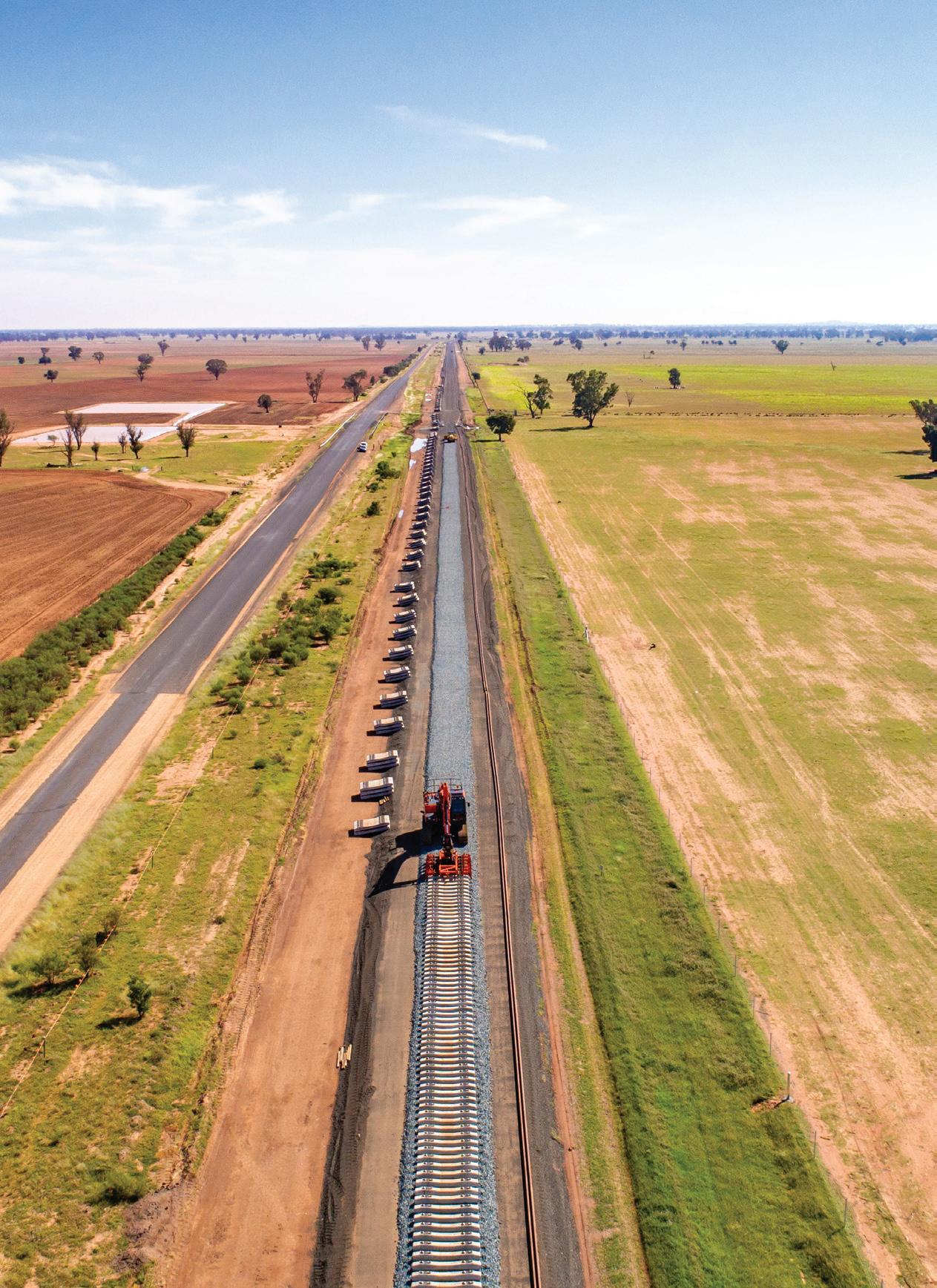
SLEEPER BY SLEEPER:
SLEEPER BY SLEEPER:
When drilling in rock, you need a rig that can take on the tough ground conditions. Vermeer’s latest additions to the HDD market are two new intuitive compact rock drills; the D23x30DR S3 and the D40x55DR S3.
The new DR HDD range has the benefit of superior steering in extreme conditions. They are easy to use, versatile for both rock and clay drilling, and have a quieter noise level at the operator's ear, making them the perfect machines when minimal disruption in urban areas is required. Call Vermeer Australia today for further information.
Monkey Media Enterprises
ABN: 36 426 734 954
204/23–25 Gipps St
Collingwood VIC 3066
P: (03) 9988 4950
F: (03) 8456 6720
monkeymedia.com.au
info@monkeymedia.com.au infrastructuremagazine.com.au news@infrastructuremagazine.com.au
Editor Jessica Dickers
Journalists
Lauren Butler
Imogen Hartmann
Eliza Booth
National Media and Events Executives
Rima Munafo
Brett Thompson
Design Manager
Alejandro Molano
Designers
Jacqueline Buckmaster
Danielle Harris
Marketing Assistant
Stephanie Di Paola
Publisher Chris Bland
Managing Editor
Laura Harvey
Welcome to the last issue of Infrastructure magazine for 2020. It’s crazy to think that we have produced three out of four issues this year remotely and under lockdown in Melbourne due to the COVID-19 pandemic. The upcoming summer is looking cautiously brighter though, with the hope of continued eased restrictions around the country.
Throughout it all, Australia’s infrastructure industry has done a tremendous job in keeping critical assets working and in optimal condition, as well as progressing work on major construction projects. The recently released Federal Budget also shows the significant role infrastructure is set to have moving forward, with the government committing to major funding for transport and road safety projects around the country. You can read a full funding breakdown of the budget on page 14.
One of the biggest milestones the Infrastructure team has hit since our last edition was hosting the inaugural Critical Infrastructure Summit – a series of five Virtual Conferences that ran every Wednesday in September.
Like a lot of other businesses, we had to adapt quickly to the impact of COVID and move the Summit to an online format which allowed infrastructure professionals from around the country to tune in virtually to Critical Infrastructure: State of play; Construct 2020; Asset Management for Critical Infrastructure; Disaster Management; and The Future of Infrastructure
There were so many important discussions at these events and for those that attended, we hope you got a lot of value from our expert speakers. We have covered some of these throughout this issue of the magazine, including key takeaways
from the Summit (page 34), Tony Histon’s Disaster Management keynote presentation (page 70), and the machine learning and artificial intelligence panel from Asset Management for Critical Infrastructure (page 78).
We’ll be running the Critical Infrastructure Summit again in April 2021 so keep an eye on upcoming issues for more information on next year’s event.
In addition to our Summit coverage, this edition also has a big focus on the rail sector as Infrastructure is a media partner for the AusRAIL Live and On Demand virtual event. As confirmed in the Federal Budget announcements, the rail sector will help drive infrastructureled economic recovery thanks to both new funding and the huge projects that are already underway.
Australasian Railway Association (ARA) Chief Executive Officer, Caroline Wilkie, recently said, “The flow on benefits of rail investment will be significant as new projects bring more jobs and sustainable infrastructure that will deliver community benefits for years to come.
“The future of rail in Australia will rely first on improvements to existing infrastructure, followed by the development of new, faster rail connections.”
We’re already seeing these rail projects progress in all states, making it an exciting time to be a rail professional.
As we wrap up the last few months of 2020, I’d love to hear your thoughts and predictions for 2021, as well as what topics you want to hear about.
Infrastructure is proud to be the voice of the industry, especially as we have navigated some uncharted waters this year, and we thank you for your continued support.
Jessica Dickers EditorDefend industrial networks at all levels.
Secure industrial networks with OT-IT integrated security.
Identify and mitigate system vulnerabilities in industrial networks before weaknesses are exploited by a cyberattack.
9 Build reliable and secure networks to maintain business operations
9 Integrate OT/IT perspective on network protection
9 Detect and mitigate cyberthreats for system integrity
9 Protect critical assets with tailor-made OT cybersecurity technologies
Connect with confidence.
Madison Technologies has been distributing Moxa’s reliable networking infrastructure Australia wide for more than 14 years. Our team is dedicated to ensuring our Moxa portfolio is fully supported with an extensive range held locally across our national supply chain, and a team of Moxa certificated sales and technical support engineers.
THE TEN PRINCIPLES FOR AUSTRALIA’S INFRASTRUCTURE-LED RECOVERY
In this excerpt from her keynote address at the Critical Infrastructure Summit 2020, Infrastructure Australia Chief Executive, Romilly Madew, outlines ten principles that should underpin the infrastructureled recovery from COVID-19.
GLOBAL INFRASTRUCTURE
WILL GLOBAL INFRASTRUCTURE BEND OR BREAK UNDER CLIMATE STRESS?
Infrastructure is the backbone of the global economy, connecting people, enhancing quality of life, and promoting health and safety. But climate change is revealing infrastructure vulnerabilities.
INDUSTRY INSIGHTS
STIMULUS FOR INFRASTRUCTURE: THE MARSHMALLOW EXPERIMENT OF SOCIETIES
With infrastructure set to lead a post-COVID economic recovery, Dr Naderpajouh from RMIT looks at the role of developing new infrastructure systems to face challenges and compares the current situation to the famous ‘marshmallow experiment’.
BECOMING AN INNOVATIVE AUSTRALIAN TRENCHLESS TECHNOLOGY CONTRACTOR
HEALTHY HEADS: IMPROVING MENTAL HEALTH IN THE LOGISTICS INDUSTRY
KEY TAKEAWAYS FROM THE CRITICAL INFRASTRUCTURE SUMMIT
BOOKING ACCOMMODATION FOR YOUR UPCOMING INFRASTRUCTURE PROJECT
AUSTRALIA’S BIGGEST RAIL INFRASTRUCTURE PROJECTS
There’s a lot happening in the rail infrastructure space across Australia. From expansions and new metros, to rail linking suburbs and new stations – the rail sector is continuing to boom. With the number of projects running concurrently, we’ve taken a look at some of the biggest rail projects around Australia and their progress to date.
HOW THE RAIL INDUSTRY IS DRIVING A POST-COVID ECONOMY
DIGITALLY ENABLED ASSETS: INFRASTRUCTURE MANAGEMENT FOR THE 20S
USING VULCANISED RUBBER IN TRACK DAMPING SYSTEMS
LEADERSHIP IN THE RAIL INDUSTRY
IoT & CLOUD COMMUNICATION
WHAT’S IN STORE FOR THE FUTURE OF INFRASTRUCTURE?
HOW TO SEAMLESSLY INTEGRATE AUDIO AND VISUAL PASSENGER INFORMATION
RECREATING SOUTH EAST QUEENSLAND IN THE DIGITAL WORLD
THE CIRCULAR ECONOMY IS HERE AND IT'S A BIG OPPORTUNITY
ACCESSING INFRASTRUCTURE SUSTAINABILITY DATA
NORTHCONNEX: MISSING LINK
A GAME CHANGER FOR SYDNEY
Road planners have talked about “missing links” for decades. Like that other cliché to describe big infrastructure – “game changer” – it can sound impressive but mean very little to motorists stuck in traffic. But if there ever was a motorway you could confidently call both a “missing link” and a “game changer”, it’s NorthConnex, which will connect Sydney’s M1 and M2 via 9km twin motorway tunnels.
SETTING THE STANDARD FOR SODIUM SILICATE STORAGE
METRO TUNNEL’S ADVANCE WORK PAYS OFF
DISASTER MANAGEMENT
A NEW PARADIGM FOR MANAGING INFRASTRUCTURE DURING DISASTERS
CONTACT HARALD – THE PLATINUM STANDARD CONTACT TRACING SOLUTION FOR YOUR COVID-SAFE PLAN
MACHINE LEARNING
CHALLENGING TIME FOR AUSTRALIA’S AIRPORTS MACHINE LEARNING AND AI CHANGING THE GAME
THREE SHORTLISTED TO BUILD WESTERN
INTERNATIONAL AIRPORT
PROJECTS ADDED TO THE INFRASTRUCTURE PRIORITY LIST
FEDERAL BUDGET BREAKDOWN – $7.5 BILLION FOR TRANSPORT INFRASTRUCTURE AROUND THE COUNTRY
Lisa is a circular economy and zero-carbon business transformation leader. She has been successfully advising industry and governments in developing new policy frameworks and regulations that bring about market change to enable the circular zero-carbon economy over the past 14 years. This work has covered the energy, water, waste and mobility sectors in the UK and Australia. Lisa established and led the Open Cities Alliance, a peak industry association with unique membership from government to private sector and research organisations. In Australia, Lisa initiated and established the Australian Solar Thermal Association (AUSTELA), advised electric mobility providers, and worked with Flow Systems from a startup sustainable water utility to its major role in shaping a new sustainable water and now multi-utility market.
Transport for NSW Project Director, NorthConnex
One of Australia’s most experienced construction professionals, Pat has enjoyed an outstanding 42-year career in the construction industry. His previous work experience includes the Sydney Harbour Tunnel, Eastern Distributor, M5 East and Cross City Tunnel.
Lachlan BensonInterim CEO Chief Executive Officer, Healthy Heads in Trucks & Sheds Foundation
Lachlan is also the Managing Director of consultancy Blue Arcadia and sits as a Non-Executive Director on a number of industry related boards including the iMOVE Cooperative Research Centre into freight mobility. He has previously been the interim CEO of the Australian Logistics Council, as well as five years as Executive General Manager of Logistics at Sydney Ports Corporation where he oversaw the highly successful Port Botany Landside Improvement Strategy. This built on extensive experience in supply chain management issues gained in other senior logistics roles including as NSW and QLD State Manager for grain exporter AWB Limited, as a Senior Policy Advisor for ports and freight within the NSW Department of Transport and as Manager of the Transport Logistics & Infrastructure Group at Informa Australia.
CEO, Australian Airports Association (AAA)
James Goodwin was appointed Chief Executive Officer of the AAA in June 2020. Prior to this, James was the Chief Executive of Australia’s leading vehicle safety advocate, the Australasian New Car Assessment Program (ANCAP) since 2015. Before joining ANCAP, James held the position of Director – Government Relations & Communications at the Australian Automobile Association and also held a highprofile senior community and corporate affairs position at AirServices Australia. A former journalist and news presenter, James worked for major network news outlets in Sydney and Canberra including several years in the Parliamentary Press Gallery.
CEO, Infrastructure Australia
Romilly is responsible for overseeing Infrastructure Australia’s critical role in helping governments prioritise projects and reforms that best serve our communities. Before joining Infrastructure Australia, she was CEO of Green Building Council of Australia (GBCA) for 13 years. In acknowledgment of her contribution to Australia’s sustainable building movement, Romilly was awarded an Order of Australia in 2019. She is currently a Commissioner for the Northern Territory Economic Reconstruction Commission, Member of Placemaking NSW Advisory Committee, and Independent Chair of the Currawong State Park Advisory Board (NSW). She has sat on numerous Federal Government panels including the Cities Reference Group, National Sustainability Council, Climate Futures Independent Expert Group and the National Urban Policy Forum.
Transmission & Distribution Lead, Accenture Asia Pacific, Middle East & Africa
Tony leads Accenture’s Transmission and Distribution Practice in Asia Pacific, Africa and the Middle East. Over the last 20 years, he has helped utility businesses across Asia Pacific deliver resilient energy infrastructure and systems. Tony develops Accenture’s capability, research and offerings to digitally enable network operations, field work and asset investments. Tony holds an Executive MBA from the AGSM, a Masters in Engineering Science, a Bachelor of Electrical Engineering with Honours and electrical trade certifications.
Three parties have been shortlisted to build Western Sydney International (NancyBird Walton) Airport’s passenger terminal in a major step for the project.
The three shortlisted parties are:
♦ Lendlease CPB Joint Venture (a joint venture between Lendlease Building and CPB Contractors)
♦ Multiplex Constructions
♦ Watpac Construction
Western Sydney Airport CEO, Simon Hickey, said the integrated international and domestic passenger terminal will offer passengers and their families a stress-free travel experience.
“The advantage of designing a new airport from the ground up is taking a fresh, new approach, learning from the global experiences of airports, passengers and airlines,” Mr Hickey said.
“As well as looking at what makes the world’s best airports work so well, we gained insights from our airline MOU partners that helped us design a terminal that will make catching a plane fast and easy.”
The terminal precinct will include a public plaza, retail and dining options, and will be connected to the new M12 Motorway and Sydney Metro – Western Sydney Airport train service.
Mr Hickey said sustainability was a key consideration in the terminal design and will take advantage of natural sunlight and air flows to reduce energy use and create a healthier, more comfortable environment.
The design of Western Sydney International’s passenger terminal is ongoing, and is said to be finalised when the winning contractor is appointed in mid-2021. Terminal construction is due to begin by the end of 2021.
The first stage of Western Sydney International is on track to open in 2026, and will cater for up to ten million passengers a year.
The full line-up of sought after John Deere construction equipment is now available across Australia, supported by trusted and reliable sales and service from AFGRI Equipment and RDO Equipment. They know what it takes to support production-class machines and each is armed with advanced machine monitoring, remote diagnostic capability and world-class parts availability. It’s a New Day and a New Deere.
Infrastructure Australia has added two projects from NSW and ACT to the Infrastructure Priority List, to support the national infrastructure-led COVID recovery.
The construction of Parkes Bypass on the NSW Newell Highway and the upgrade of Canberra’s Commonwealth Avenue Bridge have both been named Priority Projects. Infrastructure Australia Chief Executive, Romilly Madew, said, “With the addition of two new Priority Projects – Parkes Bypass and Commonwealth Avenue Bridge – the Infrastructure Priority List now showcases more than $65 billion worth of nationallysignificant investment opportunities for governments at all levels to choose from.”
