9 minute read
CLEANER FUEL
Next Article
B.C. cleantech primed to power industry’s decarbonization
NELSON BENNETT
Thirty years hence, after demand for Alberta’s oil has entered a predicted decline, the Trans Mountain pipeline, currently under expansion, might be used to move other, lower carbon fuels through Vancouver.
Thirty years hence, after demand for Alberta’s oil has entered a predicted decline, the Trans Mountain pipeline, currently under expansion, might be used to move other, lower carbon fuels through Vancouver.
Fuels like ammonia, for example. Three parts hydrogen to one part nitrogen, it is an excellent carrier for hydrogen, which by 2050 could be produced in large quantities in Alberta from natural gas and exported worldwide.
And by 2050, hydrogen fuel cell-powered trains could also be moving through B.C. transporting carbon black — a by-product of hydrogen production from natural gas using methane pyrolysis — to B.C. ports for export to rubber manufacturers around the world.
This is how Matthew Klippenstein, branch manager for Hydrogen BC, imagines the energy transition unfolding in Western Canada. But between now and then, a whole lot of clean technology needs to be deployed, and B.C. is positioned to be a key provider.
There are significant opportunities for B.C.-made clean technologies in the resources, energy and heavy industry sectors, particularly in the areas of hydrogen and carbon capture utilization and storage (CCUS). “We have the opportunity to lead on CCUS and hydrogen in the country,” says Jeanette Jackson, CEO of the Foresight cleantech accelerator.
A number of federal and provincial programs are providing funding for the cleantech sector. One is the federal government’s $1.5 billion clean fuel fund. Another is the new Centre for Innovation and Clean Energy (CICE). In addition, Foresight has a new program, called Grow, which helps more advanced cleantech companies with commercialization. “In 18 months, we’ve supported over 25 B.C. ventures, and as of last month those ventures have secured $428 million in capital, $220 million revenue and created over 475 jobs,” Jackson says.
Expected to be up and running this fall, the new CICE program is being set up with $105 million in funding from Shell Canada, and B.C. and federal governments. It will help B.C. cleantech companies get to commercialization by working with Canadian industries.
The five main areas of focus for the CICE program are: ■ CCUS; ■ hydrogen production, use and distribution; ■ biofuel and synthetic fuel production; ■ renewable natural gas; and ■ battery technology, storage and energy management.
While there are opportunities for B.C. cleantech companies in all of Canada’s resource industries — from mining to forestry — the biggest domestic market is in oil and gas. Since Alberta and Saskatchewan have the biggest challenges when it comes to decarbonisztion, thanks to their oil and gas industries and their use of coal for power production, those two provinces represent the biggest markets for cleantech focused on decarbonization.
“There will be a huge amount of work on carbon capture,” Klippenstein predicts. “B.C. is absolutely a leader in carbon capture technology.”
Hydrogen production and CCUS go hand-in-glove, at least in the Canadian context, since CCUS is a critical part of blue hydrogen production from natural gas.
Svante, which developed a new kind of filter for capturing carbon dioxide (CO2) from flue stacks, sees big opportunities in Alberta, where hydrogen production from natural gas is seen as a logical transition industry. Svante recently secured the old Best Buy headquarters in Burnaby, where it will set up a new
B.C. BIOFUELS
Pulp mill sector ripe for biofuel production
Full use of B.C.’s forestry
waste for biofuels could reduce
the province’s greenhouse
gas emissions by 10% to 15%,
says Tony Bi, director of the
Biorefining Research and
Innovation Centre • CHUNG CHOW
Heavy industry accounts for 14% of B.C’s greenhouse gas emissions. One sector that may be uniquely positioned for fuel switching, from natural gas to biofuels, or for making other low-carbon fuels for other sectors, is the province’s pulp and paper industry.
Douglas Singbeil, sector leader of bioproducts at FP Innovations, says B.C. craft pulp and paper mills account for about 10% of the natural gas consumed in B.C. The gas is used in lime kilns during the pulp and paper bleaching process.
