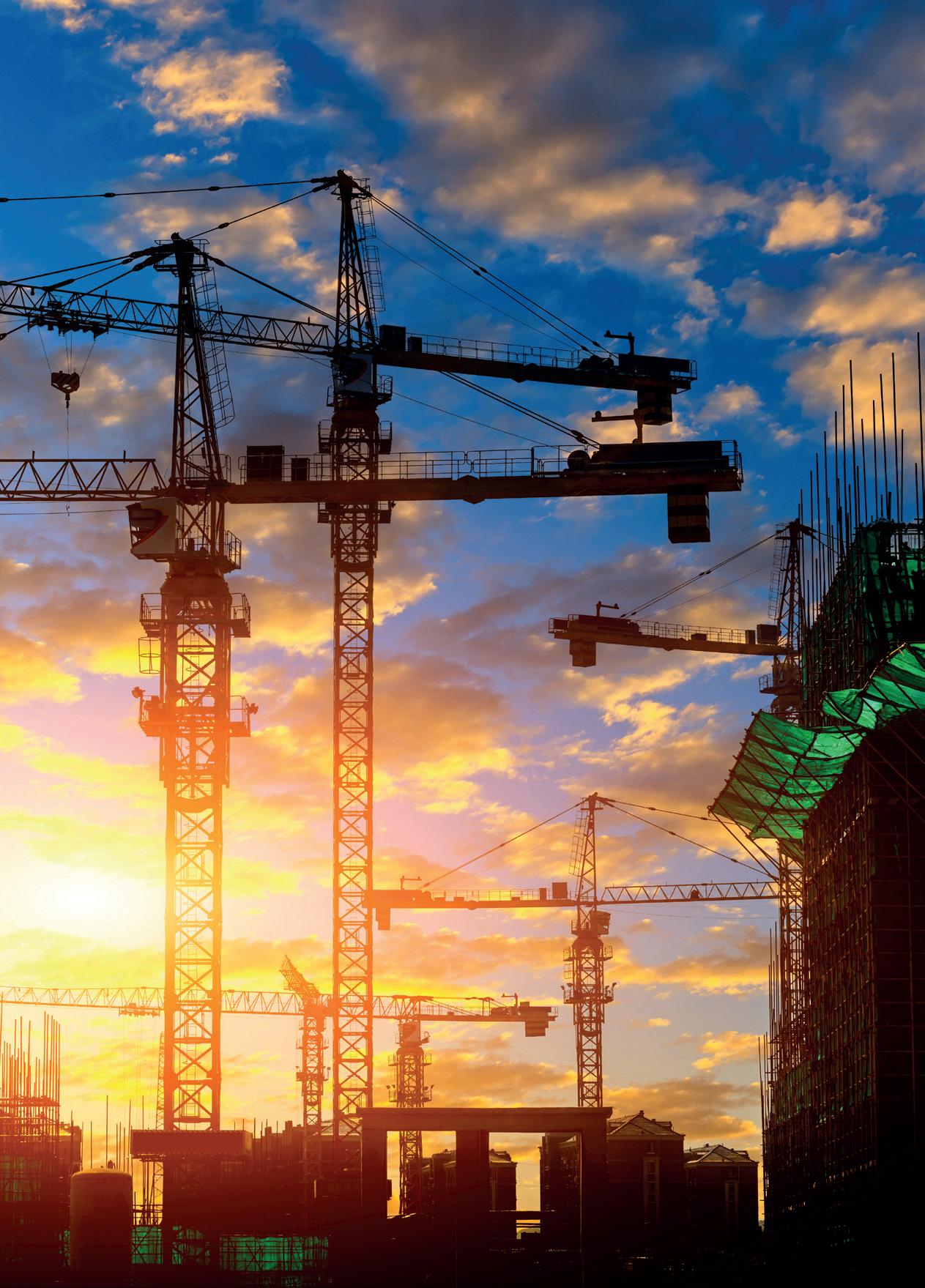
Airports flying towards net-zero

Airports flying towards net-zero
In this game, there’s no substitute for experience. But finding expert Motor Grader operators can be tougher than the terrain they’ll be tackling. That’s why John Deere is the only player in Australia to be offering Motor Grader automation upgrades to all machines from 2019 onwards. Spec’d out with the latest tech including Machine-Damage Avoidance, Auto-Articulation, Auto-Pass, Auto-Shift Plus, and Blade Stow, less experienced operators can get to grips with the machine double quick, and takes the pressure off your more experienced hands. Take your operation to a whole new level. Check your serial number with your local dealer, today.
MOTOR GRADER
JOB SITE AUTOMATION
Published by
Monkey Media Enterprises
ABN: 36 426 734 954
C/- The Commons, 36–38 Gipps St, Collingwood VIC 3066 P: (03) 9988 4950 monkeymedia.com.au info@monkeymedia.com.au infrastructuremagazine.com.au news@infrastructuremagazine.com.au
Editor April Shepherd
Assistant Editor Stephanie Nestor
Journalists
Tess Macallan, Tayla Oates, Steph Barker
National Media and Events Executives
Rima Munafo, Brett Thompson
Design Manager
Alejandro Molano
Senior Designer
Luke Martin
Designers
Danielle Harris, Ozlem Munur, Jacqueline Buckmaster
Marketing Manager
Radhika Sud
Marketing Associates
James Holgate, Natalie Ta
Digital Marketing Assistants
Rhys Dawes, Isabella Predika
Publisher Chris Bland
Managing Editor
Laura Harvey
ISSN: 2206-7906
As I write this the sector finds itself in a state of flux, with long-held promises of culture change and inclusion finally coming to fruition.
Fittingly, Infrastructure Magazine itself is going through a change of its own – our Editor since November 2017, Jessica Dickers – has moved on and handed the publication to me. I have been editing Infrastructure’s sister magazine Council Magazine for 18 months, and I am excited to delve into one of the nation’s most critical sectors as it moves into a new era.
It seems like perfect timing in a way – I have entered the scene just as the Australian Constructors Association (ACA) pledges to change the industry’s culture for the better. As a young woman entering this sector this is music to my ears, and I can’t wait to bring our audience the latest updates and stories along this journey.
To cover this pledge in more detail, this issue features a op-ed by ACA President Annabel Crookes, discussing the challenges the sector is facing and how it is imperative that it transforms to be more inclusive.
Amanda Rose, Founding Director of Western Sydney Women, also weighs in on the gender ratio in the sector, exploring the issue in her article and offering advice.
Our June issue also highlights the other ways the sector is changing – such as the Australian Airport Association’s (AAA) article covering net-zero being a top priority in the industry; and Healthy
Trucks & Sheds showcasing how mental health can be prioritised and improved in the workplace.
Another hot topic is cyber security, as data breaches become an every-day threat, with the Cyber and Infrastructure Security Centre explaining the new rules for the industry, and how they affect critical infrastructure operators.
All of the above points to a slow – but steady – change. As we await the results of the Federal Government’s 90-day review of the Infrastructure Investment Program the future may seem uncertain, but historic change for the industry is a non-negotiable.
I look forward to delivering the latest news and content from the sector, and if you have a story idea or a tip, reach out – my digital door is always open.
PAVING THE WAY TO A CIRCULAR ECONOMY
Milk bottles, bread bags, food wrappers and bubble wrap may seem like unlikely source materials for a road project. But 570t of these hard-to-recycle materials – equivalent to the plastic waste collected from 25,000 Victorian households in just one year – was transformed into the noise walls that line Mordialloc Freeway in Victoria. This one story illustrates the possibilities when we stop seeing waste and start seeing wasted potential.
RESULT BREAKDOWN: 2023 CIVIL CONTRACTORS
FEDERATION NATIONAL INFRASTRUCTURE MARKET CAPACITY SURVEY
The 2023 Civil Contractors Federation (CCF) National Infrastructure Market Capacity Survey has once again produced valuable data on the productive state of the civil construction industry in Australia.
INDUSTRY INSIGHT
WHAT THE AUKUS SUBMARINE DEAL MEANS FOR THE CONSTRUCTION SECTOR – WILL IT TAKE OUR RESOURCES?
FEDERAL BUDGET 2023-24: THE BUSINESS PLAYBOOK
OPINION: WHY A CULTURE TASKFORCE WON’T GET MORE WOMEN INTO THE CONSTRUCTION INDUSTRY
PAINT
COMING INTO LAND: MOVING TOWARDS NET-ZERO AT AUSTRALIAN AIRPORTS
Australian airports are striving to achieve emission reduction goals through good planning, new technology and critical investment, with many already on the path to cleaner and greener operations.
READY FOR TAKE-OFF: PAVEMENT STABILISING SOLUTIONS FOR AUSTRALIA’S AIRPORTS
EXPANDING VICTORIA'S REGIONAL AIRPORTS FOR THE 2026 COMMONWEALTH GAMES
The Commonwealth Games are coming to Victoria in 2026, with preparations underway to deliver the infrastructure required to host the grand sporting event. But while stadiums and accommodation are vital, the aviation sector is just as essential to ensuring interstate and international visitors can access the iconic event.
WASTE NOT, WANT NOT: MRPV’S NEW RECYCLING PARTNERSHIP
Due to the rigorous nature of construction projects, work clothes and personal protective equipment (PPE) experience plenty of wear and tear and are often sent to landfill once considered unwearable. However, initiatives such as the recent partnership between Major Road Projects Victoria (MRPV), Seymour Whyte and UPPAREL are enabling these assets to be recycled, creating new possibilities for discarded materials.
CREATING THE PERFECT BALANCE BETWEEN SAFETY AND SUSTAINABILITY
AUSTRALIA’S FIRST TRUE DIAGONAL ARCH BRIDGE
THE POWER OF A CONNECTED WORKFLOW FOR GEOTECHNICAL SUCCESS
MAJOR CONTRACTORS PLEDGE TO TRANSFORM THE CULTURE OF THE CONSTRUCTION INDUSTRY
DIGITAL INFRASTRUCTURE DELIVERED:
GEELONG’S LEADERSHIP JOURNEY
THE NEW RULES OF CYBER SECURITY: RISK MANAGEMENT PROGRAM NOW REQUIRED
Australian businesses and critical infrastructure operators continue to face a deteriorating risk environment – from cyberattacks and ransomware, to fire and flood, malicious insiders and malign foreign powers – there’s no shortage of risks that need to be thought about and managed in the modern era.
HOW SMART TECH HELPS ICONIC TRAM NETWORK DELIVER 500,000 TRIPS A DAY
WHY COLLECTING SUBSURFACE UTILITY INFORMATION IS CRITICAL FOR INFRASTRUCTURE PROJECTS
SNOOZE CONTROL: HOW WEARABLE TECHNOLOGY CAN TACKLE FATIGUE
Despite decades of attention and countless safety campaigns, the number of injuries and fatalities on construction worksites remains unacceptably high, however wearable technology could change that.
IS YOUR SURVEILLANCE BEST IN THE MARKET?
CHARGING AUSTRALIA’S EV UPTAKE WITH STRATEGIC INTEGRATION
With the increasing uptake of electric vehicles, researchers at the Reliable, Affordable Clean Energy for 2030 Cooperative Research Centre (RACE for 2030) are leading a project to demonstrate how strategic integration with Australia’s electricity grid and energy storage is vital for electric vehicle adoption.
PORT OF NEWCASTLE DELIVERS FOR AUSTRALIA USING SAAS
CREATING PSYCHOLOGICALLY SAFE WORKING ENVIRONMENTS IN TRUCKS AND SHEDS
Principal Consultant, Shivendra & Co
Dr Kumar is the founder of Shivendra & Co, a business consultancy firm that works with small to medium-sized engineering and construction companies to improve performance and maximise growth potential. Shivendra & Co. assists clients on strategy execution, process improvement and digital transformation.
Dr Kumar's mission is to help build thriving businesses that will lead the transformation of the construction industry while concurrently helping develop a future-ready infrastructure delivery ecosystem.
He is also the host of The Competitive Contractor podcast, where he invites infrastructure’s key players to share insights and advice for business success.
Ms Rose is a founder of six founder of six businesses (since sold one), Australia’s foremost strategic connector, professional development trainer, business consultant and keynote speaker.
Ms Rose is the founding director of Western Sydney Women which is a grassroots organisation committed to advocating for all women in Western Sydney. She is also the founder of Small Business Women Australia, an organisation dedicated to providing a voice for women in small business.
President, Australian Constructors Association (ACA)
Director - Legal, Laing O'Rourke Australia Construction Pty Ltd
Ms Crookes has more than 22 years’ experience in the construction industry and, for the last 15 years, has held a number of leadership positions at Laing O’Rourke Australia. She joined the Australian Executive in June 2018, and was the first female Australian Executive.
Ms Crookes was elected as Director of the Australian Constructors Association (ACA), and the first female Vice President in December 2019. She has also been a SteerCo member and Industry Lead of the Construction Industry Leadership Forum (CILF), a collaboration between the New South Wales and Victorian Governments, since 2018.
Mr Goodwin is an experienced executive and non-executive director with a corporate affairs and public policy background, with a particular interest in the transport, aviation and infrastructure sectors.
He was appointed Chief Executive of the Australian Airports Association in early 2020 and successfully guided the AAA through one of its most difficult challenges in history.
He continues to lead the AAA in supporting its members and advocating for national airport policy to ensure the nation has a thriving aviation system that is safe, secure, competitive, and environmentally responsible, with a skilled workforce to benefit all Australians and visitors.
A former journalist and news presenter, he worked for major network news outlets in Sydney and Canberra, including several years in the Federal Parliamentary Press Gallery.
Acting Chief Executive Officer, Infrastructure Australia
Mr Copp was appointed Acting Chief Executive of Infrastructure Australia in August 2022. An accomplished and transformational public sector leader, he has over 15 years’ experience in the Australian Government holding a range of policy, strategy and public affairs roles across infrastructure, workplace relations and the Council of Australian Governments. Prior to his appointment, Mr Copp was Infrastructure Australia’s Chief Operating Officer.
As Chief Operating Officer, Mr Copp was responsible for leading Infrastructure Australia’s Strategy, Finance, People & Culture and Digital Technology functions. He joined Infrastructure Australia in 2014 and set up the public affairs and stakeholder engagement function, before expanding his role across the other operational functions of the business. He is a passionate advocate for Reconciliation and First Nations engagement.
Research Program Manager – RACE for 2030 Cooperative Research Centre (CRC), Electric Vehicles & Energy Networks
Mr Hill is a Research Program Manager focused on network integration for the RACE for 2030 CRC. RACE for 2030 is an industry led cooperative research centre established in 2020 with $68.5 million of Commonwealth funding – to invest $350 million of resources over ten years to catalyse lower energy costs and a substantial reduction in carbon emissions.
Prior to RACE for 2030 he worked on the development and delivery of collaborative industry initiatives such as the Australian Energy Transitions Initiative and consulted professionally across sustainability, environmental and mining sectors.
The Federal Government has announced that it will undertake a 90day independent review into its Infrastructure Investment Program, in efforts to ensure the land transport infrastructure projects it delivers are “nationally significant, and nationshaping projects”.
The government said it is maintaining its commitment to the ten-year $120 billion infrastructure pipeline, and following through on projects already under construction.
Under the previous coalition government, the number of infrastructure projects in the pipeline increased from nearly 150 to 800.
In a media release on 1 May 2023, the Federal Government stated that these projects did not have adequate funding or resources, projects without real benefits to the public were approved, and the clogged pipeline has caused delays and overruns in important projects.
State and Territory Governments agreed to support this review at the National Cabinet, and local governments will be consulted throughout the review.
This process is intended to allow all levels of government time to consider the projects that are priorities and assess their cost and deliverability in the current climate.
