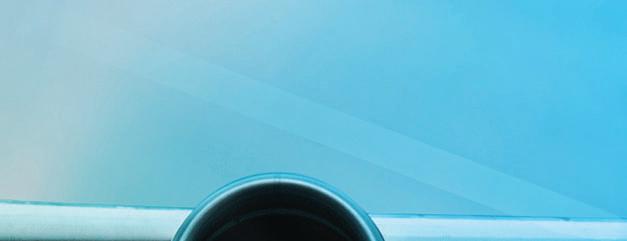
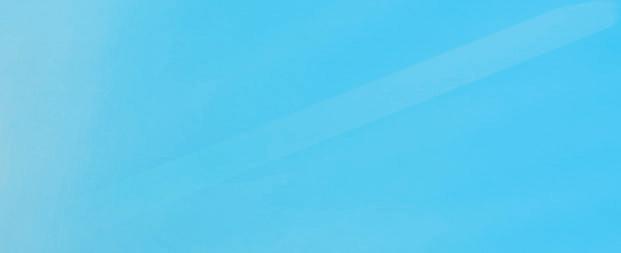


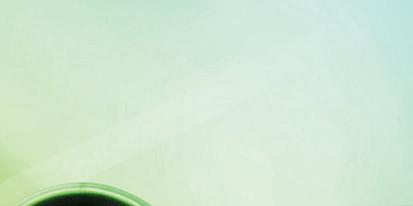
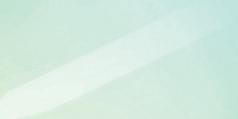
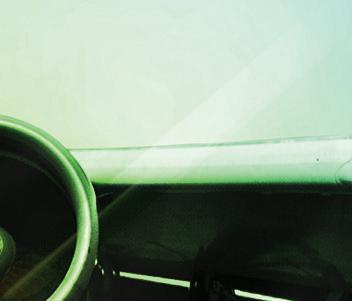




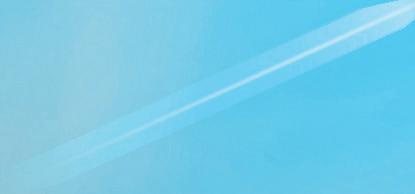
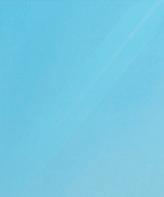
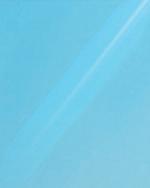
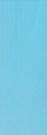
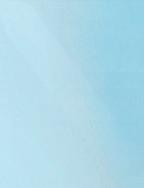

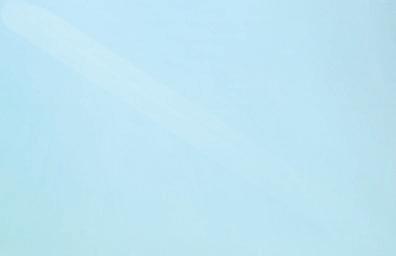

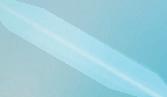


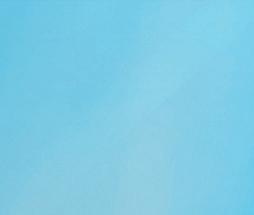
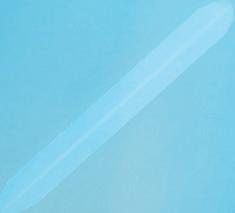
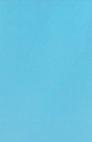
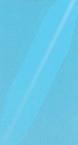
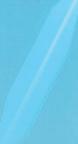
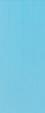

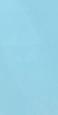
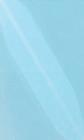

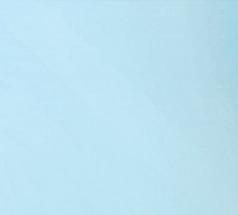

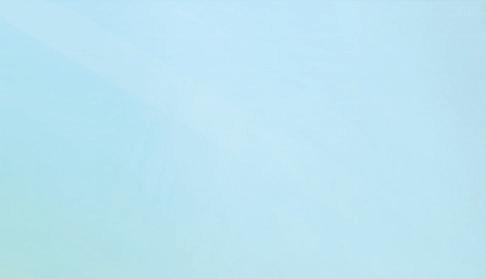
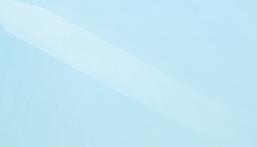
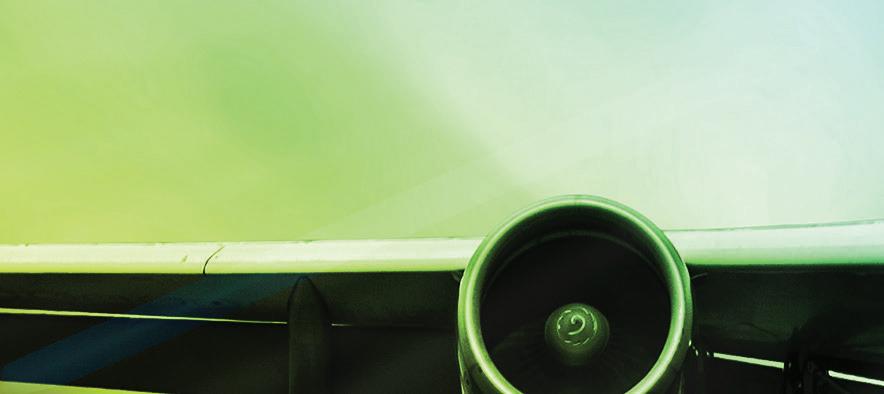
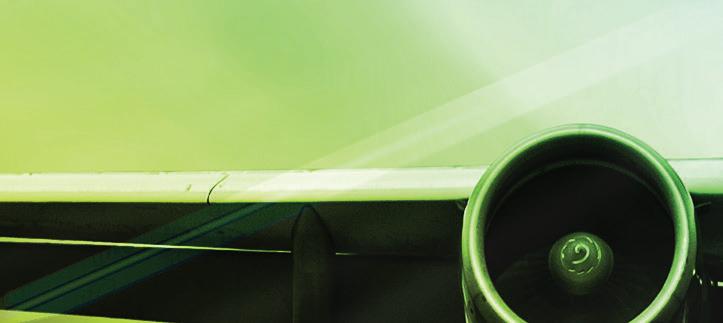
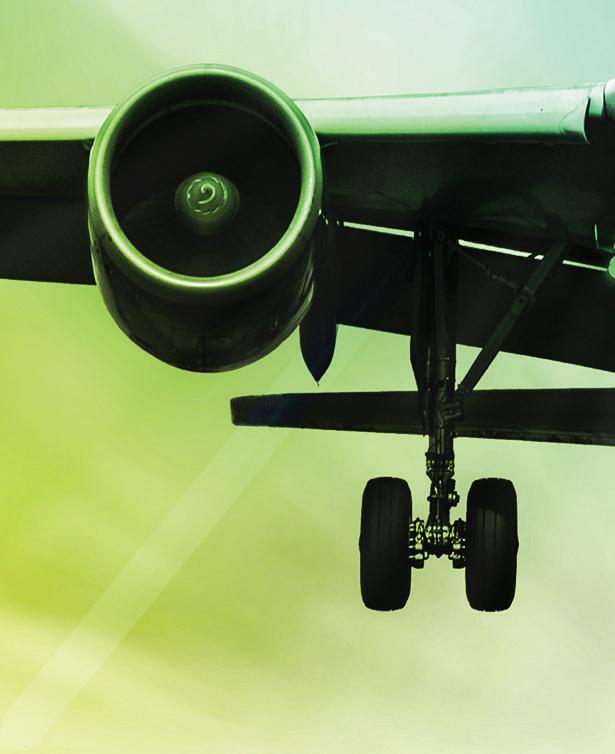
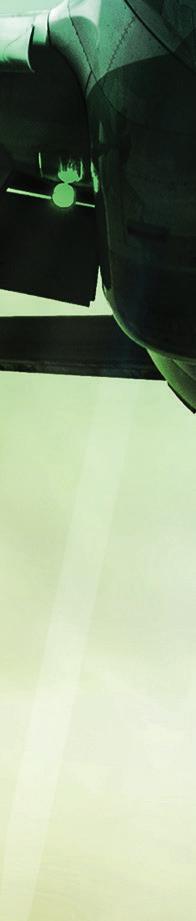
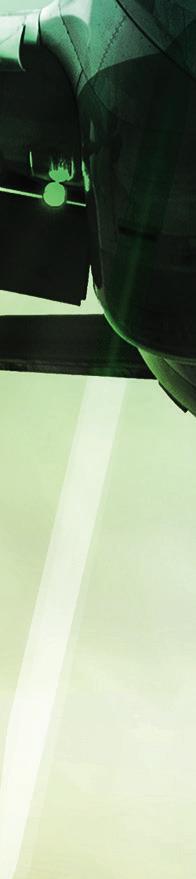

