9 minute read
FOR SAFETY SAKE
Next Article
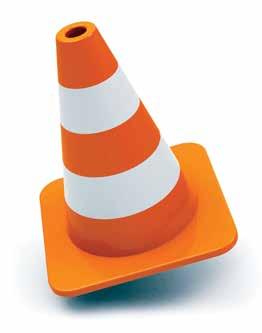
4 STEPS TO CREATING A PREVENTATIVE SAFETY CULTURE
Hitting a thumb with a hammer or dropping a two-by-four on a toe are common workplace injuries. These represent the roughly 3 million nonfatal incidents enterprises reported yearly, according to the Bureau of Labor Statistics. But chalking up more severe incidents as accidents and not doing anything about them creates a much more dangerous threat—lack of a safety culture.
The Occupational Health and Safety Administration recently released a study detailing results from the first year of its severe injury reporting program, and the outcome looks bleak. OSHA believed that although roughly 10,000 severe injuries were reported, nearly 50 percent of these types of accidents went unreported in an era where the spotlight is on improving employee safety by preventing predictable injuries.
18 | Official Publication of The Ohio Landscape Association Software in various industries. But to effectively stop injuries in their tracks, prevention should be at the top of every safety manager’s mind.
1. DEVELOP AN ALL-INCLUSIVE CULTURE You can’t keep employees safe without getting them on board. It’s a difficult task for a safety manager revising the perception of a workplace riddled with oversight and rampant violations. Injury prevention isn’t possible if the people experiencing problems don’t want to make a change.
continued on page 20
SWITCH TO THE GREEN INDUSTRY RISK EXPERTS NOW! Before your crew gets busy.
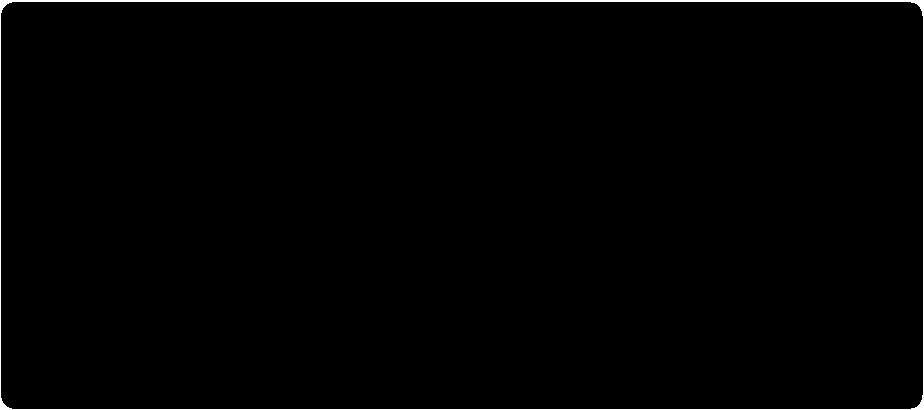
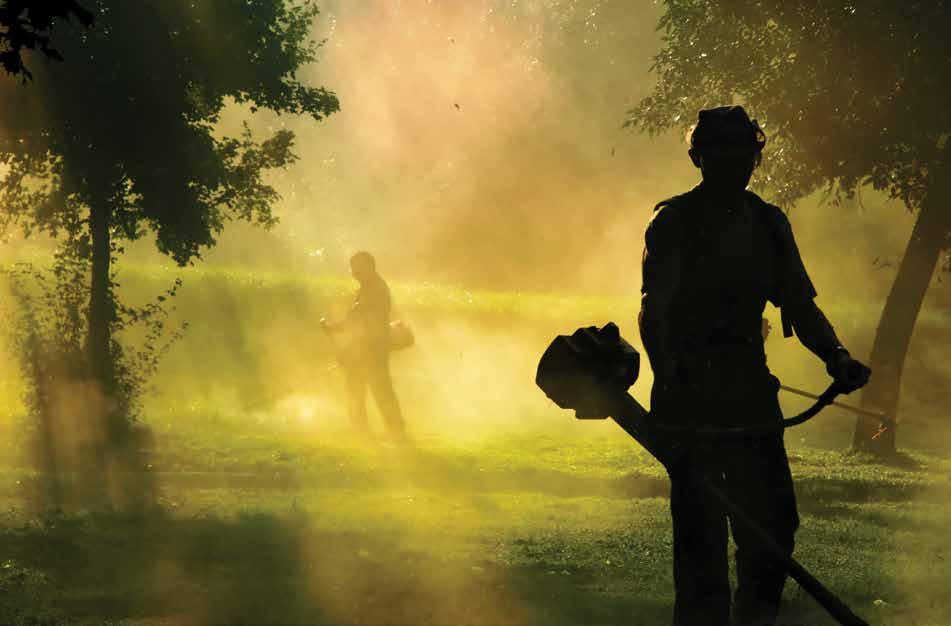
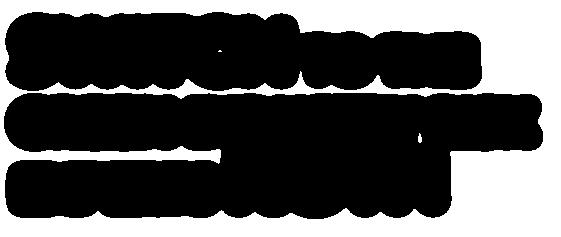

EASIER, SAFER AND BETTER WITH BOTSON! At Botson Insurance we see beyond insurance to provide you with practical solutions to the problems that face the Green Industry—and we may be able to save you money while doing it.
