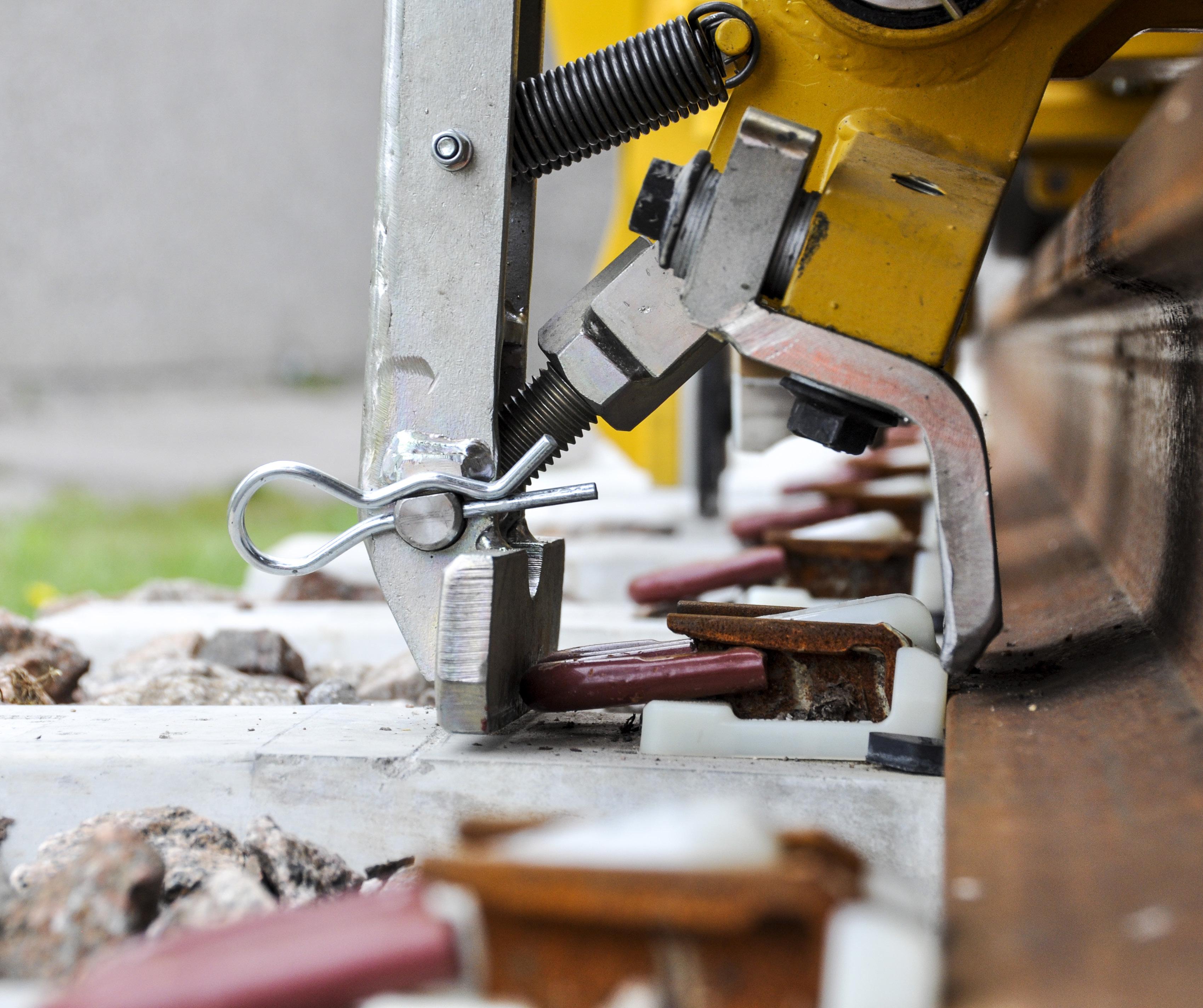
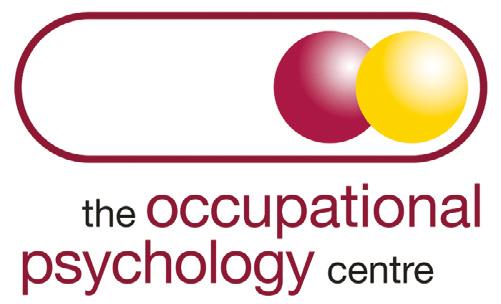
With over 30 years’ experience working in the rail industry, specialising in the safety sector, the OPC provides practical, reliable ways of improving performance and assessing ability.
Sam
RECRUITMENT
The two biggest stories this month revolve around data and decisions – with the figures for 2022/23 published recently by the Office of Rail and Road (ORR) and the unveiling of the Spring Budget early in March.
Our columnist Chris Cheek takes a deep dive into the numbers from the ORR report, the figures are encouraging, with patronage growth of 19.9 per cent in the quarter, and as much as 27 per cent in the rolling year to 31 December. Chris also sees indications of a continuing recovery in the latest quarterly statistics, published on 21 March. And we have compiled the industry’s response to the budget with the major announcements being faster completion of East West Rail, news of additional East Coast Mainline services and more information on the Network North schemes. We also have more extensive analysis of the budget from Andrew Baldwin, Head of Policy and Public Affairs at APM.
My interview this month is with Arcadis alumna and newly appointed Managing Director at Zinc Consult, James Redmayne. The central theme of the interview was about changing the narrative around the supply chain and the importance of SMEs in project delivery, as well as how we can change the way different organisations view their responsibility to the whole – including training and skills with James offering up an interesting opinion about how we should change our approach to shoring up our industry’s skillset and developing a new skills base to launch the next generation of engineers from.
This month we’re focussing on specialist skills and cooperation, with stories from Amey explaining how they are tackling the skills gap in the rapidly changing engineering industry and then Nick Lowe of Whitfield Consulting Services (WCS), Lindsey McKerlie of Andromeda and Craig Anger of J. Murphy & Sons look ahead to Control Period 7.
Covering cooperation, Frazer Nash use two case studies to explain how they deliver innovation through cooperation and we have Fred Sammut, Business Development Manager – Rail & HS2 at Mabey Hire on the value of temporary works design.
Alongside that we have our usual collection of opinion pieces from the industry including Sarah Booth and Dr Cristina Ruscitto on fatigue risk management, Ciaran Cotter, Technical Director at Solivus discusses how infrastructure can support the decarbonisation of railways and more.
SAM SHERWOOD-HALE EDITOR• High performance
• Enhanced user safety
• Reduced environmental impact *reducing environmental impact through verifiable criteria.
09 NEWS
The latest figures from ORR, East Midlands Railway, Great Western Railway, Network Rail, FirstGroup, Alstom and more
16 INTERVIEW
With James Redmayne, Managing Director at Zinc Consult
VIEWPOINT
22 Jacqueline Starr, Chief Executive of Rail Delivery Group takes us behind the statistics that prove rail is the green choice for business travel
25
28
Revenue
The slow arrival of new rail laws – but at least they are on their way
31 VIEWPOINT
Plans to Fast-track East West Rail
33 WOMEN IN RAIL
Empowering yourself to become more significant
34 VIEWPOINT
Sarah Booth and Dr Cristina Ruscitto on fatigue risk management
37 VIEWPOINT
Phil Pavey takes a look at how rail operators that adopt a modular building approach can access opportunities that go beyond simply charging points
38 VIEWPOINT
Ciaran Cotter asks how can infrastructure support the decarbonisation of railways?
41 VIEWPOINT
Davie Carns on the training blueprint
42 IN CONVERSATION
Lee Woodcock, Key Account Manager – Contractors At Polypipe Civils & Green Urbanisation
46 IN CONVERSATION
Jacob Landström, Managing Director at Rosenqvist Rail
50 IN CONVERSATION
Stuart Evans, Business Director at Mass Transportation
53 IN CONVERSATION
Simon Critchley, Railtech UK General Manager at Tracsis Plc
55 VIEWPOINT
Andrew Baldwin, Head of Policy and Public Affairs at Association for Project Management responds to the Spring Budget
56 IN CONVERSATION
Lorna Gibson, Managing Director at QTS Training Ltd
58 IN CONVERSATION
Neil Hughes, Head of Transport, EV Infrastructure and Automotive at Schneider Electric
62 IN CONVERSATION
Gavin Adams, Head of Sales – UK at Concrete Canvas Limited
65 VIEWPOINT
A railway town called Swindon
66 IN CONVERSATION
Yvain Cornet, COO at Pulsaart by AGC
68 IN CONVERSATION
Jonathan Abbott, Job Site Solutions National Rail Manager at Milwaukee (TTI)
70 IN CONVERSATION
Simon Rehill, General Manager at Pulsar Instruments Plc
72 IN CONVERSATION
Michelle Ionn, Marketing Manager Emeia – Professional Brands at CRC Industries
74 SPECIALIST SKILLS
Tackling the skills gap in engineering
76 SPECIALIST SKILLS
The Occupational Psychology Centre (OPC) sheds some light on why some employees find it hard to stick to the fundamentals of safety
80 SPECIALIST SKILLS
With Network Rail’s Control Period 7 (CP7) starting in April, specialist skills and experience are vital to its success
83 SPECIALIST SKILLS
Virtual Reality (VR) has been making waves throughout various industries, however its potential in the Rail Industry seems to have been overlooked
85 SPECIALIST SKILLS & COOPERATION
Delivering innovation through cooperation
88 COOPERATION
In Conversation with Steve Whitmore, Managing Director of enGauged with a personal reflection on the role SMEs play in the UK rail industry
90 IN CONVERSATION
Fred Sammut, Business Development Manager – Rail & HS2 at Mabey Hire delves into the detail of temporary works design for the rail sector, exploring the clear need for speed, safety and reliability
92 RAIL RESPONSE
Spring Budget 2024 Response
95
97 Officine Maccaferri
99
101
102 PEOPLE
Danny Vaughan, Jamie Ross, Nick Clarke, Iris Schnittler, Mark Hooper, Liz Baldwin, Andy Steel, Andy Bagguley
A total of 417 million rail passenger journeys were recorded in Great Britain (GB) in the latest quarter (October to December 2023). This is a 20 per cent increase on the 348 million journeys in the same quarter in the previous year (October to December 2022). There were 1.6 billion journeys in the year to 31 December 2023. This is a 20 per cent increase on the 1.3 billion journeys made in the previous twelve months (1 January 2022 to 31 December 2022).
A total of 15.2 billion passenger kilometres were travelled in Great Britain in the latest quarter. This is a 20 per cent increase on the 12.6 billion passenger kilometres travelled in the same quarter in the previous year.
Total passenger revenue was £2.6 billion in the latest quarter. This is a 20 per cent increase on the £2.2 billion in the same quarter in the previous year (when adjusted for inflation).
Commenting on ORR’s passenger rail usage statistics for October to December 2023, a spokesperson said: ‘Although the latest ORR data shows an increase in passenger numbers, passengers are still not using trains at the levels seen before the pandemic. This underlines the urgent need for rail reform to create a new public body to oversee the railways, but also to give operators the commercial freedoms to attract customers back to rail. Increasing passenger numbers will grow revenues, reduce taxpayer support, encourage modal shift and help Britain to reach net zero.’
Commenting on the figures Darren Caplan, RIA Chief Executive, said: ‘The return to rail continues apace and this substantial 20 per cent uplift year-on-year is a really encouraging increase in the number of passenger journeys and revenues. This follows the excellent recent DfT passenger statistics which – despite changing
calculations methodologies to exclude all Elizabeth Line passengers – has in March exceeded one hundred per cent of pre-Covid figures. Inclusion of those passengers would take overall numbers to nearly 110 per cent, which is real progress considering the comparison year, 2019-20, was the second highest on record.
These new ORR and DfT figures are a reminder that the railway will need more capacity in the future, especially with the recent RIA-commissioned Steer report forecasting passenger numbers to grow between 37 per cent and 97 per cent to 2050, depending on which policy levers the UK Government adopts in the coming years.
‘It is clear that there needs to be rail reform and a long-term rail strategy, including a plan for more capacity, to deliver the connectivity, economic, levellingup, and sustainability benefits everyone wants to see.’
Network Rail and partners from across the emergency services have joined forces to test emergency response plans to an ‘incident scenario’ within a railway tunnel just outside of Sutton Coldfield station.
On 16 March partners from West Midlands Fire Service, West Midlands Ambulance Service, British Transport Police, West Midlands Police and West Midlands Railway, joined Network Rail to complete some practical emergency rescue training within the railway tunnel at Sutton Coldfield station.
To begin the training exercise, a train, provided by the Rail Operations Group, was ‘dressed’ as if it had struck a fallen tree that had brought down the overhead wires, which provide power to electric trains, and was positioned in the railway tunnel at Sutton Coldfield station. Partners then sprung into action to begin rescuing volunteers posing as train crew and passengers, as if it were a live scenario.
The training exercise, which involved around 250 people, took place through the night from Saturday to Sunday while the railway wasn’t operational and to cause least disruption to passengers and nearby residents. The nighttime scenario made rescuing ‘passengers and train crew’ more complex as the response teams had to deal with a demanding environment including; lack of light, confined space underneath the tunnel, no power to the train and ‘smoke’ to imitate a fire.
The ceremony will take place at RIA’s fifth Annual Dinner on 27 June 2024 at the Landmark, London.
Deadline for nominations is 19 April 2024
An inspiring range of community rail initiatives, delivered by community rail partnerships, station friends volunteers, and other community groups across Britain, has been celebrated at the 19th Community Rail Awards.
The event, organised by Community Rail Network and jointly sponsored by Transport for Wales and Great Western Railway, was this year held in Swansea and joined by 430 guests including senior rail and transport leaders and community rail officers and volunteers. It recognised projects supporting diversity, accessibility and inclusion,
sustainable travel and tourism, youth and schools engagement, community-led station improvements, empowered communities and influencing positive change.
19 winners were recognised, chosen from 180 entries, demonstrating the positive impact of the community rail movement, enriching lives, enhancing local places, and promoting sustainable and inclusive travel and mobility.
The Community Rail Awards recognise the crucial, often unsung work of community rail partnerships, station friends and other community rail groups, which continue
to grow in number and impact, under Community Rail Network’s umbrella. There are now 77 CRPs and an estimated 1,200 station groups spread across Britain (and now a few beyond too).
Rail Minister Huw Merriman MP said: ‘The Community Rail Awards are important in recognising the incredible work of volunteers and community groups improving our rail network. I was lucky enough to see first hand the difference these projects are making when I met with some of those taking part including during my rail tour last summer.
‘Whether it’s improving accessibility in stations or engaging with young people about rail, I’d like to thank each and every one for their contribution and the impact they’ve made.’
The Outstanding Contribution to Community Rail Award was awarded jointly to Gloucestershire Community Rail Partnership and Coöperatie Stationspark Deurne, a station volunteer group in the Netherlands putting community rail on the world map. Gloucestershire Community Rail Partnership were recognised for their inspirational initiatives in the past year such as an impressive programme of activities engaging over 950 young people, empowering them through rail, and helping them have a voice. Improving accessible travel confidence, including highlighting step-free and accessible routes from each station. Working with housing developers to encourage sustainable and active travel for new homeowners. Developing ‘Train Tripper’, a website promoting car-free travel by highlighting the carbon reduction and savings of sustainable trips by rail.
A modern new station building has opened at Reading West Railway Station. The transformation of the station in Oxford Road includes new ticket gates, new lighting and CCTV cameras to significantly improve safety and security of the local community and travelling public, and opened to the public on Tuesday 19 March. Reading Borough Council has worked with Network Rail and Great Western Railways to deliver the £5 million project.
The new station building on Oxford Road is the centrepiece of the Reading West station upgrade, containing an information counter,
customer toilet and retail space. New ticket gates have also been installed at the Oxford Road and Tilehurst Road entrances to ensure that paying passengers only have access to the platforms.
The improvements have been made possible by the Council working with the railway industry to develop a masterplan for the station, secure significant external funding for the current works and deliver the realignment of the highway to provide space for the new station building, interchange improvements and resurfacing of the road and footpath.
FirstGroup has joined the United Nations (UN) Global Compact initiative – a voluntary leadership platform for the development, implementation and disclosure of responsible business practices. The UN Global Compact is a call to companies everywhere to align their operations and strategies with ten universally accepted principles in the areas of human rights, labour, environment and anti-corruption, and to take action in support of UN goals and issues embodied in the Sustainable Development Goals (SDGs).
Launched in 2000, the UN Global Compact is the largest corporate sustainability initiative in the world, with
more than 15,000 companies and 3,800 non-business signatories based in over 160 countries, and more than 69 Local Networks.
FirstGroup run a fifth of all local bus services in the UK outside of London, with a fleet of more than 4,500 buses and 51 depots, carrying more than 1.1 million passengers a day. The Group is also the UK’s largest rail operator, with three Government-contracted rail operations and two open access routes including the all-electric Lumo service. FirstGroup’s bus and rail services play a vital role in creating a connected, healthy, zero carbon world, contributing to local prosperity and growth,
reducing congestion on the roads, improving air quality and helping to reduce carbon emissions.
Graham Sutherland, FirstGroup Chief Executive Officer, said: ‘We are delighted to have joined the United Nations Global Compact, demonstrating our commitment to working together with companies globally to take responsible business action that drives real change. The ten UN Global Compact principles are critical to us as an organisation, as we push forward our ambition be the partner of choice for innovative and sustainable transport, accelerating the transition to a zerocarbon world.’
Alstom, global leader in smart and sustainable mobility, plans to operate a new passenger rail service across England and Wales. Working in partnership with consultancy SLC Rail, the open access operation will be known as Wrexham, Shropshire and Midlands Railway (WSMR).
As the country’s foremost supplier of new trains and train services, and a leading signalling and infrastructure provider, Alstom will operate its own rail service in the UK for the first time.
WSMR is seeking to introduce direct connectivity to and from North Wales, Shropshire, the Midlands and London that doesn’t exist today, linking growing communities and businesses, and making rail travel more convenient, enjoyable and affordable.
WSMR offers passengers in Wrexham, Gobowen, Shrewsbury, Walsall and Coleshill a direct link with the capital, alongside Darlaston once its new station opens. Meanwhile, journey times between Shrewsbury and Walsall will be dramatically reduced from the current alternative.
Rail Minister Huw Merriman said: ‘These exciting proposals could see better connections for communities across North Wales and the Midlands, including direct services to London from Shrewsbury, Telford and Wrexham. Competition delivers choice for passengers and drives up standards, which is why we continue to work with industry to help make the most of open access rail.’
It is anticipated that WSMR services could begin as early as 2025 and it is expected the new operation will create around 50 new jobs, with roles mostly based
The proposal envisages a service of five trains per day in each direction Monday to Saturday, with four travelling both ways on Sundays. Trains will stop at Gobowen, Shrewsbury, Telford Central, Wolverhampton, Darlaston, Walsall, Coleshill Parkway, Nuneaton and Milton Keynes on their journey between Wrexham General and London Euston.
WSMR estimates it would serve a core catchment area of around 1.5 million people outside London, a population which is set to grow by 16 per cent over the next decade.
Ian Walters, Managing Director at Midlands-based SLC Rail said: ‘From the Welsh borders to the Midlands, our routes will forge new connections, linking overlooked regions of England and Wales with direct services to and from London. Passengers will benefit from more competitive fares and new technology to simplify ticket purchasing for our new services. Delighting the customer will be at the forefront of what we do; we want WSMR passengers to experience a new excellence in customer service onboard our intercity trains. Our proposal will support sustainable housing growth, nurture communities, and
unite business, leisure, and commerce along the corridor. This will enhance economies and bring a positive impact to both communities and the environment – and we can’t wait to get started!’
In the West Midlands, WSMR trains will avoid Birmingham – one of the most complex and congested parts of the British rail network – by utilising the Sutton Park line, which is currently only used for freight services. This would enable Wolverhampton and Walsall to serve Nuneaton directly for the first time, offering new travel options across the West Midlands, North Warwickshire and beyond.
Healthy rail
Harmonised rail
Sustainable rail
Automated rail
Efficient rail
Digitised rail
Resilient rail
Insightful rail
GB Rail 2024-2029: Safe rail
We’re with you every step of the way
We’re used to providing continuity while embracing change – a vital balance that defines how RSSB operates. We preserve the industry’s institutional memory while encouraging innovation and our five-year strategic plan for 2024-2029 is designed to keep us on track.
Our ambition is that by 2030, every rail employee will use at least one RSSB tool or service every day, from the Rule Book to cuttingedge research. It’s a challenging target, but we believe we can achieve it – with your help.
To find out more about our latest strategic plan, visit www.rssb.co.uk/continuityandchange
Great Western Railway’s innovative fast-charge battery trial officially commenced on 18 March. Over the past two weeks, specialist GWR engineers have successfully tested the compatibility of the fast-charge technology with the Class 230 battery train on the Greenford branch line.
The industry-leading trial will now start in earnest and it is hoped the technology could one day see battery-powered trains in operation across the UK’s approximately 2,000 miles of 80-plus branch lines. The fast-charge technology solves the problem of delivering reliable, battery-only trains and is designed to help meet the Government and wider rail industry’s target to reach net-zero carbon emissions by 2050.
GWR Managing Director Mark Hopwood said: ‘We want GWR to be at the forefront of the railway’s commitment to phase out diesel-only traction by 2040 and this
demonstrates that we put our customers at the heart of everything we do.
‘This is why we took on the challenge and are taking an industry-leading approach in not only battery train operation, but the development of the fast-charge system. It’s important to remember this work has never done before. It’s designed to test the capability and viability of the fast-charge technology – and demonstrates Great Western Railway taking a bold and broad approach towards replacing diesel-only trains with greener units.’
Rail Minister Huw Merriman said: ‘We're ambitious about making the railways even more sustainable and this trial, backed by Government funding, could pave the way for greener journeys for millions of passengers across the network. Rail is already the most environmentally friendly form of public transport and battery-powered technology
will play an important role in further decarbonising it, helping us reach our netzero target by 2050.’
The use of batteries for extended operation has typically been constrained by their range and meant widespread implementation has, until now, not been possible. It also negates the need for overhead electric lines which are expensive, time consuming to install and impact the landscape.
At West Ealing, the train will charge for just three-and-a-half minutes before restarting its journey on the Greenford branch line. GWR has already carried out simulations on other branch lines in the Thames Valley to explore how it could be rolled out even further in the future. This could reduce GWR emissions alone by over 1,700 tons of CO2e per year.
East Midlands Railway (EMR) has announced the start of a £60 million programme to refurbish its fleet of Class 360, Class 158 and Class 170 trains. The project is being delivered in partnership with Angel Trains, Siemens, Porterbrook, and Eversholt and leverages significant private sector investment. All the work will be carried out in the UK providing a significant boost to the supply chain.
Together with the introduction of the new Aurora Intercity trains, this will mean that all of EMR’s trains will either be replaced with new trains or refurbished.
EMR’s electric Class 360 fleet operates EMR Connect and Luton Airport Express services between Corby and London St Pancras stopping at Kettering, Wellingborough, Bedford, Luton, Luton Airport Parkway.
The trains will be upgraded to provide better facilities for commuter, leisure and airport passengers including new 2+2 seating throughout the trains in a mixture of airline style and bay seats, luggage racks, charging points and new passenger information systems.
EMR’s Class 170 fleet operates regional services across the East Midlands including, Matlock to Derby and Nottingham, Nottingham to Worksop via Mansfield, Newark Castle to Crewe via Nottingham, Derby and Stoke-On-Trent, Peterborough to Doncaster via Lincoln, Nottingham to Skegness via Grantham, Cleethorpes to Leicester via Lincoln and Nottingham, and Cleethorpes to Barton on Humber.
The trains have come to EMR from different operators and will be upgraded to provide a consistent customer experience across the fleet. All trains will receive new seat foams and covers, an extensive refresh as well as new passenger information systems and CCTV. EMR's Class 158 fleet mainly operates on the Liverpool to Norwich route via Nottingham, Manchester and Sheffield. The trains will receive new seat covers and foams, an interior refresh and CCTV.
Sam Sherwood-Hale spoke to James Redmayne, Managing Director at Zinc Consult about his recent appointment, the role SMEs can play in the sector and how he thinks we can tackle the skills gap
At the end of 2023, Zinc Consult appointed James Redmayne as Managing Director. James joined following an eleven year stint leading the regional rail team for the global consultancy Arcadis. Having spent 28 years as a quantity surveyor, James’ worked his way into senior management positions from the bottom-up, having started as a junior. By the age of 35 he was an associate director and sought out the MD role in order to help ‘grow himself’ as a leader.
His arrival further bolsters Zinc Consult’s workforce, which helps to deliver the firm’s range of pre and post-contract commercial services by utilising its indepth knowledge of the rail industry.
Launched almost a decade ago by former Network Rail colleagues Michael Phillips and Jonathan Blenkey, Zinc Consult provides an extensive range of consultancy services with a specialist focus on the rail sector.
During the past ten years, the Leedsbased firm has expanded its footprint by establishing itself as a northern powerhouse in the industry – with bases in Glasgow, Birmingham and Teesside. Besides rail, it also offers consultancy services for sectors like energy, infrastructure and highways.
The company is constantly exploring new opportunities, recent exciting developments include an expansion into the renewables sector and the successful creation of an Estimating and Cost Planning Division.
SSH: Co-founder Jonathan Blenkey, referred to your appointment as ‘a real coup’ and that the hope is to turn Zinc Consult into a ‘Northern Powerhouse’. How do you hope to do that and how can SMEs have a bigger impact on the rail sector?
JR: I think there are so many organisations out there that can make a real difference and they are just not given that voice.
Firstly, small companies have only got the time and bandwidth to just get on with the job, their focus is on delivering what they said they were going to deliver – that’s where their success is. Bigger organisations can promote on the back of their successes, write the reports related to the project and generally get their name and brand out there in the same conversation. It’s that balance
of availability of resource. Most of what is new gets off the ground by the smaller companies, but they lack the resource making it difficult to sustain.
SMEs are good for the marketplace as we are incentivised to come up with new ideas to develop and grow as a business, but upstream of that is an understanding from our clients, such as Network Rail or the TOCs, that they do not need to go to the big organisations to get the answers they need. Changing the client’s awareness of who is actually the lead on innovation, smaller, more agile company’s are not out there for a major, multimillion pound order – we’re out there to make a difference, earn the margin necessary to succeed and sustain ourselves but then ultimately to give a return to our clients.
When I became a partner at Arcadis, it was the proudest day of my professional career. My move to Zinc comes after watching them for four or five years and I’ve seen an organisation that’s developed a digital product, trying to shake up the procurement methodology and become something that the others aren’t. Using intelligence and knowledge to make a wider offering, that became a very exciting draw to me and my energy and enthusiasm that came from the experience at Arcadis made it a perfect fit.
The train operators absolutely like the idea of something different because their focus is purely on offering a value product. For large organisations like Network Rail, once procurement and the reviews commence, the ideas tend to get watered down and in the end what they want is far less than what was originally requested. My goal over the next couple of years is to try and evolve Network Rail and other clients’ thinking and get them to embrace SMEs more and ultimately not be worried about challenge from the big organisations, and embrace what the smaller organisations can bring.
SSH: What is the medium of that conversation, are you going directly through contacts you’ve established so far personally over the years, are you working with the Rail Industry Association or Rail Partners or these sort of advocacy groups?
JR: I have worked with RIA in the past and found them very useful in terms of putting forward good ideas and good processes, especially with electrification
‘My hope for Zinc is that we are able to show what the value of something is rather than just currently tell everyone what the cost is.’
which is something I’ve been involved in. I'm currently working on the Transpennine Upgrade for Network Rail and I will be using that as an opportunity to express what is possible.
SSH: There's a lot of very talented people working in the rail industry who are very good at explaining what the problems are, but then the message from the trackside gets lost on the road to the decision makers at the top. How will new organisations, such as Great British Railways, that are going to be managing the railway help that?
I’ve currently been working as part of an enterprise programme with TRU. We’ve been trying to work alongside the other stakeholders as a collective with the same goal of delivering an improved railway for The North, however the amount of friction that causes is quite amazing. That friction is there for all the right reasons, there are a lot of different businesses involved with different requirements and objectives but ultimately, on this programme we are all working towards the same goal and will see it through together.
I think that’s a huge change from where we used to be. Therefore, I think the idea of Great British Railways is a very positive step and it should be a lean organisation where direction is set and decisions can be made to promote quality and efficiency. That’s a long way off though, and the pain we will have to go through before then will be challenging. I think the rail industry suffers from a lack of knowledge resilience. There’s a lot of individuals with a good understanding of the railway, but take those individuals away and the next level does not have that appreciation.