Federal Minister for Infrastructure, Transport, Regional Development and Local Government, Catherine King, said, “A properly functioning infrastructure investment pipeline means projects can be delivered with more confidence about timeframes and budgets.
“Easing the pressure on the construction sector will help drive inflation lower and deliver more predictable investment and delivery outcomes from governments.
“Communities will benefit from national significant infrastructure with shorter and safer travel, more liveable cities, suburbs and regions, while the economy benefits from the certainty brought by a smoother delivery of investment matched to project timelines.”
“Importantly for industry, projects under construction will proceed and we have committed to maintain significant infrastructure investment for the medium term,” Ms King said.
The review will be undertaken by Mr Reece Waldock AM, Ms Clare GardinerBarnes and Mr Mike Mrdak AO, who all have extensive expertise in land transport infrastructure.
Australian Constructors Association
The Australian Constructors Association (ACA) has expressed concerns over the review, stating that it has the potential to cause significant cancellations and deferrals.
Cancelling or deferring projects can have a significant impact on the construction industry, as it takes time and resources to assemble teams and develop capabilities to deliver large projects.
Australian Constructors Association CEO, Jon Davies, said delivery of infrastructure is not like a tap; it can’t simply be turned on and off.
“Developing teams and capabilities that are equipped to bid and deliver large projects can take years, and once assembled, it is difficult to relocate them, particularly if there is a widespread deferral of projects,” Mr Davis said.
“It is vital that industry is consulted in the review to avoid inflicting further pain on an industry that is already doing it tough as a result of having to absorb significant rises in material and labour costs.”
Mr Davies said if projects are cut, governments must take action to reallocate a proportion of the saved funds to help the industry by compensating contractors who have incurred significant additional costs without any fault of their own and currently lack contractual relief.
“It is unethical and uneconomical for a government to pay less for an infrastructure project than its
construction cost due to uncontrollable factors like a pandemic or distant war,” Mr Davies said.
“Construction currently accounts for 26 per cent of all business insolvencies in Australia and the implications of these failures on the wider economy are huge.
“As contractors mitigate risk by subcontracting works, any relief provided at a head contract level will similarly flow through the supply chain feeding into areas of the market beyond government infrastructure that have no other opportunity for support.
“Having a steady and transparent pipeline of government infrastructure projects is crucial for the industry to plan and invest for the future, and project cancellations and deferrals undermine this effort.”
Engineers Australia
Engineers Australia has welcomed the review, with CEO, Romilly Madew AO, stating that it will provide an opportunity to target investment to ensure best value for money is achieved.
“This is critical to helping ensure spending doesn’t further fuel current economic challenges,” Ms Madew said.
“Australia’s construction sector is already at breaking point, rising materials costs and labour shortages has caused budgets to blow out and project slippage.
“Over the past two years, engineering vacancies have grown by 80 per cent nationally. A significant contributor to this increase is infrastructure projects.”
Ms Madew said infrastructure projects are mostly medium-to-long term endeavours, taking years to be completed, so a healthy pipeline of projects to support Australia’s future is vital.
“When reviewing the pipeline, it will be important to give due consideration to changing consumer behaviour and economic priorities.
“Fiscal policy needs to balance tackling the cost-of-living crisis currently being experienced with investment targeted to support changing societal needs.
“Any funding allocation should also match the importance of policy
outcomes, such as sustainability and emissions reductions, rather than just individual projects.”
Civil Contractors Federation
Civil Contractors Federation National (CCF) said it looks forward to contributing to the review.
Civil Contractors Federation CEO, Chris Melham, said, “CCF welcomes the opportunity to work with the Government and the review panel to ensure they take into account the current capacity of the civil construction industry as well as other challenges affecting the delivery of projects.
“CCF welcomes the Federal Government’s commitment to maintain funding for projects already under construction and to maintain investment for the medium term, as well as their recognition of the importance to the country of the local construction industry and the infrastructure it provides.
“However, it is imperative that the independent review not only takes into account the current capacity of the civil construction industry in delivering the infrastructure pipeline, but also addresses the key issues that continue to hamper our land transport projects
including inefficient and under-resourced state and territory government procurement agencies.
“In the context of this review, it is important to point out that CCF’s previous surveys have found that there is additional capacity among mid-tier companies, a point which has been previously acknowledged by Infrastructure Australia in its 2022 Market Capacity Report
“The 2022 CCF Market Capacity Survey found the civil construction sector is not operating at capacity, with a large proportion of companies taking part indicating they can take on additional work.
“A key to activating additional capacity is to smooth the infrastructure pipeline over the long term and bring to market more small and mid-sized infrastructure projects, invested across metropolitan, rural, regional and remote Australia, which collectively will increase industry capacity building to deliver our shared nation building objective.
“The economic multiplier for every one dollar spent on civil infrastructure is a return of three dollars to the Australian economy and seven jobs for every $1 million spent – it would be a huge mistake in the current economic climate to reverse engineer the economic multiplier by cutting back on civil infrastructure investment.”
Monday 13 NovemberThursday 16 November 2023
International Convention Centre, Sydney
Registration is now open for the national conference and exhibition of the Australasian Railway Association.
Don’t miss your chance to be part of the largest event in the Asia Pacific region for rail professionals. Organised by the industry, for the industry, AusRAIL PLUS 2023 promises unparalleled networking opportunities and invaluable insights.
Register now to secure your social function tickets and to save on the late registration rates.
Visit the AusRAIL website for pricing and to register.
Exhibition already 70% sold!
Sponsorship and exhibition sales are open. Contact hello@ausrail.com to confirm your interest.
The Victorian Government has announced that tunnel boring is complete on the twin tunnels which form a key part of the West Gate Tunnel project.
The project is expected to provide an alternative to the congested West Gate Bridge.
Victorian Premier, Daniel Andrews, said, “We promised we’d build an alternative to the West Gate Bridge to keep our city moving, and we’re getting on with it – creating thousands of jobs and setting our booming western suburbs up for the future.”
“The West Gate Tunnel Project will slash travel times, take thousands of trucks off local roads, and get families home sooner and safer.”
Tunnel Boring Machine (TBM) Bella broke through in South Kingsville, completing a 4km journey from the west side of the Maribyrnong River under Yarraville to just east of Millers Road near the West Gate Freeway.
Victoria Minister for Transport and Infrastructure, Jacinta Allan, said, “This is a significant breakthrough, completing one of the most challenging parts of the West Gate Tunnel Project – in just a few years’ time, thousands of Victorians will travel through this tunnel each day, transforming Melbourne’s west.”
Since 2022, TBM Bella has operated 24/7, excavating enough soil to fill the MCG while installing more than 15,000 individual concrete segments to create the tunnel walls.
The significant milestone comes after TBM Vida completed her journey, marking the largest tunnel breakthrough to occur in the southern hemisphere.
The massive TBM will be dismantled and removed piece by piece, with the 450t cutterhead buried on-site, and other components either recycled or returned to the manufacturer.
Crews will continue the important work of building the road deck and installing electrical, lighting and safety systems to prepare both tunnels for completion in 2025.
Above ground, work is now underway to construct the ventilation system at the outbound portal and prepare for the installation of the iconic eel net structure.
When complete, the West Gate Tunnel Project plans to transform travel in Melbourne’s west. It will deliver an alternative to the West Gate Bridge, provide a second river crossing, and remove more than 9,000 trucks from residential streets.
Journeys will be safer and more reliable with travel times between Melbourne’s west and the city slashed by up to 20 minutes.
There will also be 14km of new and upgraded walking and cycling paths, and close to 9ha of new parks and wetlands.
No matter where your business travel takes you, you can live as local as you like. Want to find an award-winning flat white? How about the best restaurant to charm clients in town? Because we’re local, we can point you towards the very best. Book direct via the Quest App, the website or by calling the property direct and earn Air New Zealand Airpoints on your stay.
-Hear from key players
-Catch up with peers
-Visit the exhibition
-Celebrate at the awards night
Brisbane Airport Corporation (BAC) is set to undertake the largest industrial project in its history for global logistics and delivery company Aramex Australia, with the company also becoming the first anchor tenant within the airport’s new industrial precinct.
BAC will kickstart the development of Airport Industrial Park with the construction of international courier business Aramex’s new 26,120m² office and warehouse – equivalent in area to more than 3.5 rugby league fields.
This marks the first stage of development of the landmark estate, which is a 100h plus master-planned warehousing, logistics and manufacturing precinct, more than five times the size of Brisbane’s South Bank.
Development of the Aramex facility will involve up to 1,500 workers during the construction phase. Once opened, Aramex will employ 60 people with over 120 Courier Franchises operating from the site each day.
BAC has accelerated its commercial property offering to become South East Queensland’s premier industrial zone, offering unparalleled amenity, transport connectivity and development potential.
Brisbane Airport Corporation Executive General Manager Commercial, Martin Ryan, said securing Aramex as the first anchor tenant within the new industrial precinct demonstrates its attractiveness amongst global brands.
“We are excited to welcome Aramex to launch Airport Industrial Park with us,” Mr Ryan said.
“The size of this development highlights the potential for logistics and industrial development at Brisbane Airport at scale.
“With freight and logistics industries becoming increasingly important, the unrivalled transport links of Brisbane Airport offer an ideal home for companies providing these essential services.”
The development for Aramex will include a warehouse with approximately 25,070m² of Net Lettable Area (NLA), an office of 1,050m² NLA and 157 car parking bays and racks for 14 bicycles plus end-of-trip facilities. There will be space for pallet racking, freight sortation and a customer collection zone.
The development will also feature approximately 1,000kW of commercial rooftop solar panels, about 117 times more than the average current household install.
This adds to Brisbane Airport’s sustainability credentials, with approximately 6,000 solar PV panels already fitted to the rooftops of six recent major developments.
This is in addition to a further 18,000 solar panels already in operation across the airport with more on the way.
Aramex Brisbane General Manager, Jacob Marsters, said the new Brisbane facility would boost their delivery and logistics capability in South East Queensland.
“Brisbane Airport’s direct access to road and air transport means we can deliver our goods even more efficiently to customers,” Mr Marsters said.
“In our business, speed and efficiency are critical. That’s why being located at the Brisbane Airport precinct and connected to major arterial roads were key factors in our decision-making.
“The quick access to the northern, western and southern distribution networks, along with multiple access points in the precinct will be an advantage for our operations.”
The Aramex site is centrally positioned within the industrialzoned 49,571m² precinct, anticipated to be complete by Q2 2024.
Airport Industrial Park stage one is under development, with land preparation for subsequent stages underway.
This development is part of BAC’s 2,700h overall lease holding, among the biggest sites under single ownership in SEQ and the premier gateway to Queensland.
With Australia’s freight demand growing significantly –tipped to rise 60 per cent on pre-pandemic levels in urban areas by 2040 according to government estimates – Brisbane Airport is well-placed to meet demand for quality industrial land development.
Logistics and supply chain companies are a growing sector at Brisbane Airport with a number of national and international companies among more than 425 businesses located across the airport.
The first stage of an $80 million upgrade to a key freight link between the Midland and Bass Highways, in Tasmania, is now complete.
The Illawarra Road project is jointly funded by the Federal and Tasmanian Governments, and aims to improve productivity and efficiency in moving freight and increase safety for all road users.
The Federal Government has committed $64 million under the Roads of Strategic Importance program and the Tasmanian Government committed $16 million to upgrade Illawarra Road from the Bass Highway to the Perth Link.
The completed first stage includes widening the lanes and road shoulders between the Longford roundabout and Bishopsbourne Road and improving safety at the Bishopsbourne Road intersection.
A heavy vehicle rest area has also been created near the Longford roundabout.
Work started on the first stage in March 2022 and was completed in May 2023.
Illawarra Road is a key link providing efficient access to the freight hubs between Hobart and the northern regions of Tasmania.
Planning is progressing on the next stage of improvements, with detailed design underway on a 2.9km section at the Bass Highway end of the Illawarra Road.
Federal Infrastructure, Transport, Regional Development and Local Government Minister, Catherine King, said, “The Australian Government believes in infrastructure investment that not only improves safety for those on our roads but reduces congestion and allows motorists to get to their destination sooner.
“The completion of this road will benefit Tasmania and provide a major economic stimulus to the centres which feed in and out of the Illawarra Road.
“This project, which is funded under our Roads of Strategic Importance
initiative, is important to both Tasmanian businesses and the tourism industry.
“Improved infrastructure and enhanced safety will benefit all motorists travelling on this key transport link.”
Tasmania Infrastructure and Transport Minister, Michael Ferguson, said, “The Tasmanian economy has been growing strongly and improving our freight transport infrastructure will ensure that growth continues.
“Improving the efficiency and safety of transport networks enhances productivity in the broader economy and is a priority for the Tasmanian Government.
“We are investing heavily in upgrading key freight routes and strengthening bridges to cater for modern heavy vehicles.
“Illawarra Road is a key link between the north and south of the State. Its upgrade will benefit not only our freight operators but provide a safer, more efficient route for everyone using this road.”
The Federal Government has announced that doublestacked trains will not travel through the City of Logan following an independent review of the Inland Rail project.
City of Logan Mayor, Darren Power, welcomed the review by Dr Kerry Schott, recommending the construction of an intermodal terminal at Ebenezer, near Ipswich, to effectively end the Inland Rail route at that point for the doublestacked carriages.
The Federal Government has agreed ‘in principle’ to this recommendation. Single-stacked trains would continue to Kagaru, Acacia Ridge and Bromelton, including through Logan, to allow connectivity to ports and other rail networks.
“After years of standing firm on our opposition to the proposed Inland Rail,
I was delighted to hear the news today,” Mayor Power said.
“This really was a ‘David and Goliath’ clash but it shows you should never give up on something that is worth fighting for.”
Dr Schott’s Inland Rail review made 19 separate recommendations, as it forecast the budget for the project to double to $31 billion with completion not expected this Decade.
The Mayor said it was a small and long overdue win when the Federal Government committed to the independent review of the project in 2022.
“When I met with Minister for Infrastructure, Catherine King, in 2022, I made her aware of our community’s long-held concerns about the project,” Mayor Power said.
“We know the route was selected without consultation and impacted residents did not get an opportunity to have their say on the route or offer alternatives.”
Logan City Council’s Infrastructure Chair, Teresa Lane, praised the decision to seek a new direction for Inland Rail.
“This just makes common-sense to explore a new route that has less impact on our growing city and booming residential areas,” Ms Lane said.
“I join the Mayor in thanking the new Federal Government for listening to local residents’ genuine concerns about this project.”
Featured image: Tim Frazer, Infrastructure Chair Teresa Lane, Mayor Darren Power and Natalie Willcocks at the rail bridge on Pub Lane, Greenbank. Provided by City of Logan.
Victoria’s manufacturers and suppliers of green construction materials will be showcased to the world this September, as ecologiQ’s Greener Infrastructure Conference returns.
The Victorian Government’s ecologiQ program is leveraging the state’s significant infrastructure investment to boost the use of recycled and reused materials, make these products business-as-usual and build local markets.
ecologiQ’s three-day conference at Melbourne Convention and Exhibition Centre will bring together leaders in sustainability, infrastructure and research to plan pathways to a greener future and explore how to take it even further.
The event, held on 18-20 September, builds on the resounding success of last year’s inaugural conference, which was attended by almost 900 industry leaders across the infrastructure, government and sustainability sectors.
The trade hall was brimming with innovative suppliers and manufacturers of recycled products and led to some incredible success stories, including for OC Connections Enterprises – an Oakleigh-based social enterprise that employs people with disabilities and manufactures 100 per cent recycled traffic bollards.