The NSW Government’s proposed $172 million Parkes Bypass project involves construction of a 10.5km bypass along the Newell Highway, including bridges over existing railway lines, connections to the Parkes Special Activation Precinct and upgrades to local roads.
Connecting Melbourne and Brisbane, the Newell Highway is a vital freight corridor for consumer, manufacturing and agricultural goods.
The existing highway runs directly through the Parkes town centre, which contributes to congestion and safety risks in the town and limits the ability of high performance freight vehicles to use the corridor.
The Parkes Bypass is expected to help remove heavy vehicle traffic from the town and improve connectivity between local producers and the Parkes Special Activation Precinct, which is being established to leverage the Inland Rail project.
Proposed by the Federal Government, the $124.9 million upgrade to Commonwealth Avenue Bridge will deliver critical safety improvements to an iconic and critical part of Canberra’s transport infrastructure.
The proposal includes structural upgrades to meet modern safety requirements and accommodate the increasing number of vehicles and active transport users travelling on the bridge.
The bridge forms part of the corridor for the planned extension of the Canberra Metro light rail network, which would be assessed under a separate business case.
•Reduce rattle gun use
•Eliminate hot works
•Faster turn-around
•Better productivity
•Fits conventional bolts
•No special tools
Waterjet cutting is a process of precision cutting that utilises high pressure water.
We can process a wide array of materials. Heavy gauge plate, thin sheet stock and composite materials (i.e. carbon fibre, phenolics etc.). It is not uncommon for 6+ inch aluminium and titanium to be cut on waterjets to near final shapes. Edge quality of the parts can vary depending on customer requirements.
We can process anything from a very rough cut for hog-outs, to a very fine edge for precision, finished parts:
Cut up to 6 m x 3 m (20 ft x 10 ft)
Thickness up to 254 mm (10 in)
Improved yield and less waste material
Supplied close to net shape reducing customer machine time
Shorter lead times
Zero heat effected zone
Processing of customer supplied materials
Anew feature roof is being installed for Sydney’s Central Station, as part of the Sydney Metro construction works, creating a new landmark for the city.
Minister for Transport and Roads, Andrew Constance, said the roof over the Northern Concourse is nearly two thirds complete, after workers installed the steel girders, affectionately known as the “hockey sticks”, and cassette roof sections.
“The 80m-long and 40m-wide roof extends from the northern end of
Platform 8 to Platform 16, and will sit more than 16m aboveground to enable natural light to filter into the station,” Mr Constance said.
“More than 500 workers are currently delivering the Sydney Metro works at Central, with more than 5,000 working across the Sydney Metro City and Southwest project.”
The roof structure was manufactured and pre-assembled in the Hunter Valley town of Kurri Kurri, before large sections were transported to Sydney in the middle of the night.
Key highlights about the roof installation include:
♦ 58 cassette sections being installed, each weighing around five tonnes
♦ Largest cassettes are 16m long and 4.5m wide
♦ Eight girders being installed, each weighing 30 tonnes
♦ Longest girders are near the Station Master’s Office, measuring 21m long
♦ 21,000 square metres of existing canopy was demolished for the new roof
♦ Roof has perforated aluminium cladding panels, 21 distinctive diamond-shape skylights, lighting and speakers
Sections of the roof will be progressively installed over the Northern Concourse until the end of 2020, with the Central Walk expected to be open to commuters in 2022. Sydney Metro construction will continue with metro rail services through the city expected to start in 2024.
Absafe Group supplies a comprehensive range of products and services focused on safety and flexibility, with high levels of customisation. As the National Distribution and Service Agent for Sky Climber, Absafe excels in providing the right solution for your access requirements.
The Sky Climber Swing Stage System allows infrastructure workers to set up in any location where wire ropes can be hung, providing extremely flexible and efficient access to structures of any height.
Its modular design and articulation capabilities allow it to fit into all locations.
As the Swing Stage requires fewer parts to access the same working area as a scaffold, it is considerably faster to install and a more cost-effective option for getting tradesmen to the right point, at the right time.
The Alpha series has often been referred to as the most premium hoists in the powered suspended access business. With superior engineering design, they boast a unique traction mechanism which allows wire rope to enter without friction and then squeezes the rope with equally distributed pressure over 360° to attain the lifting traction.
Sky Climber Swing Stages provide significant value through improved efficiency and the reduction of risks, project duration, and disturbances to daily operations. It is suitable to be implemented on new commercial construction, heavy industrial works, maintenance, big projects, and anything in between. The Alpha hoist motors are robust, reliable and safe.
As the primary Australian distributor, reseller, and master service agent of Sky Climber Swing Stage equipment and Alpha hoists, Absafe provides businesses with the opportunity to purchase these products for themselves, saving a considerable amount of money compared to the cost of renting for lengthy projects.
Absafe works closely with companies to develop custom designs to suit each specific scope of work, and provides engineered design and on-site training to guarantee safety, reliability and the perfect match for your task.
Coupled with a highly efficient planetary gearbox, this combination has been a true success in meeting users’ needs. This series is offered in many variations to fit the needs of any project.
If you are having issues with access or are in need of quality safe swing staging, please contact Matthew Van Brink on 0431 299 157 or matt.vanbrink@absafe.com.au. Absafe Group is here to help.
The highly anticipated 2020-21 Federal Budget was released on 6 October and featured significant funding for Australia’s infrastructure industry, including a $7.5 billion investment in transport infrastructure around the country as part of the Federal Government’s COVID-19 economic recovery plan.
Since the start of the COVID-19 pandemic, the government has committed to invest an additional $14 billion in new and accelerated infrastructure projects over the next four years. These projects will support a further 40,000 jobs during their construction.
Some of the key infrastructure funding announcements from the budget include:
♦ $7.5 billion for transport infrastructure
♦ Funding for ‘shovel-ready projects’ including $2 billion for road safety initiatives and $1 billion for the Local Roads and Community Infrastructure Program
♦ Additional $4.5 billion investment in nbn co
♦ An investment of $2 billion for new projects under the National Water Infrastructure Development Fund. This more than doubles the fund to a total of $3.5 billion. Key funding in this includes: $325 million for Wyangala Dam and $242 million for the Dungowan Dam project
♦ Infrastructure Australia has received additional funding in the 2020-21 Federal Budget to provide reform and investment advice in support of the infrastructure-led COVID recovery
♦ An additional $1.2 billion to support Australian businesses to employ 100,000 new apprentices or trainees as part of the COVID-19 economic recovery plan. Businesses who take on a new Australian apprentice will be eligible for a 50 per cent wage subsidy, regardless of geographic location, occupation, industry or business size
The funding builds on a series of infrastructure investments from the Commonwealth in response to the COVID-19 pandemic, which now totals more than $11.3 billion. Prime Minister, Scott Morrison, said the Federal Budget would deliver funding for infrastructure, which supports the government’s JobMaker plan.
“We have been working closely with state and territory governments to invest in the infrastructure that is ready to go and can help rebuild our economy and create more jobs,” the Prime Minister said.
“This investment through the budget will boost the national economy and is part of our plan to support an estimated 30,000 direct and indirect jobs across the nation.”
The 2020-21 Federal Budget includes funding for key transport infrastructure projects across the country. Here is the state-by-state breakdown:
Federal Budget funding: $2.7 billion
Expected jobs created: 8,000 direct and indirect jobs across the state
Total federal infrastructure funding for COVID-19 recovery: $5 billion+
Key transport infrastructure investments for New South Wales include:
♦ $560 million for the Singleton Bypass on the New England Highway
♦ $360 million for the Newcastle Inner City Bypass between Rankin Park and Jesmond
♦ $120 million for the Prospect Highway Upgrade
♦ $491 million for the Coffs Harbour Bypass (bringing the total federal contribution to $1.5 billion)
Federal Budget funding: $1.3 billion
Expected jobs created: 5,150 direct and indirect jobs across the state
Total federal infrastructure funding for COVID-19 recovery: $1.7 billion+
Key investments for Queensland include:
♦ $750 million for Stage 1 of the Coomera Connector (Coomera to Nerang)
♦ $112 million for the Centenary Bridge Upgrade in Brisbane
♦ $76 million for Stage 2 of the Riverway Drive Upgrade between Allambie Lane and Dunlop Street in Townsville
♦ $42 million for the Mt Lindesay Highway Upgrade between Johanna Street and South Street in Jimboomba
Federal Budget funding: $1.1 billion
Expected jobs created: 3,850 direct and indirect jobs across the state
Total federal infrastructure funding for COVID-19 recovery: $1.6 billion+
Key investments for Victoria include:
♦ $320 million for the Shepparton Rail Line Upgrade
♦ $208 million for Stage 2 of the Warrnambool Rail Line Upgrade
♦ $292 million for the Barwon Heads Road Upgrade
♦ $85 million to upgrade Hall Road in Cranbourne
Federal Budget funding: $1.1 billion
Expected jobs created: 6,800 direct and indirect jobs across the state
Total federal infrastructure funding for COVID-19 recovery: ~$1.3 billion
Key investments for WA include:
♦ $88 million for the Reid Highway Interchange with West Swan Road
♦ $70 million for the Roe Highway Widening and Abernethy Road Upgrade
♦ $16 million to undertake sealing of priority sections of the Goldfields Highway between Wiluna and Meekatharra
♦ $16 million to undertake upgrades on the BroomeCape Leveque Road and associated community access roads
Federal Budget funding: $625 million
Expected jobs created: 2,600 direct and indirect jobs across the state
Total federal infrastructure funding for COVID-19 recovery: $785 million+
Key transport infrastructure investments for South Australia include:
♦ $200 million for the Hahndorf Township Improvements and Access Upgrade
♦ $136 million for Stage 2 of the Main South Road Duplication between Aldinga and Sellicks Beach
♦ $100 million for the Strzelecki Track Upgrade
Federal Budget funding: $360 million
Expected jobs created: 2,200
Total federal infrastructure funding for COVID-19 recovery: $410 million+
Key transport infrastructure investments for Tasmania include:
♦ $150 million for the Midway Point Causeway (including McGees Bridge) and Sorell Causeway as part of the Hobart to Sorell Roads of Strategic Importance corridor
♦ $65 million to upgrade the Tasman Bridge
Federal Budget funding: $190 million
Expected jobs created: 1,050 direct and indirect jobs across the territory
Total federal infrastructure funding for COVID-19 recovery: $240 million+
Key investments for the Northern Territory include:
♦ $120 million to upgrade the Carpentaria Highway
♦ $47 million for National Network Highway Upgrades
AUSTRALIAN CAPITAL TERRITORY
Federal Budget funding: $155 million
Expected jobs created: 400 direct and indirect jobs across the state
Total federal infrastructure funding for COVID-19 recovery: $180 million+
Key transport infrastructure investments for the ACT include:
♦ $88 million for the Molonglo River Bridge
♦ $50 million for a South West Corridor upgrade package
An additional $2 billion over 18 months will be directed towards road safety initiatives, continuing efforts to reduce road trauma in Australia. This funding will be under a new Road Safety Program to deliver an estimated 3,000km of lifesaving road improvements and support thousands of jobs right across the country.
The program will deliver works such as new shoulder sealing, rumble strips to alert drivers they are moving out of their lane, median treatments to prevent head-on collisions, and barriers to prevent run-off-road crashes and protect against roadside hazards.
The program will be delivered in three, six-month tranches and on a ‘use it or lose it’ basis. Funds that states and territories do not spend will be re-allocated to those that can, with jurisdictions required to provide road safety data as a key condition of funding.
To monitor and evaluate its progress in this area, the Federal Government is also investing $5.5 million to establish a National Road Safety Data Hub. The Data Hub will establish the first nationally-available road safety data collection to assess the effectiveness of road safety efforts by all Australian governments in the move towards the nationally-agreed target of zero fatalities and serious injuries by 2050.
An additional $1 billion will also be allocated for local governments to enhance local road infrastructure through the Local Roads and Community Infrastructure Program. This will also be on a ‘use it or lose it’ basis.
This builds on the Federal Government’s initial $500 million announced in May 2020. This investment, together with the new Road Safety Program, will support around 10,000 jobs over the life of the projects.
According to Safe Work Australia, in the past two years more than 230 Australians were killed at work, with almost half of this number being employees in the transport, postal, warehousing and construction sectors. What these figures don’t account for though are the near misses and injuries sustained by workers. Technology can help make these incidents more preventable.
Temporary traffic controllers are critical to managing the safe passage of vehicles through road work sites. Traffic control workers, whether working on busy highways, country roads or large private sites, are putting their lives at risk every day to keep others safe.
The number of speeding vehicles, distracted drivers and heavy machinery they deal with on a daily basis can be up to 10,000 vehicles over an eight-hour period. For this reason, it is important for traffic controllers to be able to carry out their duties in a safe environment by removing them from the roadside where possible.
Traditionally STOP/SLOW signs are used by workers to control traffic, but this requires controllers to be next to, or directly on, the road. These signs can be dangerous for a number of reasons: the first being that traffic controllers are directly in the line of fire of incoming traffic; and secondly, they can be difficult to see from a distance in large vehicles.
STOP/SLOW signs can expose traffic controllers to speeding or careless drivers. Relocating the operator from busy roadways removes the greatest risk of injury or death.
The best way to remove workers from harm’s way without compromising a job’s effectiveness is to use a portable traffic light. The PTL Portable Traffic Signal System (PTSS) uses smart and innovative technology to enhance visibility, making it safe and efficient for traffic control operators. Controllers can easily control the temporary traffic lights with a Handheld Remote Control (HRC) at a safe distance from traffic.
After using the PTL system a Traffic Control Manager said, “Keeping my workers safe is the most important thing to me. That’s why I love using PTL. They are simple and easy to learn and make it that much safer for me, my team and the other workers we are protecting.
“This happens not just by removing us from the roadside, but out of the sun, where possible, so we are able to stay alert to manage the traffic in the safest and most efficient way we can.”
With transport authorities all over the country campaigning for more regulations and awareness for safety around traffic controllers, implementing a portable traffic signal is a simple and definitive way to reduce the risks surrounding the work of traffic controllers.
While these devices can require an upfront investment, you can’t put a price on the safety and life of a person.
Madison Technologies’ Portable Traffic Light system is ITS Approved in Queensland and Western Australia, with more states to come. If you would like more information on the PTL, please visit portabletrafficlight.com.au
Portable Traffic Light is the next generation portable traffic signal system, that’s built to last.
9 Portable lightweight design for quick set-up 9 Removes traffic controller/operator from vehicle path 9 Lightweight Hand Remote Controller with backlit low power LCD display 9 Lithium LiFePO4 battery run time of 20+ hours
Highly stable tripod that’s adjustable to suit any terrain
Designed and manufactured in Australia
Connect with confidence.
Madison Technologies is Australia’s and New Zealand’s well-connected supplier of reliable commercial and industrial communications technology products. We deliver comprehensive solutions for our customers’ complex industrial and commercial connectivity challenges. We provide all the products you need in one place, with a streamlined supply chain, responsive team, a comprehensive distribution network, and technical support and training. Contact our team to learn more.
In this excerpt from her keynote address at the Critical Infrastructure Summit 2020, Infrastructure Australia Chief Executive, Romilly Madew, outlines ten principles that should underpin the infrastructure-led recovery from COVID-19.
Australia’s infrastructure sector will be critical as we navigate the rolling series of crises facing our country – drought, flood, bushfires and COVID-19 – as well as the long-term transformation of the economy and the ‘new normal’ of record investment highlighted in Infrastructure Australia’s 2019 Australian Infrastructure Audit
Before the pandemic, over 20 per cent of Australia’s GDP could be attributed to our infrastructure sectors. Given the significant economic contribution of the sector, we should be proud that during COVID-19, the industry has proven that it can be resilient and agile in dealing with a fast-changing landscape.
In addition to infrastructure-led stimulus and recovery plans announced by the Australian Government and numerous state and territory governments, we are seeing a reprioritisation of projects and a greater focus on investments that will deliver the greatest economic benefits.
We have seen an increased focus on resilience, a key theme from the 2019 Australian Infrastructure Audit and our 2020 updates to the Infrastructure Priority List, as well as greater collaboration across the public and private sector as we together work to streamline and fast-track approval processes.
Since the beginning of the dual health and economic crises, Infrastructure Australia has been working closely with the Australian Government, infrastructure bodies in the states and territories, and industry on policy advice to guide the COVID-19 response.
Working collaboratively with our colleagues in the states and territories, our focus has been on improving our ability to move quickly to identify investments that will boost productivity, keep the economy growing and help create jobs.
We are advocating for a staged infrastructure recovery response, beginning with protecting and maintaining the existing pipeline of projects. Mobilising new projects both small and large is the second phase, with industry reform also to be considered as part of Australia’s long-term recovery response.
To support this staged approach and ensure infrastructure can play its role in driving the recovery, we have worked closely with Building Queensland, Infrastructure NSW, Infrastructure SA, Infrastructure Victoria, Infrastructure WA and Infrastructure Tasmania, as well as our counterparts in the NT and ACT.
Together we have established a set of principles that should underpin Australia’s infrastructure-led recovery from COVID-19:
1. Build confidence in the sector and the future project pipeline: support the timeliness of the existing pipeline, address constraints across the sector and prepare for future disruption by accelerating infrastructure planning and approvals, finance and procurement, delivery, maintenance, and renewal.
2. Select projects and reforms that deliver lasting benefits: projects should offer more than short-term stimulus by enhancing productivity, improving sustainability, building resilience, or encouraging innovation.
3. Provide a staged and proportionate response: with the response commensurate to the location and scale of impact on the sector, as well as the appropriate time-scale of interventions.