SSH: This idea that we are losing skilled people and not replacing them in any meaningful way seems to be a running theme through the industry and the conversations I have – how can we tackle that problem?
JR: The development of training has been reduced by a desire to save money within an individual organisation, therefore training and development have been pushed further and further down the supply chain. It's now down to the contractors, the subcontractors and the SMEs to do the training and development.
Responsibility has been slowly passed down the supply chain, which then struggles to keep it going as there is minimum government support. The concept of winning jobs at the lowest price means cutting costs and so why would we keep development programmes in place when we could poach from others. So the whole process has become a burden that we’re not collectively willing to pay for.
We have to sit back and look at this as leaders of our industry and ask ourselves how we want to develop and grow.
Ironically enough, going forward we will need a different skillset compared to what we had in the past. Actually, the fact that we have eroded our skillset isn't necessarily a bad thing. The way we can do that is by training more people who understand technology, more people who understand the variety of all systems. Rail is a systems industry, it isn’t infrastructure – it is a completely integrated piece and organisations that can work and develop as an integrated piece are the ones which will succeed.
That knowledge base requires a completely different training and development ethos from what it was ten years ago. We have access to design standards, we have our processes – so it's then how you apply them, not ‘do you know it’. For me within Zinc what I would like to do is tap into that younger generation and train them in a different way so they are able to understand why they are doing something, putting it all together rather than just siloed delivery of their specific service.
SSH: What would be the main focus point for you to achieve that?
JR: I would first ask what is the platform we’re working to. With Zinc we’ve just developed a digital twin process, so for example we have a train station and we can go and digitally twin that station into an exact model to a very high accuracy. What we can then do is use that as a training ground; I can use it for estimators to price from; work out constructability assessments, we can turn it into an operational station and have people with 3D vision walking around the station to understand what works and how it operates.
‘Responsibility has been slowly passed down the supply chain, which then struggles to keep it going as there is minimum government support.’
from abroad for a couple of years but if we start buying these from abroad the UK industry will see there is a benefit to making it in this country. What is really needed is a centralised team within Network Rail and other major clients to work out the opportunity and using their full portfolio of work to understand what the real difference could be.
SSH: Any commitment to big projects always seems to be up in the air and I'm wondering in your experience of working with individuals do you feel that commitment to these specific things that you mentioned?
If a fire goes off for example you can actually see how people would move within that space and how the wayfinding would work.
A lot of the big issues that we have with rail can be all done through modelling, through process and through analytics therefore the training and development requirements change. It is no longer designing a rail on the ground it is now designing a journey from A to B –encompassing everything. Therefore, the training and development of that person is more than just engineering it's more than just systems, it’s more than just cost, it’s about the interface.
The people we have working on these projects won't necessarily need to be trained in a pure subject anymore as AI technology can provide a competent structure, it will be about finding the person to understand whether the structure fits into the surroundings and satisfies the requirements.
SSH: How do the various government targets, such as Net Zero, factor into all this?
JR: The Transpennine Route Upgrade is absolutely focused on developing and growing its net zero, sustainability and biodiversity strengths not just because it's the right thing to do but because it's such a major programme that the impact of the change will be much greater. I've been involved with quantifying all of the CO2 equivalent carbon within the programme, and we’re actively looking at ways of reducing it. We're trying to blend that requirement into the cost and estimating process, so overall whenever any estimates are done in the future you'll be able to immediately see what the carbon footprint is and provide opportunities to reduce it.
Our biggest stumbling block has actually been data from organisations about what the CO2 savings are, we had large debate over certain products that, because they come in from abroad, have a higher CO2 component but the actual product itself is a lot lower. Yes, we may have to buy it
JR: They’re too far away from it, they’ve passed all the supply to the contractors. Network Rail will say it, will talk about it, will love the idea of it, but ultimately they've passed the decision to somebody below and that's why I'm saying they need to take the lead and enable the supply chains.
SSH: Is that something that is likely to happen or trending in that direction?
JR: It's definitely trending in that direction, Network Rail are looking at the whole life carbon process – starting with where it's coming from, its end of life costs and all the in between. It will probably be a few years before it really gets up and running and someone passionate takes the lead.
SSH: What do you consider to be the most pressing issue facing UK rail?
JR: We still do not consider the value of something just the cost, for example HS2 has been the typical major project where the cost loses control, interestingly it is amazing how nobody talks about the cost when it’s a success. So, the focus has to be on the value of what we're doing and therefore what multiplier is acceptable, what do we get for the cost and do we have the right controls in place to hit that value. Everything should have a multiplier on it, we should remove cost from being such an emotive subject.
We need take cost control seriously, it must be a leading indicator, whereas currently it is a prevailing one. We have to change the whole terminology and understanding around cost, something I am endeavouring to do by using benchmarking, and should cost models all of which focus on value.
We may make investments which on paper look to have a high cost, but will provide many benefits, in rail the biggest one is freight. More freight by rail is hugely beneficial in terms of the multiplier effect for investment, yet it costs so much to put in a mile long loop and separate from passenger trains. The cost of something or the value of something? My hope for Zinc is that we are able to show what the value of something is rather than just currently tell everyone what the cost is.
Jacqueline Starr is Chief Executive of Rail Delivery Group. She joined the rail industry in 2015 as Managing Director of Customer Experience before progressing to Chief Operating Officer. She was appointed Chief Executive of RDG in December 2020.
Jacqueline
Chief
Rail
We all know that rail is the green option for business travel but that assertion was merely anecdotal and we didn’t have the evidence –until now.
In February this year, we released Green Travel Pledge carbon emission data showing that rail is almost nine times greener than using a petrol or diesel car for the top one hundred business travel routes across Britain.
The new data also showed taking the train is four times greener than driving a plug-in hybrid electric car, and almost twoand-a-half times greener if using a battery
electric car. Air comparison is to follow this month.
Up until now businesses had to rely on an average figure to measure the carbon emissions of a rail journey, which only takes into account an average of energy usage by train across the entire rail network in Britain and the straight line distance between your origin station and destination.
It didn’t take into account the type of train that serves that route (whether it’s an electric or diesel train), the exact distance you travel, whether you sit in first class or standard class and, most importantly for a per passenger measurement, how many people are usually on your train.
At Rail Delivery Group, we want to help promote a future where business travellers can see the exact amount of carbon emissions their journey will produce at the point of sale. We want customers to be informed of the benefits of electrified trains and busy routes which ensure per passenger emissions are significantly lower than using other transport options.
For example, travelling by train for business between Haymarket in Edinburgh and London King’s Cross creates nearly 20 times less emissions than if you were to drive the same route in a diesel or petrol car.
For the first time Green Travel Pledge data provides detailed, per passenger carbon emission figures for each route. The data takes into account the exact journey distance, the type of train used, type of fuel, number of passengers/carriages as well as how many people are in standard class and first-class carriages.
Why is that important? Businesses are now having to report on their Environmental, Social and Governance (ESG) goals in more detail than ever before. For many companies, business travel is one of the most significant contributors to their carbon footprint. Embracing ways to support their people in choosing lower carbon journeys will help them reduce this.
Last year we spoke to business leaders and the ask was clear – we need better data to support accurate reporting of carbon emission savings that can be made by switching from air and car travel to rail for business travel.
We’re working with some of the main travel management companies and online booking tools to ensure that once we have carbon data for all point-to-point routes in Britain this summer, it will be able to be seamlessly integrated into booking systems immediately.
This is critical as we know customers want to make an informed, green travel choices. More than four out of five customers (82 per cent) we surveyed last year thought that using an environmentally friendly transport mode in their everyday life is important.
And it’s the same in the business travel community, with more than half of corporate travel managers (51 per cent) surveyed for the Business Travel Show last year saying they would like to set and monitor carbon budgets but their online booking tool technology doesn't have the functionality.
As an industry, we have invested in reliable carbon data to equip businesses and individuals with the carbon data to support a modal shift towards rail. But we know that sustainability isn’t the only factor people think of when choosing a transport mode. We have a responsibility to make the benefits of choosing to travel by train more compelling. Rail has been around for almost two centuries so it’s easy to forget the benefits it offers over other forms of transport.
People who travel by train arrive in better shape for business – having had a chance to rest, refresh or catch up with colleagues. People can be more productive on trains than on other travel modes as they can commit time to either work or read without needing to concentrate. And finally, trains take people to the heart of business destinations. Train stations are placed at the centre of our towns and cities so you can quickly and easily get where you need to go. As an industry, we
know there’s still more work to be done.
We’re working on simplifying fares to make it easier for people to find the right ticket for their journey and have flexibility when plans change.
Over the past ten years, we’ve replaced or upgraded more than half of all trains in Britain. That represents a huge investment in improving customer experience as well as supporting the rolling stock industry, which contributes at least £1.8 billion to the
UK economy annually and supports around 30,000 jobs in the UK supply chain.
We know that rail across Britain holds the key to a sustainable future for business travel. As we get closer to the UK’s 2050 net zero emissions target, we are looking to proactively work as an industry with businesses and the business travel sector to ensure rail is at the heart of our collective efforts to create a sustainable future for transport in Britain.
Rail finance figures highlight improvements, but full recovery still a long way off, Chris dives into the numbers
The passenger rail industry’s finances took a turn for the better in 2022/23, according to figures published recently by the Office of Rail and Road (ORR). However, there was still a deficit on the passenger business of some £4.2 billion, which had to be met by the taxpayers.
Total passenger income during the year was £8.4 billion, 32.6 per cent ahead of the previous year. A further £628 million of other operating income brought the total income to £9.03 billion, 27.6 per cent up. Operating costs during the year totalled £13.2 billion, 7.7 per cent down on the previous year, leaving the £4.2 billion deficit. This represented a 42 per cent improvement on 2021/22.
The government paid £4.36 billion in subsidies to the train operating companies, leaving them an operating profit of £193 million, at a margin of 2.1 per cent. The net figure, after finance and taxation, was £159 million giving the operators a 1.2 per cent uplift on operating costs.
Despite the substantial improvement, revenue figures continued to be well below pre-Covid numbers. The total passenger income in 2018/19 was £11.95 billion, so last year’s total remained 29.7 per cent short. Costs, meanwhile, were 1.4 per cent lower than before the pandemic.
The figures also give some breakdown of operating costs, enabling us to look at both their movement and the percentage breakdown. Highlights include:
• The largest component was staff costs, which, at £3.73 billion, represented 28.2
per cent of the total. The cost was 6.3 per cent lower than 2021/22, and 3.6 per cent down on 2018/19.
• Track access charges paid to Network Rail totalled £3.43 billion, accounting for 26 per cent of the total. The figure was 1.4 per cent up on the year, and 7.4 per cent higher than pre-Covid.
• Rolling stock charges were the third highest component, on 23.4 per cent, giving a total figure of £3.09 billion. This represented a saving of six per cent over the previous year but were 7.4 per cent higher than before the pandemic.
• Diesel fuel is the smallest component identified separately, accounting for 3.1 per cent of total costs, but showing the largest increases. The £404 million total was 30.7 per cent higher than the previous year, and 22.5 per cent up on 2018/19’s figure.
• The balance of costs, comprising 19.3 per cent, covered other operating costs. The total, at £2.55 billion, was almost 24 per cent down on the previous year, and 15.6 per cent down on the prepandemic figure.
Looking at sector performance, the InterCity operations saw revenue growth of 40.1 per cent, whilst operating costs rose by just 1.4 per cent. The subsidy requirement fell by 49 per cent to £910 million, but income remained 25.2 per cent below the 2018/19 total.
The commuter services in London and the South East (excluding the Elzabeth Line) came next in terms of revenue growth,
AtkinsRéalis, a fully integrated professional services and project management company with offices around the world, has been appointed by Translink – Northern Ireland’s main public transport operator – to provide design and construction management on its rail network’s signalling and telecommunications.
AtkinsRéalis is one of two suppliers to win a place on a competitive framework, which has a total estimated value of £150 million – £250 million and will run until 2029, with the option to extend by a further 36 months.
Translink operates passenger rail and bus services in Northern Ireland. Its rail network covers around 300 miles of track which facilitate almost 13 million passenger journeys annually. Under the framework, AtkinsRéalis will perform multidisciplinary design, construction and commissioning works on a wide range of projects to renew and refurbish Translink’s signalling and telecommunications infrastructure, including lineside signalling assets, level crossings, and control and interlocking systems.
With an office in Belfast, AtkinsRéalis has worked closely with Translink in the past to provide design and consultancy services to assess, repair and maintain its rail network, as well as support with the delivery of the world-class Belfast Grand Central Station transportation hub.
Following the publication of the Making Tracks Towards Sustainability study, an overview of sustainability in the European railway infrastructure management, Standard Ethics announces the upcoming launch of the SE Global Railway Manufacturers Index. The Index will be officially published in June 2024 and revised every six months, at the end of March and September. The SE Global Railway Manufacturers Index constituents will be selected from the largest global manufacturers of rolling stock (from metros to high-speed trains), rail transport services and infrastructures, including their maintenance and modernisation.
achieving 33.8 per cent. Operating costs were 7.6 per cent lower, and the subsidy requirement fell by 53.6 per cent to £1.34 billion. Income remained 28.9 per cent below pre-Covid levels. The Elizabeth Line earned revenue of £336 million, against costs of operation of £498 million, leaving a subsidy requirement from TfL of £166 million.
The regional franchises saw revenue growth of 26.9 per cent, whilst costs rose by 3.7 per cent. The subsidy bill totalled £1.93 billion, down from £2.04 billion a year earlier. Income remained 25.2 per cent short of pre-pandemic levels.
Amongst individual TOCs, the largest subsidy was paid to the state-run ScotRail, at £697 million. This public support covered 72 per cent of its total operating costs, with the passenger and other income of £278 million not quite covering the operation’s labour costs. The subsidy was down from £761 million a year earlier, but up from £454 million pre-Covid. The income figure compared with £199 million in 2021/22 but still some way short of the £419 million earned in 2018/19.
Also topping the £600 million figure was another state-run business, Northern. Here, total subsidy of £602 million paid for 64 per cent of operating costs. The passenger and other income of £336 million managed to pay for 84 per cent of the wages. The subsidy bill fell from £636 million in 2021/22 and compared with the £368 million paid in 2018/19. Income growth of £26 million had been achieved over the previous year’s total of £310 million, but still fell short of the £392 million received in 2018/19.
At the other end of the scale, one operator, the Greater Anglia, now owned by the Transport UK Group in joint venture with Mitsui, actually paid a small premium of £26 million to DfT during the year. This small premium compared with a £226 million subsidy bill in the previous year but fell short of the £232 million paid to government in the last pre-Covid year. The company’s £603 million worth of income
compared with £336 million in 2021/22, although it was still short of the £746 million earned in 2018/19.
The next lowest subsidy spending came at Arriva’s Chiltern operation, which received £20 million in aid, down from £63 million in 2021/22 but compared with a £68 million premium from 2018/19. The company’s revenue of £184 million had grown from £128 million in the previous year but was still short of the £266 million earned in 2018/19.
The highest proportional revenue growth was achieved by GWR, the FirstGroup subsidiary. Income totalled £953 million, up 135.6 per cent from the previous year’s £694 million, though this remained just under 16 per cent below pre-pandemic levels. Next came London Overground, operated by Arriva for TfL, which saw 80.3 per cent growth, taking the total to £242 million, coming to within 11.2 per cent of 2018/19. Greater Anglia saw a similar advance of 79.4 per cent, taking the total to £603 million, 19.1 per cent below full recovery.
The lowest revenue growth occurred at Merseyrail, the Serco/Transport UK joint venture, at just 3.3 per cent, taking the revenue to £73 million, but this was within 1.4 per cent of what was being achieved before the pandemic. The only other TOC with revenue growth in single figures was Essex Thameside, Trenitalia’s heavily commuter-dependent operation, where growth of 4.4 per cent took the total to £135 million but left it 32.6 per cent short of recovery. One operator, Caledonian Sleeper, recorded income above that achieved before the pandemic. Franchisee Serco saw revenue £2 million or 5.8 per cent up on its 2018/19 figure in its last full year of operation before renationalisation in June 2023.
The ORR’s figures paint a fascinating picture of an industry still in recovery from the shocking events of 2020 and 2021, and their ongoing consequences. As with the quarterly demand figures I discuss regularly in these
‘Total passenger income during the year was £8.4 billion, 32.6 per cent ahead of the previous year. ’
pages, we see an industry badly affected by ongoing falls in commuting as hybrid and home working become further established and where the goose of business travel has ceased to lay its golden egg of full price and first class revenue.
In a year of economic and political turmoil, high inflation and a cost of living crisis, not to mention ongoing industrial action and poor performance in several companies, one could argue that the remarkable thing about these numbers is that growth was achieved at all.
From the government’s point of view, the ongoing need for at least £4 billion in revenue support for the train operators is clearly unwelcome – as DfT ministers are wont to remind the industry – and, as the fiscal year 2023/24 draws to a close as I write, it remains to be seen how the figures for 2023/24 will pan out.
Indications of a continuing recovery came as I write in the form of the latest quarterly statistics, published on 21 March, which I hope to analyse in more detail in my next article. At first glance, the figures are encouraging, with patronage growth of 19.9 per cent in the quarter, and as much as 27 per cent in the rolling year to 31 December. Revenue was 20 per cent up on the quarter (after adjusting for inflation), and 15 per cent ahead on the rolling year, giving an annual total of above £10 billion for the first time since the start of the lockdowns.
Like the economy has a whole, the rail industry may have turned a corner.
One
Kilborn Consulting Limited is an independent railway engineering consultancy and design business, with over 21 years of railway experience.
We specialise in the design of new and altered railway Signalling & Telecoms systems for the UK railway infrastructure.
Our areas of specialism are:
•Signalling and Telecoms Consultancy, including technical advice & support;
•Asset Condition Assessments, Correlation and Surveys;
•Signalling & Level Crossing Risk Assessments;
•Feasibility and Optioneering Studies;
•Concept and Outline Signalling Design;
• Telecoms Option Selection Reports (including AiP), Reference System Design and Detailed Design;
•Detailed Signalling Design;
•Competency Management & Assessments;
•Signal Sighting assessments, covering the full Signal Sighting Committee process with a competent Chair.
The new office which is located in the heart of Wellingborough can accommodate all staff and visitors alike and offer widespread views across Wellingborough and the surrounding green spaces
We would be delighted to welcome you to our office to discuss your requirements and how we can support you to achieve those.
Kilborn Consulting Limited 6th Floor, South Suite, 12 Sheep Street Wellingborough, Northamptonshire NN8 1BL
Email: pmcsharry@kilbornconsulting.co.uk
Phone: 01933 279909
When it comes to introducing new legislation, it often takes some time from its inception until it is added to the Statute Book and actually becomes the law of the land
The legislation to bring the main proposals of the Williams-Shapps Plan for Rail has been long talked about, the Plan for Rail having been published in May 2021, with the Great British Railways Transition Team being established later that year. However, the introduction of new laws was only announced in the King's Speech to Parliament in November 2023, and it took until 24 February of this year for the draft Rail Reform Bill (the "draft Bill") to be published.
As a further point of note, the Bill has been published as a ‘draft’ Bill, so that instead of going straight into Parliament to be debated by MPs and members of the House of Lords, it must first be scrutinised, in this case by the Commons Transport Committee (Transport Committee). The Transport Committee have made it clear that they wish to move this examination process on quickly and have already issued a call for evidence from the rail industry and other interested parties. The Transport Committee will be holding an enquiry into the draft Bill immediately after Easter with the intention to have completed their review and recommended any changes to the Bill by the summer. However, the potential for a general election in October means that there is limited time for the draft Bill to be debated in Parliament and it is highly likely that it will be shunted into the sidings until a new Government is formed after the election.
Those people who have already read the draft Bill, will have noted that in addition
to the main sections on reforming the management and organisation of Britain's railways, there is an additional section on introducing the Luxembourg Rail Protocol (the ‘Rail Protocol’) into UK law.
First, a quick debunking. The Rail Protocol has nothing to do with the EU or being a way of introducing EU law into the UK. It is instead one of 4 protocols to the Cape Town Convention on International Interests in Mobile Equipment (the ‘Cape Town Convention’). The Cape Town Convention itself is an agreement managed by UNIDROIT, an intergovernmental organisation whose objective is to harmonise international law across countries through uniform rules, international conventions and other procedures. The reference to ‘Luxembourg’ is to the capital city of Luxembourg, which shares the same name as the country, and is the place where, in February 2007, a diplomatic conference was held to agree the terms of the Rail Protocol.
The Cape Town Convention provides for a common set of rules for registering a security interest in different types of mobile asset. This allows a creditor to have a clearer path to take control of the asset that they have financed where the debtor is not repaying that finance under the terms of the finance agreement. This could either be in conjunction with a cash loan to buy the asset or be part of a leasing transaction. The Aircraft Protocol to the Cape Town Convention has been in force since March 2006 and has provided considerable savings to airlines leasing aircraft in the intervening years.
The Rail Protocol supports the financing of railway rolling stock and has a very broad definition of ‘railway rolling stock’. It covers
Martin Fleetwood is a Consultant at Addleshaw Goddard’s Transport practice. The Rail Team has over 30 lawyers who advise clients in both the private and public sectors across a wide range of legal areas. As well as contractual issues, the team advises on operational matters, franchises, concessions, finance, regulatory, property, employment, environmental and procurement issues.
Disclaimer: This article is for informational purposes only and does not constitute legal advice. It is recommended that specific professional advice is sought before acting on any of the information given.
Although the UK has a sophisticated finance sector supporting the rail industry the Rail Protocol will:
• Provide additional security for lenders and lessors
• Lower the cost of finance for rolling stock assets
• Lower barriers to market entry for new financiers
• Support train services that run internationally
• Create new markets for funding overseas projects
• Allow UK manufacturers to offer finance packages similar to overseas competitors
all types of vehicles which run on rails or above or below a guideway and includes:
• Traditional trains and trams.
• Funiculars and cable cars.
• People movers at airports.
• Road vehicles which also have rail wheels such as maintenance unimogs and jcbs.
• Tunnel boring machines which run on rails.
• Moving cranes in freight exchange sidings or docks which run on their own rails.
If the Rail Protocol were agreed in 2007 why is it appearing in the draft Bill now? International treaties have to pass a number of hurdles before they can become enforceable law, and the Rail Protocol is no different.
The Rail Protocol had two hurdles:
• At least four countries to have recognised the Rail Protocol in their domestic law and made it enforceable in their courts.
• OTIF (the Intergovernmental Organisation for International Carriage by Rail) to confirmed that the International Registry where the security interests would be registered was fully functional.
In February 2023 Spain was the fourth country to include the Rail Protocol in its domestic law and on 8 March 2024 OTIF confirmed that the International Registry was ready to start operations. After just over 17 years, the Rail Protocol came fully into force in Luxembourg, Sweden, Spain and The Gabon.
With the Rail Protocol now fully functional, its inclusion in the draft Bill is therefore very appropriate. The UK signed the Rail Protocol in February 2016, and the draft Bill provides the right mechanism to start the process to bring it into force under UK law.
Using benefits of the Rail Protocol now
While the UK has not yet ratified the Rail Protocol, rail is a global marketplace and transactions with the UK rail sector may
involve countries where the Rail Protocol does apply. The Rail Protocol is designed to protect financial interests in railway rolling stock, reducing risk and thereby allowing for lower cost finance, supporting exports. A UK bank financing new rolling stock for a rail project in Sweden can now get a stronger security over that rolling stock by registering its interest at the International Registry.
Although the Rail Protocol is not "live" in the UK, there is an opportunity to register an interest in the International Registry. Being recorded in a public registry, this interest should defeat a challenge by a third party claiming they had no notice of the interest. Information held on a public registry is deemed to be known to all –whether you decide to look or not.
There is also the opportunity to get ready for the Rail Protocol to arrive in the UK. Leasing documents can be updated to include a "rail protocol clause" allowing for registrations to take place once the Rail Protocol is adopted into UK law. Each item of rolling stock requires a unique identification number issued by the International Registry which needs to be attached to each item of rolling stock and this process can be started now.
Some laws take a while to arrive, but hopefully they are worth the wait!
The SB60 SKR Automaster allows one machine operator to replace and fasten a sleeper in a single cycle. This reduces the risk of work related accidents to rail workers during sleeper replacement.
The sleepers can be changed from both middle and side of track, with high precision fastening of Pandrol Fastclip and FE. The high capacity allows the operator to change up to 60 sleepers per hour.
Network Rail Product Approval: PA05/04237 - Issue 2
Connected Places Catapult, the UK’s innovation accelerator for cities, transport, and place leadership, has announced the names of three companies chosen by the Catapult, Network Rail and GWR to trial new technology as part of the Station Innovation Zone at Bristol Temple Meads. The three firms – Chrome Angel Solutions, Co-You, and CrossTech – were selected from a longlist of eight companies announced in January, who were keen to demonstrate new ideas to help improve various aspects of the passenger experience at the station. Each of the three shortlisted companies will receive funding of up to £75,000 to take their proposals forward for trial, testing and evaluation, after initially being awarded £2,000 to develop a trial plan and receiving business support and pitch coaching.
Business leaders have hailed the news that works on the Bletchley to Bedford section – the Marston Vale Line (MVL) – of East West Rail will be bought forward
The Government reaffirmed its commitment to delivering EWR in full in the 2024 Spring Budget by announcing that £240 million in existing funding would be made available to fast-track works on the MVL.
These works will enable passenger services between Oxford to Bedford (EWR Phase 2) to start by the end of the decade as a supplement to services on the first phase of the project between Oxford and Milton Keynes/Bletchley, which are due to start next year.
This investment will allow people living between Oxford and Bedford the chance to reap the benefits of EWR much sooner than originally planned. It will improve access to innovation and economic hubs in Oxford, Bedford, and Milton Keynes, boosting connectivity and unlocking productivity across the region as well as allowing better access to jobs, education, healthcare and leisure opportunities.
The accelerated works will bring forward level crossing works, track and signalling upgrades, as well as safety and accessibility improvements to allow a one train per hour service between Bletchley and Bedford.
Richard Tunnicliffe, Regional Director (East of England), Confederation of British Industry, said: ‘The CBI welcomes the commitment to fast-track the Bletchley to Bedford section of East West Rail. New infrastructure can bring major benefits to businesses and help fuel local economies, so it’s vital that towns like Bedford and the businesses there get the transport connections they need so they can prosper.
‘East West Rail will be a key driver of economic prosperity, providing businesses with the confidence to invest in the area with the prospect of greater connectivity, giving greater accessibility to more trade and a larger labour market. This can only be a good thing for business in the region and we look forward to its many benefits.’
Charlotte Horobin, CEO, Cambridgeshire Chambers of Commerce, said: ‘We welcome the news that the Government has reconfirmed its commitment to building East West Rail in full to Cambridge and are delighted that plans will be brought forward which will allow services to start running between Bletchley and Bedford much sooner.
‘The East West Rail project represents a unique opportunity to drive both local and national growth. Its benefits extend far beyond transportation, promising to transform our region into a dynamic and prosperous economic hub. This is good news for businesses, commuters and everyday people looking to use East West Rail both in Cambridgeshire and across the wider region as part of their daily lives.’
Suzanna Austin, Development Manager (Beds, Cambs and Herts), Federation of Small Businesses, said: ‘It is good to see the next stage of East West Rail receive the
‘Construction work on the Marston Vale line between Bedford and Bletchley will be brought forward, enabling services to Oxford to begin in 2030’
green light to proceed with upgrading the existing section of line between Bletchley and Bedford. When complete this upgrade will enable faster greener connections for the many small businesses in the area, connecting key towns and cities across the wider region.’
Beth West, CEO, EWR Company, said: ‘This announcement is great news for people living between Bedford and Oxford as it means some work can now start earlier than
planned to enable a quicker introduction of a new Oxford-Bedford service so that local communities and businesses can enjoy the benefits of EWR sooner. East West Rail will give people living between Oxford and Cambridge better access to jobs, education and improved healthcare, as well as to their family and friends and leisure – the things that matter in our daily lives.
‘These accelerated works demonstrate Government’s ongoing commitment to the
full EWR route and will allow us to progress with further work, including securing Government approval, to deliver the full Oxford to Cambridge service in parallel.’
Business leaders’ backing for the fasttracking of works along the MVL comes after the final section of track was laid on the first stage of EWR between Bicester and Bletchley, which was marked with a ceremony last week.