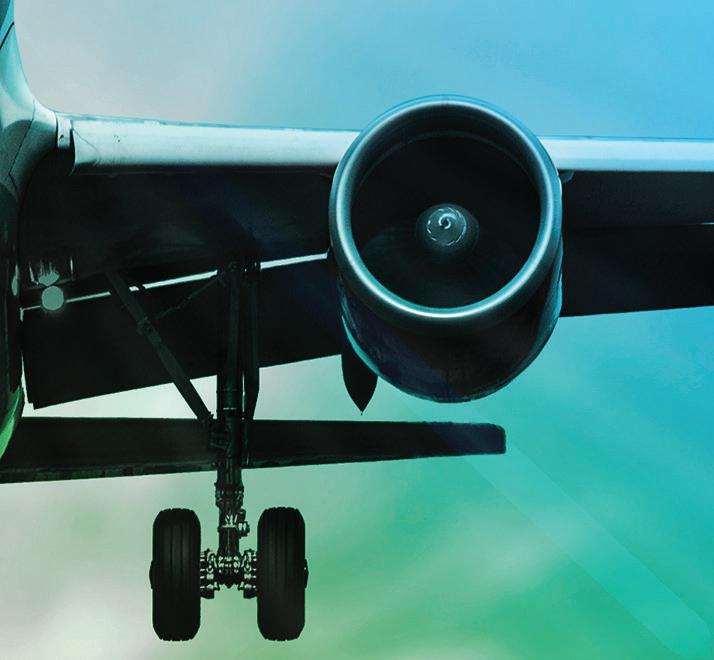
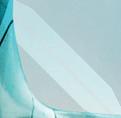
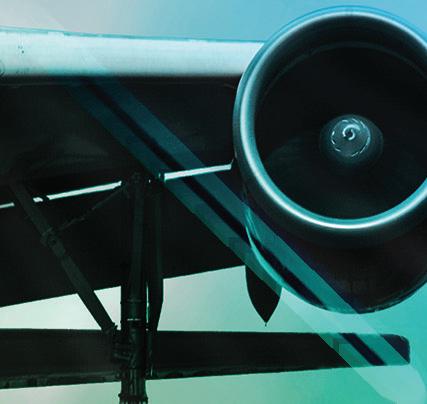

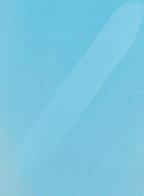
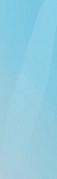

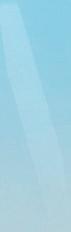
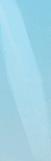
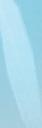

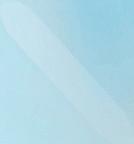
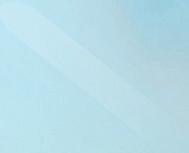


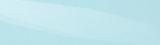


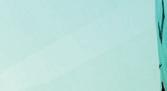

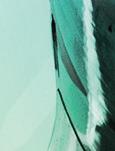

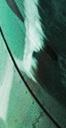
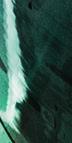




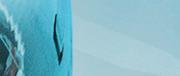


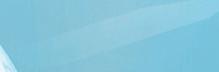

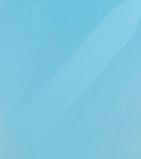
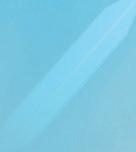


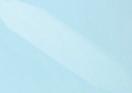

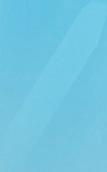



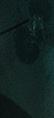


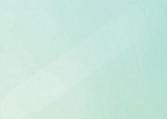
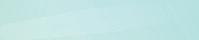

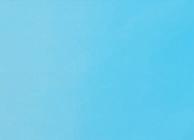


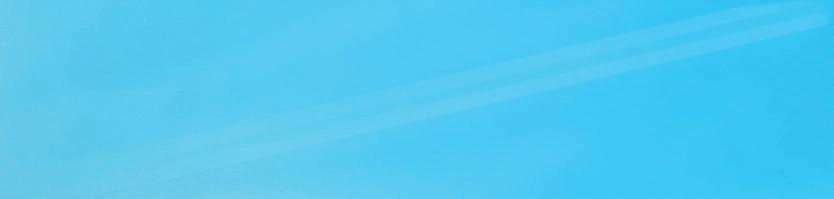
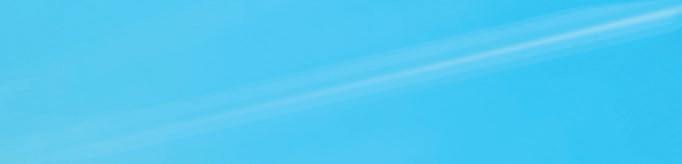
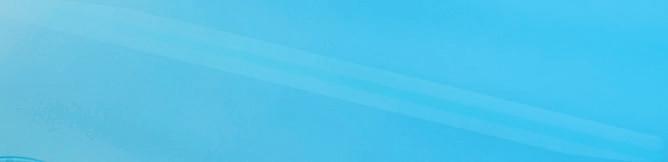
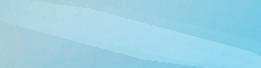
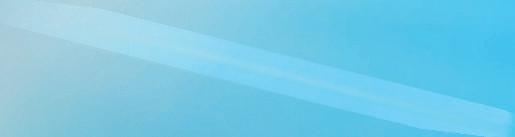
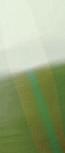