4. Target intervention: for the regions and industry sectors experiencing the greatest impacts, and with the greatest capacity to benefit from a response, such as building, tourism and retail.
5. Coordinate action across industry and jurisdictions: the industry is interconnected and the capacity of the market finite, so an infrastructure response must be equally
coordinated across all three levels of government, regional development frameworks, and responses to climate and other disasters.
6. Reduce time to market and accelerate delivery: maintain rigour while facilitating timely decision-making, planning approval and funding decisions. Align decision-making frameworks and fast-track approvals within agreed programs or project pipelines.
7. Build industry capacity and capability: through leadership development, building skills and capability, supporting innovation and exchanging experience across the public and private sectors.
8. Increase collaboration and openness in contracting: engage industry early and openly on scope, budget and timing, in return for transparent contracting, supporting industry sustainability. Facilitate reasonable commercial outcomes and provide a foundation for lasting reform.
9. Address the funding challenge and amplify private investment: public funding and reform should unlock private investment or innovation, multiplying the dollar for dollar impact.
10. Remove supply chain bottlenecks: infrastructure supports supply chain efficiency, while benefiting from its effectiveness. Regulation and pricing should be reviewed to ensure it is flexible and outcome focused.
In developing these principles with our colleagues in the states and territories, our aim has been to support a balanced approach to rebuilding right across the nation and the transformation of the economy to the ‘new normal’.
Australia’s response to COVID-19 should progress policy priorities by enabling the long-term sustainability of the sector, building community resilience and transforming the economy. Alongside the State Infrastructure Strategies, the Australian Infrastructure Plan due for release in 2021, will provide a template for this reform.
Jonathan Woetzel, Mekala Krishnan – McKinsey Global Institute; Dickon Pinner, Hamid Samandari, Hauke Engel, Brodie Boland, Peter Cooper, and Byron Ruby – McKinsey & Company
Infrastructure is the backbone of the global economy, connecting people, enhancing quality of life, and promoting health and safety. But climate change is revealing infrastructure vulnerabilities.
When Hurricane Sandy struck the eastern seaboard of the United States in October 2012, subways, airports and roads were flooded, causing transportation to grind to a halt. Millions lost power, some for days or weeks, shutting down businesses and creating public safety issues. In addition to winds knocking out a quarter of mobile phone towers in the Northeast, the loss of electricity forced many towers offline after depleting their emergency batteries. $11 billion gallons of sewage flowed into rivers, bays and coastal waters because severe inundation overwhelmed municipal wastewater systems.
In total, the storm caused about $70 billion in damages. But despite being one of the costliest and most destructive storms on record, this event was not an aberration. Nine of the costliest mainland US hurricanes on record have occurred in the past 15 years. Going forward, climate change is expected to further intensify these risks.
Infrastructure usually involves large investments in assets that are designed to operate over the long term. For example, coal-fired plants are designed for 40 to 50 years, and hydropower dams and large geotechnical structures for up to 100 years. To date, the design of these facilities typically has assumed a future climate that is much the same as today’s. However, a changing climate and the resulting more extreme weather events mean those climate bands are becoming outdated, leaving infrastructure operating outside of its tolerance levels. This can present direct threats to the assets, as well as significant knock-on effects for those relying on the services those assets deliver.
HOW FOUR GLOBAL INFRASTRUCTURE SYSTEMS ARE IMPACTED BY CLIMATE CHANGE
This article examines four critical infrastructure systems –the electric power grid, transportation, telecommunications, and water storage, treatment, and purification – to determine how vulnerable global infrastructure is to a changing climate.
In the four major infrastructure classes, we identify a total of 17 types of assets to evaluate against seven global climate hazards: tidal flooding amplified by sea level rise, riverine and pluvial flooding, hurricanes/typhoons and storms, tornadoes and other wind events, drought, heat (temperature increases in both air and water), and wildfires. Each type of infrastructure system has specific elements vulnerable to specific climate hazards. We map those hazard infrastructure intersections where risks will most be exacerbated by climate change.
Overall, we find that climate change could increasingly disrupt critical systems, increase operating costs, exacerbate the infrastructure funding gap, and create substantial spillover effects on societies and economies1. We find that there is a range of unique vulnerabilities of different types of infrastructure assets to different categories of climate hazards. Few assets will be left completely untouched.
In certain countries, heat-related power outages could increase in severity and may push the grid to cascading failure. Aircraft could also be grounded more frequently as both planes and airports cross heat-related thresholds.
Understanding these differences is crucial for successful planning. To that end, we have produced a heat map that explores the risk of potential future interruptions from typical exposure to climate hazards by 2030 (Exhibit 1).
Our analysis reveals two different sets of risks involving infrastructure: direct (for example, a power plant goes offline because it floods) and indirect (for example, a power plant cannot transmit power because the power transmission lines have gone down). A typical asset’s direct risk is estimated in our heat map analysis. But direct vulnerabilities are only half the story. Risk is further exacerbated by the vulnerabilities of a specific infrastructure asset to failures in the infrastructure systems within which that asset is embedded.
These dependencies can spread risk. We find that each system (for example, energy and water) has at least one severely vulnerable element. Because of the interdependency of these infrastructure systems, the high-risk assets may represent critical points of failure for the entire system, causing operational losses for all other assets in the chain and knock-on effects for a broader set of institutions and individuals.
The power grid is highly vulnerable to climate risk from both acute and chronic impacts, amplified by fragile components and relatively low redundancy. The effects of climate-related hazards on the power grid are already apparent. Higher temperatures lower generation efficiency, increase losses in transmission and distribution, decrease the lifetime of key equipment including power transformers, boost peak demand, and force certain thermoelectric plants offline. Day to day, these pressures cause rising operating costs and reduced asset life. In rare cases, these stressors can overwhelm the grid and lead to load shedding and blackouts.
Instances and associated costs of disruptions to the power
grid are likely to rise as temperatures increase. As average heat levels increase, so does the frequency of extreme heat events and the duration of less severe periods of higher than average heat that cause efficiency losses. Hot periods will be hotter than systems are used to, increasing the degree of failure and thus the associated recovery times, lost revenues, and repair costs.
Transportation infrastructure is widely distributed, interconnected, and can be affected by relatively minimal climate hazards, resulting in significant societal impacts. For example, extreme heat is already disrupting global air travel. In July 2017, approximately 50 flights were grounded for physical and regulatory reasons when temperatures in Phoenix, Arizona, skyrocketed to 48° Celsius.
We analysed the effect of extreme heat on global air travel. Assuming regional aircraft are largely similar to today’s and keeping the number of regional flights constant to isolate climate impact, if no adaptation measures are taken (for example, lengthening runways or improving aircraft technology), this translates into about 200 to 900 flights grounded per year by 2030 and about 500 to 2,200 flights by 2050. This could directly affect about 16,000 to 75,000 passengers per year in 2030 and about 40,000 to 185,000 passengers per year in 2050, up from an estimated 4,000 to 8,000 today (these events are not currently systematically recorded) from extreme heat.
More or fewer passengers may be affected depending on whether heat waves strike on heavier travel days (when flights are fuller) and how long the heat conditions persist. Air transportation delays cost the US economy $4 billion USD (approximately $5.6 billion AUD) in 2007, with most direct costs falling on passengers.
Water supply systems can also experience long-lasting outages from acute shocks like hurricanes and flooding. Two weeks after Hurricane Katrina in 2005, 70 per cent of affected drinking water facilities were still offline. Flooding can also result in long recovery periods. Effects are more dramatic in the developing world, where contamination of drinking water is common, and cholera and E. coli frequently cause widespread diarrhea outbreaks in the aftermath of floods. Water treatment systems, however, such as desalination plants, could be increasingly used to limit the impacts of drought.
Wastewater systems also suffer as a result of climate shocks. During drought, sewers can have inadequate flow, resulting in blockages and the inability to process human waste. Blockages lead to the possibility of sewerage systems bursting in the middle of urban areas. But the biggest threat to wastewater systems is flooding, particularly during hurricanes. Similar but more gradual wastewater overflows are also happening because of chronic stresses.
A fast-growing sector, telecommunications infrastructure has more agility and redundancy, yet as the world’s dependence on the communications network increases, climate risks will also grow. High winds or trees can topple cell phone towers and telephone poles, blow down telephone lines and base stations, and knock microwave receivers out of alignment. Aboveground cabling is more at risk than buried lines of support and pole failures, damage from debris and falling objects (such as trees), and breakage from tension caused by extreme wind speeds.
Flooding and hurricanes are the biggest global threats. In 2015–16, floods in the United Kingdom inundated a number of key telecom assets, cutting off thousands of homes, businesses and critical public services such as the police. Hurricanes Irma and Maria caused devastation to telecom infrastructure in the Caribbean, with over 90 per cent of mobile sites destroyed in Puerto Rico, St Martin, Dominica, Antigua and Barbuda. These threats interfere with the system just when it is needed most for disaster recovery.
Infrastructure is expected to bear the brunt of anticipated climate change adaptation costs, typically estimated to be between 60 and 80 per cent of total climate change adaptation spending globally, which could average $150 billion to $450 billion USD per year on infrastructure in 2050.
However, most estimates of the cost of adaptation relative to current assets are small compared with the scale of infrastructure investment. Estimates vary significantly, but consensus puts adaptation spending for new assets at about one to two per cent of total infrastructure spending a year.
Adaptation should be tailored to the specific hazard and infrastructure risks. However, opportunities exist for adaptation that are relevant for all infrastructure sectors. Examples of ways to adapt current and future infrastructure to climate risks can be considered, including by:
♦ Reducing exposure through transparency
♦ Accelerating investment in resilience
♦ Mobilising capital to fund adaptation
How global infrastructure evolves over the next 50 years may be a major determinant of the impact of climate change on civilisation. More money will need to be spent both on and in support of infrastructure, and in new ways. Building slightly higher walls, metaphorically or literally, may not be the best solution. And the risks extend beyond infrastructure.
A failure to adapt by not taking climate change into account in the design, construction and maintenance of infrastructure assets will not only cause costs to owners and operators, but will leave entire communities exposed and vulnerable. Adaptation can deliver a strong return both by reducing costs from climate-related damage to infrastructure itself and by avoiding significant knock-on effects in wider society.
¹Climate science makes extensive use of scenarios ranging from lower (Representative Concentration Pathway 2.6) to higher (RCP 8.5) CO2 concentrations. In our analysis, we have chosen to focus on RCP 8.5 because the higher-emission scenario it portrays enables us to assess physical risk in the absence of further decarbonisation. (We also choose a sea level rise scenario for one of our cases that is consistent with the RCP 8.5 trajectory). Such an “inherent risk” assessment allows us to understand the magnitude of the challenge and highlight the case for action. For a detailed description of the reason for this choice, visit McKinsey.com/climaterisk
With infrastructure set to lead a post-COVID economic recovery, Dr Naderpajouh from RMIT looks at the role of developing new infrastructure systems to face challenges and compares the current situation to the famous ‘marshmallow experiment’.
Increasingly we hear about economic recovery in response to the COVID-19 pandemic and its consequent recession.
The recovery revolves around stimulus packages at the global level such as the economic stimulus plan by the European Commission, at the country level such as the US or Australian Governments’ stimulus packages, or at the local level such as the economic recovery package by the City of Melbourne. Within the response mechanisms there is often encouraging news about the focus on infrastructure.
The focus on infrastructure is remarkable news, as infrastructure systems tend to be neglected in comparison to other competing priorities. There is an old saying that nobody thinks about infrastructure systems such as sewerage or utility networks until they stop working. In this context, we should be pleased that there is a potential for investment in infrastructure and politicians, corporations and communities can play a role in pushing infrastructure to the top of the agenda on any fiscal discussion including the stimulus package.
However, news of infrastructure investment within such stimulus packages often point to short-term economic gains such as employment and productivity impacts (productivity often referring to GDP). This should always be taken with a grain of salt.
A primary purpose of infrastructure systems is to serve the needs of communities and societies in the long term. They are often capital-intensive projects that have a substantial impact on societies and lock us in for decades. Therefore, we should be very cautious and ensure that short-term economic gains such as employment and productivity do not jeopardise the selection of alternative infrastructure systems.
The selection of alternative infrastructure systems and prioritising investment is a complex process involving a range of criteria. Theoretically, the core of a decision-making process is cost-benefit analysis that is also practically driven by the power relation between the proponents of the projects. While the majority of cases include social and environmental criteria in addition to economic and technical criteria, historical trends suggest that market driven criteria often dictate the final selection of alternative infrastructure systems.
Therefore, in cases such as economic recovery, there is a need to give greater weight to social and environmental criteria. This is because investment in infrastructure is already providing market driven gains of economic recovery.
The temptation to sacrifice long-term quality of life driven by well-planned infrastructure versus short-term economic gains is hard for societies to resist. The case of selecting infrastructure systems for economic recovery post-pandemic is similar to the marshmallow test.
The marshmallow test is a famous social science experiment on delayed gratification that was first conducted at Stanford University in the 1970s. In the study, children were put into a room by themselves with one marshmallow on a table in front of them. The children were told that once the researcher left the room they could either eat the one marshmallow straight away, or wait a period of time until the researcher got back, and then they could instead have two marshmallows.
Organisations facing the urge of snapping back are sitting behind the desk and can’t take their eyes from the potential stimulus package in front of them. But the communities who collectively weigh their decisions and consider the long-term
implications for resilience and quality of life, will also enjoy the long-term benefits of the service of infrastructure that is designed to be fit for the communities’ needs and new environmental realities.
The difference is that unlike the kids in the marshmallow test that just need to wait to get their reward, organisations need to work hard to refine their selections. Here are my five suggestions for the way forward.
1. There is a need to give extra weight to quality of life, liveability and resilience criteria in the selection of alternative infrastructure for investment, especially focusing on the priorities such as social equality. This is especially important as the infrastructure projects within the stimulus package are already satisfying economic needs of creating jobs and increasing productivity, therefore, they need to have higher focus on social and environmental criteria and less on market criteria to offset the high bias to market.
2. These times are perfect windows for innovation. For example, we could have a proportion of the projects to be prioritised based on a different set of criteria (purely social and resilience oriented), and assign a certain proportion of the stimulus package to the projects that are prioritised in this separate list.
3. We can encourage communities to develop shovelready projects, and invest in efforts to engage them in the development of projects. Major corporations and political parties use the post shock times very efficiently to drive their preferences. Communities can learn and can be assisted financially and technically to engage in the development and selection of their infrastructure systems through the stimulus package. This is the perfect time for community-driven projects, the ones that are often pushed back in normal situations. If a community needed an infrastructure system and had constantly faced challenges such as lack of budget, now they should vehemently pursue the stimulus package for their long due infrastructure needs.
4. Another major point is the diversification of the economy, which will be based on diversification of related infrastructure. The stimulus package should target infrastructure systems that we do not fund in normal situations to diversify the economy.
5. Maintenance and future-proofing of existing infrastructure is also very important. This is especially true given that they are not prioritised compared to new projects in normal situations because there is no ribbon cutting involved.
Considering all of these recommendations, the most important point is to make sure no processes and regulations are overlooked, and all the checks and balances in the processes are followed. In the volatile environment of the new normal, we cannot afford low-quality infrastructure that is not well planned.
We must learn from Australia’s history of building defects, such as the combustible cladding issue and the poor execution of apartments, to ensure necessary processes are followed and that we do not compromise our long-term quality of life with solely focusing on short-term market driven economic benefits.
This is a perfect time for community driven projects, and part of stimulus can help communities define their needs
Vermeer is a pioneer of trenchless technology – one of the broad range of complementary technologies offered by the company for underground service installations. Here, Aaron Forbes, Director of Versatile Services Australia (VSA), explores what Vermeer Australia means to an innovative trenchless technology contractor.
We started in early 2018 with the aim of filling a need for a modern underground utility specialist focused on smaller, more technically challenging projects. Two years later, we have a staff of 12 and have expanded beyond our Perth base into the Sydney market, with NBN installation and maintenance being an important part of our work.
I’ve been in the industry for 20 years, working my way up from an offsider position to a plant operator, then site management and construction management until becoming a director of a Horizontal Directional Drill (HDD) company.
I was trained on a Vermeer 7x11A and 16x20 15 years ago, and I’ve worked with Vermeer Australia ever since as I had great experiences with it early on. As I moved into management roles, I got to appreciate the team that supports Vermeer equipment more, so it’s a combination of the equipment itself and the company that supports it.
Vermeer Australia has the traditional sales and support values of a company that has been working with Australian contractors – both large and small – for 30 years. This capability has been further extended with Vermeer Australia now a fully owned part of the RDO Australia Group – one of the largest specialist equipment dealer organisations in the world.
Our D24x40DR was a good reliable machine for the work we did at the time, but we needed a bigger machine for the Sydney work which is mostly hard rock and limestone. The results have been consistently outstanding; we often rack out the drill in solid rock without complications, racking out up to 250m a day, many times in complete rock conditions. Our operators love how easily it handles difficult conditions, particularly the D40x55DR’s automated system which has made getting through the sandstone on the Sydney jobs a breeze. Its reliability and strength in the inner rod system is incomparable to any other drill manufacture.
We are currently focusing on tightening our internal gears so we may expand outward. This refers to both an increase in manpower but also machinery. We hope to continue to expand our network of Vermeer drills and other machinery on an ongoing basis. With the high volume of work we are seeing begin to appear in WA, our next step for this goal would be to attain some more heavy duty Vermeer drills to match our Sydney capacity.
We’ve enjoyed good support from Vermeer, whether in Perth or in Sydney. As someone who has worked in all ranks within the drilling industry, I can confidently recommend Vermeer to any and all users. Yellow iron all day, every day!
