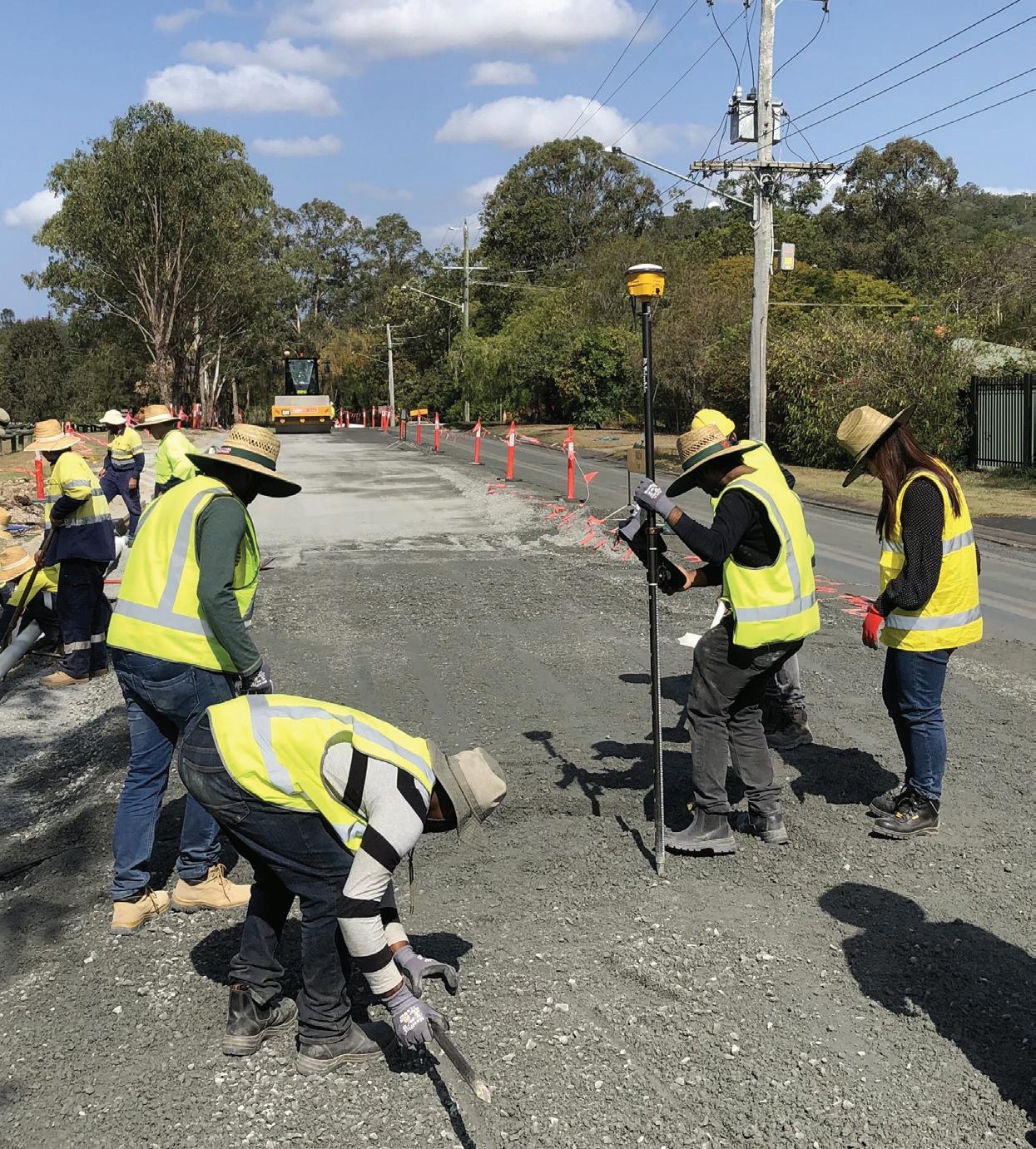
Do we need private INVESTMENT TO FUND RECOVERY?
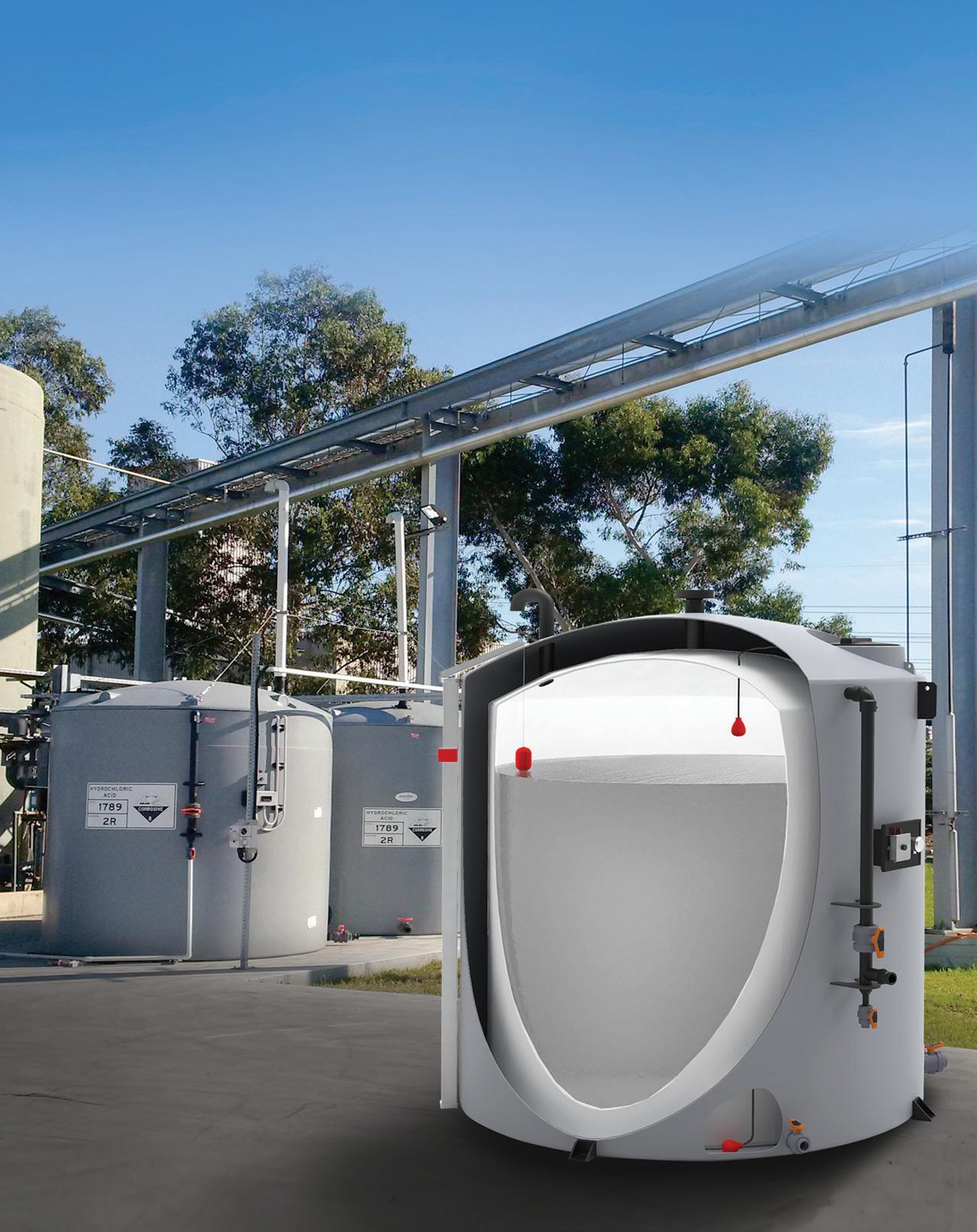
Do we need private INVESTMENT TO FUND RECOVERY?
Breaking new ground in the motor grader industry, John Deere SmartGrade Motor Graders offer the first-of-its-kind mastless 3D integrated grade control from the factory, arriving at your jobsite ready to work. Unlike traditional aftermarket grade-control systems, John Deere’s innovative SmartGrade graders have no external masts or cables, allowing virtually unlimited range of grade-control and hydraulic functions. SmartGrade Motor Graders also include a new suite of intuitive automated features designed to lessen operator workload and boost productivity. Plus these machines are backed by your local John Deere dealer support team for added peace of mind. It’s a New Day and a New Deere.
Published by
Monkey Media Enterprises
ABN: 36 426 734 954
204/23–25 Gipps St
Collingwood VIC 3066
P: (03) 9988 4950
F: (03) 8456 6720
monkeymedia.com.au
info@monkeymedia.com.au infrastructuremagazine.com.au news@infrastructuremagazine.com.au
Editor Jessica Dickers
Journalists
Imogen Hartmann
Eliza Booth
Michelle Goldsmith
National Media and Events Executives
Rima Munafo
Brett Thompson
Design Manager
Alejandro Molano
Designers
Jacqueline Buckmaster
Danielle Harris
Marketing Assistant
Stephanie Di Paola
Publisher Chris Bland
Managing Editor
Laura Harvey
After a disruptive and unpredictable year, we have finally made it to 2021. While all of the challenges of 2020 did not completely disappear when the clock struck midnight, we’re being cautiously hopeful of a successful and fulfilling upcoming year for the infrastructure industry.
Over the last few issues we’ve talked about the sector’s role in the postCOVID economic recovery, and this year we should start to see this more in action with the progress of major projects across the road, rail, port and airport sectors.
A recent Infrastructure Australia (IA) study that looked at the future of infrastructure beyond COVID-19 found that the sector proved itself to be relatively resilient to the pandemic and that the impacts of the last year have helped to accelerate trends such as digitisation, more local and regional infrastructure use, and service innovations and adaptations.
Infrastructure Australia is also set to release its 2021 Priority List in February, and this year it is partnering with Infrastructure magazine for a virtual launch event. The Priority List is a critical document for Australia's infrastructure sector, and we’re very excited to be working with IA to get this key information out to you. For more information and to register, visit www.ipllaunch2021.com.au.
Infrastructure Partnerships Australia also recently released its 2020 Australian Infrastructure Budget Monitor, which showed that across Australia, governments are investing $225 billion in infrastructure over the next four years – an increase of $46 billion from last Budget season. This funding aims to combat the economic downturn from COVID-19, with NSW set
to spend the most – $84 billion over the next four years.
NSW and Victoria ($70 billion) combined account for 68 per cent of total infrastructure funding across the country, so expect to see some more funded projects start to come to fruition this year.
We’ve touched on a few of these topics in this issue of the magazine, with articles on private investment, new service models and opportunities for reform. This edition also looks at the role of software, communications and connectivity in the sector, as well as updates in rail, from asset management to innovation deficits, funding and projects. The rail sector is one area in particular that will be stepping up when it comes to supporting the country’s economic recovery.
As we’ve seen from multiple COVID clusters that broke out over the New Year break, causing rapidly changing restrictions and border closures, there is still a lot of uncertainty and risk around domestic travel, and this seems likely to continue, potentially even once vaccine distribution begins.
This means that for the industry, virtual events are still the best way to network and find out new information and updates on the sector. Infrastructure magazine will be running the Critical Infrastructure Summit virtually over two weeks in April to keep you up to date on projects, industry outlook, funding, asset management, disaster management and the future of infrastructure. Head to www.criticalinfrastructure.com.au to register for free.
In addition, we’ve got other exciting plans for 2021 across our print and digital channels, and will continue to be the voice of the industry as the sector works to meet the post-COVID infrastructure demand.
Jessica Dickers EditorEARLY ACTION, ADAPTABILITY AND NEW SERVICE MODELS: HOW COVID-19 IS SHAPING INFRASTRUCTURE USE
Infrastructure Australia has released its findings from research into how the COVID-19 pandemic is changing the way Australians use infrastructure, the impact on long-term planning and development, and the key trends that have emerged.
INDUSTRY INSIGHTS
DO WE NEED PRIVATE INVESTMENT TO FUND RECOVERY?
As stimulus spending ramps up, a ten-year trend study shows private investment in new infrastructure has declined since 2010.
FIXED AND PORTABLE INTERNET FOR REMOTE INFRASTRUCTURE PROJECTS
Reliable, business-grade internet is critical to the ongoing operations of infrastructure projects. The necessity of connectivity for continued operation is just as pressing for permanent, fixed sites as it is for temporary, field sites.
REPLACING CRITICAL ASSETS IN A PANDEMIC
THE CRITICAL INFRASTRUCTURE SUMMIT IS BACK IN APRIL 2021
CONSTRUCTION’S COVID-19 OPPORTUNITY FOR REFORM
IT’S TIME TO FOCUS ON THE SOCIAL VALUE OF INVESTMENTS
As the industry voice for design, advisory, and engineering businesses in the built and natural environment sectors, Consult Australia has been working with members to build the case for a greater focus on social value in considering infrastructure investments, which it sees as critical to Australia’s COVID-19.
SIGNALLING, TRACKING AND CONTROL SYSTEMS
DEVELOPING A NEW TRAIN MANAGEMENT SYSTEM
Advanced Train Management System (ATMS) is a modern, communications-based, safe-working system for the ARTC, which has been custom engineered for Australian conditions by ARTC and technology partner Lockheed Martin. It enhances the operation of the national interstate rail network, and provides a quantum leap forward in safety, capacity and productivity for freight rail operations..
CONDITION MONITORING AND MAINTENANCE
PREPARING ASSETS FOR WHATEVER THE SUMMER BRINGS
INFRASTRUCTURE-BASED SENSOR TECHNOLOGY FOR "COOPERATIVE AWARENESS" PROJECTS
CREATING AUSTRALIA'S FIRST SMART AIRPORT
THE DIGITAL TECHNOLOGIES OPTIMISING CONSTRUCTION IN 2021
INTELLIGENT TRANSPORT SYSTEMS: A REVOLUTION ON OUR ROADS
WHAT’S IN STORE FOR THE FUTURE OF DIGITAL TWINS?
The 2020 NSW Spatial Digital Twin is part of the Western Sydney City Deal partnership that brought together federal, state and local government under a set of 38 commitments. The Digital Twin was part of the project’s commitment to coordinating information that supports planning and broader liveability targets.
FINDING THE FAST TRACK FOR RAIL INNOVATION
As COVID-19 restrictions hit Australian supply chains, three quarters of rail businesses surveyed by the Australasian Railway Association (ARA) said they were looking to increase their use of local suppliers to support their operations..
RAIL TRESPASS PREVENTION –DETECTION AND INTERVENTION
RATCHETING PERFORMANCE OF HIGH STRENGTH RAIL STEELS
INTELLIGENT COMPACTION IMPROVING THE QUALITY OF ROAD CONSTRUCTION
VIRTUAL REALITY ENABLING ‘TEST DRIVES’ OF ROAD PLANNING
MATERIALS UNDER THE MICROSCOPE
INFRASTRUCTURE SKILLS IN A POST-COVID WORLD
ECONOMY-WIDE IMPACT OF DRONES
MITCHELL FREEWAY EXTENSION TRAINING AND SKILLS SPATIAL & GIS ROAD SURFACING AND DESIGN
From condition monitoring on remote assets to mapping the spread of bushfires, drones have had a significant impact on many sectors in recent years, including infrastructure. But the technology has even more potential for the future, including a predicted economic boost of $14.5 billion in GDP for Australia and the creation of 5,500 full-time jobs each year, over the next 20 years.
MILLION INVESTMENT INTO NARRABRI TO TURRAWAN RAIL UPGRADE
RUNWAY UPGRADE COMPLETE AT GOLD COAST AIRPORT
HARBOUR BYPASS GETS
Preamble
In this role, Tom is responsible for the design and implementation of all technology and cyber security aspects of Australia’s first smart airport, which is due to open in 2026. Over his career, Tom has been involved in the creation, implementation and operations of complex technology systems across a range of sectors, including financial services, transportation, public sector and media amongst others. With a great deal of experience across both the FMCG and aviation industries, Tom has held a number of transformational technology leadership roles within a range of global brands. He is widely regarded for providing thought leadership in technology outsourcing.
Freptatibus nes ationse aut et aut mo quos aruptatus int, nonsequid magnis nonsedipsunt explitas andi que sandae veles cuptatiis et as ut omnimetur acerum ese eos sit, cus non restrum que nat maximod mi, quia dolupta tustis dent pra prat as sus.
Managing Director, Infrastructure Skills Advisory
With over 20 years’ experience in education, major projects and the private sector, Claire Parry is an internationally recognised expert in social procurement, workforce development and industry participation. Claire is Managing Director of Infrastructure Skills Advisory, a specialist consultancy that enables government, industry and businesses to deliver socio-economic outcomes through major infrastructure projects. She advises organisations that commission, procure or deliver jobs, skills development, diversity and inclusion, and industry outcomes.
Claire works with education and industry to develop and deliver new competency frameworks, qualifications and training programs, and industry training facilities for infrastructure, construction, engineering and rail.
Claire’s experience spans major infrastructure projects in Australia and internationally, including Sydney Metro, Regional Rail, Inland Rail, WestConnex, Sydney and Canberra Light Rails, and Crossrail, UK
Jerome Pun Senior Research Engineer, Monash Institute of Railway TechnologyJerome conducts applied research and consulting work for different railway operators and organisations His expertise includes multi-body dynamic simulation, plastic deformation behaviour of high strength rail steels and contact mechanics. Over the last four years, he has been involved in multiple projects to assist different railway operators and organisations within Australia and overseas resolve various wheel-rail interface related issues, and improve the efficiency of their operations. Jerome also recently won the Australasian Railway Association’s (ARA) Emerging Rail Specialist Award for his work.