6 February 2024 saw Deloitte hosting the Women in Rail London Region as they offered their members the opportunity to attend a self-development masterclass and networking session
Over 140 Women in Rail London members from across the industry participated in Sylvia Baldock’s Empower Yourself to Become More Significant workshop – the key message: if you put the work in to becoming significant, success will follow.
But what does becoming significant mean and how can you achieve it? Sylvia took her audience through a roadmap to success, signposted with small changes you can make to your daily life to level up and feel more empowered. And it starts, she says, with continually reminding yourself that what you do matters.
Additional key takeaways include:
• Work in ‘flow’ by making sure that you’re playing to your strengths and not spending the majority of your time struggling to progress meaningfully.
• Realise what you want your personal brand to look like. What impressions or impact do you want to have on others?
• Who you’re constantly interacting with has an impact on your wellbeing. Ask yourself, are you surrounded by ‘radiators’ or ‘drains’?
Sylvia also talked about physical actions that can improve your wellbeing and performance, emphasising the importance of ‘eating the rainbow’ and getting good
quality sleep. She had the audience up on their feet several times throughout the masterclass, advocating for regular movement and showing some examples of stretches and exercises that can be done between long periods of working at a desk.
The audience was engaged throughout and participated fully with the interactive elements, often with a chorus of giggles and jokes which contributed to the wholesome and supportive feel in the theatre. These were members who valued the guidance and wanted to also share their experiences and knowledge to bolster everyone in the room.
Deloitte had kindly provided a generous spread of food and drink for members to enjoy whilst they took full advantage of the opportunity to widen their network and engage in discussions with people in a broad variety of roles and companies from across the industry. A key element of Women in Rail’s purpose to improve diversity in the UK Rail industry is achieved through important initiatives such as influencing change in stakeholder strategies, promoting industry collaboration, and sharing of best practise. A secondary benefit, and arguably one of the most beneficial impacts Women in Rail has on its individual members, is the ability to assist them in fostering a diverse, inclusive, and supportive networking platform.
Women in Rail has eight regional committees to hold events like this for
their members to connect with like-minded people in their locality. Last year 43 regional events were held across the UK for regional members to benefit from, and several have already been advertised for 2024. The London regional committee were delighted to see so many people attend for their first event of 2024 and recognise the value people gain from a variety of events.
Post-Covid, WR membership nationally and within regions has increased, as industry colleagues look to expand their network and enhance their abilities and knowledge through talks, panels and visits that cover a breadth of relevant topics and themes. Upcoming event details for all regions can be found on the Women in Rail website and on their social media platforms.
Women in Rail London members who attended the event on 6 February shared their appreciation through a number of comments, highlighting how worthwhile members find regional events – a selection of which are below:
• ‘Sylvia was fabulous, sharing so many great insights! The energy in the room was so high; probably one of the best WR events I have attended. Thank you to the London WR team’.
• ‘Great event – very uplifting. It was great to be reminded of all the ways we already have the power to be our best selves!’
• ‘Thank you for a lovely evening of gaining knowledge and networking.’
As Co-Chair of the Women in Rail London Region, on behalf of my co-chair, our committee, and our members I would like to take this opportunity to thank Sylvia Baldock for her inspirational workshop, Mary Hewitt at Deloitte for hosting us so generously and Sam Lane for her wonderful photography to capture the event.
As we move through 2024 it is worthwhile reflecting on the message that Syliva ended her workshop with. A reminder to focus on being totally present and to fully listen rather than merely listening to respond. And don’t wait for this vague notion of a future Utopia or spend all of your time racing down life’s corridor – breathe, enjoy the now and harness your power to become the best version of yourself.
Sarah Booth is Senior Manager of Fatigue Risk Management. A specialist in human performance, Sarah has worked with operators to develop and implement Fatigue Risk Management Systems (FRMS) across multiple regulatory environments and provides scientific support to Regulators assessing FRM submissions and scientific safety cases.
Dr Cristina Ruscitto is a Senior Researcher in the Fatigue Risk Management Team, specialising in the psycho-behavioural predictors of fatigue through the development of fatigue surveys and survey analysis, development of fatigue investigation process, and review and recommendations of procedures.
In its Annual Report on the Health and Safety on Britain’s Railways, published in July 2023, the ORR (Office of Rail and Road), highlighted that fatigue management remains a focus area for continued review and improvement
Recent investigations by the RAIB which find discrepancies in operators’ Fatigue Risk Management Systems (FRMS) also support that there are improvements to be made within the industry. This article provides a view on how those within the UK Heavy and Light Rail industry can act to improve the effectiveness of their FRMS, based on our years of experience supporting operators implementing FRMS.
The ORR defines fatigue as ‘a state of perceived weariness that can result from prolonged working, heavy workload, insufficient rest and inadequate sleep’, reducing the ability of an individual to work safely and effectively. Whilst some effects of fatigue may appear obvious, such as unintentionally falling asleep, workers can be unaware of how much their performance is being adversely affected by fatigue, including any lapses in attention or microsleeps (brief periods of unintentional sleep). This means the risks associated with fatigue must be managed systematically,
rather than only relying on individuals to act when they experience elevated fatigue levels. Managing fatigue effectively also provides business benefit. Workers who are too fatigued to work safely may report sick rather than as being fatigued, meaning that not only is that worker lost to the business for the day, but also no data is collected on the causes of that fatigue. This data could inform strategies to reduce fatigue and therefore the likelihood of that individual – or others in a similar circumstance – being too fatigued to work safely in the future. Training is a significant cost across multiple industries, and the rail sector is no exception. Evidence clearly shows that fatigued individuals pick up skills more slowly and are worse at retaining information. This increases training durations and associated costs. In many organisations, elevated fatigue is also associated with inefficiency – reducing fatigue levels can increase roster efficiency and effectiveness.
The regulatory requirement to manage the fatigue of the workforce in the UK
Baines Simmons helps to advance best practice, shape safety thinking and drive continuous improvement to safety performance through its consulting, training and managed services. Baines Simmons experts are dedicated to improving safety across aviation, rail and other sectors, taking a practical approach to guide, influence and improve the safety and performance of a range of organisations. Baines Simmons is part of Air Partner Group, a Wheels Up company.
www.bainessimmons.com
Rail sector is long-standing. It is outlined under Regulation 25 of the Railways and Other Guided Transport Systems (Safety) Regulations (ROGS, 2006). In 2012, the ORR best practice guidance for fatigue risk management was published in Managing Rail Staff Fatigue, alongside a call for Fatigue Risk Management Systems (FRMS) to be part of the wider Safety Management System in organisations with safety critical workers, and/or where the risks of fatigue are higher due to shift work or long working hours.
Fatigue Risk Management Systems are an evolution and specialism of Safety Management Systems. This systematic application includes multiple levels of controls, and recognises that limiting hours of work in isolation is insufficient to manage the risk of fatigue. For example, prescriptive limitations which outline minimum rest periods between work periods do not guarantee sufficient sleep – factors such as commuting and the time of day the rest period is taken are usually not considered, but can have a big impact on sleep duration.
A comprehensive data-driven FRMS manages risk holistically and is embedded in the culture of an organization. An effective FRMS will ensure the best safety outcomes, protect the long-term health and wellbeing of staff, and reduce the risk of reputational damage and potential associated costs to an organisation. However, to reach this effective position requires ongoing effort from the organisation, and buy-in across all levels, from senior leadership through to all members of the workforce.
Key components of FRMS should include:
• Using a data driven approach to identify, mitigate and manage fatigue risks, which include multiple sources of data to capture the complete fatigue ‘picture’.
• Ensuring competence across the workforce, both for those who may
experience fatigue, and those who may influence the fatigue of others.
• A shared responsibility for managing fatigue between the organisation and individual workers.
To effectively implement an FRMS, ORR recommends a POPMAR approach:
• Policy.
• Organising (i.e. developing your organisation, identifying roles and functions).
• Planning and Implementing (Where are you now? How do you get to where you want to be? Training all appropriate members of the workforce, comparing working patterns to the fatigue factors).
• Measuring Performance (measuring fatigue in actual operations, fatigue reporting, use of fatigue models, fatigue surveys and incident investigation).
• Auditing and Reviewing Performance (Key Performance Indicators, internal and external audits for compliance and effectiveness, feeding back to FRMS improvements).
Ensuring that all these elements are in place is key to ensuring an effective FRMS. The final step (Auditing and Reviewing Performance) should inform you where there are gaps – as does learning from others within the industry.
Whilst FRMS is a regulatory requirement under the ROGS, it is not uniformly and effectively applied throughout the industry. In an accident report published in 2022, the Rail Accident Investigation Branch (RAIB) noted that a review of the operator’s FRMS found it did not follow current industry guidance and good practice, resulting in a recommendation being made by the RAIB to the operator regarding its FRMS.
The operator was utilising the HSE Fatigue and Risk Index (HSE:FRI), a biomathematical model designed to predict fatigue levels according to work shifts, sleep opportunities and circadian factors that is used widely across the industry. However, the model was used in isolation as a means of identifying fatigue associated with working patterns.
Best practice recommends that multiple means of identifying fatiguing patterns are used, including comparing working patterns against the ORR ‘fatigue factors’ i.e. time of day, duty length, intervals between duties, recovery time, cumulative fatigue, and circadian phase shift factors. Without using all these elements, it is not possible to demonstrate that fatigue is being effectively identified and managed, in accordance with the requirements of Regulation 25 of the ROGS.
A broad assessment of your FRMS, looking at the components and effectiveness of the FRMS can highlight any gaps or weaknesses. Baines Simmons has undertaken assessments – called Fatigue Risk Management Diagnostics – for operators within both heavy and light
‘In many organisations, elevated fatigue is also associated with inefficiency – reducing fatigue levels can increase roster efficiency and effectiveness.’
rail, allowing the organisations to meet their regulatory obligations, manage risk effectively, and gain operational benefits from effectively managing fatigue risk.
Bio-mathematical fatigue models are used widely in the rail industry. They are useful for predicting fatigue levels and ‘hotspots’ where high levels of fatigue are likely, supporting fatigue risk management when used alongside other tools. These software tools usually calculate average fatigue levels, and need to be used with a clear understanding of what the results do and do not consider (for example most models do not consider workload effectively), and what ‘threshold’ values mean.
Understanding and identifying appropriate thresholds is a key decision for those managing the FRMS, and must be appropriate to different workgroups, according to their role and working patterns. For example, in the HSE:FRI, the fatigue scores range from 0-100, with a Fatigue Index Score of 50 representing a 50 per cent chance of employees achieving a Karolinska Sleepiness Scale (KSS) score of eight or nine.
In the KSS a score of one reflects being extremely alert whilst scores of eight or nine reflect high levels of sleepiness, where microsleeps are highly likely. Research by the Health and Safety Laboratory (HSL) and the ORR found that the majority of working patterns in the rail sector produced HSE:FRI fatigue scores of 30-35 for day shifts and 40-45 for night shifts – and these values have subsequently been used as ‘thresholds’ by many within the rail industry. However, the report did not aim to identify safe thresholds. Rather, individual TOCs should identify the level of fatigue risk that they are willing to accept in their own operation and manage this risk through their FRMS. The identified thresholds, and subsequent use of the model should reflect that operators should control fatigue risk to As Low As Reasonably Practicable (ALARP) – always seeking to reduce the risk, unless the means of further mitigation are grossly disproportionate.
Even where the working pattern has been designed to reduce fatigue risks as far as possible, disruptions, overtime, elevated workload, or personal difficulties of the worker can still result in elevated fatigue
on the day. This is where another critical barrier comes in – the ability of a worker to remove themselves from work due to fatigue, supported by fatigue reporting. Another RAIB report, published in 2023 found there were no effective channels for safety critical workers to express if they are experiencing high levels of fatigue or to declare themselves unfit for duty. For fatigue reporting to work as an effective part of the FRMS, many elements must be in place:
• Workers are competent to recognise when they are no longer fit to operate safely, and know what steps to take to reduce risk.
• Company culture means that declaring yourself unfit due to fatigue is welcomed as a positive safety action. Or are there fears of negative consequences?
• Other policies do not conflict with removing oneself from duty due to fatigue, such as absence management, or communications regarding avoidance of delays.
• The organisation monitoring instances of fatigue to identify common themes, and acting to reduce them where possible.
When the FRMS is working effectively, not only can you identify new contributors to fatigue, but also measure the effectiveness of mitigations, and identify where fatigue may have played a role in incidents or nearmisses. Using the mitigations and planning rosters with the intent to reduce fatigue can also support reducing absences, alongside the associated reduction in risk. For example, through an effective FRMS, fatigue reporting and near-miss data may indicate that there is elevated fatigue on consecutive early shifts, or at the end of night shifts, despite planning according to the fatigue factors, and using the HSE:FRI.
Mitigations then need to be implemented to reduce the risk, such as adjusting the shift pattern, shortening shifts, or adding breaks to ensure fatigue risk is controlled to an As Low As Reasonably Practicable (ALARP) position. However, if the reports or incidents are from a small number of individuals, mitigations may also be applied at an individual level – such as providing support or discussing alternative shift patterns. No matter the origin of the reported fatigue, feedback and ongoing monitoring of the controls put in place are essential, and form part of the Auditing and Reviewing element of the FRMS.
Operating Companies in both Heavy and Light Rail in the UK have used FRMS principles for many years, given how long the requirement to manage fatigue has been in place. However, there is still further work to do to ensure that the FRMS is effective, that fatigue is truly being managed, and the companies and the workforce can reap the benefits of effectively managed fatigue. Both the ORR and the RAIB are calling for improvements to be made – as an operator, are you comfortable with your current approaches?
STAUFF are a premier global manufacturer of components and kits for railway applications.
A comprehensive range of quality products and innovative services delivered to your production line side for the manufacture of rolling stock.
Presented in kit form, tested and ready for immediate installation, reducing logistic, production and inventory costs.
The STAUFF Line process is adopted by global OEMs to successfully achieve cost savings in rolling stock manufacture.
www.stauff.co.uk
Sheffield Tel: 0114 251 8518
Email: uk.sales@stauff.com
Aberdeen Tel: 01224 786166
Email: uk.absales@stauff.com
Ireland Tel: 02892 606900
Email: uk.irsales@stauff.com
Phil Pavey, Managing Director at Algeco Offsite, takes a look at how rail operators that adopt a modular building approach can access opportunities that go beyond simply charging points
Electric vehicles (EVs) are gaining popularity as a sustainable mode of transportation, and the need for convenient charging infrastructure is crucial to support their widespread adoption. Network Rail has taken a significant step forward by installing new EV charging points at many railway station car parks. It is an initiative that aims to encourage more use of EVs and promote cleaner air quality in and around stations. The initiative is part of a wider Environmental Sustainability Strategy, with Network Rail working towards delivering a low-emission railway and aiming to reach net-zero emissions by 2045 in Scotland and by 2050 in the rest of Britain.
By providing affordable, efficient and reliable charging points, it is hoped that it will encourage more EVs on the road and contribute to lower carbon end to end journeys. The initial phase of installations by Network Rail include charging points in Reading, Manchester, Edinburgh, Leeds, and Welwyn Garden City. These locations have been strategically chosen to cover a wide geographic area and cater to the needs of passengers in different regions.
Many of these charging points are powered by renewable energy, ensuring that the electricity used to charge EVs comes from sustainable sources.
The advantages of modular buildings
This is a similar approach that Gridserve is taking with its motorway network electric vehicle charging stations, which also allow customers to shop and eat at brands including M&S Food, Costa and WHSmith, along with offering rentable office pods. These are opportunities that might resonate with railway operators looking for ways to enhance the passenger experience and attract new customers to the network.
To meet the growing demand for EV charging infrastructure on the UK’s transport networks, we are supplying a two-storey modular forecourt building to the Gridserve development in Stevenage. Thise charging point with retail and office facilities has a relatively small footprint.
It offers customers charging technology powered by one hundred per cent renewable energy, creating a sustainable and, with retail outlets and rentable office space, an enjoyable and productive charging experience.
Available as single or multiple storey formats, the retail modules are manufactured at our factory in east Yorkshire using an innovative platform design solution. This offers sustainability benefits, lower embodied carbon, and faster construction times compared to traditional on-site builds and even conventional offsite systems.
Modular buildings offer several advantages that make them ideal for EV charging infrastructure at any transport hub including railway stations. They are manufactured off-site, allowing for efficient production and quality control. This provides a rapid and safe deployment on site with minimal disruption to commuters.
The modules also provide flexibility in design and layout, accommodating the unique needs of EV charging infrastructure. This flexibility allows for the integration of additional facilities such as retail spaces, food outlets, and office pods, enhancing the overall experience for railway users.
We’ve seen an increase in demand for these types of modular building solutions recently, and it’s one of the reasons why we will be showcased them at the UK Infrastructure Show (UKIS) at The NEC on 12 March.
The installation of EV charging points at railway stations has a positive impact on both commuters and the environment. Commuters who rely on EVs for their daily travel can conveniently charge their vehicles while they take the train, eliminating the need for separate charging stops and saving time. This seamless integration of charging infrastructure at railway stations encourages more people to consider EVs as a practical and sustainable transportation option. Combining this with retail and rentable office space can even attract new rail users.
From an environmental perspective, the use of renewable energy to power the charging points significantly reduces the carbon footprint and contributes to the reduction of greenhouse gas emissions. This helps improve air quality, and mitigate the effects of climate change. Network Rail's commitment to a low-emission railway extends beyond the current phase of EV charging point installation. The
organisation plans to install charging points across ten per cent of car parking spaces at its managed car parks. This ambitious target demonstrates its dedication to providing widespread access to EV charging infrastructure and further supporting the transition to sustainable mobility.
Modular and offsite can be an essential part of delivering this infrastructure to the high quality expected, avoiding disruption to passengers. The fact that retail spaces and short term office rental – space permitting – provide an additional income add to its appeal. In addition, a modular approach enables efficient and scalable expansion of EV charging points, ensuring that charging infrastructure keeps pace with the increasing demand for EVs.
The successful implementation of EV charging points at railway stations sets a positive example for other transportation sectors. It highlights the importance of investing in sustainable infrastructure and promoting convenient transportation options for the benefit of both commuters and the environment.
The provision of affordable, efficient, and reliable charging infrastructure encourages the adoption of EVs and contributes to lowemission end-to-end journey. By leveraging modular building solutions and taking learnings from the motorway network, the expansion of EV charging points at railway stations becomes more efficient and flexible, meeting the evolving needs of EV users.
The expansion of EV charging infrastructure in the UK is a critical step towards achieving a more sustainable transportation system. By overcoming the challenges using modular construction and implementing strategic solutions, cities and governments can pave the way for low carbon journeys.
The benefits of electric vehicles, including reduced emissions, cost savings, and enhanced driving experiences, make them an attractive choice for individuals and society as a whole. With continued investments, collaborations, and policy support, the UK is on track to build a comprehensive and robust EV charging network, ensuring a seamless transition to a cleaner and more connected future.
Algeco will be exhibiting at the UK Infrastructure Show (UKIS) on 12 March at Birmingham, NEC Stand 20. To find out more about Algeco permanent modular buildings, visit: www.algeco.co.uk/permanent/ permanent-modular-retail-and-restaurantbuildings.
There is no doubt that the rail industry is facing a challenging time as it pivots to net zero goals, all while meeting soaring demand in the now and remaining primed for future growth,
Ciaran Cotter, Technical Director at Solivus discusses
In infrastructure, this will see an accelerated shift towards not just sustainable construction materials and processes but significant innovation leaps and novel new ways of thinking. One great example can be found in a new partnership between Solivus and one of the world’s biggest infrastructure names which is set to create a new blueprint for securing sustainable off-grid power supply.
It is widely established that large-scale electrification is needed to replace diesel trains and decarbonise the UK’s rail network. Electrical traction is, after all, not only an environmentally friendly, pollution-free and energy efficient mode of transport but it can be powered by renewable energy sources.
But while the case for rail electrification may be a net zero imperative, it’s equally important that the sector does not overlook the opportunity to lead the way in other opportunities to self-generate and negate diesel reliance.
Take, for example, diesel generators. Traditionally, large-scale rail construction has relied on diesel generators to provide the reliable off-grid power needed to support rail renewal work. However, while their advantages in terms of power,
performance and portability cannot be argued, they do come with some major environmental drawbacks.
Thus, in light of government policies and regulations on greenhouse gas emissions and the underpinnings of the Paris Agreement, it was clearly only a matter of time before diesel generator use come under closer scrutiny.
Of course, this was seen in April 2022 when it became illegal to use to use red diesel in cranes, bulldozers, or for powering mobile generators on construction sites. Then last year we saw the Construction Leadership Council set out plans for the industry’s best-performing contractors to ban the use of diesel generators on sites by 2025.
Clearly then, the days of diesel generators are numbered – but what’s the alternative?
At one point, it might have appeared that there is no obvious, cost-effective solution which can scale to deliver the same level of reliability and performance as a diesel generator. Yes, there have long been renewable options, but they have traditionally been costly, and installation and maintenance has been expensive. In addition, when it comes to solar, a major prohibitive has been the associated weight of standard rigid panels, making them unviable for the temporary structures, such as cabins, used on construction sites.
However, the good news is that there is now a much more flexible, cost-effective and high-performance alternative.
Thanks to advances in technology, the latest generation of innovative lightweight solar panels are a fraction of the weight of conventional panels and have more universal applications for fixing methods which have opened up new roof space opportunities.
Big benefits
A great example of this opportunity can be found in Solivus’ recent work with one of the world’s biggest infrastructure names. Hereby, the challenge was to create a solarfuelled alternative to the diesel generators currently used to power our client’s construction site cabins portfolio.
To achieve this, Solivus created an innovative, low carbon set up which combines lightweight solar panels with a battery storage system and a backup diesel generator. An off-grid, decentralised, selfsufficient energy hub. The system works by storing the excess energy generated by the solar panels in a connected battery storage unit. As a result, site cabins can be powered continuously, with the system automatically releasing the reserve energy even when there is no sunlight.
The recent pilot project – a modular building with a roof space of approximately 100m2 – is estimated to have saved our
client up to 14,416kg of carbon dioxide emissions, 5,223 litres of diesel with a gross annual saving of £9,140, while ensuring a reliable, resilient, clean energy supply. This is a solution they now plan to roll out to their clients.
Underscoring this too is a dedicated operations and maintenance (O&M) programme designed to ensure the project continues to reach its full value potential. This is supported with a fiveyear workmanship warranty, a twelve-year product warranty and a twenty-five-year performance warranty.
The result is a clear indication of the gains to be had by transitioning to clean, carbon-free off-grid working, especially as Network Rail works towards its target to reduce non-traction energy consumption by almost 20 per cent and carbon emissions by 25 per cent by 2024.
While we continue to see the rapid acceleration of rail electrification investment, it’s vital that operators do not overlook the opportunity to dercarbonise its approach to temporary off-grid power supply. For progressive rail operators, the recommendation is to seize the solar- opportunity now in order to reduce
AARC Professional Services Limited draws from over five decades of experience to provide expert support to the industry.
We are a railway consultancy bringing together likeminded rail professionals with a common aim to deliver outstanding outcomes by..
• Helping clients achieve their goals...
• Through strategic and technical expert advice...
• Across a range of disciplines...
• From the frontline through to the boardroom
Whether you’re looking for high level advice & guidance or direct project support, we’re here to help you deliver excellent outcomes.
emissions, improve reliability and efficiency and, in turn, make even greater headway in their own sustainable journey.
Solivus is on a mission to decarbonise the built environment by making it as easy as possible for commercial buildings and homeowners to self-generate their own clean energy and save money with its ultrathin and lightweight solar solutions.
On the commercial side, Solivus overcomes weight issues with its innovative ‘skin like’ lightweight solar solutions. This includes large commercial buildings, such as warehouses, hangars, stadiums and large offices, with it estimated that 40 per cent of buildings cannot take the weight of conventional solar.
For homeowners, the Solivus Arc is a designer solar sculpture for the home, designed to overcome the aesthetical challenges associated with traditional solar panels. Solivus is a winner of the Department for International Trade’s Green Builder of Tomorrow Prize 2022, is Tech Nation 2.0 Alumni, and has been voted one of J.P. Morgan’s Top 200 Female Powered Businesses. Solivus is the energy behind lightweight solar. For further information please visit: www.solivus.com
The recent launch of TRIA was another milestone moment for National Infrastructure Solutions (NIS) in its bid to rewrite the rail sector’s training handbook. NIS Founder Davie Carns explains
hen we launched National Infrastructure Solutions (NIS) five years ago we made the conscious decision to reverse the training ecosystem and positively disrupt the status quo. Rather than deliver a standard suite of courses, some of which may have been useful, we switched our focus to the full range of jobs that key employers had available. Once we understood the needs of the employer, this enabled us to create learning journeys to get people to the relevant skill levels to support their employment aspirations.
It wasn’t ‘rocket science’, more a case of matching supply and demand. Most importantly, we wanted to make sure that no one was left behind. This meant tailoring our training courses so they would be suitable for the unemployed, people battling mental health issues, career transitioners or return to work parents, as well as supporting the complex training requirements of former forces veterans and ex-offenders.
Fast forward five years and it’s a formula that has delivered phenomenal achievements, not least the Rail Training Centre developed in partnership with the City of Wolverhampton College (CoWC) and that 85 per cent of our learners are now in sustainable employment – this number is significantly higher than the national average.
Tellingly, we have embedded a similar approach into the launch of our latest venture with CoWC, the Transport, Rail and Infrastructure Academy (TRIA), which will give individuals the entry level skills in addition to the advanced qualifications required to work in the construction and maintenance of the railway, tram routes and wider infrastructure sectors.
The initiative, which has received £1.1 million of West Midlands Combined Authority (WMCA) funding to bring it to life, will create 432 training places at its first site at Black Country Innovative Manufacturing Organisation (BCIMO)'s Very Light Rail National Innovation Centre in Dudley.
This location boasts more than 2,000 metres of conventional rail track, including two split-level platforms, an 870-metre tunnel and signalling components which give students hands-on training in multiple disciplines across the industry. All schemes are designed to enhance the learning
experience of students by working with the same equipment that is used across the rail infrastructure.
Encouragingly, this latest development has also seen us leverage considerable investment from the private sector as employers rush to back our shared training model, with the new Black Country Signalling Academy highlighting even further how training courses are being developed to meet real needs within the industry.
The high-profile TRIA launch event attracted sizeable interest from the rail and infrastructure sector, with the focus centring around what this means for Dudley and local people. That is only natural considering the location of the event and the fact there are bricks and mortar in place that is going to be home to hundreds of leaners. There is a bigger picture, however.
Transport, Rail and Infrastructure Academy is more than just the one facility, it is an umbrella brand the gives us the ability to set-up multiple sites all over the region. Growing the partnership with the City of Wolverhampton College means we will continue to innovate and enhance the training experience for residents across the West Midlands.
Our next two sites are currently being developed in Aston and Coventry, whilst contracts are now being awarded in the East Midlands and Wales. In short, what we’ve collectively created in Wolverhampton and the wider Black Country, is now in demand and recognised as a ‘go to solution’ to meet the skills gap that industry is facing.
Speaking at the launch event, Mayor of the West Midlands Andy Street said: ‘Hundreds of millions of pounds are being invested right now into the region’s train and tram network, with new rail lines and stations being built and new Metro routes under construction.
‘That’s great news for the travelling public but we also need to make sure this unprecedented investment benefits local people in terms of new jobs and careers.’
That’s where NIS come firmly into play, whether it is entry level courses and mentoring to support individuals onto the first rung of the rail, transport, and infrastructure ladder or whether it’s technical training that enhances earning potential while giving industry highly skilled individuals.
Put simply, if we can continue to develop employees then we know we have the pipeline to backfill those positions and the cycle can begin all over again.
Regardless of where you fit in this roadmap, you can access wraparound and mentoring support that builds confidence and breaks down barriers to sustainable employment.
Like I said at the start, it’s not rocket science, but we believe we have found a training blueprint that works for the rail and transport sectors both at home in the Midlands and further afield.
Buy why stop there? With a bit of tweaking our approach could also be just as successful for other industries where the skills and recruitment gaps are widening by the day.
Tel: 01902 973473
Email: contact@nisgroup.co.uk
Visit: www.nisgroup.co.uk
KEY ACCOUNT MANAGER –CONTRACTORS AT POLYPIPE CIVILS & GREEN
Lee Woodcock is Polypipe Civils & Green Urbanisation’s Key Account Manager for Contractors. Having been at Polypipe CGU for a decade, Lee brings a wealth of experience to the team. He covers a range of sectors within his role –including the rail industry.
