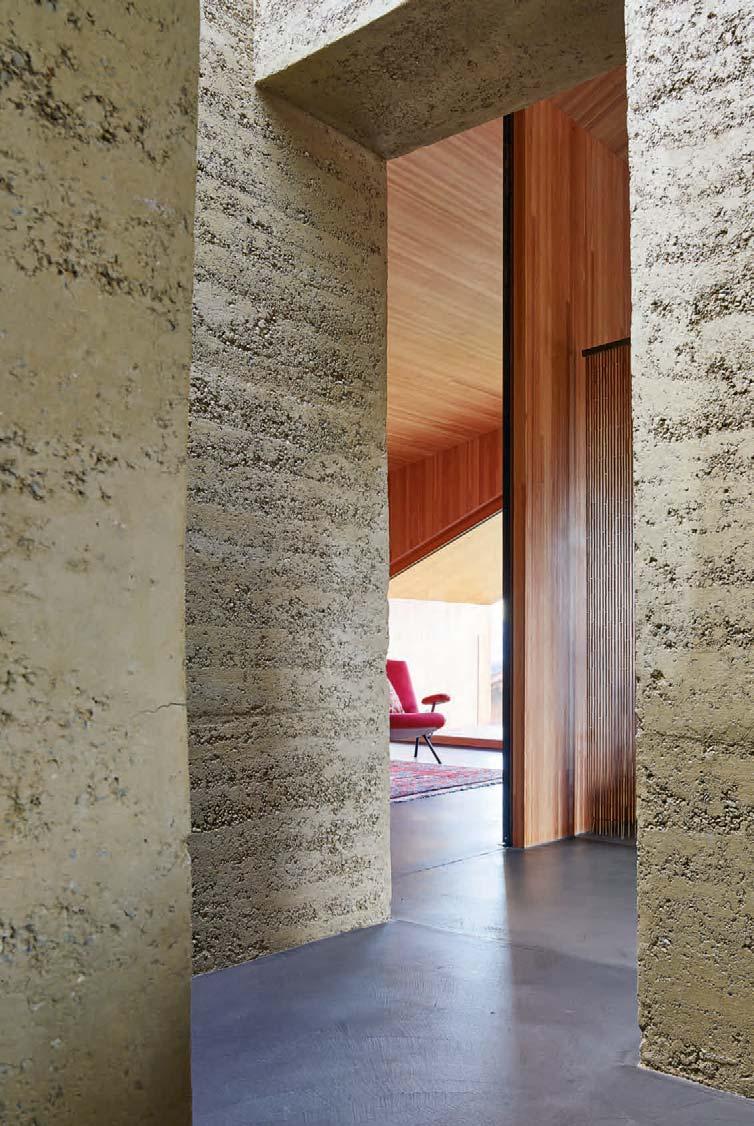

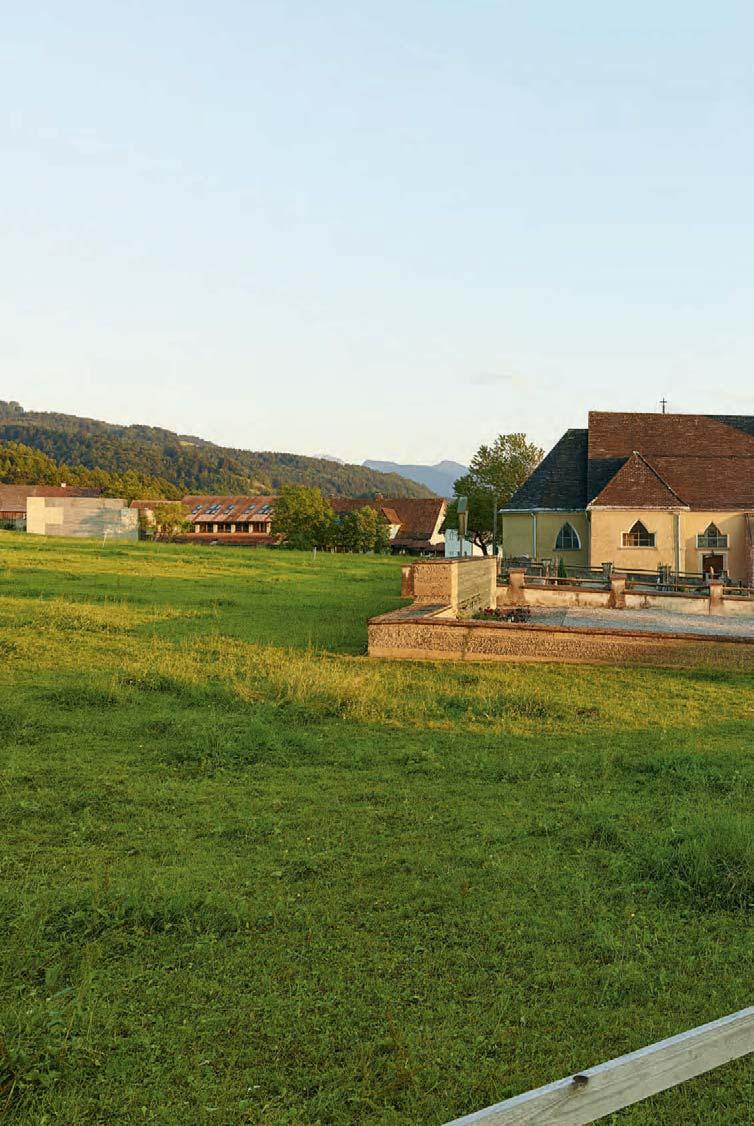
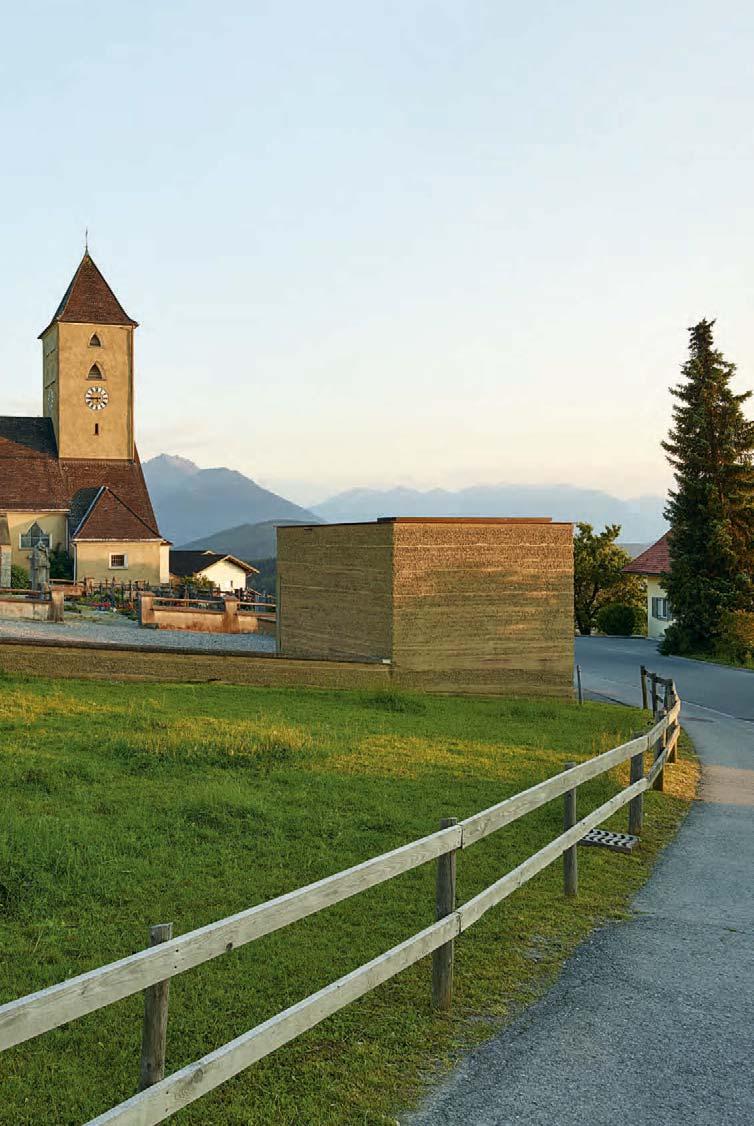
Civilization is the sustainable shaping of the earth into a figure that serves mankind. Otto Kapfinger
Rammed Earth Flooring
Earthen floors have existed for as long as humans have been building. No other material bears such a direct relationship to the ground on which we walk and stand. A floor composed of rammed earth is natural, simple, and, as such, commonly found in cultures all around the world. With the most elementary means, a space can be created from a clod of earth: a place to live in, set apart from nature. The floor of one’s home carries the living traces of its history. Smooth and responsive to the senses, rammed earth has a distinctly tactile quality. Its irregular surface is not only visually appealing but also acts as a sensual stimulus to the feet. Such floors, which require daily maintenance, can still be found in certain rural areas. Each evening, they are mopped with water to regenerate their sensitive surface. This type of floor is too rustic for contemporary tastes – even if the proximity to the earth retains its appeal, it is simply too inconvenient for people used to higher levels of comfort.
To bring the earthen floor into the twenty-first century, it was necessary to refine its conception. Its surface, in particular, has become easy to care for and extremely durable in modern implementations: a layer of customdesigned carnauba hard wax stabilizes the loam and infuses the floor with the necessary level of resilience. The process of construction has also been further developed. In traditional rammed earth flooring systems, only the lowest layers contain coarse gravel, with a finer-grained composite at the top. This creates a homogeneous finished surface, but it is susceptible to mechanical stresses and strains. By contrast, modern earthen floors are filled with the same gravel mixture until just below the surface, and the quality of the earth mixture is the same as would be used for rammed earth walls (see Material, p. 122). This increases the floor’s ability to withstand the tests of time and wear. However, these advances do not change the fact that constructing a rammed earth floor requires both mastery and experience of the techniques involved, since every step in the design process must take into account the unique conditions of the particular situation. One must know the material and have the skill to use it effectively to be capable of cultivating the full beauty and longevity of an earthen floor.
Earth-based flooring is labour intensive. It will occupy a craftsman for three to four weeks, because the construction work progresses in a series of staggered steps that are individually tailored to the job. Compared to standard flooring systems, this means higher costs; small floor areas tend to be more expensive, since they still involve the same complex preparation and the work requires the same sequence of steps. However, the effort is reflected in the result: each rammed earth floor is one of a kind – with an outstanding degree of warmth and comfort.