For more information on Vermeer’s products and services, please visit vermeeraustralia.com.au
The need for a national mental health body for the freight and logistics sector has reached a critical point. Infrastructure spoke to mental health and wellness initiative, Healthy Heads in Trucks & Sheds, Interim CEO, Lachlan Benson, about the goals of the organisation and what can be done to improve mental health outcomes for workers in freight and logistics.
Alot of time, effort and finances are invested in minimising and eradicating workplace accidents. However, there is often an aspect of workplace safety that is overlooked – mental health and wellness. One industry that is especially susceptible to poor workplace mental health is the freight and logistics sector.
Realising the critical need for improved workplace mental health in the freight
and logistics industry, national initiative Healthy Heads in Trucks & Sheds is looking to raise awareness and improve the lives of workers across the whole sector.
Healthy Heads in Trucks & Sheds is the national body responsible for the promotion and management of improved mental health and well-being
outcomes for the freight and logistics sector. From truck drivers and delivery drivers, to warehouses and head offices, Healthy Heads is working with industry to create conversations, provide support and improve the mental health and well-being of workers to ensure they are happy and healthy.
“The aim of Healthy Heads in Trucks & Sheds is to deliver a single national mental health plan to road transport and logistics industries,” Mr Benson said.
“The principal object of the foundation is to promote the prevention and control of mental health issues in truck drivers, distribution centres, warehouse staff, and other road industry participants, as well as to support healthier options around diet, exercise and individual well-being.”
The Healthy Heads in Trucks & Sheds initiative was officially launched on 18 August 2020, marking two years of preparation work that involved raising awareness, creating support systems and national industry initiatives.
“It began as a working group, and then a steering committee of the major transport logistics industry players and their customers,” Mr Benson said.
“It’s been driven very heavily by those founding members, particularly Woolworths, Coles, Linfox, Toll, Qube, Ron Finemore Transport and Australia Post, all of whom have had senior representatives involved in the process since day one to tackle the issue of mental health, which they saw as a challenge, not only in their own businesses, but across the sector as a whole,” Mr Benson said.
Statistics show that mental health in this industry is a major issue, not just for individual workers, but also companies both large and small.
Mr Benson said that factors such as long hours, shift work, contact work, fatigue, isolation, traumatic critical incidents, and being away from friends and family for extended periods of time, all contribute to poor mental health outcomes.
“If you look at the statistics across the sector, we’re at a point where almost one in two workers in the sector will experience a mental health issue. Of those, close to 40 per cent of them will say that that issue was caused, or exacerbated by work.”
Furthermore, Mr Benson said that surveys indicate that over 13 per cent of truck drivers have been diagnosed with depression, meaning there are tens of thousands of drivers across the country struggling with potentially fatal mental health issues.
“What we are seeing is that drivers who have depression are seven times more likely to be involved in a crash. But even when you look at the well-being piece, the leading cause of death in this industry is heart attack, heart disease and suicide. These are significant issues.
“In fact, when looking at the major statistics from the Super industry around the sector, you’ll find that mental health is the second highest disability claim consistently,” Mr Benson said.
With the COVID-19 pandemic forcing numerous sectors to slow down and even shut up shop for months, the exact opposite is happening in the freight and logistics sector. As panic buying swept the nation at the beginning of the lockdowns in Australia, and more people requiring home delivery as retail outlets closed, the demand for goods has risen exponentially. This has caused a massive strain on workers and resources across the sector and resulted in heavier workloads than ever before.
“It has undoubtedly been a very tough period for the freight logistics sector, very tough,” Mr Benson said.
“This has placed incredible stress on supply chains, because at the same time as everyone was being asked to stay at home, we were asking the people in our sector to keep working, and to work above and beyond to keep supply chains functioning.
“It was effectively like the equivalent of Christmas day every day.”
The lockdowns have been especially difficult on truck drivers who are facing a number of unique challenges and restrictive rules, causing even more isolation and concern than usual. Mr Benson said that what many people didn’t realise is that when businesses closed, truck stops also closed, which prevented drivers across the nation from accessing these integral safe spaces.
“That’s the lifeline to keeping those guys on the road and actually their only place of social interaction on those deliveries. To either talk to someone behind a counter, or over a cup of coffee next to their truck,” Mr Benson explained.
“So we actually increased the pressure on them by initially shutting those facilities, and took away their support mechanisms. Fortunately, that decision was reversed very quickly.
“By the same token, when you look at environments around the border closures, there are different rules for borders, so it’s difficult for a transport operator because he’s obviously doing a job and delivering essential goods to people across the country. But in the back of his mind is the question, ‘Will I be able to get home again?’. That’s pretty tough for someone.”
Yet throughout the difficult circumstances and pressure on workers, Mr Benson said that the sector should
be recognised for its role in helping to keep the economy afloat and businesses open.
“It’s been a period of heightened pressure for the sector, but the sector should be equally commended for its efforts in keeping the economy open, and keeping the economy moving,” Mr Benson said.
The culmination of industry challenges, coupled with the added stress of the pandemic, has highlighted the drastic need for better mental health support of workers to not only save lives, but improve business outcomes for companies – leading to more jobs and happier workers.
In fact, Mr Benson said that it has been demonstrated that for every dollar that goes into mental health in the transport sector, there can be up to a $2.80 return. This can be seen through improved worker productivity, reduced sick leave and longer serving employees.
Mr Benson also said that as an industry it is integral for the larger companies to pitch in and help out the smaller-scale businesses who may be struggling to fund and implement health initiatives in their teams, creating a holistic approach to mental wellness across the sector.
“Those companies that have invested in mental health, which is typically the larger end of town where they have the resources to do so, have mental health programs. The challenge is that the majority of the industry, starting with single-owner drivers, through to mum and dad transport companies or warehouse companies, and family businesses, is where we need to get the most help, and that’s what Healthy Heads is about.
“This is about the big end of town
coming together to support the industry as a whole. We’re doing this for the whole industry. If we don’t look after the people in our sector, we’re not going to have people to drive our trucks or work in our warehouses.”
Mr Benson said the work of Healthy Heads is centred around three main pillars of action: training, standards and wellness. These three pillars inform initiatives with the aim of improving mental health and wellness across the sector including:
♦ Increasing and introducing more trained mental health care professionals at transport and freight facilities, including warehouses, distribution centers and truck stops
♦ Standardising policies and regulation at transport and logistics facilities, forming a cohesive and industry-wide standard of operations
♦ Focusing on the physical, dietary and overall mental wellness of individuals
However, Mr Benson said that the Healthy Heads initiative is only as strong as the support it receives from the industry. It is integral for companies to back the foundation and support the advancement of mental health programs that are available and accessible to all.
“This is an industry for industry solution, and we are only going to be successful if we have all of the industry behind us. We want to work with everyone, and to support all the excellent initiatives that are going on around mental health in the sector.
“What we need is for companies to reach out to Healthy Heads and get involved in the campaign, and to put their resources behind what we’re trying to achieve. We can’t do it on our own, we need the support and participation of the whole industry.”
If you, or someone you know, is experiencing a personal crisis, or needs someone to talk to, please reach out for help.
Lifeline: 13 11 14
Beyond Blue: 1300 22 4636 or beyondblue.org.au
Beyond Blue Coronavirus support service: 1800 512 348 or coronavirus. beyondblue.org.au
Headspace: 1800 650 890 or headspace.org.au
Suicide Call Back Service: 1300 659 467 or suicidecallbackservice.org.au
The inaugural Critical Infrastructure Summit featured five Virtual Conferences running every Wednesday in September, thousands of delegates tuning in, and a speaker lineup of leaders from across the infrastructure sector offering their expertise on current challenges, major construction projects, asset and disaster management, and future industry predictions.
It was a huge month, kicking off with Critical Infrastructure: State of play; then Construct 2020; Asset Management for Critical Infrastructure; Disaster Management; and wrapping up with The Future of Infrastructure.
Each Virtual Conference in the Summit had more than 1,000 people register and featured important discussions on the most pressing issues facing Australia’s infrastructure industry.
Romilly Madew, CEO of Infrastructure Australia (IA), opened the Summit with her keynote presentation outlining ten infrastructure principles IA has agreed upon with its counterparts in the states and territories as part of the postCOVID recovery. Romilly wrote an article to go alongside her presentation, which you can read on page 18 of this issue.
We also had Mark Crosweller AFSM, Head of National Resilience Taskforce at the Australian Strategic Policy Institute, share his expertise in developing resilience in an increasingly complex global environment. Delegate Scott Ryall said it was “one of the most thought-provoking presentations I
The last six months in infrastructure. Kirk Coningham, CEO, Australian Logistics Council; Marie Lam-Frendo, CEO, Global Infrastructure Hub; and Chris Melham, CEO, Civil Contractors Federation (National) created a fascinating discussion, not only around how their sectors have been impacted by COVID-19, but also at issues around skills, data and infrastructure funding.
Construct 2020 delivered fantastic insights into some of the country’s biggest infrastructure projects. The conference kicked off with welcome remarks from the Hon Michael McCormack MP, Deputy Prime Minister, and Minister for Infrastructure, Transport and Regional Development.
He said the government is accelerating works under the record $100 billion blueprint and he had some words for our delegates throughout the construction industry.
“Our national construction sector represents 8.4 per cent of Gross Domestic Product, supporting more than a million Aussie jobs. This means infrastructure will help lead us through the worst of this pandemic and into the light at the other end.
“You are all an integral part of this and the government thanks you for your commitment, your dedication to infrastructure development, especially at this tough time.
“Together we're doing two vital things, tackling the current downturn right now, but importantly, using this to build
Our keynote speaker Priscilla Radice, CEO, Infrastructure Association of Queensland, further built on the idea that we need a mix of “short run and long run projects; small spend and larger spend; local and regional; place-based and interregional projects – that together create a legacy.”
Priscilla gave a great exploration of Queensland’s role for infrastructure in revitalisation; including the future of its cities, the industry ecosystem, and new models for growth. After a higher level look at the pipeline and project funding, we then delved deep into some technical construction information on three of the biggest construction projects underway in Australia, across different sectors.
Tom McCormack, Chief Information Officer, Western Sydney Airport, outlined the construction task ahead for the Western Sydney Airport, and how the project will become Australia’s first smart airport.
Paul Thomas, Deputy Director of Tunnels and Stations, Rail Projects Victoria, gave delegates a closer look at the Melbourne Metro Tunnel project with an informative exploration of the current and future works.
Then Peter Engelen, GM Planning and Infrastructure, NSW Ports, closed the conference with a detailed analysis of construction works at NSW Ports, such as the on-dock rail at Port Botany.
Peter Seltsikas, Senior Manager, Asset Management at SA Water, gave delegates advice on how to develop strategic asset management plans in an uncertain future.
He explored concepts around connecting with customers, building capabilities, and resilience, but one of the fundamental takeaways was about really understanding how your assets are performing, something that SA Water is doing with the implementation of smart technology on its water main networks.
“Better understanding of asset performance will allow you to make the best decisions in an uncertain future,” Peter said.
Then, Matt Henson, Asset Management Systems Manager and Acting Lead for Asset Systems & Assurance at Jemena, gave us a detailed presentation on the interplay between asset management, risk management, resilience and change adaption.
We were also joined by Nicola Belcher, Director of Rail Assets, Projects and Compliance at the Victorian Department of Transport; Russell Riding, Automation Team Leader at Melbourne Water; and Bruce Thompson, Executive Director Spatial Services at the NSW Department of Customer Service, for the industry panel The role of machine learning, AI and digital twins in asset management. You can read some of the key discussion points from this panel on page 78.
Wrapping up the event was Bradley Hocking, Program Lead, Asset Management Systems at Shoal Group, who provided some great industry case studies looking at the work he’s done on an innovative Asset Management System Framework.
We were fortunate to have Tony Histon, Transmission & Distribution Lead, Accenture Asia Pacific, Middle East & Africa, deliver the keynote on achieving resilience through a new harsh reality, and then stick around for an extended Q&A session to give delegates the chance to join in on the conversation. Tony also delved deep into his presentation topic in the article on page 70.
Then we were joined by Mark Cannadine, Manager Business Resilience, ElectraNet SA; Victoria Chantra, Associate DirectorEnvironment, AECOM; and John Kilgour, CEO Civil Contractors Federation, Victoria, for the industry panel Preparing for the next disaster: how can we be ready for whatever is in store
John provided interesting insights on how the construction industry is coping with COVID-19; Victoria was able to speak to the importance of ensuring sustainability is embedded into the heart of the work we do to rebuild in the years to come; and Mark reflected that while there has been enormous change this year, it has brought opportunity. What we have learned this year, as organisations, is just how adaptable our people are.
Adrian Hart, Associate Director - Construction and Maintenance at BIS Oxford Economics, looked at future infrastructure opportunities and challenges. He said that over the next two years the sectors that will experience the strongest growth are transportation sectors including bridges, railways and roads.
On the other end of the scale, telecom and pipelines, as well as utilities sectors, electricity and water, will have the least amount of growth. One major point in Adrian’s presentation was about sustainability in infrastructure, from sustainability of funding to environmental factors.
Then, Yale Wong, PhD, ANZ Market Lead (Public Transport) at the Cities Forum, presented lessons for public transport, infrastructure, procurement and the future of our cities. With a focus on Australia’s public transport, Yale explored what our systems could look like post-pandemic, including the use of technologies (sanitation, predictive analytics, artificial intelligence); creating agile and resilient operations; and reforms in the public/private incentivisation model.
He looked at how Mobility as a Service (MaaS) and travel demand management (TDM) can allow us to leverage the potential of active and micro-mobility modes to better spread demand. He also outlined a series of policy recommendations and said, “We stand at a critical juncture to leverage this crisis into an opportunity to remake our cities and communities for the better.”
We were then joined by Caroline Wilkie, CEO, Australasian Railway Association (ARA); Claire Parry, Managing Director, Infrastructure Skills Advisory; and Radmila Desic, Queensland Women on Tools Committee Member and Lifetime Member, National Association of Women in Construction (NAWIC), for the industry panel The future of skills and training
This was a fascinating discussion and a great way to end the conference, and the entire Summit. Our panellists talked about a number of pressing industry topics, everything from current skills shortages, to the impact of evolving technologies; areas workers should be upskilling in; and encouraging the participation and training of underrepresented groups including women, Indigenous workers, and young people.
The Critical Infrastructure Summit will be running again in April 2021. As we saw from this year, a lot can change in six months, so we’ll be bringing you an update on where the infrastructure industry sits next year and explore some of the biggest topics and challenges across different sectors. Keep an eye on Infrastructure magazine for further announcements on next year’s Summit
COVID-19 has caused disruptions to many infrastructure projects with strict restrictions in place. But now that plans have been announced for an infrastructure-led economic recovery, project managers must ensure they have everything ready for future work.
With more than 60 locations across Australia, Nightcap Hotels is the hotel group of choice for the infrastructure industry and can accommodate all trade needs as projects start to ramp up.
One critical component of projects that is often forgotten is securing affordable, comfortable and convenient accommodation for workers. Location and affordability are key when it comes to choosing accommodation. You’ll need to choose a hotel that is close to the project site but won’t take up a huge part of your budget, while still providing somewhere that workers enjoy staying.
Having accommodation close to project sites saves valuable time, allowing workers to spend less time commuting and more time on-site. There are 19 Nightcap Hotels in VIC, 14 in NSW, 12 in QLD, eight in SA, four in WA, and three in TAS – all in areas where the industry has major projects underway. Nightcap Hotels offers workers the opportunity to maximise productivity without compromising on comfort.
The hotel group has amenities in place to cater specifically for infrastructure professionals, including large vehicle parking to accommodate trucks and machinery, which is one less thing to worry about.
Workers also have access to high speed WiFi, 40-inch smart TVs, a welcoming on-site bar and bistro that both offer discounts to the infrastructure sector, as well as Australianmade King Koil beds to relax at the end of a hard day on-site.
There’s a lot happening in the rail infrastructure space across Australia. From expansions and new metros, to rail linking suburbs and new stations – the rail sector is continuing to boom. With the number of projects running concurrently, we’ve taken a look at some of the biggest rail projects around Australia and their progress to date.
At 1,700km, the Inland Rail project is currently the biggest freight rail infrastructure project in Australia. The project will link ports between Brisbane and Melbourne, providing a 24-hour or less transit time for goods between, and along, the two cities.
The project is estimated to cost $10 billion with a ten-year delivery schedule and is estimated to benefit Australia’s GDP by $16 billion during its construction and first 50 years of operation, while delivering 16,000 new jobs at the peak of construction.
Construction of the rail infrastructure was split into 13 smaller projects that span across Victoria, New South Wales and Queensland, and includes upgrading 1,100km of existing track and building 600km of new track.
The first section of the Inland Rail construction, the Parkes to Narromine section, was completed in September 2020. The project has also implemented a new procurement strategy in line with the Australian Government’s commitment to fast-track investment in critical infrastructure projects and is in response to industry feedback.
As part of the Federal Government’s 2020-2021 budget, the government announced that it will make a $150 million investment into additional grade separations on the project’s alignment in New South Wales.
METRONET is Western Australia’s governing body for Perth’s biggest rail project and manages multiple projects, including new railway lines, extensions, station construction and upgrades, level crossing removal and signalling.
Once completed, the project will deliver 78km of new passenger rail as well as 18 new stations, helping Perth communities grow and travel.
In early August 2020, the first kilometre of the $1.86 billion 8km METRONET Forrestfield-Airport Link rail was laid, following the completion of tunnelling in April. Following this breakthrough in the project, the Western Australian Government awarded a $36 million contract for METRONET tracklaying work at Claremont Station.
