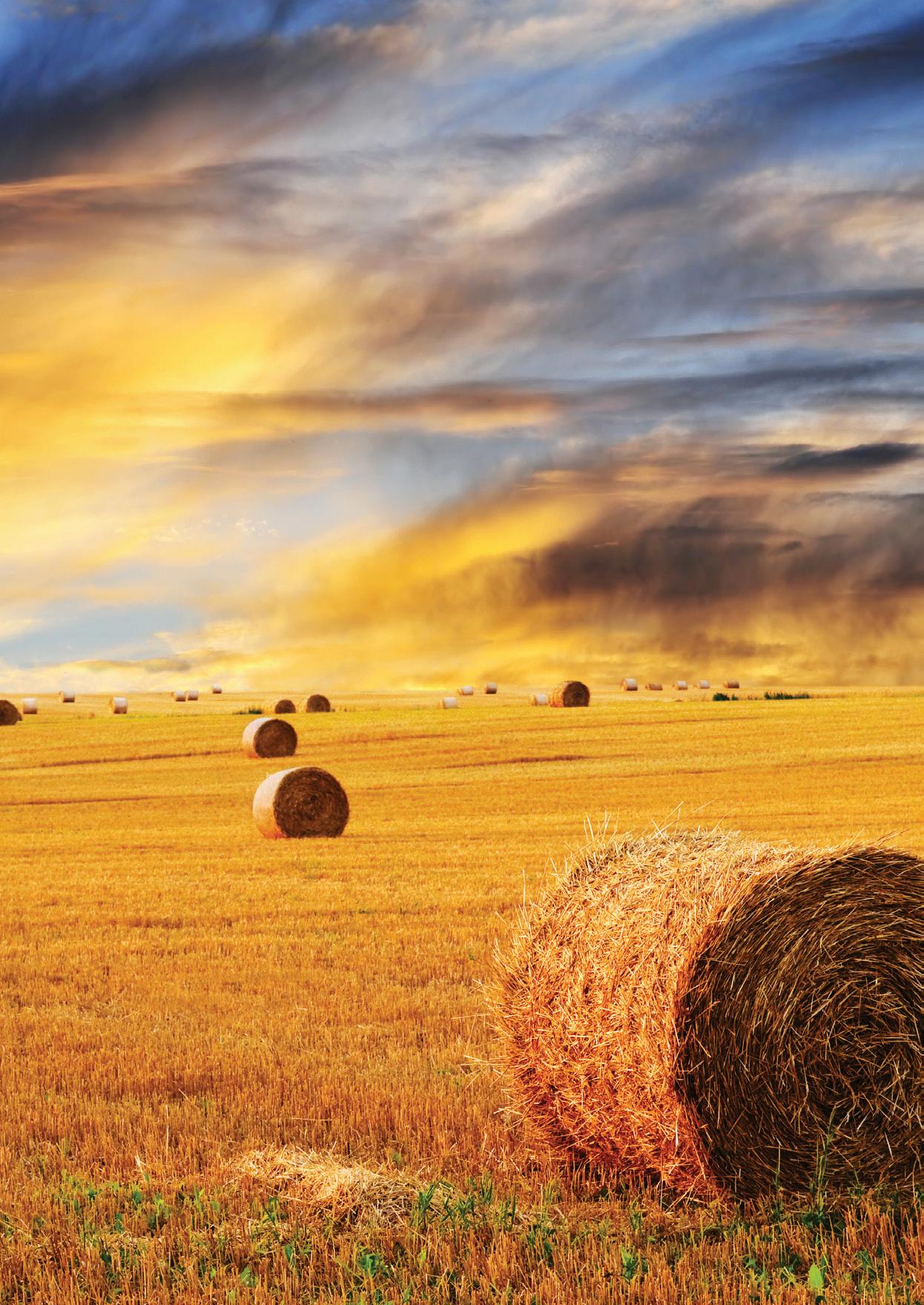
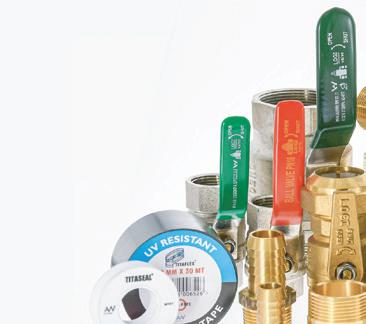
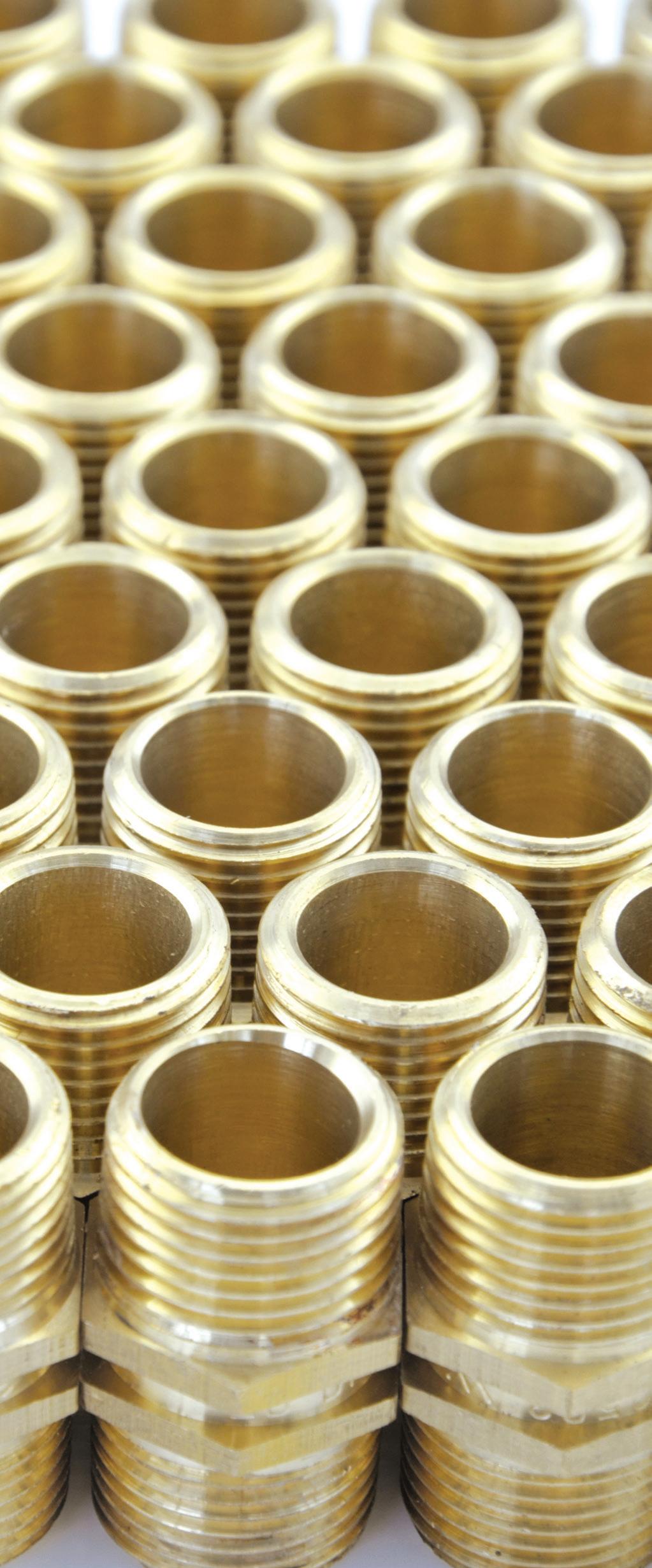
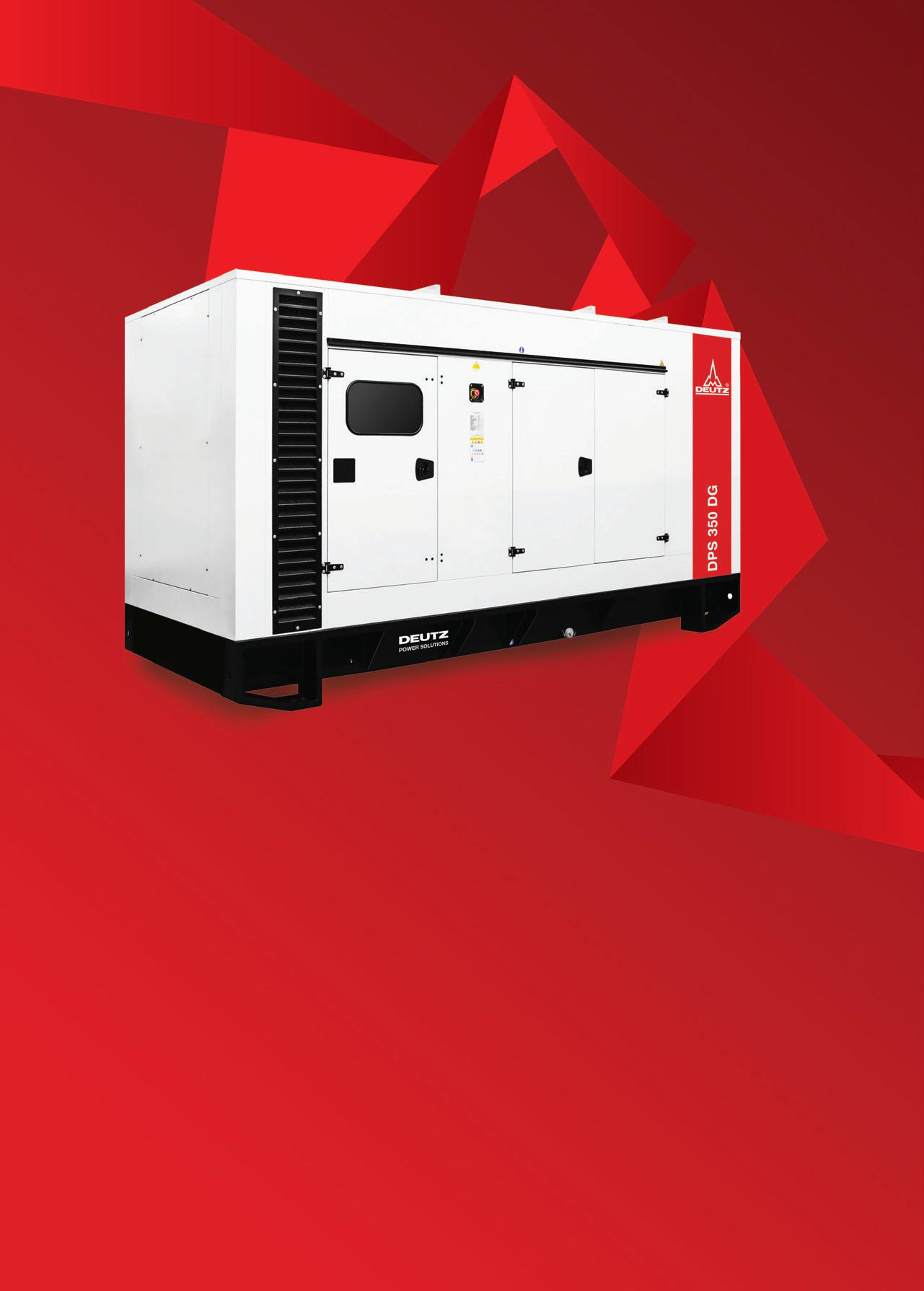
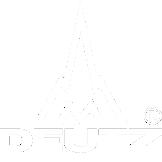
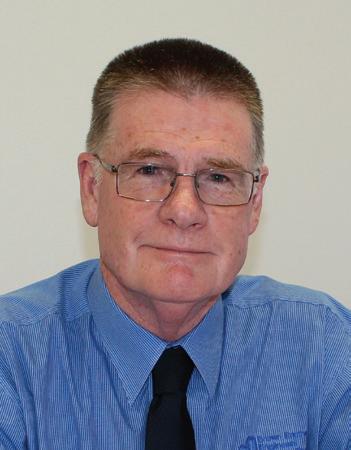
HPump Industry Australia Incorporated C/-340, Stuarts Point Road Yarrahapinni NSW 2441 Australia Ph/Fax: (02) 6569 0160 pumpsaustralia@bigpond.com www.pumps.org.au
PIA Executive Council 2020
John Inkster – President Brown Brothers Engineers
James Blannin – Vice President Stevco Pumps & Seals
Kevin Wilson – Treasurer/Secretary Executive Officer
Alan Rowan – Councillor Executive Officer – Publications and Training, Life Member
Ken Kugler Executive Officer – Standards, Life Member
Louise Black – Councillor Envirotech Water Solutions
Geoff Harvey – Councillor Irrigation Australia Limited
Joel Neideck – Councillor TDA Pumps
Mike Bauer – Councillor DynaPumps
Steve Bosner – Councillor Pioneer Pumps
Hem Prakash – Councillor Davey Water Products
Anant Yuvarajah – Councillor ASC Water Tanks
ello all and welcome to this Spring edition of Pump Industry Magazine. In the Winter edition, I commented on how we had seen an enormous amount of change in 2020 and, unfortunately, the words that come to mind now are tumultuous change. Instead of seeing an easing of COVID-19, we’ve seen a dramatic surge in new cases centred around Melbourne – tragically in aged care homes – a continued lockdown of our borders, an inevitable increase in unemployment, a slower recovery and economic uncertainty. Much is dependent on the length of Victoria’s restrictions and whether we’ll see continued restrictions imposed by other states, and the federal response now totalling more than $314 billion – over 15 per cent of GDP.
