8 minute read
MAINTENANCE
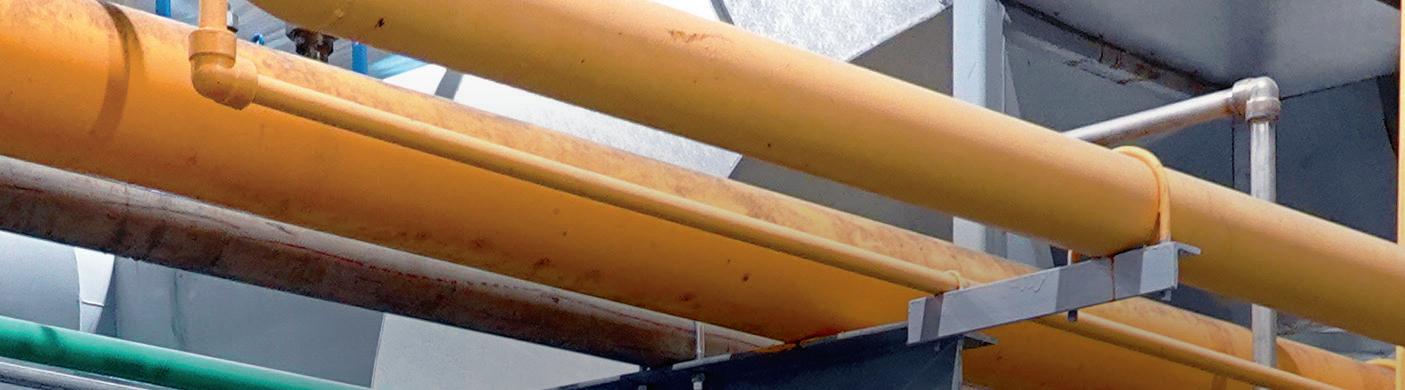
SHIFTING
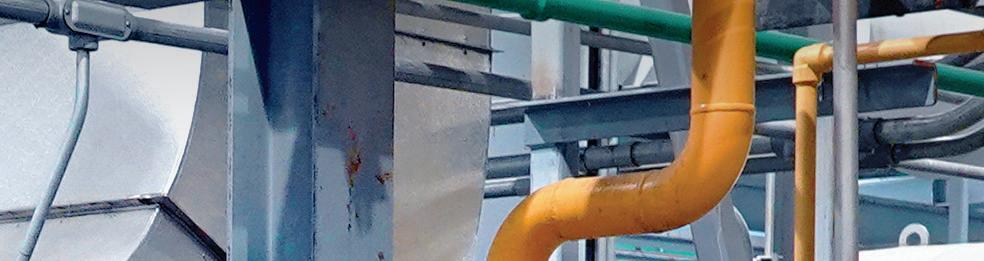
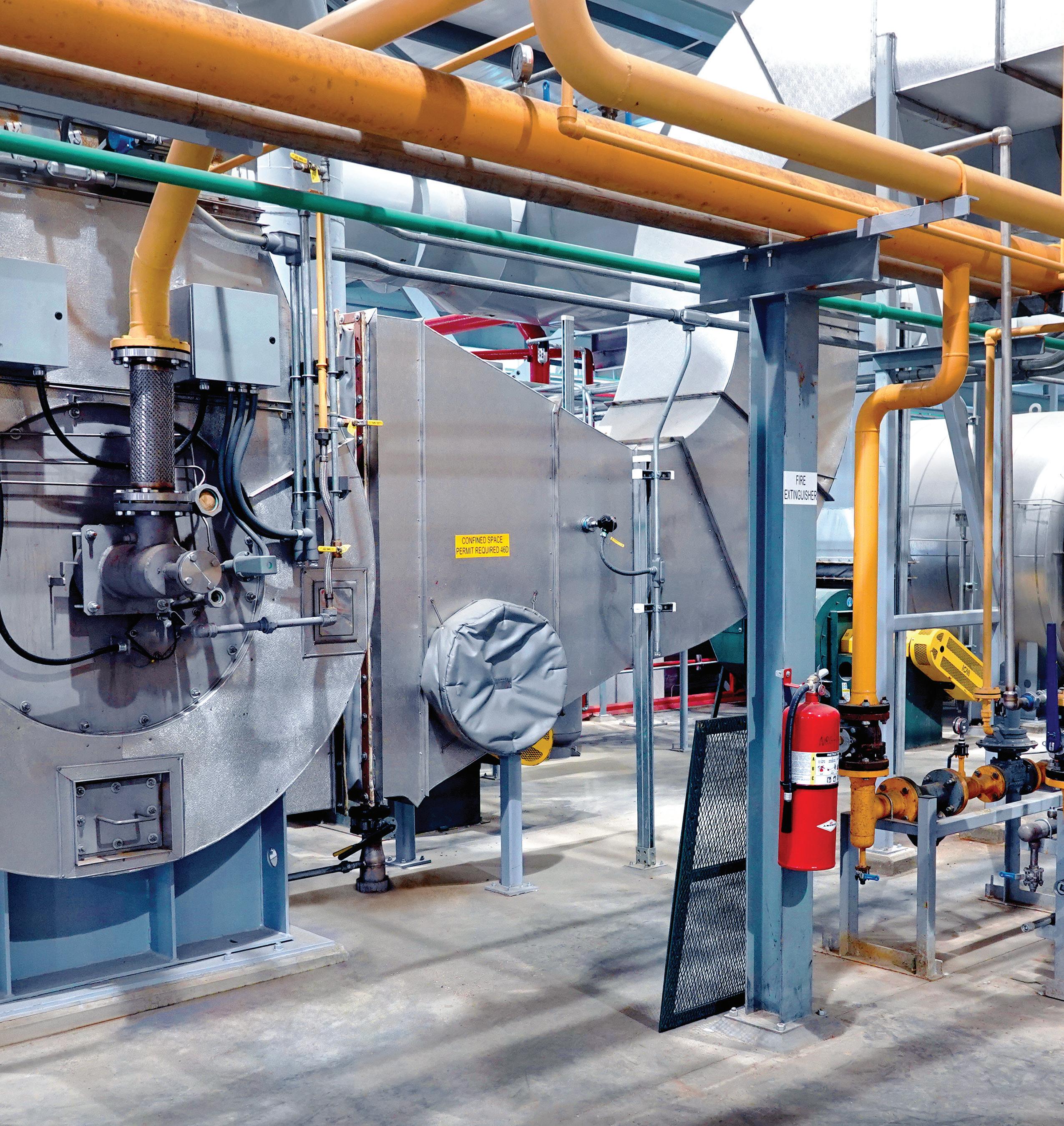

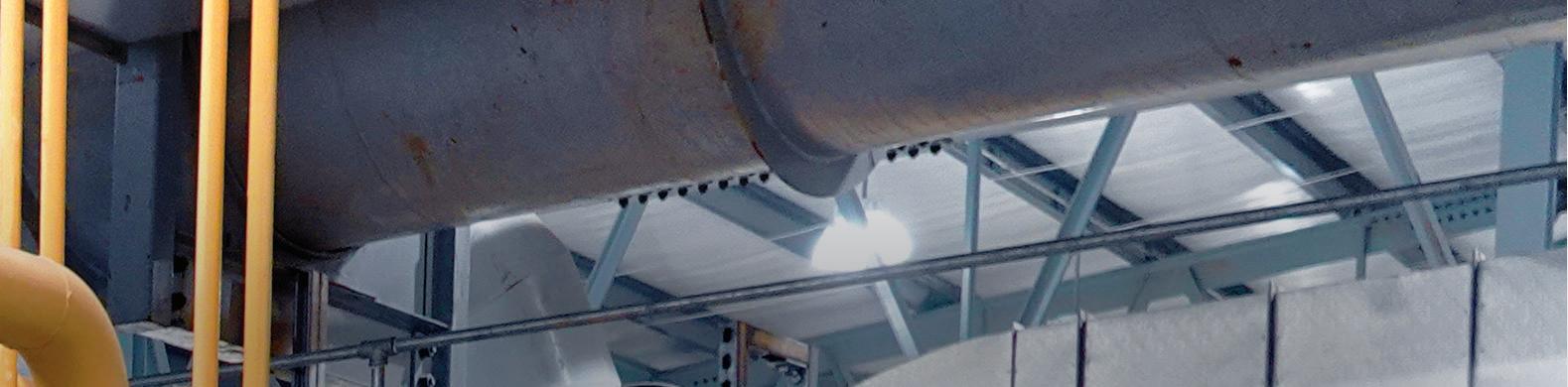
SHUTDOWNS
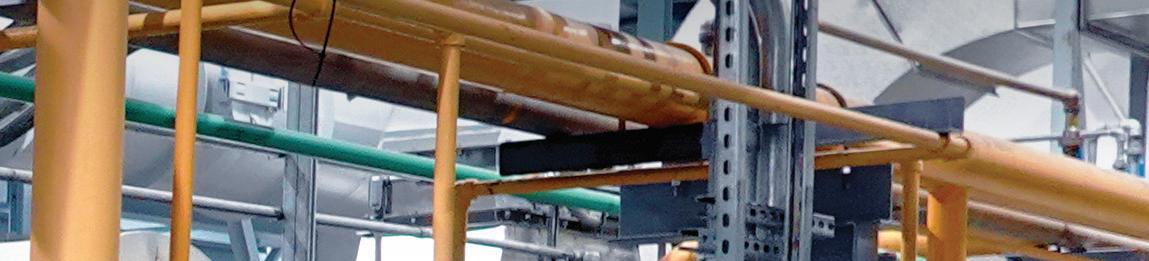
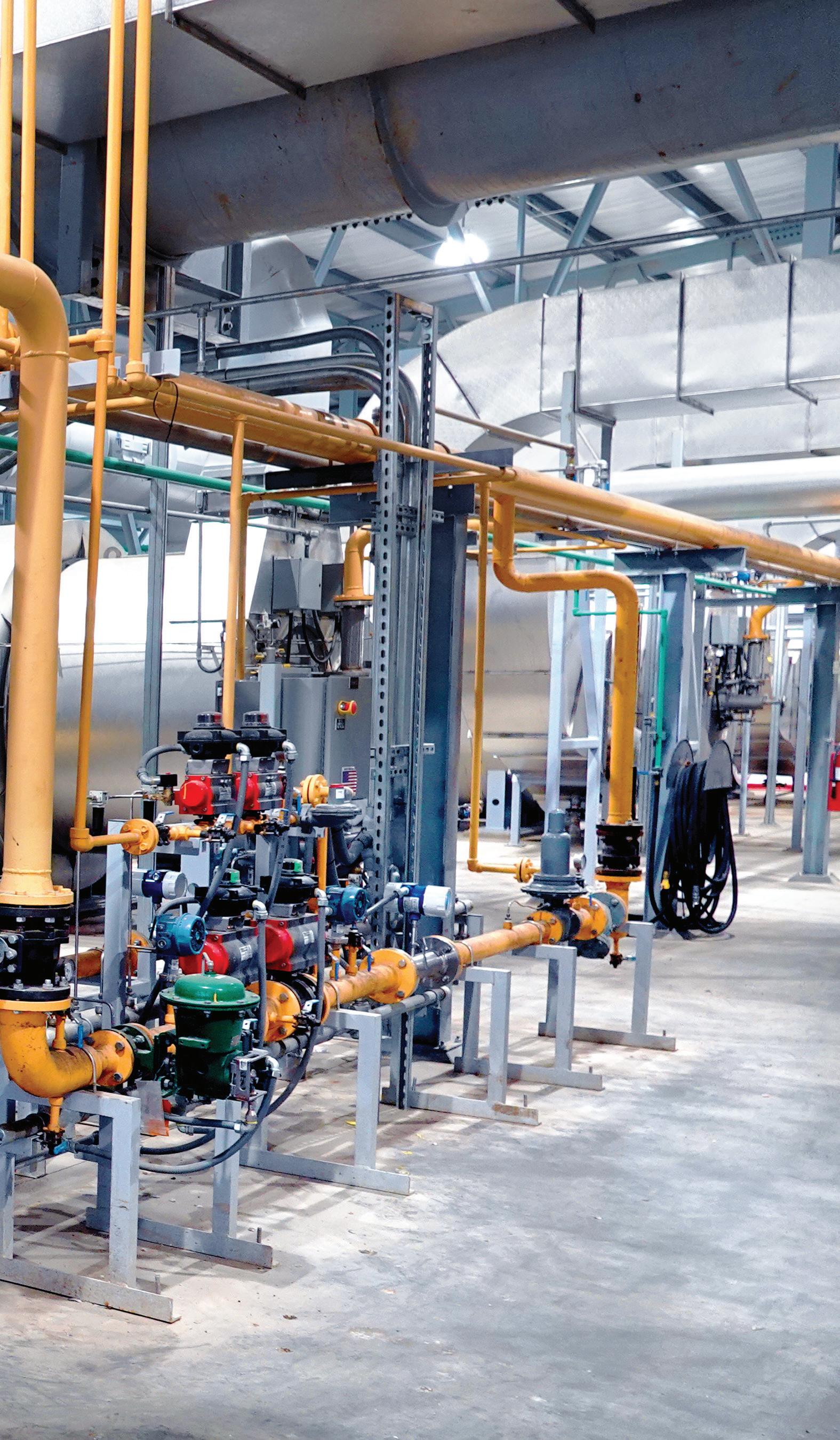
The pandemic in 2020 aff ected many aspects of ethanol production, including shutdown schedules. The updated, staggered timelines might remain in place, as plants and service providers evaluate their benefi ts.
By Lisa Gibson
Western Plains Energy in Oakley, Kansas, only implemented one of two planned shutdowns in 2020. COVID-19
concerns forced deviation from its traditional spring and fall shutdown schedule for cleaning and maintenance. Plant Manager Rick Holaday says it’s a course many ethanol plants found themselves taking during the pandemic.
“Before 2020 rolled around, I wouldn’t have had the guts to do one shutdown,” Holaday says. “It did help us a little bit because we were slowed down for the month of April and part of May. We weren’t pushing the plant as hard as we normally would, so we were fi ne with one.”
In a normal production year, just one shutdown would be a bit concerning, he says.
The strife in 2020, and even that of 2019, changed business for shutdown service providers and contractors performing the cleaning and maintenance, too. Moving
