8 minute read
Depots
Next Article
Staying safe driving in depots
Dr Stephen Fletcher, Director and psychologist at the Occupational Psychology Centre (OPC) shares some job analysis work that has helped to identify key Non-Technical Skills (NTS) for safe and effective depot driving
We don’t need to tell you that train depots can be very busy places! Trains may be there for a variety of different reasons – they may be in for routine maintenance or an emergency repair; fault diagnosis or brake/ wheel checking, or they may simply be there for a wash!
Activities in the depot, can be very varied. Each day may not be the same twice. During a shift, a depot driver may need to move a train across a number of different locations in the depot. They may need to move a number of engines to different areas of the depot in a scheduled and orderly fashion. Moves may simply be driving one locomotive to an area or it may be more complicated with the driver having to move more than one engine, like pieces in a puzzle, in order to get the required traction into the right place for the job needed. A day’s schedule may be very efficiently mapped out, which is great, but if an emergency maintenance job comes in then the whole schedule and system of moving various trains may need to be re-thought and re-scheduled.
Due to the functional nature of a depot, there may also be a number of different teams working there – drivers, engineers, maintenance crews etc. Different safety critical employees can undertake numerous safety tasks. It can be dangerous and the consequences of errors can still be enormous. All in all, it can be a hive of activity and a very demanding place to work and drive in. So, if we need our depot drivers to be safe and effective, then what are the key NTS they need to demonstrate their day-to-day work?
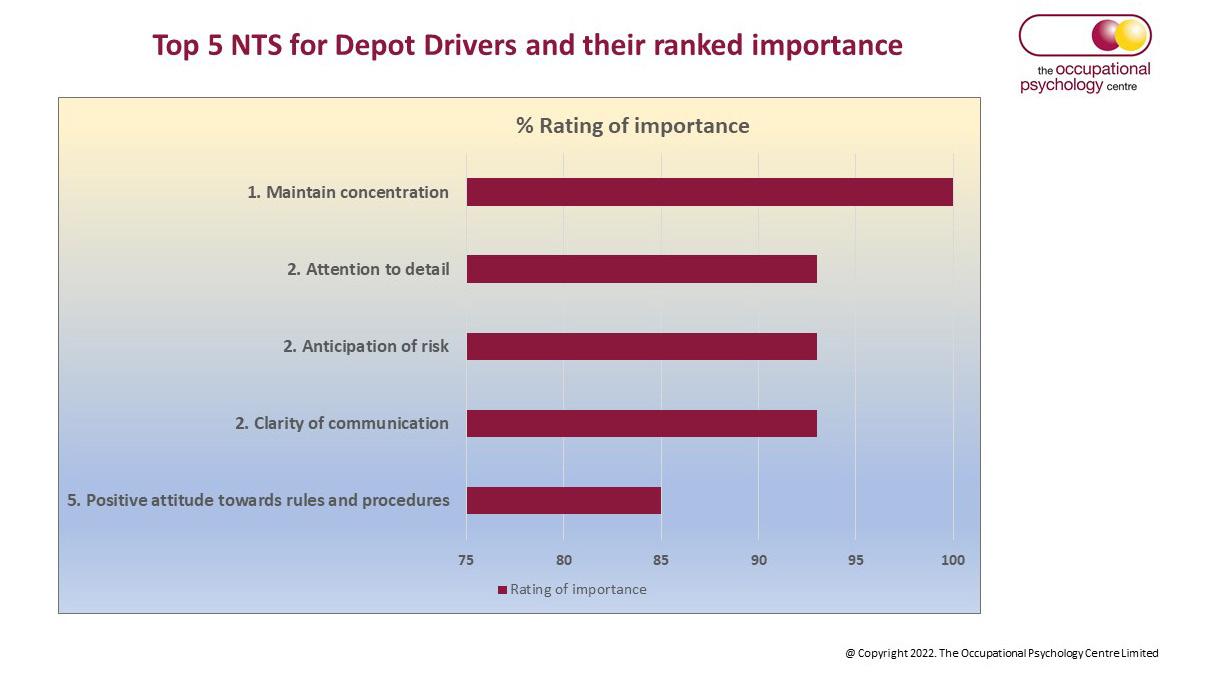
So, what do depot drivers need for safe and effective performance? OPC psychologists undertook job analysis for the depot driver role with two separate UK train operating companies. With the first train operator, job experts with indepth knowledge of the depot driver role were asked to rate the importance of 26 NTS to the role. Working alongside a second train operator, in conjunction with an in-depth role profiling exercise, a critical incident technique was also used. This involved identifying occasions when drivers had performed both very well and other occasions when they may have performed poorly with safety incident consequences – this technique helped to identify behavioural indicators that are important to display (or not) to be safe and effective in the role. OPC psychologists analysed the outputs from the job experts at the first train operator and ranked the NTS in order of importance (see chart). Work alongside the second train operator confirmed and enriched these findings.