As the Victorian Government declared a State of Disaster and imposed a Stage 4 lockdown, PIA was able to share with members the State Government’s releases relating to Permitted Work Premises via our weekly newsletter and website. Fortunately for our industry, most Members would have been able to demonstrate a link to agriculture, fishing, mining, food and beverage, pharmaceutical, water supply and sewage to name a few, and carry on business as a permitted industry.
Since the Autumn edition, aside from endeavouring to keep Members informed about COVID-19 restrictions on business, PIA Council has been busy in other areas. On 4 August, a new revamped website was released with a fresh new logo, a Flow Technology Virtual Conference was held on 12 June with over 200 attendees, and later in the month Council held its first ever Pumps & Systems Training Course, held over three days from 23-25 June. The course was very successful with 14 attendees. On completion of the one-day practical, attendees will receive a Statement of Attainment – a Nationally Recognised Accreditation. Our thanks go to IAL, under whose umbrella as an RTO the course was run, and to Geoff Harvey, who brought it all together, and to the two trainers John Harvie and Ashley White. The response from participants was very encouraging, giving Council the stimulus to hold another course later in the year. Council has also reviewed the Annual Subscription amount for Category A
businesses employing more than 100 people from $1,500 to $750 inclusive of GST, keeping it in line with those businesses employing 25 or more people. It’s hoped this may make it more attractive for the larger companies to renew or retain their membership, as it is important that we have representation across the industry. On a pleasing note, we have seen an upswing in new Members with membership now standing at 98, with 94 per cent being financial.
I failed to mention previously that Australian Pipe Friction Handbook – 5th Edition (PFH) is now available. The layout of the handbook is the same as previous editions with the book split into two sections: the first covering friction tables, and the second covering how to calculate friction losses in a wide range of pipe fittings, valves etc. The PFH is a comprehensive, easy-touse resource and remains very popular amongst engineers and designers. The Handbook is available for purchase from the PIA website, www.pumps.org.au/ publications. Thanks to Alan Rowan for his work here.
Our Standards EO, Ken Kugler, has also been busy with activities on various Standards Committees – too numerous to include in detail here, but including FP008 Fire Pump Committee, ME-030 Pump Committee, EL-58 Energy Efficiency for Swimming Pool Pumps and the Australian Government’s E3 Energy Efficiency Equipment Working Group. A detailed account of these activities was included in our regular weekly newsletter.
These are challenging times for all and I trust the information posted by PIA has been helpful to you and your business as COVID-19 continues to invade our lives and test our resolve. The Melbourne lockdown is expected to lower GDP by 2ppt in Q3, weakening the outlook for the future amid predictions that we can expect another 90,000 fewer people employed by the end of September. There are also the physical and mental health issues to contend with.
One thing that would certainly improve expectations is news of a safe and broadly available vaccine. We can only hope that this comes sooner as opposed to later, maybe as early as Q2 next year.
John Inkster PresidentABN: 36 426 734 954 204/23–25 Gipps St
Collingwood VIC 3066
P: (03) 9988 4950
F: (03) 8456 6720
monkeymedia.com.au
info@monkeymedia.com.au pumpindustry.com.au magazine@pumpindustry.com.au
Editor: Lauren Cella
Assistant Editor: Eliza Booth
Business Development Manager: Rima Munafo
Design Manager: Alejandro Molano
Designer: Jacqueline Buckmaster
Publisher: Chris Bland
Managing Editor: Laura Harvey
ISSN: 2201-0270
Australian OEM Sterling Pumps completed a major business acquisition of specialised local oil and gas pump manufacturer United Pumps Australia – effective late June – expanding its product portfolio of reliable and high-quality pumps.
United Pumps Australia was founded in 1984, and is focused on developing and supplying a wide range of pumps for Australian and international specialised oil and gas projects, including API 610 rated centrifugal
pumps and systems. The company is based in the inner western suburbs of Melbourne and will continue to be managed by current management, now reporting to Sterling Pumps.
Anton Merry, Managing Director of Sterling Pumps, said the United Pumps acquisition is positive for Sterling Pumps and the group, contributing an extensive product portfolio of reliable and high-quality pumps for both the water, and oil and gas segments. United Pumps brings to the company
extensive technical and manufacturing capabilities, a large pump test facility and enhanced market knowledge.
The company will continue to operate both production facilities in Pakenham and Sunshine, with each plant having comprehensive testing capabilities and industry-leading people to allow United Pumps to continue to focus on the specialised oil and gas markets, while Sterling Pumps continues its expansion into the water focused rural/irrigation, fire protection and mining markets.
AVAILABLE IN PRESSURES FROM 200 BAR TO 3000 BAR
Waterjet cutting is a process of precision cutting that utilises high pressure water.
We can process a wide array of materials. Heavy gauge plate, thin sheet stock and composite materials (i.e. carbon fibre, phenolics etc.). It is not uncommon for 6+ inch aluminium and titanium to be cut on waterjets to near final shapes. Edge quality of the parts can vary depending on customer requirements.
We can process anything from a very rough cut for hog-outs, to a very fine edge for precision, finished parts:
Cut up to 6 m x 3 m (20 ft x 10 ft)
Thickness up to 254 mm (10 in)
Improved yield and less waste material
Supplied close to net shape reducing customer machine time
Shorter lead times
Zero heat effected zone
Processing of customer supplied materials
North East Water has chosen its preferred contractor to deliver a major upgrade to a pumping station in Wodonga to future-proof the city’s water supply system.
CCB Envico has been awarded the contract for the upgrade and will use local companies throughout the project, meaning a large portion of North East Water investment will stay within the region.
North East Water has invested $5 million into the station, which draws water from Wodonga Creek and pumps it to the water treatment plant at Huon Hill.
Some of the existing infrastructure was installed as far back as the 1960s, and North East Water has engineered the new upgrade to serve a growing Wodonga for decades to come.
The refurbishment is underway to support the predicted growth of the area over the next 40 years, and will include several new pumps along with upgrades to electrical and security systems.
It will allow larger volumes of water to be pumped to the treatment plant more efficiently, helping to reduce the utility’s carbon footprint.
The new pumps will transfer 1,000L per second on peak days, with capacity for higher flows as the community grows.
North East Water Senior Project Engineer, Dean Jones, said real-time
monitoring of water flow rates and power consumption would also lead to greater energy efficiencies and cost savings.
“The project includes a permanent on-site generator that will give greater security to the city’s water supply during power failures,” Mr Jones said.
The construction work is expected to be completed over the next 12 months.
The key to successful, hassle free sump pumping is to eliminate priming issues.
Which is exactly how our ‘V’ Series Vertical shaft column pump works. Unlike a surface mounted unit, the ‘V’ Series is always primed as it’s submerged in the liquid, avoiding the need and expense of a suction line or foot valve and the NPSH restrictions associated with surface mounted pumps.
Its space saving design minimizes or eliminates floor space required for installation with the motor out of the liquid for easy maintenance and monitoring.
With the ability to pump water, suspended solids or semi viscous products and be used in high temperature applications and explosive atmospheres, the ‘V’ Series is also very versatile.
Save time, money and space up top, with an ASM ‘V’ Series pump down below. For more information contact ASM Pumps on (03) 9793 7577 or visit asmpumps.com.au
Dreamworld’s parent company, Ardent Leisure, has pled guilty to failing to comply with its health and safety duty in the 2016 accident where a pump failure proved fatal for four people.
The independent Work Health and Safety Prosecutor, Aaron Guilfoyle, brought charges against Ardent Leisure on Wednesday 21 July 2020.
Mr Guilfoyle charged Ardent Leisure with three charges under s.32 of the Work Health and Safety Act 2011, for failing to comply with its health and safety duty under the Act and exposing individuals to a risk of serious injury or death.
It was alleged that Ardent Leisure failed to ensure:
• The provision and maintenance of safe plant and structures
• Provision and maintenance of safe systems of work
• The provision of information, training, instruction or supervision that was necessary to protect all persons from risks to their health and safety arising from work carried out as part of the conduct of the business or undertaking
Ardent Leisure has announced it will plead guilty to all three charges, which bear a maximum penalty of $4.5 million.
The matter has been scheduled for a hearing on 28 September 2020.
Coroner James McDougall delivered his 274-page inquest findings to the Brisbane Magistrates Court on 24 February 2020, which revealed that there was a “total” and “systemic failure by Dreamworld to ensure all aspects of safety”.
Mr McDougall found that unregulated “ad hoc” modifications to the Thunder River Rapids ride had not been properly assessed for safety by a qualified engineer. In fact, it was determined that the ride had not received any such assessment since its opening in 1986.
It was also found during the inquest that managers at Dreamworld had ignored previous incidents where there had been problems on the ride, including serious incidents where rafts had also flipped in 2001, 2004, 2005, 2008 and 2014.
Mr McDougall said that, based on these findings, it was only a matter of time before a fatal accident happened.
