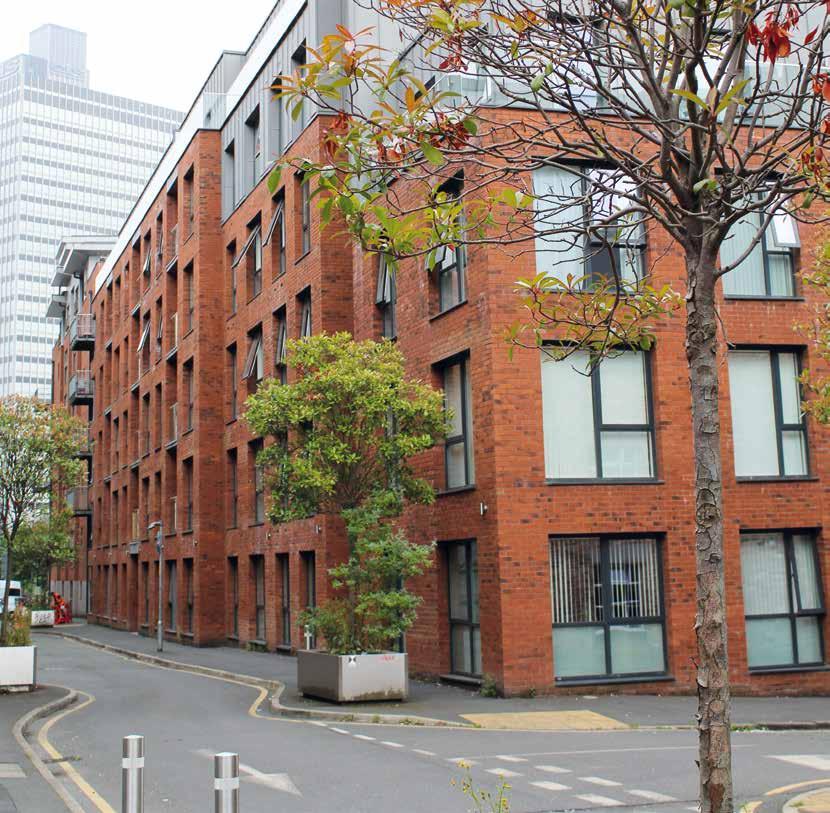
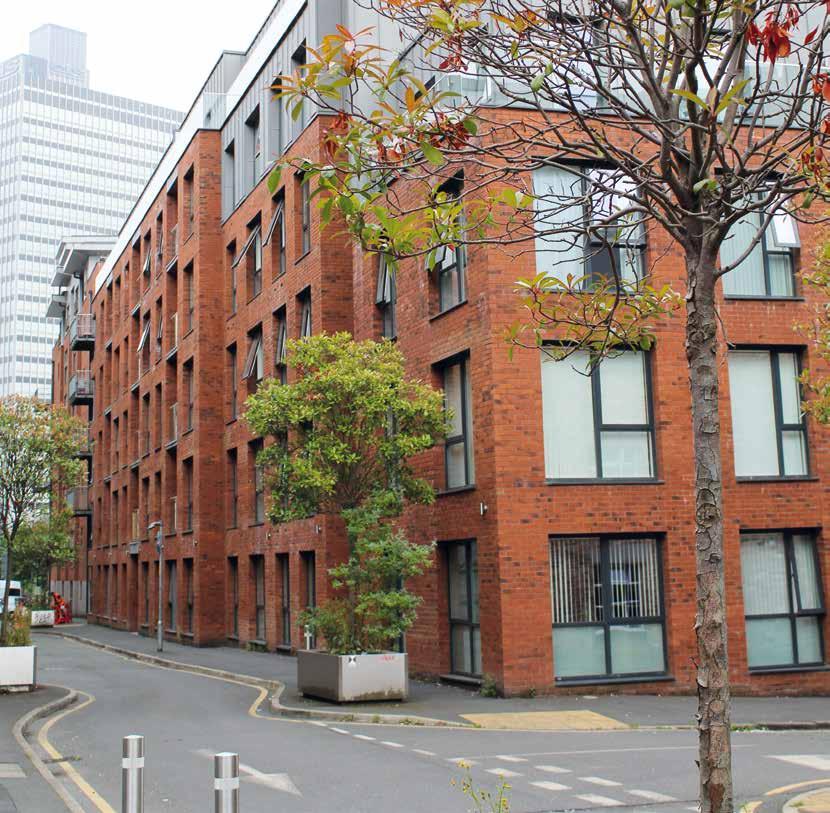
Building on solid foundations
BRINGING TOGETHER THE BEST OF THE UK & IRELAND’S OFFSITE CONSTRUCTION EXPERTS - SIGMAT, EOS & HORIZON
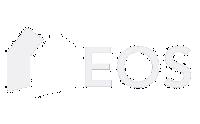
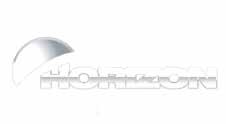

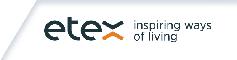
CONTENTS
PUBLISHING In this issue...
FRONT COVER: voestalpine Metsec
PRINTED ON:
FSC Mix paper by Buxton Press
PUBLISHER:
Light Steel Framing Magazine is produced in partnership with the Light Steel Frame Association and published by Radar
Communications:
©Radar Communications Ltd.
Radar Communications Ltd, 101 Longden Road, Shrewsbury, Shropshire, SY3 9PS
T: 01743 290001
www.radar-communications.co.uk
SUBSCRIBE TO RECEIVE:
www.lightsteelframingmagazine.co.uk
ADVERTISING ENQUIRIES PLEASE CONTACT:
Julie Williams // T: 01743 290001
E: julie.williams@radar-communications.co.uk
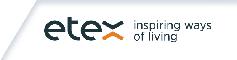
SEND US YOUR NEWS:
T: 01743 290001
E: info@lsf-association.co.uk
FOR ENQUIRIES PLEASE CONTACT:
E: info@lsf-association.co.uk
DISCLAIMER: The content of Light Steel Framing Magazine does not necessarily reflect the views of the editor or publishers and are the views of its contributors and advertisers. The digital edition may include hyperlinks to third-party content, advertising, or websites, provided for the sake of convenience and interest. The publishers accept no legal responsibility for loss arising from information in this publication and do not endorse any advertising or products available from external sources. The publisher does not accept any liability of any loss arising from the late appearance or non-publication of any advertisement. Content including images and illustrations supplied by third parties are accepted in good faith and the publishers expect third parties to have obtained appropriate permissions, consents, licences or otherwise. The publisher does not accept any liability or any loss arising in the absence of these permissions for material used in both physical and digital editions. No part of this publication may be reproduced or stored in a retrieval system without the written consent of the publishers. All rights reserved.
04 06 24 28 32 36
New Guide Simplifies Framing Specification
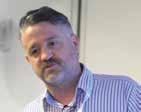
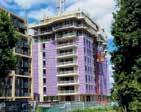
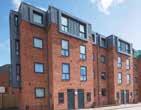
Showcasing voestalpine Metsec’s new 60-page online guide which provides a comprehensive reference manual for the specification of Metframe.
Industry News
Highlighting the latest construction industry initiatives, project developments and building technology innovations in the UK light steel framing sector.
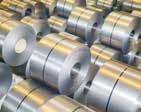
LSFA on Circular Construction
Transitioning from a linear to a circular construction economy offers significant opportunities by keeping materials and assets in use for as long as possible to retain their value.
Technically Advanced Material

Steph Hazlegreaves, Digital Managing Editor explores whether light steel framing is truly the most technically advanced material in the offsite technology portfolio.
Focus on Framing
Details of a project Brebur recently presented at the Focus on Framing conference.
Product Testing Reforms
The Morrell review recommends a series of sweeping reforms aiming to ensure products used on buildings are safe – with a major shake-up in the regulatory system likely to follow.

NEW GUIDE SIMPLIFIES FRAMING SPECIFICATION
VOESTALPINE METSEC HAS LAUNCHED A NEW ONLINE VERSION OF ITS POPULAR SPECIFICATION GUIDE FOR METFRAME, THE MARKET LEADING, PRE-PANELISED OFFSITE FRAMING SOLUTION.

In keeping with the modern trend, the new edition will be available as a digital document only, reducing the environmental impact of paper usage as well as providing a more interactive, responsive and convenient presentation for the reader.
The 60-page document provides a comprehensive reference manual for the specification of Metframe, presented in double-page spreads which can be quickly and easily called up from the guide’s interactive list of contents.
Aimed at architects, developers and the project design team, the specification guide builds on the content of the Architectural Guide and Metframe System Guide, both of which have proved to be invaluable mainstays for specifiers over the years. The new guide is intended to enable design teams to make informed choices when specifying the Metframe system.
The new full-colour guide features comprehensive information on Metframe’s advantages and the speed, efficiency and economy benefits that the system delivers to every project.
Covering Metframe’s many accreditations, including UKCA and CE Marking, compliance with a plethora of technical performance standards, 30-year wall performance warranty, professional indemnity and industryleading sustainability credentials – the new guide provides the designer with every assurance of the system’s performance, quality and reliability.
In addition, the specification guide covers details on voestalpine Metsec’s support for architects and designers, including CPD presentations and detailed design services together with
an eight-stage RIBA Plan of Works, which clearly lays out the processes involved in the design, specification, construction, handover and ultimate use of the building.
The guide also includes an easyto-follow graphic flowchart of the processes involved when Metsec is engaged, from initial consultation through manufacture to final installation of the Metframe panels as well as the incorporation of other key building elements such as stairs, lift shafts, balconies and floors.
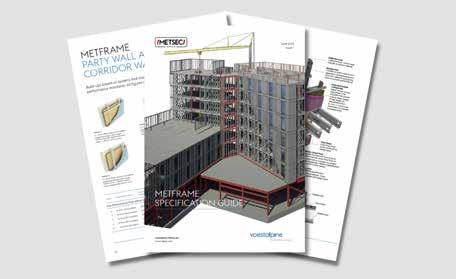
In designing the new guide, voestalpine Metsec’s sales and specification teams were keen to include examples of typical Metframe details for external walls, party walls, internal walls, internal floors, roofs, stairwells and lift shafts. Each area of application is explained with the help of high-quality technical drawings showing the most commonly encountered applications. These include foundation interfaces, window details, party walls with concrete floors, stairwells and roofs.
Framing Sales Director, Chris Holleron comments: “We know how much the design community has valued our previous architectural and system guides and we took the responsibility of creating this new publication very seriously.
“In addition to presenting the speed, efficiency and economy benefits that Metframe is renowned for, the guide also features comprehensive performance and technical details, such as our design services, investment in through wall testing and 30-year Performance Warranty.
“We believe that when it comes to choosing a framing system, designers would be hard pushed to find a better solution than Metframe. The performance and quality of the system is backed up by an array of support
services covering every aspect of the design, manufacture and installation process.
“We hope this new guide will provide design teams with a compelling argument for specifying Metframe as well as acting as a useful reference source for their projects.”
IMAGES 01-04. Metframe, a pre-panelised light steel solution, is used across the UK for various project types including apartments, care homes, student accommodation and hotels.
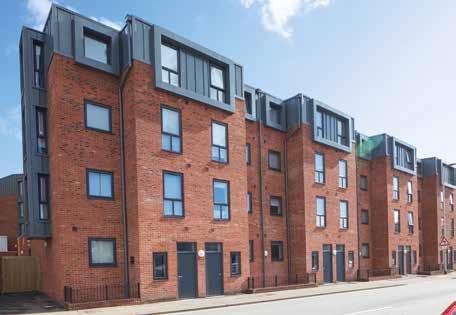
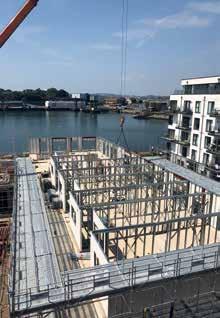
ETEX GROUP LAUNCH
NEW OFFSITE CONSTRUCTION BRAND, REMAGIN
GLOBAL BUILDING MATERIALS COMPANY ETEX GROUP IS DRIVING INNOVATION IN THE CONSTRUCTION INDUSTRY BY LAUNCHING A NEW BRAND, REMAGIN – FOCUSED ON OFFSITE CONSTRUCTION.
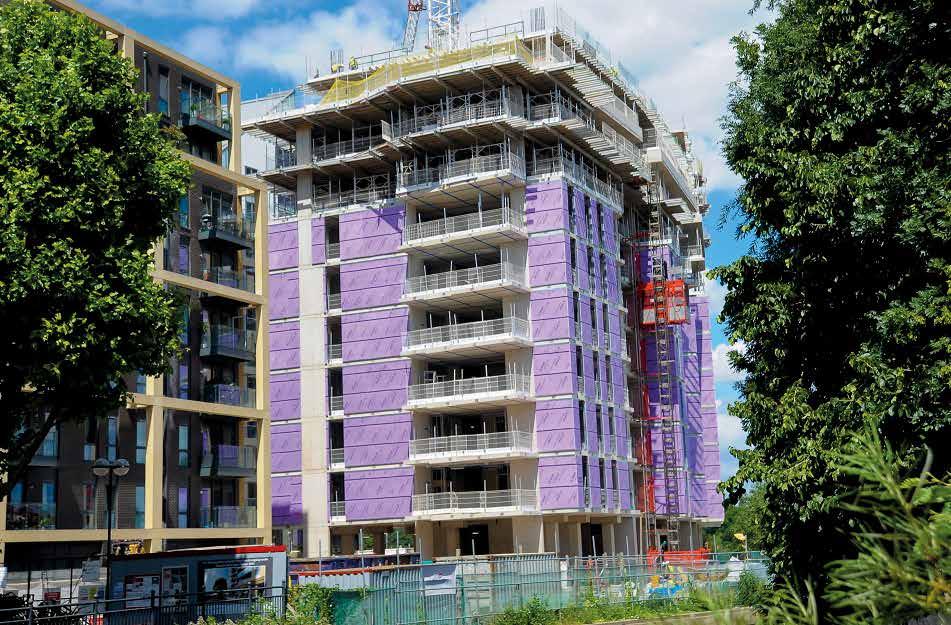
The trend towards greater offsite production has prompted Etex Group to leverage its existing offsite construction companies to create a comprehensive, full-service business, from design to installation, to meet customer demand and drive performance.
By combining the best of their design and engineering expertise, along with manufacturing and installation knowhow, the new brand will offer industry leading, lightweight factory-assembled panels and associated services, all based on sustainable, light gauge steel framing (LGSF).
market leading products, delivered by those at the forefront of design, engineering, manufacturing and installation of complete and compliant light gauge steel systems.
The new brand – called Remagin – brings together the collective capabilities of three existing businesses, Leeds-based Sigmat, County Durhambased EOS and Horizon, operating from Ireland. These businesses have been established in the sector for a considerable time and have developed leading positions in their respective markets in their own right.
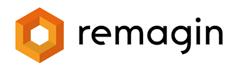
And, backed by the €3.7 billion turnover Etex Group with its significant investments in innovation, system testing capacity through five global R&D centres and its building materials expertise – Remagin is well placed to accelerate the scale and impact of offsite construction.
This move offers assurances to existing and potential customers through a powerful combination of financial security, comprehensive services and
The new commercial branding is part of a broader growth strategy which targets the turnover of the combined companies across the UK and Ireland to more than double between now and 2030 – which will open up significant employment opportunities in various roles across both countries.
Patrick Balemans, Head of the New Ways division of Etex Group of which Remagin is a brand, says: “As part of our sustained efforts to contribute to a better future, we continuously look to evolve what we do and how we do things.
“I’m proud to announce the launch of our new commercial brand, Remagin, which offers highly efficient, costeffective, and sustainable integrated building systems that surpass those of traditional construction methods.” Remagin’s product range spans from kit-form supplied steel frame systems (SFS) for closing off the external envelope on traditionally built structures, through to full loadbearing LGSF superstructures, which it can design, manufacture and install for buildings up to fifteen storeys high. Remagin is well suited to serve sectors as diverse as housing, flats and apartments, retirement living, care homes, hotels, student accommodation, education and healthcare.
Performance is paramount to Remagin. Full-scale testing regimes study the performance of all products within the Remagin portfolio – including metal, boards and insulation – to see how they work together as systems in real-world environments like fire, wind and rain, and ensure that the solutions perform as expected when installed in projects. It is this approach which has led to the development and launch of a number of successful product innovations such as Thrubuild®, Thruwall® and PreAssembled Frames (PAF) over the last few years.
This emphasis on consolidating several products within the Remagin solution not only provides greater assurance on performance; it can also accelerate construction considerably, as several
components can be installed at the same time in the same panel. For example, external panel products integrating boards, insulation, membranes and factory-fitted windows have recently been introduced and installed on a number of customer sites with great success. As well as construction speed, site efficiency is also improved, as the number of operatives on site and the need to co-ordinate them (and deliveries) is reduced.
As the industry addresses the challenges inherent to building a more sustainable world, offsite construction and light gauge steel frame can have an important role to play. As light gauge steel frame has a high strength to weight ratio, relatively fewer resources are extracted and consumed compared to traditional construction – and the steel Remagin uses has a high recycled content (59%), and already has a high recovery rate in terms of recycling (>90%). Much of Remagin’s steel is already covered by EPDs, with the complete range due to be covered by the end of 2023. Beyond steel, Remagin solutions also work well in sustainability terms on other levels. Due to controlled conditions, waste is minimised during manufacturing and at site is virtually eliminated. And, as Remagin solutions often consolidate several components into a single system, vehicle movements to and from site are reduced and emissions consequently minimised.
Scott Bibby, Country Manager for the UK and Ireland, explains: “This is
an exciting time in the development of not just our own business but the wider offsite construction sector. Due to the flexibility and proven benefits of panelised building systems, things are really taking off and by combining our joint strengths we are confident we can accelerate and maximise sector growth.
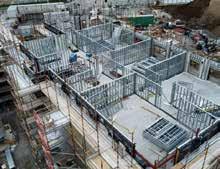
“Remagin is building on the solid foundations established by Sigmat, EOS and Horizon and is backed by Etex Group with its significant R&D and testing capacity and materials expertise. We are in a strong position to add significant lifecycle value and sustainability benefits to our customers.”
For more information visit: www.remagin.world
IMAGES
01. Riverside Quarter – the first development in the UK to use Pre-Assembled Frames (PAF)
02. Patrick Balemans, Head of the New Ways division of Etex Group