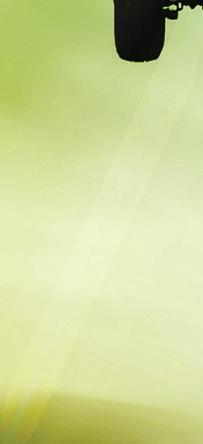
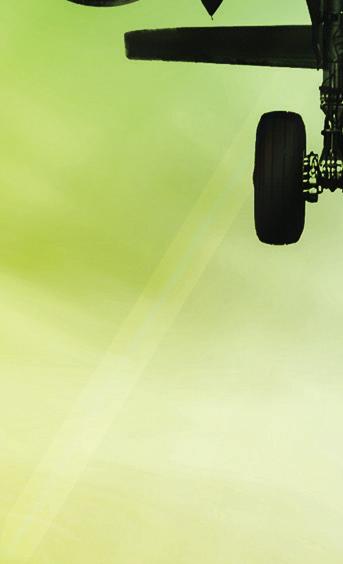
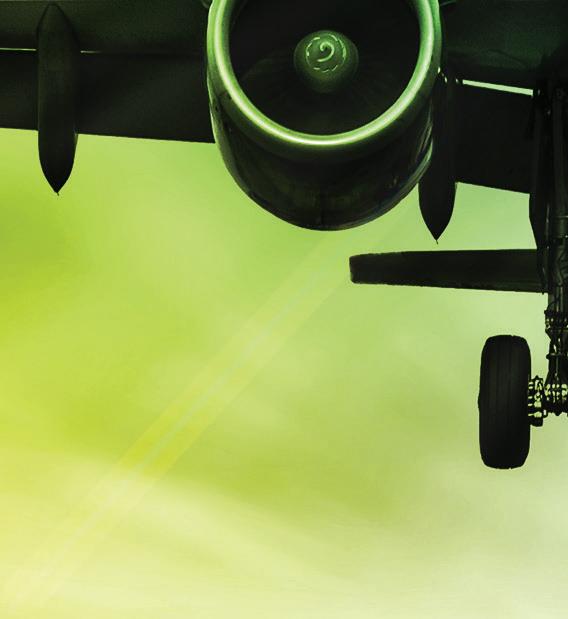
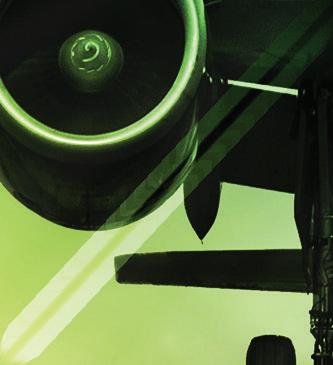
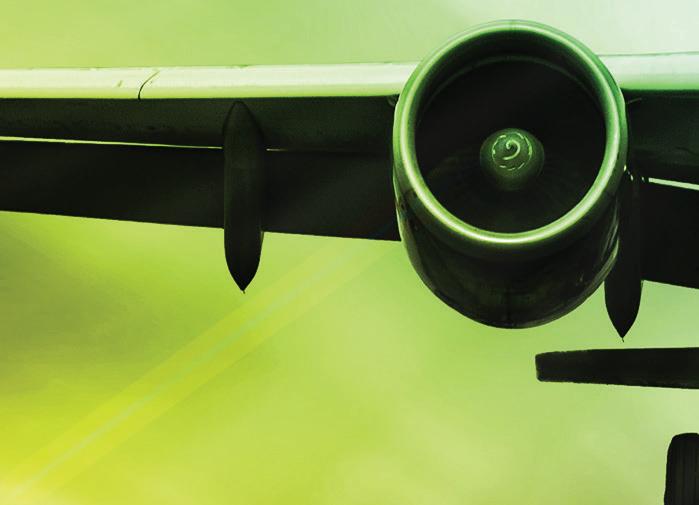
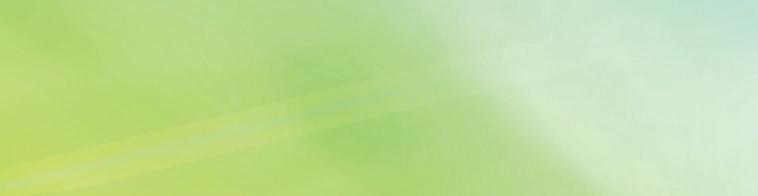
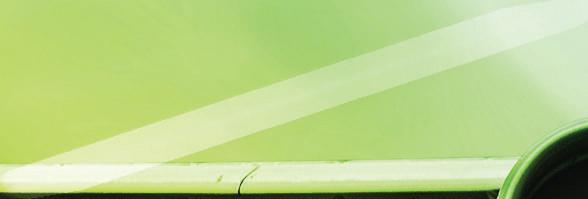
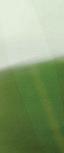
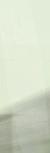
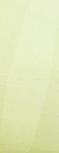
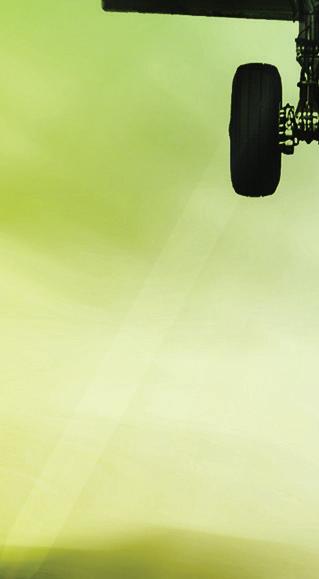
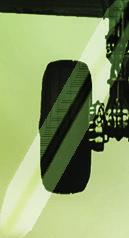
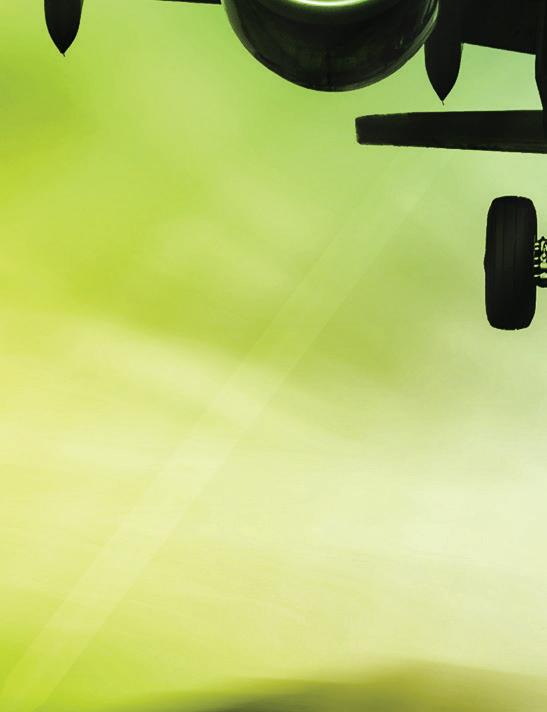
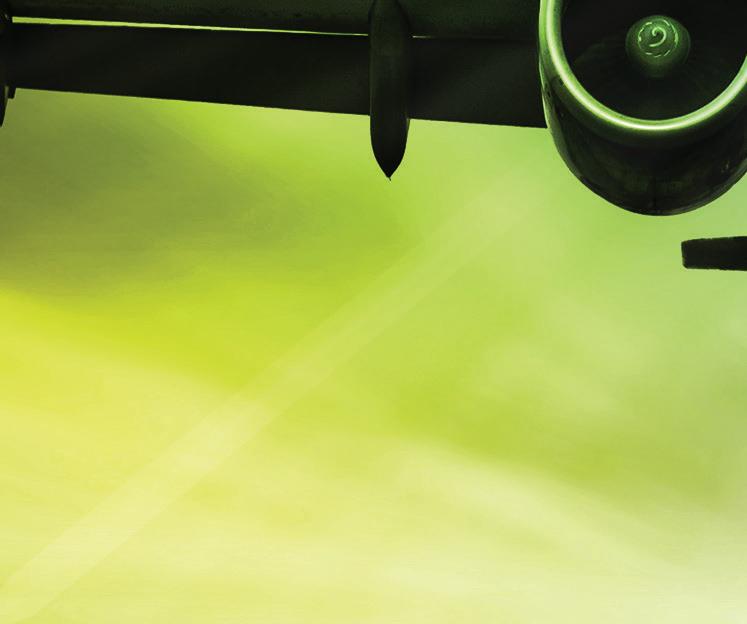
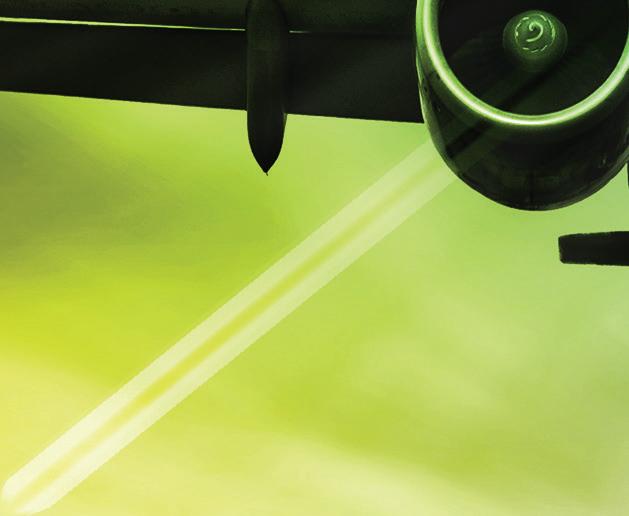
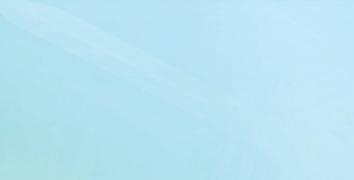
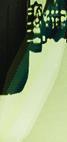
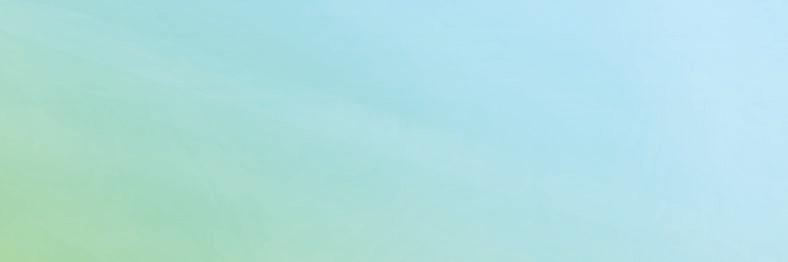
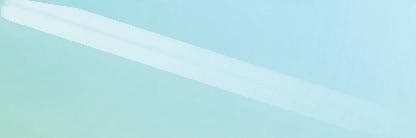
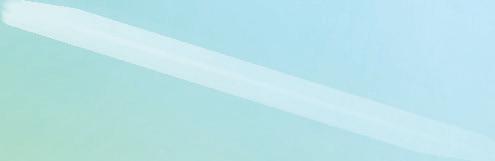
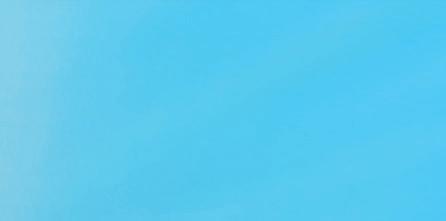
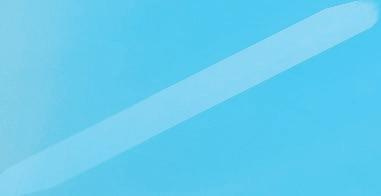
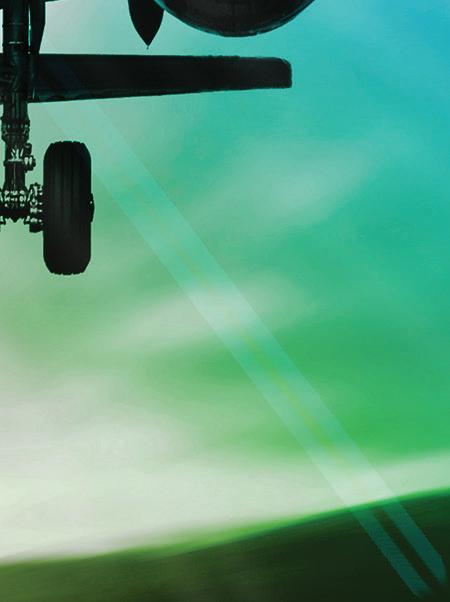



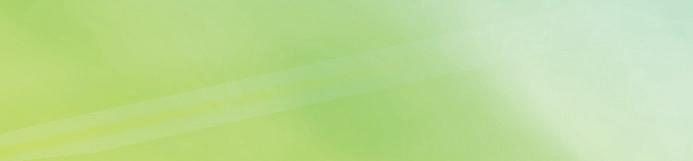
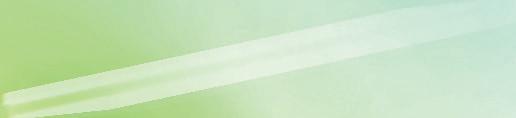