“That time happened on October 25 2016,” Mr McDougall said.
The cause of the accident was attributed to a water pump that had the ability to pump 4,000 litres per second, failing an,d therefore resulting in significant water loss.
The ride was designed to carry six-person circular rafts, simulating white water rafting.
When the water reached low levels due to the pump failure, a raft, which was travelling up a ramp with wooden slats, stalled.
This resulted in a second raft colliding with the first raft causing it to flip. Two children were flung free, but the four remaining adults died when the raft smashed onto the ramp.
Under a conveyor belt were two pumps, 'north and south' due to their positioning, operated by separate stop and start buttons on the main control panel.
Despite the ride operator’s hurried attempts to stop the ride, inadequate emergency features, including an overriding stop button, meant it did not happen until after the raft flipped.
The inquest also found that there was an absence of formal water markers in the trough where rafts were loaded and unloaded.
“Rather, operators were required to measure the water level by reference to a scum mark on the wall of the trough, which was made from years of the ride operating,” Mr McDougall said.
Mr McDougall said it was clear the failure of the south pump was to blame for the disaster, but that the lack of emergency safeguards was incomprehensible.
“It remains unknown and impossible to understand why the conveyor kept going if the water level dropped on the ride,”Mr McDougall said.
Duncan B Gilmore, an independent engineering expert from Gilmore Engineers, conducted a review and assessment of the ride.
“Having considered the design of the ride, Dr Gilmore notes that the ride is clearly dependent on an adequate water level,” the coroner’s findings state.
“When this drops, the rafts settle on the steel supporting rails and cannot travel through the watercourse, which includes at the end of the conveyor discharge point.
“This means that rafts can collide before a raft has cleared the conveyor.”
The coroner’s first recommendation of many was for reforms to Queensland’s regulatory framework with respect to the inspection of “major amusement park devices”, “given the circumstances of this tragic incident”.
Mr McDougall said that a major inspection or full risk assessment by a competent person at stipulated intervals must be completed, as suggested by the manufacturer or at a mandated duration.
After hearing the findings of the inquest in February, Ardent Leisure appointed a former Qantas safety executive, Geoff Sartori, as safety adviser to its board.
“We are well progressed on the way to global best practice,” Ardent Leisure Chairman, Gary Weiss, said.
“We want to ensure a tragedy like this never happens again.”
Barrister Bruce Hodgkinson, who appeared for Ardent Leisure at Southport Magistrates Court on Wednesday 29 July said the company would comply with the court’s orders.
SANDPIPER Air Operated Double Diaphragm Pumps
• Capacity: To 1,147 L/min
• Pressure: To 8.6 bar
• Temperature: To 177°C
• Viscosities: To 25,000 cps
Applications
Chemical Processing, Mining, Paints, Food Processing, Industrial Maintenance, Electronics, Construction, Utilities
PULSAFEEDER Metering Pumps
• Capacity: To 8,676 L/min
• Pressure: To 350 bar
• Temperature: To 260°C
• Viscosities: To 25,000 cps
Applications
Water and Wastewater Treatment, Chemical Processing, Hydrocarbon Processing, Food Processing
ALBIN Peristaltic / Hose Pumps
• Capacity: To 155m³/hr
• Pressure: To 15 bar
• Temperature: To 50°C
• Viscosities: To 100,000 cps
Applications
Mining, Thickener Underflow, Pulp and Paper, Filter Press, Brewery, Water Treatment, Quarry, Grout, Concrete, Waste Liquids
LOWARA Single & Multistage Centrifugal Pumps
• Capacity: To 200m³/hr
• Pressure: To 40 bar
• Temperature: To 150°C
• Viscosities: To 500,000 cps
Applications
Pressure Boosting, Industrial Washing, Water Supply, Water Conditioning, Demineralised Water, Glycol, Boiler Feed, Multi-pump, Pressure Sprinkler Systems
range today.
TasWater’s largest water treatment plant upgrade is gaining momentum, with the next phase of works underway at the Bryn Estyn Water Treatment Plant (WTP).
The upgrade has been designed to bolster water supply security for Hobart residents and those in surrounding suburbs.
Ian Penman, Alliance Program Manager for the TasWater Capital Delivery Office, said it’s great to see the Bryn Estyn WTP upgrade taking shape.
“Significant initial works are underway in preparation for the main construction activities including making internal roadways, parking, laydown areas and site facilities,” Mr Penman said.
“Hazell Bros Group is carrying out the site preparation earthworks for the project, just one of a number of local contractors employed on-site, demonstrating our commitment to provide work for Tasmanian companies.”
Consultants Pitt & Sherry has worked with KMR Drilling to establish bores to monitor groundwater levels, and this will inform the placement of pipework and tanks.
Additionally, Tasmanian contractors Spectran Group, Rogerson and Birch Surveyors, Cranes Combined Hobart, Howrah Plumbing, UDM Group, and Southern Allsorts Electrical, have been engaged to conduct a variety of site investigations and preparation works.
The Bryn Estyn upgrade, with an estimated investment of around $200 million, is the largest single infrastructure project undertaken by TasWater.
“The redevelopment of Bryn Estyn is a crucial project that will ensure TasWater can continue to provide its customers with safe and reliable drinking water for decades to come,” Mr Penman said.
“Importantly, at a time when the community and the economy is struggling due to COVID-19 impacts, Tasmanian contractors will continue to be deeply involved with us in this major investment.”
The Bryn Estyn WTP is scheduled for completion in 2023.
At Brown Brothers Engineers we have expanded our capabilities with two more quality pump manufacturers. In addition to the current world leading brands we can now offer the following range:
WELCOME TO THE BIG END OF TOWN.
VERTICAL TURBINE PUMPS
Layne Bowler vertical turbine pumps have a proven record under the most demanding and toughest of conditions.
• Flows to 2,300 L/Sec
• Heads to 350 m
• Power to 1000+ kW
• Temperatures to 150°C
• Bowls Diameter up to 45 inch
Call us today to
When high head and high flows are required look no further than this quality Italian made range.
• Flows to 5000m³/h
• Head to 220m
• Pumps that exceed EN733 (DIN 24255 standard)
pumping solution.
Rexnord Elastomeric Couplings have been an industry benchmark for over 40 years.
Ideal for the Pump Industry — Rexnord® Elastomeric Omega®, and Wrapflex Couplings are non-lubricated, material flexing couplings. These products have excellent vibration dampening capability and high misalignment capacity, providing extended life to connected equipment, making them ideal for the demanding pump industry.
Reduce Maintenance Costs and Downtime — Designed for quick replacement, Rexnord elastomeric elements can be installed without moving the driving or driven equipment from their mounted locations or removing the hubs.
Designed for Specific Applications — Each of the elastomer coupling designs feature attributes that meet unique customer needs. The Wrapflex Coupling incorporates a patented hub design to reduce operating thrusts on seals and bearings and the Omega Coupling is available in the HSU model designed specifically for hot and humid applications.
Contact Rexnord today to see which coupling is right for your application. sales.australia@rexnord.com or Tel 02 4677 6000
As part of its emergency drought response for regional areas, the New South Wales Government has invested almost $57 million in critical water infrastructure projects for Orange, Bathurst and Condobolin.
NSW Water Minister, Melinda Pavey, said the three water security projects will receive an additional $33 million –building on the $24.5 million announced in 2019.
“While the drought has eased in some areas, many towns continue to be at risk of water shortages or have already been living on severe water restrictions,” Mrs Pavey said.
“Despite recent rainfall, water supplies for communities in the Central West region continue to be at risk and this funding is crucial to ensuring their long-term water security.”
Member for Bathurst, Paul Toole, said the projects would diversify water supply options and improve long-term water security.
“In Bathurst, the investment will kick start the implementation of a stormwater harvesting system and replace the existing pipeline from Winburndale Dam to the Bathurst Water Treatment Plant,” Mr Toole said.
“The new pipeline from Winburndale Dam will allow access to water from the dam so it can be used to supplement drinking water supplies.”
NSW Nationals Upper House MP, Sam Farraway, said sustaining town water supply was critical to the maintenance of businesses and community viability, particularly during these challenging times.
“The investment will mean two critical projects will begin in Orange: a pipeline from Spring Creek Dam to the Icely Road
Treatment Plant, and the Blackmans Swamp stormwater harvesting project,” Mr Farraway said.
“And Condobolin will be able to complete and connect a series of groundwater bores to the town’s water supply, and construct a pipeline to connect these groundwater bores to the Condobolin water supply.”
Since 2017, the NSW Government has invested more than $275 million for critical drought infrastructure projects and town water carting for regional NSW.
The NSW Department of Planning, Industry and Environment will partner with Orange City Council, Bathurst City Council and Lachlan Shire Council to continue the work already underway on all projects.
“The government has moved quickly and decisively to assist regional NSW during the drought and the COVID-19 crisis,” Mrs Pavey said.
“These projects are drought response projects, but they will create permanent infrastructure that will improve the resilience of the central west for the years ahead and support its communities and economies.”
Smart Conveying Technology (SCT) provides quick maintenance, significantly reduced life cycle costs and the shortest downtime. Smart Seal Housing, the newest innovation for SCT pumps, removes the need to dismantle the suction or discharge pipework for inspection and replacement of the mechanical seal.
Adjustable stator restores pump efficiency
Reduced maintenance time by up to 85%
Increased energy savings compared to conventional progressive cavity pumps
Easy retrofit onto your existing SEEPEX pumps
Up to 200% longer stator life
Rapid removal and reassembly of mechanical seal
Anew consultancy company has been appointed to fast-track final planning for the Granite Belt Irrigation Project (GBIP).
National engineering consultancy Premise will oversee obtaining final permits and construction tenders for the Emu Swamp Dam, marking a serious commitment of resources on GBIP’s behalf to expediting the project.
GBIP will deliver the 12,000ML dam at Emu Swamp, south-west of Stanthorpe, and 117km of pipeline to provide water to 51 agribusiness customers and bring wide-reaching benefits to the region.
Core pre-construction activities include confirming contracts to purchase water with irrigators, which will confirm where water needs to be delivered; commencing negotiations with landholders to access or acquire land along the pipeline route; detailed planning and tendering to accurately cost the project; and obtaining approvals necessary to enable construction.
Tenders to construct the dam and provide the pipeline infrastructure will be released in coming months.
When operational, the GBIP is expected to create 250 jobs during construction, and 700 new full-time agriculture and supporting jobs in the region which will boost the well-being of the local community.
Granite Belt Water CEO, Lloyd Taylor, said the appointment is a major step needed to move through the permit stage, and then onto construction contracting.
“A vast amount of work has been done since GBIP planning began in 2007, and we’re working as quickly and as diligently as possible to allow our Board and governments to make a final decision on this desperately-needed water project,” Mr Taylor said.
“The work to be completed by Premise puts serious horsepower behind the final steps needed to draw all this information together to obtain necessary government permits and approvals, and to prepare tenders for construction of the dam and pipeline.
“A decision to begin construction is expected in early 2021, and this will be based in large part on the final permits and detailed budgets that will result from this engineering work in coming months.”
Premise Director, Patrick Brady, said the firm’s Toowoomba regional office will
deliver the project and draw on technical expertise from across the company.