03. Sandy Park, Exeter – a new 5 star, nine-storey Marriott Hotel
04. A light steel frame systems approach
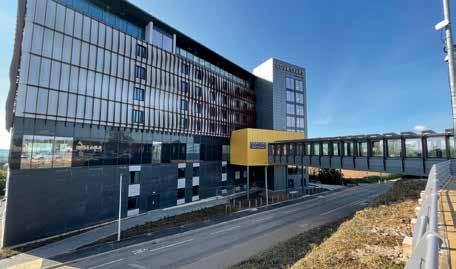
1000 DISCOVERY DRIVE HITS PROJECT MILESTONE
Prologis UK, developers of life sciences real estate, held a topping out ceremony at 1000 Discovery Drive on 21 March alongside contractor SDC. The event followed the completion of the structure for the new laboratory and business use space at the Cambridge Biomedical Campus.
Light steel frame specialists Metek are installing a steel frame infill panel system for the project. The double-height system was manufactured offsite, complete with an external sheathing board, insulation and vapour membrane, before being transported to the site.
To mark the milestone, a commemorative plaque signed by the project team was attached to one of the steel beams before being lifted into place. Once complete, 1000 Discovery Drive will offer a variety of laboratory and office space. It will also feature amenities for the wider campus and community, such as a café and open-source community centre.
Daniel Changer, Director at SDC, spoke at the event, offering insight into the next stage of construction and the increased opportunities 1000 Discovery Drive would provide to the area. “We know this building will be fundamental in shaping the future of the Biomedical Campus as an incubator project
for both the companies that become tenants and the surrounding research-led organisations. As we continue to develop 1000 Discovery Drive, the vast social and economic benefits that the space will bring become clearer, in both increased job opportunities and continued business growth in the area. Our whole team understands the profound responsibilities of their involvement.”
Project handover is set for October 2023, following which the fit-out will commence.

Image: Prologis UK 1000 Discovery Drive will offer a variety of laboratory and office space.
Steel framed modular housebuilder CoreHaus has announced the promotion of Dan Selby as its new Managing Director. Dan has been with the company since 2020 and played a pivotal role in setting up the production facility at Jade Park, Seaham.
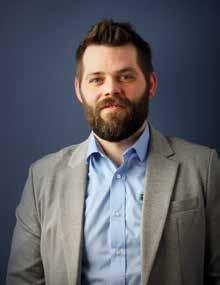
Following the news, Dan said: “I’m thrilled to be taking on the role of Managing Director at CoreHaus. It’s been a pleasure to head up operations for the company over the last two years and be directly involved in everything from launching the factory and building the team to developing the product and securing our first commercial projects. I’m looking forward to building on the strong foundations we have in place and driving this next phase of growth.”
Dan will be focusing on driving growth and expansion within the business. The company
has plans to scale up production following the delivery of its first affordable modular homes for Believe Housing in conjunction with housebuilder Homes by Carlton.
Dan added: “We are currently in the final pre-construction phase on two projects in the northwest with a leading housing association and have developed a strong pipeline for the next two years across the north. At CoreHaus, we are perfectly placed to provide a sustainable, flexible, high-quality, and competitively priced solution. We have an ambitious five-year plan to build over 1,000 units per year. I look forward to growing and developing the team over the coming years and helping our partners deliver high-quality affordable housing with our modular solution.”
Image: Dan Selby, Managing Director, CoreHaus.
COREHAUSAPPOINTS DAN SELBY AS NEW MANAGING DIRECTOR
How to Choose the Right Howick Framing System



Standard Howick Framing Systems. The quickfire guide to finding the right Howick machine
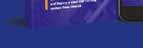



































From the workhorses FRAMATM 3200 and 5600 – great for all standard framing needs – to specialised machines like the X-TENDATM 3600 (extendable frames for infill spaces) and the FRAMATM 6800 (floor joist system) that are highly optimised to produce specific components, you will find we have a system available that meets most framing component manufacturing needs.
If you are thinking of something out of the ordinary, we also provide a range of customised options for our standard machines; we have even designed and manufactured new innovations to help solve specific challenges. Just talk to us about what you are trying to do.








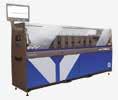
Want a great compact workhorse system that will produce most standard framing requirements for housing and low-rise? You do not need to look any further than the FRAMA™ 3200.

You want a workhorse capable of making heavier load-bearing framing for large build projects, low-rise and commercial with greater capacity and increased flexibility? The FRAMA™ 5600 is the right horse to jump on.
You want a dedicated truss system that is highly efficient and produces in volume? Step up to the FRAMA™ 4200 and try that for size. It is the system you can truss. (See what we did there?)






You want a dedicated flooring system that manufactures more efficiently than assembling lattice flooring? The FRAMA™ 6800 pops out floor joist cassettes with gusto. Plus, you will find them much more efficient to install.


You want a convertible frame and truss system with high output capacity that can be adjusted to handle 5 different profiles in the one machine? Welcome to the ultimate flexibility of the FRAMA™ 7600. It offers 5 different profiles and can be configured for floor joist production, framing production, or customised for both frame and joist tooling.
You want a convertible system that can handle heavier gauge than the FRAMA™ 7600? The FRAMATM 7800 is the big brother of all the rest, it offers everything the FRAMATM 7600 does, and it can handle thickness of up to 2.5mm / 13 gauge.
You want the fastest way to build retrofit and infill framing for interior spaces? The X-TENDATM 3600 makes telescopic framing that is extendable in any direction to fill any space fast. It is the latest innovation in infill framing technology.


You want to improve the efficiency of your framing plant by 5%? Just add the option of a Howick dedicated coil-loading system. Over a 7-hour shift, you will improve efficiency by 5%.







To find out more about setting up construction manufacturing with light gauge steel framing automation, simply scan the QR code to download our Machine Buyer Guide.
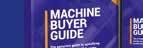
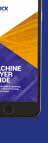

£2M INVEST NI FUND SEES SFM ENGINEERING EXTEND FACTORY
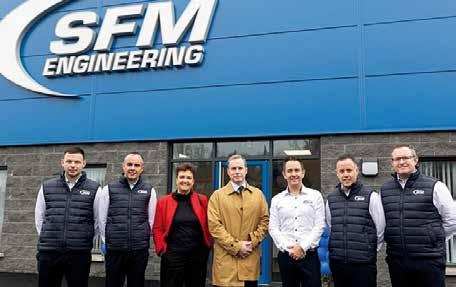
Light Steel Frame Association (LSFA) member SFM Engineering is celebrating the opening of a new factory extension. The £2 million investment has seen a 20,000 sqft extension added to their current facility.
At the opening, Paul Breen, Director of SFM Engineering, said: “We are thrilled and very proud of the completed works to the factory. The new extension allows for greater capacity, giving us a fantastic opportunity to capitalise on the growing materials-handling industry. We have built strong strategic relationships with our customers, and this increased capacity allows us to develop these further. Invest NI has also supported us with the refurbishment works and helped us purchase new equipment, making us more competitive globally."
MORGAN SINDALL DELIVER ENERGY-FRIENDLY BRIGHTON HOMES
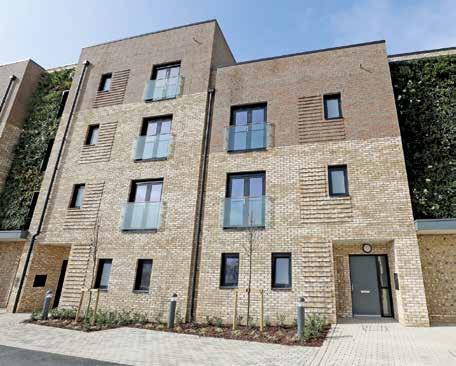
An £11 million council housing development constructed in Portslade, Brighton as part of the Brighton and Hove Council New Homes and Neighbourhoods scheme, is complete. Morgan Sindall Construction's Southern Homes Counties business has delivered a mix of one, two and three-bed sustainable homes close to Portslade Town Hall.
The energy-friendly homes use sustainable features such as solar panels and ground-source heat pumps, while the addition of communal gardens provides a green area for residents. Each home has been designed to reduce carbon emissions and lower energy bills. The Morgan Sindall team worked in partnership with offsite construction specialist Sigmat, to target carbon reductions with the design, manufacture and installation of a light steel frame system for the scheme.
Morgan Sindall is working with Brighton & Hove City Council to provide a range of affordable housing under the council’s five-year Strategic Construction Partnership, launched in 2018. It is on track to deliver 800 new homes within the city.
SFM Engineering is a manufacturer for the material processing equipment industry, playing a key role in the global supply chain. The cutting-edge facilities and equipment will help increase its manufacturing capability and open new market opportunities. In previous years,
Invest NI has supported SFM with investments in marketing, leadership training and technical assistance.
Guy Hannell, Area Director for Morgan Sindall Construction in the Southern Home Counties, said: “It is an exciting moment for everyone involved in the Victoria Road project at Morgan Sindall and Brighton & Hove City Council, as we have delivered high-quality, sustainable homes for the long-term future for the people of Brighton & Hove. In line with the council’s carbon-neutral target of 2030, and as part of our intelligent solutions approach to
creating sustainable facilities, the project team has prioritised carbon-reduction techniques at every stage throughout the build and in operation. This will secure the long-term future of these muchneeded homes.”
Image: Morgan Sindall
The energy-efficient homes combine a light steel structure with sustainable features.
At Frameclad, we manufacture light steel frame secons from our 50,000sq facilies in the West Midlands. With constant product development and tesng we now produce material from 6 state of the art machines giving you an extensive range of products to meet your demands. With in house design and engineering capabilies in our North East office, we can supply you various products ranging from simple lengths of secon through to large high rise load bearings structures and everything in between. Find our details online or email us at enquiries@frameclad.com