Marie was appointed Global Infrastructure Hub CEO in January 2019. Prior to joining the GI Hub, she was the Head of Asia-Pacific for Acuity, the advisory services business of the SNCL group, helping clients in regard to infrastructure project strategy and finance. From 2011 to 2014, Marie headed the Infrastructure Initiatives department of the World Economic Forum, where she led their thought leadership activities, publishing thought leadership reports on best practices in the infrastructure sector. She led the dissemination effort of these best practices to governments and advocated to coalitions such as the B20 and the G20.
Before that, Marie worked for European utilities Essent and RWE where she drove their business development activities in the Africa and Central Asia region for various commodities, including their equity investment in LNG and hydro power plants. She started her career in 2001, and worked for various engineering consulting firms holding several technical and commercial positions for energy and transport projects in Africa, Middle East and Europe.
Nicola is responsible for implementing Consult Australia’s strategy, building ongoing external relationships, and for leading its advocacy and government relations agenda on behalf of member firms.
Nicola is a government relations specialist, and has represented industry associations in the United Kingdom, the European Union and Australia. She has worked across a range of sectors including general insurance, consumer finance, alcohol and education, in addition to consulting engineering. She has an Honours Degree in Law from the United Kingdom, and was previously Consult Australia’s Director of Policy and Government Relations.
Steve KanowskiPartner - Transport & Infrastructure, Deloitte Access Economics
Steve has more than 35 years of experience working in transport and infrastructure advisory positions for both Commonwealth and state government organisations, as well as in commercial consultancy.
Steve has extensive experience advising Australian government departments, government-owned corporations and private companies (financial institutions, operating firms and investors) on a range of economic and commercial issues in the transport and infrastructure sectors across aviation and airports, maritime and ports, railways, roads, freight and supply chain logistics, and public transport etc.
Steve joined Deloitte in 2017, after four years in the Queensland Government, with roles including Chief Economist & General Manager (Strategic Policy), Transport & Main Roads, and Chief Economist & Executive Director (Infrastructure Policy) with the Department of State Development, Infrastructure & Planning.
The Federal Government will invest $44.7 million in the Australian Rail Track Corporation’s 35km upgrade of the Narrabri to Turrawan Line between the Hunter Valley Coal Network and Inland Rail.
The project will deliver a corridor from Northern NSW to the Port of Newcastle capable of 25 Tonne Axle Load (TAL) trains at 80km/h. Currently the 35km section of track is only capable of accommodating 20.5TAL and comprises steel and timber sleepers, aging 47kg/m rail for most of the line, and poor track geometry, formation and ballast in some locations, resulting in limitations on its capability.
The upgrade represents a significant benefit to agricultural producers transporting grain, cotton and other primary products from Northern NSW to domestic and export markets, as well as the opportunity to back-haul materials, supplies and agricultural inputs into the region more efficiently and cost-effectively.
Deputy Prime Minister and Minister for Infrastructure, Transport and Regional Development, Michael McCormack, said, “We are investing in this project to greatly improve the quality and capacity of this crucial rail connection, better linking northern New South Wales, Inland Rail and the Port of Newcastle.
“This upgrade will allow longer and heavier freight trains from Northern NSW –transporting food and fibre – to access the Newcastle and Sydney ports.
“Greater volumes of freight moved on each train will reduce transport costs and make Australian exports more competitive.”
The project will see the steel and timber sleepers replaced with heavy-duty concrete ones, as well as upgrading critical level crossings and improving the rail quality on the Narrabri Coal Junction to Turrawan and the Turrawan to Narrabri North sections.
The project will commence in mid2021 and aims to be completed in 2023.
A$5 million upgrade of the Gold Coast Airport runway has been completed, with asphalt resurfaced on the southern 450m of the runway and 280m of adjoining taxiways recently grooved – a process which allows water to run off the surface under aircraft tyres.
The window for night works was increased due to fewer late night and early morning flights during COVID-19 travel restrictions, allowing the project to be completed sooner and delivering a cost saving of about five per cent.
Gold Coast Airport COO, Marion Charlton, said airside infrastructure projects required many months of careful planning and coordination.
“Critical maintenance projects like these are forecasted years in advance,” Ms Charlton said.
“The overlay was a priority project that we needed to deliver and the reduction in flights provided a benefit, allowing the project to happen more quickly and with a cost saving.
“This essential investment is critical to ensuring safe aircraft operations at Gold Coast Airport now and into the future.”
Work was undertaken at night to limit any operational impact as a result of closing the runway.
The project, delivered by Fulton Hogan, covered a total area of 32,000m², requiring 6,500 tonnes of asphalt.
A crew of up to 100 was on-site each night, completing the works in sections of about 90m per night on average.
Overlay projects are generally undertaken every 10-15 years. The other 2km of the runway was resurfaced in 2016.
The Federal Government has given the Coffs Harbour bypass, the town’s biggest ever infrastructure project, the green light following its assessment and approval under the Environment Protection and Biodiversity Conservation Act (EPBC Act)
Deputy Prime Minister and Minister for Infrastructure, Transport and Regional Development, Michael McCormack, said the 14km bypass, which received official planning approval, is one of the 15 major projects that the Federal Government committed to fast-tracking in June 2020.
“The bypass is going to take more than 12,000 vehicles a day out of the centre of Coffs Harbour, reduce travel times by as much as 12 minutes by bypassing 12 sets of traffic lights, and improve safety for all road users,” Mr McCormack said.
“Transport for NSW has now received the final stamp of approval after close scrutiny by the NSW Minister for Planning and Public Spaces, and the Australian Minister for the Environment.
“This approval includes the proposed tunnels at Roberts Hill, Shephards Lane and Gatelys Road, as well as assessing the project for its social, environmental, heritage and economic impacts, and gives the project team the green light to go ahead with major work.”
NSW Minister for Regional Transport and Roads, Paul Toole, said the Pacific Highway was a major contributor to Australia’s economy, and the Coffs Harbour bypass would be a key link in this vital piece of the nation’s infrastructure.
“This bypass alone will support about 12,000 jobs over the whole lifecycle of the project, providing about 2,000 local jobs for the community of Coffs Harbour during construction, which shows how serious we are about investment in regional NSW,” Mr Toole said.
“The local community has played a huge role in developing this project – from helping shape the design for the bypass to engaging with the experts in the field to ensure we can get on with the job of delivering on our promise.”
The project is expected to take around five years to build, weather permitting.
The Port of Townsville has announced the winner of the largest contract of the $232 million Channel Upgrade project, with the contract awarded to Hall Contracting.
The works include capital dredging to widen 14.9km of sea channels over two years and reclamation of 62 hectares of land through beneficial reuse of dredged material.
Employing a local workforce of more than 70 full-time employees, the contract follows the extensive work over the past 18 months to build a 2.2km rock perimeter wall to receive the material.
Port of Townsville Chief Executive Officer, Ranee Crosby, said Queensland-based Hall Contracting has partnered with Townsvillebased Pacific Marine Group to offer extensive experience in dredging and reclamation.
The pair has committed to almost 100 per cent of this project being resourced from Queensland-based businesses.
“Hall Contracting has presented the best offer to complete the works,” Ms Crosby said.
“Over the course of the project, they will provide meaningful training across a range of vocations including vessel crew, marine engineers, diesel fitters, hydraulic fitters, boilermakers, earthmoving operators and dredge operators.”
The Channel Upgrade project will widen the current shipping channel from 92m to 180m at the inshore (Port) end, tapering to 120m wide in the Sea Channel, increasing the size of cargo, cruise and defence vessels able to access the Port of Townsville.
“Their strong commitment to local industry and First Nations people’s participation, as well as employment and learning opportunities for tertiary students, apprentices and trainees, presents significant opportunities for our region.
The Port has committed $17 million for environmental monitoring and management programs as part of the project, including those covering dolphins, turtles, seagrass, coral and shorebirds.
An Independent Technical Advisory Committee is also providing expert oversight of the monitoring programs during the capital dredging works. Hall Contracting is expected to begin capital dredging in May 2021.
The Channel Upgrade is a joint project of the Queensland and Australian Governments, and Port of Townsville Limited.
The Channel Upgrade is a key initiative under the Townsville City Deal signed in December 2016.
The South Australian Government appointed a private operator to take over the running of Adelaide’s rail network from 31 January 2021.
Keolis Downer was announced as the new operator of the rail network.
Minister for Infrastructure and Transport, Corey Wingard, met with both the Rail, Tram and Bus Union (RTBU), and a representative from a breakaway group of local train drivers, to discuss the upcoming transition and future employment and training opportunities.
During the meetings, Mr Wingard made it clear the timeline won’t be shifting and that the current offer on the table for drivers to transfer over to Keolis Downer won’t be changed.
“As it stands, a total of 83 drivers have accepted an offer of employment with Keolis Downer and another 88 remaining on the government payroll will be made available to Keolis Downer to ensure essential public transport services continue to be delivered to the community,” Mr Wingard said.
Drivers who’ve accepted a job with Keolis Downer have secured permanent ongoing employment with no loss of terms or conditions, a transfer of all entitlements, free public transport travel, and a $15,000 incentive payment.
They have also secured a commitment of no forced redundancies for the next three years, and the right to transfer to the future operator at the end of Keolis Downer’s contract.
In late-2020, a new enterprise agreement was also reached providing a two per cent per annum pay rise for train drivers and other rail staff.
The RTBU had been pushing for a $65,000 incentive payment and a four per cent per annum pay rise over four years despite both nurses and tram drivers accepting a two per cent rise just months earlier.
“From next month Keolis Downer will also start delivering training programs for drivers to join the workforce,” Mr Wingard said.
“Experienced drivers from other networks will undertake a 22 week program and will be ready to join the workforce in August.
“Further intakes for 33 week-long programs in May and September 2021, and also early in 2022 for new drivers will mean that progressively drivers made available to Keolis for the transition will no longer be required and will be moved into roles elsewhere in government.
“More than 1,000 applications were received by Keolis Downer for train driver positions and it’s clear there’s plenty of people excited and eager to join the sector.
“This transition will not only deliver better services but will also mean very significant savings to SA taxpayers.”
• Pre-award audits of manufacturers, subcontractors and suppliers
• Experienced, certified and qualified inspectors
• Verification of manufacturing and testing in accordance with AS standards
• Surveillance inspections throughout the entire manufacturing process
• Individual inspection and test of completed equipment
• Pre-delivery and ship loading inspections
• ISO 9001-2015 QMS certified company
Defend your industrial networks.
Strengthen network security with cyber secure ready hardware.
As industrial devices become more connected through the Industrial Internet of Things (IIoT) there is not only great potential for businesses to optimise operations, there is also a significant challenge – cybersecurity. Moxa’s range of robust network devices meet the technical security requirements of the globally recognised IEC 62443 standard, which ensures your industrial control systems are well protected against network intrusions or attacks.
Connect with confidence.
Madison Technologies has been distributing Moxa’s reliable networking infrastructure Australia wide for more than 14 years. Our team is dedicated to ensuring our Moxa portfolio is fully supported with an extensive range held locally across our national supply chain, and a team of Moxa certificated sales and technical support engineers.
With increased awareness of cyber security attacks on industry, companies are starting to understand the devastating production and financial losses these attacks are capable of. Industrial networks are often full of legacy hardware that was never envisaged to be connected to the internet. This has led to the rise in targeted attacks on these networks and the need to implement security mechanisms to avoid exploitation and compromise.
The IEC-62443 standard was developed to assist with providing an international framework to work towards securing vulnerabilities in Industrial Automation and Control Systems (IACS) networks. Guidelines for basic, medium and high security levels within the standard denote increasing levels of security policy adoption.
A basic level includes items such as default password changes, account timeouts and enabling trusted access to the device. A high level of adoption may include device configuration file encryption.
Adoption of any level of IEC-62443 is optional and dependent upon a risk assessment of the network. While not a guarantee of threat immunity, it does serve as an excellent and agreed upon starting point.
To assist with adoption of the highest level of IEC-62443 conformity, Moxa has developed an “E” series managed switch range. These easy-to-install and configure switches allow the user to implement the highest level of the IEC62443 standard – with security built into the component. Not limiting itself to just switches, Moxa has also developed a range of compliant devices, including serial to Ethernet servers, protocol gateways, firewalls and wireless access hardware that are also IEC-62443 aware.
Obtaining an understanding of how secure your network is may seem like a difficult and long winded process, however Moxa’s MxView is the component supplier’s answer to a Network Management System (NMS). While it will effortlessly discover all Moxa and non-Moxa hardware on your network, automatically draw a topology map and provide an excellent overview of your network, it can also do a lot more.
The latest version will provide you with a colour coded visual of how secure your network connected devices are.
Four colour codes relate directly to the IEC-62443 standard (open, basic, medium, high). MxView allows you to centrally view security events as well as provide the ability to mass configure settings from a central location.
Being able to deploy changes and updates of settings relating to the IEC standard ensures a uniform deployment across the network. The MxView software suite is licensed based on the number of network connected devices being monitored. This makes it an extremely cost-effective network monitoring tool, with the added benefit of the security awareness monitoring, link bandwidth monitoring, and centralised administration of your network.
The contract for the construction of the fasttracked $215 million Mitchell Freeway Extension has been awarded to a new Joint Venture, with works expected to start in early 2021.
The contract for the highly anticipated Mitchell Freeway Extension from Hester Avenue in Clarkson to Romeo Road in Alkimos was awarded to the Mitchell Extension Joint Venture (MEJV), a consortium of BMD Construction and Georgiou Group.
When complete, this project, combined with the current widening works underway along the Mitchell Freeway northbound, is expected to save drivers travelling from the Narrows Bridge to Alkimos during the PM peak period up to 15 minutes travel time.
Fast-tracked to boost the economy post COVID-19, the $215 million freeway extension is expected to support 1,200 direct and indirect jobs during construction.
Major works are expected to start in early 2021 and completion is scheduled for late 2022.
The Mitchell Freeway will be extended 5.6km and the project scope also includes:
♦ A new interchange at Lukin Drive including duplicating the road between Mitchell Freeway and Connolly Drive
♦ A new connection from Marmion Avenue to Wanneroo Road through the extension and construction of a dual carriageway on Romeo Road in Alkimos
♦ Upgrade of Wanneroo Road to a dual carriageway road from Romeo Road to Trian Road
♦ A priced option to upgrade Butler Boulevard will remain, pending further discussions
The project will improve safety and reduce congestion on the freeway and local road networks within the fast growing outer northern suburbs
of Yanchep, Butler, Alkimos, Eglinton and Nowergup.
The Mitchell Freeway Extension Project, from Hester Avenue to Romeo Road, is jointly-funded by the Australian and Western Australian Governments, with each contributing $107.5 million.
Infrastructure Australia has released its findings from research into how the COVID-19 pandemic is changing the way Australians use infrastructure, the impact on long-term planning and development, and the key trends that have emerged.
As the COVID-19 pandemic spread, Australia's governments took early action, introducing travel bans, lockdowns and border controls, and supporting domestic supply chains. Communities adopted social distancing and moved to working from home. While these early measures successfully contained national case numbers, they prompted profound changes to the way people moved, consumed and worked, which changed patterns of infrastructure use.
The continuation of infrastructure construction across major projects was a key source of economic activity and employment at the height of the COVID-19 pandemic in Australia. However, months of lockdowns, social distancing and working from home has driven sweeping changes in how Australians use critical infrastructure.
Although the pandemic put our infrastructure to the test over the past year, Australia’s governments and infrastructure providers navigated dramatic changes to community behaviour and network requirements, and rapidly adjusted their service provision across the transport, telecommunications, digital, energy, water, waste and social sectors.
Infrastructure Australia’s new report, Infrastructure Beyond COVID 19: A national study on the impacts of the pandemic on Australia, found that compared with other OECD countries, our infrastructure networks have proven to be resilient under pressure and open to innovation.
Developed in collaboration with L.E.K. Consulting, our report presents a moment-in-time snapshot of how the pandemic has
changed the way we use infrastructure, and considers which of these changes could have lasting impacts on how we plan, fund and deliver the services we all rely on.
It finds that while COVID-19 has put a pause on the traditional driver of infrastructure – Net Overseas Migration –the pace of change in the sector has generally increased, with new emerging trends.
Major shifts in how Australians work, travel and consume goods and services in the wake of COVID-19 has driven the redistribution of existing demand, mode or channel switches, and acceleration of longer-term trends that were already underway.
We estimate that around four million Australians have been working from home since March 2020, representing 30 per cent of the total workforce. Our report found that a third of those people would like to continue doing so at least once a week, suggesting a permanent move towards a hybrid structure that will see a split of working time between the office and home –with significant impacts for infrastructure use.
Add to this 17.2 million telehealth consults between March and June 2020, teaching curricula and students moving online, and countless Zoom meetings, the past year has been characterised by a rapid shift from physical to virtual interaction with our health and safety front of mind.
Not surprisingly, this put significant strain on our broadband networks, with spikes in NBN bandwidth congestion growing to an average 60 minutes per week per
service at the height of the lockdowns in March 2020, and increased instances of customer complaints – particularly from small to medium-sized businesses.
The impact of large-scale remote working led to a surge in usage, with telecommunication providers responding by leveraging extra capacity in the network.
Latent broadband capacity was released to cope with the surge in demand – an example of responsive repurposing of infrastructure and assets that speaks to the resilience and adaptability of the network.
However, some suburban areas experienced network outages, and many regional Australians experienced internet access issues during lockdown restrictions, impacting their ability to work from home or undertake schooling remotely.
Working from home also catalysed a rapid uptake of digital collaboration tools – accelerating developing trends and triggering investment in cloud-based systems and cyber security.
Australians also accelerated their move to online retail channels and digital services, resulting in a substantial uplift in online sales and increased broadband network congestion.
The pandemic drove a 100 per cent growth in monthly online retail, five times the annual growth recorded in 2019, resulting in a growth in parcel delivery and micro-freight.
As a result of social distancing and work from home opportunities, some households embraced the opportunity to move away from dense metro areas, resulting in a 200 per cent increase in net migration from capital cities to regional areas. This caused an immediate increase in capital city vacancies, while rental demand increased in regional and coastal towns including Newcastle, Wollongong and the Sunshine Coast.