“Premise has advanced skills in pipeline and irrigation works, and a deep understanding of the challenges associated with delivering infrastructure into regional areas,” Mr Brady said.
“We’re also proudly a regionally-based company with a strong focus on building the strength of local communities and, like for GBIP, it is highly important to us to support local people and businesses throughout this process and to build
the skills, capacity and prosperity of the region for the long term.”
The GBIP is funded by $23.4 million from local irrigators, the highest proportion of private investment in water infrastructure in Queensland’s history, in addition to $47 million from the Federal Government and a conditional commitment of $13.6 million from the Queensland Government.
The Queensland Government has released $6 million of its contribution to fund pre-construction activities.
The Western Australian Government is investing over $30 million to upgrade Rottnest Island’s infrastructure, including an overhaul to aging water supply pipework, pump stations and desalination plants.
The major water improvements will overhaul the island’s drinking water network which is under increased pressure from sustained visitor growth and increased business activity.
This includes replacing the aging pipework, upgrading pump stations and overhauling the desalination plant to shore up both drinking water supply and firefighting capacity.
The project is set to begin in late-2020, and will be completed by 2024.
Western Australian Tourism Minister, Paul Papalia, said, “These projects represent the biggest infrastructure investment Rottnest Island has ever seen.
“We have worked hard over the last three years to elevate Rottnest to the status of a true tourism icon for Western Australia, with the quokka selfie among our efforts to market the island paradise to the world.
“Attracting record visitor numbers is great for the state’s tourism industry, but it has put pressure on the island’s water supply.
“This investment will allow us to plan for future tourism growth and business activity. We are firmly focused on increasing accommodation, hospitality, experience and tour options on the island, while preserving its natural wonders.
“With this latest initiative, the McGowan Government has now invested almost $50 million towards Rottnest Island in major infrastructure projects alone.”
The investment will also include road upgrades, which will begin in late August and will see more than 10km of the island’s roads resurfaced with over 47,000sqm of dense-graded asphalt.
This will improve the road surface for cyclists and pedestrians, and increase the life-span of the road network.
Western Australian Transport Minister, Rita Saffioti, said, “This investment in the island’s roads will ensure safer, easier access for residents as well as improving the visitor experience for the 700,000-plus tourists visiting the island each year.
“There may be some disruption for visitors while works are ongoing – however long term they will help improve the amenity of the island.
“The installation of the aerodrome’s new weather broadcast system is so important for aircraft using the airstrip, improving aircraft safety, particularly between dusk and dawn.
“Currently, pilots have to call up on their mobiles to get the latest weather, but this new system means pilots can automatically be updated on weather conditions via radio, while they are in the air.”
The investment is in addition to the State Government’s $16.2 million funding over four years for maritime infrastructure upgrades at Rottnest Island, including reconstruction of the Fuel Jetty.
This brings the State Government’s infrastructure investment up to $47.2 million in the last three years, on top of recurrent capital funding.
Pump Industry Australia (PIA) is pleased to introduce the print and electronic 5th edition of its Australia Pipe Friction Handbook, bringing it up to date with the latest Australian standards for pipes and tubes that are commonly used in Australia, as well as additional corrections as required.
Containing a comprehensive manual of friction tables, calculated for pipe sizes and materials conforming to the latest Australian and international standards, it is an essential and invaluable technical resource for all engineers, designers, and users of pumps and fluid control systems.
The main changes for this edition are:
• The recalculation of the two ductile iron pipe table sets as the latest standard upgrade involved a change to many internal pipe diameters
• The addition of an extra page at the start of the commercial steel pipe tables which explains that they can be used – up 250mm N.B. – for stainless steel pipe as well as wrought steelpipe.
Quiet
Electric
Please note that these are the only tables in the handbook not to an Australian standard, they conform to ASME/ANSI B36:10M-2013 for wrought steel pipes and ASME/ANSI B36:19M-2013 for stainless steel pipes
The layout of the handbook is the same as the previous editions, with the book split into two sections – the first covering friction tables for the following pipes and tubes:
• Commercial steel and stainless pipe
• Large fabricated steel pipe
• Medium and heavy duty galvanised steel pipe
• Uncoated and cement lined ductile iron pipe
• Copper tube
• Brass tube
• Stainless steel tube
• Series 1 and 2 PVC pipe
• Polyethylene pipe
• Rural polyethylene pipe
• Aluminium irrigation tube
• Elastomeric rubber hose
• Concrete pipe
The second section covers how to calculate the friction loss in a wide range of pipe fittings, valves, etc., together with instructions on how to calculate a pump system total head using the tables in the first section and the fittings in section two. As well as the data on pipe fittings etc., this section has a range of tables that are useful for pump engineers.
The Australian Pipe Friction Handbook is a comprehensive, easy-to-use resource providing everything required to calculate friction losses for most commonly used pipes in Australia.
The revised and updated 5th edition of PIA’s Australian Pipe Friction Handbook is now available for purchase via the PIA website at www.pumps.org.au/publications
Remote monitoring of weather and system operation
Intelligent adaptive control system to eliminate spray drift
No clogging in high TDS waters and suitable for any pH water
Enquiries: gjc@gjc.com.au
10 Peekarra Street, Regency Park, SA 5010
Phone: 08 8118 6450 www.gjc.com.au
Trust your motor and pump protection to the experts. Littelfuse protection relays stand up to the harshest conditions and safeguard the most critical parts of your operation. Our field application experts will help you update your protection to extend the life of your equipment, mitigate arc-flash hazards, and reduce the risk of electric shock.
relays@fuseco.com.au www.fuseco.com.au
Ebara has rethought the hydraulic design used in multistage pumps. Utilising the latest in computational fluid dynamics and design, followed by rigorous testing, Ebara has developed a unique impeller design that offers solutions and value to the customer – the Shurricane.
The imbalance of forces acting on the front and rear shrouds of a conventional impeller results in axial thrust. This thrust load is compounding in multistage pumps, and has to be allowed for in the pump design.
For pumps with conventional impellers, the existing solutions include having a thrust bearing built in the pump, or to use a special motor fitted with a larger thrust bearing. Both are costly and can be complicated. Another solution has been to simply have a smaller diameter back shroud to reduce the thrust.
Ebara has rethought the hydraulic design used in multistage pumps. Utilising the latest in computational fluid dynamics and design, followed by rigorous testing, Ebara has developed a unique impeller design that offers solutions and value to the customer.
The optimised shape of the Shurricane maintains high efficiencies and very significantly reduces the axial thrust –meaning that any standard IEC motor can be used and bearing life is improved.
Built like a Katana
A Katana is a traditional Japanese product manufactured with care and precision. Only years of experience can give the necessary capacity to build a masterpiece.
This is what Ebara does with its pumps. As a result of over 100 years of Japanese experience in pump design and manufacturing, their pumps offer high-quality performance, reliability, and cutting-edge technology.
Ebara’s vertical multistage pumps are manufactured in Italy to the highest standards of quality, and achieve reliable operating performance by means of
strict technical evaluation criteria and control programs that involve the whole manufacturing process.
The range of Ebara vertical multistage pumps are suitable for a wide range of applications, in the industrial, commercial and agricultural fields. They can be used at water treatment plants (for reverse osmosis and filtration), for the pumping of hot or cold water for HVAC systems, for the pumping or boosting of water in general, and in boiler feed, irrigation and fire fighting systems.
The pumps can be coupled with any motor, anywhere. Optional materials are part of the unique hydraulic design, and there are optional connections for customers to consider.
Innovative hydraulic solutions
• Commercial motors can be fitted to all of the pump models without any modifications thanks to low pump axial thrust load
• Long life of the motor bearing
• Patent Application
Energy saving
• High pump efficiency with MEI (minimum efficiency index) > 0.7
• Fitted with high efficiency motors
• Suitable for use with Variable Frequency Drives for further energy savings
Piping connection options
• Various types of connections are available to best suit different installation requirements
• The external dimensions are to the industry standard, and are interchangeable with most other brands
• The cartridge type shaft seal is able to be replaced without disassembling the motor bracket
• The spacer coupling allows easy maintenance without having to remove heavy motors 5.5kW and above
Smart plug solutions
• Air ventilation plug
• Water filling and sensor plug
• Commercial sensor fitting
• Tappings for suction and discharge pressure, and/or drain
The optimised shape of the new Shurricane impeller maintains high efficiencies and very significantly reduces the axial thrust – meaning that any standard IEC motor can be used, and bearing life is improved.
A project to expand the Lihir Gold mine, located on volcanic Lihir Island in Papua New Guinea’s north-east, proved to be a challenge due to a high water table. To reduce the water level in the pit to allow for expansion, experts were brought in to design and provide a dewatering solution. Crusader Hose was one of the equipment manufacturers that was involved in the project, supplying flexible layflat hose.
The Lihir Gold mine is an open-pit mine located within one of the island’s large volcanic calderas, the Luise Caldera, which borders the sea. While the volcano is considered extinct, it is still geothermally active, evidenced by fumaroles – smoke emanating from the rocks within the pit. Due to the pooling of rainfall and regular seepage of seawater through the crater rim into the pit, the pit needed to be pumped out in order for the mine expansion plans to go ahead.
Designing the dewatering system
The prime contractor for the project was a large pumping company from NSW, who are experts in designing mine dewatering systems. The company was brought in to provide a solution to lower the water table, so that mining could be expanded.
The final design included a dewatering system that used 3 x 350kW submersible bore pumps inside an angled poly-pipe casing suspended from flexible hose. Each pump was driven by a separate generator and connected to a platform, which cantilevered over the pit wall.
In order to construct the angled bore casing, 900mm diameter poly-pipe
sections were welded together to form an insulation sleeve, which rested at an angle along the pit slope. The length of poly-pipe into the pit was 175m long and the water level was about 45m below the headworks. The bore casing was then securely anchored from the headworks, which incorporated a concrete-padded, steel-framed platform, which was surrounded with safety rails.
Once the bore casing had been secured, installation of the submersible pumps commenced.
Each 350kW stainless steel submersible pump was mounted on a skate which slid within the casing, allowing the pumps to be let down inside the poly-pipe, plus acting as a centraliser. The pumps were connected to Flexibore, the flexible layflat hose supplied by Crusader Hose, which suspended each pump under its own weight, as it was lowered 175m into the pit.
The hose of choice for the
Flexibore was chosen for the project as it allowed for easy installation of the pumps over a roller while clamped from a crane.
“As the hose is manufactured from woven fabric that acts like a lifting sling, a high tensile load of up to 16 tonnes can be suspended from it,” said Francois Steverlynck, Managing Director of Crusader Hose. “The hose is also supplied in one continuous length.”
“The 8” Flexibore also has a burst pressure of 440m, which was well within the design pressure for the project.”
With the submersible pumps safely lowered inside the poly-pipe casing, they were then connected to the diesel generators via the power cables attached to the Flexibore hose. Settings and flow rates were controlled until each pump attained a flow rate of 168 litres per sec.
The CAT diesel generators were supplied by Taranis Power of WA.
Gabriel Hoascar, the engineer from Taranis who connected the pump cables and fired up the generators, said, “I was impressed at how efficiently the system worked.