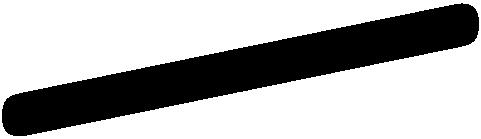
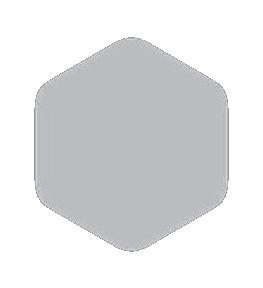
✓Lowest General Liability Rates in Ohio up to 50%-80% ✓ Faulty Workmanship Coverage for as little as $425 per year ✓ Over 160 Green Industry professionals in our program.
botsoninsurancegroup.com (440) 537-2292 greg@botsoninsurancegroup.com
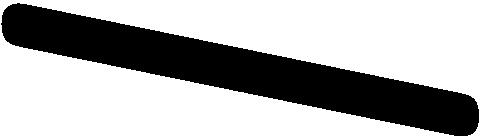
We’ve been protecting the Green Industry and providing great rates for 28 years!
EASIER Provided expert advice and built strong client relationships over 28 years.
GREG BOTSON MORE THAN A TRUSTED ADVISOR
SAFER Free distracted driving and safety seminars, resources, training and more.
BETTER Replacement cost coverage on equipment and more f lexible driver requirements.
R e v i e w R e p o r t
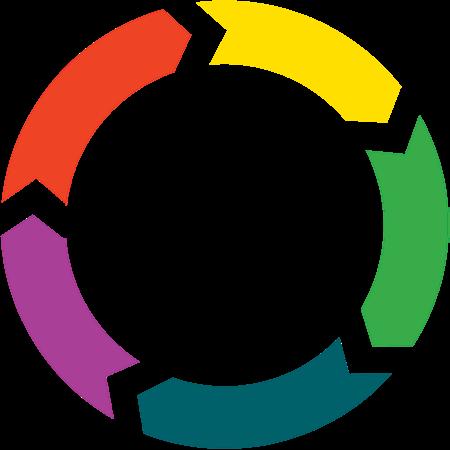
A c t EMPLOYEE SAFETY
S h a r e
continued from page 18
What exactly is a safety culture though? A study from the Safety and Health At Work journal identified five pillars:
• Visible, public commitment for safety from management. • Safety valued above costs. • Unified decision-making on safety. • Employees consistently reviewing safety performance. • Safety integration in every aspect of the organization.
Implementing this culture carries financial value as well. The Vermont Department of Labor reported that for every $1 invested in a program like this, a company can expect to yield $3 to $10 through direct and indirect savings for expenses like workers compensation, legal fees and hiring.
Key takeaway: A strong culture of safety is the foundation to preventing injuries.
2. ANALYZE WHAT YOU KNOW When building this program, employee input should be highly encouraged, Chief Executive magazine reported. This facilitates a relationship where it’s OK to point out flaws in
L e a r n
ANALYZING SAFETY CONCERNS
REPORT • Report all injuries & near misses to the proper personnel. • Involve the whole team.
LEARN • Identify & investigate causes of injuries. • Use these findings as learning opportunities.