Some regions are also seeing a local boom of regional
tourism and population growth, and are experiencing less severe COVID-19 impacts. Strengthened regional cities, huband-spoke service models, and improvements to liveability and affordability can refocus regional investment.
The longevity of these changes is uncertain, however the impacts are likely to persist for some time as Australians continue to seek more affordable housing outside of the inner metro areas. If this trend continues, we could see reduced demand for urban transport and increased pressure on broadband networks in regional centres.
In 2020, Australians have evidently cherished greenspaces, both in metro areas and national parks.
There has been a 23 per cent increase in our use of national parks and greenspaces nationally. Research also shows that 87 per cent of Australians have noticed a positive shift in community attitudes towards urban green space, particularly amongst those living in high-density areas.
In a survey conducted by the NSW Department of Planning, Industry & Environment, 46 per cent of respondents claimed to have spent more time in parklands and gardens with many (94 per cent) using these spaces to undertake personal exercise.
Further, 72 per cent of NSW survey respondents cited that local parks have been ‘especially useful’ or ‘appreciated more’ during COVID-19, with Hermitage Foreshore, Western Sydney Parklands and Centennial Park visits up by around 144 per cent and around 100 per cent respectively compared to the previous year.
Generally, increased local activity including intense use of local greenspace could lead to reduced demand on toll roads. Policy reforms and programs supporting access and uptake could drive even greater sustainability.
Across the country, public transport providers moved quickly to support social distancing and hygiene measures, making improvements such as increased cleaning, and applying real-time occupancy data to public transport in line with social distancing initiatives.
However, in a reversal to the earlier trend of increasing public transport use, patronage in most cities fell to 10–30 per cent of normal levels in the initial lockdown and settled at a ‘new norm’ of 60–70 per cent of pre-COVID-19 levels. Traffic levels rebounded quickly, along with an uplift in second-hand car purchases, potentially indicating that higher car mode share may persist for some time.
A key focus for government and industry in 2021 will be to understand the structural impacts of COVID-19 on travel demand within Australia.
Together with the Bureau of Infrastructure and Transport Research Economics, Infrastructure Australia has convened a COVID-19 Cross-jurisdiction Roundtable to facilitate the exchange of ideas, techniques and tools for considering the long-term impacts of COVID-19 in travel demand models.
Taking a collaborative approach, we are working with industry, sector experts and thought leaders across government to understand how COVID-19 has changed the way we use infrastructure.
This will inform the Australian Infrastructure Plan, a major reform document that will provide a roadmap for the infrastructure sector to support recovery from the impacts of the pandemic, due for release in mid-2021.
As stimulus spending ramps up, a ten-year trend study shows private investment in new infrastructure has declined since 2010.
Infrastructure is the backbone of developed and emerging economies worldwide. Yet, even as many countries turn to infrastructure stimulus to help drive COVID-19 recovery, the $15 trillion global infrastructure financing gap stands as a stark reminder of what the public sector has not been able to achieve alone.
The latest Global Infrastructure Hub (GI Hub) report, Infrastructure Monitor 2020, shows declining private sector investment in new infrastructure, despite the appealing riskreturn profile of infrastructure investments. Private investment in infrastructure through primary market transactions is only about US$100 billion per year, down from US$156 billion in 2010. This figure is a drop in the ocean compared to the US$15 trillion global infrastructure financing gap that the GI Hub calculated in 2017 based on projections to 2040.
Currently, the industry is taking a hard look at its objectives and practices in light of what the pandemic has taught us about the role infrastructure plays in inclusivity, resilience and other essential aspects of society. This presents a unique opportunity for the public and private sectors to build on their alignment of purpose to increase investment and close, together, the financing gap.
A 2019 Global Infrastructure Investor survey by GI Hub revealed that 97 per cent of investors now believe environmental, social and governance (ESG) factors are important considerations in infrastructure investment decisions, an increase from 86 per cent in 2016.
This widespread recognition by infrastructure fund managers, lenders and investors appears only to have strengthened since the global pandemic. There is a distinct shift in emphasis from viewing ESG factors as useful considerations to seeing them as future-focused must-haves. This can only work in infrastructure’s favour for attracting private investment.
There are a few reasons why investors are looking the other way when it comes to investing in infrastructure. Firstly, there are limited opportunities for investment as the number of public-private partnerships (PPPs) shrinks globally. Infrastructure Monitor showed that private participation in PPP projects has gradually declined as a share of private infrastructure investment – falling from 36 per cent in 2010 to 28 per cent in 2019. There is also a shortage of bankable projects and fewer privatisations coming to market.
Secondly, risk-adjusted returns have become less attractive over the last decade with returns dropping due to serious competition among providers. The risk of infrastructure projects for investors is perceived to be high, particularly if the private sector is being asked to carry the burden of excessive risk. This perception is challenged by Infrastructure Monitor, as it found that infrastructure loans on average perform like an investment grade security by year ten in high-income countries, and by year 14 in middle and low-income countries, and even faster in PPPs.
From a performance perspective, our industry can raise awareness that infrastructure does not perform like other asset classes in having increasing default rates over time. And increasingly, we have the data to show this. In addition to the composite view provided in our Monitor 2020 report, there are the annual Moody’s publication of default and recovery rates of over 7,000 projects, and the EDHECinfra infra300 index of how unlisted infrastructure performs. The data is clear that once through the initial higher-risk phase (i.e. construction), infrastructure that is contracted or regulated by the state generally provides long-term, predictable and stable yields.
This finding is a clear signal to the world that infrastructure is a safe environment to play in, and the time is ripe for private investors to move away from focusing only on high-yield investment. By investing in infrastructure, the private sector
can diversify its portfolio, have a longer retainer and have a social license to play.
Lastly, the industry can break barriers to private investment by understanding how the public sector can be a deterrent to private investment. Capital charges associated with infrastructure investment can push investors towards other asset classes, and low interest rates make investment by the state more attractive and affordable.
As part of our work for the G20, the GI Hub recently conducted a market scan to understand the key challenges to mobilising private capital. We spoke to more than 40 investors, policymakers and market experts globally and identified three primary actions associated with attracting investment into infrastructure.
1. Ensure the availability of programmatic pipelines
Governments need to develop a clear vision for their infrastructure development agenda and goals. Without the required clarity, they will not be able to develop a robust and properly prioritised pipeline of projects. A good example of an infrastructure project pipeline is the online Mexico Project Hub. Launched in 2017, the pipeline aims to accelerate private investment in Mexican infrastructure development. The first of its kind in the world, it has quickly strengthened Mexico’s ability to fund multiple large projects across the nation.
2. Navigate regulatory, political and economic uncertainty
Infrastructure development is often politically complex, requiring the approval of multiple, diverse and sometimes competing stakeholder groups. Misaligned interests can inhibit projects. Therefore, governments need to create the proper
regulatory frameworks and economically robust environments if they are to nurture trust in their infrastructure programs.
One government that succeeded in this is Azerbaijan. Our InfraCompass, which quantifies the strength of countries' enabling environments, found it had the most improved regulatory framework of any InfraCompass 2020 country. In 2018, Azerbaijan made resolving insolvency easier by making insolvency proceedings more accessible for creditors and granting them greater participation in the proceedings, improving provisions on the treatment of contracts during insolvency and introducing the possibility to obtain postcommencement financing. Then, in 2019, Azerbaijan made resolving insolvency even easier by providing for the avoidance of preferential transactions (transfers or payments made to unsecured creditors that result in a creditor receiving a preference over the remaining unsecured creditors at a time when the debtor was insolvent).
3. Develop projects with attractive risk-weighted return profiles
Governments can keep in mind two key principles in the creation of their programs and projects: value creation (ensuring all projects have strong revenue potential) and value capture (ensuring key risks are mitigated and projects are appropriately financed to secure profitability). Projects that do not include plans for the fair and equitable generation and distribution of revenue will struggle to attract willing investors.
Activating private capital is key to closing the global infrastructure financing gap. The industry currently has an opportunity to explore investment options and create stronger partnerships between the public and private sectors, helping drive economic recovery in the short term while also driving longer-term economic and social outcomes.
The Global Infrastructure Hub (GI Hub) supports the G20 to drive an ambitious agenda on sustainable, resilient and inclusive infrastructure through action-oriented programs.
Based in Sydney, Australia and Toronto, Canada, the GI Hub team provides data, insights and best practice to create a common language on infrastructure. Strategic partnership is at the core of what the GI Hub delivers through events, thought leadership and tools. It is the G20’s only dedicated infrastructure entity.
Find out more and engage with the Hub at www.gihub.org.
Reliable, business-grade internet is critical to the ongoing operations of infrastructure projects. The necessity of connectivity for continued operation is just as pressing for permanent, fixed sites as it is for temporary, field sites.
The increasing adoption of remote monitoring systems and near real-time analysis of data flows to-and-from facilities has necessitated a constant, reliable internet service on every site. Activ8me Business Services’ satellite solutions can ensure sites can be connected online no matter how limited the local connectivity options may be.
With consistent data flows being a standard requirement both for operational functionality and safety and compliance, isolated locations can present significant challenges for infrastructure projects, with ongoing work dependent on continuous internet service in regions with very limited or no existing communications infrastructure.
With unlimited satellite internet for fixed and portable infrastructure sites, Activ8me’s custom-built hardware facilitates business-grade communications anywhere, with auto-aligning satellite dishes able to have a service operational in under ten minutes.
With custom contention rates and enhanced business SLAs, Activ8me’s solutions enable continuous, uninterrupted service, which is a common requirement both for operational functionality as well as safety and compliance.
Services can be customised based on requirement, however a typical service includes a 30Mbps download/5Mbps upload speed tier on a 20:1 contention.
Services are augmented to meet the unique requirements of clients, taking into account expected usage of the connection, the volume of users, types of applications and much more to ascertain bandwidth requirements.
IoT connections, for instance, are configured to handle the large amounts of small data packets, routinely transferred to-and-from IoT networks every few seconds. For IoT, a connection of 5Mbps down/5Mbps up with 35:1 contention provides optimal connectivity.
Up to 20 users, or hundreds of small IoT devices, can share a 'pipe,' with customised contention and speed tiers coordinated to best suit the operational aim of the network.
The solution can be used as a redundancy network to backup existing fibre-optic or microwave networks, ensuring that operations can stay up and running in the event of a primary network failure.
These same satellite data services are available in portable solutions, allowing for easy transport and relocation. The satellite dish can be mounted on a vehicle or trailer, be set up using a non-penetrable ground mount, or even built into a case.
This Mobile-On-The-Pause solution is perfect for projects with changing locations or remote project teams. WiFi networks are built into Activ8me’s portable satellite hardware, with optional WiFi antenna for extended range of up to 100m.
With an in-house R&D team, Activ8me often designs customised hardware to meet the unique demands of clients and additional functionality can be built into existing hardware when required.
Point-to-Point and extended WiFi can offer connections over extended distances, while WiFi-Mesh networks and LoraWAN technology can also be incorporated into network architecture.
Utilising these various technologies, Activ8me can formulate an end-to-end networking solution to suit practically any infrastructure project.
For more information, please visit business.activ8me.net.au.
Activ8me Business Services offers communications solutions for utility operators in remote Australia.
Our solutions include:
Unlimited data plans
Low contention rates
Fixed or portable hardware
Solar, self-sufficient options
Optional P2P, Extended Wi-Fi and Public Wi-Fi
Installation & Field Support Australia-wide
Our solutions overcome the communications limitations of operating in remote locations.
With our internet services, operators can access Cloud-based applications, integrate remote monitoring and utilise M2M/IoT technologies.
No matter your challenge, we offer scalable solutions to meet any requirement. Our in-house team can even design a bespoke solution to fit your needs.
For more information contact our Corporate Sales team or visit: business.activ8me.net.au
With COVID-19 restrictions significantly decreasing passenger numbers across all Australian airports in 2020, it became a suitable time to complete large maintenance and construction projects that would have otherwise caused extensive shutdowns. Brisbane Airport used this time to replace the entirety of its skylight that spans the length of the Domestic Terminal to maintain safety compliance.
As the gateway to Queensland for domestic and international visitors, Brisbane Airport's terminals have been designed to create a unique sense of space that makes a welcoming and lasting impression.
This sense of space encapsulates Queensland perfectly, capturing the warmth and light of the Sunshine State by bringing the outdoors in. At Brisbane Airport’s Domestic Terminal, visitors are welcomed by natural light that floods in overhead from the extensive skylight spanning 480m across the terminal’s ceiling. This architectural masterpiece has been a feature of the Domestic Terminal since its construction in the 1980s, providing opportunity for airlines and retailers to reap the resulting ambience and atmosphere.
Like all structures exposed to the elements, the skylight had reached the end of its life and required replacement in order to comply with relevant safety standards and protect the terminal from the elements.
Throughout the COVID-19 pandemic, Brisbane Airport Corporation (BAC), the operator of Brisbane Airport (BNE), reassessed all projects within the pipeline in order to prioritise those that were essential to ongoing operations.
Robert Scodellaro, Head of Project Services at BAC, said the skylight replacement project was identified as essential in order to ensure ongoing compliance of the Domestic Terminal.
“Construction for the replacement commenced in June, with practical completion being reached in October," Mr Scodellaro said.
Despite COVID-19 not having a significant impact on the project, the decreased passenger numbers did allow for some flexibilities around construction.
“The skylight project could only be accessed from the roof of the terminal itself, with all materials being craned to that location.
“In order to have a crane operating in an active airside environment, there are a number of complexities to overcome, including the need for both internal and external exclusion zones.
“With reduced passengers and flights, the removal of aircraft bays from the allocation plan to enable the required exclusion zones resulted in a reduced impact to airlines," Mr Scodellaro said.
Though it wasn’t only the aircraft bays that were affected. Despite operating in a heavily reduced capacity due to border restrictions, Brisbane Airport remained open and operational throughout the pandemic.
“Despite a significant decrease in passengers throughout the terminals, customer experience remained top-of-mind for any construction activities at the airport,” Mr Scodellaro said.
“This meant that all disruptive activities had to occur outside of operational hours, so they largely took place between 10pm and 4am."
The Principal Contractor, Box & Co, took each of these challenges in their stride, delivering the project on time and with an impeccable safety record. Box & Co’s Managing Director, Simon Box, said the project came with its challenges, but the team committed to a collaborative approach with BAC to find solutions.
“As a proud local business, safety is always our priority and this project gave us the opportunity to really practice what we preach and prove our capability.”
With 1,090 glass panels and nearly a kilometre of roofing flashing that needed replacement, Box & Co facilitated 168 crane lifts to the rooftop, all from the airside environment.
“Prior to commencing on site, we worked through risk mitigation and safety procedures. Ultimately, we knew we had to send people to work from a rooftop at night in a really niche environment, so there were a number of challenges we had to design out of the process before we could commence,” Mr Box said.
“On top of the external environment, we were also very aware that the works were occurring above critical airport infrastructure such as check-in counters. We knew that any issues during the night shift could have an impact on airport operations the following morning.
“Scaffold harnessing and catch nets for dust and debris beneath the skylight internally are examples of the types of risk mitigation measures utilised throughout the project."
With the strong team dynamic at Box & Co, Simon Box knew he had the right people on board who would be able to deliver
this project to a high quality, and most importantly, safely.
“We are a small company, and we were in the height of a global pandemic – utilising local suppliers who we have built relationships with over the years was critical to us,” Mr Box said.
“Knowing that we were giving additional work to trusted suppliers made the project a little sweeter in a time that was so unknown for the building industry.
“Box & Co is extremely happy to say that we were able source 93 per cent of construction materials from South East Queensland, with more than 90 per cent of the total employees working on this project living in South East Queensland.
“That not only includes the Box & Co team, but also subcontractors working on various aspects of the works," Mr Box said.
As Brisbane Airport looks to recovery, the newly replaced skylight at the Domestic Terminal will be sure to give passengers a warm welcome to the Sunshine State.
After a huge inaugural event in 2020, the Critical Infrastructure Summit – Australia’s premier event for the whole infrastructure lifecycle – is back to bring infrastructure professionals the latest news, innovations and thought-leading discussion on the industry’s most pressing issues.
In 2021, the Critical Infrastructure Summit will feature four Virtual Conferences over two weeks from 13–22 April.
Brought to you by the team behind Infrastructure magazine, the four free-to-attend conferences will explore the industry’s biggest challenges and predictions across the entire infrastructure lifecycle – construction, asset management and disaster resilience.
The 2021 conferences include:
♦ Critical Infrastructure: State of play – 13 April
♦ Asset Management for Critical Infrastructure – 15 April
♦ Disaster Management – 20 April
♦ The Future of Infrastructure – 22 April WHY ATTEND?
The infrastructure industry is set to play a major role in Australia’s post-COVID recovery, creating enormous growth and opportunities, but also new challenges and pressure to meet demand.
This means it is critical for infrastructure professionals to stay informed on the latest in the industry, from projects to technologies, innovations and the future outlook.
Topics across the four events for 2021 include: meeting COVID recovery demand in 2021; funding; the project pipeline; the last six months in the infrastructure industry; state of the airport sector; operating models and organisational design for success in asset management; digital asset management industry panel; bushfire mitigation; cyber security; futureproofing infrastructure; digital twins; building our future cities – connected, sustainable and accessible; and much more.
As well as the four major Virtual Conference events, the Summit will also feature online networking opportunities, enabling delegates to make genuine connections with other industry professionals.
Building on the high-quality content from the 2020 event, 2021’s Summit will feature a new expert speaker lineup of leaders from across the infrastructure industry.
We want to give delegates more of what they liked best about the inaugural event, so we’ll be dedicating more time for delegate interaction and speaker Q&As. This means greater participation, with attendees becoming a part of the discussion and having greater access to senior industry figures.