In House Design and Engineering Services





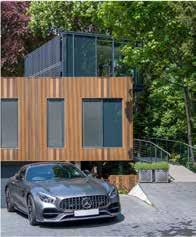
Mul Profile SFS component Supply
Infill SFS Supply inc assembled soluons
Offsite Manufacturing Supply
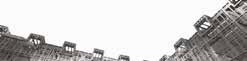
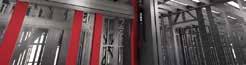
Low to High Rise Load Bearing Light Steel Framing
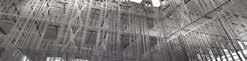
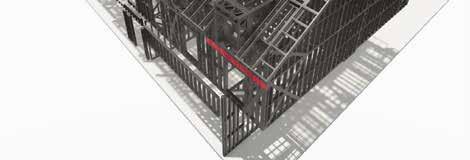
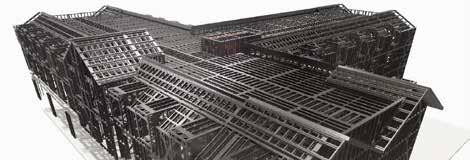
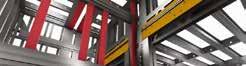
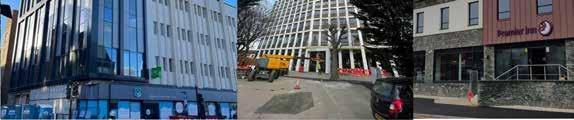

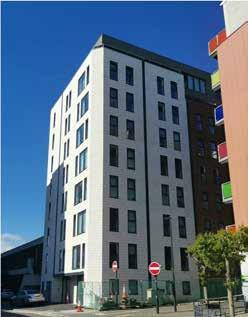
www.frameclad.com
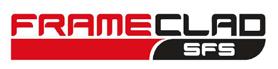
TEKLA 2023 STRUCTURAL BIM SOFTWARE UPDATE
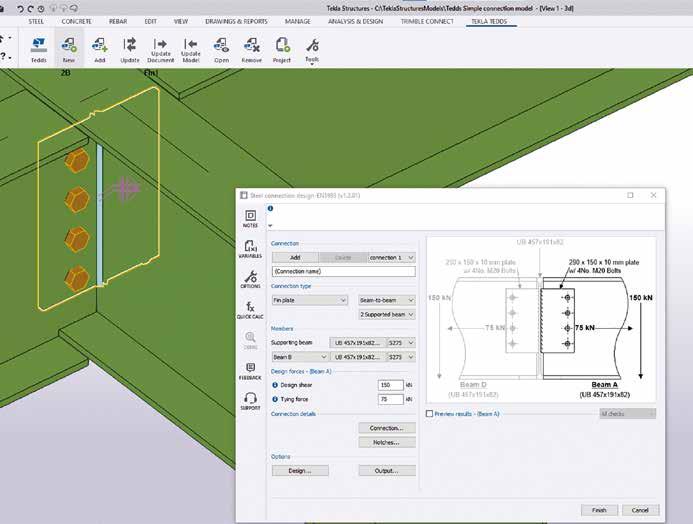
Trimble has announced the introduction of the latest versions of its Tekla® software for constructible Building Information Modelling (BIM), structural engineering and steel fabrication management. Tekla Structures 2023, Tekla Structural Designer 2023, Tekla Tedds 2023 and Tekla PowerFab 2023 all offer significant improvements in construction productivity, efficiency and quality.
These latest Tekla versions include significant performance enhancements, enabling smoother information delivery on projects that are typically growing in both size and intricacy. Robust software performance is key to enabling multiple stakeholders to consult, use and feed data into the models in connected workflows. The Tekla software provides a connected construction environment with an integrated suite of solutions, centralised data, streamlined workflows and comprehensive visibility throughout the course of a project. Connected construction enables precision production and reducing rework through constructible design. It forms the basis for green construction strategies to optimise the use of resources, minimise waste and enable full asset lifecycle maintenance.
With the use of open standards, Trimble’s Tekla software products have an active partner community, developing on the Tekla API complementary applications and integrations for specialised industry sectors such as scaffolding design, industrial projects and detailing for modular construction such as light metal framing.
The structural BIM software continues to improve the user experience of both new and more experienced users by making it easier to learn and adopt time-saving functionalities faster. Apart from several improvements in software performance, the upgraded drawing editing user experience makes the software easier to learn and use.
Tekla Structures raises advanced detailing for fabrication workflows and project communication to a new level. In rebar detailing, complex bar shape designs are easier to share with procurement, manufacturing and the construction site. Customers in steel fabrication benefit from greater flexibility by being able to cover more detailing options related to bolts and holes for specialised industries. The software also features updated outputs and exports in the field of detailing for fabrication of multiple types of projects and materials.
Speaking about the launch, Michael Evans, Senior Product Director of Trimble Structures, said: “Our product development focuses on delivering solutions that make building information more easily available, constructible and shareable to stakeholders across the industry, to optimise the use of resources. Through continuous enhancements, in-product intelligence and expanded support for sustainable construction, we provide our customers with one of the most advanced BIM technology platforms on the market today.”
Information Security
As part of Trimble’s ongoing efforts to provide enterprise-level security required in environments that thrive on data sharing, all Tekla products are certified to be fully compliant with ISO27001, the leading global standard for information security management.
To learn more and to download Tekla 2023 versions, visit: https://support.tekla.com/tekla-2023
JOINT VENTURE TO DELIVER £10B OFFSITE FRAMEWORK
UK infrastructure services, construction and property group Kier, alongside Joint Venture Partners McAvoy and Metek, have been appointed to a new £10 billion Offsite Construction Solutions (OCS) framework. The new framework replaces the existing modular building framework and consists of six lots due to run until 2027, potentially extending to 2030.
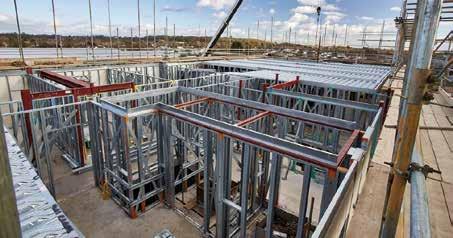
McAvoy is one of the UK and Ireland’s market leaders in the precision manufacture and delivery of high-quality modular buildings. Gloucestershirebased Metek has been at the forefront of light steel framing for many years.
The two joint ventures, Kier McAvoy and Kier Metek, will allow for the delivery of high-quality, innovative, and precision design. Kier McAvoy will deliver projects using pre-manufactured 3D primary structural systems. Kier Metek will deliver projects using pre-manufactured 2D primary light steel structural systems.
The OCS framework consists of six lots determined by Crown Commercial Service (CCS). These include built estate, healthcare, residential, justice, defence and thermal efficiency upgrades. The CCS ensures maximum commercial value when procuring public sector common goods and services.
Stuart Togwell, Group Managing Director at Kier Construction, said: “Building on the ambitions of the Construction Playbook of using MMC and offsite solutions to drive improvements is a core imperative
FLOOR DECK FOR LIGHT STEEL FRAME CONSTRUCTION.
for Kier and securing a place on all lots means we are well-placed to support the delivery of vital new infrastructure in the UK. Our forward-thinking JVs with McAvoy and Metek will allow us to provide more capacity and high-quality end-to-end solutions for our public sector clients and to continue to deliver the best value through innovation across the wider industry.”
Image: Kier Metek will deliver projects using pre-manufactured 2D primary light steel structural systems.
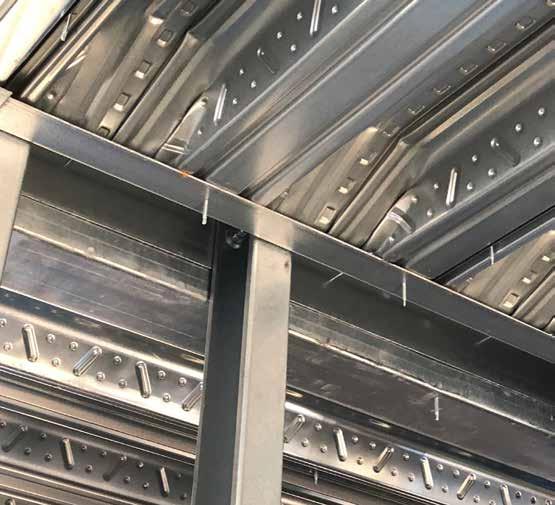
Our dedicated Supply Only team are happy to help with customers design and installation queries.
Our product range and crushed end finish are perfect for the light gauge solution.
Due to demand, our dedicated production line manages large volumes and quick delivery times.
LIGHT GAUGE DIVISION
DECK SOLUTIONS
PRODUCTION LINE
HOWICK SURVEY REVEALS CHALLENGES AND OPPORTUNITIES FOR SOFTWARE DEVELOPERS
Howick, the New Zealand based manufacturer of light steel roll-forming technology, recently undertook a global construction software survey. The results of the survey are now available, providing valuable insights into the brands of software in use, how those tools are being used and how they might be improved for the benefit of users.
The survey was completed by 242 leaders in the construction industry. It explored the overall usage of construction technologies like framing automation and CNC-driven technology. It looked at how the take-up of software changed by sector. Then it delved into specific categories, including architectural design, MEP design, framing detailing, engineering analysis, cloud-based BIM and the usage of 2D and 3D technology.
Construction Software Insights
The survey findings provide significant insights to benefit users and software developers. As well as ranking the penetration of the different brands in use across construction sectors. While the use of technology in the industry is increasing, the results revealed challenges to be addressed, as well as opportunities for future development to encourage
NEW FACTORY WILL SEE WESTON HOMES EXPAND PRODUCTION
Essex-based housebuilder Weston Homes has taken possession of a 180,000 sqft factory facility in Great Notley. The company is set to produce 4,000 light steel frame homes per year which will be used to supply their own and other developer's projects.
Weston Homes has been based in Braintree since 2019, delivering bathroom pods and lightweight steel external panel systems which can be fitted within concrete frame structures. Production of the panel systems - UniPanel, UniWall and UniHouse - will now move to the Great Notley site, expanding their production capacity significantly. The firm has invested £6.5 million in robotic technology made by experts in automation solutions, Randek for the assembly of the systems.
further adoption. There were several common themes highlighted in the overall responses relating to desired features and functionality.
In conclusion, the survey results validate that the light steel frame construction industry is increasingly embracing technology to improve efficiency and streamline processes.
Access the Full Construction Software Survey Findings