“Our company will look to supply more systems using Flexibore hose.”
Dimensional tolerances are small on vertical pumps, as pumps can be 0.2-0.5m in diameter and 20-40m long. Conversely line shaft bearings, often carbon bearings are generally used which do not perform well under prolonged stress and slowly loosen over time. These resultant increased bearing clearances culminate in shaft whipping, high vibration and severe pump damage. At ITT Blakers, we upgrade line shaft bearings with a selection of engineered materials used for extreme wear applications. Without these modifications line shafts, line shaft couplings and line shaft bearings are frequently replaced during overhaul. The ITT solution provides the redesign of the bearings to introduce shaft sleeves. Here, the sleeve becomes a consumable item, thus protecting the shaft. For extreme wear conditions such as those experienced
by seawater intake/lift pumps, ITT has also successfully developed hard-faced shaft sleeves using laser bonded plasma arc technology, increasing the wear resistance of the shaft.
Saltwater also damages the wetted parts severely, the bowl assembly, columns and line shafts. The ITT solution to this is to upgrade standard materials to Super Duplex, SS Grade 5A with PREN>45 to significantly increase corrosion resistance. In addition, we also offer impeller and/or bowl redesign plus hydraulic changes for the ultimate life extension and energy reducing solution.
In all instances, a separate bearing retainer with additional accessory parts makes it difficult to achieve positive alignment. The ITT solution is to upgrade columns with a Goulds integral bearing retainer which are economical to produce and vastly reduce any chance of misalignment.
“I
Screens are an essential addition to water intake and diversion systems to conserve fish populations whilst protecting water management infrastructure.
Traditionally, placing a screen on your pump intake meant:
Installing a coarse screen
(This often delivers poor quality water, causing blocked lines and screens, resulting in high pump maintenance).
Installing a fine screen
(This method delivers unreliable flow volumes, with regular screen blockages that are difficult to clean).
Both these outcomes are undesirable, inefficient and costly.
An efficient pump intake screen provides: finer filtration, a low approach velocity and an integrated screen cleaning system. These proven features deliver uninterrupted flows (with no need for back flushing), prevents clogging of spray nozzles and requires minimal maintenance, all whilst reducing power consumption and operating costs. The environment also benefits, as innovative screen technology protects aquatic fauna and flora in waterway and catchments.
Efficient screens feature:
• Integrated brush cleaning system
• Internal baffling to control even flow over full screen area
• Aperture size <3mm
• Approach velocity of <0.12m/s
• Screen life of 25+ years Australian made
• Deliver full rated unobstructed pump flows
There are three main design considerations when selecting a quality fit-for-purpose screen:
1. Aperture size
Intake screens are available in a variety of aperture sizes. The size required is site specific based on the quantity of water, characteristics of debris, and weed and aquatic life present (including fish species and breeding patterns).
2. Approach velocity
The velocity of the water approaching and passing through the screen should be as low as possible. This prevents entrainment and impingement of both debris and fish. Low approach velocities also reduce head loss.
3. Self-cleaning functionality
Traditional pump intake screens require regular manual cleaning with significant operational and safety risks. Advances in intake screen technologies include innovative cleaning systems. A self-cleaning screen ensures efficient operation,
with fish protection, without comprising flow. Additionally, a sustainably clean screen improves pump efficiency.
Sustainable solution
AWMA screens are designed to suit gravity and piped, pump intake structures. They draw low flow velocities, distributed evenly across the screen to ensure the sustainability of fish health and efficiency of water extraction. This even flow distribution across the entire screen surface combined with controlled low approach velocities prevents debris entrainment and impingement on the screen. This is complimented by energy efficient, automated, brush cleaning.
Screen solutions are custom designed to be site specific to ensure the rated flow demand of the pump or diversion is maintained.
AWMA screens provide a win-win for the operator with reduced costs whilst protecting the environment with the preservation of aquatic life.
Make sure your next screen decision is based on the inclusion of the key elements: aperture size, controlled approach velocities and an integrated cleaning system.
Choosing the right positive displacement pump for an application can be a difficult task. It is essential to find a supplier who is not only an expert in the field, but also provides efficient, reliable and trusted products with the ability to customise solutions to fit the end user. Finding the right manufacturer will not only save you time and money, it will also help you avoid system downtime and increase productivity.
For Roto Pumps – a global manufacturer of positive displacement pumps – a strong foundation of experience and expertise; efficient, reliable and readily available stock; and cost-effective solutions have seen it become a global leader in the pump industry.
In 2001, Roto Pumps established a local branch in Australia with warehouse, assembly and marketing infrastructure to provide positive displacement pumping solutions to various industries across the country.
The new Australian market presented its own challenges, with strong competitors, but Roto Pumps was not new – it had a rich legacy of over 50 years’ experience internationally, with a large number of screw pump installations in critical applications across the globe to draw from.
To gain a strong foothold in the Australian market, Roto Pumps focused on providing customised engineered pump packages, strong service support, and ensuring ready availability and optimum stock levels of pumps and spares. Roto Pumps Australia also established an intensive network of distributors and channel partners.
Roto Pumps Australia’s capabilities:
A pioneer in manufacturing
Known for pioneering the manufacturing process of progressive cavity pumps in India in 1968, Roto Pumps has continued to grow into one of the most trusted global leaders in the field. Today, the company supplies pumps to more than 10,000 customers across 50 countries and have installed over 250,000 pumps globally.
Throughout its five-decade journey, Roto Pumps has also established operations in the UK, South Africa, US, Germany and Malaysia, thanks to its highly dedicated team, and passion towards research and development of highly efficient positive displacement pumping solutions.
Now, with 18 years of experience in the Australian market, Roto Pumps has established itself as an expert in application engineering i.e. understanding complex pumping requirements, handling critical media, and optimising pump lifecycle cost. It is also credited with supplying customised pumps in different materials like Hastelloy, Super Duplex, Tungsten Carbide Coatings, and Double Hard Chrome Plating etc.
• 18 years of strong presence in Australia’s robust supply chain network
• Strong sales and service support team in Australia
• Readily available pumps and parts stocks
• Cost-effective and customised engineered packages
In addition to pumps, its stators are world famous for their stringent quality. Roto Pumps’ in-house captive elastomer manufacturing unit manufactures world-class quality stators conforming to international standards. To deliver quality stators, Roto Pumps procures raw material from certified vendors and has implemented strict process control and quality checks.
A leader of innovation
Roto Pumps is also a leader of innovation in pumping solutions. Some of its key innovations include Roto Kwik-Maintenance in Place Pumps for quick maintenance of Roto Progressive Cavity Pumps without removing pipelines; the Tirrana Agriculture Progressive Cavity Pump range for agriculture and light industrial duties; and the upgraded Biomix and Biomass Progressive Cavity Pumps.
Roto Pumps believes in customer satisfaction and has a team of experienced application and sales engineers in Australia who completely take care of every customers’ concern right from receiving the inquiry to providing prompt after-sales support.
2,50,000
With Queensland experiencing drought conditions, the quantity and quality of available feed has become scarce, requiring graziers to supplement feed with additional nutrients. Wilmar AgServices produces a natural protein supplement that can be used for this purpose. When the company decided to produce a new phosphorus-enriched product range, it approached Polymaster to provide a precise dosing and storage solution.
Wilmar AgServices (part of the Wilmar Group) operates a liquid fertiliser and stockfeed business based near its bioethanol plant in Sarina, Queensland.
The company is known in the sugar cane, horticulture and agribusiness industries as an award-winning and innovative producer of efficient and environmentally-friendly nutrient solutions. This is especially crucial as a number of its customers are within sensitive Great Barrier Reef Catchment areas.
Wilmar AgServices produces a natural protein supplement for cattle, using co-product from its bioethanol fermentation process. This fermented product is called Suplaflo 10NP, a flowable supplement containing natural protein, with inherent nutritional value and a capability to carry other important nutrients. Wilmar’s Suplaflo 10NP is used in a range of liquid supplements for cattle.
Wilmar AgServices needed to be able to add a precise dosage of phosphorus at its Oonooie plant to deliver a whole new product range enriched with phosphorus.
As phosphorus requires precise dosing and at relatively small amounts needed per tonne, an accurate metering and chemical storage system was necessary.
Wilmar AgServices approached Polymaster to provide a solution to store the phosphoric acid (30kL), as well as for dosing in the Suplaflo 10NP production line at its facility.
The physical footprint on-site was a major consideration when proposing a solution.
Image 1.
After consultation, the Polymaster engineers were able to guide Wilmar AgServices to a 30kL rectangular forecourt-style unit (Image 1), instead of a round tank.
The forecourt-style unit ticked the functional box as it could fit into the designated area comfortably and at the same time provide protection from the elements for the equipment contained within its built-in control room.
The final design was constructed on a Duragal hot-dipped galvanised base frame, with a CAT 2 wind loading (Region C) frame which was wrapped in 100mm insulated wall and roof panelling. This unit was built to withstand wind gusts up to 50m/s (cyclonic).
The unit perfectly housed three 10kL interlinked doubledwalled tanks. Within the control room, two 3-phase diaphragm pumps (filling and dosing), and a Polymaster power control panel with variable speed drives, tank level monitors, instrumentation and programmed safety switches were installed.
Additionally, Wilmar AgServices required roof access and a full safety handrail system with ladder – all constructed to meet AS1657-2018.
Logistics were top-of-mind from the onset as this project required road transport of 2,019km to Sarina without the need for pilot vehicles – a freight saving.
The result was a truly fit-for-purpose, easily maintainable unit with safe access points to the inner tanks, which incorporated appropriate ventilation within all confined spaces.
As with most Polymaster products, the unit has been designed to be a ‘plug and play’ solution to minimise on-site installation costs.
Helping agricultural businesses realise energy savings
The Energy Savers Program is part of the Queensland Government's $2 billion Affordable Energy Plan. The program aims to assist agricultural businesses identify what equipment or processes are using the most energy, and what options are available to upgrade equipment or new processes that can be implemented that will achieve energy savings or productivity improvements.
Agriculture is an energy-intensive industry, with energy making up a large portion of operating costs. However, there are numerous opportunities to significantly reduce these costs by improving and optimising equipment and practices; and switching from obsolete or to a more appropriate tariff. To help Queensland farmers reduce their energy costs, through its Energy Savers Program, the State Government has been working in partnership with the Queensland Farmers’ Federation (QFF) to conduct energy audits on farms to identify energy use and costs, and to provide recommendations for changes – and funding help to implement these – to help them focus their efforts. Pump Industry magazine spoke to Andrew Chamberlin, Project ManagerEnergy at QFF, about the program and one of the many farms that have benefited from it.
The program is funded by the Department of Natural Resources, Mines and Energy (DRME) and delivered by Ergon Energy in partnership with the Queensland Farmers’ Federation (QFF) and its member organisations.
Findings have indicated farmers can significantly reduce their electricity bills through more efficient practices, with the Energy Savers Program helping them realise this saving by providing free personalised audits that identify opportunities to cut costs in areas such as on-farm heating, irrigation
pumping, cooling, lighting, processing, packing, ventilation and household energy use. The program also provides them with helpful information on financing options to help with energy efficiency upgrades, as well as rebates of up to 50 per cent to a maximum of $20,000 to implement the recommendations of the audit, including to fund equipment and plant upgrades.