ELITE COMBUSTION: ICM Inc. off ers maintenance at ethanol plants across the Midwest, with experts spread out to off er “local” service to as many plants as possible. Pictured is combustion equipment at Elite Octane in Atlantic, Iowa.
PHOTO: ICM INC.
forward, some ethanol plants might opt to maintain those shifted timelines, or even stick to a reduced number of shutdowns as a cost-saving measure where applicable.
Trends in Timing
Ethanol plants commonly schedule their two annual shutdowns in the spring—April or May—and fall—October. “We aim for two days but plan for three,” Holaday says of shutdown length.
It all happens on the same schedule each time: Monday night, staff works to shut down the plant, emptying and draining, so it’s ready for contractors by 7 a.m. Tuesday. “It’s basically organized chaos,” Holaday says.
Then the contractors come in to hydroblast evaporators, replace pipelines and conduct any extra projects coinciding with the shutdown, such as tank floor replacements.
In 2020, the spring shutdown was delayed until July, and the fall shutdown wasn’t done. It wasn’t a budget crunch that adjusted the schedule, Holaday says, but concerns about having so many contractors on-site. And July in Kansas is not ideal, he adds, with temperatures soaring above 100 degrees Fahrenheit. This year, Western Plains is looking at April and August shutdowns, Holaday says.
While the July shutdown won’t stick, Western Plains has considered adjusting its shutdown schedule. It would help spread the work of contractors who service several ethanol plants during the common spring and fall shutdown schedules, Holaday says. “It’s not just for efficiency, but other plants use the same vendors. There is quite a bit of cooperation between us and our marketing department and local contractors to be able to stagger it enough.”
ICM Inc.’s James Weber, manager, reliability services, and Kirsten Gordon, director, aftermarket services, saw the shift in shutdown scheduling during 2020, as well. “A lot of these plants stuck to the fall and spring,” Weber says. “It was engrained in them that they had to shut down in the fall and they had to shut down in the spring. We did a lot more work in the summer months (in 2020) than what we normally do and we’re seeing a lot more this winter.” Whether the new schedule stays in place is yet to be determined, he adds.
ICM provides maintenance services including internal tank repairs, conveyor work and dryer inspections and repairs. Gordon says 2020 was overall a bit slower because of tighter margins, but Weber adds ICM primarily stuck with its main services. The work at plants, however, differed, many opting for little projects versus larger shutdowns, he says.