LEE WOODCOCKTell us about Polypipe Civils & Green Urbanisation.
With a robust manufacturing operation and facilities strategically located across the UK, we operate at a substantial scale, ensuring high-quality production while minimising environmental impact and carbon emissions. We are dedicated to the circular economy, shown through our innovative use of recycled materials and our advanced polymer processing plant, which transforms plastic waste into useable materials on-site.
Our USP lies in our commitment to sustainability, innovation and efficiency. Unlike many of our competitors, we prioritise the use of one hundred per cent recycled materials in our products, reducing environmental impact and supporting the circular economy.
Manufacturing in the UK using recycled materials and through processes that are powered by renewable energy sources means that we can divert waste from landfill and reduce the demand for virgin resources, and this also significantly reduces carbon emissions in transportation. Our products are designed for quick, easy and safe installation so, paired with our focus on innovation and collaboration, we’re able to offer holistic solutions that meet stringent quality and environmental standards, providing organisations with sustainable options to reduce their carbon footprint and promote greener construction practices.
What types of products and services do you offer?
We offer an extensive range of products and services that are tailored to meet the needs of the construction and infrastructure sectors, including the rail industry. Our comprehensive offering includes modular access chambers like SubTerra, cable protection systems such as Ridgiduct, and surface drainage solutions like Ridgidrain.
We also provide geocellular systems like Polystorm and Permavoid for water retention, attenuation and infiltration and, just like the rest of our product range, these are all designed for easy installation, high performance and sustainability – once again aligning with our commitment to environmental responsibility and efficiency in construction projects. Our services also encompass support for innovation, collaboration and compliance, ensuring our clients receive the best solutions for their railway infrastructure needs.
How passionate are you about sustainability in the rail sector, and how do you go about sourcing the materials for your products?
To put it simply, sustainability is at the core of what we do – and this is especially true
for our work in the rail sector. We’re incredibly passionate about reducing environmental impact and promoting greener practices in railway construction and infrastructure projects.
We source our materials responsibly, with our sourcing strategy revolving around utilising recycled plastics through initiatives like our ‘Wash & Squash’ plastic collection scheme, which encourages people to bring their end-of-use household HDPE waste to be recycled within our advanced polymer processing plant at our Horncastle site.
By transforming plastic waste into high-quality usable materials on site, we’re able to ensure that our products not only meet but exceed industry standards for sustainability, but our commitment to sustainability isn’t just related to sourcing materials – we also focus on local manufacturing and supply chain and power our manufacturing operations with one hundred per cent renewable energy, further reducing our carbon footprint.
What do you have planned for the year ahead?
We’re also actively engaged in initiatives like the circular economy concept. Our commitment to innovation and collaboration is what drives us to continuously improve and develop greener solutions for the rail industry, and our green strategy as a whole encompasses a holistic approach to sustainability, ensuring that our products and practices contribute to a greener, more sustainable future for the rail industry.
It’s a busy time for Polypipe CGU, and we have lots planned for the year ahead. For one, we’re very much focused on advancing our sustainable solutions for railway construction and infrastructure projects. We want to expand both our product offerings and our presence in the sector by obtaining additional PADS approvals for our existing products – particularly our SubTerra range for trackside cable management. We’re also aiming to strengthen our relationships with industry stakeholders, like Network Rail, to promote innovation and collaboration and set new benchmarks for sustainable solutions in the industry through continued investment into research and development to keep enhancing the environmental characteristics and performance of our product.
Do you think the rail industry could be greener and what is your organisation’s green strategy?
Absolutely. The rail industry has great potential to become greener and we at Polypipe CGU are committed to driving this through.
We believe that, by prioritising sustainability in every aspect, we can minimise the environmental impact, reduce carbon emissions and promote greener practices. Our green strategy revolves around several key pillars – these include those previously mentioned: our use of 100% recycled materials within our products, manufacturing locally to reduce carbon miles, and using renewable energy sources to power our production plants.
What are your views on collaborative working?
We’re firm believers in the power of collaborative working to drive positive change and innovation. It allows us to leverage diverse expertise, resources and perspectives to address complex challenges and deliver optimal solutions.
Collaboration enhances transparency, communication and trust, which ultimately ensures that projects are completely efficiently, on time and within budget. In fact, we believe that collaborative working is essential for driving the change we want to see and achieving sustainable outcomes in the industry. At Polypipe CGU, we are committed to developing and nurturing strong partnerships that foster creativity, accelerate progress and deliver maximum value to both our clients and the wider community – all at the same time as ensuring that our solutions meet the evolving needs of the rail industry.
At some point, every company will face the question of how to continue maximising earnings from their current business practice whilst also investing enough in innovation so they can turn a profit in the future. How can a company achieve the necessary creativity to innovate without compromising their existing business?
It requires a strategic and balanced approach, balancing short-term goals with long-term vision. Companies can foster creativity by encouraging a culture of continuous learning and experimentation, empowering
employees to explore new ideas and technologies. We do exactly that here at Polypipe – investing in research and development, staying abreast of industry trends and emerging technologies, and encouraging cross-functional collaboration both internally and with external partners to bring fresh perspective and insight.
We know it’s essential that we maintain a clear vision and strategic direction while remaining adaptable to market trends and customer feedback but, through continuously challenging the status quo and embracing a growth mindset, there’s a great chance to identify new opportunities for innovation, while still ensuring the sustainability and success of our existing operations.
On the whole, achieving creativity and innovation requires a strategic mindset, a supportive culture and a willingness to embrace change – all of which have been, and continue to be, integral to our success at Polypipe.
Part of the Genuit Group, Polypipe Civils & Green Urbanisation is a UKbased manufacturer at the forefront of sustainable infrastructure. We are committed to delivering products and services that prioritise sustainability, efficiency and safety, and our comprehensive product range includes innovative solutions for railway construction, emphasising sustainability and ease of installation.
Want to know more about Polypipe Civils & Green Urbanisation?
Tel: 01509 615100
Email: civilsenquiries@polypipe.com
Visit: www.polypipe.com/civils
In his role as Technical Director at Pandrol from 2018 to 2023, Jacob led global R&D and engineering in the equipment division. Managing teams across Sweden, China, USA, and France, he coordinated global R&D efforts, improving efficiency and market share through innovative technologies. Previously, as the Technical Manager at Rosenqvist Rail AB, Jacob oversaw the engineering department, served as a Customer Project Manager, and spearheaded the development of numerous products.
Rosenqvist Rail develops, manufactures, and sells equipment to streamline the construction and maintenance of railways. Its range includes machines for rail fastening, handling and replacement of sleepers, and rail trailers for transporting equipment and materials. Since its establishment in 1994, it has delivered machines for railway projects worldwide. In 2008, the company was acquired by Pandrol, becoming part of their offerings.
Want to know more about Rosenqvist Rail?
Tel: +46 650 16505
Email: info@rosenqvistrail.se
Visit: www.rosenqvistrail.se
How did you get started in the industry?
I was initially hired at the age of 27 as a relatively inexperienced mechanical engineer for a small, almost garage-like business known as Rosenqvist Rail in Hudiksvall, Sweden. It proved to be the most thrilling and dynamic work environment I had ever encountered, and I flourished in it. Being a member of this ambitious and entrepreneurially driven company, dedicated to mechanizing processes in railway track maintenance and construction, allowed me to share my enthusiasm with fellow employees throughout the organization.
What is your role within Rosenqvist Rail?
I am thrilled to step into the role of Managing Director for our esteemed company as of January this year. This opportunity excites me profoundly as it signifies a new chapter filled with growth, innovation, and collaborative success. I am eager to lead our talented team, leveraging their skills to drive the company to new heights. The prospect of implementing strategic initiatives, fostering a culture of excellence, and steering the organization towards greater achievements fills me with anticipation. Together, we will navigate challenges, explore new opportunities, and reinforce our commitment to delivering unparalleled value. I am ready to embark on this exciting journey, confident in our collective potential for success.
What was the inspiration behind starting Rosenqvist Rail?
Mr. Anders Rosenqvist, the founder, commenced his career by establishing a contracting company in 1985, dedicated to performing maintenance work for the Swedish railways. Over the ensuing nine years, he diligently developed and expanded this enterprise. As the company flourished, plans crystallized for the inception of a new venture. This envisioned entity would
focus on transforming ideas, concepts, and prototypes, previously cultivated within the contracting company, into commercial products. This strategic move was born out of the necessity to address the dearth of efficient equipment hindering productivity. The aspiration was to harness innovation and elevate productivity through the development and commercialization of cutting-edge products.
How long has your company been in business?
Established in 1994, the company is commemorating its 30th anniversary in 2024, signifying a momentous milestone. While this year holds historical significance for various reasons, let's rewind to understand the journey. The company swiftly encountered the innovative rail fastening system, Pandrol Fastclip, when its sister company, Rosenqvist Entreprenad, engaged in destressing work in Norway. The need for more efficient machines to unfasten and fasten rails led to the inception of the legendary ‘Clip Driver 400’ commonly known as the CD400 clipping machine—a cornerstone in our product portfolio. The CD400 was the pioneering machine capable of seamlessly clipping or unclipping Fastclips while traveling down the track, swiftly becoming the industry benchmark for contractors seeking to streamline track possessions and eliminate manual handling.
Throughout the '90s, the company diversified its portfolio with numerous products revolving around excavator attachments, all designed for track maintenance tasks. This expansion also involved converting excavators into Road Rail vehicles, fostering the growth of an efficient ecosystem of carrier machines with accompanying tools. This approach quickly became the preferred alternative for many track maintenance tasks, particularly in Scandinavia.
Tell us about Rosenqvist Rail.
The company undertook numerous intriguing projects and emerged as a significant player with a growing portfolio of clipping machines around the early part of the millennium. In 2008, Pandrol International, owned by the Delachaux group, expressed interest in acquiring the company to implement a system approach to the market, combining its successful rail fastening system, Fastclip, with Rosenqvist clipping machines.
This synergy proved highly effective, enabling destressing operations to be completed in an unparalleled short amount of time. A noteworthy milestone
was achieved in 2011 through close collaboration between Pandrol’s equipment experts and Rosenqvist Rail, resulting in the CD200, now succeeded by the CD200 IQ model. These models have become the preferred choice for many customers due to their robustness, high capacity, and unique sleeper lifter functionality.
In 2018, the company was rebranded as Pandrol AB when the Delachaux group decided to unify all their railway-related companies under the Pandrol name. Concurrently, the engineering department was established as the "Center of Engineering Excellence" for the Equipment & Control product line in Pandrol. This department serves as an R&D centre for
most track equipment within the group, and I was honoured to be appointed as the Technical Director, leading this newly created unit.
What types of products and services do you offer?
In addition to our status as industry leaders in clipping machines, we provide distinctive solutions for sleeper replacement, sleeper laying, rail handling, rail trailers, and, notably, the rail conversion of excavators. Approximately half of our turnover is generated from the rail conversion of excavators, a niche sector where we have solidified our position as market leaders in Scandinavia and supply products to various parts of the world, a standing we've maintained for over 20 years. Crafting products in this category demands highly skilled personnel and adherence to stringent certifications with elevated standards to ensure the complete safety of our products in the intricate railway environment.
What types of companies do you collaborate on projects with?
We have a rich history of close collaboration with our customers, primarily small and medium-sized trackwork contractors seeking more efficient equipment and innovative methods to enhance the quality, speed, and safety of their work. When a client presents a specific problem, our approach involves a dedicated process to devise a solution, maintaining a close partnership throughout the project.
Our emphasis lies in thoroughly understanding the customer's challenges. We cultivate a professional yet warm relationship, fostering a relaxed environment that promotes innovation and a collaborative spirit with our customers. To ensure success, we leverage our experience, striving to blend proven technology with new innovations, creating solutions that offer optimal reliability while advancing efficiency in terms of time and cost for the customer.
What are your plans going forward to ensure Rosenqvist Rail services are still around for years to come?
Since the beginning of this year, Rosenqvist Rail has new owners. The founder has acquired the company from Pandrol, and we are now reclaiming our former name, Rosenqvist Rail AB. As part of the agreement, Pandrol will become the exclusive distributor of Rosenqvist Rail equipment for specific markets, including the UK, Ireland, France, and Australia. There is an ambition to expand business into many other markets, fostering a robust technological partnership. The commercial agreement signed with Rosenqvist Group will also enable Pandrol to uphold its service standards by providing an end-to-end solution for their customers.
I am confident that this arrangement will empower both parties to leverage our respective strengths and excel in our endeavours.
What are some of the biggest challenges this sector currently faces and what are some potential solutions?
To attract new talent to the railway track sector, a crucial shift toward safety,
cleanliness, and technological advancement is essential. Acknowledging the challenge of attracting skilled staff, a key strategy involves the mechanization and automation of tedious and hazardous tasks. By embracing remote operation and utilizing sensor and camera technology, the sector can achieve a higher level of autonomy for tools and machines. This not only enhances safety but also modernizes the work environment, making it more appealing to the younger generation. Highlighting these advancements alongside professional growth opportunities and competitive incentives will play a pivotal role in overcoming current staffing challenges and securing a robust workforce for the future.
How do you make your business a good place to work?
To foster a positive work environment, businesses must prioritize employee well-being and engagement. Cultivate a culture of respect and open communication, encouraging collaboration and celebrating achievements. Prioritize work-life balance by offering reasonable working hours and flexible arrangements. Invest in employee growth through training and development programs, providing clear career paths and advancement opportunities. Recognize and reward performance to motivate and appreciate hard work. Support health and well-being with wellness programs and mental health resources. Effective leadership is crucial, promoting transparency and open communication. Ensure a comfortable physical environment with a focus on safety and aesthetics. Champion inclusivity and diversity, creating an environment where everyone feels valued. Facilitate team-building activities to strengthen relationships and encourage regular
feedback. Offer competitive compensation and attractive benefits, aligning with industry standards. Engage in socially responsible practices and allow flexibility in work arrangements.
Finally, maintain a fun and enjoyable atmosphere by incorporating recreational activities and celebrating milestones. Regularly listen to employee feedback, acting on concerns to continually enhance the workplace experience.
At some point, every company will face the question of how to continue maximising earnings from their current business practice whilst also investing enough in innovation so they can turn a profit in the future. How can a company achieve the necessary creativity to innovate without compromising their existing business?
In navigating the delicate balance between maximizing current earnings and fostering innovation, companies must adopt a strategic approach to secure long-term profitability. Establishing a dedicated innovation culture within the organization is paramount. Encouraging employees to think creatively and providing them with time and resources for experimentation fosters a fertile ground for new ideas without jeopardizing existing operations.
We are exploring partnerships with the local universities and are part of an innovative cluster of companies to leverage the sum of competence as examples. By embracing a dual strategy that values both current success and future innovation, companies can position themselves to thrive in an ever-evolving business landscape, ensuring they remain competitive and resilient in the face of changing market dynamics.
Stuart has over two decades of experience in the rail market, garnered through his tenure at several high profile firms within the connectivity and technology sector. Having started his career as a Quality Engineer, Stuart has developed comprehensive understanding of the industry across various operational roles including engineering, project management and business development.
With over 70 years of history, Aerco is a long-established stockist and distributer of electrical components. Offering specialised products to manufacturers in the aerospace, defence, medical, industrial, rail and transportation markets globally.
Want to know more about Aerco?
Tel: 01403260206
Email: sales@aerco.co.uk
Vist: www.aerco.co.uk
LinkedIn: linkedin.com/in/stuartevans-b65a7a64
Tell us about your career so far.
I have only recently joined Aerco but I have been in the mass transit and Rail sector for over 20 years. I started as an electrical engineer at TT Electronics and moved my way through the business as a quality engineer to project management. I started my Business Development journey representing Schaltbau in the UK, then moved on to Rowe Hankins. The last eight years I was an Account Manager at TE Connectivity.
Over the years, I have worked on many projects supporting the UK Rolling Stock manufacturers, their supply chain, and the maintenance providers with solutions that meet their requirements and in line with Rail Standards.
I am extremely excited to join Aerco as a Business Director for Mass Transportation. The business has put a real focus on rail and some interesting opportunities are opening up. Some of the key brands we work with have gained Network Rail approval for their products and I am looking forward to opportunities where I can bring my engineering background to good use and help improve the supply chain.
How long has Aerco been in business?
Aerco has been with us for over 65 years and specialises in providing a comprehensive range of products tailored for the rail market, ensuring safety, reliability, and efficiency in rail applications. Our offerings include electrical and electronic components such as relays, switches, and connectors designed to meet the demanding requirements of the rail industry. Additionally, we supply sensors and monitoring solutions for temperature, speed, vibration, and condition monitoring of critical rail infrastructure. We provide customised solutions, providing design, engineering, and manufacturing services to meet the specific requirements of rail projects. Overall, Aerco’s products play a crucial role in ensuring the safe, reliable, and efficient operation of rail systems.
Initially specialising in Aviation, Aerospace and Defence, working in these markets has really laid the foundations for the core business values. Aerco knows the importance of keeping track of where our products come from and being able to trace them back if needed. This has always been a big deal for us, especially coming from a background in civil aviation where safety is paramount. As things have evolved, so have our processes. We've stayed on top of certification requirements, like being one of the first distribution companies in the UK to get UL approval for respooling cable while keeping the UL approval for the product intact. It's all about being flexible and making sure we're meeting the needs of our customers and the standards of the industry. That's how we've built trust over the years and become a go-to supplier.
We work with a range of organisations ranging from sub-suppliers to OEMs to maintenance providers including CAF, Alstom, Siemens and Knorr Bremse and have great success with supplying components for rolling stock over the last few years. We are now making inroads with signalling and trackside. Aerco work with a portfolio of top quality electrical and electronic component and cabling brands including TT Electronics, ABB, TE Connectivity and Belden, the company has a great relationship with them and there is a deep knowledge and understanding of these product families.
Recently TT AB Connectors gained Network Rail Approval for their ABCIRH connector series and we have been championing these products which offer alternatives and options to rail engineering and manufacturing companies involved in Plug N Play applications who may be looking to overcome supply chain challenges on components.
What most excites about you in the industry right now?
We're really excited about our position in the Signalling market. At Aerco, we've worked hard to ensure that we can provide a wide range of connectors and accessories that have received approval from Network Rail. Additionally, we supply cable and wire from industry-leading brands like Belden, Alpha Wire, and Amokabel.
We're gearing up to exhibit in the Network Rail Signalling zone at Rail Live this June, and we can't wait to showcase our product depth and knowledge in this area. It's a great opportunity for us to connect with others in the industry, demonstrate our expertise, and show how Aerco can meet the unique needs of the Signalling market. We're looking forward to it!
We are also continually looking to bolster our product range to give real depth and variety to the product spectrum we can provide for the rail market. For example, our recent announcements of the franchise relationship with Belden brings the Hirschmann brand of Ethernet wired and wireless switches designed for harsh environments and with rail approval, with potential applications both in rolling stock and for communications between vehicles and track-side systems
What are some of the biggest challenges you’re facing?
The rail supply chain faces a huge challenge at the moment as lots of component manufacturers are looking to reduce their overheads and cut back on non-core activities, which have seen them reduce sales team numbers and, on some occasions, reduce technical support to end-users, too. This leaves a void of support, especially for small and mid-size engineering companies that still require the technical expertise of
the component manufacturer to assist with the design process.
At Aerco we see the need to support our customers with our in-house technical support and have developed our Aerco Academy to help grow the knowledge of new staff but also harness the experience and expertise of our longer-standing team members. With our technical support, we can help with the component selection and evaluation activities in our customers’ design process.
The approval and acceptance of new technology within the rail community poses a significant challenge that needs to be addressed. Frustration is mounting among technology companies and this reluctance to embrace innovation is holding back progress for the whole industry.
Initiatives like the new Global Centre of Rail Excellence in South Wales go some way to tackling this issue by hopefully accelerating the testing process for new products. With more facilities like these, rail companies can gain greater confidence in the industry standards compliance of new technologies, potentially leading to quicker adoption. This not only addresses supply chain challenges by opening doors to alternative products but also facilitates faster resolution of operational issues
through readily available replacements or upgrades.
The GCRE is a step in the right direction, but the UK needs more facilities like these to give the rail industry confidence in new technology.
Hydrogen-powered trains offer a promising avenue for sustainable rail transportation, demonstrated by Germany's Coradia iLint trains. Their performance will serve as a valuable learning opportunity for the UK, particularly regarding operational effectiveness and market viability.
However, the UK faces significant challenges in adopting hydrogen trains due to insufficient infrastructure. The slow pace of electrification, with only 38% of rail track currently electrified, highlights the need for a concerted effort to prioritize extended electrification across the entire rail network. This effort should involve close collaboration between the Department of Transport, Network Rail, and Train Owners to roll out electrification.
New regulatory bodies like Great British Railways could bring some positive changes to the rail industry. Hopefully, they'll help make things run smoother, improve services
‘The GCRE is a step in the right direction, but the UK needs more facilities like these to give the rail industry confidence in new technology.’
for passengers, and hold rail operators more accountable for their performance.
It'd be great to see these bodies prioritize passenger needs, safety, and sustainability, while also encouraging innovation and healthy competition in the industry. Clear communication and teamwork between all involved parties will be key to making these changes work well and address any issues that come up along the way. Aerco will follow this process with a keen eye and an interest in how it develops, with a view to taking part at every opportunity.
encompasses train planning, rostering, and resource management, aiding operational decision-making for timely and efficient service delivery.
experiences, utilising satellite data to bolster railway safety measures, and incorporating machine learning and AI into our software solutions.
What is the history of Tracsis PLC and the
Tracsis has undergone substantial growth particularly in the realm of rail technology. This encompasses a wide spectrum ranging planning, extending to the domain of digital railway safety protocols to safeguard railway track. This period has witnessed a series of entities into a unified business entity, aptly named Railtech UK, marking a significant Performance Software, Remote Condition Operational
Additionally, performance software facilitates delay attribution and event recording to foster continuous improvement. The Remote Condition Hardware and Software portfolio focuses on remote monitoring, analytics, and proactive maintenance of railway assets, ensuring optimised operation and safety. Our Risk Management and Safety Software helps to safeguard workforce and helps with maintenance procedures.
The Smart-Ticketing and Customer Experience portfolio offers diverse services such as pay-as-you-go ticketing, smart ticketing, delay repay, and customer feedback software like mystery shopping tools. These portfolios collectively enhance operational efficiency, safety, and customer satisfaction within the rail industry.
How have the products and services you offer developed over the years?
Over the years, our development has been multifaceted, with strategic acquisitions expanding our reach across various aspects crucial to the advancement of the railway industry. Each acquisition has allowed us to delve deeper into specific areas vital for industry progression. Simultaneously, we have focused on refining our products through organic investment, harnessing technological advancements to enhance their capabilities.
This includes integrating cuttingedge technologies such as geofencing for streamlined pay-as-you-go ticketing
While some may perceive these terms as overly used, we are committed to leveraging ML and AI to support operational efficiency, serving as complementary tools rather than replacements for human expertise. Our aim is to empower the operational community with additional insights, ensuring optimal utilisation of every available asset.
What are some major projects you’re working on?
We take great pride in two significant projects currently underway. Firstly, we are in the design phase of our next-generation rail safety platform, a collaborative effort with our strategic partner. Further details on this initiative will be forthcoming in the following months.
Secondly, our focus is on the development of Hopsta, a pay-as-you-go mobile app set to revolutionise passenger payment methods, offering a convenient and cost-effective ticketing solution. These projects represent key endeavours within our portfolio.
While we have numerous projects spanning various aspects of our RailTech UK business unit, including resource management, train planning, and delay attribution implementation for other operators, these two projects stand out as flagship initiatives. We believe they will significantly advance the industry by integrating technology for enhanced customer experience while prioritising health and safety concerns.
What are your views on collaborative working?
Collaboration is paramount for success across industries, particularly in the rail sector, where Tracsis champions a culture of partnership. Whether it's collaborating closely with strategic allies on advancing rail safety software or engaging with customers and even competitors, we firmly advocate for collaborative efforts. Each entity within the industry contributes uniquely, leveraging their strengths to enhance the overall process. Given the critical role of the rail industry in the UK's economy, facilitating passenger transport, and ensuring safety, it's imperative that all stakeholders collaborate effectively. This entails fostering a positive environment where stakeholders work together towards the common goal of maintaining an efficient and safe rail network. Collaboration stands as the cornerstone for achieving this collective objective.
In terms of technology, how do you anticipate things might change in the next five to ten years?
In any industry, adaptation to evolving conditions is essential. With the railway sector facing increased demand, heightened
Approved Hydraulics have been supplying some of the largest rail build and maintenance firms for over 10 years. Now considered some of the best in the world!
performance expectations, and the pressing issue of global warming, our strategic focus on leveraging machine learning and AI becomes imperative. These technologies support the effective optimisation of operations, aligning with our commitment to address contemporary challenges.
Moreover, as we navigate a changing landscape, utilising data to forecast changes and vulnerabilities within the railway network is paramount. This is especially crucial given the complexities arising from both the emergence of a technologically driven travel community and the challenges posed by an aging infrastructure amidst shifting climate conditions.
Our strategic direction emphasises the importance of predictive tools in ensuring the continued safe operation of the railway. By integrating comprehensive data analysis and predictive modelling, we aim to identify vulnerabilities and mitigate potential risks proactively. This approach underscores our commitment to maintaining safety and efficiency in railway operations amidst dynamic environmental and societal shifts.
Do you think the rail industry could be greener and what is Tracsis PLC’s green strategy?
The rail industry, including operators and regulators, prioritises environmental sustainability. Similarly, Tracsis places high importance on its green strategy, which is a collective responsibility. Ensuring environmental consciousness extends beyond group efforts, impacting individual priorities such as travel habits and energy consumption. We maintain a comprehensive approach through various working groups dedicated to implementing and reinforcing our green initiatives.
We're progressing through organic development, consistently investing in our four core portfolios: Operational Performance Software, Remote Condition Hardware and Software, Smart Ticketing and Customer Experience and Risk Management and Safety Software. Our expansion isn't limited to the UK; we're venturing into the US through Tracsis US. Moreover, we aim to broaden our offerings across all portfolios to support our colleagues in the US and cater to that market as well as exploring other geographical expansion opportunities.
Andrew Baldwin is Head of Policy and Public Affairs at APM. He has over ten years’ experience in public affairs, having worked at two other professional bodies developing influencing strategies, building political relationships and promoting members’ views in supranational, national and subnational legislatures across the world. Before working in public affairs, he ran the Westminster office of a UK Member of Parliament and worked in the Secretary of State’s office in a UK government department.
Ahead of the Spring Budget Association for Project Management (APM) called on the Government to factor in concerns for project stability and success into its plan, along with greater clarity on the Network North schemes and commitment to levelling up and net zero projects. Certainty, consistency, and confidence are key to future investments in projects and project delivery.
The Chancellor however failed to provide much certainty on project delivery, at a time when much uncertainty prevails, following the scrapping of HS2 Phase 2. UK infrastructure has veered towards vaguer plans in recent months, and although the merits of the HS2 project will be debated for years to come, overnight ‘a concrete plan to deliver major benefits to the UK and its three largest cities’ was lost.
Instead, we were left with more uncertainty, speculation and (in Network North) a list of disparate projects that may or may not get started before the next General Election. Billed as a ‘tidal wave of new investment; to better connect parts of the North of England’, Network North does not deliver a consistent approach to improving the country’s infrastructure.
It is simply not the way to go about project delivery. You don’t start with the money – you start with the need. What do we need to deliver, and how can we do that? Only after long consideration of potential schemes would you start thinking about how much it’ll cost. In Network North we’ve seen the opposite – money first, need second, and so we should get away from the pot of money approach to projects. Work out what is needed, then see what funding is available, and reassess deliverables.
APM called for a more focused strategy outlining firstly how all these smaller projects link together into a plan which
will improve society, and secondly how the Government plans to use projects more generally to improve the UK – as when projects succeed, society benefits. Certainty and consistency lead to confidence.
Implementing the next National Infrastructure Strategy, delivering the next carbon budget, and ‘reallocating HS2 funds’ for the north and Midlands will be the responsibility of the next Government, and we are unlikely to see any significant changes to infrastructure projects and spending before the election. We will work with the next Government to ensure that existing and new projects can be delivered. And this means addressing the skills gap and calling on Government and employers to invest in training and development for project professionals and increased funding for professional development and qualifications.
In a recent APM survey, more than 85 per cent of project professionals said they trust the UK Government to deliver projects well. But we need to invest to keep that level of trust high. APM members’ confidence needs to be repaid through consistent, stable, long term project investment. But society also needs confidence to move forward. You don’t invest in major projects or skills development when there’s no certainty or consistency.