But pulp and paper mills already consume large amounts of wood waste, some of which could be turned into biogas to displace the natural gas they use, or into other types of biofuel.
“The mills would reduce the amount they use to a very small proportion of what they do today,” Singbeil says.
The pulp and paper industry is one sector the new Biorefining Research and
Innovation Centre (BRIC) at the University of British Columbia (UBC) wants to help decarbonize. The new research centre will be working with the BC Pulp &
Paper Bio-Alliance to identify opportunities in B.C.
Bark from trees (called hog fuel) is not used in the pulp making process, so it’s a waste product that could become a feedstock to make biogas or liquid biofuels. There are a number of technology approaches for that, including conventional pyrolysis, fast pyrolysis and hydrothermal liquefaction.
Canfor is already making the move into biofuels in partnership with Australia’s
Licella Fibre Fuels Pty Ltd. Their joint venture, Arbios Biotech, plans to build a new biofuel plant — at an estimated capital cost of $25 million to $30 million — at Canfor’s Intercontinental Pulp Mill in Prince George.
The plant will use Licella’s hydrothermal liquefaction process, which can turn a wide variety of feedstocks — not just wood waste — into biofuel. The new plant will produce biocrude to be sold to oil refiners. It would have a 70% to 80% lower carbon intensity than fossil fuel crude.
The first phase of the new Arbios Biotech plant would turn 25,000 tonnes of wood waste — mostly bark — into 50,000 barrels of biocrude annually, and would employ 25 workers. The partners aim to have the plant in production in the first half of 2023.
Shell Catalysts and Technologies is looking to use the biocrude in Shell’s refineries. It would have a 70% to 80% lower greenhouse gas emission intensity than fossil fuel crude.
Alan Nicholl, Canfor’s former chief financial officer and executive vice-president, is the new CEO of the Arbios Biotech joint venture. He believes biofuels open up a whole new value-added dimension for the forestry sector.
“Canfor believes that the forestry industry is uniquely positioned to play a leading role in the world’s transition to a low-carbon future,” Nicholl says. “If the technology is successful, we would be looking at further deployment across Canada and, indeed, if all goes well, across North America and Europe.”
BRIC director Tony Bi says the centre wants to work with industry to help other companies make similar moves to lower carbon fuel production. The centre will help solve engineering and economic pain points for industry and their technology partners.
“We need to team up with the industry to see how we can help them, to develop the technology or evaluate the technology from other developers,” Bi says.
Converting dry wood waste to syngas typically involves pyrolysis — high heat and low oxygen. UBC already has some expertise in that space. Ten years ago, UBC partnered with Nexterra Systems and General Electric to build a demonstration gasification plant that uses wood waste to produce heat and power for the campus.
B.C. produces a significant amount of wood waste, as well as agricultural waste, which can also be used for making a variety of biofuels. One B.C. company, BC Biocarbon, is using conventional pyrolysis to turn wood and agricultural waste into a range of biofuels and other products, including biochar.
But the conventional approach to pyrolysis is slow, Bi says. One company in Ontario, Ensyn, has developed fast pyrolysis method for making biofuels that vastly improves on the pyrolysis process, Bi says.
While that approach has the potential to produce biocrude for oil refineries to lower their emissions intensity, Bi says there are challenges when it comes to upgrading that biocrude to the standards required by refineries. Fixing that kind of pain point is the sort of problem BRIC is being set up to do.
“If we could only fully utilize biomass refuse in B.C., we can help B.C. to reduce greenhouse gas emissions by 10% to 15%,” Bi says.