The conference resulted in construction teams ordering more than 4000 bollards, while other suppliers of products made with recycled material – including recycled plastic railway sleepers and pavement made from discarded tyres – have also reported a boost in sales.
This year’s trade hall will be filled with even more makers of waste-to-resource products, who are a growing part of Victoria’s $31 billion manufacturing industry. The sector is in a prime position to supply the resources needed to deliver the Victorian Government’s transport infrastructure projects and beyond.
As Victoria transitions to a circular economy, these businesses will take on even greater importance and ecologiQ will connect them to a sustainable pipeline of demand, using the Recycled First Policy to drive action.
The Recycled First Policy requires constructors on Victorian Big Build projects to optimise their use of waste materials. It has resulted in almost three million tonnes of recycled materials being committed to transport projects – more than enough to fill the MCG.
The Victorian Government’s Recycling Victoria plan underpins these efforts with funding to grow recycled material suppliers, with the transition to a circular economy anticipated to create 3900 new jobs and boost the economy by up to $6.7 billion.
Major Road Projects Victoria, Director of Program Services & Engineering, Alexis Davison, said, “I’m proud that Victoria’s biggest road and rail projects have been such a powerful force for positive change in driving a circular economy. Our continued ambition will ensure Victoria stays at the forefront of innovative use of recycled and reused materials.”
“The flow-on economic, environmental and social benefits of Victoria’s transition to a circular economy will be felt for decades to come.”
The economic, social and environmental impact of establishing a circular economy will be detailed during the conference, which will feature a range of keynote speakers, panel discussions and networking events.
Attendees will have the opportunity to learn about how greener materials are currently being integrated into transport infrastructure and how collaboration and innovation can take it to the next level.
18–20 September 2023
Melbourne Convention & Exhibition Centre
Registration is now open.
Victoria’s infrastructure industry is joining forces to create a greener future and deliver purposely greener projects. Be part of the change.
The three-day conference will feature industryleading speakers, expert panels, networking events and a trade hall that’s bigger and better than ever.
Scan code to register ecologiq.vic.gov.au/conference-2023
Australia has a ballooning waste problem. The most recent National Waste Report lays it out in black and white: 76 million tonnes of waste generated in just one year equates to 2.95 tonnes per person.
We are also making record investments in road infrastructure, with the 998 road projects to be delivered between 2015 to 2031 demanding around 200 million tonnes of conventional materials.
To address these challenges in tandem, we must start paving the way to a circular economy.
Australia has an extensive road network covering more than 877,000km – and that network is growing – with around $149 billion being spent on major transport projects over the next five years.
For decades, road agencies have used recycled materials to reduce waste and emissions. But unprecedented public infrastructure investment, which places extra pressure on already stretched material supply chains, is driving us towards the circular economy at speed.
Late last year, Infrastructure Australia launched the Replacement Materials report to spark new conversations about how road projects can make better use of recycled materials.
By Adam Copp, Acting CEO Infrastructure AustraliaMilk bottles, bread bags, food wrappers and bubble wrap may seem like unlikely source materials for a road project. But 570t of these hard-to-recycle materials – equivalent to the plastic waste collected from 25,000 Victorian households in just one year – was transformed into the noise walls that line Mordialloc Freeway in Victoria. This one story illustrates the possibilities when we stop seeing waste and start seeing wasted potential.
To understand the size of the opportunity, Infrastructure Australia worked collaboratively with the Australian Government’s Department of Climate Change, Energy, the Environment and Water as project sponsor, the National Transport Research Organisation (formerly Australian Road Research Board), EY as project contractors and ecologiQ in Victoria as project advisor.
We estimate, based on current technology and standards, that around 27 per cent of conventional materials – roughly 54 million tonnes – could be replaced with a range of recycled materials.
But if we work together to address the obstacles preventing large-scale adoption of recycled materials, the outlook is even more optimistic – with the replacement rate rising to as high as 59 per cent, eliminating the need for nearly 119 million tonnes of conventional materials.
Infrastructure Australia’s report found several significant roadblocks must be addressed. The first is the industry’s low level of familiarity with available recycled material products, their performance, environmental benefits or the market opportunities. For example, around 38 per cent of recycling and waste processing businesses reported that they have customers who perceive recycled materials to be of lower quality.
The solution is to develop performance-based standards and consistent specifications that foster trust and transparency, and that build awareness of the opportunities.
Unfavourable regulatory conditions, which contribute to market uncertainty, negative perceptions and a risk-averse culture, also hold us back. Almost one in five (18 per cent) recycling industry businesses we surveyed noted that this impacted industry confidence, by creating doubts in the minds of businesses and users on the quality and durability of such materials.
To advance market innovation and grow the circular economy, greater engagement is needed between regulators and recycling industry representatives. Governments can also revisit regulations that treat recovered materials as waste, rather than as potential resources.
Low demand leads to low supply. To create certainty and provide a strong boost to the market, governments can focus on facilitating procurement-driven demand, providing easy-to-access market and cost information, and sending clear demand signals to support market growth.
Capacity building is also key to ensuring the recycling industry can deliver high-quality products. Governments can provide incentives and financial support to modernise and extend the reach of recycling infrastructure, and to boost workforce capacity.
There are also a mix of common and specific issues causing supply capacity constraints. Fly ash, a by-product of coal that is commonly used in recycled concrete products, is becoming harder to source as coal-fired power generation is phased out, for instance. Geographic barriers also exist, with recycled material supplies often concentrated in metropolitan areas, making access limited in more remote areas.
These examples illustrate the complexity of the challenge ahead.
Nothing short of market transformation is required. But the Mordialloc Freeway project is a stand-out success story of how circular economy thinking can create new shared value.
The 32,000m² of recycled noise walls – which used the equivalent of 30 million water bottles – were made by 70 local workers at PACT Group’s manufacturing facility.
At less than half the weight of steel or concrete panels, the wall panels are quicker and safer to install than their traditional counterparts. They are non-porous, which makes them graffiti
proof. The panels, which should be in place for at least four decades, can also be recycled again at the end of their life on the road.
Australia’s recent stockpile of soft plastics is a very visible manifestation of a massive problem for our nation. But this stockpile also shows that millions of Australians want to be part of the solution to our waste problem.
One of those solutions is right before us. As Infrastructure Australia’s latest report shows, recycled materials can literally pave the way to a circular economy.
The 2023 Civil Contractors Federation (CCF) National Infrastructure Market Capacity Survey has once again produced valuable data on the productive state of the civil construction industry in Australia.
CCF undertook this anonymous survey over a four-week period in April/May 2023 involving around 100 companies spread evenly across all states and territories.
The survey delved deep into the industry's productive capacity throughout the sector and across Australia.
CCF thanks its members for undertaking the survey and acknowledges Infrastructure Magazine for supporting this important industry initiative.
The survey captured companies who are working across all facets of the civil construction industry, including roads, bridges, drainage, land development and water.
In addition to capacity, the survey also analysed some of the challenges facing the industry in delivering the civil infrastructure pipeline now and into the future, including skill constraints, risk allocation and procurement processes.
In many cases, the results reconfirm what we found in the 2022 Market Capacity Survey, which was that industry is in a strong position to take on additional work, particularly when large-scale projects are de-bundled to attract greater involvement of mid-tier companies.
CCF has provided the results of the 2023 survey to Infrastructure Australia and other government agencies who are responsible for advising the government on infrastructure investment, procurement and skills matters.
We will also incorporate the results in our submission to the Federal Government’s Independent Review Panel which is currently undertaking a review of the federal $120 billion, ten year rolling Infrastructure Program.
The economic multiplier for every one dollar spent on civil infrastructure is a return of three dollars to the Australian economy and seven jobs for every $1 million spent –the CCF is therefore pleased that the Federal Government reaffirmed its commitment to retain the $120 billion infrastructure program in the budget recently handed down by Federal Treasurer the Hon. Jim Chalmers MP.
Key findings from the 2023 Civil Contractors Federation National Infrastructure Market
Capacity Survey include:
♦ A quarter of respondents indicated their volume of work has increased more than 50 per cent over the past 12 months
♦ Almost half the respondents advised their costs have increased by between 10 per cent and 25 per cent
♦ When asked if they could take on additional work if it became available, a large proportion of mid-tier companies said they could take on additional work, with around a third saying they could take on between 10 per cent and 25 per cent
♦ Construction companies confirmed they had additional capacity to take on this additional work in both metropolitan and rural/regional areas
♦ An overwhelming majority advised that if additional projects were tendered, they would be able to meet this additional demand within six months
♦ Similar to the 2022 survey, the study showed that the key challenges in the successful delivery of infrastructure projects are unfair allocation of risk in contracts, the need to include rise and fall clauses to make the contracts fairer, and the need to attract and train more skilled tradespeople to undertake projects
♦ Plant operators, tradespeople and construction workers are three of the most in demand occupations at the present time – reinforcing the need for civil occupations to be appropriately classified as trades in the ANZSCO Coding system
♦ One of the main challenges in recruiting additional staff is that candidates applying for positions do not have the necessary level of skills or experience to undertake the role
♦ Significant challenges and barriers continue to impact on the ability of companies to reduce emissions from their operation, with many indicating that complexity and cost is limiting their ability to address emission reductions
The survey’s findings reinforce the need for urgent action by all levels of government to address the policy challenges facing industry, particularly in the area of skills, procurement and risk allocation.
CCF will continue to focus on these issues as we work with governments on behalf of industry to create a stronger, more sustainable civil construction industry.
For further information on the 2023 Civil Contractors Federation National Infrastructure Market Capacity Survey, visit the CCF website www.civilcontractors.com.au.
The recently announced AUKUS nuclear-powered submarine pathway is the single biggest investment in defence capability in Australia’s history. While there is some infrastructure construction required, questions are being raised around the impact of increased defence spending on current construction projects, especially when it comes to resource allocation, skilled workers, and supply chains. However, there may be opportunities to use what’s happening in defence to overhaul construction models and ecosystems, so that it becomes a win-win for all industries.
WHAT THE AUKUS
DEAL MEANS FOR THE CONSTRUCTION SECTOR – WILL IT TAKE OUR
The AUKUS initiative will be carried out in stages, with an expected $6 billion to be invested in Australia’s industrial capability and workforce over the next four years.
There will be some overlap with infrastructure required for defence projects and businesses across Australia will have the opportunity to contribute. Businesses that can align themselves with these opportunities will reap enormous rewards. However, the deal also poses challenges for the industry.
An overlap between the skills required for both industries, particularly in the early phases, will inevitably result in a dilution of resources from infrastructure to defence. Not only will this impact field workers, but also engineers, commercial, administrative, IT and HR roles.
Defence provides long-term prospects, high-level skills and the opportunity for employees to engage with multinational organisations who will work across the UK and the US. There’s a risk of higher skilled staff being diverted to defence, given its attractiveness with technology, exposure and hype.
Same can be said for business investment, as the benefits of a defence contract could look more rewarding than other transport, energy or utility projects. With the construction sector continuing to face financial risks, and small and medium-sized contractors often carrying the weight of these, perhaps defence could offer fairer commercial models and lower risk to businesses.
This could all lead to an increase in costs, not only labour costs, but materials, as increased pressure will be placed on supply chains. Will manufacturers be able to support the greater volume of material demand? An increase in demand for steel, electrical and other products may drive prices up.
While the AUKUS announcement creates many questions for infrastructure, it could also be viewed as an opportunity to enact major change. When it comes to major construction projects, how can we deliver projects more reliably, efficiently, and economically?
And beyond this, could the AUKUS deal spark the change required to make construction businesses more desirable to be involved in global mega-projects?
There’s a few specific things the industry must now do. Firstly, the time to review contract and risk allocation models is long overdue. We need to identify how to make construction projects less risky.
In my previous discussion with Jon Davies, CEO of the Australian Constructors Association (ACA), we agreed that innovation for the larger methodologies of projects, rather than investing in individual projects, must be a key focus.
The industry should shift away from fixating on the lowest possible price and focus attention on non-cost criteria for success.
Improving productivity is also critical. Businesses need to learn how to do more with less by utilising technology, implementing structured processes, and increasing adoption of prefabrication and standardisation.
To drive productivity improvements and deliver projects smarter, businesses should focus on innovation. This requires the prioritisation of investment and long-term vision.
It is difficult for businesses to navigate the peaks and troughs of construction in a volatility, uncertainty, complexity and ambiguity (VUCA) world.
Whereas defence provides a secure outlook and stability, with projects like AUKUS minimising risks.
Defence is attractive as there is huge potential within one agency, whereas infrastructure projects are distributed between federal, state and local governments, and between departments/agencies.
Construction needs to build communities of businesses, skills and professionals who provide a centre of excellence for particular types of projects e.g roads and tunnels. These businesses can then be given a longer pipeline of projects with productivity incentives and the mandate to enhance local capability.
These pipelines should go beyond election dates, with the ecosystem approach enabling businesses to have a long-term view, securing investment, recruiting the best people, and investing in technology.
This also helps small to medium businesses as they can grow – instead of current models where they are engaged but may not last the project or not engage with the prime on the next projects. We need to see more small, family-owned and First Nations local businesses becoming national businesses.
The Federal Government released its Defence Strategic Review 2023 on 23 April, providing more detail on how it is shifting the country’s approach to defence and how this will impact the Australian industry.
The document contains a sense of urgency concerning the need to translate the strategy into outcomes. With the drive to recruit and train more Australians in defence and defence-related industries, one can expect to see a significant percentage of the small to medium-sized construction business workforces migrate to defence-related jobs.
As defence prioritises and streamlines approvals and acquisition, it might also be easier and faster for contractors to secure contracts and be paid on defence projects, making them more attractive overnight.
While there are still many unknowns around the impact of AUKUS – will businesses involved find it rewarding? Will it provide fairer commercial models and lower risk? Will it dilute Australia’s resources and create an environment of increased costs? Regardless, this deal should be viewed as a chance for construction businesses and the wider sector to assess how productivity can be improved to deliver better projects overall.
Whilst the new infrastructure projects and affordable housing projects featured in this year’s budget were welcomed by many in May, every budget has winners and losers. The question now is which businesses will survive long enough to deliver on these projects? The Finance Consultancy Director, Chris Slack, gives his thoughts below
In recent years the construction industry has dominated the list of businesses that have entered insolvency –the largest by number since May 2020 – whilst one of the leading lenders to businesses in construction also recently ceased trading.
The budget outlines a government’s fiscal policy, while this financial year many mortgage owners are focused on monetary policy as RBA announcements making repayments more and more unaffordable.
Government spending can affect inflation, which then in turn influences whether the RBA increases interest rates, and this then affects the value of Australia’s currency relative to other countries.
As such the measures of the budget may mean that the RBA has no choice but to make further rate increases in 2023. This would be a welcome relief for those businesses importing goods; but temper the demand for exports – depending on how a business chooses to manage currency risk.
The instant asset write-off reverting to a lower turnover threshold was inevitable, however many businesses relied on ‘sugar hits’ post-COVID, whether it be a rebate, quicker depreciation, or now with the payment for eligible businesses towards rising electricity bills.
The requirement to pay employees superannuation in real time makes sense albeit a few years away.
Most businesses have not had an issue with meeting superannuation responsibilities – besides the few that have been considered ‘persona non grata’ by lenders.
Many businesses with higher turnover and lower margins already utilise debtor finance to cover payroll as they grow –which will add to any cash flow challenges.
Federal Treasurer, Jim Chalmers, has outlined his budget playbook – so what is yours?
HERE ARE THE FINANCE CONSULTANCY’S TOP TIPS:
♦ Set your own capital expenditure budget for the next 12 months. What is the opportunity cost of not having the new vehicles/equipment?
