9 minute read
Cast in concrete
from THINK - Issue 36
by Think
Next Article
Author: Becky Catrin Jones
A reinforced concrete water tower, dated from the early 20th century and a unique reminder of Malta’s industrial heritage, was in desperate need of extensive repair and attention. Combining a wealth of expertise, cutting-edge technology, and a community of support, Prof. Ruben Paul Borg and Prof. Edward Gatt tell Becky Catrin Jones how they brought a new lease of life to an important aspect of modern history.
An old, 15m-high water tower, with a concrete shell tank resting on 12 slender columns, stood unused and superfluous over the Public Abattoir in Marsa, Malta. A lasting relic of the British period of Maltese history and the intense industrial activity in the inner harbour area, the 1930s tower lay disused, having been replaced at the abattoir by newer technology, leading to its gradual degradation. With no need for it, given the danger presented, the local authorities at the time were considering pulling it down.
For Prof. Ruben Paul Borg (Faculty for the Built Environment, University of Malta), this was a tragedy. While to some, the tower looked like nothing more than a degrading structure, Borg was aware of its significance. Constructed in reinforced concrete and with technologies illustrative of the period, the tower was an important part of industrial heritage in Malta. So how could he convince the authorities to give it a second lease of life?
‘I am very passionate about preserving our industrial heritage,’ says Borg. Combining this with his expertise as a structural and materials engineer, he was determined to find a way to use his academic research as a means to save the tower. His latest project, a high-performance, durable, sustainable concrete developed at the University of Malta, might just be the answer. Following the signature of a collaboration agreement between the University of Malta and what was then the Ministry for Sustainable Development, the Environment and Climate Change on the restoration of the Water Tower, work started apace.
THE SALTY PROBLEM
Funded by an EU HORIZON 2020 project (supported by the European Union’s Horizon 2020 Research and Innovation programme under Grant Agreement No 760824), Borg had been working on the development of a highly durable concrete, designed to be used in aggressive environments, particularly in coastal regions. The ReSHEALience Ultra High Durability Concrete research project, combining the expertise of 13 partners across Europe, including Borg and the University of Malta, aimed to produce materials which would protect structures in extreme climates or environments.
The Water Tower is one of the key pilot projects in the ReSHEALience Research project.
The new self-compacting fibre-reinforced concrete would should be based on new nano-materials for higher performance, with self-healing characteristics.
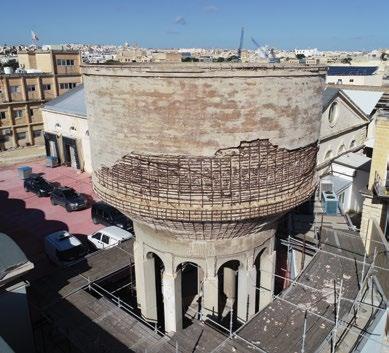
The tower before and after restoration.
Before: the tower restoration showing extensive degradation, including spalling (detached concrete) and loss of section.
After: Restored structure through the application of advanced materials including: self-healing properties, ultra-high performance and self compacting concrete for the columns, and carbon-textile reinforced concrete for the tank.
Photo courtesy of Prof. Ruben Paul Borg
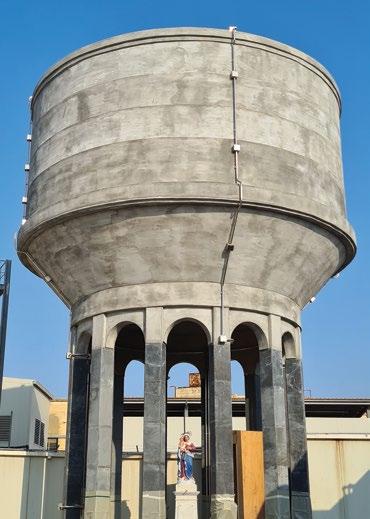
With careful monitoring, it shoud provide a more environmental and sustainable alternative to current construction materials. Developing state-of-the-art material requires considerable research.
Borg had been working in this area for some time, using nanotechnology within concrete to give it extra properties to improve its performance, including durability and sustainability. He was confident in a prototype which, in the lab at least, was performing well in challenging situations.
The EU project required realworld test sites to demonstrate the possibilities of the new materials. These locations would need to be in extreme environments to really push the materials. In Italy, the research group found a geothermal power plant basin that needed to resist an acidic environment; in Spain and Ireland, a floating concrete platform and a floating pontoon must survive aggressive marine environments.
Malta is a hot, wind-swept, rocky island, and the water tower sits on the coast of Marsa in an industrial area making it a perfect place to test whether the new concrete can resist a highly aggressive, salty coastal environment. The ReSHEALience project would provide part of the funding necessary to support the research and make this possible; all Borg needed to do was convince the local authorities to get on board.
A HIGH TECH SOLUTION
The Public Abattoir, agreed to embark on the restoration of this unique structure using such cutting-edge technology and support it financially. The project was then taken on by the Ministry for Agriculture, Fisheries and Animal Welfare. Permissions for restoration were sought with the Planning Authority, who also financially supported the project. Borg was free to go ahead and start the rescue mission.
Using the new high-performance concrete to repair the tower was one thing, but Borg wanted to go one step further. Calling on previous collaborations, he reached out to Prof. Edward Gatt (Faculty of ICT, Dept of Micro and Nano Electronics, University of Malta), an expert on sensors, in order to develop an advanced structural health monitoring system together. Incorporating the sensors would give the project an extra dimension, allowing the team to gain a better understanding of how the concrete responds to its environment.