Visit www.howickltd.com/stories/constructionsoftware-survey-insights to download the full Howick construction software survey findings and get a detailed look at how the construction industry is adopting and using software currently.
Image: Courtesy of Tekla Tekla Structures BIM Software in use.
Weston Chairman and CEO, Bob Weston said: “The production line in the new British Offsite factory has been installed with the ambition for the facility to be fully operational this month.
Image: Weston Homes/ British Offsite
The new British Offsite factory is set to produce 4,000 light steel frame homes per year.
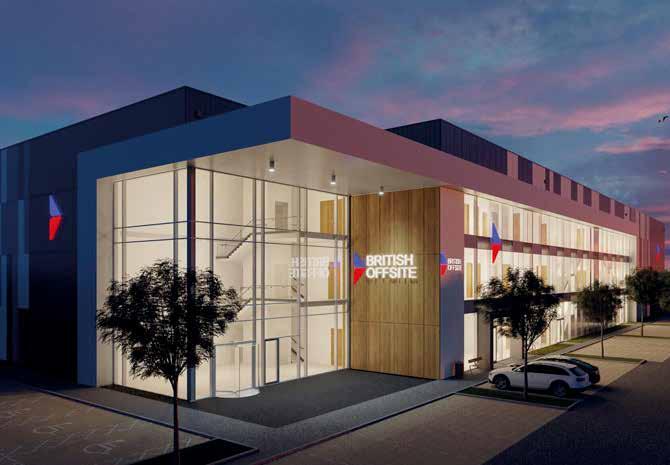
A DIFFERENT WAY OF THINKING
CREATORS OF UNISYSTEM, A TECHNICALLY ADVANCED LIGHT GAUGE STEEL PANEL SYSTEM, SUITABLE FOR HOUSE, MID-RISE AND HIGH-RISE DEVELOPMENTS. ALL PROJECT SIZES CONSIDERED.
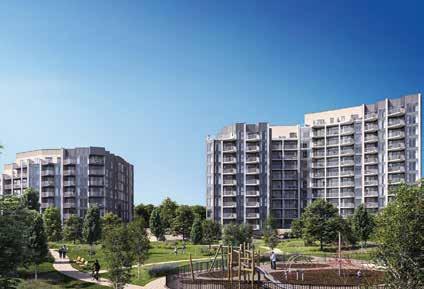
British Offsite is part of the new high-tech manufacturing sector in the UK, with a world class team that’s bringing the best of automotive manufacturing and the logistics industry to home building.
We have two state-of-the art factories; Skyline and our new 137,000 sq ft Horizon factory, which has the capacity to create a complete set of panels for one apartment every 60 minutes. With our two factories we can create 4,000 new homes with internal fit-outs, every year.
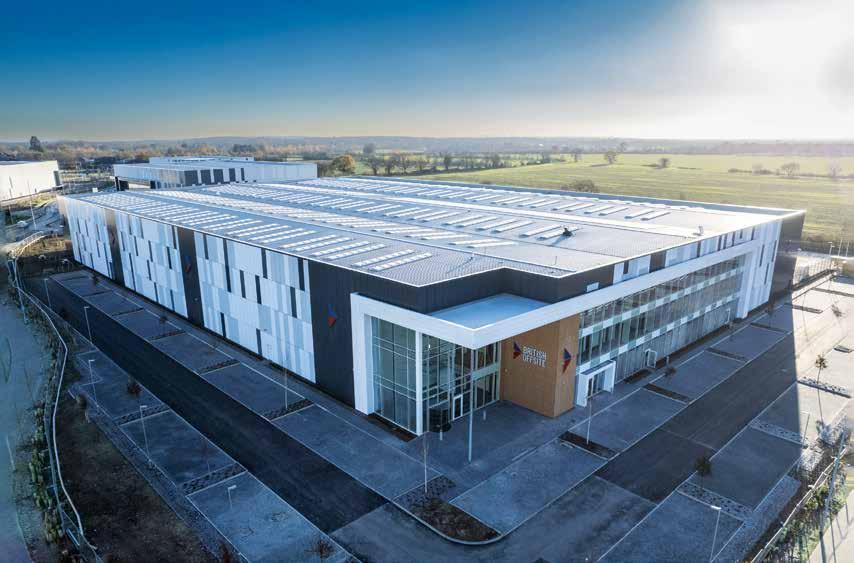
WE’RE BRINGING THE BEST OF AUTOMOTIVE MANUFACTURING AND LOGISTICS TO HOME BUILDING
Think British Offsite from the offset
Dylon Riverside, SydenhamCOLLABORATION WILL BRING 184 HOMES TO JERSEY
A planned project between Sigmat, ROK Group, and Andium Homes will see 184 new homes built in Jersey. Sigmat announced the joint venture, which will offer much-needed housing to the area, with 169 of the planned homes being affordable social housing.
The Northern Quarter project will involve the demolition of existing warehouse buildings before construction can begin. The residential scheme will be located opposite Millennium Town Park and
INTELLIGENT STEEL GO INTO LIQUIDATION
South London residential contractor Henley Construct has gone into administration after it was announced that sister firm Intelligent Steel Solutions went into liquidation earlier this year. Concerns rose for the contractor after reports that Intelligent Steel owed £1.4 million to suppliers.
will be built across four blocks offering apartment housing. Sigmat will provide 418T transfer structures for the development.
Head of Sigmat, Paul Smith, said “This is a very exciting collaboration for us. We are pleased to help more companies recognise the potential of building using Modern Methods of Construction. Safety, quality, and programme are part of our core pillars and a key advantage of offsite construction and the Sigmat process.”
Andium, Jersey's largest affordable housing provider, plans to deliver 3000 new homes to Jersey by 2030. Sigmat is working with the planning team to provide the most cost-effective and environmentally friendly solution, intending to be on the site later in 2023.
Image: Rok Group/Andium Homes
The residential scheme will be built across four blocks offering apartment housing.
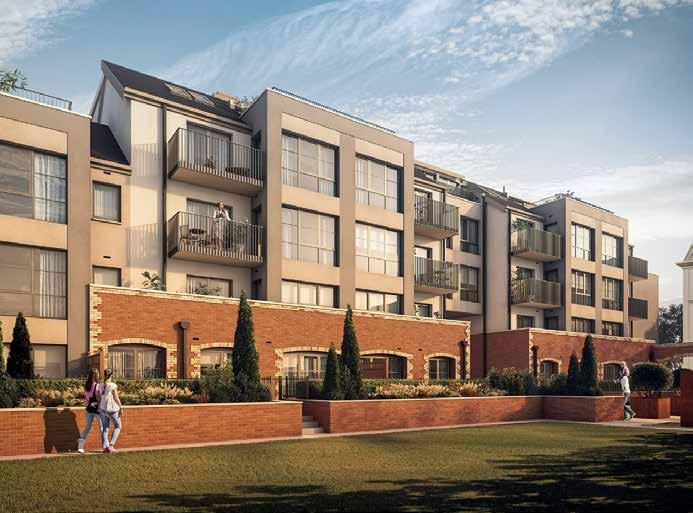
The two companies share the same Directors, Kashif Zafir Usmani and Tariq Zafir Usmani, with 360 Insolvency stating that the firm “relied to a large extent on supplying structural steel for projects being conducted by Henley Construct.”
Staff for both companies were put on unpaid leave and are at risk of redundancy. Intelligent Steel claimed the move to unpaid leave in early February was due to the aftermath of Brexit,
Covid, and the onset of a recession affecting the industry. It is currently expected that creditors will not receive payment for unpaid invoices.
County Durham based Intelligent Steel Solutions is reported to have 55 unsecured creditors, having amassed a £4 million loss in the last 15 months. Both companies have headquarters in Battersea in South London.
MAX PowerLite tools are extremely powerful yet their size is 40% smaller and tool weight is 30% lighter than conventional regular pneumatic tools with a wide variety of fasteners.




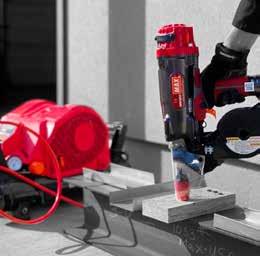
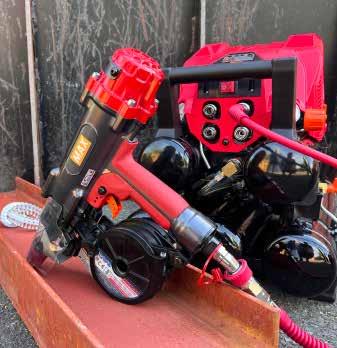

WELSH FIRST MINISTER OPENS INNOVATION CENTRE
The Rt Hon Mark Drakeford MS, First Minister of Wales, has conducted the official opening of the Innovation Centre at Maesteg. The £1 million facility will provide a bespoke space for the enhancement and quality control testing for developing passive fire protection systems.

Siderise Insulation, a global leader in the design, manufacture and supply of high-performance passive fire protection solutions, will use the innovation centre to enhance its research and development. The purpose-built facility features a specialist fire test furnace. Siderise seeks to achieve UKAS accreditation for the test furnace, which would allow others in the construction industry to use it.
This would help support fire safety standards across the sector and highlight Wales as a leader in safety innovation. Siderise's unique manufacturing and testing processes have seen significant success, helping the company to expand into the global market.
DRYWALL PREPARE FOR MOVE TO NEW FACTORY
A Black Country manufacturer is expanding its operating base with a new, purpose-built factory following a £9.5million investment by the West Midlands Combined Authority. Drywall Steel Sections is getting ready to move to the soon-to-be constructed 39,500 sqft factory on four-and-a-half acres of brownfield land in Ettinghall, Wolverhampton.
Drywall, manufacturers of light structural steel framing systems, wall partitions and ceiling systems, say the facility will enable the firm to safeguard existing jobs and provide the extra capacity required as the business grows.
Andy Street, Mayor of the West Midlands and WMCA chair, said: “Firms like Drywall remain the backbone of the West Midlands economy and keep our proud manufacturing heritage burning bright. I am pleased we can support them in this way and look forward to seeing them move into their new factory and continue to prosper.”
Chris Mort, R&D Director at Siderise Insulation, said: "Opening the doors of our Innovation Centre marks a huge step forward for Siderise and represents a huge investment in our Maesteg head office and manufacturing site. Our core guiding principle is 'integrity in all we do' - this means that the products we create and the services we provide are underpinned by clear research and proven results."
The ceremony was also attended by special guests Huw Irranca-Davies, member of the Senedd for Ogmore, and Cllr Martyn Jones, Mayor of Bridgend.
Image: Siderise Insulation
The Rt Hon Mark Drakeford opening of the Innovation Centre at Maesteg.
Drywall Managing Director, Mayank Gupta, said: “We are extremely grateful to the WMCA for their support in unlocking this brownfield site. The new Drywall Steel Sections unit and the smaller units in the new Industrial Park will provide a significant contribution to the overall regeneration and economic renaissance currently underway all over the West Midlands. We are proud to move our manufacturing business headquarters back to our home city of Wolverhampton, retaining all existing staff, with further plans to create more jobs as the company grows”.
around 150 new jobs.
Image: West Midlands Combined Authority. Credit: Dale Martin dale@dmphotos.com
Andy Street, Mayor of the West Midlands and WMCA Chair with Drywall Managing Director, Mayank Gupta.

With excellent circular construction credentials, light steel is strong and durable, lightweight, safe, adaptable, cost efficient and reusable.
LONG LASTING ASSET
99% of structural steelwork is reused or recycled
Steel can be recycled or reused endlessly without detriment to its properties Steel components can be reused with very little or no reprocessing Reuse offers even greater environmental advantages than recycling

LIGHT STEEL SPECIFIED FOR NEW MOLECULAR
SCIENCE FACILITY
The University of Birmingham is investing in a new Molecular Sciences building, which will provide a designated hub for the School of Chemistry along with facilities for the School of Geography, Earth and Environmental Sciences (GEES).