Of the Government’s current commitments, we would like to see greater clarity and commitment to levelling up and net zero projects, and to see a future Government continue good work in these areas. But skills development must be part of that. Another APM survey highlighted that although the majority of project professionals working in the transport and logistics sector, who took part in the survey, are confident the UK government will meet its 2050 net zero targets; 77 per cent highlighted concerns over the profession’s
‘More than 85 per cent of project professionals said they trust the UK Government to deliver projects well’
pipeline talent to sustain the delivery of net zero projects. This needs addressing.
One thing is for sure, the sector cannot afford another HS2 style slamming of the brakes. As the only chartered membership organisation for the project profession, APM will continue to call for a certain and consistent approach, which will build confidence to deliver investment in projects and project professionals.
APM can support businesses and project professionals who are seeking to improve the standards of their project management through project management qualifications which lead to Chartered Project Professional (ChPP) status. To find out more, visit apm. org.uk/qualifications-and-training/.
Porterbrook, the UK’s leading rolling stock financier and asset management company, has been successful in its bid to take ownership of 30 Class 379 Electrostars. The intention is for the fleet to be leased to Govia Thameslink Railway (GTR) to run on the Great Northern route, as per the notice published 12 March 2024. The EMU fleet, which was previously operated by Greater Anglia before coming off lease, was built in 2011 and is expected to be able to run for at least another 20 years.
Bentley Systems, the infrastructure engineering software company, has opened its new UK headquarters in London, which marks the beginning of the company’s 40th anniversary celebrations. The office is located at 8 Bishopsgate, a new landmark 50-story tower on the corner of Bishopsgate and Leadenhall Street in the City of London.
Lorna Gibson is Managing Director for QTS Training, a subsidiary company of QTS Group, which supplies railway safety, on-track plant, health and safety and construction management training to the rail and wider industries across the UK. Lorna has been part of the Rail industry for over ten years and is a founding member and Chair of Women in Rail Scotland and is the Vice Chair of RIA Scotland.
QTS Training delivers railway, health and safety, personal development, small plant, confined space and IRATA rope access training to a wide variety of customers and has training centres in Lanarkshire, Scotland, Yorkshire and Nottinghamshire, England. It works in the railway, engineering and off-shore sectors.
Want to know more about QTS Training?
Tel: 01357 440 222
Email: qtstraining@qtsgroup.com
Visit: www.qtstrainingservices.co.uk
‘QTS’ own Rail Skills Academy is a collaboration between QTS Group, QTS Training, a number of railway contractors, Network Rail, local authorities and employability partners.’
What are some standout projects you’ve been involved in over the years?
In the last two years, QTS Training has developed the QTS Rail Skills Academy. This programme has been introduced to help address the skills shortage in our industry. The lack of young people attracted to join the rail industry and the lack of diversity in the workforce across the industry. It is a unique programme which provides young people with previous barriers to work with a pathway into the rail industry. It is a 10 week programme which provides the trainees with a range of accredited competencies in Health & Safety, Small Plant, Railway Safety Critical and First Aid training together with four weeks of on site work experience. During the programme, we invite a number of supply chain partners to meet and speak to the young people about their work, and on conclusion the young people take part in a celebration event with invited guests and a speed interview session with a number of potential employers.
How long has your company been in business?
QTS Training has been in business for 15 years and is celebrating its 15th anniversary in April 2024.
Tell us about QTS Training.
QTS Training was established by QTS Group Ltd to provide its operatives with a high standard of training and ensure that they were fully competent to work safely on the railway infrastructure. Once QTS Training was launched, it became known for the quality of its training and external customers began to see it as a training provider of choice for railway training. Over the last 15 years the company has grown significantly and is now one of the top rated railway training providers in the UK, recently achieving NSAR Gold status across Compliance, Delivery and Premises for the third time.
QTS Training is accredited by a range of assurance and accrediting bodies including NSAR (National Skills Academy for Rail), City & Guilds, SQA, CITB SSP, IRATA, PASMA, NuCo and MP Awards. Regular audits and assurance visits by these organisations ensure the quality of the training delivered.
What is your Unique Selling Point?
As part of a large railway engineering contracting group, QTS Training has an in depth knowledge of the work that our learners carry out in their day to day roles. Our trainers all maintain their operational experience and knowledge and are very aware of the safety requirements of this work which we are able to embed in all the training we deliver.
To date, 50 young people have successfully completed the programme and over 90 per cent of them are now enjoying new careers in the rail industry. The QTS Rail Skills Academy was the winner of the Rail Spotlight Award for Training Excellence and Highly Commended in the Women in Rail Awards for Best Training and Development Programme. The biggest reward, however, comes from seeing these nervous, unsure, young people grow into confident, happy trainees being offered jobs they could previously not have dreamt of, overcoming some of the difficulties that they have experienced in their young lives and developing careers for life in the rail industry.
What are your plans going forward to ensure QTS Training services are still around for years to come?
The railway training sector has a critical skills shortage, the majority of trainers and assessors are reaching, or beyond, retirement age and, for many specialisms, such as On-Track Plant and Overhead Line training, there are only a handful of experienced trainers. QTS Training has, over the last three years, been putting a strategy in place to upskill new, younger trainers and assessors, and bring them into the industry. We currently have four new trainers and assessors at various stages of mentorship. This is a significant investment for QTS Training but will strengthen our team, provide a succession plan and bring new trainers into the industry.
What do you have planned for the year ahead?
QTS Training is looking forward to growing our presence in England, we have recently invested in the expansion of our Yorkshire training centre, to continue strengthening
our team through our upskilling strategy and to grow the QTS Rail Skills Academy throughout the UK.
How can the industry tackle its skills shortage and how do you recruit/retain/ train your staff?
The skills shortage is becoming a critical issue for the rail industry and one that must be addressed and resolved.
To resolve this in a sustainable way this has to start in schools, and particularly in primary schools. Young people must be made aware of the potential of the rail industry and the vast range of career opportunities available to them, and this has to be continued through all stages of education, particularly by industry working with educators and ensuring that the curriculum includes relevant learning for future jobs. We must also look at transferable skills, for example, armed forces leavers. Many of these individuals have skills that are directly relevant to the rail industry with experience that lends itself to working on the railway infrastructure.
Many organisations carry out some great work engaging with education, armed forces, ex offenders etc but to successfully deal with the skills shortage this has to be done through collaboration and an industry wide, consistent, effort.
The industry also needs to fully recognise why the diversity of our workforce needs to improve, only by attracting a diverse range of people will we be able to meet all our needs and build a successful, future proof industry, and a much more strategic approach is required for this. By developing its own training company, QTS Training Ltd, QTS Group has ensured that its workforce receives the highest level of quality training, are competent and safe to carry out work on the railway infrastructure and deliver efficiently and cost effectively to clients. The development and progression that is offered to QTS Group team members, and the confidence that clients have in their abilities, together with the continuous work that is undertaken to provide team members with the best terms and working conditions, assists with attracting and retaining team members.
How can we make the rail industry a place people want to work in?
To attract, and retain, people in the rail industry we must make it a place where people enjoy working, feel safe, feel valued and are given the opportunity to grow and develop. People also need to feel secure and with the current issues with control
With state-of-the-art facilities situated throughout the UK, QTS Training is renowned for its expert, specialist trainers, excellent customer service and unrivalled training facilities.
We pride ourselves in delivering quality training providing an enjoyable and worthwhile learning experience for all.
•
•
•
•
Accredited by:
•
•
•
•
periods and investment it can be difficult for employers to offer this security and to have the confidence to invest in their workforce.
The working hours are also something that many people find off putting, regular weekend and nightshift working with lack of mid-week work available does not provide the security that potential employees are looking for. To allow the industry to resolve the skills shortage and attract new talent, consideration must be given to changes in working hours and practices and how this could work together with keeping passengers happy and providing a reliable train service.
What are your views on collaborative working?
To create a truly successful industry, collaboration is imperative. Some of the most successful railway projects over the last few years are the result of collaboration. QTS’ own Rail Skills Academy is a collaboration between QTS Group, QTS Training, a number of railway contractors, Network Rail, local authorities and employability partners. Without these partnerships there is no doubt that the programme would not have resulted in the success for young people that it has.
NEIL HUGHES
HEAD OF TRANSPORT, EV INFRASTRUCTURE AND AUTOMOTIVE AT SCHNEIDER ELECTRIC
Neil is dedicated to instigating a shift towards sustainable transportation. He believes that EVs, coupled with innovative sustainable energy sources, can significantly reduce harmful emissions and promote an eco-friendly future. He has been Head of Transport, EV Infrastructure and Automotive since May 2004.
What does sustainability mean to you?
To me sustainability is about all of us being able to live our lives how we want to now, without compromising the ability of our children and grandchildren to meet their own needs in the future. I feel it is also about balancing economic, social, and environmental considerations to ensure the long-term health and well-being of both people and the planet. In order to do this from a business perspective, we must look at strategies to minimise our environmental impact and make sure that we prioritise social responsibility as well as economic viability.
How has technology developed since you started in the industry?
Since I started in the industry there have been lots of advancements in technology. A few that have moved at pace over the years would be Smart Grid, the integration of digital communication technology into the electrical grid has allowed for more efficient energy distribution, better load management, and improved reliability.
I’d also point to Renewable Energy Integration, due to climate change and the need to electrify we have seen a substantial increase in the integration of renewable energy sources such as solar and wind power, this has obviously been helped by the advancements in energy storage and grid management systems.
Another would be Internet of Things (IoT). IoT technology has totally changed the industry, allowing for remote monitoring, predictive maintenance, and improved energy efficiency in electrical systems.
Also, the development of advanced energy management software has helped us better control and optimise energy usage in commercial buildings and industrial facilities. And finally I’d say the rise of electric vehicles has led to the development and increased roll out of charging infrastructure and smart grid solutions to support widespread adoption.
How long has your company been in business?
Schneider Electric has a long history dating back to 1836, when it was founded by Adolphe Schneider and his brother JosephEugène Schneider in France. Initially, the company started as a foundry and steel industry business. Over the years, it expanded into various industrial sectors, eventually becoming a global specialist in energy management and automation.
With a history spanning nearly two centuries, Schneider Electric has evolved and adapted to the changing technological and industrial landscapes, establishing itself as a leading provider of energy and automation solutions worldwide.
‘IoT technology has totally changed the industry, allowing for remote monitoring, predictive maintenance, and improved energy efficiency in electrical systems.’
Tell us about Schneider Electric.
We are a technology company providing energy and automation digital solutions for efficiency and sustainability for our customers around the world. We are a 34-billion-euro revenue company with 150,000 employees in over 100 countries. We have two key businesses: Energy Management and Industrial Automation. We provide a wide range of products, solutions, and services for various industries, including the energy and infrastructure industry, buildings and data centres.
We are known for our innovative and sustainable energy management solutions and services which include products for power distribution, industrial automation, and energy efficiency. We also offer digital solutions and software for energy management and automation through leveraging technologies such as IoT, cloud computing, and artificial intelligence.
With a focus on sustainability and efficiency we aim to help our customers optimise energy usage, reduce environmental impact, and achieve operational excellence. We are always committed to driving digital transformation and advancing the adoption of renewable energy sources.
We operate as one Schneider Electric for our customers. We have specialties, and we are the most integrated solution provider in our industry. We are a technology company, we focus on the part of the technology where we can bring value to our customers – yet we operate, put in place our solutions, and produce our technologies with suppliers, integrators, and partners.
Our strength lies in our ability to provide end-to-end solutions for energy management and automation. Including a wide range of solutions, software and services that help customers optimise energy usage, enhance operational efficiency, and achieve sustainability goals. Schneider Electrics focus on innovation, digitisation, and sustainability sets it apart in the industry.
What would you say is the most exciting technology in the industry?
One of the most exciting technologies in the rail industry today is autonomous train technology; both in terms of its development and integration. Autonomous trains have the potential to revolutionise rail operations by leveraging AI, advanced sensors, and control systems to enable trains to operate with minimal human intervention. This technology promises significant benefits, including improved safety, enhanced operational efficiency, increased capacity, and potential cost savings.
Autonomous trains can optimise speed, braking, and energy usage, leading to smoother and more efficient operations. Furthermore, they have the potential to reduce the risk of human error and enhance overall system reliability. As this technology continues to advance, it holds the promise of transforming the way rail networks are managed and operated, offering a glimpse into the future of smart and autonomous transportation systems.
What type of government-level collaboration takes place within this sector?
Government-level collaboration within the rail sector often involves various forms of partnership and coordination to address key aspects of rail infrastructure, operations, and regulations. Some of the common types of government-level collaboration in the rail sector are:
• Infrastructure Investment – governments collaborate with rail authorities and private entities to plan, fund, and execute infrastructure projects such as the construction of new rail lines, expansion of existing networks, and modernisation of rail infrastructure.
• Regulatory Frameworks – collaboration occurs in the development of regulatory standards, safety protocols, and operational guidelines to ensure compliance with national and international regulations, as well as to promote interoperability and harmonisation across different rail systems.
• Funding and Subsidies – governments often provide funding, subsidies, or financial incentives to support rail projects, promote modal shift to rail transportation, and improve accessibility and affordability of rail services. (For example, CP7 is a five-year period (20242029) during which Network Rail will invest £44 billion in the UK railway)
• Technology and Innovation –collaboration in the research, development, and deployment of advanced rail technologies, such as signalling systems, energy-efficient solutions, and digitalisation initiatives aimed at improving safety, efficiency, and sustainability.
• Intermodal Integration – coordination between different transportation authorities to facilitate seamless integration of rail with other modes of transportation, such as road, air, and sea, to create efficient and interconnected transportation networks.
• Policy Development – collaboration in the formulation of policies related to environmental sustainability, urban planning, and economic development to promote the role of rail as a sustainable and efficient mode of transportation.
These collaborative efforts aim to drive the growth, modernisation, and sustainability of the rail sector while addressing societal needs and environmental challenges.
How can we get more use of the rail assets and what is your vision of rail in 10 or 20 years?
To get more use out of rail assets, it's important to focus on modernisation, digitisation, and sustainability. This involves leveraging technologies like predictive maintenance, IoT, and data analytics to optimise asset performance and reliability. Additionally, integrating rail systems with smart grid technologies and renewable energy sources can enhance efficiency and sustainability.
Looking into the future 10 to 20 years, I think the vision for rail is likely to include even greater automation, connectivity, and sustainability. This may involve widespread adoption of autonomous trains, advanced signalling systems, and electrification to reduce carbon footprint.
What are your hopes for the new regulatory bodies, such as Great British Railways?
I hope the establishment of new regulatory bodies like Great British Railways presents an opportunity to bring about positive changes in the rail industry. These bodies can potentially streamline operations, improve customer experience, and drive investments in modernisation and sustainability. They may also lead to better coordination and collaboration between different stakeholders and the fostering of innovation and efficiency in the Rail sector.
What do you expect to be the biggest challenges that come from this transformation of the railway industry?
I feel that the transformation of our railway industry will likely bring several significant challenges, including:
• The Integration of Technology –implementing new technologies such as IoT, AI, and automation while ensuring seamless integration with existing infrastructure and systems.
• Cybersecurity – the need to safeguard the railway systems from cyber threats
as digitalisation always increases vulnerability to cyberattacks.
• Regulatory Compliance – adapting to evolving safety and regulatory standards as new technologies and operational practices are introduced.
• Legacy Infrastructure – modernising and upgrading aging railway infrastructure to support digitalisation and automation, which may require significant investments and planning.
• Workforce Skills – equipping the workforce with the necessary skills to operate and maintain advanced digital systems and managing the impact of automation on employment.
• Customer Experience – balancing the need for operational efficiency with providing a seamless and enjoyable experience for passengers, ensuring that technology enhances rather than detracts from the customer journey.
• Sustainability – addressing environmental concerns and ensuring that the transformation aligns with sustainability goals, including reducing carbon emissions and energy consumption.
All these challenges will require careful planning, investment, collaboration, and innovation to navigate successfully.
In terms of technology, how do you anticipate things might change in the next five to ten years?
In the next five to ten years, I think there will be many technological advancements that may significantly impact the rail industry, including:
• Autonomous Trains – the development and deployment of autonomous or semi-autonomous trains, leveraging AI, sensors, and advanced control systems for enhanced safety and efficiency.
• Condition based Maintenance – increased adoption of predictive maintenance technologies using IoT sensors and analytics to anticipate and prevent equipment failures, reducing downtime and maintenance costs.
• Digital Twins – widespread use of digital twin technology to create virtual models of rail assets, enabling real-time monitoring, simulation, and optimisation of operations and maintenance activities.
• Electrification and Energy Efficiency – continued focus on electrification of rail networks and the integration of energy-efficient technologies to reduce environmental impact and operational costs.
• Passenger Experience – enhanced passenger experience through the integration of connectivity, entertainment, and personalised services within trains, as well as streamlined ticketing and boarding processes.
• Big Data and Analytics – leveraging big data analytics to optimise scheduling,
routing, and resource allocation, improving operational efficiency and service reliability.
• Cybersecurity Measures – heightened focus on cybersecurity measures to protect critical rail infrastructure and rolling stock from cyber threats and ensure the integrity of data and operations.
These advancements are expected to reshape the rail industry, driving improvements in safety, reliability, sustainability, and passenger experience.
What Innovations have Schneider been working on for the Rail Industry?
Schneider Electric have been developing a new concept of a Compact PSP that provides signalling equipment the secure power it requires to operate reliably, whilst offering the benefits of reduced size and the opportunity to access system/network status remotely.
The security of the power supply is facilitated by an uninterruptible power supply with automatic bypass capabilities. This means that if the mains supply is interrupted, it will continue to deliver power and keep services running while an engineer works to fix the Issue.
Crucially, a more compact PSP design removes the need for Relocatable Equipment Buildings for signalling supplies. The Compact PSP can be installed on a standard location case base, eliminating the need for expensive civil engineering work. It is built into a bespoke enclosure that is slightly larger than a standard full location case, minimising use of trackside space.
Schneider Electric drives digital transformation by integrating world-leading process and energy technologies, end-point to cloud connecting products, controls, software, and services, across the entire lifecycle, enabling integrated company management, for homes, buildings, data centres, infrastructure, and industries.
Want to know more about Schneider Electric?
Tel: 0330 587 8030
Visit: www.se.com/uk
The Compact PSP is the ideal response to the challenges faced by the rail industry.
The small size of the Compact PSP gives engineers greater freedom in system design. The solution is ideal for placement in track-side areas where space is limited, or for islands of signalling assets where a traditional PSP would not be suitable.
An award winning solution offering signalling supplies up to 20kVA at a fraction of the cost of a conventional PSP in a REB type building or ISO container. This solution offers features and benefits including;
At just 5.6% weight of a full-sized PSP, the decrease in material usage and transport emissions offers a lower carbon footprint alternative.
If the DNO supply is lost the integral 20kVA UPS will provide power for up to 15 minutes.
Autonomy can be extended with additional batteries in a second location case.
To learn more, watch the video here!
Electromechanical bypass of the UPS ensures continuity of supply should a fault occur.
Internal environment of the Compact PSP managed to ensure normal operation under extreme climatic conditions.
Integral HMI enables operators to see the current syste status instantly, reducing track side time for engineers.
Gavin Adams has been with Concrete Canvas Ltd for over eight years and has spent 19 years working in ground engineering with a wealth of experience across multiple sectors. Gavin is head of Sales – UK and works closely with regional consultants, contractors and clients, including The Coal Authority, Network Rail, National Highways and local authorities.
Created specifically for erosion control, containment and shelter applications, Concrete Canvas® (CC) products are part of a revolutionary class of new, innovative materials called Geosynthetic Cementitious Composite Mats (GCCMs). CC is a flexible, concrete filled geosynthetic which provides a thin and durable concrete layer when hydrated.
Want to know more about Concrete Canvas?
Tel: 0345 6801908
Email: info@concretecanvas.com
Visit: www.concretecanvas.com
When did you join Concrete Canvas Limited and what is your role within the company?
I have recently celebrated eight years at Concrete Canvas Limited, time flies when you’re having fun. After several years working as a Technical Sales Representative for the Midlands & North region, I was delighted to be appointed Head of Sales –UK in September last year. Working with the team at CCUK, we are responsible for promoting the material we manufacture, providing specification work to key clients, consultants, and contractors, and educating them on the best installation practices for the successful installation of the material in various applications.
Tell us about your career before you joined Concrete Canvas Limited?
I have always worked in ground engineering, previously working for a pipe and fittings manufacturer in the water and wastewater sector. Having dealt with all the major water companies across the UK and Ireland, including some major projects such as the 2012 London Olympics, I gained valuable knowledge working on framework periods (called AMP periods in the water sector) and with many of the major contractors and JVs that service the water sector. I found the knowledge built up over a decade useful as I transferred my skills from the water sector to the rail sector.
What does sustainability mean to you?
Sustainability is fundamental, not only in our working lives but also on a personal level. Having a couple of children, I want to make sure we do as much as we can now to ensure they have a sustainable future in years to come. I’m very proud of all the
work we do at Concrete Canvas Limited to lessen environmental impacts. Whether this be the drive to use as much renewable energy as possible – we have just invested over £1 million in solar panels – or the tireless work of our R&D team developing a new formulation for our material. After five years of work, we launched the CC T-Series in 2022, reducing our embodied carbon characteristics from 55 per cent to 63 per cent compared to ST4 poured concrete in channel lining applications.
How long has your company been in business?
Concrete Canvas was incorporated in 2005, initially making semi-permanent shelters for the humanitarian relief and defence sectors, supplying them globally. Due to the versatility of the material and its potential in the domestic and international civil sectors, the decision was made to start manufacturing the material on an industrial scale in 2009. We now supply material to over one hundred countries, manufacturing over 20,000m² a week in our South Walesbased production facility, where we also showcase the uses of Concrete Canvas in our purpose-built Demo Park.
Which sectors do you work in?
In the UK, the transportation sector makes up around 60 per cent of our business, with the rail sector being a big part of that. However, the versatility of our material allows us to work in several sectors, including the petrochemical, utilities, public works, and mining sectors.
What is your Unique Selling Point?
Our material has numerous advantages over the traditional hard armour alternatives
specific to the rail sector. Firstly, our material is very flexible in its pre-hydrated state and acts like a geotextile. Installing in either channels, on slopes or as a weed suppression barrier is effortless. It will conform very closely to the ground and can cope with small undulations in the ground conditions. This means you don’t have to be super precise with your excavation/grading, and the material can be directly installed onto the substrate.
The second advantage we have is the speed of installation. We regularly see install rates of up to 125m² an hour. For the rail sector, this means the quicker it is to install, the faster you can off-hire equipment and reduce line possession, greatly reducing the overall cost of a scheme.
What types of products and services do you offer?
Concrete Canvas currently offers several materials suitable for the client's needs. If the requirement is for hard armoured erosion control, scour resistance or weed suppression, then this would be a range of materials classed as Geosynthetic Cementitious Composite Mats or GCCMs for short. This material comes in three types depending on the scheme requirements and are called CCT1, CCT2 or CCT3. If, however, the requirement is for full containment of a liquid or a chemical, it would be a classification of material called a Geosynthetic Cementitious Composite
Barrier or GCCB. This material is available in two tytpes (CCHT1 or CCHT2) and is called CC Hydro.
How have the products and services you offer developed over the years?
Innovation is at the heart of Concrete Canvas. It has always been imperative to continually develop the material for our clients and their requirements to achieve their goals and successes for the schemes they are involved in. Whether this development is in the continued improvement of the cementitious formulation from our excellent R&D team or the creation and development of the ASTM international standards for the classification of material from our esteemed Technical Department, the team here at Concrete Canvas is incredibly passionate. It will continue to develop a range of materials to perform the very best for our customers.
What are some standout projects you’ve been involved in over the years?
Since starting in the rail sector in 2009, Concrete Canvas has delivered material to over 700 rail schemes across the UK’s rail network, so it is almost impossible to highlight some. If I had to choose a few, I always like the scheme where we supplied material to Farnley Haugh, where our material was used to line a newly created crest drain around a landslip repair. We have
also recently seen many schemes where our material is used for weed suppression around access steps and GRP walkways. This has helped dramatically reduce or eliminate the need for maintenance near these assets. We are currently trialling our material on a section of Japanese Knotweed with a couple of Network Rail depots, and I’m excited to see the results of these trials over the coming months. Watch this space.
What types of companies do you collaborate on projects with?
We've worked with many different companies over the years depending on the requirements of a scheme, whether that be other suppliers to the rail sector or other organisations. We recently supplied material to a scheme with multiple agencies involved, and our material was used as part of an Environment Agency flood alleviation scheme. Due to the scheme's location, the contractor and designer needed approval from National Highways and Network Rail. As we've worked with both companies on many occasions, we pointed to our extensive back catalogue of case studies with both parties. We were able to seek approval for the scheme to go ahead with our material. What are some of the biggest challenges this sector currently faces?
Climate change is the biggest challenge to the rail sector and all sectors and walks of life; we will have to face this head-on in the
coming years. It is clear that the issues are related to dealing with more frequent and heavier rainfall events and how it is best to manage these higher flows seen on the drainage network.
Where flooding events were happening once every ten years or so, we see more and more flooding events yearly and sometimes monthly. Concrete Canvas have worked hard to ensure our material provides a high level of abrasion resistance and scour protection to cope with heavier, faster flows through open channels. We have recently been working on new technical drawings to include baffling details to help dissipate water flow before it leaves the rail drainage systems.
Where do you think the industry will be in the next 10-15 years?
The rail sector is vital for the country's continued economic development; we cannot function without one. While passenger numbers are still down compared to pre-pandemic levels, it is important for the sector to continually improve its assets to ensure the fare-paying passenger gets an on-time, frequent, clean, and efficient service. Continuing to improve the drainage systems across the rail network is vital, as a
fully functioning drainage system can help reduce train delays due to landslips on lines and keep the rail network moving.
What are your views on collaborative working?
Collaborative work is crucial for the rail sector. There are thousands of excellent organisations working in the rail sector, and one of the ways we can ensure the success of the rail industry over the coming years is to ensure that suppliers work together on projects or schemes. Whether that be the implementation of a 5G signal so passengers can work while commuting or for the continued improvements of railway assets, such as drainage, we all need to work together for the common goal of a worldclass rail network.
How do you make your business a good place to work?
Concrete Canvas is not a good place to work; it’s a great place. I have some of the best colleagues in our marketing department, R&D, engineering, technical, admin and logistics, and production. The company ethos is to work hard and strive to be the best at what we do, which is clear to the
owners, Will Crawford and Peter Brewin. We may have many departments at CCHQ, all working hard on their own projects and schemes, but we are one team and one I feel very proud to be a part of.
Hannah is an artist, author, ex teacher and self-confessed history anorak. She is a trustee for The Mechanics Institution Trust, and education lead for the Railway Village Museum. www.hannahdosanjh.co.uk
Hannah Dosanjh, author and illustrator of A Railway Town Called Swindon thinks more young people should learn about the Great Western Railway Works
The story of how the Great Western Railway Works at Swindon grew from a greenfield site to become the biggest locomotive manufacturer in the world is fascinating.
Daniel Gooch built this success by recruiting skilled labour, and GWR sustained it by training successive generations through apprenticeships. The work was tough, dangerous, and dirty, but the men ‘inside’ developed an attitude to problem solving and innovation that extended beyond the factory walls.
I’d moved to Swindon in 2002, and loved it. It was a bit faded and downbeat but there were some interesting buildings that caught the eye as you walked past. Victorian pubs, Methodist Chapels, streets of terraced housing. But no signs or explanations. Even after steering my children around the STEAM museum I hadn’t grasped the fact that the GWR works at Swindon had covered 300 acres.
It took a pandemic to educate me. I finally had time on my hands to read Alan Peck’s wonderful book “The Great Western at Swindon Works” written shortly before the factory’s closure in 1986. I began to see how much of the original factory had been demolished and built over. Yet although the buildings have gone, we still benefit from the progressive ideas of its engineers.
Brunel needed a railway repair facility roughly half way between London and Bristol. A young Daniel Gooch identified Swindon as being the best place; empty fields near two canals. Work began on a “Railway Village” built directly south of the repair works; with a school, a church, a park for cricket, pubs and basic shops.