♦ Ensure your business is up to date with lodgement deadlines and tax responsibilities – the bank of the ATO is firmly closed
♦ Assess whether your financials have improved this financial year and consider locking in any increase to your overdraft/lines of credit now to take advantage of future opportunities
♦ Look at your currency risk management
♦ Review your payment terms – both what you are receiving from suppliers and giving to customers. Can you access discounts for earlier payment that may be less than your costs of borrowing?
♦ No business is too big to fail – get quotes for Trade Credit Insurance and strengthen your company
♦ Regularly review the Personal Properties Securities Register (PPSR) at least twice yearly and get advice around this – are suppliers and financiers affecting your credit and opportunities without you being aware?
♦ Review your advice team – accountants, lawyers, consultants etc. to constantly seek out best practice–and consider using a finance broker to keep your existing lenders honest
If you’d like to find out more, go to https://www.thefinanceconsultancy.com.au.
With only 12 per cent of women making up its workforce, it’s no secret that the construction industry is dominated by men. The real story is that despite their best efforts, neither government nor industry can shift the stubbornly entrenched gender ratio as quickly as they’d like.
Even in the face of a higher-thanaverage earnings potential and a critical shortage of skilled workers, a career in construction fails to have widespread appeal to women, resulting in a serious imbalance that is steadily getting worse.
The current lack of qualified workers is so acute it’s estimated that in 2023 there'll be 105,000 jobs that won’t be filled. To further compound the issue, forecasts by IHS Markit show total real construction industry spending is expected to grow by 3.5 per cent in 2022 to reach 4.2 per cent by 2024, meaning that one of Australia’s biggest employers will continue to suffer from a lack of skilled labour without some form of serious intervention.
It’s laudable that the New South Wales Government’s Connecting Women to Trades program has received a second
bout of funding, however programs are just the start – we need to address the entrenched inequality that is currently rife within the industry.
When at least 51 per cent of women working in building and construction have experienced sexual harassment at work, a commitment to creating safe and inclusive workplaces is hardly a vote of confidence for working in construction. It needs to be a top down bottom up approach.
According to a NAWIC survey 73 per cent of women in construction said they had experienced gender adversity while on the job. Simple things such as a lack of female or gender-neutral toilets on site, to intimidating treatment at the hands of colleagues; all contribute to a toxic work environment that endangers women’s wellbeing.
The reality is women are keen to work, but they’re unlikely to jump on board if they perceive the industry to be irredeemably hostile to their interests.
Beyond a more female-friendly culture and equal pay, effort needs to be directed towards fostering an interest in construction from a young age, increasing the opportunity for young women and girls to have practical experience in the industry and making mentors and role models more accessible.
As other traditionally male-dominated industries like law and finance rapidly undergo image rehabilitation to meet the 21st century standard, construction is consistently being left behind – and it’s not always because of lack of effort on the part of employers.
Recent research into the issue revealed women believe they would ‘not be respected’ and felt they would be ‘intimidated’ and discriminated against if they worked in construction. These negative perceptions are deeply held, and the stereotype that construction is all about manual labour, high vis gear and toxic masculinity is pervasive.
Without female role models to look to and no chance to experience the modern construction industry or learn about the variety of roles it offers, women can’t even picture themselves in a successful career in construction. On the other hand, examples of blatant discrimination are rampant and do little to assuage women’s doubts and fears about the sector.
We also need more male mentors that can set a standard and be an example to the rest of their team, company and industry.
According to a 2020 study on women in construction by RMIT, women’s professional capabilities were regularly “scrutinised, questioned or devalued”.
They subsequently felt the need to work harder than male co-workers to prove themselves; mistakes were put down to their gender and complaints about poor treatment would frequently lead to further victimisation.
Even the matter of entry into construction is rife with pitfalls – from the recruitment process which is often through informal networks and wordof-mouth recommendations to the way apprenticeships are set up, which routinely disadvantage women over men.
For there to be long-lasting change, legislators and industry must take a ‘ground-up’ approach where young women and girls are exposed to the various roles available in construction.
Not only does there need to be education and awareness starting from an early age for all genders, but parents, educators, and career counsellors also need to be made aware of the rich opportunities that exist within the field.
Construction is not just limited to plumbing, carpentry, or electrical and mechanical work; there are positions in project management, engineering, land surveying, commercial management and more.
Beyond apprenticeships, alternative pathways into the industry include university, internships, and TAFE. As it stands, career counsellors are poorly informed about career options in modern construction and many fail to share them with young women at the same rate as young men.
Increasing the opportunities for young women to have practical experience in the industry also makes sense, because for women to feel comfortable enough to pursue a career in construction, there needs to be more tailored programs to develop the skills, knowledge and contacts needed to progress in the sector.
Developing apprenticeships to suit more women – including mature age candidates – is another way to boost female participation in construction and trades.
Grassroots initiatives like the Building Your New Career program primes women with effective communication
and technical skills to enter the industry via a series of valuable microcertifications, such as a construction White Card and first aid certificate.
Last of all, making female mentors and role models more accessible to women gives them a valuable point of reference in a majority-male environment. It is grassroots memberled support that will help affirm women’s value in construction and enable them to truly thrive.
If women can have direct exposure to the industry from a younger age and access to a wide range of mentors and role models, they’ll feel more confident and well-equipped to take on its challenges.
Without sustained effort to demolish the fundamental barriers women and girls face in entering construction, the new government is unlikely to achieve its goal of boosting female participation by 15 per cent by 2030.
Solving the issue of too few women in construction would go a long way to alleviating the pressures on the industry during this unprecedented time. Without it, the infrastructure sector will continue to stagnate and eventually take its toll on the wider economy.
Australia's cities are focused – now more than ever – on building sustainable spaces that can stay cool in extreme heat, and boost canopy cover for the region. Light rail presents a great way for these areas to increase greenery by prioritising green track installation in urban planning.
Green tracks, using lawn or sedum, retain a large amount of rain water and bind fine particulate and road dust to improve the micro environment in urban centres. Moreover, recycled rubber encapsulation of rail ensures primary airborne noise and vibration is reduced significantly.
The STRAILastic Top of Rail (TOR) Light Rail system provides, not only the opportunity for new routes to be greened using its various green track options, but also simple, cost-effective green track conversion of ballasted track using the STRAILastic R Green track design.
STRAILastic TOR has helped provide Sydney’s T1 Dulwich Hill Line and Melbourne’s Canterbury Road, St Kilda line with a new lease on life and created a cheaper solution for extensions.
STRAILastic TOR provides a track system that is stable and reliable in Australia’s unpredictable climate. The benefits of the vulcanised rubber solution extend beyond its resilience and stability. While made from 70 per cent recycled rubber, the outer cover of virgin rubber contains UV, ozone and fireresistant materials to withstand the elements.
Cities across Australia can have rapid temperature changes. Melbourne often has four seasons in one day with temperature variations of 10 degrees or more in an hour. A southerly change in Sydney can turn a 40°C day into a 20°C evening, and South-East Queensland’s tropical storms can rapidly drop the mercury.
Besides wreaking havoc on what to wear, these temperature variations place significant stress on tram and light rail track infrastructure, whether it be asphalt, pavers or concrete. Installing ‘green tracks’ can mitigate these rapid temperature changes, reducing the high stresses by expanding and contracting.
Andreas Göschl, STRAILastic’s International Operations Director, said, “Based on 40+ years experience in moulding vulcanised rubber, the STRAILastic TOR track systems have a high temperature stability, and easily manage the expanding and contracting of temperature ranging between -40°C and +90°C, with a glass transition point of -55C, ensuring a stable TOR product under normal operating conditions.”
Installation is simple, with the precisely moulded selfclamping chamber filler fitting like a glove against the rail without glue, and finishing level with the railhead. It withstands the wear and tear of traffic, is easy to undertake rail replacement, and has a non-slip moulded surface for bikes and pedestrians.
Its small tolerances avoid gaps, preventing entry of water, sand, sediments, and dirt between the rail and the chamber filler. This ensures there are no electrical conductivity issues or corrosion of the rail web.
Chamber-filling elements are common in many light rail networks, but not all are created equal.
“STRAILastic does not use polyurethane as it is more like plastic, expanding when warm and shrinking when cold, reducing the life of the track,” Mr Göschl said.
STRAILastic has experience in long-life light rail track damping in over 60 cities and with 300km of light rail track, keeping city’s trams and light rail quietly moving.
For more information, please visit https://www.strail.de/en/
mini soundprotection wall with high absorbing surface
The new version of the STRAILastic_mSW adds a higher wall to the product range. This version is used for train speeds of up to 120 km/h.
¬ No foundation required for installation
¬ easy and quick installation
¬ Short delivery times > noise hot spots can be supplied with products quickly
¬ Closer to the noise source than any other sound protection
¬ Break-proof due to fibre-reinforced rubber compound with a cover layer of virgin rubber > UV and ozone resistant
¬ No material fatigue caused by vibrations or pressure and suction forces
¬ No problems with oversized loads
Due to the higher design, it gains even more effect in the area of the wheel.
STRAILastic_mSW 730 is fastened to both rails with an insulated, decoupled substructure or directly in the subsoil using ground screws.
STRAILastic_mSW 730 > mini goes maxi.
1. STRAILastic_mSW 730 new version of the mini sound protection wall
2. STRAILastic_IP the infill panel
3. STRAILastic_mSW the established mini sound protection wall
4. STRAILastic_A inox 2.0 rail dampers
Australian airports are striving to achieve emission reduction goals through good planning, new technology and critical investment, with many already on the path to cleaner and greener operations.
Airports had already set or were planning their own emissions targets well before the current Federal Government committed Australia to net-zero by 2050.
Most of Australia’s major airports have already committed to net-zero between 2025-2040, beating the government’s own timelines, with many using renewable energy to reach these targets whilst making space for broader conversations.
As a first step, most airports are tackling Scope 1 and 2 emissions through initiatives such as building design, energy-efficient lighting and heating, rainwater harvesting, and solar panels.
Runway surfaces loom as a critical sustainability project for airports, with regular resurfacing works producing significant emissions.
To combat this, airports are working with partners in the civil engineering space to study recycled materials that are being used to build roads, to see if they are appropriate for airfields.
Scope 3 represents emissions that are outside the airport’s operational control but occur due to the airport’s activities, including carbon emissions generated by ground transport to and from the airport and by aircraft taking off and landing.
The next step for airports will be to focus on airlines and alternative fuel sources over the next 15 to 20 years. The alternative fuel option is Sustainable Aviation Fuels (SAF), produced from sustainable feedstocks that are very similar in chemistry to traditional fossil jet fuel.
Using SAF results in the reduction of carbon emissions compared to conventional jet fuel, especially when looked at over the full lifecycle of its use.
Typical feedstocks used in SAF include cooking oil and other non-palm waste oils from animals or plants; solid waste from homes and businesses, such as packaging, paper, textiles, and food scraps that would otherwise go to landfill or incineration. Other potential sources include forestry waste, such as waste wood, and energy crops, including fast-growing plants and algae.
Airport
Airports, as a critical enabler of SAF, will continue to play an important role in the discussion in Australia. If one airline doesn’t want to use SAF, but one does, that would mean using different fuel tanks – which would not be of any net benefit to the aviation sector.
To help combat emissions goals across airports, the Federal Government has established an Australian Jet Zero-style Council (the Council) to
inform the design of policy settings – to encourage emissions reduction across the aviation industry.
The AAA is waiting for further guidance on the makeup of representatives of the Council, but airports want and need to be included.
Through the Council, the Department of Infrastructure, Transport, Regional Development, Communications and the Arts would like to understand the infrastructure needed to support SAF at airports.
While airports wait for more guidance from the government on how reducing emission measures will work across the aviation and airport sectors, individual airports are committed to doing their part to reach their own net-zero targets.
The AAA will continue to focus on net-zero for its members, and having that goal front and centre while planning for the future.
The AAA’s support to airports is just beginning as the sector looks to transition to net-zero.
The AAA is hosting net-zero webinars and including this topic in upcoming conferences and events, to ensure all airports understand what is required to transition to renewable energy.
Aviation is critical to the continued success of Australia’s economy, supporting more than 200,000 jobs and prior to the pandemic contributed $35 billion – around two per cent – to the nation’s GDP.
Airports across Australia are used for more than travel. Major airports are international gateways to connect communities to essential services and maintain access to world markets.
Regional airports support exportoriented agribusiness, assist in medical evacuation and bushfire fighting operations and are gateways to world-renowned tourist destinations. Therefore reaching these emission targets on time will benefit the industry and the everyday people who use airports in the short and long term.
The AAA is the national voice for airports, representing the interests of more than 340 airports and aerodromes across Australia. It also represents over 150 corporate members supplying products and services to airports and the wider aviation industry.
Airports are an integral part of Australia’s transport infrastructure and contribute significantly to the country’s economy. As the aviation industry operates according to complex air traffic management systems, any infrastructure failure can lead to costly disruptions – this is why proactive remediation with reduced downtimes is especially effective for the sector.
Airport pavements are a huge investment. Profitability and operational efficiency are greatly impacted by pavement failure, which can cause damage to aircrafts and potentially result in catastrophic accidents. For customers, if an airport runway or taxiway is not fit for use, it can lead to delays and cancellations.
Airport pavement failure is often caused by underlying issues in the infrastructure. Not addressing these issues can result in further damage requiring more costly repairs.
Since 1995, Mainmark has been successfully delivering its Resin Injection products and methods to support and re-level subsided pavements and structures, as well as strengthening the subgrade soils often associated with pavement failures at airports. Mainmark
is the industry leader with its proprietary Teretek® Resin Injection solution.
Teretek® Resin Injection is a technology that has been qualified, tested, and adopted by infrastructure authorities across Australia. It offers a unique method for addressing bearing capacity issues and voiding common in aging infrastructure foundation systems while avoiding the significant operational disruption and high costs often associated with pavement removal and replacement.
Teretek® materials expand in a controlled manner, allowing its targeted placement to fill voids, reconfirm support, and raise subsided pavements with precision.
Mainmark has delivered effective airport pavement repair solutions with major airports across the Asia-Pacific region, including many of Australia’s commercial and defence airport facilities in our capital cities and across regional locations.
Mainmark’s Russell Deller, said, “Mainmark has been working with airports around the Asia Pacific region to implement lowimpact, non-invasive and sustainable solutions. Using our Resin Injection technology, these airports have been able to minimise operational downtimes and get back to business sooner.”
Teretek® is a particularly effective, non-invasive solution due to its unique material and mechanical properties.
Mainmark’s void filling, re-levelling and ground improvement solutions are completely machine pre-mixed before injection. The result is an inert material that is non-toxic, low-impact, noninvasive, has an indefinite lifespan and is environmentally sustainable.
Teretek® materials and processes have a low carbon footprint since expansive resins significantly reduce material consumption compared to alternative methods, substantially cutting down on production and transportation emissions.
“The materials used are lightweight and strong, resistant to water and have a high chemical resistance, meaning that once injected, they will retain their mechanical properties for many years.
“This makes them an ideal solution for repairing airport runways, taxiways, and structures without adding additional weight to the underlying soils,” Mr Deller said.
As a fast, non-disruptive, and economical solution, Mainmark’s Teretek® is particularly well suited to address the complex challenges of airport pavement repair, including:
♦ The filling of voids directly beneath pavements to reconfirm support and limit deflection and deterioration
♦ Raising subsided pavements to re-establish design levels and/or drainage gradients
♦ To provide targeted ground improvement to weak subgrade soils
Mr Deller said, “In almost every airport project we are contracted to, water is often a common denominator – whether via failed construction joint seals permitting surface water to access the subgrade, because of a failing service pipe causing washout voiding, or by excessive accumulation due to loss of surface drainage causing ponding/ icing issues.