Morgan Sindall has awarded Drywall Contracts Limited the steel framing systems works at this flagship six-storey building. Due for completion in 2024, the £45 million scheme is the first
DORMAN HOUSE COMPLETE AND FULLY BOOKED
Dorman House, Linthorpe Road in Middlesbrough is Atha Students’ flagship development of 55 apartments all fully equipped with state-of-the-art kitchens and ensuite shower rooms.
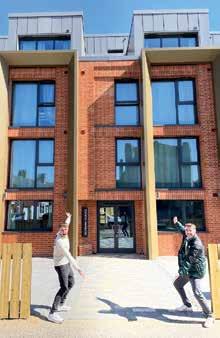
Only recently completed, this brand new accommodation designed for students and young professionals – is fully booked right up until the end of 2024. As well as superior private apartments, Dorman House offers the chance to socialise in a fully equipped residents lounge, as well as an adjoining high tech private cinema and secluded courtyard garden.
stage of a multi-phased master plan that will provide further academic accommodation in the coming years. Facilitating greater collaborative working, the building will be a showcase for innovation and research at Birmingham University and a place to connect that research to education.
Professor Rachel O'Reilly, Head of School of Chemistry, said: “The Molecular Sciences building will strengthen our core research capabilities in the chemical, environmental and
Atha Students is a property developing company founded in 2011 that specialises in student housing, with an aim to become the biggest private supplier of luxury student accommodation for Teesside University.
Using a light steel frame systems approach, Dorman House provides safe and sustainable student accommodation which will stand the test of time. The brothers behind this development – the Atha Property Twins said: “It has been a labour of love, but we are so chuffed that our flagship student accommodation, Dorman House is now fully up and running – filled with some awesome students.
We believe that our students deserve the best in terms of luxury accommodation and aftercare services and that is why we were determined that our new development offers all the comforts of home, along with some cool added extras.”
Image: Atha Property Twins celebrate the launch of Dorman House.
biomolecular sciences, fostering an environment for carrying out world-class research. This vibrant, inclusive workplace with state-of-the-art facilities will attract talent from the broadest pool. We look forward to working in our flexible space that will allow greater staff, student and external stakeholder interaction.
Image: Morgan Sindall appoint Drywall Contracts Limited for the steel framing works at the new Molecular Science facility.
ROB HEEBINK STEPS UP AS NEW FRAMECAD CEO
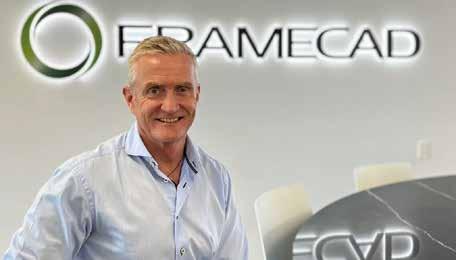
Framecad has announced the appointment of its new CEO following an expansion of its leadership team. Rob Heebink has been Framecad's Chief Technology Officer since July 2022 and steps into the role with 14 years of experience in research and development. Founder and former CEO Mark Taylor will now act as Executive Director of the Framecad Group.
Framecad is a global leader in advanced end-to-end steel frame building systems for residential and commercial construction. The company offers technology and design-led methodology, further boosting the use of cold-formed steel solutions and offsite construction.
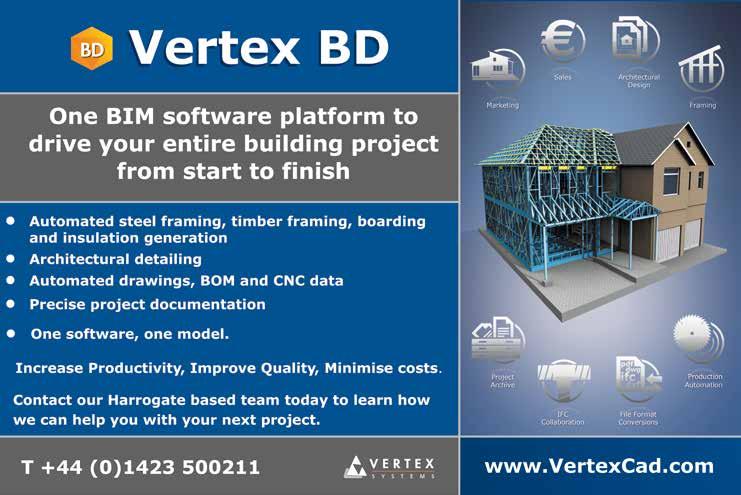
Mark Taylor said: “We have added multiple roles to the leadership team, both locally and within our key markets, to structure the company for its next phase of growth. The next logical step was to appoint a
new CEO to lead this team. I plan to devote my time to support the business and to work with Rob and the team to identify emerging opportunities, strategic partnerships and accelerated growth initiatives.”
A global search for the candidate led to the appointment of Heebink due to his in-depth understanding of the challenges and opportunities of executing a product-growth strategy on a worldwide scale.
Framecad Executive Chair Mike Riley said: "The market opportunity for the Framecad building system is large and growing. The challenges of constantly changing building practices in an industry subject to accelerating climate change and materials shortages present enormous opportunities for Framecad’s innovation and vision for the future of construction."
Image: Former Chief Technology Officer, Rob Heebink has been appointed Framecad’s new CEO.
RADICALLY RETHINKING REUSE TO CUT CARBON IN STEEL
CONVERSATIONS ABOUT DECARBONISATION MUST CONTINUE AT PACE AND FOR THESE DISCUSSIONS TO BRING ABOUT REAL CHANGE, AS AN INDUSTRY
WE HAVE TO PUSH FORWARD IN A NUMBER OF AREAS, ONE OF THOSE BEING THE ACCELERATION OF OUR TRANSITION TO A NET ZERO STEEL FUTURE. BUT WHAT DOES THE BUILT ENVIRONMENT NEED TO DO – BOTH RIGHT NOW AND IN THE FUTURE, TO HELP MAKE LOWER CARBON STEEL A TANGIBLE PROSPECT? ADRIAN BYWATERS, OPERATIONS DIRECTOR FOR ENGINEERING AT MACE, CONSIDERS THE OPTIONS.
1000 times stronger than iron, steel is one of the most commonly used materials on the planet. There are challenges impacting steel’s carbon footprint, but one of the main obstacles is the manufacturing process, which is typically carbon intensive. So decarbonising new steel production will be driven largely by powering furnaces with sustainable energy alternatives. Hydrogen-fuelled furnaces are being
billed as a promising option, and there are new steel producers entering the market adopting less carbon intensive manufacturing methods.
Reuse is King
By rethinking our approach to design, material use and collaboration, there are things we can do immediately to reduce carbon in steel. But we must
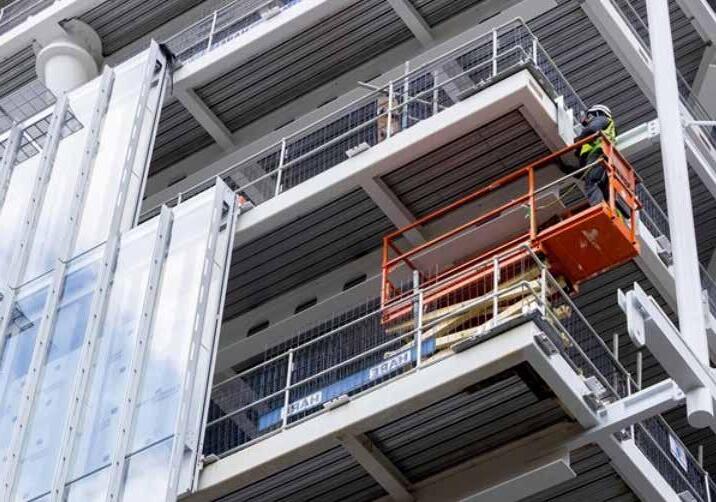
also play the long game – engaging with each other to make better use of resources, while considering the whole lifecycle of a building and its component parts.
When it comes to carbon, reuse of materials will always be preferable to new production. Once steel has been manufactured, it is a permanent
resource, so can be infinitely reused and repurposed – without any loss of material properties.
Repurposing steel involves taking existing beams and columns, trimming, cleaning, and treating them, so that they can be used again without adding carbon to the process. But securing supply of the right grade and section size of steel can pose challenges.
Steel can also be melted down if it cannot be reused directly, making recycling a viable option. While melting does require carbon expenditure, it still generates less than manufacturing new steel from raw materials.
Options like electric arc furnaces can incorporate higher scrap content rates and generates a fifth of the carbon compared to the traditional Basic Oxygen Furnace.
We should also be sharing our aspirations with steel suppliers, challenging them to create and find products which meet carbon targets. We can do this by requesting steel and stating the desired level of embodied carbon, instead of defining the manufacturing process or source. This gives suppliers the freedom to source the most carbon efficient way
for any given project. As such, this approach does not constrain projects to a manufacturing process or single supplier and engages the steel suppliers’ expertise to find the lowest carbon solution available.
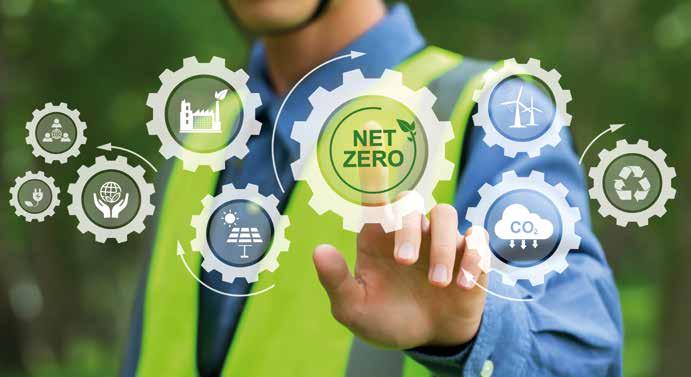
Existing Structures and Circularity in Design
Promoting partial or complete repurposing of buildings enables reuse of materials in situ, saving a huge amount of carbon. Wherever possible, we should drive clients to opt for refurbishment, instead of demolishing and building from scratch.
We also owe it to future generations to think about what happens at the end of an asset’s life when we are designing new buildings. The buildings we are trying to repurpose now were designed or built 30 to 50 years ago. We should be designing buildings for easier reuse or dismantlement to encourage circularity, creating structures which are easy to repurpose and dismantle. Because if you can dismantle a structure, you can reuse the component parts, reducing the need for raw materials for future projects. Design teams must review architectural intent, structural design, and material availability to assess the options available and constraints of a project
- this will enable the lowest carbon solution to be identified.
Acting Now
While the use of sustainable energy to decarbonise the steel supply chain will soon be a workable option, we still need to do everything we can right now to decarbonise steel itself. That means sourcing existing or refurbishing more to utilise steel already available in a structure - instead of building a new one from scratch. When we do have to build new structures, it means designing and building them as sustainably as possible with the lowest embodied carbon.
And the
journey doesn’t stop there.
We need to think about the future use of chosen materials by making those structures easy to demount and repurpose, giving a head start to future generations decarbonisation efforts in the built environment.
For more information visit: www.macegroup.com
IMAGES
01. Image courtesy of Mace
02. By rethinking our approach to design, material use and collaboration, there are things we can do immediately to reduce carbon in steel.
100% RECYCLABLE INFINITELY REUSABLE
THE OFFSITE INDUSTRY CAN PLAY A VITAL ROLE IN ACHIEVING A CIRCULAR ECONOMY, REDUCING THE BURDEN ON NATURE BY ENSURING RESOURCES
REMAIN IN USE AS LONG AS POSSIBLE. LARGE SCALE USE OF RAW MATERIALS IS STANDARD IN CONSTRUCTION, BUT MIKE FAIREY CHAIR OF THE LIGHT STEEL FRAME ASSOCIATION (LSFA) SAYS THERE HAS TO BE A BETTER WAY.

At its simplest, the circular economy prioritises the reuse of materials, preventing the over extraction of natural resources and the amount of usable construction components that end up in landfill. There is growing pressure on the construction industry to reduce waste and to achieve this we have to move towards resource efficiency.
But first we have to address the commercial realities associated with making this practically happen by ensuring information is readily available. Steel has excellent circular economy credentials both as a material which is strong and durable and as a structural framing system which is lightweight,
adaptable and reusable. The qualities of strength, longevity, recyclability, availability, versatility and affordability make light steel frame unique.
Circular Construction Principles
Design optimisation is crucial in a circular construction approach and a lot of thinking has to be done up front. Once the architectural priority was form and function but now there are a raft of considerations coming to the fore such as design for longevity, flexibility, adaptability and the offsite mantra of –design for manufacture and assembly (DfMA). But that is not all, it is imperative to plan for a building’s ‘end’ right at the beginning of the design stage to
enhance the sustainability value chain through design for disassembly and recoverability protocols.
Long Lasting Asset
Manufactured from the most abundant component on earth, steel can be recycled or reused endlessly without detriment to its properties. This unique characteristic gives steel a high value at all stages of its lifecycle. The recovery infrastructure for steel recycling is highly developed and extremely efficient and has been in place for decades. Current recovery rates from demolition sites in the UK are 99% for structural steelwork and 96% for all steel construction products – figures
that far exceed those for any other construction material.
Research carried out by the LSFA’s technical partner, the Steel Construction Institute (SCI) has estimated that there are around 100 million tonnes of steel in buildings and infrastructure in the UK. This ‘stock’ of steel is an important and valuable material asset that means we are largely self-sufficient in steel and can virtually produce all the steel we need through recycling or reusing our latent stock to satisfy market demand. The LSFA is on a mission to champion steel’s sustainability benefits and its role in the circular economy. Many of our members use light steel framing systems which contain over 50% of recycled stock.
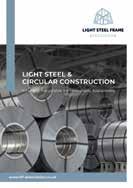
Recycling is often seen as the ultimate goal although reuse for its original or similar purpose without vastly altering the physical form, is equally if not more important but it rarely gets a mention. But how many construction components can be reused with little or virtually no reprocessing? I can only think of one. Reuse offers even greater environmental advantages than recycling since there is no, or few environmental impacts associated in reprocessing.
Material Efficiency
Light steel frame is often used for complex buildings where additional structural integrity is necessary and provides the answer to complex questions where a lightweight response is required. Low weight equates to improved efficiencies – you get a lot of structure for relatively little weight which reduces embodied carbon. This
is where steel cannot be beaten. Lighter structures not only reduce material consumption but also concrete in the ground with foundation loads and sizes reduced by over 70% relative to blockwork construction.
World Leading
The UK leads the world in steel construction commercially, technically and in terms of quality. The industry has made dramatic improvements in technology, productivity and efficiency. According to research carried out by independent consultants Construction
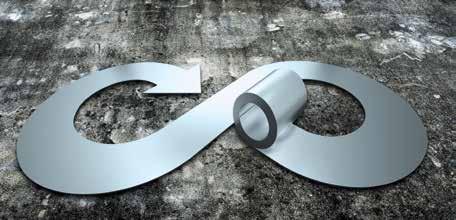
LIGHT STEEL & CIRCULAR CONSTRUCTION
Markets – steel continues to be overwhelmingly the structural framing material of choice with their survey showing that steel now has a 72.5% share of the multi-storey office market and a 60.9% share in the ‘other multistorey buildings’ which includes retail, education, leisure and healthcare sectors.
without detriment to its properties
Transitioning from a linear to a circular construction economy offers significant opportunities reducing the adverse impacts on the environment by re-thinking the way that we design our homes and buildings and consume resources. We need to adopt innovative approaches that design out waste, use resources more efficiently and keep materials and assets in use for as long as possible to retain their value.
For more insights into the benefits of circular construction: Download the Light Steel & Circular Construction brochure - www.lsf-association.co.uk
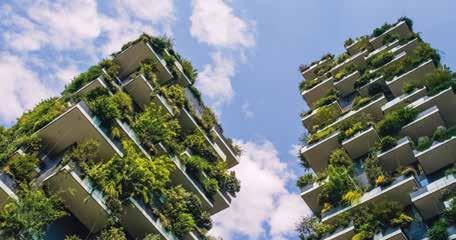
BOX ARCHITECTS’ LATEST COLLABORATION WITH MCCARTHY STONE
SITUATED IN AN AREA KNOWN LOCALLY AS THE SQUARE IN THE HEART OF MAGHULL NEAR LIVERPOOL, MCCARTHY STONE ARE DEVELOPING A NEW RETIREMENT LIVING COMPLEX USING A LIGHT STEEL FRAME SYSTEM MANUFACTURED BY SIGMAT.
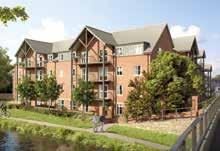
Using this fast-track, tried and tested method, the 23 one bedroom and 21 two bedroom apartments will be ready for occupation in December. Eleven apartments will have patios and 23 will benefit from walk out balconies - many with views over the Leeds and Liverpool canal, which borders the development. All will share elegant communal facilities and a prime location with amenities on the doorstep and easy access to Ormskirk, Southport and Liverpool city centre.
The project is being delivered using modern methods of construction (MMC) – part of a national commitment by McCarthy Stone. But while a lowimpact light steel frame approach will reduce energy bills, waste and construction time, the design will still respect traditional architecture in the area.
Embracing MMC can help us deliver high-quality retirement communities that push the boundaries of what
consumers expect, while cutting energy bills, waste and construction time,” said McCarthy Stone CEO John Tonkiss.
Box Architects has designed the retirement living development for McCarthy Stone using intelligent ergonomics and high spec interiors offering fully-fitted kitchens with integrated high-energy rated appliances, while master bedrooms have walk in wardrobes or fitted wardrobes as standard.
Situated in one of the older parts of the town, Poppy Grange will use red brick and pitched slate roofs to match the local vernacular. And despite being a mix of three and four storeys, it has also been designed to reduce loss of amenity to surrounding properties through overlooking.
“Not all MMC buildings are the same and this development is a good example of how the method is just as applicable in a traditional setting as in
a contemporary one,” said Box CEO Graham Place.
McCarthy Stone’s commitment to create its next generation of retirement homes using eco-friendly offsite construction is predicted to cut development times by as much as 50% and fast-track the delivery of housing for older people.
For more information visit: www.boxarchitects.co.uk
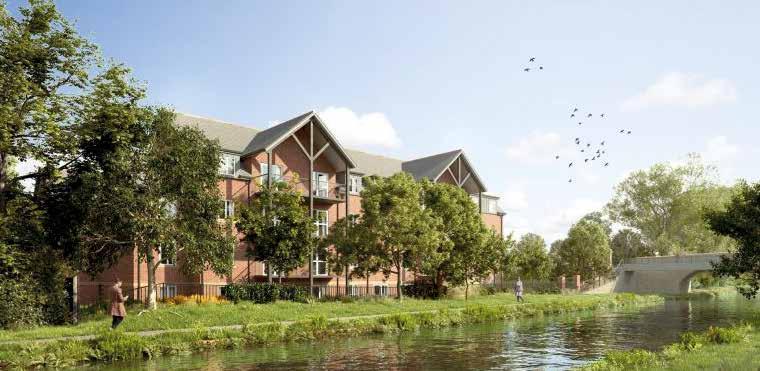
IS LIGHT STEEL FRAMING THE MOST ADVANCED MATERIAL IN OFFSITE TECHNOLOGY?
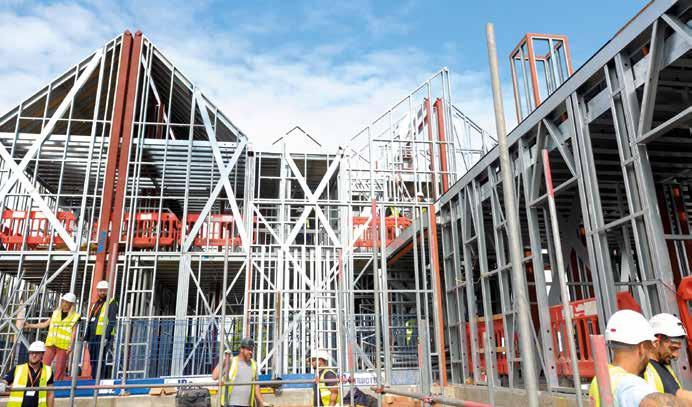
OUR GUEST CONTRIBUTOR STEPH HAZLEGREAVES, DIGITAL MANAGING EDITOR FOR PBC TODAY ANSWERS SOME OPPORTUNE QUESTIONS
AND EXPLORES WHETHER LIGHT STEEL FRAMING IS TRULY THE MOST TECHNICALLY ADVANCED MATERIAL IN THE OFFSITE TECHNOLOGY PORTFOLIO.
Offsite technology has made significant advancements in recent years, with light steel framing emerging as one of the leading materials. Light steel framing offers a variety of advantages over traditional construction methods such as faster assembly times and increased design adaptability. It is quickly becoming an attractive option for developers looking for efficient building solutions within project budgets.
What are the Advantages of Using Light Steel Framing?
Light steel is a type of construction that has become increasingly popular in recent years due to its increased durability, cost-effectiveness and versatility. It is often used for framing materials in offsite technology applications such as modular building systems or prefabricated components.
Not only are systems lighter than their counterparts allowing for easier transportation, but the price point is also generally lower making them attractive choices for projects with tight budgets. Light steel framing provides cost savings when compared to traditional stick-framing, as well as increased design flexibility and faster build times.
Additionally, light steel frames require less maintenance than other forms of construction. The main advantage of using light steel framing is its strength. The metal components are designed to be extremely tough and stable, meaning they can withstand high loads with minimal deformation over time. Furthermore, because the frame assembles quickly and easily on site, it reduces labour costs significantly. As a
result, light steel frames offer greater economic benefits than conventional building materials such as timber or concrete blockwork.
In addition to being strong and economical, light steel frames also provide excellent thermal insulation properties due to their airtight nature. Moreover, the frames have exceptional acoustic performance which makes them suitable for use in areas where noise pollution needs to be reduced or eliminated altogether.
What is the Environmental Impact of Light Steel Framing?
As the construction industry continues to prioritise green building solutions, light steel framing has become increasingly attractive as an environmentally friendly material
option. This type of steel framing offers several environmental benefits that make it well suited for numerous applications in both residential and commercial buildings.
One of the primary advantages of light steel is its high levels of recyclability. Steel production requires large amounts of energy, but when steel is reused or recycled, this reduces the overall amount of energy needed for manufacturing new materials. Additionally, since lightweight steel frames are made from thin sheets cut into specific sizes, so there is much less waste generated during installation than with traditional timber framing methods.
The use of light steel also allows for more efficient insulation systems compared to other materials used in offsite technology portfolios such as concrete or masonry blocks. Lightweight metal studs create air pockets that can be filled with insulation which helps reduce heat loss through walls or roofs and increases thermal efficiency within a structure’s envelope. Furthermore, since these structures require fewer resources to build and maintain while providing greater durability over time, they often have longer lifespans resulting in lower longterm costs associated with upkeep and repairs.
Overall, light steel provides many environmental benefits. Its low weight facilitates easy transport and quick assembly on site while its ability to support multiple types of finishes makes it suitable for a variety of design options allowing architects greater scope in their designs without compromising
sustainability goals. In addition, its excellent thermal properties offer significant potential savings in terms of heating and cooling costs throughout the lifespan of light steel buildings.
What are the Design Considerations When Using Light Steel Framing?
The use of light steel framing in offsite technology can be likened to a finelytuned instrument, providing the perfect blend of design flexibility and structural integrity. When considering this material for construction projects, there are several key design considerations that must be taken into account:
• Building Regulations: Light steel frames meet all building regulations standards, ensuring safety and security for occupants.
• Design Adaptability: Due to its strength-to-weight ratio and ease of installation, light steel frames offer greater versatility when it comes to designing complex structures.
• Loadbearing Capacity: Light steel is one of the strongest materials available for loadbearing capacity, making it an ideal choice for large scale projects such as commercial or multi-storey buildings.
How Does Light Steel Framing
Compare to Timber Framing in Terms of Durability?
Light steel has far greater strength than timber framing when it comes to resisting movement due to wind loads or seismic activity. In addition, light steel is non-combustible and can stand up better against fire than many other types of construction materials. These qualities make it an excellent choice for projects where safety and performance are top priorities.
When comparing the two materials, light steel offers several advantages over timber framing:
1. Steel does not shrink or expand due to changes in humidity and temperature levels.