The works expanded quickly, but Brunel’s
Railway Village was built too slowly to keep up with demand and its drainage couldn’t cope, which led to outbreaks of typhoid and cholera, compounded by a lack of available fresh water. But the workers were intelligent and practical people, who might have said ‘if life gives you lemons, invent lemonade’ they came together to improve their own living conditions by creating a medical fund. By making paid membership a condition of employment, they ensured this would expand with the factory, eventually offering such comprehensive medical care that Nye Bevan used it as one of his inspirations for the NHS.
Education was important; from the 1840s, the men would swap books, and this quickly developed into a very early public lending library in the Mechanics Institution building which also offered lectures and readings, music, dancing, baths, a café and evening classes for apprentices. Thousands of apprentices learned their trade ‘inside’ and could find work anywhere in the world as their Swindon training was so highly regarded.
Then there was ‘Trip Week’; what started in 1849 as a day trip to Oxford grew to become an annual week’s holiday with free rail travel. 1924 was a record year; 29,000 adults and children crammed themselves onto trains, their luggage travelling separately (but never mislaid) perhaps to visit family in Wales, or relax on a beach in Weymouth or St Ives. Elsewhere in Britain, most working people could not enjoy such perks until 1939.
Closure came, and by then Swindon had taken measures to ensure it was no longer a one industry town. But as the Works shrank Swindon lost its sparkle; while it was a tough life, working inside the factory had
offered community, continuity, pride in a job well done and a reputation for excellence, Swindon families had better healthcare than most, enjoyed educational opportunities, clubs, and leisure activities, and as you can see in the photos taken by William Hooper, the place had a certain elegance.
I have barely scratched the surface. Slowly it dawned on me that if I hadn’t known any of this, how many recent arrivals to Swindon wouldn’t either? A lightbulb moment: write a story that appeals to children, draw accurate pictures, and include two dogs to help tell the story; Isambark Kingdog Brunel and Spaniel Gooch!
I was given the necessary encouragement from Karen Phimister of the Heritage Action Zone, who put me in touch with local historians.
It took two years to complete and selfpublish A Railway Town Called Swindon. I sold through a local bookshop, a wine merchant, two libraries and my website. People liked it, my historian friends liked it, I felt huge relief. Folks born in Swindon to family who had worked ‘Inside’ recognised it as a way to share the story with children and grandchildren; the book had readers from three to 90 years old. But I couldn’t seem to reach readers who had moved here more recently.
As an ex-teacher I had written the book with the classroom in mind with rhymes and funny details. I sent a flyer to every Swindon primary school, offering to visit and talk about our history, and waited. Nothing. Did the flyer go straight in the bin? I tried again by email, but again, nothing.
Last autumn I met Mayor Barbara Parry at a heritage event and explained the problem. Barbara works in a secondary school and is an enthusiastic “joiner upper”. She told me she would love to see one copy of the book in every Primary school in the Borough. Neither of us knew how this might happen, but it felt positive.
She must have spoken to Paul Gentleman. Paul is Deputy Head of External Communications for GWR and a great organiser, and knows everybody; that is no exaggeration. In some ways Swindon still behaves like a small town, not so much six degrees of separation, more two or three. Paul was attending a remembrance service in Radnor Street cemetery when he bumped into the GWR’s grants officer. He put the case to her and she agreed to fund one hundred books – one for every school in the borough.
So, this is my hope; that teachers read the book and decide it might make an interesting topic. Because before long they will find themselves hooked; and perhaps those children they teach will love it enough to go looking for the buildings that are left, and imagine how it must have been. And when they’ve understood the impact the railway had, they might want to protect these heritage buildings, restore them, use them again, and who knows? Become the engineers of the future.
Yvain Cornet, COO of Pulsaart by AGC, oversees the rollout of the company's connectivity solutions in Europe. With vast experience in automotive connectivity and antenna product deployment, he now also leads the implementation of Pulsaart by AGC's rail connectivity solutions, including the innovative WAVETHRU™ Retrofit, across the continent.
How long has your company been in business?
AGC, established in 1907 in Japan, has evolved to become a global leader in glass manufacturing, ranking among the top three worldwide. Beyond its core activities in raw glass production, AGC has been at the forefront of glass technology innovation. Through dedicated research and development, the company has successfully transformed glass into functional materials and active devices, showcasing its prowess in glass connectivity for nearly five decades and demonstrating expertise in customized glass coating.
Tell us about Pulsaart by AGC. Which sectors do you work in and what types of products and services do you offer?
Pulsaart by AGC is a connectivity solutions provider in the mobility industry to a wide range of clients. Established by AGC Automotive, the company is known for its high-quality work in the car industry. Recently, Pulsaart by AGC has also successfully expanded its services to the rail industry, introducing new solutions like WAVETHRU™ Retrofit that improve connectivity inside trains.
Want to know more about Pulsaart by AGC?
Tel: +32 2 409 12 21
Email: pulsaart@agc.com
Visit: www.pulsaart.com/ wavethru-retrofit
Pulsaart by AGC was launched in 2021 by AGC Automotive Europe and is a startup specializing in advanced antenna connectivity solutions on glass. The company offers a wide range of connectivity services and products, including antenna testing, design, and development, serving clients across all mobility industries such as automotive, rail, and aerospace. To the rail companies, we offer glass coating RF treatment called WAVETHRU™ Retrofit.
What are some major projects you’re currently working on?
Speaking of our ongoing projects, despite our primary focus on developing connectivity solutions for automotive OEMs, we are actively implementing the WAVETHRU™ Retrofit solution on trains. Additionally, we are exploring smart city applications.
What are some of the biggest challenges the rail sector currently faces? What are some potential solutions?
One of the rail sector's most pressing challenges is maintaining continuous
connectivity for passengers, as modern trains have coated windows that block the outdoor cellular network signals. Obviously, one of the solutions is to replace such windows with the ones that are already transparent to cellular signal. But it is very cost-ineffective and time-consuming. Besides that, it’s not a sustainable solution at all. However, our WAVETHRU™ Retrofit solution provides an innovative alternative to glass replacement. This service enhances signal strength inside trains by up to 300 times, offering an environmentally friendly retrofit option that is cost-efficient and can be applied on already installed glass.
With increasing passenger expectations for digital services, how can rail companies keep pace with the demand for constant connectivity?
To address the growing demand for digital services and uninterrupted connectivity,
Pulsaart by AGC’s solution is universally compatible, maintenance-free, and durable for the lifetime of the glass, ensuring passenger satisfaction and ease of adoption for rail companies. It is also compatible with all cellular phones and operators. This makes WAVETHRU™ Retrofit a perfect solution to make any travellers happy for all rail companies.
Can you give us an overview of WAVETHRU Retrofit and how it emerged as a solution in the rail industry?
Initially WAVETHRU™ technology was developed by AGC for the automotive market to facilitate the use of sensors behind coated glass in cars. Later it was adapted for the buildings sector and has now proven to be an effective solution for the rail industry by being adaptable to any type of glazing and offering quick and flexible service.
What are the key technical innovations in WAVETHRU Retrofit that differentiate it from other connectivity solutions in the rail industry?
WAVETHRU™ Retrofit distinguishes itself by avoiding the need for glass replacement, offering both economic and ecological benefits. Its superior performance, compatibility with all mobile phone bands and operators, maintenance-free longevity position it as an optimal service solution. Also, our service is customer-tailored to fit rail companies’ maintenance schedules as we perform all the work at our clients’ sites with a speed of one retrofitted train per day.
In what ways does WAVETHRU Retrofit provide value to rail operators?
This innovative service not only significantly improves the user experience and customer satisfaction in the transportation sector but also aligns with Pulsaart by AGC's commitment to delivering high-quality, technologically advanced solutions.
Could you share some success stories or case studies where WAVETHRU Retrofit has been implemented effectively?
Pulsaart by AGC has achieved notable success. One of the recent success stories would be the completion of more than one hundred train treatments for a client who, satisfied with the initial project for 30 trains, requested the WAVETHRU™ Retrofit service for their entire fleet. I believe it’s a testament to our ability to deliver timely and high-quality solutions.
What challenges did you face during the development and deployment of WAVETHRU Retrofit, and what lessons have you learned?
The development and deployment of WAVETHRU™ Retrofit faced challenges in seamlessly integrating our service with train maintenance operations. Therefore, we focus on enhancing the ergonomics of our equipment for flexibility and high-quality glass treatment, with a strong emphasis on safety during maintenance periods.
Which other connectivity solutions can you offer to the rail industry?
As a glass antenna designer and manufacturer, Pulsaart by AGC offers numerous advanced connectivity solutions besides WAVETHRU™ Retrofit. Over the years, catering to different industries, we have developed a series of invisible glass antennas designed to support 4/5G and Wi-Fi communications in MIMO configurations. As seen on the picture, these antennas integrate seamlessly into both new and existing glass panels, optimizing functionality without compromising the glass's aesthetics or the antenna's performance. This innovation not only facilitates signal transmission across different environments but also enhances the visual appeal of windows with its sleek, modern design.
Although not yet applied in the rail industry, this solution has been successfully utilized in buildings to boost office connectivity, suggesting significant potential for enhancing railway communications. The retrofit capability simplifies certification processes and offers a novel alternative to traditional rooftop equipment placements, promising a transformative impact on rail technology infrastructure.
Building on this foundation, Pulsaart by AGC's approach provides an economical solution, particularly valuable to the railway industry where updating communication systems often involves significant expense. By embedding these innovative antennas directly into glass panels, we offer a costeffective and sustainable alternative to conventional system upgrades, avoiding the need for extensive structural modifications or the acquisition of additional equipment. This method significantly reduces both initial and long-term maintenance costs, offering an attractive return on investment. The blend of technological advancement with economic efficiency highlights Pulsaart by AGC's commitment to delivering valuedriven solutions that meet the dynamic needs of modern connectivity.
How do you see the future of connectivity in the rail industry evolving in the next five to ten years?
Looking forward, the future of connectivity in the rail industry over the next five to ten years is poised to prioritize passenger experiences, with a focus on enabling seamless digital interactions. WAVETHRU™ by Pulsaart is set to be a key enabler in this evolution, facilitating advanced signal exchanges between trains and trackside equipment.
Jonathan has been with Milwaukee for over two years, initially as the Rail Specialist where he was heavily involved with NWR and rail end users. He is now the National Rail Manager and leading the team by example and passing on knowledge, continuing to support the company’s end users.
Milwaukee is a multi-national company that develops, manufactures, and markets power tools, hand tools, tool accessories, tool storage, and personal protective equipment.
When did you join Milwaukee and what is your role within the company?
I joined in January 2022 and I’m the Jobsite Solutions National Rail Manager – responsible for managing our excellent rail team and providing solutions to our end users.
What does sustainability mean to you?
Future proofing – ensuring our end users continue to get the best possible service and products continuously. New product and technology enhancements will be developed under our current battery platform. Our end users can then always have the peace of mind that when they invest into Milwaukee, our new battery technology can be used with a tool purchased ten years previously, as well as a brand new tool.
What is your Unique Selling Point?
Our range of product and battery technology within this range. Primarily our M18 (18V platform) that is being used in the rail industry. We have roughly 280 solutions on the M18 platform, therefore our end users don’t have to worry about having different types of batteries or chargers hence improving productivity and manual handling.
What types of products and services do you offer?
Milwaukee has three different battery platforms – M18 (18v) M12 (12V) and MX (72V). These fluctuate from small impact wrenches to big breakers. We offer on-hand Job Site Solutions Support. This is where we attend sites and look at the work they are doing and provide feedback on the solutions they are currently using. We provide demonstrations and trials of our range so that the end user has full confidence that the specific equipment will work in their real-life environment.
Warranty – we give our end users peace of mind that if anything was to go wrong, we offer a free extended warranty for three years on any power tool or lighting and two years cover on our batteries.
What are some major projects you’re currently working on?
‘Milwaukee can potentially look at adding specific HAVs data based on rail applications, so we provide accurate readings based on the work our end users are doing, rather than the worst case solution.’
meetings to go over our range and benefits, one of them including the one-key tool tracking and inventory management system which we offer free of charge and is included in a majority of our range.
When a client comes to you with a particular problem, what’s your process for coming up with a solution, and how closely do you work with clients throughout the projects?
We undertake an initial phone call or meeting to understand our end user’s issues, so we can understand roughly what type of tools we need to be looking at to assist with their issue. Next, we attend site to see what current tool they are using and get an understanding of the actual issue and experience it firsthand.
Being on site is vital to provide them with the best solution possible. After this we can understand how their current solution is performing and compare this against ours to see if ours would suit the application better. We would do this by demonstrating our tool on the application and then allowing the end user to trial it before looking at purchasing to ensure they are satisfied.
What are some of the biggest challenges this sector currently faces?
Product approval – some of our products are perfect for certain solutions but because they don’t have specific ‘on track’ approval it is unable to be used. We base our HAVs on worst case scenario. We might project 18MS2 on a tool but actually on the end user’s application, it could record under 5MS2. However, because it’s stated as 18MS2 it would get knocked back, frustratingly. Also, rail needs to focus more on time on trigger and not HAVs because a tool could take two seconds to do a job and therefore there would be no issues with HAVs but again they knock it back as it isn’t product approved.
Want to know more about Milwaukee (TTI)?
Tel: 07511 222 109
Email: jonathan.abbott@tti-emea.com
Visit: uk.milwaukeetool.eu
The Milwaukee Rail Impact Wrench 1” which we are working closely with Network Rail and ARGIS on in order to get product approval. We have built up a good relationship with NWR to find out what the requirements are to get our products accepted. This is helping Milwaukee bring out more relevant solutions for our end users.
NWR Tender – working with NWR Wales and boarders deal where they potentially primarily use Milwaukee power tool and lighting products. We have undertaken
On the example above, Milwaukee can potentially look at adding specific HAVs data based on rail applications, so we provide accurate readings based on the work our end users are doing, rather than the worst case solution. We have grown from a team of two into a team of seven within the last twelve months which means we continue to work closely with rail end users and take feedback onboard to help with potential solution solving.
Simon Rehill, General Manager at Pulsar Instruments Plc for 6 years, leads the company in manufacturing sound and vibration meters. An Associate Member of the Institute of Acoustics and Technical Member of IOSH, he specialises in noise and vibration compliance, drawing on 22 years in manufacturing to enhance workplace safety.
As noise measurement experts, Pulsar Instruments has been helping companies around the world meet their legal requirements for safeguarding their employees’ hearing for over 50 years by providing affordable, robust, accurate and easy to use noise measurement devices.
‘By working closely with the people in charge of safety, we’re able to tailor our services to meet the unique needs of each sector, ensuring safer work environments across the board.’
efforts, enhancing dealership relationships, and conducting field demonstrations in key regions of the UK and Ireland.
Earlier, with CNH, I handled various responsibilities, from product management in diverse climates to overseeing farm machinery operations on a new farm in Romania. My career began with handson technical roles, working as a service technician and a precision engineer, where I dealt with everything from machinery repair to manufacturing precise components. These experiences taught me the importance of technical knowledge, business strategy, and international collaboration, which have been invaluable in my role at Pulsar Instruments.
Want to know more about Pulsar Instruments?
Tel: 01723 339 715
Visit: www.pulsarinstruments.com
What is your role within Pulsar Instruments?
I am the General Manager at Pulsar Instruments Plc where I've had the pleasure of leading for the past six years. With a rich history spanning over 50 years, Pulsar is at the forefront of sound level meter manufacturing, and I'm proud to contribute to our legacy in sound monitoring.
My passion lies in helping businesses navigate and comply with safety standards like the Noise at Work and Vibration at Work Regulations. As an Associate Member of the Institute of Acoustics and a Technical Member of IOSH, along with achieving Competent Person status in Noise and Vibration assessment, I bring a deep understanding of acoustics and noise control to our work.
My journey over the last 22 years has taken me through various facets of the manufacturing sector, from business management and product development to sales and business growth. At Pulsar, we're committed to making workplaces safer and helping our clients meet stringent safety regulations with ease and confidence.
Tell us about your career before you joined Pulsar Instruments.
Before I joined Pulsar Instruments, my career took me around the world, developing a rich mix of skills and experiences. I spearheaded the UK operations for Airinov AG, setting up a new company from scratch, and diving into the innovative drone sensing market. This role involved building a network, organizing shows and seminars across the UK and Europe, and establishing a strong market presence.
In a previous role as a European Sales Manager for Micron Sprayers, I managed sales across Europe, including the challenging markets of Eastern Europe and the CIS, contributing to product development and organizing international events. My experience also includes working as a Territory Manager for HARDI UK Ltd, where I focused on sales and marketing
What success have you experienced in the last twelve months and how do you measure success?
This past year at Pulsar Instruments has been really exciting and successful. We’ve expanded our range of products to include Gas Detectors and Particulate Monitors, which means we can now help businesses in even more ways. Plus, we’ve started working with new distributors in the Middle East, helping us grow our business further.
One of our biggest highlights was launching two new products: the Pulsar vB², a hand-arm and whole-body vibration meter that’s super simple to use, and the Pulsar Nova Pro, an Environmental Noise Analyser that’s all about giving the user all the data they need for their environmental reports. For us, success isn’t just about these new products and expansions; it’s about making a real difference for our clients.
We measure our success by how much we help improve safety and make compliance with regulations easier for businesses. It’s been a great year of growth and making a positive impact, and we’re looking forward to what’s next.
How long has your company been in business?
Pulsar Instruments started in 1969 in California, created by university experts to make a special sound meter for safer workplaces. Early on, we were the first to show both sound levels and exposure times on our meters, and we kept innovating with new technology and designs. Through the 1970s and 1980s, we made the world’s first linear scaled meter and the first Leq meter, always staying ahead with the latest standards. After becoming independent in 1999, we grew into one of Europe’s top sound meter manufacturers, selling to over 50 countries. Now, as a PLC since 2003, we’re recognized as one of the leading names in sound measurement worldwide.
Which sectors do you work in?
At Pulsar Instruments, we partner closely with Health and Safety managers from a
wide variety of industries to make sure workplaces are safe for everyone. While we’re here to help all sectors, we’ve found our expertise to be especially valuable in a few key areas.
Construction sites, oil & gas operations, and the transport sector often deal with high levels of noise and vibration, making our meters essential tools for them.
But it’s not just these industries we support; any workplace that’s likely to be exposing their employees to high levels of noise and vibration can benefit from our products. Whether it’s a manufacturing plant, an entertainment venue, or even a busy warehouse, we’re committed to providing solutions that help keep noise and vibration at safe levels. Our goal is to make sure everyone can go about their work comfortably without worrying about health risks. By working closely with the people in charge of safety, we’re able to tailor our services to meet the unique needs of each sector, ensuring safer work environments across the board.
What types of products and services do you offer?
At Pulsar Instruments, we offer a variety of tools designed to keep work environments
safe. Our products include sound level meters, which help monitor and manage noise levels to protect workers’ hearing. For individuals concerned about their personal noise exposure, we have noise dosimeters that can be worn throughout the day. We also provide vibration meters to assess the risk of injury from using vibrating tools or machinery. Additionally, our lineup features gas detectors for measuring exposure to harmful gases, audiometers for hearing tests, and particulate monitors to check air quality. These tools are essential for ensuring workplace safety and health compliance in various industries.
What are your views on collaborative working?
Working together with our partners around the world is a big part of why we succeed. It helps us understand what different places need and make sure our products fit right in. Also, teaming up with new companies to bring more products into our lineup is great for staying ahead and bringing in fresh ideas. This way, we can offer more to our customers, improve what we sell, and get our products out there faster. Collaborating like this helps us grow, keeps our customers happy, and makes us stand out in our field.
How do you make your business a good place to work?
Making our business a great place to work is all about trust, support, and communication. We believe in giving our employees the freedom they need to do their jobs well. This means trusting them to make the right decisions and allowing them the space to bring their own ideas and solutions to the table. But freedom doesn't come without support. We're committed to providing our team with the training they need to grow and succeed. Whether it's learning new skills, advancing their knowledge, or exploring new areas of interest, we want to make sure everyone has the opportunity to develop professionally.
Clear communication is another cornerstone of our workplace culture. We strive to keep the lines of communication open across the entire company, ensuring that everyone, from the newest recruit to the most seasoned executive, is on the same page. By fostering an environment where information flows freely, we help prevent misunderstandings and build a stronger, more cohesive team.
How did you get started in the industry?
I started to work for CRC Industries in 2016 as an end-user focussed Sales Manager in the North-West, working closely with several regional and national rail operators, rolling stock manufacturers, and train maintenance depots.
Michelle is a Marketing Manager based in the United Kingdom. Having worked with the rail sector at CRC Industries for a number of years, she has developed a keen interest in innovations within rail, particularly green technology and sustainability.
After completing a master's in international business leadership and management, in 2024 I moved from the sales team into marketing where I am now the EMEIA marketing manager for the SmartWasher brand. The SmartWasher bioremediating parts washer has strengthened the relationship between CRC Industries and the end user, by offering a truly valuable and sustainable proposition.
While some may associate sustainability solely with protecting the environment, to me the meaning of sustainability runs much deeper. It is vital that the environment is protected, and we should be conscious of our impact when undertaking our activities in our personal and working lives. Aside from the environment, sustainability is the key to ensuring that we can do tomorrow what we do today. This means having robust corporate social responsibility (CSR) procedures in place, protecting internal
and external organisational stakeholders, creating a culture where everybody plays their part to continuously improve to protect the future today. Whether this is by optimising work patterns for employees, reducing consumption of single use plastics, or simply choosing to walk or cycle instead of driving, we can all contribute.
How long has your company been in business?
CRC Industries has been in business since 1953, having started in the USA as a single product development and manufacturing company, it now has multiple manufacturing sites around the world, supplying over 2,000 different products to >3,000 customers in Europe and UK. In 2004 CRC acquired the well-known and respected aerosol manufacturer, AMBERSIL LTD which has been serving professional, industrial, user for many decades. Now, with the Ambersil brand in its 75th year – CRC has broadened its product portfolio through the global acquisition of the bioremediation ‘SmartWasher’ brand; delivering a one-stop solution for engineers.
Many manufacturers supply similar products to CRC Industries; however, CRC is the leading manufacturer focussing its brands on the maintenance department at the end user. With an enthusiastic and proactive research team continuously monitoring legislation and application trends, a dynamic sales team, and strong distributor network CRC remains committed to supplying products to help the user get the job done.
What types of products and services do you offer?
CRC offers a broad range of products, specialising in cleaning and degreasing solutions, backed up with lubricants, greases, oils, and anti-corrosion products. The addition of SmartWasher to the product portfolio has enabled us to provide new, sustainable, technology to our customers that meet their requirements for reduced environmental impact, enhanced user safety, without compromising on performance. Engineers can spend time on their scheduled maintenance commitments knowing that CRC SmartWasher with Ambersil provides trusted performance and nationwide availability.
How have the products and services you offer developed over the years?
Everyone is aware of the importance of the environment and ‘sustainability’ in all aspects of our lives none more so for professional users. The legislative and regulatory impacts alongside corporate social responsibility (CSR) and environmental social governance (ESG)
initiatives launched by forward-thinking organisations means that there has been a dramatic shift in the requirements for suppliers of products into the rail industry. Whether it is biodegradability, elimination of SVHC’s (substances of very high concern) or organisational level changes, such as facilities running on 100 per cent renewable energy; these combine to impact and influence our offer to the market.
Our chemists have developed biodegradable formulas for popular products, whilst parts washer cleaning technology has moved forward from solventbased to bioremediation. The evolution and innovation of products never stops, yet always retains the underlying top-line performance demanded by users.
How passionate are you about sustainability in the rail sector, and how do you go about sourcing the materials for your products?
I am passionate about the development of green technologies which improve outcomes not only for rail users, but also stakeholders in the rail sector and wider community. The rail sector is a critical part of daily life for many, and sustainable practices and materials allow the sector to improve and develop. Our chemists are in close partnerships with raw material suppliers and are continuously developing formulations which allow operations to continue, whilst minimising environmental impact.
When a client comes to you with a particular problem, what’s your process for coming up with a solution, and how closely do you work with clients throughout the projects?
As a manufacturer we work with an extensive number of distribution partners, whilst maintaining a close relationship with end-user clients. Whenever a client comes to us either directly, or through a distributor, with a particular problem, we visit the site to discuss the problem and, where possible, view the problem in-situ. For example, a member of the team visited a rail manufacturing site where the client had an issue with a critical component rusting during operations in harsh weather conditions. We discussed suitable anticorrosion products and initiated trials. After a successful trial period, the problem was resolved, and a new procedure was written into the company maintenance handbook. The client subsequently reviewed the rest of their chemical usage and invited us to provide a cost-saving and performance improvement on a degreasing application.
How do you work with the supply chain within this sector?
Collaboratively: we love it! Working with distribution partners such as RS Components, Rubix, Cromwell, Hayley/
Hayley Rail, Eriks and many independent distributors who have a relationship with the engineers; we are often requested to visit a site to undertake specific problem-solution recommendations, or even general chemical audit to remove duplicate products and nonapproved products on site.
Some of the most enjoyable collaborations are when we deliver a specific solution that excites the user so that they specify a product and recommend it to other sites as a real benefit, such as with our SmartWasher bioremediation parts washer at a leading rolling stock manufacturer in the North of England to replace a monthly contract solvent unit. Working with the user and their preferred supplier; together, we get the job done.
Do you think the rail industry could be greener and what is your organisations green strategy?
There is always room for improvement when it comes to environmental impact, but specifics often differ based on locations, policies, and real-world application limitations. The key takeaway is an organisational culture where environmental improvement, along with social responsibility, and robust, ethical, governance allow the space for forwardthinking initiatives to be given the consideration they require.
Here at CRC, we have once again passed an EcoVadis ESG audit and been upgraded to the silver medal. EcoVadis is the leading provider of ESG audits globally, and the silver medal represents a top 25 per cent position for CRC, globally. So strong is the belief in a ‘greener’ way of doing things at CRC; we have appointed two new ESG coordinators to assist our European ESG Director; as well as launching the dedicated ‘Green Force’ range of products that must meet at least six of nine environmental or user safety science-based criteria. We are investing for the long-term.
At some point, every company will face the question of how to continue maximising earnings from their current business practice whilst also investing enough in innovation so they can turn a profit in the future. How can a company achieve the necessary creativity to innovate without compromising their existing business?
Companies should continue to innovate to stay relevant. Innovation is not necessarily large and may often be evolution rather than revolution meeting changing demands in the market. It is certainly the case with maintenance solutions that there is a dual pressure from the need to meet (or exceed) user requirements as technology changes, as well as the updating of legislation that often results in the reclassification of raw materials.
These pressures may be somewhat unique to the chemical sector and the
‘There is a dual pressure from the need to meet (or exceed) user requirements as technology changes, as well as the updating of legislation that often results in the reclassification of raw materials.’
manufacturing of MRO solutions, yet they often deliver a dual benefit to engineers: safer products without performance compromise whilst delivering the added benefit of verifiable reduced environmental impact. An innovation mindset and openness to new ideas is a critical first step on the innovation path. Whilst not all ideas make it through the evaluation process; a ‘no’ today, may be the differentiator of tomorrow.
CRC Industries produces a complete range of cleaners, lubricants, corrosion inhibitors, protective coatings, degreasers, greases, additives, and specialty products which have been tailored for specific customer maintenance and repair needs. Today, CRC manufactures, sells, and distributes its products worldwide.
Want to know more about CRC Industries?
Address: CRC Industries UK Ltd Ambersil House, Wylds Road
Castlefield Industrial Estate Bridgwater Somerset TA6 4DD England
Tel: 01278 727272
Email: sales.uk@crcind.com
Address: CRC Industries Europe BV (Belgium)
Touwslagerstraat 1, BE-9240 ZELE België/Belgique
Tel: (+32)52/45.60.11
Email: marketing@crcind.com
The engineering and infrastructure sector is developing at a rapid pace. There has been growth over the past decade, with the number of people working in engineering increasing from 5.4 million in 2010 to 5.7 million in 2021, with a peak of 6.3 million in 2019
On top of this, the UK is ramping up its focus on becoming a net zero economy, and a report commissioned by Engineering UK found that demand for engineers is predicted to grow faster than for other occupations, with vacancies for ‘green engineering’ roles increasing by more than half (55 per cent) over the last five years.
In light of this, the report also found that recruitment activity for engineering roles accounted for a quarter of all job postings in the UK, pointing toward a rising concern that has been looming in the engineering sector: skills shortages. These findings suggest that the skills gap is either greater in engineering than in other sectors, that employers are hiring for future growth or a combination of the two.
Jonathan Hornagold, Apprenticeship Manager at Amey – a leading provider of full-lifecycle engineering, operations and decarbonisation solutions for transport infrastructure and complex facilities – agrees with this, explaining how the speed of digital and IT is impacting the engineering industry. He tells us: ‘Keeping pace with the changes that are occurring in the engineering industry – and beyond – is certainly a challenge for many businesses.