“When water accumulates beneath a pavement, it can weaken the supporting soil or subgrade.
As a result, the pavement may start to deflect under load, sink or settle, which can lead to cracking and other significant types of failures.”
Mainmark’s efficient processes involve no demolition, excavation or heavy machinery and create no waste, helping repair Australia’s infrastructure without harming the environment.
Unlike traditional repair methods, Teretek® can be delivered in just a
few hours. The completed pavement sections are returned to full operation immediately after the repair work, and no curing time is required.
In addition to void filling & lifting, Teretek® can be utilised for targeted ground improvement to restore or improve bearing capacity to weak or failing subgrades. The primary improvement mechanism is densification of the soil due to aggressive expansion of the Teretek® product. Secondary effects such as improved composite stiffness, cementation, and horizontal stress increases are also present.
The expansion of the injected material results in compaction of the adjacent soils, due to the new material being introduced into a relatively constant soil volume.
This means the injection process can also strengthen the subgrade soils beneath the pavements, increasing its load-bearing capacity and restoring/ providing additional support. Injection of weakened or failing subgrade is often applied as an early intervention measure at the first signs of pavement failure, restoring or improving subgrade capacity to mitigate against further pavement deterioration that can lead to extensive demolition, excavation, and interruption to operations.
Mainmark works closely with client engineers to align design requirements to ensure achievable improvement targets.
The design is determined by the initial soil properties and the target outcome for the target structure. This influences the injection depths
and extent of improvement required – following the site application; the design is then validated using standard geophysical tests.
Mainmark offers a range of specialist ground engineering and asset preservation solutions for the residential, commercial, industrial, civil infrastructure and mining sectors.
Functional transportation infrastructure is a key component of a stable economy and plays an essential role in supporting communities’ well-being and economic growth.
Maintenance and replacement of aged infrastructure is crucial for public safety and is one of the largest draws on federal funding. Finding ways to increase the lifespan of existing infrastructure and avoid complex reconstruction is an effective way to reduce budget demands.
This is why finding proactive ways to increase the lifespan of existing infrastructure and avoid complex reconstruction through remediation is an effective way to reduce airport budget demands.
For more information visit https://mainmark.com/
The Commonwealth Games are coming to Victoria in 2026, with preparations underway to deliver the infrastructure required to host the grand sporting event. But while stadiums and accommodation are vital, the aviation sector is just as essential to ensuring interstate and international visitors can access the iconic event.
Australia has hosted the Commonwealth Games five times, with Victoria 2026 set to be the sixth time. Each time, the Games has attracted hundreds and thousands of visitors and injected millions of dollars into the Australian economy.
In 2018, the Commonwealth Games in Brisbane attracted almost 7,000 athletes and team officials from over 70 Commonwealth nations and territories.
1.5 billion people watched the Games worldwide, while over 100,000 visitors made their way to the Gold Coast to watch the Games in person.
Victoria last hosted the Games in Melbourne in 2006, with over 150,000 visitors and 8,000 athletes and team officials visiting the city.
The Games in 2026 are sure to bring just as many, or more, visitors and officials – which makes it a great opportunity to expand Victoria’s airports.
Through the adoption of a multi-city model, the 2026 Commonwealth Games are not being held in one city, but rather across different parts of Victoria, with regional cities and towns holding key events. There will be four regional hubs – Geelong, Bendigo, Ballarat and Gipplsand – to host athletes, officials and visitors, each with their own athlete villages and arenas.
The Games bring huge economic benefits for whichever city or state holds them. For example, in Melbourne, the Commonwealth Games contributed $1.6 billion and 13,600 jobs to the state.
To maximise these economic benefits, reliable transport systems that can handle a surge in overseas and interstate visitors need to be established, which means upgrading regional airports.
Most of Victoria’s regional airports are typically used for flight training, cargo handling, small passenger flights or private use. With the announcement of the Commonwealth Games, regional cities have made plans to include airport upgrades as part of their preparations for the event.
As Victoria’s largest regional city, Geelong will be an epicentre for the Games, as it will host seven events including the aquatics (swimming, para swimming and diving), beach volleyball, gymnastics, hockey, triathlon and para
triathlon, T20 cricket matches, table tennis and para table tennis.
The City of Greater Geelong is investing significantly in transportation, including aviation, to provide reliable and regular services for spectators.
Part of this investment includes building a new rail station at Avalon Airport and developing a 100ha commercial precinct. With almost a million passengers a year passing through the airport, these long-term upgrades will ensure Avalon Airport can meet the demands of the Games and the future.
Meanwhile, the City of Greater Bendigo has similar plans for the city’s
airport. Bendigo Airport is already set up for regular passenger services, including direct interstate flights, but the Games offer a chance to attract more people to fly through Bendigo to experience regional Victoria.
Bendigo will be hosting six sporting events, including lawn bowls and para lawn bowls, table tennis and para table tennis, netball and squash.
After receiving $9 million in funding from the Victorian Government since 2017, the City of Greater Bendigo has committed to upgrading its airport in time for the Commonwealth Games.
The upgrade will see a modernised terminal capable of handling more
domestic interstate flights. There are already flights from Bendigo to Sydney and other parts of the country, but a terminal with new facilities and technology will allow for more passengers to pass through the airport.
But for smaller airports, upgrades will not just be about meeting the increasing demands during the Games, but about preparing airports to provide extra services long after the athletes have left Victoria.
At Ballarat Airport, early works have begun to extend the runway from 1.3km to 1.8km, which will accommodate
more flights for the regional airport. These works are being jointly funded by the City of Ballarat and the Federal Government as part of the Regional Airports Program.
The City of Ballarat has advocated for this extension for years, and with the Commonwealth Games around the corner, now is the best time. This extension is part of a larger three-stage upgrade, outlined in the Ballarat Airport Masterplan 2013-33, which aims to stimulate economic growth in the region and improve aviation transport connections.
The upgrade will mean that more business, emergency and passenger
services can come through the airport. Further works include shifting primary airport access, strengthening the runway to provide capacity for larger aircraft, building a new taxiway and upgrading the terminal.
The masterplan states that most of the region’s aviation growth will be driven by increasing demand for regular passenger transport. With priorities focusing around boosting commercial aviation and tourism, the Commonwealth Games presents a great opportunity to extend and modernise the airport.
As Ballarat is set to host athletics and para athletics, boxing and T20 cricket events during the Games, the airport will see direct domestic passenger flights for athletes and visitors, bringing much needed economic growth for the area.
City of Ballarat Mayor, Des Hudson, said the upgrades will offer existing businesses new opportunities while also attracting new aviation opportunities.
“The Ballarat Airport has a strong history as a facility that has adapted to the needs of the community over the years, having been originally constructed in 1940 as a training base for the Royal Australian Air Force Base at the outset of the Second World War,” Mayor Hudson said.
“The Ballarat Airport is a significant aviation facility servicing Western Victoria which will be enhanced to support diversified aviation growth and provide benefits for the community and economy.
“The extension of the runway is the first stage upgrade which will ultimately allow for larger commercial freight aircraft, large firefighting and emergency services aircraft and increase opportunities to attract new aviation businesses to the airport.”
With a few years before the Games arrive in Victoria, it’s clear regional cities see this worldwide event as an opportunity for the aviation sector. The Games present an opportunity to showcase regional Victoria to international visitors, which will be supported through these airport upgrades.
While these spectators will only stay for a few weeks while the Games are on, these upgrades will ensure Victoria’s regional airports can adapt to support Australia’s growing aviation sector, population and tourism industry.
Due to the rigorous nature of construction projects, work clothes and personal protective equipment (PPE) experience plenty of wear and tear and are often sent to landfill once considered unwearable. However, initiatives such as the recent partnership between Major Road Projects Victoria (MRPV), Seymour Whyte and UPPAREL are enabling these assets to be recycled, creating new possibilities for discarded materials.
Waste is a significant issue facing Australia, with the construction sector one of the largest wastegenerating industries in the country. As the number of infrastructure projects continues to rise, recycling work clothes and equipment is one way the industry can improve circularity and promote sustainable waste management.
MRPV’s Pound Road West Upgrade team has joined forces with Victorian company UPPAREL to recycle used work clothes and PPE that would normally end up in landfill.
Through a partnership between MRPV, its construction partner Seymour Whyte and UPPAREL, project workers are encouraged to hand in workwear and PPE they no longer use so UPPAREL can repurpose 100 per cent of the recoverable materials, with nothing sent to landfill.
Major Road Projects Victoria Program Director, Marc Peterson, said, “We’re excited to team up with UPPAREL on an initiative where every member of the project team can play their part to reduce waste in the construction industry, while supporting local business.”
The MRPV recycling initiative builds on the Victorian Government’s ecologiQ program, which is integrating recycled and reused content across Victoria’s $100 billion Big Build initiative and making the use of the green materials standard practice.
One driving force behind this change is the Victorian Government’s Recycled First Policy, which came into effect in March 2020. Under the policy, all tenderers on Victorian major transport projects are required to demonstrate,
within their bid, how they will optimise the use of recycled and reused materials at the levels allowed under current standards and specifications.
The Recycled First Policy allows for continuous improvements to transport standards, specifications, research and development, helps create new markets and develop greener, more sustainable transport infrastructure outcomes.
Supported by ecologiQ, the policy has had a powerful impact resulting in commitments to use more than 3.3 million tonnes of recycled and reused
materials, which is more than enough to fill the MCG. Over 2.4 million tonnes are already incorporated into Victorian transport infrastructure construction.
This includes:
♦ 6,400t of recycled plastic –equivalent to more than a billion plastic bags
♦ 86,026t of waste glass – equivalent to 13 million house bricks
♦ 267t of crumb rubber – equivalent to more than 28,000 passenger car tyres
UPPAREL is the only direct-toconsumer and commercial textile recovery and recycling company operating in Australia and New Zealand. As a Certified B Corporation, the company is recognised as a leader in the global movement for an inclusive, equitable and regenerative economy.
UPPAREL CEO and Co-Founder Michael Elias, said, “At UPPAREL, we believe making a positive environmental impact is key to a sustainable future. Local partnerships such as this not only make a measurable impact but continue to raise awareness around the global issue.”
From its Braeside-based headquarters in Melbourne’s southeast, UPPAREL has diverted a total of nearly seven million items from landfill.
UPPAREL uses a non-chemical process which converts end-of-life textiles
into sustainable materials that can be repurposed into new commercial products. These recycled materials can also replace non-sustainable materials such as polystyrene, fibreglass and cellulose that have traditionally been used in the manufacture of some consumer products.
Through UPPAREL, unwearable work clothing is able to be recycled into fibre that is used in a vast range of construction materials such as wall and ceiling insulation, furniture filling, flooring underlay, acoustic panels, suspended ceiling tiles and office partition walls. It can also be used in cushion filling, pet beds and protective packaging for products such as crockery and glassware.
Recycled PPE such as hardhats, safety glasses and boots are being repurposed into gym flooring, outdoor playground flooring and rubber mats.
Any work clothing and PPE that is still in good condition is offered to UPPAREL’s charity and not-for-profit partners for reuse.
The Pound Road West Upgrade team has responded very positively to the initiative, with a strong participation rate among workers and contractors. The items most commonly handed in have been hi-vis work shirts.
For workers and contractors, handing in their used work clothes and PPE has
been a simple process. At the project’s site office, two boxes have been set up in the crew sheds every day, one for work clothing and the other for boots, hard hats, glasses and gloves. Once the boxes are full, they are freighted to UPPAREL’s Braeside headquarters.
The Pound Road West Upgrade project team has already handed nearly 500 items of work clothing and PPE to UPPAREL, resulting in a total of 80kg of materials being diverted from landfill and preventing the creation of 280kg of carbon dioxide.
Seymour Whyte Southern Region General Manager, Courtney Hoops, said, “Sustainability is a strategic priority for Seymour Whyte and adopting a circular economy approach to workwear is ‘smart business’ that’s good for the planet and promotes a social-responsibility-centred partnership – creating a sustainable future for all.”
Two other Victorian Big Build projects have also recently partnered with UPPAREL to recycle their used work clothes and PPE – the West Gate Tunnel Project and the Level Crossing Removal Project for the upgrade of the Frankston and Hurstbridge lines.
While these initiatives alone won’t solve Australia’s infrastructure waste issue, adopting sustainable waste management solutions can help promote circularity in the industry and leave behind a more positive impact on the environment.
As many in the infrastructure industry seek ways to reduce their carbon footprint, cut emissions and champion sustainability, recycled products are emerging – providing a circular economy solution for construction site safety.
Cacti Conserve’s recycled products are sustainable consumables, and include Eco Traffic Flags, Eco Barrier Tape and Eco Safety Bunting. These Eco Site Safety products meet the needs of trade contractors and builders that work on large government and commercial projects – where social procurement and recycled materials targets are mandated.
The company’s Eco Site Safety products are made from 100 per cent ocean harvested plastic and recycled post-consumer and industry plastic waste.
Alongside this, Cacti Conserve is also committed to making a wider impact to the community and building a circular economy.
To do this, the company donates 50 per cent of profits to conservation projects and supports training and meaningful employment for disadvantaged communities.
Cacti Conserve Founder and Managing Director, Jackson Ellis, said, “We’re deeply committed to helping construction companies minimise their waste footprint.”
Mr Ellis explained that sustainability has become, and will continue to, be a major selling point and way to secure industry tenders.
“Expectations are that single use plastics shall become a thing of the past eventually, and that project waste reduction planning and reporting, and the use of sustainable site consumables, shall be key to winning tenders in the construction sector,” Mr Ellis said.
Mr Ellis said that placing high priority on the implementation of site safety measures is already a given in the industry, and Cacti Conserve has combined all of these concepts to deliver site safety solutions using recycled and recyclable materials.
“Our products are Australianmade, we can customise styles and printing on our product lines, and we’ve partnered with Social Enterprise groups to ensure that we are giving back to the community, the environment and to all stakeholders involved,” Mr Ellis said.
As the first true diagonal arch bridge to be designed and constructed in Australia, the Alfred Street Bridge has been a complex undertaking for the City of Parramatta. But once complete, this new urban gateway will provide a convenient, safe and scenic walking and cycling link over the Parramatta River, connecting locals directly to the Parramatta Light Rail.
As the bustling suburb of Parramatta grows, so does its infrastructure – with the Alfred Street Bridge showcasing a focus on active transport and innovative engineering.
The Alfred Street Bridge is located over the Parramatta River between James Ruse Drive and Gasworks Bridge, with the 4.5m-wide, 200m-long active transport link in its final stages of construction – as bridge ramps and decks were installed in late March 2023.
A true diagonal arch bridge is designed so the arches are arranged diagonally in relation to the bridge’s horizontal axis.
The $19 million project has been funded by the City of Parramatta Council and the New South Wales Government – which has provided a $11.5 million funding contribution through grants from Transport for New South Wales and the Department of Planning and Environment.
City of Parramatta Lord Mayor, Cr Sameer Pandey, said, “Alfred Street Bridge will be a great new landmark that will benefit so many people as they travel through Parramatta.
“The bridge acts as a river gateway to our city, creating better active transport links. We live in a beautiful city and we want to make it easier for people to walk, run, cycle, skate or wheel across the LGA and connect to public transport.
“For those who live north of the Parramatta River, this bridge will cut the trip into the CBD by up to 20 minutes,”
Mayor Pandey said.
A spokesperson for Council said the project would provide many benefits for the growing Parramatta community, creating an essential connection to open green space, the future light rail stop, restaurants, urban services and would create easy access to the Parramatta River.