2. Steel frames require less maintenance since they do not need painting or staining.
3. Steel is lighter than timber but still provides sufficient structural support for larger buildings.
4. Steel frames offer superior soundproofing capabilities as metal absorbs sound waves much better than timber.
Future Trends and Opportunities for Light Steel Framing

The continued growth of light steel framing is expected to open up new avenues for collaboration among industry professionals. As more companies begin to recognise the advantages of using lower cost yet highly durable steel frames. Furthermore, advancements in digital technologies could enable more efficient design processes, thereby further expanding the scope of possibilities available through offsite technology. These developments present an immense opportunity for those involved in projects utilising light steel frame.
For more information visit: www.pbctoday.co.uk
IMAGES 01. EOS Framing, Gardiner Place 02-03. Light steel frame construction has become increasingly popular in due to its increased sustainability, durability, cost-effectiveness and versatility.
SHOWCASING INNOVATIVE TECHNOLOGIES
AS THE LARGEST DEDICATED EVENT OF ITS KIND OFFSITE EXPO, TAKING PLACE ON 19 – 20 SEPTEMBER 2023 AT THE COVENTRY BUILDING SOCIETY ARENA, IS LEADING THE WAY IN PROMOTING THE TECHNOLOGIES THAT ARE TRANSFORMING THE BUILT ENVIRONMENT.
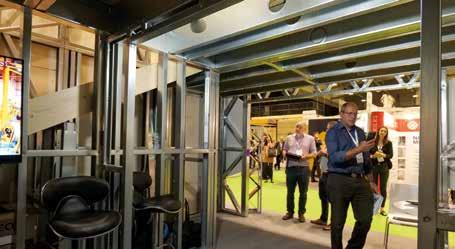
British Offsite
Light Steel Frame Association (LSFA)
The LSFA works to drive engagement, champion change, and spread the word about the cost, productivity, performance and sustainability benefits of contemporary light steel systems.
www.lsf-association.co.uk
O'Dwyer Steel
Recognised as one of Ireland’s and the UK’s leading suppliers of CE certified structural steel and cladding, O’Dwyer Steel has over 60 years’ experience. With a first-class reputation gained through a balance of competitive prices, commitment to quality, customer satisfaction and proven capabilities.
www.odwyersteel.ie
SCI (Steel Construction Institute)
As a trusted, independent source of information and engineering expertise globally for over 30 years, SCI remains the leading, independent provider of technical expertise and best practice advice to the steel construction sector.
www.steel-sci.com
Voestalpine Metsec plc
Bringing together those who are driving change in the construction sector, the event will play host to the leading UK and international offsite manufacturers and component suppliers over two days showcasing a broad spectrum of panelised, volumetric modular systems, pod and prefabricated MEP solutions, as well as the latest in digital technology.
Light Steel Framing Technologies
OFFSITE EXPO showcases one of the most comprehensive displays of light steel framing technologies – exhibitors include but are not limited to:
Ayrshire Metals
A leading supplier of cold rolled products to a diverse range of markets and industries, Ayrshire Metals has a long history and extensive experience backed by a forward-thinking approach. www.ayrshire.co.uk
The creator of UNI Systems, advanced light steel panelised solutions, British Offsite is part of the new hightech manufacturing sector bringing innovative capabilities to the UK construction industry. www.britishoffsite.com
Frameclad SFS
Frameclad design, manufacture and supply light steel frames, components and structures. Operating across all areas of the construction industry, Frameclad offer a broad range of services.
www.frameclad.com
Howick
Technical innovators in the fast-build construction space for decades, Howick’s precision light steel cold rollforming technology brings accuracy, speed and performance that is trusted by construction businesses throughout the UK and the world.
www.howickltd.com
One of the UK’s largest specialist cold roll forming companies, providing products for the construction and manufacturing industries, Voestalpine Metsec focus on adding value through expert design, precision manufacturing and on-time in full product delivery.
www.metsec.com
CPD Accredited Masterclass Sessions
Presenting rapid and efficient access to the latest information, the Offsite Masterclass Theatre provides over 40 hours of CPD Accredited presentations in a dynamic and interactive format. With dedicated light steel masterclass sessions curated and chaired by the Light Steel Frame Association, speakers from Steel Construction Institute, Voestalpine Metsec and WSP will presenting a range of informative case studies and technology innovations.
To secure your free place go to:
www.offsite-expo.co.uk
For more information on getting involved in OFFSITE EXPO 2023 as an Exhibitor or Sponsor email: julie.williams@radar-communications.co.uk

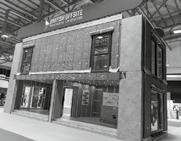
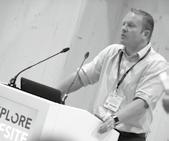
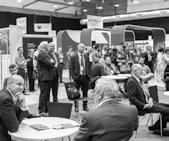
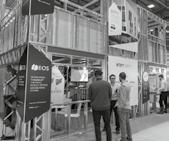
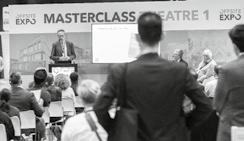