With extra maintenance in place for vulnerable equipment like evaporators, some plants might even explore one shutdown per year, amounting to a significant
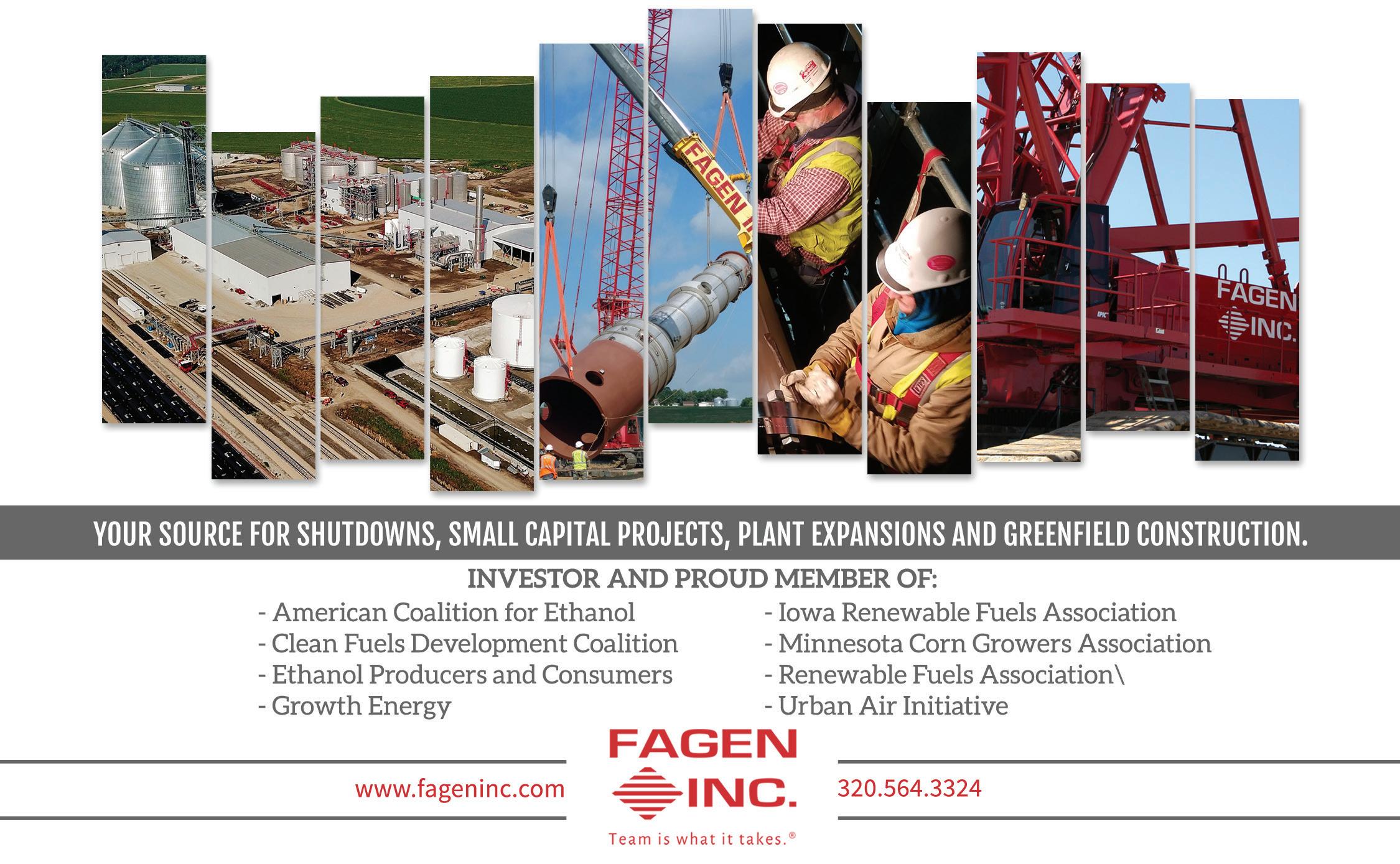
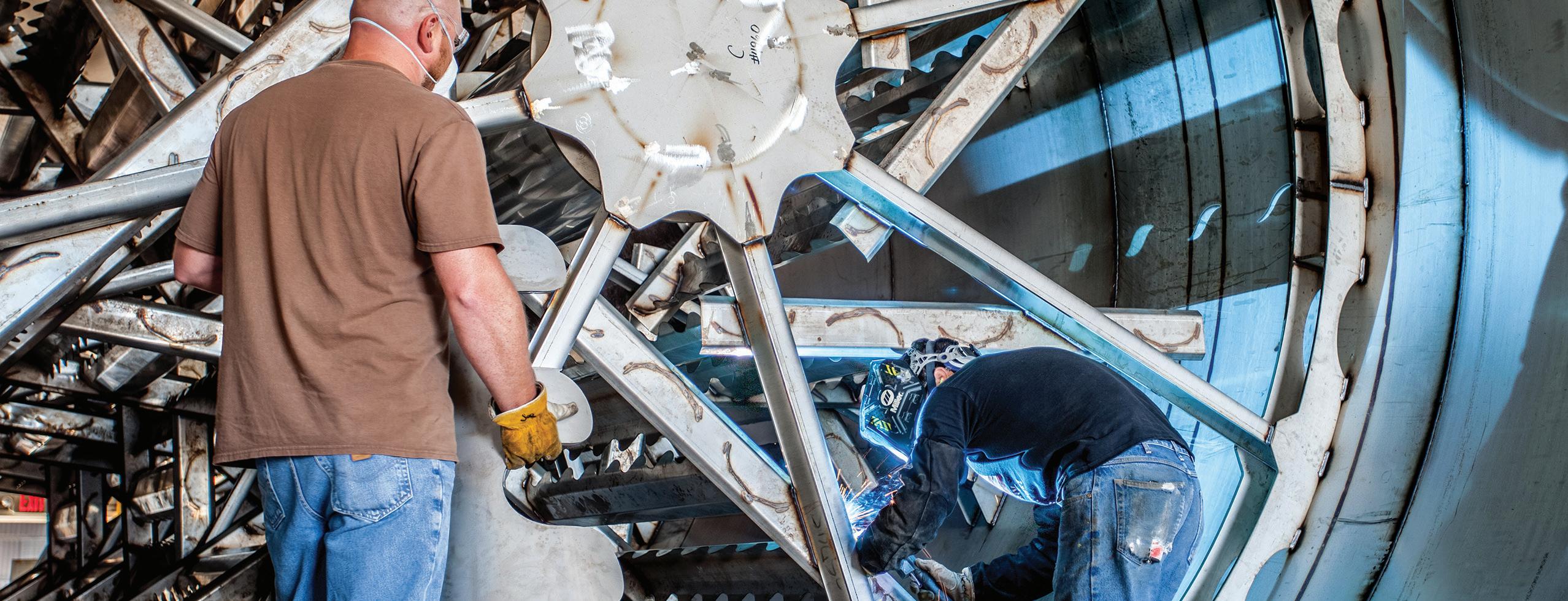
DRYER DOUBLE: ICM staff conduct dryer maintenance during a planned ethanol plant shutdown.