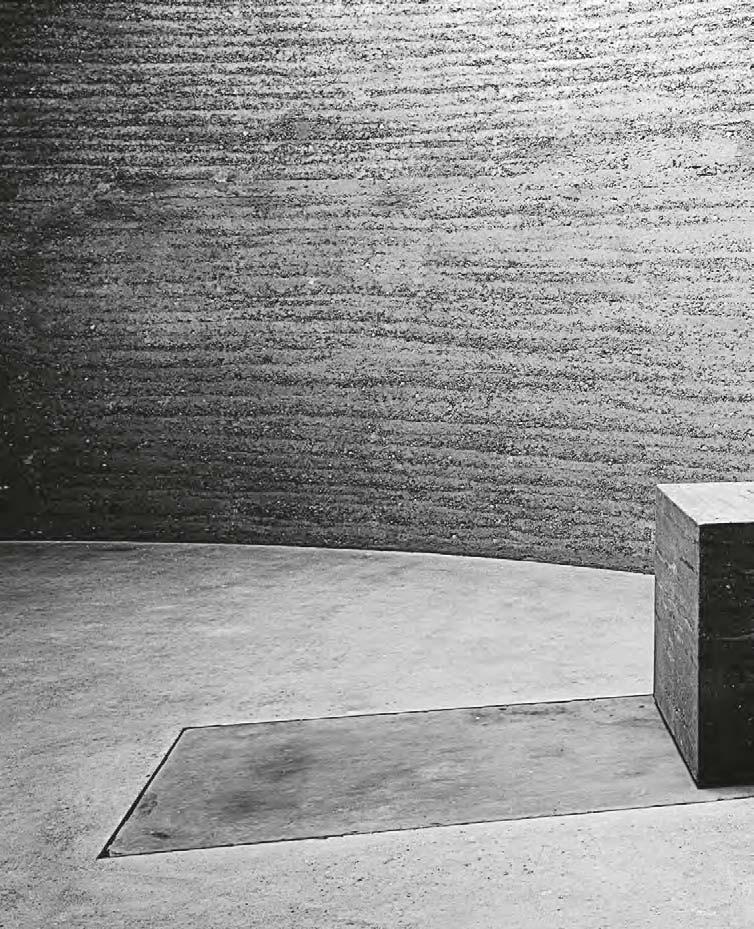
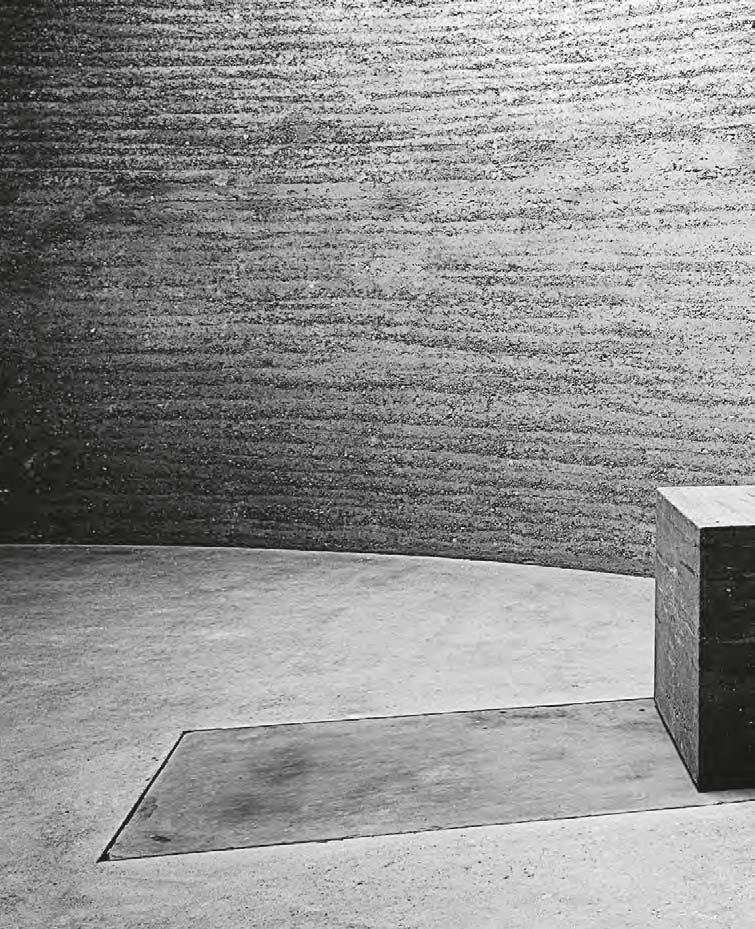
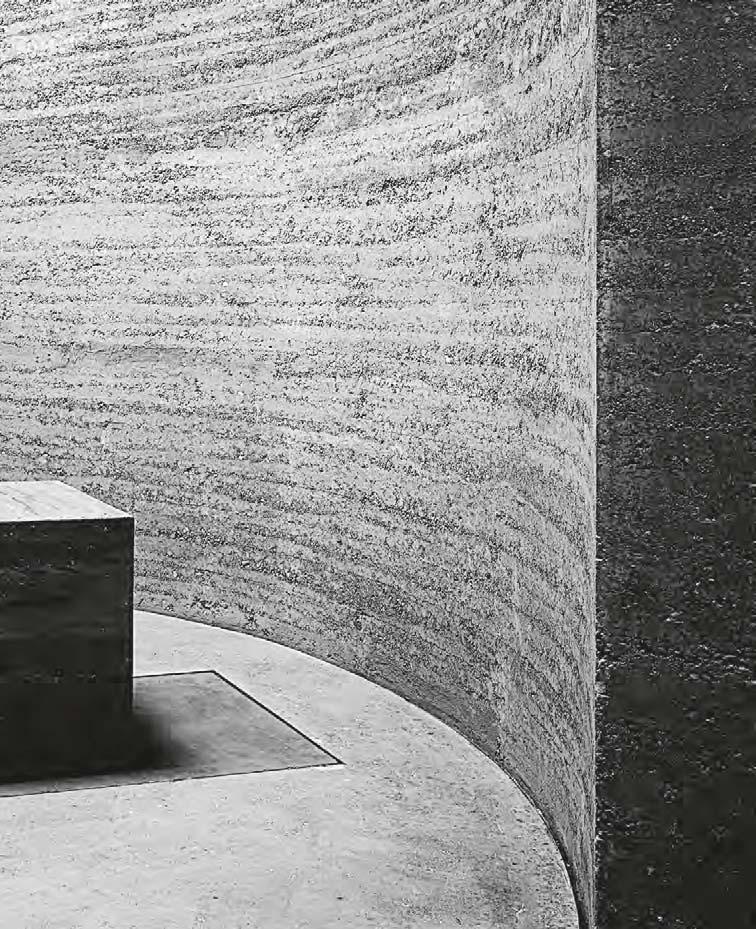
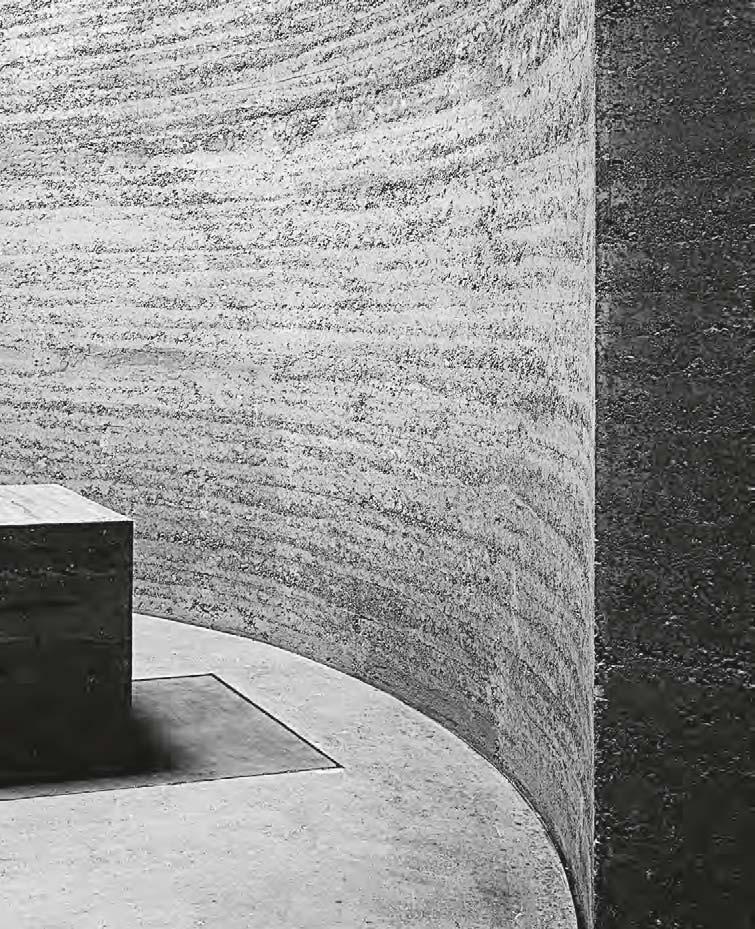
The Chapel of Reconciliation in Berlin was built on the foundations of the former Protestant Church of Reconciliation, which was demolished by the GDR government in 1985. An oval, in situ rammed earth wall surrounds the interior space of the church. The rammed earth floor was constructed in two layers directly on top of a 1 m thick base of compacted sand, preserving the remains of the former church below. The chapel is part of the Berlin Wall Memorial and hundreds of thousands of visitors have already walked across this floor.
Indoor production is the basis of prefabrication: this allows earth construction to proceed independently of the weather and expedites the building process. However, construction detailing becomes correspondingly more complex, as the walls must be split into elements.
Prefabrication
Another method of producing rammed earth walls is to manufacture them in a workshop. The first projects containing prefabricated wall elements were completed in the 1990s. This came about as a result of problems with production, which are still the main reason for prefabrication: firstly, earth cannot be rammed throughout the year during times of potential frost, and, secondly, construction schedules are frequently so tight that ramming a wall in situ would be impossible.
The solution to these problems was to produce elements that could be joined on-site to create entire walls (see Prefabrication, p. 124). Of course, this alters the mode of production, because formwork no longer needs to be installed on the building site. The challenge lies in connecting these elements to form a wall without losing homogeneity – and with as few visible joints as possible. The segments are typically custom-sized in workshops and prepared for installation. Most of the time, large sections are rammed and are then cut into individually sized pieces. This ensures a uniform optical layering and reduces the amount of retouching that needs to be done on-site. In the process, the vertical seams, which are a few centimetres in width, are filled in according to the natural compaction rhythm.
This is not only important for the visual appearance but is also a technical requirement for the erosion checks, as any break in this band – as with a crack in a dam – can lead to increased erosion.
The joints are filled with the rammed earth material and retouched by hand. After they have dried, the seams are nearly invisible. The erosion process eventually results in a thoroughly monolithic appearance.