The Energy Savers Program was rolled out in a number of rounds across Queensland, with the first two stages including farms in both Ergon and Energex territories:
• Irrigators Energy Savers Program 2013-2015: 30 irrigation audits were conducted on a range of different farms and irrigation types
• Energy Savers Plus Program 2015-2017: Almost 100 audits were conducted across a range of irrigation and onfarm processing systems in a number of sectors
In total, the previous rounds of the program have:
• Delivered over 128 energy audits
• Identified more than $4 million per year in potential electricity saving
• Measured $0.63 million in actual annual bill savings across 24 sites
• Identified over 7,500MWh per year in energy savings with a payback of less than five years
• Generated over 40 case studies
• By the end of the Energy Savers Plus Program, over 62 per cent of farms had implemented or were planning to implement recommendations
• Promoted best practice energy management strategies
QFF has recently completed all audits under the latest round, the Energy Savers Plus Extension Program, and is currently working with the farmers to help them access up to $4 million in program rebates from the Queensland Rural and Industry Development Authority (QRIDA) to implement audit recommendations. So far, over a third of farmers who had an audit have applied for funding, with a number already moving forward and implementing the recommendations.
Farmers that use over 100MWh per year were eligible to apply for the Large Customer Adjustment Program, which will provide audits and a rebate of up to $250,000 per business to help implement recommendations.
Once an audit has been completed, farmers are not obligated to implement all or any of the recommendations, and there are a variety of reasons why some do not choose to do so.
Andrew Chamberlin, Project Manager - Energy at QFF, said in one instance the farmer chose not to implement the recommendations because they changed their strategy and are now irrigating from a dam using efficient variable speed pumps.
“Now that they have set the new system up efficiently they will add solar power to cut costs even further,” Mr Chamberlin said.
The Energy Savers Program has undertaken audits of onfarm irrigation and processing systems for many industries throughout Queensland, including cane, horticulture, cotton, nursery and garden, dairy, intensive animal industries, eggs, pork and poultry.
Irrigation is a key audit area, as it makes up a large proportion of on-farm energy use for many sectors and there are often significant opportunities to save energy with improved systems.
In particular, pumping systems are one of major areas where there is an opportunity to save energy, as around 85 per cent of the lifecycle cost of a pump is made up of energy costs. Improvements to elements of the pumping
system for an irrigation application that can result in energy efficiencies include:
• Increasing poly pipe diameter from 32mm-50mm (over 200m at 2L/s) can cut pumping costs per ML by around 90 per cent
• Removing trash from suction inlets can improve pump performance by up to 20 per cent
• Reducing air entrainment from suction ends – two per cent air can reduce pump performance by 20 per cent
• Electronic diesel engines can be up to 13 per cent more efficient than mechanical engines
• Limiting water velocities to 2m/s
The three key aspects to efficient irrigations systems are:
1. Needs analysis, design and planning to balance water and energy efficiency objectives to deliver the right amount of water at the right time, at the least cost
2. Optimising equipment to ensure the system delivers the best result for the energy inputs
3. Energy source – using the most cost effective and efficient energy source
Mr Chamberlin said many of the farms had irrigation systems that were looked at as part of the audit, so many of the recommendations made were related to improve and optimise irrigation system efficiency.
“There have been a lot of irrigation recommendations; everything from upgrading pipes to reduce friction losses, such as larger diameter pipes and less right-angled bends; to upgrading pumps to more efficient models. This can be because (a) pumps are very old and replacing them with a new more efficient model will get savings, or (b) the crops or something else has changed,” Mr Chamberlin said.
One of the audits completed by the QFF under the Energy Savers Program was for an Atherton Tableland pasture farm.
The farm produces around 8,300 tonne of hay, irrigating on sloping land with a centre pivot and travelling irrigator operated separately from a single pump which used around 130,000kWh of electricity per year. At the time of the audit, the farm was using the obsolete Tariff 62, pumping at night during off-peak times.
Mr Chamberlin said the farmer decided to apply for the program because they wanted to identify measures to keep energy consumption below 100,000kWh per year (or 100MWh) so that the farm could remain a Small User and move to small business tariffs.
“Energy costs were getting too high and they wanted to have the farm considered a Small User so they could earn the feed in tariff for exporting surplus solar power, and they would not have to pay demand charges,” Mr Chamberlin said.
From the energy audit and discussions with the local pump shop and electrician, the best efficiency and production outcomes for the site included:
• Installing a smaller pump and motor, and adding a Variable Speed Drive (VSD) with remote pressure sensors
• Adding a 40kW solar system with a 30kW inverter to cover pump load power with possible export
• A small solar system for the farm shed
• Retrofit existing lighting with LEDs
• A change in strategy to day-time pumping using energy produced from solar on-site, with a change to Tariff 20
Table 1: Audit recommendations comparing savings between tariffs.
Mr Chamberlin said the farmer chose to implement the recommendations from the audit, but that it did take some time and help to get all the different elements right.
The 55kW pump that supplied a small centre pivot and a large traveling irrigator was removed and downsized to 45kW, and positioned lower to the water to reduce suction lift and improve efficiency. To overcome reduced efficiencies as the irrigator moves across the paddock due to the slope, a VSD was installed on the electric motor which controls the motor speed to improve the irrigation system efficiency.
“To start with they couldn’t get enough pressure and the pump was cavit,ating, so they had to work closely with the pump shop and they ended up having to adjust the inlet and outlet piping a bit,” Mr Chamberlin said.
“They are now getting the pressure they need all the way up the top of the run, and as soon as it comes down the hill, you can hear the VSD slowing the pump right down. They are going to try larger sprinkler heads after the dry season to see if they can put more water through and gain more off the paddocks.”
Pressure control has been further improved with the establishment of a new radio link between the lateral irrigator, centre pivot and the pump, which measures the pressure available at the irrigator or pivot and sends the data back to the VSD, ensuring the correct water pressure is maintained. The pump runs slower, using less power at the bottom of the paddock and increasing up the slopes to maintain perfect pressure and even water distribution.
Mr Chamberlin said the radio link also allows remote starting, and should the pump stop or there is a fault with the pivot or irrigator, the pump will not operate.
“The pump is actually located on another property a few minutes drive from the house. Previously, they would need to go to the pump to turn it on or off. Now, the controller is in the shed near the house, and the VSD automatically turns off the pump when the irrigator hits the end of its run,” Mr Chamberlin said.
“Previously, they would have to go over at, say 2am to turn the pump off, so that means they don’t have to go down to the pump if there’s an issue – as the VSD shuts things off. That means they don’t have to leave the kids in the house and go and turn the pump off – especially at 2am. One of them would have to stay up so they could go down and turn the pump off.
“The farmer has reported that it’s made life so much easier for them as it’s one less thing to worry about.”
The farm also installed a 39.6kW solar array with 30kW inverter, arranged in an east-west configuration, which will cover most of the load required by the new pump. As the irrigators run for long periods, the panels facing east will reach maximum capacity earlier in the morning, with the panels facing west producing maximum power in the afternoon.
As the inverter capacity is no larger than 30kW, the installation was treated as a micro embedded generating unit, keeping the connection process simple and ensuring the farm is still able to export during times when the irrigation system is not running. Maintaining grid connection allows the irrigator to draw grid power when required.
The farmer reports they are very happy with the results of changes they have made so far based on the recommendations of the audit.
By reducing consumption and generating power from solar PV, the audit estimated the farm was likely to reduce its energy consumption below 100,000kWh per annum while still being able to access the small business tariffs, removing any possible demand charges.
With requirements to move off obsolete Tariff 62 by June 2021, a move to Tariff 20 will provide quicker paybacks from changes made to the pumping system. However, moving the farm to Tariff 20 has not been a quick process.
Mr Chamberlin said the farm was originally classed as a Large User, which meant they had to pay demand charges and were not allowed to earn a feed-in tariff for exporting power from their solar panels. Due to this, Ergon would not allow them to switch to Tariff 20 until they could demonstrate their consumption had been reduced below the threshold. However, energy savings achieved through the solar and pump charges has now brought them below the threshold, making them eligible.
“The farmer has advised that electricity consumption this year has halved compared to last year on a month by month basis. Because of that, they have agreed with Ergon that they are no longer a Large User and that they can now get the feedin tariff for any surplus and pay the lower Tariff 20 rate,” Mr Chamberlin said.
“They are now irrigating during the day on a flat tariff and expecting to have costs significantly reduced as well.”
The change of tariff will extend the payback period on the smaller solar system. In the future, should the farm implement changes at the shed, the savings from the irrigation changes will cover any potential difference.
For more information about the Energy Savers Program and to view case studies, vist https://www.qff.org.au/projects/energy-savers
The valve is an inconspicuous element in the pump circuit. Yet – like a fuse in a power circuit – it is essential for the safety of a plant. In addition, given its operating principle, it makes a valuable contribution to energy efficiency.
Most centrifugal pumps operate with a constant speed along a fixed curve. The pumps are integrated into plants with variable discharge flows. The variable flows lead to working areas where process-related flow rates are below the required pump specific minimum flow.
The pump minimum continuous flow (MCF) is the lowest permitted flow rate that the centrifugal pump can handle permanently without damage, as well as ensuring safe and economic operation.
To ensure the required flow rate does not fall below the permissible minimum, it is common to install a bypass with orifice between the pump’s discharge branch and the first shut-off device in the pressure line. The orifice device permanently allows the constant minimum flow to pass to the tank or to the suction line.
The orifice solution permits a constant loss of flow rate that considerably reduces the efficiency of the pump assembly. Based on economic and ecological aspects, this solution is only acceptable for smaller low pressure pumps with low minimum flows.
For assemblies with larger pumps and higher operating pressures, the following solutions are applied:
• Systems with an actuated control valve, with flap valve and according measurement technology
• The automatic recirculation check (ARC) valve which practically includes all the above-mentioned functions of an actuated control valve
Systems with actuated control valves are relatively complex and expensive, while solutions that incorporate an automatic recirculation check valve are considerably simpler and more robust.
Automatic recirculation check valves are mounted on the discharge branch of the pump or in the pressure line right after the pump. The bypass branch of the valve is connected to the bypass line.
The valve operates on demand flow. In start-up conditions with no demand flow to process, the valve will allow the MCF through the bypass. As the process demand is opened, the valve will modulate flow between the process and bypass branch. As the process demand exceeds the MCF, the bypass will fully close and all flow through the valve is sent to process. If the actual process flow rate falls below the required minimum flow, the valve automatically opens the bypass line and the determined flow rate can be discharged through the bypass.
The ARC valve ensures that the entire pump flow rate (process flow plus bypass flow) is always greater than the required minimum flow. In this scenario, the pump is always protected from low flow conditions.
ARC valves consist of a three-way body with three integrated flange connections that are the interfaces to the pump assembly. Internally there is a guided and spring-loaded valve cone which provides the check function and prevents backflow of the medium through the pump.
The stroke of the check valve is reliable and mechanically operates the bypass lever. The operation of the bypass lever regulates the opening and closing of the bypass branch and consequently the bypass flow.