IN AN INTERVIEW WITH LIGHT STEEL FRAMING MAGAZINE, JAMIE BRENTON TALKS ABOUT HIS CAREER IN THE LIGHT STEEL SECTOR AND DETAILS OF A PROJECT HE RECENTLY PRESENTED AT THE FOCUS ON FRAMING CONFERENCE.
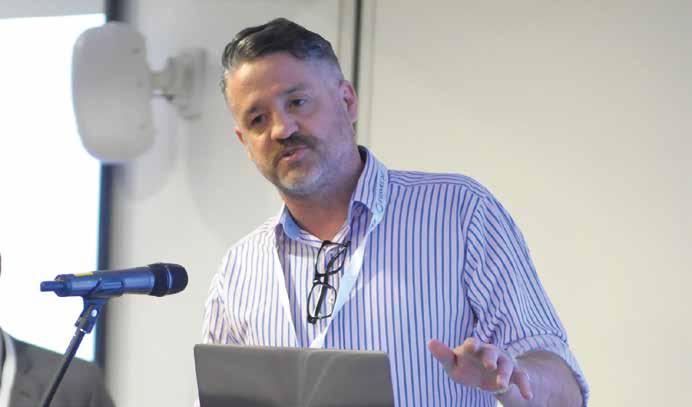
Q: Can you share with our readers your experience in the light steel framing sector?
Jamie Brenton (JB): Like many in the industry, I started my career in construction ‘working on the tools’ and installed a limited number of steel framing systems (SFS). Now as Managing Director of Brebur, a drylining, suspended ceiling and steel framing systems installer – the installation of steel framing systems is a major part of our business.
Based in Yorkshire with a rich trading history spanning more than 20 years, when Brebur started installing we realised there was a knowledge gap between the manufacturing output and the installation service.
So, we have made our partnering approach to the design development of SFS our USP. Our clients rely not only on our installation experience but also our expertise in supporting the design process and getting projects to a point where they can be safely installed and practically delivered.
Q: You recently presented a case study at the Focus on Framing Conference –can you share a little about the project and the challenges involved?
JB: The York Emergency Department is part of an ongoing scheme with Kier and York Hospital. This particular element involved an extension for critical care beds to a new hot rolled steel framed building, with a metal deck and concrete floor slab construction and a steel framing system around the outside. We were engaged to install
the new steel framing infill system, sheathing boards, column encasements and the partitions as well as fire compartments inside the new building extension. The client had already engaged EOS, part of Etex Group to supply the light steel infill system. We reviewed the information and there were areas that required further development so we could efficiently install the system without impacting on warranties. Working in partnership, Etex recommended an excellent Thruwall® solution to overcome the challenges involved and improve fire protection around the hot rolled steel frame and SFS interfaces.
Q: Why specify a light steel frame systems approach for this project?
JB: Kier decided to go down this route with the design manager and
architect prior to our involvement. This was our first job with them using the Etex Thruwall® system incorporating steel encasements. Between the construction partners, Kier, Etex, the architect and ourselves – we came up with an excellent solution using the Thruwall® light steel infill system to overcome the challenges. The system itself was a bit of a revelation –providing a complete and compliant all in one specification. The beauty of the Thruwall® system is that it integrates light steel frame from EOS, non-combustible insulation, column encasements, Siniat's Weather Defence external sheathing board and internal Framing board, providing performance assurance and all required warranties in one place.This systems approach gave the architect and main contractor a lot of confidence – ‘dotting the i's and crossing the t's’ as it were!
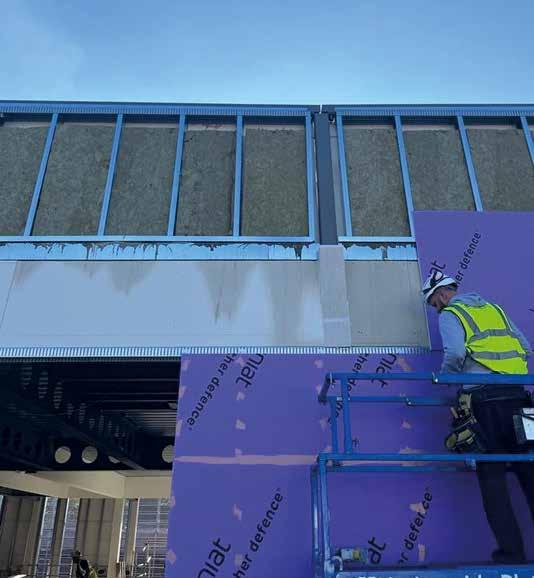
Q: Can you explain a bit more about the framing solution and the Thruwall® system?
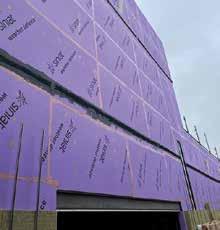
JB: The concept was to use the fire resistant Thruwall® system as infill to the hot rolled steel main frame. There were some challenges fixing through the cladding boards into the steelwork but the introduction of Z bars, as a structural element for fixing the SFS to, resolved this. Because the SFS infill and the hot rolled steel encasement were from the same manufacturer, penetrating them did not infringe on any warranties.
Using various Thruwall® column encasement systems offering 60 – 120 fire resistance, enabled us to not only improve fire safety but also enhance acoustic and airtightness performance. The air seal was taken care of through the sealing the weatherboard to the beam encasement.
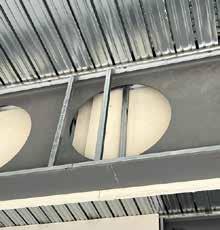
Q: Can you tell me a bit more about the benefits of Thruwall® when it comes to warranties and performance?
JB: With a 30-year Etex product and performance warranty, Thruwall® delivered certainty and clarity for the client. Knowing that the warranties and product detailing are all in one place without having to ‘bridge the
gaps’ between different manufacturers and suppliers. Working with multiple supply chain partners introduces an element of risk with warranties (if any) and product details dispersed across many companies which have to be collated and managed by the architect or in some cases installers such as us. But using a Thruwall® approach with all components manufactured and supplied by Etex Group partners –performance testing and warranties
are all in one place offering assurances to Keir as the main contractor and York Hospital as the client.
For more information visit: www.breburltd.co.uk
Managing Director,
Thruwall® light steel framing system.
uses the
Gain control of your budgets by de-risking through a detailed design process, a precise manufacturing process, and pre-programmed site delivery.
HadleyFRAME steel MMC delivers the superstructure with minimal time on site. Our recent project in Jersey called The Limes - 127 apartments across two blocks - delivered on-programme in only 31 weeks.
Alongside speed, offsite construction reduces risk by minimising the workforce and material storage by 33%, and allows follow-on trades to start sooner.

SCAN HERE
To learn more

An SFS through-wall you can rely on
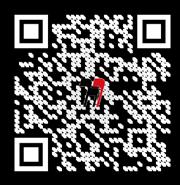
A tested and accredited solution to meet your needs.
Achieve your project performance requirements through the collaboration of experienced construction partners, Hadley Group and British Gypsum. Submit your free indicative design request today, and our team will return it in 10 days.
The HadleySFS Infill system is independently tested and accredited, and covered by our collateral warranty and £10m professional indemnity insurance.
GypLyner Xternal is a trusted solution with clear and detailed fire testing, as well as acoustic and thermal performance options - all supported by technical evidence and specified to meet your project requirements.
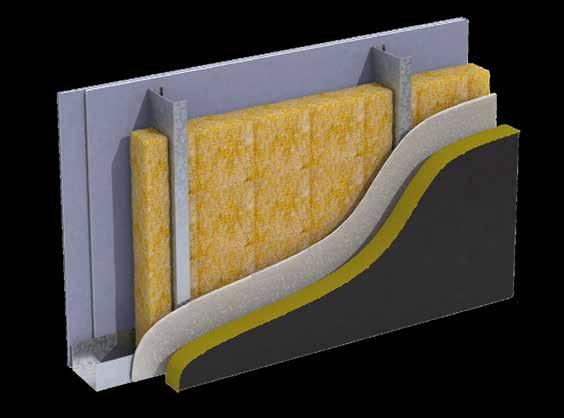
MORRELL REVIEW PROPOSES NEW REGULATORY REGIME
The review recommends a series of sweeping reforms aiming to ensure products used on buildings are safe –with a major shake-up in the regulatory system likely to follow. The Grenfell Tower tragedy and the failings it has laid bare have made clear the imperative for change. The UK’s exit from the EU provides an opportunity to look again at the whole system of construction product regulation and how it might be both simplified and strengthened.
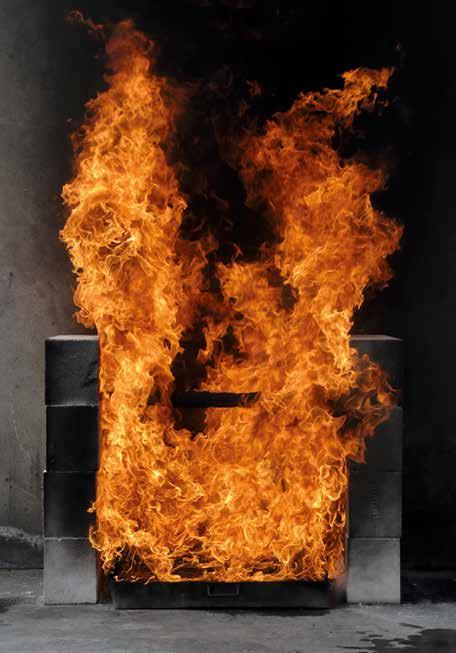
As the government’s first Chief Construction Advisor, Paul Morrell co-chaired the 174-page review with construction legal expert Anneliese Day KC. It provides advice on how the new National Regulator for Construction Products (CPR), based in the Office for Product Safety within the Department for Business and Trade, will work with the new Building Safety Regulator, based in the Health and Safety Executive.
Currently, it is estimated that only a third of all construction products in manufacture are covered by the regulator, leaving around 20,000 to 30,000 products unregulated. Some products not currently covered will be brought into the CPR regime by a new designated standard or by being added to a list of ‘safety-critical’ products to be set out in regulations by the Secretary of State.
THE FIRE AT GRENFELL TOWER HAS EXPOSED SERIOUS WEAKNESSES IN THE REGULATION OF CONSTRUCTION ACTIVITY AND CONSTRUCTION PRODUCTS. ORDERED IN THE WAKE OF DISTURBING EVIDENCE HEARD FROM MATERIAL MANUFACTURERS AT THE PUBLIC INQUIRY, THE GOVERNMENT HAS RECENTLY PUBLISHED PAUL MORRELL’S LONG-AWAITED INDEPENDENT REVIEW OF THE CONSTRUCTION PRODUCT TESTING REGIME.
The report issued a ‘call for honesty’ on the part of manufacturers and ‘full disclosure’ to the approved body conducting the product assessment. Manufacturers will be required to share all technical documentation and information with the regulator and enforcement authorities, including all marketing materials and other communications relating to products. A breach of any part of this duty would be an offence subject to new sanctions available to the regulator with effective enforcement action being taken.
The report strongly criticises the current enforcement system, which it says appears to have not made a single prosecution since it was enacted in 2011 and carried out only a limited number of investigations. It added that there is no centralised database of products that might represent a risk.
In a statement to the House of Commons, Housing Secretary Michael Gove, said:
“We recognise that more needs to be done and are carefully considering the recommendations put forward by the independent reviewers. I will also consider how our regulatory regime can ensure that only responsible businesses can make and sell construction products. It is unacceptable that cladding and insulation manufacturers have neither acknowledged their part in the legacy of unsafe buildings in the UK or contributed to the cost of remediating buildings.”
Judith Hackitt, who authored the landmark 2018 report Building a Safer Future in the wake of the disaster, said the report marked a major step forward: “Paul Morrell and Anneliese Day are to be commended. We must move from a state where up to two-thirds of products are unregulated, there is lack of clarity around purpose of testing, the fitness for purpose of current standards is questioned and there is no enforcement to implement a process that delivers quality and confidence.”
Morrell and Day also looked into the history of the UK regulatory regime and how it had led to the Grenfell fire. They said the outsourcing of regulations to the European Union following the publication of the Construction Products Directive in 1988 had led to a ‘hollowing out’ of expertise.
“The CPR assessment process is so complex that few people properly understand it and there is a concerning disconnect between those involved in the assessment process and those who design and construct buildings,” the report says. “The criteria by which products are directed towards the different levels of this system are also unclear, and sometimes inconsistent. This renders the process opaque and a system that cannot be readily understood is unlikely to be routinely observed and enforced, providing an opportunity for those who may seek to take advantage of a lack of transparency.”
The report also suggests there was a lack of understanding between the government and the UK Accreditation Service (UKAS), which regulates testing bodies, over what had gone wrong in the process that led to the Grenfell fire.
To download the full review, go to: www.gov.uk/government/publications/independent-review-of-the-construction-product-testing-regime
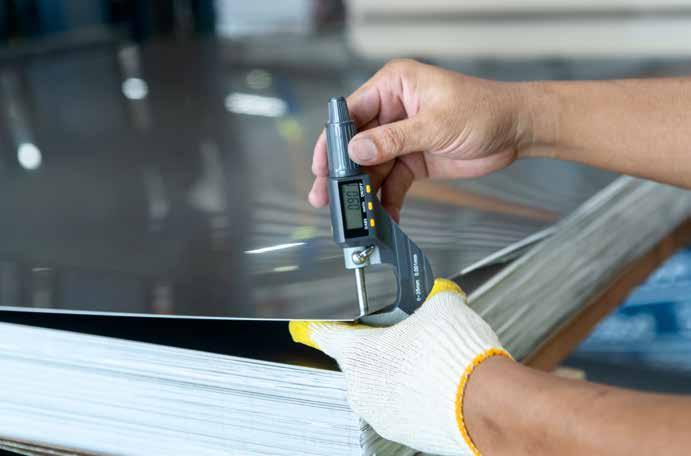
PRODUCT CERTIFICATION
MORE THAN JUST A CERTIFICATE
There are many different certification and assessment schemes available in the construction sector and knowing the details are vital for determining if the scheme is appropriate for a given situation, product, or process. This can be a minefield. Some specific certifications will be a prerequisite by particular parties such as those required by warranty providers, other certifications or independent assessments are optional but they provide added assurance and competitive advantage for the product or service.
Credible Certification Services
It is clear that organisations carrying out certification must have the necessary knowledge and expertise. Some certification schemes will be accredited by UKAS which means that the scheme itself will have been independently assessed to ensure the organisation and those individuals carrying the certification are competent and that the scheme is appropriate. Some certifications or assessment schemes will not be accredited, in which case it is likely to be the company’s known expertise, status and reputation within a particular sector which enable it to offer a credible certification service.
CERTIFICATION AND INDEPENDENT VALIDATION OF PERFORMANCE HAS NEVER BEEN MORE IMPORTANT. ANDREW WAY, ASSOCIATE DIRECTOR AT THE STEEL CONSTRUCTION INSTITUTE (SCI), PROVIDES AN OVERVIEW ABOUT THE VALUE OF PRODUCT CERTIFICATION AND HIGHLIGHTS THE IMPORTANCE OF UNDERSTANDING THE SPECIFICS WHETHER YOU ARE A MANUFACTURER NEEDING CERTIFICATION OR A SPECIFIER SEEKING A SUITABLE PRODUCT.
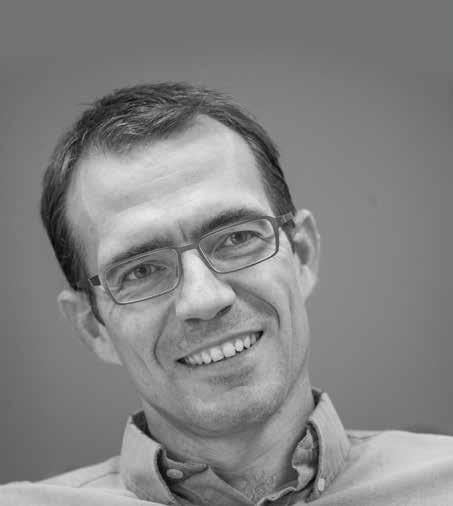
The basic premise of certification is that something has been independently checked or verified, thereby giving confidence to users and specifiers that it meets defined requirements. Certification can be applied to a
product, a service or performance data. It can also be applied to process, such as a design process whether that be automated carried out by software or a more manual process carried out by a designer.
Certification bodies which are accredited by UKAS should be accredited to ISO 17065 which specifies the ‘requirements for bodies certifying products, processes and services.’ However, over recent years UKAS has reviewed their accreditations in the construction sector and many of the organisations which previously held accredited to ISO 17065 have had this withdrawn by UKAS and are now converting their accreditation to ISO 17020. The conformity assessment standard ISO 17020 specifies the ‘requirements for the operation of various types of bodies performing inspection’ – which is not the same as ISO 17065 for bodies certifying products.
Key Differences Between ISO 17065 and ISO 17020
Manufacturers and product specifiers should be aware of the key differences between ISO 17065 and ISO 17020.
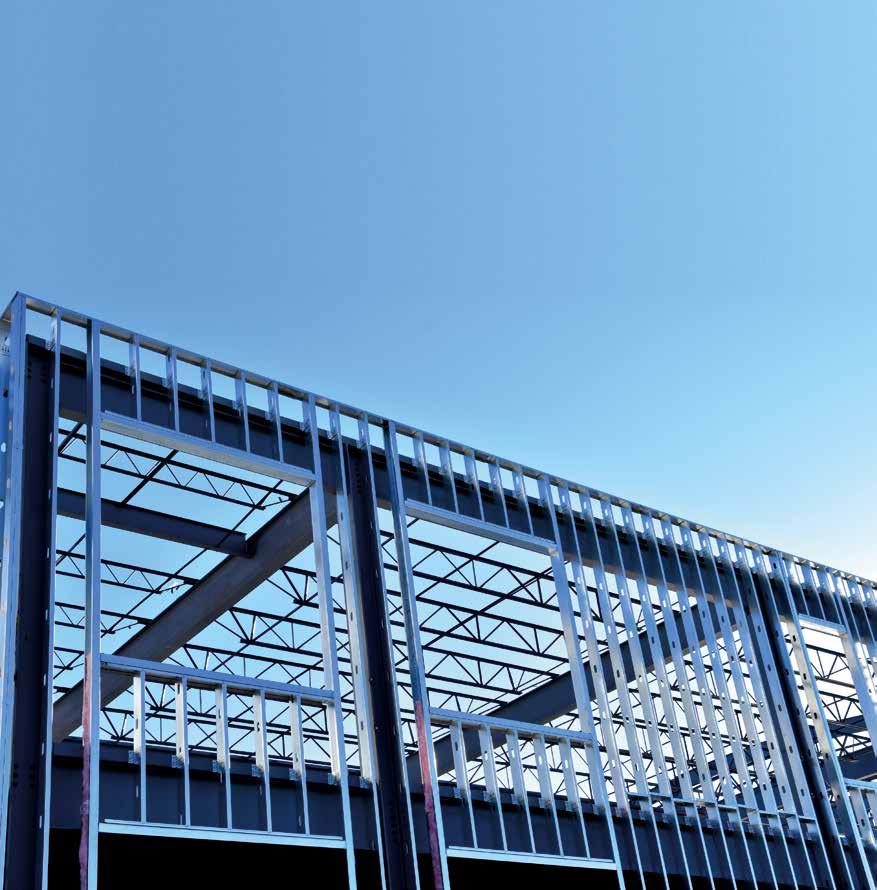
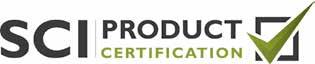
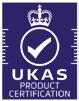
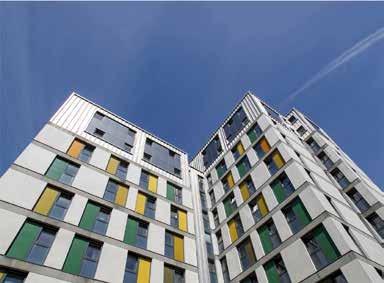
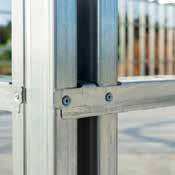