‘We want to ensure that we continue to serve those we work alongside with the best, most up-to-date solutions. Our purpose is to deliver sustainable infrastructure solutions and to protect our shared future; upskilling, therefore, is a massive part of that. We want to be able to keep pace and traction when it comes to serving our clients and the public, while simultaneously meeting our employees’ needs.’
With the engineering industry becoming increasingly competitive, it is not surprising that many in the sector are fighting for the right people to stay. Talent retention is growing in importance, with many businesses in various sectors looking towards how they can invest in their employees.
On top of this, the engineering industry experiences employee turnover at a greater rate than most other sectors. According to LinkedIn data, the tech and media industry has the second-highest turnover rate; this not only places more value on talent retention but actually points towards the sheer importance of effective leadership. In fact, it has been found to be among the top business skills prospective employers in the engineering industry seek in candidates.
Expanding on this is Stacey Allen, Director of Corporate Partnerships at Arden University. She says: ‘Upskilling serves a twofold purpose: it keeps businesses relevant in a rapidly transforming economy, while also showing that your business is investing in and cares about your employees’ development and career goals. This, in turn, helps with talent retention. More engineering companies need to take advantage of this.
‘But employee happiness trickles down from leadership teams. With senior leaders directing the way, it’s vital that they refine their skills to ensure they’re matching business needs to push forward in a tough climate. With the industry needing more and more specialised talent to compete effectively, showing you can invest in your employees’ career growth is a great way to keep people on board.’
Closing the leadership gap
Jonathan shares how he is helping his team at Amey to upskill through apprenticeship degrees. With many engineering qualifications often leaving graduates with the technical skills but none of the soft skills needed to progress into management and leadership roles, he wanted employees to progress through apprenticeship degrees.
‘The Level 7 Senior Leader Apprenticeship Degree allows our employees to develop the management skills needed to progress upward in Amey’ explains Jonathan.
‘We also wanted the culture of learning to trickle down to the rest of the business, so getting our team to learn and develop at a senior level will hopefully set the tone for more junior members of our team to also get stuck into lifelong learning.
‘This is not a ‘tick box’ exercise. We want our employees to demonstrate and put into practice what they’re learning in the workplace and exercise that learning within our business – and apprenticeship degrees are perfect for that.’
Working alongside Arden University, Amey has placed several employees on their Level 7 Senior Leadership Apprenticeship Degree. Covering modules such as managing digital transformation and innovation, and leading global teams and organisations, this senior leader apprenticeship helps businesses refine and sharpen their employees existing skills.
Stacey shares: ‘What makes a Level 7 Senior Leader Apprenticeship different is that the delivery of our course is blended into day-to-day work. Our apprentices
attend live sessions with academics and have an assigned professional coach who will have virtual meetings to help support them in turning workplace experiences into learning experiences.
‘Once apprentices have successfully completed our programme, they’ll be awarded an Executive Master of Business Administration (EMBA) qualification, as well as the Chartered Management Institute Diploma in Strategic Management and Leadership Practice. They will also receive an accreditation from the Chartered Management Institute, offering them the opportunity to obtain the professionally recognised status of Chartered Manager. These qualifications can really make employees stand out. But more importantly, it will prepare them for a step-up role at Amey.’
There are practical aspects involved when it comes to upskilling in the engineering sector. As Jonathan tells us: ‘We needed a flexible approach for our employees
due to them working in demanding roles. Studying online means if they’re commuting throughout the UK to be on-site for work, they can still log on and study – something which was really important for my team.’
This also opens up access to education. For those with families to take care of, or even those unable to personally fund an MBA, an online apprenticeship degree with Arden can provide them with the opportunity to build their skillset and grow. This, in turn, can help with solving other issues the engineering industry is currently facing, especially the need to improve diversity.
‘With how fast changes are occurring, and how quickly the industry needs to respond, upskilling our employees is definitely a strong and much needed approach for us at Amey. It’s served us well, and we are hoping to get more of our people involved and partnering with Arden University, to hopefully mitigate the risks that come with the growing skills gaps’ concludes Jonathan.
The Occupational Psychology Centre (OPC) sheds some light on why some employees find it hard to stick to the fundamentals of safety and considers the importance of creating a culture of accountability and risk awareness
Safety incidents in the rail industry can have severe consequences, especially for safety-critical employees like track workers, engineers, shunters, and train drivers. The nature of their roles can put them in ‘harm’s way’ at the forefront of potential risks. Even minor safety lapses could lead to catastrophic incidents like personal injury and harm. Or, it could have a wider impact, jeopardising passenger safety or railway integrity.
In some organisations, safety performance can fluctuate over time. There may be periods of high accidents or incidents frequency, prompting safety training or a new initiative, resulting in improved safety focus and a subsequent
decrease in incidents. However, sustained improvement may not continue, leading to a cycle of rising and falling safety performance interjected by safety initiatives.
Laura Hedley, a Senior Occupational Psychologist at the OPC said: ‘As a team of safety-specialist psychologists, in our experience, while poor safety performance can stem from various factors like insufficient equipment or training, human factors are often a primary cause. While most individuals get it right, sticking to safety protocols, we're all prone to mistakes. However, in safety-critical roles, even minor errors can have significant consequences compared to other positions. In many cases, incidents can occur simply because we just don’t get the basics right.’
When we refer to the basics, we mean the fundamentals of personal safety. This includes ensuring any necessary Personal Protective Equipment (PPE) like hi-vis gear, protective trousers, and goggles are readily available for the job.
It's important that all necessary equipment is in good working condition and regularly maintained to minimise the risk of accidents. Any equipment faults or hazards should be promptly reported and escalated if not resolved. A full safety briefing should always precede any work.
Always abiding by the rules is a fundamental. Industry regulations have been devised over years of safety experience and are in place for the protection of
everyone—employees, contractors, and customers alike.
Prioritising safety over any work, time, or commercial pressures is crucial. It means having the right people assigned for the right task, and balancing the tension between safety and service delivery.
Laura said: ‘The Non-Technical Skills (NTS) of vigilance and conscientiousness also play a key role in the basics of safety. Sometimes, seemingly inconsequential things like leaving tools behind, an incomplete job or an untidy site can cause an incident. Risk awareness and situational awareness are also crucial. Assessing for risks, especially personal risks like fatigue or stress prior to work is vital. In the OPC’s experience, incidents often result from a buildup of small, cumulative risks rather than a single factor. Employees with a heightened awareness of potential hazards and their consequences are much better equipped to identify and manage risks effectively, reducing the likelihood of an incident.”
What prevents us from mastering the basics of safety?
Fundamentally, our own fallibility and some specific human factors tend to get in the way. Based on research and insights gathered when undertaking hundreds of Post Incident Assessments (PIA), OPC psychologists identified several recurring themes:
• Effort vs payback.
• Balancing the job vs. the basics.
• The trap of self-reliance.
• Why bother!
• A false sense of security.
• Not my responsibility!
Effort vs payback. Sometimes it’s tempting to take the path of least resistance. When we’re under time pressure or something interferes with pre-planning it can be more tempting to ‘skip the basics’, forget safety rules and protocols, leading us to prefer convenience over compliance.
Balancing the job vs. the basics. Sometimes it may seem easier to prioritise the task completion – to get on with it, and get it done – rather than ‘waste time’ focussing on the safety fundamentals.
The trap of self-reliance. It can be easy to be deceived ourselves into believing we know everything, being self-reliant in our own abilities. Just because we’ve never had an incident or ‘near-miss’ previously we think that everything will be ok – therefore I don’t need to focus on the safety basics.
Why bother! When there’s been a lack of positive action regarding a safety or hazard request, it can breed a sense of futility and apathy, meaning people just give up and stop reporting a risk. We need to generate a culture of ‘safety is everyone’s responsibility’ not just for front-line employees.
A false sense of security. Failure to recognise risks properly can give an illusion of reassurance. Just because risks haven’t been spotted or acknowledged doesn’t mean
there aren’t any. Over-confidence can hinder us sticking to the safety basics and adhering to the rules.
Not my responsibility! Lastly, this pervasive attitude can mean a culture of disengagement and neglect, leading to a failure in getting the basics right.
Laura said: ‘Most of the time, people try hard to act in the right way and make sure they get the safety basics right. However, we’re only human! And we can and do make mistakes, but recognising and being aware of this fallibility is essential. It helps us understand why we make errors. It’s also crucial for individuals to speak up and voice their concerns when mistakes are made –whether organisationally, in the team or at a one-on-one level, regardless of their seniority. This helps to ensure any unsafe behaviour is addressed.’
Why do we find challenging so hard?
Challenging an error around the basics of safety at an organisational level is a lot easier to do than challenging an individual about their safety behaviours.
Laura pointed out: ‘Putting a report in about an asset like a faulty piece of equipment, a broken rail, or unavailable flashlights is a lot easier and less effort than challenging an individual about their unsafe behaviour or safety mistakes. Sometimes people wait to see the outcome before making a challenge – holding out to pluck up the courage, and reflecting on the potential impact to their relationships.’
Through our work over the years, we have identified some of the key reasons why people may not want to confront others.
Fear of reprisal or negative consequences from speaking up, especially if the person committing the breach is in a position of authority over the employee. This may extend to disbelief that more senior or experienced individuals could have committed a safety breach.
Fear of rejection or ridicule and how others in the team may perceive an employee after a safety breach report.
A fear of being misunderstood
Worry about damaging relationships or creating conflict within a team by addressing safety concerns. This may be especially pertinent if the colleague is a friend, not just a work colleague. A contractor might worry about their future job opportunities if they raise a concern.
A lack of self-confidence may inhibit people from challenging a safety breach in others. A lack of confidence in their own knowledge or understanding of safety protocols can lead to hesitancy in challenging others. Similarly, a lack of self-assertiveness can mean some people are filled with horror at the prospect of having to challenge another individual.
Some people prefer to be ‘followers’ rather than ‘leaders’ and would never consider challenging someone on their behaviour. Being a ‘people pleaser’ and sacrificing a safety challenge to avoid upsetting someone or not wanting to ‘rat on my mates!’
If there is a prevailing norm of overlooking safety issues or prioritising productivity over safety in the organisation, people may be less inclined to speak up. If safety issues are persistently disregard then this can foster apathy in reporting along with a general feeling of futility.
Overall, a combination of fear, social dynamics, confidence levels, and organisational culture can contribute to the reluctance to challenge safety breaches, but it’s good to keep in mind that our colleagues are our ‘railway family’. In a recent project, OPC Psychologists asked over 600 rail workers, many of whom work together closely, about their willingness to have
‘In the realm of safety, risk awareness and sticking to the basics go hand in hand. Safety is everyone's job. It's about consistently choosing the path of diligence over convenience.’
Laura Hedley, Senior Occupational Psychologistat the OPC
someone point out their safety mistakes to help their personal safety and that of others. Happily, over 90 per cent said they’d prefer to be told.
It’s also important to be aware of our ‘duty of care’ in a legal context. Under UK health and safety legislation, failing to uphold safety standards can have serious legal ramifications. From criminal charges to civil suits, individuals can find themselves in legal jeopardy if they neglect their duty to ensure workplace safety. Section 7 of the Health and Safety at Work Act 1974 places the onus on organisations and employees— including contractors—to take reasonable care of their own health and safety, as well as that of others.
Doing things differently
It's about taking personal responsibility. Each employee proactively recognising they're responsible not only for their own safety but also for that of their colleagues. Whether it's speaking up about unsafe practices, reporting a fault and escalating it if unsolved, or going the extra mile to ensure
‘Making the workplace safe isn't just down to one person—it's about all of us looking out for each other. We need to be willing to speak up and hold each other accountable, even if it means a difficult, uncomfortable conversation. The stakes are high.’
A Maintenance Delivery Manager
the rules are followed, everyone plays a part in better, safer and more effective working.
A Maintenance Delivery Manager said: ‘Making the workplace safe isn't just down to one person—it's about all of us looking out for each other. We need to be willing to speak up and hold each other accountable, even if it means a difficult, uncomfortable conversation. The stakes are high. Potential consequences of safety breaches, such as fatalities or legal accountability highlight the importance of this collective responsibility. That's why we need to create a culture where safety is everyone's top priority.’
The OPC offers various training programmes designed to help improve safety performance. Among these are NonTechnical Skills training, a Back-to-Basics workshop and an Accelerate Your Safety Leadership (AYSL) workshop. The AYSL initiative helps safety leaders to critically examine their operational safety behaviours from a legal perspective; explore safety culture and leadership, and provides an opportunity to improve personal and organisational safety-critical responsibilities and leadership.
Laura concluded: ‘In the realm of safety, risk awareness and sticking to the basics go hand-in-hand. Achieving the best safety standards isn’t just about following the rules
and completing training; it’s also a collective commitment to personal responsibility and having the courage to speak up when needed. It's about taking personal responsibility, displaying courage, and consistently choosing the path of diligence over convenience. Safety is everyone's job. Ignoring it has serious consequences. It isn't just a legal obligation – it's a moral imperative.’
Contact the friendly OPC team if you think your employees need some support getting back to the basics of safety.
Tel: 01923 234646
Email: admin@theopc.co.uk
Visit: www.theopc.co.uk
Norbar is a UK manufacturer of battery, electric, pneumatic and manually operated torque multipliers, wrenches, torque measurement equipment and bespoke torque control solutions specially developed for the rail industry
The rail industry is preparing for new activity, and reflecting on CP6, during which the industry faced significant challenges, from Covid-19 lockdowns to inflation and increased extreme weather events.
Looking ahead, ensuring the longterm success, continuity of service, safety and sustainability of the network is a key priority for Network Rail and Office of Rail and Road (ORR). Continued work on electrification is expected, alongside a program of maintenance and renewals focused on ensuring climate resilience. At the same time, limited funding makes efficiency and cost-effectiveness a top priority. Everyone in the sector will be expected to work smarter in CP7 and make the most of every pound available.
Collaboration and efficiency developed during the current period will be a key factor in future success. During CP6, there has been a growing trend for specialised, small-scale civil engineering consultancies to team up on projects to compete with large
industry players; equipped with specific expertise, these smaller firms working in collaboration offer creative, innovative, and cost-effective solutions to complex rail construction projects.
To explore why this is so, Whitfield Consulting Services (WCS) gathered a couple of its regular partners for a round-table discussion. Our Associate Director Nick Lowe was joined by Lindsey McKerlie, Head of Design at Andromeda, and Craig Anger, E&P Portfolio Manager at J. Murphy & Sons.
As part of the UK government’s ambitious Decarbonising Transport plans, rail electrification is key to end the use of dieselpowered trains by 2040 and deliver a net zero network by 2050. As regular partners on a wide range of rail civil engineering projects, our teams have extensive experience collaborating on a variety projects, including on the substations needed to deliver these goals.
Reflecting on the value experience brings, Nick commented: ‘Substation structures and foundations can be designed by any civil engineer. But, do they have the specific experience to allow them to properly consider how equipment – such as the transformer – will be brought onto site? Planning around the most suitable approach road, and whether there is room to turn into the location, can easily be overlooked, for example, if the engineer hasn’t witnessed this first hand in the past.’
Concurs Craig: ‘I prefer to work with SMEs due to the specialist knowledge and experience they bring. In fact, every supplier I have as a regular partner currently is an SME. On a recent project for example, a bigger consultancy was interested in supporting us, but acknowledged that none of their team had specifically delivered the design required. Looking to smaller suppliers, I saw experience in similar projects again and again in their tenders. It just made sense to offer it to them. They will get it done quickly and well.’
Smaller organisations also have less managerial overhead to recover, and less red tape slowing communications. ‘We tend to be very accessible,” comments Lindsey, “and WCS is the same. I know I can pick up the phone and get Nick or Asa, and I know that if Nick is mentioned on the tender, he will actually be the engineer on the project. That’s not something you can assume with larger consultancies.’
This reduction in red tape can permit more flexibility when deciding how to complete a project, though compliance and safety, of course, remain paramount in all cases.
‘With the smaller partners, I have found myself saying that some required change or addition to the scope is urgent, and asking if we can just implement it so as not to impact programme and then agree the finer details of the commercial aspects as we go along’ says Craig. ‘That wouldn’t be possible with a larger firm.’
He does acknowledge that a relationship of trust is needed for this to be possible. ‘It’s always a two-way street. We look after our regular partners and ensure they are treated fairly on every project. We wouldn’t get their flexibility or commitment in return without that. That’s true partnership and commitment on both sides to getting a
project delivered as seamlessly as possible, with the best outcomes always front of mind.’
Adds Nick: ‘Just yesterday I attended a meeting where it became clear there was insufficient survey information. Access to the site was also limited, so I said the best thing would be for us to attend on an upcoming weekend. It was no problem; the project needed it.’
Often, our partners have worked with individual members of our team for some time, building strong relationships. This applies to the interactions between SMEs as well as those between client and consultant. ‘We each have our expertise, and we trust each other’s judgement’ says Lindsey.
Again, Craig is quick to emphasise the two-way nature of the commitments needed. ‘When I am pitching for a project, I don’t just sell Murphy, I sell the team. I name the SMEs that have delivered before on similar projects, and that I will be using again.’
Smaller consultancies may also be more willing to challenge assumptions or propose new solutions to problems. Craig raised the example of a recent rail substation project. WCS had identified a design approach that would simplify the foundations work required, but it was incompatible with the standard and accepted designs for the 25kV substations involved.
‘We found an alternative supplier, an SME themselves, and I was able to offer my client – Network Rail – a quicker, more cost-effective solution’ he explains. ‘They supported us on this less tried solution because they saw the benefits it would bring to the project, and that the same SME team would be able to offer the same solution for new projects with little adaptation.’
We believe the future of rail, and engineering generally, lies in collaborative teams, where small specialists combine to offer what no generalist can. The upcoming CP7 period will bring fresh challenges which we can overcome together, in partnership.
Lindsey McKerlie is Head of Design at Andromeda, an SME specialising in Overhead Line Equipment, Low Voltage & Plant, and Signalling design. Lindsey worked for Network Rail on maintenance and infrastructure projects, including the West Coast Main Line and Great Western Main Line schemes before joining Andromeda in 2013 as Senior Project Engineer.
Business leaders have hailed the news that works on the Bletchley to Bedford section – the Marston Vale Line (MVL) – of East West Rail will be bought forward. The Government reaffirmed its commitment to delivering EWR in full in the 2024 Spring Budget by announcing that £240 million in existing funding would be made available to fast-track works on the MVL.
These works will enable passenger services between Oxford to Bedford (EWR Phase 2) to start by the end of the decade as a supplement to services on the first phase of the project between Oxford and Milton Keynes/Bletchley, which are due to start next year.
Nick Lowe is an Associate Director at Whitfield Consulting Services (WCS), an SME civil engineering design company serving numerous tier 1 contractors and other clients across the rail and power & energy industries.
Craig Anger is E&P Portfolio Manager at J. Murphy & Sons, a leading global, multi-disciplined engineering and construction company, working across all key infrastructure sectors; transport including rail, highways, aviation, and ports; water; power; communications; and natural resources to deliver sustainable solutions.
This investment will allow people living between Oxford and Bedford the chance to reap the benefits of EWR much sooner than originally planned. It will improve access to innovation and economic hubs in Oxford, Bedford, and Milton Keynes, boosting connectivity and unlocking productivity across the region as well as allowing better access to jobs, education, healthcare and leisure opportunities.
The accelerated works will bring forward level crossing works, track and signalling upgrades, as well as safety and accessibility improvements to allow a one train per hour service between Bletchley and Bedford.
Richard Tunnicliffe, Regional Director (East of England), Confederation of British Industry, said: ‘East West Rail will be a key driver of economic prosperity, providing businesses with the confidence to invest in the area with the prospect of greater connectivity, giving greater accessibility to more trade and a larger labour market. This can only be a good thing for business in the region and we look forward to its many benefits.’
Virtual Reality (VR) has been making waves throughout various industries, however its potential in the Rail Industry seems to have been overlooked
Virtual Reality has the potential to revolutionise our onboarding here at GeoAccess, providing a more thorough, immersive, and effective learning experience. The current GeoAcademy serves a crucial role in working alongside traditional classroom learning, therefore providing greater opportunities for hands-on, practical training on site. With the earthworks industry experiencing significant expansion and heightened demand, ensuring proficient and streamlined onboarding training methods is important. In response to this, we are actively enhancing our training capabilities through our new Virtual Reality training tool, in order to meet the evolving needs of our industry.
Using VR offers many benefits to replace the first day of our onsite training. First and foremost, it provides a safe and controlled environment to guide trainees in the right direction in their preparation for onsite training. VR also allows for a more immersive and realistic experience, which will enhance their learning, as trainees can interact with their surroundings by answering questions, learning key takeaways and practicing getting into a good working rhythm when examining a site efficiently. The site that we choose allows users to experience many earthworks features but also assists by allowing them to encounter safety hazards along the way, which in turn, prepares them for tricky conditions and situations when out on site.
Mark Coleman, Co-founder and Managing Director at GeoAccess says: ‘Our VR training provides a really important step between learning in the classroom and being out on a live railway for the first time. From the comfort and safety of a controlled environment, the user embarks on an interactive immersive experience, guided through the stages of conducting an Earthworks Inspection in line with the
Network Rail standards. Being exposed to multiple features in one scene enables the user to get their eye in quicker on the more technical aspects of an inspection. Having full control over the weather conditions and sounds encountered, all senses are engaged making it as realistic an environment as you can besides being out on site.’
The VR can be used in many ways with our examiners either being sent their own VR package, including a headset that can be used at home for the full experience or used on their laptop/mobile devices. This is a benefit to our examiners as travelling from all corners of the country can be time-consuming, whereas with this technology, it’s easier to get them prepared in advance for their training out on site.
Joint Venture
Techcare Digital and GeoAccess are embarking on a pilot project to enhance the current GeoAccess digital academy framework with an innovative VR training tool. Jamie Dorrance, Co-Founder of Techcare Digital says: ‘This advanced platform, which merges immersive 360-degree videos with interactive functionalities, is designed to provide a versatile training experience accessible on desktop, mobile, and virtual reality devices. By enabling real-world rail scenario simulations in a virtual setting, the project aims to significantly improve learning engagement and operational efficiency across various user platforms. This initiative reflects Techcare Digital’s commitment to pioneering digital innovation and GeoAccess’s drive to refine training methodologies. It promises a transformative approach to traditional training, ensuring staff are better prepared and more effectively trained, while offering the flexibility to learn from virtually anywhere.’
Once completed, we can then analyze the data, to determine which areas of the experience people are struggling with, and which touchpoints they are using for longer, which will provide us with the information on where to focus the future development of the Academy website. As this is one of the first, if not the first VR implemented in our industry, using this data and feedback from our examiners during the production stage is key to adapting the experience to their ways of learning, and of course, for future projects.
Our vision for the GeoAcademy is incredibly ambitious, aimed at revolutionising the earthworks industry by extending our training to a multitude of individuals. In addition to our cutting-edge VR technology, our website will serve as a dynamic platform, offering timely and comprehensive training through a blend of engaging videos and interactive assessments.
As the demands for performance, efficiency, safety, and sustainability grow, so do the challenges that confront rail operators and engineers
In this challenging environment, cooperation between organisations can be harnessed to help the rail sector not only navigate these challenges, but to innovate and excel. Embracing innovation is essential for delivering efficiency and productivity to meet the complex demands of modern rail systems. Recent major advancements in machine learning and data analytics have resulted in digital skills and data science becoming invaluable for optimising processes and innovating. Typically, no single organisation
has all the skills and connections within the rail sector to implement these novel solutions. Within Frazer-Nash Consultancy, collaboration across diverse stakeholders and supply chains is standard practice and required to solve our client’s problems.
Frazer-Nash is a leading engineering consultancy at the forefront of leveraging data science and machine learning to tackle real-world challenges across the transport, defence, and energy sectors. Their teams of data scientists and engineers have extensive experience in the optimisation of operations
and enhancing decision-making processes. As increasingly large amounts of data are generated, these skills – required to make sense of data and build tools for predictive analytics and informed decision making – have been increasingly in demand by customers.
Through two case studies, we uncover the transformative impact that collaboration between organisations, each bringing their own specialist skills, can have towards innovation within the rail sector.
Rail possession management is central to the safe and efficient delivery of Network Rail’s programme of maintenance and renewal works in 2024 and beyond. Possession management revolves around delivering essential works in and around the track, often requiring the diverting, blockading, and restricting of services across the rail network.
Handing back the track on time after engineering works is vital to allow services to make their journeys as planned. With increasing pressure and congestion in the rail timetable the opportunities for possessions are less obvious and the potential for delays to freight and passenger services heightened. Enabling Network Rail and their contractors to better manage and mitigate their risks from the planning stages right through to delivery is crucial to allowing the whole rail network to run to time and schedule.
eviFile has delivered a real time possession management solution for Network Rail covering multiple projects across the UK, for Tier 1 contractors such as VolkerRail and Alstom, and the entire Transpennine Route Upgrade. The possession management solution acts as the single source of truth, enabling auditable data to be collected and visualised live across possession activities including access times, activity completion and quantitative tracking.
Having met at the 2022 Railway Industry Association Innovation Conference, both organisations recognised that by combining their complementary expertise, they could offer a game changing advancement in how possessions are managed. The combination of Frazer Nash’s machine learning and data science principles with eviFile’s rich insight and field data engine provides a unique opportunity to collate, manage and provide actionable recommendations to possession planners.
Funded by the Department for Transport through a Small Business Research Initiative First of a Kind grant, Frazer-Nash Consultancy and eviFile worked together to develop a possession optimisation and forecasting tool to revolutionise the understanding and management of rail possession planning and delivery.
Using rich historical possessions data collated by eviFile, FrazerNash developed an AI toolset that leverages advanced statistical methods to create a digital twin of live possessions. Given live trackside data fed from the eviFile platform, the tool makes forward predictions on the likely completion time of all activities using learned historical experience, and sensitivity analysis to flag key programme delivery risks. Notably, through its interactive and visual dashboard, the tool allows the nominal schedule to be modified on the fly allowing mitigation plans to be tested and prepared when works are behind schedule.
not experts in AI to harness its power and identify bottlenecked activities at the earliest opportunity, inform impacted stakeholders, and test remedial plans of action when works are behind schedule.
The initial trials of this tool have shown that it can predict significant activity risks and challenges to plans ahead of time. As a result, the solution is now being developed so that it is suitable for more widespread use by Network Rail and its major contractors. This new tool will allow contractors to better plan possessions and operate to tight schedules and deadlines with greater confidence. The tool will allow possession managers who are
Understanding how delays will propagate and recover on the UK rail network is a complex challenge; the network has a complicated infrastructure and is used heavily by both passengers and freight. With information recorded by every train as it passes through the thousands of timing points on the network, there is an abundance of data that is too detailed to give operators the holistic view required to make informed decisions.
However, if aggregated and presented suitably, this data has the potential to provide valuable insight.
Frazer-Nash Consultancy with a strong track record in implementing innovative Machine Learning and AI solutions
recognised that through collaboration, they could put the data available from Lampada Digital Solutions NR+ environment to work. Lampada’s NR+ environment is a rich source of digitalised data required for effective route planning and analysis on the UK rail network, creating a strong base for bespoke applications focussed on improving efficiency and effectiveness of the network’s capability.
Originally funded under a grant from Network Rail and RSSB as part of its Data Sandbox+ competition, Frazer-Nash Consultancy and Lampada developed REPAIR (Rapid Evaluation and Planning Analysis Infrastructure for Railways).
REPAIR applies a machine learning model trained on historic delay data to live data feeds from Network Rail. This allows predictions to be made on how delays might improve or worsen in the following hours, akin to ripples across a pond. A visualisation tool provides an overview of these delays on a map of the rail network, allowing users to quickly identify locations that have delays which may impact their operations.
Extensions to the predictive model have also been developed utilising NR+’s routefinding methodology to offer alternative routing solutions and allow the user to run ‘what if’ scenarios to evaluate the impact of different incidents on the system.
These extensions were designed following engagement with an advisory board, made up of major players in the rail freight operating sector.
REPAIR could empower controllers to make faster and better decisions. In the UK, the required information for planning and scheduling is fragmented. REPAIR enables operators to at a glance visualise train delay across the entire rail network – or in specific areas – as well as to see how train delay is likely to develop over the next few hours. This improved understanding of the current and predicted state of the UK rail network has the potential to allow train operations staff and freight planners to better replan services when significant disruption is expected and so minimise the effects on services, the travelling public and freight customers.