Rammed earth has a distinctive horizontal structure. In order to preserve this continuous striation, elements created during a single ramming process are installed in the same order.

Roof Edge and Plinth
An old saying states that “a rammed earth wall needs a good hat and good boots”. The hat must be formed such that no rainwater can collect, permeate the construction, or drain from the coping across the rammed surface in significant quantities. Here, the roof overhang is not nearly as important as the impermeability and functionality of the technical solutions found for the detailing.
During project work, countless ways of covering the top of rammed earth walls have been developed and reams of experience gained. The following assembly has been thoroughly tried and tested: a thin layer of trass-lime mortar is prepared directly on the edge of the roof – ideally in combination with a ring beam – and bituminous waterproofing is affixed to it. In general, this constitutes the point of interface between the work of an earth building expert and a roofer. On top of this construction, a conventional roofing system can be installed – for example, sheet metal with a drip cap. As such, the edge of the roof must conform to standard building regulations. The roofing edge can also be anchored into the ring beam (see Ricola Kräuterzentrum, edge detail, p. 85).
In plinth detailing, the main job is to prevent capillary action from causing rising damp through the use of a damp-proof membrane. Another concern is exposure to water splash at the intersection of the horizontal and vertical planes – this applies not only to the point where the wall comes into contact with the ground but also to balconies and terraces on the upper storeys. Earth alone is therefore not a suitable material for foundations or plinths, an alternative being a lean concrete mixture or reinforced concrete. In order not to differentiate too strongly between plinth and wall, the concrete is often coloured with an earth-like pigment or constructed as rammed concrete. The rammed earth walls of the Sihlhölzli buildings are subject to increased erosion, due to the higher velocity of wind-driven rain flowing down the smooth faces of the concrete that lies directly above. To reduce this phenomenon, a porous, coarse layer of trass-lime mortar was integrated in between the rammed earth and concrete as an erosion check. This creates a step-like transition between the extremely hard concrete roof and the nonstabilized rammed earth wall. Nevertheless, practical experience indicates that this joint is subject to intensified erosion. To avoid this entirely, a small overhang with a drip cap should be integrated into the design.