Product certification schemes to ISO 17065 must have a standard scope and defined product requirements. This means that similar products certified under the same ISO 17065 accredited scheme will have undergone the same level of assessment covering the same scope and the same product performance requirements. The same cannot be said of products certified through an ISO 17020 inspection scheme. ISO 17020 does not demand a standard scope or defined product performance requirements. Certification
via ISO 17020 is based on a judgement of fitness for purpose rather than defined product performance criteria. This is open to an inconsistent approach and potential variations in the basis on which certification may be provided.
SCI Certification
SCI provide certification and assessment through several different schemes, each scheme being designed to satisfy the needs of a particular sector, or product type. We have a
combination of prescriptive product certification schemes accredited by UKAS to ISO 17065, non-accredited schemes which provide flexibility to suit the bespoke nature of many innovative construction products, and schemes developed at the request of warranty providers.

Our experience of providing certification and assessment services has demonstrated the importance of independent validation as during the process it is not uncommon to discover errors in the technical information which is submitted. The issues that are identified (and corrected) obviously vary from case to case but most fall into some common categories. These categories include the incorrect or incomplete application of design calculations which may be based on expressions from codes and standards or engineering first principles, the improper derivation of design values from test data, and the inappropriate use of performance data for alternative materials.
Without independent certification and assessment by organisations with the necessary expertise many of these inaccuracies or omissions would not necessarily be identified. This is particularly true because much of the design information or performance data that is accessible to the market is presented as fact in the form of product information sheets or load span tables, or even software output. This ‘blackbox’ approach to performance data means that individuals do not have the opportunity to investigate the derivation or accuracy of such data.
For more information visit: www.steel-sci.com or contact: certification@steel-sci.com
IMAGES
01. Andrew Way, Associate Director, The Steel Construction Institute (SCI)
02. Installation of completed external wall panel for a residential development. Image courtesy of EOS and Osco Homes.
03. Installation of a module for a two-storey modular hall system. Image courtesy of Portakabin© – Culverstone Green Primary School.
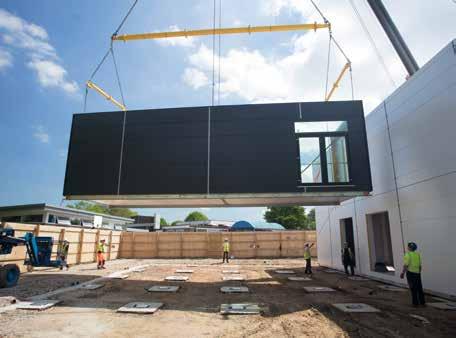
INNOVATIVE USE OF TECHNOLOGY BRIDGING THE LABOUR GAP
According to surveys, 96% of supply chain firms are affected by labour shortages. As the UK construction industry continues to feel pressure to ensure on-time and on-budget delivery, innovative use of new technology and digital software supports a whole new skill set. Mark Munns, CEO of Frameclad, considers how light steel systems can benefit contractors struggling with the labour gap.
Production of light steel framing solutions has shifted considerably in the last decade. Manufacturing now requires far less labour and relies more on automated processes managed by skilled operatives. This can be of significant advantage to developers.
The fact that we can provide faster, simpler installation with the requirement for less skilled workers on site has benefits not only in terms of cost but in improved productivity and safety. We are offering something precisionengineered and turning to technology allows us to offer something highly specialised and project-specific. What might have taken an entire team several weeks if not years to complete is now quicker, safer and more cost-effective.
We can offer more comprehensive light steel framing systems through experienced engineers working alongside digital experts to improve design and integrate new technology into our production processes. We need to think of our workforce in the same way as we do the systems we offer –the sum of many parts, working with synergy. I think as a sector, light steel is leading the way in that aspect.
For more information on light steel framing systems and services visit: www.frameclad.com
THE PERFECT BRICK SOLUTION FOR THE MODULAR HOUSING MARKET
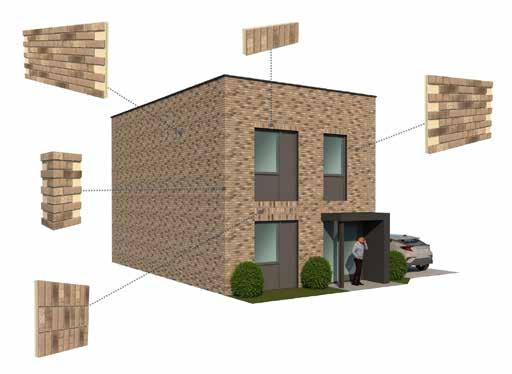
Modular construction relies on a smooth, fast process that remains consistent.
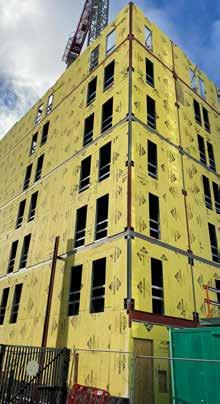
A factory-produced brick cladding panelised system, the Gebrik Modular system allows for fast-track construction, providing you with a solution that is quick and easy to use and allows you the creativity and flexibility needed to get the finish and details that you want from your brick façade.

• Different house types available • Choose from 700 brick finishes
• Supplied in kit form
• Quick and easy to install
• Free training provided
To find out more, contact us on: (0)808 223 9080
info@aquariancladding.co.uk
www.aquariancladding.co.uk
A PACKED AGENDA FEATURING LIGHT STEEL EXPERTS AT THE FOREFRONT OF THE INDUSTRY
Simon Lovering of Fusion Steel Framing took delegates on a journey around Holburne Park, a high-end £26 million residential development in the heart of the World Heritage City of Bath which was successfully delivered to great acclaim. Jaime Livingston, Associate Director of Corstorphine and Wright presented a case study on Becketwell, Derby, a year on from the project start, sharing how light steel framing is providing benefits to this innovative regeneration project.
After lunch and networking, Craig Johnson from Trimble considered Connected Construction, with over 20 years of experience in the light steel industry, Craig has extensive knowledge of whole steel manufacturing workflow. Nik Teagle - Technical Director, Frameclad gave some words of warning in his presentation, Don’t Paint Over Light Steel Frame. Daniel Leech - CEO, CADCOE & Design4Structures posed the question: Would you Encourage Your Children to Work in Construction? These informative presentations were followed by lively debates and the opportunity to ask some challenging questions and gain informed responses from those at the forefront of the light steel framing sector.
Save the Date
FOCUS ON FRAMING
Leading experts from the light steel framing sector took to the stage to offer insight and share valuable intelligence with the assembled delegates. Presented in partnership with the Light Steel Frame Association (LSFA), the representative body for the sector, Focus on Framing is the only specialist event of its kind.
With a packed agenda featuring awardwinning case studies, ground-breaking projects and an in-depth look at the key topics currently affecting the industry, Mike Fairey, Chairman of the Light Steel Frame Association (LSFA), opened proceedings.

First up, Michelle Hannah, Director of Cast Consultancy presented MMC of Yesterday, Today and Tomorrow – an overview of the industry’s journey to modernise through offsite construction. Michelle was swiftly followed by Andrew Way, Associate Director of SCI (Steel Construction Institute), who presented a detailed talk on technical updates, giving insight into upcoming changes and need-to-know information.
A raft of informative case studies were presented, including Sally WalshSenior Engineer for WSP who shared insight into steel reuse at the Elephant & Castle Town Centre and Sloane Square House projects. Next up, Jamie Brenton, Managing Director, Brebur, alongside Ben Palmer, Architectural Specification Manager from Etex Group, gave a talk on the light steel frame extension at York Hospital. Read our interview with Jamie on page 32.
Focus on Framing provides an opportunity to gain insight and meet with forward-thinking professionals from across the business network. Delegates can also learn about new systems and products via a dedicated exhibition area. As architects, engineers, specifiers, and developers look for ways to increase building safety performance and reduce environmental impact, Focus on Framing brings together a wealth of industry knowledge, support and technical information to help shape the future of the UK construction sector.
If like many of the delegates, you found the Focus on Framing seminar beneficial, then make a note – the 2024 event will be taking place once again in May, keep an eye on the website for more announcements: www.focusonframing.co.uk
BACK IN APRIL CONSTRUCTION PROFESSIONALS GATHERED AT THE BUILDING CENTRE, LONDON FOR THE 2023 FOCUS ON FRAMING SEMINAR.

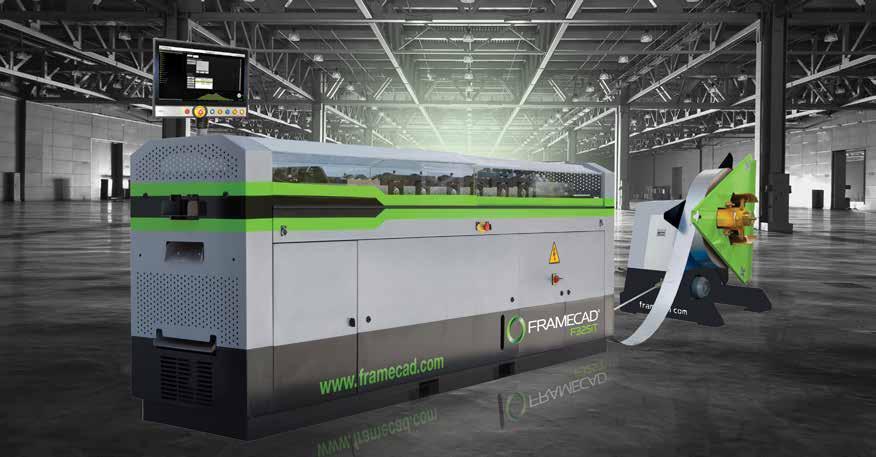
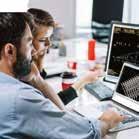


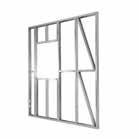
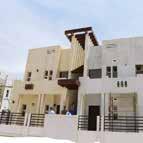
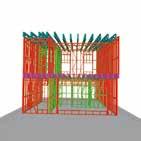