There have also been ongoing contracts and procurements for portions of the project, with the latest Request for Proposal focusing on starting work on the Byford Rail Extension, with the main contract to be awarded in mid-2021.
In one of the biggest undertakings in rail infrastructure for Melbourne, the Melbourne Metro Tunnel will create a new end-to-end rail line from the city’s west to the south-east. The project is estimated to cost $11 billion and will feature high capacity trains and five new underground stations.
The project includes twin 9km tunnels from the west of the city to the south-east, five new underground stations, high capacity signalling, and train/tram interchange between Anzac Station and the Domain Interchange in the south of the city.
Currently the project is deep in the construction phase, with stations in the CBD being built and four boring machines working to create the tunnels. The project is also utilising acoustics sheds in some of the CBD locations to minimise noise during the construction process.
As the Metro Tunnel is considered to be a critical infrastructure project, the COVID-19 restrictions have not shut down work on the project. Read more on the challenges of this project on page 68.
The Sydney Metro Project is currently Australia’s largest public transport project, estimated to cost between $11.5 billion to $12.5 billion. Sydney Metro is split into three main projects: Sydney Metro City & Southwest; Sydney Metro West; and Sydney Metro – Western Sydney Airport.
The City & Southwest project is well underway, with tunnelling completed in early 2020 on the 15.5km twin railway tunnels between Chatswood and Sydenham.
In June, it was announced that construction on the Western Sydney Airport line would begin in late 2020. It was also announced in the 2020 Federal Budget that $1.8 billion would be dedicated to the project.
In late August 2020, the Metro West project and the NSW Government announced the shortlisting of three consortia to deliver the project’s first two major tunnelling packages.
With population growth and congestion reaching capacity in Brisbane, Cross River Rail will help ease congestion and improve accessibility to Brisbane’s transport network.
The underground railway project will go through central Brisbane and allow more trains to run more often and avoid bottlenecks in the transport network.
The project is currently under construction and is being delivered in partnership with the private sector through three infrastructure packages including: the Tunnel, Stations and Development public-private partnership; the Rail, Integration and Systems alliance; and the European Train Control System contract, which will provide a new signalling system.
Construction is currently underway at all of the project’s main station sites, and in March 2020, tunnelling began at the Cross River Rail’s Roma Street site. The tunnelling site is covered by a large acoustics shed, helping to minimise noise to the local community while tunnelling continues.
There will be five roadheader excavation machines used in total on the project, which will also dig the southern section of the project’s twin tunnels, running from Woolloongabba to Boggo Road.
In March 2019, the Victorian and Federal Governments formally signed off on the new Melbourne Airport Rail Link project, giving the green light for the $10 billion project to go ahead after the preferred route was agreed to in November 2018.
The project will help alleviate congestion on the Tullamarine Freeway, the city’s main road connection to the airport, as well as helping to unlock capacity for Melbourne’s growing population in the north-west. Once completed, the link will provide city to airport travel times of 20 minutes, trains every ten minutes, 24 hours a day, and will help take up to 15,000 vehicles off the road.
Work is now underway developing a Business Case, which is expected to be completed in 2020, and will assess station and procurement options, value capture and creation opportunities, and economic analysis. Construction is set to begin in 2022 and is expected to take up to nine years to complete.
There has been a lot written about how the pandemic has brought out the best in
the human condition,
but
not
as many column inches have been devoted to how business has stepped up to the plate in its own way.
There has not been one corner of the country untouched by the COVID-19 crisis. For some businesses the pandemic has been the second or third extremely difficult situation they have found themselves facing this year.
It is fair to say 2020 has been a truly difficult experience for us all – personally, professionally and socially, with few exceptions, and business has certainly done its fair share of heavy lifting.
Banks bought in early with mortgage holidays and interest free periods. Insurance companies froze premium increases. And, with the support of governments, infrastructure companies helped not only to fast-forward projects where possible, but to stimulate investment and create jobs for their contractors and their staff.
Protecting infrastructure jobs and skills, and the people who have them, is in everyone’s interest and it applies particularly to regional Australia – where many areas have been amongst the hardest hit – following years of devastating drought, bushfires and floods.
No one had foreseen a global pandemic and the unprecedented impacts on businesses, employment and confidence that it would have.
Regional Australia has done it hard in the past, and these areas embody the term resilient. Regional Australia will, like it has before, dig deep to help us turn the fortunes of our great country around.
The Australian Government has done its part to help with record stimulus packages such as JobKeeper and JobSeeker to support Australians through the immediate crisis. But it falls to Australian businesses to help the country build our way out of the recession.
Just like the Sydney Harbour Bridge and Snowy Mountains scheme were both essential components of the government’s post-war strategy in the 1920s and 1950s respectively, so are mega infrastructure projects to support the post-COVID recovery today.
The Australian Rail Track Corporation is immensely proud of the role we’re playing in the nation’s economic response to the COVID-19 crisis, and also very aware of our commitments and responsibilities to the regional communities that we are a part of.
Three years ago, we were tasked with a project of national significance – to build a more direct freight link between Melbourne and Brisbane to unlock freight transit time of less than 24 hours.
Inland Rail is a world-class project that is delivering enormous economic and social benefits to our country at a time when we need it most.
It will complete the backbone of our freight rail network, it will help businesses move freight safer, faster and cheaper. It will reduce our reliance on busy roads and highways. It will continue to create thousands of jobs for years to come.
Ultimately, it will reinvigorate regional Australia while bolstering our national economy.
We have already created more than 1,800 jobs in the construction of Inland Rail, including 762 in regional areas where they are needed badly. This is just the beginning of the Inland Rail evolution. These jobs have been created while we have completed 103km of what will be a 1,700km rail line.
Over the breadth of the project we expect to create more than 16,000 jobs during the construction of Inland Rail, while another 700 workers will be needed for sustainable, long-term jobs when it becomes operational.
At this critical juncture in our recovery from COVID-19, we are doing our best to bring forward projects and accelerate construction in those areas that we can. We are working with our suppliers and subcontractors to keep supply chains moving in the face of difficult circumstances surrounding border controls. This is an environment in which we operate every day as we help facilitate the movement of freight around the country.
And we are using significant amounts of Australian-made steel, concrete and ballast in our big build, backing Australian jobs, manufacturing and businesses.
Inland Rail is truly a national project. It is being made for Australians, by Australians and we are using Aussie goods and know-how to get the job done.
In New South Wales, we’ve already sourced more than 14,000 tonnes of steel rail from Whyalla, 200,000 concrete sleepers from Mittagong, almost 400,000 tonnes of ballast from Parkes, a similar number of new rail clips from Blacktown and close to 27,000 tonnes of precast culverts from Tamworth.
It is staggering to think we’ve only completed just six per cent (103km) of track of the Inland Rail. Just ask the people of Parkes where the project has started about the effect it has had on the regional economy, and the buzz and excitement it has created in the town.
We expect this ripple effect to be felt right along the alignment and the next section between Narrabri and North Star is focusing national attention on the centres of Moree and Narrabri.
What is exciting is the prospect of what may be yet to come. Private investment is already happening in several sections along the alignment and promises a long-term renaissance for regional Australia.
A $35 million freight terminal has been built in Parkes on the back of Inland Rail, and hundreds of millions more is expected to be unlocked through Inland Rail construction.
We have other major projects underway that will also boost our transport future and create jobs now when they are most needed.
The North East Rail Line upgrade in Victoria, for example, has seen more than $70 million invested into the regional economy by the project in its first year of major construction. More than 173 Victorian subcontractors and suppliers of goods and services have benefited – including 85 businesses in local North East Victoria.
Everything from local equipment hire, to accommodation, to fuel purchase, to materials like ballast and asphalt providers.
Another $28 million will see new Australian-made rail laid in the Southern Highlands of NSW.
These are only some examples of the dozens of projects we have underway right across the country – investing in local people and business whilst creating a safer, reliable and more resilient transport network for our future.
By creating a reliable transport network, we will allow manufacturers to set up shop at competitive locations anywhere on the line between Melbourne and Brisbane, but also as far as the project is connected to Perth and Adelaide and regional centres like Wodonga, Toowoomba or Narrabri.
This will significantly reduce business costs and make local manufacturing more competitive. Inland Rail will not only dramatically improve local supply chains, but help Australia to create a world-class quality, highly skilled manufacturing sector.
The Australian Government through ARTC is investing billions in this project, but the value of backing business and keeping the Australian economy moving in these very difficult times is simply priceless.
• Pre-award audits of manufacturers, subcontractors and suppliers
• Experienced, certified and qualified inspectors
• Verification of manufacturing and testing in
• Individual inspection and test of
• Pre-delivery and ship loading inspections
• ISO 9001-2015 QMS certified company
The need to leverage digital is paramount to being an efficient infrastructure owner, manager or operator. To best embrace and realise benefits from digital enablers, a strategy for how they will be used across the organisation in a joined up manner is needed. This ensures that workflows are end-to-end and that information has traceability to enable high confidence decisions.
With the complexity of modern infrastructure management, operations and maintenance, there are now many distinct variables that can impact stakeholder outcomes. To efficiently deal with this complexity, many of the process and workflows need to be automated. The decision-making leavers for any organisation need to be responsive to changing customer needs and the forecasted needs of infrastructure assets that deliver the service.
Traditional manual decision-making methods are becoming obsolete when the volume of near real-time and dynamic data is truly connected and streams into enterprise platforms. Furthermore, stakeholders are requiring more transparency in decision-making and traceability to source data. There is little room for subjective options and therefore leveraging a digital approach is a preferred route.
Price limitations have been a challenge when introducing new technology and approaches. It is not until a solution is cheaper and the outcome is better, that organisations have the appetite to change traditional methods. Technology like cloud computing, digital design and automated monitoring has advanced to a point that cost is no longer a reason not to adopt.
Digitally Enabled Assets are those which are designed by a digital vision, managed throughout the lifecycle by digital processes and are supported by a workforce that leverages digital to provide insights through analytics and make the most informed decisions. The diagram to the right describes some of the building blocks for digital considerations across the operating model for infrastructure management. These building blocks may materialise as individual digital twins that can be brought together under a connected family of twins.
A digitally enabled asset strategy is needed to capture the voice of customers and stakeholders leveraging platforms like social media to distil public sentiment. Utilising existing public strategies such as the Transport for NSW Digital Engineering Framework, the Victorian Digital Asset Strategy, or the Smart Cities Council Digital Twin Guidance Note, are a good starting place. This can then feed into a more dynamic strategy formation that captures inputs from across the organisation to ensure a balanced view that is supported by management, finance, HR, IT, engineering and operations.
DIGITALLY ENABLED LIFECYCLE
Digitally enabled asset planning drives a more robust way for understanding forecasted needs of asset interventions. By capturing performance and condition information about assets in a structured manner, we are able to automatically draw correlations and leverage machine learning to propose optimal interventions that humans can then make the ultimate decision on.
Digitally enabled asset procurement practices mean that sharing the right existing asset information with the supply chain can be seamless and provide the opportunity to ‘try before you buy’ in an integrated common data environment.
Digitally enabled asset design has been a staple for several decades, however, it continues to evolve to leverage
automated parametric design procedures that seek to standardise asset configurations by limiting the number of parameters that can be adjusted. This significantly speeds the design process, but also improves the operability and maintainability of similar assets across a portfolio.
Digitally enabled asset construction is improving to better leverage robotic equipment, modular 3D printing and autonomous vehicles for excavation and earthmoving. There are significant advances in leveraging artificial intelligence to monitor site changes over time, through fixed cameras and the use of drones to repeatedly build 3D models of a site and identify confidence of project progress and delivery. This can also enable automated contract payments based on 4D known milestones.
Digitally enabled asset operations needs to extend further than just technology that monitors asset movements. For instance, European Train Control Systems (ETCS) provide the ability for a more dynamic utilisation of rail infrastructure for train movements, however it needs to be connected to how other supporting infrastructure is performing to operate the network as a system and optimise i.e. space between trains and energy usage. Likewise, Digital Meters for power and water utilities enabled by IoT, provide a more real-time feel to customer demand, however it needs additional analytics to make sense of the tidal wave of data so that correlations can be drawn for further insight.
Digitally enabled asset maintenance is set to leverage a multitude of analytical techniques that provide insight into how assets are performing and how to predict when potential failures may occur. For instance, understanding failure modes and being able to infer these using digital techniques can provide the forecast needed to make timely interventions and reduce the chance of service outage.
Digitally enabled asset renewals can be forecast based on understanding the end-of-life of an asset and having an integrated way of estimating if that asset should be renewed to maintain a service level, should be re-designed to remove potential operational issues, or changed to optimise either an increase or decrease in demand. By having asset intervention analysis joined up, we can better budget and sequence works to optimise how works are packaged and therefore reduce the impact to customers.
Digitally enabled asset decommissioning can also be achieved through the creation of a digital twin to simulate how the asset can be taken out of service for reuse and recycling. This approach can also be implemented in the early design
phases of an asset to leverage a digitally enabled circular economy where it is possible to track embodied carbon, materials, hazards and other sustainability metrics.
A digitally enabled asset workforce is needed to provide the right information to the right decision makers at the right time. This information needs to be presented on the right platform depending on the role of the resource. A field-based workforce can also be empowered through technology wearables that can aid in workers safety and optimise scheduling and location of crews.
Digitally enabled asset data acquisition has had a sharp increase in activity through the use of IoT sensors, drones to capture 3D photogrammetry, the use of LiDAR and other satellite photography. Also leveraging data capture through proxy information gathered by existing workforce or public crowdsourcing is an attractive option to rapidly build knowledge.
Digitally enabled asset risk and review provides a more dynamic way of assessing business risk, supply chain risk, and asset risk. By having a joined-up method to measure key performance indicators and metrics, organisations are able to better manage risk exposure and trade-off between risk and cost where the cost of an intervention provides a net positive benefit compared to the risk of doing nothing.
Digitally enabled asset review and improvement provides senior stakeholders with the confidence that all parts of the operating model are working in unison and can help target focus areas of the organisation where they are needed most i.e. using lead indicators as metrics for automatic validation.
There is an incredible opportunity to realise significant latent value from your assets at every step of an organisations digital asset enabling journey, however the first step is to get started. If you already have a clear digital strategy and vision on how to join and enhance your digital support areas of people, tools, technology etc. then undertaking an assessment of your organisations digital maturity and end-to-end workflows is a valuable next step, and is already helping asset owners to prioritise where an organisation can focus its limited energy. Developing a roadmap does not need to be difficult, with a clear vision and focus on benefit realisation, building an organisational digital twin can be achievable and most importantly enjoyable.
The use of vulcanised rubber for track damping systems has a number of benefits over other typical materials used in the rail sector, including increased design flexibility and durability, ease of installation and reduced maintenance costs.
Since its establishment in 1947, STRAILastic has become a world-leading expert in the design and manufacture of vulcanised rubber products, providing customers with high-quality products and services to meet their requirements.
Its rubber product range is made from 70 per cent secondary raw materials, with the hot vulcanisation production process permanently bonding the surface of the virgin rubber with the recycled rubber and mineral compound. This process results in precisely moulded, electrically isolated, and durable elements that are resistant to wear, fire and UV ozone.
Vulcanised rubber is used in a number of STRAILastic systems, including STRAILastic_TOR, STRAILastic_TOR Simplex and green track systems. All of these products can be fully recycled and repurposed at the end of their service life making them environmentally friendly.
STRAILastic_TOR
The STRAILastic_TOR system is used for both grooved light rail or sleeper tracks and can accommodate all types of rail fastening while meeting stray current insulation requirements. It provides noise attenuation of the wheel rail interface and reduced vibration. The design geometry of the system is independent of the sleeper or fastening type, and its modular design provides flexibility to adapt to different track support designs and sleeper spacing.
STRAILastic_TOR Simplex
This unique system combines the flexibility of the TOR system with the simplicity of a bottom up construction track support system, which eliminates the need to place an initial bottom concrete slab, saving considerable time, inconvenience and cost to both the community and project delivery schedule.
Combined with the STRAILastic_GRS track section baseplate, TOR Simplex allows for infinite rail top and line adjustment with different spring numbers to meet requirements and can reduce track installation times by 15 per cent.
The vulcanised chamber filling elements of the TOR and TOR Simplex systems extend around and up to the top of the rail, making them suitable for all types of track structures and making maintenance-intensive joint sealing obsolete.
As the chamber units are designed to fit snugly to the rail profile, they can be installed quickly, easily and without adhesive, significantly reducing construction time and costs, and minimising community disruption.
STRAILastic’s green track systems can be adapted for different installation heights depending on the track and sleeper type, and they can be used with vignole as well as grooved rails on ballasted track for additional savings, while ensuring the corridor remains both accessible for emergency vehicles and safe for pedestrians and cyclists to cross.
Green tracks can retain a large amount of rainwater, and absorb road and fine dust pollution, improving the microclimate of urban centres. As the track is encapsulated, primary airborne noise is also significantly reduced compared to ballast tracks.
The STRAILastic_R green track system protects the track structure from stray current, and is UV ozone and fire resistant, while its modular design simplifies maintenance, allowing for easy renewal and replacement. It also gives the track a natural appearance, making it visually attractive.
Having dealt with the pressure of making decisions under fire, and the need to act in the face of uncertainty, his experience on the battlefield has yielded lessons that are equally applicable on the project site or in the boardroom.
He will join AusRAIL this year to talk about the value of leaders being agile in their decision-making, and why it is important for people to have the skills needed to deal with any outcome, including uncertainty.