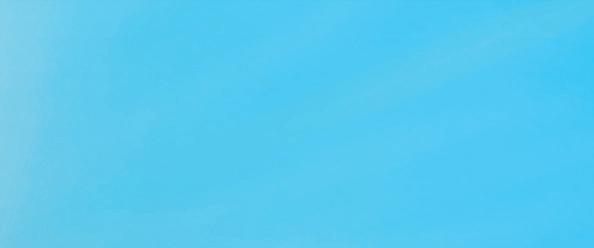
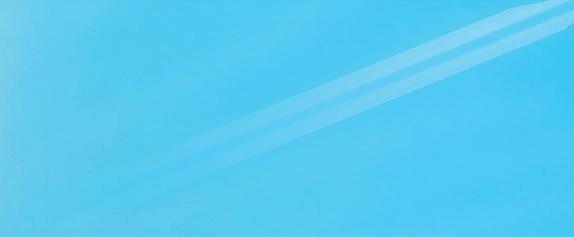
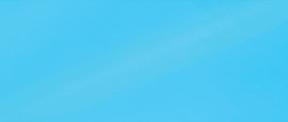
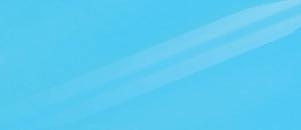
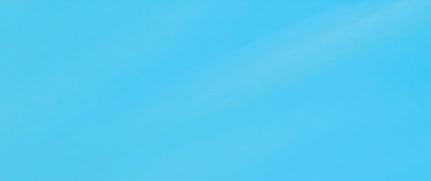
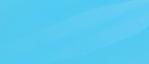
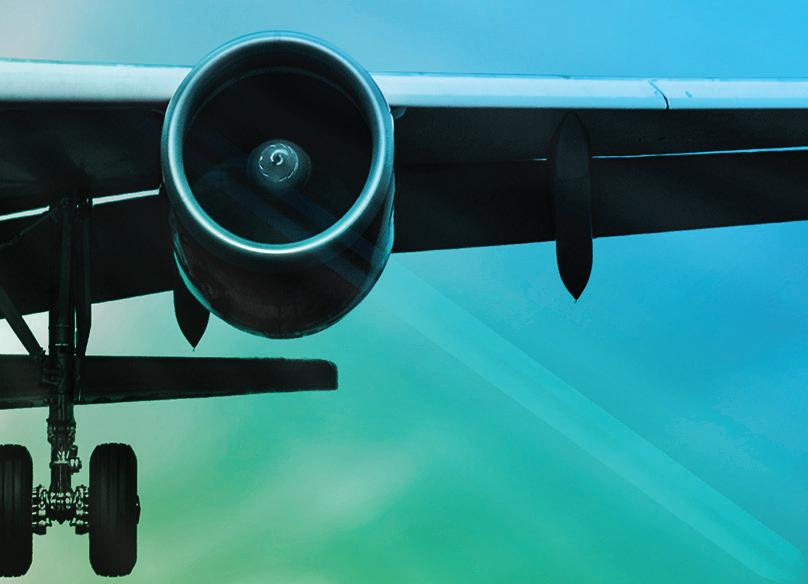
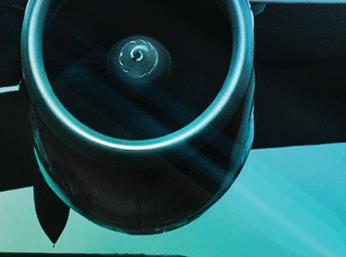
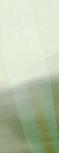

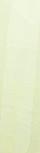
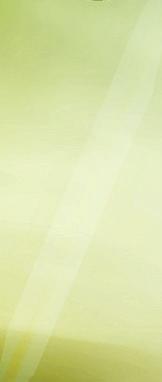
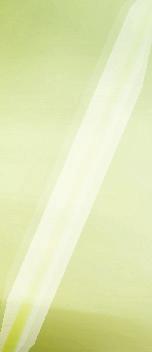


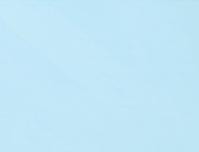
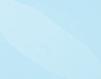

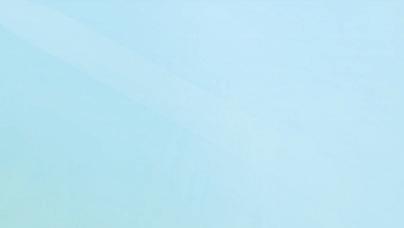
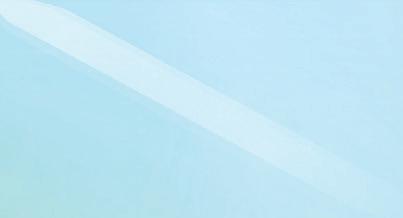
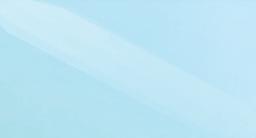
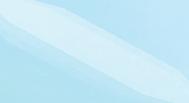
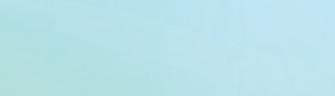
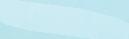

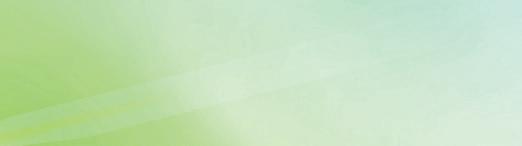
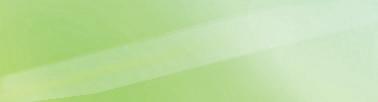
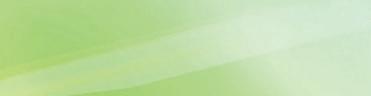
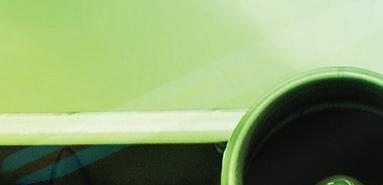
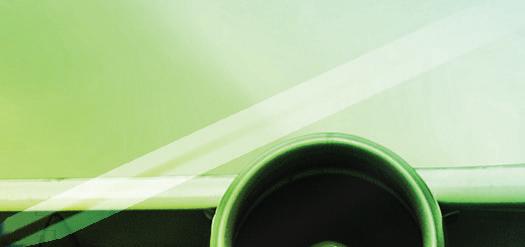
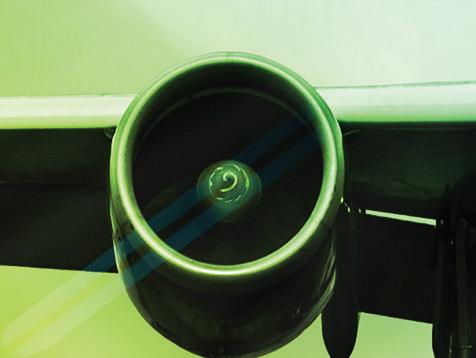
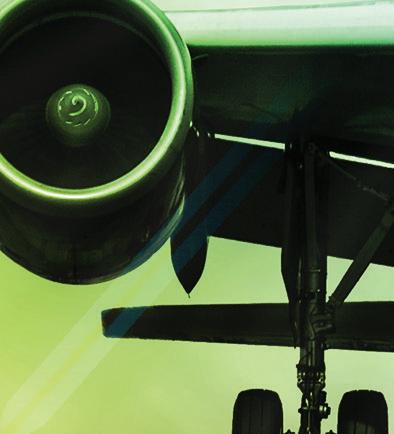
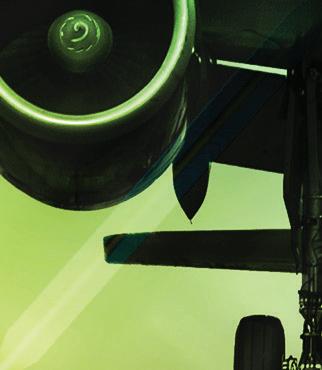
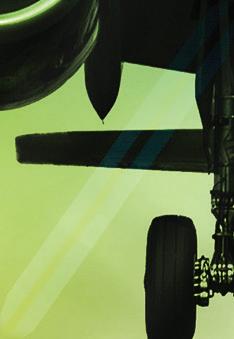
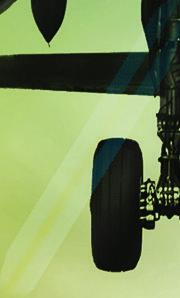
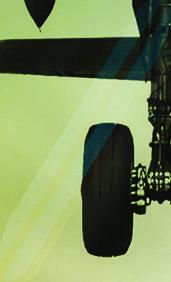

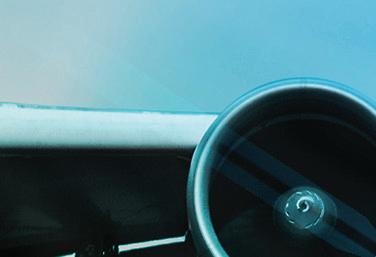
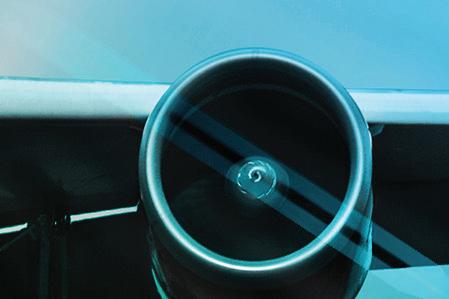
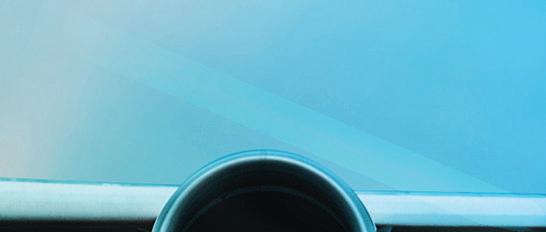
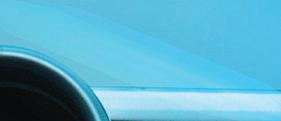
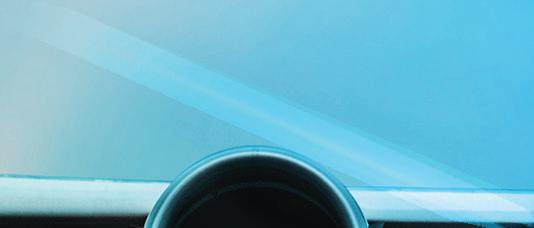