COVID-19 made it impossible to network with other infrastructure professionals due to restrictions, but in 2021 we’re introducing a live networking element to the event.
Attendees can still enjoy the entire Summit from the comfort of their homes or offices, but for those who want to get extra value from meeting up with peers in the real world, there will also be two live networking events to make connections and build new relationships.
Pending COVID restrictions, the live networking events will be held on Thursday 15 April in Melbourne and Thursday 22 April in Sydney.
This is the chance for delegates to network with like-minded infrastructure professionals in a fun and informal environment.
Australia’s premier event for the whole infrastructure lifecycle –construction, asset management and disaster resilience.
A thought-leading Summit keynote session on the biggest issues currently facing Australia’s critical infrastructure.
Asset Management for Critical Infrastructure
Bringing together utility and infrastructure leaders to discuss the most pressing issues in asset management.
Helping critical services prepare, survive and thrive in the face of major disaster events.
A look at what’s next for the industry – digital infrastructure, the Circular Economy, skills, funding, future sector trends and more.
Thursday 15 April in Melbourne
Thursday 22 April in Sydney
All 4 virtual events are FREE TO ATTEND
With great optimism, I anticipate 2021 will be the year that marks the turning point in the quest for a more sustainable construction industry. We have a unique opportunity to achieve real and lasting reform, but it will require the support of the entire sector.
Governments are relying heavily on the construction industry to lead the economy out of recession, but our industry is sick. Profitability is at an alltime low and productivity growth over the last 30 years trails that of other significant industries by 25 per cent. Women make up only 12 per cent of the construction workforce, and construction workers are six times more likely to die from suicide than a workplace incident.
There is a broad consensus that this sustainability crisis must be addressed for the construction industry to deliver the planned pipeline of projects efficiently, with the resources available, whilst leveraging opportunities to increase training, local procurement and engagement of indigenous and social enterprise.
In late-2020, the ACA published a series of documents that charted a clear way forward. Starting with an analysis
of the most pressing problems facing the industry, we then developed a framework for a more sustainable sector, followed by an industry charter comprising ten commitments to reform embraced by Australia’s leading construction and infrastructure contracting companies.
Amongst other things, we identified that a sustainable construction industry is one built on the three key pillars of: equitable and aligned commercial frameworks; a strong positive culture; and the capability, capacity and skills to execute the projects it is called upon to deliver.
All three pillars are interlinked, and therefore improvement in one requires improvement in all. As an example, it is widely understood that adversarial commercial frameworks negatively impact culture, and a positive industry culture is a key factor in attracting people into the industry.
Part of the solution to the challenges faced by the industry is greater use of contracts that promote a collaborative industry culture and incentivise innovation. True value can only be achieved when all the parties' interests on a project are aligned, and when open and transparent sharing of information is encouraged.
This is not a call for widespread use of alliance contracts, although the use of alliance contracts to deliver the Level Crossing Removal Program in Melbourne is delivering an exceptional outcome. There will always be instances where the use of lump sum or design and construct contracts are more appropriate. However, there is no reason why these traditional commercial frameworks cannot be drafted to contain more collaborative and equitable provisions, particularly regarding management of project risk.
More collaborative and equitable forms of contracts are in use elsewhere in the world and could easily be adopted here
to save time and effort developing new contracts or amending existing forms. The best example of which is the NEC suite of contracts from the UK.
While there have been some improvements to industry culture in recent times, construction workplaces and behaviours need to take a quantum leap if we are to make our industry a more resilient and attractive sector to work in, particularly for women.
The Construction Industry Culture Taskforce will shortly start consultation on a draft Culture Standard that seeks to align all parts of industry on the requirements necessary to make this leap.
To avoid capacity and capability constraints in the long term, there needs to be increased collaboration between government and industry to better identify potential skills shortages well in advance. This can be achieved through skills mapping and transparent, accurate project pipeline data. The data could then be used to smooth resource peaks by amending project start dates or to inform training initiatives to address potential shortfalls.
In the short term, with closed international borders and long lead times to train new people, we need to focus on increasing the efficiency of our procurement and delivery processes.
For example, we should put our valuable resources to work optimising designs and de-risking projects through advance works, rather than tying them up at tender producing volumes of information that add little or no value.
If we could just halve the gap in productivity growth that has been created between the construction industry and other industries over the past 30 years, we could construct an extra $10 billion of infrastructure every year for the same level of expenditure! This will be vital in a post-COVID-19 world with high levels of government debt, but no less of a requirement to construct productivity-enhancing infrastructure.
As a starting point, we need more collaborative partnerships between state governments and the private sector to enhance the three pillars supporting the sustainability of the industry.
To fully realise this opportunity, the Federal Government needs to take a more active role in defining and incentivising the use of best practice procurement and delivery processes.
The Construction Playbook, recently published by the British Government, accompanied by a direction to use it or explain why not, is a good example of how this could be done.
In comparison to many other countries, Australia has done a remarkable job in managing COVID-19. In part, this is the outcome of strong collaboration between the public and private sectors. This collaboration is transferable, and it is incumbent upon us all to grasp this unexpected opportunity for change with both hands in order to rebuild trust and develop a more sustainable industry for the benefit of all Australians.
For more information, and to view ACA’s document series and industry charter, please visit www.constructors.com.au/initiatives/industry-reform.
As the industry voice for design, advisory, and engineering businesses in the built and natural environment sectors, Consult Australia has been working with members to build the case for a greater focus on social value in considering infrastructure investments, which we see as critical to Australia’s COVID-19 economic response.
Despite sometimes being seen as such, the social value from infrastructure investments is not distinct from its economic value. Instead, an increased focus on social value can help shape and inform our investment decisions, ensuring that what we spend our money on results in economic benefits in areas of greatest community need. We see this as a ‘dual-lens’ approach, as a way to align future growth opportunities from investments with the values, objectives and priorities of our communities – the end users of these assets.
To deliver social value from investments and maximise community benefits, we must consider social impacts as early as possible in infrastructure projects – particularly in the business case phase of a project, where we look at whether an investment stacks up.
Social impacts are the consequences, both positive and negative, experienced by people due to changes in their surroundings from a project. While these social impacts can sometimes be difficult to consistently measure, they are no less real for those experiencing them. The earlier we think about them, the more influence we can have on the social value of a project, which in turn can improve the outcomes from a project and ultimately save time and money.
If we spend more time coming up with better ways to fully understand the impacts on how people live and interact, as well as the community’s composition and sense of place during the business case phase of a project, then we have a more complete picture of the ‘problem’ we are seeking to solve through the investment. This will inform whether or not the proposal is the right solution, and importantly, help refine and shape the proposal to align well with community needs.
It is also important to note that following this process in itself leads to greater social value because it helps create greater community acceptance and lowers the risk of conflict as the project proceeds through its various stages. Arguably, a failure to follow this process is a significant cause for many projects around the country being cancelled or delayed, rather than a failure in the projects’ merits.
So how can we increase our focus on social value through infrastructure business cases?
Many of our members are developing clever ways to better understand social value by utilising new technology and innovative practices – both from a community-wide perspective and for certain cohorts.
The key lesson we are seeing showcased in these new approaches is the need to move away from a one size fits all approach, or cost-benefit analysis thinking, and instead be more flexible and considerate of the context and objectives.
For example, how we consider the social impacts in a business case for a rail project in a rural area should not be applied to a business case for an arts precinct in an inner urban area. The approach taken must be more tangible and specific to the problem or the opportunity that the business case is looking at.
We have also considered the benefits of bringing forward what happens later in the project to the business case development stage – primarily social impact assessments, which usually happen alongside environmental regulatory approvals once the business case is finalised.
Much can also be learned by looking at some of the practices that sit outside typical ‘infrastructure projects’, such as mining projects, as these have a long history of considering the social value and licence to operate from the community. We believe many of these practices are transferable to infrastructure projects.
One example is the NSW Department of Planning, Industry and Environment’s Social Impact Assessment Guidelines, which apply to state significant resource projects. Positively, an updated version of this guide is currently being proposed for all state significant projects, including new infrastructure proposals.
Consult Australia has published a report looking at this topic in more detail which can be viewed at www.consultaustralia.com.au/home/advocacy/pipeline.
We hope that the report adds to the growing public debate about how we can extract more social value from infrastructure investments. We believe Australia’s economic response to COVID-19 is the catalyst to improve how we assess the investments that are important to us as users of infrastructure, and the legacy that we would like to create for future generations. As such, improving how we consider and shape social value from investments is essential.
Advanced Train Management System (ATMS) is a modern, communications-based, safe-working system for the ARTC, which has been custom engineered for Australian conditions by ARTC and technology partner Lockheed Martin. It enhances the operation of the national interstate rail network, and provides a quantum leap forward in safety, capacity and productivity for freight rail operations.
ATMS is capable of providing the driver with a 10km look ahead including all rail traffic, track possessions, track speed, end of authority,
ATMS replaces traditional trackside signalling equipment and implements intelligent software technology that allows information to be directly shared digitally between ARTC’s Network Control Centre and a train-borne unit on board a locomotive via mobile telecommunications.
After more than a decade of intense development, testing and design – a cutting-edge train management system has gone ‘live’ in South Australia.
The Advanced Train Management System (ATMS) has completed its final commissioning trials into service and is now the train control system for ‘live’ train services between Port Augusta and Whyalla in South Australia.
The system also has larger ramifications for the national rail network as it will eventually be rolled out nationwide, with work on the next phase along 1,700km of track between Port Augusta and Kalgoorlie already underway.
The Federal Government’s showpiece freight rail infrastructure project – the Inland Rail between Melbourne and Brisbane – will also be ATMS-ready when each section begins operation.
Recently-appointed Australian Rail Track Corporation (ARTC) Chief Executive Officer, Mark Campbell, said this is an important step in the process of upgrading the national network with proven technology that boosts safety, capacity, reliability and enhances the customer experience.
“The Interstate Rail Network is the backbone of our freight system and it’s crucial we have the latest systems and technology available to serve our customers well into the future, especially with the Inland Rail coming online,” Mr Campbell said.
“This will revolutionise the way we manage rail freight services by increasing capacity and improving operational flexibility, safety and reliability.
“ARTC is extremely proud of ATMS which has been ten-years in development. This product has been Australian made to benefit the people of Australia.
“This system has been developed from the ground up for Australian conditions. It has been tested under Australian conditions on the South Australian network. It has undergone rigorous testing before we brought the system into operation in August and it has passed every test.”
Mr Campbell said further benefits and applications will continue to be incorporated as the ATMS is rolled out to new areas.
“Benefits for our customers will continue to flow as we continue to integrate new features such as fuel and energy management systems, as well as better timetabling of trains through the increases of capacity on the network that ATMS will enable,” he said.
“ARTC has ensured that industry has been at the forefront of consultation during the development of ATMS and we
will continue to ensure that this system delivers substantial benefits to our customers.
“Moving more freight from road to rail will benefit the nation as our freight task continues to escalate. To be the mode of choice, rail needs to introduce cutting-edge technologies. ATMS is a key step in that objective.”
The Australian Government has invested $50 million into the development of the system alongside investment from ARTC and Lockheed Martin.
“While rail already has an impressive safety record, ATMS harnesses digital technologies to reduce risk across the rail network even further,” Mr Campbell said.
ATMS is capable of automatically applying the train's brakes where an overspeed has occurred and when predicting the train will exceed its end of authority should a train fail to take appropriate action for the conditions at hand.
For example, ATMS can enforce a train to a stop before it passes an end of authority displaying a stop indication, or before diverging on a switch which is improperly lined, thereby averting a potential collision.
“This system has an automatic safety intervention which provides the ability to apply a train’s brakes which prevents a train from exceeding the section of track it has permission to operate within,” Mr Campbell said.
“ATMS will prevent a range of potential issues such as train-to-train collisions, overspeed derailments and authorised incursions into an established work zone. It also means all ATMS equipped locomotives will ‘talk’ to each other to allow ‘fleeting’ to improve productivity.”
“The rail freight industry and the Federal Government are working closely together to explore the opportunities to accelerate ATMS implementation across the interstate rail network,” Mr Campbell said.
“This is being done through the Freight on Rail Group (FORG) which is reporting on progress to the Deputy Prime Minister, Michael McCormack.
“Rail is an essential part of the freight supply chain and the COVID-19 pandemic has shown just how much we rely on our rail network to support vital domestic trade and manufacturing supply chains.
“With freight demand set to increase, shifting long-haul freight from road to rail is a strategic priority and part of the Australian Government’s broader agenda for a resilient, efficient and sustainable national freight and supply chain network.
“The operation of ATMS marks a leap forward in train control, not only in Australia, but for the rail freight industry worldwide.”
Pacific National Operations Supervisor, Bernie Reid, said after consulting drivers utilising ATMS there were many identified benefits.
Mr Campbell said Australia’s nine leading rail freight businesses identified ATMS as the priority train control project to advance industry as a whole.
Between 2011 and 2031, the total domestic land freight task is expected to grow by 80 per cent. This is being driven by unprecedented population growth, coupled with increased demand from our trading partners in Asia and rapid changes in technology, e-commerce and consumer behaviour.
Without investment and reform to increase capacity and better manage demand, the annual cost of congestion in our capital cities could exceed $53 billion by 2031 underlining the need for better rail infrastructure to combat the growth in the freight task and the impact on road systems.
“The system is easy to use and understand, and there is no need to contact train control and provide times at locations which limits some of the distractions. There is also no need to raise or take a written train working authority, which means less paperwork,” Mr Reid said.
“Once we have entered the information ‘it’s set up and off we go’. Also having the ability to see up to 10km ahead to view oncoming services, any speed restrictions on the line or track worker authorities is a real benefit. The system provides realtime information and feedback with drivers looking forward to interacting with other trains and services.”
Mr Reid added that in the future ATMS will allow for trains to follow each other and have an increased safety aspect.
Victorian electricity distributor United Energy (UE) worked right through Melbourne’s COVID restrictions in 2020 to keep electricity supplies safe and reliable for its customers, but it was also preparing for summer, which usually sees more extreme conditions impact the network and put a strain on power systems.
The distributor rolled out a $185 million program of works to ensure the network was better prepared for this summer than ever before to support its customers, which are in Melbourne’s eastern and south eastern suburbs, as well as on the Mornington Peninsula.
United Energy General Manager, Electricity Networks, Mark Clarke, said heatwaves, high winds and wet weather could all cause power outages over summer, noting several storm events over the last few months of 2020.
“Our crews worked year-round to make sure our network is reliable, but we recommend everyone has a plan to have the power they need over summer,” Mr Clarke said.
United Energy and its resource partners undertook more than one million work-hours to ensure all network inspection, maintenance and testing was complete ahead of the annual bushfire season.
The highlights of this work include upgrading 47 local substations, (including eight in hazardous bushfire risk areas), installing 2.9kms of covered conductor to insulate powerlines – with another 2.2km to be constructed over coming months –and 91 network spreaders to prevent clashing.
Three Rapid Earth Fault Current Limiter (REFCL) devices were also installed to act as a network safety switch to reduce
the risk of fires starting from electrical assets in high bushfire risk areas. These devices are active in Dromana, Frankston South and Mornington, and protect 680km of powerlines servicing 63,500 customers.
The annual, extensive vegetation inspection and cutting program also completed 100 per cent of inspections in high risk areas, with vegetation cut back from tens of thousands of powerline spans.
Mr Clarke said the extensive efforts created greater capacity to deal with peak summer demand, while keeping the network safe and reliable.
“What we’ve also seen is that while customers were working or studying from home, they have become more conscious about their reliance on electricity,” he said.
“Our customers use more power in summer than any other season, so we recommend they know what they need to do if the power goes out for any reason.”
One of the key upgrades United Energy made this summer was a $1.7 million roll out of new technology on the Mornington Peninsula to reduce the risk of fires and outages.
United Energy replaced 5.1km of high-voltage powerlines with covered conductor across the Mornington Peninsula, with 2.9km completed before Christmas and another 2.1km delivered by February.
Covered conductor is a technology that covers long lengths of powerlines and acts like insulted sleeves.
They are being rolled out in targeted high bushfire risk areas across the network where powerlines can also be affected by extreme weather like strong winds, salt spray, moisture or frost.
By protecting powerlines, the covers also help reduce the likelihood of faults and fires.
The areas chosen for the rollout are based on bushfire risk and the number of previous outages in the area, and follow United Energy’s successful trial of covered conductors in Cape Schanck in recent years.
Project Manager, Rob Doyle, said the covered conductor works were part of a broader five-year program to roll out the technology across high risk areas.
“We’re progressively replacing the most vulnerable highvoltage wires with this technology across our network to increase reliability and to decrease the risk of fires starting,” Mr Doyle said.
“This means the network is much better protected if an object such as a tree branch or an animal happens to comes into contact with powerlines.”
The roll out included installations at Merricks North, Somerville, Red Hill and Hastings.
Meanwhile, specialist crews moved almost 600m of highvoltage lines underground along Valley Views Lane in Main Ridge on the Mornington Peninsula ahead of summer.
At the site, there were at least 55 large pine trees located on the side of a slope that had been leaning towards powerlines, posing a risk of starting a fire or causing a power outage if a nearby tree or limb fell.
Mr Doyle said undergrounding the powerlines had reduced the risk of fires starting from electrical assets as well as minimising unplanned outages in the future.
“This line is located on the north west face of the slope, meaning any potential fire start would move quickly given the hot summer winds which normally come in from that direction,” Mr Doyle said.
In early 2020, one of the large trees fell onto the powerlines, affecting power to customers for 12 hours.
Mr Doyle said undergrounding powerlines was just one way United Energy was improving safety in the Mornington Peninsula.
“The Peninsula is a high-risk area for fires and throughout the year we have continued conducting critical maintenance and major projects to ensure the network is ready for summer,” he said.
No matter the preparation a network does, there are likely to be extreme conditions each summer that leads to outages.