Compared to the operating pump pressure level, the pressure level in the bypass line is considerably lower (since the bypass line either leads to the tank or the suction line). The bypass of the valve provides an additional feature of pressure reduction in the bypass line. This pressure reduction feature prevents flashing and cavitation in the bypass line and return tank.
• Process fluid controlled and they do not require any external energy source
• Highly reliable, robust and low maintenance
• Bypass flow rates are regulated at a permanent minimum and the pump assembly is protected safely
• Pump head losses are minimised – the pump assembly’s efficiency remains high keeping operating costs low
• Applicable for almost all liquid mediums where centrifugal pumps are used. The temperature range extends from minus 273°C up to plus 400°C
• Made from materials ranging from carbon steels to super duplex steels according to technical or customer requirements. The interior parts are made from stainless steel
• Simple design and plant-specific installation conditions (i.e. piping connections) are often considered
• All Schroeder ARC valves undergo flow testing after manufacturing to simulate the pump design conditions the valves are designed to protect
The innovative design of the German-engineered automatic recirculation check valves by Schroeder Valves, ensures they are extremely reliable, low maintenance and exceptionally durable. With these attributes, Schroeder’s ARC valves allow for shorter downtimes and higher system efficiency. Without the need for any auxiliary energy or measuring technology, they guarantee lower system and operating costs.
TECO Electric and Machinery is a market leader, well known for producing high-quality motors. Unsatisfied with producing only motors, TECO committed to the manufacture of motor drives over 20 years ago. In 2016, the company launched the TECO MV510 range of medium and high voltage drives that showcases its manufacturing prowess.
TECO moved from investor-supplier to owner-supplier when it acquired Westinghouse Motor Company in 1995, which strengthened its core business, increased competition and solidified its global brand leadership.
Since then, it has successfully diversified into a conglomerate with worldwide business operations covering five continents, and has become the one of world’s largest manufacturer of industrial motors.
TECO drives and motors are used in a variety of applications including industrial automation, industrial machinery, air conditioning systems, mining, oil and gas, energy-saving projects, pipelines, and wastewater treatment.
The MV510 range of drives is in compliance with global specifications for energy efficiency and environmental protection. The comprehensive portfolio ranges from 200–8,000kW, boasts power-unit connection overlapped-wave technology, and is capable of lowering damage to the insulated stress of a motors copper wire dv/dt and providing timely monitoring of operational status.
Options of IP31 and IP42 grade protections are available, plus RS485 interface, various communications formats – such as Modbus, Profibus, Devicenet, and Ethernet – and passage of CE and IEC certifications.
The power supply input and output of MV510 general medium voltage drive meet the most stringent IEEE 5191992 and GB/T14549-1993 standards, so there is no need for an independent input filter, saving customers the cost for harmonic elimination.
Because of the high power factor of the system, the compensation device for power factor is not needed, thus the reactive input and the input capacity are reduced, and the cost for capacity increasing the power network is minimised.
Compared with other high voltage and high power MVDs, the MV510 has a number of significant advantages. Firstly, there is no need for extra output filtering devices or direct driving of the general high voltage synchronous or asynchronous motor, and the temperature of the motor will not increase. There is also no need for motor derating operation, and no dv/dt damage will occur to the motor and cable insulation.
Due to the modular design of the power cell, it is quite simple to replace it and moreover, only a few spare parts are necessary. The power cells are universal and can be used in drives of the same current rating, regardless of voltage class. Other functions and features include:
• Protection of overload and overcurrent
• Protection of open phase and grounding
• Protection of overvoltage
• Overheat protection
• Current limited function
• Interlock protection of control power supply
• Two sets of control power for redundancy power cell bypass function (optional)
• Motor Bypass System (optional)
• Frozen-charge
• Cabinet door opening alarm function
• Lock-phase function
• Synchronising switch function between variable frequency and work frequency
• Soft start of motors, no impact to mechanical equipment and network
• IoT (Internet of Things) With units already being sold, the TECO MV510 range of drives is making a significant contribution to the motor and drive market.
Melbourne Water has launched the first stage of an ambitious program to transform our water transfer network.
As the wholesale water supplier for Greater Melbourne, we distribute water to our retail water customers via a vast network of pipes, valves and service reservoirs spread out across the greater Melbourne Metropolitan area. We are always exploring innovative ways to build on and improve our operational efficiencies as we do this.
Customer experience is also central to the process. At Melbourne Water we are continually looking to increase reliability and provide more information to retailers to optimise their operation.
To that end, we have introduced an exciting new program called Water Transfer Network Automation (WTNA). Put simply, it will minimise pumping costs, chemical usage in the treatment process (through the smoothing of flows out of the treatment plants) and help us maximise operational knowledge. Flattening flow peaks and troughs will reduce energy usage for the transfer and treatment of our water supply.
The problems and finding a solution
Previously, pumping was carried out at various times of the day depending on local requirements which caused some energy use inefficiencies. Also, the transfer of water didn’t always account for any effects the variance in flow rates had on the water treatment plant supplying the source water and the correlating energy needed for the treatment process. This could result in additional and unnecessary power usage.
Melbourne Water addressed these issues head-on – went to market with an expression of interest to determine the way forward – and chose the product AquAdvanced® Energy (AAE) by Suez.
The Water Transfer Network Automation Project was launched!
Technology to remotely monitor and control sites
Automation Team Leader at Melbourne Water, Russell Riding, said the AAE software package works in conjunction with Melbourne Water’s Supervisory Control and Data Acquisition (SCADA) system. This software is used to remotely monitor and control field-based sites and equipment such as pumping stations and water treatment plants.
“The system is able to assess the whole network every half hour and uses hydraulic demand modelling and inbuilt analytics to make any necessary adjustments to time-based scheduling across the entire system. The technology will allow the bulk of our water transfer system to be automated,” Mr Riding said.
Phase 1 of the project involved a data collecting activity of all of the potential operational constraints and knowledge held by the local teams, and along with Melbourne Water’s hydraulic demand model, was used to create an offline solution for bench testing.
an integrated intelligent pumping system with an electronically driven, permanent magnet motor and an embedded electronic drive, these simply smart pumps will greatly enhance system performance and maximize
The offline solution was then developed for a small part of the network to check viability and to assess potential benefits. It took about three months to complete. The results were positive, showing clear energy savings with the smoothing of flows out of the major treatment plants.
This intel was subsequently used to build the business case for implementation.
Phase 2 commenced in 2019, and the offline solution was deployed for operational application – on a site-by-site basis across one of our critical transfer networks, the WinnekePreston transfer network. This involved new ways of operating within the control system at each offtake asset. Once again, all signs were positive.
In June 2020, since commissioning the system across the whole of our Winneke-Preston transfer network, the technology has consistently delivered; more water is being shifted using less power, there are smoother flows out of the main treatment facility and more reliable transfer operations.
AquAdvanced® energy uses a schedule-based system in 30-minute blocks for each supply asset to work out the water movements across the network.
The system incorporates a version of Melbourne Water’s hydraulic network demand model so that it has a starting point for the required volumes that need to be transferred.
Also built into the solution are optimal water levels for all reservoirs and tanks, and the energy cost profiles for each site. This allows the system to “load shift”, ensuring pumping is carried out at the lowest possible electricity price point.
The benefits to Melbourne Water’s transfer network are large and the flow-on gains to our customers are many. This system also compliments our innovative use of 14 hydroelectricity plants in our water supply network, which can generate up to 69,500 megawatt hours of electricity each
year. These power stations generate energy from the flow and pressure of moving water, and feed it back into the electricity grid. Another three mini-hydro plants are in the pipeline and when complete will generate an extra 7,000 megawatt hours of electricity per year.
With automation of the Melbourne Water water transfer network well underway at our Winneke-Preston network corridor, the second phase will focus on Tarago-Cardina in early 2021, and then Silvan-Greenvale network in mid-2021.
For the Melbourne Water workforce, this makes us nimbler, more efficient, introduces our operators to ‘skills for the future’, and once again puts us at the cutting edge in the use of innovative technology for our operations.
Russell Riding, Automation Team Leader, Melbourne Water.
With its modern design, the CFW500 is a high performance VSD for applications that require speed and torque control of three-phase induction motors. The standard control strategies of Sensorless vector, Closed loop vector and Scalar V/f ensure optimal performance in any industrial installation. The imbedded SoftPLC feature adds PLC (Programmable Logic Controller) functionality further reducing install cost, whilst Safe Torque Off, Safe Stop 1 and Safety Integrity Level 3 rating ensure compliance to all applicable machine and installation safety standards. Flexibility and Connectivity are further enhanced through a wide selection on plug in modules.
Designed to drive centrifugal and submersible pumps, the CFW500 Solar Pump Drive turns solar energy, provided from photoelectric panels, into hydraulic energy, bringing great efficiency and maximizing system availability.
The CFW500 IP66 Drive provides protection against contact with internal live parts, avoiding the entrance of dust or water coming from jets. This design maximises the simplicity of the drive while meeting extreme environmental conditions eliminating the need for large and expensive panels or switchrooms.
Further enhancing the application of CFW500 in pumping installations is the inclusion of Pump Genius. Pump Genius provides dedicated functionality for pumping systems including Simplex, Multi-pump, Multi-plex, Sleep and Wake, Broken Pipe and Pipe Charging.
Pump Genius is a customisable feature of WEG drives that enables your standard CFW500 to become dedicated for pumping systems. It ensures accurate pressure/flow control throughout the processing cycle, starting with raw water and its usage, through to wastewater treatment. With an easy-to-use programming wizard, Pump Genius helps you to minimise downtime and maximise energy savings. All you need to do is select the option that best fits your application:
Pump Genius Simplex software adds ideal features to the VSD for a single source of pump control.
Pump Genius Multipump allows two or more pumps to be driven with only one inverter.
Pump Genius Multiplex permits the VSDs to control, monitor and manage the entire system on their own, eliminating the need of external PLC.
The use of the CFW500 with the Pump Genius Multipump improves performance and provides electrical energy savings. Using this solution together with WEG W22 Premium motors, and reducing the pump speed even if slightly, it is possible to reduce electrical energy consumption by approximately 15 per cent, thus contributing to the sustainable development of the planet.
The sleep function keeps the pump in the standby mode when the demand or flow is below the minimum, avoiding it running at low speed for long periods, providing electrical energy savings and increasing the lifetime of the pump. The wake up function restarts the drive automatically when the pressure falls below the set point.
Note: 1) Under development. Find out more about Pump Genius by visiting www.weg.net
Pump Genius detects when the pump is consuming more electrical energy than it should, by means of information on the pump load and speed, automatically generating an alarm warning of leaky pipes. In addition, with the monitoring of the system pressure, a clogging condition may be detected by configuring the maximum pressure to trigger the alarm of clogged pipe
It allows lubrication and smooth initial charging of the pipes, making the pump operate at a lower preset speed for a certain time and avoiding waterhammer, which may damage the piping system.
Drive Systems has expanded its range of couplings stocked in Australia to include the Escodisc DPU series of coupling to API 610 standards.
Escodisc DPU series couplings have a maximum torque capacity of 23,100Nm and bore capacity up to 220mm.