Slope 10%
Slope 1%
In the small, uninsulated structures of the Sihlhölzli sports complex in Zurich, the concrete roof was cast directly onto the rammed earth wall (see section on Reinforced Concrete Slabs, p. 116). To avoid water damage from above, the rammed earth is protected with bituminous waterproofing. Roof edge at 1:20 scale.
Reinforced concrete 25 cm
Trass-lime mortar
Bituminous waterproofing 0.5 cm
Rammed earth wall 40 cm
Trass-lime check
Corten steel covering 0.3 cm
Wooden substructure
Bituminous waterproofing 0.5 cm
Trass-lime coating 2 cm
Reinforced trass-lime ring beam 15 x 10 cm
Trass-lime check
Rammed earth façade 45 cm
Friction-fit bracket fixed to load-bearing structure
The roof edging of the Swiss Ornithological Institute in Sempach incorporates a conventional detail with sheet-metal capping. The rammed earth wall can be treated in the same way as any other form of massive construction. Roof edge at 1:20 scale.
Slope 10%
Slope 7%
Rauch House
In the Rauch House, the structural system of rammed earth also serves as the façade. The bituminous roof cladding continues right up to the edge of the wall; the parapet is covered with an additional metal sheet and finished with fired clay tiles, which extend seamlessly into the roof cladding. The tiles are set but not grouted. As a result, rainwater seeps into the coarse-grained foam-glass fill below and is drained off down a slight gradient.
The rammed earth walls that come into contact with the ground have 10 cm thick exterior foam-glass insulation and are protected from moisture with multilayered bituminous waterproofing. The bitumen layer also extends to the upper edge of the plinth, where the junction is clad with clay tiles. As an additional permanent form of protection, the plinths and surfaces touching the ground are coated with a rich clay slurry. Façade cross section at 1:20 scale.
Bituminous waterproofing
Foam-glass insulation
Rich loam
Low-fired mud tile covering 4 cm
Crushed volcanic rock filling 17 cm
OSB board with bituminous waterproofing 2.5 cm
Reed insulation 20 cm
Granulated cork–loam–trass-lime slope 0-10 cm
Solid wood slab (“Dippelbaum”) 18 cm
Wooden frame to level ceiling joists 3 cm
Clay board and finish clay plaster 3+1 cm
Rammed earth wall 45 cm
Reed insulation 2x5 cm
Clay undercoat and finish clay plaster 3+1 cm
Rammed earth floor 8 cm
Cork–clay–trass-lime mixture 8 cm
Reed insulation 2x5 cm
Reinfored trass-lime mortar 25 cm
Low-fired mud brick
Clay mortar
T-beam 60/60
Rammed earth floor 8 cm
Cork–clay–trass-lime mixture 20 cm
Foam-glass filling 20 cm
3% Ricola Kräuterzentrum
The walls of the Kräuterzentrum in Laufen do not carry any additional loads. The prefabricated façade acts as cladding for a post-and-beam reinforced concrete structure and is attached with anchoring channels.
The edge of the roof consists of corrugated sheet metal attached to concrete coping. The roof is composed of in situ concrete slabs, which are supported by a concrete frame. The plinth is also constructed as a pigmented strip of lightweight concrete. It protects the wall from rain splash while simultaneously providing a base for the various elements. Façade cross section at 1:20 scale.
Slope
Corrugated sheet covering
Concrete wall coping
Covering mounting parts
Reinforced trass-lime ring beam
Emergency overflow
Trass-lime check
Rammed earth façade 45 cm
XPS insulation 7 cm
Reinforced concrete pillar 55 cm
Friction-fit bracket fixed to façade
Stainless steel profile
Rammed earth façade 45 cm
Trass-lime check
Bitumen coating and clay mortar 1.2 cm
Plinth made of pigmented insulating concrete
Gravel drainage
XPS insulation
Gravel lawn
Subsoil drain
Blinding concrete
Omicron:CrossingBorder–Artinstallation
Klaus, Austria, 2014, Design: ARGE Anna Heringer & Martin Rauch , load-bearing, in situ, 80 m2, 33 t
Single-FamilyHouseB.-S.–Rammedearthwall
Almens, Switzerland, 2014, Architecture: Norbert Mathis Architekt, non-load-bearing, prefabricated, 42 m2, 44 t
Single-FamilyHouseÖ.-E. – Rammedearthwall
Ruggell, Liechtenstein, 2014, Architecture: Architektur Atelier, non-load-bearing, prefabricated, 37 m2, 26 t
NovartisCampus – Trass-limewall
Basel, Switzerland, 2015, Landscape architecture: Vogt Landschaftsarchitekten, free-standing, in situ, 1,050 t
SwissOrnithologicalInstitute–Rammedearthfaçade Sempach, Switzerland
2013 − 2014, Architecture: mlzd Architekten, non-load-bearing, prefabricated, 1,240 m2, 1,130 t
ETHMaterialsWorkshop–Rammedearthcupola –Zurich, Switzerland, 2013 − 2014, Organization & design: D-ARCH, Chair of Prof. Annette Spiro, research assistant: Gian Salis, Martin Rauch, Andreas Galmarini, load-bearing, prefabricated, 39 t
KindergartenMuntlix – Rammedearthfloor Muntlix
Austria, 2013, Architecture: Hein Architekten, 492 m2, 93t