A checklist for customers on how to prepare for summer power outages is available at www.unitedenergy.com.au and includes advice on:
1. Looking after your health – particularly if you rely on life support equipment
2. Staying connected – by having mobile phones and laptop computers charged to stay connected with family and friends
3. Pre-cooling your home – if a power outage is planned as part of ongoing maintenance activities on the network
4. Having backup energy ready – like batteries, lamps and barbeques
5. Staying up to date – by downloading the VicEmergency app and signing up for United Energy SMS notifications about power supplies
The last few years have seen digital twins explode in popularity due to the significant benefits around cost-effectiveness and accuracy, and the ability to identify problems before they occur. They are allowing for more informed decision-making, which keeps project costs from soaring and avoids unnecessary delays – issues infrastructure professionals are constantly facing, especially now with the industry’s key role in the post-COVID economic recovery. Here, Infrastructure explores the technology and its impact on construction operations and maintenance.
The concept of a digital twin refers to a digital model of a physical object, process or system. In order to make the model identical, or a “twin” to the reallife subject, the digital model utilises historical and real-time sensor data.
The originators of the term, Dr Michael Grieves and John Vickers, said that a digital twin is “based on the idea that a digital informational construct about a virtual or a physical system could be created as an entity on its own. This digital information would be a 'twin' of the information that was embedded within the virtual or physical system itself and be linked with that system through the entire lifecycle of the system”.
The ability for a digital twin to be able to mirror the developments and changes
in an asset is an important function for the infrastructure industry, as it allows for the use of the technology throughout all phases of an asset’s development, including the planning, construction, operation and maintenance stages.
By replicating the physical world in the virtual world, data can be analysed and systems can be monitored to prevent problems before they occur. This allows for infrastructure companies to potentially save costs by using the twin to troubleshoot any issues before the asset is built, and avoid wasting resources, labour and time that would have otherwise been spent fixing a problem.
OPPORTUNITIES AND RISKS
Digital twins offer several benefits, such as the ability to provide a safe
virtual environment where users can simulate and test the impact of changes to assets, products, systems and processes based on real-time data.
Benefits to the infrastructure industry include:
♦ Monitoring of an asset in real time
♦ Virtual scenario modelling and testing
♦ Supporting informed planning decisions, detecting and troubleshooting issues
♦ Providing more accurate predictions of potential problems
♦ Measuring performance and efficiencies of assets and equipment
♦ Information sharing with citizens and businesses
Although the technology is developing quickly, there are still some challenges to overcome. Potential risks of using digital twins include:
♦ The type and quality of data that is shared between the asset and the digital twin may mean that the latter is less accurate
♦ Potential challenges in the digital twin’s functionality with existing assets, products, systems and processes
♦ Digital twins with long lifecycles (such as buildings and infrastructure) may outlast the short lifecycles of data formats.
Design software formats have a high risk of becoming unreadable by modern systems at some point in their service life
♦ Potential disputes over ownership of the data being input into, and contained in, the twin
♦ Due to the high level of complexity, digital twins may be expensive to design and create
The creation of a digital twin often requires a specialist, such as an expert in data science or mathematics that can identify the physics underpinning the physical object, so that the data can then be used to develop a virtual simulation of the original.
Sensors are then integrated into the original asset to gather data about its real-time status, working condition, or position, all of which is then input into the twin. This is achieved through a cloud-based system that receives and processes all the data the sensors monitor. Throughout this process, the twin is able to simulate the physical object in real time, whilst offering insights into performance and potential problems.
To use an example, a factory might employ digital twin technology to measure the effectiveness of its systems and machinery. This would first require the use of historical data to replicate the factory in a digital simulation. Then, the sensors would be able to feed in real-time data to the digital twin user, allowing them to remotely assess the factory activities as they’re occuring.
In other cases, a prototype of an asset (such as a building, railway, or water pipe) can be used before the end product is built, allowing the technology to provide feedback as the end product is refined. In the absence of a physical asset, the twin itself can also act as a
prototype. For example, a digital twin of a building before it is built can allow the designers, architects and engineers to identify any potential problems or opportunities for improvement before construction commences.
Digital twin technology has the capability to process complex data and systems, but it can also be simplified depending on the level of data used to construct and update it. For example, a digital twin of a road junction or traffic light might require more complex data in order for the user to monitor peak times, types of vehicles passing through, weather conditions and safety hazards.
However, a simpler digital twin might be beneficial for an energy company that operates a wind farm if it wants to optimise operations but is struggling because of the unpredictability of the weather. A digital twin could use historical data from a certain period of time to see how much energy was generated and in what conditions, then use this to predict the ideal angles for the wind turbines, as well as monitor wear and tear to forecast the lifespan of the assets.
Digital twin technology not only helps to inform decision-making in planning and construction phases, but it can also support companies in maintenance and condition monitoring. If an issue arises in an asset that the asset manager isn’t sure how to fix, technicians can use digital twins to test solutions before applying them to the physical twin, allowing them to ensure safety and effectiveness.
The live data feed provided by the sensors also allows the digital twin to monitor the condition of an asset for issues in real time. This live condition monitoring means digital twins can be used for predictive maintenance, where faulty components or assets at the end of their useful life can be replaced prior to an issue arising. This process also eliminates the need for some manual inspection, and increases safety by allowing the operator or owner to proactively identify and remedy potential problems before they occur.
One example of digital twins being utilised for maintenance and condition monitoring is a project by Victorian Power Networks (VPN) and United Energy (UE) which saw the development of a digital twin using LiDAR data to help with vegetation management of their electricity infrastructure.
VPN and UE own and operate large electricity distribution networks, totalling over 850,000 poles and more than 800,000km of powerline. The energy networks are also responsible for complying with strict regulations, requiring innovative and cost-effective safety solutions for maintaining network infrastructure.
To do this, the companies launched a LiDAR Lab to use digital twin technology as a surveillance method, measuring the distance to a target by illuminating the target with a pulsed laser light, and measuring the reflected pulses with a sensor, to create a digital model of the terrain.
The digital mapping allowed the networks to measure the distance between vegetation and powerlines to within 10cm. As vegetation-topowerline proximity poses significant bushfire risks, the ability to closely monitor these distances affords the networks an important level of infrastructure safety.
It then used LiDAR to develop a digital twin of the entire network for asset management-related activities, such as determining the clearance between the conductors and the ground – a process that is currently done manually.
Despite some potential challenges, digital twins are being dubbed by experts as one of the most imperative strategic technologies for businesses and governments, particularly within construction and asset management.
Dr Samad Sepasgozar from UNSW Built Environment said the digital twin is “not a pipedream, but the next frontier of construction management”.
“At the strategic level, the digital twin is a new game-changing approach to construction automation … that will transform the industry quicker than ever before,” Dr Sepasgozar said.
Digital twins have already been adopted by factories and manufacturing industries, automotive companies, aerospace engineers, local governments and councils, as well as the utility, energy and healthcare industries.
Digital twins are expected to unlock new collaboration opportunities among physical world product experts and data scientists in the future, as well as enhancing customer experiences and improving products, operations and services.
As part of V2X (C-ITS) projects, or when preparing roads for autonomous vehicles, it is necessary to gather data on all road users (cyclists, pedestrians, etc.) in the transport infrastructure.
SICK Sensor Intelligence offers a uniquely broad portfolio of 2D and 3D LiDAR sensors for this purpose that are suitable for harsh outdoor applications. The outdoorScan3 safety laser sensor is the world’s first 2D LiDAR safety sensor to be approved for outdoor environments and is certified in accordance with ISO 13849-1 and standard IEC 62998.
The outdoorScan3 safety laser scanner is designed to allow man and machine to work safely side by side, and thanks to its patented safeHDDM® technology and intelligent algorithms, disruptive weather influences such as rain, snow, sunlight and fog are filtered out with ease. As a result, it offers limitless potential for increasing business productivity and efficiency, both indoors and outdoors.
From basic safety mat replacement and presence detection, through to protecting multiple hazardous areas at the same time, the outdoorScan3
is the ideal choice. Suitable horizontal protective fields can be set up and monitored to protect against the dangers posed by hazardous machines, plants or open spaces.
Radar technology-based sensors from SICK can also be used for similar applications. The MRS1000 multi-layer 3D LiDAR sensor detects and measures objects in multiple dimensions. By collecting large volumes of data on multiple scan layers and from different angles, it can detect and respond to objects on the floor as well as objects that are obstructing the path.
On construction sites, excavators often collide with objects while maneuvering or reversing due to reduced visibility around the rear of the vehicle. The driver assistance system’s sensors must be able to classify objects and their relevance to the collision warning system. The MRS1000 3D LiDAR sensor features an IP67 enclosure and detects up to 55,000 measuring points across four layers, enabling it to recognise objects standing on the floor or located in the vehicle’s travel path in plenty of time. Cutting-edge HDDM+ technology with multi-echo evaluation guarantees precise measurements, regardless of the weather conditions.
High personnel and operational costs necessitate a higher degree of automation in airports, for example, through the automated docking and
undocking of passenger boarding bridges. With the outdoorScan3, fast and smooth connection and disconnection can be achieved under extreme weather conditions on the runway. The safety laser scanner also ensures the safety of people in the vicinity whenever the boarding bridge drive unit is moving.
Modern traffic management on road, rail and sea routes is geared towards safety, efficiency and a good environmental balance. Rugged sensor solutions provide reliable control and monitoring systems for transportation applications. With solutions from SICK, you rely on many years of experience indoors and outdoors. Laser measurement systems classify vehicles as part of the road toll system, automation light grids reliably detect people at train door systems, and dust measuring devices and gas analysers measure pollutant concentrations in tunnel areas.
The wide range of rugged and innovative products combined with a worldwide service and sales structure has made SICK a market and technology leader in many fields of data acquisition in traffic engineering.
Why tagging each train wagon with on-metal UHF RFID tags and mounting RFID long-range readers at the WTMS? The additional information of the unique RFID tag will enable a link between the critical measured values (detected failure) and the specific vehicle, wheel set, axle, brake, and suspension. Using RFID allows you to know in advance the specific part that requires rework. RFID also provides the following benefits: Reducing maintenance costs; Reducing high-cost emergency maintenance; Better planning due to real-time information about the vehicle’s condition; and Higher availability of rail vehicles and better reliability during operation. For more information, please visit: www.sick.com/au/en
As technology continues to influence and shape every aspect of our day to day lives, airports have yet to fully leverage this emerging capability of technology to deliver a seamless and stress-free travel experience.
Over the last 20 to 30 years, airport operations remained largely unchanged – largely reliant on segregated technology systems and manual processes managed by in-person interaction. This has made it harder to respond to changing resource needs and increased strain during peak periods.
In recent years, small evolutionary changes to improve and simplify passenger flow through a terminal have started to become standard practice. Self-service check-in and baggage drops at automated kiosks are commonplace. More recently, upgrades to security and passenger screening queueing ahead of departure are becoming more common and upon arrival in Australia, e-gates for immigration are a welcome change.
As we are designing Western Sydney International (Nancy-Bird Walton) Airport, we’re thinking beyond these discrete systems upgrades and considering how tomorrow’s technology will come together with great design and customer service to create a stress-free experience for our customers.
From the moment passengers arrive, through check-in, security and immigration to the boarding gate, we want every stage to be fast and easy.
Throughout an airport, there are more than 100 technology systems, ranging from baggage handling to airside access,
building utilities to aircraft apron management, and customer information to freight management. In a smart airport, these systems must communicate and work together effectively from your front door to the aerobridge.
A 2019 survey of more than 1,000 Brits found that the single most stressful part of air travel was getting to the airport (63 per cent), followed by baggage collection (49 per cent), and passing through security and waiting for transfers (47 per cent).
Australian airports are prone to the same concerns. We all know the delight of the captain’s announcement upon landing that you are ten minutes ahead of schedule, only to discover there is no operator available to connect the aerobridge to the aircraft. The desperation of the connecting flight dash between terminals, only to discover the flight has moved gates. These situations are frustrating and unnecessary. That’s why we are putting ourselves in our passengers’ shoes, and taking advantage of the latest technology, so we can build the best airport possible.
Western Sydney Airport is focused on designing and delivering a fit-for-purpose airport, digitally enabled at the terminal, for our passengers and airline customers. What if we could identify you as a passenger even before you arrived, and you could place your bag on a conveyor belt, and walk through
passenger screening without breaking your stride? You could be identified through digital means and smart devices, and be placed safely with other passengers on your flight with ease. Upon arrival, your bag would be returned to you with precision, or could be easily transported to the office, your home or hotel for your convenience on a dedicated service.
On the landside, we are closely collaborating with Transport for NSW, Sydney Metro, Australian federal law enforcement agencies, the Department of Agriculture and a range of other organisations to deliver tightly integrated transport and logistical access for both customers and cargo.
Two new Sydney Metro train stations at the Airport Terminal and Airport Business Park, and integration with the new M12 motorway into and out of the airport precinct, will ensure passenger and freight arrival alike will be fast, more accurate and reliable from kerbside to the plane, safely, seamlessly and stress free.
While we are still early in the design journey, safety, privacy and security is front of mind. The requirements of running a smart and modern airport in a heavily regulated industry are complex. Compliance with federal and state legislation is necessary, and while there’s a lot of work ahead, our team
is committed to delivering the people of Western Sydney a game-changing airport that we can all be proud of.
A smart airport for passengers and their families means a better passenger journey, a consistent service, real-time information and getting you where you need to go safely. For airlines, efficient and smooth turnaround of aircraft is crucial to maximise asset usage, build profitable routes and demonstrate value for money.
According to IATA’s 20-year global forecast, while the aviation industry is resetting in a post COVID-19 reality, there will be 2.8 billion more passengers per year by 2039. Opening in 2026, Western Sydney International stands ready as the full-service airport of choice for international, ultra-long haul and domestic travel on full-service airlines and low-cost carriers.
Within 20 years, one in two Sydneysiders will call Western Sydney home, and demand for passenger journeys in the Sydney region alone will more than double from 40 to 87 million. Coupled with the power of technology to deliver a seamless, stress free travel experience – Western Sydney International will be the smart choice.
In order to keep up with increasing demand, Australia’s construction industry can no longer rely on labour intensive 2D methods to support construction, as they run the risk of creating unnecessary design transactions, or can lack the information consistency needed on projects.
Virtual twins and 3D modelling on the other hand can improve manufacturing and construction efficiency and speed up processes. A virtual simulation of a construction project can identify any potential issues or risks companies might face in the field. These risks can be fixed or mitigated before construction begins, avoiding costly delays. 3D processes can be used in every step of a project’s lifecycle; from design and construction, through to operations and maintenance.
Recent supply chain challenges caused by COVID have increased costs for major construction projects, creating an urgent need for companies to utilise faster and more efficient ways of building. Some of the new and innovative digital transformation technologies that can help optimise construction include BIM, modular construction, additive manufacturing, big data, augmented reality, robotics, IoT and virtual twins.
In the recent series of webinars Smart Construction Rendez-vous, run by global leader in 3D design and engineering software Dassault Systèmes, Global Strategic Business Development Director, Prashanth Mysore, outlined the construction simulation technologies that can help accelerate projects, increase construction predictability and improve long-term value for project owners as well as profitability for project contributors.
“Our experience says that 80-85 per cent of project challenges occur in the execution/construction side, compared to 10-15 per cent during planning, so there is an opportunity for construction companies to take advantage of the benefits of emerging technologies like smart construction,” Mr Mysore said.
“It is expected there will be a wider use of technology in construction and construction management in the future, as companies realise the long-term benefits on productivity, efficiency and cost savings.”
Building information modelling (BIM)
BIM creates a digital prototype of an actual building or asset before it’s built. This enables the consolidation of information relating to the design, simulation, project management and construction functionality. All stakeholders – designers, contractors, suppliers etc. – can access the latest update of the project in 3D, allowing for faster decision-making between all participants collaborating on a single project.
Virtual twin experience for construction monitoring
Dassault Systèmes’ 3DEXPERIENCE
platform is essentially a unified digital cockpit that monitors construction execution so companies can make informed decisions. It can connect and collect data from machines, equipment and facilities on construction sites, enabling managers to dramatically improve construction performance by accelerating identification of errors and subsequently fixing errors using collected real-time data.
It is a true virtual twin experience model, monitoring live and capturing data that can be used later in operations and maintenance phases. The platform is a lifecycle management system so it not only includes 3D models, but also the project information, simulations and all of the project data in one single source.
Modular construction with 5D
Modular construction is best practice for the manufacturing industry and involves constructing sections off-site then delivering to the location. The 5D methodology for modular construction is essentially an integrated simulation of 3D plus time plus cost. It involves the simultaneous process of creating models
while the site work is occurring, with the basis of prefabricated construction being the initial design in 3D. BIM is also used to ensure suitability of the location and the design requirements. Modular construction allows developers and contractors to deliver shorter timelines with less risk, with techniques reducing the length of construction schedule by up to 50 per cent.
3D printing/additive manufacturing
3D printing, also known as additive manufacturing, is currently gaining traction in the industry as it allows you to create construction components or modular parts of buildings. Construction is well suited for 3D printing as the information needed to create a part already exists in the 3D BIM design. It allows for faster and more accurate construction of complex or bespoke items, lowering labour costs and producing less waste.
Big data and predictive analytics
Big data can support fast, accurate decision-making from multiple data sources in real time, making construction sites smarter and improving productivity. For example, when it comes to maintenance and operations, 3D contextualisation of IoT data can help identify specific issues on-site.
Using in-built machine learning algorithms, data scientists can identify a piece of equipment that is causing a maintenance issue. The maintenance log inside Dassault Systèmes’ 3DEXPERIENCE platform helps to identify particular equipment that is causing production stoppages, with the data able to be compared with sensor and historical data. With in-built machine learning and AI algorithms, companies can pre-emptively identify issues with various equipment within maintenance and operations phases.