PHOTO: ICM INC.
cost savings. Western Plains pays about $65,000 to contractors per shutdown.
But when Western Plains is at full capacity, “Two is better than one,” Holaday says.
A Shift in Services
Midwest Ironworks in Horace, North Dakota, provides shutdown services to ethanol plants, including tie-ins for future projects, regenerative thermal oxidizer maintenance, pump alignments, gear box rebuilds and removal of relief valves to prepare for another party to rebuild and replace them. “The part that we’re involved with usually involves piping disconnects,” says Ryan Haugo, president of Midwest Ironworks. “Then we come back after the shutdown to help button it all back up.”
Haugo says most of Midwest Ironworks’ ethanol clients plan for four- or five-day shutdowns, “From shutting the boiler down to warming the boiler back up.” He says his workload decreased a bit in 2020, as plants with tight margins did their own shutdowns, in lieu of hiring
ETHANOL PRODUCER_HALF PG AD_ESSENTIAL_FAST TRACK_AFTERMARKET_FIELD SERVICES_01-21-2021.pdf 1 1/21/2021 12:50:38 PM
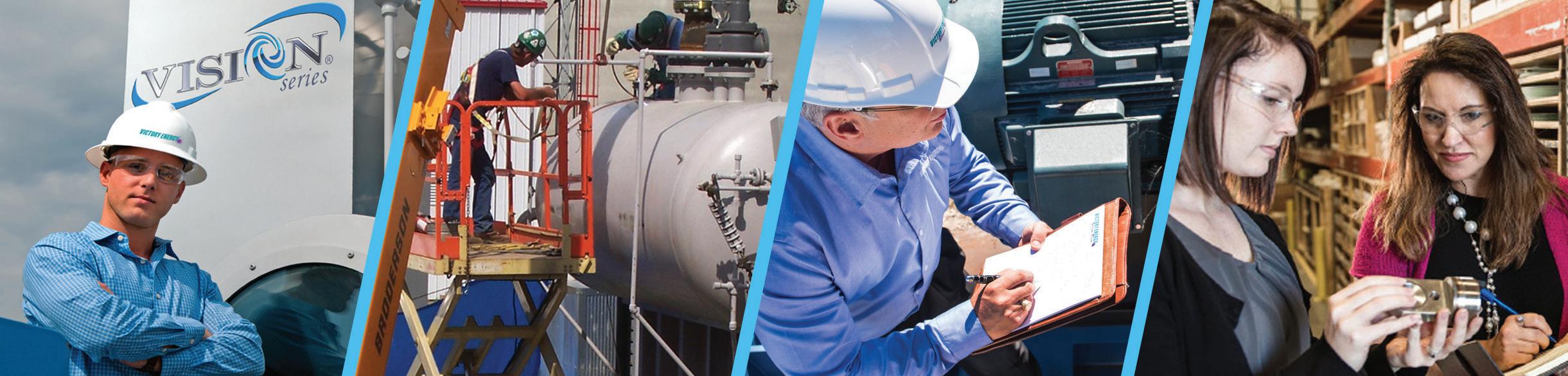
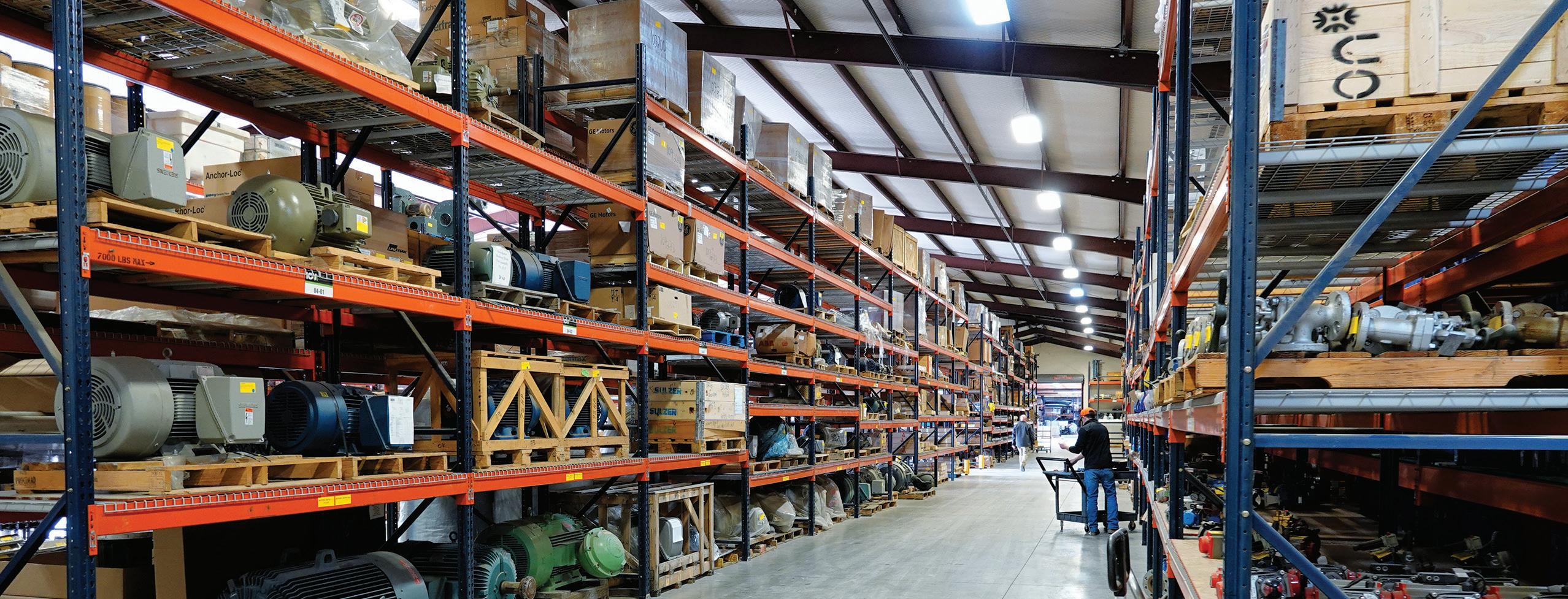
SPARE STOCK: ICM’s warehouse is stocked with more than $1 million of critical spare parts.