RicolaKräuterzentrum – Rammedearthfaçade Laufen, Switzerland
2012 − 2013, Architecture: Herzog & De Meuron, non-load-bearing, prefabricated, 2,780 m2, 2,935 t
HarvardUniversityWorkshop–MudWorks
Cambridge , USA, 2012, Design: ARGE Anna Heringer & Martin Rauch, free-standing, in situ, 30 m2, 45 t
Single-FamilyHouseF. – Rammedearthwall&Lehmo
Schwarzach, Austria, 2012, Architecture: Heim & Müller non-load-bearing, in situ, 55 m2, 46 t
SchoolPavilionAllenmoosII – Rammedearthfaçade Zurich, Switzerland
2011 − 2012, Architecture: Boltshauser Architekten, load-bearing, in situ, 130 m2, 119 t
EarthBuilding,MerianGardens – Rammedearthfaçade
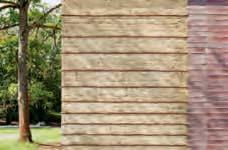
Basel, Switzerland, 2011 − 2012, Architecture: Barcelo Baumann Architekten, non-load-bearing, prefabricated, 281 m2, 169 t
Single-FamilyHouseB.-S. – Rammedearthwall Flims, Switzerland
2011, Architecture: Fehlmann Brunner Architekten, load-bearing, prefabricated, 230 m2, 195 t
EschenCemetery – Rammedearthwall
Eschen, Liechtenstein, 2010 − 2012, Architecture: Hans-Jörg Hilti, free-standing, prefabricated, 125 m2, 112 t
EarthWorksSummerSchool – Workshop
Gmunden, Austria, 2010, Organization & design: Linz University of Art and Design – BASEhabitat; Anna Heringer & Martin Rauch, free-standing, prefabricated, 15 t
MezzanaAgriculturalCollege – Rammedearthfaçade Coldrerio, Switzerland, 2010 − 2012
Architecture: Conte Pianetti Zanetta Architetti, non-load-bearing, prefabricated, 930 m2, 760 t
KingAbdulazizCentreforWorldCulture – Rammedearth wall Dhahran, Saudi Arabia, 2010 − 2014, Architecture: Snøhetta, non-load-bearing, prefabricated, 2,823 m2, 3,009 t
MartinRauchErosion–Exhibition Haus der Architektur Graz 2010, Design: Martin Rauch, Eva Guttmann
Single-FamilyHouseStallPlazzaPintgia – Rammedearthwall Almens, Switzerland
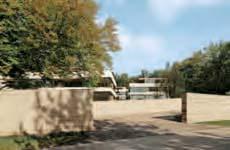
2010, Architecture: Gujan + Pally, load-bearing, prefabricated, 59 m2, 70 t
GönhardSchoolComplex–Trass-limefaçade Aarau, Switzerland, 2009 − 2010, Architecture: Boltshauser Architekten, non-load-bearing, prefabricated, 243 m2, 200 t
LohbachHomefortheElderly–Rammedearthwall Lohbach, Austria, 2009, Architecture: marte.marte architekten, non-load-bearing, prefabricated, 16 m2, 2 t

JungFuneralParlour–Rammedearthsculpture Salzburg, Austria, 2009, Design: Martin Rauch non-load-bearing, prefabricated, 47 m2, 12 t
EmbachSpiritualCentre–Rammedearthwall Embach, Austria, 2009 − 2010, Architecture: LP Architektur, load-bearing, in situ, 85 m2, 39 t
SilPlazCinema–Rammedearthwallandfloor
Ilanz/Glion, Switzerland, 2009 − 2010, Architecture: Capaul & Blumenthal Architects, non-load-bearing, in situ, 182 m2, 67 t
LetziApartmentComplex–Rammedearthwall Küsnacht, Switzerland 2009, Architecture: Peter Kunz Architektur, free-standing, prefabricated, 287 m2, 238 t
“PlantRoom”,KunstraumDornbirn–Artinstallation
Dornbirn, Austria, 2008, Artist: Simon Starling load-bearing, in situ
ConfignonCommunityCenter–Rammedearthwall Confignon, Switzerland, 2007, Architecture: atelier b & m architecture & territoire, free-standing, in situ, 54 m2, 57 t
NovartisCampus–Trass-limewall
Basel, Switzerland, 2007, Landscape architecture: Vogt Landschaftsarchitekten, free-standing, in situ, 800 t
FlunternCemetery–Rammedearthwall Zurich, Switzerland, 2007, Landscape architecture: Berchtold.Lenzin Landschaftsarchitekten, free-standing, in situ, 25 m2, 29 t
Single-FamilyHouseRauch–Rammedearthfaçadeandfloor Schlins, Austria 2005 − 2008, Architecture: Roger Boltshauser & Martin Rauch, load-bearing, in situ
VerwaltungsgebäudeUVEK–Artinstallation Bern, Switzerland, 2005 − 2006, Design: raderschallpartner landschaftsarchitekten, Martin Rauch, 6 m2, 27 t
HergiswilCemetery–Rammedearthwall Hergiswil Switzerland, 2005, Architecture: Richard Kretz, Renato Lampugnani & Martin Rauch, free-standing, in situ, 41 m2, 70 t
RiemChurch–Rammedearthfloorandaltar
Munich, Germany, 2005, Design: Florian Nagler
Architekten & Martin Rauch, 28 m2, 9 t
WarehouseGrounds–Trass-limewall
St. Gallen, Switzerland, 2005, Architecture: Vogt Landschaftsarchitekten, free-standing, in situ, 47 m2, 81 t
Kardinal-Schwarzenberg-Haus–Rammedearthwall
Salzburg, Austria, 2005, Architecture: Flavio Thonet non-load-bearing, in situ, 77 m2, 31 t
LaRaiaVineyard–Rammedearthfaçade Novi Ligure, Italy
2005, Architecture: Ivana Porfiri, non-load-bearing, in situ, 223 m2, 239 t
WellnessAreaatWaldhausMountainResort–Rammed earthwall Flims, Switzerland, 2004, Architecture: Hans Peter Fontana & Partner, non-load-bearing, in situ, 130 m2, 99 t
QuasiBrick,LaBiennalediVenezia–Exhibition
Venice, Italy, 2003, Artist: Olafur Eliasson
VigiliusMountainResortHotel–Rammedearthwall
Lana, Italy, 2003, Architecture: Matteo Thun, free-standing prefabricated, 230 m2, 98 t