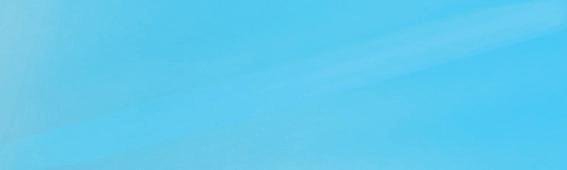
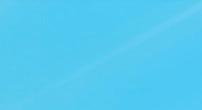
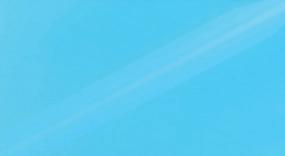

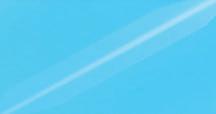

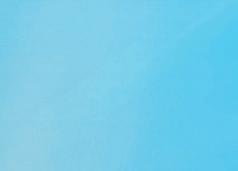

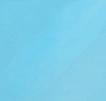
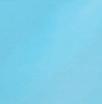
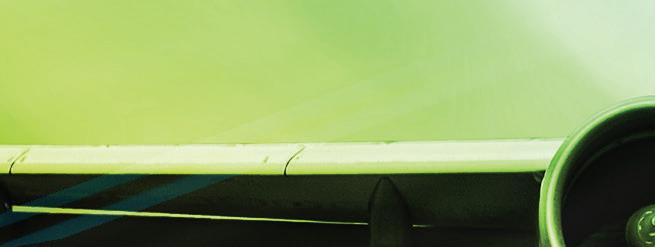

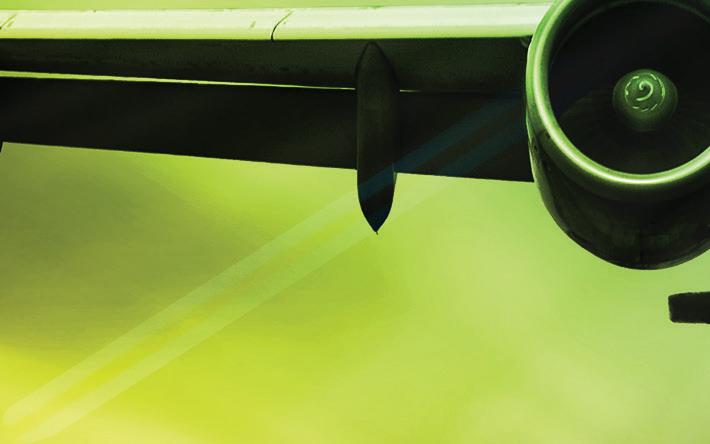
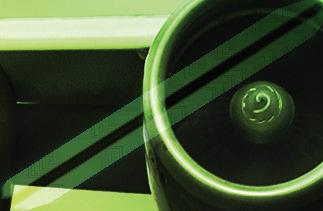
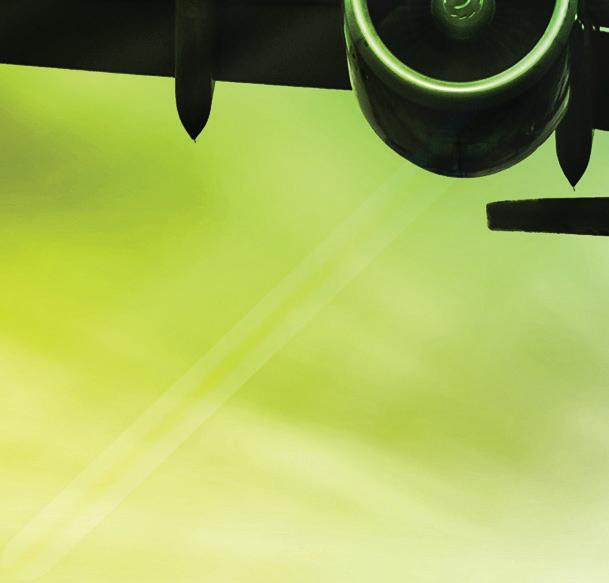
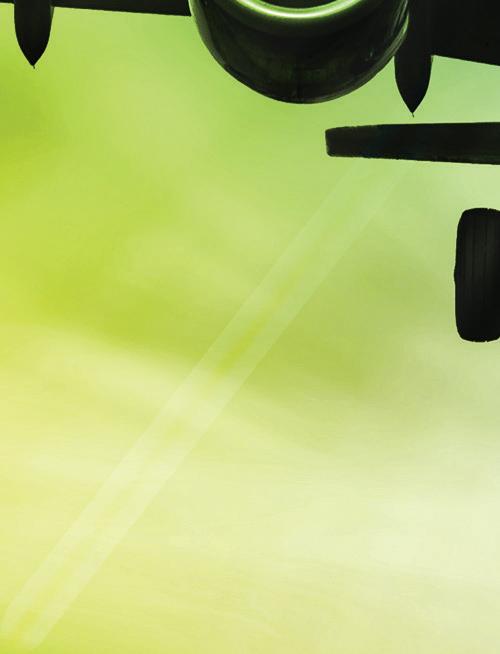
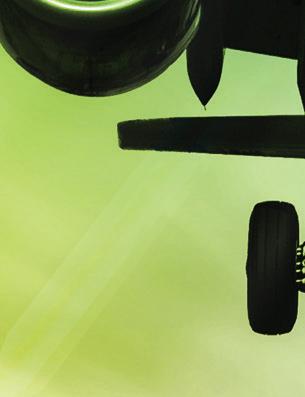
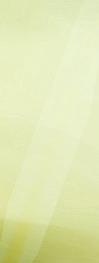

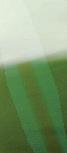
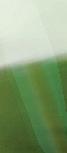
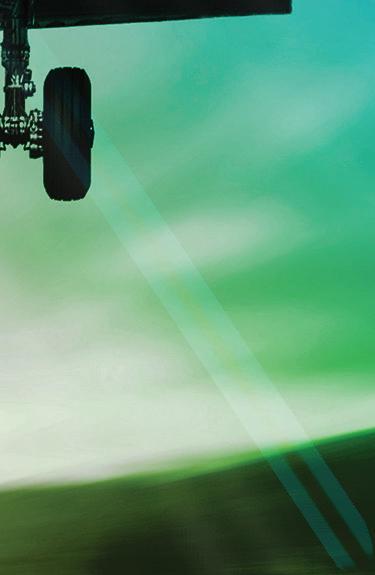
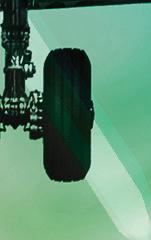
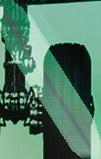
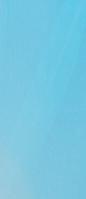
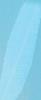
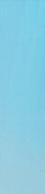


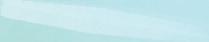

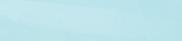

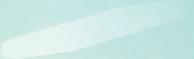
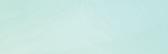
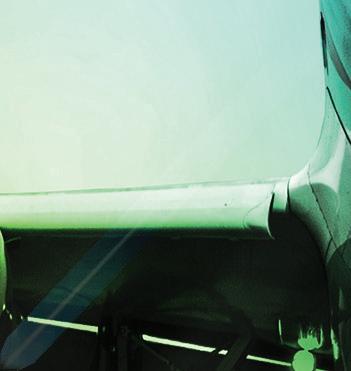

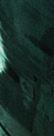
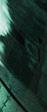

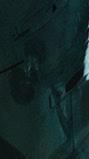

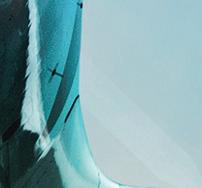

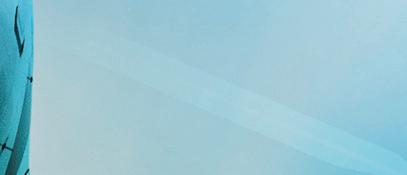

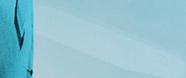

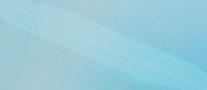

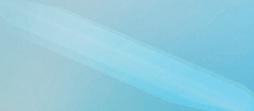

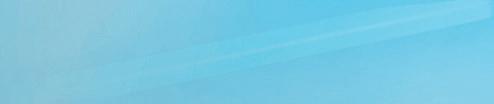
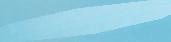
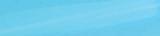
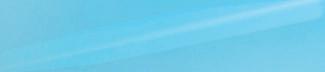
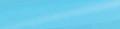
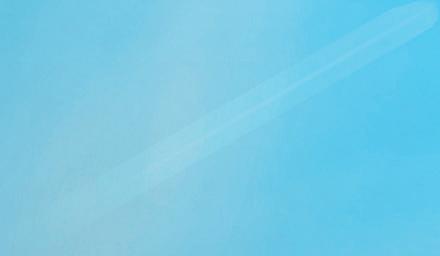
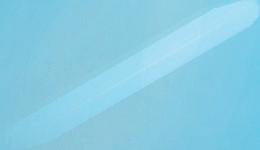


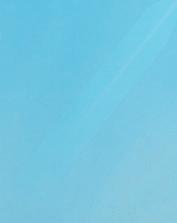

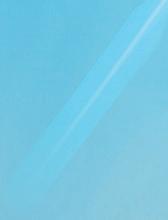




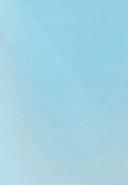
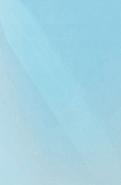
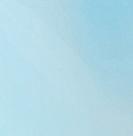