SHARE • Discuss your findings with other departments to promote companywide learning.
ACT • Make changes to current practices.
REVIEW • Review the changes to these practices periodically & update as necessary.
protocol, such as the absence of machine guards or methods that expose workers to danger.
Make internal injury reports public; most of the external data on severe injuries already is. This allows the safety manager to work with employees to understand which practices carry the most risk, where most employees are injured and how company safety lines up with the national standard.
There are a number of incidents that can be easily prevented, but if no one sifts through the data to see their trending significance, they’re easily forgotten. Liberty Mutual’s Workplace Safety Index is an excellent barometer of the most pressing injuries facing the workforce at large. For example, overexertion accounts for roughly 24 percent of the most disabling workplace injuries, and these types of injuries often come from outdated techniques or use of manual equipment.
Key takeaway: There must be a simple process in place to report and view reports so employees can learn through means other than trial by fire.
continued on page 23
Your success brightens our day... and night.
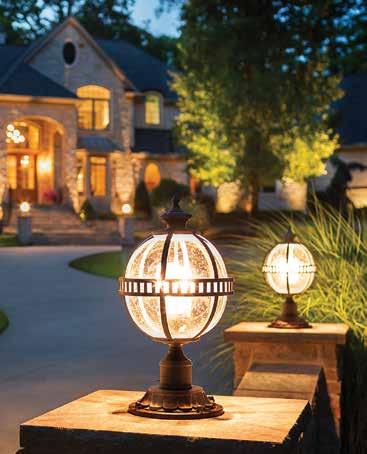
At Cascade Lighting, your success is our top priority and it’s been that way since we set up shop over 20 years ago. We’ll partner with you to provide expert advice on the best lighting solution to fit your project and budget. Our team also offers design and technical support at no additional cost. And to ensure the job gets done on time, our warehouse stocks a huge inventory of products ready for same day shipment.
Call us today at 800.758.6359 or visit cascadelighting.com
Providing over 40 lines of outdoor and landscape lighting products including:
klynnurseries.com
Over 1800 Different Species And Cultivars To Meet Your Needs!
bamboo grasses perennials ferns vines roses dwarf conifers bog & marginals shade & ornamental trees
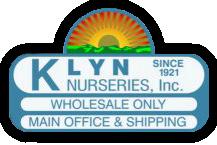
Visit Our Website For Product Availability, Our 2016 Catalog, Quote Form, And More! (contact us to receive your username and password.) 2019
klyn nurseries, inc. 1-800-860-8104 klynnurseries.com
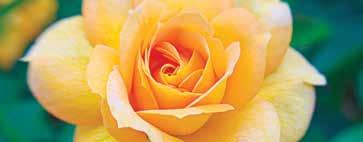
COURSE INFO WEDNESDAY, APRIL 8, 2020 ST. MICHAEL’S WOODSIDE 5025 EAST MILL ROAD BROADVIEW HEIGHTS, OH
AGENDA REGISTRATION / BREAKFAST 8:00AM - 8:30AM CLINIC 8:30AM - 4:30PM BREAKFAST & LUNCH INCLUDED!
COST MEMBERS NON MEMBERS SPONSORED BY - $99 - $129 - $129 - $159 BEFORE 03/25/20 AFTER 03/25/20 BEFORE 03/25/20 AFTER 03/25/20
As winter comes to a end, Mother Nature shifts her focus towards spring – and so must our crews! This year’s Spring Training Clinic will teach your employees industry best practices from start to finish, as well as how to be safe while performing them – all in effort to get them ready for the 2020 season! Spring Training Day

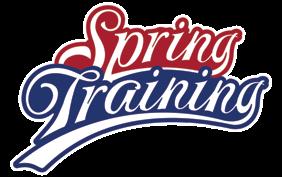
This year’s topics of dicsussion will include: • Stretching: Starting Your Day Off Right • Travel Safety: Pre-trip Inspections & Proper Loading/Hauling Practices • Equipment Utilization, Operation & Safety - Mower & Small Equipment - Tree & Shrub Work - Chemical Applications & Pesticides - Small Engine Equipment • First Aid: ‘What to do in Emergency Situations’ & ‘How to Deal with Cuts, Lacerations & Heat Stroke’ • Post Trip Work: Dumping, Cleaning & Equipment Maintenance Best Practices
Having a trained crew is the key to fostering a culture of safety within your company. Owners, Crew Leaders, Crew Members – anyone working in the Green Profession – is encouraged to attend!