The chart below shows the top five ranked NTS: drivers. A depot driver needs to stay constantly focused whilst moving trains around the depot. They need to be watching for signals; aware of what is going on around them and people working nearby, as well as being able to deal with repetitive tasks without losing concentration. As with other key safety critical roles the NTS of ‘maintaining concentration’ is crucial to safe performance. The next three NTS were equally rated by job experts at 93 per cent importance.
The NTS of ‘attention to detail’ is rated as key to depot driving. Depot drivers need to make sure they attend to the detail of their tasks incorporating information they have been given about where to move trains from and to. They need to adhere to depot speeds, pay absolute attention to their instructions, as well as work with signal and
road numbers. Because of the busy nature of a depot and its daily variations, a safe and effective depot driver cannot be complacent, relying on what they ‘usually’ do. Neither can they depend on habit i.e., that train
These top NTS are based on the research published by the RSSB 2012 ‘Research Programme. Operations and Management. Non-technical skills for rail: A list of skills and behavioural markers for drivers, with guidance notes’.
Top five NTS for safe and effective depot driving The results from our job experts indicated that the NTS of ‘maintain concentration’ was rated as most important for depot
Image credit: iStock
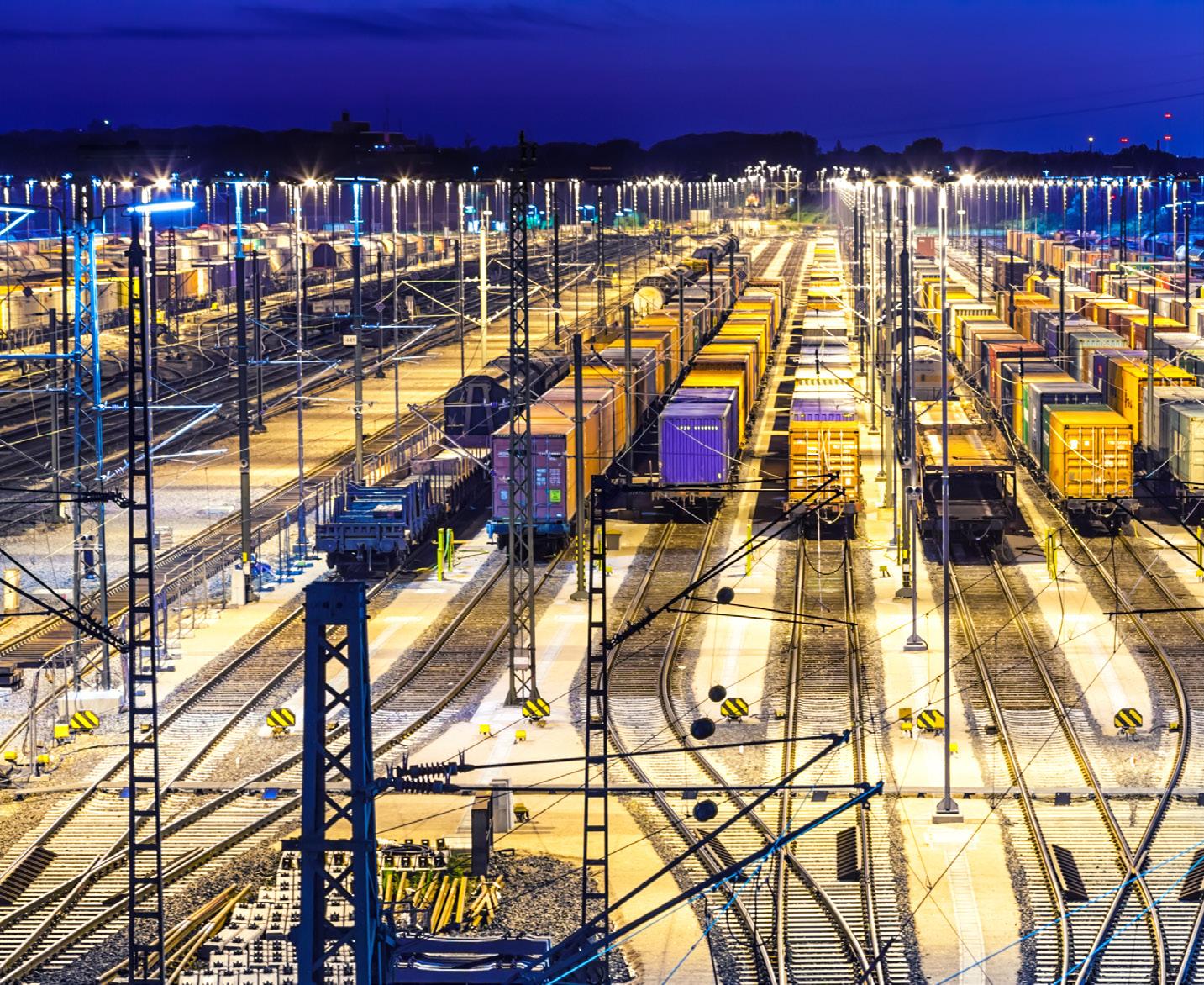
always goes into road number X. They must be meticulous in following instructions and getting the detail right.