ChesaValisaHotel–Rammedearthwall
Hirschegg, Austria, 2002, Architecture: Architekten
Hermann Kaufmann, load-bearing, prefabricated, 69 m2, 65 t
SchlinsCemetery–Rammedearthwall
Schlins, Austria , 2001, Design: Martin Rauch free-standing, in situ, 68 m2, 79 t
ChapelofRestattheBatschunsCemetery–Rammedearthfaçade Batschuns, Austria 2001, Architecture: marte.marte architekten, load-bearing, in situ, 17 6 m2, 153 t
ThüringenBusStation–Rammedearthwall
Thüringen, Austria, 2001, Architecture: Bruno Spagola non-load-bearing, prefabricated, 17 m2, 6 t
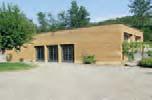
SihlhölzliSportsComplex–Rammedearthfaçade
Zurich, Switzerland, 2001 − 2002, Architecture: Boltshauser Architekten, load-bearing, in situ, 250 m2, 247 t
“TheMediatedMotion”,KunsthausBregenz–Exhibition
Bregenz, Austria, 2001, Artist: Olafur Eliasson & Günther Vogt, 470 m2, 50 t
“Earthwall”,HamburgBahnhof–Exhibition
Berlin, Germany, 2000, Artist: Olafur Eliasson free-standing, in situ, 96 m2, 100 t
ChapelofReconciliation–Rammedearthfaçade
Berlin, Germany, 1999 − 2000, Architecture: Rudolf Reitermann & Peter Sassenroth, load-bearing, in situ, 180 m2, 250 t
EtoshaHouseatBaselZoo–Rammedearthfaçade Basel, Switzerland
1998 − 1999, Architecture: Peter Stiner, load bearing, in situ, 420 m2, 400 t
GuglerPrintersOfficeBuilding–Rammedearthwall Pielach, Austria
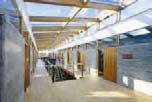

1998 − 1999, Architecture: Ablinger, Vedral & Partner, non-load-bearing, prefabricated, 350 m2, 210 t

AlpbachCongressCentre–Rammedearthwall
Albpach, Austria, 1998, Architecture: DINA4 Architektur non-load-bearing, in situ, 270 m2, 110 t
Single-FamilyHouseR.–Rammedearthwall
Hard, Austria 1997, Architecture: Architekten Hermann Kaufmann, non-load-bearing, in situ, 14 m2, 9 t
St.Gerold’sPrioryCemetery–Rammedearthwall St. Gerold, Austria, 1994, Design: Martin Rauch free-standing, in situ, 145 m2, 40 t
Single-FamilyHouseM.–Rammedearthfaçade
Rankweil, Austria, 1993 − 1996, Architecture: Robert Felber & Martin Rauch, load-bearing, in situ, 150 m2, 160 t
FeldkirchStateHospital–Rammedearthwall Feldkirch, Austria
1992 − 1993, Design: Martin Rauch, non-load-bearing, in situ, 550 m2, 250 t
LehmTonErdeStudio–Rammedearthfaçade Schlins, Austria
1990 − 1994, Architecture: Robert Felber & Martin Rauch, non-load-bearing, in situ, 132 m2, 144 t
AtelierGassner–Rammedearthwall
Schlins, Austria, 1984, Architecture: Rudolf Wäger non-load-bearing, in situ, 8 m2, 8 t
Single-FamilyHouseR.–Rammedearthwall
Schlins, Austria, 1982 − 1986, Architecture: Johannes Rauch non-load-bearing, in situ, 70 m2, 40 t
Glossary
Airrammer
Carnaubahardwax
Casein
Clay
Druckluftstampfer
Carnauba-Hartwachs
Air pressure rammers are pneumatic compaction devices that are usually operated by hand.
Wax that is derived from the leaves of the carnauba palm. It is the hardest known form of natural wax.
The main protein present in milk – a traditional, natural, and powerful binding agent
Clay is composed of natural, fine-grained minerals. With the addition of water, it becomes malleable. After it dries, the clay hardens but the process remains reversible; after firing, the bond becomes non-water-soluble.
Construction documentation
Drumcompactor
Walzen
Earthbuilding
Earth-moist
Earthmortar
Equilibrium moisturecontent
Lehmbau erdfeucht
Lehmmörtel
Gleichgewichtsfeuchte
Erosion
Excavation
Erosion Aushub
Construction documentation refers to the preparation of drawings for elements to be produced in the factory or the in situ formwork plan for the building site.
Compaction rollers are commonly used in civil engineering and were originally used to compact the earth for trenches. The same process is also possible in solid formwork.
General term for building with loam using a variety of techniques
Describes the natural moisture content of earthen material. During the construction process the rammed earth mixture should be earth-moist.
Used to join together different earthen elements. Composed of a simple mixture of slightly fluid loam, sand, and water, earth mortar is reversible and can be reinforced with plant fibres.
The water content of a material that has stabilized after being stored under stable conditions over a period of time. The equilibrium moisture content of earth is 6–7 per cent, which is less than that of wood (ca 9 per cent).
The natural weathering and abrasion of stone and soil. In rammed earth building, calculated erosion refers to a predictable form of erosion whose development is determined by structural features (erosion checks) and the quality of both the material and the compaction process.
The material that is removed from a construction pit (through the digging out of cellars and foundations). With rammed earth, this cannot contain any topsoil.