It is a timely message as we prepare for a new year that will undoubtedly bring new opportunities for growth for those that can weather the uncertainty, and new challenges that we may encounter in a post-pandemic world.
But it is also a reflection of what we have already seen in the rail industry time and time again this year.
Leaders have changed how they operate to keep delivering essential services – safely, efficiently and with their customers at the top of mind. Frontline workers continue to head out into their communities to do their essential work, even as many of us ventured inwards.
People are dealing with uncertainty and change in everything they do, at home and at work. AusRAIL Live & On Demand is another example of opportunity from change. Our move this year to a fully online format has allowed us to reach out to international speakers that may not have been able to join if we were meeting in person.
Delegates will get to hear from some of the top rail industry executives from across the globe, including Crossrail Chief Executive, Mark Wild, who is currently overseeing Europe’s largest infrastructure project.
With trials running on the project’s Elizabeth line expected to start next year, this is a good time to hear about the complexity of this major rail project, and the plans to bring the line into passenger service by 2022.
LA Metro Chief Innovation Officer, Joshua Schank, will talk about innovation and experimental program and policy, providing a new perspective on ways to move the industry forward.
Mr Schank’s Office of Extraordinary Innovation is leading a range of projects that aim to provide faster, better options for passengers as part of a more responsive service that supports the creation of vibrant communities.
These are ambitious goals that will no doubt have parallels with innovation projects underway here in Australia. We will also hear from Grand Paris Express Project Director, Nicholas Massart, who will tell us how that project is transforming Paris into a more sustainable city.
It is rare that you can access keynote addresses, ask questions and interact with speakers of this calibre directly from your home or office, but at AusRAIL Live & On Demand, delegates will have the chance to do just that.
This front row seat to presentations of the projects that are shaping the future of the industry globally is an unmatched
Mark Donaldson VC knows a thing or two about leadership and resilience. The decorated former SAS soldier will be among the featured keynote speakers at the Australasian Railway Association’s (ARA) expanded and fully online AusRAIL Live & On Demand conference in 2020.
professional development opportunity. There are also plenty of ideas, insights and lessons from 2020 that are creating new opportunities for the industry right here in Australia and New Zealand.
AusRAIL Live & On Demand will provide more opportunities to hear from leaders of the region’s operators, contractors manufacturers and suppliers to provide a snapshot of the industry, its most innovative projects and initiatives and plans for the future.
In total, we have added 14 new streams to allow delegates to tailor their conference experience and access more content than ever before.
The Cross River Rail, Inland Rail and WA’s METRONET will all be showcased in a dedicated infrastructure projects stream to allow you to hear the latest on their progress. Sustainability and accessibility streams will highlight how the industry is contributing to more vibrant cities and towns, delivering long-term benefits for the people that live in them.
For those working in freight and ports, dedicated sessions will provide greater insight on the implications of the National Rail Freight Action Plan for the sector, and share the latest updates on the implementation of the Advanced Train Management System.
Rail suppliers will hear more about the opportunities ahead, and the emerging technology that will shape our industry.
Meanwhile, our passenger transport stream will reflect on how COVID-19 is changing passenger behaviours, now and in the future. And virtual tours will take you behind the scenes
of some of our most interesting rail operations, bringing you close to the action from the comfort of your home or office.
This is just a taste of the many streams on offer as part of AusRAIL’s expanded, three-day program for 2020. We are really pleased to be able to offer a program that will not just deliver more content than ever before, but will provide continuing access to content for up to six months after the event.
This will be a huge advantage for delegates, who can go back and reference presentations or specialist streams as they start new projects and initiatives in the new year. The continuing value of AusRAIL’s offering this year, long after the event, simply cannot be underestimated.
With delegates given early access to the platform, you can start your industry networking a full month before AusRAIL actually gets underway. Log on in November to set up meetings with the exhibitors you want to connect with, and start your 1:1 video chats to find out more about their offering.
See which delegates have bookmarked the sessions you will attend as well to find like-minded people to enhance your networking over the course of the event and beyond.
The ARA looks forward to seeing the rail industry come together again at AusRAIL Live & On Demand. To register, go to ausrail.com
The last few months have seen a dramatic change in how we live, work and move around our cities due to the pandemic. Some states like Victoria are still facing strict lockdowns, while other states have started to open things back up. While there is a lot of uncertainty, now is the time to start exploring what the industry will look like post-COVID.
To help provide some answers to this big issue, Infrastructure magazine gathered the infrastructure industry’s leading experts to explore their predictions at the first Future of Infrastructure Virtual Conference in July.
Speakers delved deep into issues including the rise of cloud-based infrastructure; using the economic rebuild to make assets more sustainable; how mobility and transport usage will change, and what the sector can do to meet this new demand; as well as what nation rebuilding will look like post-COVID and the new waves of innovation for the sector.
Frank Zeichner, CEO, Internet of Things Alliance Australia (IoTAA), spoke about the Internet of Things (IoT), digital infrastructure and what’s needed for Australian IoT infrastructure.
IoT by International Standards Organisation/IEC definition is “an infrastructure of interconnected objects, people, systems and information resources together with intelligent services to
allow them to process information of the physical and virtual world and react”.
Frank said he and IoTAA work from the premise that data will be the tool that we will use to make better decisions, and that while the internet had a dramatic effect on the way businesses ran when it first emerged, the Internet of Things will have an even bigger impact.
“We're collecting some of the information that allows us to start making faster decisions about how we might optimise services, how we might better use our assets, how we might provide warnings for safety, for example. So the Internet of Things is a systemic thing, and it’s about collecting, transforming and sharing data,” he said.
“It's ultimately about gaining insights and information from data, to improve business processes in operations and customer engagement.”
When looking at how different Australian sectors ranked in a McKinsey Australia Industry Digitisation Index, the level of
digitisation for manufacturing, mining, utilities, construction, transport and agriculture is patchy at best. This is where Frank sees a massive opportunity.
SO WHAT’S NEEDED FOR AUSTRALIAN IoT INFRASTRUCTURE?
According to Frank, the things that are needed are:
A culture and understanding of collecting, analysing and sharing data inside businesses and externally with suppliers and customers
♦ Understanding where data, especially real-time data can help business processes
♦ Having the skills inside or with partners to apply IoT technologies to collect, analyse and share data
♦ Drive through process change
Investment in “hard infrastructure” will require investment on "soft" data and IoT investment
On this point, Frank said, “We need to build roads, rail, ports and airports. My view is that we shouldn't be building those without the soft as well. The data collecting and sharing requirements need to be built into that infrastructure, which builds our IoT national infrastructure.”
Security by design
♦ Build security in at the start, it's way less expensive than adding it later
Nationwide connectivity – for high and low bandwidth
♦ Businesses need to be able to connect via broadband and wirelessly. There will be a need to enable greater incentives for regional/rural coverage
♦ We need findable and accessible data repositories for public good and industry enablement – preferably located in Australia
♦ We should be applying artificial intelligence and machine learning in Australia — there is a massive opportunity here
So where should the infrastructure and construction industry start on their digital and IoT journey?
Frank said the first thing to do is to find people who are doing it.
“Talk to others in your industry who are already doing it. In the construction industry, I’d say look for those who are standouts and learn first.”
Smart pi is an equipment manufacturer providing high-quality hardware and software for public information systems. Now the innovative Smart pi ECOsystem offers more than just products and applications that communicate information to the general public.
The Smart pi ECOsystem is a fully integrated Smart Public Information environment; it works as one seamless system across public spaces and transportation hubs of all sizes.
The Smart pi ECOsystem has been designed to look, feel and work as one. For example, the Smart pi DVA (Digital Voice Announcement) range can integrate with the Smart pi EYE (Digital Information/Signage System) to display the metadata of announcements being made on the visual displays as they are playing.
The ECOsystem includes:
♦ Smart pi Audio Systems
♦ Smart pi Help and Information Points
♦ Smart pi Visual Systems
Smart pi ECOsystem has been designed to offer ease of operation for the user. Training is simple as there is no need to learn to use a range of different products. All of the components of the Smart pi ECOsystem range work as one from a web-based configuration.
The size of the ECOsystem is scalable, from the smallest installation right up to the huge systems containing 10,000 devices and beyond. It uses and supports all open standards such as GTFS and GTFS-R for the transport industry. For control, AES 70/OCA are used and fully supported by the Ecosystem.
tm stagetec systems is the exclusive Australian distributor of the Smart pi ECOsystem. Contact them at www.tm-systems.com.au to learn more.
AP 2021 Brisbane Convention & Exhibition Centre
Queensland, Australia | 12-15 April 2021
In April 2021, the four-day forum will connect transport technology professionals from across the Asia Pacific region. Featuring a hybrid—in-person and digital—program, you can join the 17th ITS Asia Pacific Forum wherever you are in the world.
The forum theme, “ITS Innovation Creating Liveable Communities”, will demonstrate Australia’s new initiatives and adapted learnings from the advances of our neighbouring megacities. Key topics to be covered include MaaS, Automated Vehicles, Data Analytics, Transport Inclusivity, and Network Development.
Hosted by
South East Queensland (SEQ) is a region of unmatched potential, with the ability to combine its natural assets, people, economic opportunity and liveability to deliver a significant contribution to the state and national economy. It is a region that is expected to see a lot of investment over the next few years and there are critical infrastructure projects that are currently ongoing in the region, from the NSW border to the Gold Coast, Brisbane and the Sunshine Coast.
The SEQ region’s idea to develop a City Deal was the first of its kind in Australia and contributed to the Australian Government including the concept in its Smart Cities Plan in 2016. The City Deal aims to benefit more than three million residents and paves the way for a prosperous and sustainable future for generations to come. At the core of this deal is a vision to transform regional connectivity to address congestion, ignite future employment potential and build lifestyle destinations.
There are high-impact infrastructure projects in the SEQ region including the Gold CoastBrisbane Transport Upgrade, Cross River Rail, and the new airport in the Sunshine Coast region, among others.
These infrastructure projects are being supported by vast amounts of 3D data that has been captured and processed for the region, with the support of government departments at different levels.
The region is a combination of extremely important
commercial and tourism centres, and these 3D assets will help shape a larger digital twin for the region, which the State and Federal Governments are working on as part of a SEQ City Deal. One of the critical aspects for the region’s development is transport infrastructure, and these 3D models will underpin the planning involved in upgrading multiple road, rail and airport links across the region, mainly connecting the Gold Coast and Sunshine Coast regions to the commercial hub of Brisbane.
"The street level 3D data is awesome. We appreciate the partnership between Sunshine Coast Council, DNRME and Aerometrex to deliver such a great set of industry-leading products to the government and the community. Our internal stakeholders consisting of senior management are really impressed with the quality"
– Mike Symonds, Project Manager, SCCInstead of numerous development projects commissioning 3D data, the government’s foresight makes sure that all critical projects can utilise the information and make proactive decisions, minimising delays and costly rework.
Aerometrex has worked closely with numerous members of ANZLIC – the peak government body in Australia and New Zealand for spatial information – as well as critical stakeholders in the Queensland State Government and local councils in the region to capture 3D data at multiple resolutions using various platforms (fixed wing airplanes, helicopter, and street level capture).
Spanning most of the SEQ region, this forms one of the largest continuous 3D datasets in Australia after the one produced for the NSW Government’s Western Sydney Digital Twin project.
These projects have been great examples of collaboration between the state government, local government and private industry, and offered an ideal platform to test what was possible.
“The collaboration and transparency across the different organisations was crucial to the success of projects of such scale, and credit goes to each government department involved in being open to such dialogue with us,” Rob Clout, 3D Sales Manager, Aerometrex, said.
Aerometrex delivered the 3D data for some of these projects in up to 30 different formats, allowing the information to be accessible for future projects and varying applications. These formats ensure that the data can be used, not just on its own, but also integrated with different technology and accessible through any other application that is out there – whether it is for engineering design, CAD design, architects’ models, or other GIS data.
The street level captures undertaken across the Sunshine Coast area, enable viewers to walk along a digital version of the near-natural streets and experience the shops, cafes, buildings, complex street furniture, trees, etc. The Sunshine Coast projects are a great example of the future of street level 3D modelling that can be integrated with aerial 3D models seamlessly. We are now in an environment where the evolution of gaming engines is enabling large infrastructure projects to be showcased in real time.
Matthew Walker, 3D Product Manager, Aerometrex, said, “Digitised 3D data is great at providing the perfect backdrop to represent infrastructure designs and communicate plans to decision makers. They form the basis for digital twins and create changing scenarios for corridors, precincts, etc. These scenarios can help visualise impact on pedestrian movement and business accessibility, among other key things.”
These vast datasets across South East Queensland will support infrastructure, engineering, construction and urban design projects – where users can not only see what a particular design would look like, but also assess its impact on surrounding assets. These evaluations can be made early in the design cycle, saving companies both time and money.
So, while the data looks amazing, its real value is in its detail and accuracy. That is what this 3D digital replica offers many – the ability to accurately represent the real world and your development projects within it.
The circular economy represents a unique and significant opportunity; $210 billion to Australia's GDP by 20501. It is capable of driving new efficiencies and productivity improvements unseen over past decades.
New circular businesses, products and services are emerging – such as fashion and white goods as-aservice, recycled water, local renewable energy generation and shared mobility. They are disrupting linear approaches that encourage us all to flush and throw away valuable resources.
Circular economy is an accelerator for a sustainable recovery. It aims to redefine growth, focusing on positive society-wide benefits, by gradually decoupling economic activity from the consumption of finite resources, and designing waste out of the system.
It’s based on three principles:
1. Design out waste and pollution
2. Keep products and materials in use
3. Regenerate natural systems
NSW alone generates over 20 million tonnes of waste – enough to fill 8,000 olympic-sized pools, and 35 per cent of this waste goes to landfill, costing households and businesses over $750 million in waste levies every year.
But it's not just the cost of the levies – what about the resources locked in landfilled materials? If we look at a solar panel, for example, the silver, silicon and aluminium inside are a huge untapped resource. Other precious metals can be found in e-waste and textiles, and smart organisations are beginning to mine this waste instead of virgin resources.
Metals are very recyclable and require less energy to produce than virgin products. For example, one tonne of recycled steel saves 1,131kg of iron ore, 633kg of coal and 54kg of limestone2 Copper can be recycled indefinitely, and recycled copper is worth up to 90 per cent of the cost of the original copper, with every tonne of recycled copper amounting to a saving of 3.4 tonnes of CO2 (equivalent to 16,602km driven), 36 GJ of energy (equivalent to 20 houses’ monthly energy consumption), 6kL water (34 bath tubs) and 1.1 tonnes of waste (equivalent to 20 wheelie bins).3
¹Centre for International Economics, Headline economic value for waste and materials efficiency in Australia, commissioned by the Department of the Environment and Energy, Oct 2017
²Suez Australia and New Zealand, https://www.suez.com.au/en-au/sustainability-tips/learn-about-waste-streams/general-waste-streams/metal-aluminium- and-steel-recycling (Accessed 13 Aug 2020) ³Planet Ark, https://businessrecycling.com.au/recycle/copper (Accessed 13 Aug 2020)
Australian business and finance sectors have an immediate opportunity to step up. They should not wait for policy, but need to get on with establishing new circular business models. In Europe, banks are already providing new competitive financial leverage for companies choosing a circular economic production model, such as Intesa SanPaolo in Milan which has dedicated $6 billion Euro ($9.8 billion AUD) to innovative circular economy projects.
Circular sharing and reuse business models and services are more sustainable and often highly profitable because they have multiple revenue streams. They are paid to take away a resource which they re-purpose and sell again, extracting value by keeping it in the market for longer.
Circular economy principles are also proving cost-effective for utilities. Technological advancements are also converging traditional utility infrastructure. Water and organic waste is energy, solar is mobility. This is disrupting traditional investment and revenue models. It's not just solar panels and batteries that can store and trade excess energy, technologies can turn organic waste into fertiliser and energy, and autonomous vehicles are avoiding the need for every household to own a car. Precinct and household recycled water systems are also reducing water demand by 50 per cent through products like Hydraloop, a box the size of a small fridge that can recycle 85 per cent of household water.
Circular utility solutions are also saving money on gold-plated infrastructure because they have skinny grid connections that avoid costly upstream and downstream infrastructure augmentation. For example, local energy generation and microgrids reduce demand and enable renewable energy to be sold back to the grid, while recycled water can halve water demand and remove wastewater outflows harnessing them to recycle locally.
As we enter the circular economy era, the way we think about infrastructure needs to change. To date, it has largely been dominated by siloed infrastructure
planning for water, energy, waste and mobility due, in part, to a constructionled approach.
The World Economy Forum has been emphasising the need to address the connections and interdependencies between our siloed infrastructure sectors and systems to give communities what they need to flourish.
In Australia, we need to make sure infrastructure is circular and interconnected, that it can leverage clearer insightful data and manage energy, water, waste and transport as a system of systems capable of tackling climate change and keeping us resilient and safe in pandemics. Infrastructure Australia is already working to promote circular infrastructure in its Priority Infrastructure List.
Companies and researchers are designing out waste by making products that last and can be repaired. Nextgeneration infrastructure and services are reducing costs and creating an abundance of sustainable resources that can be shared.
When we look at the benefit driven by a circular economic approach to externalities such as avoiding carbon emissions from landfill, or water resilience and productivity from water recycling, and cost savings of up to $6,000 annually achieved by sharing a car instead of owning one, the case for a circular economy is compelling.
The COVID-19 pandemic has revealed our current economic system’s vulnerability to risks, challenging us to rethink and redesign for resilience. The circular economy is more relevant now than ever. It offers a solution to embrace innovation to build a more resilient zero-carbon economy by combining economic opportunities with benefits to society and the environment.