PHOTO: ICM INC.
help. Some plants he works with already do just one shutdown per year, normally in the spring.
Into 2021, Haugo expects a return to the normal spring and fall schedule, but he has updated his offerings to accommodate one more major trend from 2020. “We’re seeing a shift where a lot of the plants are trying to spend some capital money on producing higher-grade alcohol. So we’re getting involved on the front end of a couple of those projects right now.” Midwest Ironworks will be the general contractor on one such project in Illinois, adding a couple more evaporators and other equipment for the new coproduct, headed for food and pharma markets.
The new service added to Midwest Ironworks’ portfolio will open new doors, Haugo says. “We would sub out some of the facets of the project, and the tasks we normally do we would still perform.”
While a few plants are working with Midwest Ironworks to evaluate production of higher-grade alcohol, the Illinois project is the first where Haugo’s team is “boots on the ground,” he says.
“And it’s great for the plants. If they have the capital to spend on it, now is the time to spend it because margins are low and downtime doesn’t hurt you as much. Once they can produce it, their margins are much better.”
Trust in Timelines
“The biggest part is they want someone they trust has enough staff and the hours to get it done,” Haugo says of providing shutdown services. “The biggest problem is contractors going past startup time. It’s a big issue.”
Trustworthiness goes a long way, Weber and Gordon agree. “The big difference in using someone like us and using a local re-
Interstates
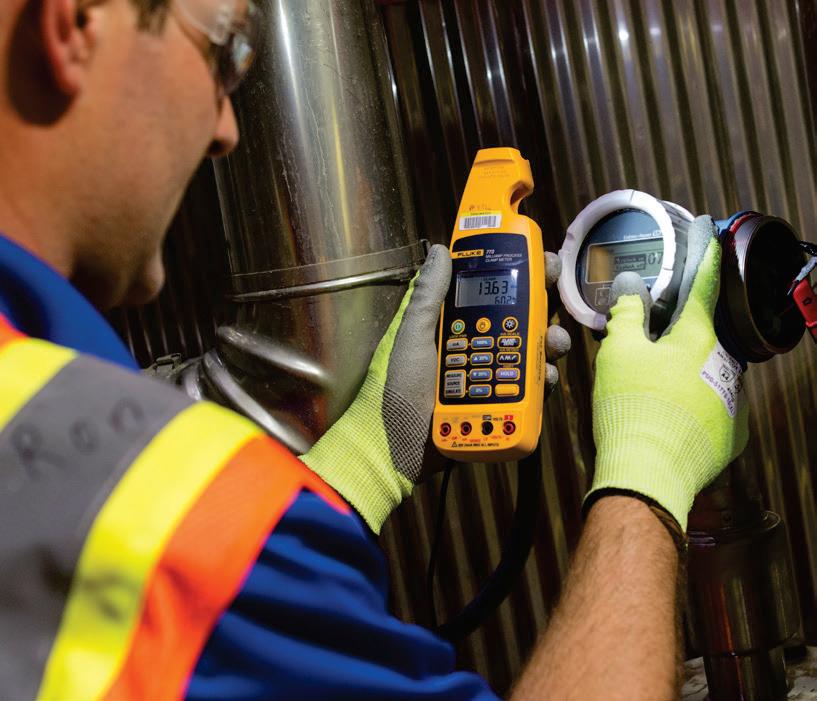
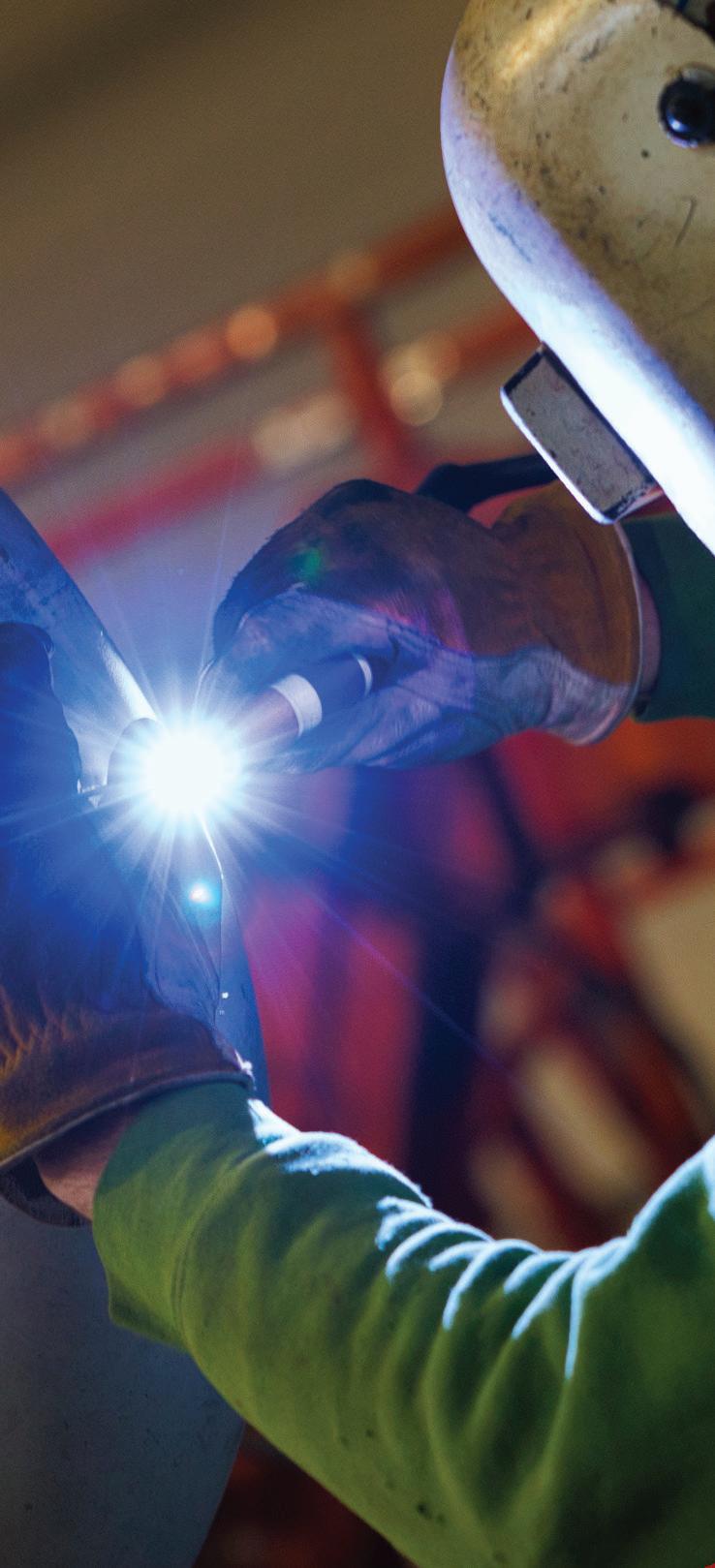
LIGHT REPAIRS: Piping work constitutes a large portion of the shutdown services provided by Midwest Ironworks in Horace, North Dakota.
PHOTO: MIDWEST IRONWORKS
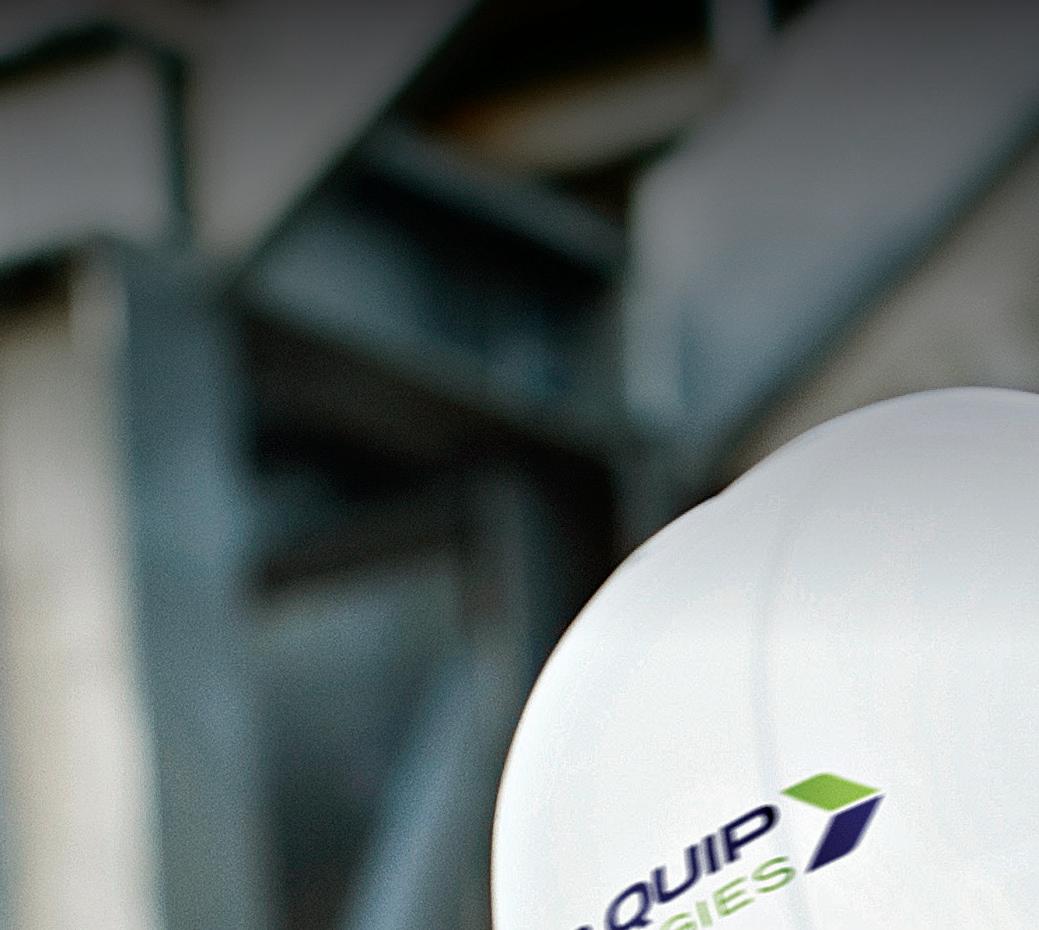
pair shop is the local repair shop might only work in two ethanol plants in their local area,” Weber says. “We work in 60, 70 plants a year. So we see a lot more, we hear a lot more and, overall, we have a lot more tribal knowledge.”