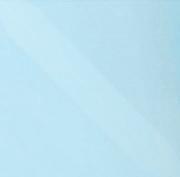
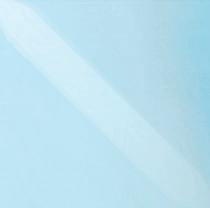
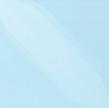



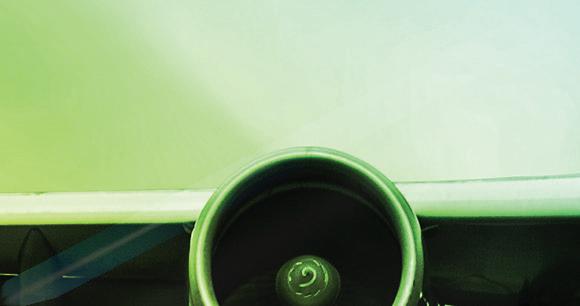
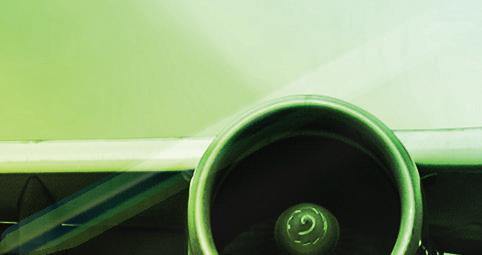



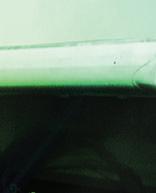



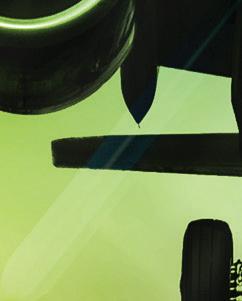
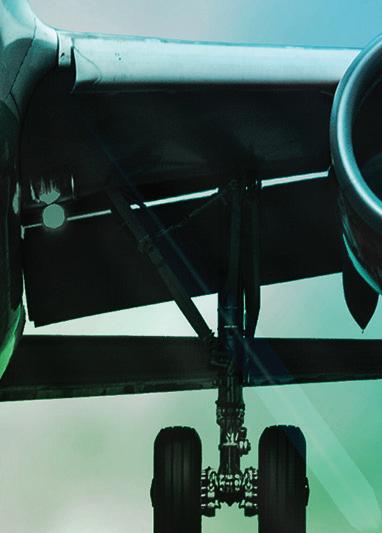


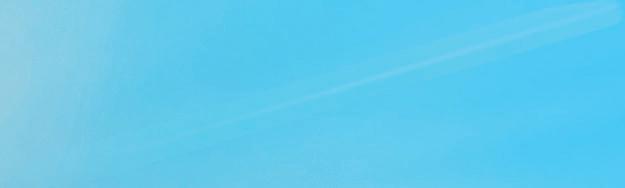
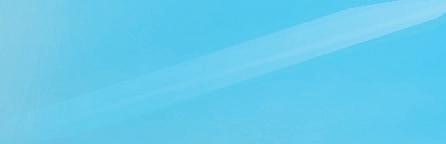







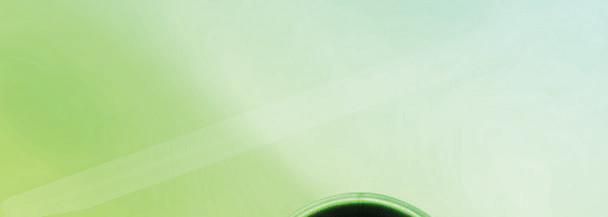




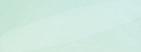
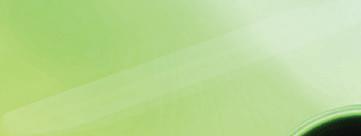
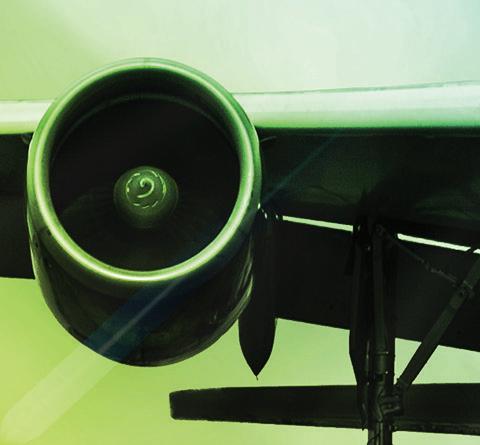
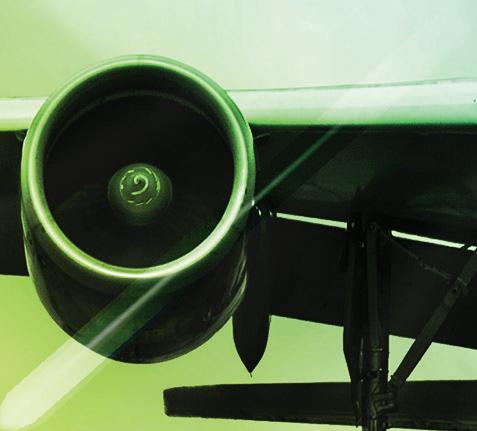

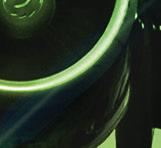


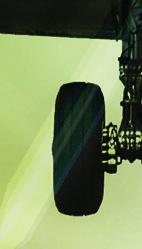
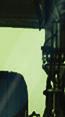
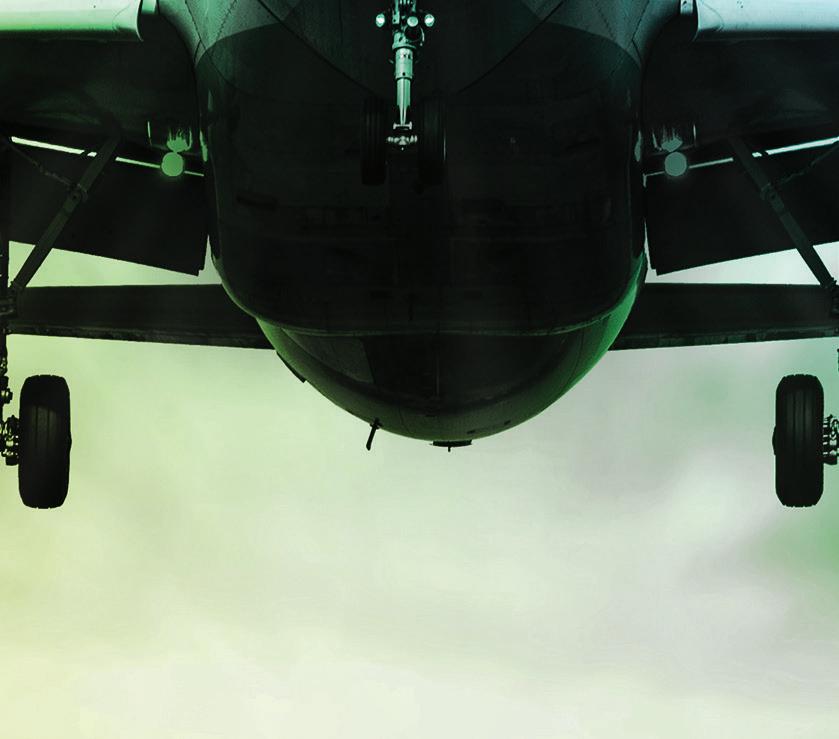




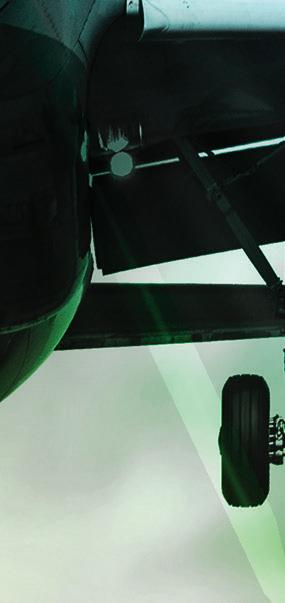
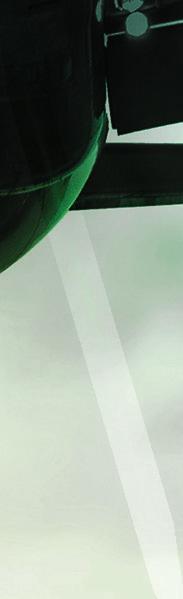
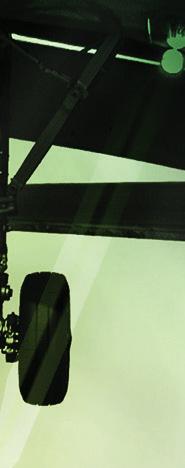


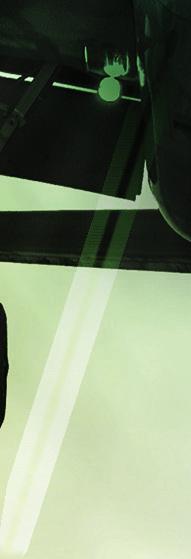
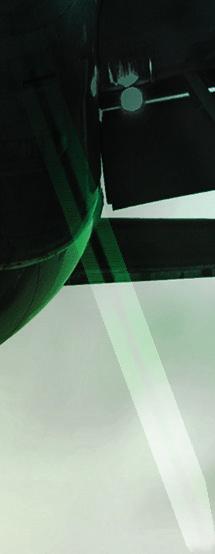
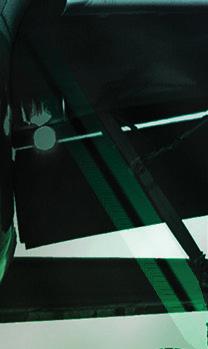