“The bridge will connect our community to the great outdoors and allow users to explore more than 20km of offroad paths along the Parramatta River. It also establishes two new recreational loops based on the two bridges either side of Alfred Street,” the spokesperson said.
The project is a key element within a network of planned pedestrian and cyclist networks centred on the Parramatta River and Alfred Street. Council has worked in collaboration with the New South Wales Government to plan and deliver this network, which is expected to be completed within 12 months.
As an important gateway in and out of the Parramatta CBD, the Alfred Street Bridge design has had to meet high expectations.
“The design team for the bridge was selected in the tender not just on their experience, but through demonstrating how the architectural and engineering teams would work together to deliver an exceptional result,” the spokesperson said.
“The design team was challenged by Council to prepare a number of simple yet elegant solutions for the review of an expert Design Review Panel. Ultimately, the diagonal arch was recommended by the Panel as not only the most appropriate response to the setting, but it also meant people travelling on the river over the bridge would pass ‘through’ the arch.”
The spokesperson also explained that strong coordination between Council, the New South Wales Government and local stakeholders – throughout the design and construction phases – has been key to the success of this project.
Council's State Government partners will also be involved in the official launch scheduled for July 2023.
“The bridge was very complex to design and deliver. The design was tested to withstand both high-velocity winds and floodwaters,” the spokesperson said.
Off-site in Western Sydney more than 30 workers fabricated the deck and arch using 280t of Australian BlueScope steel, with transporting these assets to the site proving to be a challenge.
“Each was fabricated in three pieces, then trucked from Western Sydney to the site on oversized prime movers in the night. The deck pieces, then the arch, were assembled on site and each lifted into position using a 750t crane. The steel cables that support the deck had to be manufactured in Italy. A specialist team flew in to oversee the installation,” the spokesperson said.
The final piece of the puzzle will be positioning the steel cables that support the deck from the arch.
“There has been growing enthusiasm especially as we get closer to the public opening,” the spokesperson said.
“Residents in nearby apartments have been eagerly watching the bridge being built. We have a lot of cyclists, riding groups, and keen pedestrians who are very excited about the opening during winter this year.”
The project has been trending on social media, with members of the community expressing enthusiasm and curiosity about the bridge, as well as sharing pictures as it progresses.
“Our community is excited about the progress of the Alfred Street Bridge, affectionately known as “Alfie” for now,” Mayor Pandey said.
Long-time Parramatta resident, Greg Temme, has lived in the area since 1985. He has been watching the bridge come to life from his apartment window, and said the Alfred Street Bridge will cut down his travel times by up to 20 minutes.
“We’re really looking forward to the opening of the Alfred Street Bridge. It will be a life-changing addition for us, it’s going to make it so much quicker to visit the town centre and the local shops,” Mr Temme said.
“We’ll be able to cross the bridge and connect to the future Parramatta Light Rail stop at Tramway Avenue where we can travel straight to Western Sydney University, Westmead Hospital, Eat Street and Parramatta CBD.”
The bridge is in its final stages with civil works and landscaping underway. In addition to the works, a new urban plaza on the southern approach to the bridge is being established.
The Alfred Street Bridge is expected to open in the coming months.
Once formally opened, the City of Parramatta will work with the community on naming the bridge. A proposed name will then be submitted to the Geographical Names Board of New South Wales for formal exhibition and determination.
Mayor Pandey said, “Now that the arch has been lifted into place, landscaping and civil works are underway. Our $19 million Alfred Street bridge will make it safer and faster to move in and out of the Parramatta CBD.”
Ask any geotechnical engineer and they will agree – understanding conditions below ground is key to reducing risk above it. But unlike other engineering disciplines, their challenge is finding solutions across the natural variability of soil and rock.
“Abetter understanding of the subsurface to help identify geological complexities is crucial to building more resilient infrastructure,” Paul Grunau, Senior Vice President of Geotechnical Solutions at Seequent, said.
With over 30 years of software expertise, Mr Grunau has led Seequent’s geotechnical analysis team for the last four years, focussed on connecting digital innovation with industry needs.
Seequent software enables teams to ‘see’ the subsurface to avoid major risks and support robust decision-making across infrastructure, tunnels, slope stability, embankments, deep excavations and more.
“The importance of having a connected workflow to help ensure geotechnical engineering success cannot be overstated,” Mr Grunau said.
“With our innovative 3D modelling technology, you can combine all geotechnical information into connected, auditable workflows and easily collaborate across your teams, contractors and projects.”
Large-scale projects such as buildings, tunnels, bridges and dams are exposed to a multitude of complex subsurface conditions.
“And we see common industry challenges,” Mr Grunau said.
“Often workflows are siloed – geologists work with their own data, geotechnical engineers have their own design, and project engineers simply have a copy of all the data produced.
“For geotechnical engineers to create accurate designs, detailed, dynamic updates on areas of geological uncertainty that require additional information are a must.”
Having the latest 3D geological models at your fingertips means teams can share insights and collaborate on the most up-to-date understanding of the subsurface.
“Helping to minimise errors, optimise efficiency in the design and construction process, make better-informed decisions and more quickly progress a project,” Mr Grunau said.
Seequent is The Bentley Subsurface Company, with Seequent’s expertise in examining the subsurface complementary to Bentley’s infrastructure engineering software prowess.
“Together we intersect the worlds of built asset certainty above ground with the art of understanding the complexities below it,” Mr Grunau said.
With GeoStudio, PLAXIS and OpenGround, Seequent offers the world’s most extensive suite of geotechnical analysis and information management solutions.
PLAXIS enables you to design and perform advanced finite element analysis of soil and rock deformation with OpenGround offering a secure, cloud-based geotechnical information management platform.
GeoStudio is an integrated software suite for slope stability, groundwater flow, and environmental challenges. It includes the recent release of SLOPE3D, an advanced slope stability analysis tool to improve safety and reduce project risks and costs.
SLOPE3D capabilities help navigate complex geology, topography and groundwater conditions to improve the safety of construction by increasing understanding of a slope’s potential fail points.
“Geotechnical engineers can also access stronger and more connected digital workflows with other Seequent subsurface solutions such as Leapfrog Works for geological modelling and Seequent Central, for model management and collaboration,” Mr Grunau said.
“And bringing a much more comprehensive understanding of subsurface conditions to help design and build safer, more sustainable, longer-lasting infrastructure.”
Bring together the power of Seequent’s connected geotechnical workflow to ensure the safety and sustainability of your next infrastructure project, to find out more go to https://www.seequent.com/civil
When you collaborate around a shared understanding of ground conditions, you can deliver projects faster with more certainty and achieve a better outcome.
Geotechnical Engineers, Engineering Geologists, and Geophysicists use our software on infrastructure projects to plan, design, and construct roads, rail, bridges, tunnels, buildings, dams and levees.
See how civil engineering projects are succeeding with our software worldwide.
Acareer in Australia’s construction industry offers many great things – including a chance to be a part of delivering our nations’ future infrastructure.
I’ve spent my entire life around our industry – as a child watching my dad go off to work, as a construction lawyer when I first started my career, and now as a Director at Laing O’Rourke and President of the Australian Constructors Association (ACA).
AN INDUSTRY STUCK IN TIME
I am passionate about this great industry, and while some change has occurred the reality is that construction productivity is lower today than it was in 1990. We have gone backwards.
The pressure I remember seeing my dad deal with was immense – burnout and fatigue were commonplace – and this continues to be an issue for our people today.
Whilst other industries have evolved to compete on innovation and adopting advancements in technology, we are still building roads largely like the Romans did.
Despite an increasing number of studies espousing the benefits of a four-day week, we are still trialling the possibility of a five-day week.
As more and more Australians realise the value of a work-life balance, our industry is facing a challenge in attracting a new generation of workers. The next generation is telling us they don’t want to work long, inflexible hours in an ‘old school’ industry that values presenteeism, focuses on cost and is struggling to reduce its impact on the environment.
The clock is ticking, and the stakes have never been higher. Equally, the opportunity has never been more exciting.
We can offer people from all walks of life a rewarding career, where they are challenged to solve complex problems and leave a legacy that serves local communities for generations.
To make our offering compelling, we must make changes now to ensure a career in our industry doesn’t come in the way of a social life or watching the kids play sport on the weekend.
The construction industry accounts for 26 per cent of all insolvencies in Australia – so we must make changes now to ensure a fair return on a project is celebrated.
Together we can refuse to be a part of the problem any longer and instead be the solution. As President of the association representing the nation’s largest contractors, I know there is so much we could do and that is why I was immensely proud when all of the members of the ACA took a stand at our Future of Construction Summit and pledged to transform the culture of the industry.
Setting ambitious goals for gender equality and workplace flexibility, the nation’s major contractors have committed to 75 per cent of the Association’s membership being certified an Employer of Choice by the Workplace Gender Equality Agency (WGEA) within five years.
As the most male-dominated industry in Australia and with the widest pay gap of any (29 per cent compared to Australia’s overall 22.8 per cent as cited in WGEA’s Australia’s Gender Equality Scorecard December 2022 report), this is an ambitious target that will promote gender equality, greater diversity and inclusion.
Workforce analysis of WGEA Employers of Choice revealed that
Australian employers awarded WGEA status are closing the gender pay gaps faster and successfully implementing work environments that support more equal sharing of caring responsibilities at home. This proves that a commitment to change is getting results.
At Laing O’Rourke, we were the first tier 1 constructor to receive a WGEA Employer of Choice citation in 2020, and since then I have witnessed firsthand the deliberate and accelerated behavioural changes it has driven across our organisation and at all levels.
The rigorous criteria to meet and maintain the citation have supercharged our efforts across all parts of our business.
As a result, we have increased overall female participation from 26 per cent to 35 per cent and increased the number of women in senior leadership roles on projects from 11 per cent to 19 per cent, meaning now, if you work on a Laing O’Rourke project, there is double the chance you are reporting to a female manager.
We have also increased our already industry-leading parental leave policy, introduced processes to ensure pay parity across the business and agreed to pay superannuation on both paid and unpaid parental leave.
I have no doubt we would have eventually achieved all of this without the WGEA citation, but it places an urgency on gender equality that is undeniable in its effectiveness.
To further raise the bar industrywide, the second target area is workplace flexibility. Our members will mandate flexible work plans for employees on every project in a move to address the long hours, high stress and poor work-life balance that characterises the industry.
With major workforce shortages right now, the pledge includes a commitment to highlight the many positive aspects of the industry, in order to attract more workers to join from other sectors. Construction is a varied and exciting industry that solves complex challenges every day and provides opportunities for people with a range of skills.
By aligning these opportunities with a culture of collaboration, innovation, flexibility and inclusiveness, the Australian construction industry can truly become the envy of the world.
The City of Greater Geelong has partnered with ENE.HUB – part of digital infrastructure provider Indara – to deliver a range of digital infrastructure projects across the city to improve community connectivity, enhance safety and improve environmental management.
ENE.HUB has installed a network of its SMART.NODEs™ across the Greater Geelong region and will continue to manage and maintain the network as part of a 20year Digital Infrastructure Agreement.
The SMART.NODE™ is the world’s most advanced street light alternative, ready to accommodate a full suite of digital services and features.
The product offers a range of essential and activated digital services such as public Wi-Fi, intelligent lighting, IoT gateways, and CCTV – enhancing connectivity, security and convenience for users.
The City, in partnership with AARNet, delivered 22km of new high-speed optical fibre, which provided critical backbone infrastructure for a network of 54 SMART.NODEs™.
The Geelong community will be benefiting from increased connectivity and safety in multiple precincts such as the Geelong Arts Centre, Kardinia Park, the iconic Waterfront and the North Bellarine Aquatic Centre.
This work was undertaken as part of the City-led Smarter Suburbs Program, which is enabling connectivity from the city centre to the northern suburbs of Greater Geelong and has been delivered in collaboration with the Victorian
Government through the Connecting Regional Communities Program.
ABOUT THE SMART.NODE™
Featuring a sleek, integrated design, the SMART.NODE™ can be fully customised around the needs of local councils and land authorities for applications related to communications, energy, safety, transport, environmental monitoring, infrastructure and more.
It is designed in Australia and manufactured to evolve with a place and community over time. Whether it be urban renewal projects, place making investments or changing mobility arrangements, the digital services offered via the SMART.NODE™ are innovative and ample.
New services, upgrades to existing services and ongoing maintenance can be managed through ENE.HUB’s partnership approach and commercial model that is characterised by coinvestment, shared benefit and ongoing value creation.
To complement the digital services offered by the SMART.NODE™ ENE. HUB has a IOT data and analytics platform called ‘e3’, which has been built from the ground-up to help city authorities monitor and control their digital services.
The platform is also designed to seamlessly integrate legacy systems, and it allows for real-time visualisation of data and sophisticated data analysis.
ABOUT ENE.HUB (PART OF THE INDARA GROUP)
ENE.HUB enables urban digital connectivity by activating and measuring engagement in public places and spaces through the design, manufacture and deployment of smart poles and smart street furniture.
Indara recently completed the acquisition of ENE.HUB, a world leading company that designs, manufactures, and manages digital infrastructure, services, and data analytics to help create the best public places.
Indara, ENE.HUB’s parent company, is Australia’s leading owner and operator of telecommunication sites, providing a network of critical infrastructure to meet Australia’s digital needs now and into the future.
Indara has a portfolio of over 4,300 tower and rooftops sites, as well as several hundred new sites under construction.
• Gun
• Fire rated, fuel resistant, chemical resistant and biodegradation resistant sealants
• Pouring grade sealants – designed exclusively for horizontal joints in floors and pavements Fosroc. Future Proof.
Australian businesses and critical infrastructure operators continue to face a deteriorating risk environment – from cyberattacks and ransomware, to fire and flood, malicious insiders and malign foreign powers – there’s no shortage of risks that need to be thought about and managed in the modern era.
To some critical infrastructure sectors this comes as no surprise – managing risk has been part of the parcel of doing business for many years. But for others, thinking about the full range of hazards modern critical infrastructure faces, and planning reasonable, practicable mitigations across the realms of cyber, physical, personnel, and supply chain security, is relatively new.
To assist owners and operators conceptualise risk across these dominions – and to empower them to take action that will lower risk to the ongoing operation of their systems, assets, and businesses – the Critical Infrastructure Risk Management Program (CIRMP) requirement is now live.
The CIRMP is the third and final of the three positive security obligations legislated within recent amendments to the Security of Critical Infrastructure Act 2018 – the other two being
Mandatory Cyber Incident Reporting, and the Critical Infrastructure Asset Register requirement.
Working together, these obligations uplift Australia’s critical infrastructure security and resilience, further protecting the essential services all Australians rely on.
The Minister for Home Affairs, Clare O’Neil, ‘switched on’ the CIRMP rules on 17 February 2023, following an extended period of consultation. Through this consultation process, the Minister was able to incorporate feedback from critical infrastructure stakeholders that has ultimately made the rules simpler and easier to implement.
Now the rules are in effect, responsible entities for critical infrastructure assets are required to adopt, maintain and comply with a risk management program that identifies and manages material risks of hazards that could have a relevant impact on a critical infrastructure asset.
The plan must identify each hazard where there is a material risk that the occurrence of that hazard could have a relevant impact on the asset, and – as far as it is reasonably practicable to do so –must minimise or eliminate any material risk of such a hazard occurring.
Through the implementation of agnostic rules, the Cyber and Infrastructure Security Centre (CISC) –within the Department of Home Affairs – hopes to create a baseline for security across all critical infrastructure sectors in the Australian economy.
While many organisations will no doubt already exceed the thresholds set out in the rules, the CISC hopes that the Risk Management Program (RMP) rules will uplift all critical infrastructure entities, right through supply chains.