Many plants opt for local contractors to avoid mobilization costs. “We try to use local because we’re out here in the middle of nowhere, so we save a little bit of money,” Holaday says. “It really depends on expertise. So we’ll go for the group that has the most experience doing some of these projects.”
Luckily, Holaday adds, Western Plains has a nearby ICM location and taps its expertise for projects. ICM has service providers spread throughout the Midwest to avoid mobilization costs, Weber says.
Even so, the trust in experience of a longtime provider can offset any mobilization costs, Gordon says. ICM’s experts often detect needs during their pre-shutdown inspections that plant managers were unware of.
“We’re using our senses: What do we hear, what do we see? Are there things we’ve seen at other plants that we can suggest they do? Are we hearing a knocking noise when we walk by a conveyor?” Gordon says. “All of those things help us help the plant develop what the scope of the shutdown needs to be.” ICM’s experts will also ensure the plant has the right parts to complete all shutdown maintenance and projects on the timeframe they’ve slotted, she adds.
“Every inspection that we go in and do, we find stuff that is going to need repair that they did not notice or didn’t find,” Weber says. “The guys that are going out and doing inspections have been working in these plants for a long, long time. They pick up on things.”
Gordon adds, “We’re always trying to provide additional knowledge.”
The experts providing that additional knowledge learn on the job, he adds, starting out “turning wrenches” to become familiar with ethanol plants before performing inspections.
Haugo, Weber and Gordon will continue to provide their teams’ expertise, whether it’s reduced to once per year per plant, or on a more staggered schedule. A continuation of 2020’s spread-out work schedule “would make everyone’s life easier,” Gordon says.
Author: Lisa Gibson Editor, Ethanol Producer Magazine 701.738.4920 lgibson@bbiinternational.com
VALUE IS...
THE GUARANTEE BEHIND THE TECHNOLOGY.
For 25 years, the Fluid Quip Technologies team has continuously developed and created Value for our customers.
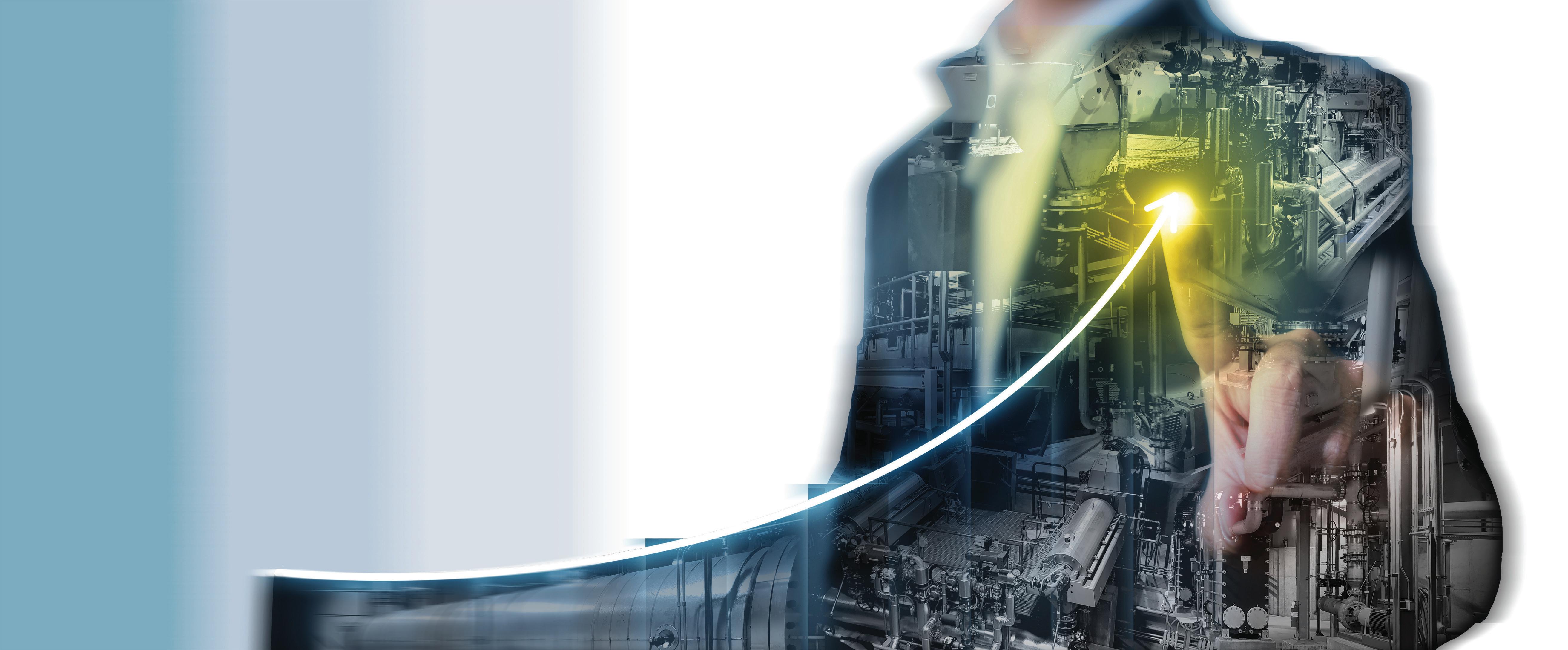