Graveladditives
Insituconstruction
Loam,lean
Loam,rich
Loam,soil,earth,mud
Gesteinszuschläge
Mineral additives made of different kinds of stone; in rammed earth they can vary in size by up to 32 mm.
On-site processes of fabrication refer to the production of rammed earth walls and floors directly on the job site.
Loam with a low clay content is described as lean.
Loam with a high proportion of cohesive clay is described as rich.
Loam is a mixture of sand, silt, and clay. It is created by the processes of weathering and erosion.
Marl
Micro-crack
Mergel
Mikroriss
A sedimentary stone composed of clay, silt, and lime.
A very fine crack invisible to the naked eye. During the drying process, loam is subject to shrinkage. In the case of rich loam, the visible cracks will always be accompanied by countless micro-cracks.
Moisture
Feuchtigkeit
Moistureexpansion
Prefabrication
quellen
Vorfertigung
Rammedearth
Rammedearthfaçade
Rammedearthfloor
Rammedearthprefebricated component
Rammedearthwall
Ramming
Retouching
Self-supporting
Shrinkage
Slaking
Slurry
Trass-lime
Watervapor diffusion
Waxemulsion
Stampflehm
Dampness – both in the form of water (moisture that is rising, standing, running off, or used as part of the mix) and as water vapour –plays an important role in earth building (moisture control).
If water is added to loam, its volume increases and it swells.
The production of rammed earth components in a workshop. The finished elements are then transported to the building site for installation.
Massive earth building technique. Rammed earth is made from a mixture of loam and granulated stone, that can be frequently be found in nature.
Stampflehmfassade
Stampflehmboden
Stampflehmfertigteil
Stampflehmwand
stampfen
Retusche
selbsttragend
schwinden
mauken
Lehmschlämme
Trasskalk
Dampfdiffusion
Wachsemulsion
A rammed earth wall that is usually self-supporting and is exposed to the weather
A massive floor made of rammed earth that has been compacted to ca 10 cm
An indoor-prefabricated segment, which is then installed on-site with other prefabricated elements to form a wall
Massive, vertically oriented building component made of rammed earth
A method of compaction to bind earth-moist loam. In the process, the loose earthen material is turned into a solid mass.
The process of making additional improvements to a surface or joint
Building element able to carry its own weight but not that of others
As moisture evaporates, the volume of loam decreases, causing it to shrink.
The deliberate storage of ready-mixed earth. The process of resting and aging increases the cohesiveness of clay as a binding material.
A mixture of loam and a large amount of water. As such, loam-based slurry is more fluid than earth mortar.
Trass is a natural volcanic stone with a high level of silicic acid, which reacts with lime to become an almost completely non-water-soluble substitute for mortar or cement.
The transmission of water vapour through a building component. If this transmission is unrestricted – i.e., it is not retarded by a damp-proof membrane – it is referred to as vapour permeability.
Water-soluble emulsion with a wax component
Editors: Otto Kapfinger, Marko Sauer
Author: Marko Sauer (except where otherwise indicated)
Production management/subeditor:
Clemens Quirin (first edition), Franziska Möhrle (second edition)
Translation from German to English: Lindsay Blair Howe
Technical copy-editing: Laura Marcheggiano
Copy-editing: Simon Cowper
Publishing coordination: Steffi Lenzen
Graphic concept and design: Atelier Andrea Gassner, Andrea Gassner
Photographs:
Reinold Amann: p. 76, Beat Bühler: pp. 73, 110 – 111, 160
Markus Bühler-Rasom: pp. 81, 120, 134 – 139, 144 –157, Ralph Feiner: p. 161
Michael Freisager: p. 96, Bruno Helbling p. 159, Bruno Klomfar: pp. 54 – 55, 163
Lehm Ton Erde: pp. 61, 76, 101, 162, Hanno Mackowitz: pp. 68 – 69, 107, 140 – 141, 142 – 143, 158
Benedikt Redmann: pp. 14 – 51, 90 – 91, 159, Dominique Wehrli: p. 163
Illustrations based on plans/details by:
Boltshauser Architekten: Haus Rauch, pp. 84, 101, 112 – 113, 114, 115, 161
Sportanlage Sihlhölzli, pp. 78 – 79, 83, 97, 116
Conte Pianetti Zanetta Architetti: Mezzana Agricultural College, pp. 104, 105, 118, 160
Fehlmann und Brunner Architekten (FeBruAr), p. 160
Robert Felber: Lehm Ton Erde Studio, pp. 98, 115, Mathies House, p. 119
Hans Peter Fontana und Partner: Waldhaus Mountain Resort, p. 97
haascookzemmrich Studio2050: Alnatura Campus, p. 86
Herzog & de Meuron: Ricola Kräterzentrum, pp. 81, 85, 92 – 93, 100, 103, 160
Lehm Ton Erde: ERDEN Werkhalle, pp. 70 – 71, 87, 106 marte.marte architekten: Batschuns Chapel of Rest, p. 101, 162 :mlzd: Swiss Ornithological Institute Visitor Centre, pp. 83, 102, 160
Rudolf Reitermann & Peter Sassenroth: Chapel of Reconciliation, pp. 56 – 57, 99, 100 Peter Stiner: Etosha House at Basel Zoo, p. 162
Plan graphics:
Pauline Sémon und Laura Marcheggiano (first edition), Franz-Felix Juan und Franziska Möhrle (revised edition)
Printing: BULU, Lustenau © 2022, 3rd revised and expanded edition
DETAIL Business Information GmbH, Munich detail.de
All rights reserved. No part of this publication may be reproduced, distributed, or transmitted without the prior written consent of the publisher, except in non-commercial uses permitted by copyright law.
Bibliographic information published by the German National Library. This publication is catalogued in the Deutsche Nationalbibliografie by the German National Library; bibliographic details can be found online at http://dnb.d-nb.de.
ISBN 978-3-95553-573-5 (Print)
ISBN 978-3-95553-574-2 (E-Book)