Augmented reality and VR
Mr Mysore said for an industry that has been notoriously slow to accept technology changes, construction is actually an early adopter of two of the most advanced technologies in existence – augmented reality (AR) and
virtual reality (VR). These technologies can visualise blueprints, maximise efficiency and improve workplace health and safety.
VR is used by developers to review real 3D environments of architectural designs. By using a combination of BIM and immersive VR headsets, architects, project managers, civil engineers and the whole project team can identify design flaws and better plan construction projects before they begin. AR is used by project managers on-site to ensure a structure is being built exactly as the design intended, rather than just using line of sight to confirm. This significantly speeds up projects and minimises errors.
Autonomous construction is the use of advanced robotics to replace or improve existing processes, making them more efficient and accurate. Mr Mysore said robotics aren’t playing a huge role in construction right now but this will soon change, so companies should get on board early. With the industry facing increasing pressure to construct quickly and in a more reliable and safer way, this is where robots can be useful.
IIoT and execution monitoring
IoT plays an important role as it can connect sites, enhance safety, reduce accidents and improve work processes. Sensors connected to the internet can continuously monitor and manage critical resources at construction sites such as electrical systems and various mobile resources in real time. IoT is commonly used to monitor machines around the site and track progress of work. Sensors mounted on construction equipment and safety hats worn by construction professionals also help optimise the utilisation of manpower and physical assets.
As illustrated, there are a number of constantly evolving technologies available to construction companies and by using smart and lean construction methods, companies can become more flexible and agile, and better prepared for future disruptions they may face.
For more information on these technologies and Dassault’s 3DEXPERIENCE platform, please visit https://ifwe.3ds.com/construction-cities-territories.
Across Australia and around the globe, Intelligent Transport Systems (ITS) are already making road travel safer, more efficient and more sustainable. Such systems are only becoming more and more relevant as population grows and the number of vehicles on the roads increases, with various ITS technologies offering solutions to decrease congestion, increase efficiency and mobility, and even save lives.
Fundamentally, ITS involve integrating information and communication technologies into transport systems to optimise operations. ITS encompass a broad range of systems and technologies, with varying levels of complexity and automation. While smart systems can be applied to any form of transport, the term ITS is most frequently used in reference to road transport.
The ‘currency’ of any ITS is its data, which is used to improve the transport system’s operations, often in real time. As such, ITS employ a variety of wired or wireless technologies to collect, transmit, communicate and interpret data, with many also including automated control functions. ITS infrastructure may involve technologies integrated into road networks (e.g. roadside sensors), within the vehicles themselves, or both. Essentially, ITS enhances connections between road users, vehicles, road infrastructure and transport system operators.
ITS solutions are generally applied to do one or more of the following:
♦ Improve the mobility of people or goods
♦ Increase safety
♦ Reduce traffic congestion and increase transport efficiency
♦ Inform road users of conditions
♦ Respond effectively to incidents and emergencies
♦ Increase the resiliency of the transport system in case of changed conditions or unforeseen disruptions
♦ Reduce air pollution or improve energy efficiency
♦ Automate billing processes
♦ Achieve policy objectives (such as demand management or transport priority)
ITS fulfill various vital functions on our roads, reaping significant benefits for road users and operators, as well as for our broader society and economy.
Traffic management
ITS traffic management is concerned with the overall management of traffic on a road. The ITS detects traffic situations and deploys traffic control strategies. Technology is applied to traffic signalling systems, traffic safety, and route and congestion management.
For example, the busiest roads around Melbourne, including the M80 Ring Road, Tullamarine, West Gate and Monash freeways, Eastlink and Citylink, use coordinated dynamic ramp metering to measure and regulate the number of vehicles entering and exiting in real time. This enables each road to handle the maximum number of vehicles while maintaining traffic flow, reducing travel times and preventing safety issues associated with congestion.
Controlling traffic signals to only allow a certain number of vehicles to merge onto a road at a time helps break up groups of vehicles that might otherwise be competing for space, reducing the likelihood of collisions. Ramp metering signals that become operational during peak times have also been deployed as part of Sydney’s $600 million M4 Smart Motorway project.
Similarly, ITS such as the Sydney Coordinated Adaptive Traffic System (SCATS) employ in-pavement detectors and other sensors at busy intersections to monitor demand for right-of-way and shifts in direction of demand. Traffic signals then adapt accordingly, resulting in a smoother flow of traffic and minimising wait times. The SCATS Priority Engine also allows essential
vehicles (such as emergency services) to be prioritised through traffic lights.
In Queensland, Hold the Red, an innovative intersection crash avoidance system trialled at four intersections in Brisbane and the Gold Coast, demonstrates the potential of ITS to prevent traffic incidents and enhance safety. The system uses radar to predict when a vehicle approaching the intersection is going to run a red light. When this occurs, the system extends the all-red phases of lights at the intersection by two seconds, preventing other vehicles or pedestrians from entering the intersection where they could collide with the offending vehicle.
A common function of ITS technology is to better inform road users about road, environment and traffic conditions. These services enable road users to plan the most efficient route, avoid delays and quickly become aware of any changed conditions, potential hazards or emergency situations. For instance, signs may display current travel times or advise of incidents or lane closures, or real-time information about conditions might be conveyed via highway advisory radio or reflected in GPS data.
Real-time traffic information signs and variable message signs are employed on a variety of roads around Australia, while certain busy car parks use parking guidance systems to advise of parking availability. For example, the Parramatta Parking Finder helps support people with accessibility issues by providing information about accessible parking spaces around the Parramatta CBD including photos of the space and a rating out of five for the size of the space, hoist suitability and kerb ramp access.
Some of the potential benefits of ITS integrated with connected and semi-autonomous vehicles have been demonstrated by a trial undertaken by the Victorian Department of Transport on Eastlink, which involved the operational deployment of semi-AVs and cooperative intelligent transport systems (C-ITS). The project developed a DSRC messaging platform that delivered real-time road warnings in a high-speed environment, with high reliability and precision (to location and lane), without interfering with the existing tolling system.
Emergency management and response
The real-time monitoring capabilities of ITS can greatly reduce emergency response times, saving lives, preventing secondary incidents and reducing disruptions. For instance, if a collision occurs, the relevant authorities are alerted, and the nearest emergency vehicle is located and dispatched to the scene. Other drivers on the road can be alerted through dynamic signage and signals may change to prevent too many vehicles entering the area of the accident until it is safe to do so.
In South Australia, on the section of the North-South Corridor between Torrens Road and River Torrens, a Thermal Video Incident Detection System detects slowing, stopped or wrong direction vehicles within 5-15 seconds, fast-tracking incident response actions. These include notifying drivers of lane closures and congestion using variable message signs and monitoring the situation with CCTV pan-tilt-zoom cameras.
Meanwhile, the Queensland Police Service employs drones and motorcycles to expedite serious crash scene clearance times, allowing traffic managers to estimate the duration and severity of congestion impacts and use existing ITS technologies to help manage congestion and prevent secondary incidents. Using drone technology to map crash scenes, the Forensic Crash Unit has reduced scene mapping time by 50 per cent, reducing road closure times and traffic congestion, while also improving the quality of evidence captured at scenes.
In Brisbane, a structural health monitoring system has been developed to detect damage to the iconic old Sir Leo Hielscher Bridge (the Gateway Bridge) in real time, before it can affect public safety. These are just some of the ways in which ITS are currently transforming Australian road travel, with much more to come.
As the field of ITS continues to develop rapidly, the deployment of smart systems on our roads can help address significant social, economic and environmental issues. With the costs of congestion predicted to rise to as much as $40 billion by 2030, and over a thousand lives still lost on our roads each year, we cannot afford to miss this opportunity to reap significant benefits at a relatively low cost, leveraging data to revolutionise road transport.
The 2020 NSW Spatial Digital Twin is part of the Western Sydney City Deal partnership that brought together federal, state, and local government under a set of 38 commitments. The Digital Twin was part of the project’s commitment to coordinating information that supports planning and broader liveability targets.
» 3,396km2 of 3D mesh
» Over 1 million images captured
» 28,500 gigapixels of visual information
» Under 6cm pixel resolution
Data has become its own type of infrastructure, and the NSW Spatial Digital Twin is an asset that will benefit private industries, government, and the public for years. The project has set a standard for how digital twins will be made and used for planning and visualisation.
The NSW Spatial Digital Twin incorporates the largest 3D modelling project ever undertaken, with the final product including 3,396km2 of seamless 3D mesh captured at under 6cm pixel resolution across the greater Western Sydney region.
Key to this endeavour was Australian 3D modelling expert Aerometrex, who captured and processed the necessary 3D data to underpin the NSW Spatial Digital Twin. It spent several months capturing, processing, and combining the imagery.
What makes the NSW Spatial Digital Twin so remarkable is its open-source presentation, publicly accessible through a browser-based web portal. That foundational information source brings compounding efficiency benefits as government, private industry, and the general public can all refer to a central and consistent data source.
Victor Dominello, the NSW Customer Service Minister, said the high availability of aggregated data will help with planning future development.
“Using the digital twin, we can model where we put the roads, hospitals, schools, etc. with precision planning like we’ve never done before. This is truly transformational technology and the best thing about it is that it’s open source – industry can use it, councils can use it, everybody can get involved and build this asset together for all of us,” Minister Dominello said.
Open source 3D mesh data reduces costs and time frames for infrastructure planning regardless of the project size. Every
project stakeholder uses the same validated source, making duplicate data investments unnecessary. 3D visualisation gives all stakeholders a more tangible and dynamic sense of space. Users can see and understand space and how the change will impact it.
Aerometrex used fixed-wing platforms carrying an array of image sensors to capture an area so large at such high detail. Aeroplanes were the ideal tool for the job, but it’s an intricate task when the busy Sydney Airport is within the capture zone. The post-processing task matched the capture process for complexity and scope. Aerometrex’s team had to turn 1.1 million images, adding up to 28,500 gigapixels of visual data, into usable 3D tiles for Data61 to build into the web portal.
“To have over 3,000 square kilometres of 3D data on a site that is available to anybody anytime shows that we as an industry and we as a country are leading the way globally with delivering spatial information to those that need it.”
Rob Clout, 3D Sales Manager, AerometrexNSW’s Spatial Digital Twin shows the value in making open source assets. They encourage and accelerate economic activity through centralised and consistent data. The concept of Digital Twins has already progressed past the proof-of-concept phase and to a mature product.
Jurisdictions of all sizes are investing in digital twin asset creation because the returns on investment are substantial. Better spatial data improves the multitudes of activities that involve the alteration of structures and space.
INFRASTRUCTURE PLANNING WITH GEOSPATIAL DATA & ARTIFICIAL INTELLIGENCE
Drive your next critical infrastructure project with Aerometrex’s geospatial data enhanced through Artificial Intelligence and Deep Learning
• Monitor critical changes over time through AI-enabled time series analysis
• Segment any object within a 2D or 3D environment with pixel-level classification
• Integrate project assets within game engines for interactive visualisation
• Obtain far richer data insights for planning and build greater process efficiencies
Aerometrex is an Australian-based leader in 3D Modelling, Aerial Imagery, and LiDAR with expertise working on infrastructure projects for over 40 years. We are investing in AI and Deep Learning with geospatial data to reduce the time between data collection and actions for critical infrastructure projects. Our goal is to classify all objects within our 2D & 3D data, leaving nothing as unclassified. This shall allow businesses to query geospatial data for objects that meet very detailed & specific criteria within a project, building truly intelligent spatial knowledge. Contact our team to learn more. Turn Big Data into Actionable Knowledge.
www.aerometrex.com.au
That shift in focus was fast and necessary in changing times, but also represented a real opportunity for government and industry to work together to create a new future for rail innovation in Australia.
As one railway technology supplier observed in the development of the ARA’s report Finding the fast track for innovation in the Australasian rail industry, “…machine manufacturing is not going to come back unless we embrace more innovative manufacturing technologies”.
So how do we embrace that innovation focus to make the most of this moment in time, and secure a greater share of the $362 billion rail technology market?
The ARA’s report found Australia’s manufacturing strengths leant itself to the production of high value, high technology goods; an area where there is an increasing focus within the rail industry.
The benefits of a rail innovation culture could be significant; improving efficiency, productivity and the customer experience across the rail network – just look at the overseas experience.
In Germany, the adoption of building information modelling (BIM) to reduce energy use and maintenance led to significant cost savings.
On Berlin’s U’Bahn network, the application of ICT tools helped halve wait times.
In the US, preventative maintenance technology such as wayside detectors, smart sensors and infrared lasers have reduced mainline equipment-caused accidents by 36 per cent over a decade.
That is a huge and important contribution to the safety of the network.
by Caroline Wilkie, CEO, Australasian Railway AssociationAs COVID-19 restrictions hit Australian supply chains, three quarters of rail businesses surveyed by the Australasian Railway Association (ARA) said they were looking to increase their use of local suppliers to support their operations.
In the UK, the Rail Sector Deal led to investments in data, digitisation and sustainability to deliver up to £31 billion in benefits.
The establishment of the UK Rail Research and Innovation Network (UKRRIN) to bring together industry, government and academia has also provided a step change in innovation and new technologies in the local rail industry.
And that ambitious focus is paying off, with the industry attracting $2 in private sector investment for every dollar in government spending.
Here in Australia, our record of achievement has not been as significant, with a lack of long-term focus on research and innovation hampering our progress.
But there have still been clear successes in the use of technology and innovative equipment solutions to support better outcomes on the rail network.
One example is VicTrack’s new sensor arrays and use of artificial intelligence to predict adverse car and track conditions.
The technology has improved safety and made it easier to direct maintenance efforts to where they are needed most.
In New South Wales, automation used on the Sydney Metro has boosted cost recovery when compared to the traditional rail network.
And while the common perception is that rail innovation perhaps is far more advanced elsewhere, there are already examples of Australian ingenuity being exported around the world.
The Monash Institute of Rail Technology has firmly established a global reputation for its work. Its condition monitoring technology improves the efficiency, safety and comfort of busy passenger rail lines, while extending the life of rail
infrastructure. So much so that the technology was implemented on the Hong Kong Metro in 2017 to support the delivery of services for 5.4 million people every week.
The question now is how does Australia make the most of the opportunity to gain a greater share of the global rail innovation market.
The first step is to make innovation a national priority.
Just as the UK experience has shown, a clear and ambitious vision by government is key to attracting private sector investment in the local innovation market.
That will require a longer-term focus on rail research and innovation funding, with a clearly defined pathway to commercialisation of new concepts developed in Australia.
A national focus on rail innovation will also be required, with a standardised approach to rail policy and procurement an essential part of ensuring the industry can gain the scale it needs to justify the investment in new research and technology.
Finally, we must be willing to adopt a culture of innovation at every level of the rail industry.
That will require industry participants working together to try new approaches that achieve better outcomes. The industry as a whole will also need to plan for digital technologies to continue to be further integrated into the network over time.
If we get these issues right, Australia will not only benefit from a faster, safer, more efficient rail network, but will also be able to export more of its talents to the world.
That is an outcome we should all be striving for.
Certain places and circumstances contribute to rail trespass, where ease of access to a particular location may influence the likelihood of an incursion. Various studies have recommended a focus on limiting access to rail infrastructure, with an elimination approach involving an increase of physical barriers. However, what can be done in the
In the moment of rail trespass, what technology exists to provide immediate detection and enable rapid intervention?
precise moment of incursion – that critical time during and just after unauthorised entry?
Technology has evolved to a point where thermal imaging and video detection can be used to provide an automated detection system for rail infrastructure. Deployed in strategic locations, automatic detection cameras can create a network of virtual IT fencing, providing accurate trespass detection and automatic notification, regardless of physical observation, shift changes, time of day, or lighting.
Physical intervention response times will vary depending on availability and response distances, which highlights
the importance of minimising detection and notification times, where the initiation of early warning measures can alert oncoming trains to take preventative action as soon as possible. The additional integration of a public announcement system to communicate that the area is being monitored could also act as a deterrent and persuade people to leave a place of danger.
In combination, thermal imaging with integrated detection technology is a proven and cost-effective measure in preventing rail trespass, enabling rapid intervention, minimising disruption, and lessening social and economic impacts.
Waterjet cutting is a process of precision cutting that utilises high pressure water.
We can process a wide array of materials. Heavy gauge plate, thin sheet stock and composite materials (i.e. carbon fibre, phenolics etc.). It is not uncommon for 6+ inch aluminium and titanium to be cut on waterjets to near final shapes. Edge quality of the parts can vary depending on customer requirements.
We can process anything from a very rough cut for hog-outs, to a very fine edge for precision, finished parts:
Cut up to 6 m x 3 m (20 ft x 10 ft)
Thickness up to 254 mm (10 in)
Improved yield and less waste material
Supplied close to net shape reducing customer machine time
Shorter lead times
Zero heat effected zone
Processing of customer supplied materials
Jerome Pun recently won the ARA's Emerging Rail Specialist Award for his work on ratcheting performance, which plays a key role in causing the rolling contact failure of high strength rail steels. Here, he looks at the performance of three high strength rail steels that are currently used in Australian heavy haul railway system and how they behave under different operating conditions.
To help reduce rail degradation i.e. wear and/or rolling contact fatigue associated with the demanding conditions imposed by higher axle loads and increasing annual haulage rates, high strength pearlitic rail steels with carbon contents of 0.8 per cent or higher (eutectoid and hypereutectoid grades) have been commonly used in Australian heavy haul railway networks.
It has been found that the application of high strength rail steels reduces rail wear under heavy haul operating conditions. However, it also influences the relative rates at which wear and rolling contact fatigue damage occur on the railhead. In some cases, the morphology of rolling contact fatigue damage is also altered.