In that vein, the CISC envisions the rule benefiting not just the responsible entity, but both its upstream and downstream suppliers; ensuring that an awareness of security standards becomes the norm for many Australian businesses.
The inclusion of a requirement for a board or governing body to sign an attestation regarding the RMP lifts the issue of risk management and security from an operational level to the board level.
By ensuring that directors of companies have these issues at the front of their minds as they make strategic decisions, the CISC aims to ensure a stronger effort to protect critical infrastructure at all levels.
This issue particularly goes to the requirement for responsible entities to consider supply chain hazards –especially since many have now seen the significant disruptions in the supply chain caused by the COVID-19 pandemic.
By requiring directors and board level decision makers of a responsible entity to be thinking about how best to mitigate possible hazards to their supply chain, the CISC hopes to see more industries consider not just cost,
but also security and reliability of supply chains going into the future.
While pursuing sensible regulation, the CISC’s approach is not intended to increase the burden on owners and operators, nor to duplicate other mechanisms. For example, where a requirement for an RMP already exists under other legislation, dual reporting won’t be enforced.
Similarly, nothing in the rules overrides any existing provisions within the Privacy Act 1988, the Australian Privacy Principles, or the Fair Work Act 2009, and nor do the Rules absolve employers of any other obligations, including relevant occupational health and safety legislation.
The Secretary of the Department of Home Affairs, Michael Pezzullo AO, also has the power to review a responsible entity’s plan to ensure actions are being taken appropriately.
This ensures the CIRMP sits alongside other important and relevant legislated requirements – it doesn’t overrule, duplicate, or impinge upon them.
Now the Rules are live, there is a sixmonth transition period for responsible entities to adopt a written CIRMP. If a responsible entity’s asset becomes a CI asset after the Rules commence, the responsible entity must meet CIRMP requirements within six months of the day the asset became a CI asset.
The CISC is committed to working in partnership with all levels of government and industry to support the wider security uplift of Australian critical infrastructure, and for some critical infrastructure entities, it recognises that implementation of a CIRMP will be an extensive task.
Wherever a business is in terms of maturity, the CISC will assist whenever possible.
Together, sensible government regulation and attentive owners and operators can secure Australia’s critical infrastructure, and in the process safeguard shared security and prosperity.
In this day and age, smart city initiatives are everywhere; but despite this technology becoming more and more commonplace, a recent questionnaire from the University of South Australia found that over half of South Australian residents don’t understand what a ‘smart city’ is, with similar results found in the UK. However, real-world results are beginning to emerge from smart city initiatives – such as Melbourne’s iconic tram network trialling innovative new technology –bringing the technology to the public eye.
Until recently, city leaders thought of smart technologies primarily as tools for becoming more efficient behind the scenes, with a lot of the smart city activity happening in the background.
As a result, a resident of a smart city, or a city implementing smart technologies, likely hasn’t seen the layers of technology and digital infrastructure contributing to their day.
Smart technologies, like IIoT devices, are enabling predictive maintenance of city infrastructure and the collection of real-time data from infrastructure systems including transportation, energy, and water management. This process optimises city-wide operations and creates a higher quality of life for citizens.
In Australia, one example of smart city technology benefiting citizens is Melbourne’s Yarra Trams, operated by Keolis Downer. Yarra Trams has recently partnered with Madison Technologies to leverage IIoT solutions to create efficiencies in the way they manage the rail network, including tram safety and speeds.
Across the Yarra Trams network, junction pits fill with water and debris, which requires a labour-intensive process to conduct routine maintenance. Yarra Trams required a solution that can detect water and solids that have built-up in junction pits, creating more efficient maintenance programs.
Secondly, during extreme weather events that bring high temperatures, the 40km of ballasted tracks managed by Yarra Trams are susceptible to buckling and need careful monitoring.
Before a visual inspection can be completed, tram speed restrictions must be implemented to keep commuters safe, which can lead to operational delays.
For the initial pilot program, Madison Technologies provided two solutions for Yarra Trams, leveraging IIoT technologies from Australian manufacturer, Kallipr. The first, a junction pit monitoring solution, provides up-to-date data on the levels of water in the junction pit. If a pit is full of water and not draining, alerts are sent, and maintenance teams can react quickly to clear it.
The second solution carefully tracks temperatures across sections of the track that are susceptible to buckling. Sensors monitoring the ambient air and rail temperature provide frequent data points back to the Yarra Trams Operations Centre, allowing for informed decision making when applying network speed limits, and reducing the reliance on visual inspection.
Both solutions use low-cost, low-power devices to enable remote monitoring and measurement, leveraging Telstra’s M2M NBIoT / CatM1 network to send small packets of low-cost data, making the overall solution incredibly cost effective.
The pilot program gives the team a chance to learn more about the technology and its possible uses, while lowering the risks connected with introducing a new technology. Yarra Trams can apply learnings and easily scale the technology across the network once perfected.
As cities become smarter, they become more liveable and responsive, with Australia only seeing a preview of what technology could eventually do in the urban environment. Smart city technologies have the potential to create a more efficient, sustainable, and equitable future for all city residents.
Learn more about this topic with Madison Technologies
If you need help building, optimising or scaling Industrial IoT solutions, we recommend booking a discovery session with our technical team, where you can take a deeper dive into the unique challenges of your operations. We’ll listen to your requirements and recommend a solution that fits your needs. Visit www.madison.tech or phone 1800 72 79 79 for more information.
Unlocking future potential with digital transformation
Connect and protect people, assets and the environment
With a 30-year legacy of providing resilient industrial technology solutions, our experience connecting and protecting people, assets and the environment means we’re the preferred partner for solving IIoT, industrial networking, cybersecurity, asset management and asset visibility challenges.
Find out more.
To prevent issues down the track, city managers and asset owners can take a proactive approach to their infrastructure projects by building a comprehensive utility map of the entire city – that can be used across a range of infrastructure projects to reduce utility strikes and improve cost and delivery timeframes.
Most local councils and construction teams have very poor visibility into the state of their subsurface infrastructure. Network and utility owners are reluctant to share accurate, upto-date data on their subsurface assets, and unlike the aboveground environment, information on the subsurface is difficult to procure and analyse without specialist utility surveying.
Inaccurate information about the subsurface is linked to project cost overruns and timeframe blowouts internationally. In New Zealand, a recent cycleway project lost 194 working days due to the discovery of buried subsurface utilities, including power, gas and telecommunications lines that were previously undocumented. Closer to home, a post-mortem report on the Sydney Light Rail scheme found the project could have been built 1.5 years quicker if the team had reliable underground utility information.
A major transport and urban rejuvenation project in Wellington, New Zealand, is taking a new approach to the problem.
Reveal was commissioned to proactively map the underground of the CBD and combine the resulting rich information into a utility asset model that could be shared with all the project stakeholders across a range of planning, design and construction functions.
Australian asset owners risk wasting millions of dollars and delaying critical infrastructure projects if they fail to collect subsurface utility information early in project design phases.
This proactive mapping effort has already delivered positive results, as Reveal was able to find several voids below the road surface of Jervois Quay that posed a danger to road traffic as well as critical infrastructure.
Engineers were able to quickly respond and repair the damage, while minimising the impact on the community and businesses.
works,
In a global survey of infrastructure projects by Geo. the availability of subsurface information produced unprecedented cost and time savings including bid reductions of 10 per cent, schedule reductions of 30 per cent, and labour reductions of 50 per cent, along with zero delays, damages, or change orders.
Geo.works stated that, “Based on a proof-of-concept trial in London conducted by Les Guest Associates, it was estimated that construction costs could be reduced by 10-25 per cent if the location of all underground infrastructure and subsurface conditions were known in advance of construction.”
With the price tag on major infrastructure projects running to the hundreds of millions of dollars, it’s clear that accurate subsurface information can be a massive cost saver, and reduce project times.
Cities have been tasked with major infrastructure upgrades to adapt to climate change, reduce carbon emissions and deal with urban intensification over the coming decades.
Proactive subsurface risk management can yield massive savings if undertaken early in the process, and can help deliver savings to ratepayers, reduce the impact on citizens, and deliver prosperous, sustainable development outcomes.
Despite decades of attention and countless safety campaigns, the number of injuries and fatalities on construction worksites remains unacceptably high; however wearable technology could change that.
One death on a construction site is one too many. But SafeWork Australia’s interactive data dashboard tells us that 647 people have died while at work in construction since 2003.
Many injuries on site can be traced back to fatigue.
Construction workers spend long hours on site. The Culture in Construction Taskforce says 50-plus hours a week is the norm for 64 per cent of workers.
Fatigue and burnout is a common problem in all industries. One large-scale study from the US National Safety Council found that 69 per cent of employees – many of whom work in safety-critical industries – are tired at work.
Construction is a physically demanding, high stress job with tight deadlines and a shrinking pool of workers willing to take on the task. Burnout may escalate to health and safety issues in the sector.
Record infrastructure investment has led to serious skills shortfalls across most job roles. Labour shortages – the Culture in Construction Taskforce consultation paper A Culture Standard for the Construction Industry has noted – are “notorious for causing other adverse impacts on mental health and increased safety risk due to increased need for overtime and worker fatigue”.
Traditionally, we’ve relied on the unreliable: self-reporting. But fatigue can creep up gradually, and construction workers can be so focused on completing their tasks that they ignore the physical and mental warning signs until it is too late.
SafeWork Australia says more than 15,500 serious safety incidents occurred on building and infrastructure sites in 2021. Analysis of the perceived causes of work-related injury on these construction sites is instructive. Two of the most frequently cited reasons for an accident were workers “being careless” or “just not thinking” – both classic symptoms of fatigue.
Deakin University established the Workforce Safety and Performance Research and Innovation group to investigate ways to minimise worker fatalities and optimise performance. The multidisciplinary group brings together four schools (Architecture and Built Environment; Information Technology; Psychology; and Engineering) to test new technologies like wearable sensors, computer vision, drones and robotics.
A wearable sensor-based system can help us obtain an objective indicator of fatigue by measuring physical signs, like heart and respiratory rate.
The group conducted its first trial of wearable sensing technology during the peak of the COVID-19 pandemic. The trial was backed by construction unions and insurance company Incolink, and assessed alternatives to temperature checks.
It collected data from 26 workers at two sites in Victoria. Four wearable devices – a vest, earpiece, underarm sensor and ring – were connected to a real-time monitoring system. This triggered an immediate ‘red zone’ alert if an elevated temperature was detected, reducing the spread of COVID-19 and potentially preventing hundreds of workers from getting sick.
The trial found all four devices were more accurate and efficient than traditional temperature screening at site entries, and avoided long testing queues. It also laid the foundation for a long-term investigation on management of fatigue.
Of the four wearable devices, the ring and vest were rated ‘comfortable’ or ‘very comfortable’ by 95 per cent of participants. This technology could also monitor people in high-risk jobs, like crane operators, using these devices and set up alerts that allow site managers to take appropriate action before serious accidents occur.
The university is currently pursuing industry partnerships for phase two of the trial, which will expand the fatigue monitoring. The group is also refining the machine learning model for physical and mental fatigue measurement.
The Culture in Construction Taskforce is championing a Culture Standard that includes a 50-hour cap on the working week. Real-time monitoring of fatigue will build the evidence base to help companies think differently about people management and make more informed decisions about rostering, schedules and contracts.
Wearables are still at the experimental phase in construction – but the cost of doing nothing is clear. Deloitte puts the productivity cost of fatigue at almost $18 billion a year.
The benefits go far beyond the financial. By prioritising the wellbeing of workers, the construction industry can attract and retain the best talent, and ensure everyone returns home from their shift, every day.
To find out more about Deakin University's wearables sensing trial and how your company can get involved, contact Associate Professor Farnad Nasirzadeh from the School of Architecture and Built Environment via farnad.nasirzadeh@deakin.edu.au.
Setting up a security system is a must for maintaining and protecting critical assets, but a good system involves more than just installing cameras and hiring security personnel. When it comes to nationally significant sites such as critical infrastructure, or large developments, there needs to be a system that can fill the gaps where others cannot.
With critical assets at stake, businesses and government agencies cannot afford to settle for less when installing a surveillance system. But some assets may face limitations such as being in a remote area where advanced security systems reliant on grid power may not be an option or cost effective.
Often these assets have limited protection or incomplete coverage from traditional wired security systems tethered to buildings or use human personnel to retroactively tackle any intruders or issues. More often than not, asset managers feel simply forced to do nothing and accept the consequences.
However, Spectur fills that gap in the market by offering surveillance solutions for critical infrastructure where it has been previously impossible to set up.
With systems that can automatically analyse and respond to various threats while being off-the-grid, Spectur provides more than just traditional surveillance – it offers advanced solutions necessary to keep essential services protected from theft and vandalism.
There are many situations where traditional security systems may not be feasible, such as having no access to grid power, being in a remote area or operating in a temporary location. But being impaired by physical location doesn’t mean surveillance is out of the question.
Spectur cameras are not reliant on electricity from the grid because they’re solar-powered. This means locations such as parks, beaches and
campgrounds can be monitored even though power connections are not available. These systems also maintain independent connectivity via the mobile phone network, removing the need for wired connections or even Wi-Fi, which can easily be disrupted.
Instead of spreading human personnel thin across the entire area and throughout the day and night, Spectur instead provides a smart platform that can discern vandals, intruders or hazards, actively deterring them automatically and call for help.
Even for non-remote locations, smart solar-powered camera platforms offer the ability to choose where to place cameras without worrying about having them near a power connection. Cameras can be placed on the perimeter of a property to stop intruders from even jumping the fence. Combined with artificial intelligence (AI), advanced motion detection algorithms and masking to reduce false alarms, this technology is like having an additional “digital fence”.
There is no other product that offers smart, flexible surveillance and deterrence for remote locations. Spectur camera platforms are built to withstand harsh conditions, require minimal maintenance, and remain online for days through inclement weather, serving as a much-needed solution for off-thegrid security.
The Spectur system does not just capture visuals, it also analyses and responds to threats in real-time. While most surveillance cameras can detect threats and record incidents, which can then be used to prosecute individuals responsible for damage or theft, Spectur
cameras utilise artificial intelligence to interpret the images being captured.
Rather than waiting to retroactively punish offenders once they have broken in and damaged or stolen anything, the Spectur system can act immediately to stop intruders in the first place.
The Spectur system can sense threats, think about the appropriate course of action, then act to prevent harm, damage or theft.
The AI can process images to recognise objects, animals, licence plates and humans to discern what is a real threat or not. From there, the system can undertake different actions depending on the threat, including visual displays, audio alarms, in-app alerts, contacting first responders and more.
As opposed to a retroactive response, Spectur is the only solution that offers reliable, automatic and realtime prevention, which is invaluable for critical assets that provide essential services.
Unlike traditional camera surveillance systems, the Spectur system is enhanced through the use of AI and the combination of cloud and edge computing. While AI can help identify and respond to threats, Spectur’s unique cloud computing allows data to be accessed remotely while also engaging local computing for fast response.
Using fog computing means you get the best of both worlds – cloud and edge computing.
Cloud computing allows data to be shared and accessed remotely, but in isolation can increase data transfer costs. Edge computing
uses local computing to store large amounts of data and doesn’t rely on a network connection.
With an exclusive licence to use CSIRO’s Data61 AI platform system, Spectur combines both edge and cloud AI to balance storage and analytics between the device and the cloud, optimising performance, power limitations and data costs. This gives industry leading device performance, including the ability to have more sensors for the same amount of power generation, at the lowest price.
This can help reduce false alarms and wireless communication costs, particularly for areas where the internet is limited. With faster and more accurate responses, issues can be resolved now rather than later.