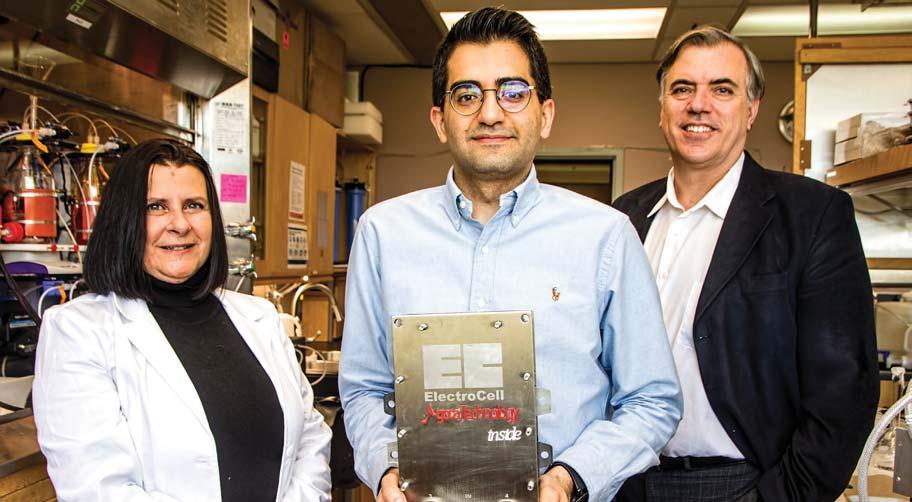
Agora Energy is killing two decarbonization birds with one stone by using captured CO2 in a flow battery that stores power from wind and
solar • CHUNG CHOW
manufacturing plant for making its carbon capture filters. “This will be the first plant in the world making filters at that scale,” says Svante CEO Claude Letourneau.
While captured CO2 is currently used mainly in enhanced oil recovery (with most of it being permanently sequestered underground), the scramble is on to find other, value-added uses for captured CO2, rather than just burying it underground.
Carbon Engineering, the B.C. company in the direct air capture space, is working with LanzaTech in the U.S. on a process that combines captured CO2 with water to produce a low-carbon jet fuel. Hydrogen production from natural gas using methane pyrolysis, meanwhile, can produce carbon black as a by-product, which is used as a filler in tires, cables and other rubber products. It’s already being done in the U.S. by Monolith Materials, so it’s a proven technology. In B.C., Ekona Power is also in the methane pyrolysis space. “The value of the carbon — the carbon black — if you can engineer it for desirable properties, could actually be more valuable than the hydrogen itself, because it’s a value-added product,” Klippenstein says.
One B.C. cleantech company, Agora Energy Technologies, is developing technology that solves two problems at once: what to do with CO2 once it’s captured, and how to store intermittent wind and solar power. Agora has developed a flow battery that uses captured CO2 as an electrolyte, and produces other products from it, like sodium carbonate, which has a wide range of industrial applications.
Redox flow batteries use chemical storage for storing large amounts of electricity from intermittent wind and solar power, and can use a range of elements for its electrolytes, including zinc or vanadium. But by using CO2 as a medium, and converting it through a chemical process into a marketable product, while at the same time providing electricity storage for wind or solar power, it could kill two birds with one stone. “It’s like, you want us to play in the energy storage sphere? That is what we do,” says Agora Energy founder and CEO Christina Gyenge. “You want to produce something out of CO2? Well, that’s what we do too. It’s two independent markets at the same time.”
As for hydrogen, B.C. companies are already leaders in the fuel cell space, although startups like Hydra Energy are now finding other uses in transportation, other than fuel cells. The company provides an injection system that displaces 40% of the diesel fuel used in trucks with hydrogen, reducing emissions by about 40%. It is currently trialing a project with a logging truck in B.C.
The company sources hydrogen from Chemtrade Logistics chemical plants in Prince George and North Vancouver that make sodium chlorate for bleaching pulp, with hydrogen being a by-product.
Hydra Energy CEO Jessica Verhagen says Class 8 trucks in return-to-base operations, like logging, is the market the company is currently targeting. Using Hydra Energy’s hydrogen-as-a-service model, fleet operators would pay the same price for hydrogen as they would diesel, but would pay lower carbon taxes, since they’d be buying less diesel.