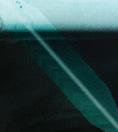
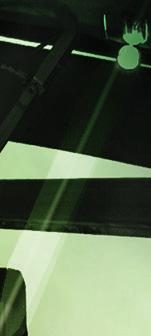
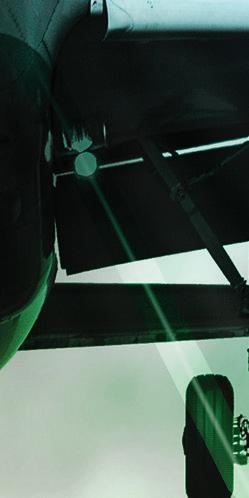
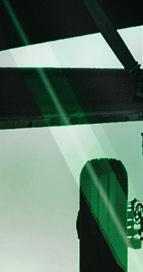
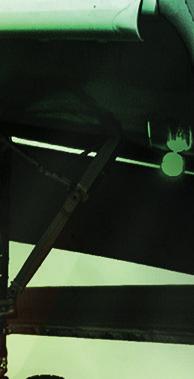
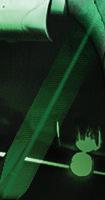

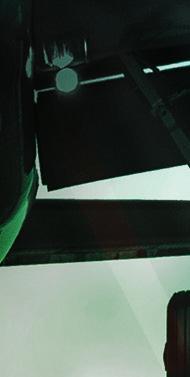
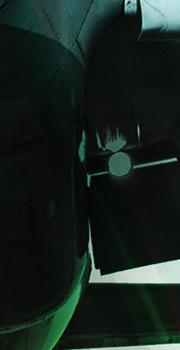
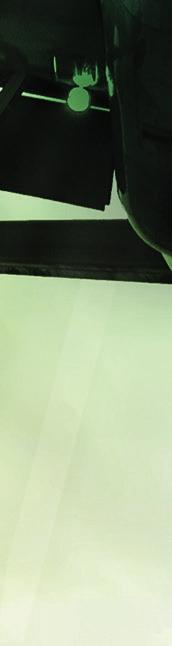


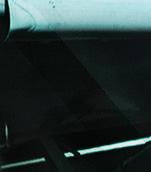

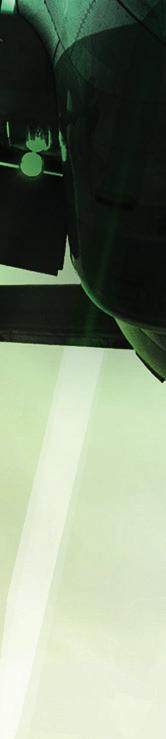
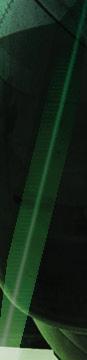
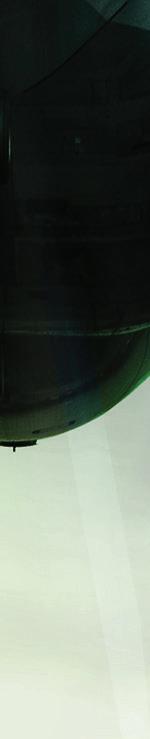






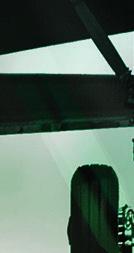



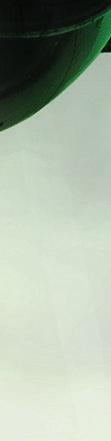
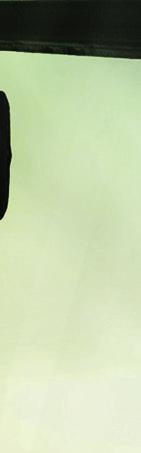

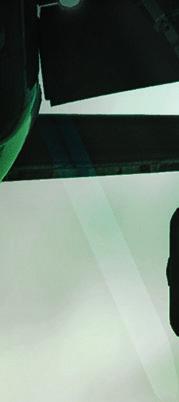

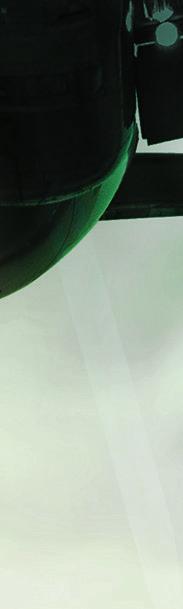

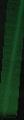

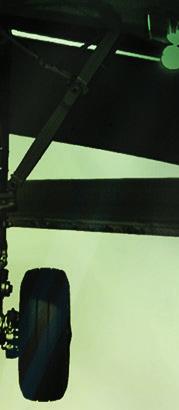
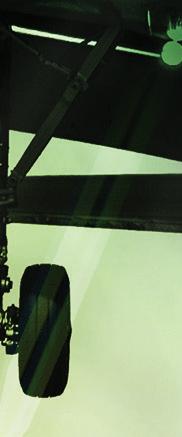

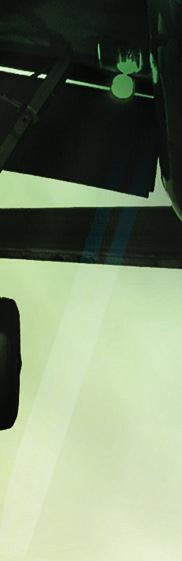
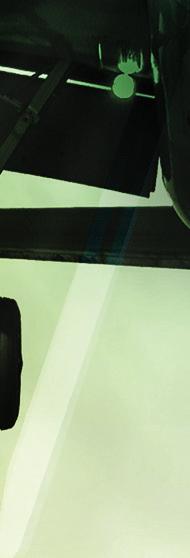

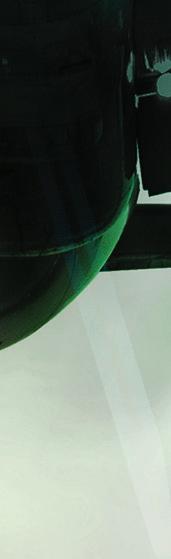
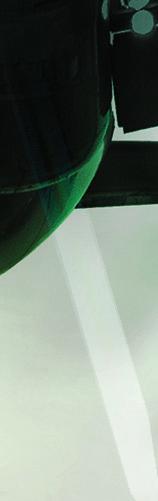
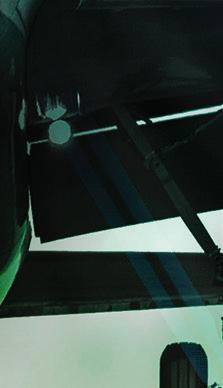

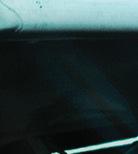
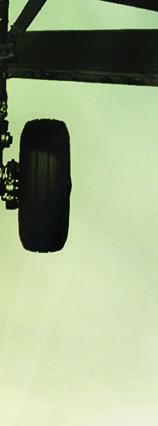
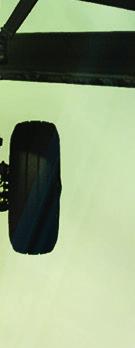

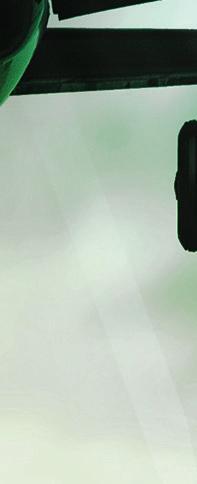
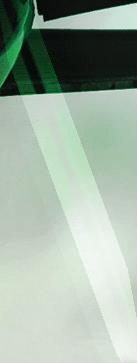
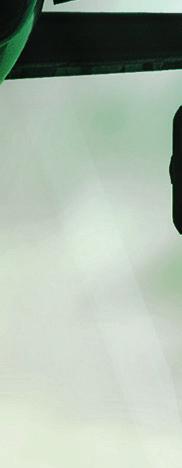

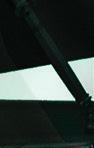


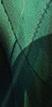
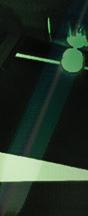


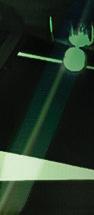
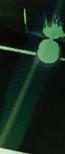

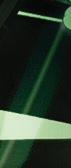










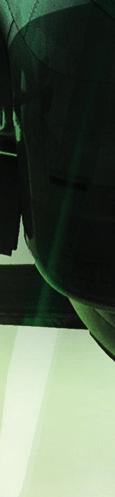
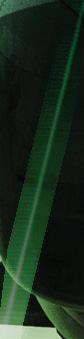
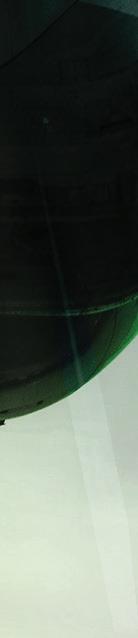
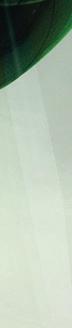
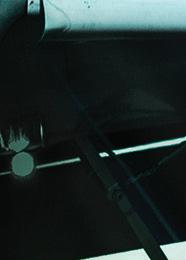