Since completion of the Sandbox grant, Frazer-Nash Consultancy have pursued a partnership with a major OEM to produce a robust product for use in station and operations control rooms. This product was demonstrated last year in the Network Rail Communications Centre to showcase its potential to the industry. Frazer-Nash are now additionally talking to SMEs and other organisations about how best to bring REPAIR to market.
The benefit of collaboration between organisations is exemplified in these two case studies. Through combining their respective areas of digital expertise and leading AI capability, they have produced innovative products with the potential to improve the efficiency and reduce costs of the rail network. These are just two examples but there are likely many more similar opportunities across the rail industry waiting to be exploited.
Tel: 07892 705 449
Email: rail@fnc.co.uk
Visit: www.fnc.co.uk/what-we-do/your-industry/ transport/rail/
We should perhaps start this piece off with a reminder of the definition of a small to medium enterprise (SME) as set out by the UK Government:
• Medium – Headcount less than 250 with turnover less than £50 million.
• Small – headcount less than 50 with turnover less than £10 million.
• Micro – headcount less than 10 with turnover less than £2 million.
It is clear from the figures above that a large number of organisations can fit into the SME category. According to Government figures (2022), SMEs account for 99 per cent of registered companies operating in the UK.
There is certainly a recognition and focus from central government to support the growth and development of the SME community with initiatives such as the appointment of an SME Champion in each department, prompt payment terms, simplification of contract conditions and meet the buyer events. This move is echoed throughout the government department client organisations with spend targets set at 33 per cent of all spend to be with SMEs and action plans in place to support.
The number of SMEs in the rail marketplace has increased over recent years and there has also been a distinct change in emphasis by clients and Tier 1 organisations to recognise the specialisms and value that using these SMEs can add.
There are a number of benefits to using SMEs. Being smaller organisations, often with fairly flat management structures, SMEs are able to react to clients’ developing needs more quickly. The decision-making pathway is shorter and more accessible then in larger organisations. SMEs often have more senior experienced staff who are hands on at getting the work delivered.
This can lead to better communication on the project, early identification of risk, and better collaboration as teams within SMEs can be well connected across the industry. SMEs can also be quick to identify
‘SMEs are able to react to clients’ developing needs more quickly. The decision-making pathway is shorter and more accessible then in larger organisations.’
and implement innovation due to their agile governance structures.
However, SMEs are often unable to deliver directly to the client organisations due to a mix of reasons, not least their ability to cashflow a project and most larger projects needing a resource pool which smaller businesses don’t carry. There are a growing number of Tier 1 suppliers who are keen to realise the benefits of utilising smaller organisations and looking at ways to overcome these issues and integrate their goods and services into their supply chains.
One way that the SME community can tackle the resources needs of projects can
be to collaborate, or partner with another organisation. This can be a simple pooling of resources for a larger project or it can be to bring a particular specialism such that the overall SME offering which addresses more of the client needs.
The trick for us within the SME community is to navigate the supply chains and find the place where our goods and services can add best value.
A recent project that enGauged has delivered for one of its clients is a good example of collaboration between SMEs to add value to the end client’s project.
enGauged has supported Kilborn Consulting with the outline design production for the new station at Wixams. Our involvement started four years ago when Kilborn Consulting asked us to develop a set of requirements and constraints for the new station. Kilborn Consulting were then more recently awarded a contract from their client, Bedford Borough Council, to deliver outline design to meet with Network Rail (NR) requirements for approval. Kilborn Consulting drew together a number of discipline specialist SMEs to support them in the design development, along with engineering
management and project management support. The project requires significant track realignment on an existing four-track electrified railway with signalling moves.
enGauged were responsible for the building and civil engineering aspects of the design covering earthworks, car park, station building, platforms, footbridges and drainage.
We understood that we in turn would need support in terms of architecture, fire engineering, earthworks design and ground investigation. So the team grew, all SMEs and all bringing their own expertise and years of experience to the project.
The project core team had a lead from each organisation and there was a great effort to deliver the ‘right for project’ solution. There was a focus on minimum viable product (MVP) and delivering value for money.
Collaboration was at the heart of the delivery with a two-weekly Teams call across the design team. Behaviours were a key part of the team. Each organisation had been chosen based on its technical ability and its attitude to being part of the wider team.
Kilborn Consulting put their trust in each supplier to liaise with interfacing organisations where required and sharing information. This prevented the one-on-one
management chain (and costs associated with it) which could otherwise have evolved across the group where each organisation in the contractual chain needed involvement in the decision-making processes.
Several mid-design review meetings were held with both internal design leads and external stakeholder teams to share the design principles and to capture comments early.
Design delivery for Wixams was issued on time and has now passed through the Network Rail approval process with all document review notice (DRN) comments now closed out, demonstrating that with the right organisation and structure, a group of SMEs can deliver a complex multidisciplinary project.
This level of collaboration, both within enGauged’s suppliers and with the wider Kilborn team, has enabled enGauged and the other SMEs to offer a joined-up service to the client for the delivery of the station design and to deliver design for a station project which otherwise could have been given over to a larger multi-discipline organisation.
enGauged often provide building and civils design, including temporary works, to other SME discipline designers such as M&E and E&P. This allows the client to have
a single point of contact with one design organisation and receive a multi-discipline design. I have found that working together can sometimes unblock the ability for the SME community to tackle different projects which would not normally be achievable. The old adage that the whole is greater than the sum of its parts can often play out.
Tel: 01270 255 731
Email: enquiries@engauged.co.uk
Visit: www.engauged.co.uk
enGauged is a privately owned rail infrastructure design practice, specialising in building and civil engineering design. Our services cover everything from feasibility studies and site surveys through planning, outline design, detailed design to construction support.
delves into the detail of temporary works design for the rail sector, exploring the clear need for speed, safety and reliability
Whether it’s scheduled track maintenance or a major infrastructure upgrade, contractors can face a number of challenges unique to the rail industry.
At the forefront, is the need for safety. Our railways can be dangerous places to work, from uneven surfaces to live running rails and the proximity to high-speed rail services. Keeping site teams safe is nonnegotiable.
Speed and efficiency are also critical, with projects often having extreme time constraints and pre-agreed possession windows, which aren’t always the same as the work window. First, comprehensive site safety briefings must be carried out and the track in question may often need to be surveyed – both before and after work has been completed –before the track can be handed back over to Network Rail upon completion. All of this makes the window of opportunity for the work itself even shorter. Possession periods are also famously expensive.
As a result, it’s vital that any equipment required for maintenance or upgrade works is deployed promptly, is right first time and then able to be removed quickly.
Temporary works can also be described as enabling works, needed to facilitate the construction of the permanent or to enable other works to be carried out safely and efficiently. Despite this, temporary works can still often be seen as an ‘add-on’, brought in at a later stage of a project.
We regularly see the value of early engagement, where temporary works are considered at an earlier stage of the project sequence. This approach is perhaps especially critical within the rail sector. While not always possible on reactive and emergency projects, for planned maintenance and
upgrades it can be invaluable. It’s all about opening up conversations and considering both the temporary and the permanent in conjunction. By doing so, you can work collaboratively on finding the optimum solution for the project and for the site.
Often, the initial solution may not always be the best choice, with other design avenues to explore that could save time, cost or improve productivity on site. When you have time to discuss, explore and collaborate, the end-result is always far better for everyone.
Let us take a common maintenance project as an example: repairing or replacing utilities (such as drainage) around the track. These will require shallow trenches to be excavated, usually up to two metres in depth. As with any groundworks project, shoring equipment is essential to make the trench safe for site teams to access.
Around 80 per cent of the groundworks equipment we supply to the rail sector is lightweight shoring. This goes back to the
‘It's essential that you have confidence in the temporary works design and trust that it will be constructible on site, taking all hazards and site constraints into account.’
two clear priorities: speed and safety. As its name suggests, lightweight shoring equipment is easy to handle, manoeuvre and install. Most solutions can be installed either by hand or by RRVs, negating the need for large plant machinery. This is essential, as getting large equipment trackside can be a challenge, especially when you consider
that our UK rail network runs through some of the most rural and remote parts of the country.
Due to the extreme time constraints, site teams simply cannot afford any downtime with the equipment. The temporary works design must be robust, and the equipment must be reliable. Within the rail sector, every project is different and hazards can vary, from embankment heights to live services and other structures.
It's essential that you have confidence in the temporary works design and trust that it will be constructible on site, taking all hazards and site constraints into account.
While cost is a factor for consideration, it is clear that safety comes first. Given the expense of the possession window, any cost savings achieved can be easily undone if there are issues with the temporary works design or equipment – especially when those issues lead to project delays. Instead, the focus is (rightly so) on getting it right first time.
Taking all of this into account, the value of collaborating with an experienced temporary works supplier is clear, providing you with the assurance that works can be completed safely, correctly and efficiently –without snags.
At Mabey Hire, we are a trusted temporary works partner to the rail industry. We’re committed to product innovation, regularly improving and expanding our product portfolio, including lightweight shoring equipment. Our dedicated engineering team uses the latest digital technology and BIM modelling to ensure a design is constructible in the 3D environment before you reach site. What’s more, with 16 depots around the country, you can be sure that our expertise isn’t too far away. Learn more at www.mabeyhire.co.uk
At the beginning of March The Chancellor unveiled his Spring Budget, the industry response has been compiled here
‘Whilst I welcome the recent progress in reform across road and rail, it is clear that investing in transport and infrastructure is not a top priority for the current government. Collaborating with both private and government stakeholders to deliver transport solutions has made us aware of the challenging years ahead for the industry, and we know the immense pressure facing public transport which will only grow without significant investment and change. The chancellor has rightly indicated that future public service investment decisions will be focussed on improving productivity. However, he has failed to build on the measures laid out in the Autumn statement, and the chancellor’s silence on overhauling the UK planning system and cut project delivery times is a cause for concern. This is consistently flagged as a barrier to investment, progress and the success in the programmes and projects needed to improve the infrastructure across the country.’
Chief Executive for Rail Partners
‘While the 14th consecutive year of fuel duty being frozen will be welcome news for motorists and lorry drivers, rail freight businesses continue to see rising costs, and rail passengers have seen fares rise by 4.8 per cent. Britain has a legally binding target to meet net zero by 2050, and the budget today does nothing to encourage people and companies to make more sustainable transport choices and choose rail over road. In order to decarbonise our transport sector government must take a more holistic approach to make sure rail freight can be competitive on price with road haulage and that the costs of passenger transport modes reflect their environmental impact.’
‘Our sector is being asked to decarbonise its plant fleet at a time when profit margins are under strain at all levels of industry. Moves towards enabling the full expensing of leased construction plant has the potential to unlock vital funds to enable the roll-out of lowcarbon machinery, as well as making it more affordable for the hirers that many contractors use to upgrade their fleets. We welcome the UK Government’s stated intention of publishing draft legislation on this issue as a move that it is taking seriously the need to decarbonise UK construction, while enabling businesses across the supply chain to remain profitable. At the same time, the condition that these changes will only be implemented ‘when fiscal conditions allow’ potentially implies unnecessary delay to the roll-out of this vital reform. CECA has long campaigned for this change as a means of unlocking necessary investment to help decarbonise our industry. We look forward to working with Government, our members, and industry partners, to ensure the delivery of this vital policy within a timescale that matches the urgency of reaching net zero.’
‘While we welcome any new investment in our places, there is no escaping the fact that the place-based services ADEPT members are responsible for delivering are struggling. A budget focused on cutting tax and a patchwork of investment will do nothing to help local authorities deliver the essential services people rely on every day. Councils across the country are making extremely difficult decisions based on painful choices that will impact everyone, but fall hardest on the most vulnerable in our communities.’
Chris Richards, Director of Policy at the Institution of Civil Engineers (ICE)
‘Today’s budget confirms that the general election will be a crucial one for infrastructure. It's now been confirmed that the spending review will take place after the election. That means the next government will be responsible for implementing the next National Infrastructure Strategy, delivering the next carbon budget, and reallocating HS2 funds for the North and Midlands. Certainty that there will be no significant changes to infrastructure projects and spending before the election is welcome, but there are still many decisions to be made. The ICE will shortly launch a programme of work that aims to spark conversations about what the next government’s day one infrastructure priorities need to be’
Darren Caplan, Chief Executive of Railway Industry Association (RIA)
‘There are some positives related to rail in the Spring Budget announced today by the Chancellor Jeremy Hunt. It is good to see aspirations for faster completion of East West Rail, news of additional East Coast Mainline services, and more information on the Network North schemes. However, overall the Railway Industry Association and our members will be disappointed that an opportunity has been missed to leverage rail to drive economic growth more widely – it is worth remembering that for every pound spent on rail, £2.50 is generated in the wider economy. Rail suppliers will be disappointed the Chancellor has failed to provide certainty or clarity on the outlook for network enhancements, and there is still a black hole on rail infrastructure pending following the scrapping of HS2 Phase 2 – the Network North schemes, whilst welcomed by rail suppliers when they go ahead, do not amount to the rail spending lost and those mentioned are subject to business cases, and the HS2 Euston proposals are far from certain. So we look forward to seeing more detailed plans from the Government in due course, whether related to infrastructure or trains, so that the railway industry can have the certainty it needs to get on with building world-class rail in the UK, whilst providing value for money for both the customer and the taxpayer.’
Andrew Baldwin, Head of Policy and Public Affairs at the Association for Project Management (APM)
‘Instead, we were left with uncertainty, speculation and (in Network North) a list of disparate projects that may or may not get started before the next General Election. We hope the Government does not rush any sale of HS2 land without first giving thought to whether it could still be used to enhance transport links. We still need a plan to improve rail capacity, which remains a real problem. Instead of Network North alone, we are calling for a more focused strategy outlining firstly how all these smaller projects link together into a plan which will improve society, and secondly how the Government plans to use projects more generally to improve the UK. When projects succeed, society benefits. We'll be looking out for any new projects that might be announced before the election so that we can work with the government to help them succeed. Of the Government’s current commitments, we would like to see more clarity and commitment to levelling up and net zero projects. A total of 61 per cent of APM members surveyed think there are not enough project experts to sustain the future delivery of net zero projects1. This is deeply concerning, because both net zero and levelling up are flagship Government programmes, the benefits of which need to be delivered.’
The tBOX110 is designed with low power consumption and heavy-duty construction that can withstand challenging day-to-day operational conditions
xiomtek – a world-renowned leader relentlessly devoted to the research, development, and manufacturing of innovative and reliable industrial computer products of high efficiency – is proud to announce its tBOX110, a compact fanless transportation embedded system now EN 45545-2, EN 50155 certified.
It accommodates varying voltage demands, effortlessly adapting to different environments. The reliable transportation system supports 12/24 VDC typical automotive power input with smart ignition, or 24 to 110 VDC for railway use and a widerange 9 to 36V DC power input for general purposes. The tBOX110 is powered by the Intel Atom® x5-E3940 processor and has a wide operating temperature range of -40°C to +70°C and 3Grms vibration resistance. Its comprehensive verification and certification provide a more sustainable and safer solution for transportation applications.
The DIN-rail and wall-mountable tBOX110 measures only 164 by 128 by 44 mm and weighs 1kg. The compact size ensures that it can fit in various spaceconstrained environments. The tBOX110 is equipped with one DDR3L-1866 SO-DIMM for up to 8GB of system memory. It also has one internal 2.5” SATA drive and one mSATA
There are two full-size Rev.1.2 PCI Express Mini Card slots – one USB/PCIe with external SIM socket and one mSATA/ USB/PCIe with external SIM socket – for high integration. Equipped with smart ignition power control, the tBOX110 enables to schedule power on/off events to protect the vehicle battery from unstable voltage and supports different power modes.
Axiomtek's tBOX110 offers comprehensive transportation gateway solutions, catering to a wide range of applications, from in-vehicle to railway. This transportation-grade embedded system not only meets ISO 7637-2 standards but also has full certification to EN 45545-2 and EN 50155. By choosing the tBOX110, customers can benefit from significant cost savings and reduced waiting time, since they no longer need to bear verification fees or lengthy certification processes. This makes the tBOX110 a highly efficient and reliable choice for transportation-related projects.
With the innovative and reliable safe shutdown feature, the tBOX110 safeguards critical components and data during power disruptions or emergencies. Customers could also easily setup power on/off scheduling in the BIOS menu. It ensures the longevity and optimal functionality of the devices as well as making tBOX110 a responsible and environmentally conscious choice for energy saving solution.
ADVANCED FEATURES OF TBOX110
• EN 45545-2 and EN 50155 certified; ISO 7637-2 compliant.
• Intel Atom® x5-E3940 processor.
• Fanless and wide operating temperatures from -40°C to +70°C.
• Supports 9 to 36VDC and 12/24VDC typical in-vehicle power input.
• Supports 24 to 110VDC for railway power input.
• Compact size with multiple COM, CANBus, and DIO for communication.
• Smart ignition for power on/ off schedule, vehicle battery protection, and different power modes.
The tBOX110 also offers rich I/O interfaces to ensure seamless connectivity and performance across transportation applications. For in-vehicle applications, the tBOX110 features two RS-232/422/485 with shield grounding, two isolated CANBus with SocketCAN, two RJ-45 10/100/1000 Mbps Ethernet ports (Intel® I210-IT), and one DB9 8-bit programmable DIO.
While for railway applications, it offers four isolated RS-232/422/485 with shield grounding, two M12 A-coded 10/100/1000 Mbps Ethernet ports (Intel® I210-IT), two M12 X-coded 10/100/1000/10000 Mbps Ethernet ports (Intel® I210-IT), and one isolated 4-in/4-out DIO (terminal block). Two HDMI 1.4b with keylock, two USB 3.0, one reset button, one power button, one remote switch, and four antenna openings are available. Moreover, the tBOX110 is compatible with Windows® 10 64-bit and Ubuntu 20.04.
Email: info@axiomtek.com.tw
Visit: www.axiomtek.com
Through the deal, Officine Maccaferri will be able to complement its product portfolio with Nesa’s cutting-edge technologies developed in remote intelligent sensor sector, thus reaffirming the Group’s long-standing innovative drive
Officine Maccaferri, a global leader in the field of civil and environmental engineering, has announced it has finalised the closing of the acquisition of a majority stake in Nesa S.r.l. (Nesa), a technology-driven company and a leading provider of environmental and industrial monitoring and Early Warning systems. With the acquisition, the Group plans to strengthen the incorporation of intelligent, remote-controlled sensing technologies within its own product range and to further enhance its offer of Internet of Things (IoT)-based systems for land and people protection.
Founded in 2004 in Vidor, Treviso, Italy, by engineers Pierluigi Bassetto and Mario Adami, Nesa is a highly specialised company in designing, manufacturing, and installing instruments such as meteorological stations, datalogger systems, as well as wired and wireless environmental monitoring instruments. It works in over 80 countries and has more than 5,500 stations installed worldwide.
Nesa stands out for its instruments installed in extreme environments, spanning from providing tsunami monitoring systems in the Indian Ocean, to building meteorological stations in the far North of Russia to endure freezing temperatures, to developing a state-of-the-art datalogger for climate monitoring in the Caribbean, thus proving its expertise and flexibility in such unique settings. Following the transaction, the two founding partners will maintain an active role in the company’s management.
By leveraging on Nesa’s technologies, which are perfectly matched with Officine Maccaferri’s existing solutions, the Group seeks to further establish itself as a cuttingedge player in the IoT segment, riding the wave that has been driving infrastructure and construction to become increasingly smarter over the past few years. According to projections contained in the latest Allied Market Research report, the scale of the
Internet of Things market in the construction industry will reach $44.2 billion (£34.7 billion) by 2031.
In this framework and through the integration of Nesa, Officine Maccaferri aspires to become the pioneer in the infrastructure and largescale works industry digitization, while strengthening its own R&D efforts to develop integrated solutions. The past collaboration between the two players has created HelloMac, an innovative alert system capable of safeguarding communities and infrastructures from geohazards, thanks to its ability to detect events such as land deformations and rockfalls and to send real-time alert and a warning notification. Therefore, Officine Maccaferri will be able to enhance the development of HelloMac by building on Nesa’s technical know-how.
Sergio Iasi, Chairman of Officine Maccaferri, said: ‘The deal marks yet another step in the growth path taken by Officine Maccaferri, which is focusing on increasing its technical expertise to address the pressing challenges of our time in terms of environmental safety. The high level of technical know-how and the great innovation degree offered by Nesa make it the ideal partner to build synergies with, allowing us to develop new cuttingedge solutions, as well as to integrate existing ones, to increase our products’ competitiveness.’
segment. Thanks to the deal, we will pursue our innovation path backed by Maccaferri’s worldwide presence and network.’
Officine Maccaferri was assisted by Gianni & Origoni, acting as legal advisor, while Spada Partners was in charge of the due diligence. Nesa was assisted by law firm Chiaventone & Associati.
Officine Maccaferri Profile
Pierluigi Bassetto and Mario Adami, founders of Nesa, added: ‘In our research and development journey, we were looking for a strong partner with the skills and expertise to provide HelloMac technologybased solutions with application visibility in the geotechnical and environmental engineering sector. The interest expressed by a historical player and market leader such as Officine Maccaferri is for us a great source of pride, reflecting the fact that, over the years, our company has established itself as a pioneer in the remote sensor
Founded in 1879, Officine Maccaferri is a global leader in civil and environmental engineering, with more than 20 factories in four continents, around 3,000 employees and a commercial presence in over 130 countries. With revenue of over €600 million (£256 million), as of 31 December 2023, Officine Maccaferri offers advanced engineering solutions for the reduction of hydrogeological risk, the development and safety of transport infrastructures and the urban environment.
Tel: 01865
770 55
Email: Info.uk@maccaferri.com
Visit: www.maccaferri.com/uk
RailSmart Virtual Campus is a total learning suite that drives staff engagement and nurtures a learning culture aligned with your goals.
Make. Change. Work.
Learning and refining employee skills and capabilities is pivotal to organisational improvements. It is the bedrock in future proofing success and ensuring that tomorrow’s problems are resolved today
This mindset thrives within 3Squared and was a key driver behind the creation of the RailSmart Virtual Campus, an effective learning management system (LMS). An efficient learning culture not only enhances the skills and knowledge of employees, but it also empowers them to take ownership of their personal and professional development. This is turn results in increased job satisfaction, motivation, and productivity.
Powered by the market leading, award winning LMS from Docebo, RailSmart Virtual Campus is a cutting-edge system that supports learning delivery and engagement with rail and transportation industries in mind.
The overarching objective of the LMS is to align business strategies with employee training and development goals. Partly as a result of remote working in recent years, LMS’ have faced a huge surge in usage, and have therefore proven how adaptable they are with the requirements of today’s digitalised world.
A good LMS provides users with a wide range of benefits; from reducing unnecessary administrative burdens, to improving accessibility and adapting to
the modern ways of working and empowering businesses to provide enhanced training and development for their leaners.
There are two types of LMS users – administrators and learners. Administrators are responsible for managing the LMS, which involves a range of tasks including course management, assigning specific learner groups to specific learner plans, and more.
Learners are on the receiving end of learning initiatives. Learners who have access to an LMS can view their course information, complete assigned courses and evaluations and measure their own progress. The optimum LMS solution ensures that this access has a streamlined user journey and prioritises accessibility and ease.
A system that evolves alongside you Modern systems evolve alongside us, learning our patterns and behaviours, adapting to our requirements and needs. RailSmart Virtual Campus does precisely this. By utilising gamification and social learning, an interactive and enjoyable learning experience is created for users. Through a personalised learning dashboard, the LMS ensures that knowledge is embedded, and workplace performance is enhanced.
The centralised knowledge hub offers a vast library of learning content (up to 100,00 items) and the ability to upload a variety of learning resources. The system also provides a combination of webinar and in-person training, making it easier for new and existing, in-person and remote employees, to learn and adapt.
Solving problems through innovation was a key motivator behind the creation of RailSmart solutions during its inception and is something that continues to be of key importance today.
There are several benefits and advantages that arise when using RailSmart Virtual Campus.
These include:
• A customisable system that caters to specific needs, ensuring scalability as learning projects become increasingly advanced.
• Streamline and simplify administrative tasks through automation.
• The ‘My Team View’ feature empowers managers with exclusive access to monitor their team’s learning activities and take immediate action of any overdue certifications.
• Remote training – employees can train from their desks or on the go, minimising time away from their work responsibilities.
The LMS is built on a secure SaaS infrastructure, ensuring the highest level of safety for users. Industry-standard safeguards and the ability to choose data centres residency options based on your location.
Since the beginning, 3Squared has held the belief that creating holistic and efficient systems can fix the problems that the industry faces, day in day out. This ethos can be seen in RailSmart Virtual Campus, which has become the ultimate go-to LMS platform, resolving the learning and compliance needs of the transportation sector. 3Squared look forward to driving it forward this year, and beyond.
Email: hello@3squared.com
Visit: www.3squared.com
Social: @3Squared
Answering the demand from customers and understanding the need for a cost effective, quick to install and low maintenance fencing solution, Elite Precast Concrete has introduced Elite Verti-Crete fencing and walling.
Saving on both time and money, VertiCrete offers looks, strength and quality, as the walling and fencing can be used for a variety of applications that customers are looking to solve. These include privacy, boundary, security and of course where clients need to install a retaining wall, to allow for extra land-take and secure the network.
Paul Cartwright, Business Development Director for Elite Precast Concrete, says: ‘With the look of masonry-like concrete, the attractive finish complements the rail network, with a finish on both sides, giving rail users a secure, beautiful fencing solution.’
He continues: ‘Quick and easy to install, our Verti-Crete ‘hollow core’ posts are placed over individual footings with rebar anchors. The wall panels are then inserted, and only when each section is squared and levelled are the posts filled with concrete. This secures the connection between the post and footing and allows for a more levelled, stable fence system. With Elite Verti-Crete you get fast installation, quality and a wall with the look of real stone at an affordable price – it’s a real winning combination.’
As an engineered fencing solution, the seamless solid-panel design provides structural strength, stability and security, which will last for decades and as our weather conditions have become increasing more unstable over the last few years, VertiCrete can endure the harshest conditions and broadest range of climates.
Made in the UK, Elite Verti-Crete is made in a variety of face finishes, speak to the Elite Precast team to find out which suits you best, get in touch via the contact information below.
Tel: 01952 588885
Email: sales@eliteprecast.co.uk
Visit: www.eliteprecast.co.uk
Southern Renewals Enterprise announces new Director for Southern Integrated Delivery Liz Baldwin has been appointed as the Southern Integrated Delivery (SID) Director to deliver Network Rail’s Southern region’s renewals portfolio for the next ten years. The SID is part of the Southern Renewals Enterprise (SRE), a new and innovative model being introduced across Network Rail’s Southern region at the beginning of Control Period 7 (CP7) in April 2024 to deliver the £9 billion renewals portfolio between 2024 and 2034.
Northern has appointed Nick Clarke as its new Head of Retail. Clarke, from York in North Yorkshire, takes up his new role in April and will be responsible for all elements of the ticket buying experience.
QTS Group has announced that Andy Steel has been appointed as the new Managing Director (MD), effective Tuesday 2 April 2024. The news follows the appointment of the current MD, Alan McLeish, to Group Chairman.
Stevedores appoints Director of Rail and Containers
Industry-leading cargo handler, Solent Stevedores, has appointed Mark Hooper as Director of Rail and Containers across operations in the Port of Southampton and London Gateway.
Alpha Trains Group, the leading lessor of locomotives and passenger trains in Europe, has appointed Iris Schnittler as its new Chief Financial Officer (CFO), with effect from 1 July 2024. Schnittler has more than two decades of experience in the financial sector, including accounting, controlling, financial reporting and compliance.
The Liverpool City Region Combined Authority (CA) has announced the appointment of Jamie Ross to the newly created post of Director of Transport. Ross, who previously held the role of Interim Director of Rail at the CA, will be responsible for leading on the commissioning and delivery of Mayor Steve Rotheram’s plans for a fully integrated, London-style public transport network that's faster, cheaper, cleaner and better connected.
After serving as an interim board member for over six months, Danny Vaughan replaces Bob Morris, former Chief Operating Officer for Transport for Greater Manchester, who has stood down from the position at the Light Rail Safety and Standards Board, following his retirement.
Safety is our number one priority. Our industry-leading safety performance is achieved only through focus and always putting safety first in everything we do. We work with our clients to educate them about best safety practices which demonstrates our safetyfirst culture by applying proven strategies, systems and innovation.
ukpowernetworksservices.co.uk
Scan here to get in touch