PRESENTED BY

Mike Spicer Associates
Cancellations made 8 to 14 days prior to the course start date will be subject to a 30% cancellation fee. NO refunds or credits will be issued for cancellations 7 days or less prior to the course, no shows, or cancellations on the day of the course. If, for any reason, the course is cancelled, enrollees will be notified, and fees refunded in full.
2020 SPRING TRAINING DAY / REGISTRATION CLOSES 04/01/20
Company Contact Address City State Zip Phone (______) Fax (______) Email
NAME OF ATTENDEE (S) FEE $ $ $ TOTAL DUE $ Check No. (Enclosed) Charge to my: MasterCard Visa AMEX Discover Acct. No . Exp. Date Security Code Name on Card Signature Billing Address + Zipcode for Card
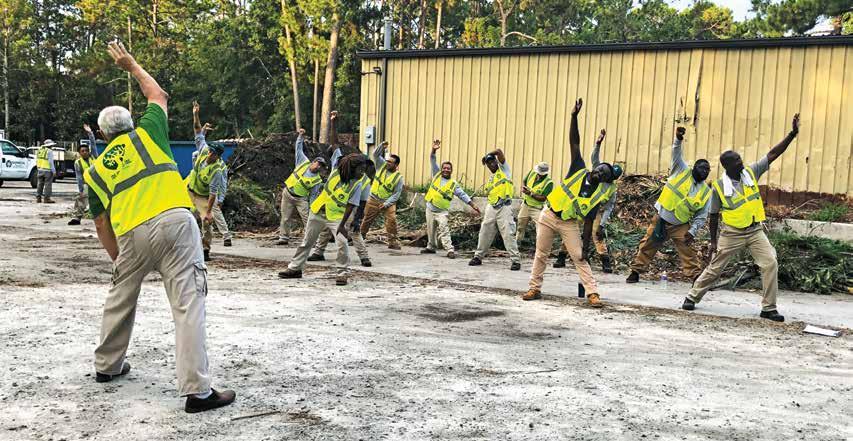
continued from page 20
3. CREATE A CULTURE OF ACCOUNTABILITY In a preventative safety culture, an entry-level employee needs to feel safe walking up to the CEO and handing him or her a hard hat to wear on the worksite. This heightened level of accountability is key in stopping injuries before they occur. Chief Executive magazine reported there are three different types:
• Individual. • Peer-to-peer. • Organizational.
From a safety manager’s perspective, organizational accountability should be the first task accomplished. This refers to internal training procedures, seminars on new occupational methods and an overall understanding from top to bottom that safety comes first. At the individual level, employees should understand safety methods and procedures pertaining to their work. This starts with the hiring and onboarding process, where workers should learn and be tested on everything they need to know to prevent accidents. Peer-to-peer accountability is self-evident and it can be extremely effective for work in remote locations.
Key takeaway: Empower employees with the ability to rectify any potentially dangerous situation.
4. PRACTICE MAKES PERFECT Historical revisionism is a powerful tool when it comes to safety. Hindsight is always 20/20 and often leaves organizations in disbelief a risk wasn’t identified beforehand. Determining the contributing factors of incidents and accidents can help safety managers identify pertinent areas for improvement, such as training or equipment upgrade. Consider this: An employee falls off a scaffold and suffers a severe injury because of it. One of the first reactions is to check the equipment. A missing bolt is identified as the main culprit behind an uneven platform, causing a worker to lose balance. Another scaffold is ordered and the problem is solved.
Upon further review, however, the safety manager finds the flaw wasn’t in the equipment itself, but rather how it was set up. In this case, simply ordering a new platform won’t solve anything— employees must be educated on the proper procedures for setting up this apparatus on site. This idea that there’s a root cause of each injury is what makes a good preventative safety culture an excellent one.
Key takeaway: By investigating past incidents, safety managers can identify potential future risks and remedy these issues through directed employee training.
Preventative safety starts with a heightened awareness of the potential dangers and a collective effort to avoid running into them and in the end can save an organization millions of dollars.
This article was written by Harold Gubnitsky and appeared on the ProcessMAP web-blog located at https://blog.processmap.com. ProcessMAP was created to help businesses overcome the complexities of managing their Environmental, Health & Safety (EHS), and risk data. ProcessMAP helps customers across the globe optimize processes and performance, while mitigating risk.