A comprehensive range of the DPU Series API 610 disc couplings are stocked with a variety of spacers to fit standard DBSE (Distance Between Shaft Ends) in 100mm, 140mm, 180mm and spacers up to 300mm off the shelf that can be quickly modified to customer specific lengths.
Flexible spacer design
Thanks to the unique design of the Escodisc spacer with its flanges bolted to the intermediate tube section, its length is easily adaptable to customer requirements. Therefore, quick delivery (even for non-standard DBSE) is possible for larger spacers above 180mm or to match imperial spacers often found in the petrochemical industry.
No buckling of discs
The Escodisc DPU series is built around Escodisc couplings' genuine and original disc pack sub-assembly design. This design with optimised disc shape and thickne,ss, is factory assembled and secured by shipping screws against damages, minimises assembly errors,
simplifies coupling mounting and guarantees worry-free performance, low operating costs, as well as long life of the connected equipment.
In order to guarantee perfect centring of the spacer under all working conditions (very important for long DBSE applications) and well controlled stresses in the disc pack, Escodisc couplings have been calculated and tested to have no buckling up to the peak torque. This results in trouble-free operation, maximum efficiency and reduced risk for disc failure.
Thanks to the standard use of shipping screws and the factory assembled transmission spacers, Escodisc DPU couplings combine the high torque and misalignment with the ease of assembly. On average, users can cut down assembly and disassembly costs by 50 per cent when using Escodisc DPU couplings.
Furthermore, because the transmission spacer is factory assembled, the risk for assembly errors is reduced to an absolute minimum level, which results in reliable operation and extended life of the coupling.
The Escodisc DPU series offers:
• High torque and high continuous misalignment capacity
• Maintenance free
• Factory-assembled disc packs secured by shipping screws and thus protected against overstressing/damage
• Positive centering and factoryassembled transmission unit/spacer minimising assembly errors and simplifying coupling mounting
• Adjustable spacer design for easily accommodating DBSE changes
• Excellent inherent balancing characteristics
• No problems in dirty and corrosive environments due to the use of AISI 301 full hard stainless-steel discs and protected bolts
• Optimised shaped stainless steel discs for equal load distribution
• Fillers avoiding contact between discs hence no fretting corrosion
• No disc buckling
• Precisely drilled and reamed flange holes
• S hub for nominal bores and L hub for larger bores
• Black oxide overall steel parts, oiled for protection
• Special plated hardware
• Easier and less costly mounting
• Refurbishment of the coupling by fitting two new disc pack subassemblies to the existing spacer piece
• Extended life
• Very low and predictable reaction forces on associated equipment
• Temperature range -40°C to 270°C
Coupling selection is important to help keep pump equipment functioning efficiently and reliably, and keeping maintenance costs down. However, with many different types to choose from for various applications, it can be difficult to determine which one is most suitable. Here, we look at the two main categories of couplings and what factors need to be considered during the selection process.
Couplings have a variety of functions, with the most common being to connect the pump shaft and motor shaft to ensure the motor is efficiently transmitting power to the pump. Other functions include accommodating misalignment and maintaining alignment, allowing for axial adjustment of the shafts, transmitting or not transmitting axial thrust loads and vibration, and acting as a spacer between the driver and driven shafts. They consist of hubs, gear or springs manufactured from various materials including synthetic rubbers and metals.
There are two primary groups of coupling: rigid and flexible.
Rigid couplings are used in applications where a solid connection between two shafts is desired, with high precision and torque, but without misalignment absorption capabilities. As they don’t allow for movement, frequent lubrication is required, and the shafts need to be perfectly aligned to ensure optimal performance and reduce the chance of breakages occurring. If the connecting shafts are not precisely aligned, increased vibration, bearing wear and a shorter mechanical seal life
are expected. Some examples of rigid type couplings include sleeve/muff, flange and clamp.
They are commonly used in some vertical turbine, vertical in-line and short set pump applications.
Flexible couplings are used in applications where compensation is needed for misalignment, movement or deflection. While they tend to have less torque transfer than rigid couplings, they are better able to reduce transmission of shock loads or vibration, as well as being better able to accommodate axial, parallel and angular misalignments. They are commonly used in horizontal, base plate mounted pump applications.
Flexible couplings can be categorised as one of three types:
• Mechanically flexible: This type compensates for misalignment by means of clearances that are incorporated in the coupling’s design.
Examples of this type include gear, chain and grid-spring
• Material flexible: This type relies on the flexing of the coupling element to compensate for misalignment.
Examples of this type include jaw, sleeve, tire, disc, grid and diaphragm
• Non-contact magnetic: This type uses rare earth magnets to transmit torque by pairing opposite magnetic poles. They are separated by an air gap. Examples of this type include spherical, eccentric, spiral and nonlinear
In order to select the most suitable coupling, the pump, and its application and maintenance requirements need to be considered as these will affect the type and size.
Some of the key considerations include:
• Motor horsepower and operating speed: These are needed to calculate torque to ensure the couplings maximum torque rating and maximum RPM rating are suitable. These ratings will differ between manufacturers and coupling type
• Operating temperature: Minimum and maximum operating temperatures are determined by the materials a coupling is manufactured from.
Thermal expansion and contraction on the components that you are coupling together can also occasionally play a factor
• Space limitations: Different couplings have a specific range of distance between shaft ends (DBSE) that they can accept, and the distance required or that will be the most beneficial is dependent on the design of the pumping equipment
• Misalignment handling requirements and axial travel: Different couplings have limitations on how much misalignment they can take based on a variety of factors. If there is too much misalignment the coupling will experience premature failure
Other key factors that need to be taken into account include:
• Shaft and keyway sizes
• Type of driven equipment
• Chemical exposure
• Run cycle (continuous or start/stop)
• Torque uniformity
These are just some of the baseline selection factors that need to be considered, but there are a number of other system specific conditions such as ease of maintenance, ease of replacement for the coupling’s flexible elements, fail-safe, plant maintenance constraints, backlash requirements, etc.
The pump industry relies on expertise from a large and varied range of specialists, from experts in particular pump types to those with an intimate understanding of pump reliability, and from researchers who delve into the particulars of pump curves to experts in pump efficiency. To draw upon the wealth of expert knowledge the Australian pump industry has to offer, Pump Industry has established a panel of experts to answer all your pumping questions.
This edition of Ask an Expert will look at the use of smart progressive cavity pumps and how they can increase your bottom line.
Q: What are smart progressive cavity (PC) pumps and how do they increase my bottom line?
A: There are various ways that PC pump manufacturers are making their pumps smart: from innovative pump designs, to integrated controls, measurement of process variables and smart field pumps that offer online monitoring and management. All these improvements aim to put the necessary pump information right at their customer’s fingertips, while customers continue to reap the normal benefits of PC pumps such as minimal pulsation, low shear and flow unaffected by pressure or viscosity.
One example of a smart pump is one that can combine dosing and pumping with up-to-date control concepts, while also offering integration into higher level controls and automation systems. Extra safety features and measurements of process variables enable increased control over the pump/ system and quick feedback from the pump itself. Various manufactures offer flow meters, pressure sensors and dryrunning protection devices either in addition to or integrated with the pump, giving you increased control over how the pump and your system operates.
Smart progressive cavity dosing pump with integrated sensors.
Connectivity to your pump and its readings are key, therefore PC pump manufacturers have been developing further digital solutions to address this issue. This has taken form as service and maintenance apps, along with apps that capture the pump’s real-time data. The collected real-time data can be remotely monitored to analyse the pump’s condition. Customers have more control over their pumps to set alarms and warnings, or to carry out planned maintenance work.
Smart not only means greater connectivity, but also cost savings with innovative designs. Smart options for the rotor, stator and seal housing are available from select PC pump manufacturers. Through a two-part stator, easy access points and/or specialised rotor, maintenance work can be carried out without needing special tools or removing the suction or discharge pipework.
Additionally, with smart sealing options, maintenance can be performed on the mechanical seal and drive-side joint without the laborious dismantling of pump components or pipework. All these easy maintenance options reduce your maintenance time and costs, and increase your productivity.
Smart seal with smart pump enables complete replacement of stationary seal without needing to dismantle further components.
Smart seal with smart pump enables complete replacement of rotating seal without needing to dismantle further components.
Overall, all these solutions work together to offer you increased energy efficiency, reduced downtime and reduced lifecycle costs, thereby increasing your bottom line.
Contact a progressive cavity pump expert now to receive a customised and intelligent design which offers you greater control over your processes.
Peter Vila, Managing Director of SEEPEX Australia, is a progressive cavity pump expert. He has been involved with pumps for over 40 years. Peter spent the first five years repairing pumps and the following 35 years in technical sales, 20 of which have been with SEEPEX progressive cavity pumps.
For more information on progressive cavity pumps, please contact SEEPEX Australia on (02) 4355 4500 or at info.au@seepex.com
The viscosity of a fluid is the property that tends to resist a shearing force. It can be thought of as the internal friction resulting when one layer of fluid is made to move in relation to another layer. A detailed discussion on viscosity is a major undertaking and this article serves to provide a basic understanding of viscosity and how it impacts on pumping.
Consider the model shown in Figure 1, which was used by Isaac Newton in first defining viscosity. It shows two parallel planes of fluid of area A separated, by a distance dx and moving in the same direction at different velocities V 1 and V2.
Figure 1.
The velocity gradient, dv dx describes the shearing experienced by the intermediate layers as they move with respect to each other.
The velocity distribution will be linear over the distance dx, and experiments show that the velocity gradient, dv dx is directly proportional to the force per unit area, f a .
Where n is constant for a given liquid and is called its viscosity.
Therefore, it can be called the "rate of shear", S. Also, the force per unit area f a can be simplified and called the "shear force" or "shear stress," F. With these simplified terms, viscosity can be defined as follows:
Viscosity = n = s f = shear str ess r ate of shear
Article courtesy of Kelair Pumps Australia “When Pump Knowledge Matters” Phone: 1300 789 466 or visit www.kelairpumps.com.au
DRIVEN SKIDS & TRAILERS
HWR SERIES
VORTEX SERIES
WET PRIME SERIES
VERTICAL TURBINES
SUBMERSIBLE MOTORS
END SUCTION CENTRIFUGAL
DRIVES & PROTECTION
CLEANWATER CENTRIFUGAL
VR SERIES
A comprehensive range of Auto Prime diesel packaged options for fixed and portable installations.
Wear-resistant pumps manufactured with high-chrome white iron to maximize resistance against destructive abrasives and maintain peak performance in light slurry applications.
A unique pumping solution that eliminates costly and disruptive downtime by passing through the most challenging solids using a recessed impeller.
Self-priming pumps designed for reliable solids and clear liquids handling. Continues to reprime automatically after initial priming.
Submersible turbine pumps available in custom configurations to meet demanding application requirements.
Our submersible motors are tough, built to last and come in a variety of construction options.
Close-coupled, electric motor driven pumps available in singleor three-phase standard voltages to fit your site requirements.
Equip a Franklin drive to protect, monitor, and meet the different needs and demands of each application with the same pump.
Centrifugal pumps that feature heavy-duty ductile iron volutes, designed to handle tough applications with high efficiency.
Vertical multi-stage pumps are available in high- and low-speed models for superior durability, efficiency, and performance in a wide variety of applications.