Ten per cent of our current global economic activity is circular but it's growing and we need it to. By 2050 we will have ten billion people on the planet and not enough virgin resources to maintain anywhere near our current levels of consumption. A circular transition is essential and inevitable, and those who are at the forefront of this change will be the successful businesses, places and economies of the future.
The new EPDs cover a range of Australian-made steel products, manufactured, processed and distributed by InfraBuild, Liberty Primary Steel and ARC, who together form part of the GFG Alliance in Australia.
As part of the GFG Alliance, InfraBuild is committed to creating a more sustainable future for industry and society. The EPDs are one part of this commitment.
InfraBuild’s continued development of innovative practices is underpinned by GFG Alliances’ GREENSTEEL strategy which promotes greater use of recycled materials, increased use of renewable energy and operation of facilities close to key markets.
The new Declarations replace those first released in November 2016, and cover products including hot rolled structural and merchant bar sections; rail and sleeper products; reinforcing rod, bar and wire; as well as finished reinforcing bar and mesh.
InfraBuild Chief Executive Officer, Dak Patel, said the business was committed to conducting its operations to the “highest environmental, social and commercial standards”.
“Our commitment to the environment includes optimising the eco-efficiency of our products through their lifecycle,” Mr Patel said.
”Sustainability and traceability of products is of increasing importance to the market and these EPDs help to provide that peace of mind.”
A key benefit of the new EPDs is the inclusion of Material Circularity Indicator (MCI) metrics. The MCI metrics are provided for all steel products covered in the EPDs, providing vital information as we shift to a more circular production model.
Sustainability, infrastructure and construction market professionals now have access to the latest sustainability data on a range of InfraBuild, Liberty Primary Steel and ARC steel products with the release of updated Environmental Product Declarations (EPDs).
David Bell, InfraBuild Steel’s Construction Market Manager, explained the importance of including the comprehensive MCI metrics across Infrabuild’s steel product range.
“The Circular Economy requires us to reconsider the entire lifecycle of all products and resources by designing out waste,” Mr Bell said.
“This means using materials and technologies that extend the lifespan and recyclability of what we produce, while minimising unintended waste and pollutants.
“To help the market understand the circularity of products, the MCI approach provides both a benchmark for measuring and improving a product, as well as a more complete picture of the product’s overall sustainability credentials.”
Developed in conjunction with thinkstep-anz and independently verified by Rob Rouwette from start2see, the updated EPDs play a major role in the overall approach taken by the business through the environmentally sustainable manufacture and application of its products, as well as delivering value and greater transparency to customers and industry more broadly.
GFG Alliance has established the CN30 programme, which builds on existing GREENSTEEL (and GREENALUMINIUM) strategies, aiming to become the first carbon neutral industrial group in the world by 2030. The program involves implementing investments in new infrastructure, renewable energy and new technologies.
InfraBuild is proud to be part of the GFG Alliance’s work towards building a secure and sustainable long-term future for the domestic steel industry, local manufacturing and communities.
Our updated Environmental Product Declarations (EPDs) are part of our ongoing commitment to sustainability. They are just another way we deliver value to our customers and the construction industry, along with our sustainable manufacturing practices, technical product and application expertise.
EPDs Now Available:
• Hot Rolled Structural and Merchant Bar
• Hot Rolled Structural and Rail: Liberty Primary Steel
• Reinforcing Rod, Bar and Wire
• Reinforcing Bar and Mesh: InfraBuild Construction Solutions
• Hot Rolled Structural and Merchant Bar: InfraBuild Steel Centre
• Reinforcing Bar and Mesh: ARC Download here
Road planners have talked about “missing links” for decades. Like that other cliché to describe big infrastructure – “game changer” – it can sound impressive but mean very little to motorists stuck in traffic. But if there ever was a motorway you could confidently call both a “missing link” and a “game changer”, it’s NorthConnex, which will connect Sydney’s M1 and M2 via 9km twin motorway tunnels.
One of Australia’s longest road tunnels and the deepest at 90m, NorthConnex will revolutionise the way people and freight move by finally filling the gap in the National Highway route and providing an alternative to the notorious Pennant Hills Road.
Winding through some of Sydney’s leafy outer north-west suburbs, you don’t have to look far to find a story about Pennant Hills Road traffic incidents.
Home to around ten schools, aged care homes, houses and shops, local traffic is forced to share Pennant Hills Road with heavy vehicles, freight and through traffic as it is the only direct route between the M1 and M2.
It is used by around 80,000 vehicles per day making it one of Sydney’s most congested roads, and regularly voted by drivers as one of the worst.
Don’t cry over it, but 2,000 bottles of milk were spilt after an incident at Normanhurst in 2017, while local Federal MP Julian Leeser had a truck smash into his Pennant Hills office building in 2018.
There are an average of 360 incidents a year – around one per day, impacting traffic and causing frustrating delays.
In the past six years there have been around 600 crashes, with three people killed and another 424 injured.
One in four crashes involved a heavy vehicle, compared to one in 14 across Sydney.
When the tunnel opens, it will take up to 5,000 trucks a day off Pennant Hills Road, returning local streets to local communities, improving safety and easing congestion to get people where they need to be sooner.
By moving traffic underground, the tunnel will also help to improve local air quality along Pennant Hills Road and reduce noise.
NorthConnex will also provide a safer and more efficient journey for trucks, enabling them to travel in taller, wider tunnels designed with grades favourable for heavy vehicle movements. It will boost state and national economies by providing more reliable journeys and shorter travel times for freight, opening up access and opportunities for areas like the Central Coast.
NorthConnex will deliver traffic-light free journeys between Newcastle and Melbourne.
Since the 1920s, there have been calls for a ‘Great Northern Roadway’, progressed in the ‘40s in the fabled County of Cumberland Plan.
After many false starts, it wasn’t until 2014, after an unsolicited proposal lodged two years earlier by Transurban, that the project was given the green light by the Australian and NSW Governments.
Alleviating congestion and improving safety on Pennant Hills Road has been something the local community has been wanting for years, and they’re excited that relief is just around the corner.
The twin tunnels will help create significant efficiencies in freight movements along the east coast, with predicted economic benefits of $4 billion.
Instead of trucks negotiating the twists and turns of Pennant Hills Road, two school zones and up to 21 sets of traffic lights, NorthConnex will provide a direct underground trip which will result in travel time savings of up to 15 minutes.
The tunnels have the capacity for around 100,000 vehicles a day and feature lighting displays of stars and trees to keep drivers alert, among the first of their kind in the world.
It has taken five years of complex construction underneath three railway lines, excavating 2.3 million cubic metres of spoil.
Around 8,700 jobs have been created over the lifetime of the project.
The $3 billion tunnel is being delivered by the Australian and NSW Governments in partnership with Transurban. The construction contractor is a joint venture between Lendlease and Bouygues, and it’s an engineering marvel.
Led by 20 roadheaders and two surface miners, work involved carving through about 21km of mainline tunnels.
Three specially designed vertical conveyers, located at each of the three tunnelling shafts, were used to transport excavated spoil to the surface.
The roadheaders used on the NorthConnex project were designed and built by Sandvik and Mitsui.
Each roadheader weighed around 100 tonnes and ‘chewed’ through roughly 25 five metres of rock per week.
More than one million cubic metres of the spoil was sustainably reused to partially fill the nearby Hornsby Quarry, laying the foundations to transform the site into a future parkland for the local community.
In an Australian first, conveyors reaching 160m in length were used to transport the spoil into the quarry, at a rate of up to 2,000 tonnes of spoil per hour.
This process helped to significantly reduce truck movements in the local area and minimised impact on the surrounding environment.
The main type of primary tunnel supports on the project consist of a thin layer of shotcrete and rock bolts.
Approximately 300,000 rock bolts up to five metres in length have been installed to support the tunnel’s structure.
Other statistics include:
♦ More than 122,000 truck-loads of concrete have been supplied for the tunnels final lining and pavement
♦ The continuous reinforced concrete pavement is 24cm thick and able to withstand the up to 5,000 trucks that will be using the NorthConnex tunnel every day
♦ 19,000 tonnes of steel was used to build the tunnel and facilities
♦ 142 jet fans will push air through the 9km twin tunnels
SYDNEY’S NEXT-GEN TUNNEL
NorthConnex has been designed to the highest safety standards, and built and fitted with the latest technology, making it one of the safest motorways in NSW.
It features highly intelligent and coordinated monitoring systems which continually check tunnel operations to detect any issues that may impact tunnel performance such as traffic volumes and speeds, incidents, smoke and overheight vehicles.
The 24/7 operations team will have access to around 850 cameras as well as stopped vehicle detection cameras to alert of potential incidents.
Transurban’s NorthConnex Project Director, Daniel Banovic, said, “We are working closely with our project partners to open as soon as possible so motorists can test-drive Sydney’s latest tunnels for themselves.”
One of Australia’s most experienced construction professionals, Pat Doyle, has enjoyed an outstanding 42-year career in the construction industry. His previous work experience includes the Sydney Harbour Tunnel, Eastern Distributor, M5 East and Cross City Tunnel.
The Melbourne Metro Rail Tunnel project, currently under construction, is just one of the tunnel projects that have formed a large part of Australia’s infrastructure spend, and requires expert advice, as well as quality concrete and storage solutions for a successful result.
The Metro Tunnel is expected to untangle the City Loop, enabling more than half a million more passengers per week to access the network, which will relieve bottlenecks and shorten commute times during peak periods.
The Cross Yarra Partnership, a joint venture of leading construction and engineering companies, is delivering this $11 billion project.
Like all modern tunnels, the Metro Tunnel uses a large amount of concrete. This concrete sets quickly when applied, requiring an admixture to accelerate the curing process to fix quickly to the walls and ceiling of the tunnel. One chemical used in the process is sodium silicate.
Given that large amounts of cement was used, vast quantities of sodium silicate were required to be stored on site. Sodium silicate is referred to as water glass and is known as an irritant when in contact with eyes and skin.
Secondary containment is required when storing sodium silicate. The Cross Yarra Partnership chose the Polymaster double-skinned storage tanks as its secondary containment solution.
Traditional secondary containment solutions, such as concrete walls, require substantial extra space around the tank. Building a tunnel in metro Melbourne means that excess space is at a premium, with all crews vying for room for their equipment.
Another drawback that has been identified with the traditional concrete bund is that it captures rainwater which instantly becomes contaminated within the bund area. Subsequently, proper and costly disposal is required to keep the bund safe and operational.
Polymaster worked with the Tunnel Engineers to understand their needs and, having provided storage solutions for sodium silicate for years, recommended the doubleskinned tank range. Basically, it’s a
tank-within-a-tank creating its own bund, having a secondary containment of no less than 110 per cent.
These tanks are a practical solution when space is tight and there is a real need to reduce any disruption to the site during installation. Each tank delivered is put in place the same day, compared to a traditional bund which can require weeks of on-site formwork.
Due to the unique design of the Polymaster tanks, the on-site footprint can be reduced by approximately half. Additionally, no rainwater can be collected as the bund is completely sealed from the elements, which ultimately saves the partnership expensive contaminated water removal fees.
These tanks also include the factory installed fittings, making installation a breeze with everything in the right position, first time. These included level indicator, multiple outlets, inlets, truck fill ports, vents and interconnecting fittings.
Walking around the Metro Tunnel site you can see Polymaster tanks dotted everywhere. There are a number of chemical tanks and a handful of tanks used in the treatment of groundwater.
Contact Polymaster for expert advice, service and quality products for your next infrastructure project at www.polymaster.com.au.
Tunnelling and underground expert Paul Thomas has worked on projects all around the world, but Melbourne has its own unique challenges when it comes to tunnelling, especially geology. As the Deputy Director of Tunnels and Stations at Rail Projects Victoria, Mr Thomas currently leads the design development of the Metro Tunnel Project and spoke with Infrastructure about overcoming ground condition challenges on the major rail project.
To someone who builds tunnels, every piece of ground tells a unique story – you just have to drill into it for all to be revealed. Paul Thomas has been listening to those stories for 30 years as he helped build underground mass transit systems, including tunnels and stations in Hong Kong, Singapore and India.
“The Metro Tunnel faces some unique challenges in its ground conditions,” Mr Thomas said.
“Melbourne has everything from 430 million-year-old early Silurian age sandstone of variable degrees of weathering and bedding profiles, to the highly sensitive and reactive Coode Island Silts, which are of the late quaternary period, first forming approximately some 12,000 years ago.”
Rail Projects Victoria (RPV) is the State Government body responsible for delivering the Metro Tunnel. The Metro Tunnel Project’s twin nine-kilometre rail tunnels are now halfway to overall completion of tunnel boring machine
(TBM) activities, with cross passages now progressing well within the six completed sections of the 12 individual tunnelling sections.
The project is using four TBMs to construct the tunnels, connected by five new stations, and roadheaders to mine out the station caverns and adits in Melbourne’s CBD.
The first TBM was launched in August last year, and by June this year, all four of these massive machines were at work deep below Melbourne’s streets.
Extensive geological and hydrogeological investigation works, as well as detailed analysis, were undertaken during the pre-construction design development stage by RPV and its consultants.
This built understanding of the geological profile and behaviour of the ground and groundwater, based on various tunnelling and underground methods, and helped engineering experts decide how the tunnels and underground structures would be best designed and constructed, to ensure least possible disruption to the existing environment.
IMPORTANT
An extensive series of boreholes were drilled to extract samples of the varying geological units and identify anticipated fault zones as well as complex geotechnical interfaces along the alignment.
These core samples revealed important information about the rock and soil found at different points along the length of the Metro Tunnel Project, which in turn would inform reference design solutions for the underground stations and shafts.
It also helped determine predicted ground and groundwater behaviour –which is critically important considering the existing surface and subsurface infrastructure that the alignment traverses through.
The early investigation works also included advance instrumentation and monitoring of existing structures along the alignment such as existing road and rail infrastructure, as well as historical structures.
“We were able to develop a very detailed picture and interpretation of the anticipated ground and groundwater conditions, which meant the detailed design and underground works solutions were well considered, informed and buildable,” Mr Thomas said.
Historically, construction contractors generally take a conservative approach on the risk of encountering difficult and unforeseen ground conditions. RPV shared its geotechnical and hydrogeological analysis/modelling data and assumptions on design approaches
and methods with all of the potential constructors involved in the bidding process, therefore providing a very informed process in developing the reference design.
“We had a ‘detailed’ reference design so when Cross Yarra Partnership (CYP) was the eventual successful bidder, instead of reinventing the wheel they looked at the work we had already done and determined that some of the key assumptions of the reference design, such as station locations and retention systems such as diaphragm walls, were developed further to form the permanent proposed underground solution,” Mr Thomas said.
The Tunnels and Stations work package is being delivered by Cross Yarra Partnership, a consortium comprising Lendlease, John Holland and Bouygues. There was also an early works package which included construction of two advance shafts in the CBD North precinct – site of the future State Library Station – which also form part of the permanent station solution.
Fast-forward to the present, and the Metro Tunnel Project has achieved significant breakthroughs.
TBMs Millie and Alice have each dug 1.7km from the site of the new Anzac Station to the tunnel’s eastern entrance at South Yarra, while TBMs Joan and
Meg have each dug 2.6km across two sections of tunnel – between the Arden Station site and the tunnel’s western entrance in Kensington, and between Arden Station and the Parkville Station site.
In keeping with tunnelling tradition, the four TBMs are named after groundbreaking women including: Victoria's first female Premier, Joan Kirner; Australian women's cricket captain, Meg Lanning; Victoria's first female Member of Parliament, Lady Millie Peacock; and wartime medical hero, Alice Appleford.
As they advance, the TBMs progressively install the precast concrete segments that create the final tunnel. The segment design adopts a six segment universal ring arrangement. The segments are 300mm thick, comprising a single EPDM gasket and hydrophilic strip. The gasket is cast in place and the hydrophilic strip installed at site.
There are two main types of segments, all incorporating steel fibres, and modified versions combining reinforcement bars in addition to steel fibres. Every segment contains polypropylene fibres for fire resistance.
“The proof of the pudding is that the response in the ground conditions we’re encountering are very similar to what we anticipated through modelling,” Mr Thomas said.
Speaking at the Disaster Management Virtual Conference in September, one of the events in the 2020 Critical Infrastructure Summit, Tony Histon, Managing Director – Transmission & Distribution for Accenture’s Transmission and Distribution Practice in Asia Pacific, Africa and the Middle East, gave insights into the report and how utilities can shift their focus from reliability to resilience in order to be better prepared for the future.
Along with high-impact weather events, regular mid-tier weather events are also occurring more often. To understand the ability of utilities to cope in the face of these events, Accenture spoke to over 200 utility executives across the globe.
The survey found that utilities around the world recognised the serious operational and financial impacts of weather events, but few are very well prepared to deal with them.
“Overwhelmingly, throughout all parts of the globe, in particular in North America and Asia Pacific, there was agreement that extreme weather events had grown in frequency and severity as it relates to utility networks over the last ten years, and an even greater percentage of respondents...felt that trend was likely to increase further over the next ten years,” Mr Histon said.
“The highest percentage was in the Asia Pacific with 94 per cent of respondents saying ‘yes, significantly’, or ‘yes, moderately’ we expect more extreme weather events to occur over the next ten years.”
Around the world, high-impact weather events are becoming more frequent and severe, with bushfires in Australia and California, floods in India, typhoons in South East Asia and heatwaves in Europe among some of the most recent examples. These events are putting increased operational stress on our electrical networks, however, findings from a recently published report from Accenture has found that most electric utilities remain unprepared for the risks of this new reality.
However, despite recognising the potential threat, increased discussion of resilience in the sector and within industryfocused literature, only 24 per cent of those surveyed felt they were very well prepared to manage the challenges.