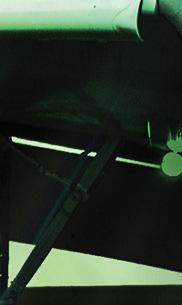
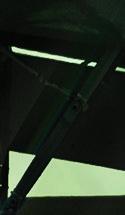
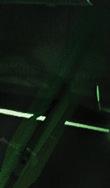





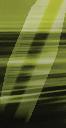




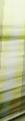
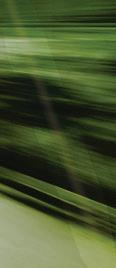

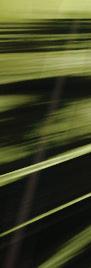
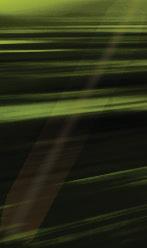
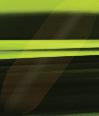
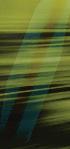
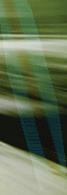
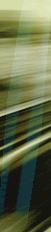

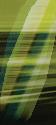
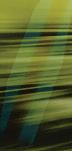

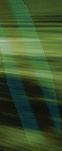
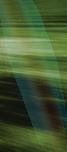
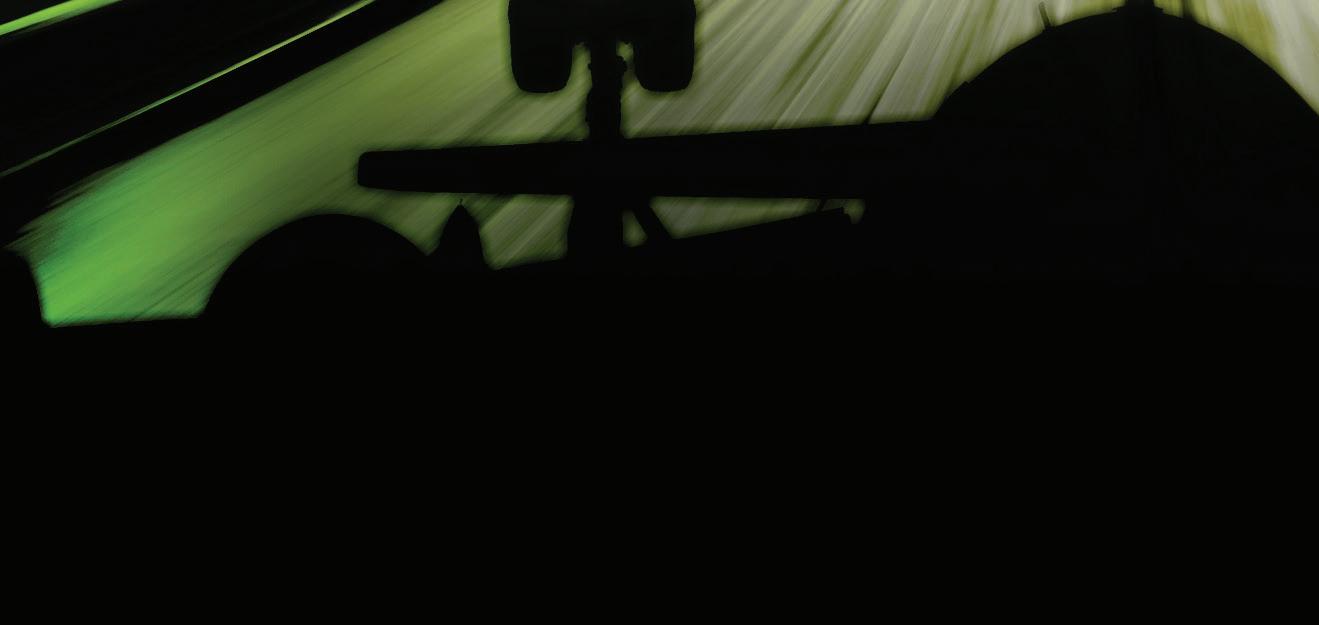











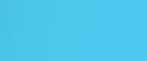
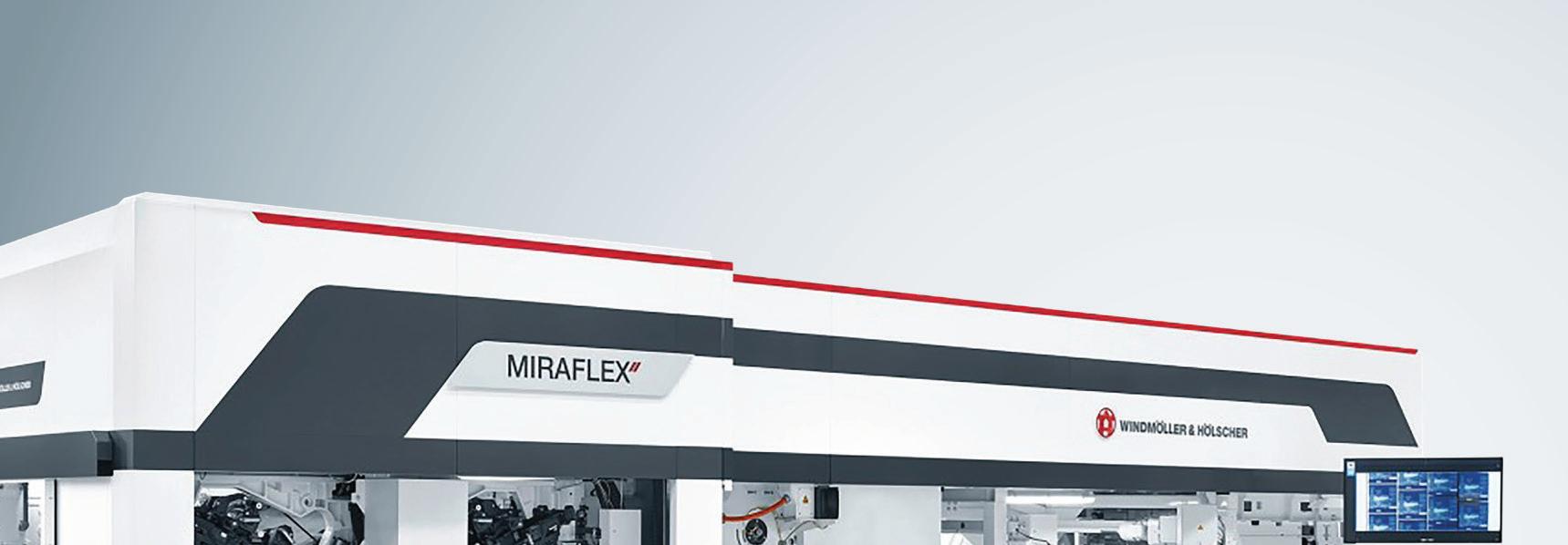




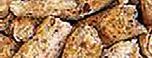
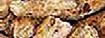


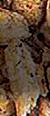

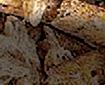
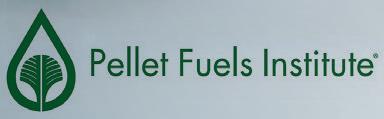


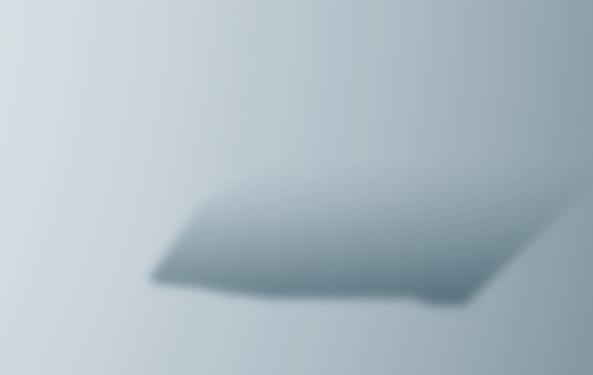

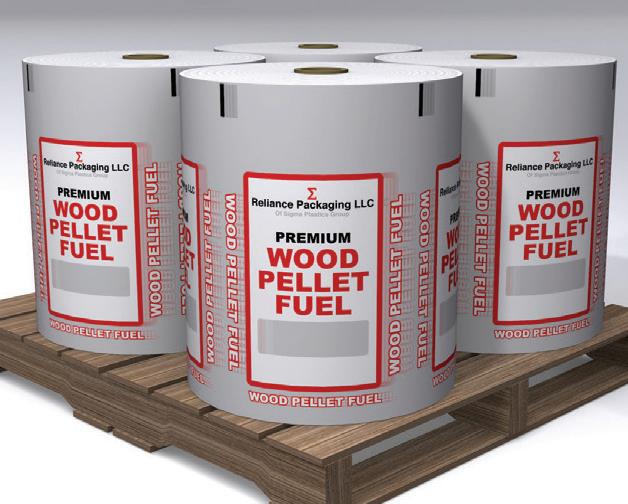
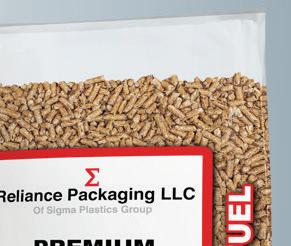
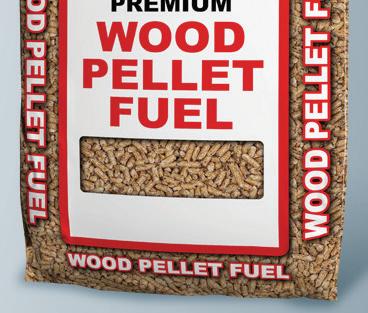