In the wheel-rail rolling contact process, the rail is subjected to cyclic loading, and the rail surface is subjected to rolling and sliding and relatively high contact stresses. The stresses endured by the rail are always multi-axial, non-proportional and randomly fluctuating in magnitude and direction. It has been found that the cyclic stresses and resulting plastic deformation are the major factors influencing the rail degradation processes.
In cases of wheel-rail contact conditions that result in stress levels above the plastic shakedown limit, also known as the ratcheting threshold of the rail material, new plastic deformation occurs and accumulates under each cycle of loading. This material response under cyclic loading condition is known as ‘ratcheting’.
When the accumulated plastic strain, also known as ratcheting strain, reaches the limiting ductility of the rail, the rail will fail at its local material point, which corresponds to the initiation of wear or rolling contact fatigue, i.e. in the form of head checks (cracks) in the railhead.
RATCHETING PERFORMANCE OF THREE HIGH STRENGTH RAIL STEELS
We conducted a comprehensive study, which consisted of both experimental and numerical studies, to investigate the multi-axial ratcheting behaviour and performance of three high strength rail steels currently used in Australian heavy haul railway operations.
The three high strength rail steels included a low alloy heattreated (LAHT) rail grade with carbon content of 0.8 per cent, and two hypereutectoid rail grades with carbon content of 1.0 per cent (HE1) and 0.85 per cent (HE2), respectively.
Our experimental studies revealed that the multi-axial ratcheting behaviour of all three rail steels is significantly influenced by the multi-axial cyclic stress amplitudes and the non-proportional loading path, albeit that all three high strength rail steels exhibit cyclic hardening.
In comparison, the LAHT rail steel shows the best resistance to ratcheting. Among the two hypereutectoid rail steels, the HE1 rail steel, which contains a higher percentage of carbon content, gives a lower ratcheting strain and ratcheting strain rate under high equivalent cyclic stress amplitude.
We also conducted wheel-rail cyclic rolling contact simulations to evaluate the ratcheting performance in terms of crack initiation life of these three rail steels under different heavy haul operating conditions.
The analysis shows that under relatively mild operating conditions – low creepage, low friction levels and lower axle load (≤ 35 tonnes) – the LAHT rail steel has the best resistance to ratcheting and performance (the longest crack initiation life). However, under high creepage and high axle load (> 35 tonnes) conditions, this rail steel shows the worst
performance compared to the other two hypereutectoid rail steels, indicating that the LAHT rail steel may not be suitable for harsh operating conditions.
For the other two rail steels, the HE1 rail steel shows a relatively worse performance compared to the HE2 rail steel under all considered operating conditions, albeit that the ratcheting strain rate endured by HE1 rail steel may be lower in some situations. This is attributed to the lower ductility limit of the HE1 rail steel, which is about 68 per cent less than the HE2 rail steel.
Microstructural analysis also revealed that pro-eutectoid cementite is observed in the prior-austenite grain boundaries in the HE1 rail steel primarily due to its high carbon content. The presence of pro-eutectoid cementite is undesirable as it is a source of embrittlement and hence, reduces the rolling contact fatigue resistance of the rail steel. This finding suggests that the use of high strength rail steels with high-end carbon content i.e. the HE1 rail steel, could potentially require more frequent maintenance due to the reduced ductility limit and hence, increased likelihood of rolling contact fatigue development.
Of the three considered rail steels, the HE2 rail steel appears to have the most consistent resistance to ratcheting and performance under all considered wheel-rail rolling contact conditions. Therefore, the HE2 steel is deemed to be more suitable to fulfil the demanding conditions in heavy haul railways among all three rail steels. The results obtained from our analysis are generally in line with the in-service performance of these three high strength rail steels under heavy haul conditions.
The in-service performance of a rail steel is directly affected by both operating conditions and the effectiveness of maintenance strategies. Based on our findings, the selection of suitable rail steels for a specific network, or even for a specific track section, should take into consideration the influence of the given operating conditions on the actual performance in terms of both wear and rolling contact fatigue of the rail steels. In addition, other considerations, such as weldability, should also be given at the time of selection of high strength rail steels.
Although the increased hardness of high strength rail steels improves the resistance to wear and deformation, it is still essential to undertake ongoing cyclic grinding at the appropriately designed intervals. The grinding activities should aim not only to rectify the rail profile to the target profile but also clean up existing rail surface defects.
It is also important to note that wear and the likelihood of rolling contact fatigue could be increased for poorly profiled rail sections such as the presence of peak or undercut in the railhead. Therefore, grinding activities should target to achieve good conformance to the target rail profile.
Appropriate selection and application of rail steels in accordance with the given operating conditions together with an effective and high-quality rail maintenance regime are expected to enhance the advantages of using high strength rail steels and extend the rail life.
The present work was partly funded by an Australian Research Council Linkage Project with the assistance from Mr Darrien Welsby and Mr Peter Mutton from Monash Institute of Railway Technology, and Dr Wenyi Yan from Monash University.
The National Asset Centre of Excellence (NACOE) has been investigating Intelligent Compaction (IC) technology and the role it can play in constructing roads in Queensland. This research focuses on the use of IC to improve the construction quality of both earthwork embankment and pavement construction, and activities have been undertaken to accelerate market acceptance in Australia.
What role does the quality of compaction in road construction have on delivering a longlasting, high performing pavement? The industry knows just how vital the compaction process is to achieve the best outcome. Many local and state governments are becoming increasingly concerned with costly repairs and maintenance that can occur later down the road due to poorly compacted pavements.
Intelligent Compaction technology has the potential to significantly reduce construction and maintenance costs by optimising the compaction process through improved uniformity and consistency of materials. It brings with it realtime feedback and monitors to assist the roller operator, using a system of hardware, software and analysis equipment.
Although Intelligent Compaction technology is quite new to Australia, it has a proven track record overseas, where it was first developed in Europe and has been increasingly used throughout Asia and the United States. As part of the NACOE program, a research project commenced in January 2019 intending to assess the suitability of implementing Intelligent Compaction for quality control in future road construction.
Through researching international best practice and field testing the technology in Queensland, Intelligent Compaction is displaying benefits in the following areas:
♦ Real-time operator feedback enabling continuous placement of material (without delays of traditional test methods)
♦ Identify weak areas on pre-mapping of underlying layers
♦ Optimise rolling pattern (coverage and speeds)
♦ Allows for 100 per cent of compacted area to be assessed, avoiding under/over compaction of isolated areas
♦ Capturing and securely storing the compaction process information as permanent georeferenced records
♦ Improved uniformity of earthworks and pavements, which is expected to lead to significant improvements in service life
♦ Reduction in greenhouse gas emissions due to more efficient construction practices and reduced maintenance
Intelligent Compaction refers to the use of a roller equipped with an integrated measurement system, often using an accelerometer mounted on the roller drum and a precision GPS unit. For the use of asphalt compaction, infrared temperature sensors are also mounted on the roller to track asphalt surface temperature during compaction.
The Intelligent Compaction technology has an on-board computer display which provides the operator with real-time feedback on the stiffness of the compacted materials and the number of roller passes the roller has made.
Intelligent Compaction rollers allow the operator to view plots of the precise location of the roller and continuously determine a measured value of the material stiffness and number of roller passes during the compaction process by maintaining an ongoing record of colour-coded plots.
MANAGEMENT
The NACOE research on Intelligent Compaction implementation is led by Dr Jeffrey Lee, who delivered the first-ever twoday Intelligent Compaction Data Management (ICDM) workshop in Queensland in 2019, alongside Dr George Chang.
The first day of the event covered the basics of Intelligent Compaction, which gave participants a hands-on experience of using the Veta software. On the second day, a field demonstration was conducted using a Dynapac smooth drum roller with a Trimble IC retrofit kit at a test strip, where the Intelligent Compaction roller was used to compact a general fill area (60m by 23m) on test strips using three different moisture contents.
The exercise familiarised participants with Intelligent Compaction technology and demonstrated how to use a test strip to establish a target Intelligent Compaction Measurement Value (ICMV) and roller passes for process control.
As part of the NACOE project, the need to draft a technical specification was identified to use on Queensland Department of Transport and Main Roads (TMR) projects to trial the Intelligent Compaction technology.
This led to the development of the first ever project-specific technical specification in Australia PSTS116 Intelligent Compaction – Earthworks and Pavements, which is intended for the use of the compaction of earthworks, unbound and stabilised pavement layers, but excludes asphalt layers and sprayed bituminous seals.
PSTS116 was initially developed to undertake a compaction audit using an Intelligent Compaction roller on the Ipswich Motorway Upgrade: Rocklea to Darra – Stage 1 (R2D) project between March and October 2020. The Intelligent Compaction roller was used to compact embankment fill, subgrade, plant mixed lightly bound material and unbound granular base material. The use of Intelligent Compaction on this project has assisted TMR to evaluate the benefit of the technology and develop a strategy to implement Intelligent Compaction into TMR’s standard specifications.
To support the implementation of PSTS116 and the wider use of Intelligent Compaction in Australia, NACOE has also funded updates to the international Veta software to allow it to be used in Australia and support GDA 2020. The Veta software was developed by the Transtec Group in 2012, and is used around the world to interpret and analyse Intelligent Compaction, Paver-Mounted Thermal Profiles (PMTP), Dielectric Profile System (DPS), and future emerging Intelligent Construction Technologies (ICT).
INTELLIGENT COMPACTION IN ACTION
NACOE was pleased to work with the Logan City Council on the Logan Street Pavement Rehabilitation Project, completed in late 2019, the first of its kind in Australia to capture data that allows the council to manage unstable ground in a more efficient way using Intelligent Compaction technology.
The project won the Local Government Managers Australia (Queensland) Excellence Award in 2020 in the collaboration category and included a collaboration of multiple parties: Logan City Council, NACOE and Queensland University of Technology (QUT). It has generated ideas in the road industry on how local governments can play a leading role in cutting-edge road research and the development of innovative technologies.
NACOE is an initiative of the Queensland Department of Transport and Main Roads and the Australian Road Research Board (ARRB), committed to delivering efficiencies and innovation through road infrastructure related research. For more information, please contact info@nacoe.com.au or visit nacoe.com.au
Older pedestrians are overrepresented in road fatalities, with a recent report from Victoria’s Transport Accident Commission finding people aged 70 and over account for 32 per cent of the state’s pedestrian deaths, despite representing only ten per cent of the population.
Research suggests road intersection design, crossing widths, location and timing of traffic lights, and density and type of traffic, all play a part in the overrepresentation of older people in road accidents.
While urban planners strive to consider all these dimensions when designing pedestrian areas, it is often very difficult to accurately predict the interaction of so many elements until they come together in a real-world scenario.
A new research project from the University of South Australia will deliver a novel solution to this design challenge, simulating upgrades to roads, crossings and footpaths using virtual reality (VR) technology in order to improve safety for elderly pedestrians.
Researchers from UniSA’s Australian Research Centre for Interactive and Virtual Environments and Brain-BehaviourBody Research Concentration will develop a walkable VR environment suitable for use by older people, which will
help planners and engineers design and test better roads and footpaths.
Supported through funding from the Road Safety Innovation Fund (RSIF), the interdisciplinary project draws upon the expertise of three UniSA researchers from diverse fields –construction management expert Dr Jun Ahn, VR technologist Dr Gun Lee, and cognitive psychologist Dr Ancret Szpak.
“Having access to a wide range of data from both virtual and real environments means we can overcome the limitations of previous ways of assessing pedestrian safety,” Dr Ahn said.
“Through this project we will create a virtual environment to simulate the road environment.
“We can easily change that virtual model to test the impact that a range of factors, such as intersection designs, crossing widths and traffic signals, have on road safety.
“The project will focus on the needs of older people, who may, for example, have impaired vision or hearing, need a walking aid, or require longer to cross the road than young people.”
The interdisciplinary nature of the project reflects the diverse challenges faced by the research team, which must not only precisely evaluate the real-world challenges encountered by older pedestrians, but also accurately recreate those challenges in an adaptable virtual environment.
“Our research combines areas of human-computer interaction, psychology, neuroscience and safety science,” Dr Szpak said.
“Each team member adds a unique perspective which has led us to develop an innovative methodology for measuring pedestrian safety factors for vulnerable road users.”
The research will draw data from multiple user experience methods including eye-tracking, ThinkAloud techniques (asking participants to verbalise their thoughts), and wearable biosensors to track physiological indicators of stress such as heart rate, skin conductance response and movement. Many of these techniques have already been successfully trialled through a pilot study at Glenelg in Adelaide.
“In the pilot study, we used eye-tracking and biosensors to identify stressors and challenges older pedestrians faced when navigating a busy Adelaide area,” Dr Szpak said.
“This new project will extend this pilot study by including a virtual reality user experience to gain further insights into pedestrian behaviour.”
The development of the VR environment will begin with testing a range of different ‘VR locomotion techniques’ –essentially the means through which participants interact with the testing platform – in order to make a VR environment suitable to older people’s particular walking characteristics.
“Recreating the physical environment in VR is time consuming and challenging,” Dr Lee said.
“As we cannot model every detail, we have to decide the right level of detail, so that VR simulation will reflect the reality enough for assessing and testing the new design of the road.
“We are working hard to explore various technical alternatives to find the right tools to achieve the goal.”
Over the course of the three-year study, researchers will compare vulnerable pedestrians’ experiences in real environments with experiences captured in the virtual environment they develop, refining the VR experience until it accurately reflects real life.
“Our ultimate ambition is for councils to be able to use this technology to test road designs virtually with vulnerable pedestrians while still in the planning stages,” Dr Ahn said.
“This means city planners can get an idea of how safe and usable the built environment will be and address any road safety issues well before construction begins.”
The researchers also believe the method they will develop could be adapted to a range of other infrastructure scenarios, allowing planners to ‘test drive’ designs and iron out any issues before committing to the costly construction phase.
“If we can demonstrate the effectiveness of our methodology, there are many other areas of urban planning that could benefit, such as construction sites, shared spaces with pedestrians and vehicles, and new urban development projects across Australia,” Dr Szpak said.
The materials used in construction are of vital importance to a road’s safety, performance, maintenance requirements and longevity. They also significantly affect the construction costs of a road project and the total lifecycle cost of the asset. In the first article in a series on road construction materials, Infrastructure takes a closer look at the different layers making up a road and the varying properties required for different applications.
Currently, the majority of Australia’s biggest and most expensive infrastructure projects underway involve constructing or upgrading our roads. According to 2017 estimates, road projects spend around $5.1 million per lane kilometre on average, varying by road class.
The pavement materials contribute significantly to these costs, at an average of $233 per square metre for an urban motorway or freeway, or $114 for a major rural road. Heavily trafficked major roads are the most expensive, while more minor roads with a lower-traffic load tend to be cheaper.
A wide range of materials can be incorporated into roads, with different mixes exhibiting different properties that affect their suitability for various applications and environments. Foremost, the material mixes used for this essential infrastructure must be fit-for-purpose due to the significant implications for the road safety, functionality, longevity, maintenance requirements, and total lifecycle costs.
For any road project, careful consideration of the materials used is required, especially when certain materials are in short supply, or when looking to reduce costs and waste, while optimising infrastructure performance.
A variety of factors affect the materials that might be suitable for any given road project. For instance, a heavily trafficked road in a high-rainfall area will have different requirements to a minor local road in a dry area.
Key factors affecting road material suitability include:
♦ The intrinsic physical properties of the material (e.g. structural stability, heat resistance, water permeability)
♦ The intensity of traffic loads
♦ The climate and moisture regime of the environment
♦ The availability of material sources
♦ Budget constraints
The available road materials and their properties have significant implications for the structural design of the pavement and entirety of the road. If suboptimal materials for the application and environment must be used, additional measures will need to be taken to ensure the road meets performance standards. These may include different pavement structures to increase durability, with different material mixes in various layers, or supplementary drainage to limit moisture on the road.
Different available materials have different intrinsic properties that will determine their performance in pavement mixes. Some of the most important physical characteristics of road materials are:
♦ Water permeability
♦ Fines content (the amount of fine soil particles)
♦ Plasticity characteristics (ability to undergo permanent deformation under stress)
♦ Stability
♦ Viscosity
♦ Durability
♦ Toxicity
The relative importance of each of these factors depends on the individual application. Ideally, the more moisture a road will be exposed to, the lower the materials’ water permeability should be to reduce failure risk, and the more important the fines content and plasticity characteristics. Likewise, the higher the traffic load the road will experience, the more stable and durable the materials should be.
A pavement structure comprises various layers of materials. Each layer spreads the imposed traffic load to the underlying layers, meaning the stress experienced by the materials is
highest at the surface of the road and lowest at the deepest level. As a result, the quality of pavement materials is usually highest at the surface, with quality decreasing by layer as stress is reduced.
A multitude of possible pavement structures are available, incorporating different materials in various mixes in each layer.
The layers can be categorised as: the wearing course (the surface of the road), the basecourse, the subbase, and the subgrade.
Each layer has different requirements, affecting which materials, and in what mix, are suitable.
The wearing course, or road surface, experiences the most load stress and exposure to the elements of any pavement layer. It must provide a safe, economical and durable surface in all weather (e.g. not become dangerously slippery when wet) and protect the lower layers from moisture, which could result in damage. Ideally, it should provide a dust-free surface to drive on, reduce vehicle operating and maintenance costs, and extend the lifespan of the overall pavement structure. It is also the visible layer
of the road, meaning that its surface characteristics (such as appearance and how it feels to drive on) need to meet community expectations.
Options include: hot mix asphalt, bituminous spray seal, bituminous slurry seal (microsurfacing), and unsealed.
Basecourse
The basecourse provides support to the overlying surface layer and distributes the load to the underlying subbase.
Options include: hot mix asphalt, concrete, unbound granular, modified unbound granular, lightly bound or bound stabilised granular.
Subbase
The subbase provides underlying support to the basecourse and wearing course, and distributes the load to the subgrade layer beneath it.