Working together, Borg and Gatt planned how the restoration effort would incorporate different sensors inside the concrete, integrating the sensor network in the architectural

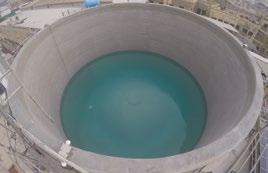
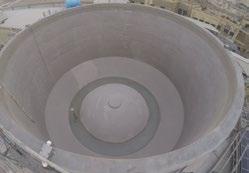
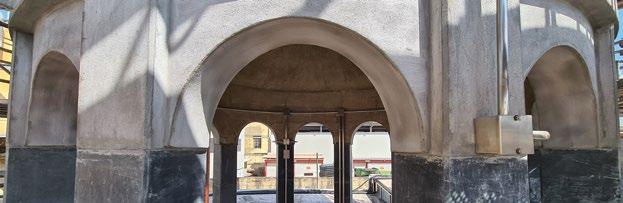
Detail of the tower structure Photo courtesy of Prof. Ruben Paul Borg
fabric as well as developing a longterm monitoring and control station. ‘We needed three monitoring systems,’ recalled Gatt. Structural monitors would measure movement of the tower in response to wind, earthquakes, and water pressure. Durability sensors would record any degradation in the concrete by checking for changes within the concrete, including moisture, temperature, or salt concentration. Finally, environmental sensors would be included to assess the weather and atmosphere around the tower.
‘Other pilot projects which we developed in the ReSHEALience scheme include sensors for structural monitoring, but this has by far the most,’ says Gatt. The water tower includes both off-the-shelf and custom-made sensors, with over 150 in total across the structure.
The perfect balance of their expertise, with a multidisciplinary approach to tackle new challenges and big projects, meant the two could combine their expertise to develop new solutions. Pulling in PhD students and researchers under their joint supervision, the team set about testing the nanomaterials and sensors on the different parts of the water tower structure. What was necessary for the 12 pillars that support the large water tank might not have applied to the circular shell elements of the tank.
Using laboratory-based research on materials and structural elements, combined with advanced finite element computer modelling approaches, the team could assess how different repairs and reinforcements using the new high-performance concrete might work in the real world and decide which would be most appropriate for the tower. Before any work was done on the water tower, Borg built replicas of the structure’s columns and shell pieces. These were used to test the materials and sensor installation processes, ensuring their theories were correct without risking any unnecessary harm to the tower.
Prof. Ruben Paul Borg Photo by Sarah Zammit TEAMWORK TO MAKE THE DREAM WORK
‘We really must stress the importance of having a diverse team working on this project,’ remarks Gatt. This mammoth task, carried out over two
Prof. Edward Gatt Photo by Sarah Zammit
The structure performance was validated through monitoring during the filling up and emptying process with 400m3 of water Photos courtesy of Mediacoop (Left)
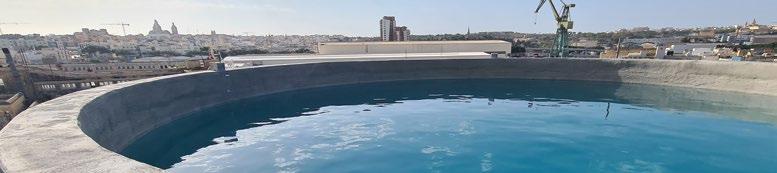
Below: Data logging stations are used to read the signals from the 150 sensors in the tower for durability and structural health monitoring. Photo courtesy of Prof. Ruben Paul Borg
years but with more than a decade of groundwork, involved students, laboratory researchers, computer modellers, contractors, site inspection teams, and many more, including the ongoing support of the Senior Management of the Public Abattoir.
The final stage of the project required further expertise, involving a collaboration to produce an engineering platform where students, researchers, professionals, and citizens can access the data produced by the sensors. Interested visitors will be able to see how the water tower performs and how the concrete materials and structure change in their environment over time: the impact of the changing weather, salt exposure, and increasingly hot summers.
The University of Malta and the Ministry for Agriculture, Fisheries Food and Animal Rights have now agreed to extend their collaboration beyond the restoration of the Water Tower, and set the basis for further collaboration using the restored structure as a platform. The water tower can now be counted as an extra research station for the University of Malta providing teaching and learning opportunities for students in architecture, materials and structural engineering, ICT, and other subjects. By including a virtual learning platform, the reach goes far further than Malta. Inviting international collaborators to partake in research analysing the data produced by the mass of sensors hopes to encourage further investment in and development of these new materials.
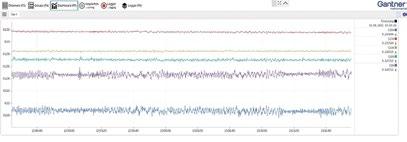
Top: The data is stored on the cloud, viewed and processed on an online platform for research and learning purposes. Image courtesy of Prof. Edward Gatt
SET IN HISTORY
After a huge amount of work, what now for the water tower? ‘The best way to preserve a public structure is to use it and make people feel they need it,’ says Borg. Following the successful completion of the project, the Public Abattoir is planning to reincorporate the water tower into the daily running of the site.
Borg and Gatt were anxious to validate the restored structure by filling the tank with 400 cubic meters of water and putting it back in operation. ‘It’s one thing to know that the materials work in the lab but another thing entirely to know if they are ready for the real world,’ Borg remarks. The successful validation exercise further confirmed the possibilities of the new highperformance materials developed and the technologies applied in the conservation process. The pioneering work has now opened new opportunities for the team in research and applications in industrial concrete heritage structures.
Perhaps the greatest success for Borg, though, is the recognition of the water tower as an important and significant structure for Maltese heritage, and the Ministry's commitment to preserve and valorise it. Following the restoration project, the tower is in the process of being recognised as a listed heritage structure, protected to preserve this piece of culture with so much historical significance. It’s a perfect example of how today’s latest innovations and cutting-edge technologies can help protect the 20th century’s industrial heritage.