‘Anticipation of risk’ is another important NTS identified by our job experts as being equally critical to depot drivers. There are many safety risks when working round a depot. Some of these are constant risks such as engineers working nearby or other risks may be more dynamic showing themselves at different times e.g. a depot driver may have a new recruit shadowing them who is inexperienced and unaware of the surrounding safety hazards. Depot drivers also need to remain vigilant to complacency or over-familiarity about the depot layout, their tasks or their routine – a failure to do so can lead to a state of ‘auto-pilot’ possibly resulting in a safety incident. They need to be constantly assessing and evaluating risks in a dynamic fashion, recognising any overreliance on routine or repetitive tasks and managing emerging risks effectively to help keep themselves and others safe.
Within a depot environment effective safety critical communication is crucial. Therefore, ‘clarity of communication’ is another key NTS for a depot driver. Depot employees will communicate extensively with each other. This could include giving each other instructions and advice about what to do and how; feedback on what’s taken place; errors that may have occurred, or discussing the best course of action with the wider depot team when an emergency maintenance job comes in, for example. They may also need to listen to other people’s priorities and perspectives, remaining calm if things need to change, as well as report faults or potential safety hazards to superiors. So, we need depot drivers to be effective communicators and have clear exchanges of information, cooperation and understanding with work colleagues. Failure to do so could leave a depot driver and other staff vulnerable to a safety incident.
The fifth ranked NTS was ‘a positive attitude towards rules and regulations’. We work in a rule bound and heavily regulated environment with rules and procedures that have been built up over many years – often based on past safety incidents. Therefore, we need drivers to be rules focused and to enjoy working in a rule bound environment. They need to work effectively with both safety critical and non safety critical rules. When under pressure to break the rules, the best driver will ‘stick to their guns’, not succumb, and instead abide by the rules.
Using NTS to help recruit safe and effective depot drivers Some train operators will use their mainline driver selection process to recruit their depot drivers, potentially reviewing the NTS performance to allocate candidates into the best fit role. Other rail companies have expressly tailored their depot driver selection process to assess for the most important NTS, taking into account the subtle differences required when driving in this environment for their own operations. However, with either talent acquisition process, the OPC would recommend some careful job analysis of the depot driver role itself to identify what key NTS are required for safe and effective performance. This needs to be undertaken by, and for each train operator as the depot driver role and therefore the key NTS may vary from operator to operator. Once this is complete then train operators can utilise a range of psychological tests and exercises that evaluate candidates for their specific NTS.
OPC Assessment has a wide range of online assessment tools for safety critical roles, some of which are used by rail companies to help recruit safe and effective depot drivers. Considering the top five NTS one the previous page, some recommendations may be: The SCAAT (Safe Concentration and Attention Test) which helps to assess the NTS of concentration. The Railway Verbal Communication Exercise (rVce) can be used to assess the quality and accuracy of his/her verbal communication. The SAFEPQ (Safe Personality Questionnaire) helps to assess an applicant’s propensity to demonstrate safe behaviours – such as cautiousness, resilience and rules focus and the RTQ (Risk Anticipation and Rules Focus) helps to evaluate a candidate’s attitudes and behaviour styles towards anticipation of risk. Using specifically selected assessment tools that evaluate and assess for these NTS can help to identify and recruit depot drivers who are safe and effective in the role.
Developing and assessing the NTS with existing depot drivers If the five NTS outlined on the previous page are indeed key to a depot driver’s safe and effective performance then we need to take every opportunity to help our existing depot drivers to excel at these NTS whilst working. So, we can take these NTS and:
1. Share them with our depot drivers showing how important they are to their safety and the safety of the depot. This could be undertaken through workshops or through one-to-one line manager meetings or appraisals. 2. Having received depot drivers’ buy-in we can help them to develop these NTS. We can provide drivers with some practical tools on how to enhance these NTS. For example, techniques to help improve concentration, getting the detail right and how to pick up and manage subtle risks. 3. We can incorporate them into drivers’ initial training before they graduate into the depot driving role. 4. Share them with managers and assessors and incorporate the NTS into the ongoing assessment of depot drivers alongside the more technical requirements of the role.
Dr Stephen Fletcher concluded by saying: ‘Our depot drivers need to have the right NTS profile to undertake their roles safely and effectively. We need to put these NTS to good use by using them in selection, training them in with new recruits and embedding and developing them in existing depot driver teams. Together these could help improve the safe performance of our depot drivers still further.’
Tel: +44 (0)1923 23 46 46 Email: admin@theopc.co.uk Visit www.theopc.co.uk