Mr Histon said traditionally, utilities have focused on the reliability of their energy systems and considered point events that may occur in particular parts of the network, and built infrastructure with a certain amount of redundancy to be able to overcome those predicted scenarios based on asset failure analysis using post hoc metrics.
“What we’re seeing now is an increase in more widespread events such as pandemics, cyber attacks or widespread
disasters that are affecting the network as a whole, and we’re also seeing a greater intensity in events. What that means is that we can’t necessarily rely on historical information and predicted scenarios to be able to plan for a response,” Mr Histon said.
“Interestingly, we asked a question about whether utility executives felt that events considered innocuous previously were now threatening network stability. Over 80 per cent said yes, and in Asia Pacific that [response] was closer to 90 per cent.
“So we can end up in situations today where the sun is shining, there’s no major storm or catastrophe but given the output from solar, wind and prevailing network conditions, there can be a threat to grid stability.”
In order to overcome these threats, the response requires a shift in mindset from reliability to resilience.
Mr Histon said that unlike a reliability strategy, a resilience strategy is focused on an analysis “of system-wide failures where multiple events may happen concurrently and there’s a requirement for the system to adapt with more flexibility to preserve supply to critical customers and maintain electricity and energy services with minimum impact to end users”.
“This is managed through engineering solutions as opposed to building and establishing redundancy. Resilience also requires a consideration, not just of how to respond when an event happens and how quickly we can repair or replace assets, it requires complex planning prior to an event and it requires analysis after the event occurs with a feedback loop to understand how we can adapt systems and improve analysis to prevent events from occurring subsequently.”
Far from shifting the focus away from reliability, resilience seeks to verify that utilities can expand their definition of reliability while also developing the additional, supporting capabilities they will need to provide an elastic response in the face of stressed or extreme conditions.
Mr Histon said the Accenture report established three strategic imperatives that are needed for utilities to establish resiliency.
1. Establish the foundations of resilience
♦ Develop leadership in resilience within and outside the business
♦ Underpin investment and performance targets with clear regulatory mechanisms based on risk and societal value of resilience
♦ Develop a robust quantitative basis for resilience risk analysis and investment decision-making
2. Build the resilient network
♦ Build new system flexibility capabilities through digital solution deployment, as well as invest in redundancy, network reconfiguration, distributed energy resources, microgrids and customer participation to limit the impact of extreme events
♦ Utilise artificial intelligence and emerging technologies to enhance outage prediction and system restoration strategies
♦ Harden the network through traditional approaches such as pole replacement, undergrounding of assets and development of flood defenses
3. Explore emerging resilience services
♦ Support the utilisation of end user resilience solutions
♦ Develop differentiated network resilience solutions to support poorly served communities and those with high resilience requirements
According to the Accenture report, flexibility in particular will be key to building a resilient network for a number of reasons:
♦ Although network hardening can be highly effective, it also tends to be very expensive, time consuming and needs to be focused on the highest-risk assets that do not have other mitigation options
♦ Since the types and locations of weather risks are evolving, being adaptable in potential responses is highly valuable in delivering long-term resilience
♦ A focus on flexibility can be more cost-effective than other options, improving the utilisation of existing asset and workforce capacity
♦ Flexibility improvements can support the wider agenda of greater active management of the distribution network, supporting greater distributed generation volumes, customer participation, reliability and resilience against other risks such as cyber attacks and earthquakes
Mr Histon said 35 per cent of survey respondents agreed flexibility was the most cost-effective resilience improvement area they expect to be their greatest priority over the next ten years.
“As an example for a remote community, in the past we may have focused on improving reliability by building a redundant network link; a more flexible solution may involve supporting that community with its own storage and generation capacity which may be engaged in conjunction with a demand management scheme that can identify and dispatch discretionary demand. That remote community might then be able to survive for an extended period without a connection back to the broader grid if we use those flexibility solutions.
“Those concepts can also be applied on a more macro scale, so that conceivably parts of our broader energy system may be able to operate in some form of islanded mode for a period of time where that part of the system or that subsystem is reliant on its own generation storage and demand management mechanisms.”
Mr Histon said the concept of flexibility can be considered from several angles, including in terms of operational flexibility that exists within a utility and the people that manage it, and the increasing number of customers, both small and commercial, that own storage and generation facilities that can be classified as discretionary and dispatched when not essential.
Mr Histon said the challenge for achieving a more resilient mindset is how it is measured and how it is incentivised.
“Typically our current mechanisms globally focus on identifying reliability metrics and incentivising meeting those metrics. Often those metrics exclude what might be considered high impact, low frequency events, such as a large scale natural disaster, so there’s more work to do to measure the societal value of resilience,” Mr Histon said.
While the challenge of becoming more resilient may be formidable, it is also unavoidable, and those utilities that do not act now are putting their organisations and their customers in jeopardy. Therefore, supporting resilience more directly is a significant part of the industry's growth trajectory and it is up to utilities to convince policymakers, customers and other stakeholders to make resilience part of the businesses' remit.
When your staff can’t work from home, systems can be put in place now to keep your workforce and your business safe.
COVID-Safe workplace plans need effective record keeping that goes beyond who was working each shift – systems need to communicate quickly and effectively should a case of COVID-19 be identified on-site.
Workforce continuity depends on timely and relevant information being available to contact tracers. If they can’t pinpoint who was a close contact to someone exposed to COVID, work sites could face continuity challenges.
Contact Harald is a fast tech-based contact tracing system and allows workplace COVID outbreaks to be contained quickly, close contacts tested and self-isolation to occur while awaiting results; also resulting in minimising further transmission in the community.
Contact Harald’s key benefit is the inherent speed at which initial alerts can reach only recorded close contacts, facilitating reduced time to contain an outbreak, implement essential testing and advise self-isolation.
Workplaces using Contact Harald become the 'first line of defence' and could readily provide digital primary contact tracing data sets (within the context of their workplace) to assist DHHS commence contact tracing earlier than when COVID-Safe details can be accessed.
The proximity detecting technology is contained within a wearable card – just like an employee ID or access card. Contact Harald differs from a mobile app in that it only works when in proximity to cards worn by others. Unlike other contact tracing technologies, Contact Harald doesn’t require a mobile phone to act as the hardware to drive the software, it doesn’t use GPS and, when used as a compliance tool in businesses, it can offer 100 per cent uptake.
Lanyard and clip-on versions are available and can be cleaned and sanitised with an alcohol wipe. As the cards use low energy Bluetooth, they also work under personal protective equipment (PPE) and have a long battery life – between six to nine months.
Contact Harald can be up and running within days. The standard system – cards, lanyards/clips, a tablet-based registration platform and operating software – is designed as an “out of the box” solution that can be deployed quickly, and set up is contactless. The system is self-contained and needs no complicated IT integration, so onboarding of new workplaces is contactless.
Software can be tailored to work seamlessly across multiple work sites. The system requirements remain the same – each staff member/contractor/visitor/resident still needs their own card, and each work site will need its own tablet to register details.
System specific requests and operational needs can be accommodated to allow the system to work across multiple workplaces. Customised systems are currently being delivered to workplaces within two to ten days of orders being received, depending on the scope of customisation required.
Plan to keep your business COVID-Safe. Be worksafe inspection ready and work through the pandemic. Get in touch with Contact Harald by calling 1800 290 566, emailing business@contactharald.com or visiting www.contactharald.com/ready
This time last year, airports were a hive of activity –thousands of people buzzing through the terminal excited to begin a new adventure, take a holiday or jet off on that important business trip. These days they’re so quiet you could almost hear a pin drop.
The gradual reopening of state and territory borders has provided a glimmer of light at the end of the tunnel, but for many airports, particularly those in regional areas, passenger numbers are still down around 90 per cent.
Our airports are hurting. It doesn’t matter if there are two planes flying in or 200 – the operating costs of keeping the runways and terminals open remains largely the same.
Larger airports are spending $300,000 a day to stay open. Knowing this, it would come as no surprise that collectively Australian airports are losing more than $320 million a month. That’s more than $2.2 billion since the pandemic began.
The aviation industry was one of the first to feel the effects of the Coronavirus crisis and will be one of the last to recover. The policy focus of the Federal Government’s aviation support package is on the airlines and government agencies including the Civil Aviation Safety Authority and Airservices Australia, and not the existing, essential infrastructure such as airports which are struggling.
They’ve had to rely on a “trickle-down” of indirect assistance from the airlines to help cover the costs of domestic security screening – a government-mandated requirement – which are in no rush to pass the rebates on.
As an essential and critical piece of infrastructure, all levels of government have been relying on airports during this pandemic. They have been good corporate citizens staying open to allow repatriation flights, to transport freight in and out of the country, and to get essential workers such as medical professionals and the military to where they’re needed.
Australia is depending on a sustainable aviation network, particularly as we try to reboot the tourism industry, but there is a growing risk airports will cut services to save costs, they will lose skills or in the case of some airports close facilities for periods of time.
Australia’s major airports were already among the world’s most lean and efficient before the pandemic and now they’re reaching the limits of how much they can absorb.
Data collected by the Australian Airports Association suggests 70 per cent of staff at regional airports have either lost their jobs, been placed on reduced hours, forced to take leave or have been redeployed. This is partly because regional council-owned airports are not eligible for JobKeeper.
Regional Australia accounts for 45 per cent of Australia’s tourism. If we are looking at a tourism-led aviation recovery, our regional airports will need government support to ensure they’re able to operate as a gateway to these holiday destinations.
All airports are doing it tough, but if there’s one positive to come from the lack of planes taking off and landing, it’s allowing for essential upgrades, particularly at our regional airports which face an infrastructure deficit over the next few years of more than $170 million.
Investing in critical aeronautical infrastructure projects such as upgrading taxiways, building perimeter fencing and resurfacing runways will create new jobs and boost spending in regional communities at a time when they need it most.
Aviation is critical to the continued success of Australia’s economy, supporting more than 200,000 jobs and prior to the pandemic contributed $35 billion – around two per cent – to the nation’s GDP.
It has a bright future and our airports will be looking to the skies, willing to work with the government on an aviation plan to reopen the borders, restart aviation and tourism, and get the economy moving again.
As technology continues to develop faster than ever before, and with the Coronavirus pandemic highlighting the need for improved digital solutions, machine learning and artificial intelligence are set to play an even bigger role in the future of asset management. At the recent Asset Management for Critical Infrastructure Virtual Conference, part of the 2020 Critical Infrastructure Summit, infrastructure and utility leaders gathered for a panel about the future of machine learning, artificial intelligence and digital twins in asset management. Here are the key points from the discussion.
Speakers on the panel included Nicola Belcher, Director of Rail Assets, Projects and Compliance, Victorian Department of Transport; Russell Riding, Automation Team Leader, Melbourne Water; and Bruce Thompson, Executive Director Spatial Services, NSW Department of Customer Service.
Since COVID-19 hit, the utility and infrastructure sectors have needed to change some aspects of the way they work very quickly, including keeping critical assets running while navigating constant changing restrictions and lockdown measures.
During the panel, the three speakers discussed the ways their work has changed this year. Ms Belcher said that the rail sector provides a critical service for the public and that while Victoria was in Stage 4 lockdown following a second COVID-19 wave, the rail industry needed to keep operating to get frontline and essential workers to their workplaces.
Ms Belcher also explained that while the majority of office staff were able to transition to remote working, projects like the Level Crossing Removal project and the Melbourne Metro Tunnel project are considered critical, with work continuing despite the lockdown restrictions.
“The biggest change to maintenance and renewal activities has been the work practices out on-site. So in Victoria we need COVID-Safe plans for people to be able to continue to work on-site and that has required high-risk areas to consider which people they have on-site, and how long they spend on-site,” she said.
Ms Belcher said the Victorian Department of Transport recognised a big opportunity for the uptake of technology on sites, including utilising drones for further workplace monitoring – something her department is looking further into for the future.
Similarly, Mr Riding said that due to the critical nature of water supply, Melbourne Water’s field staff have been required to continue working through lockdown, all work was carried out following up-to-date state health advice including specific hygiene and social distancing protocols.
“We’ve had to rely on the use of newer technologies such as video conferencing, Skype and Microsoft teams to be able to provide that support to the asset management team,” he said. This is working well.
Mr Riding said apps, which were already in use at Melbourne Water, had become more critical to the team during this time and allowed the utility to utilise, and become more familiar with, technology they already had in place.
Mr Thompson said that the NSW Department of Customer Service was fairly well prepared for the changing work environment, having trialled remote working before the pandemic hit, so processes were already in place to assist with the transition.
“We ran up about 70 additional virtual machines in our cloud-based server centre and we’re getting productivity gain out of that because large image processing jobs, and other things that we do in that knowledge space, are now taking less time,” Mr Thompson said.
Machine learning has become a major tool for infrastructure and utility companies in recent years with the need for autonomous technology to help monitor and manage critical assets.
During the panel, Mr Riding discussed one of Melbourne Water’s first machine learning projects, which focused on pump selection.
“We have a treatment plant, Winneke Treatment Plant, up in the north east of Melbourne and there’s a major pump station there that supplies water to that treatment plant – there’s actually six different pumps there,” Mr Riding said.
“We implemented a machine learning solution that basically looks at historical data and determines the most efficient combination of pumps and speeds for any particular flow rate, and it then directs the control system on-site to select those pumps in that manner.”
Mr Riding said that since the implementation of the machine learning technology approximately two years ago, Melbourne Water has seen a 20 per cent (or around $200,000) saving in the energy cost for running the pump station at the Winneke Treatment Plant.
During a follow up question from one of the delegates, Mr Riding also explored the role that apps and artificial intelligence can play in efficient water operations.
“Because [Melbourne Water] is field based, it’s easier for us to collect data via an app and have it in real time. We’ve already invested in certain apps to capture calibration data and similar sorts of asset information so that we can understand if the asset is performing correctly and do some reporting to understand where we have issues and address them correctly,” Mr Riding said.
“Overall, having those apps allows us to provide a higher level of service, whether it’s water supply, sewage treatment, or even drainage.”
Mr Riding also talked about the innovative IoT and camera technology Melbourne Water has implemented to manage blocked drains in the utility’s network. Images are taken of stormwater grates that regularly get blocked with rubbish and debris.
These images are then uploaded to a cloud platform where artificial intelligence and image recognition technology is used to alert the asset management team of blockages in the network, who then mobilise teams to clean the blocked grates on an as-needed basis.
This reduces the resources needed to manually check for blockages after storms as the technology will identify specific assets that need attention, thereby improving overall efficiency.
When it comes to other technologies having significant impacts on asset management, Mr Thompson talked about the benefits of digital twins in the sector.
“The spatial digital twin is a way of bringing together people’s data in an accurate and reliable way so that we can position private sector infrastructure, whether it’s a building
or an asset, against government infrastructure and assets,” Mr Thompson said.
“The other benefit is the temporal nature; being able to look at the world at the point in time a transport model was generated, maybe five years ago, and understand what the road network was like then rather than what it’s like now. Then being able to move forward in time and put down multiple proposals or competing proposals – a road corridor against a train line, or a road corridor against doing nothing – and compare what’s happening.
“It’s really about bringing that together on this digital workbench.”
March 2021
Deadline: 8 January 2021
Road surfacing and design Spatial & GIS
Rail equipment Training and skills
Signalling, tracking and control systems
Condition monitoring and maintenance
Software, communications and connectivity
DISTRIBUTION (TBC)
SAFETY IN ACTION 2021 THE
LOCATE 2021
September 2021 Deadline: 9 July 2021
Road and Traffic Ports
Safety and risk management
Cranes & heavy lifting Freight and logistics
Sustainability Asset Management
Asset inspection & drones/UAVs
DISTRIBUTION TBC
June 2021 Deadline: 9 April 2021
Smart cities Earthmoving outlook
Noise and vibration Bridges
Automated and electric vehicles
Urban development Intelligent Transport Systems (ITS)
Road surfacing and flexible pavements
DISTRIBUTION (TBC) CORE 2021
November 2021 Deadline: 1 October 2021
AusRail Airports
IoT & cloud communication Tunnels
Corrosion Disaster management
Machine learning Recycling and waste management
Landscaping and vegetation management
DISTRIBUTION TBC
Sign up to AusRAIL Live & On Demand to enjoy all the best of AusRAIL from the comfort of your home or office.
After an unprecedented 2020, there could not be a better time to come together with rail industry leaders from across Australia, New Zealand and beyond to network, share and plan for the future.
Our online, live and on demand format gives you more access to content than ever before and the chance to network with colleagues from across the globe without even having to leave your office. Join us live to stream events as they happen, or catch up later on demand.
Our exhibition space will be powered by AI, allowing you connect with the people that matter most to your business. Showcase live demos, share videos and product information and identify new leads through your own online booth.
Join us at AusRAIL Live & On Demand to connect with the industry leaders shaping the future of rail in Australia and New Zealand.
To become an exhibitor and promote your business, contact Deborah Bocock at Deborah.Bocock@informa.com.au.
Activ8me Business Services offers communications solutions for utility operators in remote Australia.
Our solutions include:
Unlimited data plans
Low contention rates
Fixed or portable hardware
Solar, self-sufficient options
Optional P2P, Extended Wi-Fi and Public Wi-Fi
Installation & Field Support Australia-wide
Our solutions overcome the communications limitations of operating in remote locations.
With our internet services, operators can access Cloud-based applications, integrate remote monitoring and utilise M2M/IoT technologies.
No matter your challenge, we offer scalable solutions to meet any requirement. Our in-house team can even design a bespoke solution to fit your needs.
For more information contact our Corporate Sales team or visit: business.activ8me.net.au