Options include: concrete, unbound granular, modified unbound granular, and lightly bound or bound stabilised granular.
Subgrade
The subgrade is the bottom layer of the road and provides a foundation for the overlying materials. As such, the strength of the subgrade determines the required thickness of the overlying layers and factors strongly in pavement design considerations.
It is often the in situ material, which has been compacted and prepared to make a formation above the natural surface. Sometimes, stabilisation or modification (such as lime stabilisation) of the subgrade material is undertaken to increase foundation strength.
Options include: in situ granular, and stabilised granular.
out
Governments across the world are looking for strategies for fast economic recovery following world-changing events, such as the current pandemic. Part of their solution is to leverage their own investments, by fast-tracking infrastructure projects to create new jobs and business opportunities, particularly with existing skills shortages in the construction sector. If poorly implemented, however, rather than providing a sustainable economic solution with long-term business and employment opportunities, it may simply be a short-term fix.
Infrastructure delivery involves high-risk environments demanding the highest safety standards, and often complex skills and competencies. It is not feasible to move people from COVID-impacted industries such as retail, hospitality and tourism, directly into infrastructure jobs, many of which require very different technical skill sets, qualifications and experience.
The construction sector has long experienced skills shortages and gaps in key trade, technical and professional occupations across civil, commercial and domestic subsectors. Its workforce is aging, and new technologies require new and different skills. There are insufficient numbers of young people entering the industry to meet existing demand.
The current infrastructure boom, together with the fasttracking of projects, will further exacerbate these shortages and gaps. Government is also supporting the domestic construction market through low interest rates, grants and subsidies, which decreases the availability of skilled or semiskilled workers to transfer from other construction sectors.
The industry is also heavily supported by ‘imported talent’. Skills shortages and gaps may further increase if migration into Australia continues to be restricted.
Developing economic stimulus strategies through infrastructure delivery without specific programs and incentives to support new entrants, whether from other industries or from underrepresented groups, will fail to deliver anticipated outcomes.
Opportunities exist for rapid employment and the longerterm development of highly skilled ‘homegrown’ future talent if appropriate strategies and support mechanisms are provided.
Private sector incentives and government procurement mechanisms will help the government purchase wider economic benefits alongside traditional goods, works and services.
Governments around the world have increasingly used policy and procurement mechanisms to achieve economic and social benefits through spending. Infrastructure delivery is thus linked to wider government objectives, such as employment for underrepresented groups and the retention and growth of regional populations. This approach could be further leveraged to drive opportunities for those most impacted by COVID-19.
Strategies should include robust but realistic contractual obligations that promote business capability while delivering socio-economic outcomes. The best examples are where government and industry have worked together to identify and deliver the right strategy.
When the current infrastructure boom ends, an oversupply of workers may result in unemployment rising. However, construction offers its workforces opportunities to develop highly transferable technical skills that increase employability, either within the operations and maintenance of infrastructure assets or in other industries.
Transport for NSW (TfNSW) established a Jobs, Skills and Industry Participation Advisory Group, and an Aboriginal Working Group for the Regional Rail Project, based in Dubbo. Its key objectives are to increase employment and business opportunities, workforce diversity and regional skills. Group members include NSW and Australian Government agencies, which assist TfNSW and its contractor partners to achieve contractual obligations for jobs, skills and industry participation.
This ‘whole of government’ approach brings together agencies and delivery providers that are directly responsible for the funding and delivery of employment and skills programs, with the contractors that will provide the jobs.
Project delivery, and the operation and maintenance of assets require a range of skills in both construction and nonconstruction roles. Where local supply does not meet demand, training programs and other interventions are needed.
These may range from pre-employment programs for new entrant construction operatives to upskilling programs for those transferring from other industries. Ongoing collaboration is required across government, industry and educational institutions to establish employment and skills programs.
There also needs to be investment in programs that will increase capacity in the longer term. Local school programs, supporting STEM subjects, and university partnerships that increase knowledge transfer, or provide cadetships and graduate opportunities, will contribute to future skills supply.
Victoria’s Big Build Graduate Program provides placements across high-profile projects, including the Level Crossing Removal project. Balit Barring provides Aboriginal pathways to the graduate program. ‘Training for the Future’ is the government skills and industry capability development initiative for rail and infrastructure, which offers people from marginalised backgrounds, including refugees and asylum seekers, skills and qualifications for employment in the Victorian rail industry.
New entrant pathways and attraction strategies are required to draw immediate and future talent, including those with transferable skills from other industries, and groups currently underrepresented in the industry, including women, Indigenous Australians and young people. These will be optimised where combined with more flexible working conditions and improved diversity and inclusion strategies to attract and retain underrepresented groups.
Government should identify and capitalise on longer-term
opportunities. Inland Rail will provide jobs directly through its delivery and operation, but also indirectly through developments along the alignment, providing long-term employment and business opportunities.
NSW Regional Growth Development Corporation, working with cross-government agencies and educational institutions, is developing a Jobs and Skills Strategy for its Parkes Special Activation Precinct. The strategy will identify transferable skills from the infrastructure delivery phase and other industries, and implement an employee attraction strategy and skills development program to provide around 3,000 new long-term jobs in the precinct.
There are opportunities to do more. Where large programs of work are planned, a more holistic approach could be taken across multiple projects or packages of work to achieve more sustainable outcomes. Programs that deliver employment outcomes are often limited by the duration of projects. New entrants may not access or retain further employment due to limited skills, and apprentices and trainees may be unable to complete their qualifications.
To break this cycle, the government could establish centralised ‘labour pools’. Contractors would be ‘host employers’ for the duration of their project, after which workers would be mobilised across future projects within the program. This decreases risk for employers, provides more certainty for workers and allows for ongoing skills development, enhancing career opportunities and increasing industry capability through a more skilled and productive workforce.
Infrastructure Skills Advisory has 20 years of experience delivering socio-economic growth and positive social outcomes through jobs and skills strategies.
From condition monitoring on remote assets to mapping the spread of bushfires, drones have had a significant impact on many sectors in recent years, including infrastructure. But the technology has even more potential for the future, including a predicted economic boost of $14.5 billion in GDP for Australia and the creation of 5,500 full-time jobs each year, over the next 20 years.
These figures come from a recent Deloitte Access Economics report, commissioned by the Federal Government, which investigated the economic benefit of drones in Australia, from growth of the drone industry itself, to the cost savings and productivity benefits it can provide to other sectors, including construction and transport. The report quantifies the potential benefits and savings broader drone use could have for the nation’s economy over five, ten and 20 year periods.
The key findings from the report include:
♦ The growth of drone use is expected to create and support 5,500 full-time equivalent jobs, on average, each year over the next 20 years in Australia
♦ Expanding drone and aerial taxi use is expected to provide a $14.5 billion increase in GDP over the next 20 years – of which $4.4 billion would be in regional areas across New South Wales, Queensland and Victoria
♦ The growth of the drone sector is expected to deliver significant cost savings to businesses of around $9.3 billion over the next 20 years, with $2.95 billion of this in the agriculture, forestry and fisheries industries, $2.4 billion in mining and $1.34 billion in construction
The report finds the economic potential of drones is estimated to be significant across Australia’s states and territories as well as major cities. It estimates that the present value of the deviation in real GRP over 2020 to 2040 for each state amounts to: WA – $2.5 billion; NT – $0.2 billion; SA – $1.2 billion; Brisbane – $2.0 billion; the rest of QLD – $1.8 billion; Sydney – $1.6 billion; the rest of NSW – $1.8 billion; Melbourne – $2 billion; the rest of VIC –$0.8 billion; and Tasmania – $0.4 billion.
These predictions are based on a scenario-based economic modelling approach, which outlines what could happen in the future so industry and government can be aware of risks and opportunities.
In addition to this report, the Australian Government is also planning to work with industry to develop and implement a National Emerging Aviation Technologies Policy. This policy will support the development, jobs and growth of the emerging aviation sector, including drones and aerial taxis.
In this context, “drones” refers to unmanned aerial vehicles (UAV), remotely piloted aerial systems (RPAS), as well as unmanned aerial systems (UAS). The technology can range from basic (GPS sensor, inertial sensors, image sensors and range sensors) to more specialised drones with thermal sensors, hyper-spectral and multispectral sensors.
The popularity of drones in the market began around 2015, and since then the technology has continued to
improve and become more accessible. For many sectors, commercial drone applications are still in the early to middle stages of development which suggests significant potential for the future.
There are a number of current and future uses for these technologies across multiple industries in Australia that can save time and money, and increase worker safety. Current uses of drone technology include:
Construction
Inspections across the infrastructure sector, including on powerlines, bridges and rail assets.
Mining and resources
Stockpile measurement/geotechnical modelling, blast and mine reclamation monitoring, and equipment inspection.
Agriculture
Crop, livestock and large land monitoring, and crop spraying/ pellet application.
Defence
Direct warfare and surveillance activities.
These industry uses are already in place to an extent, but there is still significant potential in these sectors to use the technology to its full potential. Then there are the areas that have been identified as compelling future use cases, which could be seen from around the late 2020s. These uses include the areas of:
Urban mobility
Including airport taxi trips, other taxis and inter-city trips.
E-commerce and deliverables
The delivery of express parcels, food deliveries, imported pharmaceutical deliveries (with high value/low weight), regional and remote pathology drone deliveries, medical deliveries in remote areas and some cargo-airfreight.
Government and community services
Such as emergency ambulance responses, fire response, search and rescue, border patrol, local law enforcement, disaster management and monitoring, conservation management, mapping and research.
Predicted growth of the drone industry has the potential to create new opportunities by automating production processes, leading to cost savings over the medium to long term. The creation and widespread adoption of new transport services such as urban/regional air mobility and e-commerce/ delivery services also shows enormous potential. The Deloitte Access Economics report found that these passenger and delivery drones, and other Lower Level Airspace (LLAS) vehicles, have the potential to address today’s industry challenges such as road congestion, improved logistics, and to generate new products, services and markets. In rural areas of Australia, LLAS is already being used by mining companies, and is expected to offer greater operational efficiency in agriculture and to improve deliveries and services to those remote areas. Many new possible applications, particularly in agriculture, infrastructure, security, transport, media and entertainment, telecommunications, mining, and insurance have been recently achieved through significant progress in technological capabilities and regulatory accommodation.
Some infrastructure companies have been implementing drones for a few years now because of the efficiency gains and reduction in labour costs. In construction, drones are helping operators to survey, map and deliver accurate measurements, and conduct remote condition monitoring and inspections. Drones can help project managers and designers eliminate risk and identify potential problems through the use of drone maps and 3D models on job sites.
The construction industry has historically been the fastest growing commercial adopter of drones ahead of mining and agriculture. Drone uptake will increase as the technology improves and drones are able to better analyse the data they collect.
Looking to the future, Deloitte Access Economics found that the ability to quickly render 3D maps of terrain could be essential to get the most out of drones. High resolution cameras and data processors will need to be able to survey landscapes at 1mm per pixel. Drones will need improved ‘surveyor grade’ global positioning satellite systems that are better georeferenced so the internal coordinate system of a digital map or aerial photo can be related to a ground system of geographic coordinates.
Deloitte Access Economics estimated that there were approximately 3,715 survey and mapping businesses in Australia in 2019. ABS innovation data1 highlighted that 15.5 per cent of businesses in construction introduced a new or significantly improved operational process. Based on this relationship, the number of businesses using drones in a construction-related activity could be 580 businesses across Australia.
Total market potential is estimated to be in the order of 38,500 drone units. The adoption curve for construction businesses is broadly reflective of the early automobile adoption curve with an adjustment to reduce growth under all scenarios. Therefore, the number of drones used in construction could range from around 19,000 units under a low uptake scenario, to 33,600 units under a high uptake scenario, by 2040.
When it comes to the cost-savings predictions that drones could provide the construction sector, it was found that the use of drones in the industry could result in labour cost savings between $130 million to $310 million in 2040 in the low to high uptake scenarios, which is in addition to the increased safety benefits.
These predicted cost savings come from drones being used to substitute existing labour intensive processes in construction such as surveying and inspections. In practice, builders can use drones to collect real-time data about projects and understand on-site conditions to track progress, as well as helping to catch problems before project timelines are delayed.
Complementary software enables builders to use site mapping data to plan, communicate and keep projects on schedule. Further to these potential operating efficiencies, drones also offer occupational health and safety benefits in the form of safer work environments.
When it comes to mobility and transport, there are two potential ways drones could be implemented in the future, with technology currently in the works, these are: Urban Air Mobility (UAM) – an alternative mode of passenger transport in the form of aerial, vertical take-off and landing (VTOL) and eVTOL passenger drones; and e-commerce and drone deliveries.
Urban Air Mobility (UAM) is still in the early stages of its technology lifecycle, with some global companies designing prototypes and undertaking trials. Some of the uses for UAM include airport transfers where passengers use drone technology to journey to and from major airports and central business districts, as well as point-to-point transfers where passengers use drones to journey between infrastructure nodes, which are likely to be located in high population density regions such as inner city/urban hubs.
Deloitte Access Economics found that there are varying viewpoints on the potential year of introduction and adoption paths for this technology. In line with the opinion of those entities consulted, including CASA and AA, its report assumes early introduction in controlled areas between 2023-2025 with more widespread adoption not occurring till later in the decade (around 2030).
The main barriers to the adoption of UAM include physical infrastructure (where they would land) and networks (the need for high speed/low latency networks, effective crash avoidance systems, capacity in electricity grids etc.). The market benefits for UAM are represented by the travel time savings accruing to business passengers. Under a low uptake scenario, these travel time savings are estimated at around $6 million in 2040, increasing to around $66 million in a medium uptake scenario, and $91 million under high uptake. Cumulatively, travel time savings over the period 2020 to 2040 amount to around $24-$453 million under the various scenarios.
An implementation that’s more likely to occur in the next few years is the use of the technology to deliver goods using automated drones to carry packages from a distribution hub to a drop-off location. Deloitte Access Economics’ report looked specifically at three types of e-commerce and drone deliveries including express parcels to complete the ‘last leg’ of a delivery; food deliveries; and pathology deliveries of samples from local medical centres to hospitals and testing labs.
The report predicts that Australia’s relatively fast adoption of new technologies and the geographical spread of cities could be a catalyst for a relatively fast uptake of this technology, with early adoption already occurring and more widespread use predicted over the next 2-3 years (around 2023).
Express parcel deliveries offer the greatest opportunity for cost savings on a per delivery basis (around $205 to $340 million in cost savings in 2040), followed by food (around $80 to $110 million) and pathology (around $35 to $75 million).
Relatively low upfront capital and operating costs (including labour costs) lend themselves to sizable cost savings.
You can already see some real-life examples of this type of utilisation with Amazon running Amazon Prime Air, which seeks to automate last-mile delivery of packages using small drones, as well as Swiss Post, Matternet and Posti who have been testing parcel deliveries by UAV since 2015.
Drones are currently implemented in the public sector for a number of uses including disaster management and recovery, firefighting, and monitoring/inspection of infrastructure. If there are fires, drones can be used to detect the locations, and thermal imaging cameras can see through smoke and assist first responders to deploy assets efficiently.
Post-disaster, drones can be used to survey or map scenes to assess damages, or even to search for missing people. They can also be used in other areas such as police, customs or border control e.g. mapping cities for disaster management efforts, monitoring ports and patrolling coastline.
Drones offer significant cost, efficiency and safety benefits as these activities are typically labour intensive. Drones are already in use throughout Australia for government services, for example in Western Australia, drones were used by the state police force to deliver public announcements at public spaces to assist in enforcing COVID-19 rules.
Deloitte Access Economics predicts lower scale drone uptake is assumed within government services, with widespread acquisitions occurring over the decade to 2030. Widespread adoption to 2030 is supported across Australia in terms of civil government applications that are less subject to infrastructure and telecommunication network limitations.
Use in government services has the potential to achieve labour cost savings between $85-$325 million in 2040. As many of the drone use cases for government services involve surveillance and mapping, labour cost savings are assumed to be comparable with those in the construction and mining industries at around 30 per cent over the case without drones. For more information, or to read the full report Economic Benefit Analysis of Drones to Australia, visit www.infrastructure.gov.au/aviation/drones/.
1 ABS 8158.0.0 – Innovation in Australia Businesses 2016-17 (released 19/07/2018)
June 2021 Deadline: 9 April 2021 September 2021 Deadline: 9 July 2021
Smart cities Earthmoving outlook
Noise and vibration Bridges
Automated and electric vehicles
Urban development
Intelligent Transport Systems (ITS)
DISTRIBUTION (TBC) CORE 2021
November 2021 Deadline: 1 October 2021
AusRail Airports Security and critical infrastructure
IoT & cloud communication Tunnels
Corrosion Disaster management
Machine learning Recycling and waste management
Landscaping and vegetation management
DISTRIBUTION TBC
Road and Traffic Ports
Safety and risk management
Cranes & heavy lifting Freight and logistics
Sustainability Asset Management
Asset inspection & drones/UAVs
DISTRIBUTION TBC
March 2022
Road surfacing and design Spatial & GIS
Deadline: TBC
Rail equipment Training and skills
Signalling, tracking and control systems
Condition monitoring and maintenance
Software, communications and connectivity
DISTRIBUTION TBC
Combining our experience in publishing, live events, digital marketing and video production, Monkey Media has the capability to deliver a range of online events for your organisation.
03 9988 4950
Specialising in the energy, infrastructure and utility sectors, we combine our expert knowledge in these fields with our behind-the-scenes knowhow to help you deliver your events in a range of online formats.
We work closely with our partners to understand why and how you want to connect with your audience online, and can recommend the right solution to help you cut through and achieve the high levels of audience engagement and participation you’re looking for.
Some of the online events we can help you deliver include:
Webinars
Virtual conferences
Awards nights
Round tables
Online learning for a complete online event solution
www.monkeymedia.com.au/services/custom-virtual-events/