Relying on surveillance software or technology developed in a country other than Australia could pose a potential security risk, especially for utilities or government assets.
Spectur’s technology, software and cameras are all designed and built in Australia. Using Australian software and technology ensures nationally significant data is not stored on foreign servers, which could potentially fall into the wrong hands.
Additionally, Spectur adheres to national data security standards and protections to prevent data breaches or leaks, which could result in damage or theft of digital assets and information.
A security system is more than just good cameras. You need advanced technology that uses AI and edge computing for real-time response, while being able to store all data and capture it in a secure fashion.
Spectur’s system differentiates itself from the rest by offering remote, autonomous and reliable surveillance that can not only spot a problem, but also make a decision and take action.
Whether you’re setting up a new system or upgrading an existing one, it pays to start with the best.
For more information on creating safe communities during natural disasters using Spectur’s smart solutions, call 1300 802 960 to talk to our team and find the right solution for your unique on-site challenges.
For more information to go https://spectur.com.au/
With the increasing uptake of electric vehicles, researchers at the Reliable, Affordable Clean Energy for 2030 Cooperative Research Centre (RACE for 2030) are leading a project to demonstrate how strategic integration with Australia’s electricity grid and energy storage is vital for electric vehicle adoption.
The adoption of electric vehicles (EVs) is growing rapidly around the world as countries endeavour to decarbonise transport sectors and as EVs become more affordable. As the uptake of EVs accelerates, one particular challenge slowing down the EV uptake in Australia is coordinating a successful integration into society.
Just like other Distributed Energy Resource (DER) solutions, such as demand flexibility, rooftop solar and battery storage, the integration of EVs into homes, businesses, and electricity networks presents a range of opportunities and challenges.
Incentives for EVs in Australia have a way to go before catching up to other developed nations, but the Federal Government has begun to think critically about EV integration.
How EVs are integrated with the energy system will have long-lasting implications for Australia, and calls for a strategic approach informed by cooperation between private industry, government, and research sectors.
The Reliable, Affordable Clean Energy for 2030 Cooperative Research Centre (RACE for 2030) is an industry led cooperative research centre that was established in 2020. With $68.5 million of federal funding and commitments of $280 million of cash and in-kind contributions from partners, RACE for 2030 aims to deliver $3.8 billion of cumulative energy productivity benefits and 20 megatons of cumulative carbon emission savings by 2030.
Cooperative Research Centres lead some of Australia’s largest industry-research collaborations, with recent impact evaluations estimating Australia's centres have delivered $32.5 billion of economic impact from $4.8 billion in government investment.
With this collaboration at the heart of the Cooperative Research Centre Program, RACE for 2030 provides a unique opportunity to bring together a diverse group of industry stakeholders to work collaboratively with leading researchers on the challenges facing the electricity distribution networks, as they look to strategically integrate EVs into the energy system.
ways to integrate EVs with renewable energy generation and storage that have promise for scalability and replicability.
Initial research funded by RACE for 2030 on EV grid integration produced a research opportunity assessment report, Electric Vehicles and the Grid, which recommended key areas of targeted research for future development including:
♦ Data collection
♦ Analysis of current trends and behaviours
♦ Business model design to incentivise beneficial EV charging patterns
♦ Impact analysis of EV adoption on mobility and the design of urban environments
♦ Design of standards and protocols for EV charging equipment and communication devices
Following this research, RACE for 2030 funded the MyV2X project, which undertook national stakeholder consultation and a technical prioritisation study on EV integration. This study, and engagement with RACE for 2030 partners, identified opportunities for partner-led demonstration projects and developed key questions for future research. The study also makes initial recommendations for a technical pathway towards grid integration of EVs and will be released in June 2023 to the public on the RACE for 2030 website.
The Australian Strategic Electric Vehicle Integration Project (SEVI) is a three-year, $3.4 million project that will investigate
Following an initial period of research co-design in 2023, RACE for 2030 partners in New South Wales, South Australia and Western Australia will lead on-the-ground demonstrations, providing matching in-kind support for the research.
Industry partners include Ausgrid, Australian Power Institute, Endeavour Energy, Planet Ark Power, Powertech Energy, New South Wales Government, South Australian Government, Selectronic, SA Power Networks, SwitchDin, Plico Energy, Western Power and Witchcliffe Ecovillage.
The research partners leading the project include Curtin University and University of Technology Sydney, with additional research from Griffith University, Monash University, RMIT University, and University of South Australia.
Through stakeholder engagement in previous projects, RACE for 2030 identified a preference for future research to investigate customer use cases that demonstrate a pathway to scale and replicability.
With this recommendation in mind, demonstration projects chosen for the SEVI project will focus on three use cases:
1. EVs in fleets – in New South Wales, this demonstration will focus on the inclusion of EVs in business fleets in both at-work and at-home charging settings, with optional support from mixed energy storage options
2. EVs in regions – in South Australia, this demonstration will focus on private EVs in regional areas that use behind-the-meter energy storage to understand how private storage capacity can support regional towns
3. EVs in precincts – in Western Australia, this demonstration will focus on private EVs in residential precincts with embedded networks, with optional support from mixed behind-the-meter and front-of-meter energy storage options
The research gathered through these three demonstrations aims to apply learnings from earlier literature on EVs to these partner-led demonstrations so RACE for 2030 can begin bridging the gaps in understanding of how these revolutionary technologies will integrate with Australia’s energy system and wider society.
By investigating on-the-ground demonstration projects that are likely to scale and replicate across Australia, the SEVI project aims to move research beyond the early adopters of EVs and begin uncovering the extent of the cost, impact and wider value that can be captured from the strategic integration of EVs.
As demand for EVs continues to grow, RACE for 2030 will remain focused on building collaboration between researchers and industry, while exploring the opportunities that can be seized as national transportation and energy infrastructure modernises.
Results from this project will build understanding and confidence in the benefits of integrated EVs among consumers, industry, and policymakers. Sharing knowledge and communicating key findings will take place throughout the project and will inform wider practice through avenues including case study reports, digital media, and industry training modules.
It is clear that the transition to electrified transport has begun, but these are just early days.
With 80,000 EVs on Australian roads at present, growing to a possible 2.5-3.5 million by 2030, the additional load EV charging places on the energy system varies depending on when and where it occurs.
Whether EVs cause a slight increase in total demand by 2030, an enormous instantaneous charging load, or are fully integrated into a decentralised energy system is not yet known.
However, what the SEVI project will discover are the approaches that can be used to supercharge government fleet transitions, electrify regional communities, and future-proof residential precincts.
The Department of Finance has appointed NGS Global to seek expressions of interest from experienced Executives and Board Directors for potential Director roles in Government Business Enterprises (GBEs) and other commercial Commonwealth entities that may become vacant throughout 2023.
The GBEs include:
• ASC Pty Ltd
• Australian Naval Infrastructure Pty ltd
• Australian Rail Track Corporation Limited
• Australia Post
• Defence Housing Australia
• National Intermodal Corporation Limited
• NBN Co Limited
• Snowy Hydro Limited
• WSA Co Limited
The Australian Government established these commercially focussed GBEs to contribute to the Australian economy, meet Government policy objectives, enhance productivity and create jobs.
The Department of Finance and partnering shareholder departments advise the Australian Government on the appointment of Directors to GBEs. Directors provide stewardship, strategic leadership, governance, and oversight of GBEs, while also acting as a bridge between Commonwealth policy-making and operational implementation by GBEs. The guide on the Role of Directors in Commonwealth Government Business Enterprises, available from the Department of Finance website, provides an overview of the GBE governance framework for Directors (including where these differ to private sector organisations).
NGS Global is seeking strong, experienced and diverse candidates that are able to contribute to the Government’s complex and significant policy agenda to inform Government of potential candidates. If you have at least two years’ industry experience and executive capabilities relevant to these organisations, please send your expression of interest, comprising of a one page pitch and a CV of no more than two pages, to GBE.director@ngs-global.com or contact Mark Lelliott or Grant Nichol on +61
or
By optimising smart technology and real-time data Australia's largest port is now ahead of the pack.
Port of Newcastle can now turn its focus to managing and delivering vital cargo for Australian businesses after rolling out the Project Lifecycle Management (PLM) module on TechnologyOne’s Software as a Service (SaaS) platform.
As the largest deepwater port on Australia’s east coast, Port of Newcastle plays an important role in the prosperity of the Hunter, New South Wales, and the country. With trade worth approximately $37 billion to Australia’s annual economy, the port enables businesses to successfully compete in international markets.
The port's deepwater shipping channel currently operates at 50 per cent capacity and has significant plans for growth, meaning room for more agricultural items imported and exported to support local farmers, more steel and metal products to support construction and manufacturing, and more fuels to keep transport moving.
Edward Chung, Chief Executive Officer of TechnologyOne said, “Working with organisations, such as Port of Newcastle, that play such a huge role in the country’s imports and
exports and seeing the difference their digital transformation makes to their communities is always exciting.”
In the shipping industry, large volumes mean even small changes can have major impacts, so efficiency and longterm thinking are by-words. According to the Project Leader at the Port of Newcastle, the organisation needed an integrated system providing full control of all projects and complete visibility of where each project is in its lifecycle, to manage them efficiently.
To gain visibility over all projects in a single system and help ensure the port met its long-term capital objectives on time, and within budget, the Port of Newcastle expanded its TechnologyOne suite to include PLM.
TechnologyOne’s PLM module provides organisations with a unified source of truth for all portfolio, program, and project management processes and activities.
It facilitates the organisation and coordination of different stages of
a project's lifecycle in a structured and efficient manner. Additionally, it enables full project visibility across the business, allowing all members to work collaboratively and communicate effectively within the same system.
Ultimately, PLM enhances the port's project management capability from a time, risk and cost perspective.
“The initial objective was to get visibility of all our projects in a single system and implement a consistent stage gate process across the portfolio. Being on SaaS means real-time data is accessible anywhere, anytime and on any device. The dashboards now produced by the system are used from project managers through to executives,” the Project Lead said.
“The benefits achieved since going live with PLM include improved project control, reduced risk of project overspend and improved control over project delivery time.”
Integrating PLM with the Port’s Financials and Asset Management solution means the team can better track and control project budgets, reducing the chances of project overspending, and allowing them to make informed decisions based on accurate and up-to-date information.
“Implementing a robust solution to support the management of projects and provide live data on their status is delivering real benefits in facilitating the project delivery,” the Project Lead said.
Mr Chung said, “Our PLM module has improved the Port of Newcastle’s chances of project success, minimised delays and cost overruns, and ultimately it is delivering better outcomes for the Port and its stakeholders.”
People working in the road transport, warehousing and logistics sector face a number of unique psychosocial challenges in their varied workplaces and roles. This is why Healthy Heads is working hard to support the mental health and wellbeing of those on the frontline of the sector.
Creating psychologically safe workplaces is critical to ensuring that people are healthy, productive and engaged. This means considering the impacts of work environments, practices and cultures on mental health, finding ways to reduce negative impacts and build on positive, protective factors.
It is important when considering mental health that we recognise that we are not only talking about those who have a diagnosed mental health condition. Mental health is something we all possess, all of the time, and it is just as important as our physical health.
Wellbeing represents the interaction between our mental and physical health that makes us feel comfortable, healthy and happy.
Our mental health moves across a continuum from thriving to unwell, with our exposure to mental health risk factors influencing where we sit over time. Risk factors may include personal or work-related challenges, events or circumstances, and are commonly described as things that cause us stress. Many risk factors can have cumulative impacts and how people respond can also vary. The sector's challenge is
to minimise the number of workplace risk factors and to proactively identity and support those who are moving towards unwell on the continuum.
Within the road transport, warehousing and logistic sector there are many inherent aspects of the work which are potential mental health risk factors. These include work environments, schedule pressures, shift work, fatigue and isolation.
The challenges with mental health are demonstrated by a 2021 study which found that 48 per cent of workers in the sector have experienced a mental health condition in the previous 12 months1. It is therefore critical to ensure risk factors are managed in a way that enables workplaces to remain psychologically safe.
Healthy Heads is an industry-led non-for-profit foundation that supports the sector to care for the wellbeing of truck drivers, distribution centre and warehouse staff, and other road transport industry members.
Launched in 2020, Healthy Heads' main focus areas include:
♦ Emphasising the importance of supporting mental health and wellbeing to ensure a thriving workforce into tomorrow
♦ Providing the industry specific resources needed to support mental health and wellbeing
♦ Advocating for and recommending solutions to the mental health and wellbeing challenges within the sector Healthy Heads collaborates and partners with organisations who support mental health within the sector and across the community – to ensure that specific mental health needs of the road transport, warehousing and logistics sector are met. These collaborations include industry stakeholders as well as expert organisations including Lifeline, R U OK? and Black Dog Institute.
Underpinning Healthy Heads' approach is the National Mental Health and Wellbeing Roadmap2. The Roadmap was produced by Healthy Heads in collaboration with industry, government, the National Heavy Vehicle Regulator, and mental health professionals. It provides clear and consistent strategic direction for improving mental health and wellbeing within the sector. The strategy adopts a framework of prevention, protection and support.
Healthy Heads has also developed a range of tailored resources to help individuals and businesses implement the strategic actions described within the Roadmap. These guidelines, toolkits, engagement materials and training courses recognise that the capacity of any one organisation to respond will vary.
To provide the greatest amount of support possible, Healthy Heads provides tailored solutions that suit small, medium and large businesses.
Building a culture that embraces engagement and considers mental health to be just as important as physical health takes time. However, taking the first step is the most important.
Healthy Heads’ philosophy is to encourage conversations about mental health between employees and management. This is often more significant for a workplace than many comprehend, as it builds inclusion, demonstrates support, and identifies areas where businesses can improve.
As engagement grows, increasing organisational capacity is vital. Healthy Heads has collaborated with some of the nation’s leading mental health training organisations to tailor online and in-person courses specifically for the sector. These range from general awareness programs to more detailed Mental Health First Aid and Lifeline's Accidental Counsellor courses. There are also workshops aimed to help businesses develop their own mental health and wellbeing action plans.
The aim for the sector is that all businesses develop, with the support of Healthy Heads resources, an organisationspecific mental health action plan that relates to the mental health risks, capacities and resources of their organisation.
Following a period of resource development, Healthy Heads' goals are now to reach an ever-increasing portion of the industry so that they may put these resources into action.
Healthy Heads is primarily industry funded through support from our Corporate Partners. It is therefore important that this support continues and grows so that we can reach everyone that needs support.
All Australians rely on the road transport, warehousing and logistics sector for the supply of essential goods and supply chain reliability, so it is critically important that the wellbeing of the individuals who operate within the sector is cared for.
To learn more and find out how Healthy Heads can support your business and employees visit healthyheads.org.au.
September 2023 Deadline: 21 July 2023
Ports Asset Management
AI and machine learning
Intelligent Transport Systems (ITS)
Safety and risk management
Sustainability
DISTRIBUTION
March 2024 Deadline: 2 February 2024
Digital
Software,
Signalling,
Condition
Spatial
November 2023 Deadline: 13 October 2023
Rail IoT & cloud communication
Security Disaster management
Tunnels Airport
Drones/UAVS Bridges
Funding/investment
DISTRIBUTION
June 2024 Deadline: 26 April 2024
Airport
Smart
Freight
While traditional trade publications have quality audiences and high levels of trust, they can lack the full range of services to guarantee a return on your investment. And while traditional marketing agencies offer the latest marketing techniques, they don’t have the audience or the industry understanding the B2B sector needs.
Monkey Media is the missing link that brings together a trusted brand and powerful audience, with a complete agency offering.
TO FIND OUT MORE SCAN THE QR CODE NOW